check engine light FORD SIERRA 1992 2.G Body Electrical System Workshop Manual
[x] Cancel search | Manufacturer: FORD, Model Year: 1992, Model line: SIERRA, Model: FORD SIERRA 1992 2.GPages: 25, PDF Size: 1.7 MB
Page 2 of 25
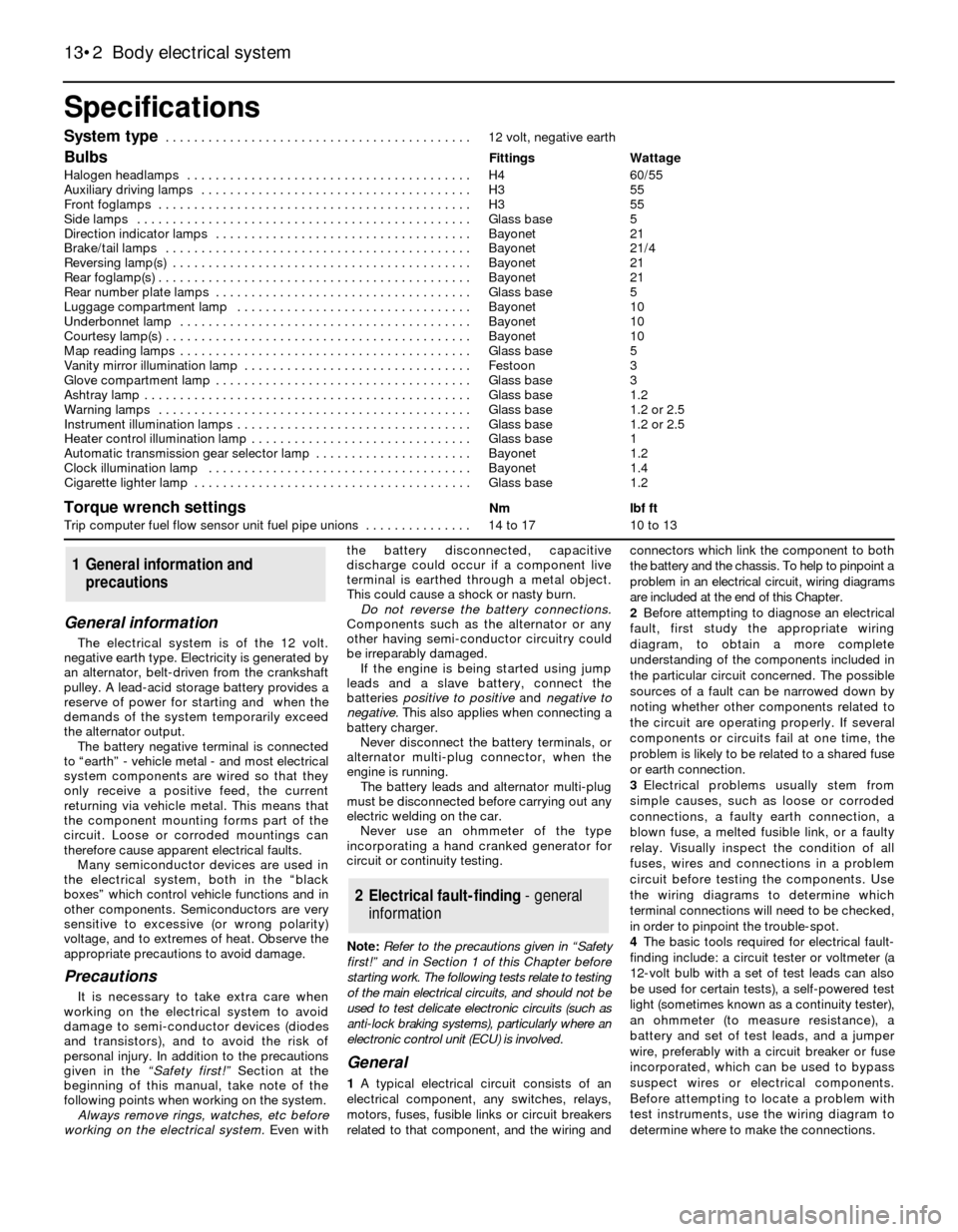
System type . . . . . . . . . . . . . . . . . . . . . . . . . . . . . . . . . . . . . . . . . . .12 volt, negative earth
BulbsFittingsWattage
Halogen headlamps . . . . . . . . . . . . . . . . . . . . . . . . . . . . . . . . . . . . . . . .H460/55
Auxiliary driving lamps . . . . . . . . . . . . . . . . . . . . . . . . . . . . . . . . . . . . . .H355
Front foglamps . . . . . . . . . . . . . . . . . . . . . . . . . . . . . . . . . . . . . . . . . . . .H355
Side lamps . . . . . . . . . . . . . . . . . . . . . . . . . . . . . . . . . . . . . . . . . . . . . . .Glass base5
Direction indicator lamps . . . . . . . . . . . . . . . . . . . . . . . . . . . . . . . . . . . .Bayonet21
Brake/tail lamps . . . . . . . . . . . . . . . . . . . . . . . . . . . . . . . . . . . . . . . . . . .Bayonet21/4
Reversing lamp(s) . . . . . . . . . . . . . . . . . . . . . . . . . . . . . . . . . . . . . . . . . .Bayonet21
Rear foglamp(s) . . . . . . . . . . . . . . . . . . . . . . . . . . . . . . . . . . . . . . . . . . . .Bayonet21
Rear number plate lamps . . . . . . . . . . . . . . . . . . . . . . . . . . . . . . . . . . . .Glass base5
Luggage compartment lamp . . . . . . . . . . . . . . . . . . . . . . . . . . . . . . . . .Bayonet10
Underbonnet lamp . . . . . . . . . . . . . . . . . . . . . . . . . . . . . . . . . . . . . . . . .Bayonet10
Courtesy lamp(s) . . . . . . . . . . . . . . . . . . . . . . . . . . . . . . . . . . . . . . . . . . .Bayonet10
Map reading lamps . . . . . . . . . . . . . . . . . . . . . . . . . . . . . . . . . . . . . . . . .Glass base5
Vanity mirror illumination lamp . . . . . . . . . . . . . . . . . . . . . . . . . . . . . . . .Festoon3
Glove compartment lamp . . . . . . . . . . . . . . . . . . . . . . . . . . . . . . . . . . . .Glass base3
Ashtray lamp . . . . . . . . . . . . . . . . . . . . . . . . . . . . . . . . . . . . . . . . . . . . . .Glass base1.2
Warning lamps . . . . . . . . . . . . . . . . . . . . . . . . . . . . . . . . . . . . . . . . . . . .Glass base1.2 or 2.5
Instrument illumination lamps . . . . . . . . . . . . . . . . . . . . . . . . . . . . . . . . .Glass base1.2 or 2.5
Heater control illumination lamp . . . . . . . . . . . . . . . . . . . . . . . . . . . . . . .Glass base1
