checking oil FORD SIERRA 1989 2.G Engine Electrical Systems Workshop Manual
[x] Cancel search | Manufacturer: FORD, Model Year: 1989, Model line: SIERRA, Model: FORD SIERRA 1989 2.GPages: 24, PDF Size: 0.93 MB
Page 1 of 24
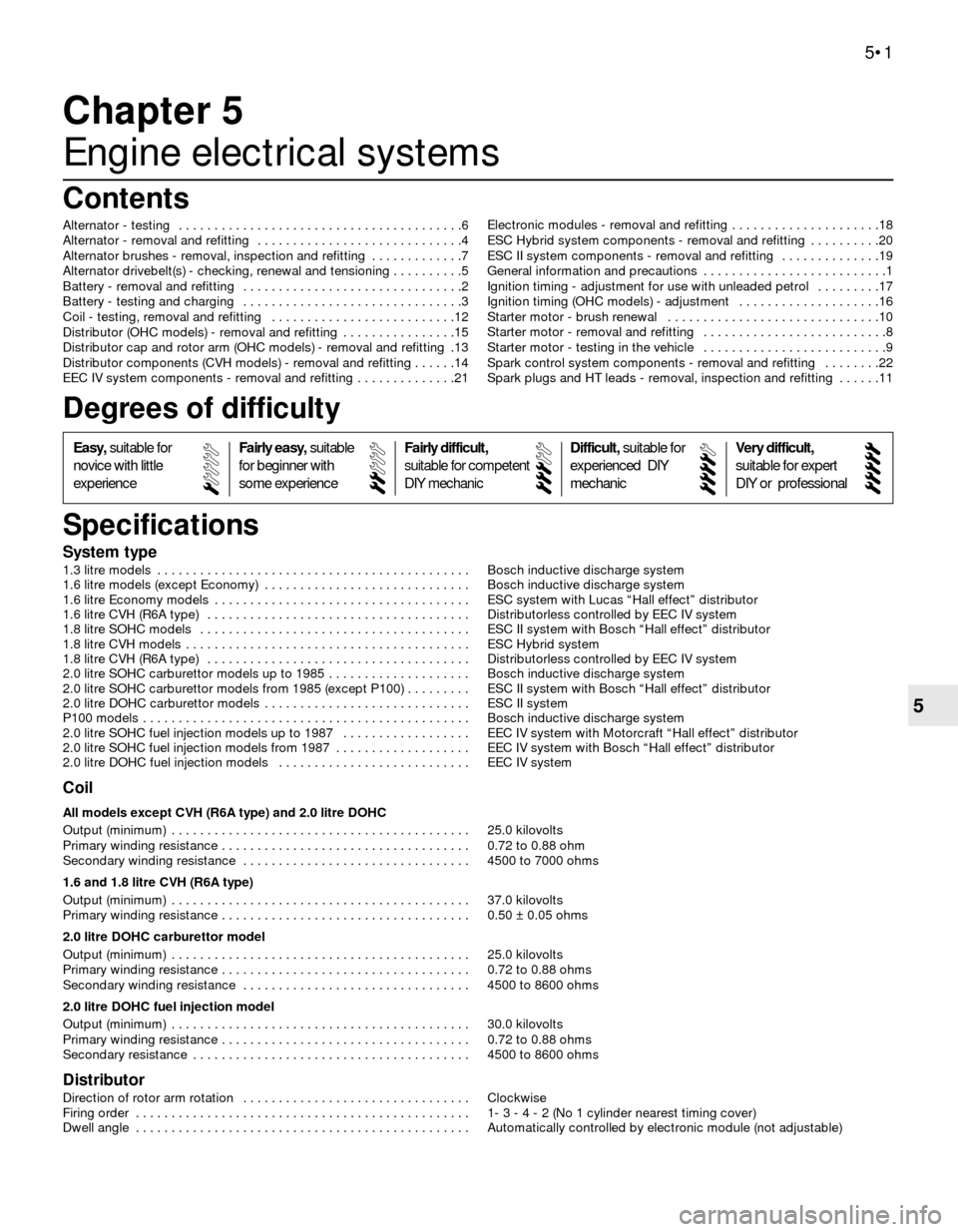
System type
1.3 litre models . . . . . . . . . . . . . . . . . . . . . . . . . . . . . . . . . . . . . . . . . . . . Bosch inductive discharge system
1.6 litre models (except Economy) . . . . . . . . . . . . . . . . . . . . . . . . . . . . . Bosch inductive discharge system
1.6 litre Economy models . . . . . . . . . . . . . . . . . . . . . . . . . . . . . . . . . . . . ESC system with Lucas “Hall effect” distributor
1.6 litre CVH (R6A type) . . . . . . . . . . . . . . . . . . . . . . . . . . . . . . . . . . . . . Distributorless controlled by EEC IV system
1.8 litre SOHC models . . . . . . . . . . . . . . . . . . . . . . . . . . . . . . . . . . . . . . ESC II system with Bosch “Hall effect” distributor
1.8 litre CVH models . . . . . . . . . . . . . . . . . . . . . . . . . . . . . . . . . . . . . . . . ESC Hybrid system
1.8 litre CVH (R6A type) . . . . . . . . . . . . . . . . . . . . . . . . . . . . . . . . . . . . . Distributorless controlled by EEC IV system
2.0 litre SOHC carburettor models up to 1985 . . . . . . . . . . . . . . . . . . . . Bosch inductive discharge system
2.0 litre SOHC carburettor models from 1985 (except P100) . . . . . . . . . ESC II system with Bosch “Hall effect” distributor
2.0 litre DOHC carburettor models . . . . . . . . . . . . . . . . . . . . . . . . . . . . . ESC II system
P100 models . . . . . . . . . . . . . . . . . . . . . . . . . . . . . . . . . . . . . . . . . . . . . . Bosch inductive discharge system
2.0 litre SOHC fuel injection models up to 1987 . . . . . . . . . . . . . . . . . . EEC IV system with Motorcraft “Hall effect” distributor
2.0 litre SOHC fuel injection models from 1987 . . . . . . . . . . . . . . . . . . . EEC IV system with Bosch “Hall effect” distributor
2.0 litre DOHC fuel injection models . . . . . . . . . . . . . . . . . . . . . . . . . . . EEC IV system
Coil
