gas type FORD SIERRA 1992 2.G Engine Electrical Systems Workshop Manual
[x] Cancel search | Manufacturer: FORD, Model Year: 1992, Model line: SIERRA, Model: FORD SIERRA 1992 2.GPages: 24, PDF Size: 0.93 MB
Page 4 of 24
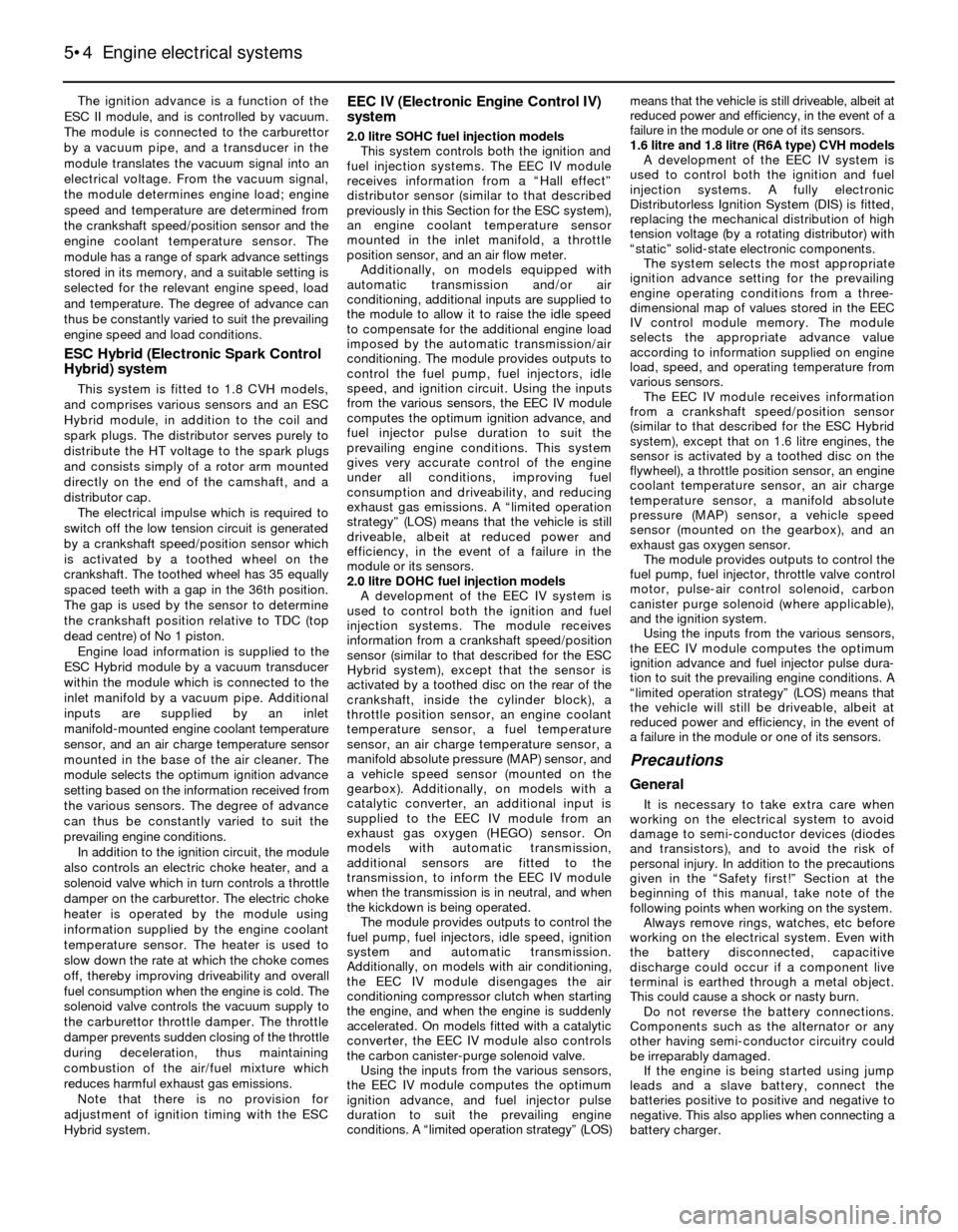
The ignition advance is a function of the
ESC II module, and is controlled by vacuum.
