check engine light GEELY FC 2008 Workshop Manual
[x] Cancel search | Manufacturer: GEELY, Model Year: 2008, Model line: FC, Model: GEELY FC 2008Pages: 419, PDF Size: 13.87 MB
Page 20 of 419
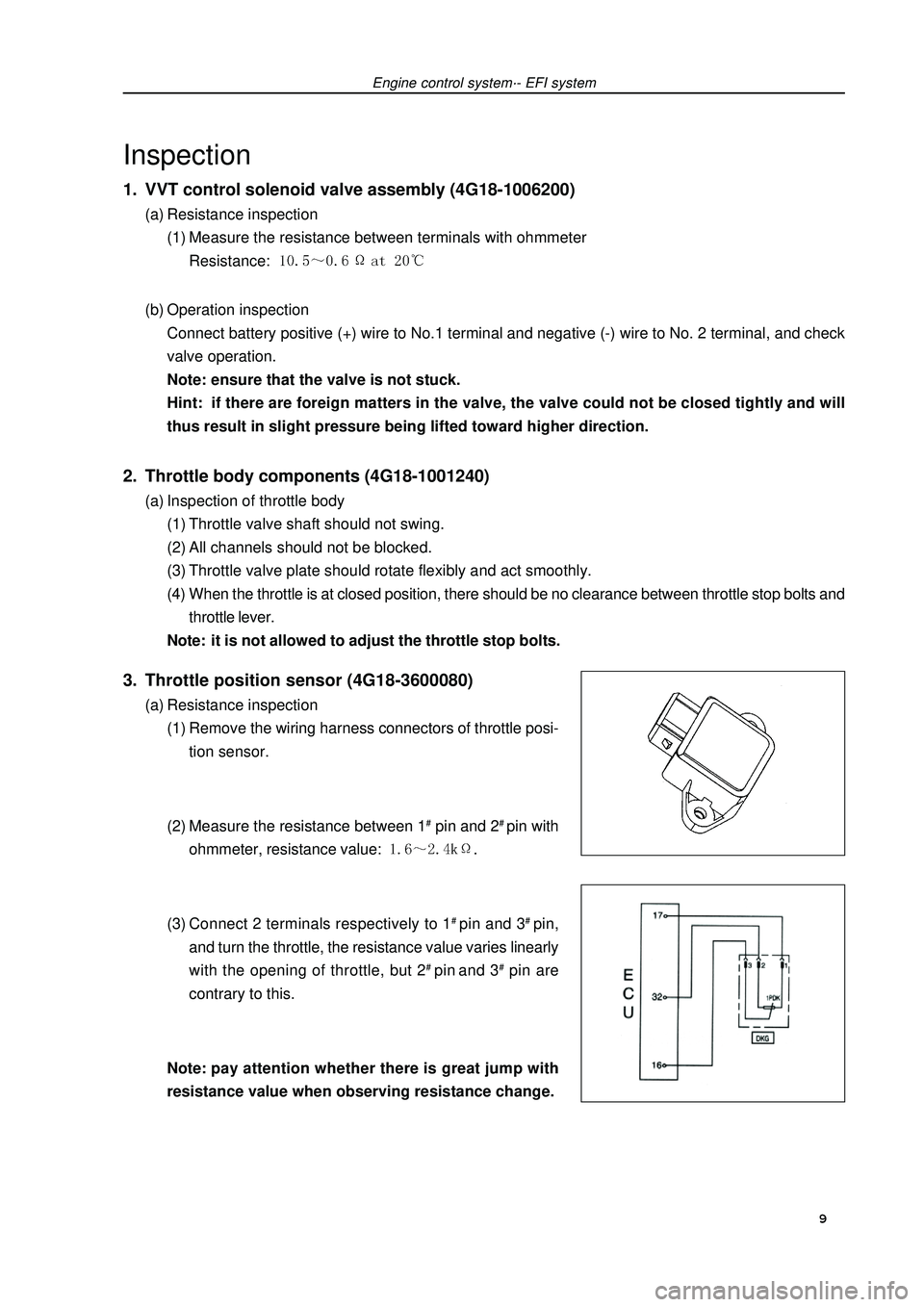
Engine control system·- EFI systemInspection1. VVT control solenoid valve assembly (4G18-1006200)(a) Resistance inspection
(1) Measure the resistance between terminals with ohmmeter
Resistance: (b) Operation inspection
Connect battery positive (+) wire to No.1 terminal and negative (-) wire to No. 2 terminal, and check
valve operation.
Note: ensure that the valve is not stuck.
Hint: if there are foreign matters in the valve, the valve could not be closed tightly and will
thus result in slight pressure being lifted toward higher direction.2. Throttle body components (4G18-1001240)(a) Inspection of throttle body
(1) Throttle valve shaft should not swing.
(2) All channels should not be blocked.
(3) Throttle valve plate should rotate flexibly and act smoothly.
(4) When the throttle is at closed position, there should be no clearance between throttle stop bolts and
throttle lever.
Note: it is not allowed to adjust the throttle stop bolts.3. Throttle position sensor (4G18-3600080)(a) Resistance inspection
(1) Remove the wiring harness connectors of throttle posi-
tion sensor.
(2) Measure the resistance between 1# pin and 2# pin with
ohmmeter, resistance value: .
(3) Connect 2 terminals respectively to 1# pin and 3# pin,
and turn the throttle, the resistance value varies linearly
with the opening of throttle, but 2# pin and 3# pin are
contrary to this.
