brake GEELY MK 2008 Owners Manual
[x] Cancel search | Manufacturer: GEELY, Model Year: 2008, Model line: MK, Model: GEELY MK 2008Pages: 416, PDF Size: 25.19 MB
Page 302 of 416
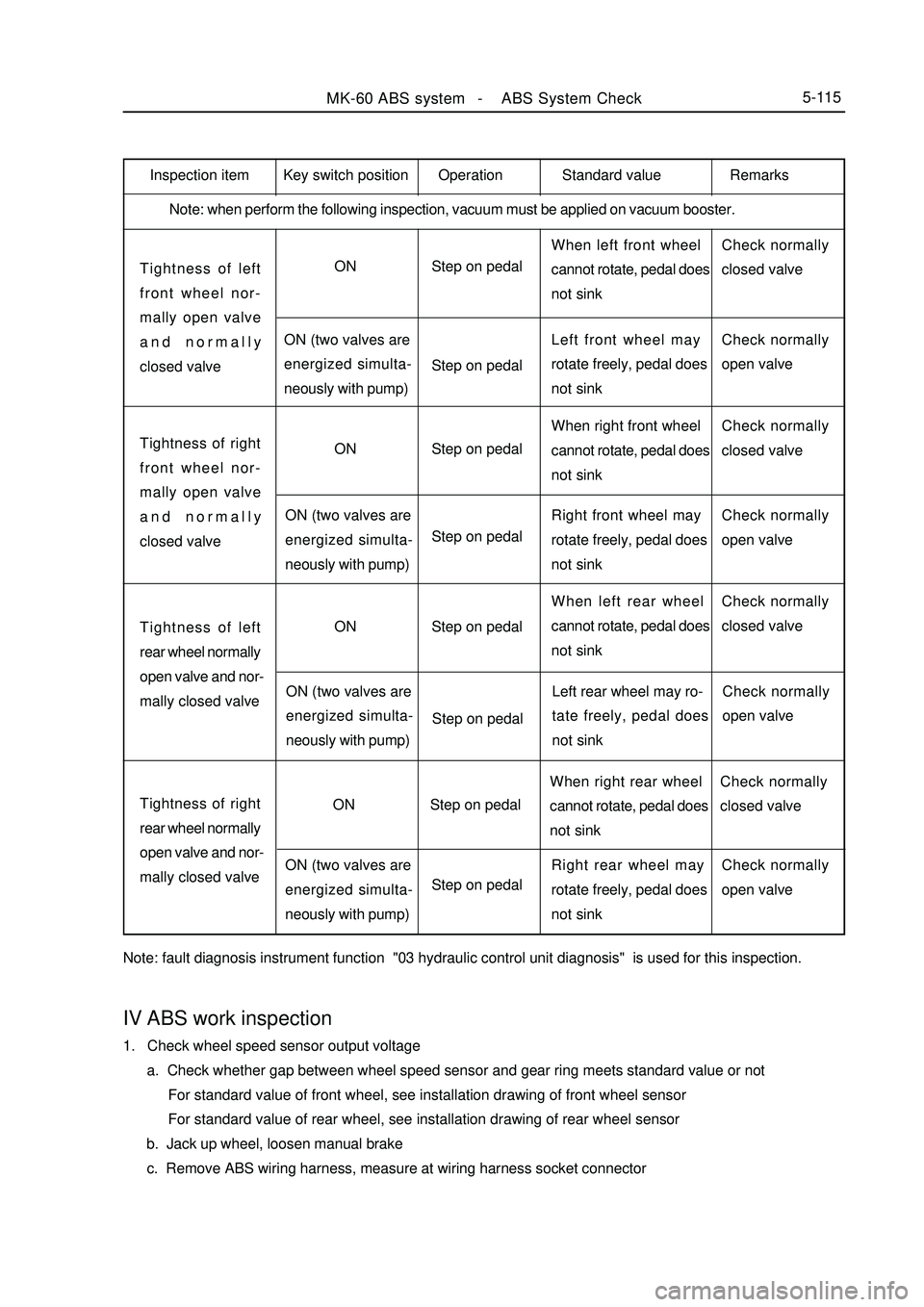
Inspection item
Note: when perform the following inspection, vacuum must be applied on vacuum booster.Tightness of left
front wheel nor-
mally open valve
and normally
closed valveON
ON (two valves are
energized simulta-
neously with pump)Step on pedal
Step on pedalWhen left front wheel
cannot rotate, pedal does
not sinkCheck normally
closed valve
Left front wheel may
rotate freely, pedal does
not sinkCheck normally
open valveTightness of right
front wheel nor-
mally open valve
and normally
closed valveON
ON (two valves are
energized simulta-
neously with pump)Step on pedal
Step on pedalWhen right front wheel
cannot rotate, pedal does
not sinkCheck normally
closed valve
Right front wheel may
rotate freely, pedal does
not sinkCheck normally
open valveTightness of left
rear wheel normally
open valve and nor-
mally closed valveON
ON (two valves are
energized simulta-
neously with pump)Step on pedal
Step on pedalWhen left rear wheel
cannot rotate, pedal does
not sinkCheck normally
closed valve
Left rear wheel may ro-
tate freely, pedal does
not sinkCheck normally
open valveTightness of right
rear wheel normally
open valve and nor-
mally closed valveON
ON (two valves are
energized simulta-
neously with pump)Step on pedal
Step on pedalWhen right rear wheel
cannot rotate, pedal does
not sinkCheck normally
closed valve
Right rear wheel may
rotate freely, pedal does
not sinkCheck normally
open valve
Note: fault diagnosis instrument function "03 hydraulic control unit diagnosis" is used for this inspection.MK-60 ABS system -ABS System Check5-115Key switch position Operation Standard value RemarksIV ABS work inspection1. Check wheel speed sensor output voltage
a. Check whether gap between wheel speed sensor and gear ring meets standard value or not
For standard value of front wheel, see installation drawing of front wheel sensor
For standard value of rear wheel, see installation drawing of rear wheel sensor
b. Jack up wheel, loosen manual brake
