front suspension INFINITI M35 2007 Factory Service Manual
[x] Cancel search | Manufacturer: INFINITI, Model Year: 2007, Model line: M35, Model: INFINITI M35 2007Pages: 4647, PDF Size: 93.69 MB
Page 1 of 4647
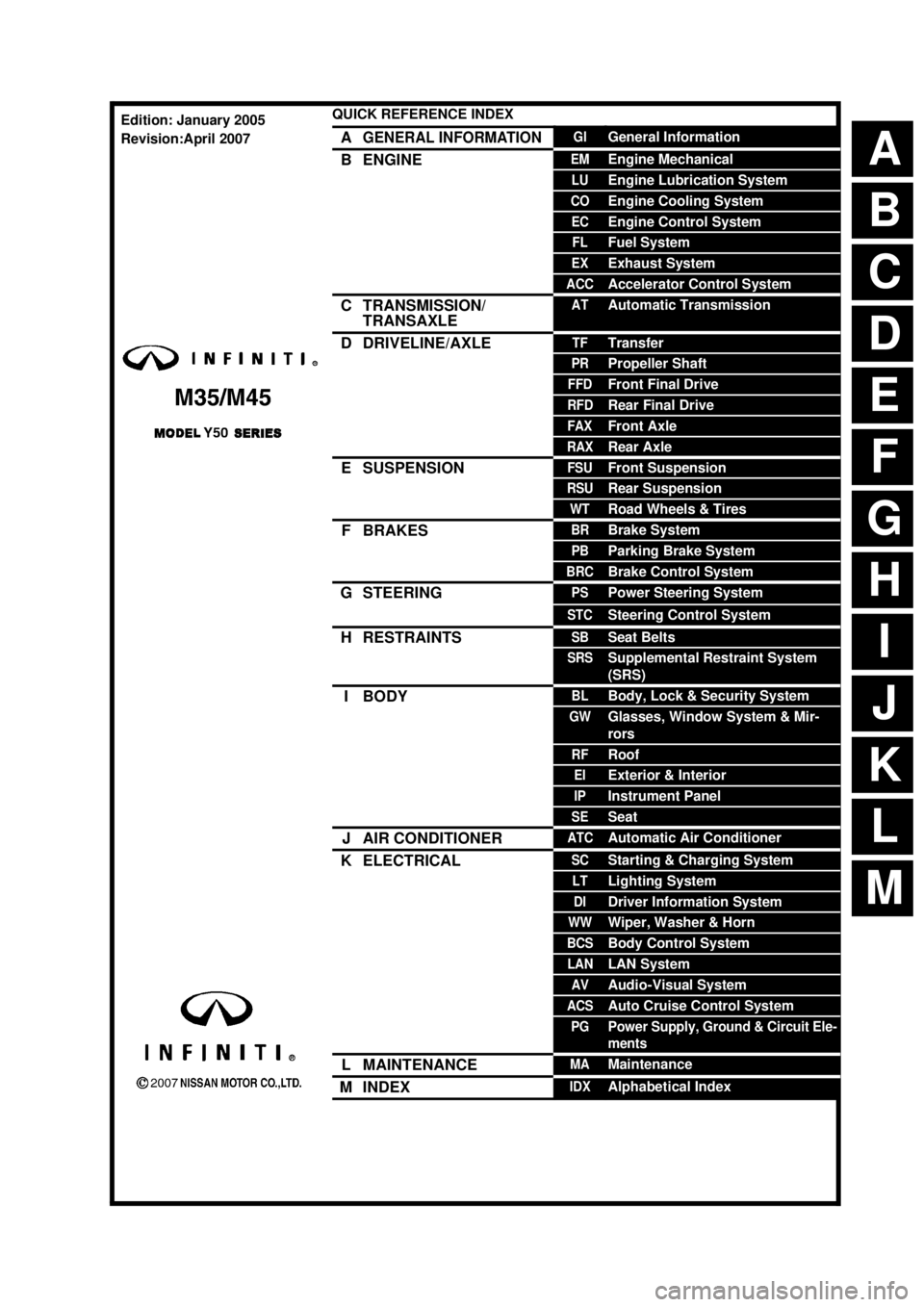
ABCDEFGHIJKMLQUICK REFERENCE INDEX AGENERAL INFORMATIONGIGeneral InformationBENGINEEMEngine MechanicalLUEngine Lubrication SystemCOEngine Cooling SystemECEngine Control SystemFLFuel SystemEXExhaust SystemACCAccelerator Control SystemCTRANSMISSION/
TRANSAXLEATAutomatic TransmissionDDRIVELINE/AXLETFTransferPRPropeller ShaftFFDFront Final DriveRFDRear Final DriveFAXFront AxleRAXRear AxleESUSPENSIONFSUFront SuspensionRSURear SuspensionWTRoad Wheels & TiresFBRAKESBRBrake SystemPBParking Brake SystemBRCBrake Control SystemGSTEERINGPSPower Steering SystemSTCSteering Control SystemHRESTRAINTSSBSeat BeltsSRSSupplemental Restraint System
(SRS)IBODYBLBody, Lock & Security SystemGWGlasses, Window System & Mir-
rorsRFRoofEIExterior & InteriorIPInstrument PanelSESeatJAIR CONDITIONERATCAutomatic Air ConditionerKELECTRICALSCStarting & Charging SystemLTLighting SystemDIDriver Information SystemWWWiper, Washer & HornBCSBody Control SystemLANLAN SystemAVAudio-Visual SystemACSAuto Cruise Control SystemPGPower Supply, Ground & Circuit Ele-
mentsLMAINTENANCEMAMaintenanceMINDEXIDXAlphabetical IndexEdition: January 2005
Revision:April 2007
Page 1216 of 4647
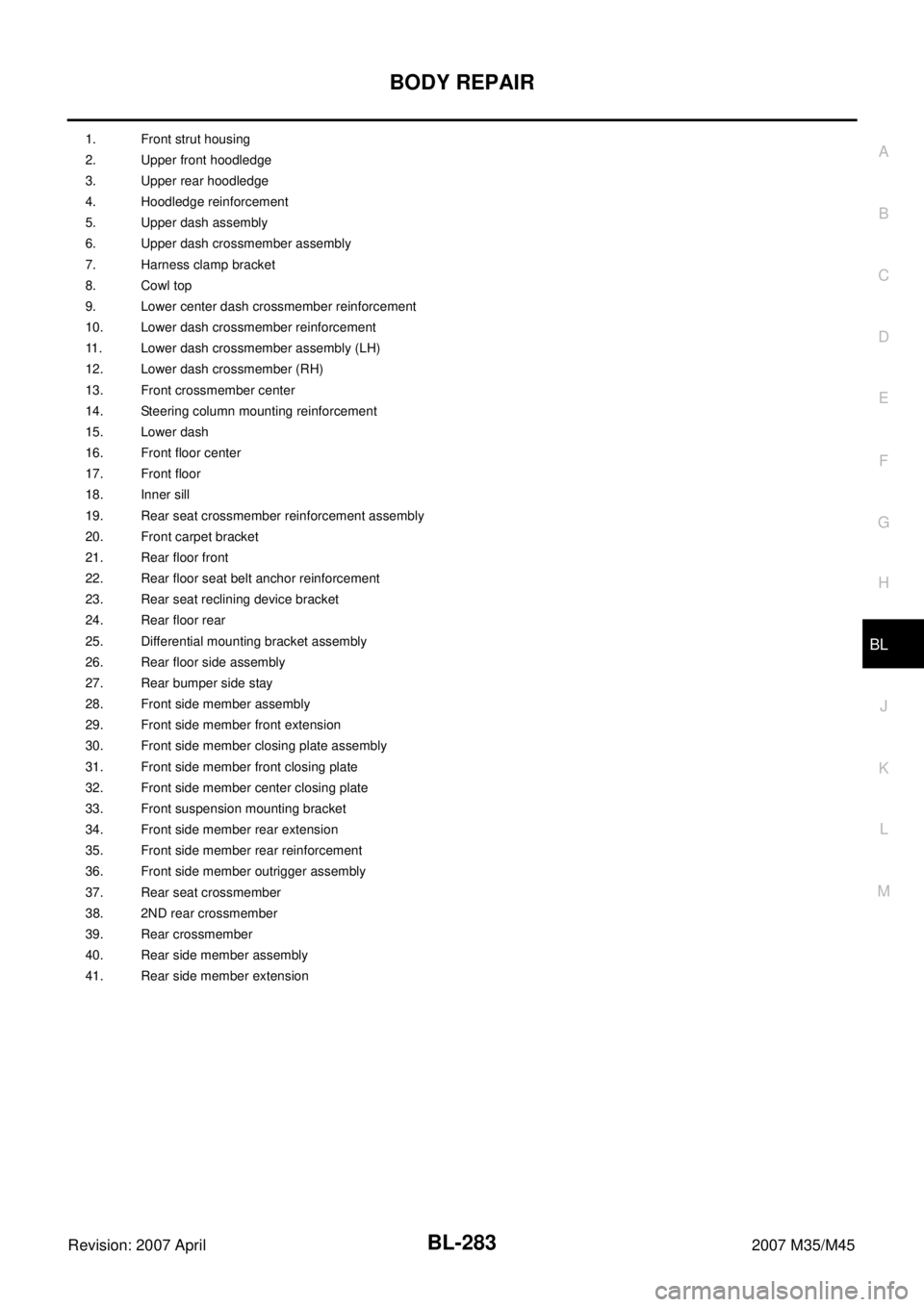
BODY REPAIR
BL-283
C
D
E
F
G
H
J
K
L
MA
B
BL
Revision: 2007 April2007 M35/M45
1. Front strut housing
2. Upper front hoodledge
3. Upper rear hoodledge
4. Hoodledge reinforcement
5. Upper dash assembly
6. Upper dash crossmember assembly
7. Harness clamp bracket
8. Cowl top
9. Lower center dash crossmember reinforcement
10. Lower dash crossmember reinforcement
11. Lower dash crossmember assembly (LH)
