lock FORD SIERRA 1992 2.G DOHC Engine User Guide
[x] Cancel search | Manufacturer: FORD, Model Year: 1992, Model line: SIERRA, Model: FORD SIERRA 1992 2.GPages: 18, PDF Size: 0.9 MB
Page 16 of 18
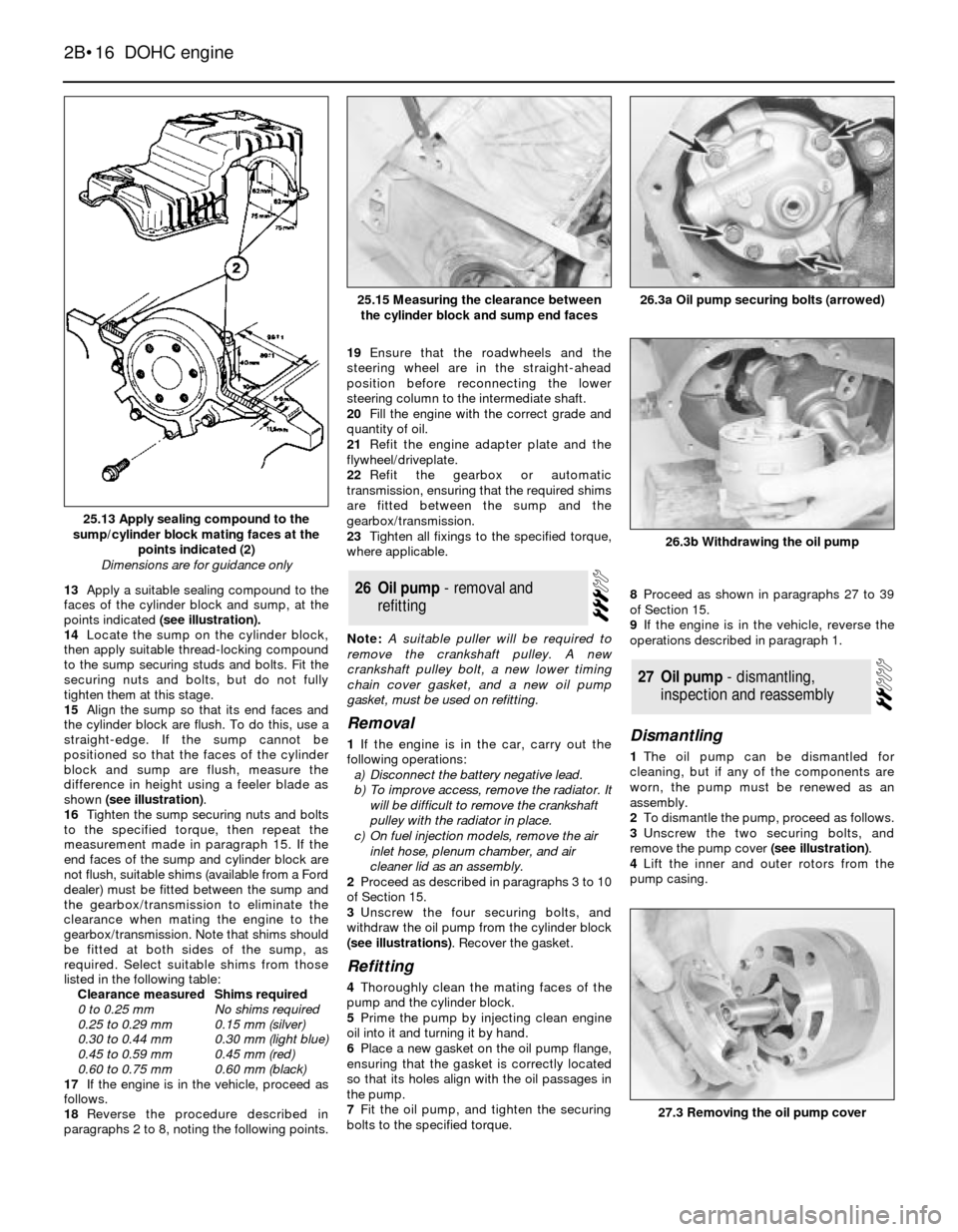
13Apply a suitable sealing compound to the
faces of the cylinder block and sump, at the
points indicated (see illustration).