Note:pay attention whether there is great jump with
resistance value when observing resistance change. 9
Page 93 of 419
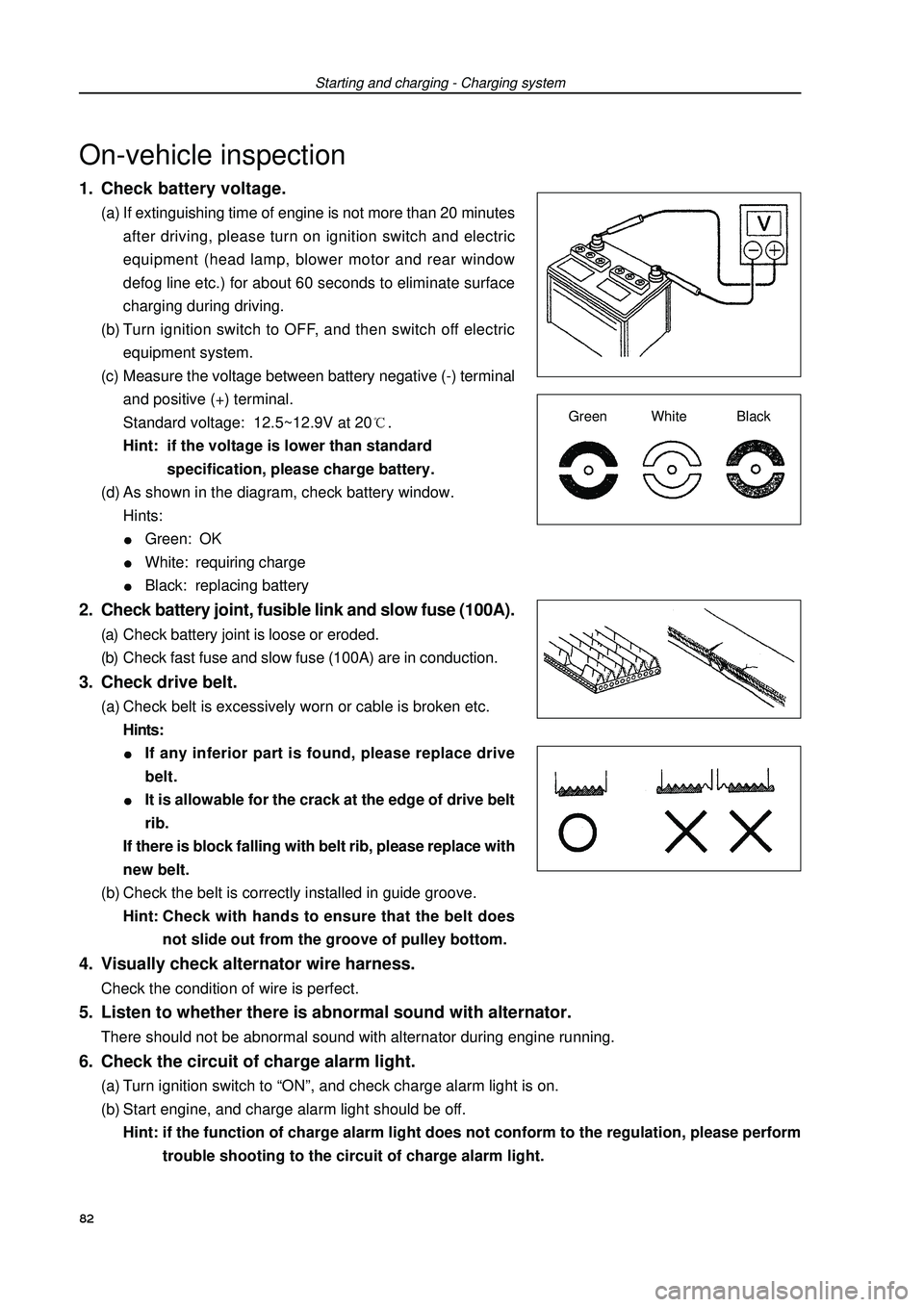
1. Check battery voltage.(a) If extinguishing time of engine is not more than 20 minutes
after driving, please turn on ignition switch and electric
equipment (head lamp, blower motor and rear window
defog line etc.) for about 60 seconds to eliminate surface
charging during driving.
(b) Turn ignition switch to OFF, and then switch off electric
equipment system.
(c) Measure the voltage between battery negative (-) terminal
and positive (+) terminal.
Standard voltage: 12.5~12.9V at 20.
Hint: if the voltage is lower than standard
specification, please charge battery.
(d) As shown in the diagram, check battery window.
Hints:Green: OKWhite: requiring chargeBlack: replacing battery2. Check battery joint, fusible link and slow fuse (100A).(a) Check battery joint is loose or eroded.
(b) Check fast fuse and slow fuse (100A) are in conduction.3. Check drive belt.(a) Check belt is excessively worn or cable is broken etc.
Hints:If any inferior part is found, please replace drive
belt.It is allowable for the crack at the edge of drive belt
rib.
If there is block falling with belt rib, please replace with
new belt.
(b) Check the belt is correctly installed in guide groove.
Hint:Check with hands to ensure that the belt does
not slide out from the groove of pulley bottom.4. Visually check alternator wire harness.Check the condition of wire is perfect.Starting and charging - Charging systemOn-vehicle inspectionGreen White Black5. Listen to whether there is abnormal sound with alternator.There should not be abnormal sound with alternator during engine running.6. Check the circuit of charge alarm light.(a) Turn ignition switch to “ON”, and check charge alarm light is on.
