speed sensor circuit HONDA CIVIC 1998 6.G Owner's Manual
[x] Cancel search | Manufacturer: HONDA, Model Year: 1998, Model line: CIVIC, Model: HONDA CIVIC 1998 6.GPages: 2189, PDF Size: 69.39 MB
Page 772 of 2189
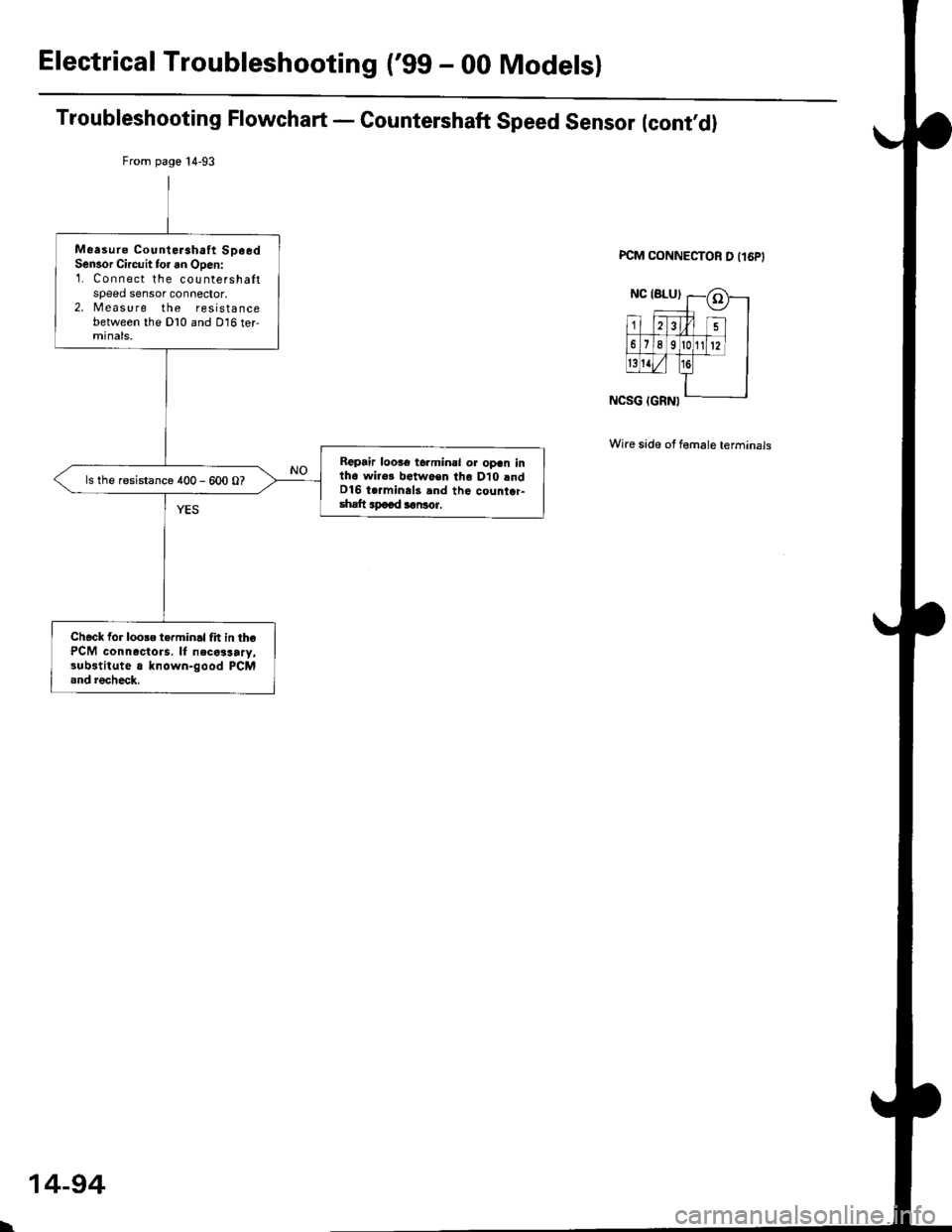
Electrical Troubleshooting ('gg - 00 Modelsl
From page 14-93
Measure CounteJahaft SpeedSensor Circuit tor an Open:1. Connect the countershaltspeed sensor connector,2. Measure the resistancebetween the Dl0 and D16 termtnats.
Roptir loo.€ t6.minal or opan inth6 wir€! betwo€n lho D10 lndD16 t.rmina13 and the count.r-shatt apaad aaNor.
ls the resistance 400 - 600 O?
Check for loose t.rminal frt in thePCM connectors. It necalsary,3ubstitute a known-good PCMand recheck.
Troubleshooting Flowchart - Countershaft Speed Sensor (cont,d)
PCM CONNECTOR D I16PI
Wire side of female terminals
\
14-94
Page 773 of 2189
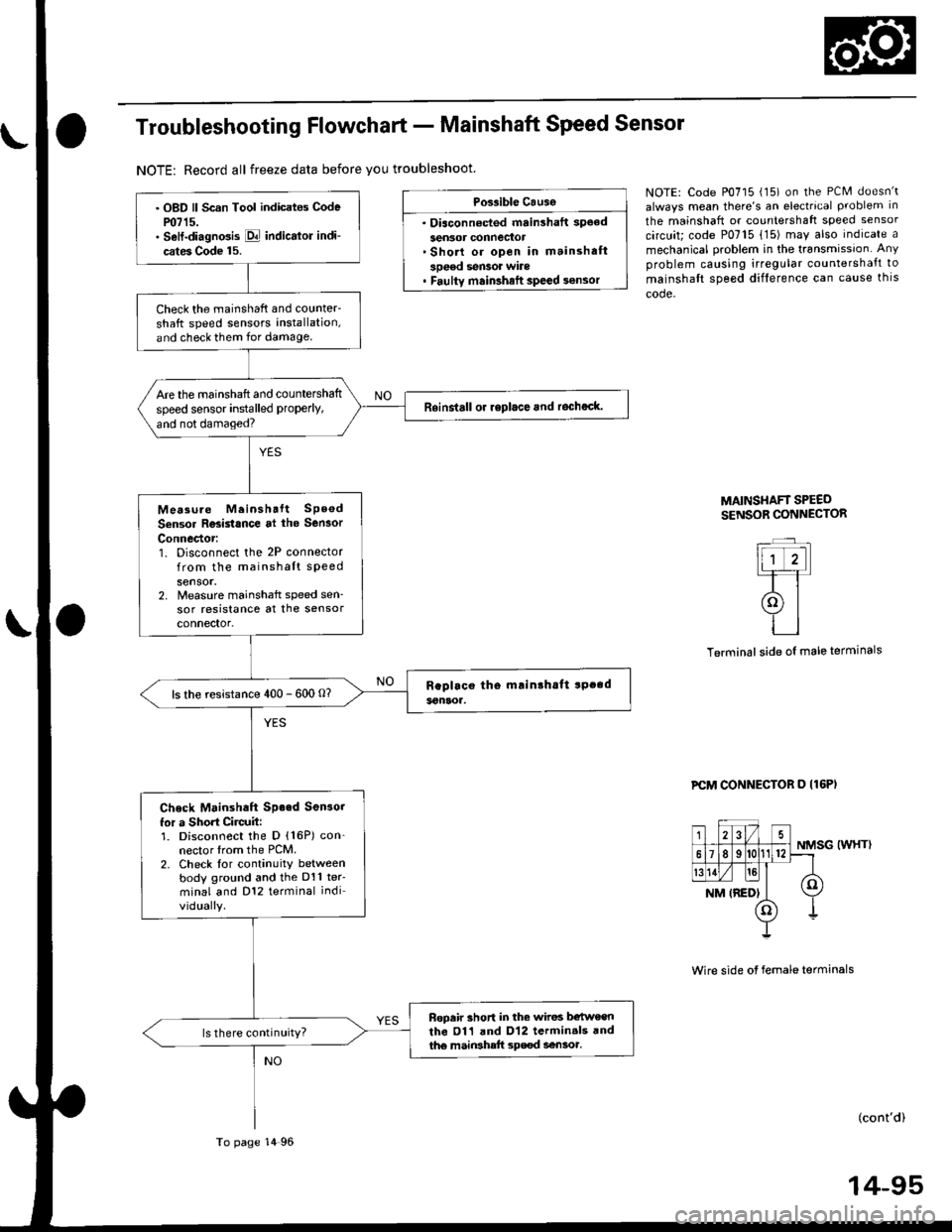
Troubleshooting Flowchart - Mainshaft Speed Sensor
NOTE: Record all freeze data before you troubleshoot.
