check engine INFINITI FX35 2006 Service Manual
[x] Cancel search | Manufacturer: INFINITI, Model Year: 2006, Model line: FX35, Model: INFINITI FX35 2006Pages: 4462, PDF Size: 57.74 MB
Page 2719 of 4462
![INFINITI FX35 2006 Service Manual IGNITION SIGNAL EC-1335
[VK45DE]
C
D E
F
G H
I
J
K L
M A
EC
Revision: 2006 December 2006 FX35/FX45
3. CHECK OVERALL FUNCTION
Without CONSULT-II
1. Let engine idle.
2. Read the voltage s INFINITI FX35 2006 Service Manual IGNITION SIGNAL EC-1335
[VK45DE]
C
D E
F
G H
I
J
K L
M A
EC
Revision: 2006 December 2006 FX35/FX45
3. CHECK OVERALL FUNCTION
Without CONSULT-II
1. Let engine idle.
2. Read the voltage s](/img/42/57019/w960_57019-2718.png)
IGNITION SIGNAL EC-1335
[VK45DE]
C
D E
F
G H
I
J
K L
M A
EC
Revision: 2006 December 2006 FX35/FX45
3. CHECK OVERALL FUNCTION
Without CONSULT-II
1. Let engine idle.
2. Read the voltage signal between ECM terminals 46, 60, 61, 62, 65, 79, 80, 81 and ground with an oscilloscope.
3. Verify that the oscilloscope screen shows the signal wave as shown below.
NOTE:
The pulse cycle changes depending on rpm at idle.
OK or NG
OK >> INSPECTION END
NG >> GO TO 10.
4. CHECK IGNITION COIL POWER SUPPLY CIRCUIT-I
1. Turn ignition switch OFF, wait at least 10 seconds and then turn ON.
2. Check voltage between ECM terminals 119, 120 and ground with CONSULT-II or tester.
OK or NG
OK >> GO TO 5.
NG >> Go to EC-812, "
POWER SUPPLY AND GROUND CIR-
CUIT" .
PBIB2094E
PBIB0044E
Voltage: Battery voltage
MBIB0034E
Page 2723 of 4462
![INFINITI FX35 2006 Service Manual IGNITION SIGNAL EC-1339
[VK45DE]
C
D E
F
G H
I
J
K L
M A
EC
Revision: 2006 December 2006 FX35/FX45
Component InspectionNBS004GW
IGNITION COIL WITH POWER TRANSISTOR
CAUTION:
Do the followi INFINITI FX35 2006 Service Manual IGNITION SIGNAL EC-1339
[VK45DE]
C
D E
F
G H
I
J
K L
M A
EC
Revision: 2006 December 2006 FX35/FX45
Component InspectionNBS004GW
IGNITION COIL WITH POWER TRANSISTOR
CAUTION:
Do the followi](/img/42/57019/w960_57019-2722.png)
IGNITION SIGNAL EC-1339
[VK45DE]
C
D E
F
G H
I
J
K L
M A
EC
Revision: 2006 December 2006 FX35/FX45
Component InspectionNBS004GW
IGNITION COIL WITH POWER TRANSISTOR
CAUTION:
Do the following procedure in the place where ventilation is good without the combustible.
1. Turn ignition switch OFF.
2. Disconnect ignition coil harness connector.
3. Check resistance between ignition coil terminals as follows.
4. If NG, replace ignition coil with power transistor. If OK, go to next step.
5. Turn ignition switch OFF.
6. Reconnect all harness connectors disconnected.
7. Remove fuel pump fuse in IPDM E/R to release fuel pressure.
NOTE:
Do not use CONSULT-II to release fuel pressure, or fuel pres-
sure applies again during the following procedure.
8. Start engine.
9. After engine stalls, crank it two or three times to release all fuel pressure.
10. Turn ignition switch OFF.
11. Remove all ignition coil harness connectors to avoid the electri- cal discharge from the ignition coils.
12. Remove ignition coil and spark plug of the cylinder to be checked.
13. Crank engine for five seconds or more to remove combustion gas in the cylinder.
14. Connect spark plug and harness connector to ignition coil.
15. Fix ignition coil using a rope etc. with gap of 13 - 17 mm between the edge of the spark plug and grounded metal portion
as shown in the figure.
16. Crank engine for about three seconds, and check whether spark is generated between the spark plug and the grounded metal
portion.
CAUTION:
Do not approach to the spark plug and the ignition coil
within 50cm. Be careful not to get an electrical shock
while checking, because the electrical discharge voltage
becomes 20kV or more.
It might cause to damage the ignition coil if the gap of more than 17 mm is taken.
NOTE:
When the gap is less than 13 mm, the spark might be generated even if the coil is malfunctioning.
17. If NG, replace ignition coil with power transistor.
CONDENSER
1. Turn ignition switch OFF.
2. Disconnect condenser harness connector.
Terminal No. (Polarity) Resistance Ω [at 25 °C (77 °F)]
1 and 2 Except 0 or ∞
1 and 3 Except 0
2 and 3
Spark should be generated.
