washer fluid INFINITI QX56 2006 Factory User Guide
[x] Cancel search | Manufacturer: INFINITI, Model Year: 2006, Model line: QX56, Model: INFINITI QX56 2006Pages: 3383, PDF Size: 51.76 MB
Page 2101 of 3383
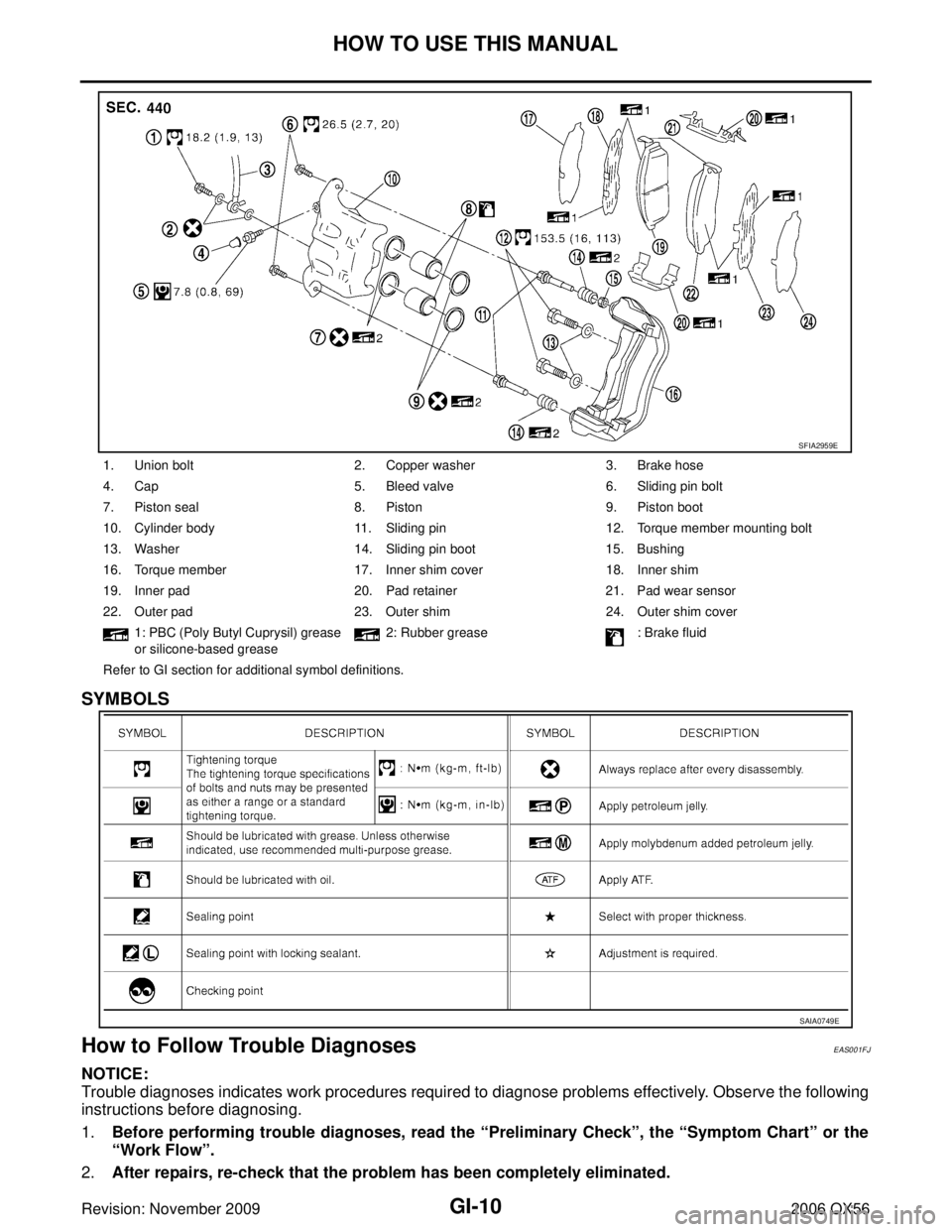
GI-10
HOW TO USE THIS MANUAL
Revision: November 20092006 QX56
SYMBOLS
How to Follow Trouble DiagnosesEAS001FJ
NOTICE:
Trouble diagnoses indicates work procedures required to diagnose problems effectively. Observe the following
instructions before diagnosing.
1.Before performing trouble diagnoses, read the “Preliminary Check”, the “Symptom Chart” or the
“Work Flow”.
2. After repairs, re-check that the problem has been completely eliminated.
1. Union bolt 2. Copper washer 3. Brake hose
4. Cap 5. Bleed valve 6. Sliding pin bolt
7. Piston seal 8. Piston 9. Piston boot
10. Cylinder body 11. Sliding pin 12. Torque member mounting bolt
13. Washer 14. Sliding pin boot 15. Bushing
16. Torque member 17. Inner shim cover 18. Inner shim
19. Inner pad 20. Pad retainer 21. Pad wear sensor
22. Outer pad 23. Outer shim 24. Outer shim cover
1: PBC (Poly Butyl Cuprysil) grease
or silicone-based grease 2: Rubber grease
: Brake fluid
Refer to GI section for additional symbol definitions.