Possible Causg
. Diaconn€cted mainshaft spoed
sen3or connector'Short or open in mainshaft
sDeed sen3or wile. Faulty main3halt speed sensor
NOTE: Code P0715 (15) on the PCM doesn't
always mean there's an electrrcal problem in
the mainshaft or countershaft speed sensor
circuit; code P0715 {15) may also indicate a
mechanical problem in the transmissjon Any
problem causing irregular countershaft to
mainshalt speed difference can cause thls
code.
lll ,..TT
(ol-i-l
tl
side oI male terminals
MAINSI{AFT SPEEDSENSOR CONNECTOR
Terminal
PCM CONNECTOR D (16P)
NMSG (WHT)
Wire side of female terminals
(cont'd)
14-95
. OBD ll Scan Tool indicates Codem715.. Sell-diagno3is E indicator indi-
cates Code 15.
Check the mainshaft and counter-
shatt speed sensors installation,
and check them for damage.
Are the mainshaft and countershaft
speed sensor installed properly,
and not damaged?
Rsinalall or replace and rocheck.
Mea3u.e Meinshalt SPeod
Sensor Residance al the Sen3or
Connector:1. Disconnect the 2P connectorfrom the mainshaft sPeedsensor.2, Nreasure mainshaft speed sen_sor resistance at the sensorconnector.
ls the resistance 400 - 600 O?
Check Mainshaft Sp.ed Sen3o.
for a Short Circult:1. Disconnect the D (16P) con-nector trom the PCM.2. Check lor continuity betweenbody ground and the D11 ter'minal and D12 terminal indi
vidually.
Bopair 3hort in the wiros b€twe€nthe 011 and D12 termin.ls rndth€ main3hett sp€€d aensoa.ls there continuity?
To page 14 96
Page 871 of 2189
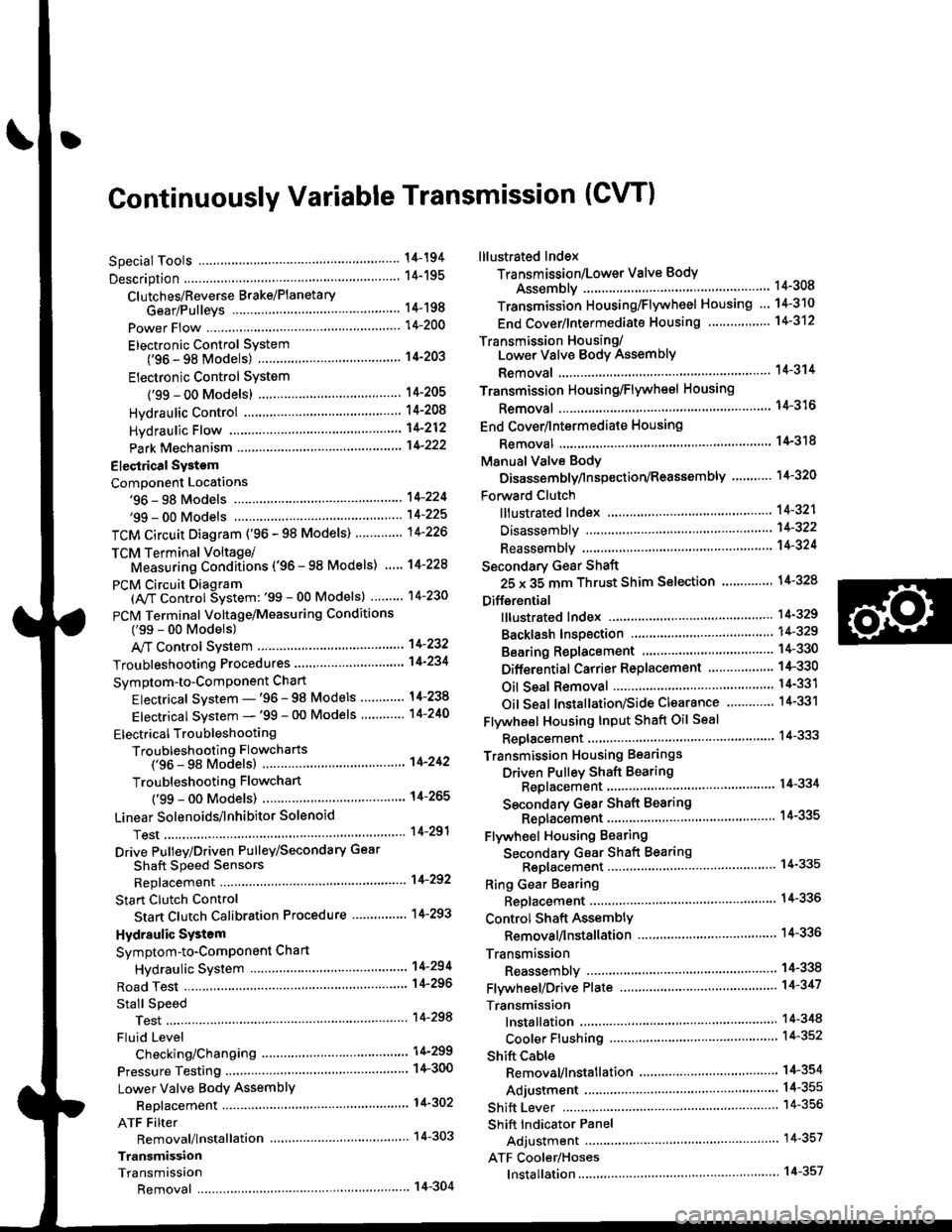
Continuously Variable Transmission (CVTI
Special Tools ................ 14-194
Description .................... 14-195
Clutches/Reverse Brake/Planetary
Gear/Pulleys .......... 14-198
power Flow ..............,..... 14-200
Electronic Control SYstem(,96 - 98 Modets) ......14-203
Electronic Control System
('99 - oo Models) " 14-205
Hydraulic Control '....... 14-208
Hydraulic Flow .'..-.....'... '14-212
Park Mechanism .....-...'.' 14-222
Eleqtrical Systom
Component Locations'96 - 98 Models """"""' 14-224,99 - 00 Modets ............. 14-225
TCM Circuit Diagram ('96 - 98 Models) ............. 14-226
TCM Terminal Voltage/Measuring Condiiions ('96 - 98 Models) '.... 14-228
PcM Circuit Oiaqram{A/T Control System: '99 - 00 Models} ...--.... 14-230
PCM Terminal Voltage/Measuring Conditions('99 - 00 Models)
A/4 Control System .'.'...14-232
Troubleshooting Procedures ... . .... .....',........."' '14-234
Symptom-to-ComPonent Chart
Electrical System - '96 - 98 Models ......'..... '14-234
Electrical System -'99 - 00 Models ..'....-..-. '11-210
Electrical Troubleshooting
Troubleshooting Flowcharts('96 - 98 Models) """'11-242
Troubleshooting Flowchart
('99 - 0O Modets) ...... 14-265
Linear Solenoids/lnhibitor Solenoid
Test ......................... . ...... 14-29f
Drive Pulley/Driven Pulley/Secondary Gear
Shaft Speed Sensors
Replacement .........'...... .14-292
Start Clutch Control
Start Clutch Calibration Procedure ....... ....,. 14-293
Hydraulic SYstem
Symptom-to-ComPonent Chart
Hydraulic System '.'.......14-294
Road Test ............................ 14-296
Stall Speed
Test......................... ...... 14-294
Fluid Level
Checking/Changing ....... 14-299
Pressure Testing ................. 14-300
Lower Valve BodY AssemblY
Replacement ..........,... 14-302
ATF Filter
Removal/lnstallation ..... 14-303
Transmission
Transmission
Removal ........... . 14-304
lllustrated Index
Transmission/Lower Valve BodY
Assembly ................. 14-308
Transmission Housing/Flywheel Housing ... 14-310
End Cover/f ntermediate Housing ..........'.'.... 14-312
Transmission Housing/Lower Valve Body Assembly
Removal ..........'.... .. " 14-314
Transmission Housing/Flywhesl Housing
Removal ................. ........ 1+316
End Cover/lntermediate Housing
14-318Removal .........,...............
