control unit INFINITI M35 2007 Factory Owner's Manual
[x] Cancel search | Manufacturer: INFINITI, Model Year: 2007, Model line: M35, Model: INFINITI M35 2007Pages: 4647, PDF Size: 93.69 MB
Page 111 of 4647
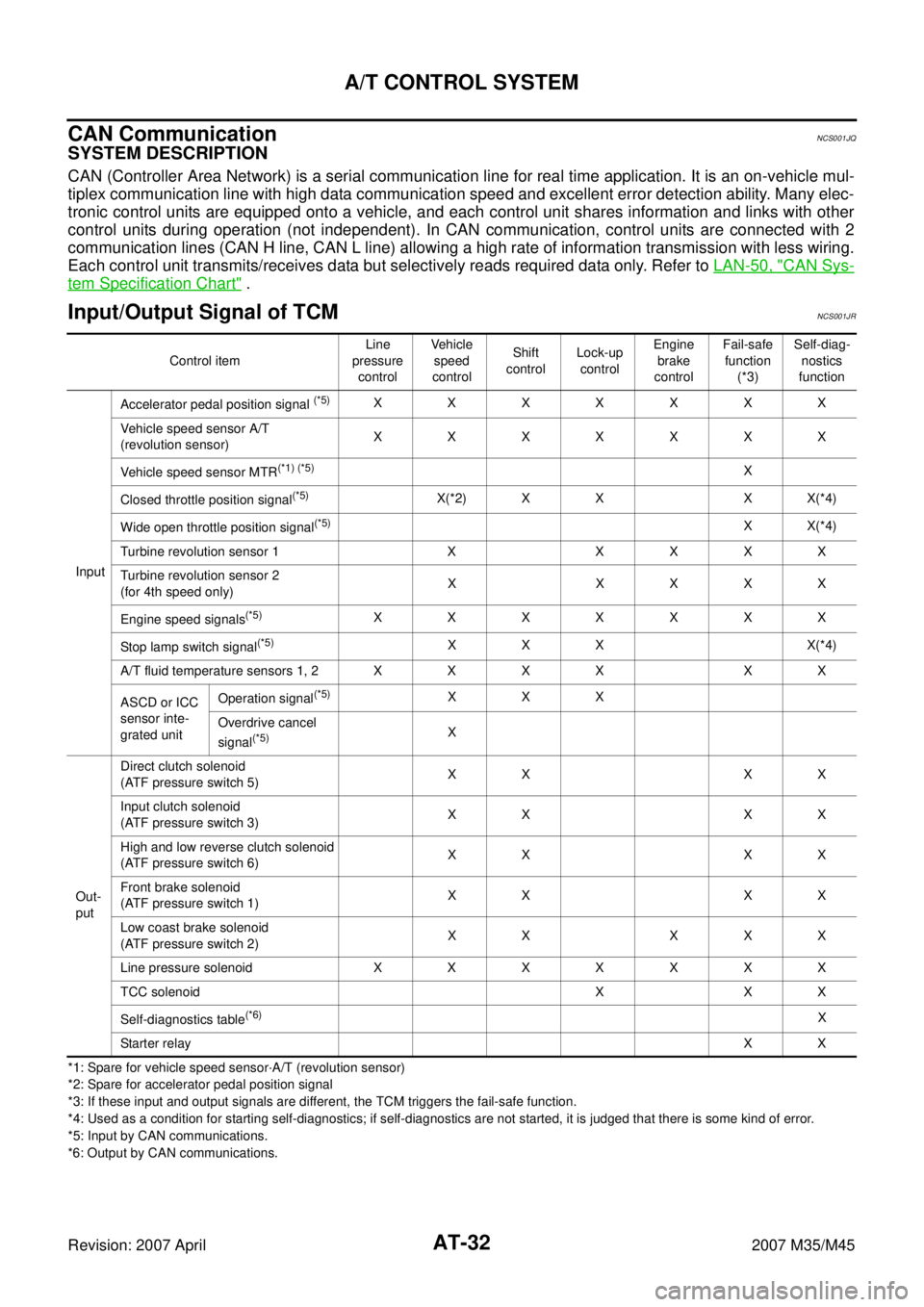
AT-32
A/T CONTROL SYSTEM
Revision: 2007 April2007 M35/M45
CAN CommunicationNCS001JQ
SYSTEM DESCRIPTION
CAN (Controller Area Network) is a serial communication line for real time application. It is an on-vehicle mul-
tiplex communication line with high data communication speed and excellent error detection ability. Many elec-
tronic control units are equipped onto a vehicle, and each control unit shares information and links with other
control units during operation (not independent). In CAN communication, control units are connected with 2
communication lines (CAN H line, CAN L line) allowing a high rate of information transmission with less wiring.
Each control unit transmits/receives data but selectively reads required data only. Refer to LAN-50, "
CAN Sys-
tem Specification Chart" .
Input/Output Signal of TCMNCS001JR
*1: Spare for vehicle speed sensor·A/T (revolution sensor)
*2: Spare for accelerator pedal position signal
*3: If these input and output signals are different, the TCM triggers the fail-safe function.
*4: Used as a condition for starting self-diagnostics; if self-diagnostics are not started, it is judged that there is some kind of error.
*5: Input by CAN communications.
*6: Output by CAN communications.Control itemLine
pressure
controlVehicle
speed
controlShift
controlLock-up
controlEngine
brake
controlFail-safe
function
(*3)Self-diag-
nostics
function
InputAccelerator pedal position signal
(*5)XXXXXXX
Vehicle speed sensor A/T
(revolution sensor)XXXXXXX
Vehicle speed sensor MTR
(*1) (*5)X
Closed throttle position signal
(*5)X(*2) X X X X(*4)
