length FORD SIERRA 1991 2.G Engine Electrical Systems Workshop Manual
[x] Cancel search | Manufacturer: FORD, Model Year: 1991, Model line: SIERRA, Model: FORD SIERRA 1991 2.GPages: 24, PDF Size: 0.93 MB
Page 2 of 24
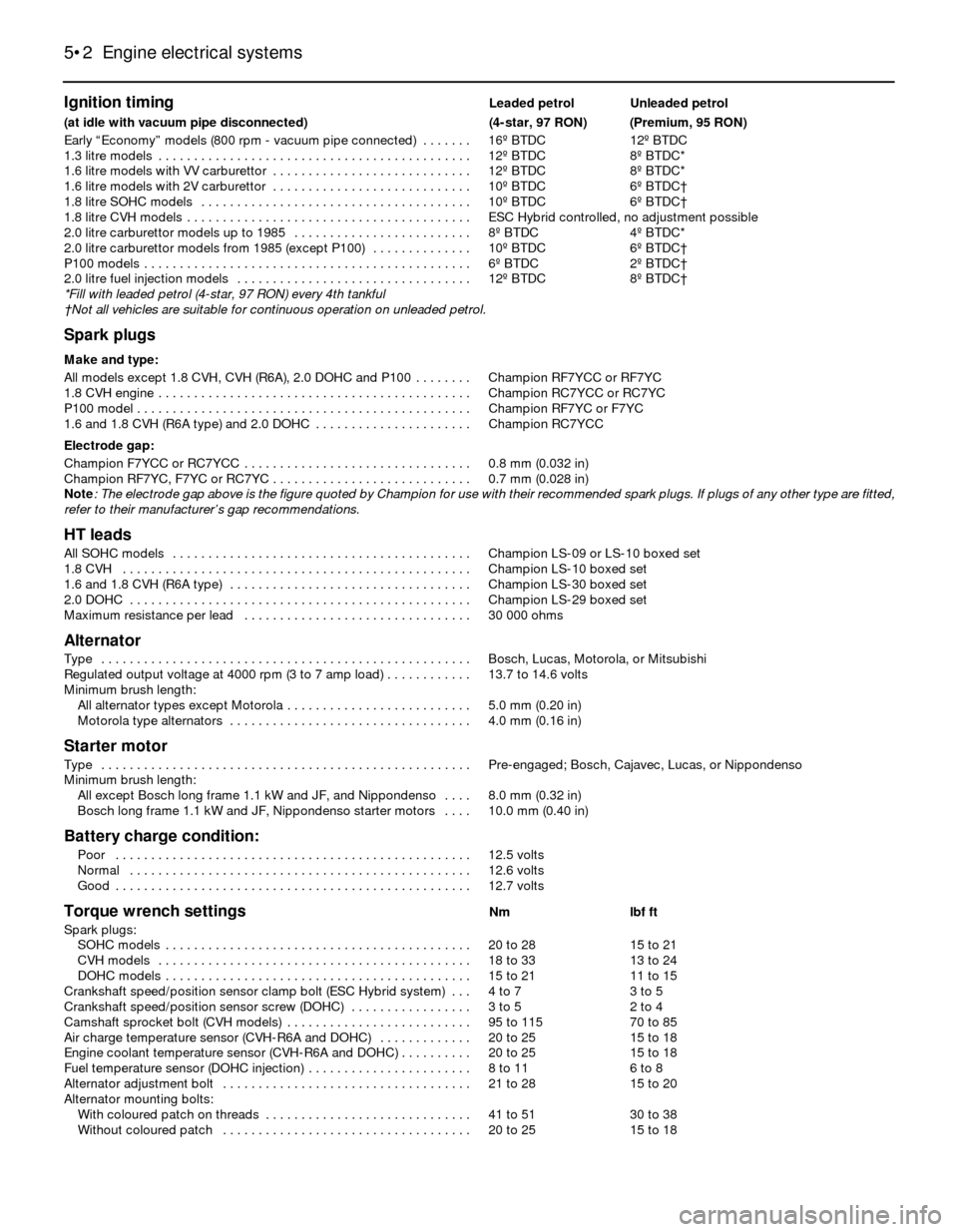
Ignition timingLeaded petrolUnleaded petrol
(at idle with vacuum pipe disconnected)(4-star, 97 RON)(Premium, 95 RON)
Early “Economy” models (800 rpm - vacuum pipe connected) . . . . . . .16º BTDC12º BTDC
1.3 litre models . . . . . . . . . . . . . . . . . . . . . . . . . . . . . . . . . . . . . . . . . . . .12º BTDC8º BTDC*
1.6 litre models with VV carburettor . . . . . . . . . . . . . . . . . . . . . . . . . . . .12º BTDC8º BTDC*
1.6 litre models with 2V carburettor . . . . . . . . . . . . . . . . . . . . . . . . . . . .10º BTDC6º BTDC†
1.8 litre SOHC models . . . . . . . . . . . . . . . . . . . . . . . . . . . . . . . . . . . . . .10º BTDC6º BTDC†
1.8 litre CVH models . . . . . . . . . . . . . . . . . . . . . . . . . . . . . . . . . . . . . . . .ESC Hybrid controlled, no adjustment possible
2.0 litre carburettor models up to 1985 . . . . . . . . . . . . . . . . . . . . . . . . .8º BTDC4º BTDC*
2.0 litre carburettor models from 1985 (except P100) . . . . . . . . . . . . . .10º BTDC6º BTDC†
