light FORD SIERRA 1992 2.G Engine Electrical Systems Workshop Manual
[x] Cancel search | Manufacturer: FORD, Model Year: 1992, Model line: SIERRA, Model: FORD SIERRA 1992 2.GPages: 24, PDF Size: 0.93 MB
Page 3 of 24
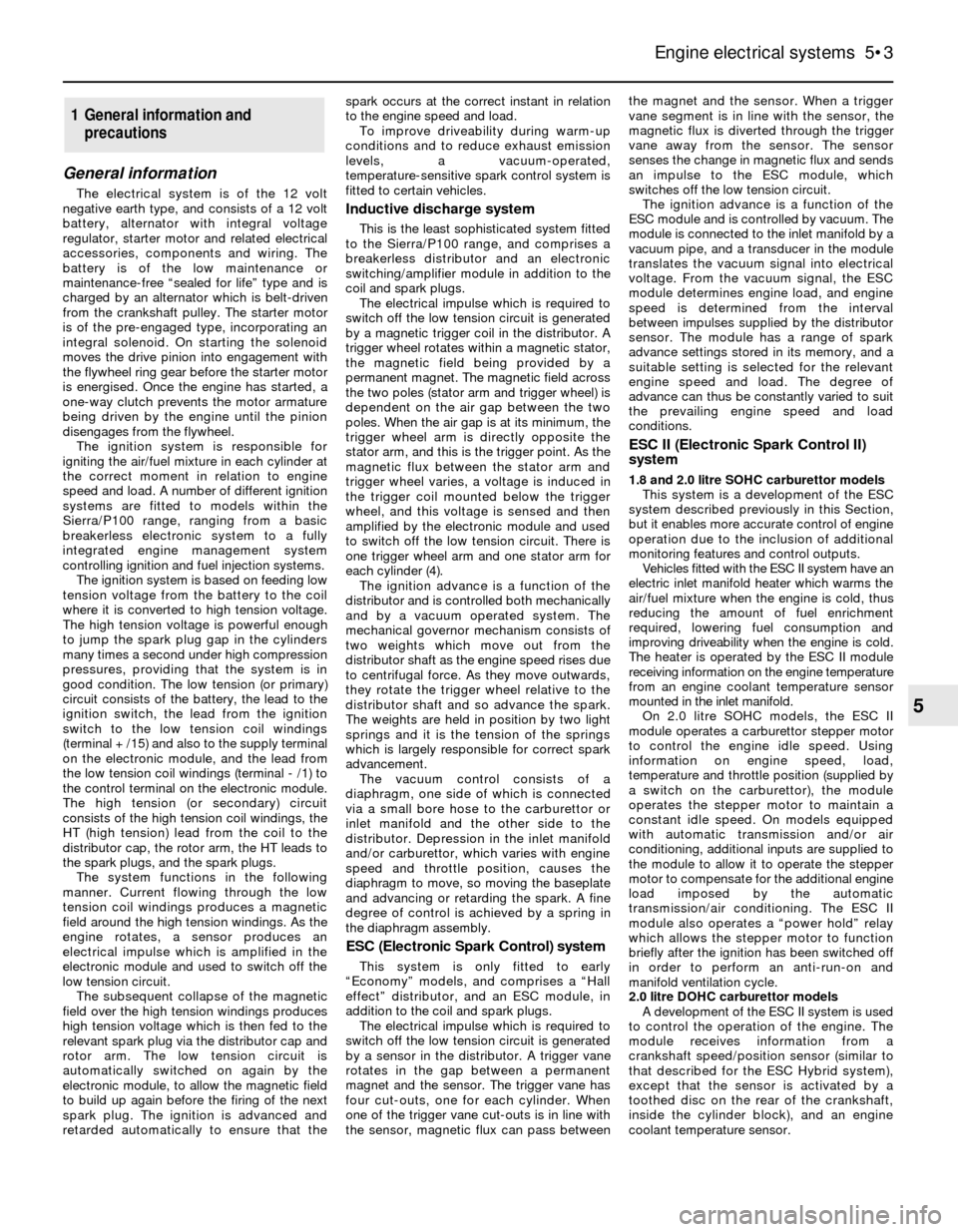
General information
The electrical system is of the 12 volt
negative earth type, and consists of a 12 volt
battery, alternator with integral voltage
regulator, starter motor and related electrical
accessories, components and wiring. The
battery is of the low maintenance or
maintenance-free “sealed for life” type and is
charged by an alternator which is belt-driven
from the crankshaft pulley. The starter motor
is of the pre-engaged type, incorporating an
integral solenoid. On starting the solenoid
moves the drive pinion into engagement with
the flywheel ring gear before the starter motor
is energised. Once the engine has started, a
one-way clutch prevents the motor armature
being driven by the engine until the pinion
disengages from the flywheel.
The ignition system is responsible for
igniting the air/fuel mixture in each cylinder at
the correct moment in relation to engine
speed and load. A number of different ignition
systems are fitted to models within the
Sierra/P100 range, ranging from a basic
breakerless electronic system to a fully
integrated engine management system
controlling ignition and fuel injection systems.
The ignition system is based on feeding low
tension voltage from the battery to the coil
where it is converted to high tension voltage.
The high tension voltage is powerful enough
to jump the spark plug gap in the cylinders
many times a second under high compression
pressures, providing that the system is in
good condition. The low tension (or primary)
circuit consists of the battery, the lead to the
ignition switch, the lead from the ignition
switch to the low tension coil windings
(terminal + /15) and also to the supply terminal
on the electronic module, and the lead from
the low tension coil windings (terminal -/1) to
the control terminal on the electronic module.
The high tension (or secondary) circuit
consists of the high tension coil windings, the
HT (high tension) lead from the coil to the
distributor cap, the rotor arm, the HT leads to
the spark plugs, and the spark plugs.
The system functions in the following
manner. Current flowing through the low
tension coil windings produces a magnetic
field around the high tension windings. As the
engine rotates, a sensor produces an
electrical impulse which is amplified in the
electronic module and used to switch off the
low tension circuit.
The subsequent collapse of the magnetic
field over the high tension windings produces
high tension voltage which is then fed to the
relevant spark plug via the distributor cap and
rotor arm. The low tension circuit is
automatically switched on again by the
electronic module, to allow the magnetic field
to build up again before the firing of the next
spark plug. The ignition is advanced and
retarded automatically to ensure that thespark occurs at the correct instant in relation
to the engine speed and load.
To improve driveability during warm-up
conditions and to reduce exhaust emission
levels, a vacuum-operated,
temperature-sensitive spark control system is
fitted to certain vehicles.Inductive discharge system
This is the least sophisticated system fitted
to the Sierra/P100 range, and comprises a
breakerless distributor and an electronic
switching/amplifier module in addition to the
coil and spark plugs.
The electrical impulse which is required to
switch off the low tension circuit is generated
by a magnetic trigger coil in the distributor. A
trigger wheel rotates within a magnetic stator,
the magnetic field being provided by a
permanent magnet. The magnetic field across
the two poles (stator arm and trigger wheel) is
dependent on the air gap between the two
poles. When the air gap is at its minimum, the
trigger wheel arm is directly opposite the
stator arm, and this is the trigger point. As the
magnetic flux between the stator arm and
trigger wheel varies, a voltage is induced in
the trigger coil mounted below the trigger
wheel, and this voltage is sensed and then
amplified by the electronic module and used
to switch off the low tension circuit. There is
one trigger wheel arm and one stator arm for
each cylinder (4).
The ignition advance is a function of the
distributor and is controlled both mechanically
and by a vacuum operated system. The
mechanical governor mechanism consists of
two weights which move out from the
distributor shaft as the engine speed rises due
to centrifugal force. As they move outwards,
they rotate the trigger wheel relative to the
distributor shaft and so advance the spark.
The weights are held in position by two light
springs and it is the tension of the springs
which is largely responsible for correct spark
advancement.
The vacuum control consists of a
diaphragm, one side of which is connected
via a small bore hose to the carburettor or
inlet manifold and the other side to the
distributor. Depression in the inlet manifold
and/or carburettor, which varies with engine
speed and throttle position, causes the
diaphragm to move, so moving the baseplate
and advancing or retarding the spark. A fine
degree of control is achieved by a spring in
the diaphragm assembly.
ESC (Electronic Spark Control) system
This system is only fitted to early
“Economy” models, and comprises a “Hall
effect” distributor, and an ESC module, in
addition to the coil and spark plugs.
The electrical impulse which is required to
switch off the low tension circuit is generated
by a sensor in the distributor. A trigger vane
rotates in the gap between a permanent
magnet and the sensor. The trigger vane has
four cut-outs, one for each cylinder. When
one of the trigger vane cut-outs is in line with
the sensor, magnetic flux can pass betweenthe magnet and the sensor. When a trigger
vane segment is in line with the sensor, the
magnetic flux is diverted through the trigger
vane away from the sensor. The sensor
senses the change in magnetic flux and sends
an impulse to the ESC module, which
switches off the low tension circuit.
The ignition advance is a function of the
ESC module and is controlled by vacuum. The
module is connected to the inlet manifold by a
vacuum pipe, and a transducer in the module
translates the vacuum signal into electrical
voltage. From the vacuum signal, the ESC
module determines engine load, and engine
speed is determined from the interval
between impulses supplied by the distributor
sensor. The module has a range of spark
advance settings stored in its memory, and a
suitable setting is selected for the relevant
engine speed and load. The degree of
advance can thus be constantly varied to suit
the prevailing engine speed and load
conditions.
ESC II (Electronic Spark Control II)
system
1.8 and 2.0 litre SOHC carburettor models
This system is a development of the ESC
system described previously in this Section,
but it enables more accurate control of engine
operation due to the inclusion of additional
monitoring features and control outputs.