14Locate the sump on the cylinder block,
then apply suitable thread-locking compound
to the sump securing studs and bolts. Fit the
securing nuts and bolts, but do not fully
tighten them at this stage.
15Align the sump so that its end faces and
the cylinder block are flush. To do this, use a
straight-edge. If the sump cannot be
positioned so that the faces of the cylinder
block and sump are flush, measure the
difference in height using a feeler blade as
shown (see illustration).
16Tighten the sump securing nuts and bolts
to the specified torque, then repeat the
measurement made in paragraph 15. If the
end faces of the sump and cylinder block are
not flush, suitable shims (available from a Ford
dealer) must be fitted between the sump and
the gearbox/transmission to eliminate the
clearance when mating the engine to the
gearbox/transmission. Note that shims should
be fitted at both sides of the sump, as
required. Select suitable shims from those
listed in the following table:
Clearance measuredShims required
0 to 0.25 mmNo shims required
0.25 to 0.29 mm0.15 mm (silver)
0.30 to 0.44 mm0.30 mm (light blue)
0.45 to 0.59 mm0.45 mm (red)
0.60 to 0.75 mm0.60 mm (black)
17If the engine is in the vehicle, proceed as
follows.
18Reverse the procedure described in
paragraphs 2 to 8, noting the following points.19Ensure that the roadwheels and the
steering wheel are in the straight-ahead
position before reconnecting the lower
steering column to the intermediate shaft.
20Fill the engine with the correct grade and
quantity of oil.
21Refit the engine adapter plate and the
flywheel/driveplate.
22Refit the gearbox or automatic
transmission, ensuring that the required shims
are fitted between the sump and the
gearbox/transmission.
23Tighten all fixings to the specified torque,
where applicable.
Note: A suitable puller will be required to
remove the crankshaft pulley. A new
crankshaft pulley bolt, a new lower timing
chain cover gasket, and a new oil pump
gasket, must be used on refitting.
Removal
1If the engine is in the car, carry out the
following operations:
a)Disconnect the battery negative lead.
b)To improve access, remove the radiator. It
will be difficult to remove the crankshaft
pulley with the radiator in place.
c)On fuel injection models, remove the air
inlet hose, plenum chamber, and air
cleaner lid as an assembly.
2Proceed as described in paragraphs 3 to 10
of Section 15.
3Unscrew the four securing bolts, and
withdraw the oil pump from the cylinder block
(see illustrations). Recover the gasket.
Refitting
4Thoroughly clean the mating faces of the
pump and the cylinder block.
5Prime the pump by injecting clean engine
oil into it and turning it by hand.
6Place a new gasket on the oil pump flange,
ensuring that the gasket is correctly located
so that its holes align with the oil passages in
the pump.
7Fit the oil pump, and tighten the securing
bolts to the specified torque.8Proceed as shown in paragraphs 27 to 39
of Section 15.
9If the engine is in the vehicle, reverse the
operations described in paragraph 1.
Dismantling
1The oil pump can be dismantled for
cleaning, but if any of the components are
worn, the pump must be renewed as an
assembly.
2To dismantle the pump, proceed as follows.
3Unscrew the two securing bolts, and
remove the pump cover (see illustration).
4Lift the inner and outer rotors from the
pump casing.
