wheel alignment FORD SIERRA 1992 2.G Reference Workshop Manual
[x] Cancel search | Manufacturer: FORD, Model Year: 1992, Model line: SIERRA, Model: FORD SIERRA 1992 2.GPages: 26, PDF Size: 0.57 MB
Page 8 of 26
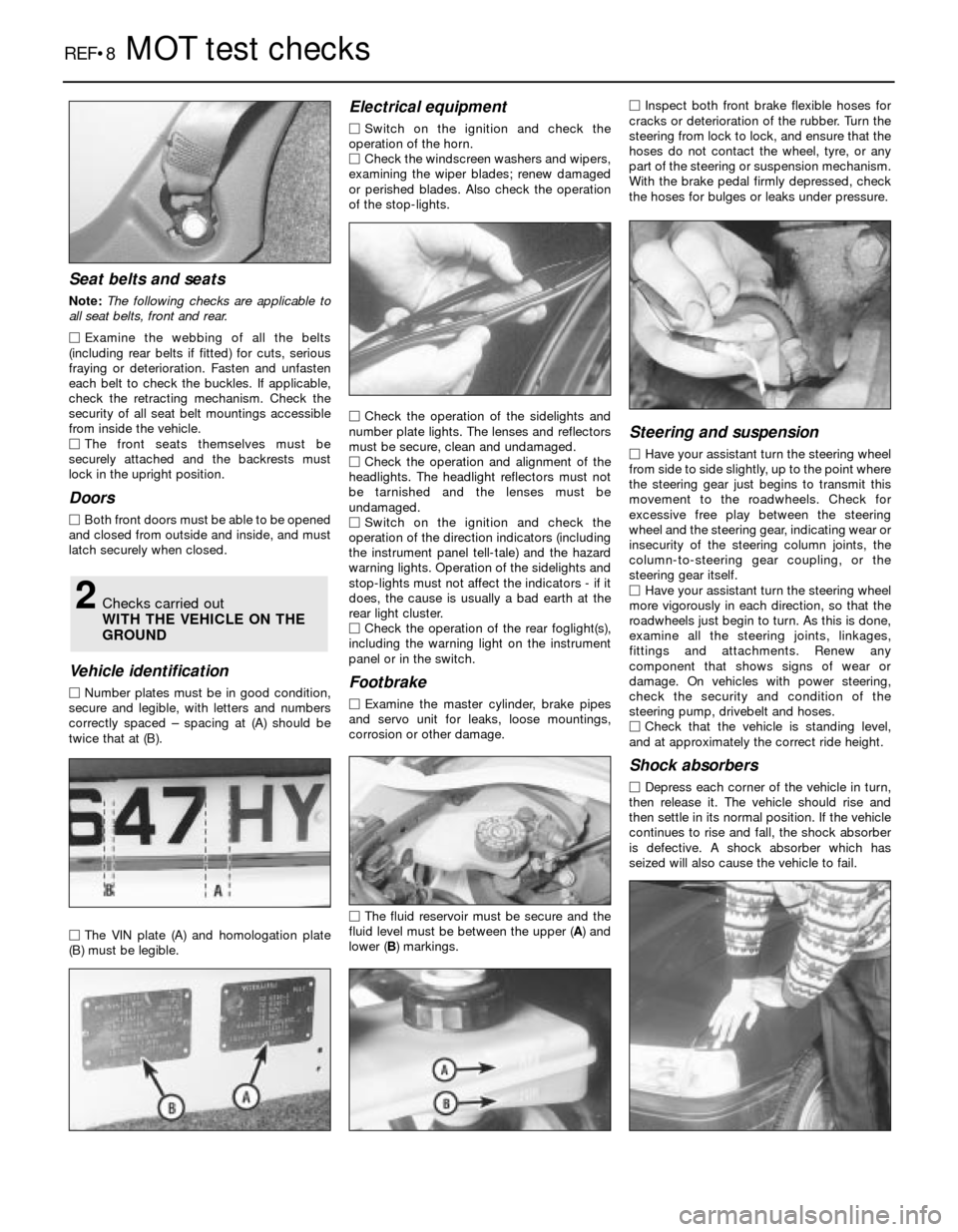
REF•8MOTtest checks
Seat belts and seats
Note: The following checks are applicable to
all seat belts, front and rear.
MExamine the webbing of all the belts
(including rear belts if fitted) for cuts, serious
fraying or deterioration. Fasten and unfasten
each belt to check the buckles. If applicable,
check the retracting mechanism. Check the
security of all seat belt mountings accessible
from inside the vehicle.
MThe front seats themselves must be
securely attached and the backrests must
lock in the upright position.
Doors
MBoth front doors must be able to be opened
and closed from outside and inside, and must
latch securely when closed.
Vehicle identification
MNumber plates must be in good condition,
secure and legible, with letters and numbers
correctly spaced – spacing at (A) should be
twice that at (B).
MThe VIN plate (A) and homologation plate
(B) must be legible.
Electrical equipment
MSwitch on the ignition and check the
operation of the horn.
MCheck the windscreen washers and wipers,
examining the wiper blades; renew damaged
or perished blades. Also check the operation
of the stop-lights.
MCheck the operation of the sidelights and
number plate lights. The lenses and reflectors
must be secure, clean and undamaged.
MCheck the operation and alignment of the
headlights. The headlight reflectors must not
be tarnished and the lenses must be
undamaged.
MSwitch on the ignition and check the
operation of the direction indicators (including
the instrument panel tell-tale) and the hazard
warning lights. Operation of the sidelights and
stop-lights must not affect the indicators - if it
does, the cause is usually a bad earth at the
rear light cluster.
MCheck the operation of the rear foglight(s),
including the warning light on the instrument
panel or in the switch.
Footbrake
MExamine the master cylinder, brake pipes
and servo unit for leaks, loose mountings,
corrosion or other damage.
MThe fluid reservoir must be secure and the
fluid level must be between the upper (A) and
lower (B) markings.MInspect both front brake flexible hoses for
cracks or deterioration of the rubber. Turn the
steering from lock to lock, and ensure that the
hoses do not contact the wheel, tyre, or any
part of the steering or suspension mechanism.
With the brake pedal firmly depressed, check
the hoses for bulges or leaks under pressure.
Steering and suspension
MHave your assistant turn the steering wheel
from side to side slightly, up to the point where
the steering gear just begins to transmit this
movement to the roadwheels. Check for
excessive free play between the steering
wheel and the steering gear, indicating wear or
insecurity of the steering column joints, the
column-to-steering gear coupling, or the
steering gear itself.
MHave your assistant turn the steering wheel
more vigorously in each direction, so that the
roadwheels just begin to turn. As this is done,
examine all the steering joints, linkages,
fittings and attachments. Renew any
component that shows signs of wear or
damage. On vehicles with power steering,
check the security and condition of the
steering pump, drivebelt and hoses.
MCheck that the vehicle is standing level,
and at approximately the correct ride height.
Shock absorbers
MDepress each corner of the vehicle in turn,
then release it. The vehicle should rise and
then settle in its normal position. If the vehicle
continues to rise and fall, the shock absorber
is defective. A shock absorber which has
seized will also cause the vehicle to fail.