Vehicles fitted with the ESC II system have an
electric inlet manifold heater which warms the
air/fuel mixture when the engine is cold, thus
reducing the amount of fuel enrichment
required, lowering fuel consumption and
improving driveability when the engine is cold.
The heater is operated by the ESC II module
receiving information on the engine temperature
from an engine coolant temperature sensor
mounted in the inlet manifold.
On 2.0 litre SOHC models, the ESC II
module operates a carburettor stepper motor
to control the engine idle speed. Using
information on engine speed, load,
temperature and throttle position (supplied by
a switch on the carburettor), the module
operates the stepper motor to maintain a
constant idle speed. On models equipped
with automatic transmission and/or air
conditioning, additional inputs are supplied to
the module to allow it to operate the stepper
motor to compensate for the additional engine
load imposed by the automatic
transmission/air conditioning. The ESC II
module also operates a “power hold” relay
which allows the stepper motor to function
briefly after the ignition has been switched off
in order to perform an anti-run-on and
manifold ventilation cycle.
2.0 litre DOHC carburettor models
A development of the ESC II system is used
to control the operation of the engine. The
module receives information from a
crankshaft speed/position sensor (similar to
that described for the ESC Hybrid system),
except that the sensor is activated by a
toothed disc on the rear of the crankshaft,
inside the cylinder block), and an engine
coolant temperature sensor.
1General information and
precautions
Engine electrical systems 5•3
5
Page 5 of 24
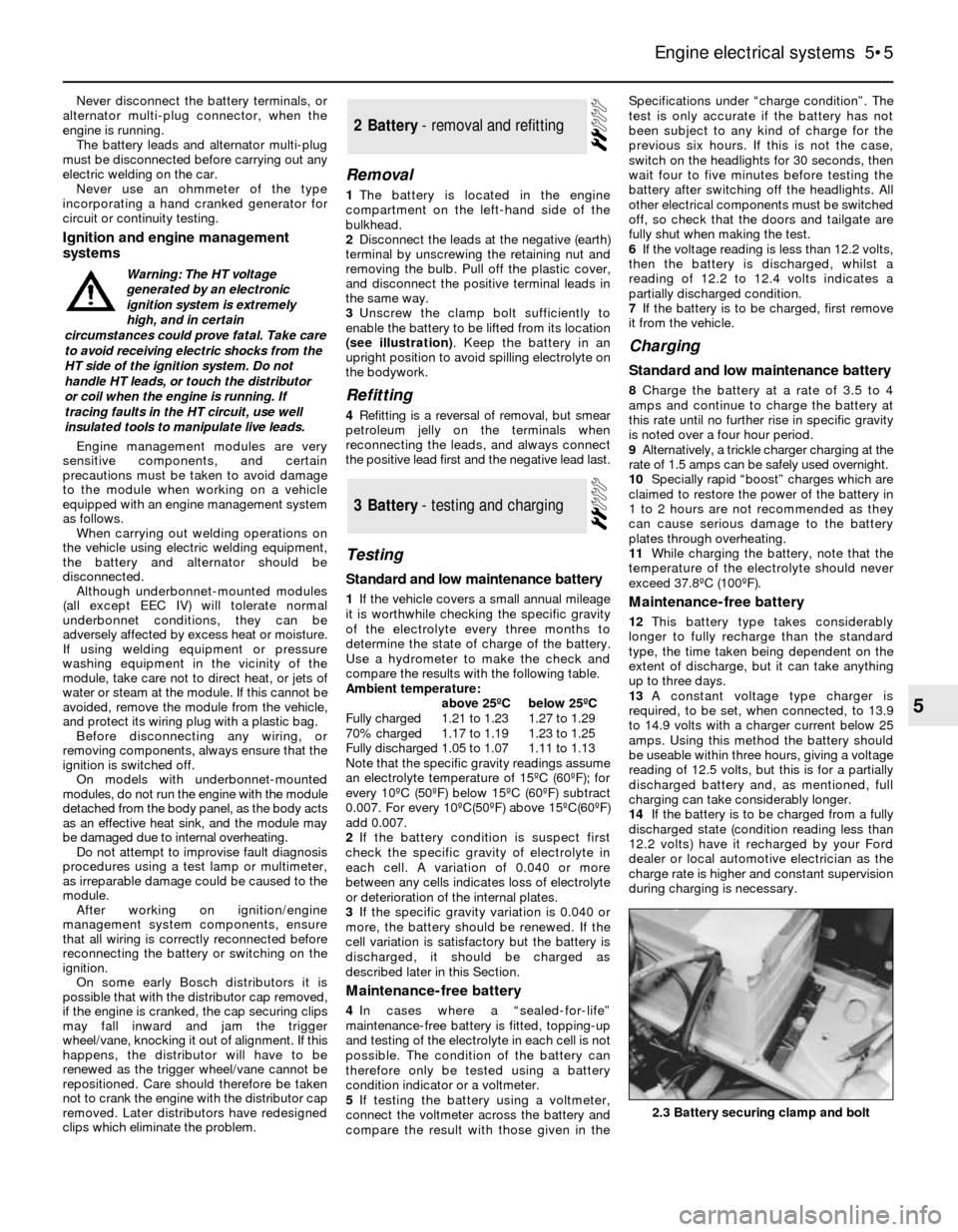
Never disconnect the battery terminals, or
alternator multi-plug connector, when the
engine is running.
The battery leads and alternator multi-plug
must be disconnected before carrying out any
electric welding on the car.
Never use an ohmmeter of the type
incorporating a hand cranked generator for
circuit or continuity testing.
Ignition and engine management
systems
Engine management modules are very
sensitive components, and certain
precautions must be taken to avoid damage
to the module when working on a vehicle
equipped with an engine management system
as follows.
When carrying out welding operations on
the vehicle using electric welding equipment,
the battery and alternator should be
disconnected.
Although underbonnet-mounted modules
(all except EEC IV) will tolerate normal
underbonnet conditions, they can be
adversely affected by excess heat or moisture.
If using welding equipment or pressure
washing equipment in the vicinity of the
module, take care not to direct heat, or jets of
water or steam at the module. If this cannot be
avoided, remove the module from the vehicle,
and protect its wiring plug with a plastic bag.
Before disconnecting any wiring, or
removing components, always ensure that the
ignition is switched off.
On models with underbonnet-mounted
modules, do not run the engine with the module
detached from the body panel, as the body acts
as an effective heat sink, and the module may
be damaged due to internal overheating.
Do not attempt to improvise fault diagnosis
procedures using a test lamp or multimeter,
as irreparable damage could be caused to the
module.
After working on ignition/engine
management system components, ensure
that all wiring is correctly reconnected before
reconnecting the battery or switching on the
ignition.
On some early Bosch distributors it is
possible that with the distributor cap removed,
if the engine is cranked, the cap securing clips
may fall inward and jam the trigger
wheel/vane, knocking it out of alignment. If this
happens, the distributor will have to be
renewed as the trigger wheel/vane cannot be
repositioned. Care should therefore be taken
not to crank the engine with the distributor cap
removed. Later distributors have redesigned
clips which eliminate the problem.
Removal
1The battery is located in the engine
compartment on the left-hand side of the
bulkhead.
2Disconnect the leads at the negative (earth)
terminal by unscrewing the retaining nut and
removing the bulb. Pull off the plastic cover,
and disconnect the positive terminal leads in
the same way.
3Unscrew the clamp bolt sufficiently to
enable the battery to be lifted from its location
(see illustration). Keep the battery in an
upright position to avoid spilling electrolyte on
the bodywork.
Refitting
4Refitting is a reversal of removal, but smear
petroleum jelly on the terminals when
reconnecting the leads, and always connect
the positive lead first and the negative lead last.
Testing
Standard and low maintenance battery
1If the vehicle covers a small annual mileage
it is worthwhile checking the specific gravity
of the electrolyte every three months to
determine the state of charge of the battery.
Use a hydrometer to make the check and
compare the results with the following table.
Ambient temperature:
above 25ºCbelow 25ºC
Fully charged1.21 to 1.231.27 to 1.29
70% charged1.17 to 1.191.23 to 1.25
Fully discharged1.05 to 1.071.11 to 1.13
Note that the specific gravity readings assume
an electrolyte temperature of 15ºC (60ºF); for
every 10ºC (50ºF) below 15ºC (60ºF) subtract
0.007. For every 10ºC(50ºF) above 15ºC(60ºF)
add 0.007.
2If the battery condition is suspect first
check the specific gravity of electrolyte in
each cell. A variation of 0.040 or more
between any cells indicates loss of electrolyte
or deterioration of the internal plates.
3If the specific gravity variation is 0.040 or
more, the battery should be renewed. If the
cell variation is satisfactory but the battery is
discharged, it should be charged as
described later in this Section.
Maintenance-free battery
4In cases where a “sealed-for-life”
maintenance-free battery is fitted, topping-up
and testing of the electrolyte in each cell is not
possible. The condition of the battery can
therefore only be tested using a battery
condition indicator or a voltmeter.
5If testing the battery using a voltmeter,
connect the voltmeter across the battery and
compare the result with those given in theSpecifications under “charge condition”. The
test is only accurate if the battery has not
been subject to any kind of charge for the
previous six hours. If this is not the case,
switch on the headlights for 30 seconds, then
wait four to five minutes before testing the
battery after switching off the headlights. All
other electrical components must be switched
off, so check that the doors and tailgate are
fully shut when making the test.
6If the voltage reading is less than 12.2 volts,
then the battery is discharged, whilst a
reading of 12.2 to 12.4 volts indicates a
partially discharged condition.