PBIB0847E
PBIB1482E
PBIB2325E
Page 2727 of 4462
![INFINITI FX35 2006 Service Manual REFRIGERANT PRESSURE SENSOR EC-1343
[VK45DE]
C
D E
F
G H
I
J
K L
M A
EC
Revision: 2006 December 2006 FX35/FX45
Specification data are reference values and are measured between each termina INFINITI FX35 2006 Service Manual REFRIGERANT PRESSURE SENSOR EC-1343
[VK45DE]
C
D E
F
G H
I
J
K L
M A
EC
Revision: 2006 December 2006 FX35/FX45
Specification data are reference values and are measured between each termina](/img/42/57019/w960_57019-2726.png)
REFRIGERANT PRESSURE SENSOR EC-1343
[VK45DE]
C
D E
F
G H
I
J
K L
M A
EC
Revision: 2006 December 2006 FX35/FX45
Specification data are reference values and are measured between each terminal and ground.
CAUTION:
Do not use ECM ground terminals when measuring input/output voltage. Doing so may result in dam-
age to the ECM's transistor. Use a ground other than ECM terminals, such as the ground.
Diagnostic ProcedureNBS004HC
1. CHECK REFRIGERANT PRESSURE SENSOR OVERALL FUNCTION
1. Start engine and warm it up to normal operating temperature.
2. Turn A/C switch and blower fan switch ON.
3. Check voltage between ECM terminal 70 and ground with CON- SULT-II or tester.
OK or NG
OK >> INSPECTION END
NG >> GO TO 2.
2. CHECK GROUND CONNECTIONS
1. Turn A/C switch and blower fan switch OFF.
2. Turn ignition switch OFF.
3. Loosen and retighten three ground screws on the body. Refer to EC-818, "
Ground Inspection" .
OK or NG
OK >> GO TO 3.
NG >> Repair or replace ground connections.
TER-
MINAL NO. WIRE
COLOR ITEM CONDITION DATA (DC Voltage)
49 PU Sensor power supply
(Refrigerant pressure sen-
sor) [Ignition switch: ON]
Approximately 5V
67 B/W Sensor ground [Engine is running]
Warm-up condition
Idle speed Approximately 0V
70 L/R Refrigerant pressure sensor [Engine is running]
Warm-up condition
Both A/C switch and blower fan motor
switch: ON (Compressor operates) 1.0 - 4.0V
Voltage: 1.0 - 4.0V
PBIB1188E
PBIB2195E
Page 2732 of 4462
![INFINITI FX35 2006 Service Manual EC-1348
[VK45DE]
SNOW MODE SWITCH
Revision: 2006 December 2006 FX35/FX45
Diagnostic ProcedureNBS004HY
1. CHECK SNOW MODE SWITICH OVERALL FUNCTION-I
1. Turn ignition switch ON.
2. Select “SNOW MODE INFINITI FX35 2006 Service Manual EC-1348
[VK45DE]
SNOW MODE SWITCH
Revision: 2006 December 2006 FX35/FX45
Diagnostic ProcedureNBS004HY
1. CHECK SNOW MODE SWITICH OVERALL FUNCTION-I
1. Turn ignition switch ON.
2. Select “SNOW MODE](/img/42/57019/w960_57019-2731.png)
EC-1348
[VK45DE]
SNOW MODE SWITCH
Revision: 2006 December 2006 FX35/FX45
Diagnostic ProcedureNBS004HY
1. CHECK SNOW MODE SWITICH OVERALL FUNCTION-I
1. Turn ignition switch ON.
2. Select “SNOW MODE SW” in “DATA MONITOR” mode with CONSULT-II.
3. Check “SNOW MODE SW” indication under the following condi- tions.
OK or NG
OK >> GO TO 2.
NG >> GO TO 3.
2. CHECK SNOW MODE SWITICH OVERALL FUNCTION-II
1. Turn ignition switch ON.
2. Start engine.
3. Check the snow indicator lamp under the following condition.
OK or NG
OK >> INSPECTION END
NG >> GO TO 7.
3. CHECK DTC WITH “UNIFIED METER AND A/C AMP.”
Refer to DI-31, "
SELF-DIAG RESULTS" .
OK or NG
OK >> GO TO 4.
NG >> Go to DI-28, "
UNIFIED METER AND A/C AMP" .
4. CHECK SNOW MODE SWITCH POWER SUPPLY CIRCUIT
1. Turn ignition switch OFF.
2. Disconnect snow mode switch harness connector.
3. Turn ignition switch ON.
4. Check voltage between snow mode switch terminal 1 and ground with CONSULT-II or tester.
OK or NG
OK >> GO TO 6.
NG >> GO TO 5.
CONDITION INDICATION
Snow mode switch: ON ON
Snow mode switch: OFF OFF
PBIB2009E
CONDITION INDICATOR LAMP
Snow mode switch: ON Illuminated
Snow mode switch: OFF Not illuminated
Voltage: Battery voltage.