Manual Valve Body
Disassembly/lnspection/Reassemblv .'.'.'..... 1 4-320
Forward Clutch
lltustrated Index ........................................ 14-321
Disassemblv .................. 14-322
Reassemblv , ,, . ',','......14-324
Secondary Gear Shaft
25 x 35 mm Thrust Shim Selection ..'.'....-... 14-324
Differential
lllustrated lndex ...,.....................,.,...-.-.-...'... 14-329
Backlash Inspection .-....14-329
Bearing Replacement ......'........'....'... ....'... 14-330
Differential Carrier Replacement ........'........ 14-330
Oil Seal Removal ........... 14-331
Oil Seal Installation/Side Clearance ....... . . 14-331
Flywheel Housing Input Shaft Oil Seal
Replacement .....,.... ...'.'.. 14-333
Transmission Housing Bearings
Driven Pulley Shaft Bearing
Replacenient ...................'. . ...................'.. 14-334
Secondary Gear Shaft Bearing
Reolacbment ...................... . .......... . ........ 14-335
Flywheel Housing Beating
Secondary Gear Shaft BearingReo1acement..................,........................... 14-335
Ring Gear Bearing
Replacement......... ........ 14-336
Control Shaft Assembly
Removal/lnstallation ....................'........... 14-336
Transmission
Reassembly .................. 14-338
Flywheel/Drive Plate .. . ...... . ...... ... . ....-.....'.'...14-341
Transmission
lnstalation ..................... 14-348
Cooler Flushing .'......... 14-352
shift cable
Removal/lnstallation....'........." """ 14-354
Adjustment .......'........ 14-355
Shift Lever ........................,. 14'356
Shift Indicator Panel
Adjustment ................ 14-357
ATF Cooler/Hoses
lnsta llation ......,,...... .... 14-357
Page 873 of 2189
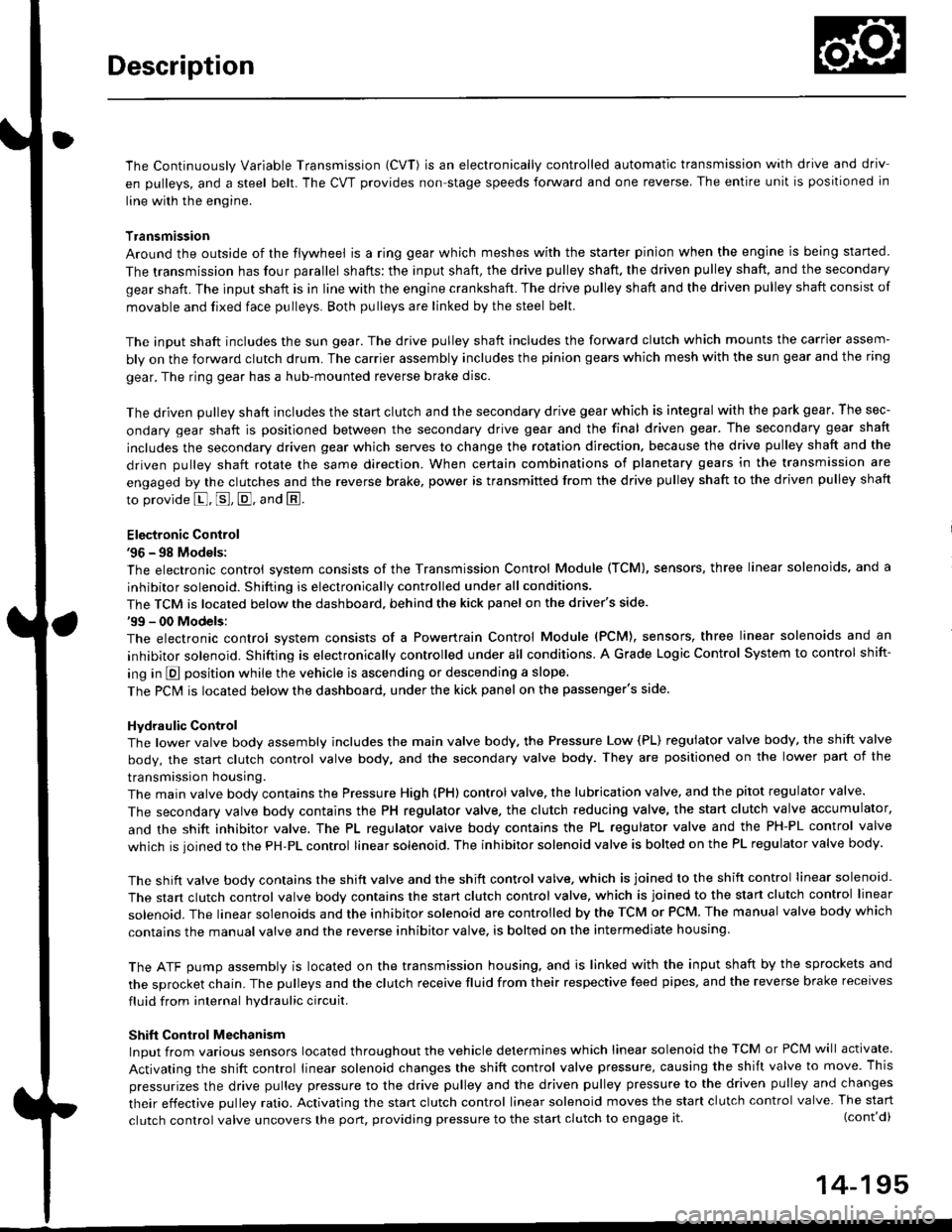
Description
The Continuously Variable Transmission (CVT) is an electronically controlled automatic transmission with drive and driv
en Oullevs, and a steel belt. The CVT provides non stage speeds forward and one reverse. The entire unit is positioned in
line with the engine.