7If the battery is to be charged, first remove
it from the vehicle.
Charging
Standard and low maintenance battery
8Charge the battery at a rate of 3.5 to 4
amps and continue to charge the battery at
this rate until no further rise in specific gravity
is noted over a four hour period.
9Alternatively, a trickle charger charging at the
rate of 1.5 amps can be safely used overnight.
10Specially rapid “boost” charges which are
claimed to restore the power of the battery in
1 to 2 hours are not recommended as they
can cause serious damage to the battery
plates through overheating.
11While charging the battery, note that the
temperature of the electrolyte should never
exceed 37.8ºC (100ºF).
Maintenance-free battery
12This battery type takes considerably
longer to fully recharge than the standard
type, the time taken being dependent on the
extent of discharge, but it can take anything
up to three days.
13A constant voltage type charger is
required, to be set, when connected, to 13.9
to 14.9 volts with a charger current below 25
amps. Using this method the battery should
be useable within three hours, giving a voltage
reading of 12.5 volts, but this is for a partially
discharged battery and, as mentioned, full
charging can take considerably longer.
14If the battery is to be charged from a fully
discharged state (condition reading less than
12.2 volts) have it recharged by your Ford
dealer or local automotive electrician as the
charge rate is higher and constant supervision
during charging is necessary.
3Battery - testing and charging
2Battery - removal and refitting
Engine electrical systems 5•5
5
2.3 Battery securing clamp and bolt
Warning: The HT voltage
generated by an electronic
ignition system is extremely
high, and in certain
circumstances could prove fatal. Take care
to avoid receiving electric shocks from the
HT side of the ignition system. Do not
handle HT leads, or touch the distributor
or coil when the engine is running. If
tracing faults in the HT circuit, use well
insulated tools to manipulate live leads.
Page 6 of 24
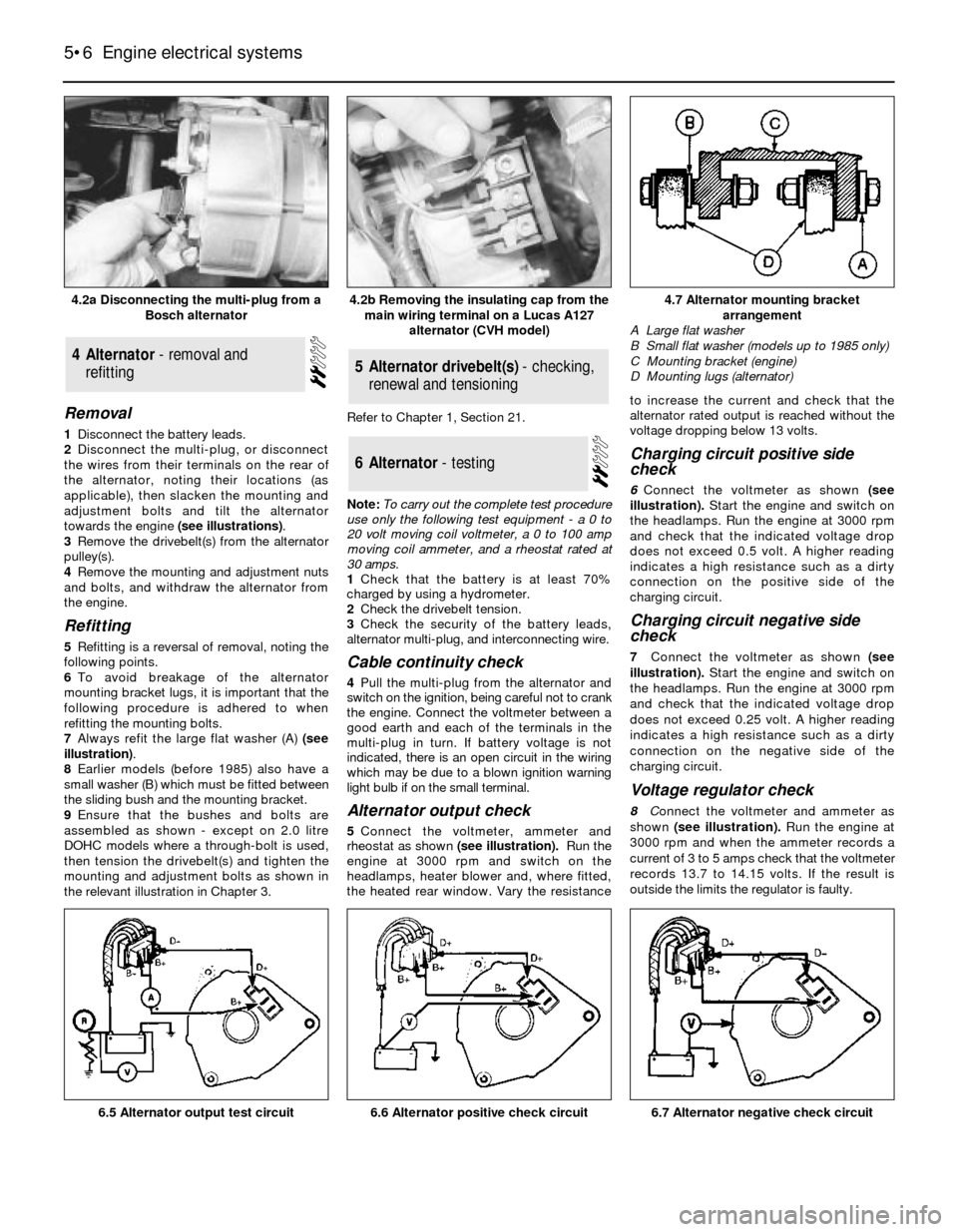
Removal
1Disconnect the battery leads.
2Disconnect the multi-plug, or disconnect
the wires from their terminals on the rear of
the alternator, noting their locations (as
applicable), then slacken the mounting and
adjustment bolts and tilt the alternator
towards the engine (see illustrations).
3Remove the drivebelt(s) from the alternator
pulley(s).
4Remove the mounting and adjustment nuts
and bolts, and withdraw the alternator from
the engine.
Refitting
5Refitting is a reversal of removal, noting the
following points.
6To avoid breakage of the alternator
mounting bracket lugs, it is important that the
following procedure is adhered to when
refitting the mounting bolts.
7Always refit the large flat washer (A) (see
illustration).
8Earlier models (before 1985) also have a
small washer (B) which must be fitted between
the sliding bush and the mounting bracket.
9Ensure that the bushes and bolts are
assembled as shown - except on 2.0 litre
DOHC models where a through-bolt is used,
then tension the drivebelt(s) and tighten the
mounting and adjustment bolts as shown in
the relevant illustration in Chapter 3.Refer to Chapter 1, Section 21.
Note: To carry out the complete test procedure
use only the following test equipment - a 0 to
20 volt moving coil voltmeter, a 0 to 100 amp
moving coil ammeter, and a rheostat rated at
30 amps.
1Check that the battery is at least 70%
charged by using a hydrometer.
2Check the drivebelt tension.
3Check the security of the battery leads,
alternator multi-plug, and interconnecting wire.
Cable continuity check
4Pull the multi-plug from the alternator and
switch on the ignition, being careful not to crank
the engine. Connect the voltmeter between a
good earth and each of the terminals in the
multi-plug in turn. If battery voltage is not
indicated, there is an open circuit in the wiring
which may be due to a blown ignition warning
light bulb if on the small terminal.
Alternator output check
5Connect the voltmeter, ammeter and
rheostat as shown (see illustration).Run the
engine at 3000 rpm and switch on the
headlamps, heater blower and, where fitted,
the heated rear window. Vary the resistanceto increase the current and check that the
alternator rated output is reached without the
voltage dropping below 13 volts.
Charging circuit positive side
check
6Connect the voltmeter as shown (see
illustration).Start the engine and switch on
the headlamps. Run the engine at 3000 rpm
and check that the indicated voltage drop
does not exceed 0.5 volt. A higher reading
indicates a high resistance such as a dirty
connection on the positive side of the
charging circuit.
Charging circuit negative side
check
7Connect the voltmeter as shown (see
illustration).Start the engine and switch on
the headlamps. Run the engine at 3000 rpm
and check that the indicated voltage drop
does not exceed 0.25 volt. A higher reading
indicates a high resistance such as a dirty
connection on the negative side of the
charging circuit.
Voltage regulator check
8Connect the voltmeter and ammeter as
shown(see illustration).Run the engine at
3000 rpm and when the ammeter records a
current of 3 to 5 amps check that the voltmeter
records 13.7 to 14.15 volts. If the result is
outside the limits the regulator is faulty.