The module is connected to the carburettor
by a vacuum pipe, and a transducer in the
module translates the vacuum signal into an
electrical voltage. From the vacuum signal,
the module determines engine load; engine
speed and temperature are determined from
the crankshaft speed/position sensor and the
engine coolant temperature sensor. The
module has a range of spark advance settings
stored in its memory, and a suitable setting is
selected for the relevant engine speed, load
and temperature. The degree of advance can
thus be constantly varied to suit the prevailing
engine speed and load conditions.
ESC Hybrid (Electronic Spark Control
Hybrid) system
This system is fitted to 1.8 CVH models,
and comprises various sensors and an ESC
Hybrid module, in addition to the coil and
spark plugs. The distributor serves purely to
distribute the HT voltage to the spark plugs
and consists simply of a rotor arm mounted
directly on the end of the camshaft, and a
distributor cap.
The electrical impulse which is required to
switch off the low tension circuit is generated
by a crankshaft speed/position sensor which
is activated by a toothed wheel on the
crankshaft. The toothed wheel has 35 equally
spaced teeth with a gap in the 36th position.
The gap is used by the sensor to determine
the crankshaft position relative to TDC (top
dead centre) of No 1 piston.
Engine load information is supplied to the
ESC Hybrid module by a vacuum transducer
within the module which is connected to the
inlet manifold by a vacuum pipe. Additional
inputs are supplied by an inlet
manifold-mounted engine coolant temperature
sensor, and an air charge temperature sensor
mounted in the base of the air cleaner. The
module selects the optimum ignition advance
setting based on the information received from
the various sensors. The degree of advance
can thus be constantly varied to suit the
prevailing engine conditions.
In addition to the ignition circuit, the module
also controls an electric choke heater, and a
solenoid valve which in turn controls a throttle
damper on the carburettor. The electric choke
heater is operated by the module using
information supplied by the engine coolant
temperature sensor. The heater is used to
slow down the rate at which the choke comes
off, thereby improving driveability and overall
fuel consumption when the engine is cold. The
solenoid valve controls the vacuum supply to
the carburettor throttle damper. The throttle
damper prevents sudden closing of the throttle
during deceleration, thus maintaining
combustion of the air/fuel mixture which
reduces harmful exhaust gas emissions.
Note that there is no provision for
adjustment of ignition timing with the ESC
Hybrid system.
EEC IV (Electronic Engine Control IV)
system
2.0 litre SOHC fuel injection models
This system controls both the ignition and
fuel injection systems. The EEC IV module
receives information from a “Hall effect”
distributor sensor (similar to that described
previously in this Section for the ESC system),
an engine coolant temperature sensor
mounted in the inlet manifold, a throttle
position sensor, and an air flow meter.
Additionally, on models equipped with
automatic transmission and/or air
conditioning, additional inputs are supplied to
the module to allow it to raise the idle speed
to compensate for the additional engine load
imposed by the automatic transmission/air
conditioning. The module provides outputs to
control the fuel pump, fuel injectors, idle
speed, and ignition circuit. Using the inputs
from the various sensors, the EEC IV module
computes the optimum ignition advance, and
fuel injector pulse duration to suit the
prevailing engine conditions. This system
gives very accurate control of the engine
under all conditions, improving fuel
consumption and driveability, and reducing
exhaust gas emissions. A “limited operation
strategy” (LOS) means that the vehicle is still
driveable, albeit at reduced power and
efficiency, in the event of a failure in the
module or its sensors.