27Oil pump - dismantling,
inspection and reassembly
26Oil pump - removal and
refitting
2B•16DOHC engine
25.13 Apply sealing compound to the
sump/cylinder block mating faces at the
points indicated (2)
Dimensions are for guidance only
26.3b Withdrawing the oil pump
26.3a Oil pump securing bolts (arrowed)25.15 Measuring the clearance between
the cylinder block and sump end faces
27.3 Removing the oil pump cover
Page 17 of 18
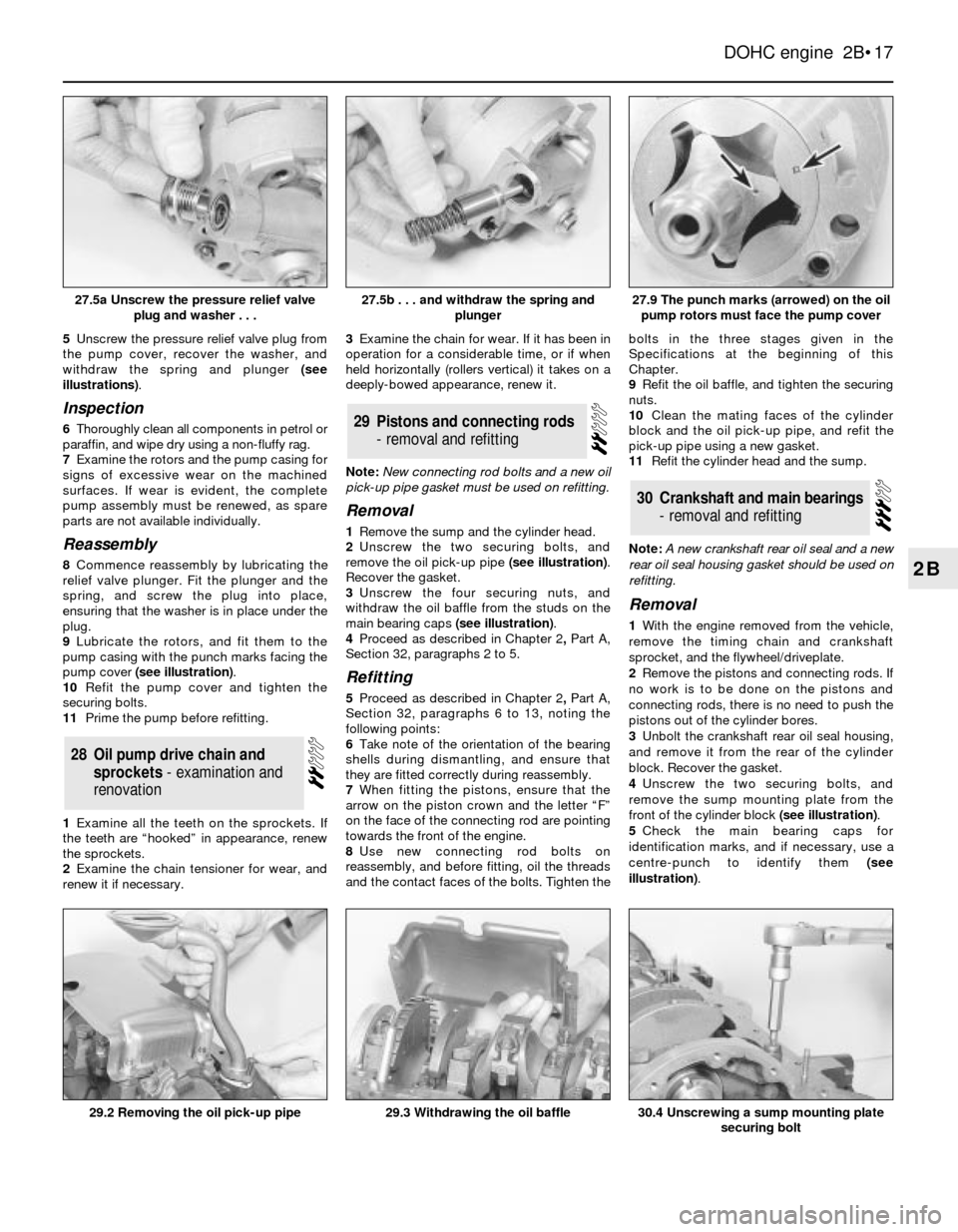
5Unscrew the pressure relief valve plug from
the pump cover, recover the washer, and
withdraw the spring and plunger (see
illustrations).