12. Lower dash crossmember (RH)
13. Front crossmember center
14. Steering column mounting reinforcement
15. Lower dash
16. Front floor center
17. Front floor
18. Inner sill
19. Rear seat crossmember reinforcement assembly
20. Front carpet bracket
21. Rear floor front
22. Rear floor seat belt anchor reinforcement
23. Rear seat reclining device bracket
24. Rear floor rear
25. Differential mounting bracket assembly
26. Rear floor side assembly
27. Rear bumper side stay
28. Front side member assembly
29. Front side member front extension
30. Front side member closing plate assembly
31. Front side member front closing plate
32. Front side member center closing plate
33. Front suspension mounting bracket
34. Front side member rear extension
35. Front side member rear reinforcement
36. Front side member outrigger assembly
37. Rear seat crossmember
38. 2ND rear crossmember
39. Rear crossmember
40. Rear side member assembly
41. Rear side member extension
Page 1307 of 4647
![INFINITI M35 2007 Factory Service Manual BRC-6
[VDC/TCS/ABS]
ON-VEHICLE SERVICE
Revision: 2007 April2007 M35/M45
ON-VEHICLE SERVICEPFP:00000
Adjustment of Steering Angle Sensor Neutral PositionNFS000Q4
In case of doing work that applies to t INFINITI M35 2007 Factory Service Manual BRC-6
[VDC/TCS/ABS]
ON-VEHICLE SERVICE
Revision: 2007 April2007 M35/M45
ON-VEHICLE SERVICEPFP:00000
Adjustment of Steering Angle Sensor Neutral PositionNFS000Q4
In case of doing work that applies to t](/img/42/57024/w960_57024-1306.png)
BRC-6
[VDC/TCS/ABS]
ON-VEHICLE SERVICE
Revision: 2007 April2007 M35/M45
ON-VEHICLE SERVICEPFP:00000
Adjustment of Steering Angle Sensor Neutral PositionNFS000Q4
In case of doing work that applies to the list below, make sure to adjust neutral position of steering angle sen-
sor before running vehicle.