PBIB2562E
Page 2739 of 4462
![INFINITI FX35 2006 Service Manual VARIABLE INDUCTION AIR CONTROL SYSTEM (VIAS) EC-1355
[VK45DE]
C
D E
F
G H
I
J
K L
M A
EC
Revision: 2006 December 2006 FX35/FX45
Diagnostic ProcedureNBS004GQ
1. CHECK OVERALL FUNCTION
W INFINITI FX35 2006 Service Manual VARIABLE INDUCTION AIR CONTROL SYSTEM (VIAS) EC-1355
[VK45DE]
C
D E
F
G H
I
J
K L
M A
EC
Revision: 2006 December 2006 FX35/FX45
Diagnostic ProcedureNBS004GQ
1. CHECK OVERALL FUNCTION
W](/img/42/57019/w960_57019-2738.png)
VARIABLE INDUCTION AIR CONTROL SYSTEM (VIAS) EC-1355
[VK45DE]
C
D E
F
G H
I
J
K L
M A
EC
Revision: 2006 December 2006 FX35/FX45
Diagnostic ProcedureNBS004GQ
1. CHECK OVERALL FUNCTION
With CONSULT-II
1. Start engine and warm it up to normal operating temperature.
2. Perform “VIAS SOL VALVE” in “ACTIVE TEST” mode with CON- SULT-II.
3. Turn VIAS control solenoid valve ON and OFF, and make sure that power valve actuator (1) rod moves.
Without CONSULT-II
1. Lift up the vehicle.
2. Start engine and warm it up to normal operating temperature.
3. Make sure that power valve actuator (1) rod moves when chang- ing the gear position to N and D alternately.
OK or NG
OK >> INSPECTION END
NG (With CONSULT-II)>>GO TO 2.
NG (Without CONSULT-II)>>GO TO 3.
PBIB0844E
PBIB3249E
PBIB3249E
Page 2740 of 4462
![INFINITI FX35 2006 Service Manual EC-1356
[VK45DE]
VARIABLE INDUCTION AIR CONTROL SYSTEM (VIAS)
Revision: 2006 December 2006 FX35/FX45
2. CHECK VACUUM EXISTENCE
With CONSULT-II
1. Stop engine and disconnect vacuum hose connected INFINITI FX35 2006 Service Manual EC-1356
[VK45DE]
VARIABLE INDUCTION AIR CONTROL SYSTEM (VIAS)
Revision: 2006 December 2006 FX35/FX45
2. CHECK VACUUM EXISTENCE
With CONSULT-II
1. Stop engine and disconnect vacuum hose connected](/img/42/57019/w960_57019-2739.png)
EC-1356
[VK45DE]
VARIABLE INDUCTION AIR CONTROL SYSTEM (VIAS)
Revision: 2006 December 2006 FX35/FX45
2. CHECK VACUUM EXISTENCE
With CONSULT-II
1. Stop engine and disconnect vacuum hose connected to power valve actuator.
2. Start engine and let it idle.
3. Perform “VIAS SOL VALVE” in “ACTIVE TEST” mode with CON- SULT-II.
4. Turn VIAS control solenoid valve “ON” and “OFF”, and check vacuum existence under the following conditions.
OK or NG
OK >> Repair or replace power valve actuator.
NG >> GO TO 4.
3. CHECK VACUUM EXISTENCE
Without CONSULT-II
1. Stop engine and disconnect vacuum hose connected to power valve actuator.
2. Disconnect VIAS control solenoid valve (1) harness connector.
–Vacuum tank (2)
3. Start engine and let it idle.
4. Apply 12V of direct current between VIAS control solenoid valve terminals 1 and 2.
5. Check vacuum existence under the following conditions.
OK or NG
OK >> Repair or replace power valve actuator.
NG >> GO TO 4.
VIAS SOL VALVE Vacuum
ON Should exist.
OFF Should not exist.
PBIB0844E
PBIB3236E
Condition Vacuum
12V direct current supply Should exist
No supply Should not exist
PBIB0845E
Page 2741 of 4462
![INFINITI FX35 2006 Service Manual VARIABLE INDUCTION AIR CONTROL SYSTEM (VIAS) EC-1357
[VK45DE]
C
D E
F
G H
I
J
K L
M A
EC
Revision: 2006 December 2006 FX35/FX45
4. CHECK VACUUM HOSE
1. Stop engine.
2. Check hoses and tu INFINITI FX35 2006 Service Manual VARIABLE INDUCTION AIR CONTROL SYSTEM (VIAS) EC-1357
[VK45DE]
C
D E
F
G H
I
J
K L
M A
EC
Revision: 2006 December 2006 FX35/FX45
4. CHECK VACUUM HOSE
1. Stop engine.
2. Check hoses and tu](/img/42/57019/w960_57019-2740.png)
VARIABLE INDUCTION AIR CONTROL SYSTEM (VIAS) EC-1357
[VK45DE]
C
D E
F
G H
I
J
K L
M A
EC
Revision: 2006 December 2006 FX35/FX45
4. CHECK VACUUM HOSE
1. Stop engine.
2. Check hoses and tubes between intake manifold and power valve actuator for crack, clogging, improper connection or dis-
connection. Refer to EC-768, "
Vacuum Hose Drawing" .
OK or NG
OK >> GO TO 5.
NG >> Repair hoses or tubes.
5. CHECK VACUUM TANK
Refer to EC-1358, "
Component Inspection" .
