stop start INFINITI FX35 2006 Owner's Manual
[x] Cancel search | Manufacturer: INFINITI, Model Year: 2006, Model line: FX35, Model: INFINITI FX35 2006Pages: 4462, PDF Size: 57.74 MB
Page 602 of 4462
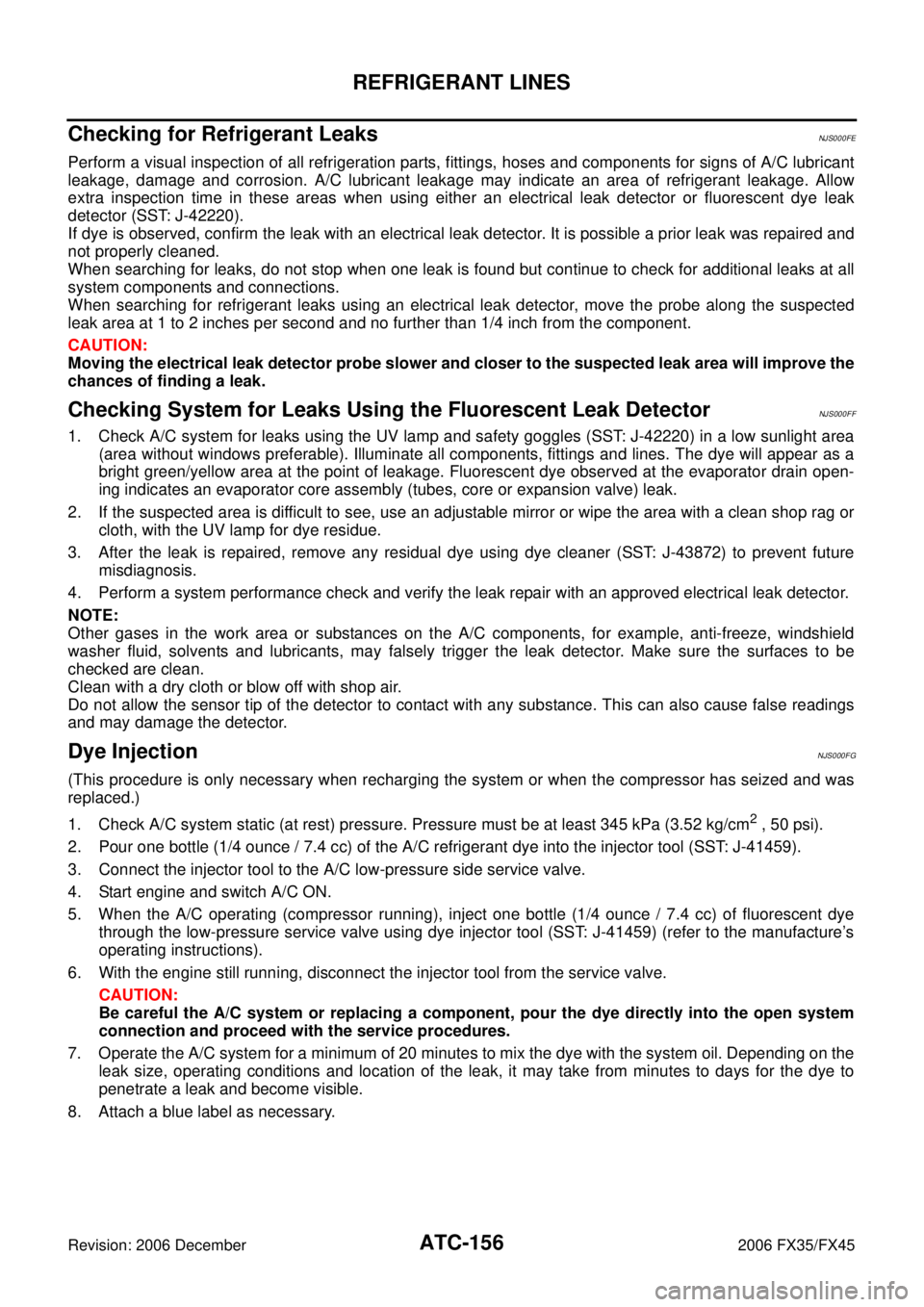
ATC-156
REFRIGERANT LINES
Revision: 2006 December 2006 FX35/FX45
Checking for Refrigerant LeaksNJS000FE
Perform a visual inspection of all refrigeration parts, fittings, hoses and components for signs of A/C lubricant
leakage, damage and corrosion. A/C lubricant leakage may indicate an area of refrigerant leakage. Allow
extra inspection time in these areas when using either an electrical leak detector or fluorescent dye leak
detector (SST: J-42220).
If dye is observed, confirm the leak with an electrical leak detector. It is possible a prior leak was repaired and
not properly cleaned.
When searching for leaks, do not stop when one leak is found but continue to check for additional leaks at all
system components and connections.
When searching for refrigerant leaks using an electrical leak detector, move the probe along the suspected
leak area at 1 to 2 inches per second and no further than 1/4 inch from the component.
CAUTION:
Moving the electrical leak detector probe slower and closer to the suspected leak area will improve the
chances of finding a leak.
Checking System for Leaks Using the Fluorescent Leak DetectorNJS000FF
1. Check A/C system for leaks using the UV lamp and safety goggles (SST: J-42220) in a low sunlight area (area without windows preferable). Illuminate all components, fittings and lines. The dye will appear as a
bright green/yellow area at the point of leakage. Fluorescent dye observed at the evaporator drain open-
ing indicates an evaporator core assembly (tubes, core or expansion valve) leak.
2. If the suspected area is difficult to see, use an adjustable mirror or wipe the area with a clean shop rag or cloth, with the UV lamp for dye residue.
3. After the leak is repaired, remove any residual dye using dye cleaner (SST: J-43872) to prevent future misdiagnosis.
4. Perform a system performance check and verify the leak repair with an approved electrical leak detector.
NOTE:
Other gases in the work area or substances on the A/C components, for example, anti-freeze, windshield
washer fluid, solvents and lubricants, may falsely trigger the leak detector. Make sure the surfaces to be
checked are clean.
Clean with a dry cloth or blow off with shop air.
Do not allow the sensor tip of the detector to contact with any substance. This can also cause false readings
and may damage the detector.
Dye InjectionNJS000FG
(This procedure is only necessary when recharging the system or when the compressor has seized and was
replaced.)
1. Check A/C system static (at rest) pressure. Pressure must be at least 345 kPa (3.52 kg/cm
2 , 50 psi).
2. Pour one bottle (1/4 ounce / 7.4 cc) of the A/C refrigerant dye into the injector tool (SST: J-41459).
3. Connect the injector tool to the A/C low-pressure side service valve.
4. Start engine and switch A/C ON.
5. When the A/C operating (compressor running), inject one bottle (1/4 ounce / 7.4 cc) of fluorescent dye through the low-pressure service valve using dye injector tool (SST: J-41459) (refer to the manufacture’s
operating instructions).
6. With the engine still running, disconnect the injector tool from the service valve. CAUTION:
Be careful the A/C system or replacing a component, pour the dye directly into the open system
connection and proceed with the service procedures.
7. Operate the A/C system for a minimum of 20 minutes to mix the dye with the system oil. Depending on the leak size, operating conditions and location of the leak, it may take from minutes to days for the dye to
penetrate a leak and become visible.