Wide open throttle position signal
(*5)XX(*4)
Turbine revolution sensor 1 X X X X X
Turbine revolution sensor 2
(for 4th speed only)X XXXX
Engine speed signals
(*5)XXXXXXX
Stop lamp switch signal
(*5)XXX X(*4)
A/T fluid temperature sensors 1, 2XXXX XX
ASCD or ICC
sensor inte-
grated unitOperation signal
(*5)XXX
Overdrive cancel
signal
(*5)X
Out-
putDirect clutch solenoid
(ATF pressure switch 5)XX XX
Input clutch solenoid
(ATF pressure switch 3)XX XX
High and low reverse clutch solenoid
(ATF pressure switch 6)XX XX
Front brake solenoid
(ATF pressure switch 1)XX XX
Low coast brake solenoid
(ATF pressure switch 2)XX XXX
Line pressure solenoidXXXXXXX
TCC solenoid X X X
Self-diagnostics table
(*6)X
Starter relayXX
Page 115 of 4647
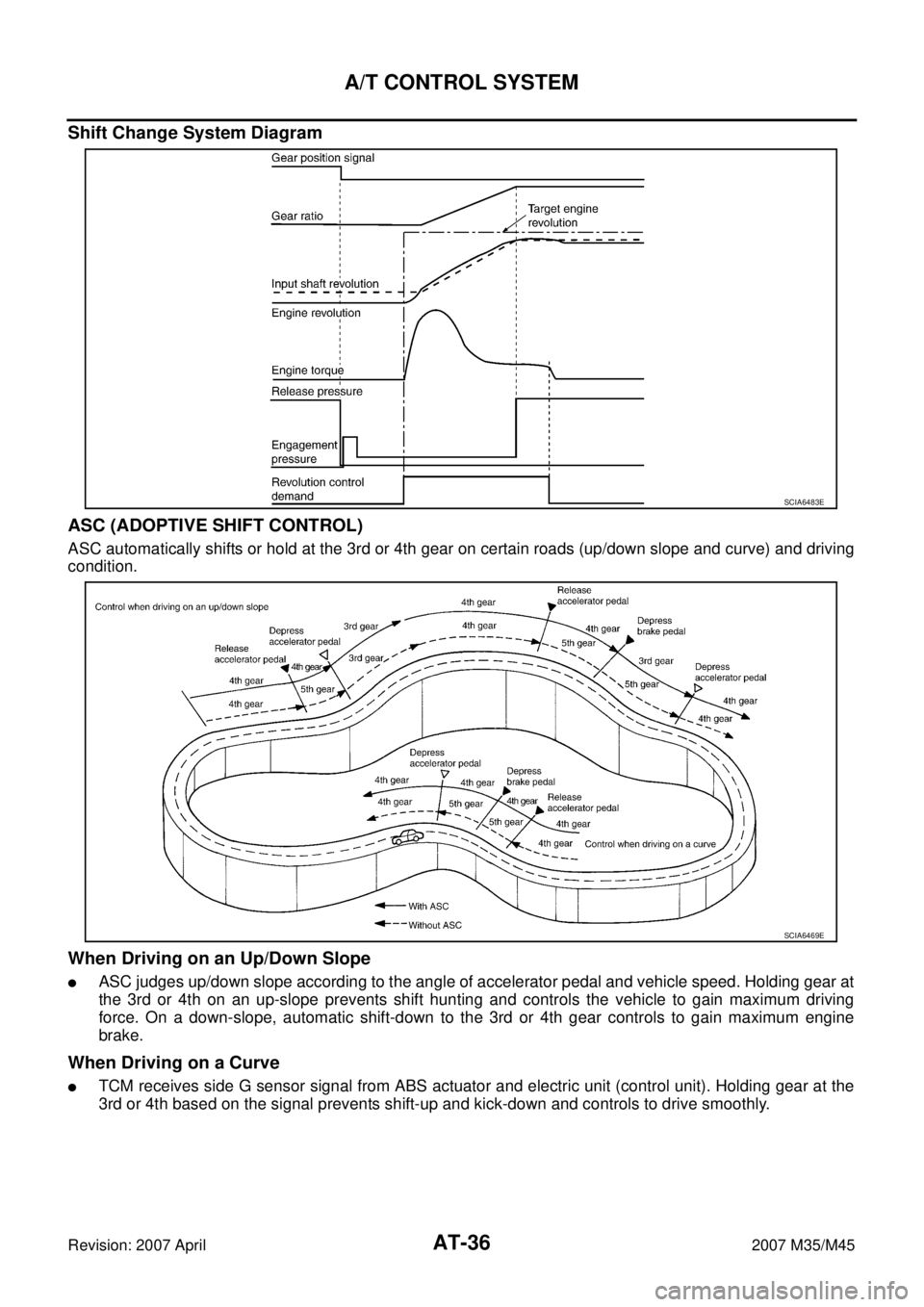
AT-36
A/T CONTROL SYSTEM
Revision: 2007 April2007 M35/M45
Shift Change System Diagram
ASC (ADOPTIVE SHIFT CONTROL)
ASC automatically shifts or hold at the 3rd or 4th gear on certain roads (up/down slope and curve) and driving
condition.
When Driving on an Up/Down Slope
ASC judges up/down slope according to the angle of accelerator pedal and vehicle speed. Holding gear at
the 3rd or 4th on an up-slope prevents shift hunting and controls the vehicle to gain maximum driving
force. On a down-slope, automatic shift-down to the 3rd or 4th gear controls to gain maximum engine
brake.
When Driving on a Curve
TCM receives side G sensor signal from ABS actuator and electric unit (control unit). Holding gear at the
3rd or 4th based on the signal prevents shift-up and kick-down and controls to drive smoothly.
SCIA6483E
SCIA6469E
Page 175 of 4647
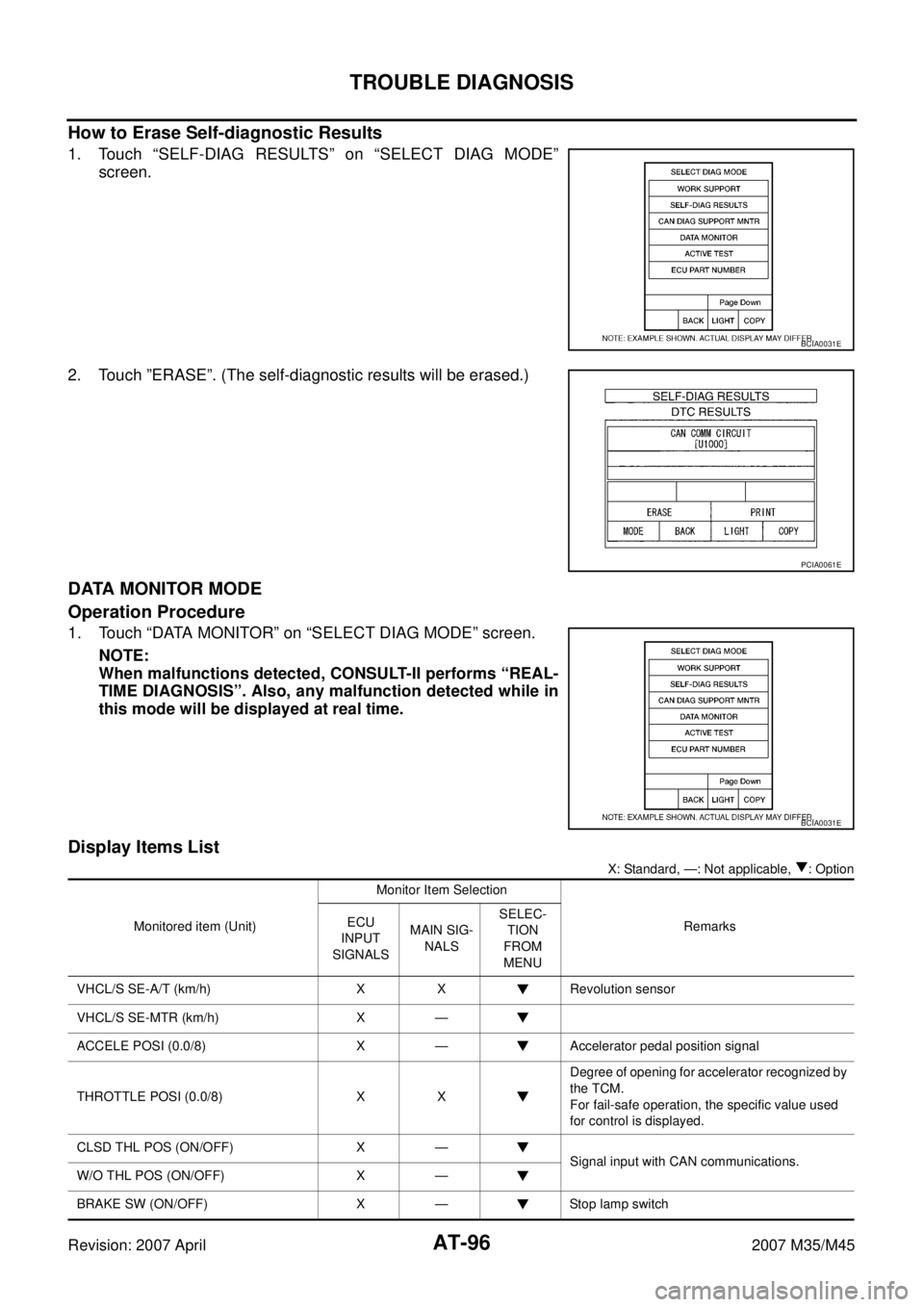
AT-96
TROUBLE DIAGNOSIS
Revision: 2007 April2007 M35/M45
How to Erase Self-diagnostic Results
1. Touch “SELF-DIAG RESULTS” on “SELECT DIAG MODE”
screen.
