torque INFINITI QX56 2004 Factory Service Manual
[x] Cancel search | Manufacturer: INFINITI, Model Year: 2004, Model line: QX56, Model: INFINITI QX56 2004Pages: 3371, PDF Size: 78.5 MB
Page 2834 of 3371
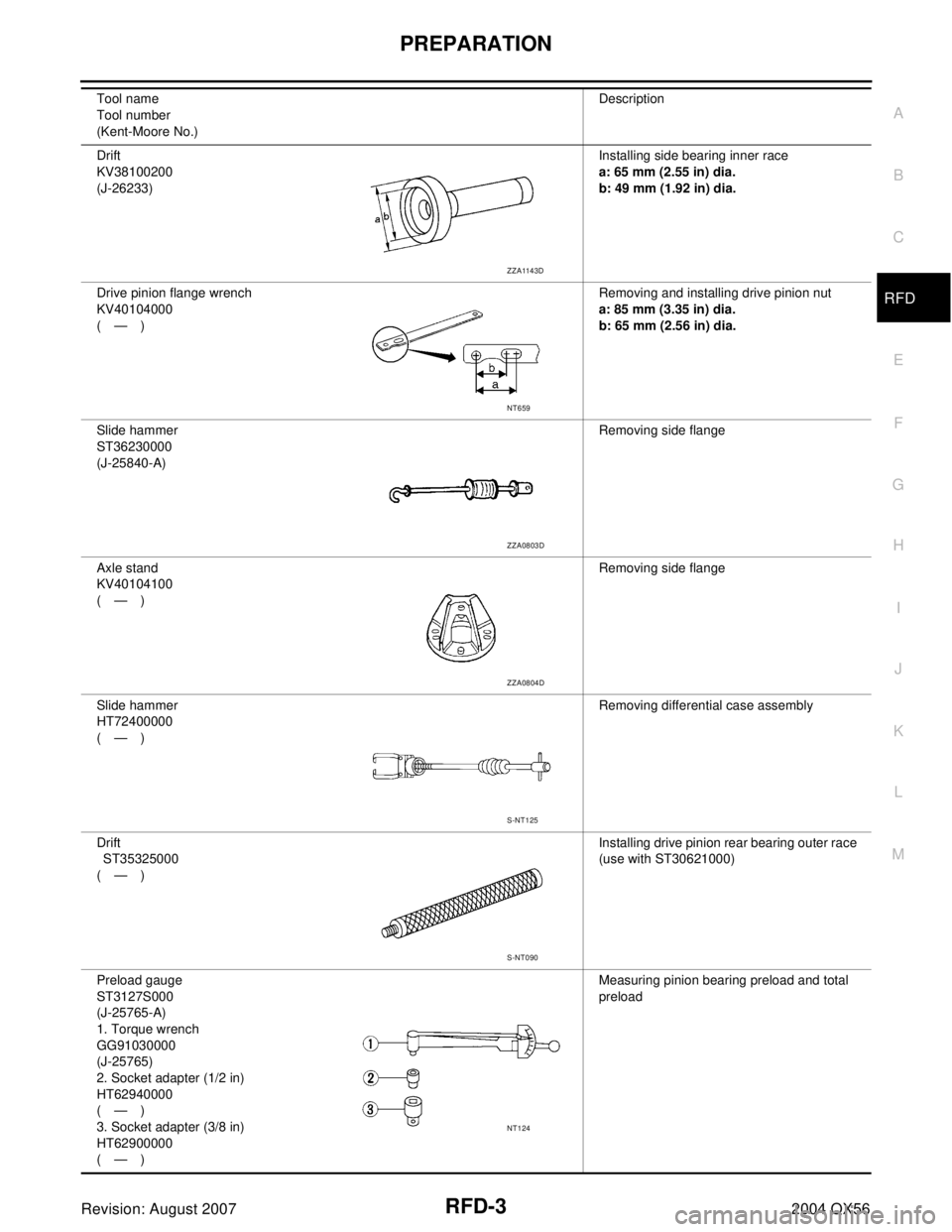
PREPARATION
RFD-3
C
E
F
G
H
I
J
K
L
MA
B
RFD
Revision: August 20072004 QX56
Drift
KV38100200
(J-26233)Installing side bearing inner race
a: 65 mm (2.55 in) dia.
b: 49 mm (1.92 in) dia.
Drive pinion flange wrench
KV40104000
(—)Removing and installing drive pinion nut
a: 85 mm (3.35 in) dia.
b: 65 mm (2.56 in) dia.