8. Attach a blue label as necessary.
Page 604 of 4462
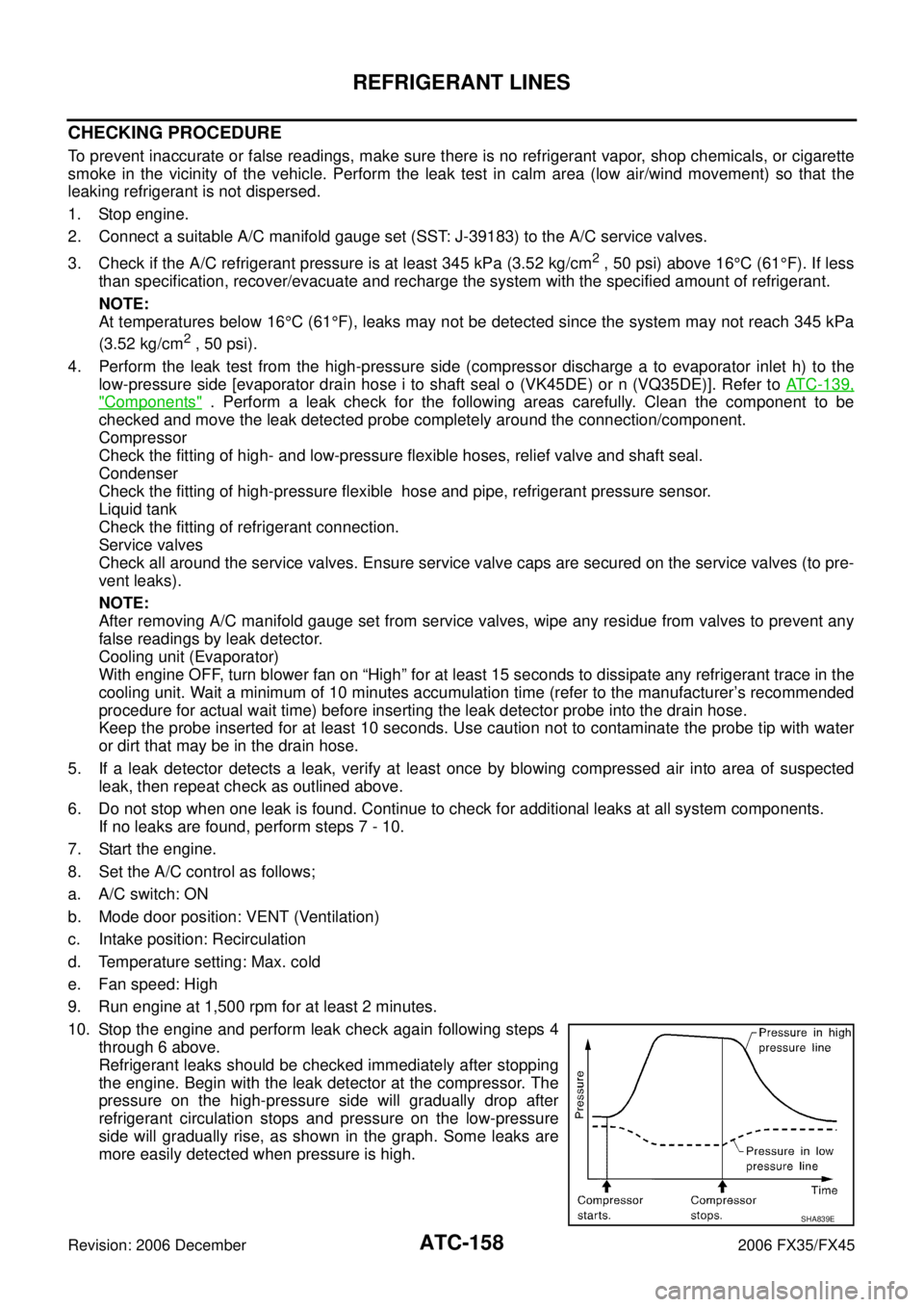
ATC-158
REFRIGERANT LINES
Revision: 2006 December 2006 FX35/FX45
CHECKING PROCEDURE
To prevent inaccurate or false readings, make sure there is no refrigerant vapor, shop chemicals, or cigarette
smoke in the vicinity of the vehicle. Perform the leak test in calm area (low air/wind movement) so that the
leaking refrigerant is not dispersed.
1. Stop engine.
2. Connect a suitable A/C manifold gauge set (SST: J-39183) to the A/C service valves.
3. Check if the A/C refrigerant pressure is at least 345 kPa (3.52 kg/cm
2 , 50 psi) above 16 °C (61 °F). If less
than specification, recover/evacuate and recharge the system with the specified amount of refrigerant.
NOTE:
At temperatures below 16 °C (61 °F), leaks may not be detected since the system may not reach 345 kPa
(3.52 kg/cm
2 , 50 psi).
4. Perform the leak test from the high-pressure side (compressor discharge a to evaporator inlet h) to the low-pressure side [evaporator drain hose i to shaft seal o (VK45DE) or n (VQ35DE)]. Refer to ATC-139,
"Components" . Perform a leak check for the following areas carefully. Clean the component to be
checked and move the leak detected probe completely around the connection/component.
Compressor
Check the fitting of high- and low-pressure flexible hoses, relief valve and shaft seal.
Condenser
Check the fitting of high-pressure flexible hose and pipe, refrigerant pressure sensor.
Liquid tank
Check the fitting of refrigerant connection.
Service valves
Check all around the service valves. Ensure service valve caps are secured on the service valves (to pre-
vent leaks).
NOTE:
After removing A/C manifold gauge set from service valves, wipe any residue from valves to prevent any
false readings by leak detector.
Cooling unit (Evaporator)
With engine OFF, turn blower fan on “High” for at least 15 seconds to dissipate any refrigerant trace in the
cooling unit. Wait a minimum of 10 minutes accumulation time (refer to the manufacturer’s recommended
procedure for actual wait time) before inserting the leak detector probe into the drain hose.
Keep the probe inserted for at least 10 seconds. Use caution not to contaminate the probe tip with water
or dirt that may be in the drain hose.
5. If a leak detector detects a leak, verify at least once by blowing compressed air into area of suspected leak, then repeat check as outlined above.
6. Do not stop when one leak is found. Continue to check for additional leaks at all system components. If no leaks are found, perform steps 7 - 10.
7. Start the engine.
8. Set the A/C control as follows;
a. A/C switch: ON
b. Mode door position: VENT (Ventilation)
c. Intake position: Recirculation
d. Temperature setting: Max. cold
e. Fan speed: High
9. Run engine at 1,500 rpm for at least 2 minutes.
10. Stop the engine and perform leak check again following steps 4 through 6 above.
Refrigerant leaks should be checked immediately after stopping
the engine. Begin with the leak detector at the compressor. The
pressure on the high-pressure side will gradually drop after
refrigerant circulation stops and pressure on the low-pressure
side will gradually rise, as shown in the graph. Some leaks are
more easily detected when pressure is high.