Inspection
6Thoroughly clean all components in petrol or
paraffin, and wipe dry using a non-fluffy rag.
7Examine the rotors and the pump casing for
signs of excessive wear on the machined
surfaces. If wear is evident, the complete
pump assembly must be renewed, as spare
parts are not available individually.
Reassembly
8Commence reassembly by lubricating the
relief valve plunger. Fit the plunger and the
spring, and screw the plug into place,
ensuring that the washer is in place under the
plug.
9Lubricate the rotors, and fit them to the
pump casing with the punch marks facing the
pump cover (see illustration).
10Refit the pump cover and tighten the
securing bolts.
11Prime the pump before refitting.
1Examine all the teeth on the sprockets. If
the teeth are “hooked” in appearance, renew
the sprockets.
2Examine the chain tensioner for wear, and
renew it if necessary.3Examine the chain for wear. If it has been in
operation for a considerable time, or if when
held horizontally (rollers vertical) it takes on a
deeply-bowed appearance, renew it.
Note: New connecting rod bolts and a new oil
pick-up pipe gasket must be used on refitting.
Removal
1Remove the sump and the cylinder head.
2Unscrew the two securing bolts, and
remove the oil pick-up pipe (see illustration).
Recover the gasket.
3Unscrew the four securing nuts, and
withdraw the oil baffle from the studs on the
main bearing caps (see illustration).
4Proceed as described in Chapter 2, PartA,
Section 32, paragraphs 2 to 5.
Refitting
5Proceed as described in Chapter 2, PartA,
Section 32, paragraphs 6 to 13, noting the
following points:
6Take note of the orientation of the bearing
shells during dismantling, and ensure that
they are fitted correctly during reassembly.
7When fitting the pistons, ensure that the
arrow on the piston crown and the letter “F”
on the face of the connecting rod are pointing
towards the front of the engine.
8Use new connecting rod bolts on
reassembly, and before fitting, oil the threads
and the contact faces of the bolts. Tighten thebolts in the three stages given in the
Specifications at the beginning of this
Chapter.
9Refit the oil baffle, and tighten the securing
nuts.
10Clean the mating faces of the cylinder
block and the oil pick-up pipe, and refit the
pick-up pipe using a new gasket.
11Refit the cylinder head and the sump.
Note: A new crankshaft rear oil seal and a new
rear oil seal housing gasket should be used on
refitting.
Removal
1With the engine removed from the vehicle,
remove the timing chain and crankshaft
sprocket, and the flywheel/driveplate.
2Remove the pistons and connecting rods. If
no work is to be done on the pistons and
connecting rods, there is no need to push the
pistons out of the cylinder bores.
3Unbolt the crankshaft rear oil seal housing,
and remove it from the rear of the cylinder
block. Recover the gasket.
4Unscrew the two securing bolts, and
remove the sump mounting plate from the
front of the cylinder block (see illustration).
5Check the main bearing caps for
identification marks, and if necessary, use a
centre-punch to identify them (see
illustration).
30Crankshaft and main bearings
- removal and refitting
29Pistons and connecting rods
- removal and refitting
28Oil pump drive chain and
sprockets - examination and
renovation
DOHC engine 2B•17
2B
27.5b . . . and withdraw the spring and
plunger
30.4 Unscrewing a sump mounting plate
securing bolt29.3 Withdrawing the oil baffle29.2 Removing the oil pick-up pipe
27.9 The punch marks (arrowed) on the oil
pump rotors must face the pump cover27.5a Unscrew the pressure relief valve
plug and washer . . .