2.0 litre DOHC fuel injection models
A development of the EEC IV system is
used to control both the ignition and fuel
injection systems. The module receives
information from a crankshaft speed/position
sensor (similar to that described for the ESC
Hybrid system), except that the sensor is
activated by a toothed disc on the rear of the
crankshaft, inside the cylinder block), a
throttle position sensor, an engine coolant
temperature sensor, a fuel temperature
sensor, an air charge temperature sensor, a
manifold absolute pressure (MAP) sensor, and
a vehicle speed sensor (mounted on the
gearbox). Additionally, on models with a
catalytic converter, an additional input is
supplied to the EEC IV module from an
exhaust gas oxygen (HEGO) sensor. On
models with automatic transmission,
additional sensors are fitted to the
transmission, to inform the EEC IV module
when the transmission is in neutral, and when
the kickdown is being operated.
The module provides outputs to control the
fuel pump, fuel injectors, idle speed, ignition
system and automatic transmission.
Additionally, on models with air conditioning,
the EEC IV module disengages the air
conditioning compressor clutch when starting
the engine, and when the engine is suddenly
accelerated. On models fitted with a catalytic
converter, the EEC IV module also controls
the carbon canister-purge solenoid valve.
Using the inputs from the various sensors,
the EEC IV module computes the optimum
ignition advance, and fuel injector pulse
duration to suit the prevailing engine
conditions. A “limited operation strategy” (LOS)means that the vehicle is still driveable, albeit at
reduced power and efficiency, in the event of a
failure in the module or one of its sensors.
1.6 litre and 1.8 litre (R6A type) CVH models
A development of the EEC IV system is
used to control both the ignition and fuel
injection systems. A fully electronic
Distributorless Ignition System (DIS) is fitted,
replacing the mechanical distribution of high
tension voltage (by a rotating distributor) with
“static” solid-state electronic components.
The system selects the most appropriate
ignition advance setting for the prevailing
engine operating conditions from a three-
dimensional map of values stored in the EEC
IV control module memory. The module
selects the appropriate advance value
according to information supplied on engine
load, speed, and operating temperature from
various sensors.
The EEC IV module receives information
from a crankshaft speed/position sensor
(similar to that described for the ESC Hybrid
system), except that on 1.6 litre engines, the
sensor is activated by a toothed disc on the
flywheel), a throttle position sensor, an engine
coolant temperature sensor, an air charge
temperature sensor, a manifold absolute
pressure (MAP) sensor, a vehicle speed
sensor (mounted on the gearbox), and an
exhaust gas oxygen sensor.
The module provides outputs to control the
fuel pump, fuel injector, throttle valve control
motor, pulse-air control solenoid, carbon
canister purge solenoid (where applicable),
and the ignition system.
Using the inputs from the various sensors,
the EEC IV module computes the optimum
ignition advance and fuel injector pulse dura-
tion to suit the prevailing engine conditions. A
“limited operation strategy” (LOS) means that
the vehicle will still be driveable, albeit at
reduced power and efficiency, in the event of
a failure in the module or one of its sensors.
Precautions
General
It is necessary to take extra care when
working on the electrical system to avoid
damage to semi-conductor devices (diodes
and transistors), and to avoid the risk of
personal injury. In addition to the precautions
given in the “Safety first!” Section at the
beginning of this manual, take note of the
following points when working on the system.
Always remove rings, watches, etc before
working on the electrical system. Even with
the battery disconnected, capacitive
discharge could occur if a component live
terminal is earthed through a metal object.
This could cause a shock or nasty burn.
Do not reverse the battery connections.
Components such as the alternator or any
other having semi-conductor circuitry could
be irreparably damaged.
If the engine is being started using jump
leads and a slave battery, connect the
batteries positive to positive and negative to
negative. This also applies when connecting a
battery charger.