SHA839E
Page 648 of 4462
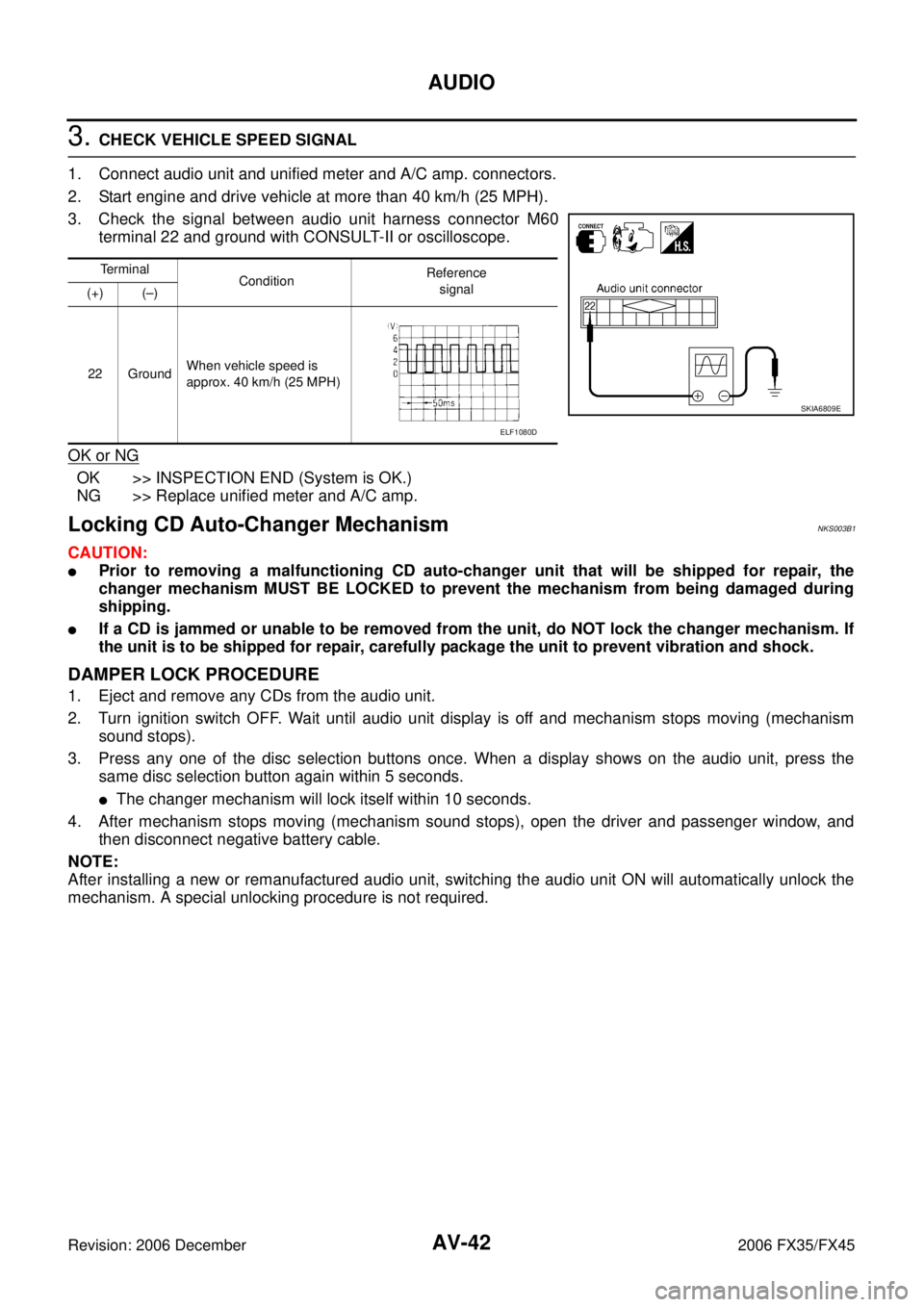
AV-42
AUDIO
Revision: 2006 December 2006 FX35/FX45
3. CHECK VEHICLE SPEED SIGNAL
1. Connect audio unit and unified meter and A/C amp. connectors.
2. Start engine and drive vehicle at more than 40 km/h (25 MPH).
3. Check the signal between audio unit harness connector M60 terminal 22 and ground with CONSULT-II or oscilloscope.
OK or NG
OK >> INSPECTION END (System is OK.)
NG >> Replace unified meter and A/C amp.
Locking CD Auto-Changer MechanismNKS003B1
CAUTION:
Prior to removing a malfunctioning CD auto-changer unit that will be shipped for repair, the
changer mechanism MUST BE LOCKED to prevent the mechanism from being damaged during
shipping.
If a CD is jammed or unable to be removed from the unit, do NOT lock the changer mechanism. If
the unit is to be shipped for repair, carefully package the unit to prevent vibration and shock.
DAMPER LOCK PROCEDURE
1. Eject and remove any CDs from the audio unit.
2. Turn ignition switch OFF. Wait until audio unit display is off and mechanism stops moving (mechanism sound stops).
3. Press any one of the disc selection buttons once. When a display shows on the audio unit, press the same disc selection button again within 5 seconds.
The changer mechanism will lock itself within 10 seconds.
4. After mechanism stops moving (mechanism sound stops), open the driver and passenger window, and then disconnect negative battery cable.
NOTE:
After installing a new or remanufactured audio unit, switching the audio unit ON will automatically unlock the
mechanism. A special unlocking procedure is not required.
Terminal Condition Reference
signal
(+) (–)
22 Ground When vehicle speed is
approx. 40 km/h (25 MPH)
SKIA6809E
ELF1080D
Page 816 of 4462
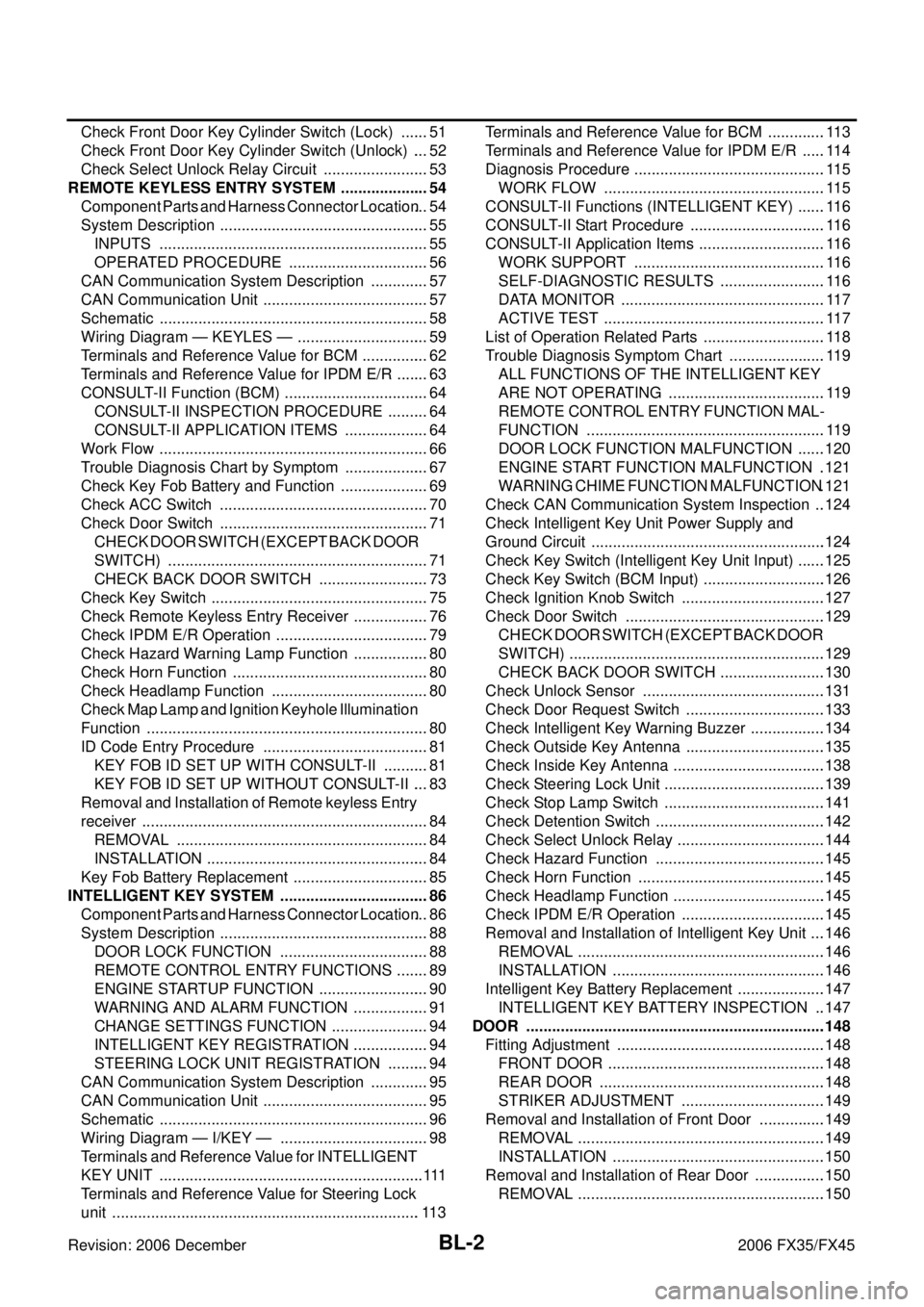
BL-2Revision: 2006 December 2006 FX35/FX45 Check Front Door Key Cylinder Switch (Lock) ....
