control unit INFINITI M35 2007 Factory Service Manual
[x] Cancel search | Manufacturer: INFINITI, Model Year: 2007, Model line: M35, Model: INFINITI M35 2007Pages: 4647, PDF Size: 93.69 MB
Page 3636 of 4647
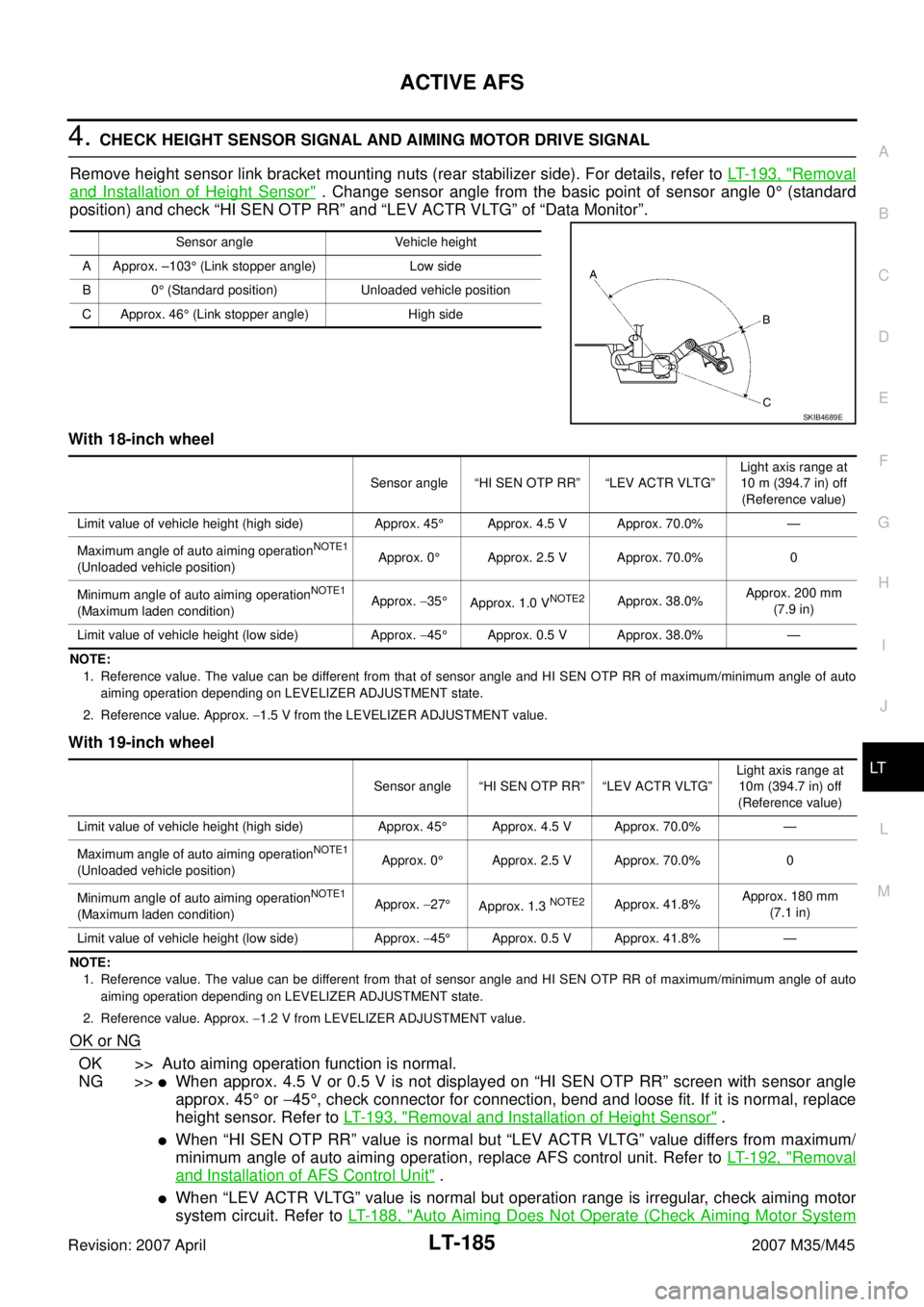
ACTIVE AFS
LT-185
C
D
E
F
G
H
I
J
L
MA
B
LT
Revision: 2007 April2007 M35/M45
4. CHECK HEIGHT SENSOR SIGNAL AND AIMING MOTOR DRIVE SIGNAL
Remove height sensor link bracket mounting nuts (rear stabilizer side). For details, refer to LT- 1 9 3 , "
Removal
and Installation of Height Sensor" . Change sensor angle from the basic point of sensor angle 0° (standard
position) and check “HI SEN OTP RR” and “LEV ACTR VLTG” of “Data Monitor”.
With 18-inch wheel
NOTE:
1. Reference value. The value can be different from that of sensor angle and HI SEN OTP RR of maximum/minimum angle of auto
aiming operation depending on LEVELIZER ADJUSTMENT state.
2. Reference value. Approx. −1.5 V from the LEVELIZER ADJUSTMENT value.
With 19-inch wheel
NOTE:
1. Reference value. The value can be different from that of sensor angle and HI SEN OTP RR of maximum/minimum angle of auto
aiming operation depending on LEVELIZER ADJUSTMENT state.
2. Reference value. Approx. −1.2 V from LEVELIZER ADJUSTMENT value.
OK or NG
OK >> Auto aiming operation function is normal.
NG >>
When approx. 4.5 V or 0.5 V is not displayed on “HI SEN OTP RR” screen with sensor angle
approx. 45° or −45°, check connector for connection, bend and loose fit. If it is normal, replace
height sensor. Refer to LT- 1 9 3 , "
Removal and Installation of Height Sensor" .
When “HI SEN OTP RR” value is normal but “LEV ACTR VLTG” value differs from maximum/
minimum angle of auto aiming operation, replace AFS control unit. Refer to LT- 1 9 2 , "
Removal
and Installation of AFS Control Unit" .
