ECO mode FORD SIERRA 1992 2.G Cooling And Air Conditioning Systems Workshop Manual
[x] Cancel search | Manufacturer: FORD, Model Year: 1992, Model line: SIERRA, Model: FORD SIERRA 1992 2.GPages: 12, PDF Size: 0.62 MB
Page 2 of 12
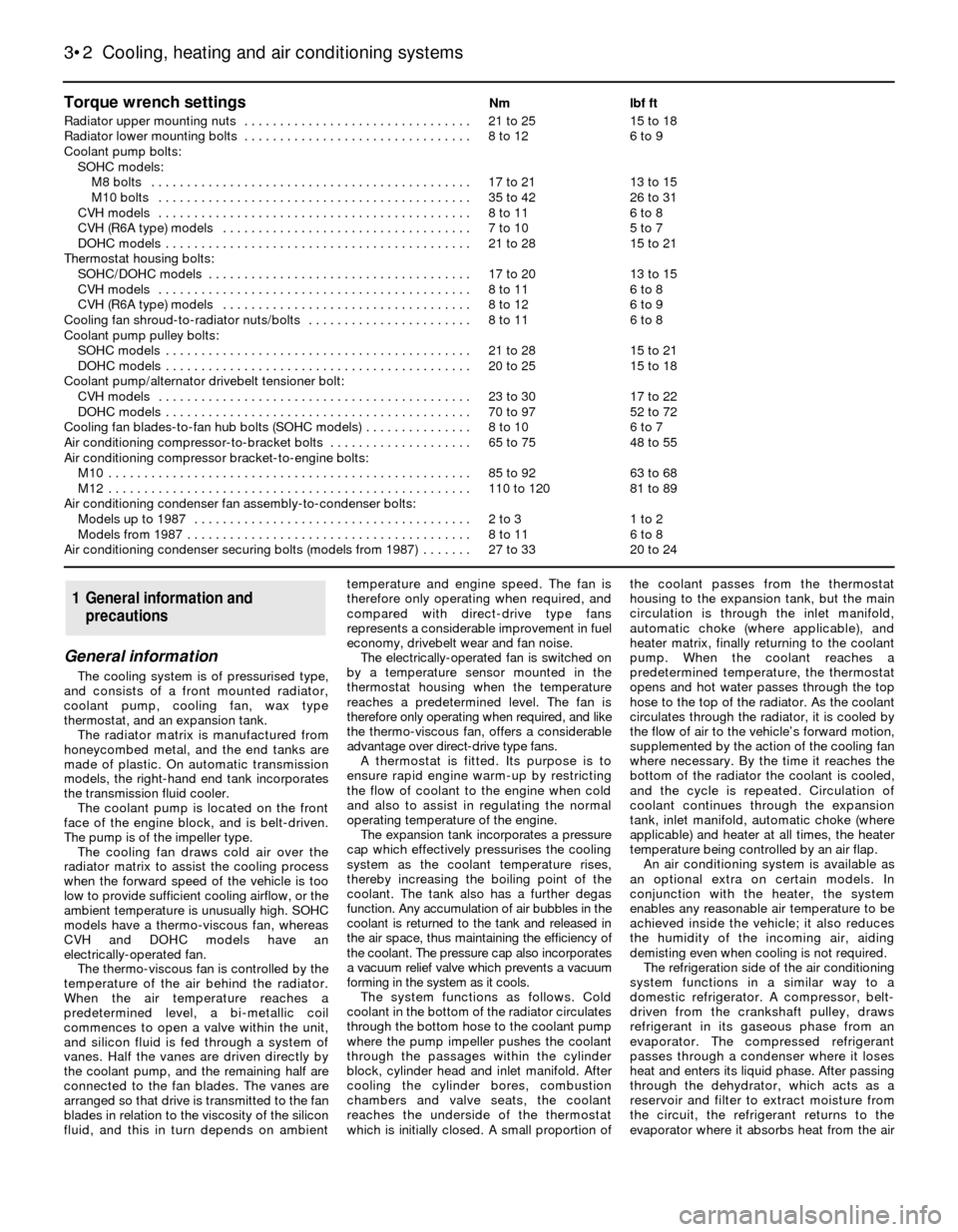
Torque wrench settingsNmlbf ft
Radiator upper mounting nuts . . . . . . . . . . . . . . . . . . . . . . . . . . . . . . . .21 to 2515 to 18
Radiator lower mounting bolts . . . . . . . . . . . . . . . . . . . . . . . . . . . . . . . .8 to 126 to 9
Coolant pump bolts:
SOHC models:
M8 bolts . . . . . . . . . . . . . . . . . . . . . . . . . . . . . . . . . . . . . . . . . . . . .17 to 2113 to 15
M10 bolts . . . . . . . . . . . . . . . . . . . . . . . . . . . . . . . . . . . . . . . . . . . .35 to 4226 to 31
CVH models . . . . . . . . . . . . . . . . . . . . . . . . . . . . . . . . . . . . . . . . . . . .8 to 116 to 8
CVH (R6A type) models . . . . . . . . . . . . . . . . . . . . . . . . . . . . . . . . . . .7 to 105 to 7
DOHC models . . . . . . . . . . . . . . . . . . . . . . . . . . . . . . . . . . . . . . . . . . .21 to 2815 to 21
Thermostat housing bolts:
SOHC/DOHC models . . . . . . . . . . . . . . . . . . . . . . . . . . . . . . . . . . . . .17 to 2013 to 15
CVH models . . . . . . . . . . . . . . . . . . . . . . . . . . . . . . . . . . . . . . . . . . . .8 to 116 to 8
CVH (R6A type) models . . . . . . . . . . . . . . . . . . . . . . . . . . . . . . . . . . .8 to 126 to 9
Cooling fan shroud-to-radiator nuts/bolts . . . . . . . . . . . . . . . . . . . . . . .8 to 116 to 8
Coolant pump pulley bolts:
SOHC models . . . . . . . . . . . . . . . . . . . . . . . . . . . . . . . . . . . . . . . . . . .21 to 2815 to 21
DOHC models . . . . . . . . . . . . . . . . . . . . . . . . . . . . . . . . . . . . . . . . . . .20 to 2515 to 18
Coolant pump/alternator drivebelt tensioner bolt:
CVH models . . . . . . . . . . . . . . . . . . . . . . . . . . . . . . . . . . . . . . . . . . . .23 to 3017 to 22
DOHC models . . . . . . . . . . . . . . . . . . . . . . . . . . . . . . . . . . . . . . . . . . .70 to 9752 to 72
Cooling fan blades-to-fan hub bolts (SOHC models) . . . . . . . . . . . . . . .8 to 106 to 7
Air conditioning compressor-to-bracket bolts . . . . . . . . . . . . . . . . . . . .65 to 7548 to 55
Air conditioning compressor bracket-to-engine bolts:
M10 . . . . . . . . . . . . . . . . . . . . . . . . . . . . . . . . . . . . . . . . . . . . . . . . . . .85 to 9263 to 68
M12 . . . . . . . . . . . . . . . . . . . . . . . . . . . . . . . . . . . . . . . . . . . . . . . . . . .110 to 12081 to 89
Air conditioning condenser fan assembly-to-condenser bolts:
Models up to 1987 . . . . . . . . . . . . . . . . . . . . . . . . . . . . . . . . . . . . . . .2 to 31 to 2
Models from 1987 . . . . . . . . . . . . . . . . . . . . . . . . . . . . . . . . . . . . . . . .8 to 116 to 8
Air conditioning condenser securing bolts (models from 1987) . . . . . . .27 to 3320 to 24
General information
The cooling system is of pressurised type,
and consists of a front mounted radiator,
coolant pump, cooling fan, wax type
thermostat, and an expansion tank.
The radiator matrix is manufactured from
honeycombed metal, and the end tanks are
made of plastic. On automatic transmission
models, the right-hand end tank incorporates
the transmission fluid cooler.
The coolant pump is located on the front
face of the engine block, and is belt-driven.
The pump is of the impeller type.
The cooling fan draws cold air over the
radiator matrix to assist the cooling process