(b) Start engine, and charge alarm light should be off.
Hint: if the function of charge alarm light does not conform to the regulation, please perform
trouble shooting to the circuit of charge alarm light.82
Page 147 of 419
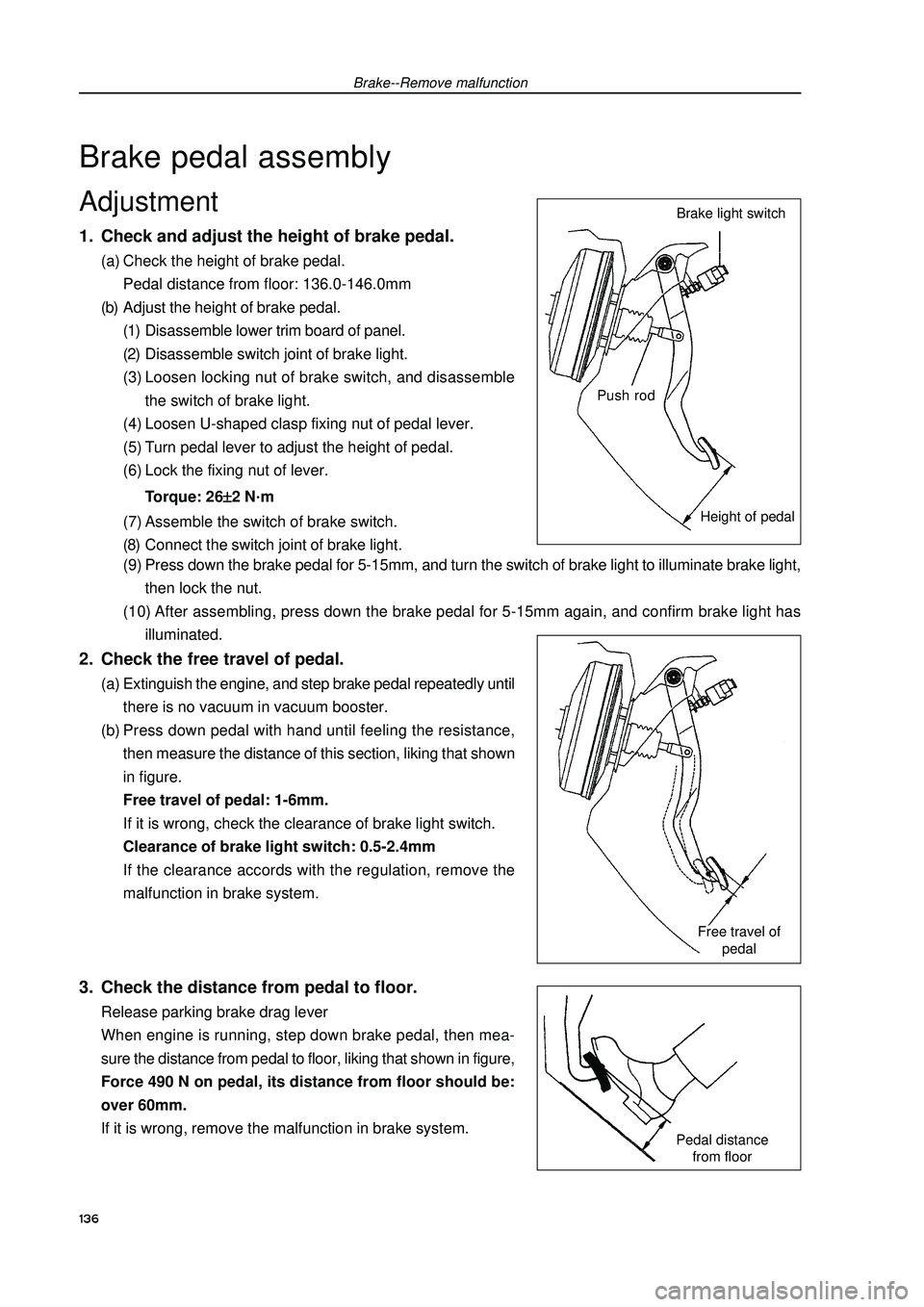
Brake--Remove malfunction2. Check the free travel of pedal.(a) Extinguish the engine, and step brake pedal repeatedly until
there is no vacuum in vacuum booster.
(b) Press down pedal with hand until feeling the resistance,
then measure the distance of this section, liking that shown
in figure.
Free travel of pedal: 1-6mm.
If it is wrong, check the clearance of brake light switch.
Clearance of brake light switch: 0.5-2.4mm
If the clearance accords with the regulation, remove the
malfunction in brake system.3. Check the distance from pedal to floor.Release parking brake drag lever
When engine is running, step down brake pedal, then mea-
sure the distance from pedal to floor, liking that shown in figure,
Force 490 N on pedal, its distance from floor should be:
over 60mm.
If it is wrong, remove the malfunction in brake system.Brake pedal assemblyAdjustment1. Check and adjust the height of brake pedal.(a) Check the height of brake pedal.
Pedal distance from floor: 136.0-146.0mm
(b) Adjust the height of brake pedal.
(1) Disassemble lower trim board of panel.
(2) Disassemble switch joint of brake light.
(3) Loosen locking nut of brake switch, and disassemble
the switch of brake light.