Slide hammer
ST36230000
(J-25840-A)Removing side flange
Axle stand
KV40104100
(—)Removing side flange
Slide hammer
HT72400000
(—)Removing differential case assembly
Drift
ST35325000
(—)Installing drive pinion rear bearing outer race
(use with ST30621000)
Preload gauge
ST3127S000
(J-25765-A)
1. Torque wrench
GG91030000
(J-25765)
2. Socket adapter (1/2 in)
HT62940000
(—)
3. Socket adapter (3/8 in)
HT62900000
(—)Measuring pinion bearing preload and total
preload Tool name
Tool number
(Kent-Moore No.)Description
ZZA1143D
NT659
ZZA0803D
ZZA0804D
S-NT125
S-NT090
NT124
Page 2838 of 3371
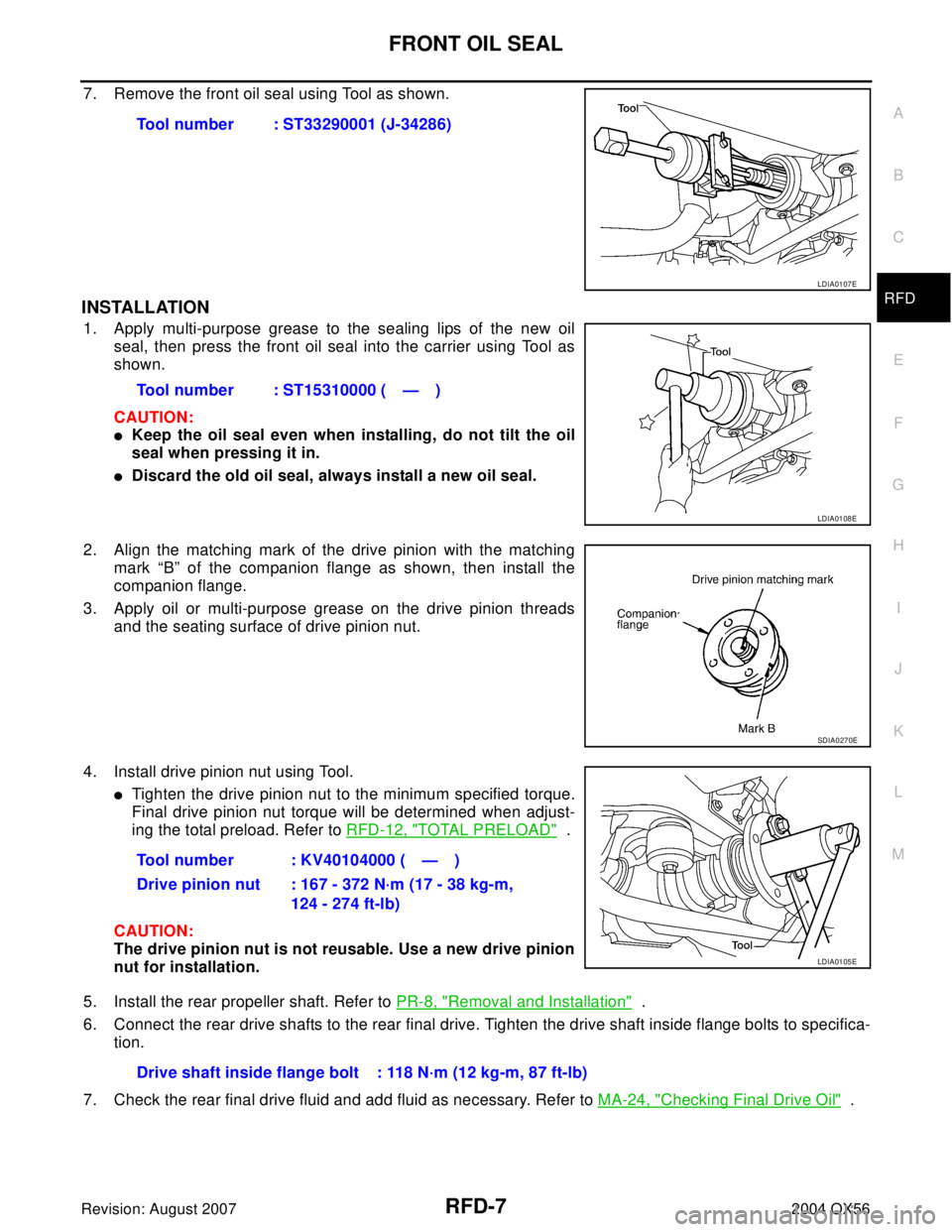
FRONT OIL SEAL
RFD-7
C
E
F
G
H
I
J
K
L
MA
B
RFD
Revision: August 20072004 QX56
7. Remove the front oil seal using Tool as shown.
INSTALLATION
1. Apply multi-purpose grease to the sealing lips of the new oil
seal, then press the front oil seal into the carrier using Tool as
shown.
CAUTION:
Keep the oil seal even when installing, do not tilt the oil
seal when pressing it in.
Discard the old oil seal, always install a new oil seal.
2. Align the matching mark of the drive pinion with the matching
mark “B” of the companion flange as shown, then install the
companion flange.
3. Apply oil or multi-purpose grease on the drive pinion threads
and the seating surface of drive pinion nut.
4. Install drive pinion nut using Tool.
Tighten the drive pinion nut to the minimum specified torque.
Final drive pinion nut torque will be determined when adjust-
ing the total preload. Refer to RFD-12, "
TOTAL PRELOAD" .
CAUTION:
The drive pinion nut is not reusable. Use a new drive pinion
nut for installation.
5. Install the rear propeller shaft. Refer to PR-8, "
Removal and Installation" .
6. Connect the rear drive shafts to the rear final drive. Tighten the drive shaft inside flange bolts to specifica-