when the forward speed of the vehicle is too
low to provide sufficient cooling airflow, or the
ambient temperature is unusually high. SOHC
models have a thermo-viscous fan, whereas
CVH and DOHC models have an
electrically-operated fan.
The thermo-viscous fan is controlled by the
temperature of the air behind the radiator.
When the air temperature reaches a
predetermined level, a bi-metallic coil
commences to open a valve within the unit,
and silicon fluid is fed through a system of
vanes. Half the vanes are driven directly by
the coolant pump, and the remaining half are
connected to the fan blades. The vanes are
arranged so that drive is transmitted to the fan
blades in relation to the viscosity of the silicon
fluid, and this in turn depends on ambienttemperature and engine speed. The fan is
therefore only operating when required, and
compared with direct-drive type fans
represents a considerable improvement in fuel
economy, drivebelt wear and fan noise.
The electrically-operated fan is switched on
by a temperature sensor mounted in the
thermostat housing when the temperature
reaches a predetermined level. The fan is
therefore only operating when required, and like
the thermo-viscous fan, offers a considerable
advantage over direct-drive type fans.
A thermostat is fitted. Its purpose is to
ensure rapid engine warm-up by restricting
the flow of coolant to the engine when cold
and also to assist in regulating the normal
operating temperature of the engine.
The expansion tank incorporates a pressure
cap which effectively pressurises the cooling
system as the coolant temperature rises,
thereby increasing the boiling point of the
coolant. The tank also has a further degas
function. Any accumulation of air bubbles in the
coolant is returned to the tank and released in
the air space, thus maintaining the efficiency of
the coolant. The pressure cap also incorporates
a vacuum relief valve which prevents a vacuum
forming in the system as it cools.
The system functions as follows. Cold
coolant in the bottom of the radiator circulates
through the bottom hose to the coolant pump
where the pump impeller pushes the coolant
through the passages within the cylinder
block, cylinder head and inlet manifold. After
cooling the cylinder bores, combustion
chambers and valve seats, the coolant
reaches the underside of the thermostat
which is initially closed. A small proportion ofthe coolant passes from the thermostat
housing to the expansion tank, but the main
circulation is through the inlet manifold,
automatic choke (where applicable), and
heater matrix, finally returning to the coolant
pump. When the coolant reaches a
predetermined temperature, the thermostat
opens and hot water passes through the top
hose to the top of the radiator. As the coolant
circulates through the radiator, it is cooled by
the flow of air to the vehicle’s forward motion,
supplemented by the action of the cooling fan
where necessary. By the time it reaches the
bottom of the radiator the coolant is cooled,
and the cycle is repeated. Circulation of
coolant continues through the expansion
tank, inlet manifold, automatic choke (where
applicable) and heater at all times, the heater
temperature being controlled by an air flap.
An air conditioning system is available as
an optional extra on certain models. In
conjunction with the heater, the system
enables any reasonable air temperature to be
achieved inside the vehicle; it also reduces
the humidity of the incoming air, aiding
demisting even when cooling is not required.