P100 models . . . . . . . . . . . . . . . . . . . . . . . . . . . . . . . . . . . . . . . . . . . . . .6º BTDC2º BTDC†
2.0 litre fuel injection models . . . . . . . . . . . . . . . . . . . . . . . . . . . . . . . . .12º BTDC8º BTDC†
*Fill with leaded petrol (4-star, 97 RON) every 4th tankful
†Not all vehicles are suitable for continuous operation on unleaded petrol.
Spark plugs
Make and type:
All models except 1.8 CVH, CVH (R6A), 2.0 DOHC and P100 . . . . . . . .Champion RF7YCC or RF7YC
1.8 CVH engine . . . . . . . . . . . . . . . . . . . . . . . . . . . . . . . . . . . . . . . . . . . .Champion RC7YCC or RC7YC
P100 model . . . . . . . . . . . . . . . . . . . . . . . . . . . . . . . . . . . . . . . . . . . . . . .Champion RF7YC or F7YC
1.6 and 1.8 CVH (R6A type) and 2.0 DOHC . . . . . . . . . . . . . . . . . . . . . .Champion RC7YCC
Electrode gap:
Champion F7YCC or RC7YCC . . . . . . . . . . . . . . . . . . . . . . . . . . . . . . . .0.8 mm (0.032 in)
Champion RF7YC, F7YC or RC7YC . . . . . . . . . . . . . . . . . . . . . . . . . . . .0.7 mm (0.028 in)
Note: The electrode gap above is the figure quoted by Champion for use with their recommended spark plugs. If plugs of any other type are fitted,
refer to their manufacturer’s gap recommendations.
