clock FORD SIERRA 1992 2.G SOHC Engines Workshop Manual
[x] Cancel search | Manufacturer: FORD, Model Year: 1992, Model line: SIERRA, Model: FORD SIERRA 1992 2.GPages: 24, PDF Size: 1.03 MB
Page 12 of 24
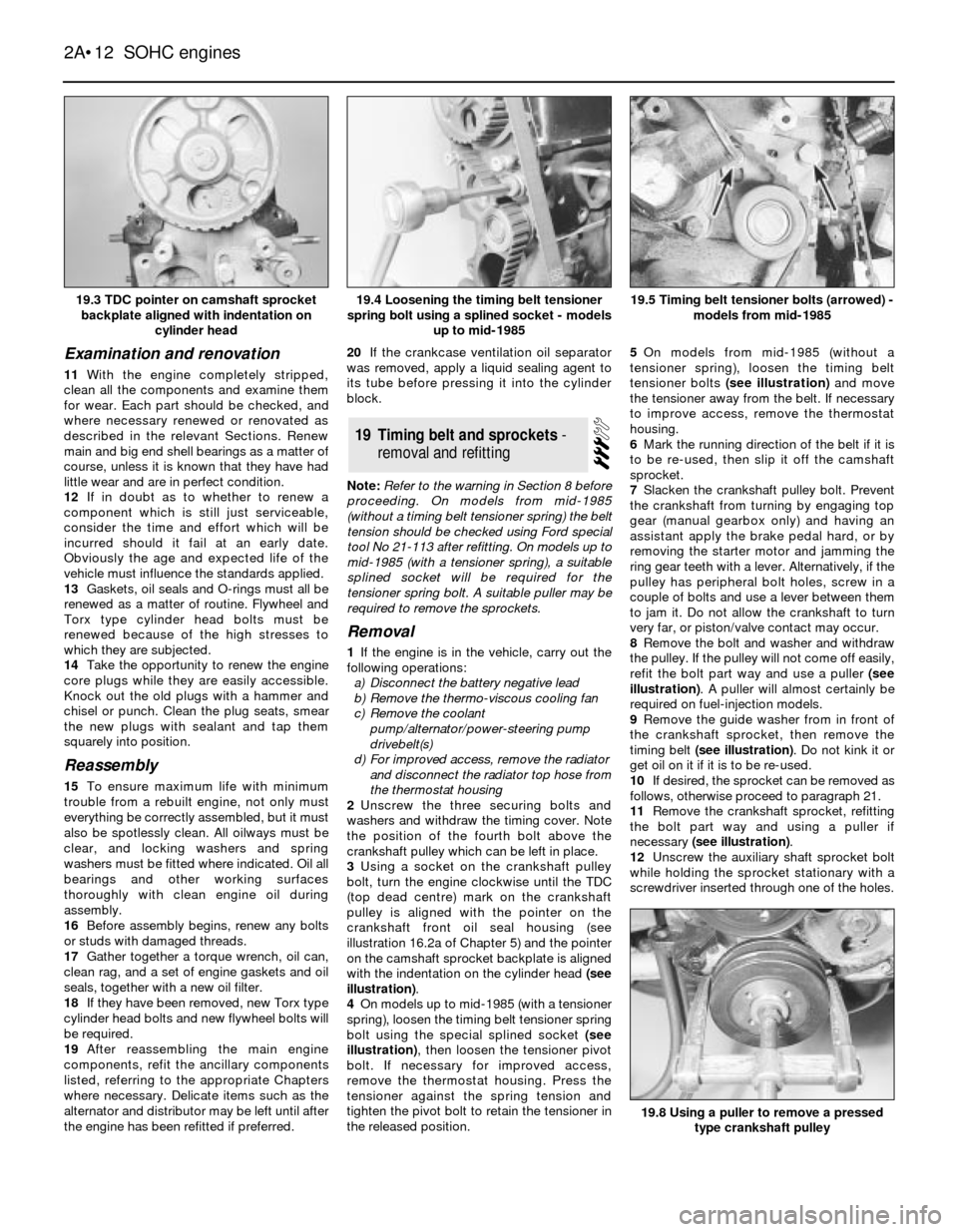
Examination and renovation
11With the engine completely stripped,
clean all the components and examine them
for wear. Each part should be checked, and
where necessary renewed or renovated as
described in the relevant Sections. Renew
main and big end shell bearings as a matter of
course, unless it is known that they have had
little wear and are in perfect condition.