The refrigeration side of the air conditioning
system functions in a similar way to a
domestic refrigerator. A compressor, belt-
driven from the crankshaft pulley, draws
refrigerant in its gaseous phase from an
evaporator. The compressed refrigerant
passes through a condenser where it loses
heat and enters its liquid phase. After passing
through the dehydrator, which acts as a
reservoir and filter to extract moisture from
the circuit, the refrigerant returns to the
evaporator where it absorbs heat from the air
1General information and
precautions
3•2Cooling, heating and air conditioning systems
Page 3 of 12
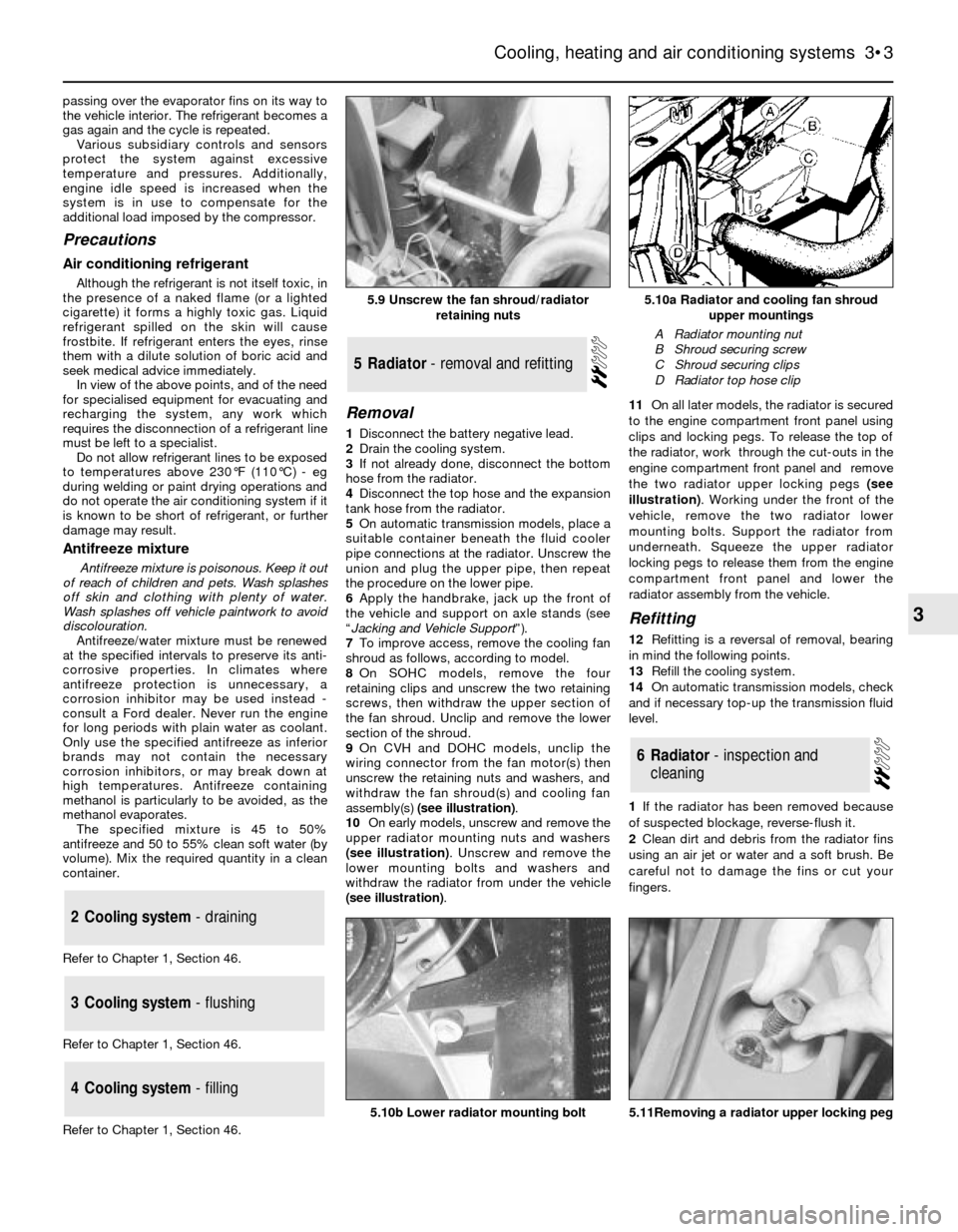
passing over the evaporator fins on its way to
the vehicle interior. The refrigerant becomes a
gas again and the cycle is repeated.
Various subsidiary controls and sensors
protect the system against excessive
temperature and pressures. Additionally,
engine idle speed is increased when the
system is in use to compensate for the
additional load imposed by the compressor.
Precautions
Air conditioning refrigerant
Although the refrigerant is not itself toxic, in
the presence of a naked flame (or a lighted
cigarette) it forms a highly toxic gas. Liquid
refrigerant spilled on the skin will cause
frostbite. If refrigerant enters the eyes, rinse
them with a dilute solution of boric acid and
seek medical advice immediately.
In view of the above points, and of the need
for specialised equipment for evacuating and
recharging the system, any work which
requires the disconnection of a refrigerant line
must be left to a specialist.
Do not allow refrigerant lines to be exposed
to temperatures above 230°F (110°C) - eg
during welding or paint drying operations and
do not operate the air conditioning system if it
is known to be short of refrigerant, or further
damage may result.
Antifreeze mixture
Antifreeze mixture is poisonous. Keep it out
of reach of children and pets. Wash splashes
off skin and clothing with plenty of water.
Wash splashes off vehicle paintwork to avoid
discolouration.
Antifreeze/water mixture must be renewed
at the specified intervals to preserve its anti-
corrosive properties. In climates where
antifreeze protection is unnecessary, a
corrosion inhibitor may be used instead -
consult a Ford dealer. Never run the engine
for long periods with plain water as coolant.
Only use the specified antifreeze as inferior
brands may not contain the necessary
corrosion inhibitors, or may break down at
high temperatures. Antifreeze containing
methanol is particularly to be avoided, as the
methanol evaporates.
The specified mixture is 45 to 50%
antifreeze and 50 to 55% clean soft water (by
volume). Mix the required quantity in a clean
container.
Refer to Chapter 1, Section 46.
Refer to Chapter 1, Section 46.
Refer to Chapter 1, Section 46.
Removal
1Disconnect the battery negative lead.
2Drain the cooling system.
3If not already done, disconnect the bottom
hose from the radiator.