When “LEV ACTR VLTG” value is normal but operation range is irregular, check aiming motor
system circuit. Refer to LT- 1 8 8 , "
Auto Aiming Does Not Operate (Check Aiming Motor System
Sensor angle Vehicle height
A Approx. –103° (Link stopper angle) Low side
B0° (Standard position) Unloaded vehicle position
C Approx. 46° (Link stopper angle) High side
SKIB4689E
Sensor angle “HI SEN OTP RR” “LEV ACTR VLTG”Light axis range at
10 m (394.7 in) off
(Reference value)
Limit value of vehicle height (high side) Approx. 45°Approx. 4.5 V Approx. 70.0% —
Maximum angle of auto aiming operation
NOTE1
(Unloaded vehicle position)Approx. 0°Approx. 2.5 V Approx. 70.0% 0
Minimum angle of auto aiming operation
NOTE1
(Maximum laden condition)Approx. −35°
Approx. 1.0 VNOTE2Approx. 38.0%Approx. 200 mm
(7.9 in)
Limit value of vehicle height (low side) Approx. −45°Approx. 0.5 V Approx. 38.0% —
Sensor angle “HI SEN OTP RR” “LEV ACTR VLTG”Light axis range at
10m (394.7 in) off
(Reference value)
Limit value of vehicle height (high side) Approx. 45°Approx. 4.5 V Approx. 70.0% —
Maximum angle of auto aiming operation
NOTE1
(Unloaded vehicle position)Approx. 0°Approx. 2.5 V Approx. 70.0% 0
Minimum angle of auto aiming operation
NOTE1
(Maximum laden condition)Approx. −27°
Approx. 1.3 NOTE2Approx. 41.8%Approx. 180 mm
(7.1 in)
Limit value of vehicle height (low side) Approx. −45°Approx. 0.5 V Approx. 41.8% —
Page 3637 of 4647
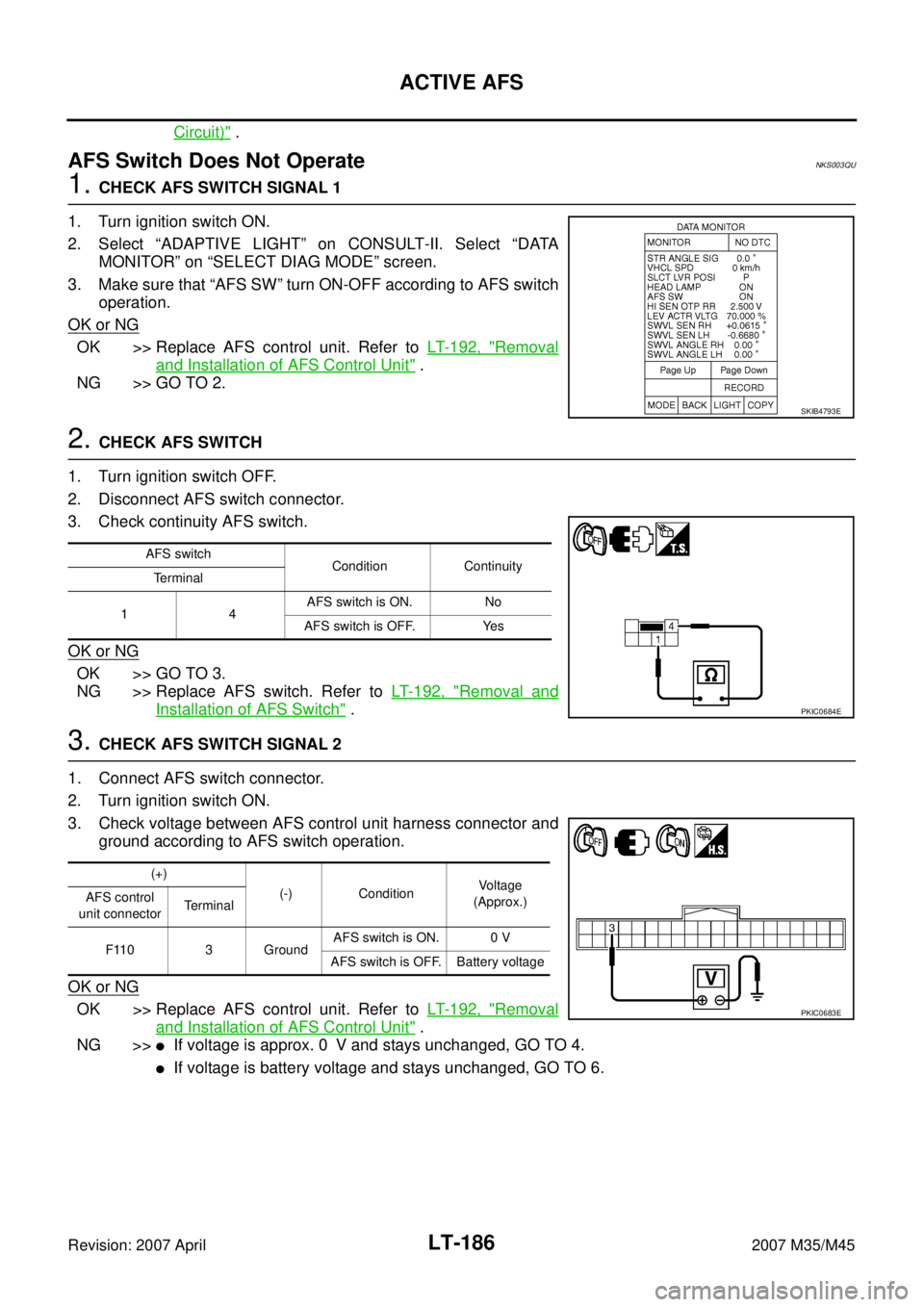
LT-186
ACTIVE AFS
Revision: 2007 April2007 M35/M45
Circuit)" .
AFS Switch Does Not OperateNKS003QU
1. CHECK AFS SWITCH SIGNAL 1
1. Turn ignition switch ON.
2. Select “ADAPTIVE LIGHT” on CONSULT-II. Select “DATA
MONITOR” on “SELECT DIAG MODE” screen.
3. Make sure that “AFS SW” turn ON-OFF according to AFS switch
operation.
OK or NG
OK >> Replace AFS control unit. Refer to LT- 1 9 2 , "Removal
and Installation of AFS Control Unit" .
NG >> GO TO 2.
2. CHECK AFS SWITCH
1. Turn ignition switch OFF.
2. Disconnect AFS switch connector.
3. Check continuity AFS switch.
OK or NG
OK >> GO TO 3.
NG >> Replace AFS switch. Refer to LT- 1 9 2 , "
Removal and
Installation of AFS Switch" .
3. CHECK AFS SWITCH SIGNAL 2
1. Connect AFS switch connector.
2. Turn ignition switch ON.
3. Check voltage between AFS control unit harness connector and
ground according to AFS switch operation.
OK or NG
OK >> Replace AFS control unit. Refer to LT- 1 9 2 , "Removal
and Installation of AFS Control Unit" .
NG >>
If voltage is approx. 0 V and stays unchanged, GO TO 4.
If voltage is battery voltage and stays unchanged, GO TO 6.