SFIA2959E
SAIA0749E
Page 2245 of 3383
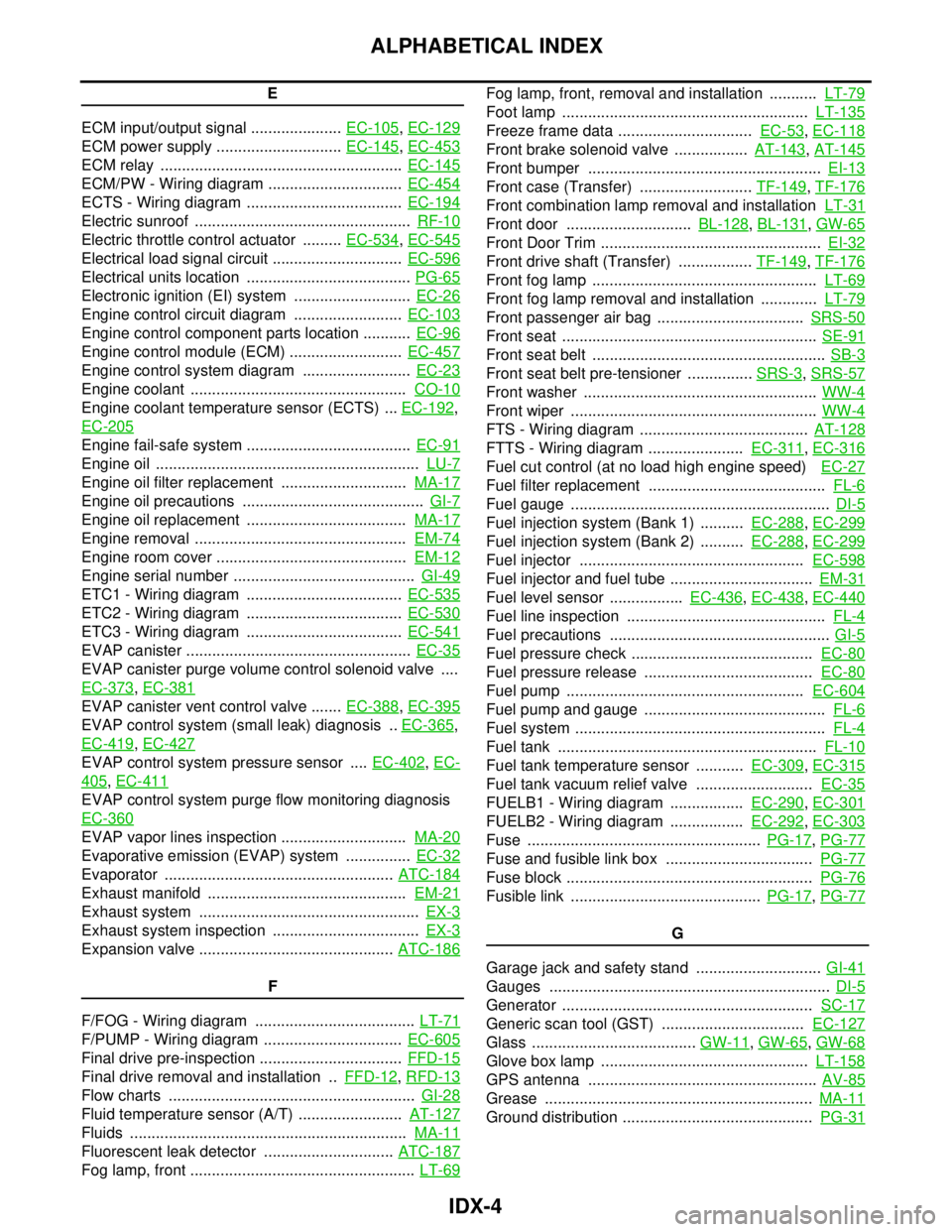
IDX-4
ALPHABETICAL INDEX
E
ECM input/output signal ..................... EC-105
, EC-129
ECM power supply ............................. EC-145, EC-453
ECM relay ........................................................ EC-145
ECM/PW - Wiring diagram ............................... EC-454
ECTS - Wiring diagram .................................... EC-194
Electric sunroof .................................................. RF-10
Electric throttle control actuator ......... EC-534, EC-545
Electrical load signal circuit .............................. EC-596
Electrical units location ...................................... PG-65
Electronic ignition (EI) system ........................... EC-26
Engine control circuit diagram ......................... EC-103
Engine control component parts location ........... EC-96
Engine control module (ECM) .......................... EC-457
Engine control system diagram ......................... EC-23
Engine coolant .................................................. CO-10
Engine coolant temperature sensor (ECTS) ... EC-192,
EC-205
Engine fail-safe system ...................................... EC-91
Engine oil ............................................................. LU-7
Engine oil filter replacement ............................. MA-17
Engine oil precautions .......................................... GI-7
Engine oil replacement ..................................... MA-17
Engine removal ................................................. EM-74
Engine room cover ............................................ EM-12
Engine serial number .......................................... GI-49
ETC1 - Wiring diagram .................................... EC-535
ETC2 - Wiring diagram .................................... EC-530
ETC3 - Wiring diagram .................................... EC-541
EVAP canister .................................................... EC-35
EVAP canister purge volume control solenoid valve ....