12If in doubt as to whether to renew a
component which is still just serviceable,
consider the time and effort which will be
incurred should it fail at an early date.
Obviously the age and expected life of the
vehicle must influence the standards applied.
13Gaskets, oil seals and O-rings must all be
renewed as a matter of routine. Flywheel and
Torx type cylinder head bolts must be
renewed because of the high stresses to
which they are subjected.
14Take the opportunity to renew the engine
core plugs while they are easily accessible.
Knock out the old plugs with a hammer and
chisel or punch. Clean the plug seats, smear
the new plugs with sealant and tap them
squarely into position.
Reassembly
15To ensure maximum life with minimum
trouble from a rebuilt engine, not only must
everything be correctly assembled, but it must
also be spotlessly clean. All oilways must be
clear, and locking washers and spring
washers must be fitted where indicated. Oil all
bearings and other working surfaces
thoroughly with clean engine oil during
assembly.
16Before assembly begins, renew any bolts
or studs with damaged threads.
17Gather together a torque wrench, oil can,
clean rag, and a set of engine gaskets and oil
seals, together with a new oil filter.
18If they have been removed, new Torx type
cylinder head bolts and new flywheel bolts will
be required.
19After reassembling the main engine
components, refit the ancillary components
listed, referring to the appropriate Chapters
where necessary. Delicate items such as the
alternator and distributor may be left until after
the engine has been refitted if preferred.20If the crankcase ventilation oil separator
was removed, apply a liquid sealing agent to
its tube before pressing it into the cylinder
block.
Note: Refer to the warning in Section 8 before
proceeding. On models from mid-1985
(without a timing belt tensioner spring) the belt
tension should be checked using Ford special
tool No 21-113 after refitting. On models up to
mid-1985 (with a tensioner spring), a suitable
splined socket will be required for the
tensioner spring bolt. A suitable puller may be
required to remove the sprockets.
Removal
1If the engine is in the vehicle, carry out the
following operations:
a)Disconnect the battery negative lead
b)Remove the thermo-viscous cooling fan
c)Remove the coolant
pump/alternator/power-steering pump
drivebelt(s)
d)For improved access, remove the radiator
and disconnect the radiator top hose from
the thermostat housing
2Unscrew the three securing bolts and
washers and withdraw the timing cover. Note
the position of the fourth bolt above the
crankshaft pulley which can be left in place.
3Using a socket on the crankshaft pulley
bolt, turn the engine clockwise until the TDC
(top dead centre) mark on the crankshaft
pulley is aligned with the pointer on the
crankshaft front oil seal housing (see
illustration 16.2a of Chapter 5) and the pointer
on the camshaft sprocket backplate is aligned
with the indentation on the cylinder head (see
illustration).
4On models up to mid-1985 (with a tensioner
spring), loosen the timing belt tensioner spring
bolt using the special splined socket (see
illustration), then loosen the tensioner pivot
bolt. If necessary for improved access,
remove the thermostat housing. Press the
tensioner against the spring tension and
tighten the pivot bolt to retain the tensioner in
the released position.5On models from mid-1985 (without a
tensioner spring), loosen the timing belt
tensioner bolts (see illustration)and move
the tensioner away from the belt. If necessary
to improve access, remove the thermostat
housing.
6Mark the running direction of the belt if it is
to be re-used, then slip it off the camshaft
sprocket.
7Slacken the crankshaft pulley bolt. Prevent
the crankshaft from turning by engaging top
gear (manual gearbox only) and having an
assistant apply the brake pedal hard, or by
removing the starter motor and jamming the
ring gear teeth with a lever. Alternatively, if the
pulley has peripheral bolt holes, screw in a
couple of bolts and use a lever between them
to jam it. Do not allow the crankshaft to turn
very far, or piston/valve contact may occur.
8Remove the bolt and washer and withdraw
the pulley. If the pulley will not come off easily,
refit the bolt part way and use a puller (see
illustration). A puller will almost certainly be
required on fuel-injection models.
9Remove the guide washer from in front of
the crankshaft sprocket, then remove the
timing belt (see illustration). Do not kink it or
get oil on it if it is to be re-used.
10If desired, the sprocket can be removed as
follows, otherwise proceed to paragraph 21.
11Remove the crankshaft sprocket, refitting
the bolt part way and using a puller if
necessary (see illustration).