Transmission
Around the outside of the flywheel is a ring gear which meshes with the starter pinion when the engine is being staned.
The transmission has four parallel shafts: the input shaft, the drive pulley shaft. the driven pulley shaft, and the secondary
gear shaft. The input shaft is in line with the engine crankshaft. The drive pulley shaft and the driven pulley shaft consist of
movable and fixed face pulleys. Both pulleys are linked by the steel belt.
The input shaft includes the sun gear. The drive pulley shaft includes the forward clutch which mounts the carrier assem-
bly on the forward clutch drum. The carrier assembly includes the pinion gears which mesh with the sun gear and the ring
gear. The ring gear has a hub-mounted reverse brake disc.
The driven pulley shaft includes the start clutch and the secondary drive gear which is integral with the park gear' The sec-
ondary gear shaft is positioned between the secondary drive gear and the final driven gear. The secondary gear shaft
includes the secondary driven gear which serves to change the rotation direction. because the drive pulley shaft and the
driven oullev shaft rotate the same direction. When certain combinations of planetary gears in the transmission are
engaged by the clutches and the reverse brake, power is transmitted from the drive pulley shaft to the driven pulley shaft
to provide E, E, E, and El.
Electronic Control'96 - 98 Models:
The electronic control system consists of the Transmission Control Module (TCM), sensors, three linear solenoids, and a
inhibitor solenoid. Shifting is electronically controlled under all conditions'
The TCM is located below the dashboard, behind the kick panel on the driver's side.'99 - 00 Models:
The electronic control svstem consists of a Powertrain Control Module (PCM), sensors, three linear solenoids and an
inhibitor solenoid. Shifting is electronically controlled under all conditions. A Grade Logic Control System to control shift-
ing in E position while the vehicle is ascending or descending a slope.
The PCM is located below the dashboard, under the kick panel on the passenger's side.
Hydraulic Control
The lower valve body assembly includes the main valve body, the Pressure Low (PL) reguiator valve body, the shift valve
body, the start clutch control valve body, and the secondary valve body. They are positioned on the lower part of the
transmission housing.
The main valve body contains the Pressure High (PH) control valve, the lubrication valve, and the pitot regulator valve.
The secondary valve body contains the PH regulator valve, the clutch reducing valve, the start clutch valve accumulator,
and the shift inhibitor valve. The PL regulator valve body contains the PL regulator valve and the PH-PL control valve
which is ioined to the PH,PL control linear solenoid. The inhibitor solenoid valve is bolted on the PL regulator valve body.
The shift valve body contains the shift valve and the shift control valve. which is joined to the shift control linear solenoid.
The start clutch control valve body contains the start clutch control valve, which is joined to the start clutch control linear
solenoid. The linear solenoids and the inhibitor solenoid are controlled by the TCM or PCM. The manual valve body which
contains the manual valve and the reverse inhibitor valve, is bolted on the intermediate housing.
The ATF pump assembly is located on the transmission housing, and is linked with the input shaft by the sprockets and
the sprocket chain. The pulleys and the clutch receive fluid from their respective feed pipes, and the reverse brake receives
fluid from internal hydraulic circuit.
Shift Control Mechanism
Input from various sensors located throughout the vehicle determines which linear solenoid the TCM or PCM will activate.
Activating the shift control linear solenoid changes the shift control valve pressure, causing the shift valve to move. This
pressurizes the drive pulley pressure to the drive pulley and the driven pulley pressure to the driven pulley and changes
their effective pulley ratio. Activating the start clutch control linear solenoid moves the start clutch control valve. The start
clutch control valve uncovers the port, providing pressure to the start clutch to engage it(cont'd)
14-195
,!
Page 931 of 2189
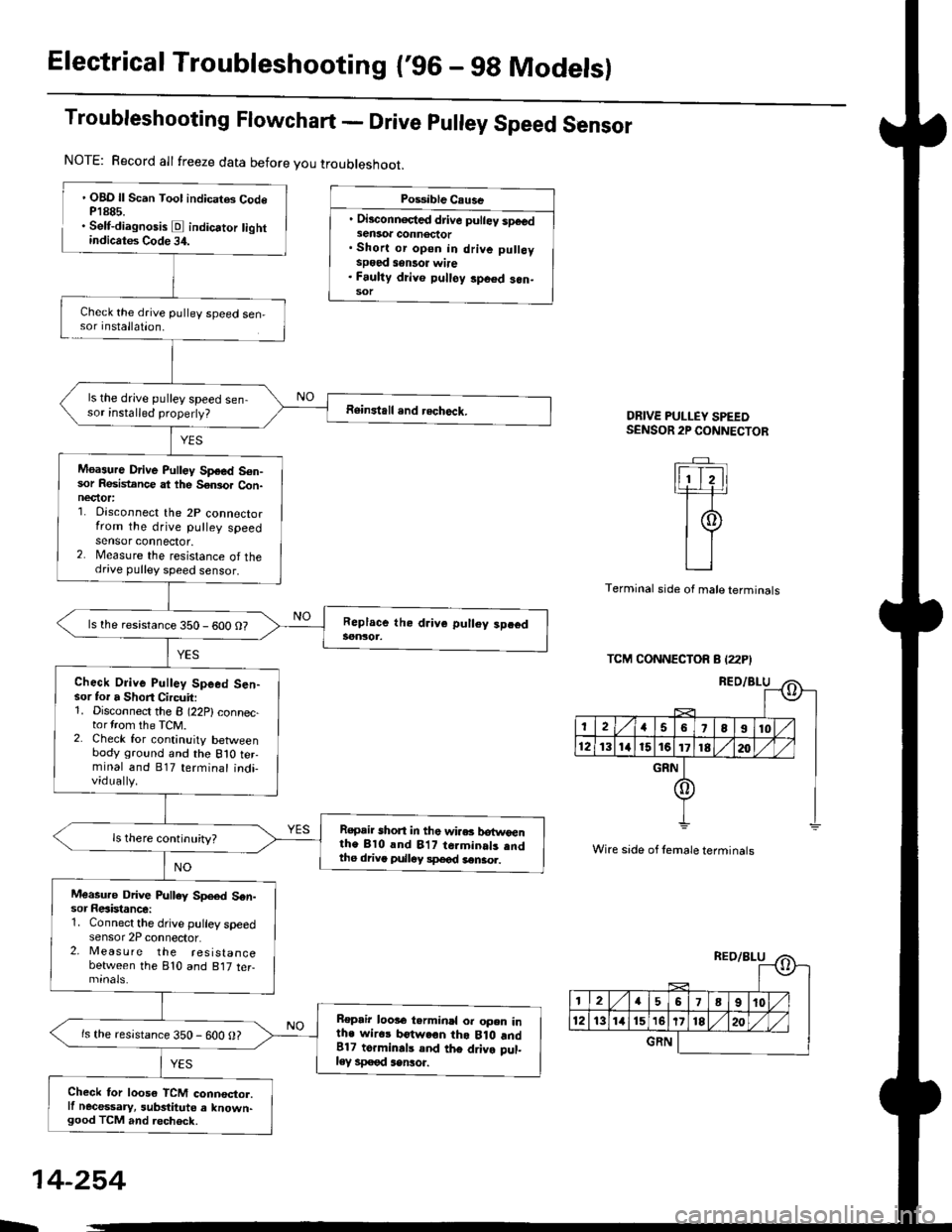
Electrical Troubleshooting {'96 - 9g Models)
Troubleshooting Flowchart - Drive pulley Speed Sensor
' OBD ll Scan Tool indicates CodeP1885.. Self-diagnosis E indicator tightindicates Code 34.