2. Touch ”ERASE”. (The self-diagnostic results will be erased.)
DATA MONITOR MODE
Operation Procedure
1. Touch “DATA MONITOR” on “SELECT DIAG MODE” screen.
NOTE:
When malfunctions detected, CONSULT-II performs “REAL-
TIME DIAGNOSIS”. Also, any malfunction detected while in
this mode will be displayed at real time.
Display Items List
X: Standard, —: Not applicable, : Option
BCIA0031E
PCIA0061E
BCIA0031E
Monitored item (Unit)Monitor Item Selection
Remarks ECU
INPUT
SIGNALSMAIN SIG-
NALSSELEC-
TION
FROM
MENU
VHCL/S SE-A/T (km/h) X X Revolution sensor
VHCL/S SE-MTR (km/h) X —
ACCELE POSI (0.0/8) X — Accelerator pedal position signal
THROTTLE POSI (0.0/8) X XDegree of opening for accelerator recognized by
the TCM.
For fail-safe operation, the specific value used
for control is displayed.
CLSD THL POS (ON/OFF) X —
Signal input with CAN communications.
W/O THL POS (ON/OFF) X —
BRAKE SW (ON/OFF) X — Stop lamp switch
Page 176 of 4647
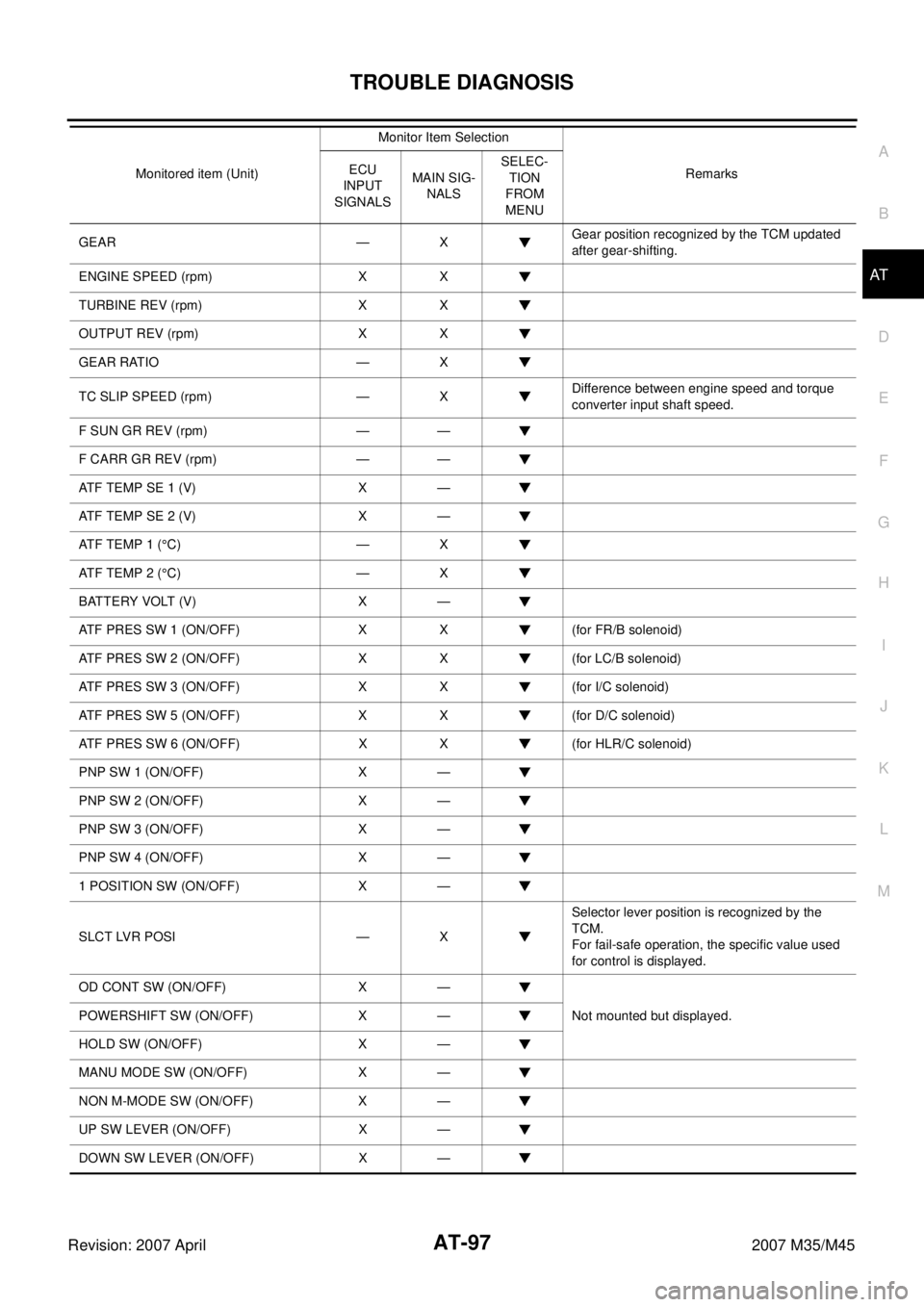
TROUBLE DIAGNOSIS
AT-97
D
E
F
G
H
I
J
K
L
MA
B
AT
Revision: 2007 April2007 M35/M45
GEAR — XGear position recognized by the TCM updated
after gear-shifting.
ENGINE SPEED (rpm) X X
TURBINE REV (rpm) X X
OUTPUT REV (rpm) X X
GEAR RATIO — X
TC SLIP SPEED (rpm) — XDifference between engine speed and torque
converter input shaft speed.
F SUN GR REV (rpm) — —
F CARR GR REV (rpm) — —
ATF TEMP SE 1 (V) X —
ATF TEMP SE 2 (V) X —
AT F T E M P 1 (°C) — X
AT F T E M P 2 (°C) — X
BATTERY VOLT (V) X —
ATF PRES SW 1 (ON/OFF) X X (for FR/B solenoid)
ATF PRES SW 2 (ON/OFF) X X (for LC/B solenoid)
ATF PRES SW 3 (ON/OFF) X X (for I/C solenoid)
ATF PRES SW 5 (ON/OFF) X X (for D/C solenoid)
ATF PRES SW 6 (ON/OFF) X X (for HLR/C solenoid)
PNP SW 1 (ON/OFF) X —
PNP SW 2 (ON/OFF) X —
PNP SW 3 (ON/OFF) X —
PNP SW 4 (ON/OFF) X —
1 POSITION SW (ON/OFF) X —
SLCT LVR POSI — XSelector lever position is recognized by the
TCM.
For fail-safe operation, the specific value used
for control is displayed.