4Disconnect the top hose and the expansion
tank hose from the radiator.
5On automatic transmission models, place a
suitable container beneath the fluid cooler
pipe connections at the radiator. Unscrew the
union and plug the upper pipe, then repeat
the procedure on the lower pipe.
6Apply the handbrake, jack up the front of
the vehicle and support on axle stands (see
“Jacking and Vehicle Support”).
7To improve access, remove the cooling fan
shroud as follows, according to model.
8On SOHC models, remove the four
retaining clips and unscrew the two retaining
screws, then withdraw the upper section of
the fan shroud. Unclip and remove the lower
section of the shroud.
9On CVH and DOHC models, unclip the
wiring connector from the fan motor(s) then
unscrew the retaining nuts and washers, and
withdraw the fan shroud(s) and cooling fan
assembly(s) (see illustration).
10On early models, unscrew and remove the
upper radiator mounting nuts and washers
(see illustration). Unscrew and remove the
lower mounting bolts and washers and
withdraw the radiator from under the vehicle
(see illustration).11On all later models, the radiator is secured
to the engine compartment front panel using
clips and locking pegs. To release the top of
the radiator, work through the cut-outs in the
engine compartment front panel and remove
the two radiator upper locking pegs (see
illustration). Working under the front of the
vehicle, remove the two radiator lower
mounting bolts. Support the radiator from
underneath. Squeeze the upper radiator
locking pegs to release them from the engine
compartment front panel and lower the
radiator assembly from the vehicle.
Refitting
12Refitting is a reversal of removal, bearing
in mind the following points.
13Refill the cooling system.
14On automatic transmission models, check
and if necessary top-up the transmission fluid
level.
1If the radiator has been removed because
of suspected blockage, reverse-flush it.
2Clean dirt and debris from the radiator fins
using an air jet or water and a soft brush. Be
careful not to damage the fins or cut your
fingers.
6Radiator -inspectionand
cleaning
5Radiator - removal and refitting
4Cooling system - filling
3Cooling system - flushing
2Cooling system - draining
Cooling, heating and air conditioning systems 3•3
3
5.10a Radiator and cooling fan shroud
upper mountings
A Radiator mounting nut
B Shroud securing screw
C Shroud securing clips
D Radiator top hose clip
5.11Removing a radiator upper locking peg5.10b Lower radiator mounting bolt
5.9 Unscrew the fan shroud/radiator
retaining nuts
Page 4 of 12
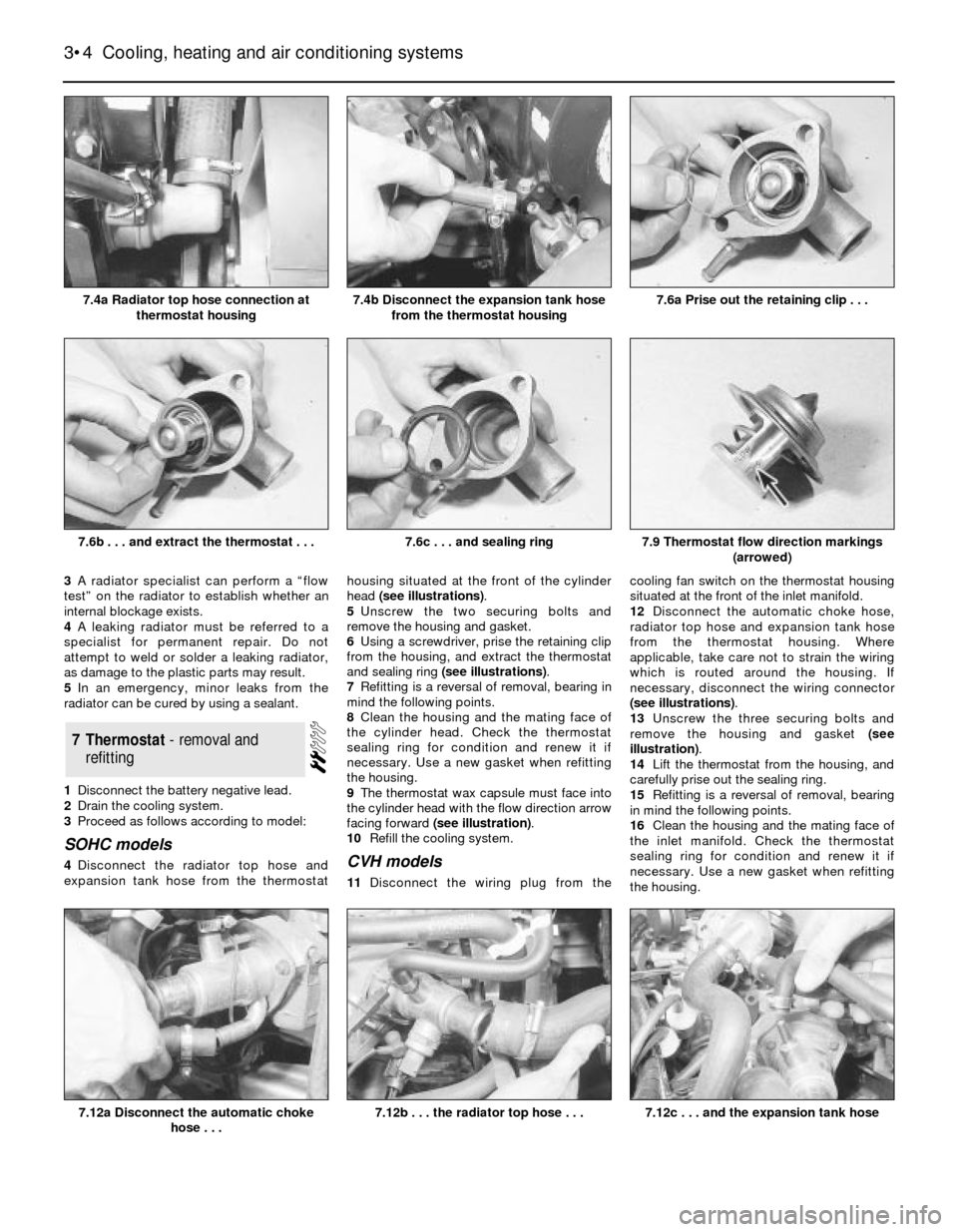
3A radiator specialist can perform a “flow
test” on the radiator to establish whether an
internal blockage exists.