Automatic transmission gear selector lamp . . . . . . . . . . . . . . . . . . . . . .Bayonet1.2
Clock illumination lamp . . . . . . . . . . . . . . . . . . . . . . . . . . . . . . . . . . . . .Bayonet1.4
Cigarette lighter lamp . . . . . . . . . . . . . . . . . . . . . . . . . . . . . . . . . . . . . . .Glass base1.2
Torque wrench settingsNmlbf ft
Trip computer fuel flow sensor unit fuel pipe unions . . . . . . . . . . . . . . .14 to 1710 to 13
General information
The electrical system is of the 12 volt.
negative earth type. Electricity is generated by
an alternator, belt-driven from the crankshaft
pulley. A lead-acid storage battery provides a
reserve of power for starting and when the
demands of the system temporarily exceed
the alternator output.
The battery negative terminal is connected
to “earth” - vehicle metal - and most electrical
system components are wired so that they
only receive a positive feed, the current
returning via vehicle metal. This means that
the component mounting forms part of the
circuit. Loose or corroded mountings can
therefore cause apparent electrical faults.
Many semiconductor devices are used in
the electrical system, both in the “black
boxes” which control vehicle functions and in
other components. Semiconductors are very
sensitive to excessive (or wrong polarity)
voltage, and to extremes of heat. Observe the
appropriate precautions to avoid damage.
Precautions
It is necessary to take extra care when
working on the electrical system to avoid
damage to semi-conductor devices (diodes
and transistors), and to avoid the risk of
personal injury. In addition to the precautions
given in the
“Safety first!” Section at the
beginning of this manual, take note of the
following points when working on the system.
Always remove rings, watches, etc before
working on the electrical system. Even withthe battery disconnected, capacitive
discharge could occur if a component live
terminal is earthed through a metal object.
This could cause a shock or nasty burn.
Do not reverse the battery connections.
Components such as the alternator or any
other having semi-conductor circuitry could
be irreparably damaged.
If the engine is being started using jump
leads and a slave battery, connect the
batteries positive to positive and negative to
negative. This also applies when connecting a
battery charger.
Never disconnect the battery terminals, or
alternator multi-plug connector, when the
engine is running.