... 51
Check Front Door Key Cylinder Switch (Unlock) . ... 52
Check Select Unlock Relay Circuit ...................... ... 53
REMOTE KEYLESS ENTRY SYSTEM .................. ... 54
Component Parts and Harness Connector Location ... 54
System Description .............................................. ... 55
INPUTS ............................................................ ... 55
OPERATED PROCEDURE .............................. ... 56
CAN Communication System Description ........... ... 57
CAN Communication Unit .................................... ... 57
Schematic ............................................................ ... 58
Wiring Diagram — KEYLES — ............................ ... 59
Terminals and Reference Value for BCM ............. ... 62
Terminals and Reference Value for IPDM E/R ..... ... 63
CONSULT-II Function (BCM) ............................... ... 64
CONSULT-II INSPECTION PROCEDURE ....... ... 64
CONSULT-II APPLICATION ITEMS ................. ... 64
Work Flow ............................................................ ... 66
Trouble Diagnosis Chart by Symptom ................. ... 67
Check Key Fob Battery and Function .................. ... 69
Check ACC Switch .............................................. ... 70
Check Door Switch .............................................. ... 71
CHECK DOOR SWITCH (EXCEPT BACK DOOR
SWITCH) .......................................................... ... 71
CHECK BACK DOOR SWITCH ....................... ... 73
Check Key Switch ................................................ ... 75
Check Remote Keyless Entry Receiver ............... ... 76
Check IPDM E/R Operation ................................. ... 79
Check Hazard Warning Lamp Function ............... ... 80
Check Horn Function ........................................... ... 80
Check Headlamp Function .................................. ... 80
Check Map Lamp and Ignition Keyhole Illumination
Function ............................................................... ... 80
ID Code Entry Procedure .................................... ... 81
KEY FOB ID SET UP WITH CONSULT-II ........ ... 81
KEY FOB ID SET UP WITHOUT CONSULT-II . ... 83
Removal and Installation of Remote keyless Entry
receiver ................................................................ ... 84
REMOVAL ........................................................ ... 84
INSTALLATION ................................................. ... 84
Key Fob Battery Replacement ............................. ... 85
INTELLIGENT KEY SYSTEM ................................ ... 86
Component Parts and Harness Connector Location ... 86
System Description .............................................. ... 88
DOOR LOCK FUNCTION ................................ ... 88
REMOTE CONTROL ENTRY FUNCTIONS ..... ... 89
ENGINE STARTUP FUNCTION ....................... ... 90
WARNING AND ALARM FUNCTION ............... ... 91
CHANGE SETTINGS FUNCTION .................... ... 94
INTELLIGENT KEY REGISTRATION ............... ... 94
STEERING LOCK UNIT REGISTRATION ....... ... 94
CAN Communication System Description ........... ... 95
CAN Communication Unit .................................... ... 95
Schematic ............................................................ ... 96
Wiring Diagram — I/KEY — ................................ ... 98
Terminals and Reference Value for INTELLIGENT
KEY UNIT ............................................................ ..111
Terminals and Reference Value for Steering Lock
unit ....................................................................... .113 Terminals and Reference Value for BCM .............
.113
Terminals and Reference Value for IPDM E/R ..... .114
Diagnosis Procedure ............................................ .115
WORK FLOW ................................................... .115
CONSULT-II Functions (INTELLIGENT KEY) ...... .116
CONSULT-II Start Procedure ............................... .116
CONSULT-II Application Items ............................. .116
WORK SUPPORT ............................................ .116
SELF-DIAGNOSTIC RESULTS ........................ .116
DATA MONITOR ............................................... .117
ACTIVE TEST ................................................... .117
List of Operation Related Parts ............................ .118
Trouble Diagnosis Symptom Chart ...................... .119
ALL FUNCTIONS OF THE INTELLIGENT KEY
ARE NOT OPERATING .................................... .119
REMOTE CONTROL ENTRY FUNCTION MAL-
FUNCTION ....................................................... .119
DOOR LOCK FUNCTION MALFUNCTION ...... .120
ENGINE START FUNCTION MALFUNCTION . .121
WARNING CHIME FUNCTION MALFUNCTION .121
Check CAN Communication System Inspection .. .124
Check Intelligent Key Unit Power Supply and
Ground Circuit ...................................................... .124
Check Key Switch (Intelligent Key Unit Input) ...... .125
Check Key Switch (BCM Input) ............................ .126
Check Ignition Knob Switch ................................. .127
Check Door Switch .............................................. .129
CHECK DOOR SWITCH (EXCEPT BACK DOOR
SWITCH) ........................................................... .129
CHECK BACK DOOR SWITCH ........................ .130
Check Unlock Sensor .......................................... .131
Check Door Request Switch ................................ .133
Check Intelligent Key Warning Buzzer ................. .134
Check Outside Key Antenna ................................ .135
Check Inside Key Antenna ................................... .138
Check Steering Lock Unit ..................................... .139
Check Stop Lamp Switch ..................................... .141
Check Detention Switch ....................................... .142
Check Select Unlock Relay .................................. .144
Check Hazard Function ....................................... .145
Check Horn Function ........................................... .145
Check Headlamp Function ................................... .145
Check IPDM E/R Operation ................................. .145
Removal and Installation of Intelligent Key Unit ... .146
REMOVAL ......................................................... .146
INSTALLATION ................................................. .146
Intelligent Key Battery Replacement .................... .147
INTELLIGENT KEY BATTERY INSPECTION .. .147
DOOR ..................................................................... .148
Fitting Adjustment ................................................ .148
FRONT DOOR .................................................. .148
REAR DOOR .................................................... .148
STRIKER ADJUSTMENT ................................. .149
Removal and Installation of Front Door ............... .149
REMOVAL ......................................................... .149
INSTALLATION ................................................. .150
Removal and Installation of Rear Door ................ .150
REMOVAL ......................................................... .150
Page 823 of 4462
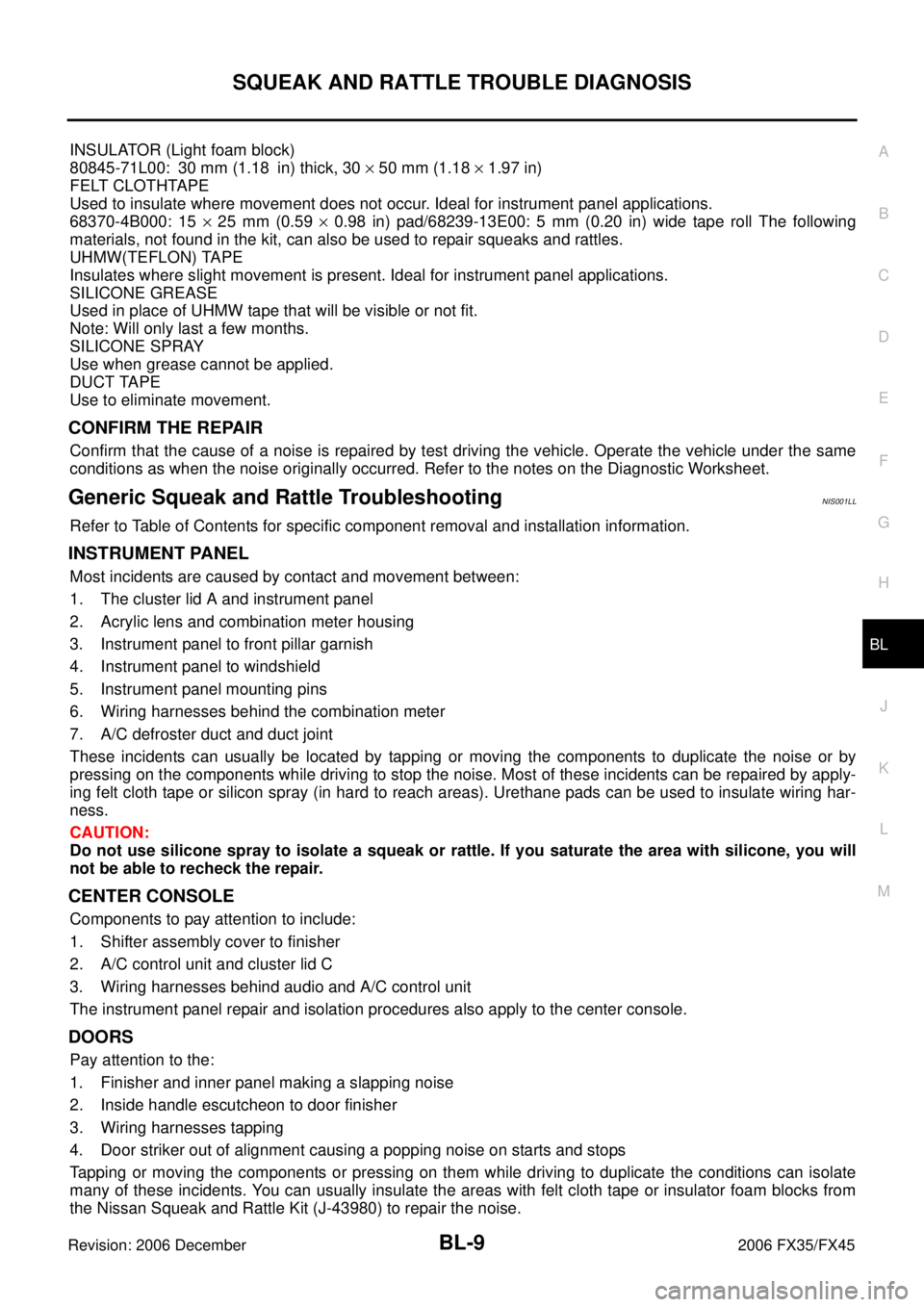
SQUEAK AND RATTLE TROUBLE DIAGNOSIS BL-9
C
D E
F
G H
J
K L
M A
B
BL
Revision: 2006 December 2006 FX35/FX45
INSULATOR (Light foam block)
80845-71L00: 30 mm (1.18 in) thick, 30 × 50 mm (1.18 × 1.97 in)
FELT CLOTHTAPE
Used to insulate where movement does not occur. Ideal for instrument panel applications.