HT leads
All SOHC models . . . . . . . . . . . . . . . . . . . . . . . . . . . . . . . . . . . . . . . . . .Champion LS-09 or LS-10 boxed set
1.8 CVH . . . . . . . . . . . . . . . . . . . . . . . . . . . . . . . . . . . . . . . . . . . . . . . . .Champion LS-10 boxed set
1.6 and 1.8 CVH (R6A type) . . . . . . . . . . . . . . . . . . . . . . . . . . . . . . . . . .Champion LS-30 boxed set
2.0 DOHC . . . . . . . . . . . . . . . . . . . . . . . . . . . . . . . . . . . . . . . . . . . . . . . .Champion LS-29 boxed set
Maximum resistance per lead . . . . . . . . . . . . . . . . . . . . . . . . . . . . . . . .30 000 ohms
Alternator
Type . . . . . . . . . . . . . . . . . . . . . . . . . . . . . . . . . . . . . . . . . . . . . . . . . . . .Bosch, Lucas, Motorola, or Mitsubishi
Regulated output voltage at 4000 rpm (3 to 7 amp load) . . . . . . . . . . . .13.7 to 14.6 volts
Minimum brush length:
All alternator types except Motorola . . . . . . . . . . . . . . . . . . . . . . . . . .5.0 mm (0.20 in)
Motorola type alternators . . . . . . . . . . . . . . . . . . . . . . . . . . . . . . . . . .4.0 mm (0.16 in)
Starter motor
Type . . . . . . . . . . . . . . . . . . . . . . . . . . . . . . . . . . . . . . . . . . . . . . . . . . . .Pre-engaged; Bosch, Cajavec, Lucas, or Nippondenso
Minimum brush length:
All except Bosch long frame 1.1 kW and JF, and Nippondenso . . . .8.0 mm (0.32 in)
Bosch long frame 1.1 kW and JF, Nippondenso starter motors . . . .10.0 mm (0.40 in)
Battery charge condition:
Poor . . . . . . . . . . . . . . . . . . . . . . . . . . . . . . . . . . . . . . . . . . . . . . . . . .12.5 volts
Normal . . . . . . . . . . . . . . . . . . . . . . . . . . . . . . . . . . . . . . . . . . . . . . . .12.6 volts
Good . . . . . . . . . . . . . . . . . . . . . . . . . . . . . . . . . . . . . . . . . . . . . . . . . .12.7 volts
Torque wrench settingsNmlbf ft
Spark plugs:
SOHC models . . . . . . . . . . . . . . . . . . . . . . . . . . . . . . . . . . . . . . . . . . .20 to 2815 to 21
CVH models . . . . . . . . . . . . . . . . . . . . . . . . . . . . . . . . . . . . . . . . . . . .18 to 3313 to 24
DOHC models . . . . . . . . . . . . . . . . . . . . . . . . . . . . . . . . . . . . . . . . . . .15 to 2111 to 15
Crankshaft speed/position sensor clamp bolt (ESC Hybrid system) . . .4 to 73 to 5
Crankshaft speed/position sensor screw (DOHC) . . . . . . . . . . . . . . . . .3 to 52 to 4
Camshaft sprocket bolt (CVH models) . . . . . . . . . . . . . . . . . . . . . . . . . .95 to 11570 to 85