OD CONT SW (ON/OFF) X —
Not mounted but displayed. POWERSHIFT SW (ON/OFF) X —
HOLD SW (ON/OFF) X —
MANU MODE SW (ON/OFF) X —
NON M-MODE SW (ON/OFF) X —
UP SW LEVER (ON/OFF) X —
DOWN SW LEVER (ON/OFF) X —Monitored item (Unit)Monitor Item Selection
Remarks ECU
INPUT
SIGNALSMAIN SIG-
NALSSELEC-
TION
FROM
MENU
Page 177 of 4647
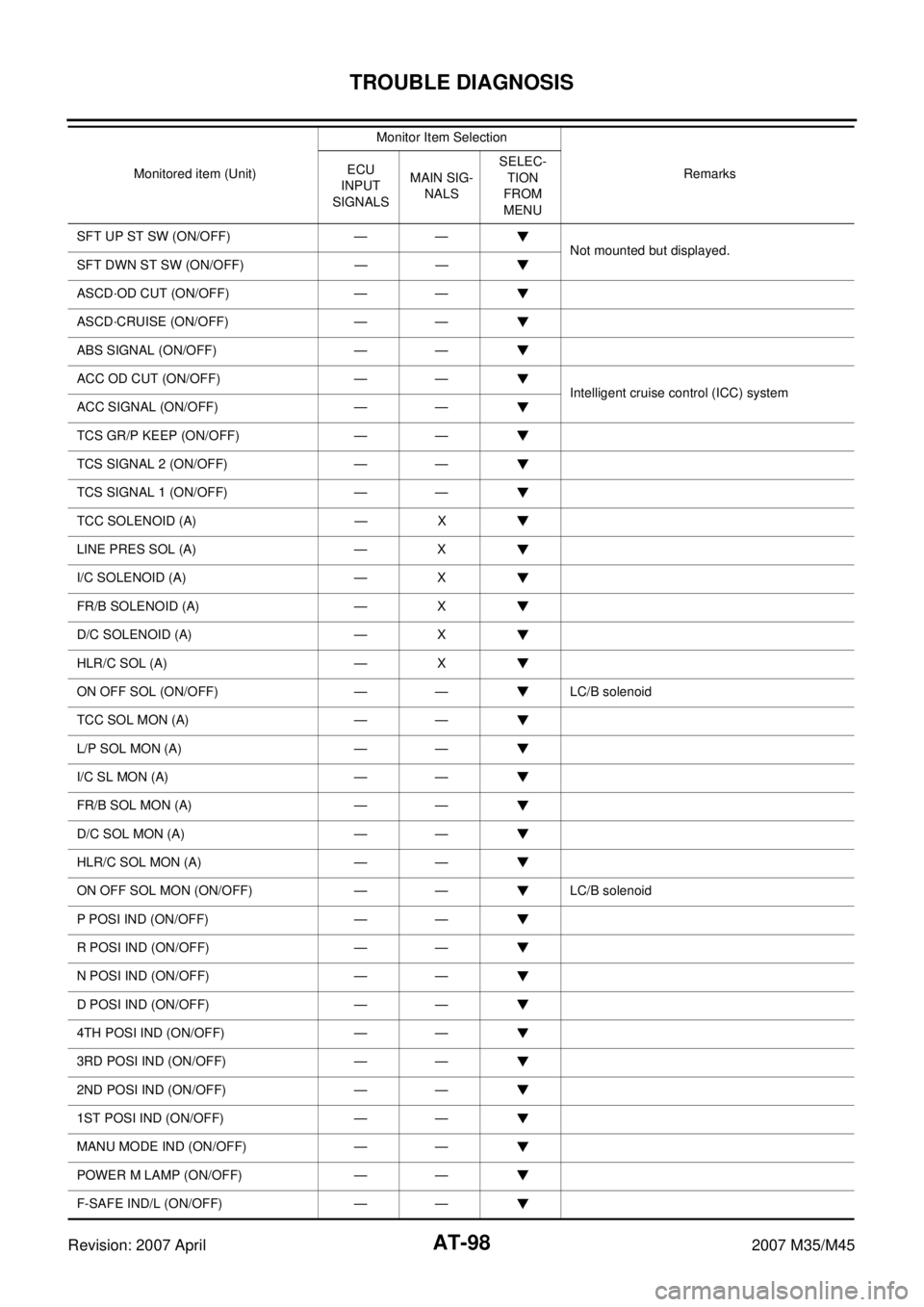
AT-98
TROUBLE DIAGNOSIS
Revision: 2007 April2007 M35/M45
SFT UP ST SW (ON/OFF) — —
Not mounted but displayed.
SFT DWN ST SW (ON/OFF) — —
ASCD·OD CUT (ON/OFF) — —
ASCD·CRUISE (ON/OFF) — —
ABS SIGNAL (ON/OFF) — —
ACC OD CUT (ON/OFF) — —
Intelligent cruise control (ICC) system
ACC SIGNAL (ON/OFF) — —
TCS GR/P KEEP (ON/OFF) — —
TCS SIGNAL 2 (ON/OFF) — —
TCS SIGNAL 1 (ON/OFF) — —
TCC SOLENOID (A) — X
LINE PRES SOL (A) — X
I/C SOLENOID (A) — X
FR/B SOLENOID (A) — X
D/C SOLENOID (A) — X
HLR/C SOL (A) — X
ON OFF SOL (ON/OFF) — — LC/B solenoid
TCC SOL MON (A) — —
L/P SOL MON (A) — —
I/C SL MON (A) — —
FR/B SOL MON (A) — —
D/C SOL MON (A) — —
HLR/C SOL MON (A) — —
ON OFF SOL MON (ON/OFF) — — LC/B solenoid
P POSI IND (ON/OFF) — —
R POSI IND (ON/OFF) — —
N POSI IND (ON/OFF) — —
D POSI IND (ON/OFF) — —
4TH POSI IND (ON/OFF) — —
3RD POSI IND (ON/OFF) — —
2ND POSI IND (ON/OFF) — —
1ST POSI IND (ON/OFF) — —
MANU MODE IND (ON/OFF) — —
POWER M LAMP (ON/OFF) — —
F-SAFE IND/L (ON/OFF) — —Monitored item (Unit)Monitor Item Selection
Remarks ECU
INPUT
SIGNALSMAIN SIG-
NALSSELEC-
TION
FROM
MENU
Page 183 of 4647
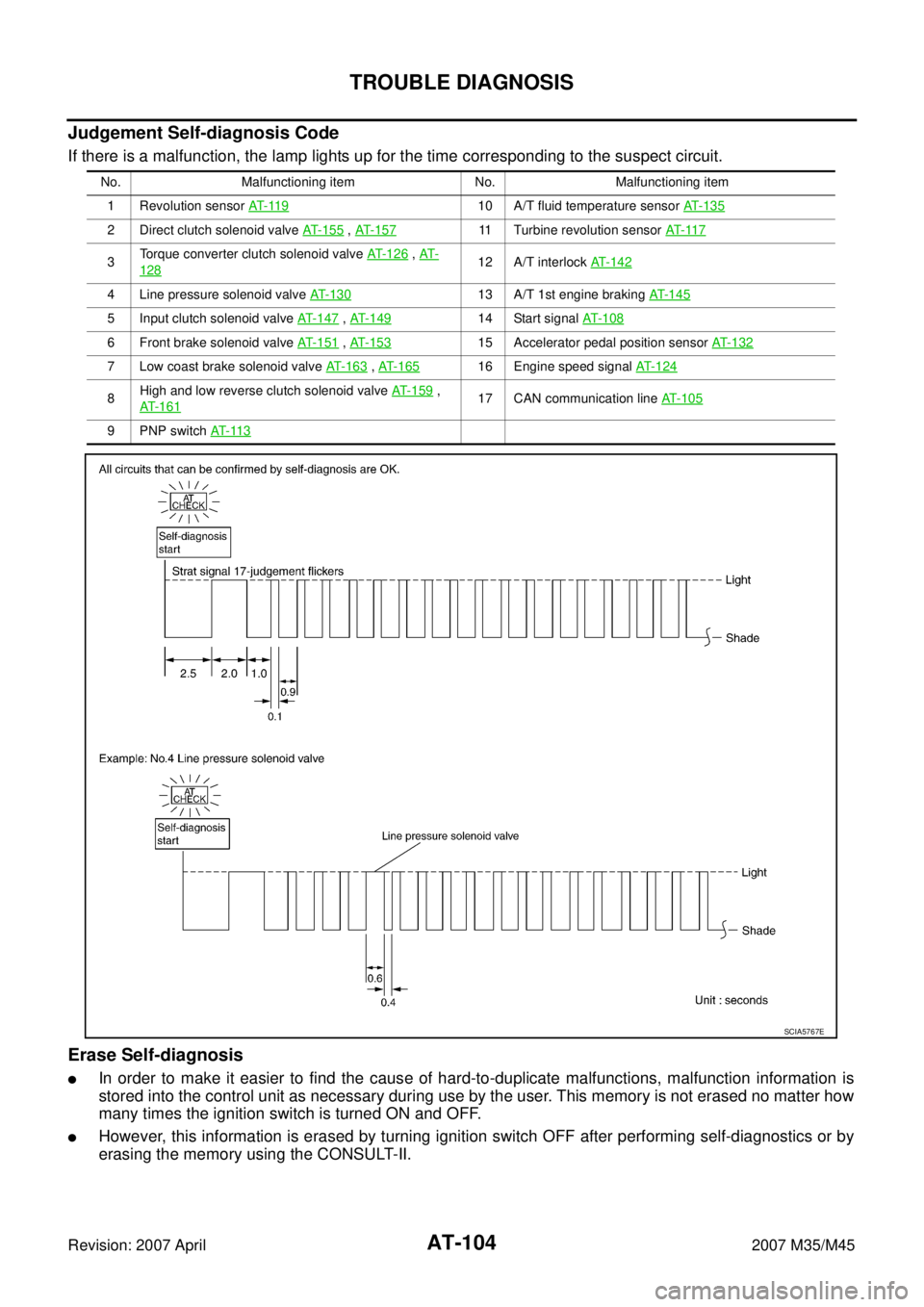
AT-104
TROUBLE DIAGNOSIS
Revision: 2007 April2007 M35/M45
Judgement Self-diagnosis Code