All models except CVH (R6A type) and 2.0 litre DOHC
Output (minimum) . . . . . . . . . . . . . . . . . . . . . . . . . . . . . . . . . . . . . . . . . . 25.0 kilovolts
Primary winding resistance . . . . . . . . . . . . . . . . . . . . . . . . . . . . . . . . . . . 0.72 to 0.88 ohm
Secondary winding resistance . . . . . . . . . . . . . . . . . . . . . . . . . . . . . . . . 4500 to 7000 ohms
1.6 and 1.8 litre CVH (R6A type)
Output (minimum) . . . . . . . . . . . . . . . . . . . . . . . . . . . . . . . . . . . . . . . . . . 37.0 kilovolts
Primary winding resistance . . . . . . . . . . . . . . . . . . . . . . . . . . . . . . . . . . . 0.50 ± 0.05 ohms
2.0 litre DOHC carburettor model
Output (minimum) . . . . . . . . . . . . . . . . . . . . . . . . . . . . . . . . . . . . . . . . . . 25.0 kilovolts
Primary winding resistance . . . . . . . . . . . . . . . . . . . . . . . . . . . . . . . . . . . 0.72 to 0.88 ohms
Secondary winding resistance . . . . . . . . . . . . . . . . . . . . . . . . . . . . . . . . 4500 to 8600 ohms
2.0 litre DOHC fuel injection model
Output (minimum) . . . . . . . . . . . . . . . . . . . . . . . . . . . . . . . . . . . . . . . . . . 30.0 kilovolts
Primary winding resistance . . . . . . . . . . . . . . . . . . . . . . . . . . . . . . . . . . . 0.72 to 0.88 ohms
Secondary resistance . . . . . . . . . . . . . . . . . . . . . . . . . . . . . . . . . . . . . . . 4500 to 8600 ohms
Distributor
Direction of rotor arm rotation . . . . . . . . . . . . . . . . . . . . . . . . . . . . . . . . Clockwise
Firing order . . . . . . . . . . . . . . . . . . . . . . . . . . . . . . . . . . . . . . . . . . . . . . . 1- 3 - 4 - 2 (No 1 cylinder nearest timing cover)
Dwell angle . . . . . . . . . . . . . . . . . . . . . . . . . . . . . . . . . . . . . . . . . . . . . . . Automatically controlled by electronic module (not adjustable)
Chapter 5
Engine electrical systems
Alternator - testing . . . . . . . . . . . . . . . . . . . . . . . . . . . . . . . . . . . . . . . .6
Alternator - removal and refitting . . . . . . . . . . . . . . . . . . . . . . . . . . . . .4