×: Required
–: Not required
CAUTION:
To adjust neutral position of steering angle sensor, make sure to use CONSULT-II.
(Adjustment cannot be done without CONSULT-II.)
1. Stop vehicle with front wheels in straight-ahead position.
2. Perform “CONSULT-II Starting Procedure”. Refer to GI-38, "
CONSULT-II Start Procedure" .
3. Turn ignition switch ON and touch the CONSULT-II screen in the order of “ABS”, “WORK SUPPORT” and
“ST ANG SEN ADJUSTMENT”.
4. Touch “START”.
CAUTION:
Do not touch steering wheel while adjusting steering angle
sensor.
5. After approximately 10 seconds, touch “END”. (After approxi-
mately 60 seconds, it ends automatically.)
6. Turn ignition switch OFF, then turn it ON again.
CAUTION:
Be sure to perform above operation.
7. Run vehicle with front wheels in straight-ahead position, then
stop.
8. Select “DATA MONITOR”, “ECU INPUT SIGNALS”, and “STR ANGLE SIG” on CONSULT-II screen. Then
make sure “STR ANGLE SIG” is within 0±2.5°. If value is more than specification, repeat steps 1 to 7.
9. Erase memory of ABS actuator and electric unit (control unit) and ECM. ABS actuator and electric unit
(control unit): Refer to BRC-24, "
ERASE MEMORY" . ECM: Refer to EC-90, "TROUBLE DIAGNOSIS"
(VQ35DE), EC-792, "TROUBLE DIAGNOSIS" (VK45DE).
10. Turn ignition switch OFF.
Situation Adjustment of Steering Angle Sensor Neutral Position
Removing/Installing ABS actuator and electric unit (control unit)−
Replacing ABS actuator and electric unit (control unit)×
Removing/Installing steering angle sensor×
Removing/Installing steering components×
Removing/Installing suspension components×
Change tires to new ones–
Tire rotation–
Adjusting wheel alignment×
SFIA0793E
Page 3041 of 4647
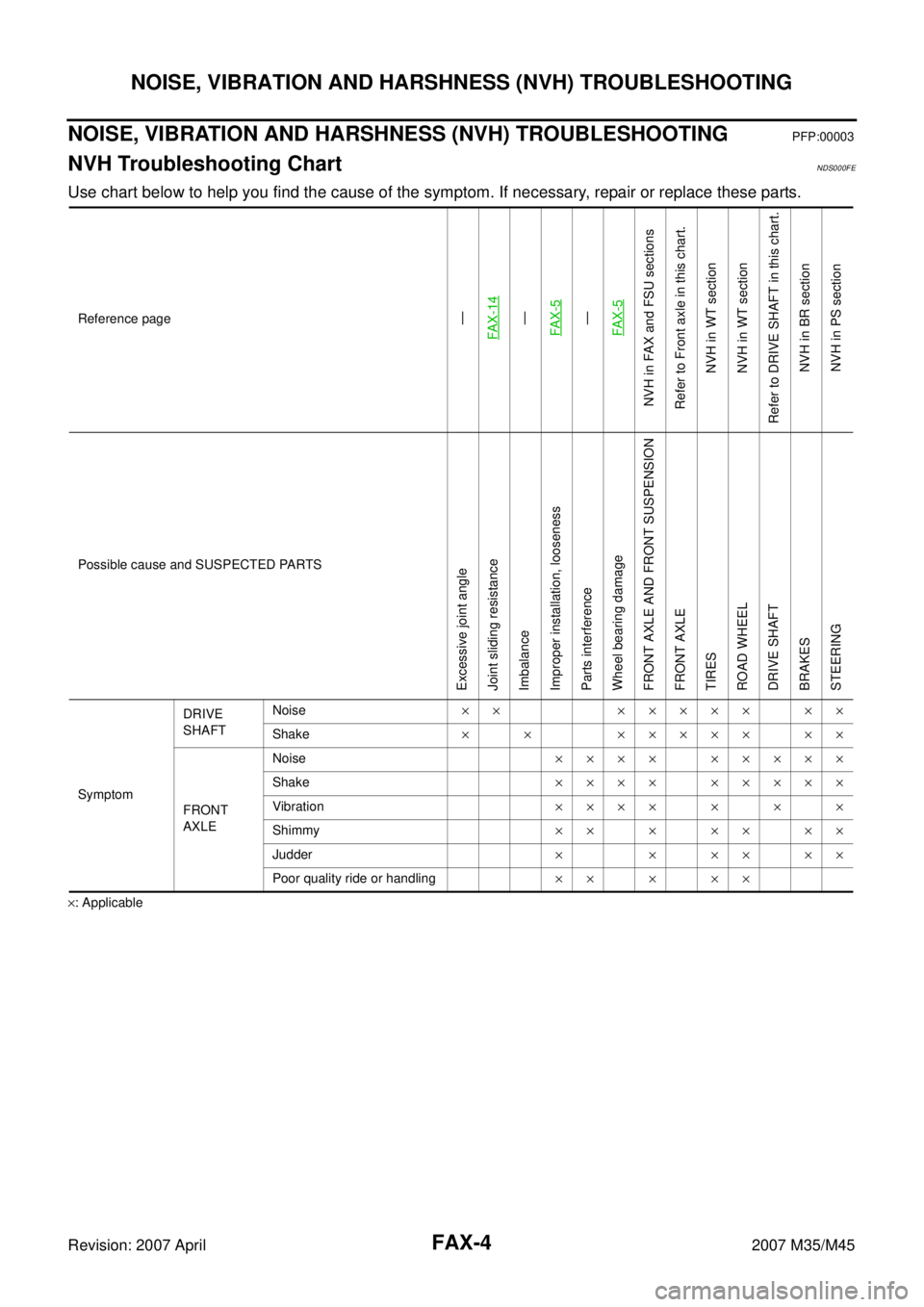
FAX-4
NOISE, VIBRATION AND HARSHNESS (NVH) TROUBLESHOOTING
Revision: 2007 April2007 M35/M45
NOISE, VIBRATION AND HARSHNESS (NVH) TROUBLESHOOTINGPFP:00003
NVH Troubleshooting ChartNDS000FE
Use chart below to help you find the cause of the symptom. If necessary, repair or replace these parts.