If there is a malfunction, the lamp lights up for the time corresponding to the suspect circuit.
Erase Self-diagnosis
In order to make it easier to find the cause of hard-to-duplicate malfunctions, malfunction information is
stored into the control unit as necessary during use by the user. This memory is not erased no matter how
many times the ignition switch is turned ON and OFF.
However, this information is erased by turning ignition switch OFF after performing self-diagnostics or by
erasing the memory using the CONSULT-II.
No. Malfunctioning item No. Malfunctioning item
1 Revolution sensor AT- 11 9
10 A/T fluid temperature sensor AT-135
2 Direct clutch solenoid valve AT- 1 5 5 , AT- 1 5 711 Turbine revolution sensor AT- 11 7
3Torque converter clutch solenoid valve AT- 1 2 6 , AT-
12812 A/T interlock AT-142
4 Line pressure solenoid valve AT- 1 3 013 A/T 1st engine braking AT- 1 4 5
5 Input clutch solenoid valve AT-147 , AT-14914 Start signal AT-108
6 Front brake solenoid valve AT-151 , AT-15315 Accelerator pedal position sensor AT-132
7 Low coast brake solenoid valve AT-163 , AT-16516 Engine speed signal AT-124
8High and low reverse clutch solenoid valve AT-159 ,
AT- 1 6 117 CAN communication line AT-105
9 PNP switch AT- 11 3
SCIA5767E
Page 184 of 4647
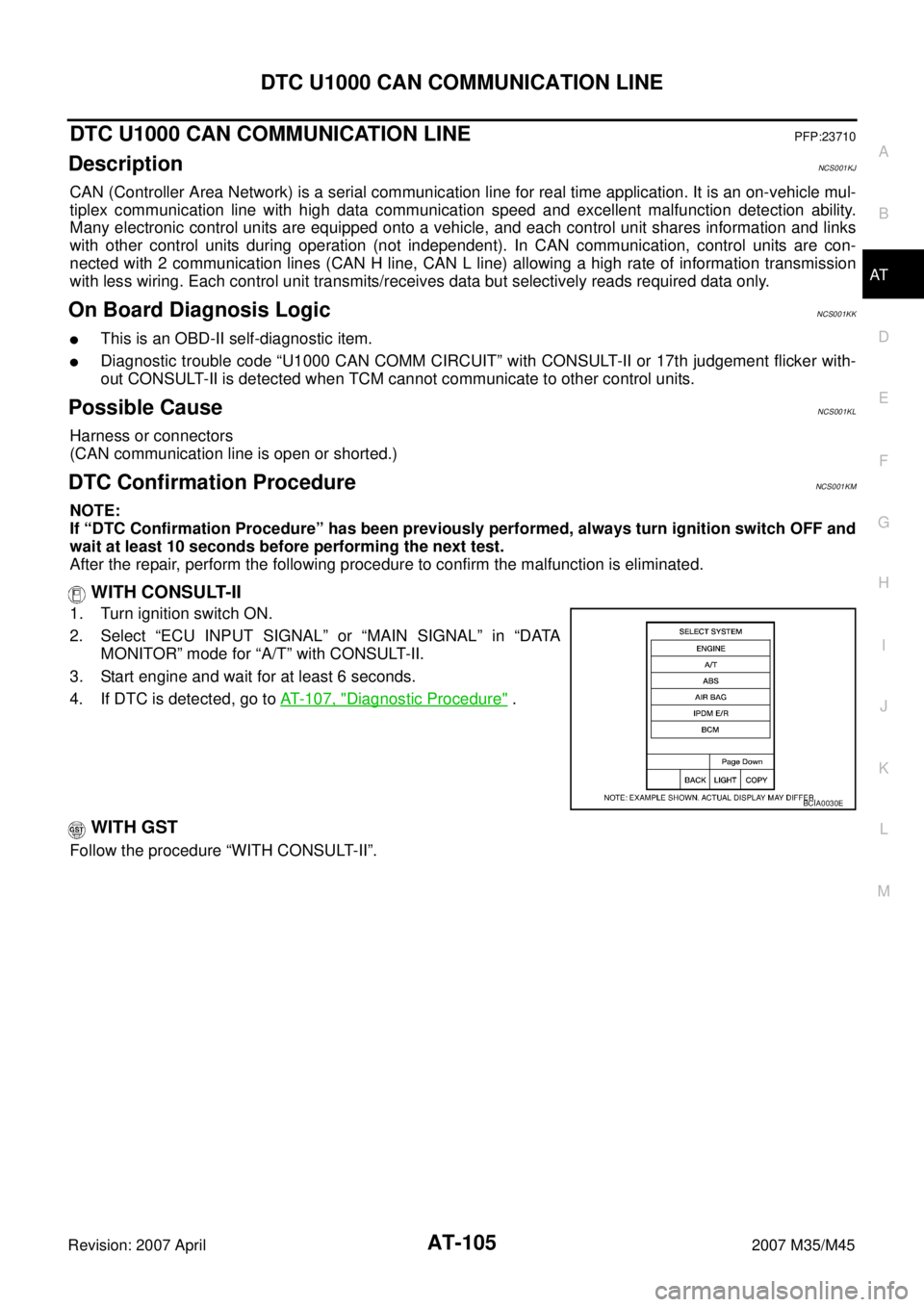
DTC U1000 CAN COMMUNICATION LINE
AT-105
D
E
F
G
H
I
J
K
L
MA
B
AT
Revision: 2007 April2007 M35/M45
DTC U1000 CAN COMMUNICATION LINEPFP:23710
DescriptionNCS001KJ
CAN (Controller Area Network) is a serial communication line for real time application. It is an on-vehicle mul-
tiplex communication line with high data communication speed and excellent malfunction detection ability.