6Alternator - testing
5Alternator drivebelt(s) - checking,
renewal and tensioning4Alternator - removal and
refitting
5•6Engine electrical systems
4.2a Disconnecting the multi-plug from a
Bosch alternator4.7 Alternator mounting bracket
arrangement
A Large flat washer
B Small flat washer (models up to 1985 only)
C Mounting bracket (engine)
D Mounting lugs (alternator)
6.7 Alternator negative check circuit6.6 Alternator positive check circuit6.5 Alternator output test circuit
4.2b Removing the insulating cap from the
main wiring terminal on a Lucas A127
alternator (CVH model)
Page 8 of 24
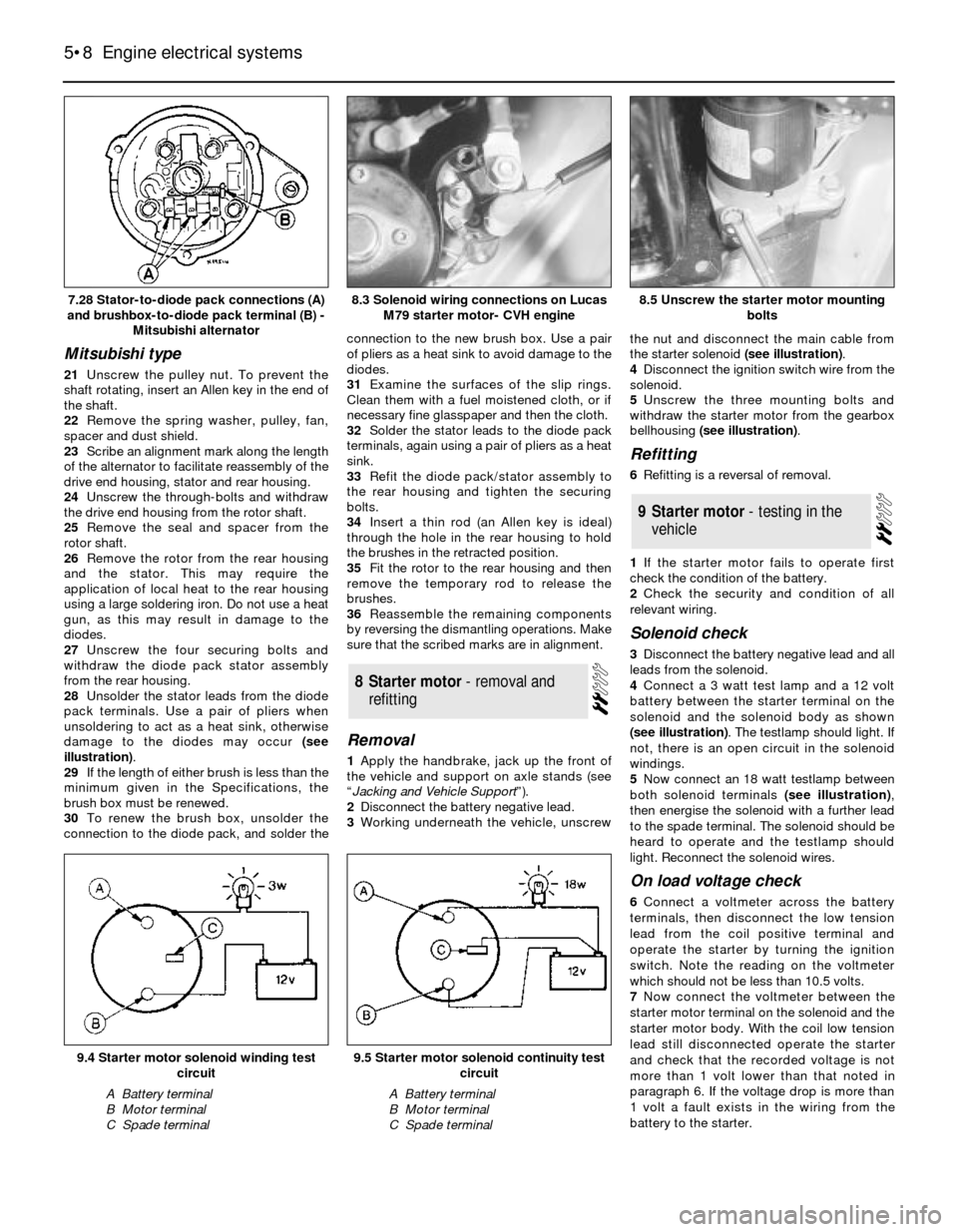
Mitsubishi type
21Unscrew the pulley nut. To prevent the
shaft rotating, insert an Allen key in the end of
the shaft.
22Remove the spring washer, pulley, fan,
spacer and dust shield.
23Scribe an alignment mark along the length
of the alternator to facilitate reassembly of the
drive end housing, stator and rear housing.
24Unscrew the through-bolts and withdraw
the drive end housing from the rotor shaft.
25Remove the seal and spacer from the
rotor shaft.
26Remove the rotor from the rear housing
and the stator. This may require the
application of local heat to the rear housing
using a large soldering iron. Do not use a heat
gun, as this may result in damage to the
diodes.
27Unscrew the four securing bolts and
withdraw the diode pack stator assembly
from the rear housing.
28Unsolder the stator leads from the diode
pack terminals. Use a pair of pliers when
unsoldering to act as a heat sink, otherwise
damage to the diodes may occur (see
illustration).
29If the length of either brush is less than the
minimum given in the Specifications, the
brush box must be renewed.
30To renew the brush box, unsolder the
connection to the diode pack, and solder theconnection to the new brush box. Use a pair
of pliers as a heat sink to avoid damage to the
diodes.
31Examine the surfaces of the slip rings.
Clean them with a fuel moistened cloth, or if
necessary fine glasspaper and then the cloth.
32Solder the stator leads to the diode pack
terminals, again using a pair of pliers as a heat
sink.
33Refit the diode pack/stator assembly to
the rear housing and tighten the securing
bolts.
34Insert a thin rod (an Allen key is ideal)
through the hole in the rear housing to hold
the brushes in the retracted position.
35Fit the rotor to the rear housing and then
remove the temporary rod to release the
brushes.
36Reassemble the remaining components
by reversing the dismantling operations. Make
sure that the scribed marks are in alignment.
Removal
1Apply the handbrake, jack up the front of
the vehicle and support on axle stands (see
“Jacking and Vehicle Support”).
2Disconnect the battery negative lead.
3Working underneath the vehicle, unscrewthe nut and disconnect the main cable from
the starter solenoid (see illustration).
4Disconnect the ignition switch wire from the
solenoid.
5Unscrew the three mounting bolts and
withdraw the starter motor from the gearbox
bellhousing (see illustration).
Refitting
6Refitting is a reversal of removal.
1If the starter motor fails to operate first
check the condition of the battery.
2Check the security and condition of all
relevant wiring.
Solenoid check
3Disconnect the battery negative lead and all
leads from the solenoid.
4Connect a 3 watt test lamp and a 12 volt
battery between the starter terminal on the
solenoid and the solenoid body as shown
(see illustration). The testlamp should light. If
not, there is an open circuit in the solenoid
windings.
5Now connect an 18 watt testlamp between
both solenoid terminals (see illustration),
then energise the solenoid with a further lead
to the spade terminal. The solenoid should be
heard to operate and the testlamp should
light. Reconnect the solenoid wires.
On load voltage check
6Connect a voltmeter across the battery
terminals, then disconnect the low tension
lead from the coil positive terminal and
operate the starter by turning the ignition
switch. Note the reading on the voltmeter
which should not be less than 10.5 volts.
7Now connect the voltmeter between the
starter motor terminal on the solenoid and the
starter motor body. With the coil low tension
lead still disconnected operate the starter
and check that the recorded voltage is not
more than 1 volt lower than that noted in
paragraph 6. If the voltage drop is more than
1 volt a fault exists in the wiring from the
battery to the starter.
9Starter motor - testing in the
vehicle
8Starter motor - removal and
refitting
5•8Engine electrical systems
7.28 Stator-to-diode pack connections (A)
and brushbox-to-diode pack terminal (B) -
Mitsubishi alternator8.5 Unscrew the starter motor mounting
bolts
9.5 Starter motor solenoid continuity test
circuit
A Battery terminal
B Motor terminal
C Spade terminal
9.4 Starter motor solenoid winding test
circuit
A Battery terminal
B Motor terminal
C Spade terminal
8.3 Solenoid wiring connections on Lucas
M79 starter motor- CVH engine
Page 12 of 24
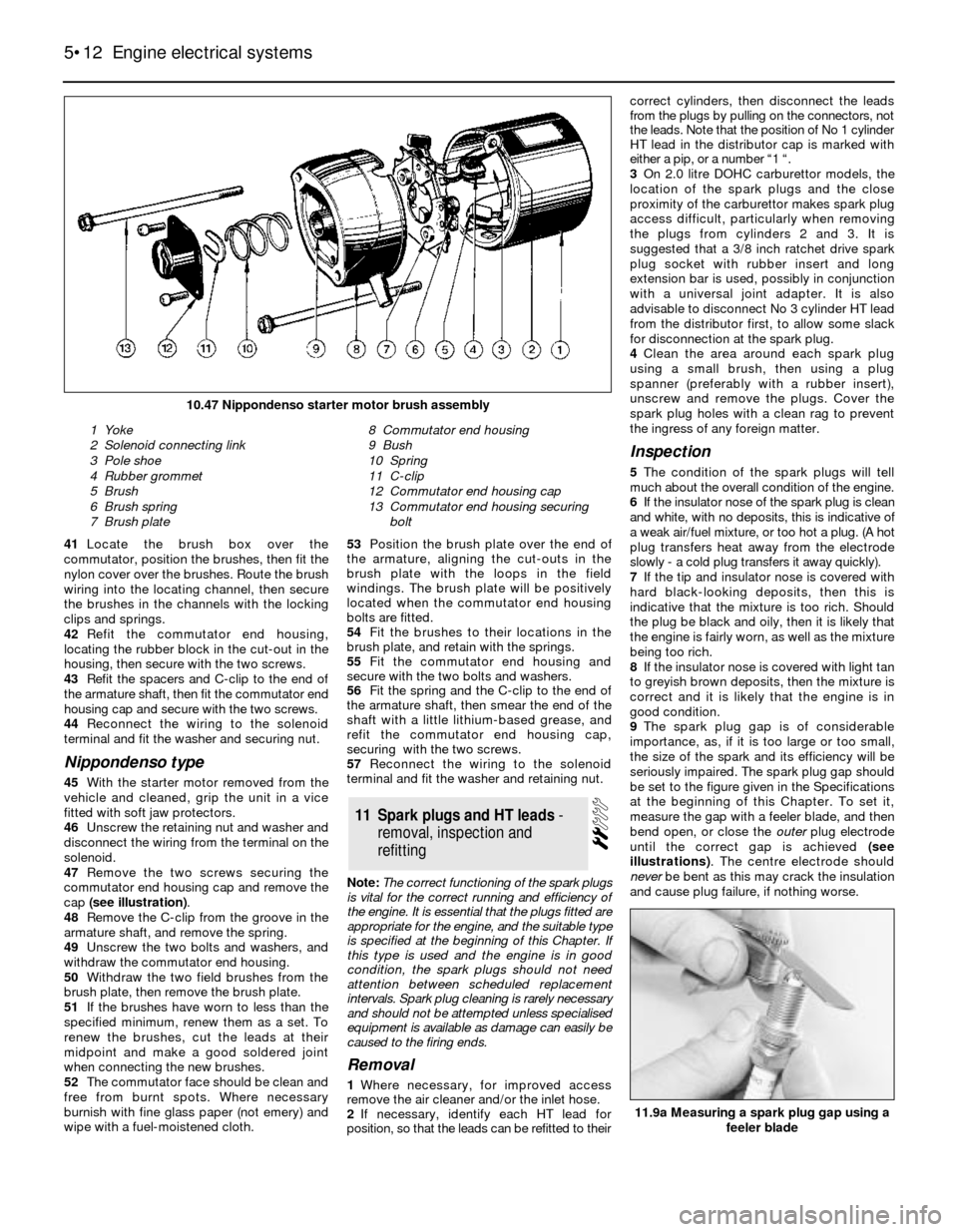
41Locate the brush box over the
commutator, position the brushes, then fit the
nylon cover over the brushes. Route the brush
wiring into the locating channel, then secure
the brushes in the channels with the locking
clips and springs.