c. Remove ABS wiring harness, measure at wiring harness socket connector
Page 303 of 416
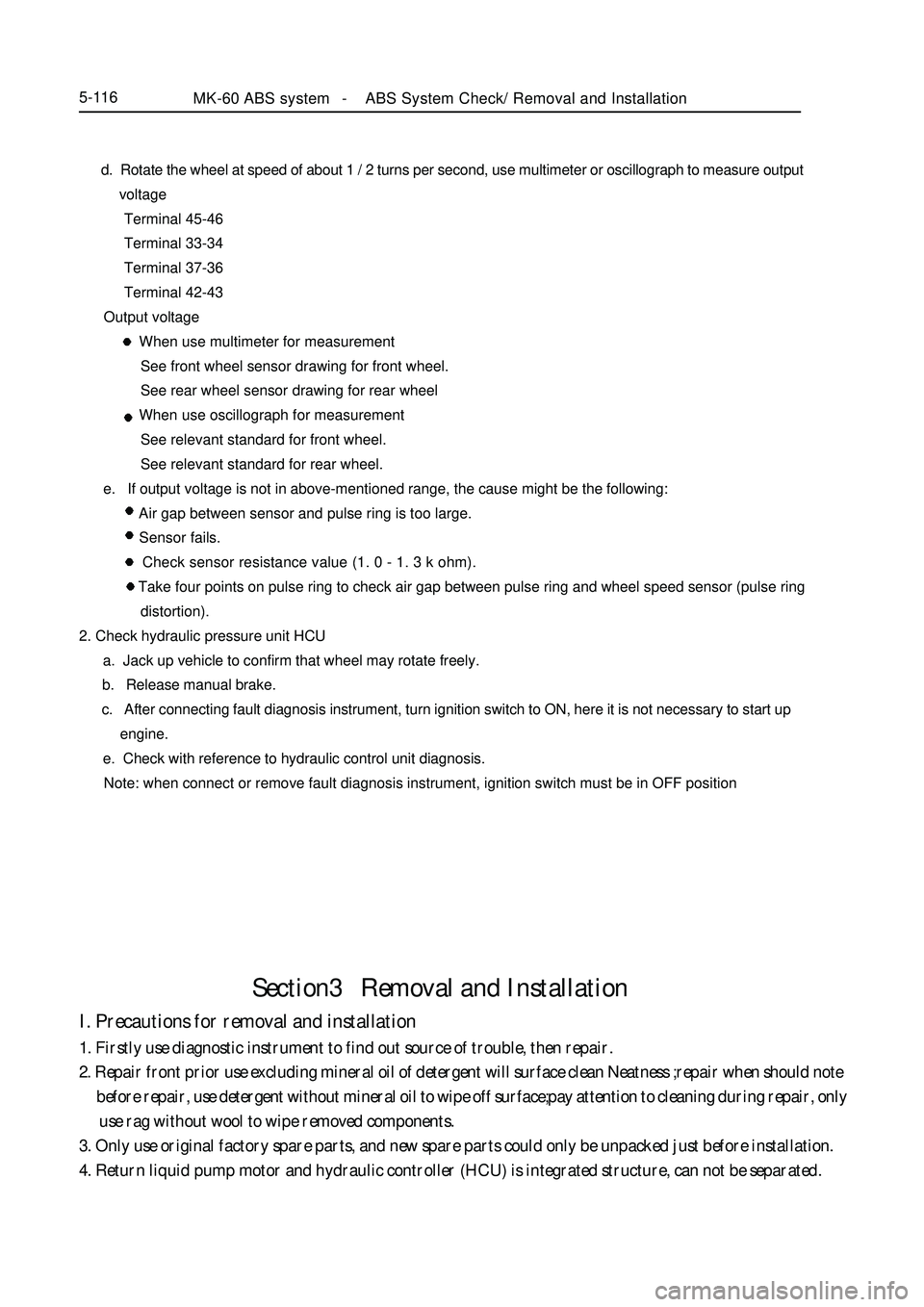
Section3 Removal and InstallationI. Precautions for removal and installation1. Firstly use diagnostic instrument to find out source of trouble, then repair.
2. Repair front prior use excluding mineral oil of detergent will surface clean Neatness ; repair when should note
before repair, use detergent without mineral oil to wipe off surface; pay attention to cleaning during repair, only
use rag without wool to wipe removed components.
3. Only use original factory spare parts, and new spare parts could only be unpacked just before installation.
4. Return liquid pump motor and hydraulic controller (HCU) is integrated structure, can not be separated.MK-60 ABS system -ABS System Check/ Removal and Installation5-116 d. Rotate the wheel at speed of about 1 / 2 turns per second, use multimeter or oscillograph to measure output
voltage
Terminal 45-46
Terminal 33-34
Terminal 37-36
Terminal 42-43
Output voltage
When use multimeter for measurement
See front wheel sensor drawing for front wheel.
See rear wheel sensor drawing for rear wheel
When use oscillograph for measurement
See relevant standard for front wheel.
See relevant standard for rear wheel.
e. If output voltage is not in above-mentioned range, the cause might be the following:
Air gap between sensor and pulse ring is too large.
Sensor fails.
Check sensor resistance value (1. 0 - 1. 3 k ohm).
Take four points on pulse ring to check air gap between pulse ring and wheel speed sensor (pulse ring
distortion).
2. Check hydraulic pressure unit HCU
a. Jack up vehicle to confirm that wheel may rotate freely.
b. Release manual brake.
c. After connecting fault diagnosis instrument, turn ignition switch to ON, here it is not necessary to start up
engine.
e. Check with reference to hydraulic control unit diagnosis.
Note: when connect or remove fault diagnosis instrument, ignition switch must be in OFF position
Page 304 of 416
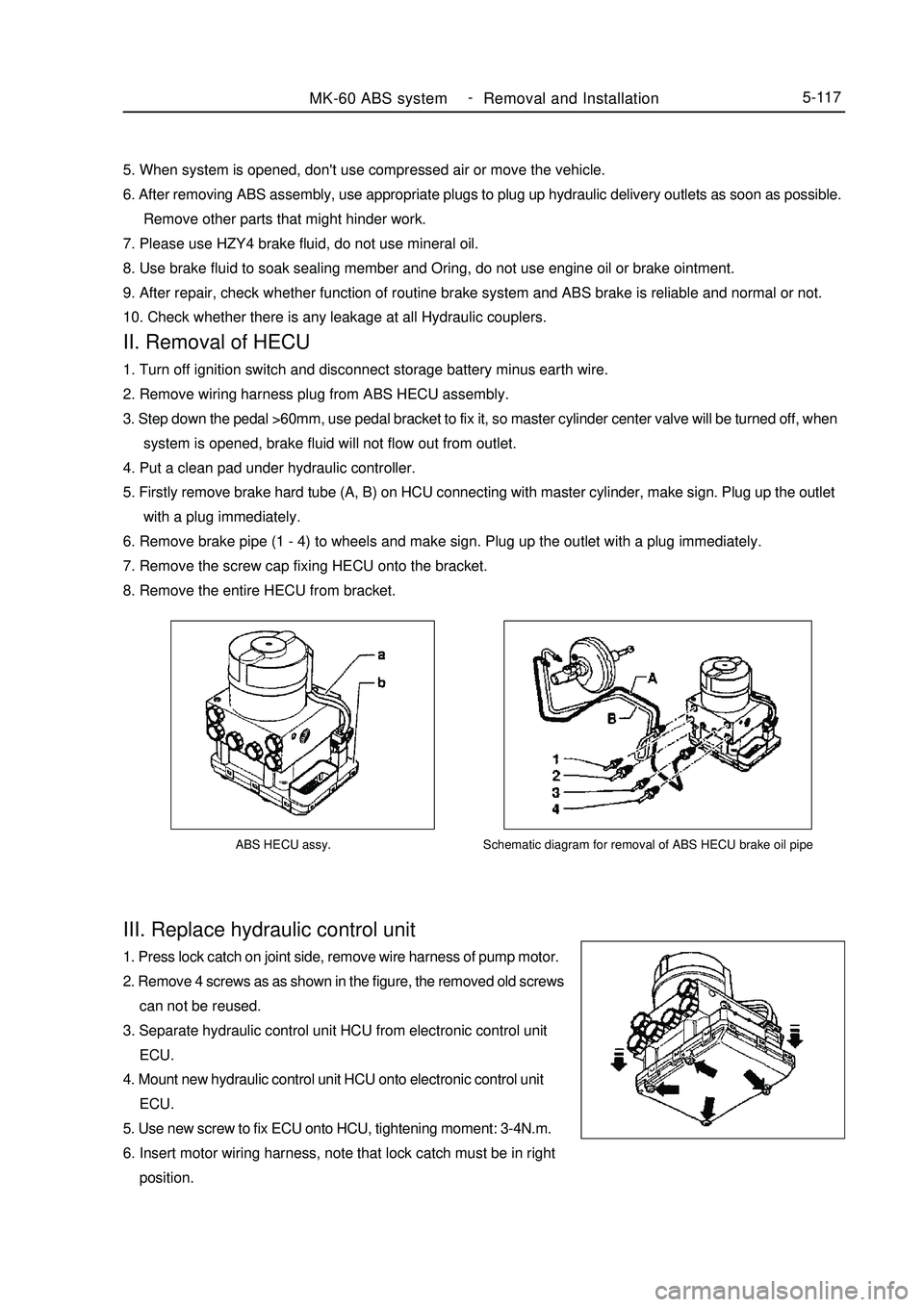
ABS HECU assy.III. Replace hydraulic control unit1. Press lock catch on joint side, remove wire harness of pump motor.