12Unscrew the auxiliary shaft sprocket bolt
while holding the sprocket stationary with a
screwdriver inserted through one of the holes.
19Timing belt and sprockets -
removal and refitting
2A¥12SOHC engines
19.3 TDC pointer on camshaft sprocket
backplate aligned with indentation on
cylinder head19.5 Timing belt tensioner bolts (arrowed) -
models from mid-1985
19.8 Using a puller to remove a pressed
type crankshaft pulley
19.4 Loosening the timing belt tensioner
spring bolt using a splined socket - models
up to mid-1985
Page 13 of 24
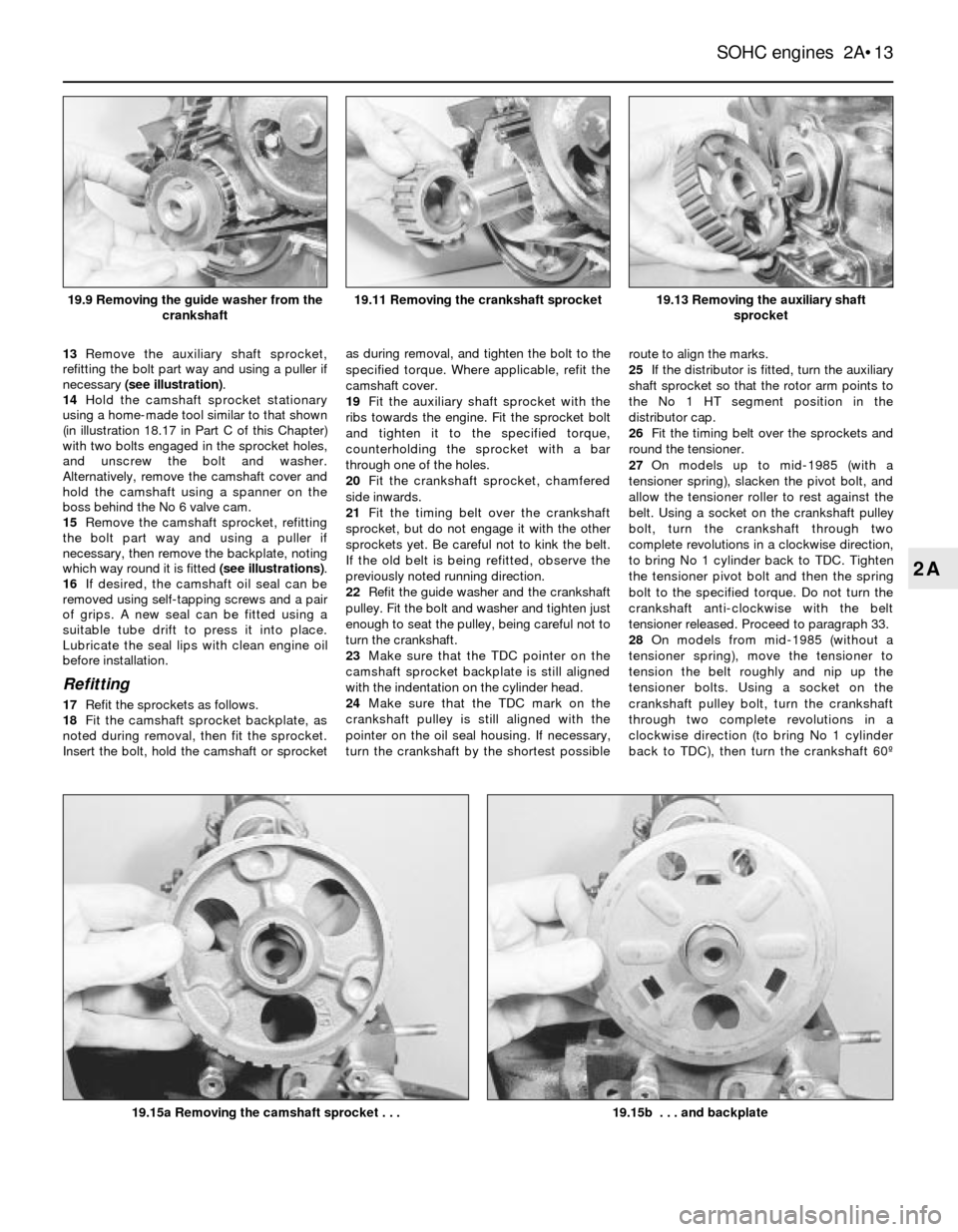
13Remove the auxiliary shaft sprocket,
refitting the bolt part way and using a puller if
necessary (see illustration).