×: ApplicableReference page
—
FAX-14—
FAX-5—
FAX-5
NVH in FAX and FSU sections
Refer to Front axle in this chart.
NVH in WT section
NVH in WT section
Refer to DRIVE SHAFT in this chart.
NVH in BR section
NVH in PS section
Possible cause and SUSPECTED PARTS
Excessive joint angle
Joint sliding resistance
Imbalance
Improper installation, looseness
Parts interference
Wheel bearing damage
FRONT AXLE AND FRONT SUSPENSION
FRONT AXLE
TIRES
ROAD WHEEL
DRIVE SHAFT
BRAKES
STEERING
SymptomDRIVE
SHAFTNoise×× ××××× ××
Shake× × ××××× ××
FRONT
AXLENoise×××× ×××××
Shake×××× ×××××
Vibration×××× × × ×
Shimmy×××××××
Judder× × ×× ××
Poor quality ride or handling×××××
Page 3068 of 4647
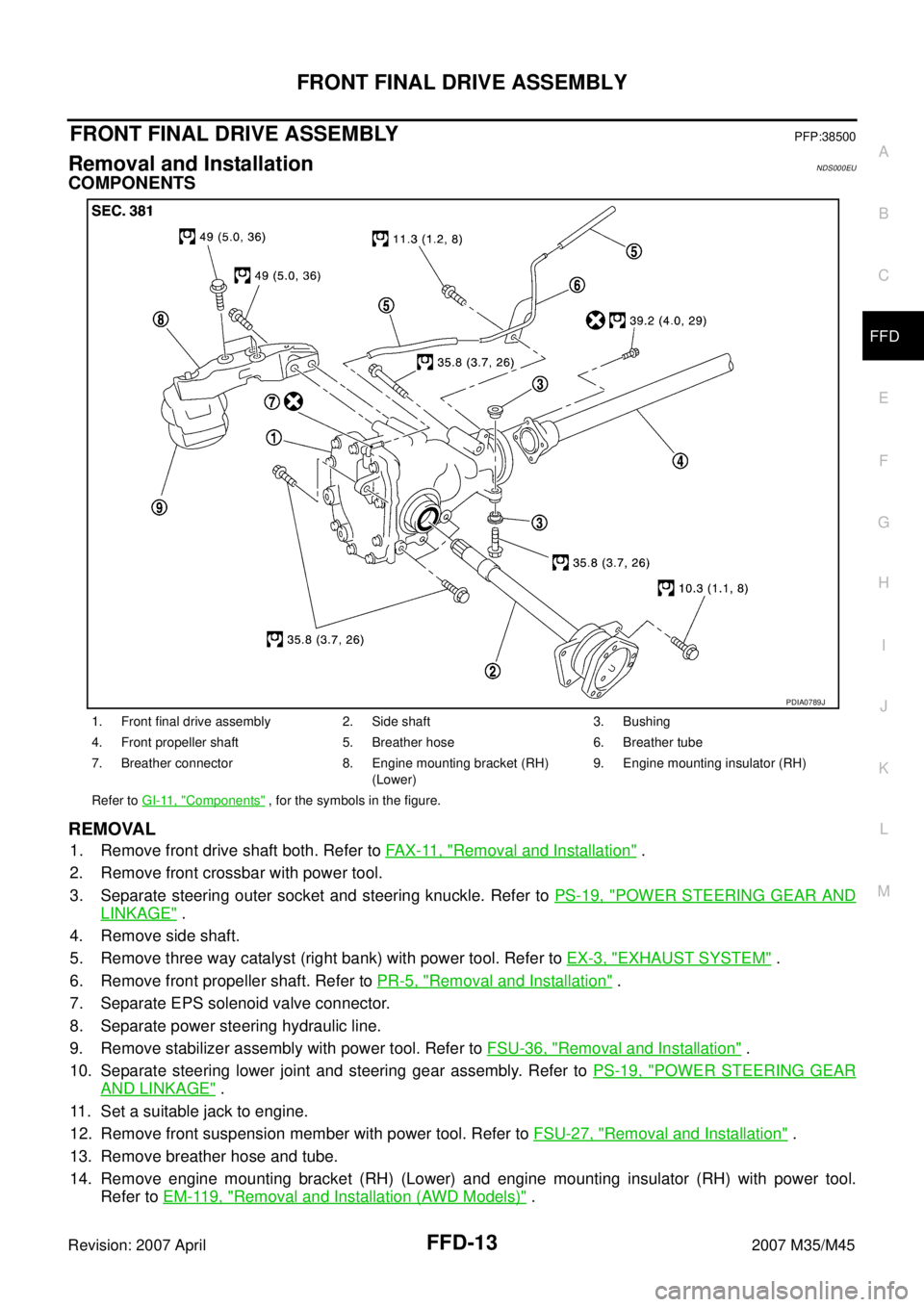
FRONT FINAL DRIVE ASSEMBLY
FFD-13
C
E
F
G
H
I
J
K
L
MA
B
FFD
Revision: 2007 April2007 M35/M45
FRONT FINAL DRIVE ASSEMBLYPFP:38500
Removal and InstallationNDS000EU
COMPONENTS
REMOVAL
1. Remove front drive shaft both. Refer to FA X - 11 , "Removal and Installation" .
2. Remove front crossbar with power tool.
3. Separate steering outer socket and steering knuckle. Refer to PS-19, "
POWER STEERING GEAR AND
LINKAGE" .
4. Remove side shaft.
5. Remove three way catalyst (right bank) with power tool. Refer to EX-3, "
EXHAUST SYSTEM" .