OK or NG
OK >> GO TO 6.
NG >> Replace vacuum tank.
6. CHECK VIAS CONTROL SOLENOID VALVE POWER SUPPLY CIRCUIT
1. Turn ignition switch OFF.
2. Disconnect VIAS control solenoid valve (1) harness connector.
–Vacuum tank (2)
3. Turn ignition switch ON.
4. Check voltage between VIAS control solenoid valve terminal 1 and ground with CONSULT-II or tester.
OK or NG
OK >> GO TO 8.
NG >> GO TO 7.
SEF109L
PBIB3236E
Voltage: Battery voltage
PBIB0173E
Page 2754 of 4462
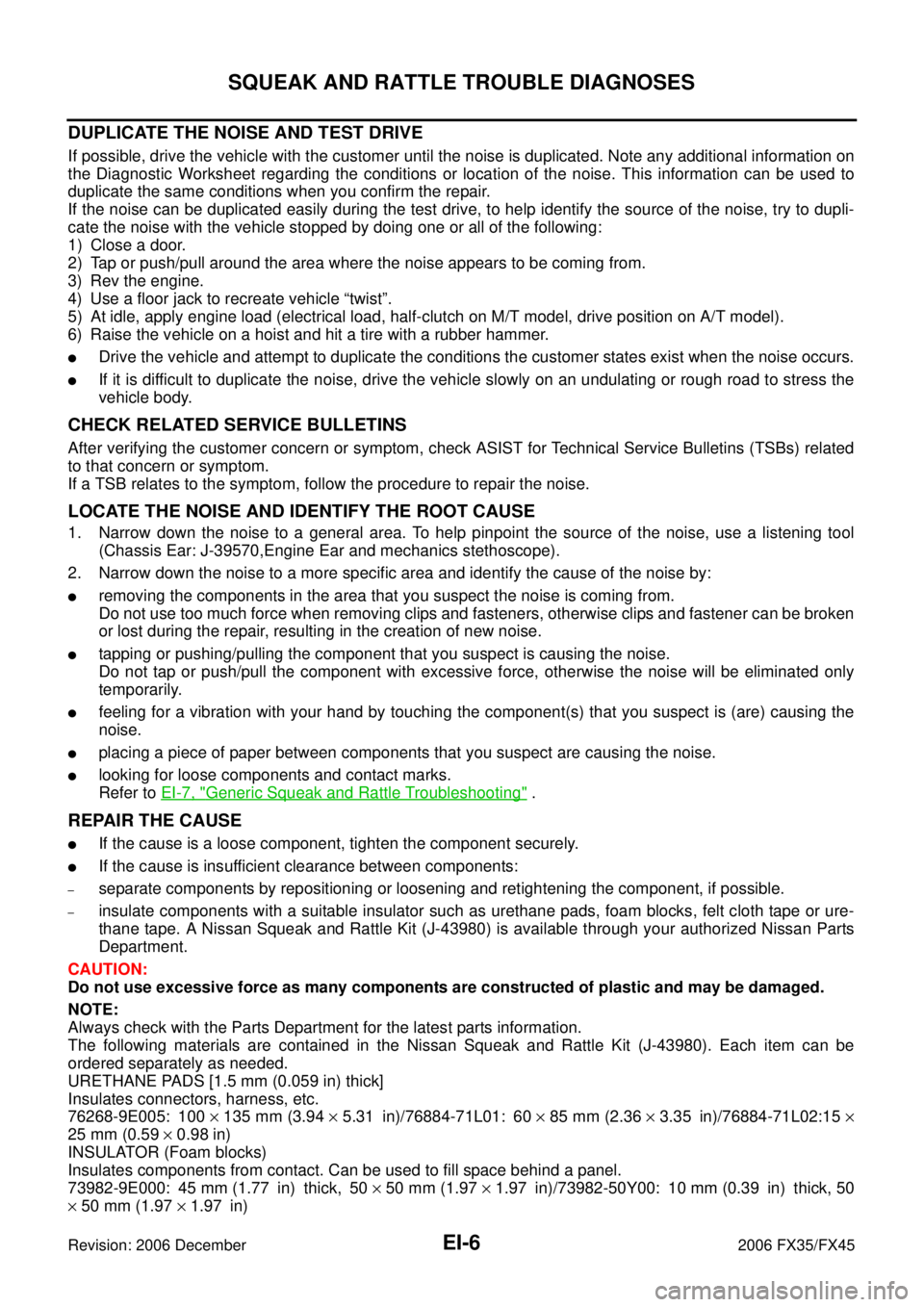
EI-6
SQUEAK AND RATTLE TROUBLE DIAGNOSES
Revision: 2006 December 2006 FX35/FX45
DUPLICATE THE NOISE AND TEST DRIVE
If possible, drive the vehicle with the customer until the noise is duplicated. Note any additional information on
the Diagnostic Worksheet regarding the conditions or location of the noise. This information can be used to
duplicate the same conditions when you confirm the repair.
If the noise can be duplicated easily during the test drive, to help identify the source of the noise, try to dupli-
cate the noise with the vehicle stopped by doing one or all of the following:
1) Close a door.