Air charge temperature sensor (CVH-R6A and DOHC) . . . . . . . . . . . . .20 to 2515 to 18
Engine coolant temperature sensor (CVH-R6A and DOHC) . . . . . . . . . .20 to 2515 to 18
Fuel temperature sensor (DOHC injection) . . . . . . . . . . . . . . . . . . . . . . .8 to 116 to 8
Alternator adjustment bolt . . . . . . . . . . . . . . . . . . . . . . . . . . . . . . . . . . .21 to 2815 to 20
Alternator mounting bolts:
With coloured patch on threads . . . . . . . . . . . . . . . . . . . . . . . . . . . . .41 to 5130 to 38
Without coloured patch . . . . . . . . . . . . . . . . . . . . . . . . . . . . . . . . . . .20 to 2515 to 18
5•2Engine electrical systems
Page 7 of 24
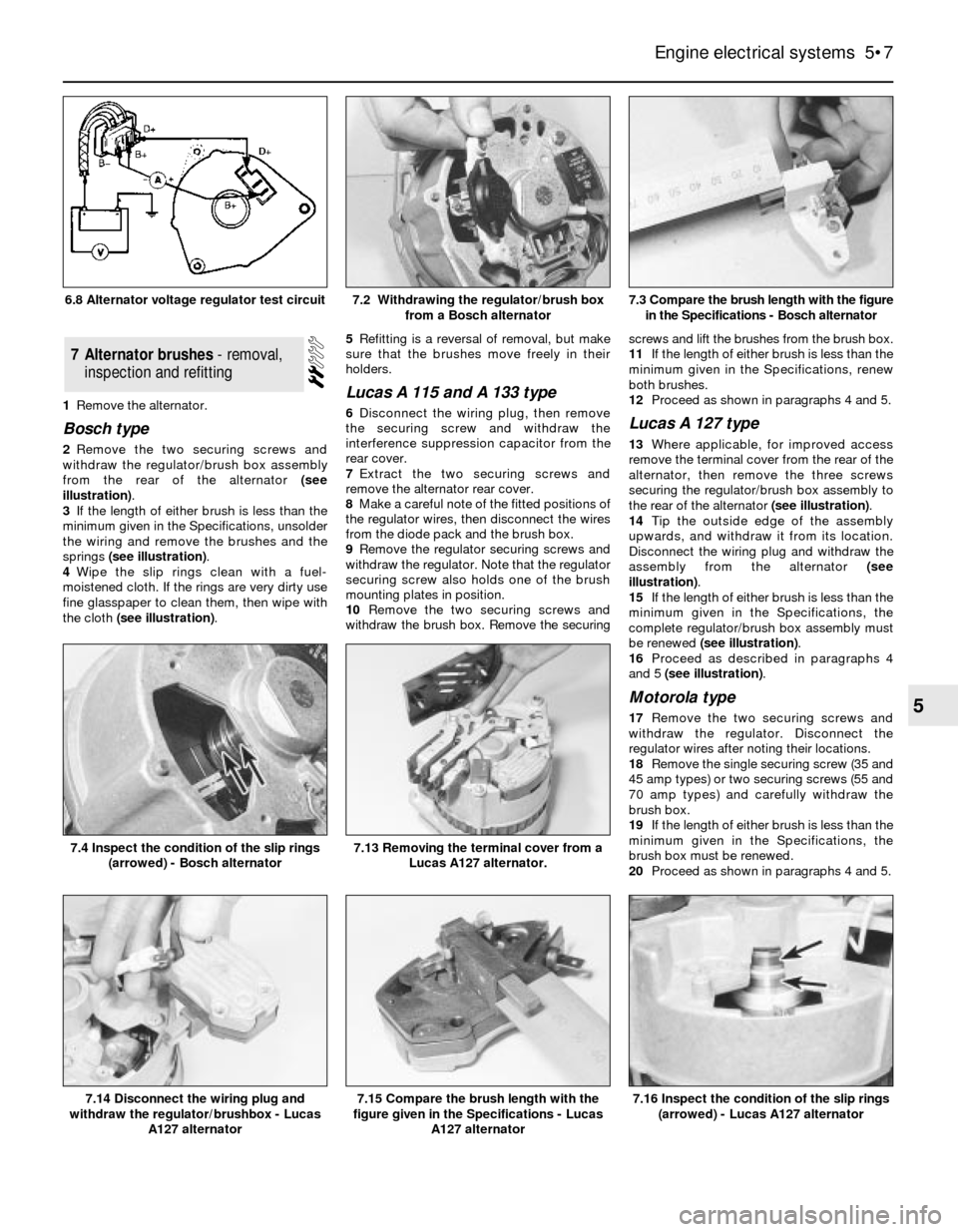
1Remove the alternator.
Bosch type
2Remove the two securing screws and
withdraw the regulator/brush box assembly
from the rear of the alternator (see
illustration).
3If the length of either brush is less than the
minimum given in the Specifications, unsolder
the wiring and remove the brushes and the
springs (see illustration).
4Wipe the slip rings clean with a fuel-
moistened cloth. If the rings are very dirty use
fine glasspaper to clean them, then wipe with
the cloth (see illustration).5Refitting is a reversal of removal, but make
sure that the brushes move freely in their
holders.
Lucas A 115 and A 133 type
6Disconnect the wiring plug, then remove
the securing screw and withdraw the
interference suppression capacitor from the
rear cover.
7Extract the two securing screws and
remove the alternator rear cover.
8Make a careful note of the fitted positions of
the regulator wires, then disconnect the wires
from the diode pack and the brush box.
9Remove the regulator securing screws and
withdraw the regulator. Note that the regulator
securing screw also holds one of the brush
mounting plates in position.
10Remove the two securing screws and
withdraw the brush box. Remove the securingscrews and lift the brushes from the brush box.
11If the length of either brush is less than the
minimum given in the Specifications, renew
both brushes.
12Proceed as shown in paragraphs 4 and 5.Lucas A 127 type
13Where applicable, for improved access
remove the terminal cover from the rear of the
alternator, then remove the three screws
securing the regulator/brush box assembly to
the rear of the alternator (see illustration).
14Tip the outside edge of the assembly
upwards, and withdraw it from its location.
Disconnect the wiring plug and withdraw the
assembly from the alternator (see
illustration).