tion.
7. Check the rear final drive fluid and add fluid as necessary. Refer to MA-24, "
Checking Final Drive Oil" . Tool number : ST33290001 (J-34286)
LDIA0107E
Tool number : ST15310000 ( — )
LDIA0108E
SDIA0270E
Tool number : KV40104000 ( — )
Drive pinion nut : 167 - 372 N·m (17 - 38 kg-m,
124 - 274 ft-lb)
LDIA0105E
Drive shaft inside flange bolt : 118 N·m (12 kg-m, 87 ft-lb)
Page 2843 of 3371
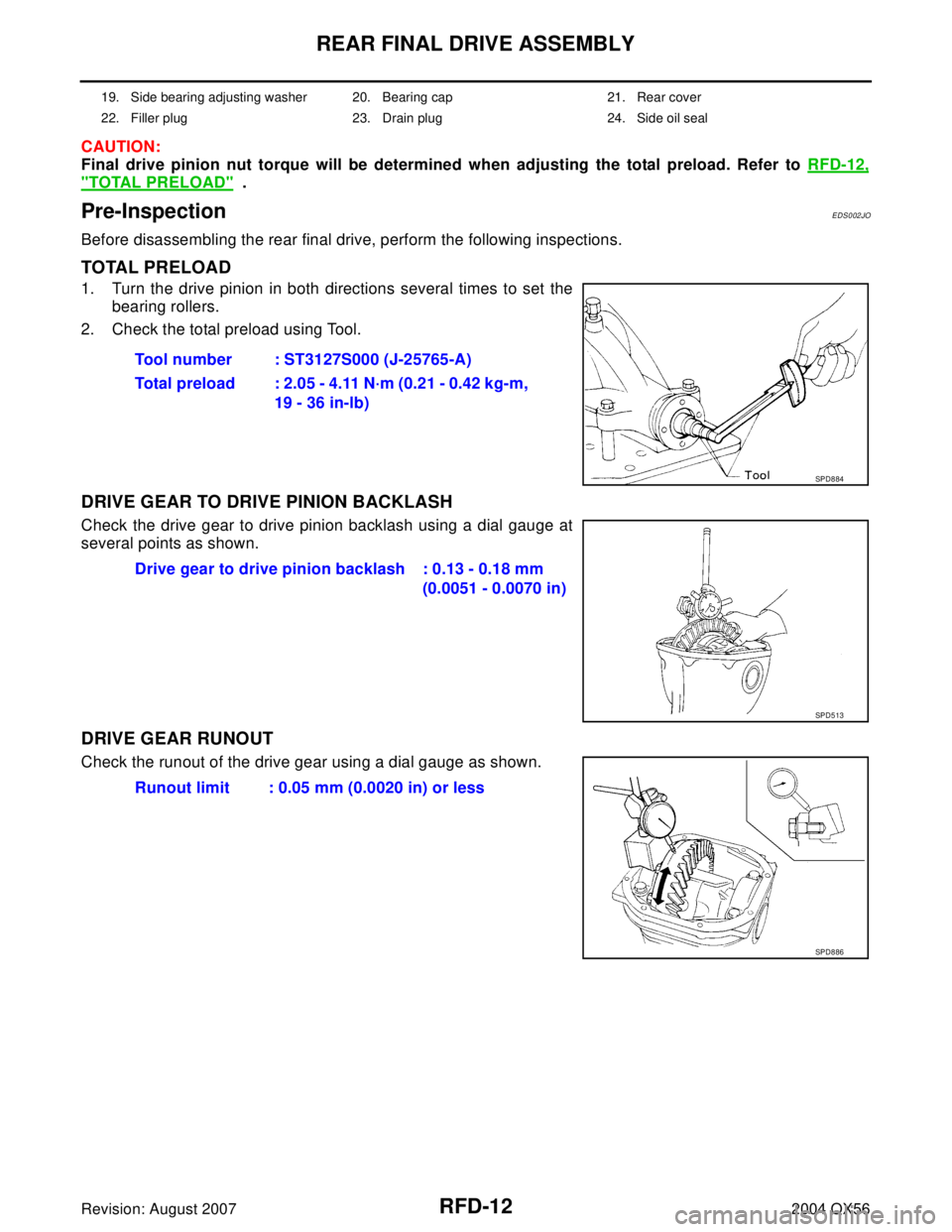
RFD-12
REAR FINAL DRIVE ASSEMBLY
Revision: August 20072004 QX56
CAUTION:
Final drive pinion nut torque will be determined when adjusting the total preload. Refer to RFD-12,
"TOTAL PRELOAD" .
Pre-InspectionEDS002JO
Before disassembling the rear final drive, perform the following inspections.
TOTAL PRELOAD
1. Turn the drive pinion in both directions several times to set the
bearing rollers.
2. Check the total preload using Tool.
DRIVE GEAR TO DRIVE PINION BACKLASH
Check the drive gear to drive pinion backlash using a dial gauge at
several points as shown.
DRIVE GEAR RUNOUT
Check the runout of the drive gear using a dial gauge as shown.
19. Side bearing adjusting washer 20. Bearing cap 21. Rear cover
22. Filler plug 23. Drain plug 24. Side oil seal
Tool number : ST3127S000 (J-25765-A)
Total preload : 2.05 - 4.11 N·m (0.21 - 0.42 kg-m,
19 - 36 in-lb)
SPD8 84
Drive gear to drive pinion backlash : 0.13 - 0.18 mm
(0.0051 - 0.0070 in)
SPD5 13
Runout limit : 0.05 mm (0.0020 in) or less
SPD8 86
Page 2844 of 3371
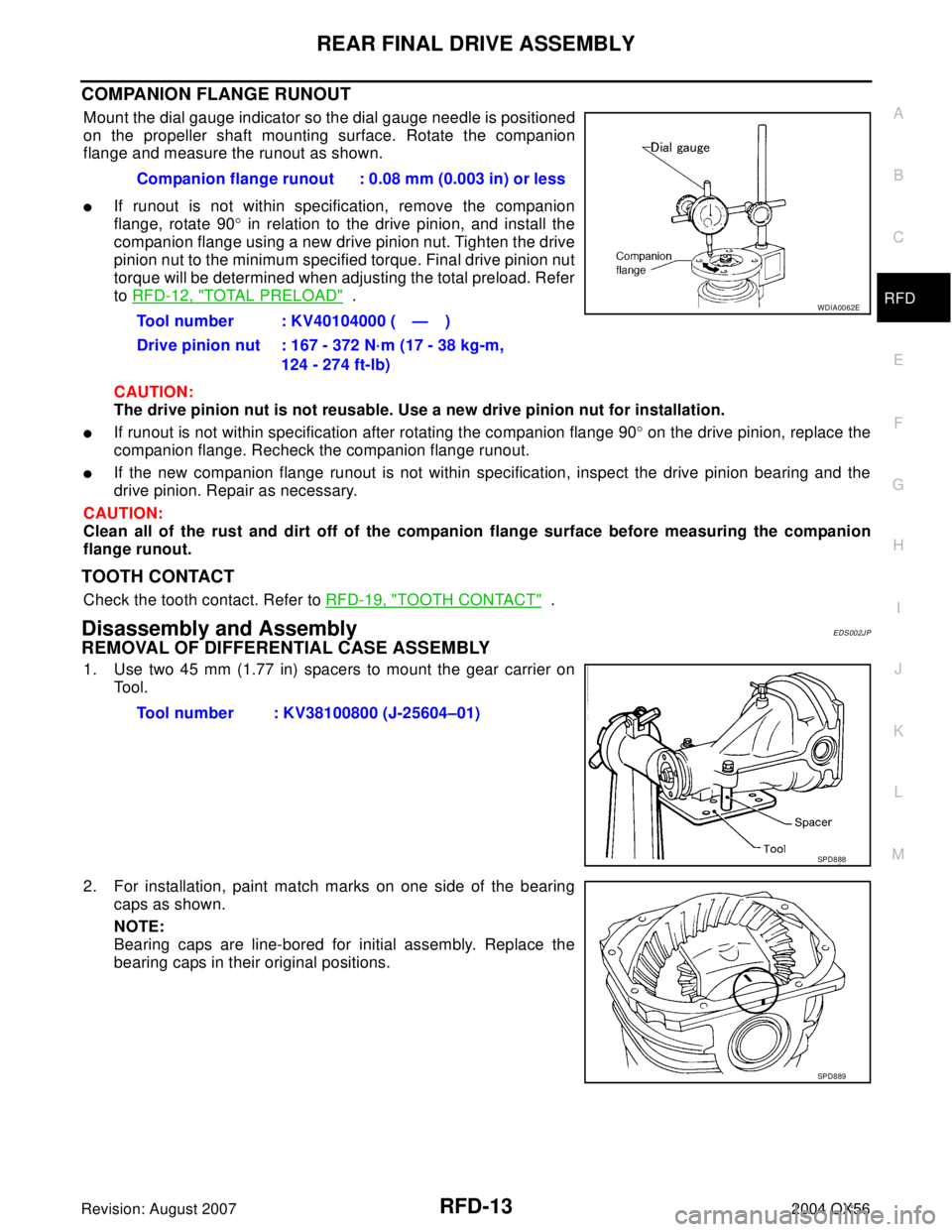
REAR FINAL DRIVE ASSEMBLY
RFD-13
C
E
F
G
H
I
J
K
L
MA
B
RFD
Revision: August 20072004 QX56
COMPANION FLANGE RUNOUT
Mount the dial gauge indicator so the dial gauge needle is positioned
on the propeller shaft mounting surface. Rotate the companion
flange and measure the runout as shown.