2Checks carried out
WITH THE VEHICLE ON THE
GROUND
Page 10 of 26
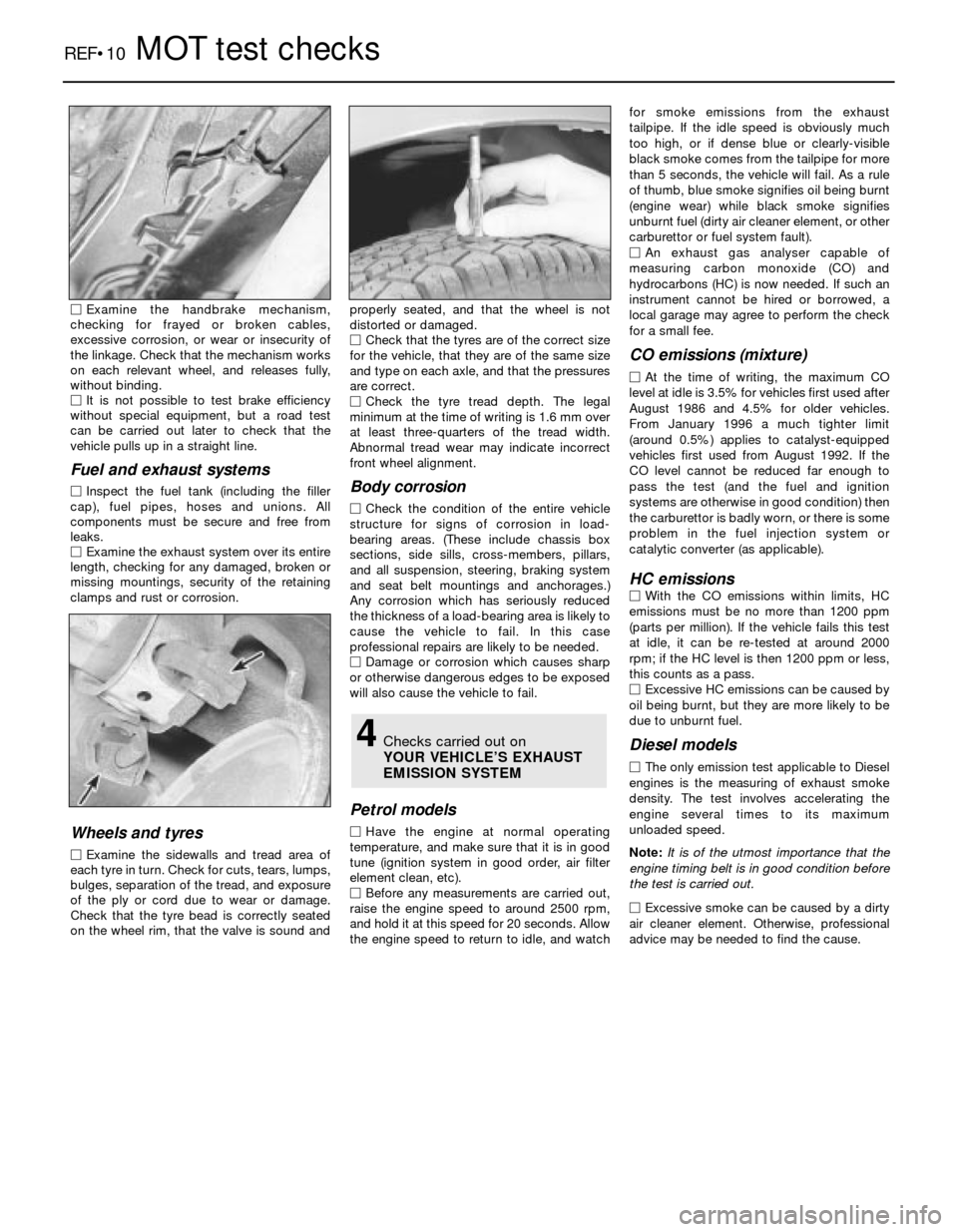
REF•10MOTtest checks
MExamine the handbrake mechanism,
checking for frayed or broken cables,
excessive corrosion, or wear or insecurity of
the linkage. Check that the mechanism works
on each relevant wheel, and releases fully,
without binding.
MIt is not possible to test brake efficiency
without special equipment, but a road test
can be carried out later to check that the
vehicle pulls up in a straight line.
Fuel and exhaust systems
MInspect the fuel tank (including the filler
cap), fuel pipes, hoses and unions. All
components must be secure and free from
leaks.
MExamine the exhaust system over its entire
length, checking for any damaged, broken or
missing mountings, security of the retaining
clamps and rust or corrosion.
Wheels and tyres
MExamine the sidewalls and tread area of
each tyre in turn. Check for cuts, tears, lumps,
bulges, separation of the tread, and exposure
of the ply or cord due to wear or damage.
Check that the tyre bead is correctly seated
on the wheel rim, that the valve is sound andproperly seated, and that the wheel is not
distorted or damaged.
MCheck that the tyres are of the correct size
for the vehicle, that they are of the same size
and type on each axle, and that the pressures
are correct.
MCheck the tyre tread depth. The legal
minimum at the time of writing is 1.6 mm over
at least three-quarters of the tread width.
Abnormal tread wear may indicate incorrect
front wheel alignment.
Body corrosion
MCheck the condition of the entire vehicle
structure for signs of corrosion in load-
bearing areas. (These include chassis box
sections, side sills, cross-members, pillars,
and all suspension, steering, braking system
and seat belt mountings and anchorages.)
Any corrosion which has seriously reduced
the thickness of a load-bearing area is likely to
cause the vehicle to fail. In this case
professional repairs are likely to be needed.
MDamage or corrosion which causes sharp
or otherwise dangerous edges to be exposed
will also cause the vehicle to fail.
Petrol models
MHave the engine at normal operating
temperature, and make sure that it is in good
tune (ignition system in good order, air filter
element clean, etc).
MBefore any measurements are carried out,
raise the engine speed to around 2500 rpm,
and hold it at this speed for 20 seconds. Allow
the engine speed to return to idle, and watchfor smoke emissions from the exhaust
tailpipe. If the idle speed is obviously much
too high, or if dense blue or clearly-visible
black smoke comes from the tailpipe for more
than 5 seconds, the vehicle will fail. As a rule
of thumb, blue smoke signifies oil being burnt
(engine wear) while black smoke signifies
unburnt fuel (dirty air cleaner element, or other
carburettor or fuel system fault).
MAn exhaust gas analyser capable of
measuring carbon monoxide (CO) and
hydrocarbons (HC) is now needed. If such an
instrument cannot be hired or borrowed, a
local garage may agree to perform the check
for a small fee.
CO emissions (mixture)
MAt the time of writing, the maximum CO
level at idle is 3.5% for vehicles first used after
August 1986 and 4.5% for older vehicles.
From January 1996 a much tighter limit
(around 0.5%) applies to catalyst-equipped
vehicles first used from August 1992. If the
CO level cannot be reduced far enough to
pass the test (and the fuel and ignition
systems are otherwise in good condition) then
the carburettor is badly worn, or there is some
problem in the fuel injection system or
catalytic converter (as applicable).
HC emissionsMWith the CO emissions within limits, HC
emissions must be no more than 1200 ppm
(parts per million). If the vehicle fails this test
at idle, it can be re-tested at around 2000
rpm; if the HC level is then 1200 ppm or less,
this counts as a pass.