15If the length of either brush is less than the
minimum given in the Specifications, the
complete regulator/brush box assembly must
be renewed (see illustration).
16Proceed as described in paragraphs 4
and 5 (see illustration).
Motorola type
17Remove the two securing screws and
withdraw the regulator. Disconnect the
regulator wires after noting their locations.
18Remove the single securing screw (35 and
45 amp types) or two securing screws (55 and
70 amp types) and carefully withdraw the
brush box.
19If the length of either brush is less than the
minimum given in the Specifications, the
brush box must be renewed.
20Proceed as shown in paragraphs 4 and 5.
7Alternator brushes - removal,
inspection and refitting
Engine electrical systems 5•7
5
7.3 Compare the brush length with the figure
in the Specifications - Bosch alternator
7.16 Inspect the condition of the slip rings
(arrowed) - Lucas A127 alternator7.15 Compare the brush length with the
figure given in the Specifications - Lucas
A127 alternator7.14 Disconnect the wiring plug and
withdraw the regulator/brushbox - Lucas
A127 alternator
7.13 Removing the terminal cover from a
Lucas A127 alternator.7.4 Inspect the condition of the slip rings
(arrowed) - Bosch alternator
7.2 Withdrawing the regulator/brush box
from a Bosch alternator6.8 Alternator voltage regulator test circuit
Page 8 of 24
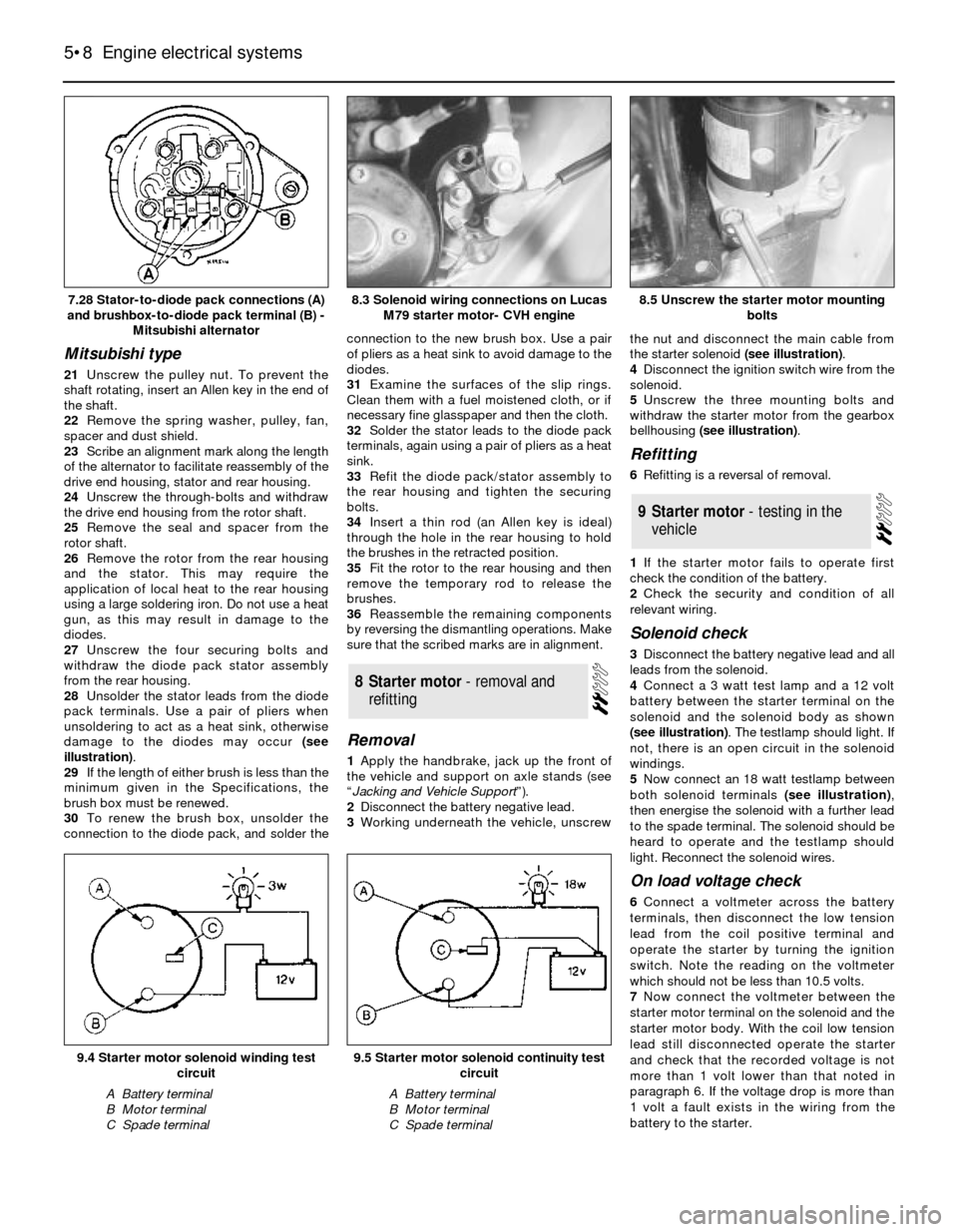
Mitsubishi type
21Unscrew the pulley nut. To prevent the
shaft rotating, insert an Allen key in the end of
the shaft.