2) Tap or push/pull around the area where the noise appears to be coming from.
3) Rev the engine.
4) Use a floor jack to recreate vehicle “twist”.
5) At idle, apply engine load (electrical load, half-clutch on M/T model, drive position on A/T model).
6) Raise the vehicle on a hoist and hit a tire with a rubber hammer.
Drive the vehicle and attempt to duplicate the conditions the customer states exist when the noise occurs.
If it is difficult to duplicate the noise, drive the vehicle slowly on an undulating or rough road to stress the
vehicle body.
CHECK RELATED SERVICE BULLETINS
After verifying the customer concern or symptom, check ASIST for Technical Service Bulletins (TSBs) related
to that concern or symptom.
If a TSB relates to the symptom, follow the procedure to repair the noise.
LOCATE THE NOISE AND IDENTIFY THE ROOT CAUSE
1. Narrow down the noise to a general area. To help pinpoint the source of the noise, use a listening tool (Chassis Ear: J-39570,Engine Ear and mechanics stethoscope).
2. Narrow down the noise to a more specific area and identify the cause of the noise by:
removing the components in the area that you suspect the noise is coming from.
Do not use too much force when removing clips and fasteners, otherwise clips and fastener can be broken
or lost during the repair, resulting in the creation of new noise.
tapping or pushing/pulling the component that you suspect is causing the noise.
Do not tap or push/pull the component with excessive force, otherwise the noise will be eliminated only
temporarily.
feeling for a vibration with your hand by touching the component(s) that you suspect is (are) causing the
noise.
placing a piece of paper between components that you suspect are causing the noise.
looking for loose components and contact marks.
Refer to EI-7, "
Generic Squeak and Rattle Troubleshooting" .
REPAIR THE CAUSE
If the cause is a loose component, tighten the component securely.
If the cause is insufficient clearance between components:
–separate components by repositioning or loosening and retightening the component, if possible.
–insulate components with a suitable insulator such as urethane pads, foam blocks, felt cloth tape or ure-
thane tape. A Nissan Squeak and Rattle Kit (J-43980) is available through your authorized Nissan Parts
Department.
CAUTION:
Do not use excessive force as many components are constructed of plastic and may be damaged.
NOTE:
Always check with the Parts Department for the latest parts information.
The following materials are contained in the Nissan Squeak and Rattle Kit (J-43980). Each item can be
ordered separately as needed.
URETHANE PADS [1.5 mm (0.059 in) thick]
Insulates connectors, harness, etc.
76268-9E005: 100 × 135 mm (3.94 × 5.31 in)/76884-71L01: 60 × 85 mm (2.36 × 3.35 in)/76884-71L02:15 ×
25 mm (0.59 × 0.98 in)