The battery leads and alternator multi-plug
must be disconnected before carrying out any
electric welding on the car.
Never use an ohmmeter of the type
incorporating a hand cranked generator for
circuit or continuity testing.
Note:Refer to the precautions given in “Safety
first!” and in Section 1 of this Chapter before
starting work. The following tests relate to testing
of the main electrical circuits, and should not be
used to test delicate electronic circuits (such as
anti-lock braking systems), particularly where an
electronic control unit (ECU) is involved.General
1A typical electrical circuit consists of an
electrical component, any switches, relays,
motors, fuses, fusible links or circuit breakers
related to that component, and the wiring andconnectors which link the component to both
the battery and the chassis. To help to pinpoint a
problem in an electrical circuit, wiring diagrams
are included at the end of this Chapter.
2Before attempting to diagnose an electrical
fault, first study the appropriate wiring
diagram, to obtain a more complete
understanding of the components included in
the particular circuit concerned. The possible
sources of a fault can be narrowed down by
noting whether other components related to
the circuit are operating properly. If several
components or circuits fail at one time, the
problem is likely to be related to a shared fuse
or earth connection.
3Electrical problems usually stem from
simple causes, such as loose or corroded
connections, a faulty earth connection, a
blown fuse, a melted fusible link, or a faulty
relay. Visually inspect the condition of all
fuses, wires and connections in a problem
circuit before testing the components. Use
the wiring diagrams to determine which
terminal connections will need to be checked,
in order to pinpoint the trouble-spot.
4The basic tools required for electrical fault-
finding include: a circuit tester or voltmeter (a
12-volt bulb with a set of test leads can also
be used for certain tests), a self-powered test
light (sometimes known as a continuity tester),
an ohmmeter (to measure resistance), a
battery and set of test leads, and a jumper
wire, preferably with a circuit breaker or fuse
incorporated, which can be used to bypass
suspect wires or electrical components.
Before attempting to locate a problem with
test instruments, use the wiring diagram to
determine where to make the connections.
2Electrical fault-finding - general
information
1General information and
precautions
13•2Body electrical system
Specifications
Page 3 of 25
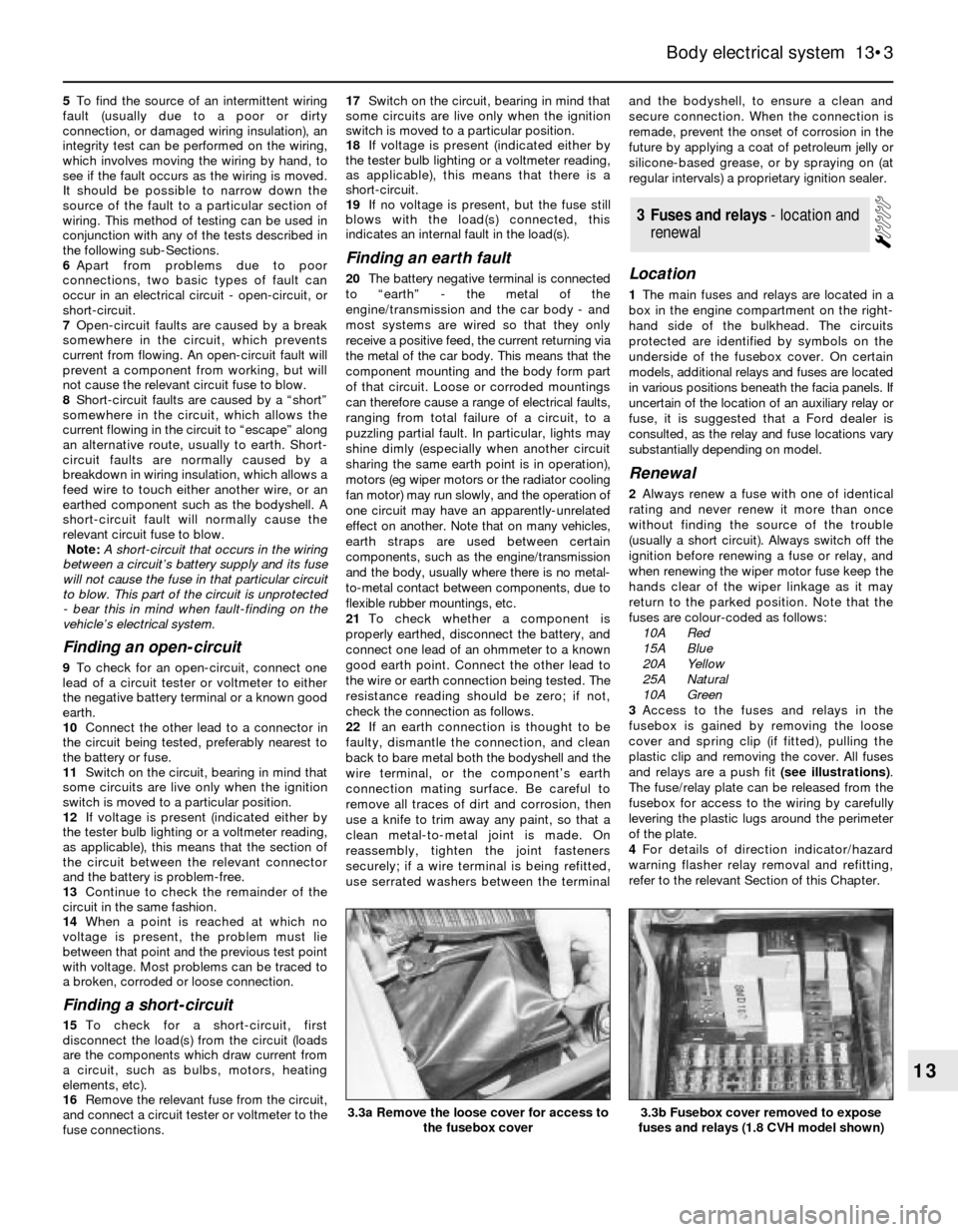
5To find the source of an intermittent wiring
fault (usually due to a poor or dirty
connection, or damaged wiring insulation), an
integrity test can be performed on the wiring,
which involves moving the wiring by hand, to
see if the fault occurs as the wiring is moved.
It should be possible to narrow down the
source of the fault to a particular section of
wiring. This method of testing can be used in
conjunction with any of the tests described in
the following sub-Sections.
6Apart from problems due to poor
connections, two basic types of fault can
occur in an electrical circuit - open-circuit, or
short-circuit.
7Open-circuit faults are caused by a break
somewhere in the circuit, which prevents
current from flowing. An open-circuit fault will
prevent a component from working, but will