MExcessive HC emissions can be caused by
oil being burnt, but they are more likely to be
due to unburnt fuel.
Diesel models
MThe only emission test applicable to Diesel
engines is the measuring of exhaust smoke
density. The test involves accelerating the
engine several times to its maximum
unloaded speed.
Note: It is of the utmost importance that the
engine timing belt is in good condition before
the test is carried out.
M
Excessive smoke can be caused by a dirty
air cleaner element. Otherwise, professional
advice may be needed to find the cause.
4Checks carried out on
YOUR VEHICLE’S EXHAUST
EMISSION SYSTEM
Page 15 of 26
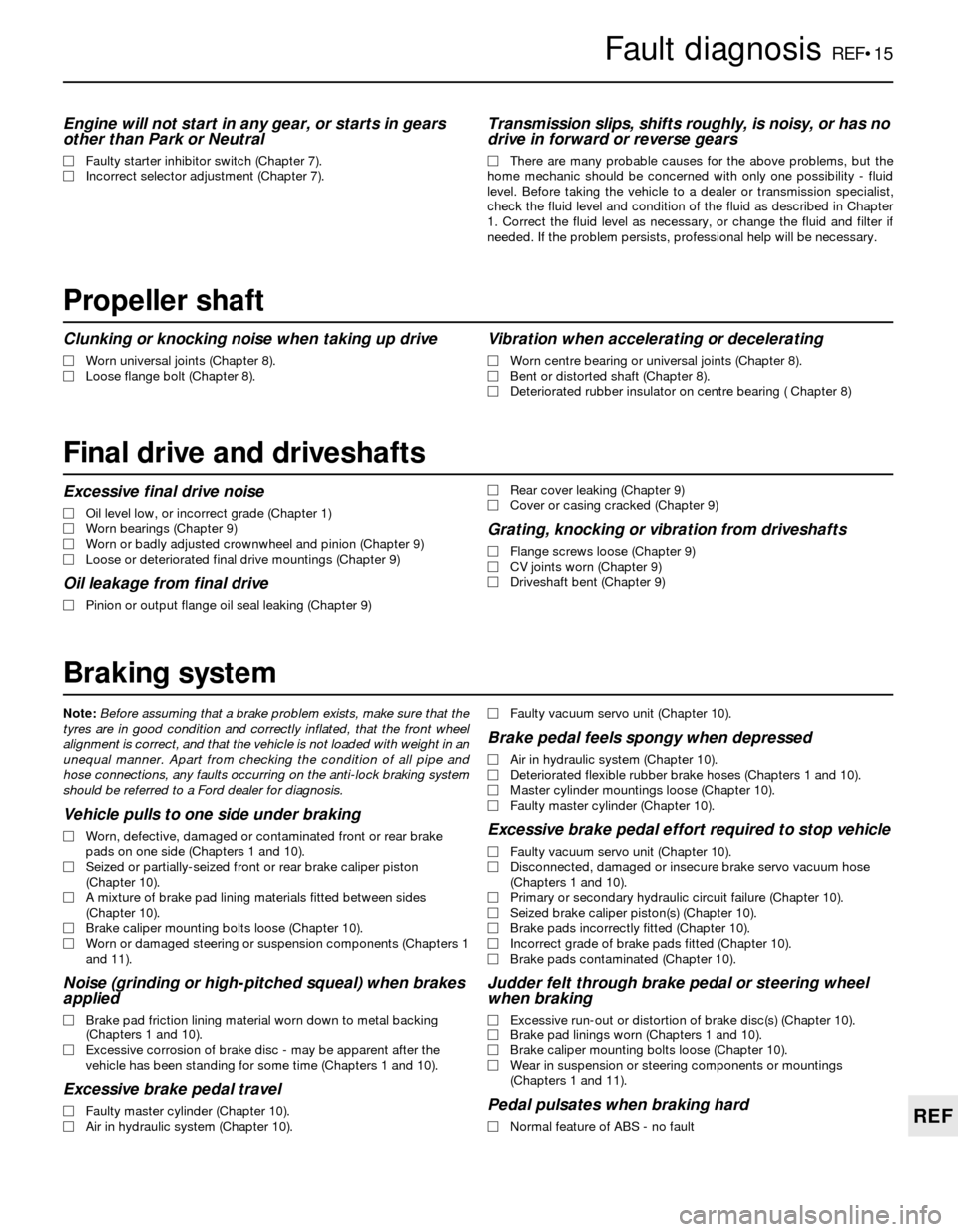
Excessive final drive noise
MOil level low, or incorrect grade (Chapter 1)
MWorn bearings (Chapter 9)
MWorn or badly adjusted crownwheel and pinion (Chapter 9)
MLoose or deteriorated final drive mountings (Chapter 9)
Oil leakage from final drive
MPinion or output flange oil seal leaking (Chapter 9)MRear cover leaking (Chapter 9)
MCover or casing cracked (Chapter 9)
Grating, knocking or vibration from driveshafts
MFlange screws loose (Chapter 9)
MCV joints worn (Chapter 9)
MDriveshaft bent (Chapter 9)
Note:Before assuming that a brake problem exists, make sure that the
tyres are in good condition and correctly inflated, that the front wheel
alignment is correct, and that the vehicle is not loaded with weight in an
unequal manner. Apart from checking the condition of all pipe and
hose connections, any faults occurring on the anti-lock braking system
should be referred to a Ford dealer for diagnosis.
Vehicle pulls to one side under braking
MWorn, defective, damaged or contaminated front or rear brake
pads on one side (Chapters 1 and 10).
MSeized or partially-seized front or rear brake caliper piston
(Chapter 10).
MA mixture of brake pad lining materials fitted between sides
(Chapter 10).
MBrake caliper mounting bolts loose (Chapter 10).
MWorn or damaged steering or suspension components (Chapters 1
and 11).
Noise (grinding or high-pitched squeal) when brakes
applied
MBrake pad friction lining material worn down to metal backing
(Chapters 1 and 10).
MExcessive corrosion of brake disc - may be apparent after the
vehicle has been standing for some time (Chapters 1 and 10).
Excessive brake pedal travel
MFaulty master cylinder (Chapter 10).
MAir in hydraulic system (Chapter 10).MFaulty vacuum servo unit (Chapter 10).
Brake pedal feels spongy when depressed
MAir in hydraulic system (Chapter 10).
MDeteriorated flexible rubber brake hoses (Chapters 1 and 10).
MMaster cylinder mountings loose (Chapter 10).
MFaulty master cylinder (Chapter 10).
Excessive brake pedal effort required to stop vehicle
MFaulty vacuum servo unit (Chapter 10).
MDisconnected, damaged or insecure brake servo vacuum hose
(Chapters 1 and 10).
MPrimary or secondary hydraulic circuit failure (Chapter 10).
MSeized brake caliper piston(s) (Chapter 10).
MBrake pads incorrectly fitted (Chapter 10).
MIncorrect grade of brake pads fitted (Chapter 10).
MBrake pads contaminated (Chapter 10).
Judder felt through brake pedal or steering wheel
when braking
MExcessive run-out or distortion of brake disc(s) (Chapter 10).
MBrake pad linings worn (Chapters 1 and 10).
MBrake caliper mounting bolts loose (Chapter 10).
MWear in suspension or steering components or mountings
(Chapters 1 and 11).