5•4Engine electrical systems
Page 10 of 24
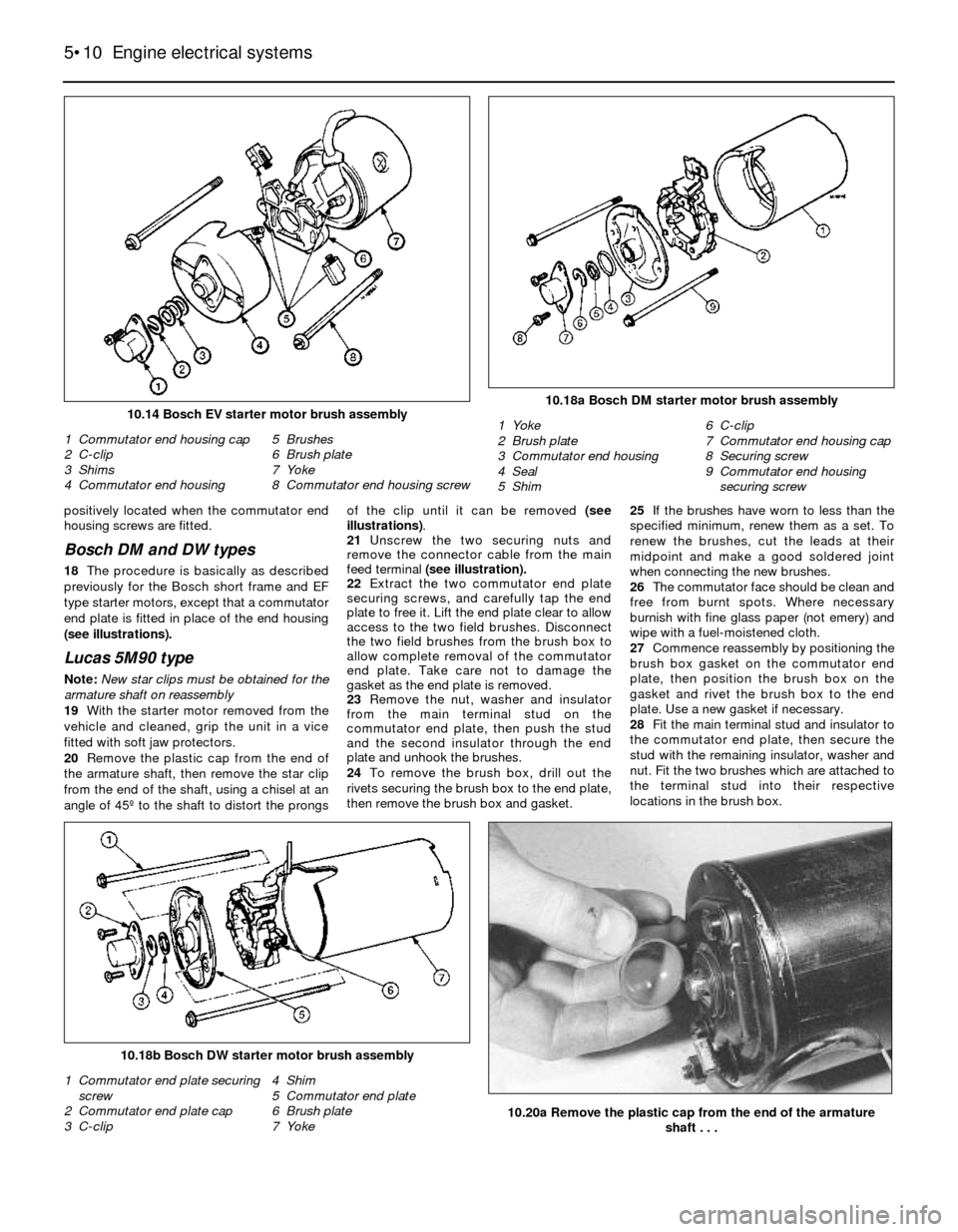
positively located when the commutator end
housing screws are fitted.