(4) Loosen U-shaped clasp fixing nut of pedal lever.
(5) Turn pedal lever to adjust the height of pedal.
(6) Lock the fixing nut of lever.
Torque: 26
± ±± ±
±2 N⋅ ⋅⋅ ⋅
⋅m
(7) Assemble the switch of brake switch.
(8) Connect the switch joint of brake light.
(9) Press down the brake pedal for 5-15mm, and turn the switch of brake light to illuminate brake light,
then lock the nut.
(10) After assembling, press down the brake pedal for 5-15mm again, and confirm brake light has
illuminated.Pedal distance
from floorFree travel of
pedal Height of pedal Push rodBrake light switch136
Page 211 of 419
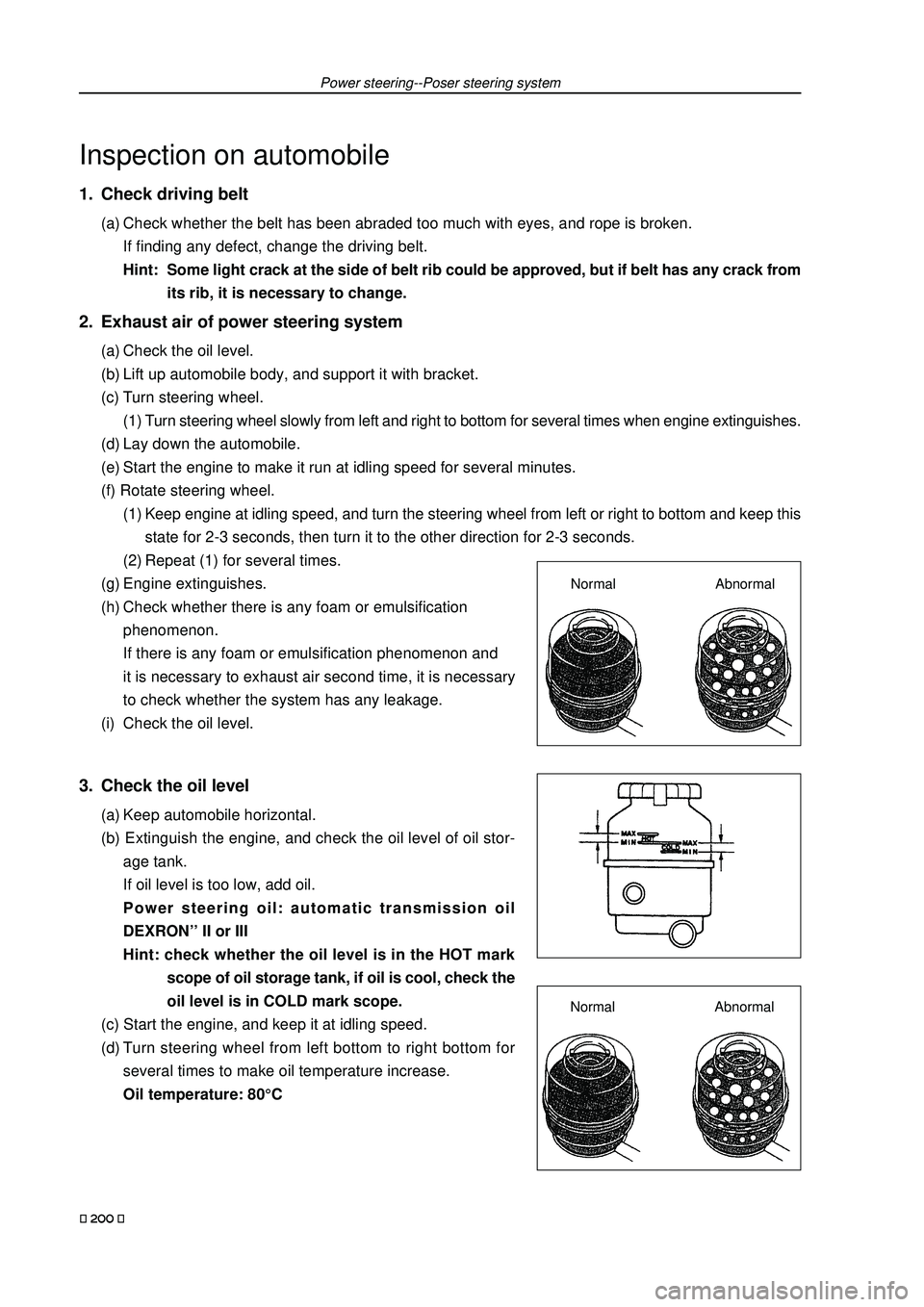
Power steering--Poser steering system
Inspection on automobile
1. Check driving belt
(a) Check whether the belt has been abraded too much with eyes, and rope is broken.
If finding any defect, change the driving belt.
Hint: Some light crack at the side of belt rib could be approved, but if belt has any crack from
its rib, it is necessary to change.
2. Exhaust air of power steering system
(a) Check the oil level.
(b) Lift up automobile body, and support it with bracket.
(c) Turn steering wheel.
(1) Turn steering wheel slowly from left and right to bottom for several times when engine extinguishes.
(d) Lay down the automobile.
(e) Start the engine to make it run at idling speed for several minutes.
(f) Rotate steering wheel.
(1) Keep engine at idling speed, and turn the steering wheel from left or right to bottom and keep this
state for 2-3 seconds, then turn it to the other direction for 2-3 seconds.
(2) Repeat (1) for several times.