Pedal pulsates when braking hard
MNormal feature of ABS - no fault
Clunking or knocking noise when taking up drive
MWorn universal joints (Chapter 8).
MLoose flange bolt (Chapter 8).
Vibration when accelerating or decelerating
MWorn centre bearing or universal joints (Chapter 8).
MBent or distorted shaft (Chapter 8).
MDeteriorated rubber insulator on centre bearing ( Chapter 8)
Engine will not start in any gear, or starts in gears
other than Park or Neutral
MFaulty starter inhibitor switch (Chapter 7).
MIncorrect selector adjustment (Chapter 7).
Transmission slips, shifts roughly, is noisy, or has no
drive in forward or reverse gears
MThere are many probable causes for the above problems, but the
home mechanic should be concerned with only one possibility - fluid
level. Before taking the vehicle to a dealer or transmission specialist,
check the fluid level and condition of the fluid as described in Chapter
1. Correct the fluid level as necessary, or change the fluid and filter if
needed. If the problem persists, professional help will be necessary.
Fault diagnosisREF•15
REF
Propeller shaft
Final drive and driveshafts
Braking system
Page 16 of 26
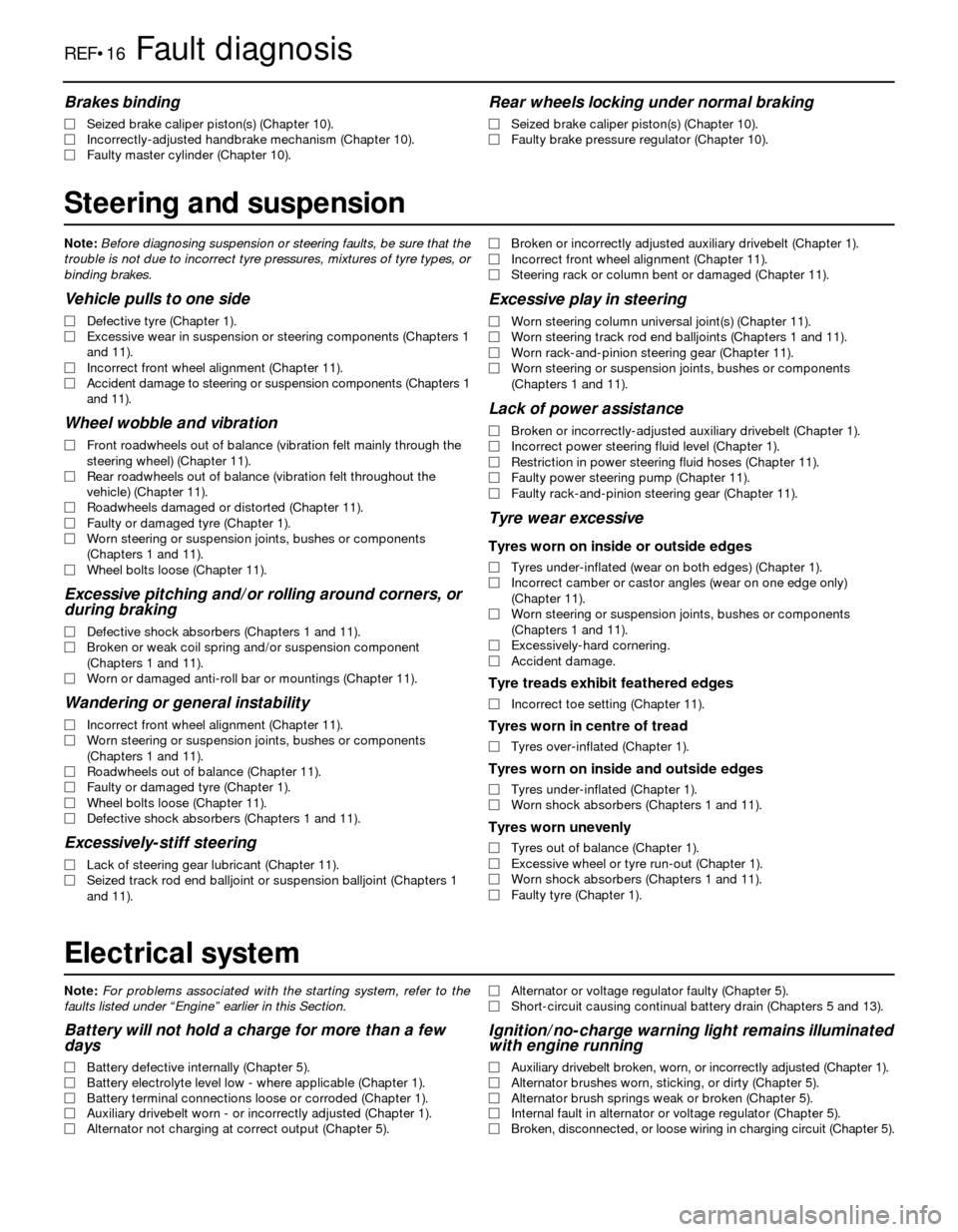
Brakes binding
MSeized brake caliper piston(s) (Chapter 10).
MIncorrectly-adjusted handbrake mechanism (Chapter 10).
MFaulty master cylinder (Chapter 10).
Rear wheels locking under normal braking
MSeized brake caliper piston(s) (Chapter 10).
MFaulty brake pressure regulator (Chapter 10).
Note:For problems associated with the starting system, refer to the
faults listed under “Engine” earlier in this Section.
Battery will not hold a charge for more than a few
days
MBattery defective internally (Chapter 5).
MBattery electrolyte level low - where applicable (Chapter 1).
MBattery terminal connections loose or corroded (Chapter 1).
MAuxiliary drivebelt worn - or incorrectly adjusted (Chapter 1).
MAlternator not charging at correct output (Chapter 5).MAlternator or voltage regulator faulty (Chapter 5).
MShort-circuit causing continual battery drain (Chapters 5 and 13).
Ignition/no-charge warning light remains illuminated
with engine running
MAuxiliary drivebelt broken, worn, or incorrectly adjusted (Chapter 1).
MAlternator brushes worn, sticking, or dirty (Chapter 5).
MAlternator brush springs weak or broken (Chapter 5).
MInternal fault in alternator or voltage regulator (Chapter 5).
MBroken, disconnected, or loose wiring in charging circuit (Chapter 5). Note:Before diagnosing suspension or steering faults, be sure that the
trouble is not due to incorrect tyre pressures, mixtures of tyre types, or
binding brakes.
Vehicle pulls to one side
MDefective tyre (Chapter 1).
MExcessive wear in suspension or steering components (Chapters 1
and 11).
MIncorrect front wheel alignment (Chapter 11).
MAccident damage to steering or suspension components (Chapters 1
and 11).
Wheel wobble and vibration
MFront roadwheels out of balance (vibration felt mainly through the
steering wheel) (Chapter 11).
MRear roadwheels out of balance (vibration felt throughout the
vehicle) (Chapter 11).
MRoadwheels damaged or distorted (Chapter 11).
MFaulty or damaged tyre (Chapter 1).
MWorn steering or suspension joints, bushes or components
(Chapters 1 and 11).
MWheel bolts loose (Chapter 11).
Excessive pitching and/or rolling around corners, or
during braking
MDefective shock absorbers (Chapters 1 and 11).
MBroken or weak coil spring and/or suspension component
(Chapters 1 and 11).