Alternator brushes - removal, inspection and refitting . . . . . . . . . . . . .7
Alternator drivebelt(s) - checking, renewal and tensioning . . . . . . . . . .5
Battery - removal and refitting . . . . . . . . . . . . . . . . . . . . . . . . . . . . . . .2
Battery - testing and charging . . . . . . . . . . . . . . . . . . . . . . . . . . . . . . .3
Coil - testing, removal and refitting . . . . . . . . . . . . . . . . . . . . . . . . . .12
Distributor (OHC models) - removal and refitting . . . . . . . . . . . . . . . .15
Distributor cap and rotor arm (OHC models) - removal and refitting .13
Distributor components (CVH models) - removal and refitting . . . . . .14
EEC IV system components - removal and refitting . . . . . . . . . . . . . .21Electronic modules - removal and refitting . . . . . . . . . . . . . . . . . . . . .18
ESC Hybrid system components - removal and refitting . . . . . . . . . .20
ESC II system components - removal and refitting . . . . . . . . . . . . . .19
General information and precautions . . . . . . . . . . . . . . . . . . . . . . . . . .1
Ignition timing - adjustment for use with unleaded petrol . . . . . . . . .17
Ignition timing (OHC models) - adjustment . . . . . . . . . . . . . . . . . . . .16
Starter motor - brush renewal . . . . . . . . . . . . . . . . . . . . . . . . . . . . . .10
Starter motor - removal and refitting . . . . . . . . . . . . . . . . . . . . . . . . . .8
Starter motor - testing in the vehicle . . . . . . . . . . . . . . . . . . . . . . . . . .9
Spark control system components - removal and refitting . . . . . . . .22
Spark plugs and HT leads - removal, inspection and refitting . . . . . .11
5•1
Specifications Contents
5
Easy,suitable for
novice with little
experienceFairly easy,suitable
for beginner with
some experienceFairly difficult,
suitable for competent
DIY mechanic
Difficult,suitable for
experienced DIY
mechanicVery difficult,
suitable for expert
DIY or professional
Degrees of difficulty
Page 5 of 24
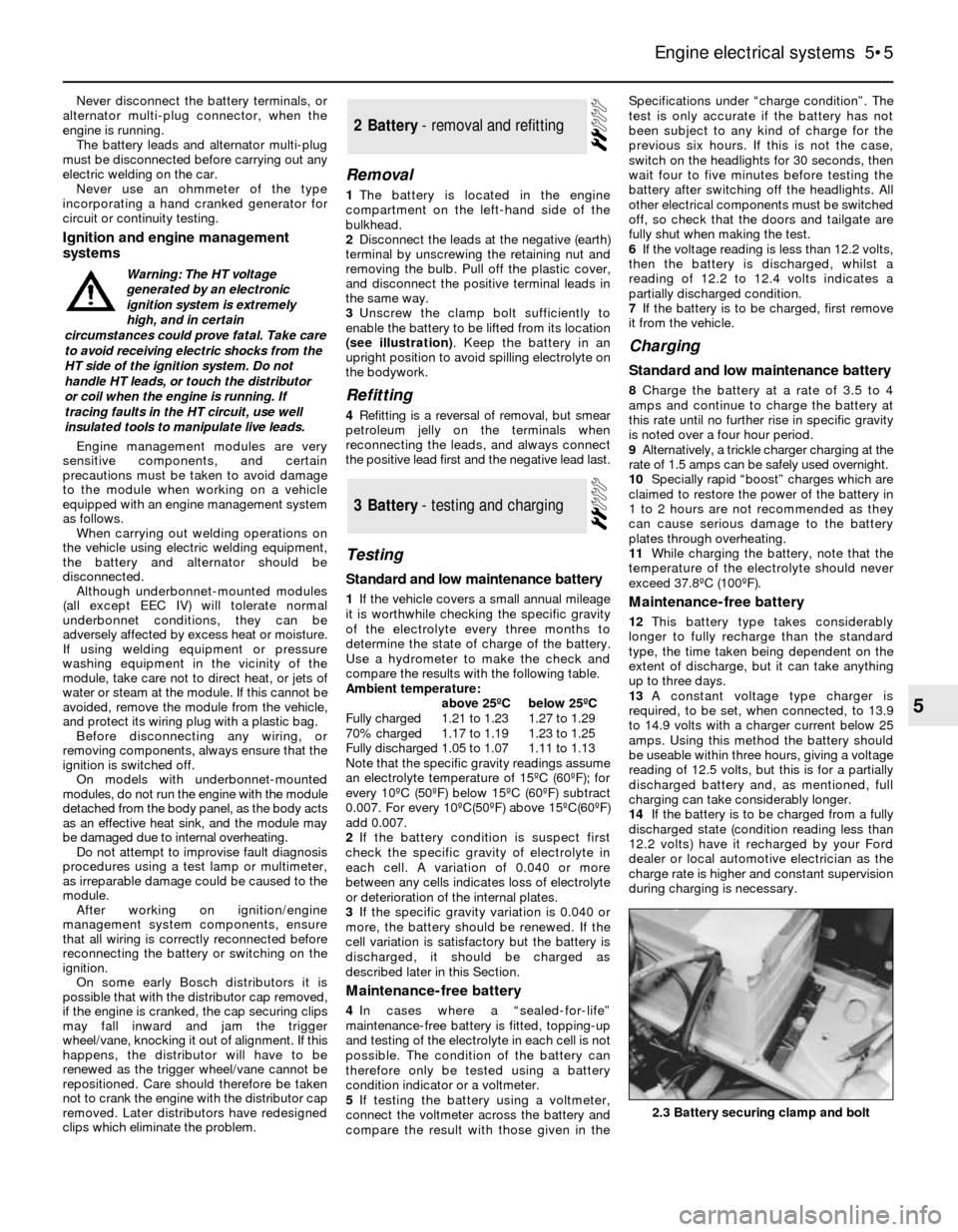
Never disconnect the battery terminals, or
alternator multi-plug connector, when the
engine is running.