INSULATOR (Foam blocks)
Insulates components from contact. Can be used to fill space behind a panel.
73982-9E000: 45 mm (1.77 in) thick, 50 × 50 mm (1.97 × 1.97 in)/73982-50Y00: 10 mm (0.39 in) thick, 50
× 50 mm (1.97 × 1.97 in)
Page 2795 of 4462
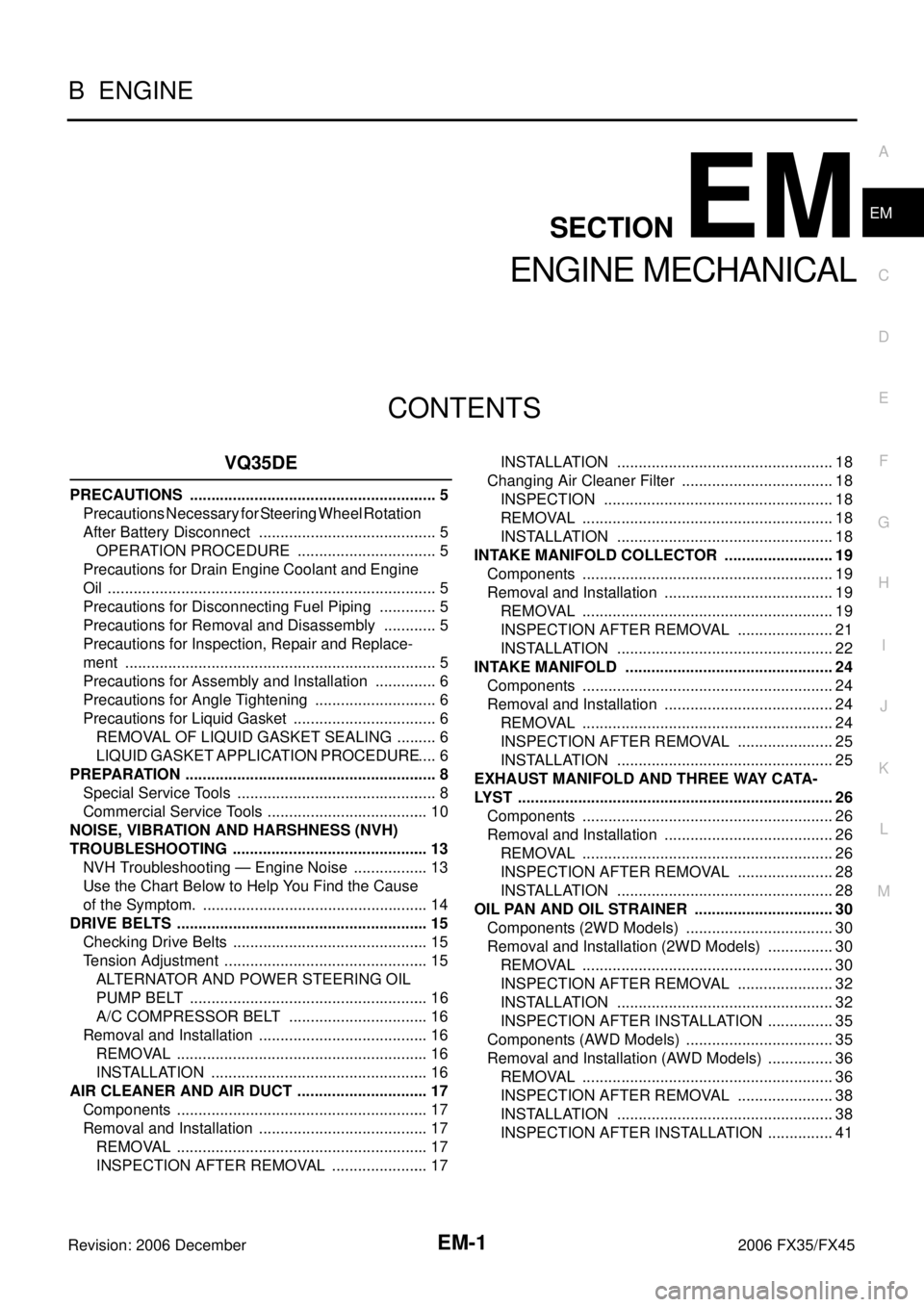
EM-1
ENGINE MECHANICAL
B ENGINE
CONTENTS
C
D E
F
G H
I
J
K L
M
SECTION EM
A
EM
Revision: 2006 December 2006 FX35/FX45
ENGINE MECHANICAL
VQ35DE
PRECAUTIONS ..................................................... ..... 5
Precautions Necessary for Steering Wheel Rotation
After Battery Disconnect ..................................... ..... 5
OPERATION PROCEDURE ............................ ..... 5
Precautions for Drain Engine Coolant and Engine
Oil ........................................................................ ..... 5
Precautions for Disconnecting Fuel Piping ......... ..... 5
Precautions for Removal and Disassembly ........ ..... 5
Precautions for Inspection, Repair and Replace-
ment .................................................................... ..... 5
Precautions for Assembly and Installation .......... ..... 6
Precautions for Angle Tightening ........................ ..... 6
Precautions for Liquid Gasket ............................. ..... 6
REMOVAL OF LIQUID GASKET SEALING ..... ..... 6
LIQUID GASKET APPLICATION PROCEDURE ..... 6
PREPARATION ...................................................... ..... 8
Special Service Tools .......................................... ..... 8
Commercial Service Tools ................................... ... 10
NOISE, VIBRATION AND HARSHNESS (NVH)
TROUBLESHOOTING ........................................... ... 13
NVH Troubleshooting — Engine Noise ............... ... 13
Use the Chart Below to Help You Find the Cause
of the Symptom. .................................................. ... 14
DRIVE BELTS ........................................................ ... 15
Checking Drive Belts ........................................... ... 15
Tension Adjustment ............................................. ... 15
ALTERNATOR AND POWER STEERING OIL
PUMP BELT ..................................................... ... 16
A/C COMPRESSOR BELT .............................. ... 16
Removal and Installation ..................................... ... 16
REMOVAL ........................................................ ... 16
INSTALLATION ................................................ ... 16
AIR CLEANER AND AIR DUCT ............................ ... 17
Components ........................................................ ... 17
Removal and Installation ..................................... ... 17
REMOVAL ........................................................ ... 17
INSPECTION AFTER REMOVAL .................... ... 17 INSTALLATION ................................................