Bosch DM and DW types
18The procedure is basically as described
previously for the Bosch short frame and EF
type starter motors, except that a commutator
end plate is fitted in place of the end housing
(see illustrations).
Lucas 5M90 type
Note: New star clips must be obtained for the
armature shaft on reassembly
19With the starter motor removed from the
vehicle and cleaned, grip the unit in a vice
fitted with soft jaw protectors.
20Remove the plastic cap from the end of
the armature shaft, then remove the star clip
from the end of the shaft, using a chisel at an
angle of 45º to the shaft to distort the prongsof the clip until it can be removed (see
illustrations).
21Unscrew the two securing nuts and
remove the connector cable from the main
feed terminal (see illustration).
22Extract the two commutator end plate
securing screws, and carefully tap the end
plate to free it. Lift the end plate clear to allow
access to the two field brushes. Disconnect
the two field brushes from the brush box to
allow complete removal of the commutator
end plate. Take care not to damage the
gasket as the end plate is removed.
23Remove the nut, washer and insulator
from the main terminal stud on the
commutator end plate, then push the stud
and the second insulator through the end
plate and unhook the brushes.
24To remove the brush box, drill out the
rivets securing the brush box to the end plate,
then remove the brush box and gasket.25If the brushes have worn to less than the
specified minimum, renew them as a set. To
renew the brushes, cut the leads at their
midpoint and make a good soldered joint
when connecting the new brushes.
26The commutator face should be clean and
free from burnt spots. Where necessary
burnish with fine glass paper (not emery) and
wipe with a fuel-moistened cloth.
27Commence reassembly by positioning the
brush box gasket on the commutator end
plate, then position the brush box on the
gasket and rivet the brush box to the end
plate. Use a new gasket if necessary.