6. Remove front propeller shaft. Refer to PR-5, "
Removal and Installation" .
7. Separate EPS solenoid valve connector.
8. Separate power steering hydraulic line.
9. Remove stabilizer assembly with power tool. Refer to FSU-36, "
Removal and Installation" .
10. Separate steering lower joint and steering gear assembly. Refer to PS-19, "
POWER STEERING GEAR
AND LINKAGE" .
11. Set a suitable jack to engine.
12. Remove front suspension member with power tool. Refer to FSU-27, "
Removal and Installation" .
13. Remove breather hose and tube.
14. Remove engine mounting bracket (RH) (Lower) and engine mounting insulator (RH) with power tool.
Refer to EM-119, "
Removal and Installation (AWD Models)" .
1. Front final drive assembly 2. Side shaft 3. Bushing
4. Front propeller shaft 5. Breather hose 6. Breather tube
7. Breather connector 8. Engine mounting bracket (RH)
(Lower)9. Engine mounting insulator (RH)
Refer to GI-11, "
Components" , for the symbols in the figure.
PDIA0789J
Page 3101 of 4647
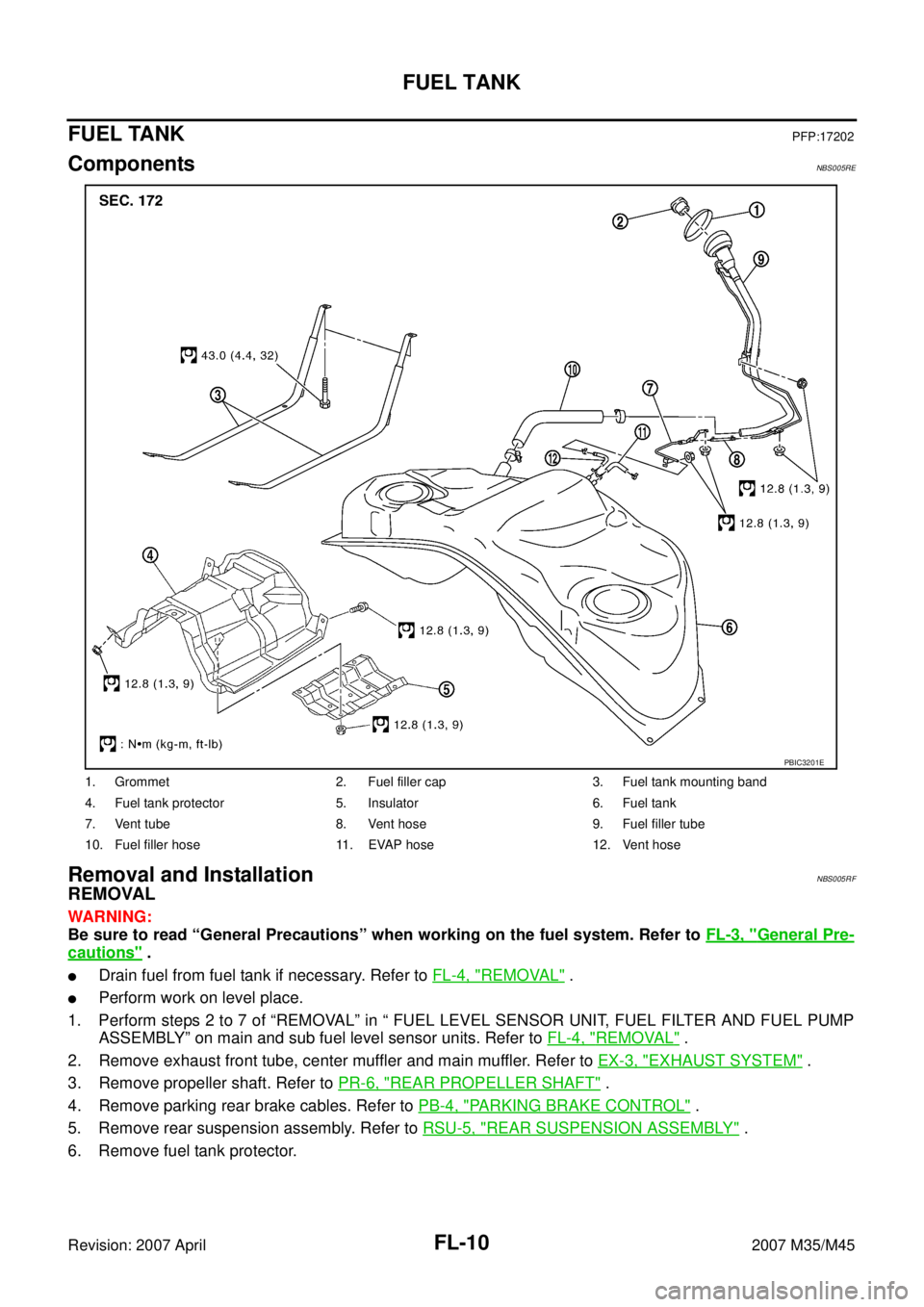
FL-10
FUEL TANK
Revision: 2007 April2007 M35/M45
FUEL TANKPFP:17202
ComponentsNBS005RE
Removal and InstallationNBS005RF
REMOVAL
WARNING:
Be sure to read “General Precautions” when working on the fuel system. Refer to FL-3, "
General Pre-
cautions" .