42Refit the commutator end housing,
locating the rubber block in the cut-out in the
housing, then secure with the two screws.
43Refit the spacers and C-clip to the end of
the armature shaft, then fit the commutator end
housing cap and secure with the two screws.
44Reconnect the wiring to the solenoid
terminal and fit the washer and securing nut.
Nippondenso type
45With the starter motor removed from the
vehicle and cleaned, grip the unit in a vice
fitted with soft jaw protectors.
46Unscrew the retaining nut and washer and
disconnect the wiring from the terminal on the
solenoid.
47Remove the two screws securing the
commutator end housing cap and remove the
cap (see illustration).
48Remove the C-clip from the groove in the
armature shaft, and remove the spring.
49Unscrew the two bolts and washers, and
withdraw the commutator end housing.
50Withdraw the two field brushes from the
brush plate, then remove the brush plate.
51If the brushes have worn to less than the
specified minimum, renew them as a set. To
renew the brushes, cut the leads at their
midpoint and make a good soldered joint
when connecting the new brushes.
52The commutator face should be clean and
free from burnt spots. Where necessary
burnish with fine glass paper (not emery) and
wipe with a fuel-moistened cloth. 53Position the brush plate over the end of
the armature, aligning the cut-outs in the
brush plate with the loops in the field
windings. The brush plate will be positively
located when the commutator end housing
bolts are fitted.
54Fit the brushes to their locations in the
brush plate, and retain with the springs.
55Fit the commutator end housing and
secure with the two bolts and washers.
56Fit the spring and the C-clip to the end of
the armature shaft, then smear the end of the
shaft with a little lithium-based grease, and
refit the commutator end housing cap,
securing with the two screws.
57Reconnect the wiring to the solenoid
terminal and fit the washer and retaining nut.
Note: The correct functioning of the spark plugs
is vital for the correct running and efficiency of
the engine. It is essential that the plugs fitted are
appropriate for the engine, and the suitable type
is specified at the beginning of this Chapter. If
this type is used and the engine is in good
condition, the spark plugs should not need
attention between scheduled replacement
intervals. Spark plug cleaning is rarely necessary
and should not be attempted unless specialised
equipment is available as damage can easily be
caused to the firing ends.
Removal
1Where necessary, for improved access
remove the air cleaner and/or the inlet hose.
2If necessary, identify each HT lead for
position, so that the leads can be refitted to theircorrect cylinders, then disconnect the leads
from the plugs by pulling on the connectors, not
the leads. Note that the position of No 1 cylinder
HT lead in the distributor cap is marked with
either a pip, or a number “1 “.
3On 2.0 litre DOHC carburettor models, the
location of the spark plugs and the close
proximity of the carburettor makes spark plug
access difficult, particularly when removing
the plugs from cylinders 2 and 3. It is
suggested that a 3/8 inch ratchet drive spark
plug socket with rubber insert and long
extension bar is used, possibly in conjunction
with a universal joint adapter. It is also
advisable to disconnect No 3 cylinder HT lead
from the distributor first, to allow some slack
for disconnection at the spark plug.
4Clean the area around each spark plug
using a small brush, then using a plug
spanner (preferably with a rubber insert),
unscrew and remove the plugs. Cover the
spark plug holes with a clean rag to prevent
the ingress of any foreign matter.
Inspection
5The condition of the spark plugs will tell
much about the overall condition of the engine.
6If the insulator nose of the spark plug is clean
and white, with no deposits, this is indicative of
a weak air/fuel mixture, or too hot a plug. (A hot
plug transfers heat away from the electrode
slowly - a cold plug transfers it away quickly).
7If the tip and insulator nose is covered with
hard black-looking deposits, then this is
indicative that the mixture is too rich. Should
the plug be black and oily, then it is likely that
the engine is fairly worn, as well as the mixture
being too rich.
8If the insulator nose is covered with light tan
to greyish brown deposits, then the mixture is
correct and it is likely that the engine is in
good condition.
9The spark plug gap is of considerable
importance, as, if it is too large or too small,
the size of the spark and its efficiency will be
seriously impaired. The spark plug gap should
be set to the figure given in the Specifications
at the beginning of this Chapter. To set it,
measure the gap with a feeler blade, and then
bend open, or close the outer plug electrode
until the correct gap is achieved (see
illustrations). The centre electrode should
never be bent as this may crack the insulation
and cause plug failure, if nothing worse.
11Spark plugs and HT leads -
removal, inspection and
refitting
5•12Engine electrical systems
10.47 Nippondenso starter motor brush assembly
1 Yoke
2 Solenoid connecting link
3 Pole shoe
4 Rubber grommet
5 Brush
6 Brush spring
7 Brush plate8 Commutator end housing
9 Bush
10 Spring
11 C-clip
12 Commutator end housing cap
13 Commutator end housing securing
bolt
11.9a Measuring a spark plug gap using a
feeler blade
Page 16 of 24
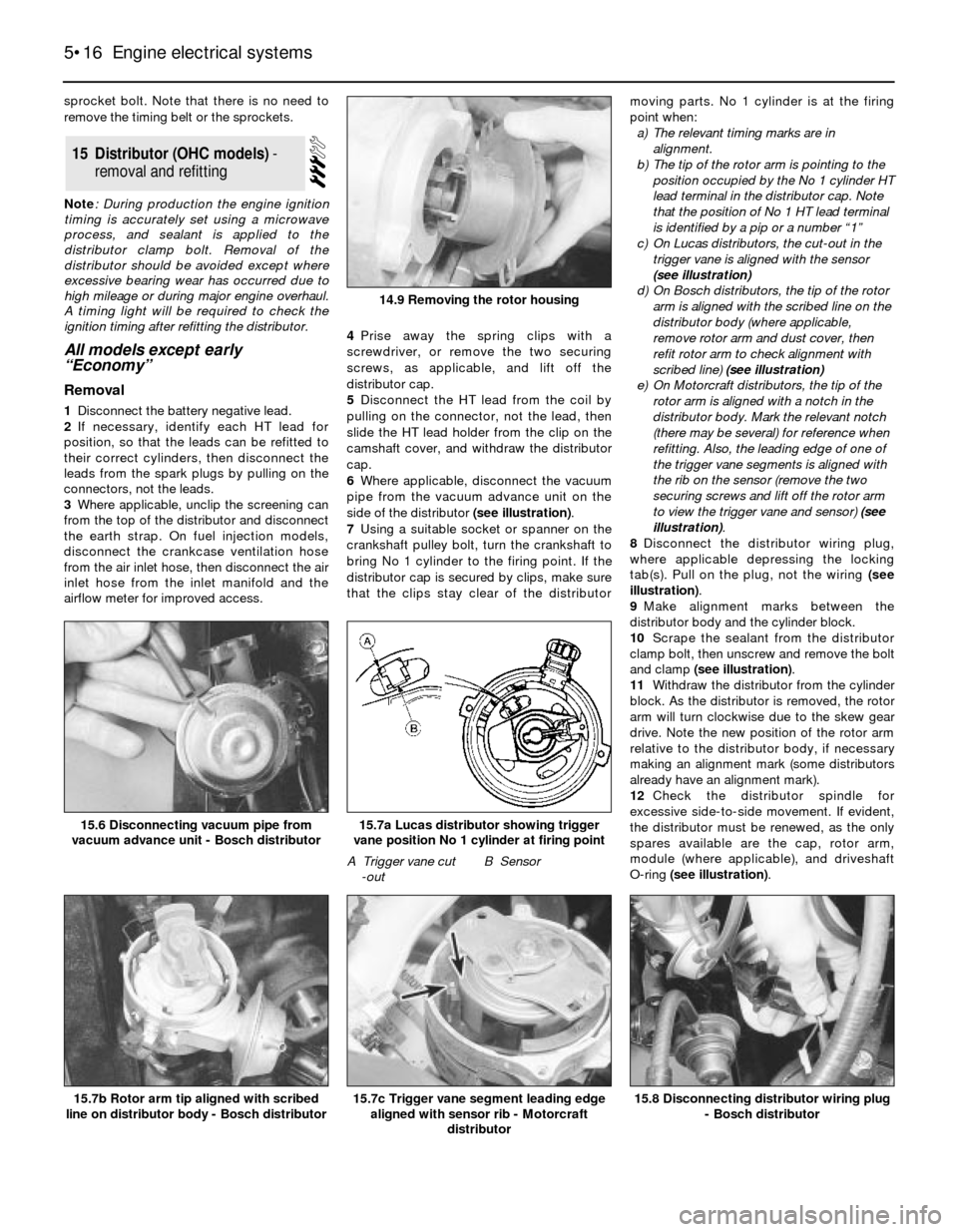
sprocket bolt. Note that there is no need to
remove the timing belt or the sprockets.