68370-4B000: 15 × 25 mm (0.59 × 0.98 in) pad/68239-13E00: 5 mm (0.20 in) wide tape roll The following
materials, not found in the kit, can also be used to repair squeaks and rattles.
UHMW(TEFLON) TAPE
Insulates where slight movement is present. Ideal for instrument panel applications.
SILICONE GREASE
Used in place of UHMW tape that will be visible or not fit.
Note: Will only last a few months.
SILICONE SPRAY
Use when grease cannot be applied.
DUCT TAPE
Use to eliminate movement.
CONFIRM THE REPAIR
Confirm that the cause of a noise is repaired by test driving the vehicle. Operate the vehicle under the same
conditions as when the noise originally occurred. Refer to the notes on the Diagnostic Worksheet.
Generic Squeak and Rattle TroubleshootingNIS001LL
Refer to Table of Contents for specific component removal and installation information.
INSTRUMENT PANEL
Most incidents are caused by contact and movement between:
1. The cluster lid A and instrument panel
2. Acrylic lens and combination meter housing
3. Instrument panel to front pillar garnish
4. Instrument panel to windshield
5. Instrument panel mounting pins
6. Wiring harnesses behind the combination meter
7. A/C defroster duct and duct joint
These incidents can usually be located by tapping or moving the components to duplicate the noise or by
pressing on the components while driving to stop the noise. Most of these incidents can be repaired by apply-
ing felt cloth tape or silicon spray (in hard to reach areas). Urethane pads can be used to insulate wiring har-
ness.
CAUTION:
Do not use silicone spray to isolate a squeak or rattle. If you saturate the area with silicone, you will
not be able to recheck the repair.
CENTER CONSOLE
Components to pay attention to include:
1. Shifter assembly cover to finisher
2. A/C control unit and cluster lid C
3. Wiring harnesses behind audio and A/C control unit
The instrument panel repair and isolation procedures also apply to the center console.
DOORS
Pay attention to the:
1. Finisher and inner panel making a slapping noise
2. Inside handle escutcheon to door finisher
3. Wiring harnesses tapping
4. Door striker out of alignment causing a popping noise on starts and stops
Tapping or moving the components or pressing on them while driving to duplicate the conditions can isolate
many of these incidents. You can usually insulate the areas with felt cloth tape or insulator foam blocks from
the Nissan Squeak and Rattle Kit (J-43980) to repair the noise.
Page 932 of 4462
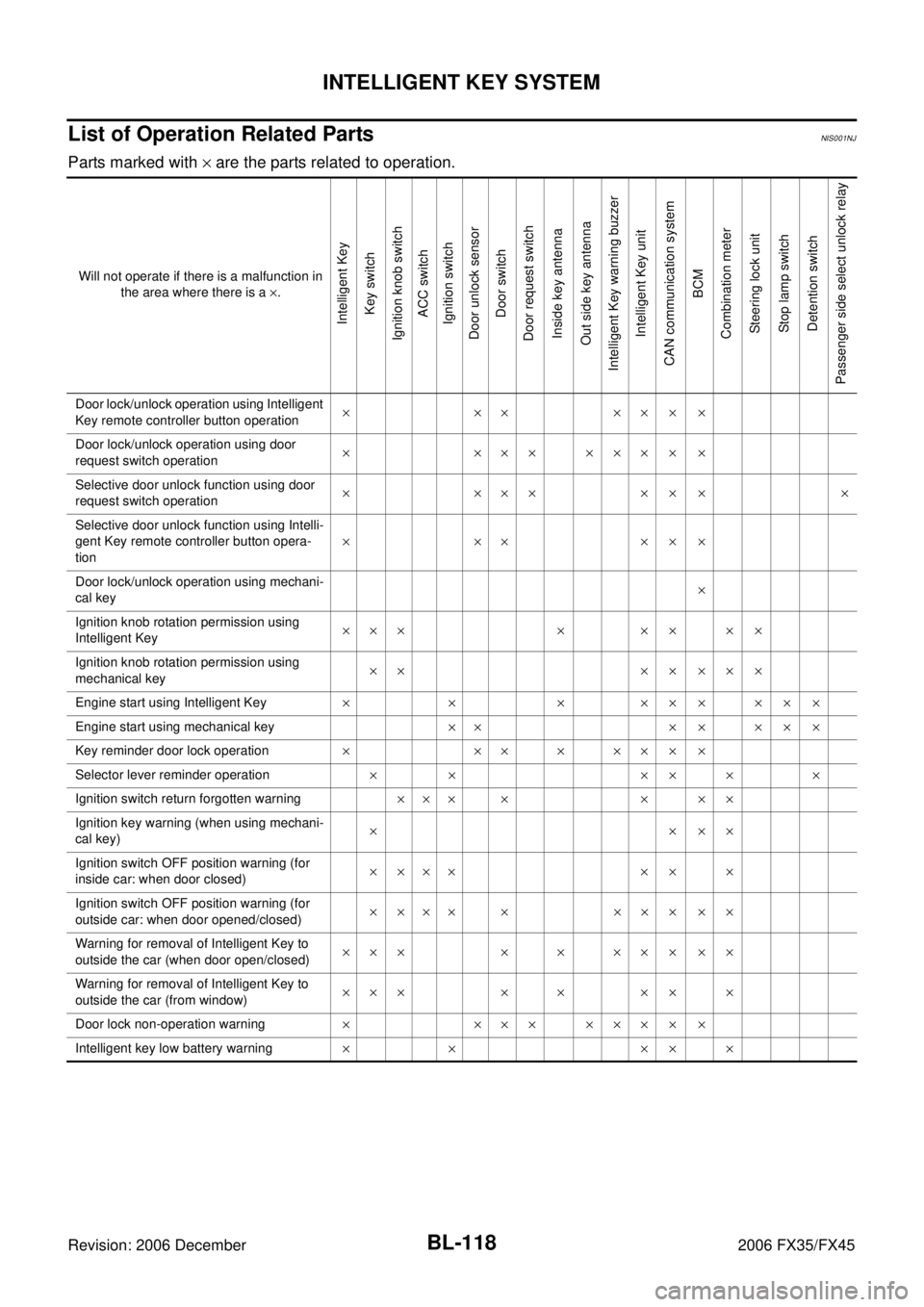
BL-118
INTELLIGENT KEY SYSTEM
Revision: 2006 December 2006 FX35/FX45
List of Operation Related PartsNIS001NJ
Parts marked with × are the parts related to operation.