Drain fuel from fuel tank if necessary. Refer to FL-4, "REMOVAL" .
Perform work on level place.
1. Perform steps 2 to 7 of “REMOVAL” in “ FUEL LEVEL SENSOR UNIT, FUEL FILTER AND FUEL PUMP
ASSEMBLY” on main and sub fuel level sensor units. Refer to FL-4, "
REMOVAL" .
2. Remove exhaust front tube, center muffler and main muffler. Refer to EX-3, "
EXHAUST SYSTEM" .
3. Remove propeller shaft. Refer to PR-6, "
REAR PROPELLER SHAFT" .
4. Remove parking rear brake cables. Refer to PB-4, "
PARKING BRAKE CONTROL" .
5. Remove rear suspension assembly. Refer to RSU-5, "
REAR SUSPENSION ASSEMBLY" .
6. Remove fuel tank protector.
1. Grommet 2. Fuel filler cap 3. Fuel tank mounting band
4. Fuel tank protector 5. Insulator 6. Fuel tank
7. Vent tube 8. Vent hose 9. Fuel filler tube
10. Fuel filler hose 11. EVAP hose 12. Vent hose
PBIC3201E
Page 3106 of 4647
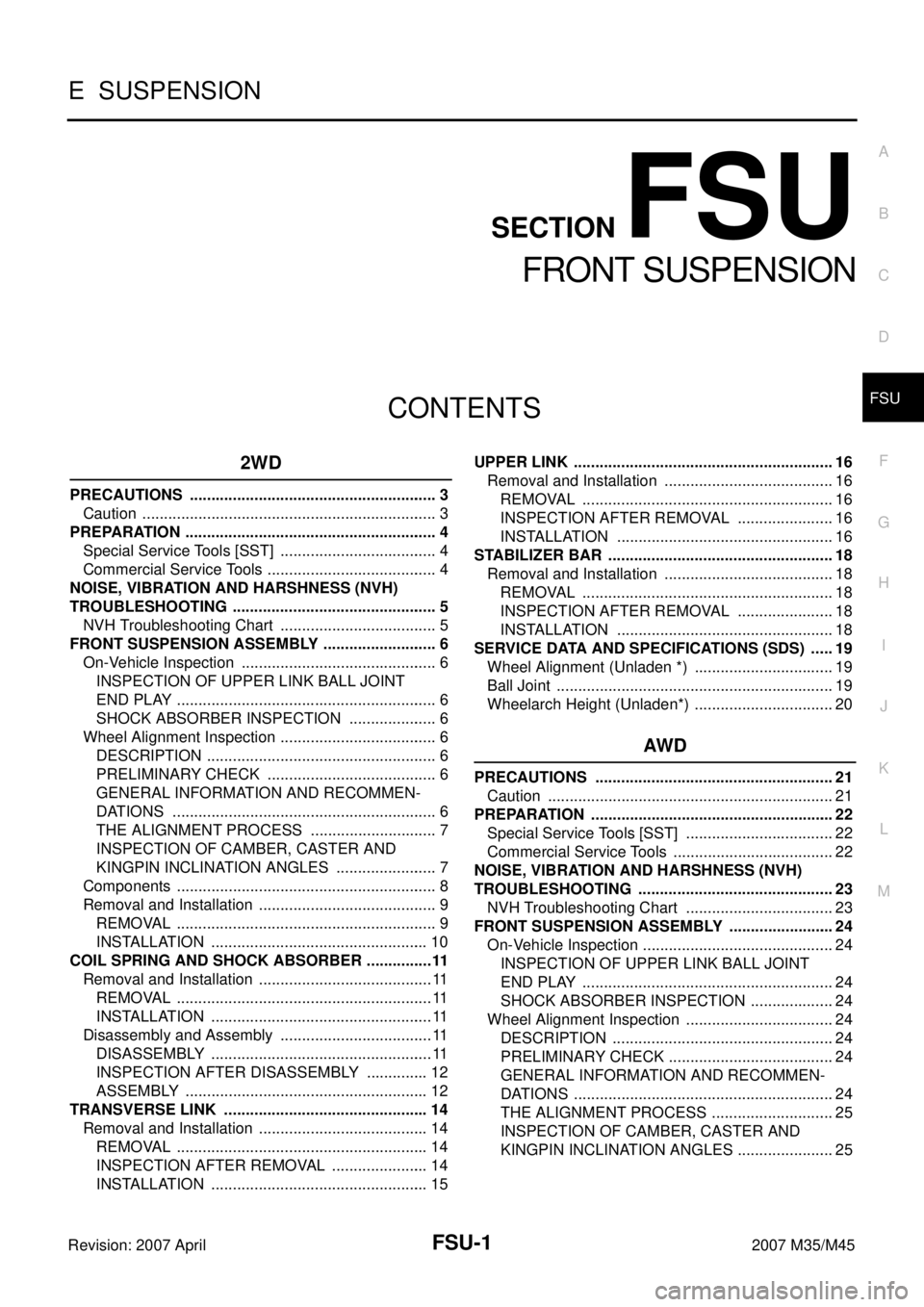
FSU-1
FRONT SUSPENSION
E SUSPENSION
CONTENTS
C
D
F
G
H
I
J
K
L
M
SECTION FSU
A
B
FSU
Revision: 2007 April2007 M35/M45
FRONT SUSPENSION
2WD
PRECAUTIONS .......................................................... 3
Caution ..................................................................... 3
PREPARATION ........................................................... 4
Special Service Tools [SST] ..................................... 4
Commercial Service Tools ........................................ 4
NOISE, VIBRATION AND HARSHNESS (NVH)
TROUBLESHOOTING ................................................ 5
NVH Troubleshooting Chart ..................................... 5
FRONT SUSPENSION ASSEMBLY ........................... 6
On-Vehicle Inspection .............................................. 6
INSPECTION OF UPPER LINK BALL JOINT
END PLAY ............................................................. 6
SHOCK ABSORBER INSPECTION ..................... 6
Wheel Alignment Inspection ..................................... 6
DESCRIPTION ...................................................... 6
PRELIMINARY CHECK ........................................ 6
GENERAL INFORMATION AND RECOMMEN-
DATIONS .............................................................. 6
THE ALIGNMENT PROCESS .............................. 7
INSPECTION OF CAMBER, CASTER AND
KINGPIN INCLINATION ANGLES ........................ 7
Components ............................................................. 8
Removal and Installation .......................................... 9
REMOVAL ............................................................. 9
INSTALLATION ................................................... 10
COIL SPRING AND SHOCK ABSORBER ................11
Removal and Installation ......................................... 11
REMOVAL ............................................................ 11
INSTALLATION .................................................... 11
Disassembly and Assembly .................................... 11
DISASSEMBLY .................................................... 11
INSPECTION AFTER DISASSEMBLY ............... 12
ASSEMBLY ......................................................... 12
TRANSVERSE LINK ................................................ 14
Removal and Installation ........................................ 14
REMOVAL ........................................................... 14
INSPECTION AFTER REMOVAL ....................... 14