Note: During production the engine ignition
timing is accurately set using a microwave
process, and sealant is applied to the
distributor clamp bolt. Removal of the
distributor should be avoided except where
excessive bearing wear has occurred due to
high mileage or during major engine overhaul.
A timing light will be required to check the
ignition timing after refitting the distributor.
All models except early
“Economy”
Removal
1Disconnect the battery negative lead.
2If necessary, identify each HT lead for
position, so that the leads can be refitted to
their correct cylinders, then disconnect the
leads from the spark plugs by pulling on the
connectors, not the leads.
3Where applicable, unclip the screening can
from the top of the distributor and disconnect
the earth strap. On fuel injection models,
disconnect the crankcase ventilation hose
from the air inlet hose, then disconnect the air
inlet hose from the inlet manifold and the
airflow meter for improved access.4Prise away the spring clips with a
screwdriver, or remove the two securing
screws, as applicable, and lift off the
distributor cap.
5Disconnect the HT lead from the coil by
pulling on the connector, not the lead, then
slide the HT lead holder from the clip on the
camshaft cover, and withdraw the distributor
cap.
6Where applicable, disconnect the vacuum
pipe from the vacuum advance unit on the
side of the distributor (see illustration).
7Using a suitable socket or spanner on the
crankshaft pulley bolt, turn the crankshaft to
bring No 1 cylinder to the firing point. If the
distributor cap is secured by clips, make sure
that the clips stay clear of the distributormoving parts. No 1 cylinder is at the firing
point when:
a)The relevant timing marks are in
alignment.
b)The tip of the rotor arm is pointing to the
position occupied by the No 1 cylinder HT
lead terminal in the distributor cap. Note
that the position of No 1 HT lead terminal
is identified by a pip or a number “1”
c)On Lucas distributors, the cut-out in the
trigger vane is aligned with the sensor
(see illustration)
d)On Bosch distributors, the tip of the rotor
arm is aligned with the scribed line on the
distributor body (where applicable,
remove rotor arm and dust cover, then
refit rotor arm to check alignment with
scribed line) (see illustration)
e)On Motorcraft distributors, the tip of the
rotor arm is aligned with a notch in the
distributor body. Mark the relevant notch
(there may be several) for reference when
refitting. Also, the leading edge of one of
the trigger vane segments is aligned with
the rib on the sensor (remove the two
securing screws and lift off the rotor arm
to view the trigger vane and sensor) (see
illustration).
8Disconnect the distributor wiring plug,
where applicable depressing the locking
tab(s). Pull on the plug, not the wiring (see
illustration).
9Make alignment marks between the
distributor body and the cylinder block.
10Scrape the sealant from the distributor
clamp bolt, then unscrew and remove the bolt
and clamp (see illustration).
11Withdraw the distributor from the cylinder
block. As the distributor is removed, the rotor
arm will turn clockwise due to the skew gear
drive. Note the new position of the rotor arm
relative to the distributor body, if necessary
making an alignment mark (some distributors
already have an alignment mark).
12Check the distributor spindle for
excessive side-to-side movement. If evident,
the distributor must be renewed, as the only
spares available are the cap, rotor arm,
module (where applicable), and driveshaft
O-ring (see illustration).
15Distributor (OHC models) -
removal and refitting
5•16Engine electrical systems
14.9 Removing the rotor housing
15.7a Lucas distributor showing trigger
vane position No 1 cylinder at firing point
A Trigger vane cut
-outB Sensor
15.8 Disconnecting distributor wiring plug
- Bosch distributor15.7c Trigger vane segment leading edge
aligned with sensor rib - Motorcraft
distributor15.7b Rotor arm tip aligned with scribed
line on distributor body - Bosch distributor
15.6 Disconnecting vacuum pipe from
vacuum advance unit - Bosch distributor
Page 17 of 24
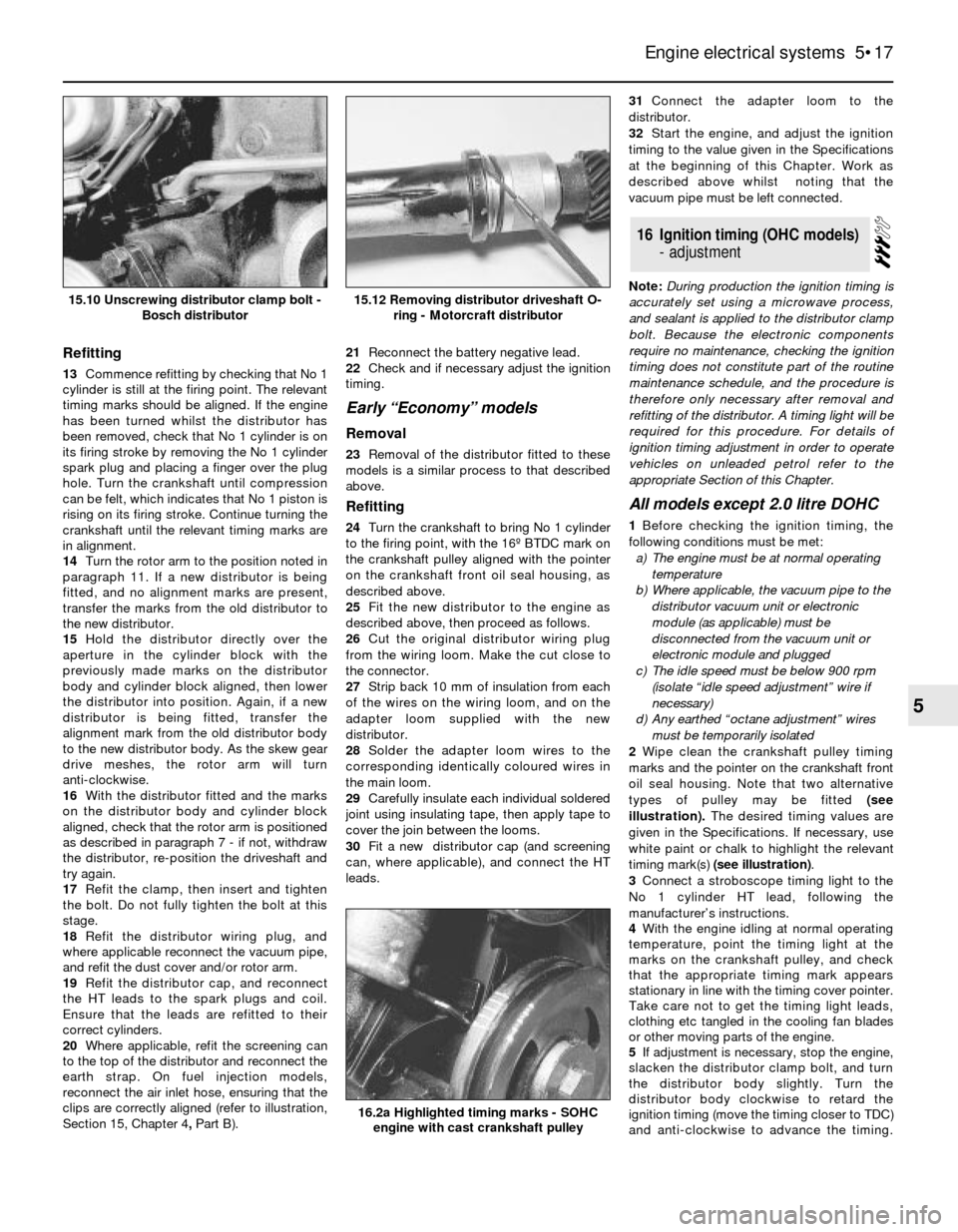
Refitting
13Commence refitting by checking that No 1
cylinder is still at the firing point. The relevant
timing marks should be aligned. If the engine
has been turned whilst the distributor has
been removed, check that No 1 cylinder is on
its firing stroke by removing the No 1 cylinder
spark plug and placing a finger over the plug
hole. Turn the crankshaft until compression
can be felt, which indicates that No 1 piston is
rising on its firing stroke. Continue turning the
crankshaft until the relevant timing marks are
in alignment.
14Turn the rotor arm to the position noted in
paragraph 11. If a new distributor is being
fitted, and no alignment marks are present,
transfer the marks from the old distributor to
the new distributor.
15Hold the distributor directly over the
aperture in the cylinder block with the
previously made marks on the distributor
body and cylinder block aligned, then lower
the distributor into position. Again, if a new
distributor is being fitted, transfer the
alignment mark from the old distributor body
to the new distributor body. As the skew gear
drive meshes, the rotor arm will turn
anti-clockwise.
16With the distributor fitted and the marks
on the distributor body and cylinder block
aligned, check that the rotor arm is positioned
as described in paragraph 7 -if not, withdraw
the distributor, re-position the driveshaft and
try again.
17Refit the clamp, then insert and tighten
the bolt. Do not fully tighten the bolt at this
stage.