SKIB4793E
AFS switch
Condition Continuity
Terminal
14AFS switch is ON. No
AFS switch is OFF. Yes
PKIC0684E
(+)
(-) ConditionVoltage
(Approx.) AFS control
unit connectorTe r m i n a l
F110 3 GroundAFS switch is ON. 0 V
AFS switch is OFF. Battery voltage
PKIC0683E
Page 3638 of 4647
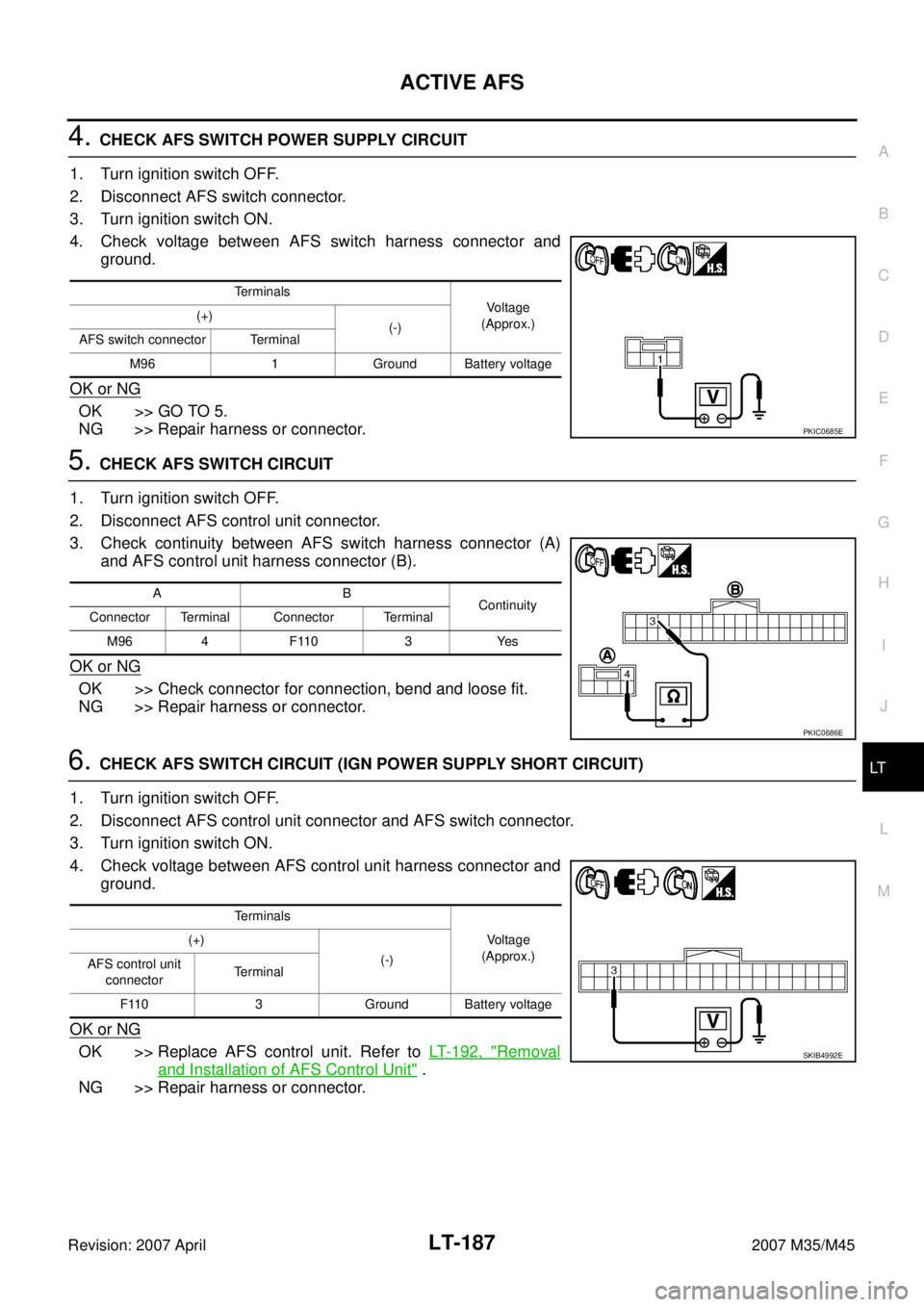
ACTIVE AFS
LT-187
C
D
E
F
G
H
I
J
L
MA
B
LT
Revision: 2007 April2007 M35/M45
4. CHECK AFS SWITCH POWER SUPPLY CIRCUIT
1. Turn ignition switch OFF.
2. Disconnect AFS switch connector.
3. Turn ignition switch ON.
4. Check voltage between AFS switch harness connector and
ground.
OK or NG
OK >> GO TO 5.
NG >> Repair harness or connector.
5. CHECK AFS SWITCH CIRCUIT
1. Turn ignition switch OFF.
2. Disconnect AFS control unit connector.
3. Check continuity between AFS switch harness connector (A)
and AFS control unit harness connector (B).
OK or NG
OK >> Check connector for connection, bend and loose fit.
NG >> Repair harness or connector.
6. CHECK AFS SWITCH CIRCUIT (IGN POWER SUPPLY SHORT CIRCUIT)
1. Turn ignition switch OFF.
2. Disconnect AFS control unit connector and AFS switch connector.
3. Turn ignition switch ON.
4. Check voltage between AFS control unit harness connector and
ground.
OK or NG
OK >> Replace AFS control unit. Refer to LT- 1 9 2 , "Removal
and Installation of AFS Control Unit" .
NG >> Repair harness or connector.
Terminals
Voltage
(Approx.) (+)
(-)
AFS switch connector Terminal
M96 1 Ground Battery voltage
PKIC0685E
AB
Continuity
Connector Terminal Connector Terminal
M96 4 F110 3 Yes
PKIC0686E
Terminals
Voltage
(Approx.) (+)
(-)