NOTE: Record all freeze data before you troubleshoot,
Check the drive pulley speed sen,sor installation.
ls the drive pulley speed sen-sor installed properly?
M6a3ure Drive Pulley Sp€ed S€n-sor Resistance ai the Seosor Con-nectot:1. Disconnect the 2P connectorfrom the drive pulley speedsensor connector.2. Measure the resistance of thedrive pulley speed sensor.
ls the resistance 350 - 600 O?
Check Orive Pulley Speed Sen-sor tor a Short Circuit:1. Disconnect the B (22P)connec-tortrom the TCM.2. Check for continuity betveenbody ground and the 810 ter-minal and 817 terminal individually.
Rspair shon in the wi.es botwoenthe Bl0 and 817 te.minals andthe driva pulloy 3peod 3eniol.
Measure Drive Pulley Sp€€d Sen-sor Re3istance:1. Connect the drive pulley speedsensor 2P connector.2, Meas u re the resistancebetween the 810 and 817 ter-mtnals.
Repair loos6 t.rmin.l or open inth. wiros botweon tho Bl0 and817 torminals and thg driva pul-ley sp€gd sensor.
ls the resistance 350 - 600 O?
Check tor looso TCM connoctor.ll necessary, substituto a known-good TCM and recheck.
Po$ible Cause
. Oisconn€cted drive pulley speedsensor connector. Shon or op€n in drive pulleyspged sonsor wire. Faulty drive pulley spoed s.n-sot
ORIVE PULLEY SPEEDSENSOR 2P CONNECTOR
lT_ T---_l
1 | 2 tlt| ]--+i-rr
l9tl
L_t
side oI male terminals
TCM CONNECTOR 8 I22PI
REO/BLU
Terminal
Wire side of female terminals
REO/8LU
J(l
24568910v1213t41516171820
GRN
o
1215iliI;W1M
1213111516tdil)lil/l
GRN
14-254
b
Page 932 of 2189
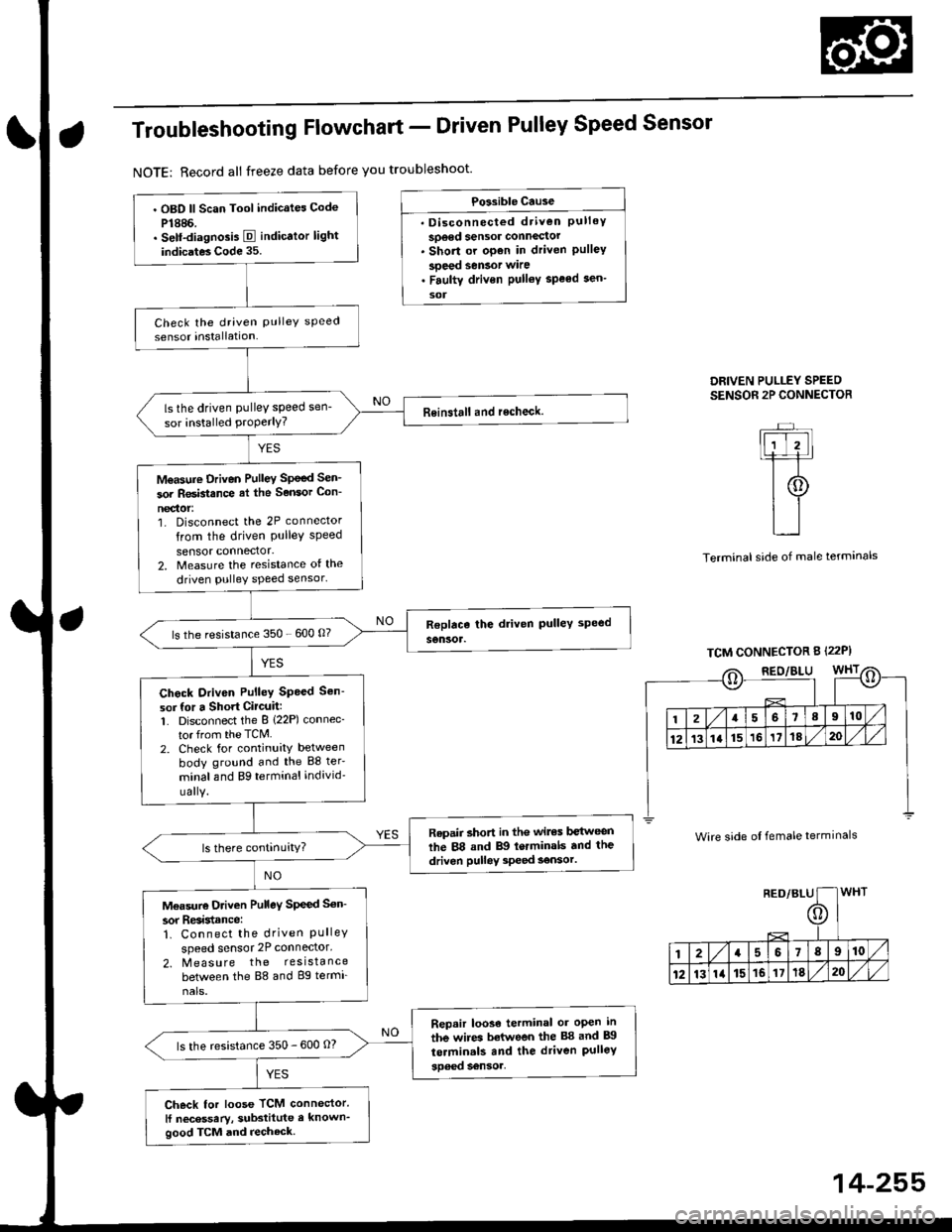
Troubleshooting Flowchart - Driven Pulley Speed Sensor
NOTE: Record all freeze data before you troubleshoot'
Po3sible Cause
. Disconnected dtiven PulleYso6ed sensor connector. Short or open in driven PulleYapeed sen3or wire. Faulty driven PulloY sPeod 3en-
DRIVEN PULLEY SPEEOSENSOR 2P CONNECTOR
l-_r-|1 2l
:-
t9tt
L_.1
Terminal side of male
TCM CONNECTOR I l22p)
WHT
termrnals
. OBD ll Scan Tool indicates Code
P1886.. Sell-diagnosis E indicator light
indicates Code 35.
ls the driven Pulley speed sen-
sor installed proPerlY?
M€asure Driven Pulley SP€ed Sen_
sor Resbt nce at the Sensor Con-
neclof:1. Disconnect the 2P connector
from the driven PUlley speed
sensor connectol.2. Measure the resistance ot the
driven pulley speed sensor.
ls the resistance 350 600 0?