(g) Engine extinguishes.
(h) Check whether there is any foam or emulsification
phenomenon.
If there is any foam or emulsification phenomenon and
it is necessary to exhaust air second time, it is necessary
to check whether the system has any leakage.
(i) Check the oil level.
3. Check the oil level
(a) Keep automobile horizontal.
(b) Extinguish the engine, and check the oil level of oil stor-
age tank.
If oil level is too low, add oil.
Power steering oil: automatic transmission oil
DEXRON’’ II or III
Hint: check whether the oil level is in the HOT mark
scope of oil storage tank, if oil is cool, check the
oil level is in COLD mark scope.
(c) Start the engine, and keep it at idling speed.
(d) Turn steering wheel from left bottom to right bottom for
several times to make oil temperature increase.
Oil temperature: 80°C
Normal Abnormal
200
Normal Abnormal
Page 244 of 419
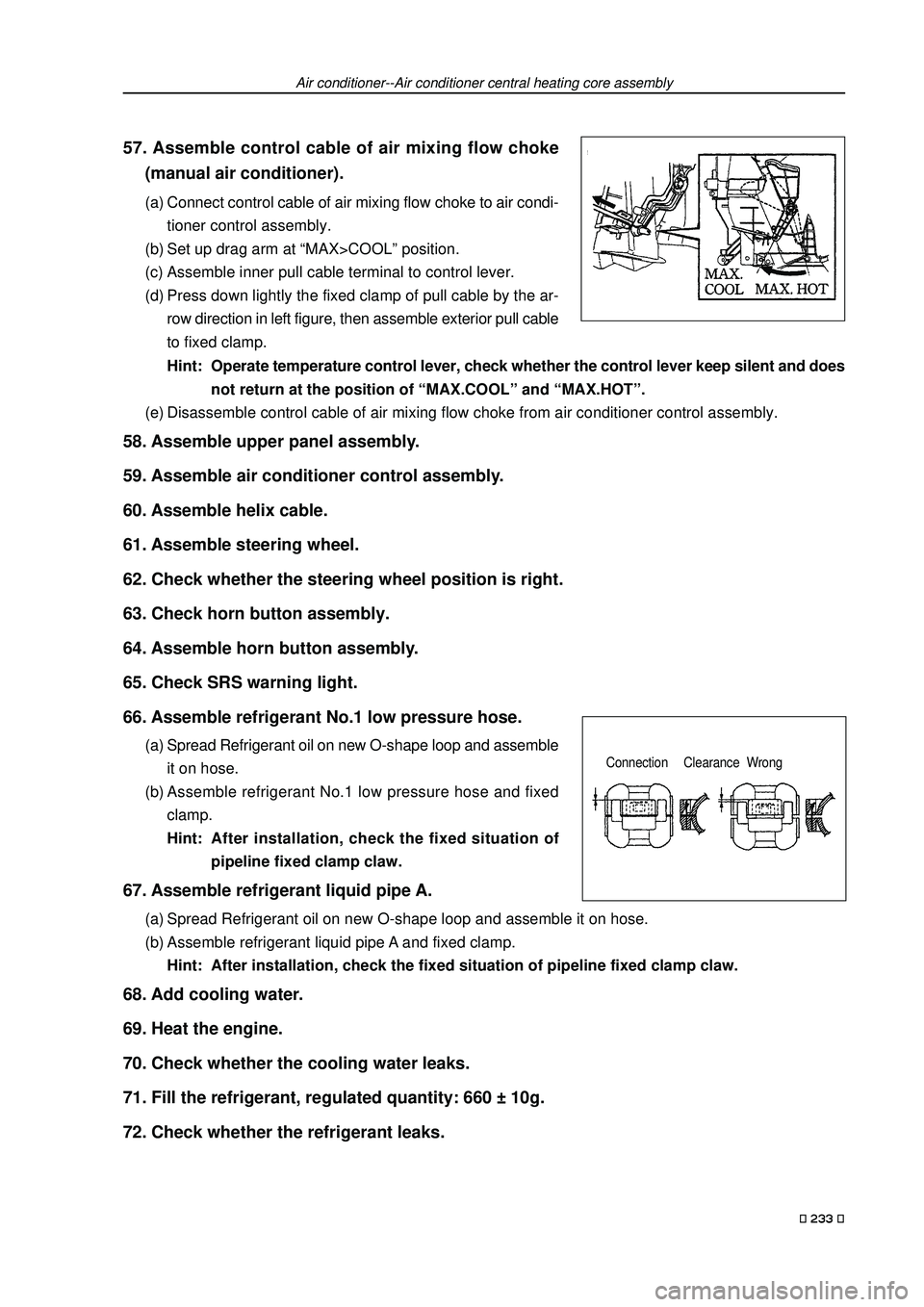
57. Assemble control cable of air mixing flow choke
(manual air conditioner).
(a) Connect control cable of air mixing flow choke to air condi-
tioner control assembly.
(b) Set up drag arm at “MAX>COOL” position.
(c) Assemble inner pull cable terminal to control lever.
(d) Press down lightly the fixed clamp of pull cable by the ar-
row direction in left figure, then assemble exterior pull cable
to fixed clamp.
Air conditioner--Air conditioner central heating core assembly
Connection Clearance Wrong
233
Hint:Operate temperature control lever, check whether the control lever keep silent and does
not return at the position of “MAX.COOL” and “MAX.HOT”.
(e) Disassemble control cable of air mixing flow choke from air conditioner control assembly.