AFS control unit
connectorTerminal
F110 3 Ground Battery voltage
SKIB4992E
Page 3639 of 4647
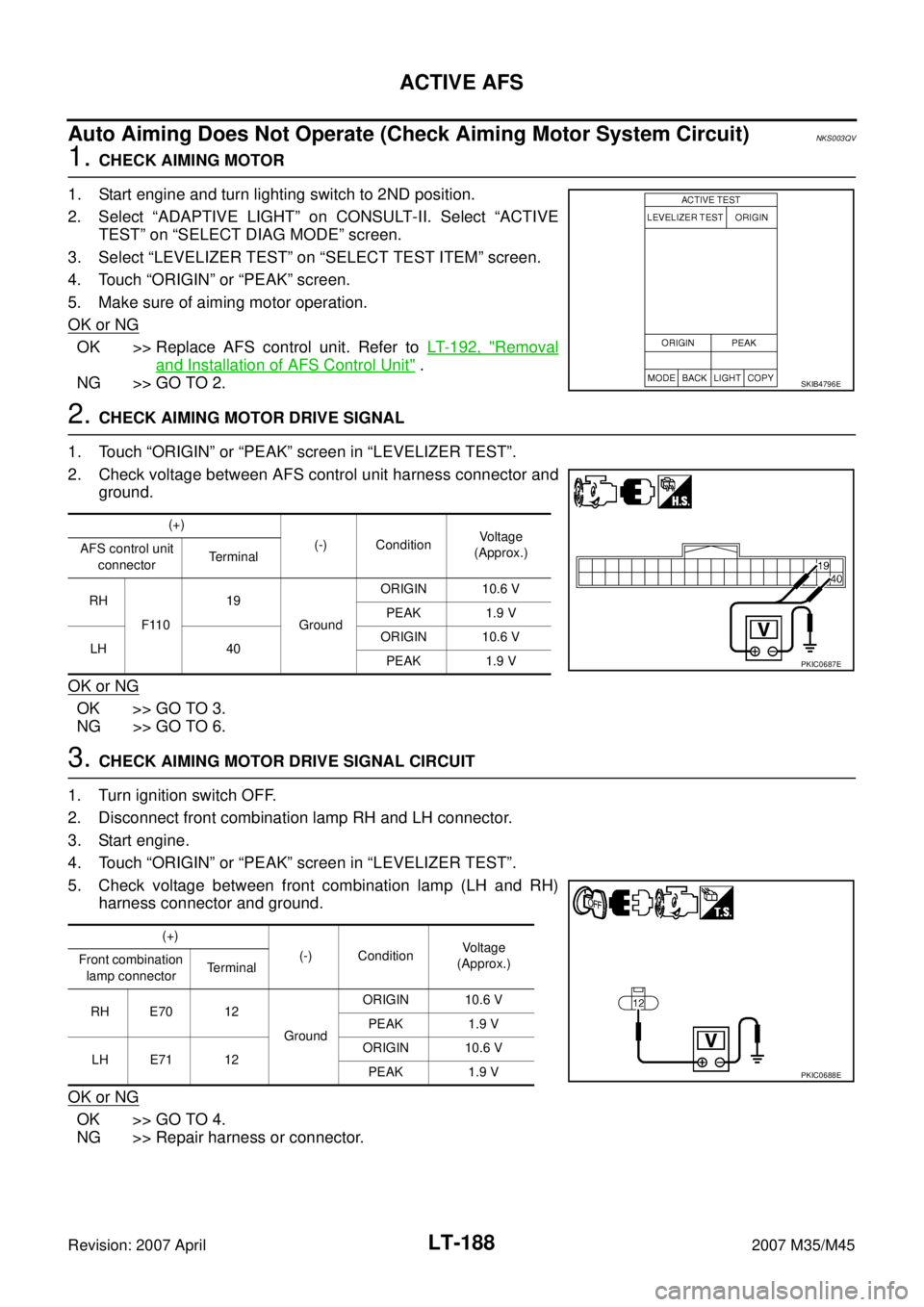
LT-188
ACTIVE AFS
Revision: 2007 April2007 M35/M45
Auto Aiming Does Not Operate (Check Aiming Motor System Circuit)NKS003QV
1. CHECK AIMING MOTOR
1. Start engine and turn lighting switch to 2ND position.
2. Select “ADAPTIVE LIGHT” on CONSULT-II. Select “ACTIVE
TEST” on “SELECT DIAG MODE” screen.
3. Select “LEVELIZER TEST” on “SELECT TEST ITEM” screen.
4. Touch “ORIGIN” or “PEAK” screen.
5. Make sure of aiming motor operation.
OK or NG
OK >> Replace AFS control unit. Refer to LT- 1 9 2 , "Removal
and Installation of AFS Control Unit" .
NG >> GO TO 2.
2. CHECK AIMING MOTOR DRIVE SIGNAL
1. Touch “ORIGIN” or “PEAK” screen in “LEVELIZER TEST”.
2. Check voltage between AFS control unit harness connector and
ground.
OK or NG
OK >> GO TO 3.
NG >> GO TO 6.
3. CHECK AIMING MOTOR DRIVE SIGNAL CIRCUIT
1. Turn ignition switch OFF.
2. Disconnect front combination lamp RH and LH connector.
3. Start engine.
4. Touch “ORIGIN” or “PEAK” screen in “LEVELIZER TEST”.
5. Check voltage between front combination lamp (LH and RH)
harness connector and ground.
OK or NG
OK >> GO TO 4.
NG >> Repair harness or connector.
SKIB4796E
(+)
(-) ConditionVoltage
(Approx.) AFS control unit
connectorTerminal
RH
F11019
GroundORIGIN 10.6 V
PEAK 1.9 V
LH 40ORIGIN 10.6 V
PEAK 1.9 V
PKIC0687E
(+)
(-) ConditionVoltage
(Approx.) Front combination
lamp connectorTerminal
RH E70 12
GroundORIGIN 10.6 V
PEAK 1.9 V
LH E71 12ORIGIN 10.6 V
PEAK 1.9 V
PKIC0688E
Page 3640 of 4647
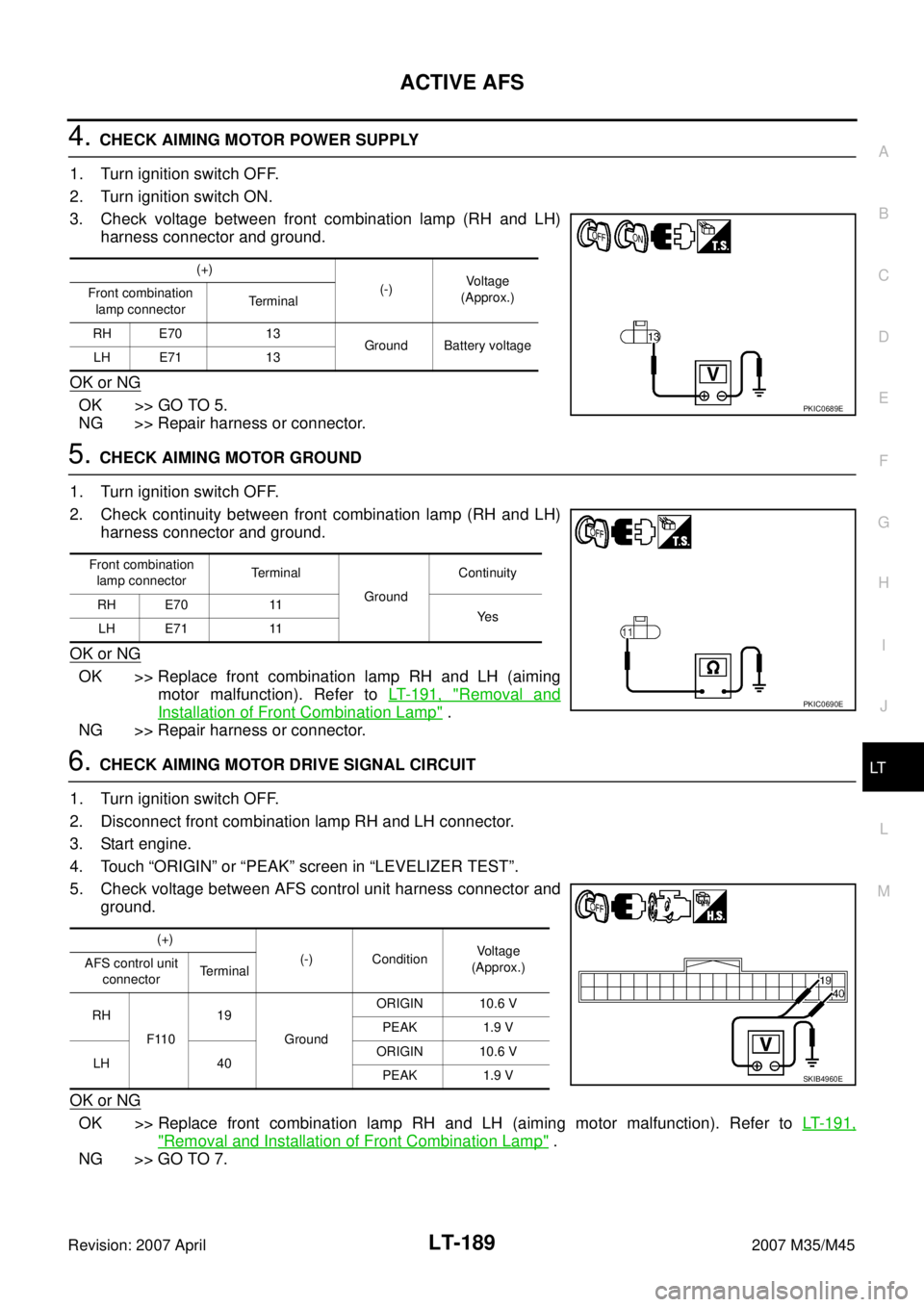
ACTIVE AFS
LT-189
C
D
E
F
G
H
I
J
L
MA
B
LT
Revision: 2007 April2007 M35/M45
4. CHECK AIMING MOTOR POWER SUPPLY
1. Turn ignition switch OFF.
2. Turn ignition switch ON.
3. Check voltage between front combination lamp (RH and LH)
harness connector and ground.