The battery leads and alternator multi-plug
must be disconnected before carrying out any
electric welding on the car.
Never use an ohmmeter of the type
incorporating a hand cranked generator for
circuit or continuity testing.
Ignition and engine management
systems
Engine management modules are very
sensitive components, and certain
precautions must be taken to avoid damage
to the module when working on a vehicle
equipped with an engine management system
as follows.
When carrying out welding operations on
the vehicle using electric welding equipment,
the battery and alternator should be
disconnected.
Although underbonnet-mounted modules
(all except EEC IV) will tolerate normal
underbonnet conditions, they can be
adversely affected by excess heat or moisture.
If using welding equipment or pressure
washing equipment in the vicinity of the
module, take care not to direct heat, or jets of
water or steam at the module. If this cannot be
avoided, remove the module from the vehicle,
and protect its wiring plug with a plastic bag.
Before disconnecting any wiring, or
removing components, always ensure that the
ignition is switched off.
On models with underbonnet-mounted
modules, do not run the engine with the module
detached from the body panel, as the body acts
as an effective heat sink, and the module may
be damaged due to internal overheating.
Do not attempt to improvise fault diagnosis
procedures using a test lamp or multimeter,
as irreparable damage could be caused to the
module.
After working on ignition/engine
management system components, ensure
that all wiring is correctly reconnected before
reconnecting the battery or switching on the
ignition.
On some early Bosch distributors it is
possible that with the distributor cap removed,
if the engine is cranked, the cap securing clips
may fall inward and jam the trigger
wheel/vane, knocking it out of alignment. If this
happens, the distributor will have to be
renewed as the trigger wheel/vane cannot be
repositioned. Care should therefore be taken
not to crank the engine with the distributor cap
removed. Later distributors have redesigned
clips which eliminate the problem.
Removal
1The battery is located in the engine
compartment on the left-hand side of the
bulkhead.
2Disconnect the leads at the negative (earth)
terminal by unscrewing the retaining nut and
removing the bulb. Pull off the plastic cover,
and disconnect the positive terminal leads in
the same way.
3Unscrew the clamp bolt sufficiently to
enable the battery to be lifted from its location
(see illustration). Keep the battery in an
upright position to avoid spilling electrolyte on
the bodywork.
Refitting
4Refitting is a reversal of removal, but smear
petroleum jelly on the terminals when
reconnecting the leads, and always connect
the positive lead first and the negative lead last.
Testing
Standard and low maintenance battery
1If the vehicle covers a small annual mileage
it is worthwhile checking the specific gravity
of the electrolyte every three months to
determine the state of charge of the battery.
Use a hydrometer to make the check and
compare the results with the following table.
Ambient temperature:
above 25ºCbelow 25ºC
Fully charged1.21 to 1.231.27 to 1.29
70% charged1.17 to 1.191.23 to 1.25
Fully discharged1.05 to 1.071.11 to 1.13
Note that the specific gravity readings assume
an electrolyte temperature of 15ºC (60ºF); for
every 10ºC (50ºF) below 15ºC (60ºF) subtract
0.007. For every 10ºC(50ºF) above 15ºC(60ºF)
add 0.007.
2If the battery condition is suspect first
check the specific gravity of electrolyte in
each cell. A variation of 0.040 or more
between any cells indicates loss of electrolyte
or deterioration of the internal plates.
3If the specific gravity variation is 0.040 or
more, the battery should be renewed. If the
cell variation is satisfactory but the battery is
discharged, it should be charged as
described later in this Section.
Maintenance-free battery
4In cases where a “sealed-for-life”
maintenance-free battery is fitted, topping-up
and testing of the electrolyte in each cell is not
possible. The condition of the battery can
therefore only be tested using a battery
condition indicator or a voltmeter.