not cause the relevant circuit fuse to blow.
8Short-circuit faults are caused by a “short”
somewhere in the circuit, which allows the
current flowing in the circuit to “escape” along
an alternative route, usually to earth. Short-
circuit faults are normally caused by a
breakdown in wiring insulation, which allows a
feed wire to touch either another wire, or an
earthed component such as the bodyshell. A
short-circuit fault will normally cause the
relevant circuit fuse to blow.
Note: A short-circuit that occurs in the wiring
between a circuit’s battery supply and its fuse
will not cause the fuse in that particular circuit
to blow. This part of the circuit is unprotected
- bear this in mind when fault-finding on the
vehicle’s electrical system.
Finding an open-circuit
9To check for an open-circuit, connect one
lead of a circuit tester or voltmeter to either
the negative battery terminal or a known good
earth.
10Connect the other lead to a connector in
the circuit being tested, preferably nearest to
the battery or fuse.
11Switch on the circuit, bearing in mind that
some circuits are live only when the ignition
switch is moved to a particular position.
12If voltage is present (indicated either by
the tester bulb lighting or a voltmeter reading,
as applicable), this means that the section of
the circuit between the relevant connector
and the battery is problem-free.
13Continue to check the remainder of the
circuit in the same fashion.
14When a point is reached at which no
voltage is present, the problem must lie
between that point and the previous test point
with voltage. Most problems can be traced to
a broken, corroded or loose connection.
Finding a short-circuit
15To check for a short-circuit, first
disconnect the load(s) from the circuit (loads
are the components which draw current from
a circuit, such as bulbs, motors, heating
elements, etc).
16Remove the relevant fuse from the circuit,
and connect a circuit tester or voltmeter to the
fuse connections.17Switch on the circuit, bearing in mind that
some circuits are live only when the ignition
switch is moved to a particular position.
18If voltage is present (indicated either by
the tester bulb lighting or a voltmeter reading,
as applicable), this means that there is a
short-circuit.
19If no voltage is present, but the fuse still
blows with the load(s) connected, this
indicates an internal fault in the load(s).
Finding an earth fault
20The battery negative terminal is connected
to “earth” - the metal of the
engine/transmission and the car body - and
most systems are wired so that they only
receive a positive feed, the current returning via
the metal of the car body. This means that the
component mounting and the body form part
of that circuit. Loose or corroded mountings
can therefore cause a range of electrical faults,
ranging from total failure of a circuit, to a
puzzling partial fault. In particular, lights may
shine dimly (especially when another circuit
sharing the same earth point is in operation),
motors (eg wiper motors or the radiator cooling
fan motor) may run slowly, and the operation of
one circuit may have an apparently-unrelated
effect on another. Note that on many vehicles,
earth straps are used between certain
components, such as the engine/transmission
and the body, usually where there is no metal-
to-metal contact between components, due to
flexible rubber mountings, etc.