OK or NG
OK >> GO TO 5.
NG >> Repair harness or connector.
5. CHECK AIMING MOTOR GROUND
1. Turn ignition switch OFF.
2. Check continuity between front combination lamp (RH and LH)
harness connector and ground.
OK or NG
OK >> Replace front combination lamp RH and LH (aiming
motor malfunction). Refer to LT- 1 9 1 , "
Removal and
Installation of Front Combination Lamp" .
NG >> Repair harness or connector.
6. CHECK AIMING MOTOR DRIVE SIGNAL CIRCUIT
1. Turn ignition switch OFF.
2. Disconnect front combination lamp RH and LH connector.
3. Start engine.
4. Touch “ORIGIN” or “PEAK” screen in “LEVELIZER TEST”.
5. Check voltage between AFS control unit harness connector and
ground.
OK or NG
OK >> Replace front combination lamp RH and LH (aiming motor malfunction). Refer to LT- 1 9 1 ,
"Removal and Installation of Front Combination Lamp" .
NG >> GO TO 7.
(+)
(-)Voltage
(Approx.) Front combination
lamp connectorTerminal
RH E70 13
Ground Battery voltage
LH E71 13
PKIC0689E
Front combination
lamp connectorTerminal
GroundContinuity
RH E70 11
Ye s
LH E71 11
PKIC0690E
(+)
(-) ConditionVoltage
(Approx.) AFS control unit
connectorTerminal
RH
F11019
GroundORIGIN 10.6 V
PEAK 1.9 V
LH 40ORIGIN 10.6 V
PEAK 1.9 V
SKIB4960E
Page 3641 of 4647
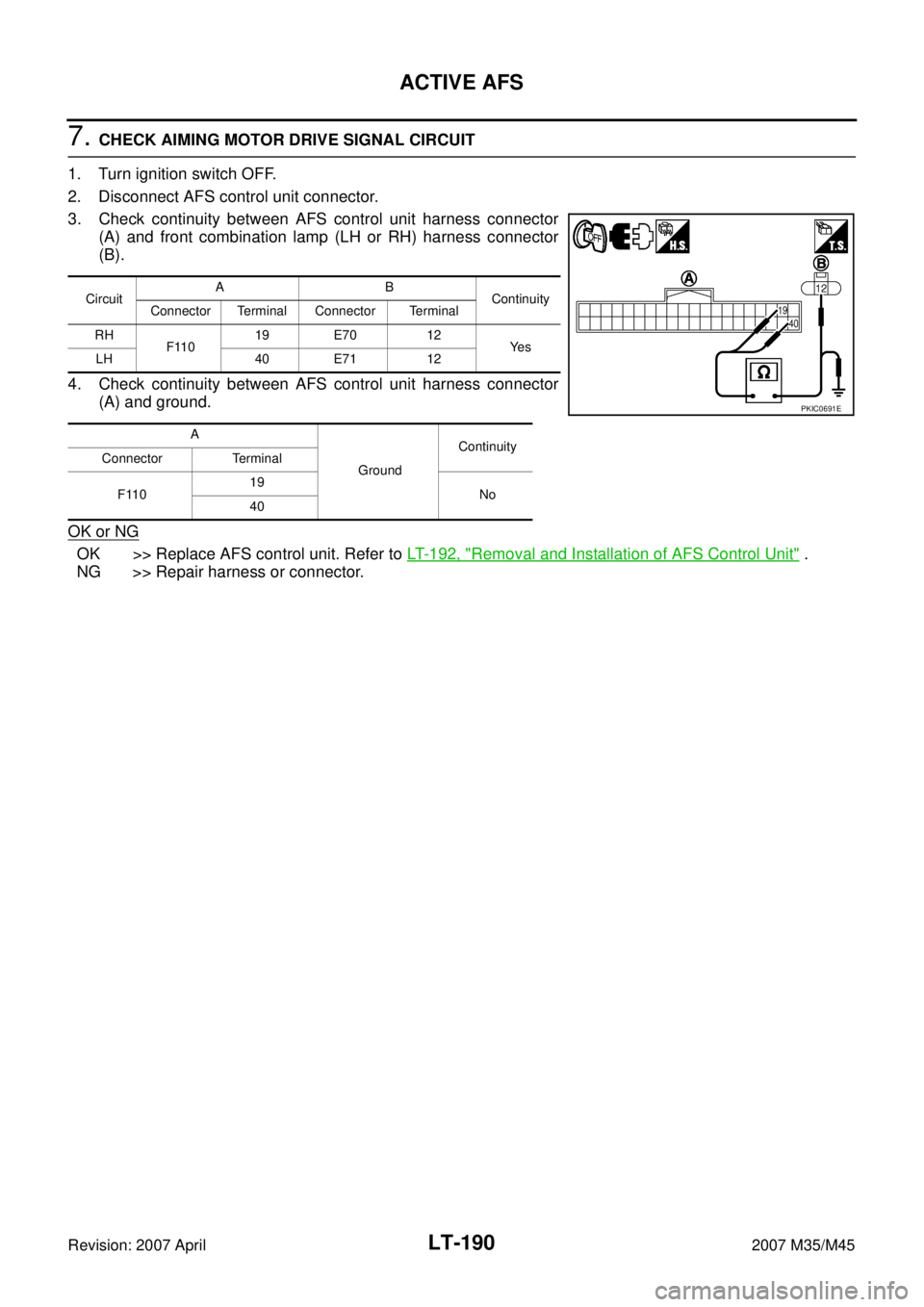
LT-190
ACTIVE AFS
Revision: 2007 April2007 M35/M45
7. CHECK AIMING MOTOR DRIVE SIGNAL CIRCUIT
1. Turn ignition switch OFF.
2. Disconnect AFS control unit connector.
3. Check continuity between AFS control unit harness connector
(A) and front combination lamp (LH or RH) harness connector
(B).
4. Check continuity between AFS control unit harness connector
(A) and ground.
OK or NG
OK >> Replace AFS control unit. Refer to LT- 1 9 2 , "Removal and Installation of AFS Control Unit" .