MWorn or damaged anti-roll bar or mountings (Chapter 11).
Wandering or general instability
MIncorrect front wheel alignment (Chapter 11).
MWorn steering or suspension joints, bushes or components
(Chapters 1 and 11).
MRoadwheels out of balance (Chapter 11).
MFaulty or damaged tyre (Chapter 1).
MWheel bolts loose (Chapter 11).
MDefective shock absorbers (Chapters 1 and 11).
Excessively-stiff steering
MLack of steering gear lubricant (Chapter 11).
MSeized track rod end balljoint or suspension balljoint (Chapters 1
and 11).MBroken or incorrectly adjusted auxiliary drivebelt (Chapter 1).
MIncorrect front wheel alignment (Chapter 11).
MSteering rack or column bent or damaged (Chapter 11).
Excessive play in steering
MWorn steering column universal joint(s) (Chapter 11).
MWorn steering track rod end balljoints (Chapters 1 and 11).
MWorn rack-and-pinion steering gear (Chapter 11).
MWorn steering or suspension joints, bushes or components
(Chapters 1 and 11).
Lack of power assistance
MBroken or incorrectly-adjusted auxiliary drivebelt (Chapter 1).
MIncorrect power steering fluid level (Chapter 1).
MRestriction in power steering fluid hoses (Chapter 11).
MFaulty power steering pump (Chapter 11).
MFaulty rack-and-pinion steering gear (Chapter 11).
Tyre wear excessive
Tyres worn on inside or outside edges
MTyres under-inflated (wear on both edges) (Chapter 1).
MIncorrect camber or castor angles (wear on one edge only)
(Chapter 11).
MWorn steering or suspension joints, bushes or components
(Chapters 1 and 11).
MExcessively-hard cornering.
MAccident damage.
Tyre treads exhibit feathered edges
MIncorrect toe setting (Chapter 11).
Tyres worn in centre of tread
MTyres over-inflated (Chapter 1).
Tyres worn on inside and outside edges
MTyres under-inflated (Chapter 1).
MWorn shock absorbers (Chapters 1 and 11).
Tyres worn unevenly
MTyres out of balance (Chapter 1).
MExcessive wheel or tyre run-out (Chapter 1).
MWorn shock absorbers (Chapters 1 and 11).
MFaulty tyre (Chapter 1).
REF•16Fault diagnosis
Steering and suspension
Electrical system
Page 19 of 26
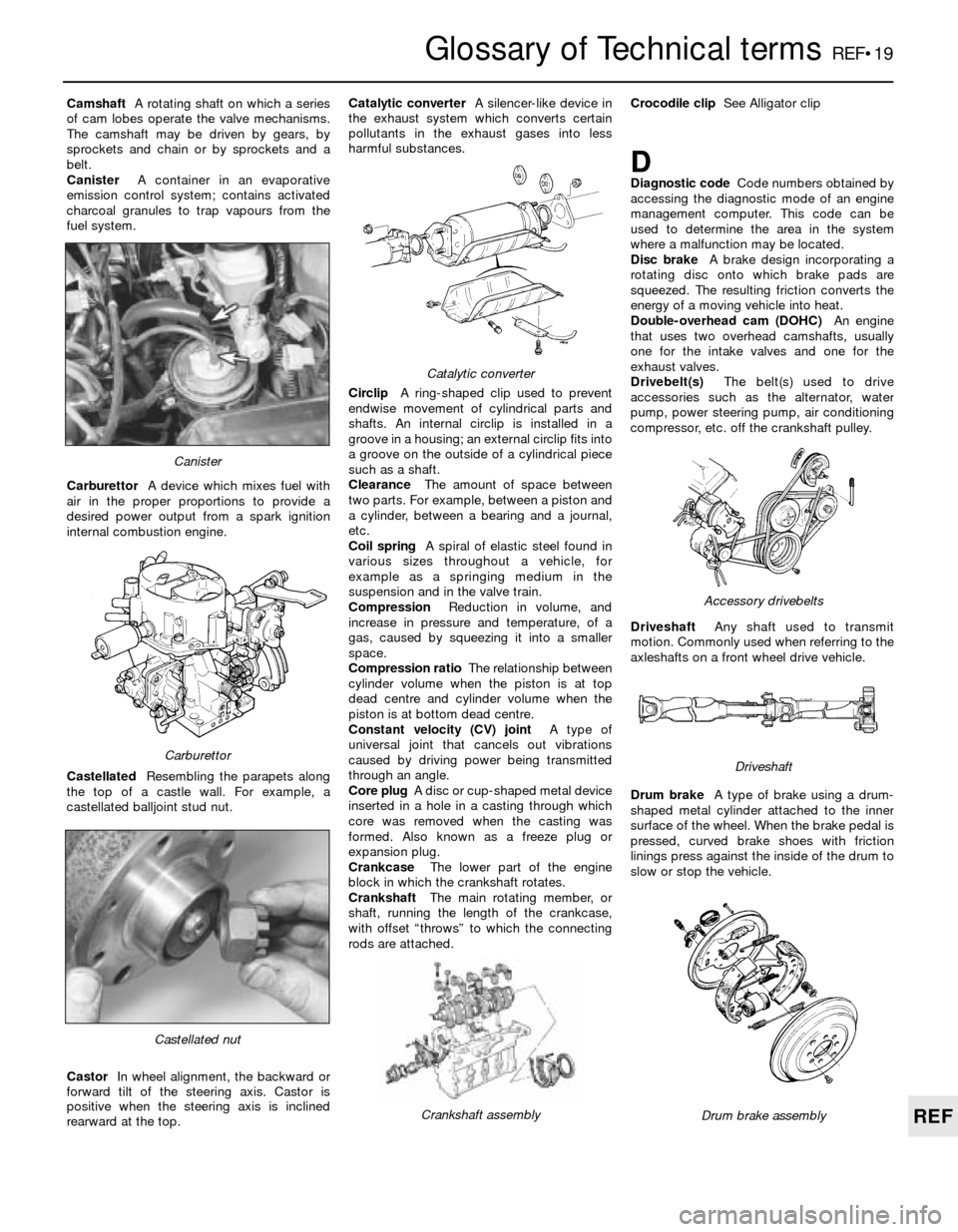
Glossary of Technical termsREF•19
REF
CamshaftA rotating shaft on which a series
of cam lobes operate the valve mechanisms.
The camshaft may be driven by gears, by
sprockets and chain or by sprockets and a
belt.
CanisterA container in an evaporative
emission control system; contains activated
charcoal granules to trap vapours from the
fuel system.
CarburettorA device which mixes fuel with
air in the proper proportions to provide a
desired power output from a spark ignition
internal combustion engine.
CastellatedResembling the parapets along
the top of a castle wall. For example, a
castellated balljoint stud nut.
CastorIn wheel alignment, the backward or
forward tilt of the steering axis. Castor is
positive when the steering axis is inclined
rearward at the top.Catalytic converterA silencer-like device in
the exhaust system which converts certain
pollutants in the exhaust gases into less
harmful substances.
CirclipA ring-shaped clip used to prevent
endwise movement of cylindrical parts and
shafts. An internal circlip is installed in a
groove in a housing; an external circlip fits into
a groove on the outside of a cylindrical piece
such as a shaft.
ClearanceThe amount of space between
two parts. For example, between a piston and
a cylinder, between a bearing and a journal,
etc.