21To check whether a component is
properly earthed, disconnect the battery, and
connect one lead of an ohmmeter to a known
good earth point. Connect the other lead to
the wire or earth connection being tested. The
resistance reading should be zero; if not,
check the connection as follows.
22If an earth connection is thought to be
faulty, dismantle the connection, and clean
back to bare metal both the bodyshell and the
wire terminal, or the component’s earth
connection mating surface. Be careful to
remove all traces of dirt and corrosion, then
use a knife to trim away any paint, so that a
clean metal-to-metal joint is made. On
reassembly, tighten the joint fasteners
securely; if a wire terminal is being refitted,
use serrated washers between the terminaland the bodyshell, to ensure a clean and
secure connection. When the connection is
remade, prevent the onset of corrosion in the
future by applying a coat of petroleum jelly or
silicone-based grease, or by spraying on (at
regular intervals) a proprietary ignition sealer.Location
1The main fuses and relays are located in a
box in the engine compartment on the right-
hand side of the bulkhead. The circuits
protected are identified by symbols on the
underside of the fusebox cover. On certain
models, additional relays and fuses are located
in various positions beneath the facia panels. If
uncertain of the location of an auxiliary relay or
fuse, it is suggested that a Ford dealer is
consulted, as the relay and fuse locations vary
substantially depending on model.
Renewal
2Always renew a fuse with one of identical
rating and never renew it more than once
without finding the source of the trouble
(usually a short circuit). Always switch off the
ignition before renewing a fuse or relay, and
when renewing the wiper motor fuse keep the
hands clear of the wiper linkage as it may
return to the parked position. Note that the
fuses are colour-coded as follows:
10ARed
15ABlue
20AYellow
25ANatural
10AGreen
3Access to the fuses and relays in the
fusebox is gained by removing the loose
cover and spring clip (if fitted), pulling the
plastic clip and removing the cover. All fuses
and relays are a push fit (see illustrations).
The fuse/relay plate can be released from the
fusebox for access to the wiring by carefully
levering the plastic lugs around the perimeter
of the plate.
4For details of direction indicator/hazard
warning flasher relay removal and refitting,
refer to the relevant Section of this Chapter.
3Fuses and relays - location and
renewal
Body electrical system 13•3
13
3.3b Fusebox cover removed to expose
fuses and relays (1.8 CVH model shown)3.3a Remove the loose cover for access to
the fusebox cover
Page 6 of 25
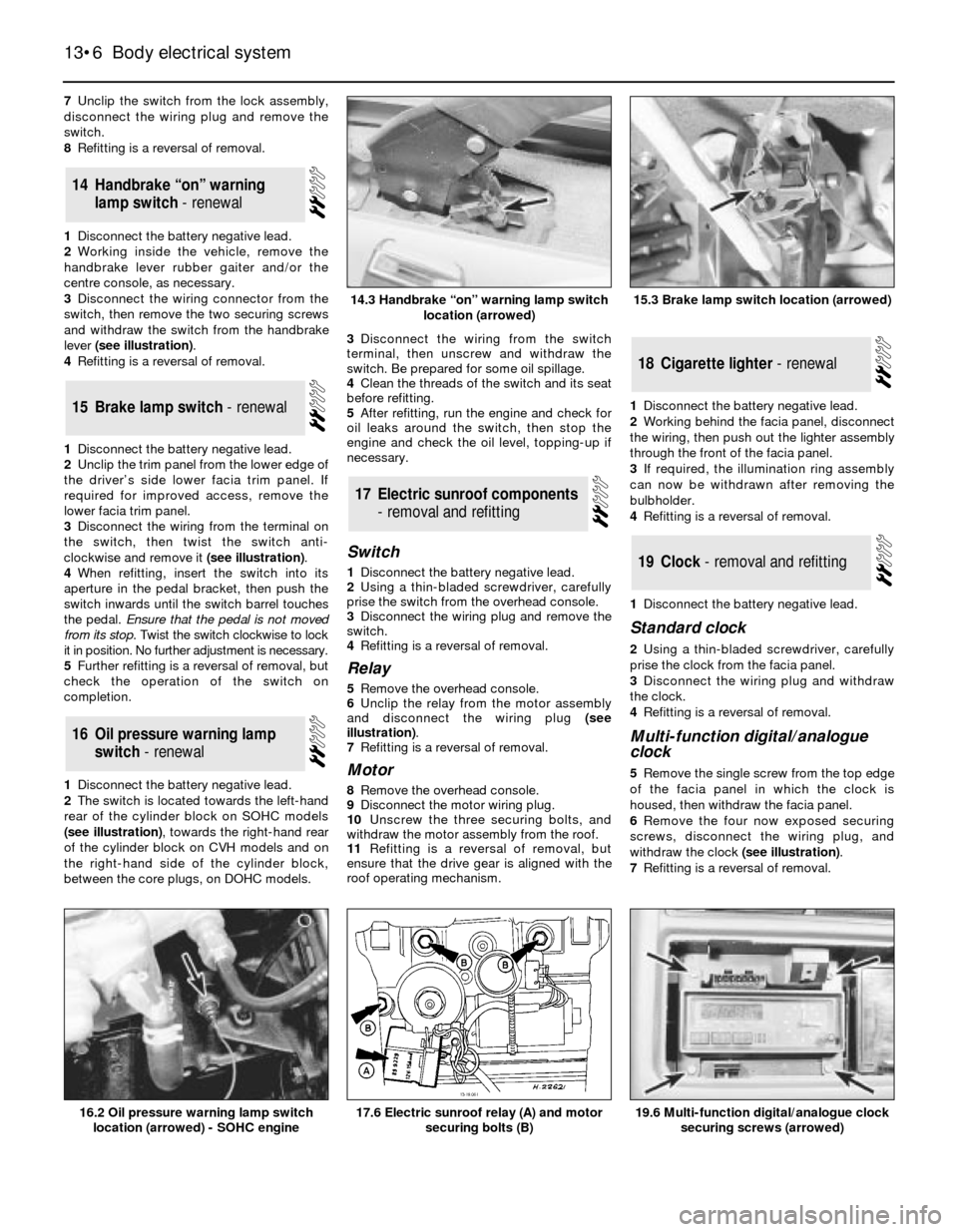
7Unclip the switch from the lock assembly,