14Hold the camshaft sprocket stationary
using a home-made tool similar to that shown
(in illustration 18.17 in Part C of this Chapter)
with two bolts engaged in the sprocket holes,
and unscrew the bolt and washer.
Alternatively, remove the camshaft cover and
hold the camshaft using a spanner on the
boss behind the No 6 valve cam.
15Remove the camshaft sprocket, refitting
the bolt part way and using a puller if
necessary, then remove the backplate, noting
which way round it is fitted (see illustrations).
16If desired, the camshaft oil seal can be
removed using self-tapping screws and a pair
of grips. A new seal can be fitted using a
suitable tube drift to press it into place.
Lubricate the seal lips with clean engine oil
before installation.
Refitting
17Refit the sprockets as follows.
18Fit the camshaft sprocket backplate, as
noted during removal, then fit the sprocket.
Insert the bolt, hold the camshaft or sprocketas during removal, and tighten the bolt to the
specified torque. Where applicable, refit the
camshaft cover.
19Fit the auxiliary shaft sprocket with the
ribs towards the engine. Fit the sprocket bolt
and tighten it to the specified torque,
counterholding the sprocket with a bar
through one of the holes.
20Fit the crankshaft sprocket, chamfered
side inwards.
21Fit the timing belt over the crankshaft
sprocket, but do not engage it with the other
sprockets yet. Be careful not to kink the belt.
If the old belt is being refitted, observe the
previously noted running direction.
22Refit the guide washer and the crankshaft
pulley. Fit the bolt and washer and tighten just
enough to seat the pulley, being careful not to
turn the crankshaft.
23Make sure that the TDC pointer on the
camshaft sprocket backplate is still aligned
with the indentation on the cylinder head.
24Make sure that the TDC mark on the
crankshaft pulley is still aligned with the
pointer on the oil seal housing. If necessary,
turn the crankshaft by the shortest possibleroute to align the marks.
25If the distributor is fitted, turn the auxiliary
shaft sprocket so that the rotor arm points to
the No 1 HT segment position in the
distributor cap.
26Fit the timing belt over the sprockets and
round the tensioner.
27On models up to mid-1985 (with a
tensioner spring), slacken the pivot bolt, and
allow the tensioner roller to rest against the
belt. Using a socket on the crankshaft pulley
bolt, turn the crankshaft through two
complete revolutions in a clockwise direction,
to bring No 1 cylinder back to TDC. Tighten
the tensioner pivot bolt and then the spring
bolt to the specified torque. Do not turn the
crankshaft anti-clockwise with the belt
tensioner released. Proceed to paragraph 33.
28On models from mid-1985 (without a
tensioner spring), move the tensioner to
tension the belt roughly and nip up the
tensioner bolts. Using a socket on the
crankshaft pulley bolt, turn the crankshaft
through two complete revolutions in a
clockwise direction (to bring No 1 cylinder
back to TDC), then turn the crankshaft 60¼
SOHC engines 2A¥13
2A
19.13 Removing the auxiliary shaft
sprocket
19.15b . . . and backplate19.15a Removing the camshaft sprocket . . .