28Fit the main terminal stud and insulator to
the commutator end plate, then secure the
stud with the remaining insulator, washer and
nut. Fit the two brushes which are attached to
the terminal stud into their respective
locations in the brush box.
5•10Engine electrical systems
10.18a Bosch DM starter motor brush assembly
1 Yoke
2 Brush plate
3 Commutator end housing
4 Seal
5 Shim6 C-clip
7 Commutator end housing cap
8 Securing screw
9 Commutator end housing
securing screw
10.20a Remove the plastic cap from the end of the armature
shaft . . .
10.18b Bosch DW starter motor brush assembly
1 Commutator end plate securing
screw
2 Commutator end plate cap
3 C-clip4 Shim
5 Commutator end plate
6 Brush plate
7 Yoke
10.14 Bosch EV starter motor brush assembly
1 Commutator end housing cap
2 C-clip
3 Shims
4 Commutator end housing5 Brushes
6 Brush plate
7 Yoke
8 Commutator end housing screw
Page 21 of 24
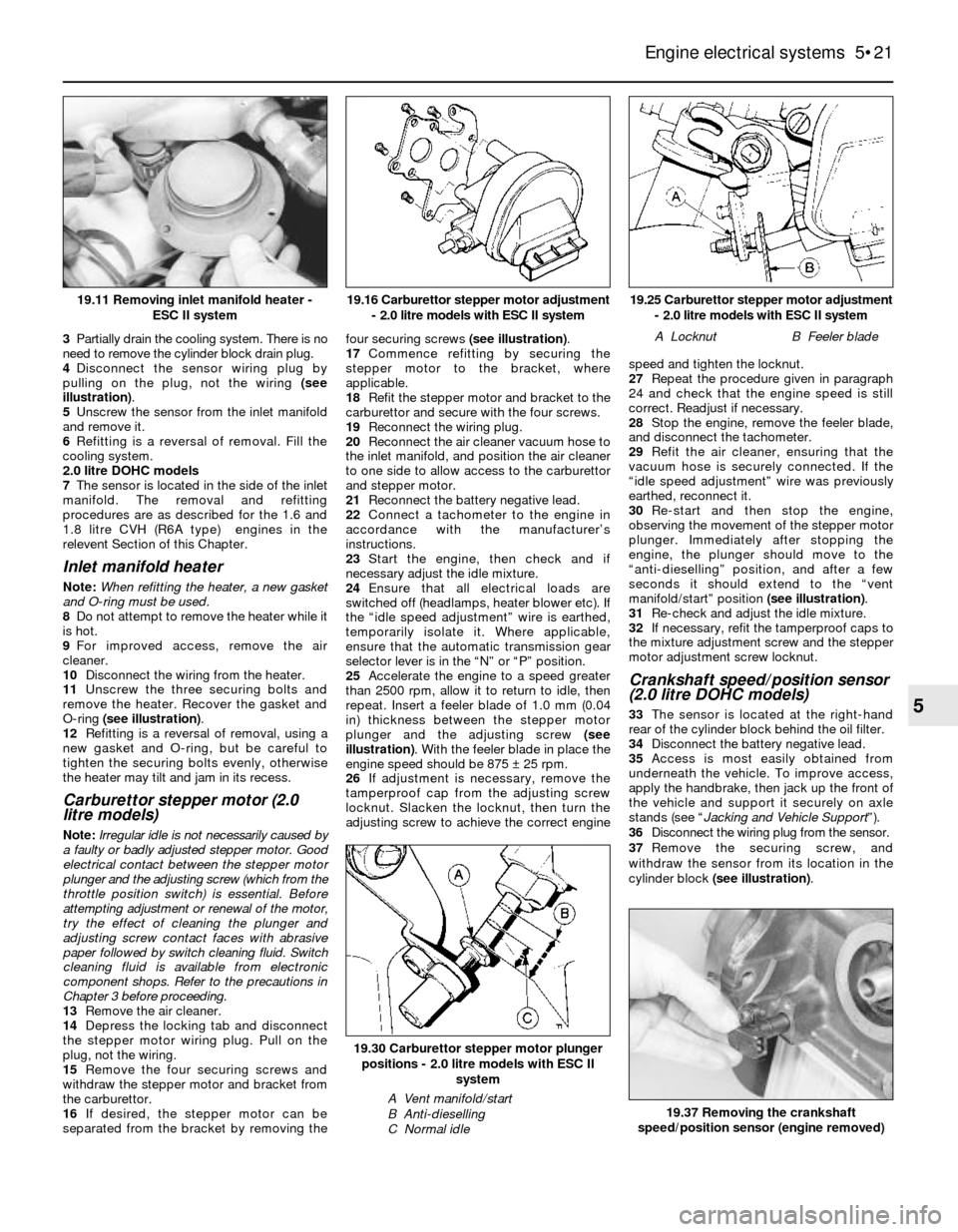
3Partially drain the cooling system. There is no
need to remove the cylinder block drain plug.
4Disconnect the sensor wiring plug by
pulling on the plug, not the wiring (see
illustration).
5Unscrew the sensor from the inlet manifold
and remove it.
6Refitting is a reversal of removal. Fill the
cooling system.
2.0 litre DOHC models
7The sensor is located in the side of the inlet
manifold. The removal and refitting
procedures are as described for the 1.6 and
1.8 litre CVH (R6A type) engines in the
relevent Section of this Chapter.
Inlet manifold heater
Note: When refitting the heater, a new gasket
and O-ring must be used.
8Do not attempt to remove the heater while it
is hot.
9For improved access, remove the air
cleaner.
10Disconnect the wiring from the heater.
11Unscrew the three securing bolts and
remove the heater. Recover the gasket and
O-ring (see illustration).
12Refitting is a reversal of removal, using a
new gasket and O-ring, but be careful to
tighten the securing bolts evenly, otherwise
the heater may tilt and jam in its recess.