NG >> Repair harness or connector.
CircuitAB
Continuity
Connector Terminal Connector Terminal
RH
F11019 E70 12
Ye s
LH 40 E71 12
A
GroundContinuity
Connector Terminal
F11019
No
40
PKIC0691E
Page 3642 of 4647
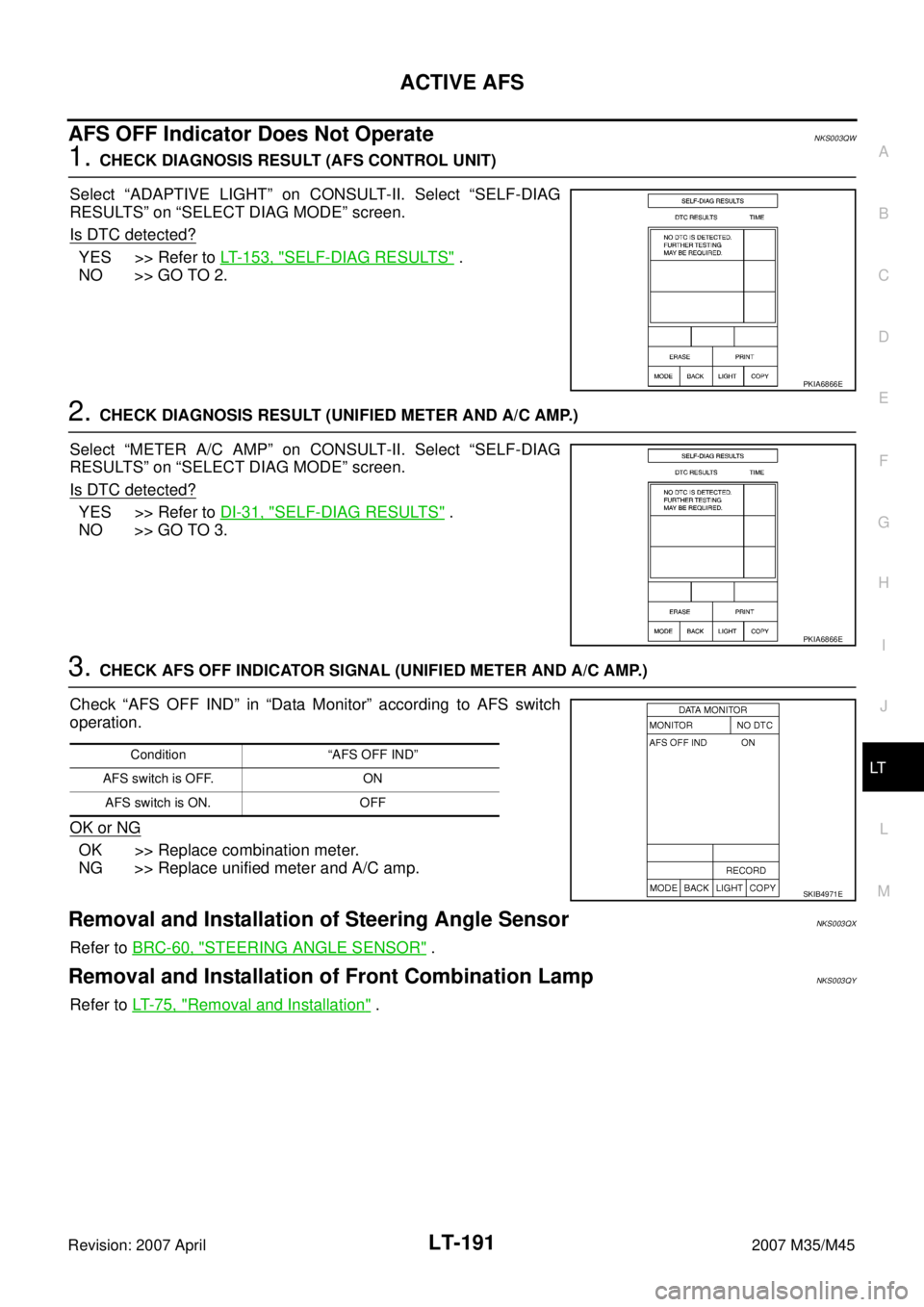
ACTIVE AFS
LT-191
C
D
E
F
G
H
I
J
L
MA
B
LT
Revision: 2007 April2007 M35/M45
AFS OFF Indicator Does Not OperateNKS003QW
1. CHECK DIAGNOSIS RESULT (AFS CONTROL UNIT)
Select “ADAPTIVE LIGHT” on CONSULT-II. Select “SELF-DIAG
RESULTS” on “SELECT DIAG MODE” screen.
Is DTC detected?
YES >> Refer to LT- 1 5 3 , "SELF-DIAG RESULTS" .
NO >> GO TO 2.
2. CHECK DIAGNOSIS RESULT (UNIFIED METER AND A/C AMP.)
Select “METER A/C AMP” on CONSULT-II. Select “SELF-DIAG
RESULTS” on “SELECT DIAG MODE” screen.
Is DTC detected?
YES >> Refer to DI-31, "SELF-DIAG RESULTS" .
NO >> GO TO 3.
3. CHECK AFS OFF INDICATOR SIGNAL (UNIFIED METER AND A/C AMP.)
Check “AFS OFF IND” in “Data Monitor” according to AFS switch
operation.
OK or NG
OK >> Replace combination meter.
NG >> Replace unified meter and A/C amp.
Removal and Installation of Steering Angle SensorNKS003QX
Refer to BRC-60, "STEERING ANGLE SENSOR" .
Removal and Installation of Front Combination LampNKS003QY
Refer to LT- 7 5 , "Removal and Installation" .