Coil springA spiral of elastic steel found in
various sizes throughout a vehicle, for
example as a springing medium in the
suspension and in the valve train.
CompressionReduction in volume, and
increase in pressure and temperature, of a
gas, caused by squeezing it into a smaller
space.
Compression ratioThe relationship between
cylinder volume when the piston is at top
dead centre and cylinder volume when the
piston is at bottom dead centre.
Constant velocity (CV) jointA type of
universal joint that cancels out vibrations
caused by driving power being transmitted
through an angle.
Core plugA disc or cup-shaped metal device
inserted in a hole in a casting through which
core was removed when the casting was
formed. Also known as a freeze plug or
expansion plug.
CrankcaseThe lower part of the engine
block in which the crankshaft rotates.
CrankshaftThe main rotating member, or
shaft, running the length of the crankcase,
with offset “throws” to which the connecting
rods are attached.Crocodile clipSee Alligator clip
DDiagnostic codeCode numbers obtained by
accessing the diagnostic mode of an engine
management computer. This code can be
used to determine the area in the system
where a malfunction may be located.
Disc brakeA brake design incorporating a
rotating disc onto which brake pads are
squeezed. The resulting friction converts the
energy of a moving vehicle into heat.
Double-overhead cam (DOHC)An engine
that uses two overhead camshafts, usually
one for the intake valves and one for the
exhaust valves.
Drivebelt(s)The belt(s) used to drive
accessories such as the alternator, water
pump, power steering pump, air conditioning
compressor, etc. off the crankshaft pulley.
DriveshaftAny shaft used to transmit
motion. Commonly used when referring to the
axleshafts on a front wheel drive vehicle.
Drum brakeA type of brake using a drum-
shaped metal cylinder attached to the inner
surface of the wheel. When the brake pedal is
pressed, curved brake shoes with friction
linings press against the inside of the drum to
slow or stop the vehicle.
Castellated nut
Catalytic converter
Crankshaft assembly
Carburettor
Canister
Drum brake assembly
Accessory drivebelts
Driveshaft
Page 24 of 26
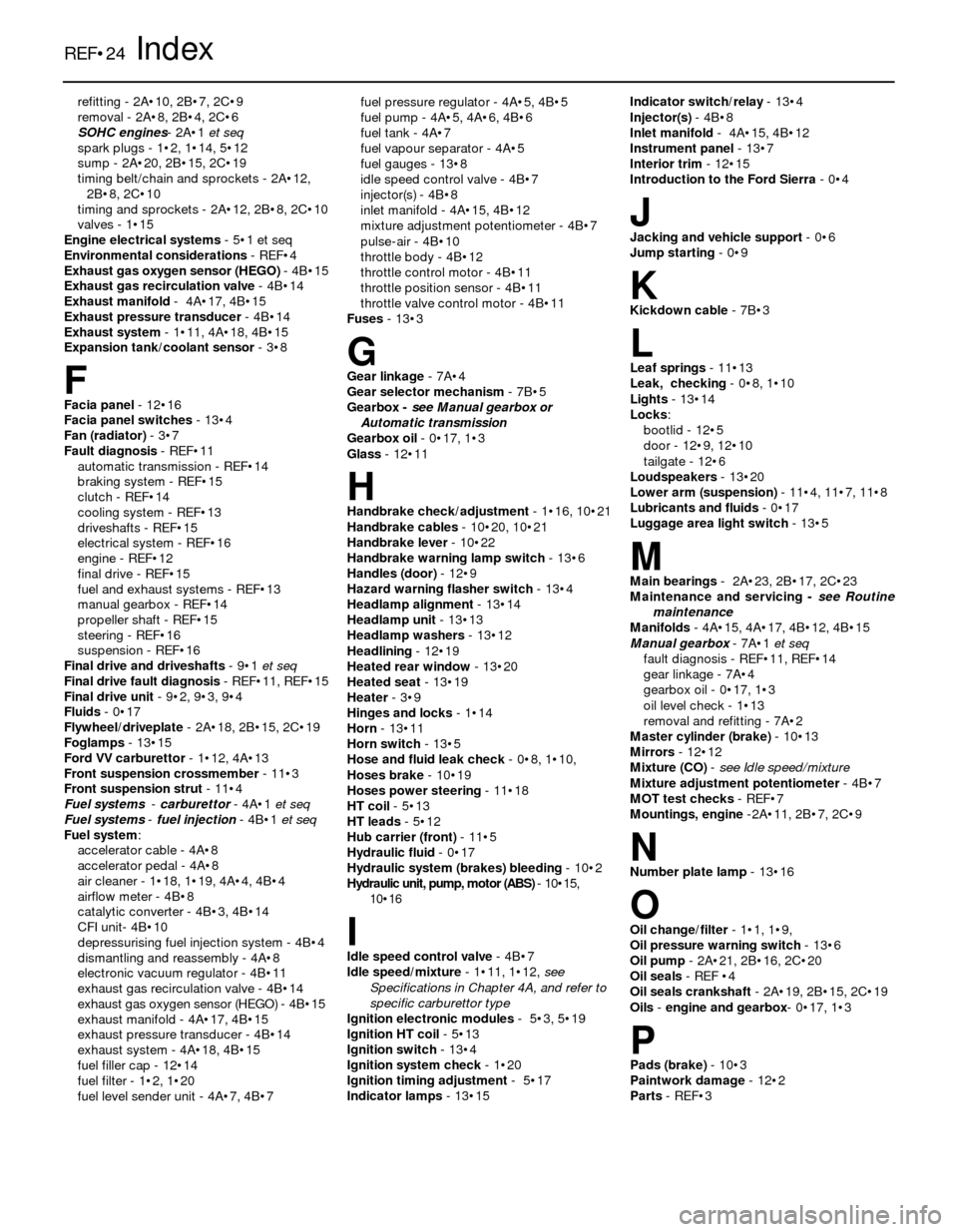
refitting - 2A•10, 2B•7, 2C•9
removal - 2A•8, 2B•4, 2C•6
SOHC engines- 2A•1et seq
spark plugs - 1•2, 1•14, 5•12
sump - 2A•20, 2B•15, 2C•19
timing belt/chain and sprockets - 2A•12,
2B•8, 2C•10
timing and sprockets - 2A•12, 2B•8, 2C•10
valves - 1•15
Engine electrical systems - 5•1 et seq
Environmental considerations- REF•4
Exhaust gas oxygen sensor (HEGO)- 4B•15
Exhaust gas recirculation valve- 4B•14
Exhaust manifold- 4A•17, 4B•15
Exhaust pressure transducer- 4B•14
Exhaust system- 1•11, 4A•18, 4B•15
Expansion tank/coolant sensor- 3•8
FFacia panel- 12•16
Facia panel switches- 13•4
Fan (radiator)- 3•7
Fault diagnosis- REF•11
automatic transmission - REF•14
braking system - REF•15
clutch - REF•14
cooling system - REF•13
driveshafts - REF•15
electrical system - REF•16
engine - REF•12
final drive - REF•15
fuel and exhaust systems - REF•13
manual gearbox - REF•14
propeller shaft - REF•15
steering - REF•16
suspension - REF•16
Final drive and driveshafts- 9•1 et seq
Final drive fault diagnosis- REF•11, REF•15
Final drive unit- 9•2, 9•3, 9•4
Fluids- 0•17
Flywheel/driveplate- 2A•18, 2B•15, 2C•19
Foglamps- 13•15
Ford VV carburettor- 1•12, 4A•13
Front suspension crossmember- 11•3
Front suspension strut- 11•4
Fuel systems- carburettor - 4A•1 et seq
Fuel systems- fuel injection - 4B•1 et seq
Fuel system:
accelerator cable - 4A•8
accelerator pedal - 4A•8
air cleaner - 1•18, 1•19, 4A•4, 4B•4
airflow meter - 4B•8