4A leaking radiator must be referred to a
specialist for permanent repair. Do not
attempt to weld or solder a leaking radiator,
as damage to the plastic parts may result.
5In an emergency, minor leaks from the
radiator can be cured by using a sealant.
1Disconnect the battery negative lead.
2Drain the cooling system.
3Proceed as follows according to model:
SOHC models
4Disconnect the radiator top hose and
expansion tank hose from the thermostathousing situated at the front of the cylinder
head (see illustrations).
5Unscrew the two securing bolts and
remove the housing and gasket.
6Using a screwdriver, prise the retaining clip
from the housing, and extract the thermostat
and sealing ring (see illustrations).
7Refitting is a reversal of removal, bearing in
mind the following points.
8Clean the housing and the mating face of
the cylinder head. Check the thermostat
sealing ring for condition and renew it if
necessary. Use a new gasket when refitting
the housing.
9The thermostat wax capsule must face into
the cylinder head with the flow direction arrow
facing forward (see illustration).
10Refill the cooling system.CVH models
11Disconnect the wiring plug from thecooling fan switch on the thermostat housing
situated at the front of the inlet manifold.
12Disconnect the automatic choke hose,
radiator top hose and expansion tank hose
from the thermostat housing. Where
applicable, take care not to strain the wiring
which is routed around the housing. If
necessary, disconnect the wiring connector
(see illustrations).
13Unscrew the three securing bolts and
remove the housing and gasket (see
illustration).
14Lift the thermostat from the housing, and
carefully prise out the sealing ring.
15Refitting is a reversal of removal, bearing
in mind the following points.
16Clean the housing and the mating face of
the inlet manifold. Check the thermostat
sealing ring for condition and renew it if
necessary. Use a new gasket when refitting
the housing.
7Thermostat -removaland
refitting
3•4Cooling, heating and air conditioning systems
7.4a Radiator top hose connection at
thermostat housing7.6a Prise out the retaining clip . . .
7.12c . . . and the expansion tank hose7.12b . . . the radiator top hose . . .7.12a Disconnect the automatic choke
hose . . .
7.4b Disconnect the expansion tank hose
from the thermostat housing
7.6b . . . and extract the thermostat . . .7.9 Thermostat flow direction markings
(arrowed)7.6c . . . and sealing ring
Page 5 of 12
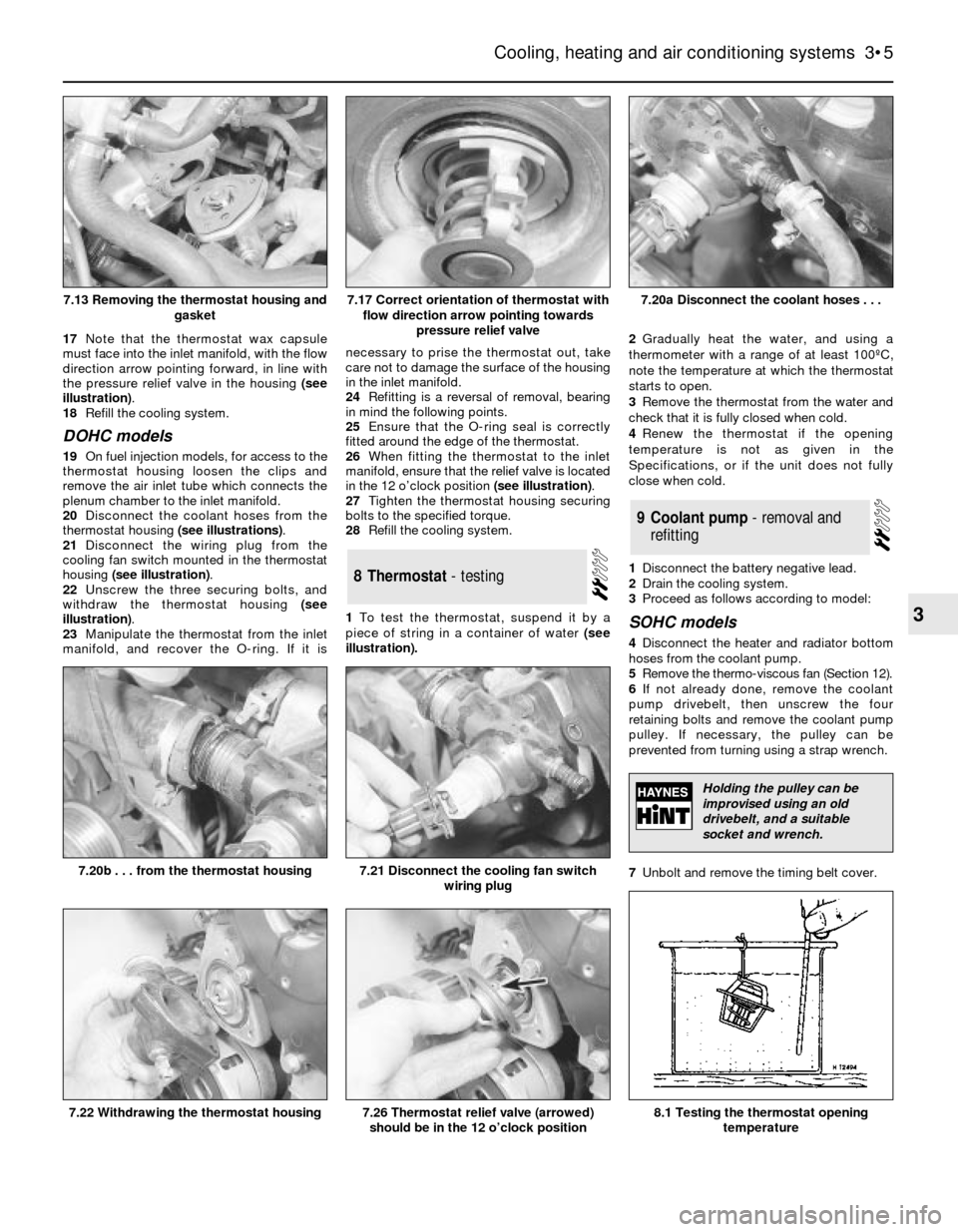
17Note that the thermostat wax capsule
must face into the inlet manifold, with the flow
direction arrow pointing forward, in line with
the pressure relief valve in the housing (see
illustration).