2. Remove 4 screws as as shown in the figure, the removed old screws
can not be reused.
3. Separate hydraulic control unit HCU from electronic control unit
ECU.
4. Mount new hydraulic control unit HCU onto electronic control unit
ECU.
5. Use new screw to fix ECU onto HCU, tightening moment: 3-4N.m.
6. Insert motor wiring harness, note that lock catch must be in right
position.MK-60 ABS system -
Removal and Installation5-117Schematic diagram for removal of ABS HECU brake oil pipe5. When system is opened, don't use compressed air or move the vehicle.
6. After removing ABS assembly, use appropriate plugs to plug up hydraulic delivery outlets as soon as possible.
Remove other parts that might hinder work.
7. Please use HZY4 brake fluid, do not use mineral oil.
8. Use brake fluid to soak sealing member and Oring, do not use engine oil or brake ointment.
9. After repair, check whether function of routine brake system and ABS brake is reliable and normal or not.
10. Check whether there is any leakage at all Hydraulic couplers.II. Removal of HECU1. Turn off ignition switch and disconnect storage battery minus earth wire.
2. Remove wiring harness plug from ABS HECU assembly.
3. Step down the pedal >60mm, use pedal bracket to fix it, so master cylinder center valve will be turned off, when
system is opened, brake fluid will not flow out from outlet.
4. Put a clean pad under hydraulic controller.
5. Firstly remove brake hard tube (A, B) on HCU connecting with master cylinder, make sign. Plug up the outlet
with a plug immediately.
6. Remove brake pipe (1 - 4) to wheels and make sign. Plug up the outlet with a plug immediately.
7. Remove the screw cap fixing HECU onto the bracket.
8. Remove the entire HECU from bracket.
Page 305 of 416
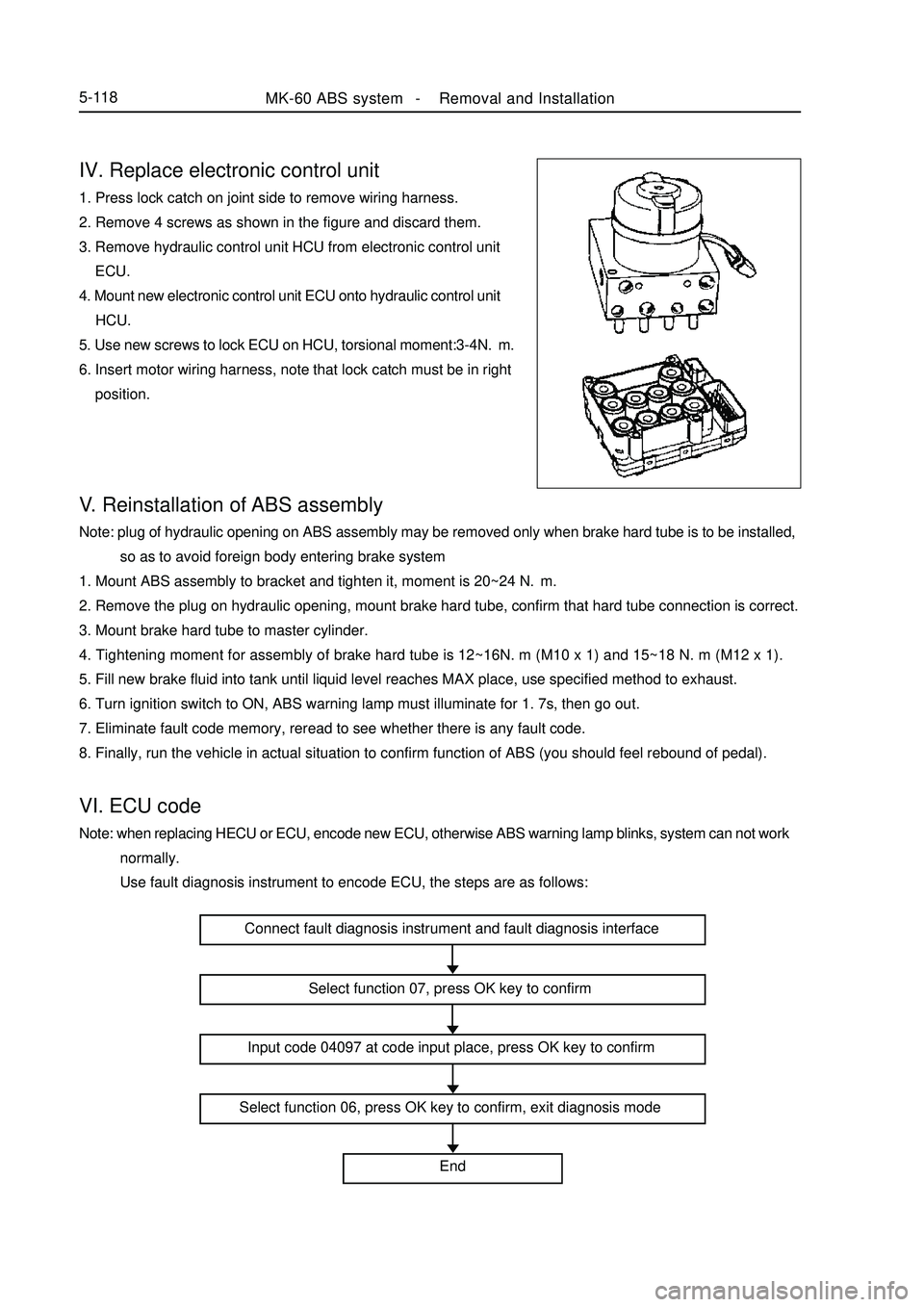
V. Reinstallation of ABS assemblyNote: plug of hydraulic opening on ABS assembly may be removed only when brake hard tube is to be installed,