Check Driven Pulley Speed Sen-
sor {or a Short Circuit:1. Disconnect the B (22P) connec_
tor from the TCM.2. Check for continuity between
body ground and the BB ter
minal and 89 terminal individ'
Repair sho.t in the wiles between
lhe 88 and Bg lerminals tnd the
driven pulleY 3Peed 3€nsor.
Measure Driven Pulley SPeed S€n-
sor Reistance:1. Connect the driven PulleYspeed sensor 2P connector'
2. M easu re the resistance
between the 88 and Bg terml_
nals.
Repair loos€ terminal or oPen in
the wires between the Bg and Bg
torminals and the dtiven Pulley3D6eO S6n50a,
ls the resistance 350 - 600 O?
Check lor loose TCM connector.
lf necessary, substitute a known_good TCM and rechack.
^\, REO/BLUo
12a68910
12131a15'16'171820
Wire side oI female terminals
RED/BLU]
o
WHT
1216810
12131a1516171820
14-255
Page 933 of 2189
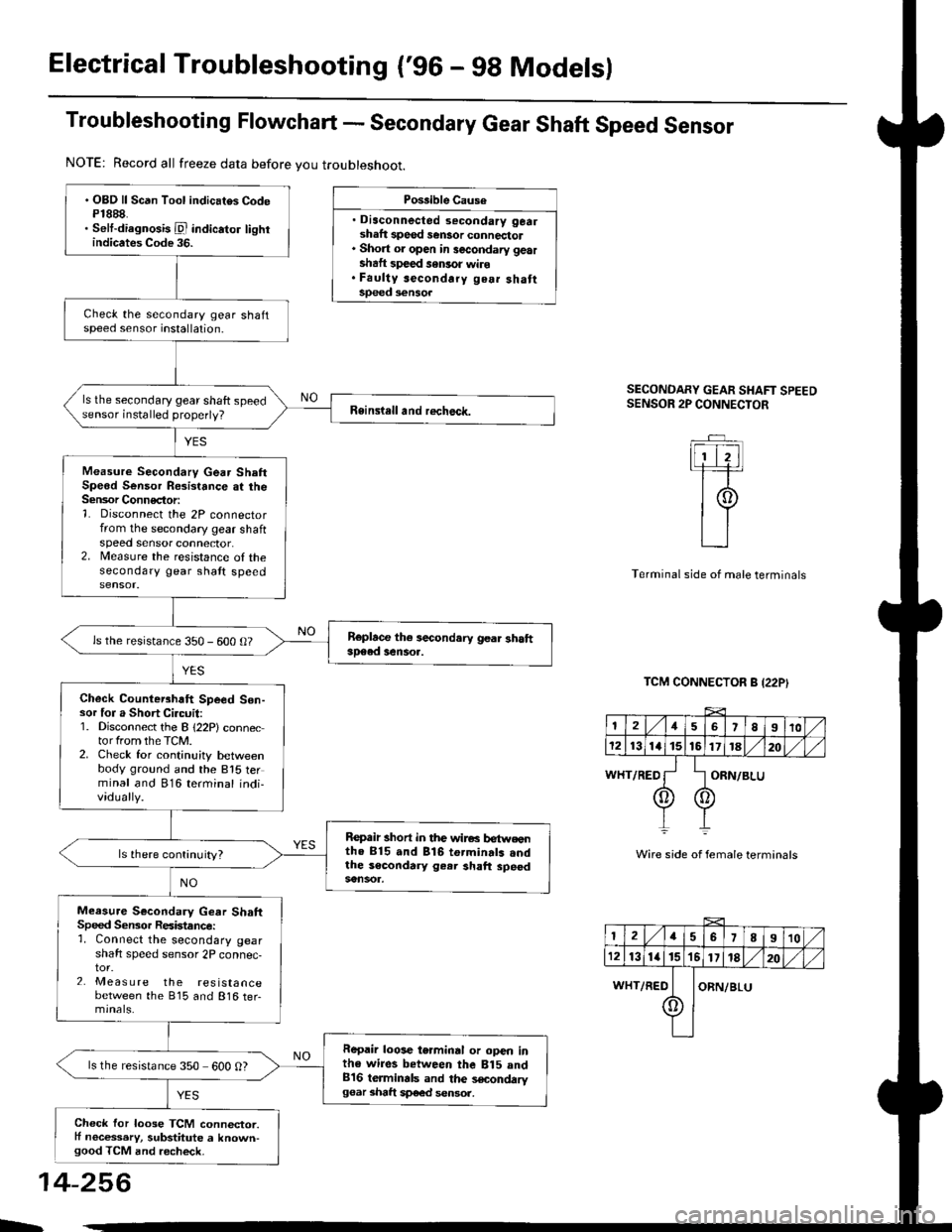
Electrical Troubleshooting ('96 - 98 Modelsl
Troubleshooting Flowchart - Secondary Gear Shaft Speed Sensor
Po$ible Cause
. Disconnected secondary gealshaft speod sen3or connectol. Short ol open in s€condary gearshaft spe€d sen3or wiro. Faulty secondary gear shattspeed s€nsor
SECONDARY GEAR SHAFT SPEEDSENSOR 2P CONNECIOR
llll;ll
T_T
l@
tl
LJ
side of male terminalsTerminal
TCM CONNECTOR B {22P}
Wire side of female termanals
14-256
NOTE: Record all freeze data before you troubleshoot.
. OBD ll Scan Tool indicates CodeP1888.. Selt-diagnosis Iq indicator lightindicates Code 36.
Check the secondary gear shaftspeed sensor installation.
ls the secondary gear shaft speedsensor installed properly?
Measure Secondary Gear SheftSpeod Sensor R8istance at theSensor Connector:1. Disconnect the 2P connectorfrom the secondary gear shaftspeed sensor connector.2. Measure the resistance ol thesecondary gear shalt speed
ls the resistance 350 - 600 0?
Check Counterchaft Speed Son-sor for a Short Circuit:1. Disconnect the B 122P) connectorfrom the TCM.2. Check for continuity betweenbody ground and the 815 terminal and 816 terminal individually.
Repair short in the wir€6 bctuveenth. 815 and 816 torminrls.ndthe s€condary ge.r shaft speodls there continuity?
Measu.e Secondary Gear ShattSpeed Sensor Resistance:1. Connect the secondary gearshaft speed sensor 2P connec-
2. Meas u re the resistancebetween the 815 and 816 te.mrnals.
Reprir loose terminal or opcn inthe wires between the 815 and8'16 terminals and the secondaryg€ar shaft sp€ed s€nsor,
ls the resistance 350 600 O?
Check lor loose TCM connector.lf n€cessary, substitute a known-good TCM and recheck.
I2156910
12131a1516171820
WHT/RED T - ORN/BLU
D (o.