EC-373
, EC-381
EVAP canister vent control valve ....... EC-388, EC-395
EVAP control system (small leak) diagnosis .. EC-365,
EC-419
, EC-427
EVAP control system pressure sensor .... EC-402, EC-
405, EC-411
EVAP control system purge flow monitoring diagnosis
EC-360
EVAP vapor lines inspection ............................. MA-20
Evaporative emission (EVAP) system ............... EC-32
Evaporator ..................................................... ATC-184
Exhaust manifold .............................................. EM-21
Exhaust system ................................................... EX-3
Exhaust system inspection .................................. EX-3
Expansion valve ............................................. ATC-186
F
F/FOG - Wiring diagram ..................................... LT-71
F/PUMP - Wiring diagram ................................ EC-605
Final drive pre-inspection ................................. FFD-15
Final drive removal and installation .. FFD-12, RFD-13
Flow charts ......................................................... GI-28
Fluid temperature sensor (A/T) ........................ AT-127
Fluids ................................................................ MA-11
Fluorescent leak detector .............................. ATC-187
Fog lamp, front .................................................... LT-69
Fog lamp, front, removal and installation ........... LT-79
Foot lamp ......................................................... LT-135
Freeze frame data ............................... EC-53, EC-118
Front brake solenoid valve ................. AT-143, AT-145
Front bumper ...................................................... EI-13
Front case (Transfer) .......................... TF-149, TF-176
Front combination lamp removal and installation LT-31
Front door ............................. BL-128, BL-131, GW-65
Front Door Trim ................................................... EI-32
Front drive shaft (Transfer) ................. TF-149, TF-176
Front fog lamp .................................................... LT-69
Front fog lamp removal and installation ............. LT-79
Front passenger air bag .................................. SRS-50
Front seat ........................................................... SE-91
Front seat belt ...................................................... SB-3
Front seat belt pre-tensioner ............... SRS-3, SRS-57
Front washer ...................................................... WW-4
Front wiper ......................................................... WW-4
FTS - Wiring diagram ....................................... AT-128
FTTS - Wiring diagram ...................... EC-311, EC-316
Fuel cut control (at no load high engine speed) EC-27
Fuel filter replacement ......................................... FL-6
Fuel gauge ............................................................ DI-5
Fuel injection system (Bank 1) .......... EC-288, EC-299
Fuel injection system (Bank 2) .......... EC-288, EC-299
Fuel injector .................................................... EC-598
Fuel injector and fuel tube ................................. EM-31
Fuel level sensor ................. EC-436, EC-438, EC-440
Fuel line inspection .............................................. FL-4
Fuel precautions ................................................... GI-5