so as to avoid foreign body entering brake system
1. Mount ABS assembly to bracket and tighten it, moment is 20~24 N.m.
2. Remove the plug on hydraulic opening, mount brake hard tube, confirm that hard tube connection is correct.
3. Mount brake hard tube to master cylinder.
4. Tightening moment for assembly of brake hard tube is 12~16N.m (M10 x 1) and 15~18 N.m (M12 x 1).
5. Fill new brake fluid into tank until liquid level reaches MAX place, use specified method to exhaust.
6. Turn ignition switch to ON, ABS warning lamp must illuminate for 1. 7s, then go out.
7. Eliminate fault code memory, reread to see whether there is any fault code.
8. Finally, run the vehicle in actual situation to confirm function of ABS (you should feel rebound of pedal).VI. ECU codeNote: when replacing HECU or ECU, encode new ECU, otherwise ABS warning lamp blinks, system can not work
normally.
Use fault diagnosis instrument to encode ECU, the steps are as follows:IV. Replace electronic control unit1. Press lock catch on joint side to remove wiring harness.
2. Remove 4 screws as shown in the figure and discard them.
3. Remove hydraulic control unit HCU from electronic control unit
ECU.
4. Mount new electronic control unit ECU onto hydraulic control unit
HCU.
5. Use new screws to lock ECU on HCU, torsional moment:3-4N.m.
6. Insert motor wiring harness, note that lock catch must be in right
position.MK-60 ABS system -Removal and Installation5-118Connect fault diagnosis instrument and fault diagnosis interface
Select function 07, press OK key to confirm
Input code 04097 at code input place, press OK key to confirm
Select function 06, press OK key to confirm, exit diagnosis mode
End
Page 306 of 416
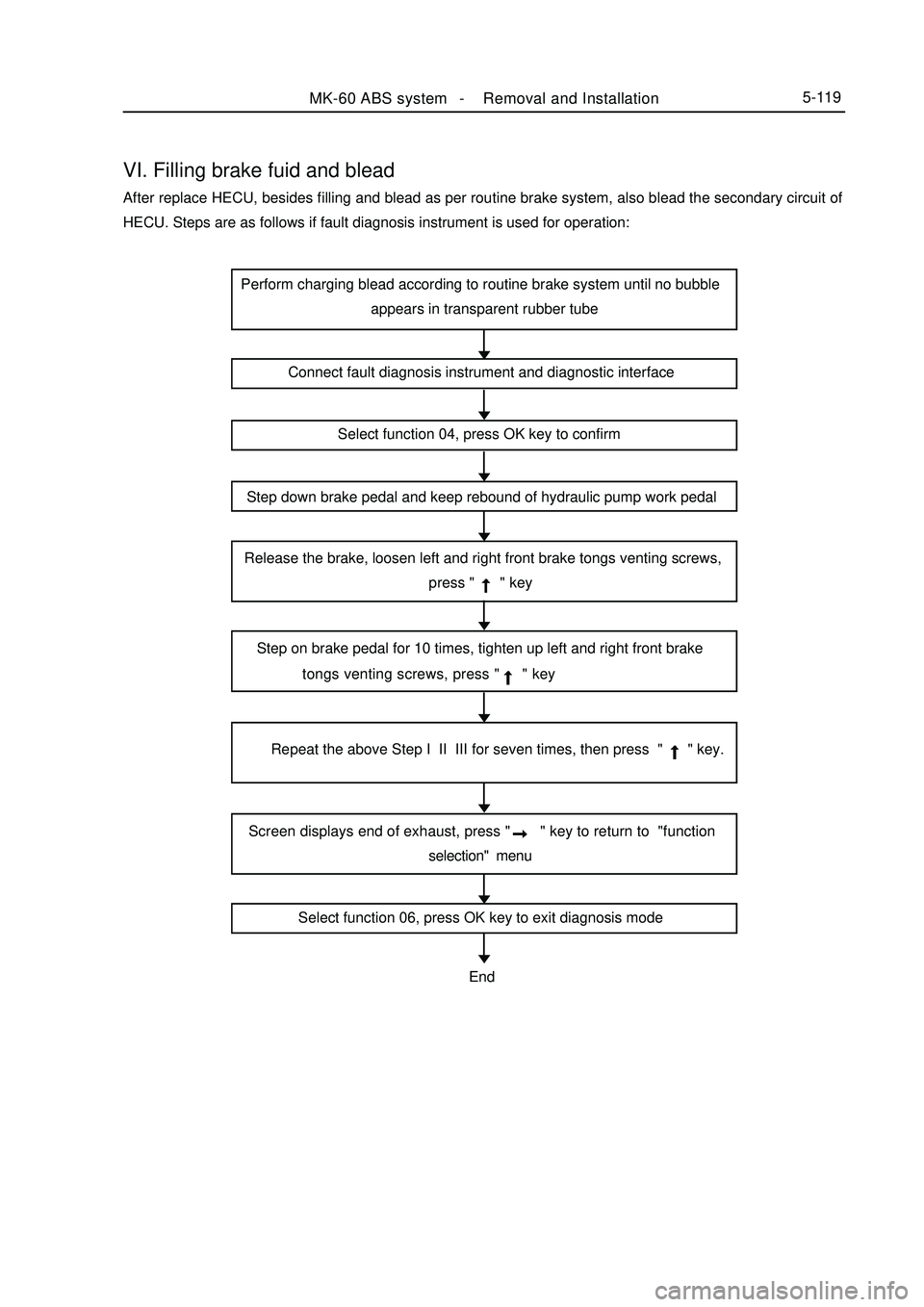
VI. Filling brake fuid and bleadAfter replace HECU, besides filling and blead as per routine brake system, also blead the secondary circuit of
HECU. Steps are as follows if fault diagnosis instrument is used for operation:MK-60 ABS system -Removal and Installation5-119Perform charging blead according to routine brake system until no bubble
appears in transparent rubber tube
Connect fault diagnosis instrument and diagnostic interface
Select function 04, press OK key to confirm
Step down brake pedal and keep rebound of hydraulic pump work pedal
Release the brake, loosen left and right front brake tongs venting screws,
press " " key
Step on brake pedal for 10 times, tighten up left and right front brake
tongs venting screws, press " " key
Repeat the above Step I II III for seven times, then press " " key.