If runout is not within specification, remove the companion
flange, rotate 90° in relation to the drive pinion, and install the
companion flange using a new drive pinion nut. Tighten the drive
pinion nut to the minimum specified torque. Final drive pinion nut
torque will be determined when adjusting the total preload. Refer
to RFD-12, "
TOTAL PRELOAD" .
CAUTION:
The drive pinion nut is not reusable. Use a new drive pinion nut for installation.
If runout is not within specification after rotating the companion flange 90° on the drive pinion, replace the
companion flange. Recheck the companion flange runout.
If the new companion flange runout is not within specification, inspect the drive pinion bearing and the
drive pinion. Repair as necessary.
CAUTION:
Clean all of the rust and dirt off of the companion flange surface before measuring the companion
flange runout.
TOOTH CONTACT
Check the tooth contact. Refer to RFD-19, "TOOTH CONTACT" .
Disassembly and AssemblyEDS002JP
REMOVAL OF DIFFERENTIAL CASE ASSEMBLY
1. Use two 45 mm (1.77 in) spacers to mount the gear carrier on
Tool.
2. For installation, paint match marks on one side of the bearing
caps as shown.
NOTE:
Bearing caps are line-bored for initial assembly. Replace the
bearing caps in their original positions.Companion flange runout : 0.08 mm (0.003 in) or less
Tool number : KV40104000 ( — )
Drive pinion nut : 167 - 372 N·m (17 - 38 kg-m,
124 - 274 ft-lb)
WDIA0062E
Tool number : KV38100800 (J-25604–01)
SPD8 88
SPD8 89
Page 2906 of 3371
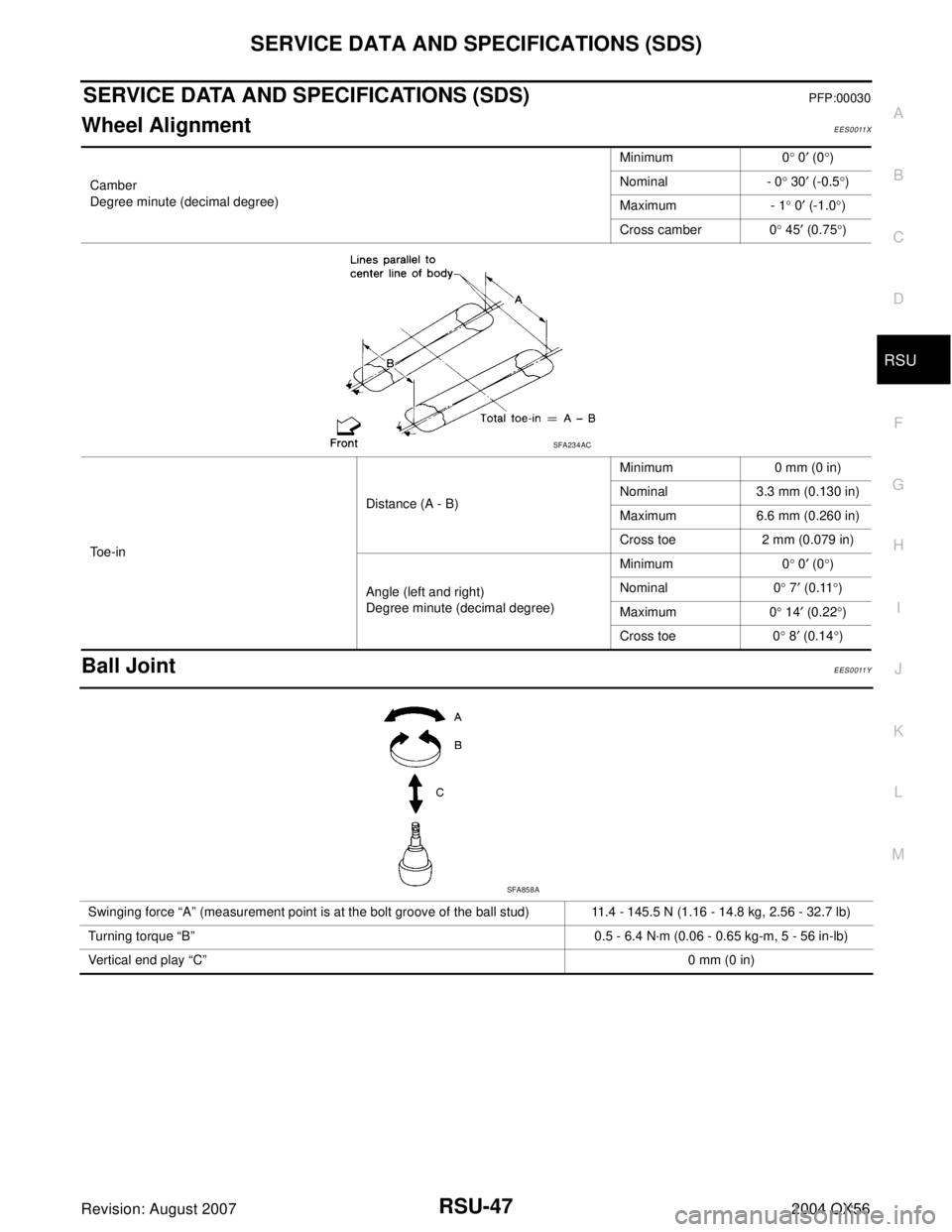
SERVICE DATA AND SPECIFICATIONS (SDS)