catalytic converter - 4B•3, 4B•14
CFI unit- 4B•10
depressurising fuel injection system - 4B•4
dismantling and reassembly - 4A•8
electronic vacuum regulator - 4B•11
exhaust gas recirculation valve - 4B•14
exhaust gas oxygen sensor (HEGO) - 4B•15
exhaust manifold - 4A•17, 4B•15
exhaust pressure transducer - 4B•14
exhaust system - 4A•18, 4B•15
fuel filler cap - 12•14
fuel filter - 1•2, 1•20
fuel level sender unit - 4A•7, 4B•7fuel pressure regulator - 4A•5, 4B•5
fuel pump - 4A•5, 4A•6, 4B•6
fuel tank - 4A•7
fuel vapour separator - 4A•5
fuel gauges - 13•8
idle speed control valve - 4B•7
injector(s) - 4B•8
inlet manifold - 4A•15, 4B•12
mixture adjustment potentiometer - 4B•7
pulse-air - 4B•10
throttle body - 4B•12
throttle control motor - 4B•11
throttle position sensor - 4B•11
throttle valve control motor - 4B•11
Fuses- 13•3
GGear linkage- 7A•4
Gear selector mechanism- 7B•5
Gearbox - see Manual gearbox or
Automatic transmission
Gearbox oil- 0•17, 1•3
Glass- 12•11
HHandbrake check/adjustment- 1•16, 10•21
Handbrake cables- 10•20, 10•21
Handbrake lever - 10•22
Handbrake warning lamp switch- 13•6
Handles (door)- 12•9
Hazard warning flasher switch- 13•4
Headlamp alignment- 13•14
Headlamp unit- 13•13
Headlamp washers- 13•12
Headlining - 12•19
Heated rear window- 13•20
Heated seat- 13•19
Heater- 3•9
Hinges and locks- 1•14
Horn- 13•11
Horn switch- 13•5
Hose and fluid leak check- 0•8, 1•10,
Hoses brake- 10•19
Hoses power steering- 11•18
HT coil- 5•13
HT leads- 5•12
Hub carrier (front) - 11•5
Hydraulic fluid- 0•17
Hydraulic system (brakes) bleeding- 10•2
Hydraulic unit, pump, motor (ABS)- 10•15,
10•16
IIdle speed control valve- 4B•7
Idle speed/mixture- 1•11, 1•12, see
Specifications in Chapter 4A, and refer to
specific carburettor type
Ignition electronic modules- 5•3, 5•19
Ignition HT coil- 5•13
Ignition switch- 13•4
Ignition system check- 1•20
Ignition timing adjustment- 5•17
Indicator lamps- 13•15Indicator switch/relay- 13•4
Injector(s)- 4B•8
Inlet manifold- 4A•15, 4B•12
Instrument panel- 13•7
Interior trim- 12•15
Introduction to the Ford Sierra- 0•4
JJacking and vehicle support- 0•6
Jump starting- 0•9
KKickdown cable - 7B•3
LLeaf springs- 11•13
Leak, checking- 0•8, 1•10
Lights- 13•14
Locks:
bootlid - 12•5
door - 12•9, 12•10
tailgate - 12•6
Loudspeakers- 13•20
Lower arm (suspension)- 11•4, 11•7, 11•8
Lubricants and fluids- 0•17
Luggage area light switch- 13•5
MMain bearings- 2A•23, 2B•17, 2C•23
Maintenance and servicing - see Routine
maintenance
Manifolds- 4A•15, 4A•17, 4B•12, 4B•15
Manual gearbox- 7A•1 et seq
fault diagnosis - REF•11, REF•14
gear linkage - 7A•4
gearbox oil - 0•17, 1•3
oil level check - 1•13
removal and refitting - 7A•2
Master cylinder (brake)- 10•13
Mirrors- 12•12
Mixture (CO)- see Idle speed/mixture
Mixture adjustment potentiometer- 4B•7
MOT test checks- REF•7
Mountings, engine-2A•11, 2B•7, 2C•9
NNumber plate lamp- 13•16
OOil change/filter- 1•1, 1•9,
Oil pressure warning switch- 13•6
Oil pump- 2A•21, 2B•16, 2C•20
Oil seals- REF •4
Oil seals crankshaft- 2A•19, 2B•15, 2C•19
Oils- engine and gearbox- 0•17, 1•3
PPads (brake) - 10•3
Paintwork damage- 12•2
Parts- REF•3
REF•24Index
Page 25 of 26
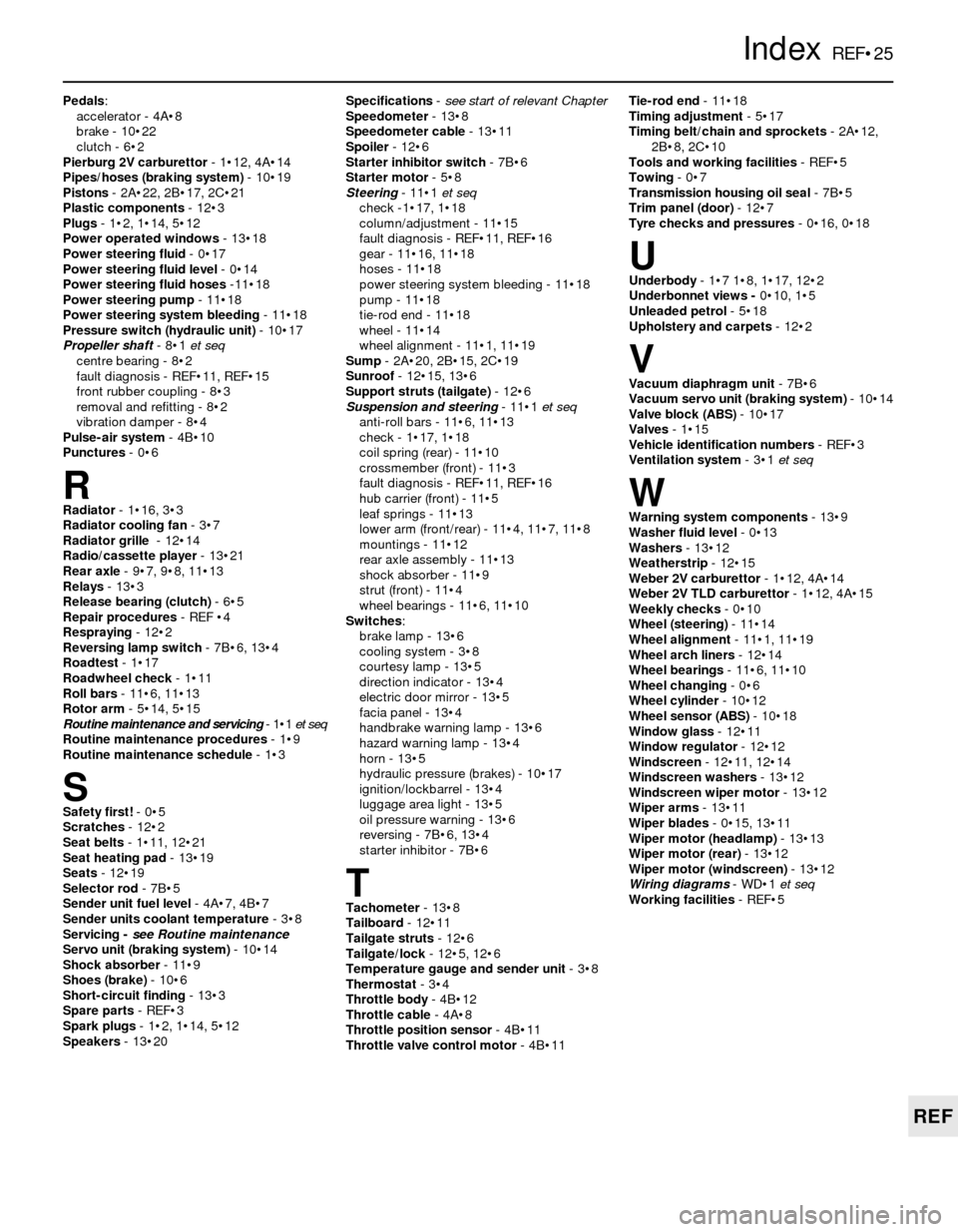
Pedals:
accelerator - 4A•8
brake - 10•22
clutch - 6•2
Pierburg 2V carburettor- 1•12, 4A•14
Pipes/hoses (braking system)- 10•19
Pistons- 2A•22, 2B•17, 2C•21
Plastic components- 12•3
Plugs- 1•2, 1•14, 5•12
Power operated windows- 13•18
Power steering fluid- 0•17
Power steering fluid level- 0•14
Power steering fluid hoses-11•18
Power steering pump- 11•18
Power steering system bleeding- 11•18
Pressure switch (hydraulic unit)- 10•17
Propeller shaft- 8•1 et seq
centre bearing - 8•2