Screen displays end of exhaust, press " " key to return to "function
selection" menu
Select function 06, press OK key to exit diagnosis modeEnd
Page 309 of 416
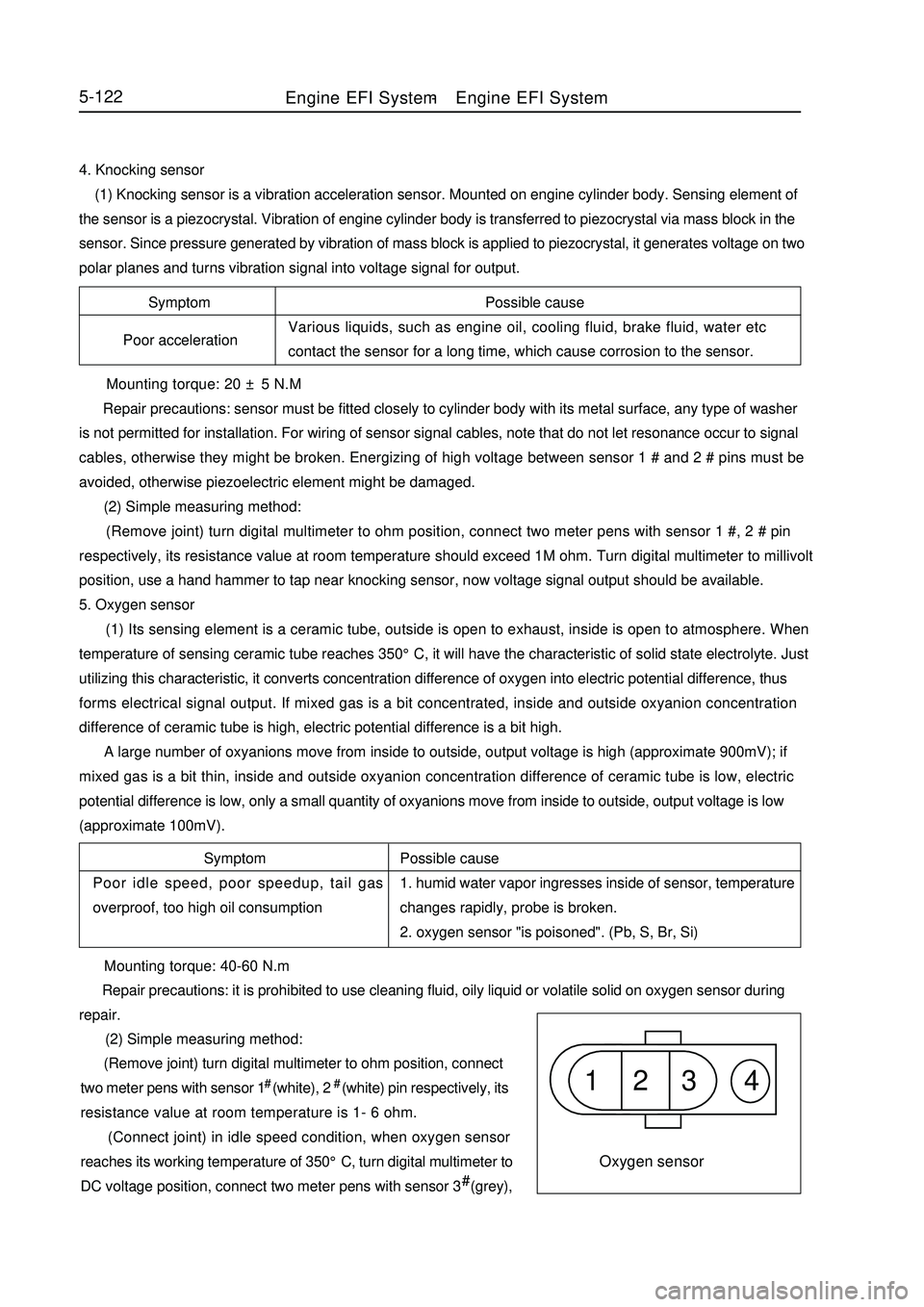
4. Knocking sensor
(1) Knocking sensor is a vibration acceleration sensor. Mounted on engine cylinder body. Sensing element of
the sensor is a piezocrystal. Vibration of engine cylinder body is transferred to piezocrystal via mass block in the
sensor. Since pressure generated by vibration of mass block is applied to piezocrystal, it generates voltage on two
polar planes and turns vibration signal into voltage signal for output.5-122Symptom
Poor accelerationPossible cause
Various liquids, such as engine oil, cooling fluid, brake fluid, water etc
contact the sensor for a long time, which cause corrosion to the sensor. Mounting torque: 20 ± 5 N.M
Repair precautions: sensor must be fitted closely to cylinder body with its metal surface, any type of washer
is not permitted for installation. For wiring of sensor signal cables, note that do not let resonance occur to signal
cables, otherwise they might be broken. Energizing of high voltage between sensor 1 # and 2 # pins must be
avoided, otherwise piezoelectric element might be damaged.
(2) Simple measuring method:
(Remove joint) turn digital multimeter to ohm position, connect two meter pens with sensor 1 #, 2 # pin
respectively, its resistance value at room temperature should exceed 1M ohm. Turn digital multimeter to millivolt
position, use a hand hammer to tap near knocking sensor, now voltage signal output should be available.
5. Oxygen sensor
(1) Its sensing element is a ceramic tube, outside is open to exhaust, inside is open to atmosphere. When
temperature of sensing ceramic tube reaches 350°C, it will have the characteristic of solid state electrolyte. Just
utilizing this characteristic, it converts concentration difference of oxygen into electric potential difference, thus
forms electrical signal output. If mixed gas is a bit concentrated, inside and outside oxyanion concentration
difference of ceramic tube is high, electric potential difference is a bit high.
A large number of oxyanions move from inside to outside, output voltage is high (approximate 900mV); if
mixed gas is a bit thin, inside and outside oxyanion concentration difference of ceramic tube is low, electric
potential difference is low, only a small quantity of oxyanions move from inside to outside, output voltage is low
(approximate 100mV).
Possible cause
1. humid water vapor ingresses inside of sensor, temperature
changes rapidly, probe is broken.
2. oxygen sensor "is poisoned". (Pb, S, Br, Si) Symptom
Poor idle speed, poor speedup, tail gas
overproof, too high oil consumption1 2 3 4Oxygen sensor Mounting torque: 40-60 N.m
Repair precautions: it is prohibited to use cleaning fluid, oily liquid or volatile solid on oxygen sensor during
repair.
(2) Simple measuring method:
(Remove joint) turn digital multimeter to ohm position, connect
two meter pens with sensor 1# (white), 2# (white) pin respectively, its
resistance value at room temperature is 1- 6 ohm.