Fuel pressure check .......................................... EC-80
Fuel pressure release ....................................... EC-80
Fuel pump ....................................................... EC-604
Fuel pump and gauge .......................................... FL-6
Fuel system .......................................................... FL-4
Fuel tank ............................................................ FL-10
Fuel tank temperature sensor ........... EC-309, EC-315
Fuel tank vacuum relief valve ........................... EC-35
FUELB1 - Wiring diagram ................. EC-290, EC-301
FUELB2 - Wiring diagram ................. EC-292, EC-303
Fuse ...................................................... PG-17, PG-77
Fuse and fusible link box .................................. PG-77
Fuse block ......................................................... PG-76
Fusible link ............................................ PG-17, PG-77
G
Garage jack and safety stand ............................. GI-41
Gauges ................................................................. DI-5
Generator .......................................................... SC-17
Generic scan tool (GST) ................................. EC-127
Glass ...................................... GW-11, GW-65, GW-68
Glove box lamp ................................................ LT-158
GPS antenna ..................................................... AV-85
Grease .............................................................. MA-11
Ground distribution ............................................ PG-31
Page 2249 of 3383
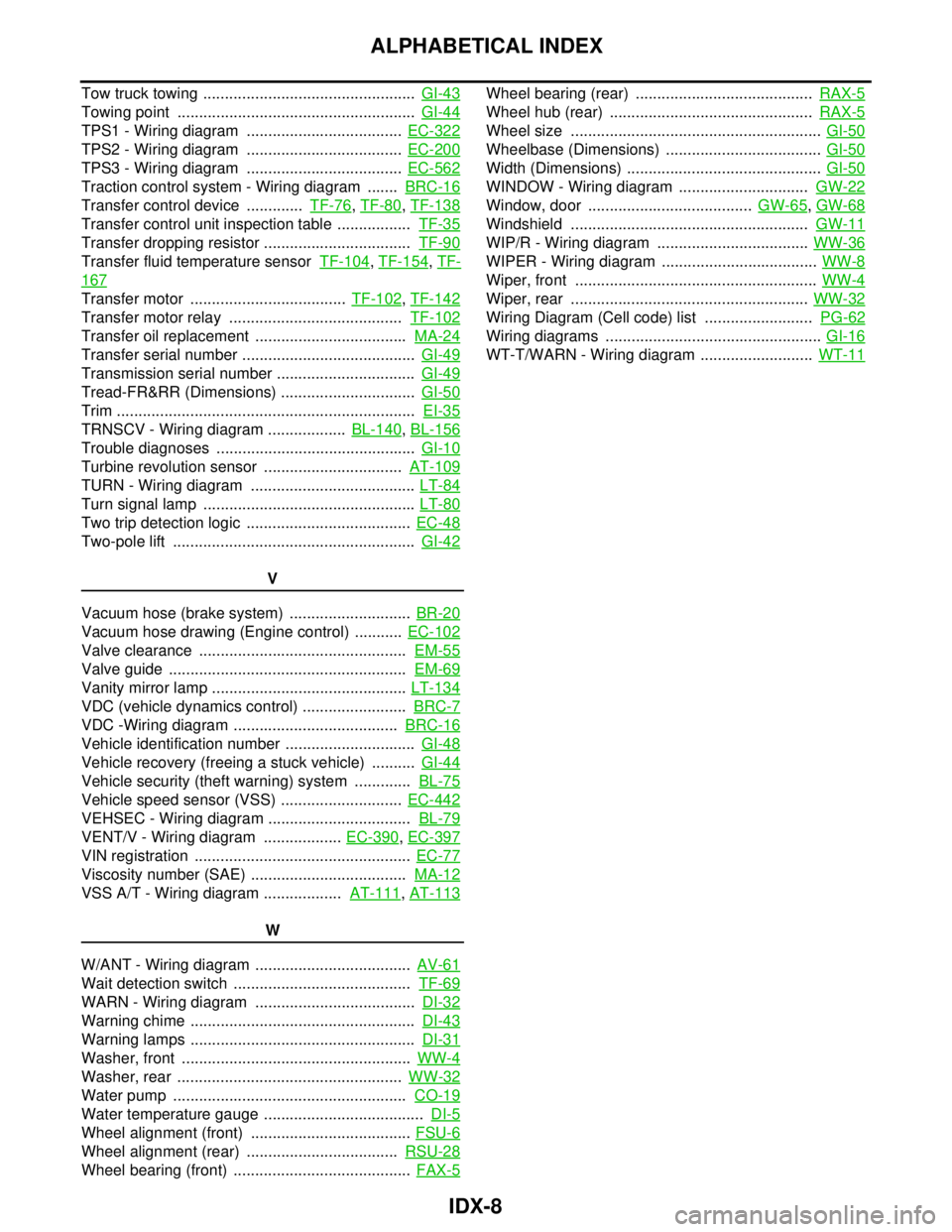
IDX-8
ALPHABETICAL INDEX
Tow truck towing ................................................. GI-43
Towing point ....................................................... GI-44
TPS1 - Wiring diagram .................................... EC-322
TPS2 - Wiring diagram .................................... EC-200
TPS3 - Wiring diagram .................................... EC-562
Traction control system - Wiring diagram ....... BRC-16
Transfer control device ............. TF-76, TF-80, TF-138
Transfer control unit inspection table ................. TF-35
Transfer dropping resistor .................................. TF-90
Transfer fluid temperature sensor TF-104, TF-154, TF-
167
Transfer motor .................................... TF-102, TF-142
Transfer motor relay ........................................ TF-102
Transfer oil replacement ................................... MA-24
Transfer serial number ........................................ GI-49
Transmission serial number ................................ GI-49
Tread-FR&RR (Dimensions) ............................... GI-50
Trim ..................................................................... EI-35
TRNSCV - Wiring diagram .................. BL-140, BL-156
Trouble diagnoses .............................................. GI-10
Turbine revolution sensor ................................ AT-109
TURN - Wiring diagram ...................................... LT-84
Turn signal lamp ................................................. LT-80
Two trip detection logic ...................................... EC-48
Two-pole lift ........................................................ GI-42
V