fault diagnosis - REF•11, REF•15
front rubber coupling - 8•3
removal and refitting - 8•2
vibration damper - 8•4
Pulse-air system- 4B•10
Punctures- 0•6
RRadiator- 1•16, 3•3
Radiator cooling fan- 3•7
Radiator grille- 12•14
Radio/cassette player- 13•21
Rear axle- 9•7, 9•8, 11•13
Relays- 13•3
Release bearing (clutch)- 6•5
Repair procedures- REF •4
Respraying- 12•2
Reversing lamp switch- 7B•6, 13•4
Roadtest- 1•17
Roadwheel check- 1•11
Roll bars- 11•6, 11•13
Rotor arm- 5•14, 5•15
Routine maintenance and servicing- 1•1 et seq
Routine maintenance procedures- 1•9
Routine maintenance schedule- 1•3
SSafety first!- 0•5
Scratches- 12•2
Seat belts- 1•11, 12•21
Seat heating pad- 13•19
Seats- 12•19
Selector rod- 7B•5
Sender unit fuel level- 4A•7, 4B•7
Sender units coolant temperature- 3•8
Servicing -see Routine maintenance
Servo unit (braking system)- 10•14
Shock absorber- 11•9
Shoes (brake)- 10•6
Short-circuit finding- 13•3
Spare parts- REF•3
Spark plugs- 1•2, 1•14, 5•12
Speakers- 13•20Specifications- see start of relevant Chapter
Speedometer- 13•8
Speedometer cable- 13•11
Spoiler- 12•6
Starter inhibitor switch- 7B•6
Starter motor- 5•8
Steering- 11•1 et seq
check -1•17, 1•18
column/adjustment - 11•15
fault diagnosis - REF•11, REF•16
gear - 11•16, 11•18
hoses - 11•18
power steering system bleeding - 11•18
pump - 11•18
tie-rod end - 11•18
wheel - 11•14
wheel alignment - 11•1, 11•19
Sump- 2A•20, 2B•15, 2C•19
Sunroof- 12•15, 13•6
Support struts (tailgate)- 12•6
Suspension and steering- 11•1 et seq
anti-roll bars - 11•6, 11•13
check - 1•17, 1•18
coil spring (rear) - 11•10
crossmember (front) - 11•3
fault diagnosis - REF•11, REF•16
hub carrier (front) - 11•5
leaf springs - 11•13
lower arm (front/rear) - 11•4, 11•7, 11•8
mountings - 11•12
rear axle assembly - 11•13
shock absorber - 11•9
strut (front) - 11•4
wheel bearings - 11•6, 11•10
Switches:
brake lamp - 13•6
cooling system - 3•8
courtesy lamp - 13•5
direction indicator - 13•4
electric door mirror - 13•5
facia panel - 13•4
handbrake warning lamp - 13•6
hazard warning lamp - 13•4
horn - 13•5
hydraulic pressure (brakes) - 10•17
ignition/lockbarrel - 13•4
luggage area light - 13•5
oil pressure warning - 13•6
reversing - 7B•6, 13•4
starter inhibitor - 7B•6
TTachometer- 13•8
Tailboard- 12•11
Tailgate struts- 12•6
Tailgate/lock- 12•5, 12•6
Temperature gauge and sender unit- 3•8
Thermostat- 3•4
Throttle body- 4B•12
Throttle cable- 4A•8
Throttle position sensor- 4B•11
Throttle valve control motor- 4B•11Tie-rod end- 11•18
Timing adjustment- 5•17
Timing belt/chain and sprockets- 2A•12,
2B•8, 2C•10
Tools and working facilities- REF•5
Towing- 0•7
Transmission housing oil seal- 7B•5
Trim panel (door)- 12•7
Tyre checks and pressures- 0•16, 0•18
UUnderbody- 1•7 1•8, 1•17, 12•2
Underbonnet views -0•10, 1•5
Unleaded petrol- 5•18
Upholstery and carpets- 12•2
VVacuum diaphragm unit- 7B•6
Vacuum servo unit (braking system)- 10•14
Valve block (ABS)- 10•17
Valves- 1•15
Vehicle identification numbers- REF•3
Ventilation system- 3•1 et seq
WWarning system components- 13•9
Washer fluid level- 0•13
Washers- 13•12
Weatherstrip- 12•15
Weber 2V carburettor- 1•12, 4A•14
Weber 2V TLD carburettor- 1•12, 4A•15
Weekly checks- 0•10
Wheel (steering) - 11•14
Wheel alignment- 11•1, 11•19
Wheel arch liners- 12•14
Wheel bearings- 11•6, 11•10
Wheel changing- 0•6
Wheel cylinder- 10•12
Wheel sensor(ABS)- 10•18
Window glass- 12•11
Window regulator- 12•12
Windscreen- 12•11, 12•14
Windscreen washers- 13•12
Windscreen wiper motor- 13•12
Wiper arms- 13•11
Wiper blades- 0•15, 13•11
Wiper motor (headlamp)- 13•13
Wiper motor (rear)- 13•12
Wiper motor (windscreen)- 13•12
Wiring diagrams- WD•1 et seq
Working facilities- REF•5
IndexREF•25
REF