22Remove the spring washer, pulley, fan,
spacer and dust shield.
23Scribe an alignment mark along the length
of the alternator to facilitate reassembly of the
drive end housing, stator and rear housing.
24Unscrew the through-bolts and withdraw
the drive end housing from the rotor shaft.
25Remove the seal and spacer from the
rotor shaft.
26Remove the rotor from the rear housing
and the stator. This may require the
application of local heat to the rear housing
using a large soldering iron. Do not use a heat
gun, as this may result in damage to the
diodes.
27Unscrew the four securing bolts and
withdraw the diode pack stator assembly
from the rear housing.
28Unsolder the stator leads from the diode
pack terminals. Use a pair of pliers when
unsoldering to act as a heat sink, otherwise
damage to the diodes may occur (see
illustration).
29If the length of either brush is less than the
minimum given in the Specifications, the
brush box must be renewed.
30To renew the brush box, unsolder the
connection to the diode pack, and solder theconnection to the new brush box. Use a pair
of pliers as a heat sink to avoid damage to the
diodes.
31Examine the surfaces of the slip rings.
Clean them with a fuel moistened cloth, or if
necessary fine glasspaper and then the cloth.
32Solder the stator leads to the diode pack
terminals, again using a pair of pliers as a heat
sink.
33Refit the diode pack/stator assembly to
the rear housing and tighten the securing
bolts.
34Insert a thin rod (an Allen key is ideal)
through the hole in the rear housing to hold
the brushes in the retracted position.
35Fit the rotor to the rear housing and then
remove the temporary rod to release the
brushes.
36Reassemble the remaining components
by reversing the dismantling operations. Make
sure that the scribed marks are in alignment.
Removal
1Apply the handbrake, jack up the front of
the vehicle and support on axle stands (see
“Jacking and Vehicle Support”).
2Disconnect the battery negative lead.
3Working underneath the vehicle, unscrewthe nut and disconnect the main cable from
the starter solenoid (see illustration).
4Disconnect the ignition switch wire from the
solenoid.
5Unscrew the three mounting bolts and
withdraw the starter motor from the gearbox
bellhousing (see illustration).
Refitting
6Refitting is a reversal of removal.
1If the starter motor fails to operate first
check the condition of the battery.
2Check the security and condition of all
relevant wiring.
Solenoid check
3Disconnect the battery negative lead and all
leads from the solenoid.
4Connect a 3 watt test lamp and a 12 volt
battery between the starter terminal on the
solenoid and the solenoid body as shown
(see illustration). The testlamp should light. If
not, there is an open circuit in the solenoid
windings.
5Now connect an 18 watt testlamp between
both solenoid terminals (see illustration),
then energise the solenoid with a further lead
to the spade terminal. The solenoid should be
heard to operate and the testlamp should
light. Reconnect the solenoid wires.
On load voltage check
6Connect a voltmeter across the battery
terminals, then disconnect the low tension
lead from the coil positive terminal and
operate the starter by turning the ignition
switch. Note the reading on the voltmeter
which should not be less than 10.5 volts.