18Refill the cooling system.
DOHC models
19On fuel injection models, for access to the
thermostat housing loosen the clips and
remove the air inlet tube which connects the
plenum chamber to the inlet manifold.
20Disconnect the coolant hoses from the
thermostat housing (see illustrations).
21Disconnect the wiring plug from the
cooling fan switch mounted in the thermostat
housing (see illustration).
22Unscrew the three securing bolts, and
withdraw the thermostat housing (see
illustration).
23Manipulate the thermostat from the inlet
manifold, and recover the O-ring. If it isnecessary to prise the thermostat out, take
care not to damage the surface of the housing
in the inlet manifold.
24Refitting is a reversal of removal, bearing
in mind the following points.
25Ensure that the O-ring seal is correctly
fitted around the edge of the thermostat.
26When fitting the thermostat to the inlet
manifold, ensure that the relief valve is located
in the 12 o’clock position (see illustration).
27Tighten the thermostat housing securing
bolts to the specified torque.
28Refill the cooling system.
1To test the thermostat, suspend it by a
piece of string in a container of water (see
illustration).2Gradually heat the water, and using a
thermometer with a range of at least 100ºC,
note the temperature at which the thermostat
starts to open.
3Remove the thermostat from the water and
check that it is fully closed when cold.
4Renew the thermostat if the opening
temperature is not as given in the
Specifications, or if the unit does not fully
close when cold.
1Disconnect the battery negative lead.
2Drain the cooling system.
3Proceed as follows according to model:
SOHC models
4Disconnect the heater and radiator bottom
hoses from the coolant pump.
5Remove the thermo-viscous fan (Section 12).
6If not already done, remove the coolant
pump drivebelt, then unscrew the four
retaining bolts and remove the coolant pump
pulley. If necessary, the pulley can be
prevented from turning using a strap wrench.
7Unbolt and remove the timing belt cover.
9Coolant pump - removal and
refitting
8Thermostat - testing
Cooling, heating and air conditioning systems 3•5
3
7.20a Disconnect the coolant hoses . . .
8.1 Testing the thermostat opening
temperature7.26 Thermostat relief valve (arrowed)
should be in the 12 o’clock position7.22 Withdrawing the thermostat housing
7.21 Disconnect the cooling fan switch
wiring plug7.20b . . . from the thermostat housing
7.17 Correct orientation of thermostat with
flow direction arrow pointing towards
pressure relief valve7.13 Removing the thermostat housing and
gasket
Holding the pulley can be
improvised using an old
drivebelt, and a suitable
socket and wrench.
Page 6 of 12
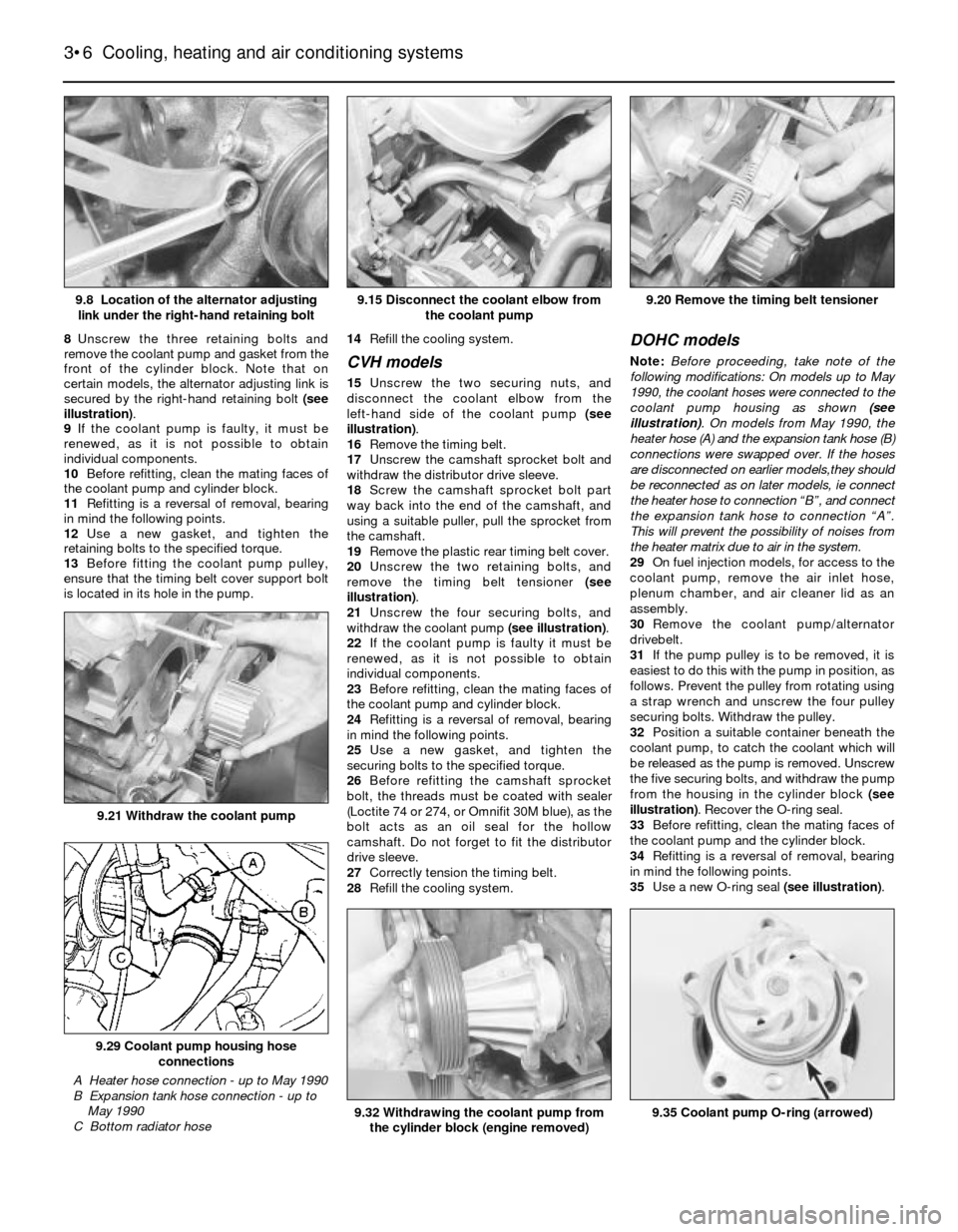
8Unscrew the three retaining bolts and
remove the coolant pump and gasket from the
front of the cylinder block. Note that on
certain models, the alternator adjusting link is
secured by the right-hand retaining bolt (see
illustration).