Many electronic control units are equipped onto a vehicle, and each control unit shares information and links
with other control units during operation (not independent). In CAN communication, control units are con-
nected with 2 communication lines (CAN H line, CAN L line) allowing a high rate of information transmission
with less wiring. Each control unit transmits/receives data but selectively reads required data only.
On Board Diagnosis LogicNCS001KK
This is an OBD-II self-diagnostic item.
Diagnostic trouble code “U1000 CAN COMM CIRCUIT” with CONSULT-II or 17th judgement flicker with-
out CONSULT-II is detected when TCM cannot communicate to other control units.
Possible CauseNCS001KL
Harness or connectors
(CAN communication line is open or shorted.)
DTC Confirmation ProcedureNCS001KM
NOTE:
If “DTC Confirmation Procedure” has been previously performed, always turn ignition switch OFF and
wait at least 10 seconds before performing the next test.
After the repair, perform the following procedure to confirm the malfunction is eliminated.
WITH CONSULT-II
1. Turn ignition switch ON.
2. Select “ECU INPUT SIGNAL” or “MAIN SIGNAL” in “DATA
MONITOR” mode for “A/T” with CONSULT-II.
3. Start engine and wait for at least 6 seconds.
4. If DTC is detected, go to AT- 1 0 7 , "
Diagnostic Procedure" .
WITH GST
Follow the procedure “WITH CONSULT-II”.
BCIA0030E
Page 308 of 4647
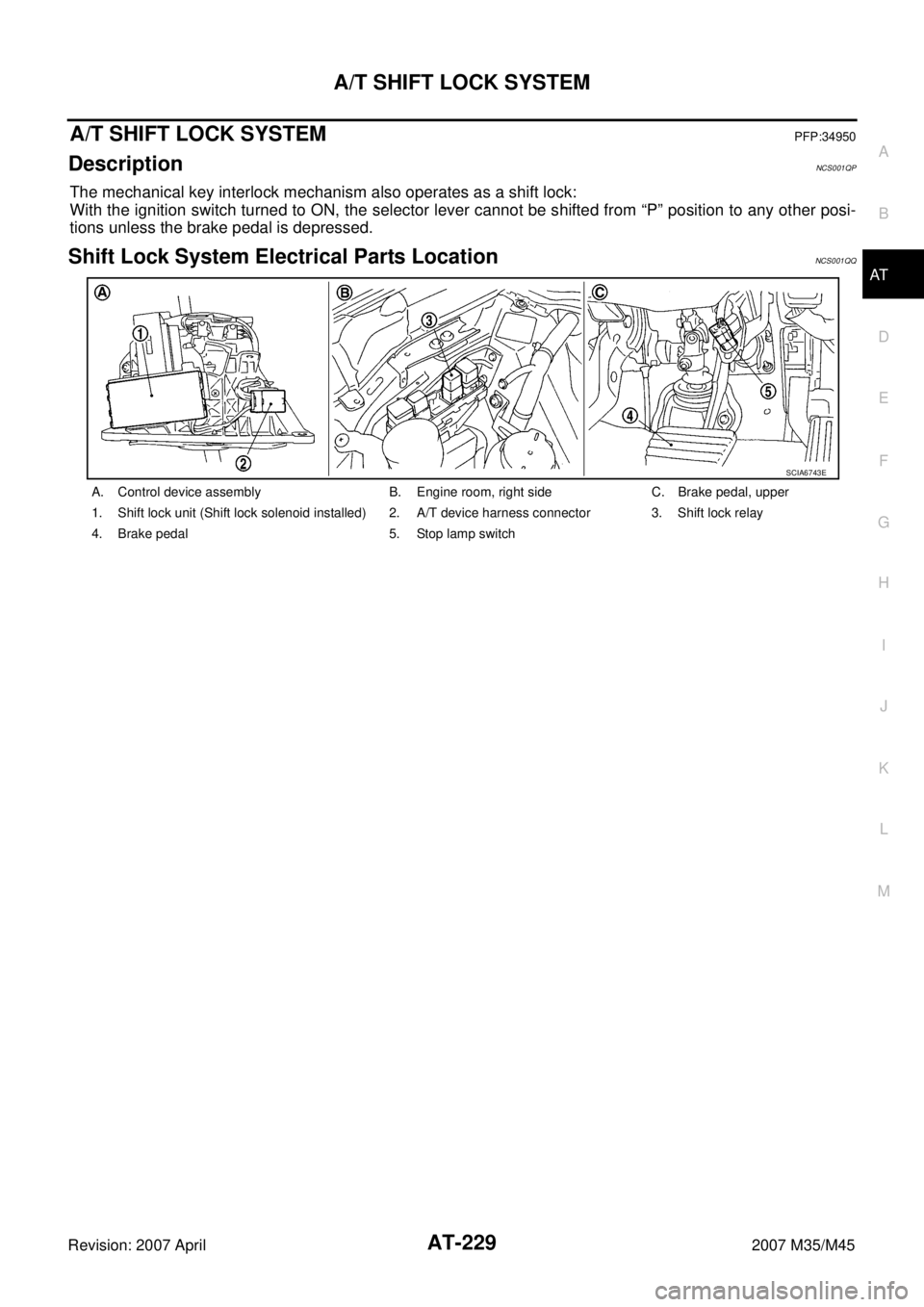
A/T SHIFT LOCK SYSTEM
AT-229
D
E
F
G
H
I
J
K
L
MA
B
AT
Revision: 2007 April2007 M35/M45
A/T SHIFT LOCK SYSTEMPFP:34950
DescriptionNCS001QP
The mechanical key interlock mechanism also operates as a shift lock:
With the ignition switch turned to ON, the selector lever cannot be shifted from “P” position to any other posi-
tions unless the brake pedal is depressed.