Page 18 of 18
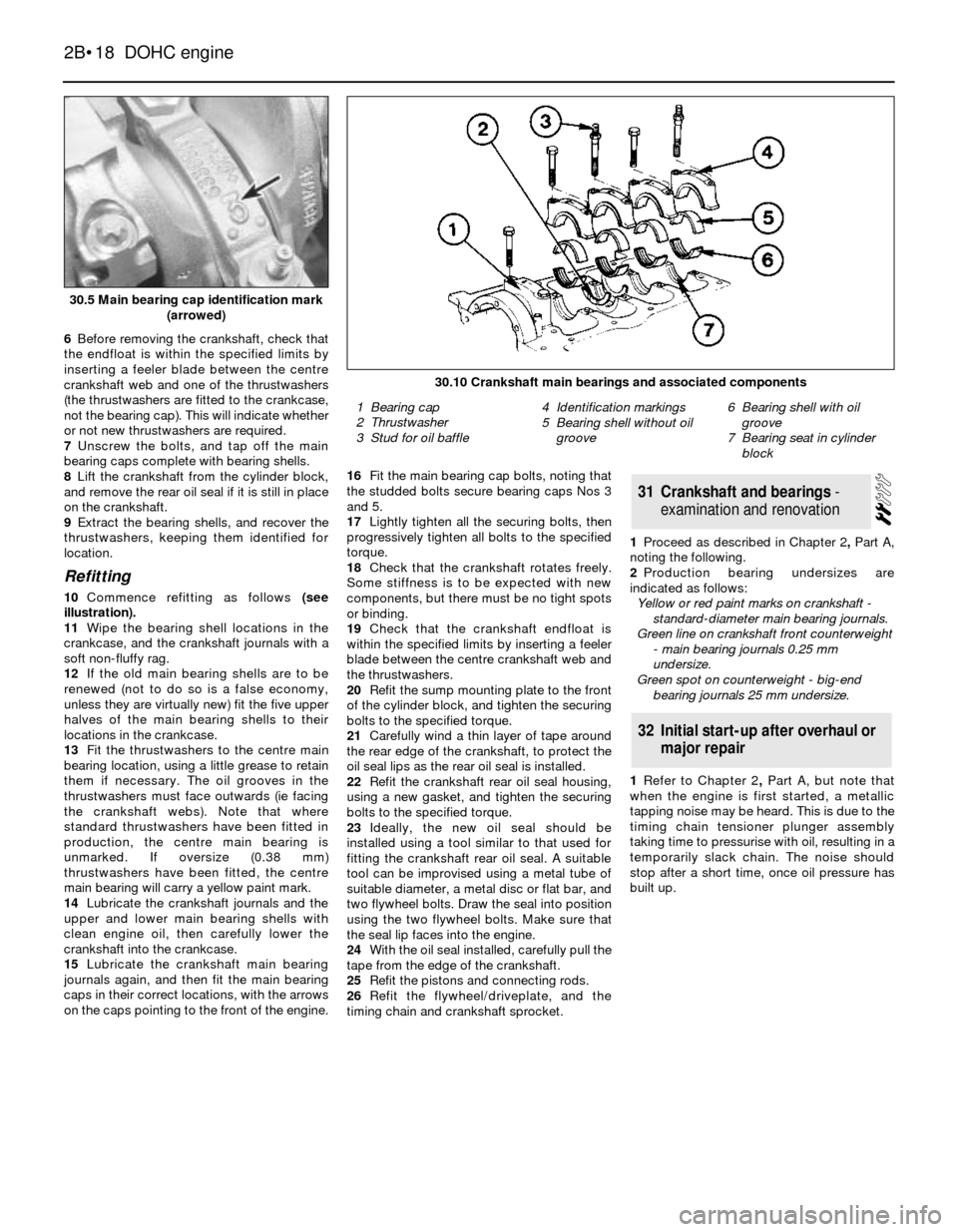
6Before removing the crankshaft, check that
the endfloat is within the specified limits by
inserting a feeler blade between the centre
crankshaft web and one of the thrustwashers
(the thrustwashers are fitted to the crankcase,
not the bearing cap). This will indicate whether
or not new thrustwashers are required.