... 18
Changing Air Cleaner Filter ................................. ... 18
INSPECTION ................................................... ... 18
REMOVAL ........................................................ ... 18
INSTALLATION ................................................ ... 18
INTAKE MANIFOLD COLLECTOR ....................... ... 19
Components ........................................................ ... 19
Removal and Installation ..................................... ... 19
REMOVAL ........................................................ ... 19
INSPECTION AFTER REMOVAL .................... ... 21
INSTALLATION ................................................ ... 22
INTAKE MANIFOLD .............................................. ... 24
Components ........................................................ ... 24
Removal and Installation ..................................... ... 24
REMOVAL ........................................................ ... 24
INSPECTION AFTER REMOVAL .................... ... 25
INSTALLATION ................................................ ... 25
EXHAUST MANIFOLD AND THREE WAY CATA-
LYST ....................................................................... ... 26
Components ........................................................ ... 26
Removal and Installation ..................................... ... 26
REMOVAL ........................................................ ... 26
INSPECTION AFTER REMOVAL .................... ... 28
INSTALLATION ................................................ ... 28
OIL PAN AND OIL STRAINER .............................. ... 30
Components (2WD Models) ................................ ... 30
Removal and Installation (2WD Models) ............. ... 30
REMOVAL ........................................................ ... 30
INSPECTION AFTER REMOVAL .................... ... 32
INSTALLATION ................................................ ... 32
INSPECTION AFTER INSTALLATION ............. ... 35
Components (AWD Models) ................................ ... 35
Removal and Installation (AWD Models) ............. ... 36
REMOVAL ........................................................ ... 36
INSPECTION AFTER REMOVAL .................... ... 38
INSTALLATION ................................................ ... 38
INSPECTION AFTER INSTALLATION ............. ... 41
Page 2796 of 4462
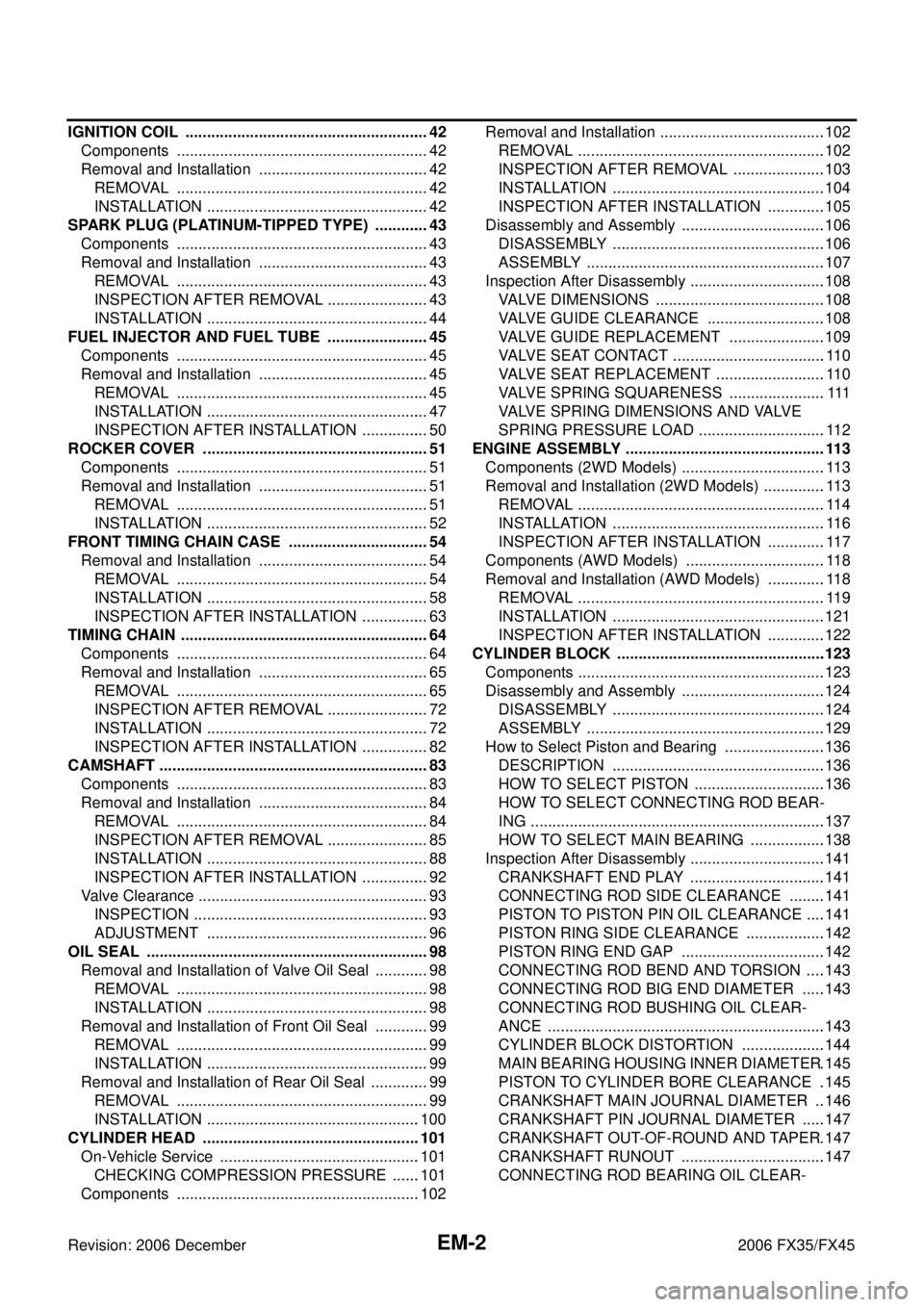
EM-2Revision: 2006 December 2006 FX35/FX45
IGNITION COIL ......................................................