Vacuum hose (brake system) ............................ BR-20
Vacuum hose drawing (Engine control) ........... EC-102
Valve clearance ................................................ EM-55
Valve guide ....................................................... EM-69
Vanity mirror lamp ............................................. LT-134
VDC (vehicle dynamics control) ........................ BRC-7
VDC -Wiring diagram ...................................... BRC-16
Vehicle identification number .............................. GI-48
Vehicle recovery (freeing a stuck vehicle) .......... GI-44
Vehicle security (theft warning) system ............. BL-75
Vehicle speed sensor (VSS) ............................ EC-442
VEHSEC - Wiring diagram ................................. BL-79
VENT/V - Wiring diagram .................. EC-390, EC-397
VIN registration .................................................. EC-77
Viscosity number (SAE) .................................... MA-12
VSS A/T - Wiring diagram .................. AT-111, AT-113
W
W/ANT - Wiring diagram .................................... AV-61
Wait detection switch ......................................... TF-69
WARN - Wiring diagram ..................................... DI-32
Warning chime .................................................... DI-43
Warning lamps .................................................... DI-31
Washer, front ..................................................... WW-4
Washer, rear .................................................... WW-32
Water pump ...................................................... CO-19
Water temperature gauge ..................................... DI-5
Wheel alignment (front) ..................................... FSU-6
Wheel alignment (rear) ................................... RSU-28
Wheel bearing (front) ......................................... FAX-5
Wheel bearing (rear) ......................................... RAX-5
Wheel hub (rear) ............................................... RAX-5
Wheel size .......................................................... GI-50
Wheelbase (Dimensions) .................................... GI-50
Width (Dimensions) ............................................. GI-50
WINDOW - Wiring diagram .............................. GW-22
Window, door ...................................... GW-65, GW-68
Windshield ....................................................... GW-11
WIP/R - Wiring diagram ................................... WW-36
WIPER - Wiring diagram .................................... WW-8
Wiper, front ........................................................ WW-4
Wiper, rear ....................................................... WW-32
Wiring Diagram (Cell code) list ......................... PG-62
Wiring diagrams .................................................. GI-16
WT-T/WARN - Wiring diagram .......................... WT-11
Page 2591 of 3383
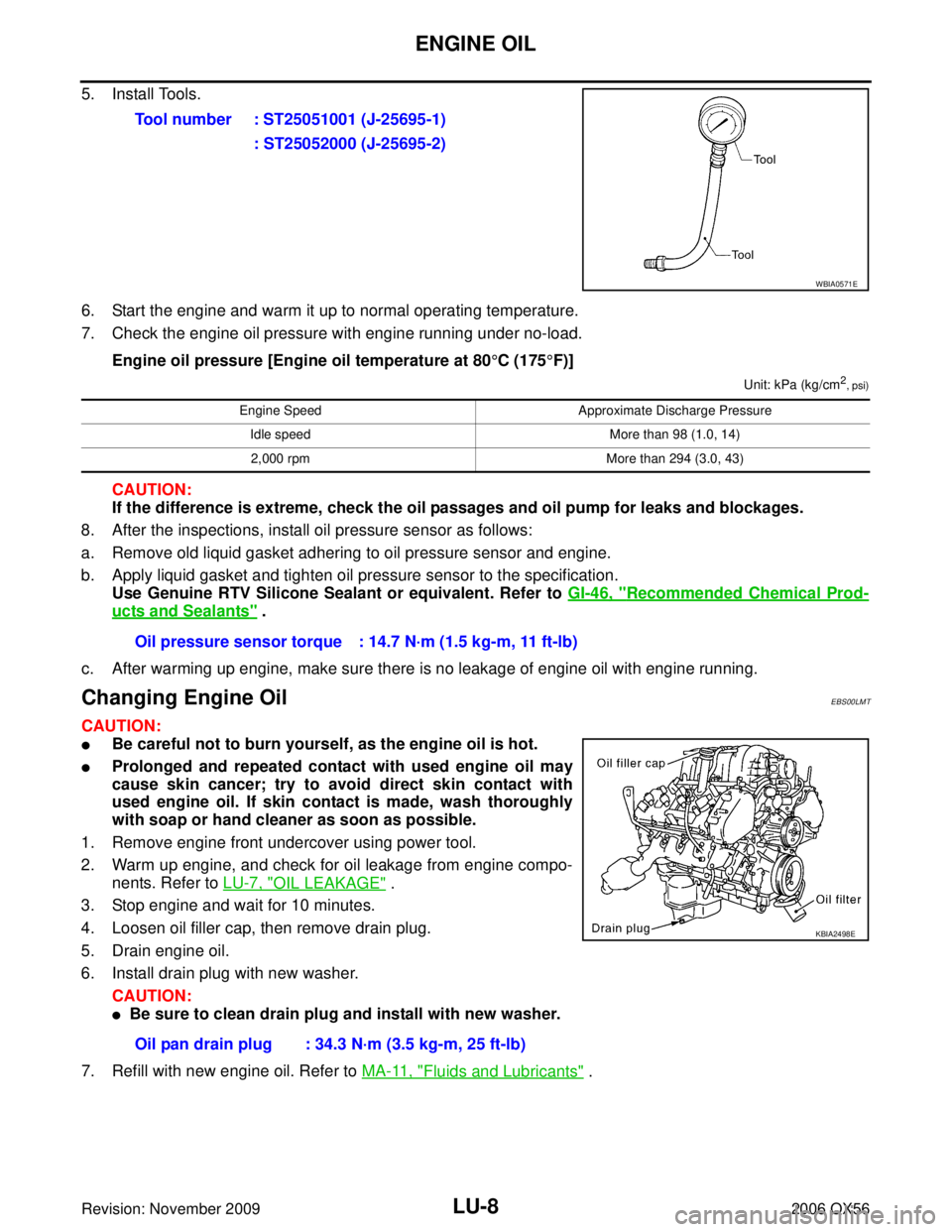
LU-8Revision: November 2009
ENGINE OIL
2006 QX56
5. Install Tools.
6. Start the engine and warm it up to normal operating temperature.
7. Check the engine oil pressure with engine running under no-load.Engine oil pressure [Engine oil temperature at 80 °C (175 °F)]
Unit: kPa (kg/cm2
, psi)
CAUTION:
If the difference is extreme, check the oil passages and oil pump for leaks and blockages.