Will not operate if there is a malfunction in
the area where there is a ×.
Intelligent Key
Key switch
Ignition knob switch ACC switch
Ignition switch
Door unlock sensor
Door switch
Door request switch
Inside key antenna
Out side key antenna
Intelligent Key warning buzzer Intelligent Key unit
CAN communication system
BCM
Combination meter
Steering lock unitStop lamp switch Detention switch
Passenger side select unlock relay
Door lock/unlock operation using Intelligent
Key remote controller button operation ×××××××
Door lock/unlock operation using door
request switch operation ×××××××××
Selective door unlock function using door
request switch operation ××××××× ×
Selective door unlock function using Intelli-
gent Key remote controller button opera-
tion ××× ×××
Door lock/unlock operation using mechani-
cal key ×
Ignition knob rotation permission using
Intelligent Key ××× × × × × ×
Ignition knob rotation permission using
mechanical key ×× × × ×× ×
Engine start using Intelligent Key ×× ×××××××
Engine start using mechanical key ×× × × × × ×
Key reminder door lock operation ××××××××
Selector lever reminder operation ×× ××× ×
Ignition switch return forgotten warning ××× × × × ×
Ignition key warning (when using mechani-
cal key) ××××
Ignition switch OFF position warning (for
inside car: when door closed) ×××× × × ×
Ignition switch OFF position warning (for
outside car: when door opened/closed) ×××× × ×× × ××
Warning for removal of Intelligent Key to
outside the car (when door open/closed) ××× × × ×× × × ×
Warning for removal of Intelligent Key to
outside the car (from window) ××× × × × × ×
Door lock non-operation warning ×××××××××
Intelligent key low battery warning ×× ×××
Page 935 of 4462
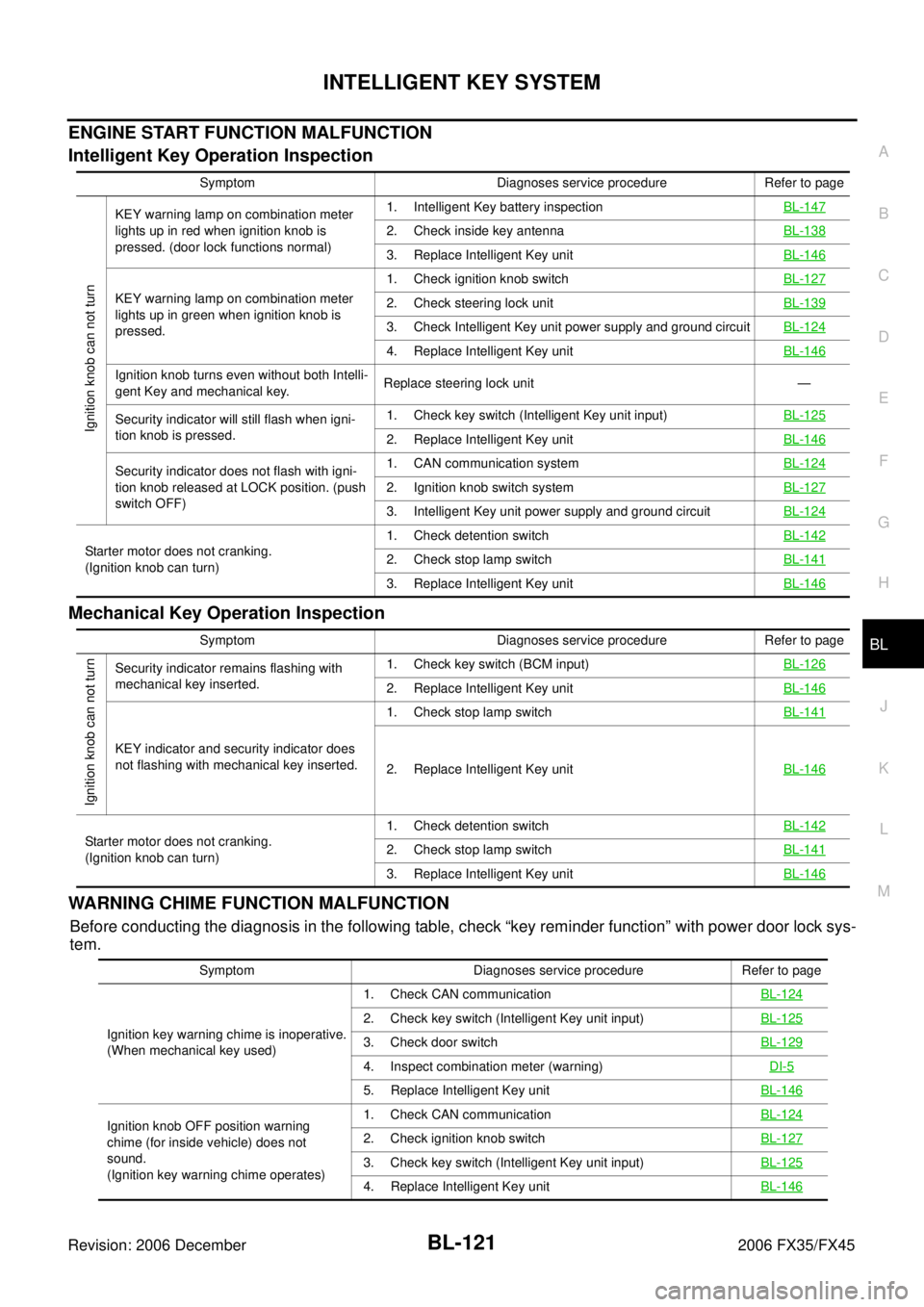
INTELLIGENT KEY SYSTEM BL-121
C
D E
F
G H
J
K L
M A
B
BL
Revision: 2006 December 2006 FX35/FX45
ENGINE START FUNCTION MALFUNCTION
Intelligent Key Operation Inspection
Mechanical Key Operation Inspection
WARNING CHIME FUNCTION MALFUNCTION
Before conducting the diagnosis in the following table, check “key reminder function” with power door lock sys-
tem.
Symptom Diagnoses service procedure Refer to page
Ignition knob can not turn
KEY warning lamp on combination meter
lights up in red when ignition knob is
pressed. (door lock functions normal) 1. Intelligent Key battery inspection
BL-147
2. Check inside key antennaBL-138
3. Replace Intelligent Key unitBL-146
KEY warning lamp on combination meter
lights up in green when ignition knob is
pressed. 1. Check ignition knob switch
BL-1272. Check steering lock unitBL-139
3. Check Intelligent Key unit power supply and ground circuitBL-124
4. Replace Intelligent Key unitBL-146
Ignition knob turns even without both Intelli-
gent Key and mechanical key. Replace steering lock unit —
Security indicator will still flash when igni-
tion knob is pressed. 1. Check key switch (Intelligent Key unit input)
BL-125
2. Replace Intelligent Key unitBL-146
Security indicator does not flash with igni-
tion knob released at LOCK position. (push
switch OFF) 1. CAN communication system
BL-124
2. Ignition knob switch systemBL-127
3. Intelligent Key unit power supply and ground circuitBL-124
Starter motor does not cranking.
(Ignition knob can turn) 1. Check detention switch
BL-1422. Check stop lamp switchBL-141
3. Replace Intelligent Key unitBL-146
Symptom Diagnoses service procedure Refer to page
Ignition knob can not turn
Security indicator remains flashing with
mechanical key inserted. 1. Check key switch (BCM input)
BL-126
2. Replace Intelligent Key unitBL-146
KEY indicator and security indicator does
not flashing with mechanical key inserted. 1. Check stop lamp switch
BL-141
2. Replace Intelligent Key unitBL-146
Starter motor does not cranking.