Shift Lock System Electrical Parts LocationNCS001QQ
A. Control device assembly B. Engine room, right side C. Brake pedal, upper
1. Shift lock unit (Shift lock solenoid installed) 2. A/T device harness connector 3. Shift lock relay
4. Brake pedal 5. Stop lamp switch
SCIA6743E
Page 454 of 4647
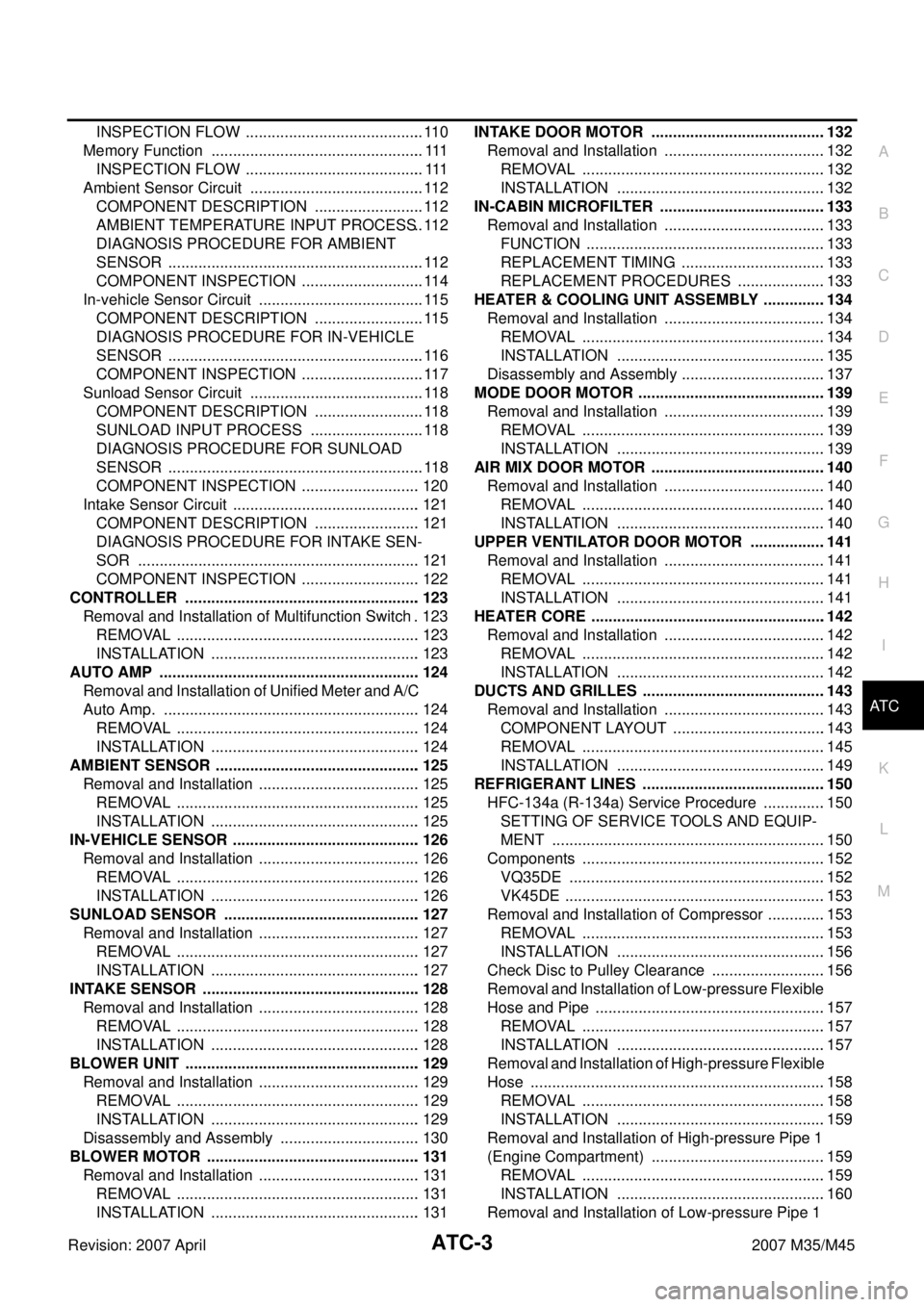
ATC-3
C
D
E
F
G
H
I
K
L
MA
B
AT C
Revision: 2007 April2007 M35/M45 INSPECTION FLOW .......................................... 110
Memory Function ................................................. . 111
INSPECTION FLOW ......................................... . 111
Ambient Sensor Circuit ......................................... 112
COMPONENT DESCRIPTION .......................... 112
AMBIENT TEMPERATURE INPUT PROCESS .. 112
DIAGNOSIS PROCEDURE FOR AMBIENT
SENSOR ............................................................ 112
COMPONENT INSPECTION ............................. 114
In-vehicle Sensor Circuit ....................................... 115
COMPONENT DESCRIPTION .......................... 115
DIAGNOSIS PROCEDURE FOR IN-VEHICLE
SENSOR ............................................................ 116
COMPONENT INSPECTION ............................. 117
Sunload Sensor Circuit ......................................... 118
COMPONENT DESCRIPTION .......................... 118
SUNLOAD INPUT PROCESS ........................... 118
DIAGNOSIS PROCEDURE FOR SUNLOAD
SENSOR ............................................................ 118
COMPONENT INSPECTION ............................ 120
Intake Sensor Circuit ............................................ 121
COMPONENT DESCRIPTION ......................... 121
DIAGNOSIS PROCEDURE FOR INTAKE SEN-
SOR .................................................................. 121
COMPONENT INSPECTION ............................ 122
CONTROLLER ....................................................... 123
Removal and Installation of Multifunction Switch . 123
REMOVAL ......................................................... 123
INSTALLATION ................................................. 123
AUTO AMP ............................................................. 124
Removal and Installation of Unified Meter and A/C
Auto Amp. ............................................................ 124
REMOVAL ......................................................... 124
INSTALLATION ................................................. 124
AMBIENT SENSOR ................................................ 125
Removal and Installation ...................................... 125
REMOVAL ......................................................... 125
INSTALLATION ................................................. 125
IN-VEHICLE SENSOR ............................................ 126
Removal and Installation ...................................... 126
REMOVAL ......................................................... 126
INSTALLATION ................................................. 126
SUNLOAD SENSOR .............................................. 127
Removal and Installation ...................................... 127
REMOVAL ......................................................... 127
INSTALLATION ................................................. 127
INTAKE SENSOR ................................................... 128
Removal and Installation ...................................... 128
REMOVAL ......................................................... 128
INSTALLATION ................................................. 128
BLOWER UNIT ....................................................... 129
Removal and Installation ...................................... 129
REMOVAL ......................................................... 129
INSTALLATION ................................................. 129
Disassembly and Assembly ................................. 130
BLOWER MOTOR .................................................. 131
Removal and Installation ...................................... 131
REMOVAL ......................................................... 131
INSTALLATION ................................................. 131INTAKE DOOR MOTOR .........................................132
Removal and Installation ......................................132
REMOVAL .........................................................132
INSTALLATION .................................................132
IN-CABIN MICROFILTER .......................................133
Removal and Installation ......................................133
FUNCTION ........................................................133
REPLACEMENT TIMING ..................................133
REPLACEMENT PROCEDURES .....................133
HEATER & COOLING UNIT ASSEMBLY ...............134
Removal and Installation ......................................134
REMOVAL .........................................................134
INSTALLATION .................................................135
Disassembly and Assembly ..................................137
MODE DOOR MOTOR ............................................139
Removal and Installation ......................................139
REMOVAL .........................................................139
INSTALLATION .................................................139
AIR MIX DOOR MOTOR .........................................140
Removal and Installation ......................................140
REMOVAL .........................................................140
INSTALLATION .................................................140
UPPER VENTILATOR DOOR MOTOR ..................141