disconnect the wiring plug and remove the
switch.
8Refitting is a reversal of removal.
1Disconnect the battery negative lead.
2Working inside the vehicle, remove the
handbrake lever rubber gaiter and/or the
centre console, as necessary.
3Disconnect the wiring connector from the
switch, then remove the two securing screws
and withdraw the switch from the handbrake
lever (see illustration).
4Refitting is a reversal of removal.
1Disconnect the battery negative lead.
2Unclip the trim panel from the lower edge of
the driver’s side lower facia trim panel. If
required for improved access, remove the
lower facia trim panel.
3Disconnect the wiring from the terminal on
the switch, then twist the switch anti-
clockwise and remove it (see illustration).
4When refitting, insert the switch into its
aperture in the pedal bracket, then push the
switch inwards until the switch barrel touches
the pedal. Ensure that the pedal is not moved
from its stop. Twist the switch clockwise to lock
it in position. No further adjustment is necessary.
5Further refitting is a reversal of removal, but
check the operation of the switch on
completion.
1Disconnect the battery negative lead.
2The switch is located towards the left-hand
rear of the cylinder block on SOHC models
(see illustration), towards the right-hand rear
of the cylinder block on CVH models and on
the right-hand side of the cylinder block,
between the core plugs, on DOHC models.3Disconnect the wiring from the switch
terminal, then unscrew and withdraw the
switch. Be prepared for some oil spillage.
4Clean the threads of the switch and its seat
before refitting.
5After refitting, run the engine and check for
oil leaks around the switch, then stop the
engine and check the oil level, topping-up if
necessary.
Switch
1Disconnect the battery negative lead.
2Using a thin-bladed screwdriver, carefully
prise the switch from the overhead console.
3Disconnect the wiring plug and remove the
switch.
4Refitting is a reversal of removal.
Relay
5Remove the overhead console.
6Unclip the relay from the motor assembly
and disconnect the wiring plug (see
illustration).
7Refitting is a reversal of removal.
Motor
8Remove the overhead console.
9Disconnect the motor wiring plug.
10Unscrew the three securing bolts, and
withdraw the motor assembly from the roof.
11Refitting is a reversal of removal, but
ensure that the drive gear is aligned with the
roof operating mechanism.1Disconnect the battery negative lead.
2Working behind the facia panel, disconnect
the wiring, then push out the lighter assembly
through the front of the facia panel.
3If required, the illumination ring assembly
can now be withdrawn after removing the
bulbholder.
4Refitting is a reversal of removal.
1Disconnect the battery negative lead.