18Refit the distributor wiring plug, and
where applicable reconnect the vacuum pipe,
and refit the dust cover and/or rotor arm.
19Refit the distributor cap, and reconnect
the HT leads to the spark plugs and coil.
Ensure that the leads are refitted to their
correct cylinders.
20Where applicable, refit the screening can
to the top of the distributor and reconnect the
earth strap. On fuel injection models,
reconnect the air inlet hose, ensuring that the
clips are correctly aligned (refer to illustration,
Section 15, Chapter 4, PartB).21Reconnect the battery negative lead.
22Check and if necessary adjust the ignition
timing.
Early “Economy” models
Removal
23Removal of the distributor fitted to these
models is a similar process to that described
above.
Refitting
24Turn the crankshaft to bring No 1 cylinder
to the firing point, with the 16º BTDC mark on
the crankshaft pulley aligned with the pointer
on the crankshaft front oil seal housing, as
described above.
25Fit the new distributor to the engine as
described above, then proceed as follows.
26Cut the original distributor wiring plug
from the wiring loom. Make the cut close to
the connector.
27Strip back 10 mm of insulation from each
of the wires on the wiring loom, and on the
adapter loom supplied with the new
distributor.
28Solder the adapter loom wires to the
corresponding identically coloured wires in
the main loom.
29Carefully insulate each individual soldered
joint using insulating tape, then apply tape to
cover the join between the looms.
30Fit a new distributor cap (and screening
can, where applicable), and connect the HT
leads.31Connect the adapter loom to the
distributor.
32Start the engine, and adjust the ignition
timing to the value given in the Specifications
at the beginning of this Chapter. Work as
described above whilst noting that the
vacuum pipe must be left connected.
Note: During production the ignition timing is
accurately set using a microwave process,
and sealant is applied to the distributor clamp
bolt. Because the electronic components
require no maintenance, checking the ignition
timing does not constitute part of the routine
maintenance schedule, and the procedure is
therefore only necessary after removal and
refitting of the distributor. A timing light will be
required for this procedure. For details of
ignition timing adjustment in order to operate
vehicles on unleaded petrol refer to the
appropriate Section of this Chapter.
All models except 2.0 litre DOHC
1Before checking the ignition timing, the
following conditions must be met:
a)The engine must be at normal operating
temperature
b)Where applicable, the vacuum pipe to the
distributor vacuum unit or electronic
module (as applicable) must be
disconnected from the vacuum unit or
electronic module and plugged
c)The idle speed must be below 900 rpm
(isolate “idle speed adjustment” wire if
necessary)
d)Any earthed “octane adjustment” wires
must be temporarily isolated
2Wipe clean the crankshaft pulley timing
marks and the pointer on the crankshaft front
oil seal housing. Note that two alternative
types of pulley may be fitted (see
illustration).The desired timing values are
given in the Specifications. If necessary, use
white paint or chalk to highlight the relevant
timing mark(s) (see illustration).
3Connect a stroboscope timing light to the
No 1 cylinder HT lead, following the
manufacturer’s instructions.
4With the engine idling at normal operating
temperature, point the timing light at the
marks on the crankshaft pulley, and check
that the appropriate timing mark appears
stationary in line with the timing cover pointer.
Take care not to get the timing light leads,
clothing etc tangled in the cooling fan blades
or other moving parts of the engine.
5If adjustment is necessary, stop the engine,
slacken the distributor clamp bolt, and turn
the distributor body slightly. Turn the
distributor body clockwise to retard the
ignition timing (move the timing closer to TDC)
and anti-clockwise to advance the timing.
16Ignition timing (OHC models)
- adjustment
Engine electrical systems 5•17
5
15.12 Removing distributor driveshaft O-
ring - Motorcraft distributor15.10 Unscrewing distributor clamp bolt -
Bosch distributor
16.2a Highlighted timing marks - SOHC
engine with cast crankshaft pulley
Page 18 of 24
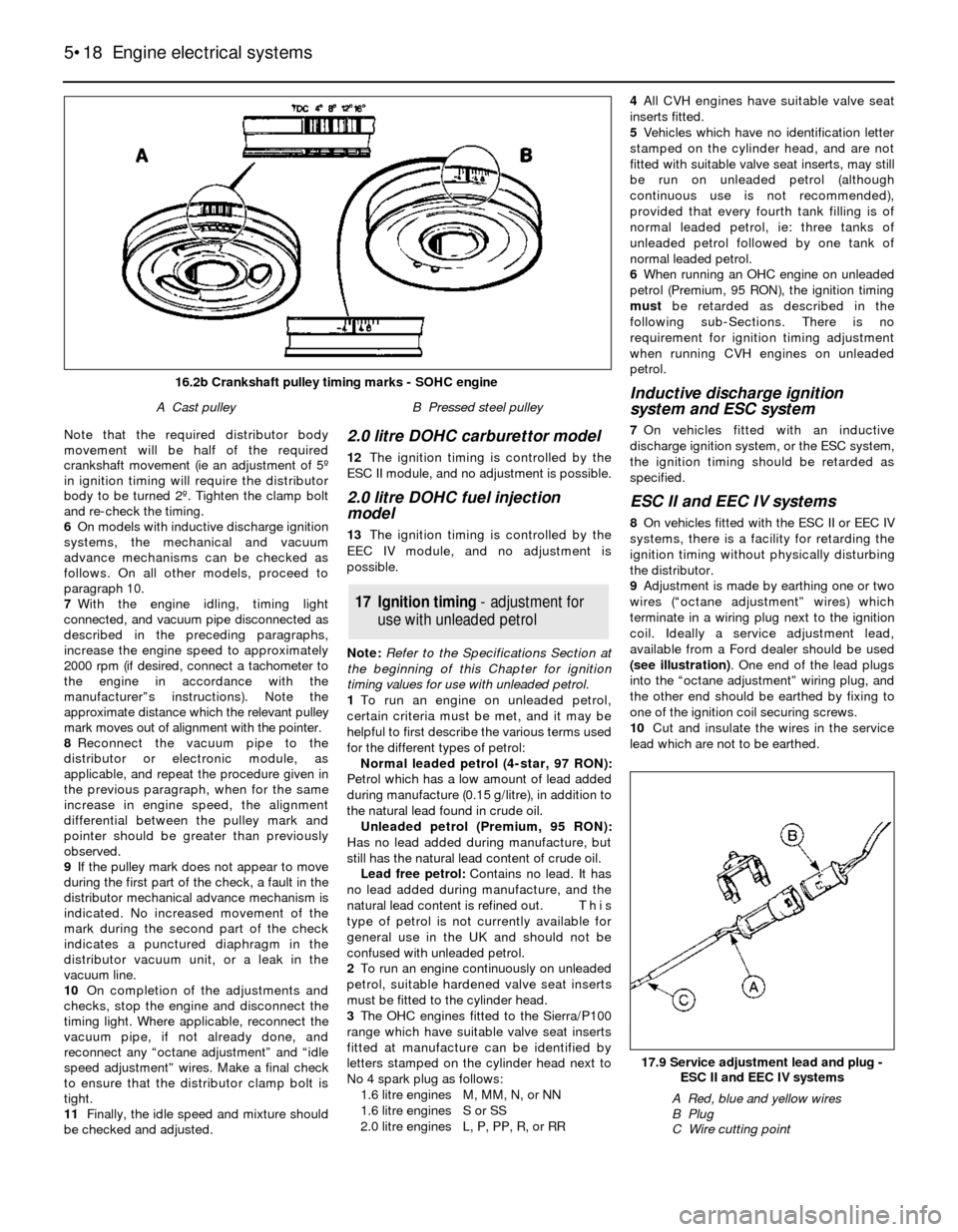
Note that the required distributor body
movement will be half of the required
crankshaft movement (ie an adjustment of 5º
in ignition timing will require the distributor
body to be turned 2º. Tighten the clamp bolt
and re-check the timing.
6On models with inductive discharge ignition
systems, the mechanical and vacuum
advance mechanisms can be checked as
follows. On all other models, proceed to
paragraph 10.
7With the engine idling, timing light
connected, and vacuum pipe disconnected as
described in the preceding paragraphs,
increase the engine speed to approximately
2000 rpm (if desired, connect a tachometer to
the engine in accordance with the
manufacturer”s instructions). Note the
approximate distance which the relevant pulley
mark moves out of alignment with the pointer.
8Reconnect the vacuum pipe to the
distributor or electronic module, as
applicable, and repeat the procedure given in
the previous paragraph, when for the same
increase in engine speed, the alignment
differential between the pulley mark and
pointer should be greater than previously
observed.
9If the pulley mark does not appear to move
during the first part of the check, a fault in the
distributor mechanical advance mechanism is
indicated. No increased movement of the
mark during the second part of the check
indicates a punctured diaphragm in the
distributor vacuum unit, or a leak in the
vacuum line.
10On completion of the adjustments and
checks, stop the engine and disconnect the
timing light. Where applicable, reconnect the
vacuum pipe, if not already done, and
reconnect any “octane adjustment” and “idle
speed adjustment” wires. Make a final check
to ensure that the distributor clamp bolt is
tight.
11Finally, the idle speed and mixture should
be checked and adjusted.2.0 litre DOHC carburettor model
12The ignition timing is controlled by the
ESC II module, and no adjustment is possible.
2.0 litre DOHC fuel injection
model
13The ignition timing is controlled by the
EEC IV module, and no adjustment is
possible.
Note: Refer to the Specifications Section at
the beginning of this Chapter for ignition
timing values for use with unleaded petrol.