(Connect joint) in idle speed condition, when oxygen sensor
reaches its working temperature of 350°C, turn digital multimeter to
DC voltage position, connect two meter pens with sensor 3# (grey),Engine EFI System-Engine EFI System
Page 349 of 416
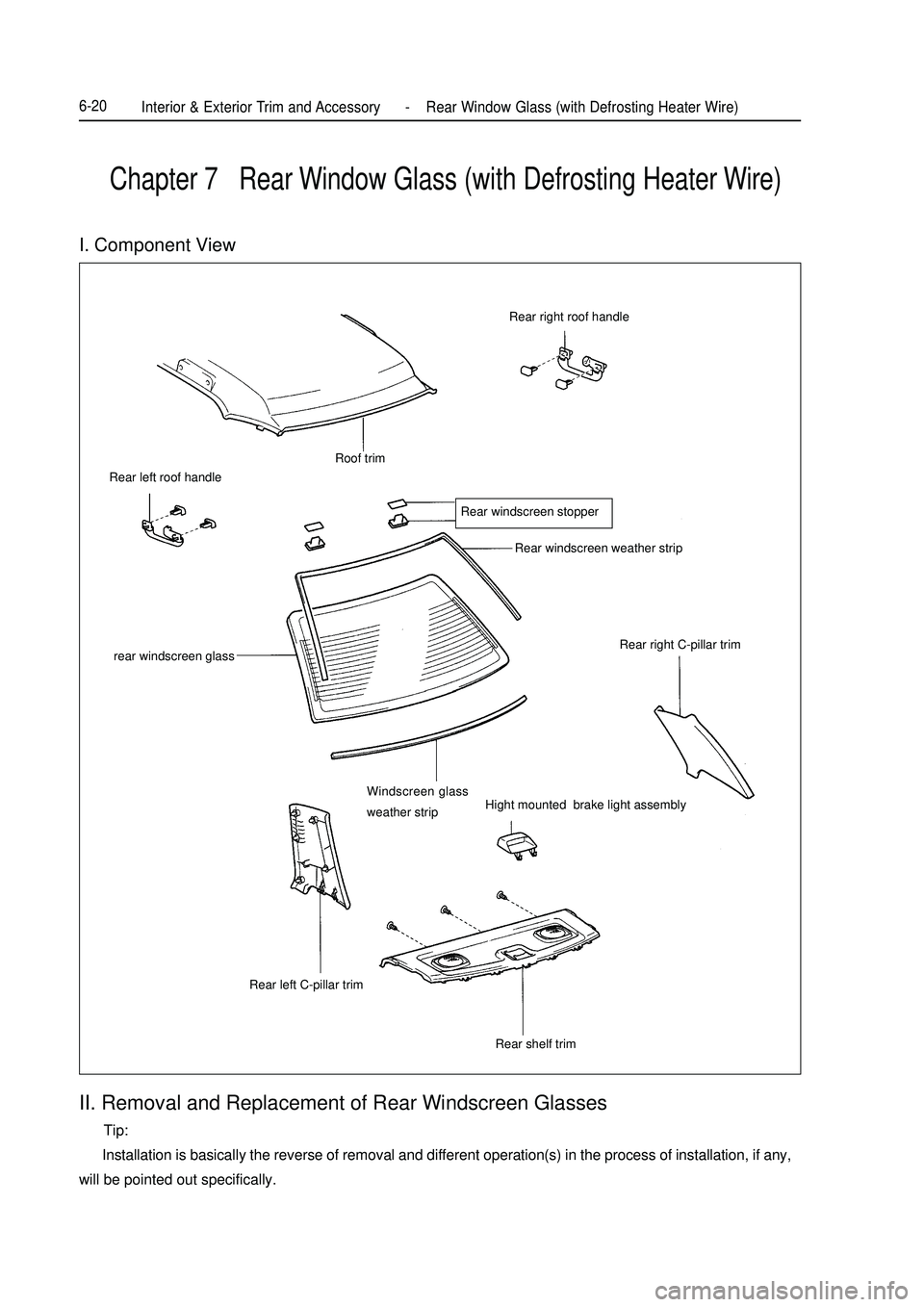
Chapter 7 Rear Window Glass (with Defrosting Heater Wire)II. Removal and Replacement of Rear Windscreen Glasses Tip:
Installation is basically the reverse of removal and different operation(s) in the process of installation, if any,
will be pointed out specifically.I. Component ViewRear right roof handleRoof trim
Rear windscreen stopperRear windscreen weather strip
Rear right C-pillar trim
Windscreen glass
weather stripHight mounted brake light assembly
Rear shelf trim Rear left C-pillar trim rear windscreen glass Rear left roof handleInterior & Exterior Trim and Accessory -Rear Window Glass (with Defrosting Heater Wire)6-20
Page 350 of 416
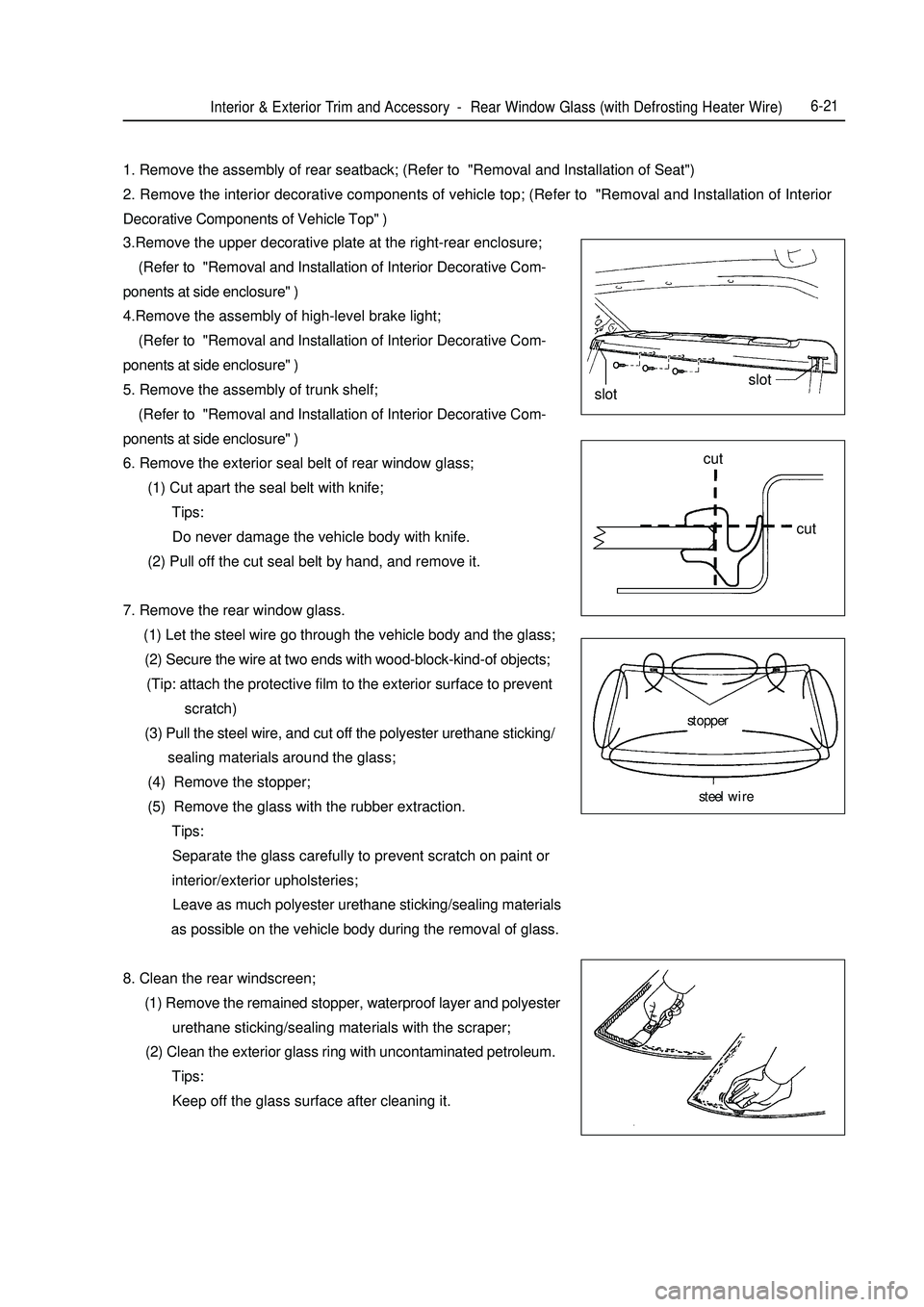
Interior & Exterior Trim and Accessory -Rear Window Glass (with Defrosting Heater Wire)6-211. Remove the assembly of rear seatback; (Refer to "Removal and Installation of Seat")
2. Remove the interior decorative components of vehicle top; (Refer to "Removal and Installation of Interior
Decorative Components of Vehicle Top" )
3.Remove the upper decorative plate at the right-rear enclosure;
(Refer to "Removal and Installation of Interior Decorative Com-
ponents at side enclosure" )
4.Remove the assembly of high-level brake light;
(Refer to "Removal and Installation of Interior Decorative Com-
ponents at side enclosure" )
5. Remove the assembly of trunk shelf;
(Refer to "Removal and Installation of Interior Decorative Com-
ponents at side enclosure" )