7Now connect the voltmeter between the
starter motor terminal on the solenoid and the
starter motor body. With the coil low tension
lead still disconnected operate the starter
and check that the recorded voltage is not
more than 1 volt lower than that noted in
paragraph 6. If the voltage drop is more than
1 volt a fault exists in the wiring from the
battery to the starter.
9Starter motor - testing in the
vehicle
8Starter motor - removal and
refitting
5•8Engine electrical systems
7.28 Stator-to-diode pack connections (A)
and brushbox-to-diode pack terminal (B) -
Mitsubishi alternator8.5 Unscrew the starter motor mounting
bolts
9.5 Starter motor solenoid continuity test
circuit
A Battery terminal
B Motor terminal
C Spade terminal
9.4 Starter motor solenoid winding test
circuit
A Battery terminal
B Motor terminal
C Spade terminal
8.3 Solenoid wiring connections on Lucas
M79 starter motor- CVH engine
Page 22 of 24
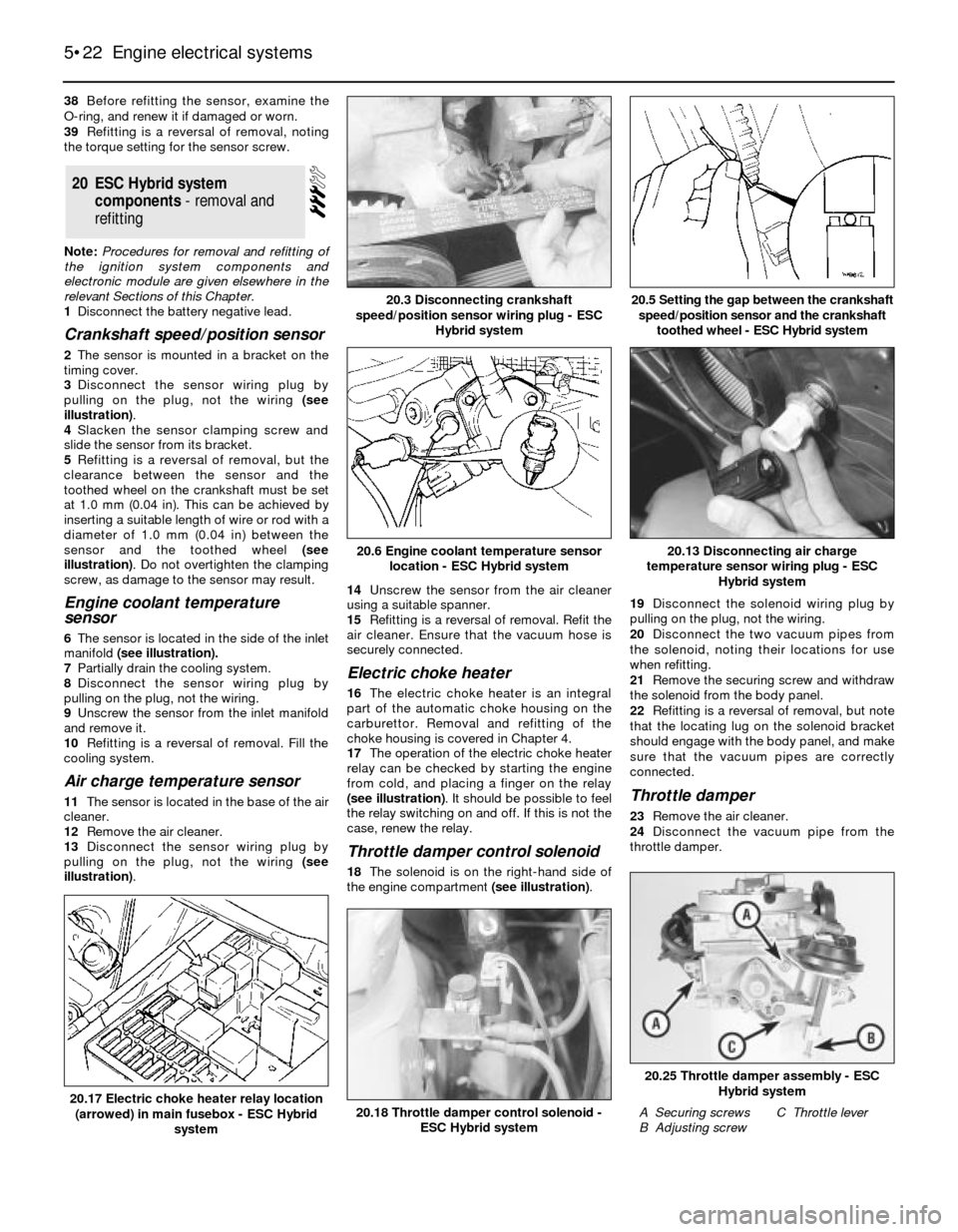
38Before refitting the sensor, examine the
O-ring, and renew it if damaged or worn.