19.11 Removing the crankshaft sprocket19.9 Removing the guide washer from the
crankshaft
Page 14 of 24
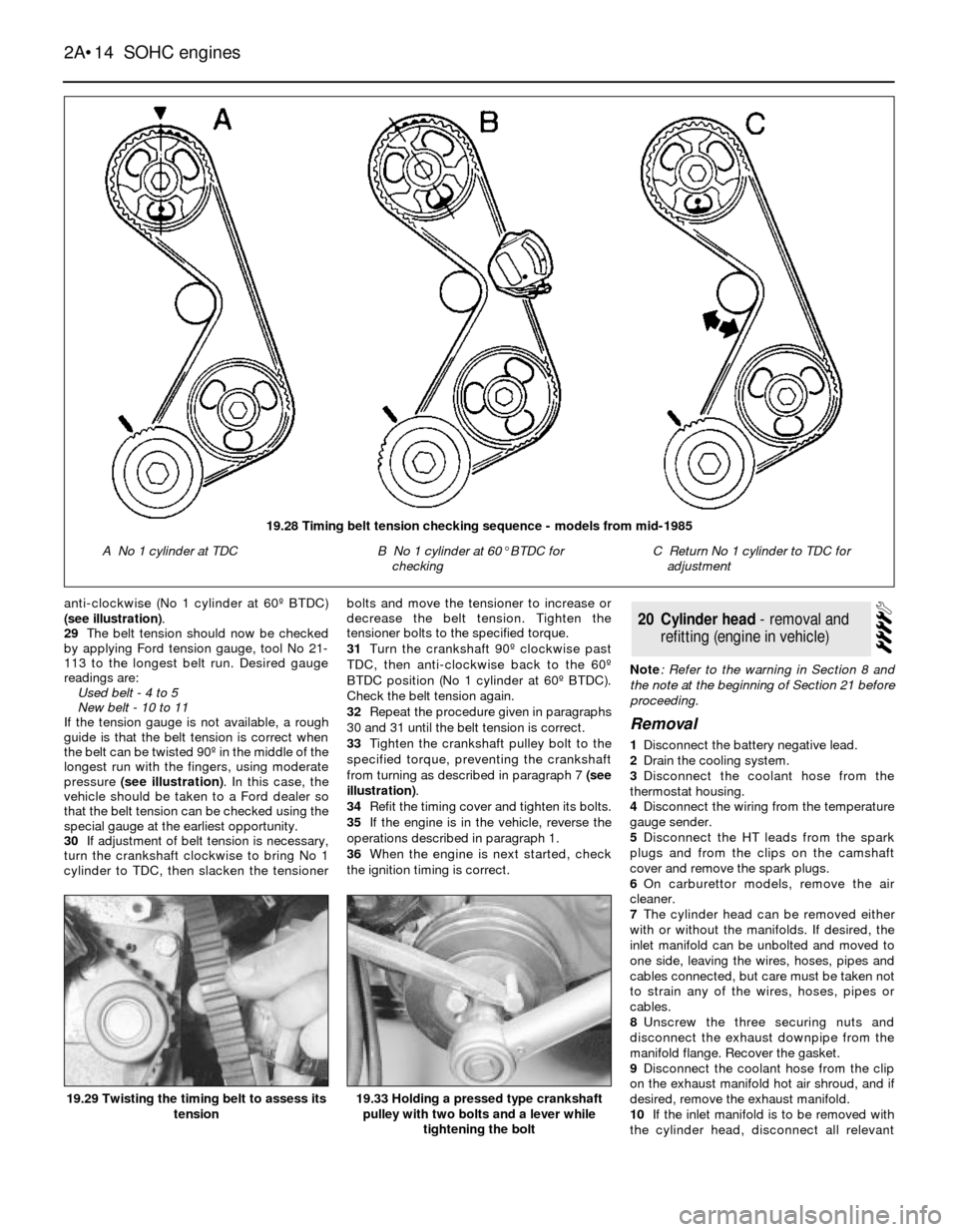
anti-clockwise (No 1 cylinder at 60¼ BTDC)
(see illustration).
29The belt tension should now be checked
by applying Ford tension gauge, tool No 21-
113 to the longest belt run. Desired gauge
readings are:
Used belt - 4 to 5
New belt - 10 to 11
If the tension gauge is not available, a rough
guide is that the belt tension is correct when
the belt can be twisted 90¼ in the middle of the
longest run with the fingers, using moderate
pressure (see illustration). In this case, the
vehicle should be taken to a Ford dealer so
that the belt tension can be checked using the
special gauge at the earliest opportunity.
30If adjustment of belt tension is necessary,
turn the crankshaft clockwise to bring No 1
cylinder to TDC, then slacken the tensionerbolts and move the tensioner to increase or
decrease the belt tension. Tighten the
tensioner bolts to the specified torque.
31Turn the crankshaft 90¼ clockwise past
TDC, then anti-clockwise back to the 60¼
BTDC position (No 1 cylinder at 60¼ BTDC).
Check the belt tension again.
32Repeat the procedure given in paragraphs
30 and 31 until the belt tension is correct.
33Tighten the crankshaft pulley bolt to the
specified torque, preventing the crankshaft
from turning as described in paragraph 7 (see
illustration).
34Refit the timing cover and tighten its bolts.
35If the engine is in the vehicle, reverse the
operations described in paragraph 1.
36When the engine is next started, check
the ignition timing is correct.Note: Refer to the warning in Section 8 and
the note at the beginning of Section 21 before
proceeding.