8. After the inspections, install oil pressure sensor as follows:
a. Remove old liquid gasket adhering to oil pressure sensor and engine.
b. Apply liquid gasket and tighten oil pressure sensor to the specification. Use Genuine RTV Silicone Sealant or equivalent. Refer to GI-46, "
Recommended Chemical Prod-
ucts and Sealants" .
c. After warming up engine, make sure there is no leakage of engine oil with engine running.
Changing Engine OilEBS00LMT
CAUTION:
Be careful not to burn yourself, as the engine oil is hot.
Prolonged and repeated contact with used engine oil may
cause skin cancer; try to avoid direct skin contact with
used engine oil. If skin contact is made, wash thoroughly
with soap or hand cleaner as soon as possible.
1. Remove engine front undercover using power tool.
2. Warm up engine, and check for oil leakage from engine compo- nents. Refer to LU-7, "
OIL LEAKAGE" .
3. Stop engine and wait for 10 minutes.
4. Loosen oil filler cap, then remove drain plug.
5. Drain engine oil.
6. Install drain plug with new washer.
CAUTION:
Be sure to clean drain plug and install with new washer.
7. Refill with new engine oil. Refer to MA-11, "
Fluids and Lubricants" .
Tool number : ST25051001 (J-25695-1)
: ST25052000 (J-25695-2)
WBIA0571E
Engine Speed Approximate Discharge Pressure
Idle speed More than 98 (1.0, 14)
2,000 rpm More than 294 (3.0, 43)
Oil pressure sensor torque : 14.7 N·m (1.5 kg-m, 11 ft-lb)
Oil pan drain plug : 34.3 N·m (3.5 kg-m, 25 ft-lb)
KBIA2498E
Page 2605 of 3383
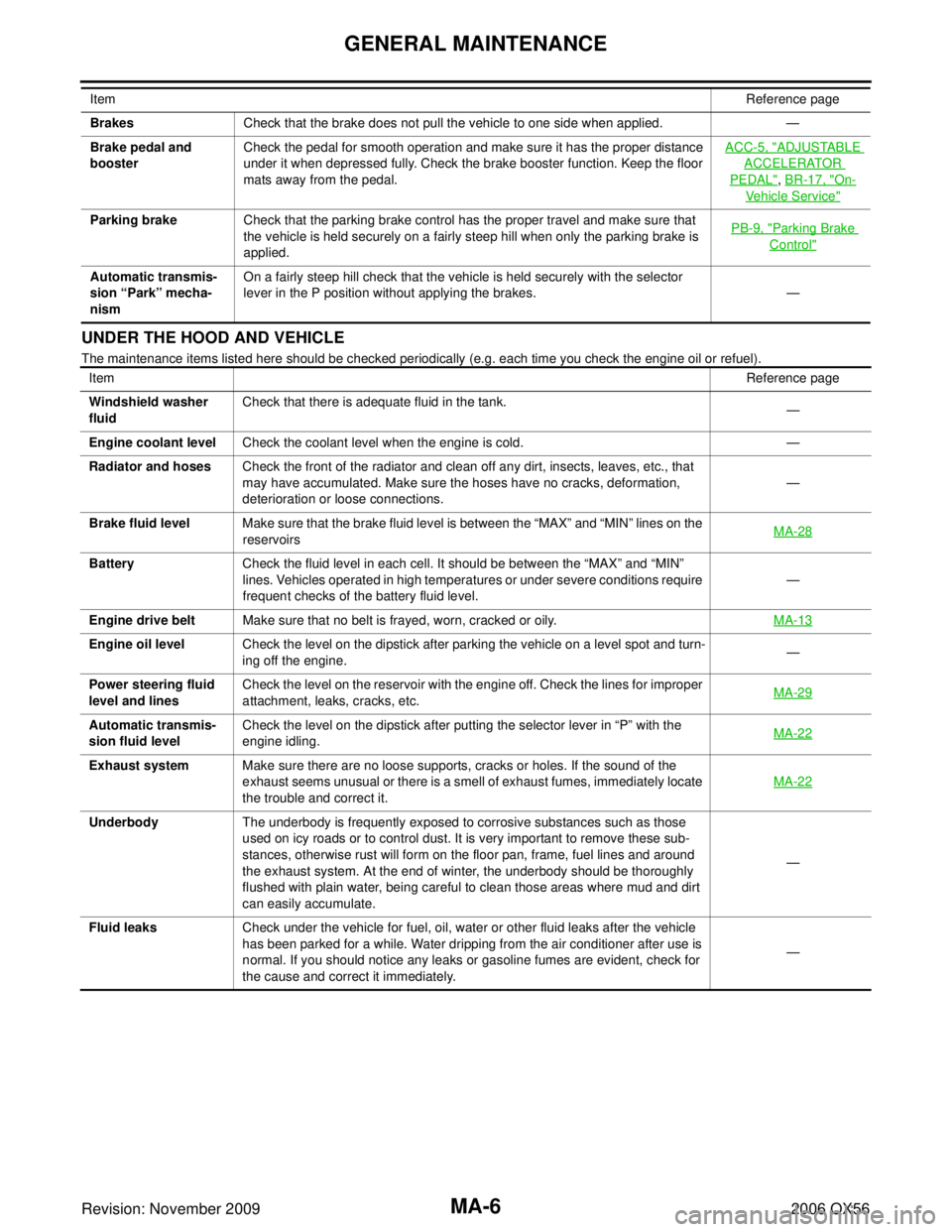
MA-6
GENERAL MAINTENANCE
Revision: November 20092006 QX56
UNDER THE HOOD AND VEHICLE
The maintenance items listed here should be checked periodically (e.g. each time you check the engine oil or refuel).Brakes
Check that the brake does not pull the vehicle to one side when applied. —
Brake pedal and
booster Check the pedal for smooth operation and make sure it has the proper distance
under it when depressed fully. Check the brake booster function. Keep the floor
mats away from the pedal. ACC-5, "
ADJUSTABLE
ACCELERATOR
PEDAL",
BR-17, "On-
Vehicle Service"
Parking brake Check that the parking brake control has the proper travel and make sure that
the vehicle is held securely on a fairly steep hill when only the parking brake is