9If the coolant pump is faulty, it must be
renewed, as it is not possible to obtain
individual components.
10Before refitting, clean the mating faces of
the coolant pump and cylinder block.
11Refitting is a reversal of removal, bearing
in mind the following points.
12Use a new gasket, and tighten the
retaining bolts to the specified torque.
13Before fitting the coolant pump pulley,
ensure that the timing belt cover support bolt
is located in its hole in the pump.14Refill the cooling system.
CVH models
15Unscrew the two securing nuts, and
disconnect the coolant elbow from the
left-hand side of the coolant pump (see
illustration).
16Remove the timing belt.
17Unscrew the camshaft sprocket bolt and
withdraw the distributor drive sleeve.
18Screw the camshaft sprocket bolt part
way back into the end of the camshaft, and
using a suitable puller, pull the sprocket from
the camshaft.
19Remove the plastic rear timing belt cover.
20Unscrew the two retaining bolts, and
remove the timing belt tensioner (see
illustration).
21Unscrew the four securing bolts, and
withdraw the coolant pump (see illustration).
22If the coolant pump is faulty it must be
renewed, as it is not possible to obtain
individual components.
23Before refitting, clean the mating faces of
the coolant pump and cylinder block.
24Refitting is a reversal of removal, bearing
in mind the following points.
25Use a new gasket, and tighten the
securing bolts to the specified torque.
26Before refitting the camshaft sprocket
bolt, the threads must be coated with sealer
(Loctite 74 or 274, or Omnifit 30M blue), as the
bolt acts as an oil seal for the hollow
camshaft. Do not forget to fit the distributor
drive sleeve.
27Correctly tension the timing belt.
28Refill the cooling system.
DOHC models
Note:Before proceeding, take note of the
following modifications: On models up to May
1990, the coolant hoses were connected to the
coolant pump housing as shown (see
illustration). On models from May 1990, the
heater hose (A) and the expansion tank hose (B)
connections were swapped over. If the hoses
are disconnected on earlier models,they should
be reconnected as on later models, ie connect
the heater hose to connection “B”, and connect
the expansion tank hose to connection “A”.
This will prevent the possibility of noises from
the heater matrix due to air in the system.
29On fuel injection models, for access to the
coolant pump, remove the air inlet hose,
plenum chamber, and air cleaner lid as an
assembly.
30Remove the coolant pump/alternator
drivebelt.
31If the pump pulley is to be removed, it is
easiest to do this with the pump in position, as
follows. Prevent the pulley from rotating using
a strap wrench and unscrew the four pulley
securing bolts. Withdraw the pulley.
32Position a suitable container beneath the
coolant pump, to catch the coolant which will
be released as the pump is removed. Unscrew
the five securing bolts, and withdraw the pump
from the housing in the cylinder block (see
illustration). Recover the O-ring seal.
33Before refitting, clean the mating faces of
the coolant pump and the cylinder block.
34Refitting is a reversal of removal, bearing
in mind the following points.
35Use a new O-ring seal (see illustration).