PKIA6866E
PKIA6866E
Condition “AFS OFF IND”
AFS switch is OFF. ON
AFS switch is ON. OFF
SKIB4971E
Page 3643 of 4647
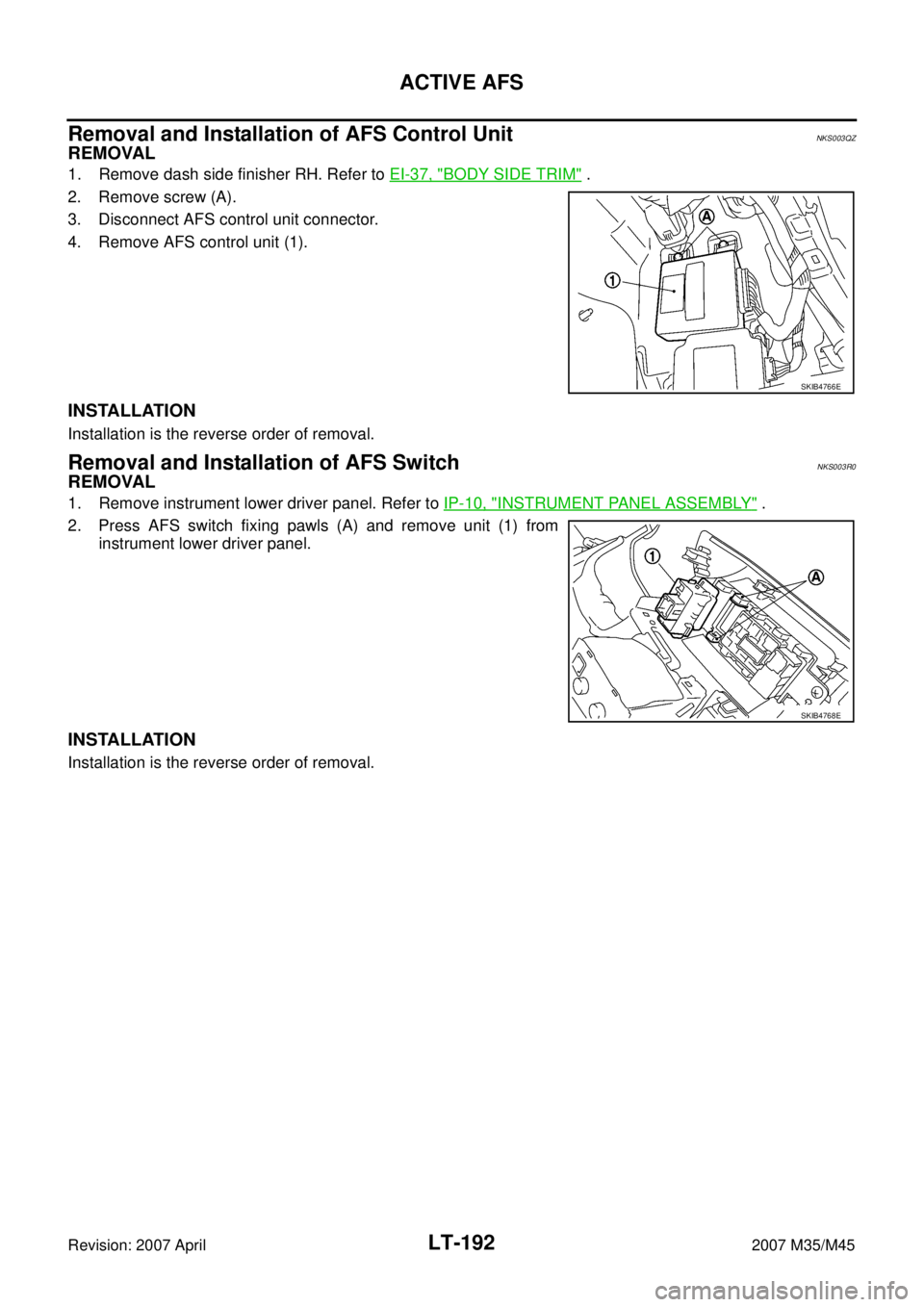
LT-192
ACTIVE AFS
Revision: 2007 April2007 M35/M45
Removal and Installation of AFS Control UnitNKS003QZ
REMOVAL
1. Remove dash side finisher RH. Refer to EI-37, "BODY SIDE TRIM" .
2. Remove screw (A).
3. Disconnect AFS control unit connector.
4. Remove AFS control unit (1).
INSTALLATION
Installation is the reverse order of removal.
Removal and Installation of AFS SwitchNKS003R0
REMOVAL
1. Remove instrument lower driver panel. Refer to IP-10, "INSTRUMENT PANEL ASSEMBLY" .
2. Press AFS switch fixing pawls (A) and remove unit (1) from
instrument lower driver panel.
INSTALLATION
Installation is the reverse order of removal.
SKIB4766E
SKIB4768E
Page 3645 of 4647
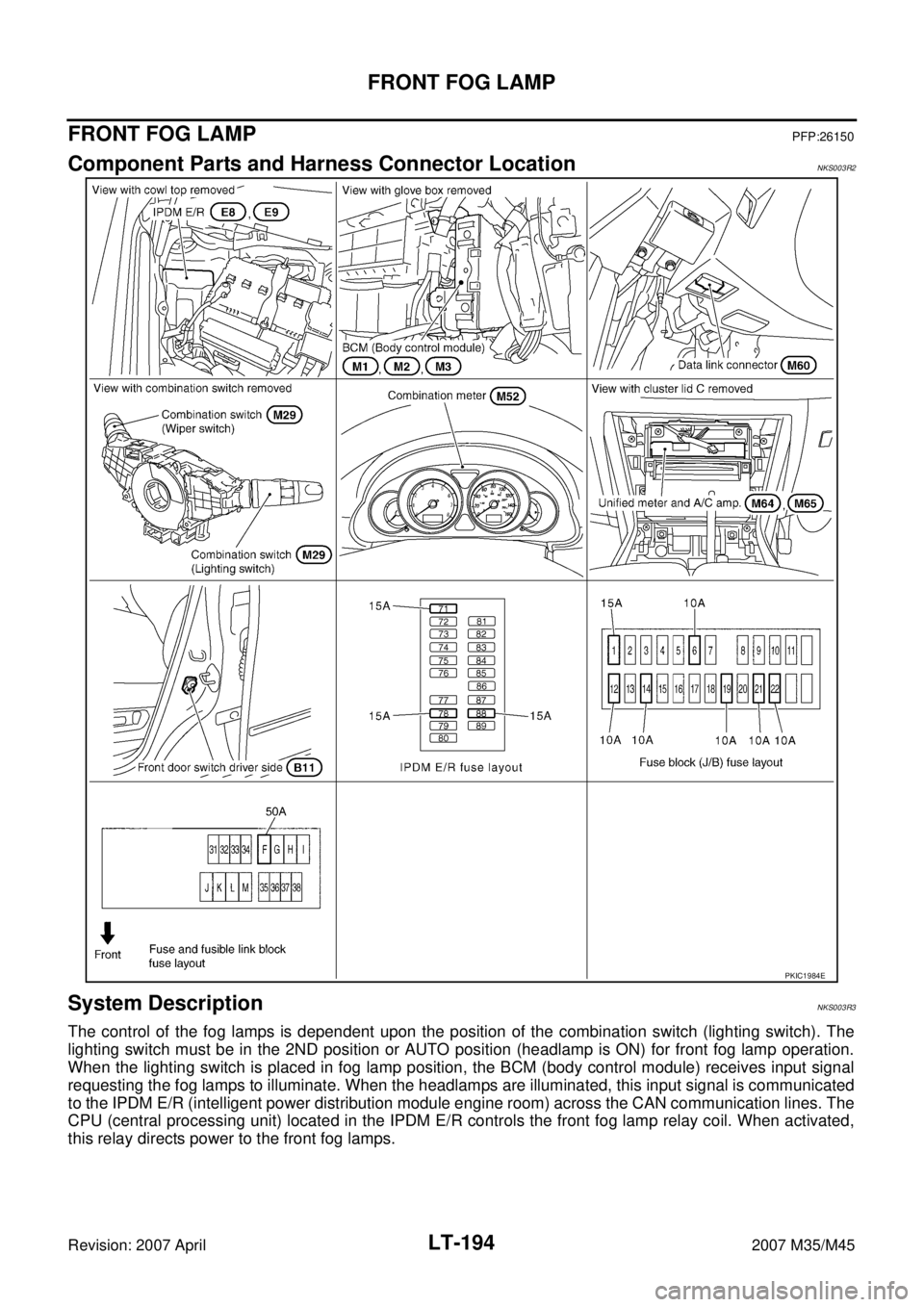
LT-194
FRONT FOG LAMP
Revision: 2007 April2007 M35/M45
FRONT FOG LAMPPFP:26150
Component Parts and Harness Connector LocationNKS003R2
System DescriptionNKS003R3
The control of the fog lamps is dependent upon the position of the combination switch (lighting switch). The
lighting switch must be in the 2ND position or AUTO position (headlamp is ON) for front fog lamp operation.