(Ignition knob can turn) 1. Check detention switch
BL-1422. Check stop lamp switchBL-141
3. Replace Intelligent Key unitBL-146
Symptom Diagnoses service procedure Refer to page
Ignition key warning chime is inoperative.
(When mechanical key used) 1. Check CAN communication
BL-124
2. Check key switch (Intelligent Key unit input)BL-125
3. Check door switchBL-129
4. Inspect combination meter (warning) DI-5
5. Replace Intelligent Key unitBL-146
Ignition knob OFF position warning
chime (for inside vehicle) does not
sound.
(Ignition key warning chime operates) 1. Check CAN communication
BL-1242. Check ignition knob switchBL-127
3. Check key switch (Intelligent Key unit input)BL-125
4. Replace Intelligent Key unitBL-146
Page 1106 of 4462
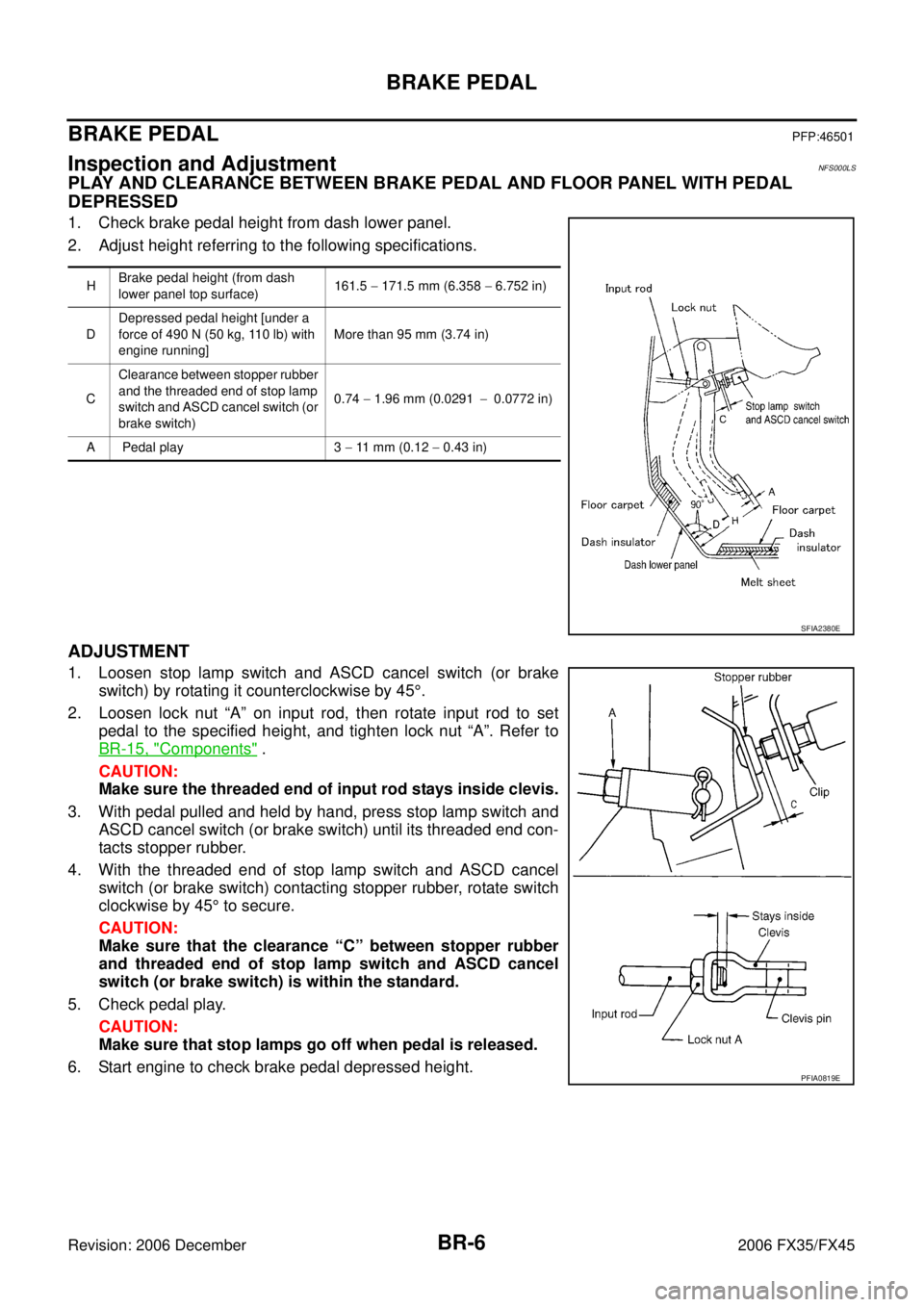
BR-6
BRAKE PEDAL
Revision: 2006 December 2006 FX35/FX45
BRAKE PEDALPFP:46501
Inspection and AdjustmentNFS000LS
PLAY AND CLEARANCE BETWEEN BRAKE PEDAL AND FLOOR PANEL WITH PEDAL
DEPRESSED
1. Check brake pedal height from dash lower panel.
2. Adjust height referring to the following specifications.
ADJUSTMENT
1. Loosen stop lamp switch and ASCD cancel switch (or brake switch) by rotating it counterclockwise by 45 °.
2. Loosen lock nut “A” on input rod, then rotate input rod to set pedal to the specified height, and tighten lock nut “A”. Refer to
BR-15, "
Components" .
CAUTION:
Make sure the threaded end of input rod stays inside clevis.
3. With pedal pulled and held by hand, press stop lamp switch and ASCD cancel switch (or brake switch) until its threaded end con-
tacts stopper rubber.
4. With the threaded end of stop lamp switch and ASCD cancel switch (or brake switch) contacting stopper rubber, rotate switch
clockwise by 45 ° to secure.
CAUTION:
Make sure that the clearance “C” between stopper rubber
and threaded end of stop lamp switch and ASCD cancel
switch (or brake switch) is within the standard.
5. Check pedal play. CAUTION:
Make sure that stop lamps go off when pedal is released.