INSTALLATION ................................................... 15UPPER LINK ............................................................. 16
Removal and Installation ........................................ 16
REMOVAL ........................................................... 16
INSPECTION AFTER REMOVAL ....................... 16
INSTALLATION ................................................... 16
STABILIZER BAR ..................................................... 18
Removal and Installation ........................................ 18
REMOVAL ........................................................... 18
INSPECTION AFTER REMOVAL ....................... 18
INSTALLATION ................................................... 18
SERVICE DATA AND SPECIFICATIONS (SDS) ...... 19
Wheel Alignment (Unladen *) ................................. 19
Ball Joint ................................................................. 19
Wheelarch Height (Unladen*) ................................. 20
AWD
PRECAUTIONS ........................................................ 21
Caution ................................................................... 21
PREPARATION ......................................................... 22
Special Service Tools [SST] ................................... 22
Commercial Service Tools ...................................... 22
NOISE, VIBRATION AND HARSHNESS (NVH)
TROUBLESHOOTING .............................................. 23
NVH Troubleshooting Chart ................................... 23
FRONT SUSPENSION ASSEMBLY ......................... 24
On-Vehicle Inspection ............................................. 24
INSPECTION OF UPPER LINK BALL JOINT
END PLAY ........................................................... 24
SHOCK ABSORBER INSPECTION .................... 24
Wheel Alignment Inspection ................................... 24
DESCRIPTION .................................................... 24
PRELIMINARY CHECK ....................................... 24
GENERAL INFORMATION AND RECOMMEN-
DATIONS ............................................................. 24
THE ALIGNMENT PROCESS ............................. 25
INSPECTION OF CAMBER, CASTER AND
KINGPIN INCLINATION ANGLES ....................... 25
Page 3109 of 4647
![INFINITI M35 2007 Factory Service Manual FSU-4
[2WD]
PREPARATION
Revision: 2007 April2007 M35/M45
PREPARATIONPFP:00002
Special Service Tools [SST]NES000I7
The actual shapes of Kent-Moore tools may differ from those of special service tools i INFINITI M35 2007 Factory Service Manual FSU-4
[2WD]
PREPARATION
Revision: 2007 April2007 M35/M45
PREPARATIONPFP:00002
Special Service Tools [SST]NES000I7
The actual shapes of Kent-Moore tools may differ from those of special service tools i](/img/42/57024/w960_57024-3108.png)
FSU-4
[2WD]
PREPARATION
Revision: 2007 April2007 M35/M45
PREPARATIONPFP:00002
Special Service Tools [SST]NES000I7
The actual shapes of Kent-Moore tools may differ from those of special service tools illustrated here.
Commercial Service ToolsNES000I8
Tool number
(Kent-Moore No.)
Tool nameDescription
KV991040S0
(—)
CCK gauge attachment
1. Plate
2. Guide bolt
3. Nut
4. Spring
5. Center plate
6. KV99104020 Adapter A
a: 72 mm (2.83 in) dia.
7. KV99104030 Adapter B
b: 65 mm (2.56 in) dia.
8. KV99104040 Adapter C
c: 57 mm (2.24 in) dia.