Removal
1Disconnect the battery negative lead.
2Drain the cooling system.
3Disconnect the coolant hose from the
thermostat housing.
4Disconnect the wiring from the temperature
gauge sender.
5Disconnect the HT leads from the spark
plugs and from the clips on the camshaft
cover and remove the spark plugs.
6On carburettor models, remove the air
cleaner.
7The cylinder head can be removed either
with or without the manifolds. If desired, the
inlet manifold can be unbolted and moved to
one side, leaving the wires, hoses, pipes and
cables connected, but care must be taken not
to strain any of the wires, hoses, pipes or
cables.
8Unscrew the three securing nuts and
disconnect the exhaust downpipe from the
manifold flange. Recover the gasket.
9Disconnect the coolant hose from the clip
on the exhaust manifold hot air shroud, and if
desired, remove the exhaust manifold.
10If the inlet manifold is to be removed with
the cylinder head, disconnect all relevant
20Cylinder head - removal and
refitting (engine in vehicle)
2A¥14SOHC engines
19.33 Holding a pressed type crankshaft
pulley with two bolts and a lever while
tightening the bolt19.29 Twisting the timing belt to assess its
tension
19.28 Timing belt tension checking sequence - models from mid-1985
A No 1 cylinder at TDCB No 1 cylinder at 60¡BTDC for
checkingC Return No 1 cylinder to TDC for
adjustment
Page 21 of 24
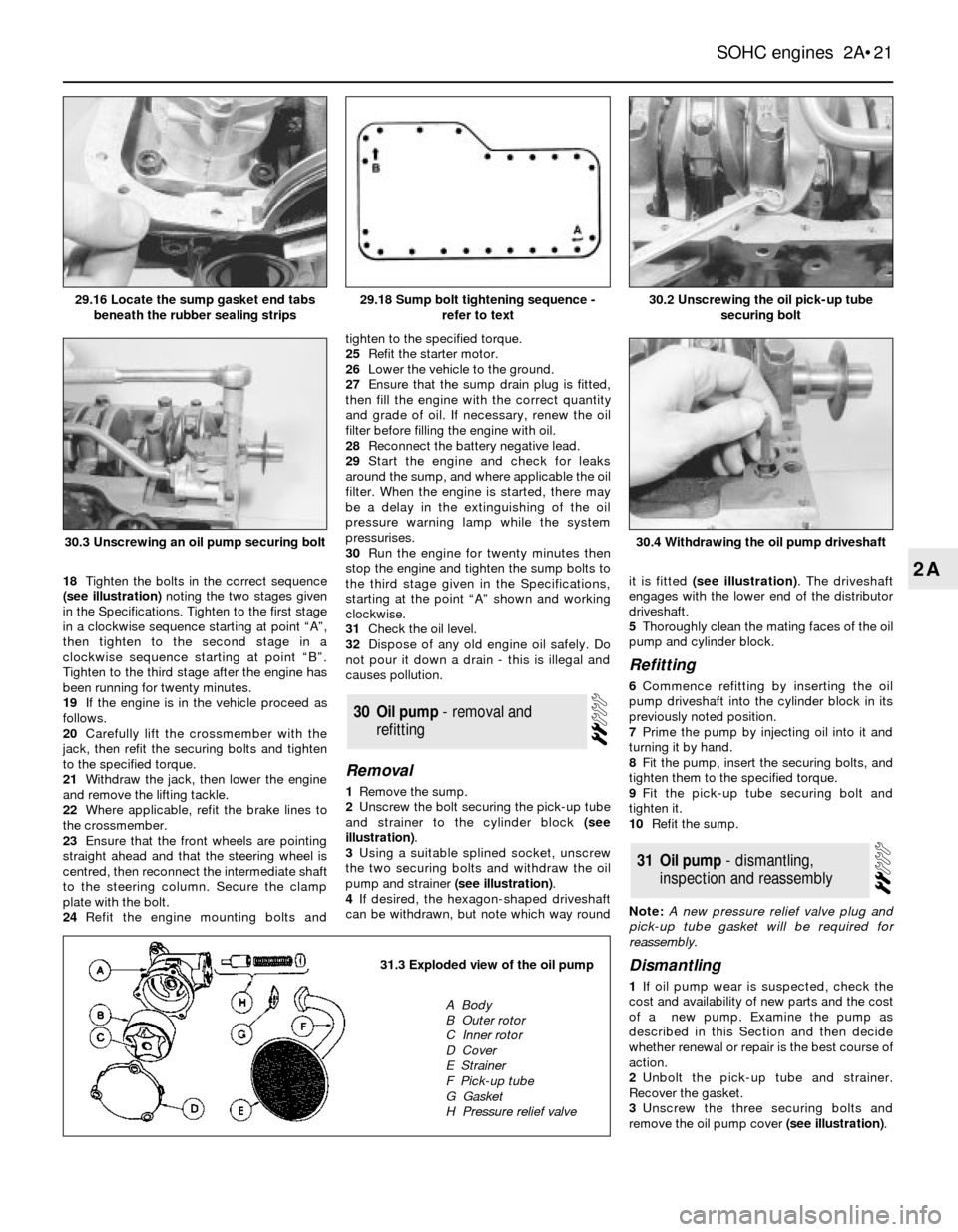
18Tighten the bolts in the correct sequence
(see illustration)noting the two stages given
in the Specifications. Tighten to the first stage
in a clockwise sequence starting at point ÒAÓ,
then tighten to the second stage in a
clockwise sequence starting at point ÒBÓ.