7Unscrew the bolts, and tap off the main
bearing caps complete with bearing shells.
8Lift the crankshaft from the cylinder block,
and remove the rear oil seal if it is still in place
on the crankshaft.
9Extract the bearing shells, and recover the
thrustwashers, keeping them identified for
location.
Refitting
10Commence refitting as follows(see
illustration).
11Wipe the bearing shell locations in the
crankcase, and the crankshaft journals with a
soft non-fluffy rag.
12If the old main bearing shells are to be
renewed (not to do so is a false economy,
unless they are virtually new) fit the five upper
halves of the main bearing shells to their
locations in the crankcase.
13Fit the thrustwashers to the centre main
bearing location, using a little grease to retain
them if necessary. The oil grooves in the
thrustwashers must face outwards (ie facing
the crankshaft webs). Note that where
standard thrustwashers have been fitted in
production, the centre main bearing is
unmarked. If oversize (0.38 mm)
thrustwashers have been fitted, the centre
main bearing will carry a yellow paint mark.
14Lubricate the crankshaft journals and the
upper and lower main bearing shells with
clean engine oil, then carefully lower the
crankshaft into the crankcase.
15Lubricate the crankshaft main bearing
journals again, and then fit the main bearing
caps in their correct locations, with the arrows
on the caps pointing to the front of the engine.16Fit the main bearing cap bolts, noting that
the studded bolts secure bearing caps Nos 3
and 5.
17Lightly tighten all the securing bolts, then
progressively tighten all bolts to the specified
torque.
18Check that the crankshaft rotates freely.
Some stiffness is to be expected with new
components, but there must be no tight spots
or binding.
19Check that the crankshaft endfloat is
within the specified limits by inserting a feeler
blade between the centre crankshaft web and
the thrustwashers.
20Refit the sump mounting plate to the front
of the cylinder block, and tighten the securing
bolts to the specified torque.
21Carefully wind a thin layer of tape around
the rear edge of the crankshaft, to protect the
oil seal lips as the rear oil seal is installed.
22Refit the crankshaft rear oil seal housing,
using a new gasket, and tighten the securing
bolts to the specified torque.
23Ideally, the new oil seal should be
installed using a tool similar to that used for
fitting the crankshaft rear oil seal. A suitable
tool can be improvised using a metal tube of
suitable diameter, a metal disc or flat bar, and
two flywheel bolts. Draw the seal into position
using the two flywheel bolts. Make sure that
the seal lip faces into the engine.
24With the oil seal installed, carefully pull the
tape from the edge of the crankshaft.
25Refit the pistons and connecting rods.
26Refit the flywheel/driveplate, and the
timing chain and crankshaft sprocket.1Proceed as described in Chapter 2, PartA,
noting the following.
2Production bearing undersizes are
indicated as follows:
Yellow or red paint marks on crankshaft -
standard-diameter main bearing journals.
Green line on crankshaft front counterweight
- main bearing journals 0.25 mm
undersize.
Green spot on counterweight - big-end
bearing journals 25 mm undersize.
1Refer to Chapter 2, PartA, but note that
when the engine is first started, a metallic
tapping noise may be heard. This is due to the
timing chain tensioner plunger assembly
taking time to pressurise with oil, resulting in a
temporarily slack chain. The noise should
stop after a short time, once oil pressure has
built up.
32Initial start-up after overhaul or
major repair
31Crankshaft and bearings -
examination and renovation
2B•18DOHC engine
30.5 Main bearing cap identification mark
(arrowed)
30.10 Crankshaft main bearings and associated components
1 Bearing cap
2 Thrustwasher
3 Stud for oil baffle4 Identification markings
5 Bearing shell without oil
groove6 Bearing shell with oil
groove
7 Bearing seat in cylinder
block