6. Remove the exterior seal belt of rear window glass;
(1) Cut apart the seal belt with knife;
Tips:
Do never damage the vehicle body with knife.
(2) Pull off the cut seal belt by hand, and remove it.
7. Remove the rear window glass.
(1) Let the steel wire go through the vehicle body and the glass;
(2) Secure the wire at two ends with wood-block-kind-of objects;
(Tip: attach the protective film to the exterior surface to prevent
scratch)
(3) Pull the steel wire, and cut off the polyester urethane sticking/
sealing materials around the glass;
(4) Remove the stopper;
(5) Remove the glass with the rubber extraction.
Tips:
Separate the glass carefully to prevent scratch on paint or
interior/exterior upholsteries;
Leave as much polyester urethane sticking/sealing materials
as possible on the vehicle body during the removal of glass.
8. Clean the rear windscreen;
(1) Remove the remained stopper, waterproof layer and polyester
urethane sticking/sealing materials with the scraper;
(2) Clean the exterior glass ring with uncontaminated petroleum.
Tips:
Keep off the glass surface after cleaning it.slotslot
cut
cut
stopper
steel wire
Page 368 of 416
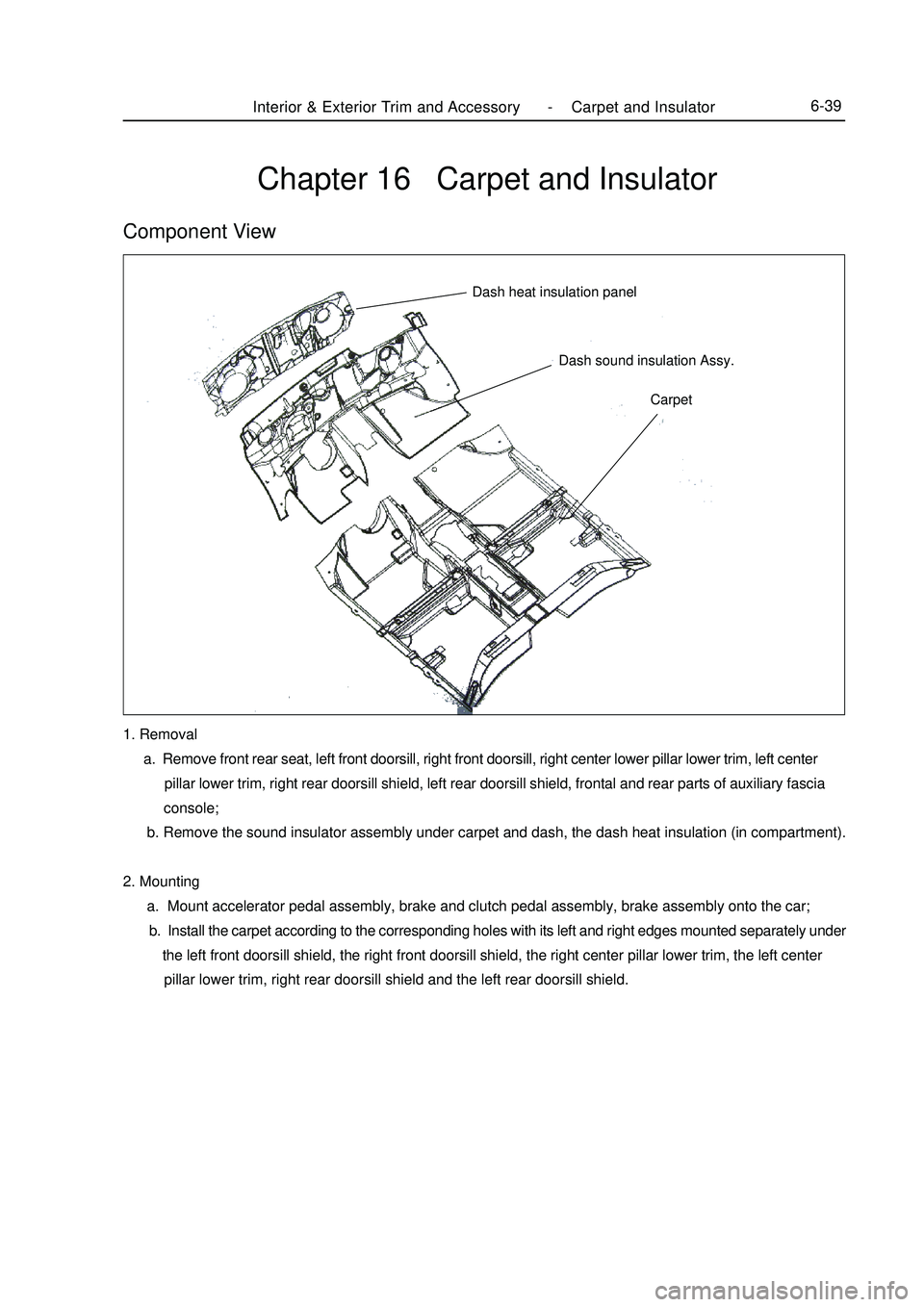
Chapter 16 Carpet and InsulatorComponent ViewCarpet Dash sound insulation Assy. Dash heat insulation panelInterior & Exterior Trim and Accessory -Carpet and Insulator6-391. Removal
a. Remove front rear seat, left front doorsill, right front doorsill, right center lower pillar lower trim, left center
pillar lower trim, right rear doorsill shield, left rear doorsill shield, frontal and rear parts of auxiliary fascia
console;
b. Remove the sound insulator assembly under carpet and dash, the dash heat insulation (in compartment).