Tighten to the third stage after the engine has
been running for twenty minutes.
19If the engine is in the vehicle proceed as
follows.
20Carefully lift the crossmember with the
jack, then refit the securing bolts and tighten
to the specified torque.
21Withdraw the jack, then lower the engine
and remove the lifting tackle.
22Where applicable, refit the brake lines to
the crossmember.
23Ensure that the front wheels are pointing
straight ahead and that the steering wheel is
centred, then reconnect the intermediate shaft
to the steering column. Secure the clamp
plate with the bolt.
24Refit the engine mounting bolts andtighten to the specified torque.
25Refit the starter motor.
26Lower the vehicle to the ground.
27Ensure that the sump drain plug is fitted,
then fill the engine with the correct quantity
and grade of oil. If necessary, renew the oil
filter before filling the engine with oil.
28Reconnect the battery negative lead.
29Start the engine and check for leaks
around the sump, and where applicable the oil
filter. When the engine is started, there may
be a delay in the extinguishing of the oil
pressure warning lamp while the system
pressurises.
30Run the engine for twenty minutes then
stop the engine and tighten the sump bolts to
the third stage given in the Specifications,
starting at the point ÒAÓ shown and working
clockwise.
31Check the oil level.
32Dispose of any old engine oil safely. Do
not pour it down a drain - this is illegal and
causes pollution.
Removal
1Remove the sump.
2Unscrew the bolt securing the pick-up tube
and strainer to the cylinder block (see
illustration).
3Using a suitable splined socket, unscrew
the two securing bolts and withdraw the oil
pump and strainer (see illustration).
4If desired, the hexagon-shaped driveshaft
can be withdrawn, but note which way roundit is fitted (see illustration). The driveshaft
engages with the lower end of the distributor
driveshaft.
5Thoroughly clean the mating faces of the oil
pump and cylinder block.
Refitting
6Commence refitting by inserting the oil
pump driveshaft into the cylinder block in its
previously noted position.
7Prime the pump by injecting oil into it and
turning it by hand.
8Fit the pump, insert the securing bolts, and
tighten them to the specified torque.
9Fit the pick-up tube securing bolt and
tighten it.
10Refit the sump.
Note: A new pressure relief valve plug and
pick-up tube gasket will be required for
reassembly.
Dismantling
1If oil pump wear is suspected, check the
cost and availability of new parts and the cost
of a new pump. Examine the pump as
described in this Section and then decide
whether renewal or repair is the best course of
action.
2Unbolt the pick-up tube and strainer.
Recover the gasket.
3Unscrew the three securing bolts and
remove the oil pump cover (see illustration).
31Oil pump - dismantling,
inspection and reassembly
30Oil pump - removal and
refitting
SOHC engines 2A¥21
2A
30.2 Unscrewing the oil pick-up tube
securing bolt
30.4 Withdrawing the oil pump driveshaft30.3 Unscrewing an oil pump securing bolt
29.18 Sump bolt tightening sequence -
refer to text29.16 Locate the sump gasket end tabs
beneath the rubber sealing strips
31.3 Exploded view of the oil pump
A Body
B Outer rotor
C Inner rotor
D Cover
E Strainer
F Pick-up tube
G Gasket
H Pressure relief valve