applied. PB-9, "Parking Brake
Control"
Automatic transmis-
sion “Park” mecha-
nismOn a fairly steep hill check that the vehicle is held securely with the selector
lever in the P position without applying the brakes.
—
Item
Reference page
Item Reference page
Windshield washer
fluid Check that there is adequate fluid in the tank.
—
Engine coolant level Check the coolant level when the engine is cold. —
Radiator and hoses Check the front of the radiator and clean off any dirt, insects, leaves, etc., that
may have accumulated. Make sure the hoses have no cracks, deformation,
deterioration or loose connections. —
Brake fluid level Make sure that the brake fluid level is between the “MAX ” and “ MIN” lines on the
reservoirs MA-28
Battery
Check the fluid level in each cell. It should be between the “MAX ” and “MIN ”
lines. Vehicles operated in high temperatures or under severe conditions require
frequent checks of the battery fluid level. —
Engine drive belt Make sure that no belt is frayed, worn, cracked or oily. MA-13
Engine oil levelCheck the level on the dipstick after parking the vehicle on a level spot and turn-
ing off the engine. —
Power steering fluid
level and lines Check the level on the reservoir with the engine off. Check the lines for improper
attachment, leaks, cracks, etc.
MA-29
Automatic transmis-
sion fluid levelCheck the level on the dipstick after putting the selector lever in
“P ” with the
engine idling. MA-22
Exhaust system
Make sure there are no loose supports, cracks or holes. If the sound of the
exhaust seems unusual or there is a smell of exhaust fumes, immediately locate
the trouble and correct it. MA-22
Underbody
The underbody is frequently exposed to corrosive substances such as those
used on icy roads or to control dust. It is very important to remove these sub-
stances, otherwise rust will form on the floor pan, frame, fuel lines and around
the exhaust system. At the end of winter, the underbody should be thoroughly
flushed with plain water, being careful to clean those areas where mud and dirt
can easily accumulate. —
Fluid leaks Check under the vehicle for fuel, oil, water or other fluid leaks after the vehicle
has been parked for a while. Water dripping from the air conditioner after use is