58. Assemble upper panel assembly.
59. Assemble air conditioner control assembly.
60. Assemble helix cable.
61. Assemble steering wheel.
62. Check whether the steering wheel position is right.
63. Check horn button assembly.
64. Assemble horn button assembly.
65. Check SRS warning light.
66. Assemble refrigerant No.1 low pressure hose.
(a) Spread Refrigerant oil on new O-shape loop and assemble
it on hose.
(b) Assemble refrigerant No.1 low pressure hose and fixed
clamp.
Hint:After installation, check the fixed situation of
pipeline fixed clamp claw.
67. Assemble refrigerant liquid pipe A.
(a) Spread Refrigerant oil on new O-shape loop and assemble it on hose.
(b) Assemble refrigerant liquid pipe A and fixed clamp.
Hint: After installation, check the fixed situation of pipeline fixed clamp claw.
68. Add cooling water.
69. Heat the engine.
70. Check whether the cooling water leaks.
71. Fill the refrigerant, regulated quantity: 660 ± 10g.
72. Check whether the refrigerant leaks.
Page 270 of 419
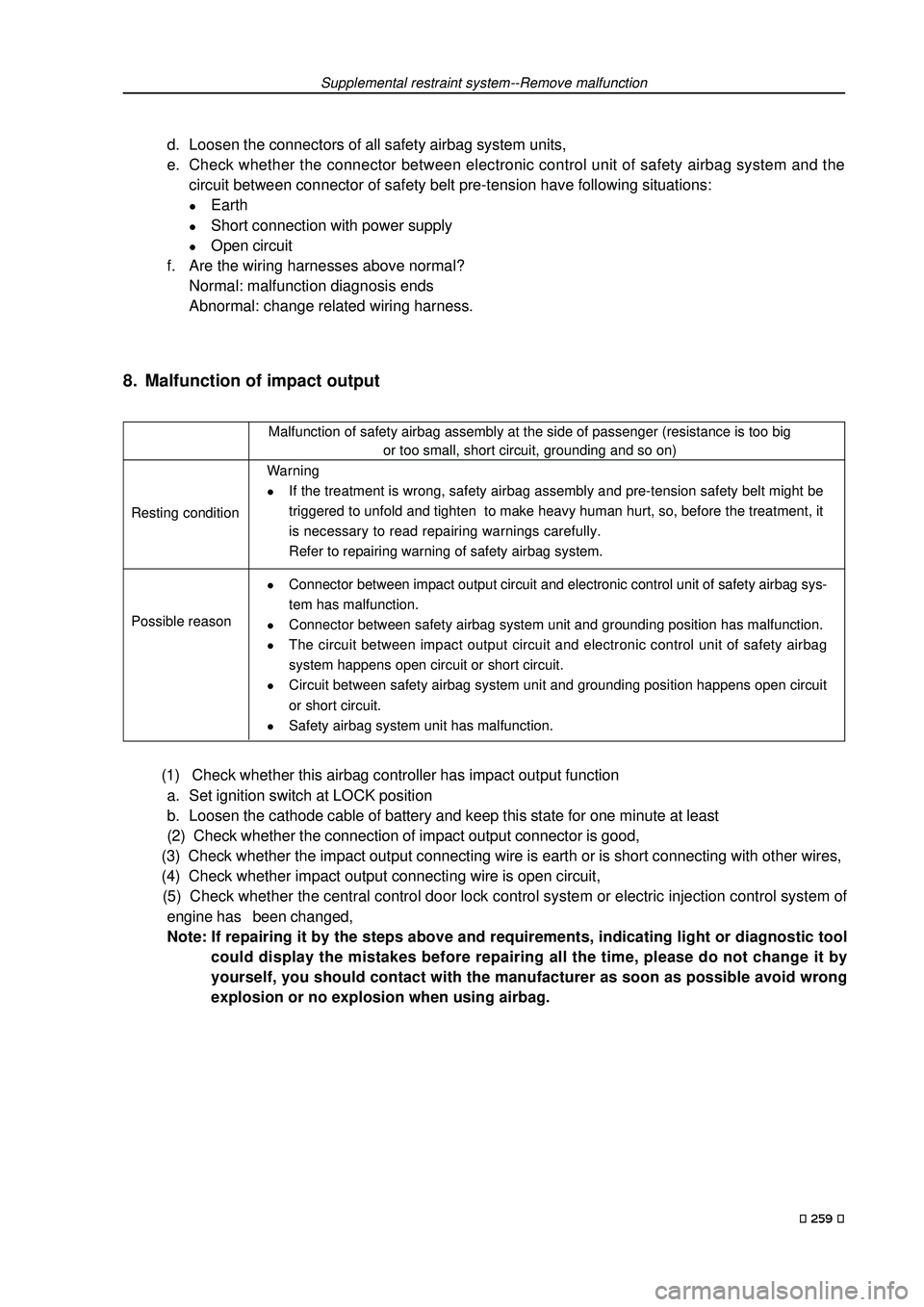
d. Loosen the connectors of all safety airbag system units,
e. Check whether the connector between electronic control unit of safety airbag system and the
circuit between connector of safety belt pre-tension have following situations:
zEarth
zShort connection with power supply
zOpen circuit
f. Are the wiring harnesses above normal?
Normal: malfunction diagnosis ends
Abnormal: change related wiring harness.