5If testing the battery using a voltmeter,
connect the voltmeter across the battery and
compare the result with those given in theSpecifications under “charge condition”. The
test is only accurate if the battery has not
been subject to any kind of charge for the
previous six hours. If this is not the case,
switch on the headlights for 30 seconds, then
wait four to five minutes before testing the
battery after switching off the headlights. All
other electrical components must be switched
off, so check that the doors and tailgate are
fully shut when making the test.
6If the voltage reading is less than 12.2 volts,
then the battery is discharged, whilst a
reading of 12.2 to 12.4 volts indicates a
partially discharged condition.
7If the battery is to be charged, first remove
it from the vehicle.
Charging
Standard and low maintenance battery
8Charge the battery at a rate of 3.5 to 4
amps and continue to charge the battery at
this rate until no further rise in specific gravity
is noted over a four hour period.
9Alternatively, a trickle charger charging at the
rate of 1.5 amps can be safely used overnight.
10Specially rapid “boost” charges which are
claimed to restore the power of the battery in
1 to 2 hours are not recommended as they
can cause serious damage to the battery
plates through overheating.
11While charging the battery, note that the
temperature of the electrolyte should never
exceed 37.8ºC (100ºF).
Maintenance-free battery
12This battery type takes considerably
longer to fully recharge than the standard
type, the time taken being dependent on the
extent of discharge, but it can take anything
up to three days.
13A constant voltage type charger is
required, to be set, when connected, to 13.9
to 14.9 volts with a charger current below 25
amps. Using this method the battery should
be useable within three hours, giving a voltage
reading of 12.5 volts, but this is for a partially
discharged battery and, as mentioned, full
charging can take considerably longer.
14If the battery is to be charged from a fully
discharged state (condition reading less than
12.2 volts) have it recharged by your Ford
dealer or local automotive electrician as the
charge rate is higher and constant supervision
during charging is necessary.
3Battery - testing and charging
2Battery - removal and refitting
Engine electrical systems 5•5
5
2.3 Battery securing clamp and bolt
Warning: The HT voltage
generated by an electronic
ignition system is extremely
high, and in certain
circumstances could prove fatal. Take care
to avoid receiving electric shocks from the
HT side of the ignition system. Do not
handle HT leads, or touch the distributor
or coil when the engine is running. If
tracing faults in the HT circuit, use well
insulated tools to manipulate live leads.
Page 6 of 24
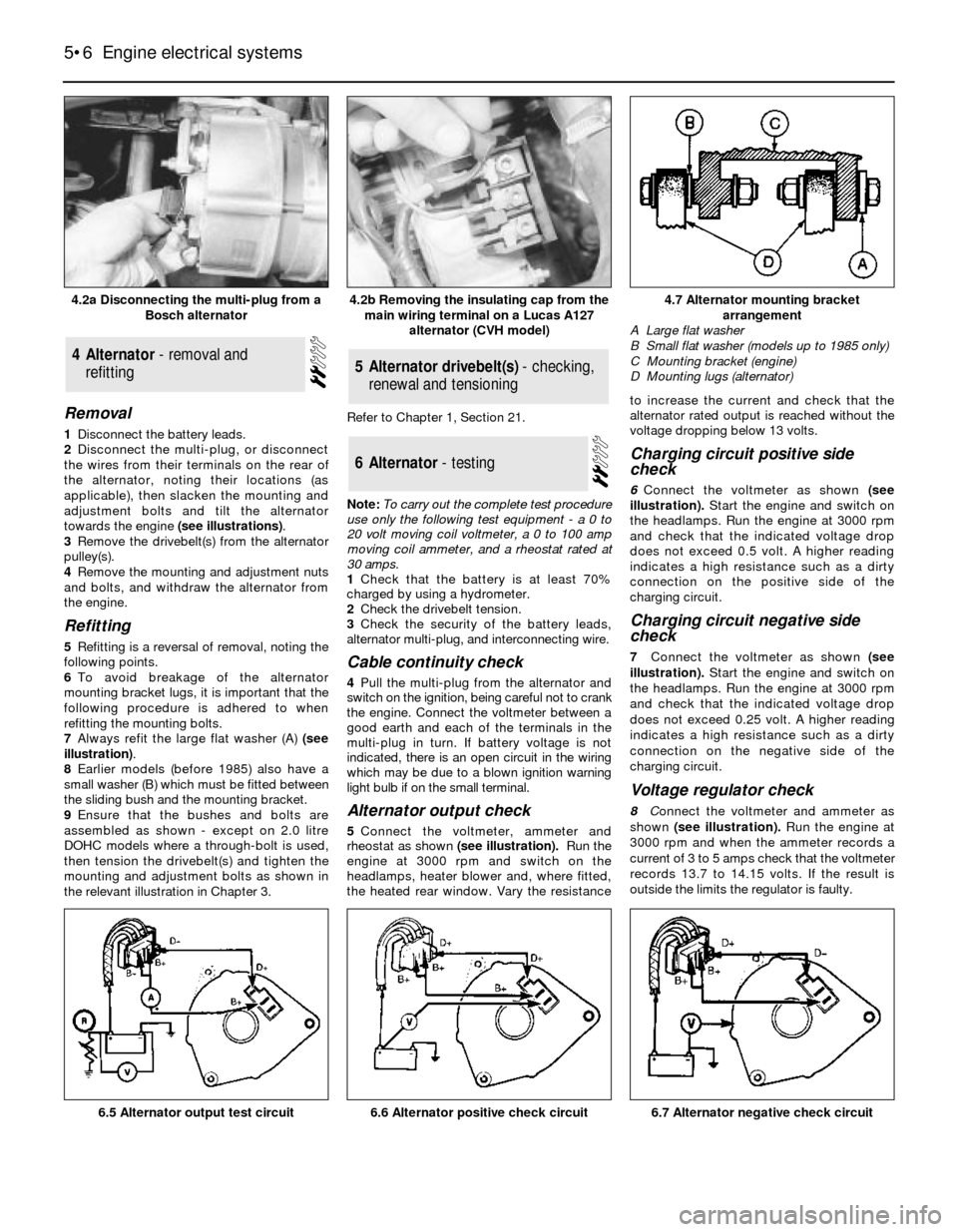
Removal
1Disconnect the battery leads.
2Disconnect the multi-plug, or disconnect
the wires from their terminals on the rear of
the alternator, noting their locations (as
applicable), then slacken the mounting and