Standard clock
2Using a thin-bladed screwdriver, carefully
prise the clock from the facia panel.
3Disconnect the wiring plug and withdraw
the clock.
4Refitting is a reversal of removal.
Multi-function digital/analogue
clock
5Remove the single screw from the top edge
of the facia panel in which the clock is
housed, then withdraw the facia panel.
6Remove the four now exposed securing
screws, disconnect the wiring plug, and
withdraw the clock (see illustration).
7Refitting is a reversal of removal.
19Clock - removal and refitting
18Cigarette lighter - renewal
17Electric sunroof components
- removal and refitting
16Oil pressure warning lamp
switch - renewal
15Brake lamp switch - renewal
14Handbrake “on” warning
lamp switch - renewal
13•6Body electrical system
14.3 Handbrake “on” warning lamp switch
location (arrowed)
16.2 Oil pressure warning lamp switch
location (arrowed) - SOHC engine19.6 Multi-function digital/analogue clock
securing screws (arrowed)17.6 Electric sunroof relay (A) and motor
securing bolts (B)
15.3 Brake lamp switch location (arrowed)
Page 12 of 25
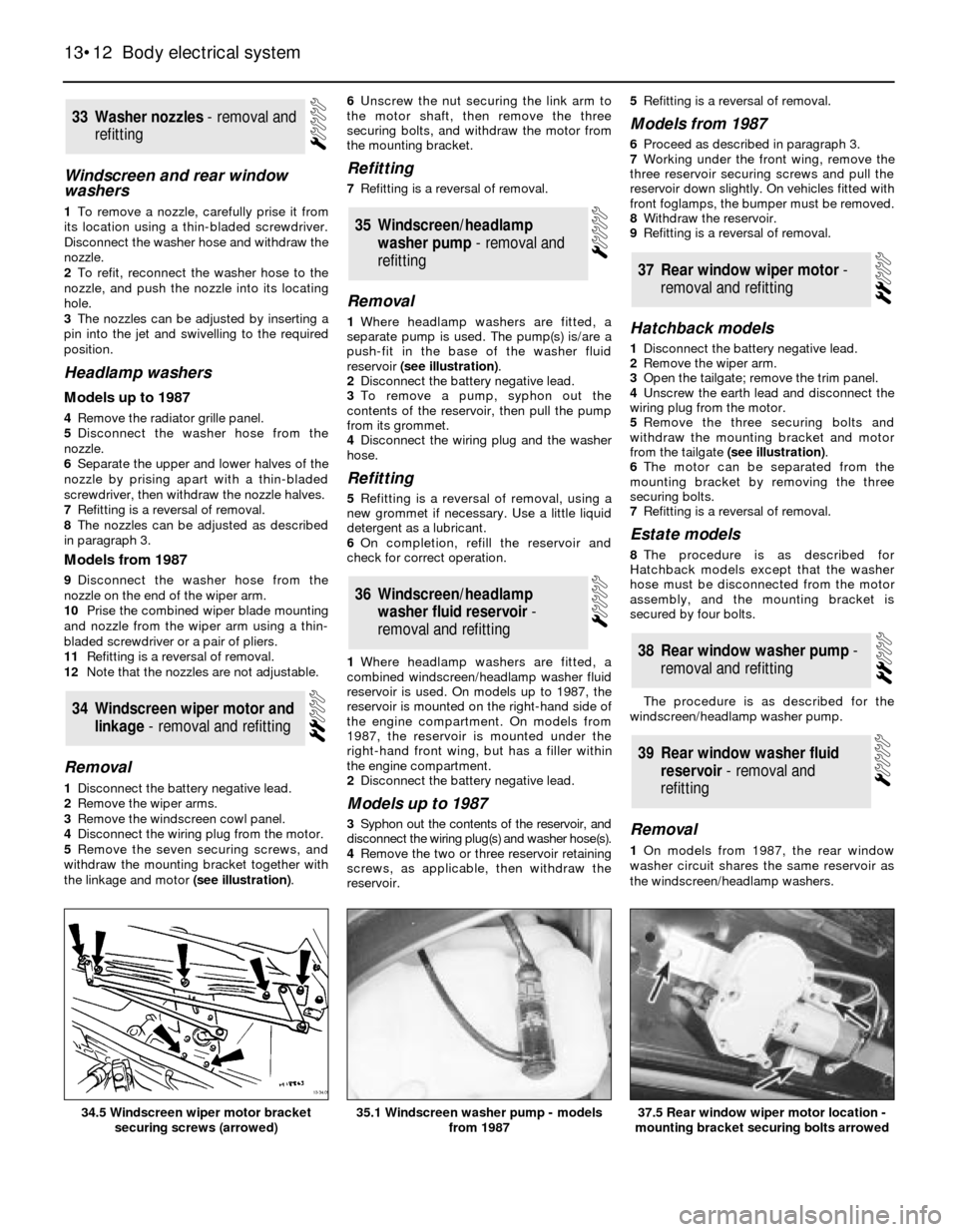
Windscreen and rear window
washers
1To remove a nozzle, carefully prise it from
its location using a thin-bladed screwdriver.