6. Start engine to check brake pedal depressed height.
H Brake pedal height (from dash
lower panel top surface) 161.5
− 171.5 mm (6.358 − 6.752 in)
D Depressed pedal height [under a
force of 490 N (50 kg, 110 lb) with
engine running] More than 95 mm (3.74 in)
C Clearance between stopper rubber
and the threaded end of stop lamp
switch and ASCD cancel switch (or
brake switch) 0.74
− 1.96 mm (0.0291 −0.0772 in)
A Pedal play 3 − 11 mm (0.12 − 0.43 in)
SFIA2380E
PFIA0819E
Page 1115 of 4462
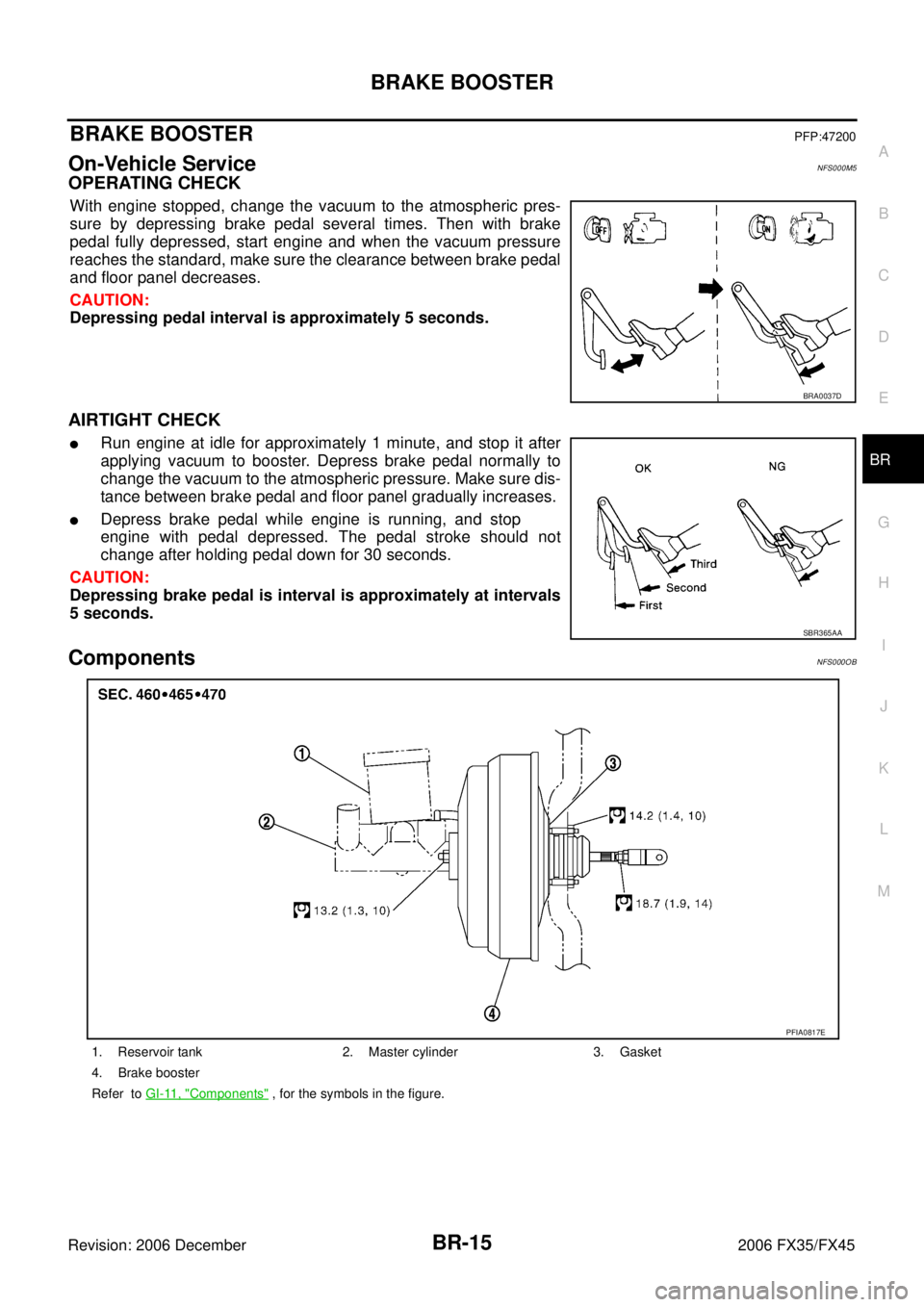
BRAKE BOOSTER BR-15
C
D E
G H
I
J
K L
M A
B
BR
Revision: 2006 December 2006 FX35/FX45
BRAKE BOOSTERPFP:47200
On-Vehicle ServiceNFS000M5
OPERATING CHECK
With engine stopped, change the vacuum to the atmospheric pres-
sure by depressing brake pedal several times. Then with brake
pedal fully depressed, start engine and when the vacuum pressure
reaches the standard, make sure the clearance between brake pedal
and floor panel decreases.
CAUTION:
Depressing pedal interval is approximately 5 seconds.
AIRTIGHT CHECK
Run engine at idle for approximately 1 minute, and stop it after
applying vacuum to booster. Depress brake pedal normally to
change the vacuum to the atmospheric pressure. Make sure dis-
tance between brake pedal and floor panel gradually increases.
Depress brake pedal while engine is running, and stop
engine with pedal depressed. The pedal stroke should not
change after holding pedal down for 30 seconds.
CAUTION:
Depressing brake pedal is interval is approximately at intervals
5 seconds.
ComponentsNFS000OB
BRA0037D
SBR365AA
1. Reservoir tank 2. Master cylinder 3. Gasket
4. Brake booster
Refer to GI-11, "
Components" , for the symbols in the figure.
PFIA0817E
Page 1135 of 4462
![INFINITI FX35 2006 Owners Manual PRECAUTIONS BRC-3
[VDC/TCS/ABS]
C
D E
G H
I
J
K L
M A
B
BRC
Revision: 2006 December 2006 FX35/FX45
[VDC/TCS/ABS]PRECAUTIONSPFP:00001
Precautions for Supplemental Restraint System (SRS) “ INFINITI FX35 2006 Owners Manual PRECAUTIONS BRC-3
[VDC/TCS/ABS]
C
D E
G H
I
J
K L
M A
B
BRC
Revision: 2006 December 2006 FX35/FX45
[VDC/TCS/ABS]PRECAUTIONSPFP:00001
Precautions for Supplemental Restraint System (SRS) “](/img/42/57019/w960_57019-1134.png)
PRECAUTIONS BRC-3
[VDC/TCS/ABS]
C
D E
G H
I
J
K L
M A
B
BRC
Revision: 2006 December 2006 FX35/FX45
[VDC/TCS/ABS]PRECAUTIONSPFP:00001
Precautions for Supplemental Restraint System (SRS) “AIR BAG” and “SEAT
BELT PRE-TENSIONER”
NFS000MW
The Supplemental Restraint System such as “AIR BAG” and “SEAT BELT PRE-TENSIONER”, used along
with a front seat belt, helps to reduce the risk or severity of injury to the driver and front passenger for certain
types of collision. This system includes seat belt switch inputs and dual stage front air bag modules. The SRS
system uses the seat belt switches to determine the front air bag deployment, and may only deploy one front
air bag, depending on the severity of a collision and whether the front occupants are belted or unbelted.
Information necessary to service the system safely is included in the SRS and SB section of this Service Man-
ual.
WARNING:
To avoid rendering the SRS inoperative, which could increase the risk of personal injury or death
in the event of a collision which would result in air bag inflation, all maintenance must be per-
formed by an authorized NISSAN/INFINITI dealer.
Improper maintenance, including incorrect removal and installation of the SRS, can lead to per-
sonal injury caused by unintentional activation of the system. For removal of Spiral Cable and Air
Bag Module, see the SRS section.
Do not use electrical test equipment on any circuit related to the SRS unless instructed to in this
Service Manual. SRS wiring harnesses can be identified by yellow and/or orange harnesses or
harness connectors.
Precautions for Brake SystemNFS000MX
Recommended fluid is brake fluid “DOT 3”. Refer to MA-12, "RECOMMENDED FLUIDS AND LUBRI-
CANTS" .
Do not reuse drained brake fluid.
Be careful not to splash brake fluid on painted areas such as body. If brake fluid is splashed, wipe it off
and flush area with water immediately.
Do not use mineral oils such as gasoline or kerosene to clean. They will ruin rubber parts and cause
improper operation.
Using a flare nut crowfoot and torque wrench, securely tighten
brake tube flare nuts.
Brake system is an important safety part. If a brake fluid leak is
detected, always disassemble the affected part. If a malfunction
is detected, replace part with a new one.
Before working, turn ignition switch OFF and disconnect electri-
cal connectors of ABS actuator and electric unit (control unit) or
battery negative terminal.
When installing brake piping, be sure to check torque.
WARNING:
Clean brake pads and shoes with a waste cloth, then wipe with
a dust collector.
Precautions for Brake ControlNFS000MY
During VDC/TCS/ABS operation, brake pedal lightly vibrates and a mechanical noise may be heard. This
is normal.
Just after starting vehicle after turning ignition switch ON, brake pedal may vibrate or motor operating
noise may be heard from engine room. This is a normal status of operation check.
Stopping distance may be longer than that of vehicles without ABS when vehicle drives on rough, gravel,
or snow-covered (fresh, deep snow) roads.
When an error is indicated by ABS or another warning lamp, collect all necessary information from cus-
tomer (what symptoms are present under what conditions) and check for simple causes before starting
diagnostic servicing. Besides electrical system inspection, check booster operation, brake fluid level, and
fluid leaks.
If tire size and type are used in an improper combination, or brake pads are not Genuine NISSAN parts,
stopping distance or steering stability may deteriorate.
SBR686C