... 42
Components ........................................................ ... 42
Removal and Installation ..................................... ... 42
REMOVAL ........................................................ ... 42
INSTALLATION ................................................. ... 42
SPARK PLUG (PLATINUM-TIPPED TYPE) .......... ... 43
Components ........................................................ ... 43
Removal and Installation ..................................... ... 43
REMOVAL ........................................................ ... 43
INSPECTION AFTER REMOVAL ..................... ... 43
INSTALLATION ................................................. ... 44
FUEL INJECTOR AND FUEL TUBE ..................... ... 45
Components ........................................................ ... 45
Removal and Installation ..................................... ... 45
REMOVAL ........................................................ ... 45
INSTALLATION ................................................. ... 47
INSPECTION AFTER INSTALLATION ............. ... 50
ROCKER COVER .................................................. ... 51
Components ........................................................ ... 51
Removal and Installation ..................................... ... 51
REMOVAL ........................................................ ... 51
INSTALLATION ................................................. ... 52
FRONT TIMING CHAIN CASE .............................. ... 54
Removal and Installation ..................................... ... 54
REMOVAL ........................................................ ... 54
INSTALLATION ................................................. ... 58
INSPECTION AFTER INSTALLATION ............. ... 63
TIMING CHAIN ....................................................... ... 64
Components ........................................................ ... 64
Removal and Installation ..................................... ... 65
REMOVAL ........................................................ ... 65
INSPECTION AFTER REMOVAL ..................... ... 72
INSTALLATION ................................................. ... 72
INSPECTION AFTER INSTALLATION ............. ... 82
CAMSHAFT ............................................................ ... 83
Components ........................................................ ... 83
Removal and Installation ..................................... ... 84
REMOVAL ........................................................ ... 84
INSPECTION AFTER REMOVAL ..................... ... 85
INSTALLATION ................................................. ... 88
INSPECTION AFTER INSTALLATION ............. ... 92
Valve Clearance ................................................... ... 93
INSPECTION .................................................... ... 93
ADJUSTMENT ................................................. ... 96
OIL SEAL ............................................................... ... 98
Removal and Installation of Valve Oil Seal .......... ... 98
REMOVAL ........................................................ ... 98
INSTALLATION ................................................. ... 98
Removal and Installation of Front Oil Seal .......... ... 99
REMOVAL ........................................................ ... 99
INSTALLATION ................................................. ... 99
Removal and Installation of Rear Oil Seal ........... ... 99
REMOVAL ........................................................ ... 99
INSTALLATION ................................................. .100
CYLINDER HEAD .................................................. .101
On-Vehicle Service .............................................. .101
CHECKING COMPRESSION PRESSURE ...... .101
Components ........................................................ .102 Removal and Installation ......................................
.102
REMOVAL ......................................................... .102
INSPECTION AFTER REMOVAL ..................... .103
INSTALLATION ................................................. .104
INSPECTION AFTER INSTALLATION ............. .105
Disassembly and Assembly ................................. .106
DISASSEMBLY ................................................. .106
ASSEMBLY ....................................................... .107
Inspection After Disassembly ............................... .108
VALVE DIMENSIONS ....................................... .108
VALVE GUIDE CLEARANCE ........................... .108
VALVE GUIDE REPLACEMENT ...................... .109
VALVE SEAT CONTACT ................................... .110
VALVE SEAT REPLACEMENT ......................... .110
VALVE SPRING SQUARENESS ...................... . 111
VALVE SPRING DIMENSIONS AND VALVE
SPRING PRESSURE LOAD ............................. .112
ENGINE ASSEMBLY .............................................. .113
Components (2WD Models) ................................. .113
Removal and Installation (2WD Models) .............. .113
REMOVAL ......................................................... .114
INSTALLATION ................................................. .116
INSPECTION AFTER INSTALLATION ............. .117
Components (AWD Models) ................................ .118
Removal and Installation (AWD Models) ............. .118
REMOVAL ......................................................... .119
INSTALLATION ................................................. .121
INSPECTION AFTER INSTALLATION ............. .122
CYLINDER BLOCK ................................................ .123
Components ......................................................... .123
Disassembly and Assembly ................................. .124
DISASSEMBLY ................................................. .124
ASSEMBLY ....................................................... .129
How to Select Piston and Bearing ....................... .136
DESCRIPTION ................................................. .136
HOW TO SELECT PISTON .............................. .136
HOW TO SELECT CONNECTING ROD BEAR-
ING .................................................................... .137
HOW TO SELECT MAIN BEARING ................. .138
Inspection After Disassembly ............................... .141
CRANKSHAFT END PLAY ............................... .141
CONNECTING ROD SIDE CLEARANCE ........ .141
PISTON TO PISTON PIN OIL CLEARANCE .... .141
PISTON RING SIDE CLEARANCE .................. .142
PISTON RING END GAP ................................. .142
CONNECTING ROD BEND AND TORSION .... .143
CONNECTING ROD BIG END DIAMETER ..... .143
CONNECTING ROD BUSHING OIL CLEAR-
ANCE ................................................................ .143
CYLINDER BLOCK DISTORTION ................... .144
MAIN BEARING HOUSING INNER DIAMETER .145
PISTON TO CYLINDER BORE CLEARANCE . .145
CRANKSHAFT MAIN JOURNAL DIAMETER .. .146
CRANKSHAFT PIN JOURNAL DIAMETER ..... .147
CRANKSHAFT OUT-OF-ROUND AND TAPER .147
CRANKSHAFT RUNOUT ................................. .147
CONNECTING ROD BEARING OIL CLEAR-