Disconnect the washer hose and withdraw the
nozzle.
2To refit, reconnect the washer hose to the
nozzle, and push the nozzle into its locating
hole.
3The nozzles can be adjusted by inserting a
pin into the jet and swivelling to the required
position.
Headlamp washers
Models up to 1987
4Remove the radiator grille panel.
5Disconnect the washer hose from the
nozzle.
6Separate the upper and lower halves of the
nozzle by prising apart with a thin-bladed
screwdriver, then withdraw the nozzle halves.
7Refitting is a reversal of removal.
8The nozzles can be adjusted as described
in paragraph 3.
Models from 1987
9Disconnect the washer hose from the
nozzle on the end of the wiper arm.
10Prise the combined wiper blade mounting
and nozzle from the wiper arm using a thin-
bladed screwdriver or a pair of pliers.
11Refitting is a reversal of removal.
12Note that the nozzles are not adjustable.
Removal
1Disconnect the battery negative lead.
2Remove the wiper arms.
3Remove the windscreen cowl panel.
4Disconnect the wiring plug from the motor.
5Remove the seven securing screws, and
withdraw the mounting bracket together with
the linkage and motor (see illustration). 6Unscrew the nut securing the link arm to
the motor shaft, then remove the three
securing bolts, and withdraw the motor from
the mounting bracket.
Refitting
7Refitting is a reversal of removal.
Removal
1Where headlamp washers are fitted, a
separate pump is used. The pump(s) is/are a
push-fit in the base of the washer fluid
reservoir (see illustration).
2Disconnect the battery negative lead.
3To remove a pump, syphon out the
contents of the reservoir, then pull the pump
from its grommet.
4Disconnect the wiring plug and the washer
hose.
Refitting
5Refitting is a reversal of removal, using a
new grommet if necessary. Use a little liquid
detergent as a lubricant.
6On completion, refill the reservoir and
check for correct operation.
1Where headlamp washers are fitted, a
combined windscreen/headlamp washer fluid
reservoir is used. On models up to 1987, the
reservoir is mounted on the right-hand side of
the engine compartment. On models from
1987, the reservoir is mounted under the
right-hand front wing, but has a filler within
the engine compartment.
2Disconnect the battery negative lead.
Models up to 1987
3Syphon out the contents of the reservoir, and
disconnect the wiring plug(s) and washer hose(s).
4Remove the two or three reservoir retaining
screws, as applicable, then withdraw the
reservoir.5Refitting is a reversal of removal.
Models from 1987
6Proceed as described in paragraph 3.
7Working under the front wing, remove the
three reservoir securing screws and pull the
reservoir down slightly. On vehicles fitted with
front foglamps, the bumper must be removed.
8Withdraw the reservoir.
9Refitting is a reversal of removal.
Hatchback models
1Disconnect the battery negative lead.
2Remove the wiper arm.
3Open the tailgate; remove the trim panel.
4Unscrew the earth lead and disconnect the
wiring plug from the motor.
5Remove the three securing bolts and
withdraw the mounting bracket and motor
from the tailgate (see illustration).
6The motor can be separated from the
mounting bracket by removing the three
securing bolts.
7Refitting is a reversal of removal.
Estate models
8The procedure is as described for
Hatchback models except that the washer
hose must be disconnected from the motor
assembly, and the mounting bracket is
secured by four bolts.
The procedure is as described for the
windscreen/headlamp washer pump.
Removal
1On models from 1987, the rear window
washer circuit shares the same reservoir as
the windscreen/headlamp washers.
39Rear window washer fluid
reservoir - removal and
refitting
38Rear window washer pump -
removal and refitting
37Rear window wiper motor -
removal and refitting
36Windscreen/headlamp
washer fluid reservoir -
removal and refitting
35Windscreen/headlamp
washer pump - removal and
refitting
34Windscreen wiper motor and
linkage - removal and refitting
33Washer nozzles - removal and
refitting
13•12Body electrical system
35.1 Windscreen washer pump - models
from 198737.5 Rear window wiper motor location -
mounting bracket securing bolts arrowed34.5 Windscreen wiper motor bracket
securing screws (arrowed)