RSU-47
C
D
F
G
H
I
J
K
L
MA
B
RSU
Revision: August 20072004 QX56
SERVICE DATA AND SPECIFICATIONS (SDS)PFP:00030
Wheel AlignmentEES0011X
Ball JointEES0011Y
Camber
Degree minute (decimal degree)Minimum 0° 0′ (0°)
Nominal - 0° 30′ (-0.5°)
Maximum - 1° 0′ (-1.0°)
Cross camber 0° 45′ (0.75°)
To e - i nDistance (A - B)Minimum 0 mm (0 in)
Nominal 3.3 mm (0.130 in)
Maximum 6.6 mm (0.260 in)
Cross toe 2 mm (0.079 in)
Angle (left and right)
Degree minute (decimal degree)Minimum 0° 0′ (0°)
Nominal 0° 7′ (0.11°)
Maximum 0° 14′ (0.22°)
Cross toe 0° 8′ (0.14°)
SFA234AC
Swinging force “A” (measurement point is at the bolt groove of the ball stud) 11.4 - 145.5 N (1.16 - 14.8 kg, 2.56 - 32.7 lb)
Turning torque “B” 0.5 - 6.4 N·m (0.06 - 0.65 kg-m, 5 - 56 in-lb)
Vertical end play “C”0 mm (0 in)
SFA858A
Page 2952 of 3371
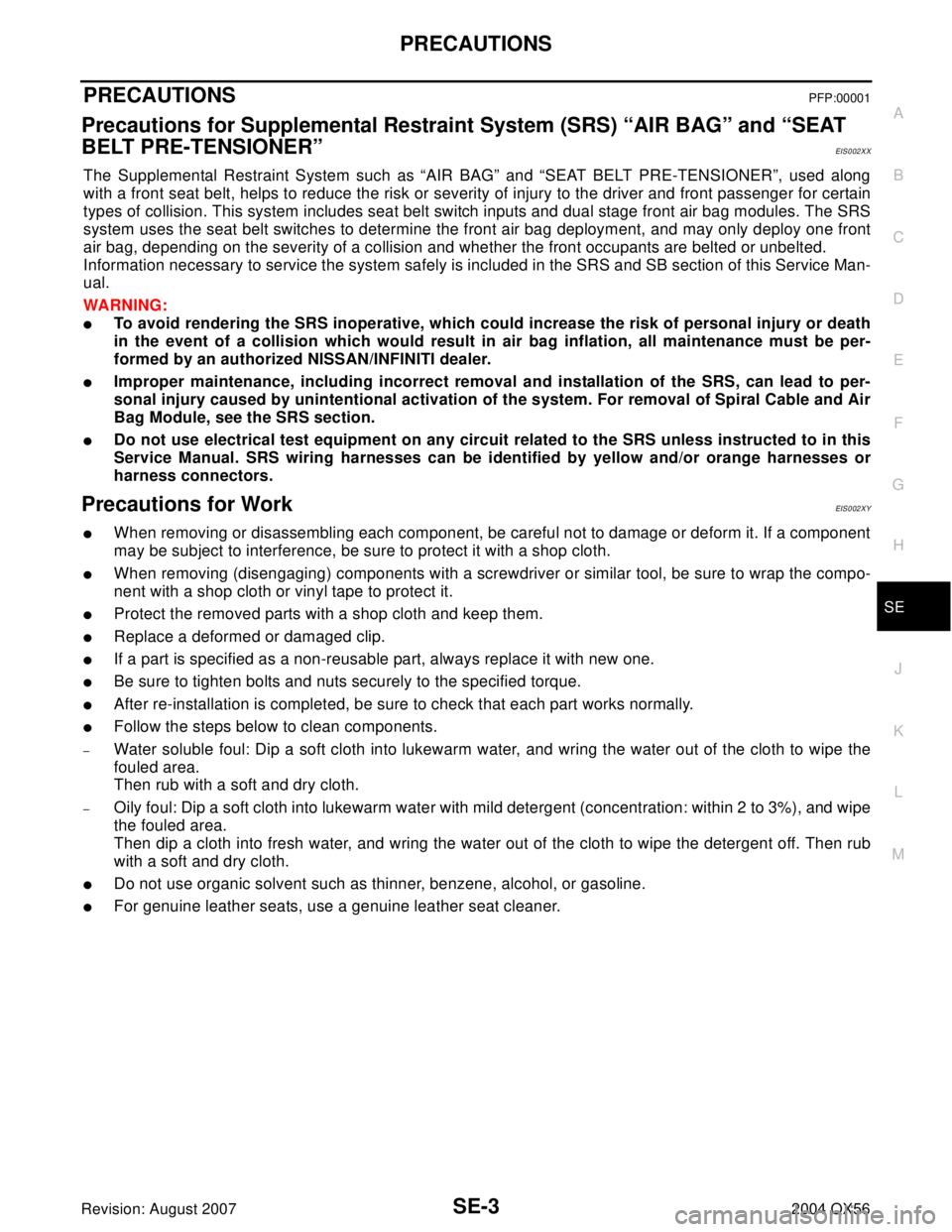
PRECAUTIONS
SE-3
C
D
E
F
G
H
J
K
L
MA
B
SE
Revision: August 20072004 QX56
PRECAUTIONSPFP:00001
Precautions for Supplemental Restraint System (SRS) “AIR BAG” and “SEAT
BELT PRE-TENSIONER”
EIS002XX
The Supplemental Restraint System such as “AIR BAG” and “SEAT BELT PRE-TENSIONER”, used along
with a front seat belt, helps to reduce the risk or severity of injury to the driver and front passenger for certain
types of collision. This system includes seat belt switch inputs and dual stage front air bag modules. The SRS
system uses the seat belt switches to determine the front air bag deployment, and may only deploy one front
air bag, depending on the severity of a collision and whether the front occupants are belted or unbelted.