adjustment bolts and tilt the alternator
towards the engine (see illustrations).
3Remove the drivebelt(s) from the alternator
pulley(s).
4Remove the mounting and adjustment nuts
and bolts, and withdraw the alternator from
the engine.
Refitting
5Refitting is a reversal of removal, noting the
following points.
6To avoid breakage of the alternator
mounting bracket lugs, it is important that the
following procedure is adhered to when
refitting the mounting bolts.
7Always refit the large flat washer (A) (see
illustration).
8Earlier models (before 1985) also have a
small washer (B) which must be fitted between
the sliding bush and the mounting bracket.
9Ensure that the bushes and bolts are
assembled as shown - except on 2.0 litre
DOHC models where a through-bolt is used,
then tension the drivebelt(s) and tighten the
mounting and adjustment bolts as shown in
the relevant illustration in Chapter 3.Refer to Chapter 1, Section 21.
Note: To carry out the complete test procedure
use only the following test equipment - a 0 to
20 volt moving coil voltmeter, a 0 to 100 amp
moving coil ammeter, and a rheostat rated at
30 amps.
1Check that the battery is at least 70%
charged by using a hydrometer.
2Check the drivebelt tension.
3Check the security of the battery leads,
alternator multi-plug, and interconnecting wire.
Cable continuity check
4Pull the multi-plug from the alternator and
switch on the ignition, being careful not to crank
the engine. Connect the voltmeter between a
good earth and each of the terminals in the
multi-plug in turn. If battery voltage is not
indicated, there is an open circuit in the wiring
which may be due to a blown ignition warning
light bulb if on the small terminal.
Alternator output check
5Connect the voltmeter, ammeter and
rheostat as shown (see illustration).Run the
engine at 3000 rpm and switch on the
headlamps, heater blower and, where fitted,
the heated rear window. Vary the resistanceto increase the current and check that the
alternator rated output is reached without the
voltage dropping below 13 volts.
Charging circuit positive side
check
6Connect the voltmeter as shown (see
illustration).Start the engine and switch on
the headlamps. Run the engine at 3000 rpm
and check that the indicated voltage drop
does not exceed 0.5 volt. A higher reading
indicates a high resistance such as a dirty
connection on the positive side of the
charging circuit.
Charging circuit negative side
check
7Connect the voltmeter as shown (see
illustration).Start the engine and switch on
the headlamps. Run the engine at 3000 rpm
and check that the indicated voltage drop
does not exceed 0.25 volt. A higher reading
indicates a high resistance such as a dirty
connection on the negative side of the
charging circuit.
Voltage regulator check
8Connect the voltmeter and ammeter as
shown(see illustration).Run the engine at
3000 rpm and when the ammeter records a
current of 3 to 5 amps check that the voltmeter
records 13.7 to 14.15 volts. If the result is
outside the limits the regulator is faulty.