Removal and Installation ......................................141
REMOVAL .........................................................141
INSTALLATION .................................................141
HEATER CORE .......................................................142
Removal and Installation ......................................142
REMOVAL .........................................................142
INSTALLATION .................................................142
DUCTS AND GRILLES ...........................................143
Removal and Installation ......................................143
COMPONENT LAYOUT ....................................143
REMOVAL .........................................................145
INSTALLATION .................................................149
REFRIGERANT LINES ...........................................150
HFC-134a (R-134a) Service Procedure ...............150
SETTING OF SERVICE TOOLS AND EQUIP-
MENT ................................................................150
Components .........................................................152
VQ35DE ............................................................152
VK45DE .............................................................153
Removal and Installation of Compressor ..............153
REMOVAL .........................................................153
INSTALLATION .................................................156
Check Disc to Pulley Clearance ...........................156
Removal and Installation of Low-pressure Flexible
Hose and Pipe ......................................................157
REMOVAL .........................................................157
INSTALLATION .................................................157
Removal and Installation of High-pressure Flexible
Hose .....................................................................158
REMOVAL .........................................................158
INSTALLATION .................................................159
Removal and Installation of High-pressure Pipe 1
(Engine Compartment) .........................................159
REMOVAL .........................................................159
INSTALLATION .................................................160
Removal and Installation of Low-pressure Pipe 1
Page 456 of 4647
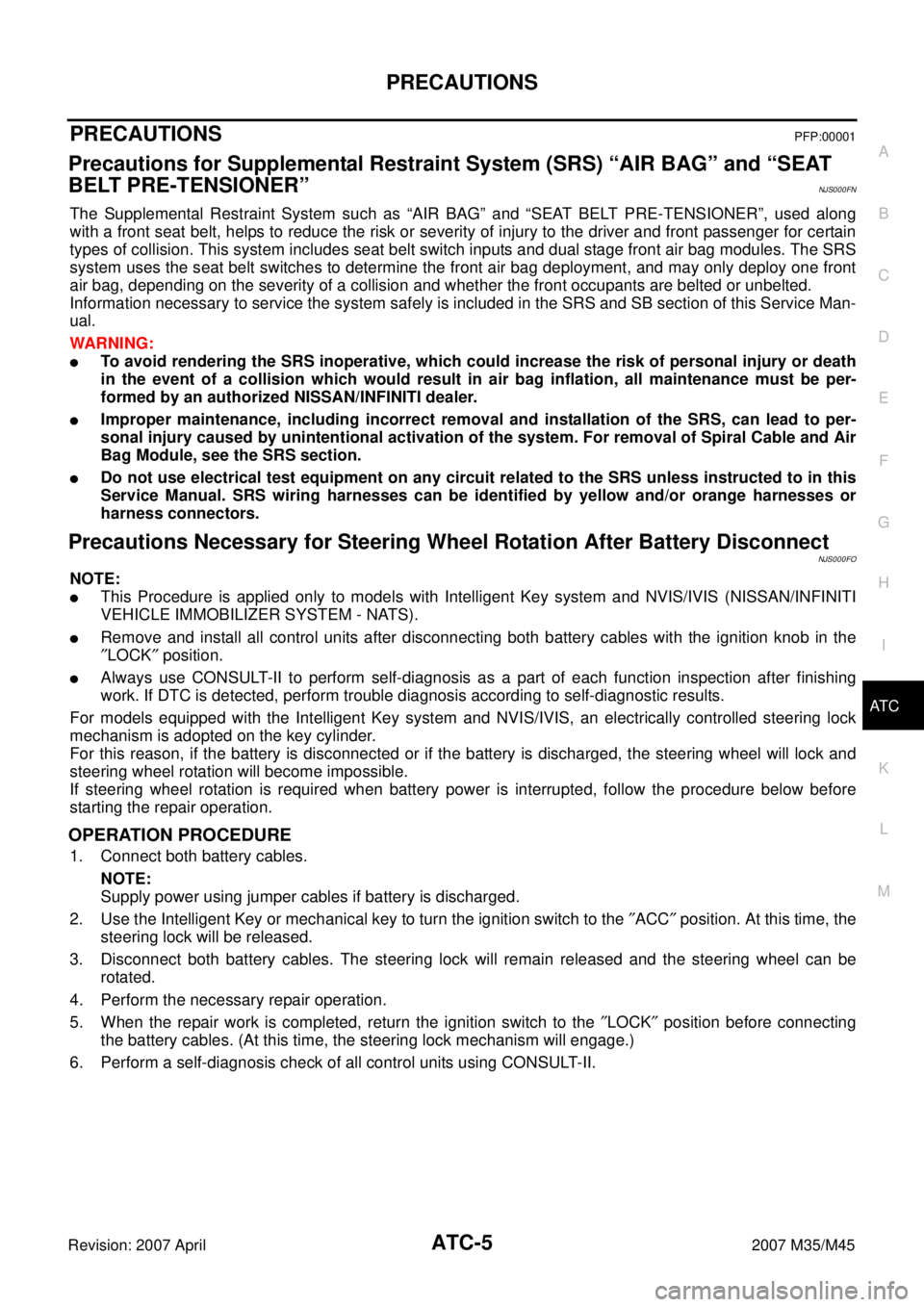
PRECAUTIONS
ATC-5
C
D
E
F
G
H
I
K
L
MA
B
AT C
Revision: 2007 April2007 M35/M45
PRECAUTIONSPFP:00001
Precautions for Supplemental Restraint System (SRS) “AIR BAG” and “SEAT
BELT PRE-TENSIONER”
NJS000FN
The Supplemental Restraint System such as “AIR BAG” and “SEAT BELT PRE-TENSIONER”, used along
with a front seat belt, helps to reduce the risk or severity of injury to the driver and front passenger for certain
types of collision. This system includes seat belt switch inputs and dual stage front air bag modules. The SRS
system uses the seat belt switches to determine the front air bag deployment, and may only deploy one front
air bag, depending on the severity of a collision and whether the front occupants are belted or unbelted.
Information necessary to service the system safely is included in the SRS and SB section of this Service Man-
ual.
WARNING:
To avoid rendering the SRS inoperative, which could increase the risk of personal injury or death
in the event of a collision which would result in air bag inflation, all maintenance must be per-
formed by an authorized NISSAN/INFINITI dealer.
Improper maintenance, including incorrect removal and installation of the SRS, can lead to per-
sonal injury caused by unintentional activation of the system. For removal of Spiral Cable and Air
Bag Module, see the SRS section.
Do not use electrical test equipment on any circuit related to the SRS unless instructed to in this
Service Manual. SRS wiring harnesses can be identified by yellow and/or orange harnesses or
harness connectors.
Precautions Necessary for Steering Wheel Rotation After Battery DisconnectNJS000FO
NOTE:
This Procedure is applied only to models with Intelligent Key system and NVIS/IVIS (NISSAN/INFINITI
VEHICLE IMMOBILIZER SYSTEM - NATS).
Remove and install all control units after disconnecting both battery cables with the ignition knob in the
″LOCK″ position.
Always use CONSULT-II to perform self-diagnosis as a part of each function inspection after finishing
work. If DTC is detected, perform trouble diagnosis according to self-diagnostic results.
For models equipped with the Intelligent Key system and NVIS/IVIS, an electrically controlled steering lock
mechanism is adopted on the key cylinder.
For this reason, if the battery is disconnected or if the battery is discharged, the steering wheel will lock and
steering wheel rotation will become impossible.
If steering wheel rotation is required when battery power is interrupted, follow the procedure below before
starting the repair operation.
OPERATION PROCEDURE
1. Connect both battery cables.
NOTE:
Supply power using jumper cables if battery is discharged.
2. Use the Intelligent Key or mechanical key to turn the ignition switch to the ″ACC″ position. At this time, the
steering lock will be released.
3. Disconnect both battery cables. The steering lock will remain released and the steering wheel can be
rotated.
4. Perform the necessary repair operation.
5. When the repair work is completed, return the ignition switch to the ″LOCK″ position before connecting
the battery cables. (At this time, the steering lock mechanism will engage.)
6. Perform a self-diagnosis check of all control units using CONSULT-II.