Information necessary to service the system safely is included in the SRS and SB section of this Service Man-
ual.
WA RN ING:
To avoid rendering the SRS inoperative, which could increase the risk of personal injury or death
in the event of a collision which would result in air bag inflation, all maintenance must be per-
formed by an authorized NISSAN/INFINITI dealer.
Improper maintenance, including incorrect removal and installation of the SRS, can lead to per-
sonal injury caused by unintentional activation of the system. For removal of Spiral Cable and Air
Bag Module, see the SRS section.
Do not use electrical test equipment on any circuit related to the SRS unless instructed to in this
Service Manual. SRS wiring harnesses can be identified by yellow and/or orange harnesses or
harness connectors.
Precautions for WorkEIS002XY
When removing or disassembling each component, be careful not to damage or deform it. If a component
may be subject to interference, be sure to protect it with a shop cloth.
When removing (disengaging) components with a screwdriver or similar tool, be sure to wrap the compo-
nent with a shop cloth or vinyl tape to protect it.
Protect the removed parts with a shop cloth and keep them.
Replace a deformed or damaged clip.
If a part is specified as a non-reusable part, always replace it with new one.
Be sure to tighten bolts and nuts securely to the specified torque.
After re-installation is completed, be sure to check that each part works normally.
Follow the steps below to clean components.
–Water soluble foul: Dip a soft cloth into lukewarm water, and wring the water out of the cloth to wipe the
fouled area.
Then rub with a soft and dry cloth.
–Oily foul: Dip a soft cloth into lukewarm water with mild detergent (concentration: within 2 to 3%), and wipe
the fouled area.
Then dip a cloth into fresh water, and wring the water out of the cloth to wipe the detergent off. Then rub
with a soft and dry cloth.
Do not use organic solvent such as thinner, benzene, alcohol, or gasoline.
For genuine leather seats, use a genuine leather seat cleaner.
Page 3134 of 3371

PRECAUTIONS
TF-9
C
E
F
G
H
I
J
K
L
MA
B
TF
Revision: August 20072004 QX56
Service NoticeEDS0017L
1. Before proceeding with disassembly, thoroughly clean the outside of the all-mode 4WD transfer. It is
important to prevent the internal parts from becoming contaminated by dirt or other foreign matter.
2. Disassembly should be done in a clean work area.
3. Use lint-free cloth or towels for wiping parts clean. Common shop rags can leave fibers that could interfere
with the operation of the all-mode 4WD transfer.
4. Place disassembled parts in order for easier and proper assembly.
5. All parts should be carefully cleaned with a general purpose, non-flammable solvent before inspection or
reassembly.
6. Gaskets, seals and O-rings should be replaced any time the all-mode 4WD transfer is disassembled.
7. It is very important to perform functional tests whenever they are indicated.
8. The valve body contains precision parts and requires extreme care when parts are removed and serviced.
Place removed parts in a parts rack in order to replace them in correct positions and sequences. Care will
also prevent springs and small parts from becoming scattered or lost.
9. Properly installed valves, sleeves, plugs, etc. will slide along bores in valve body under their own weight.
10. Before assembly, apply a coat of recommended ATF to all parts. Apply petroleum jelly to protect O-rings