8. Malfunction of impact output
Malfunction of safety airbag assembly at the side of passenger (resistance is too big
or too small, short circuit, grounding and so on)
Resting conditionWarning
zIf the treatment is wrong, safety airbag assembly and pre-tension safety belt might be
triggered to unfold and tighten to make heavy human hurt, so, before the treatment, it
is necessary to read repairing warnings carefully.
Refer to repairing warning of safety airbag system.
Possible reason
zConnector between impact output circuit and electronic control unit of safety airbag sys-
tem has malfunction.
zConnector between safety airbag system unit and grounding position has malfunction.
zThe circuit between impact output circuit and electronic control unit of safety airbag
system happens open circuit or short circuit.
zCircuit between safety airbag system unit and grounding position happens open circuit
or short circuit.
zSafety airbag system unit has malfunction.
(1) Check whether this airbag controller has impact output function
a. Set ignition switch at LOCK position
b. Loosen the cathode cable of battery and keep this state for one minute at least
(2) Check whether the connection of impact output connector is good,
(3) Check whether the impact output connecting wire is earth or is short connecting with other wires,
(4) Check whether impact output connecting wire is open circuit,
(5) Check whether the central control door lock control system or electric injection control system of
engine has been changed,
Note: If repairing it by the steps above and requirements, indicating light or diagnostic tool
could display the mistakes before repairing all the time, please do not change it by
yourself, you should contact with the manufacturer as soon as possible avoid wrong
explosion or no explosion when using airbag.
Supplemental restraint system--Remove malfunction
259
Page 383 of 419
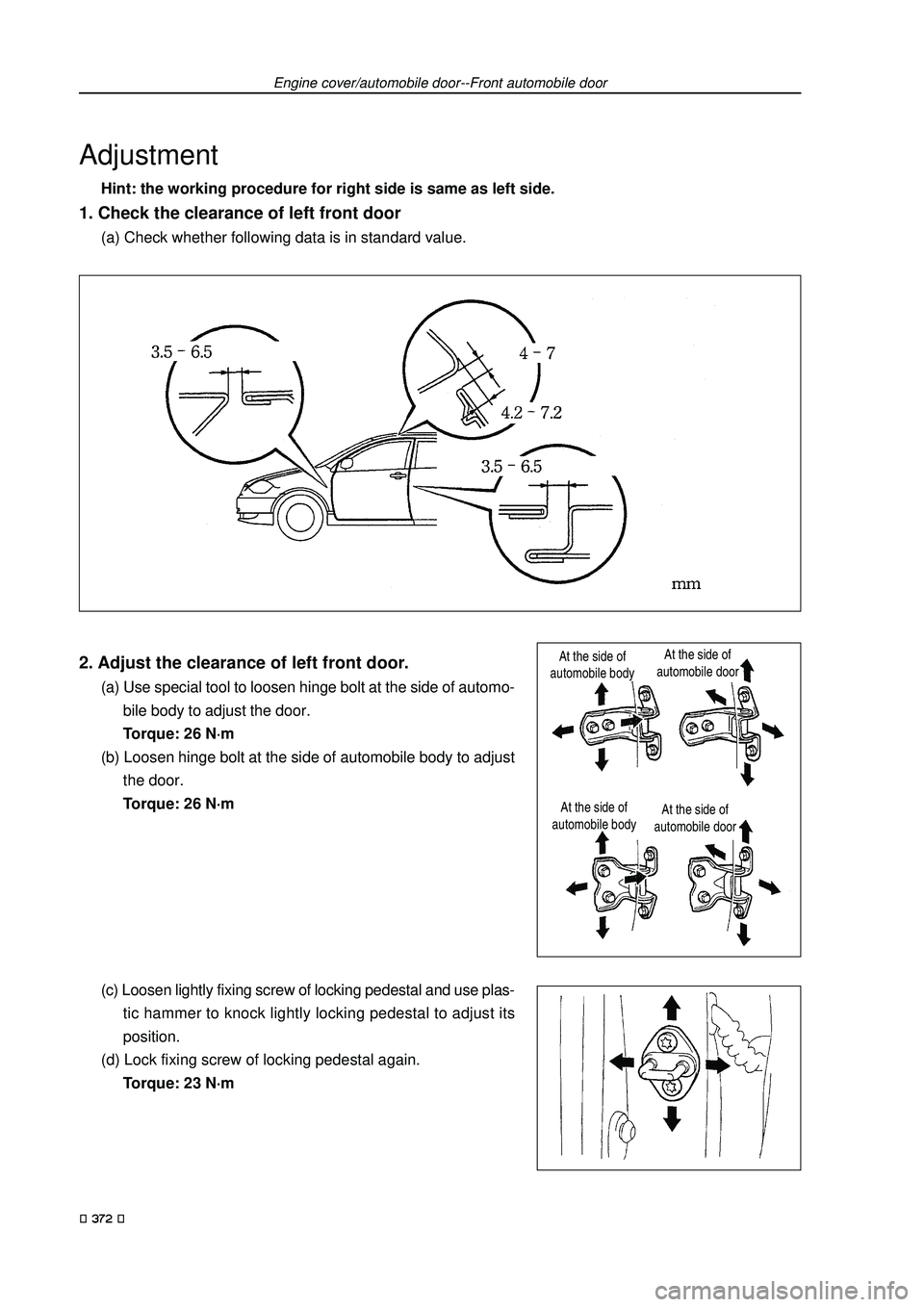
Engine cover/automobile door--Front automobile door
Adjustment
Hint: the working procedure for right side is same as left side.