2. Mounting
a. Mount accelerator pedal assembly, brake and clutch pedal assembly, brake assembly onto the car;
b. Install the carpet according to the corresponding holes with its left and right edges mounted separately under
the left front doorsill shield, the right front doorsill shield, the right center pillar lower trim, the left center
pillar lower trim, right rear doorsill shield and the left rear doorsill shield.
Page 374 of 416
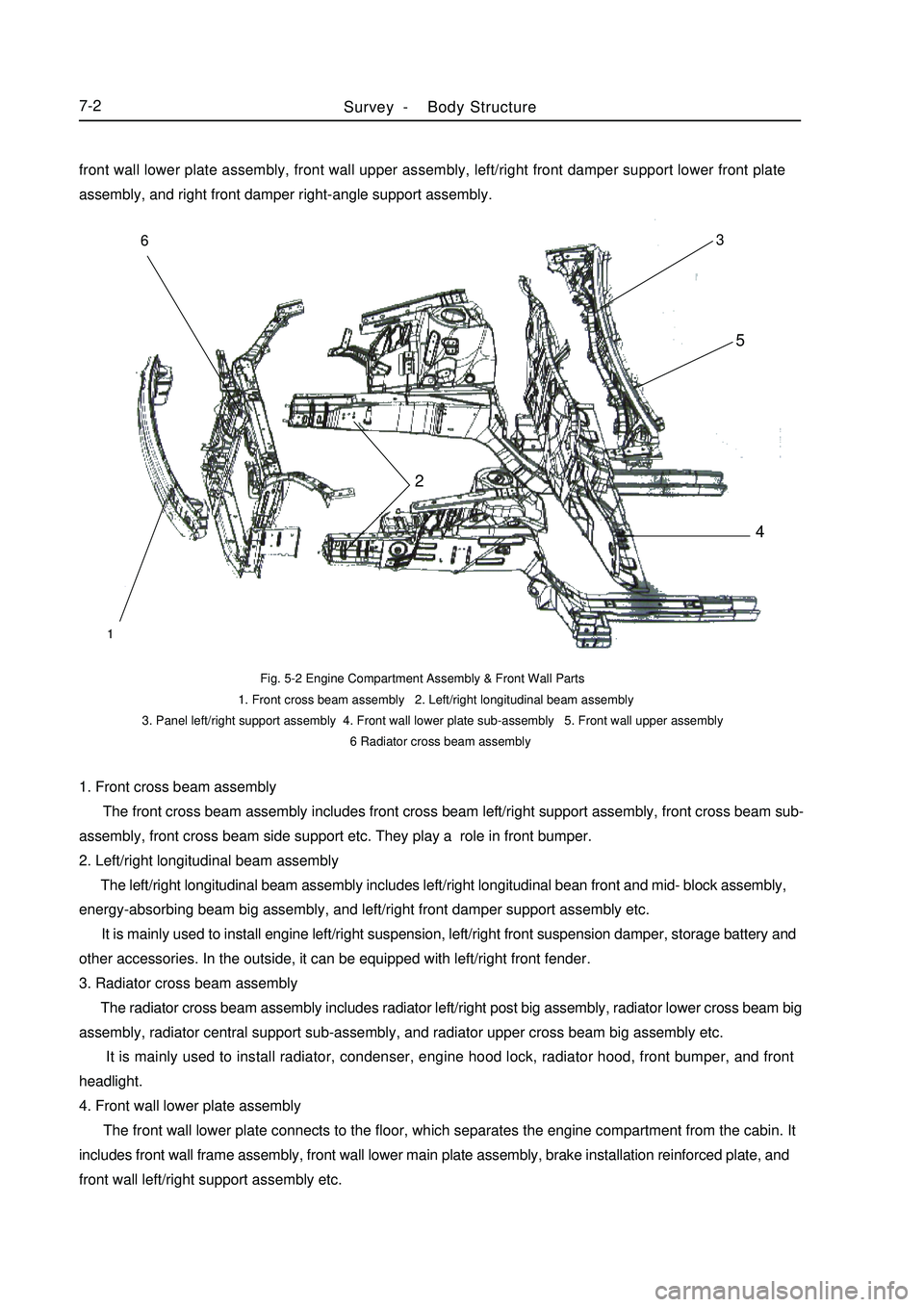
1. Front cross beam assembly
The front cross beam assembly includes front cross beam left/right support assembly, front cross beam sub-
assembly, front cross beam side support etc. They play a role in front bumper.
2. Left/right longitudinal beam assembly
The left/right longitudinal beam assembly includes left/right longitudinal bean front and mid- block assembly,
energy-absorbing beam big assembly, and left/right front damper support assembly etc.
It is mainly used to install engine left/right suspension, left/right front suspension damper, storage battery and
other accessories. In the outside, it can be equipped with left/right front fender.
3. Radiator cross beam assembly
The radiator cross beam assembly includes radiator left/right post big assembly, radiator lower cross beam big
assembly, radiator central support sub-assembly, and radiator upper cross beam big assembly etc.
It is mainly used to install radiator, condenser, engine hood lock, radiator hood, front bumper, and front
headlight.
4. Front wall lower plate assembly
The front wall lower plate connects to the floor, which separates the engine compartment from the cabin. It
includes front wall frame assembly, front wall lower main plate assembly, brake installation reinforced plate, and
front wall left/right support assembly etc.Fig. 5-2 Engine Compartment Assembly & Front Wall Parts
1. Front cross beam assembly 2. Left/right longitudinal beam assembly
3. Panel left/right support assembly 4. Front wall lower plate sub-assembly 5. Front wall upper assembly
6 Radiator cross beam assemblySurvey -Body Structure7-2123456front wall lower plate assembly, front wall upper assembly, left/right front damper support lower front plate
assembly, and right front damper right-angle support assembly.