6Alternator - testing
5Alternator drivebelt(s) - checking,
renewal and tensioning4Alternator - removal and
refitting
5•6Engine electrical systems
4.2a Disconnecting the multi-plug from a
Bosch alternator4.7 Alternator mounting bracket
arrangement
A Large flat washer
B Small flat washer (models up to 1985 only)
C Mounting bracket (engine)
D Mounting lugs (alternator)
6.7 Alternator negative check circuit6.6 Alternator positive check circuit6.5 Alternator output test circuit
4.2b Removing the insulating cap from the
main wiring terminal on a Lucas A127
alternator (CVH model)
Page 17 of 24
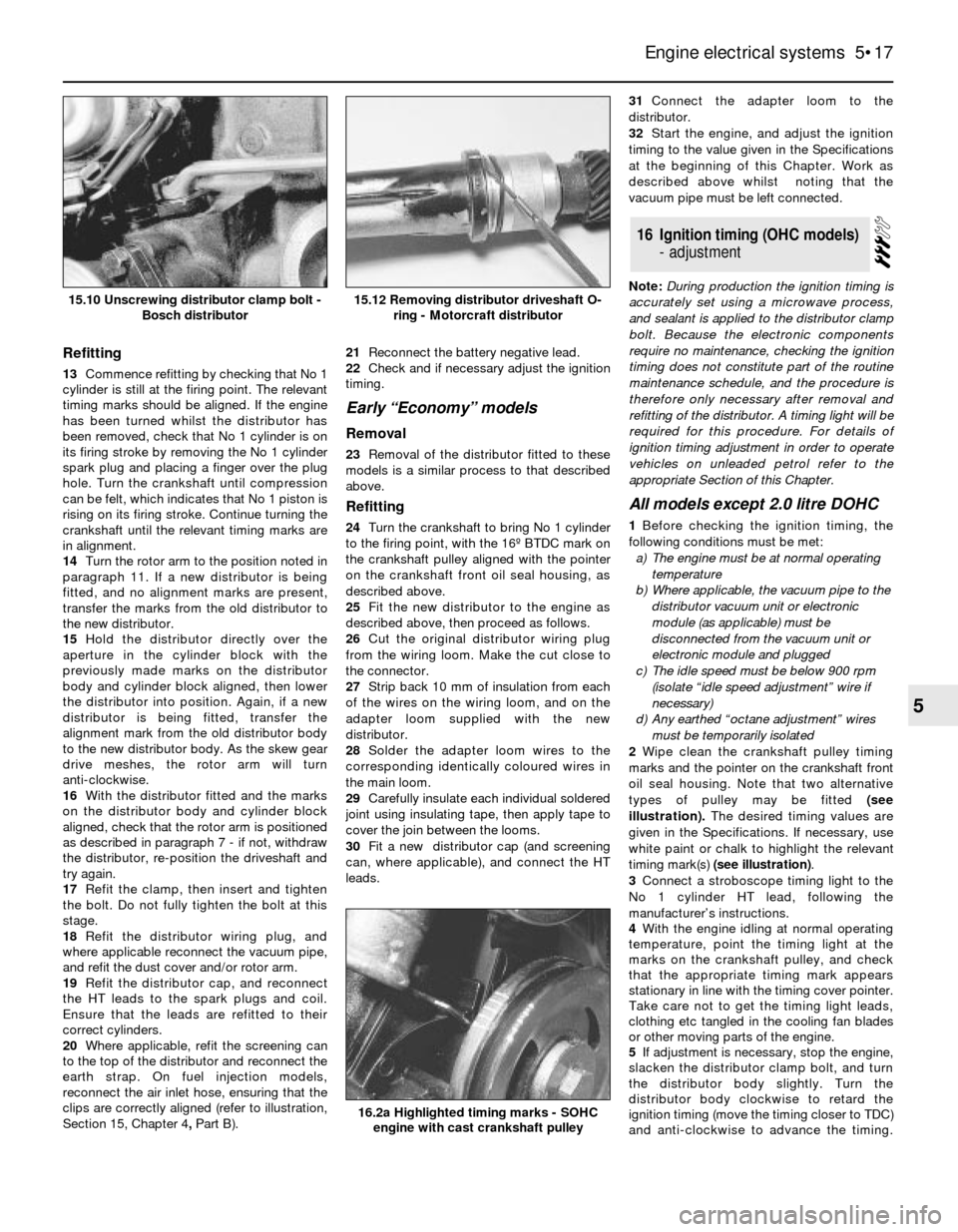
Refitting
13Commence refitting by checking that No 1
cylinder is still at the firing point. The relevant
timing marks should be aligned. If the engine
has been turned whilst the distributor has
been removed, check that No 1 cylinder is on
its firing stroke by removing the No 1 cylinder
spark plug and placing a finger over the plug
hole. Turn the crankshaft until compression
can be felt, which indicates that No 1 piston is
rising on its firing stroke. Continue turning the
crankshaft until the relevant timing marks are
in alignment.