1a5678I10
1213141515171820
WHT/REI
A
I
ORN/BLU
L
Page 956 of 2189
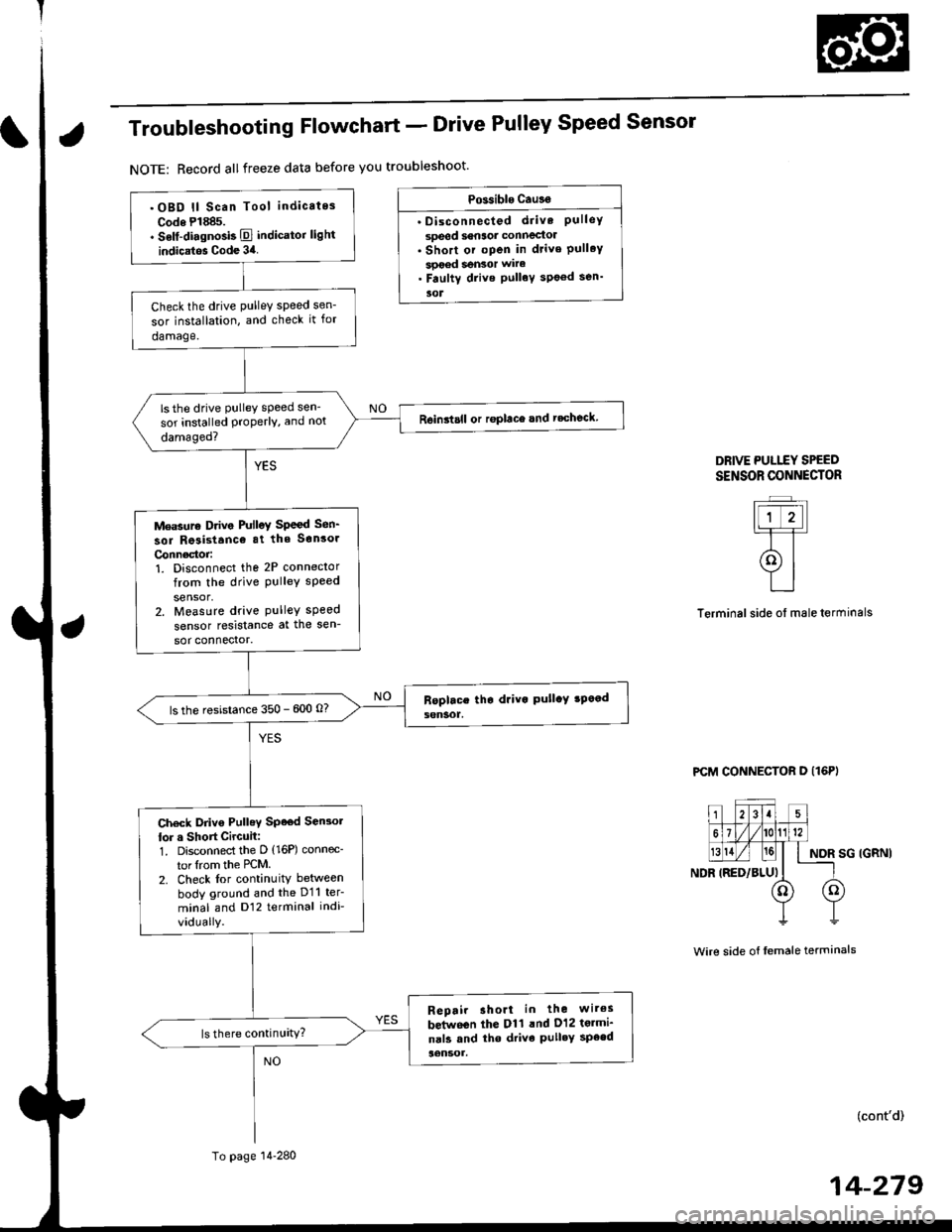
Troubleshooting Flowchart - Drive Pulley Speed Sensor
NOTE: Record allfreeze data before you troubleshoot'
Possible Cau3€
. Disconnected diive PulleYsoeed s6n3or connectol. Short or open in drive Pull.Ysooed sonsor wire. FaultY drive PulleY spo€d sen'
301
DRIVE PULEY SPEED
SENSOR @NNEfiOR
Terminal side of male terminals
PCM CONNECTOR D (16PI
NDR SG IGRNI
Wire side o{ Iemale terminals
(cont'd)
14-279
.OBD ll Scan Tool indicates
Code Pl885.. Selt-diagnosb E indicator light
indicatos Code 34
check the drive pulleY sPeed sen-
sor installation, and check it for
damage.
ls the drive PulleY speed sen-
sor installed properly, and not
damaged?
Rein3tall or roplace and techeck
Measuro Drive PulleY Speed Sen_
sor Ro3istanco at the Sonsol
Connector:1. Disconnect the 2P conneclor
from the drive Pulley speed
sensor,2. Measure drive Pulley speed
sensor resislance at the sen-
sor connecror.
ls the resistance 350 - 600 O?
Check Drivo PulleY SP6€d Sen3o.
lor . Short Circuit:1. Disconnect the D {16P) connec-
torlrom the PCM.
2. Check lor continuity between
body ground and the D11 ter
minal and D'l2 terminal indi
vidually.
Repai. short in the wiles
between the Dll lnd D12 termi-
nals and iho drive Pull.Y speed
To page 14-280
Page 957 of 2189
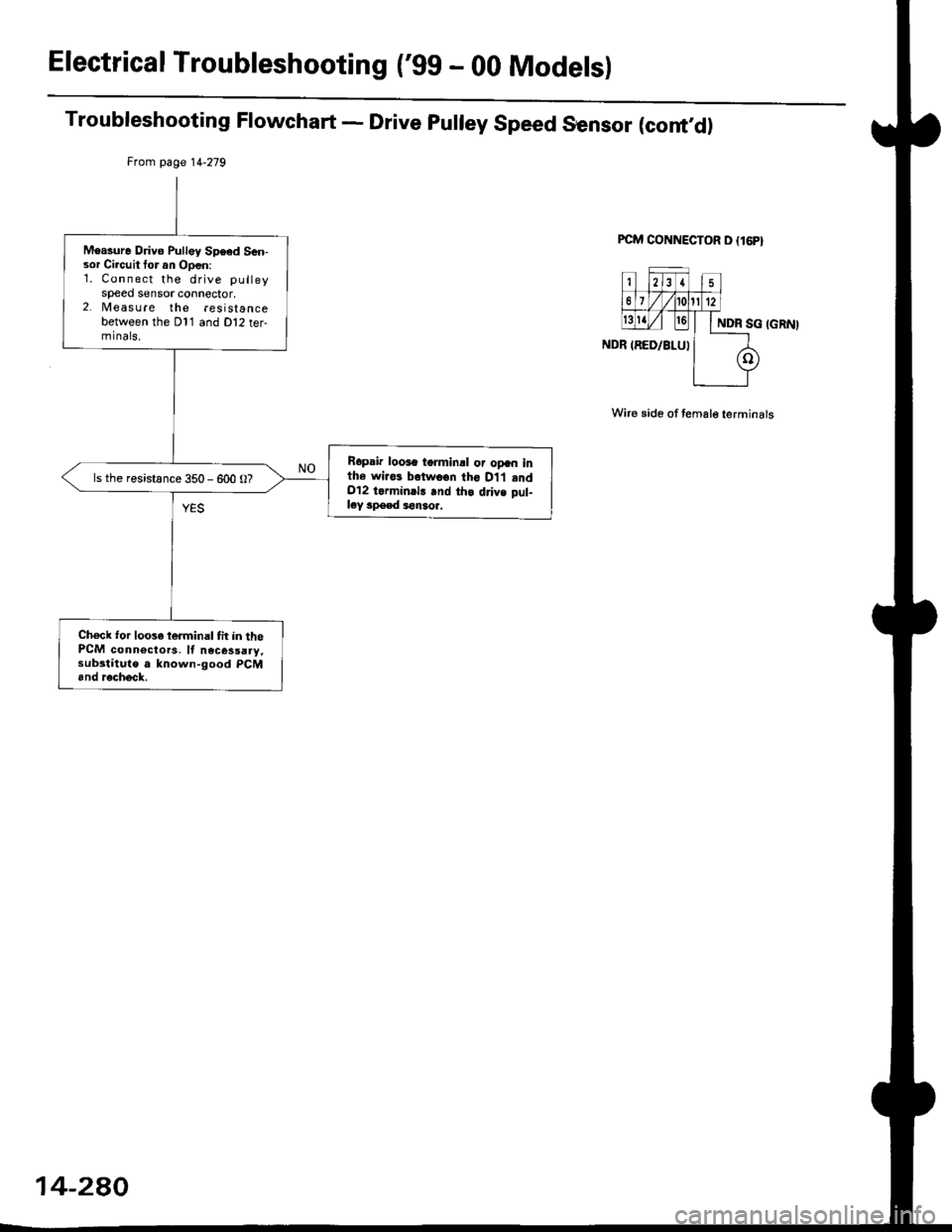
Electrical Troubleshooting ('gg - 00 Models)
Troubleshooting Flowchart - Drive pulley Speed Sensor (cont,d)
PCM CONNECTOR D {16P}
Wire side of temale terminals
From page 14-279
Measure Drivo Pulley Speed Sen-sor Circuit tor an Open:1. Connect the drive pulleyspeed sensor connector,2. lvleasu re the resistancebetween the Dl1 and Dl2 ter-minals.