39Refitting is a reversal of removal, noting
the torque setting for the sensor screw.
Note: Procedures for removal and refitting of
the ignition system components and
electronic module are given elsewhere in the
relevant Sections of this Chapter.
1Disconnect the battery negative lead.
Crankshaft speed/position sensor
2The sensor is mounted in a bracket on the
timing cover.
3Disconnect the sensor wiring plug by
pulling on the plug, not the wiring (see
illustration).
4Slacken the sensor clamping screw and
slide the sensor from its bracket.
5Refitting is a reversal of removal, but the
clearance between the sensor and the
toothed wheel on the crankshaft must be set
at 1.0 mm (0.04 in). This can be achieved by
inserting a suitable length of wire or rod with a
diameter of 1.0 mm (0.04 in) between the
sensor and the toothed wheel (see
illustration). Do not overtighten the clamping
screw, as damage to the sensor may result.
Engine coolant temperature
sensor
6The sensor is located in the side of the inlet
manifold(see illustration).
7Partially drain the cooling system.
8Disconnect the sensor wiring plug by
pulling on the plug, not the wiring.
9Unscrew the sensor from the inlet manifold
and remove it.
10Refitting is a reversal of removal. Fill the
cooling system.
Air charge temperature sensor
11The sensor is located in the base of the air
cleaner.
12Remove the air cleaner.
13Disconnect the sensor wiring plug by
pulling on the plug, not the wiring (see
illustration).14Unscrew the sensor from the air cleaner
using a suitable spanner.
15Refitting is a reversal of removal. Refit the
air cleaner. Ensure that the vacuum hose is
securely connected.
Electric choke heater
16The electric choke heater is an integral
part of the automatic choke housing on the
carburettor. Removal and refitting of the
choke housing is covered in Chapter 4.
17The operation of the electric choke heater
relay can be checked by starting the engine
from cold, and placing a finger on the relay
(see illustration). It should be possible to feel
the relay switching on and off. If this is not the
case, renew the relay.
Throttle damper control solenoid
18The solenoid is on the right-hand side of
the engine compartment (see illustration). 19Disconnect the solenoid wiring plug by
pulling on the plug, not the wiring.
20Disconnect the two vacuum pipes from
the solenoid, noting their locations for use
when refitting.
21Remove the securing screw and withdraw
the solenoid from the body panel.
22Refitting is a reversal of removal, but note
that the locating lug on the solenoid bracket
should engage with the body panel, and make
sure that the vacuum pipes are correctly
connected.
Throttle damper
23Remove the air cleaner.
24Disconnect the vacuum pipe from the
throttle damper.
20ESC Hybrid system
components - removal and
refitting
5•22Engine electrical systems
20.3 Disconnecting crankshaft
speed/position sensor wiring plug - ESC
Hybrid system
20.6 Engine coolant temperature sensor
location - ESC Hybrid system
20.25 Throttle damper assembly - ESC
Hybrid system
A Securing screws
B Adjusting screwC Throttle lever20.18 Throttle damper control solenoid -
ESC Hybrid system20.17 Electric choke heater relay location
(arrowed) in main fusebox - ESC Hybrid
system
20.13 Disconnecting air charge
temperature sensor wiring plug - ESC
Hybrid system
20.5 Setting the gap between the crankshaft
speed/position sensor and the crankshaft
toothed wheel - ESC Hybrid system