14Turn the rotor arm to the position noted in
paragraph 11. If a new distributor is being
fitted, and no alignment marks are present,
transfer the marks from the old distributor to
the new distributor.
15Hold the distributor directly over the
aperture in the cylinder block with the
previously made marks on the distributor
body and cylinder block aligned, then lower
the distributor into position. Again, if a new
distributor is being fitted, transfer the
alignment mark from the old distributor body
to the new distributor body. As the skew gear
drive meshes, the rotor arm will turn
anti-clockwise.
16With the distributor fitted and the marks
on the distributor body and cylinder block
aligned, check that the rotor arm is positioned
as described in paragraph 7 -if not, withdraw
the distributor, re-position the driveshaft and
try again.
17Refit the clamp, then insert and tighten
the bolt. Do not fully tighten the bolt at this
stage.
18Refit the distributor wiring plug, and
where applicable reconnect the vacuum pipe,
and refit the dust cover and/or rotor arm.
19Refit the distributor cap, and reconnect
the HT leads to the spark plugs and coil.
Ensure that the leads are refitted to their
correct cylinders.
20Where applicable, refit the screening can
to the top of the distributor and reconnect the
earth strap. On fuel injection models,
reconnect the air inlet hose, ensuring that the
clips are correctly aligned (refer to illustration,
Section 15, Chapter 4, PartB).21Reconnect the battery negative lead.
22Check and if necessary adjust the ignition
timing.
Early “Economy” models
Removal
23Removal of the distributor fitted to these
models is a similar process to that described
above.
Refitting
24Turn the crankshaft to bring No 1 cylinder
to the firing point, with the 16º BTDC mark on
the crankshaft pulley aligned with the pointer
on the crankshaft front oil seal housing, as
described above.
25Fit the new distributor to the engine as
described above, then proceed as follows.
26Cut the original distributor wiring plug
from the wiring loom. Make the cut close to
the connector.
27Strip back 10 mm of insulation from each
of the wires on the wiring loom, and on the
adapter loom supplied with the new
distributor.
28Solder the adapter loom wires to the
corresponding identically coloured wires in
the main loom.
29Carefully insulate each individual soldered
joint using insulating tape, then apply tape to
cover the join between the looms.
30Fit a new distributor cap (and screening
can, where applicable), and connect the HT
leads.31Connect the adapter loom to the
distributor.
32Start the engine, and adjust the ignition
timing to the value given in the Specifications
at the beginning of this Chapter. Work as
described above whilst noting that the
vacuum pipe must be left connected.
Note: During production the ignition timing is
accurately set using a microwave process,
and sealant is applied to the distributor clamp
bolt. Because the electronic components
require no maintenance, checking the ignition
timing does not constitute part of the routine
maintenance schedule, and the procedure is
therefore only necessary after removal and
refitting of the distributor. A timing light will be
required for this procedure. For details of
ignition timing adjustment in order to operate
vehicles on unleaded petrol refer to the
appropriate Section of this Chapter.
All models except 2.0 litre DOHC
1Before checking the ignition timing, the
following conditions must be met:
a)The engine must be at normal operating
temperature
b)Where applicable, the vacuum pipe to the
distributor vacuum unit or electronic
module (as applicable) must be
disconnected from the vacuum unit or
electronic module and plugged
c)The idle speed must be below 900 rpm
(isolate “idle speed adjustment” wire if
necessary)
d)Any earthed “octane adjustment” wires
must be temporarily isolated
2Wipe clean the crankshaft pulley timing
marks and the pointer on the crankshaft front
oil seal housing. Note that two alternative
types of pulley may be fitted (see
illustration).The desired timing values are
given in the Specifications. If necessary, use
white paint or chalk to highlight the relevant
timing mark(s) (see illustration).
3Connect a stroboscope timing light to the
No 1 cylinder HT lead, following the
manufacturer’s instructions.
4With the engine idling at normal operating
temperature, point the timing light at the
marks on the crankshaft pulley, and check
that the appropriate timing mark appears
stationary in line with the timing cover pointer.
Take care not to get the timing light leads,
clothing etc tangled in the cooling fan blades
or other moving parts of the engine.
5If adjustment is necessary, stop the engine,
slacken the distributor clamp bolt, and turn
the distributor body slightly. Turn the
distributor body clockwise to retard the
ignition timing (move the timing closer to TDC)
and anti-clockwise to advance the timing.
16Ignition timing (OHC models)
- adjustment
Engine electrical systems 5•17
5
15.12 Removing distributor driveshaft O-
ring - Motorcraft distributor15.10 Unscrewing distributor clamp bolt -
Bosch distributor
16.2a Highlighted timing marks - SOHC
engine with cast crankshaft pulley