When the lighting switch is placed in fog lamp position, the BCM (body control module) receives input signal
requesting the fog lamps to illuminate. When the headlamps are illuminated, this input signal is communicated
to the IPDM E/R (intelligent power distribution module engine room) across the CAN communication lines. The
CPU (central processing unit) located in the IPDM E/R controls the front fog lamp relay coil. When activated,
this relay directs power to the front fog lamps.
PKIC1984E
Page 3647 of 4647
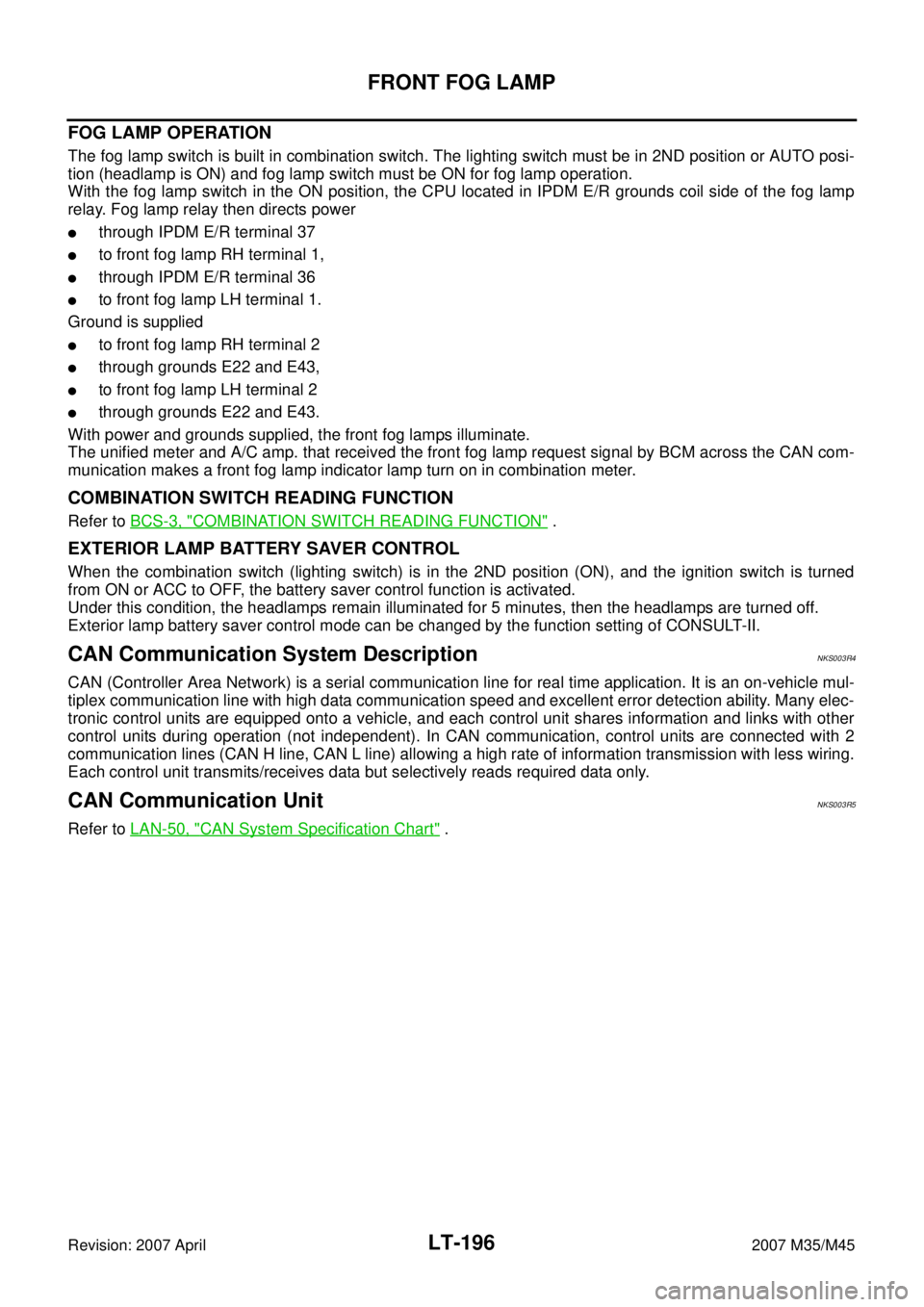
LT-196
FRONT FOG LAMP
Revision: 2007 April2007 M35/M45
FOG LAMP OPERATION
The fog lamp switch is built in combination switch. The lighting switch must be in 2ND position or AUTO posi-
tion (headlamp is ON) and fog lamp switch must be ON for fog lamp operation.
With the fog lamp switch in the ON position, the CPU located in IPDM E/R grounds coil side of the fog lamp
relay. Fog lamp relay then directs power
through IPDM E/R terminal 37
to front fog lamp RH terminal 1,
through IPDM E/R terminal 36
to front fog lamp LH terminal 1.
Ground is supplied
to front fog lamp RH terminal 2
through grounds E22 and E43,
to front fog lamp LH terminal 2
through grounds E22 and E43.
With power and grounds supplied, the front fog lamps illuminate.
The unified meter and A/C amp. that received the front fog lamp request signal by BCM across the CAN com-
munication makes a front fog lamp indicator lamp turn on in combination meter.
COMBINATION SWITCH READING FUNCTION
Refer to BCS-3, "COMBINATION SWITCH READING FUNCTION" .
EXTERIOR LAMP BATTERY SAVER CONTROL
When the combination switch (lighting switch) is in the 2ND position (ON), and the ignition switch is turned
from ON or ACC to OFF, the battery saver control function is activated.
Under this condition, the headlamps remain illuminated for 5 minutes, then the headlamps are turned off.
Exterior lamp battery saver control mode can be changed by the function setting of CONSULT-II.
CAN Communication System DescriptionNKS003R4
CAN (Controller Area Network) is a serial communication line for real time application. It is an on-vehicle mul-
tiplex communication line with high data communication speed and excellent error detection ability. Many elec-
tronic control units are equipped onto a vehicle, and each control unit shares information and links with other
control units during operation (not independent). In CAN communication, control units are connected with 2
communication lines (CAN H line, CAN L line) allowing a high rate of information transmission with less wiring.
Each control unit transmits/receives data but selectively reads required data only.
CAN Communication UnitNKS003R5
Refer to LAN-50, "CAN System Specification Chart" .