9. KV99104050 Adapter D
d: 53.4 mm (2.102 in) dia.Measuring wheel alignment
ST35652000
(—)
Strut attachmentDisassembling and assembling shock
absorber
ST3127S000
(See J-25765-A)
Preload Gauge
1. GG91030000
(J-25765-A)
Torque wrench
2. HT62940000
(—)
Socket adapter
3. HT62900000
(—)
Socket adapterMeasuring rotating torque of ball joint
S-NT498
ZZA0807D
NT124
Tool nameDescription
Power tool
Removing wheel nuts
Removing torque member fixing bolts
Removing undercover
Removing front suspension compo-
nents parts
Removing hub lock nut
Spring compressor Removing and installing coil springPBIC0190E
S-NT717
Page 3110 of 4647
![INFINITI M35 2007 Factory Service Manual NOISE, VIBRATION AND HARSHNESS (NVH) TROUBLESHOOTING
FSU-5
[2WD]
C
D
F
G
H
I
J
K
L
MA
B
FSU
Revision: 2007 April2007 M35/M45
NOISE, VIBRATION AND HARSHNESS (NVH) TROUBLESHOOTINGPFP:00003
NVH Troublesh INFINITI M35 2007 Factory Service Manual NOISE, VIBRATION AND HARSHNESS (NVH) TROUBLESHOOTING
FSU-5
[2WD]
C
D
F
G
H
I
J
K
L
MA
B
FSU
Revision: 2007 April2007 M35/M45
NOISE, VIBRATION AND HARSHNESS (NVH) TROUBLESHOOTINGPFP:00003
NVH Troublesh](/img/42/57024/w960_57024-3109.png)
NOISE, VIBRATION AND HARSHNESS (NVH) TROUBLESHOOTING
FSU-5
[2WD]
C
D
F
G
H
I
J
K
L
MA
B
FSU
Revision: 2007 April2007 M35/M45
NOISE, VIBRATION AND HARSHNESS (NVH) TROUBLESHOOTINGPFP:00003
NVH Troubleshooting ChartNES000I9
Use chart below to help you find the cause of the symptom. If necessary, repair or replace these parts.
×: ApplicableReference page
FSU-8FSU-12
—
—
—
FSU-8FSU-6FSU-18
NVH in PR section
NVH in FAX and FSU section
NVH in WT section
NVH in BR section
NVH in PS section
Possible cause and SUSPECTED PARTS
Improper installation, looseness
Strut deformation, damage or deflection
Bushing or mounting deterioration
Parts interference
Spring fatigue
Suspension looseness
Incorrect wheel alignment
Stabilizer bar fatigue
PROPELLER SHAFT
FRONT AXLE AND FRONT SUSPENSION
ROAD WHEEL
BRAKES
STEERING
Symptom FRONT SUSPENSIONNoise×××××× ×××××
Shake×××× × ×××××
Vibration××××× ×× ×
Shimmy×××× × ××××
Judder××× ××××
Poor quality ride or han-
dling××××× ×× ××
Page 3111 of 4647
![INFINITI M35 2007 Factory Service Manual FSU-6
[2WD]
FRONT SUSPENSION ASSEMBLY
Revision: 2007 April2007 M35/M45
FRONT SUSPENSION ASSEMBLYPFP:54010
On-Vehicle Inspection NES000IA
Make sure the mounting conditions (looseness, back lash) of eac INFINITI M35 2007 Factory Service Manual FSU-6
[2WD]
FRONT SUSPENSION ASSEMBLY
Revision: 2007 April2007 M35/M45
FRONT SUSPENSION ASSEMBLYPFP:54010
On-Vehicle Inspection NES000IA
Make sure the mounting conditions (looseness, back lash) of eac](/img/42/57024/w960_57024-3110.png)
FSU-6
[2WD]
FRONT SUSPENSION ASSEMBLY
Revision: 2007 April2007 M35/M45
FRONT SUSPENSION ASSEMBLYPFP:54010
On-Vehicle Inspection NES000IA
Make sure the mounting conditions (looseness, back lash) of each component and component conditions
(wear, damage) are normal.
INSPECTION OF UPPER LINK BALL JOINT END PLAY
1. Set front wheels in a straight-ahead position. Do not depress brake pedal.
2. Place an iron bar or similar tool between transverse link and steering knuckle.
3. Measure axial end play by prying it up and down.
CAUTION:
Be careful not to damage ball joint boot. Do not damage the installation position by applying
excessive force.
SHOCK ABSORBER INSPECTION
Check for oil leakage, damage and breakage of installation positions.
Wheel Alignment InspectionNES000IB
DESCRIPTION
Measure wheel alignment under unladen conditions.
NOTE:
“Unladen conditions” means that fuel, engine coolant, and lubricant are full. Spare tire, jack, hand tools and
mats are in designated positions.
PRELIMINARY CHECK
Check tires for improper air pressure and wear.
Check road wheels for runout. Refer to WT-6, "ROAD WHEEL" .
Check wheel bearing axial end play. Refer to FAX-5, "WHEEL BEARING INSPECTION" .
Check transverse link ball joint axial end play. Refer to FSU-14, "INSPECTION AFTER REMOVAL" .
Check shock absorber operation.
Check each mounting part of axle and suspension for looseness and deformation.
Check each of suspension member, shock absorber, upper link and transverse link for cracks, deforma-
tion and other damage.
Check vehicle height (posture).
GENERAL INFORMATION AND RECOMMENDATIONS
A four-wheel thrust alignment should be performed.
–This type of alignment is recommended for any NISSAN/INFINITI vehicle.
–The four-wheel “thrust” process helps ensure that the vehicle is properly aligned and the steering wheel is
centered.
–The alignment rack itself should be capable of accepting any NISSAN/INFINITI vehicle.
–The rack should be checked to ensure that it is level.
Make sure the machine is properly calibrated.
–Your alignment equipment should be regularly calibrated in order to give correct information.
–Check with the manufacturer of your specific equipment for their recommended Service/Calibration
Schedule.Axial end play : 0 mm (0 in)