Carburettor stepper motor (2.0
litre models)
Note: Irregular idle is not necessarily caused by
a faulty or badly adjusted stepper motor. Good
electrical contact between the stepper motor
plunger and the adjusting screw (which from the
throttle position switch) is essential. Before
attempting adjustment or renewal of the motor,
try the effect of cleaning the plunger and
adjusting screw contact faces with abrasive
paper followed by switch cleaning fluid. Switch
cleaning fluid is available from electronic
component shops. Refer to the precautions in
Chapter 3 before proceeding.
13Remove the air cleaner.
14Depress the locking tab and disconnect
the stepper motor wiring plug. Pull on the
plug, not the wiring.
15Remove the four securing screws and
withdraw the stepper motor and bracket from
the carburettor.
16If desired, the stepper motor can be
separated from the bracket by removing thefour securing screws (see illustration).
17Commence refitting by securing the
stepper motor to the bracket, where
applicable.
18Refit the stepper motor and bracket to the
carburettor and secure with the four screws.
19Reconnect the wiring plug.
20Reconnect the air cleaner vacuum hose to
the inlet manifold, and position the air cleaner
to one side to allow access to the carburettor
and stepper motor.
21Reconnect the battery negative lead.
22Connect a tachometer to the engine in
accordance with the manufacturer’s
instructions.
23Start the engine, then check and if
necessary adjust the idle mixture.
24Ensure that all electrical loads are
switched off (headlamps, heater blower etc). If
the “idle speed adjustment” wire is earthed,
temporarily isolate it. Where applicable,
ensure that the automatic transmission gear
selector lever is in the “N” or “P” position.
25Accelerate the engine to a speed greater
than 2500 rpm, allow it to return to idle, then
repeat. Insert a feeler blade of 1.0 mm (0.04
in) thickness between the stepper motor
plunger and the adjusting screw (see
illustration). With the feeler blade in place the
engine speed should be 875 ±25 rpm.
26If adjustment is necessary, remove the
tamperproof cap from the adjusting screw
locknut. Slacken the locknut, then turn the
adjusting screw to achieve the correct enginespeed and tighten the locknut.
27Repeat the procedure given in paragraph
24 and check that the engine speed is still
correct. Readjust if necessary.
28Stop the engine, remove the feeler blade,
and disconnect the tachometer.
29Refit the air cleaner, ensuring that the
vacuum hose is securely connected. If the
“idle speed adjustment” wire was previously
earthed, reconnect it.
30Re-start and then stop the engine,
observing the movement of the stepper motor
plunger. Immediately after stopping the
engine, the plunger should move to the
“anti-dieselling” position, and after a few
seconds it should extend to the “vent
manifold/start” position (see illustration).
31Re-check and adjust the idle mixture.
32If necessary, refit the tamperproof caps to
the mixture adjustment screw and the stepper
motor adjustment screw locknut.
Crankshaft speed/position sensor
(2.0 litre DOHC models)
33The sensor is located at the right-hand
rear of the cylinder block behind the oil filter.
34Disconnect the battery negative lead.
35Access is most easily obtained from
underneath the vehicle. To improve access,
apply the handbrake, then jack up the front of
the vehicle and support it securely on axle
stands (see “Jacking and Vehicle Support”).
36Disconnect the wiring plug from the sensor.
37Remove the securing screw, and
withdraw the sensor from its location in the
cylinder block (see illustration).
Engine electrical systems 5•21
5
19.25 Carburettor stepper motor adjustment
- 2.0 litre models with ESC II system
A LocknutB Feeler blade
19.37 Removing the crankshaft
speed/position sensor (engine removed)
19.30 Carburettor stepper motor plunger
positions - 2.0 litre models with ESC II
system
A Vent manifold/start
B Anti-dieselling
C Normal idle
19.16 Carburettor stepper motor adjustment
- 2.0 litre models with ESC II system19.11 Removing inlet manifold heater -
ESC II system