1To run an engine on unleaded petrol,
certain criteria must be met, and it may be
helpful to first describe the various terms used
for the different types of petrol:
Normal leaded petrol (4-star, 97 RON):
Petrol which has a low amount of lead added
during manufacture (0.15 g/litre), in addition to
the natural lead found in crude oil.
Unleaded petrol (Premium, 95 RON):
Has no lead added during manufacture, but
still has the natural lead content of crude oil.
Lead free petrol: Contains no lead. It has
no lead added during manufacture, and the
natural lead content is refined out. This
type of petrol is not currently available for
general use in the UK and should not be
confused with unleaded petrol.
2To run an engine continuously on unleaded
petrol, suitable hardened valve seat inserts
must be fitted to the cylinder head.
3The OHC engines fitted to the Sierra/P100
range which have suitable valve seat inserts
fitted at manufacture can be identified by
letters stamped on the cylinder head next to
No 4 spark plug as follows:
1.6 litre enginesM, MM, N, or NN
1.6 litre enginesS or SS
2.0 litre enginesL, P, PP, R, or RR4All CVH engines have suitable valve seat
inserts fitted.
5Vehicles which have no identification letter
stamped on the cylinder head, and are not
fitted with suitable valve seat inserts, may still
be run on unleaded petrol (although
continuous use is not recommended),
provided that every fourth tank filling is of
normal leaded petrol, ie: three tanks of
unleaded petrol followed by one tank of
normal leaded petrol.
6When running an OHC engine on unleaded
petrol (Premium, 95 RON), the ignition timing
must be retarded as described in the
following sub-Sections. There is no
requirement for ignition timing adjustment
when running CVH engines on unleaded
petrol.
Inductive discharge ignition
system and ESC system
7On vehicles fitted with an inductive
discharge ignition system, or the ESC system,
the ignition timing should be retarded as
specified.
ESC II and EEC IV systems
8On vehicles fitted with the ESC II or EEC IV
systems, there is a facility for retarding the
ignition timing without physically disturbing
the distributor.
9Adjustment is made by earthing one or two
wires (“octane adjustment” wires) which
terminate in a wiring plug next to the ignition
coil. Ideally a service adjustment lead,
available from a Ford dealer should be used
(see illustration). One end of the lead plugs
into the “octane adjustment” wiring plug, and
the other end should be earthed by fixing to
one of the ignition coil securing screws.
10Cut and insulate the wires in the service
lead which are not to be earthed.
17Ignition timing -adjustmentfor
usewithunleadedpetrol
5•18Engine electrical systems
17.9 Service adjustment lead and plug -
ESC II and EEC IV systems
A Red, blue and yellow wires
B Plug
C Wire cutting point
16.2b Crankshaft pulley timing marks - SOHC engine
A Cast pulleyB Pressed steel pulley
Page 19 of 24
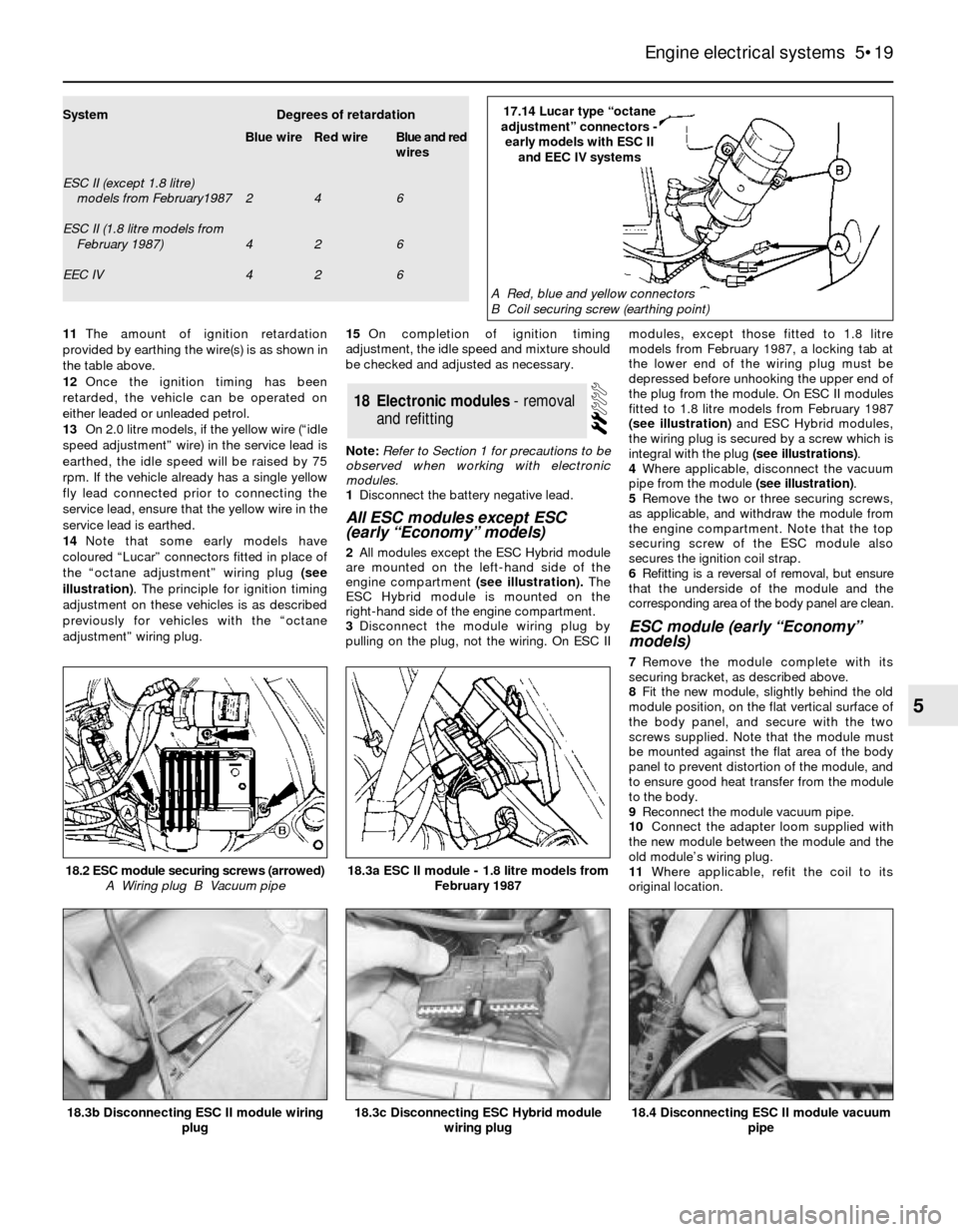
11The amount of ignition retardation
provided by earthing the wire(s) is as shown in
the table above.
12Once the ignition timing has been
retarded, the vehicle can be operated on
either leaded or unleaded petrol.
13On 2.0 litre models, if the yellow wire (“idle
speed adjustment” wire) in the service lead is
earthed, the idle speed will be raised by 75
rpm. If the vehicle already has a single yellow
fly lead connected prior to connecting the
service lead, ensure that the yellow wire in the
service lead is earthed.
14Note that some early models have
coloured “Lucar” connectors fitted in place of
the “octane adjustment” wiring plug (see
illustration). The principle for ignition timing
adjustment on these vehicles is as described
previously for vehicles with the “octane
adjustment” wiring plug.15On completion of ignition timing
adjustment, the idle speed and mixture should
be checked and adjusted as necessary.
Note: Refer to Section 1 for precautions to be
observed when working with electronic
modules.
1Disconnect the battery negative lead.
All ESC modules except ESC
(early “Economy” models)
2All modules except the ESC Hybrid module
are mounted on the left-hand side of the
engine compartment(see illustration).The
ESC Hybrid module is mounted on the
right-hand side of the engine compartment.
3Disconnect the module wiring plug by
pulling on the plug, not the wiring. On ESC IImodules, except those fitted to 1.8 litre
models from February 1987, a locking tab at
the lower end of the wiring plug must be
depressed before unhooking the upper end of
the plug from the module. On ESC II modules
fitted to 1.8 litre models from February 1987
(see illustration)and ESC Hybrid modules,
the wiring plug is secured by a screw which is
integral with the plug (see illustrations).
4Where applicable, disconnect the vacuum
pipe from the module (see illustration).
5Remove the two or three securing screws,
as applicable, and withdraw the module from
the engine compartment. Note that the top
securing screw of the ESC module also
secures the ignition coil strap.
6Refitting is a reversal of removal, but ensure
that the underside of the module and the
corresponding area of the body panel are clean.
ESC module (early “Economy”
models)
7Remove the module complete with its
securing bracket, as described above.
8Fit the new module, slightly behind the old
module position, on the flat vertical surface of
the body panel, and secure with the two
screws supplied. Note that the module must
be mounted against the flat area of the body
panel to prevent distortion of the module, and
to ensure good heat transfer from the module
to the body.
9Reconnect the module vacuum pipe.
10Connect the adapter loom supplied with
the new module between the module and the
old module’s wiring plug.
11Where applicable, refit the coil to its
original location.
18Electronic modules - removal
and refitting
Engine electrical systems 5•19
5
18.4 Disconnecting ESC II module vacuum
pipe18.3c Disconnecting ESC Hybrid module
wiring plug18.3b Disconnecting ESC II module wiring
plug
18.2 ESC module securing screws (arrowed)
A Wiring plug B Vacuum pipe18.3a ESC II module - 1.8 litre models from
February 1987
SystemDegrees of retardation
Blue wireRed wireBlue and red
wires
ESC II (except 1.8 litre)
models from February1987246
ESC II (1.8 litre models from
February 1987)426
EEC IV42617.14 Lucar type “octane
adjustment” connectors -
early models with ESC II
and EEC IV systems
A Red, blue and yellow connectors
B Coil securing screw (earthing point)