and seals, and to hold bearings and washers in place during assembly. Do not use grease.
11. Extreme care should be taken to avoid damage to O-rings, seals and gaskets when assembling.
12. After overhaul, refill the transfer with new ATF.
13. When the all-mode 4WD transfer drain plug is removed, only some of the fluid is drained. Old all-mode
4WD transfer fluid will remain in torque converter and ATF cooling system. Always follow the proper pro-
cedure. Refer to MA-24, "
Changing Transfer Fluid" .
Wiring Diagrams and Trouble DiagnosisEDS001CE
When you read wiring diagrams, refer to the following:
GI-15, "How to Read Wiring Diagrams" .
PG-4, "POWER SUPPLY ROUTING CIRCUIT" for power distribution circuit.
When you perform trouble diagnosis, refer to the following:
GI-11, "HOW TO FOLLOW TEST GROUPS IN TROUBLE DIAGNOSES".
GI-27, "How to Perform Efficient Diagnosis for an Electrical Incident".
Page 3140 of 3371
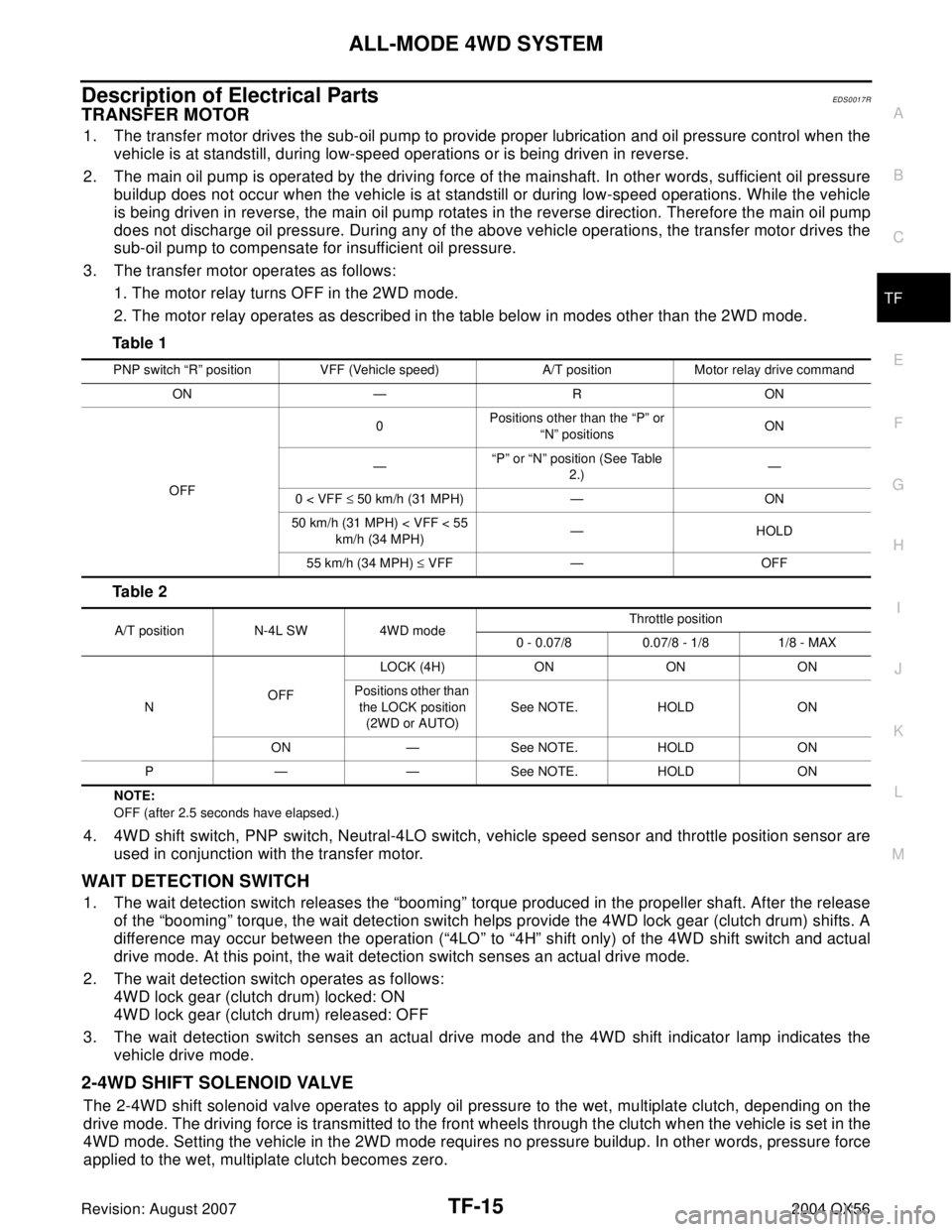
ALL-MODE 4WD SYSTEM
TF-15
C
E
F
G
H
I
J
K
L
MA
B
TF
Revision: August 20072004 QX56
Description of Electrical PartsEDS0017R
TRANSFER MOTOR
1. The transfer motor drives the sub-oil pump to provide proper lubrication and oil pressure control when the
vehicle is at standstill, during low-speed operations or is being driven in reverse.
2. The main oil pump is operated by the driving force of the mainshaft. In other words, sufficient oil pressure
buildup does not occur when the vehicle is at standstill or during low-speed operations. While the vehicle
is being driven in reverse, the main oil pump rotates in the reverse direction. Therefore the main oil pump
does not discharge oil pressure. During any of the above vehicle operations, the transfer motor drives the
sub-oil pump to compensate for insufficient oil pressure.
3. The transfer motor operates as follows:
1. The motor relay turns OFF in the 2WD mode.
2. The motor relay operates as described in the table below in modes other than the 2WD mode.
Ta b l e 1
Ta b l e 2
NOTE:
OFF (after 2.5 seconds have elapsed.)
4. 4WD shift switch, PNP switch, Neutral-4LO switch, vehicle speed sensor and throttle position sensor are
used in conjunction with the transfer motor.
WAIT DETECTION SWITCH
1. The wait detection switch releases the “booming” torque produced in the propeller shaft. After the release
of the “booming” torque, the wait detection switch helps provide the 4WD lock gear (clutch drum) shifts. A
difference may occur between the operation (“4LO” to “4H” shift only) of the 4WD shift switch and actual
drive mode. At this point, the wait detection switch senses an actual drive mode.
2. The wait detection switch operates as follows:
4WD lock gear (clutch drum) locked: ON
4WD lock gear (clutch drum) released: OFF
3. The wait detection switch senses an actual drive mode and the 4WD shift indicator lamp indicates the
vehicle drive mode.
2-4WD SHIFT SOLENOID VALVE
The 2-4WD shift solenoid valve operates to apply oil pressure to the wet, multiplate clutch, depending on the
drive mode. The driving force is transmitted to the front wheels through the clutch when the vehicle is set in the
4WD mode. Setting the vehicle in the 2WD mode requires no pressure buildup. In other words, pressure force
applied to the wet, multiplate clutch becomes zero.
PNP switch “R” position VFF (Vehicle speed) A/T position Motor relay drive command
ON — R ON
OFF0Positions other than the “P” or
“N” positionsON
—“P” or “N” position (See Table
2.)—
0 < VFF ≤ 50 km/h (31 MPH) — ON
50 km/h (31 MPH) < VFF < 55