R6pair loose tgrminal or opan inthe wiros betwo€n tho D1,l .ndOl2 tarminrl! .nd th. drivs pul-ley speed *n3or.
ls the resistance 350 - 600 O?
Ch6ck for loose lerminal tit in thePCM connectors, ll nece3saay,substituto a known-good PCM6nd r€check.
14-280
Page 958 of 2189
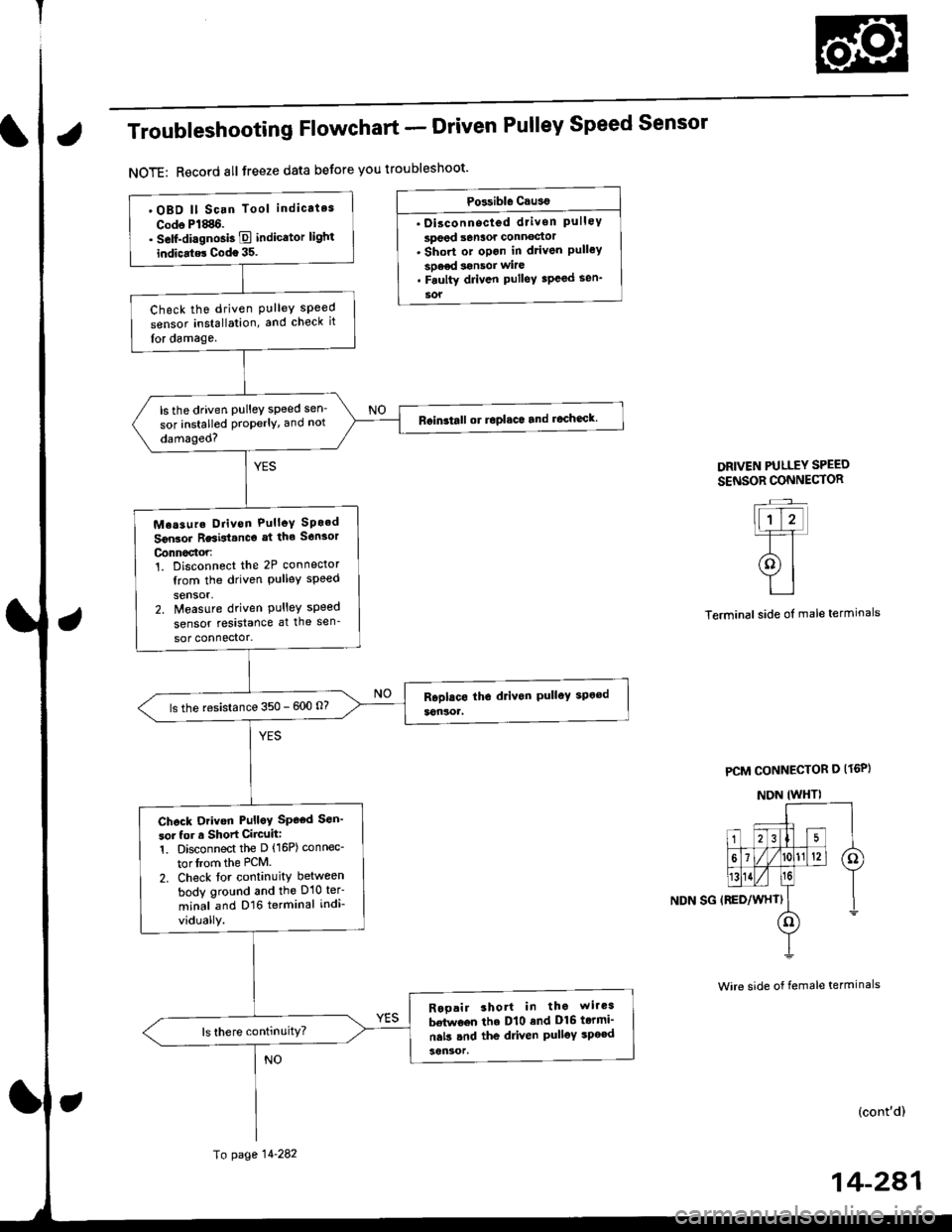
Troubleshooting Flowchart - Driven Pulley Speed Sensor
NOTE: Record all freeze data betore you troubleshoot'
Po3sible Caus€
' Oisconnected driven PulleYspeed s6nlor connoctor. Short or opon in d.iven Pulleysoeed sonsol wirc. Faulty driven Pulley speed sen_
sor
DRIVEN PULLEY SPEED
SENSOR CONNECTOR
Terminal side ol male terminals
FCM CONNECTOR D If6P)
NDN IWHTI
Wire side of female terminals
(cont'd)
'OBD lt Sc.n Tool indicates
Code Pl886.. Self-diagnosb E indicator light
indicrt€. Codo 35.
Check the driven Pulley speed
sensor installation, and check it
Ior damage.
lsthe driven pulleY speed sen'
sor installed ProPerly, and not
damaged?
Boin3tall or ropl.ca and recheck.
M..sure Drivon PulloY SPoed
Sonsor Rosblanco at the S6n3or
Conn6ctori1. Disconnect the 2P connector
trom the driven PUlley sPeed
sensor,2. lveasure driven Pulley speed
sensor resistance at the sen_
sor connector.
ls the resistance 350 - 600 0?
Check Dtivon Pulloy SP€ed Sen'
sor for a Short Circuit:
1. Disconnect the D (16P) connec-
torfrom the PCM.
2. Check tor continuity between
body ground and the D10 ter'
minal and Dl6 terminal indi-
vidually.
Raoair shott in tho wi.6s
betwoon th. Dlo end D16 tormi'
nak .nd the ddven Pulley spo€d
Fo page 14'282
14-2A1