3•6Cooling, heating and air conditioning systems
9.8 Location of the alternator adjusting
link under the right-hand retaining bolt9.20 Remove the timing belt tensioner
9.35 Coolant pump O-ring (arrowed)9.32 Withdrawing the coolant pump from
the cylinder block (engine removed)
9.29 Coolant pump housing hose
connections
A Heater hose connection - up to May 1990
B Expansion tank hose connection - up to
May 1990
C Bottom radiator hose
9.21 Withdraw the coolant pump
9.15 Disconnect the coolant elbow from
the coolant pump
Page 11 of 12
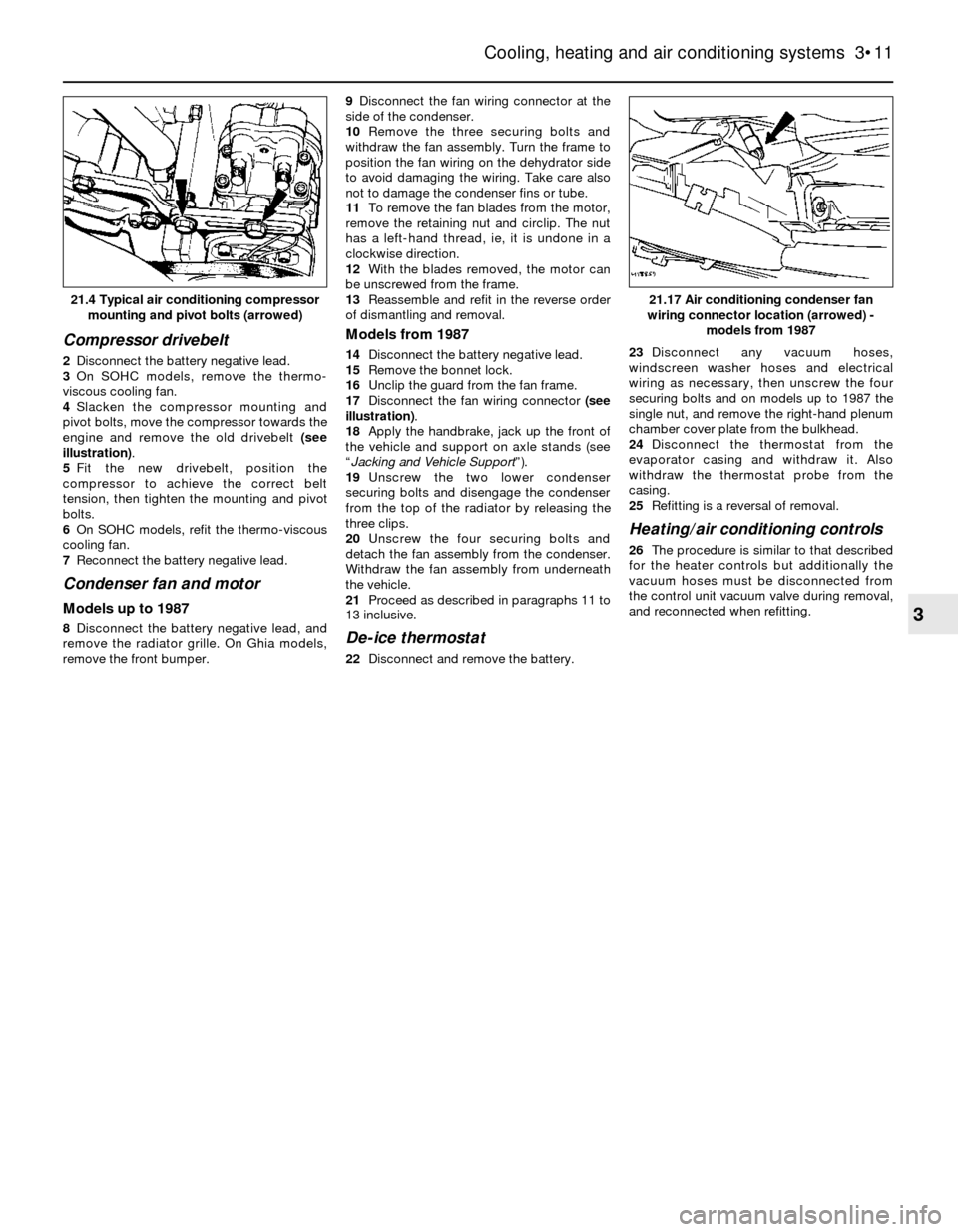
Compressor drivebelt
2Disconnect the battery negative lead.
3On SOHC models, remove the thermo-
viscous cooling fan.
4Slacken the compressor mounting and
pivot bolts, move the compressor towards the
engine and remove the old drivebelt (see
illustration).
5Fit the new drivebelt, position the
compressor to achieve the correct belt
tension, then tighten the mounting and pivot
bolts.
6On SOHC models, refit the thermo-viscous
cooling fan.
7Reconnect the battery negative lead.
Condenser fan and motor
Models up to 1987
8Disconnect the battery negative lead, and
remove the radiator grille. On Ghia models,
remove the front bumper.9Disconnect the fan wiring connector at the
side of the condenser.
10Remove the three securing bolts and
withdraw the fan assembly. Turn the frame to
position the fan wiring on the dehydrator side
to avoid damaging the wiring. Take care also
not to damage the condenser fins or tube.
11To remove the fan blades from the motor,
remove the retaining nut and circlip. The nut
has a left-hand thread, ie, it is undone in a
clockwise direction.
12With the blades removed, the motor can
be unscrewed from the frame.
13Reassemble and refit in the reverse order
of dismantling and removal.
Models from 1987
14Disconnect the battery negative lead.
15Remove the bonnet lock.
16Unclip the guard from the fan frame.
17Disconnect the fan wiring connector (see
illustration).
18Apply the handbrake, jack up the front of
the vehicle and support on axle stands (see
“Jacking and Vehicle Support”).
19Unscrew the two lower condenser
securing bolts and disengage the condenser
from the top of the radiator by releasing the
three clips.
20Unscrew the four securing bolts and
detach the fan assembly from the condenser.
Withdraw the fan assembly from underneath
the vehicle.
21Proceed as described in paragraphs 11 to
13 inclusive.
De-ice thermostat
22Disconnect and remove the battery.23Disconnect any vacuum hoses,
windscreen washer hoses and electrical
wiring as necessary, then unscrew the four
securing bolts and on models up to 1987 the
single nut, and remove the right-hand plenum
chamber cover plate from the bulkhead.
24Disconnect the thermostat from the
evaporator casing and withdraw it. Also
withdraw the thermostat probe from the
casing.
25Refitting is a reversal of removal.
Heating/air conditioning controls
26The procedure is similar to that described
for the heater controls but additionally the
vacuum hoses must be disconnected from
the control unit vacuum valve during removal,
and reconnected when refitting.
Cooling, heating and air conditioning systems 3•11
3
21.17 Air conditioning condenser fan
wiring connector location (arrowed) -
models from 198721.4 Typical air conditioning compressor
mounting and pivot bolts (arrowed)