km/h (34 MPH)—HOLD
55 km/h (34 MPH) ≤ VFF — OFF
A/T position N-4L SW 4WD modeThrottle position
0 - 0.07/8 0.07/8 - 1/8 1/8 - MAX
NOFFLOCK (4H) ON ON ON
Positions other than
the LOCK position
(2WD or AUTO)See NOTE. HOLD ON
ON — See NOTE. HOLD ON
P——See NOTE.HOLDON
Page 3141 of 3371
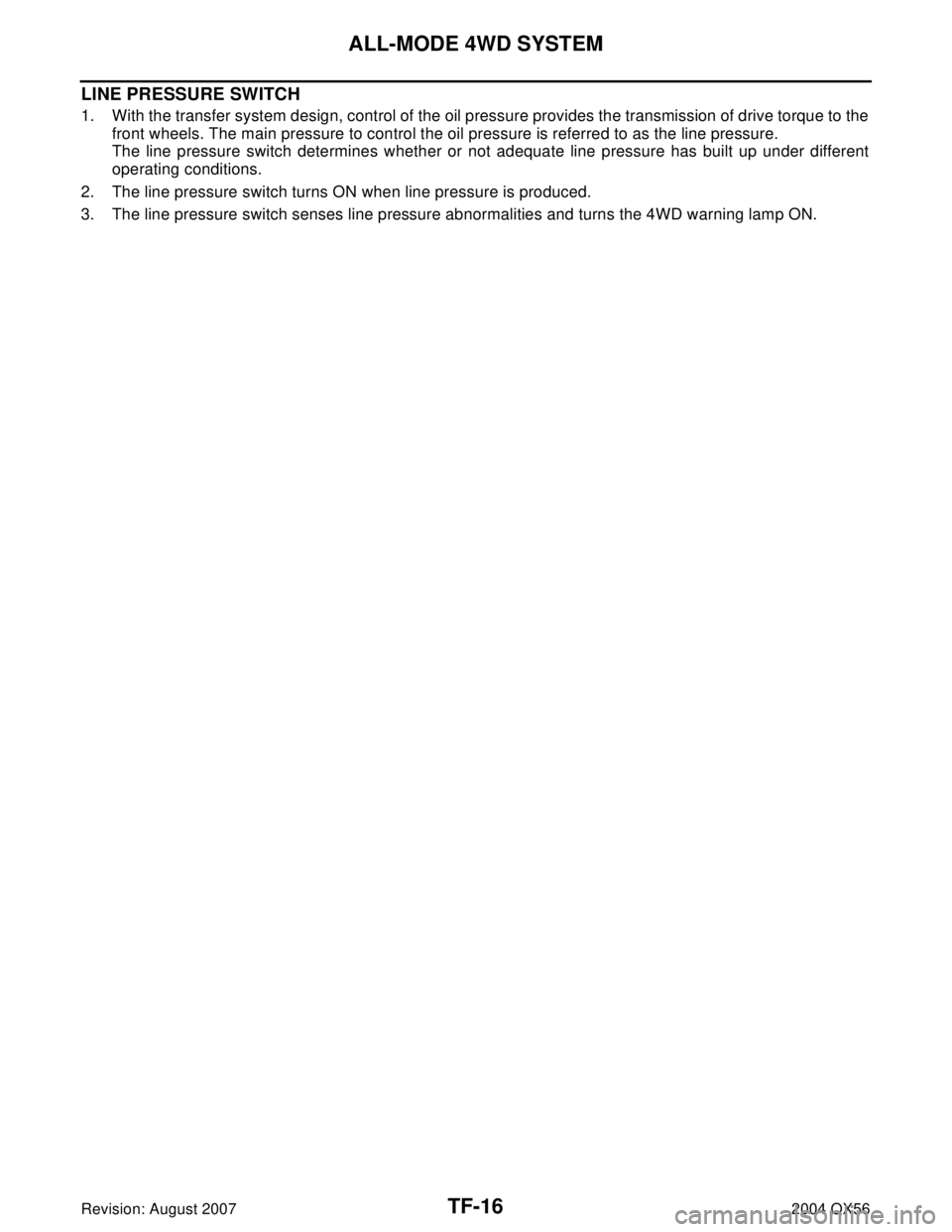
TF-16
ALL-MODE 4WD SYSTEM
Revision: August 20072004 QX56
LINE PRESSURE SWITCH
1. With the transfer system design, control of the oil pressure provides the transmission of drive torque to the
front wheels. The main pressure to control the oil pressure is referred to as the line pressure.
The line pressure switch determines whether or not adequate line pressure has built up under different
operating conditions.
2. The line pressure switch turns ON when line pressure is produced.
3. The line pressure switch senses line pressure abnormalities and turns the 4WD warning lamp ON.
Page 3161 of 3371
![INFINITI QX56 2004 Factory Service Manual TF-36
ON BOARD DIAGNOSTIC SYSTEM DESCRIPTION
Revision: August 20072004 QX56
N position switch TF [ON-OFF] N position switch of transfer
Line pressure switch [ON-OFF] Line pressure switch
Clutch pressu INFINITI QX56 2004 Factory Service Manual TF-36
ON BOARD DIAGNOSTIC SYSTEM DESCRIPTION
Revision: August 20072004 QX56
N position switch TF [ON-OFF] N position switch of transfer
Line pressure switch [ON-OFF] Line pressure switch
Clutch pressu](/img/42/57034/w960_57034-3160.png)
TF-36
ON BOARD DIAGNOSTIC SYSTEM DESCRIPTION
Revision: August 20072004 QX56
N position switch TF [ON-OFF] N position switch of transfer
Line pressure switch [ON-OFF] Line pressure switch
Clutch pressure switch [ON-OFF] Clutch pressure switch
ATP switch [ON-OFF]—
N position switch AT [ON-OFF] “N” position on A/T PNP switch
R position switch AT [ON-OFF] “R” position on A/T PNP switch
P position switch AT [ON-OFF] “P” position on A/T PNP switch
ABS operation switch [ON-OFF] ABS operation switch
Wait detection switch [ON-OFF] —
Throttle positionThrottle opening recognized by transfer
control unit
4WD-mode4WD-mode recognized by transfer control
unit (2WD, AUTO, 4H & 4LO)
Vehicle speed comp [km/h (MPH)]Vehicle speed recognized by transfer con-
trol unit
*Control torque [N·m (kg-m, ft.-lb.)]Calculated torque recognized by transfer
control unit
Duty solenoid valve [%]
(Transfer 4WD solenoid valve)—
2-4WD shift solenoid valve [ON-
OFF]
Control signal outputs of transfer control
unit Transfer motor relay [ON-OFF]
Shift activating 1 [ON-OFF]
Shift activating 2 [ON-OFF]
2-4WD shift solenoid valve monitor
[ON-OFF]
Check signal (re-input signal) of transfer
control unit control signal output is dis-
played. If circuit is shorted or open, ON/OFF
state does not change. Transfer motor relay monitor [ON-
OFF]
Shift activating monitor 1 [ON-OFF]
Shift activating monitor 2 [ON-OFF]
4WD fail lamp [ON-OFF]Transfer control unit control signal output for
4WD warning lamp (left)
Shift position switch 1 [ON-OFF] —
Shift position switch 2 [ON-OFF] —
2WD indicator lamp [ON-OFF]Transfer control unit control signal output for
4WD shift indicator lamp (rear)
AUTO indicator lamp [ON-OFF]Transfer control unit control signal output for
4WD shift indicator lamp (front & rear)
LOCK indicator lamp [ON-OFF]Transfer control unit control signal output for
4WD shift indicator lamp (center)
4LO indicator lamp [ON-OFF]Transfer control unit control signal output for
4WD shift indicator lamp (right) Item [Unit]Monitor item
Remarks ECU
INPUT
SIGNALSMAIN
SIGNALSSELEC-
TION
FROM
MENU