1. Check the clearance of left front door
(a) Check whether following data is in standard value.
2. Adjust the clearance of left front door.
(a) Use special tool to loosen hinge bolt at the side of automo-
bile body to adjust the door.
Torque: 26 N
⋅ ⋅⋅ ⋅
⋅m
(b) Loosen hinge bolt at the side of automobile body to adjust
the door.
Torque: 26 N
⋅ ⋅⋅ ⋅
⋅m
(c) Loosen lightly fixing screw of locking pedestal and use plas-
tic hammer to knock lightly locking pedestal to adjust its
position.
(d) Lock fixing screw of locking pedestal again.
Torque: 23 N
⋅ ⋅⋅ ⋅
⋅m
At the side of
automobile bodyAt the side of
automobile door
372
At the side of
automobile door At the side of
automobile body
Page 388 of 419
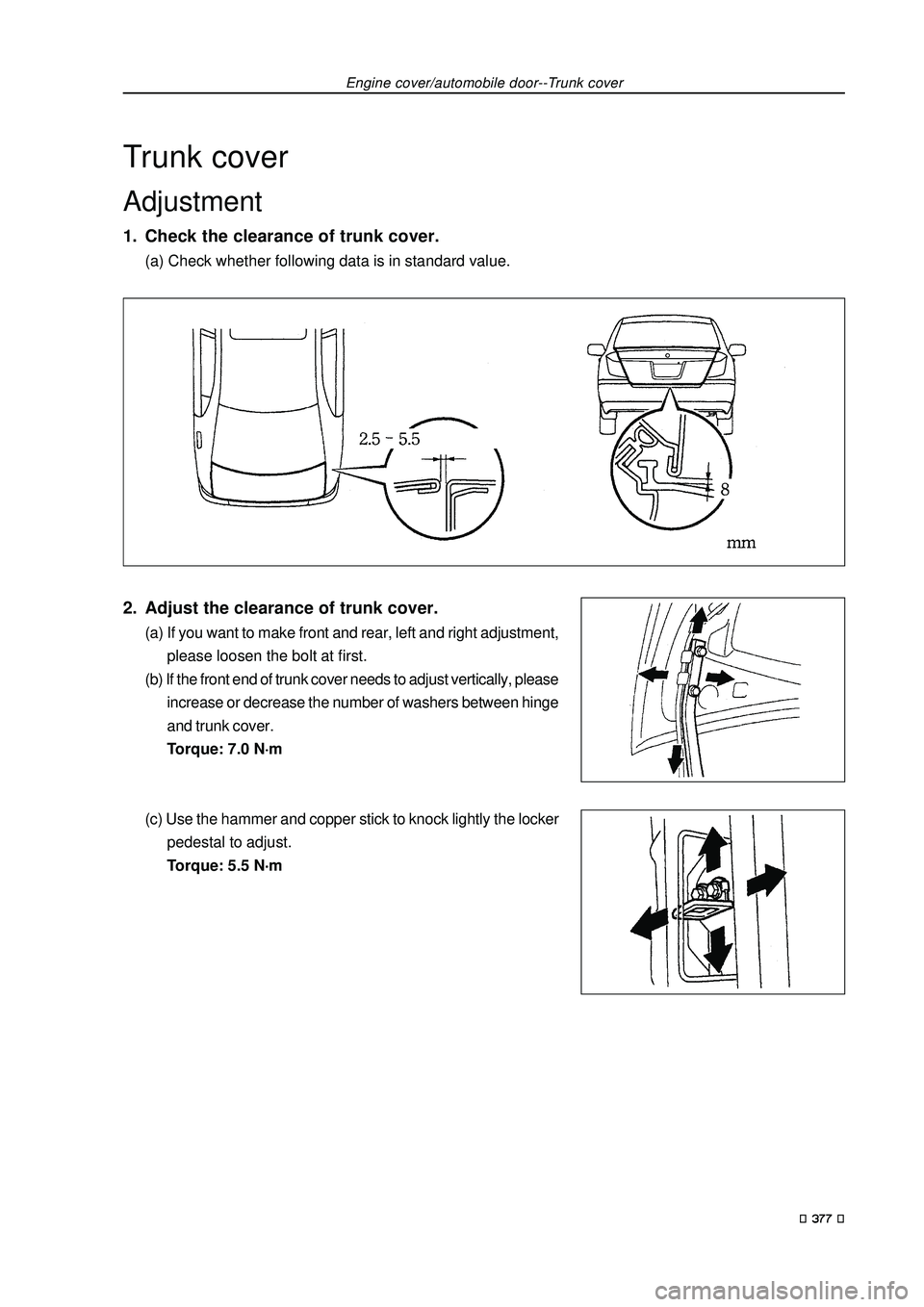
Engine cover/automobile door--Trunk cover
Trunk cover
Adjustment
1. Check the clearance of trunk cover.
(a) Check whether following data is in standard value.
2. Adjust the clearance of trunk cover.
(a) If you want to make front and rear, left and right adjustment,
please loosen the bolt at first.
(b) If the front end of trunk cover needs to adjust vertically, please
increase or decrease the number of washers between hinge
and trunk cover.
Torque: 7.0 N
⋅ ⋅⋅ ⋅
⋅m
(c) Use the hammer and copper stick to knock lightly the locker
pedestal to adjust.
Torque: 5.5 N
⋅ ⋅⋅ ⋅
⋅m
377