normal. If you should notice any leaks or gasoline fumes are evident, check for
the cause and correct it immediately. —
Page 2610 of 3383
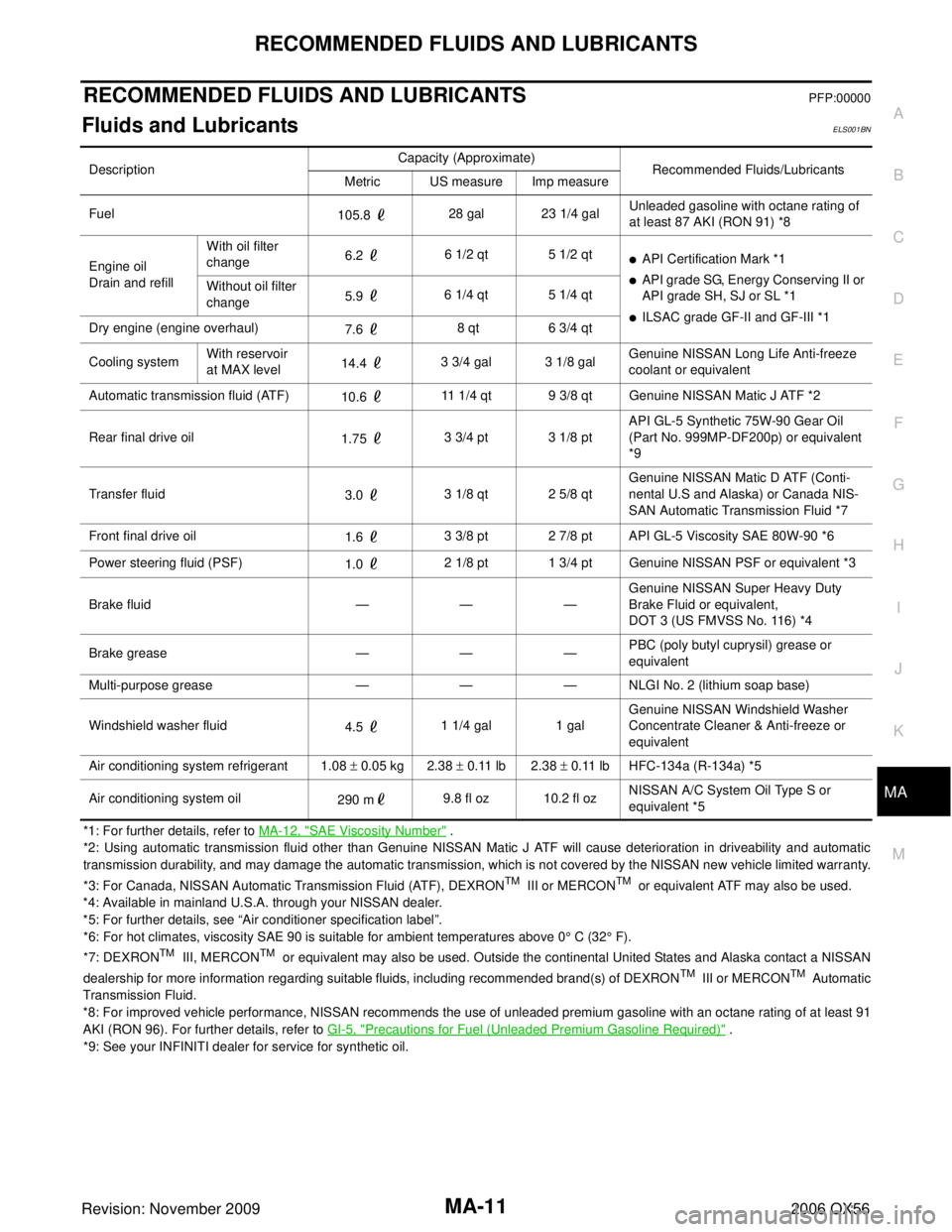
RECOMMENDED FLUIDS AND LUBRICANTSMA-11
C
DE
F
G H
I
J
K
M A
B
MA
Revision: November 2009 2006 QX56
RECOMMENDED FLUIDS AND LUBRICANTSPFP:00000
Fluids and LubricantsELS001BN
*1: For further details, refer to MA-12, "SAE Viscosity Number" .
*2: Using automatic transmission fluid other than Genuine NISSAN Matic J ATF will cause deterioration in driveability and automatic
transmission durability, and may damage the automatic transmission, which is not covered by the NISSAN new vehicle limited warr anty.
*3: For Canada, NISSAN Automatic Transmission Fluid (ATF), DEXRON
TM III or MERCONTM or equivalent ATF may also be used.
*4: Available in mainland U.S.A. through your NISSAN dealer.
*5: For further details, see “Air conditioner specification label ”.
*6: For hot climates, viscosity SAE 90 is suitable for ambient temperatures above 0 ° C (32° F).
*7: DEXRON
TM III, MERCONTM or equivalent may also be used. Outside the continental United States and Alaska contact a NISSAN
dealership for more information regarding suitable fluids, including recommended brand(s) of DEXRONTM III or MERCONTM Automatic
Transmission Fluid.
*8: For improved vehicle performance, NISSAN recommends the use of unleaded premium gasoline with an octane rating of at least 91
AKI (RON 96). For further details, refer to GI-5, "
Precautions for Fuel (Unleaded Premium Gasoline Required)" .
*9: See your INFINITI dealer for service for synthetic oil. Description
Capacity (Approximate)
Recommended Fluids/Lubricants
Metric US measure Imp measure
Fuel 105.8 28 gal 23 1/4 gal Unleaded gasoline with octane rating of
at least 87 AKI (RON 91) *8
Engine oil
Drain and refill With oil filter
change
6.2
6 1/2 qt 5 1/2 qt
API Certification Mark *1
API grade SG, Energy Conserving II or
API grade SH, SJ or SL *1
ILSAC grade GF-II and GF-III *1
Without oil filter
change
5.9
6 1/4 qt 5 1/4 qt
Dry engine (engine overhaul) 7.6 8 qt
6 3/4 qt
Cooling system With reservoir
at MAX level
14.4
3 3/4 gal 3 1/8 gal Genuine NISSAN Long Life Anti-freeze
coolant or equivalent
Automatic transmission fluid (ATF) 10.6 11 1/4 qt 9 3/8 qt Genuine NISSAN Matic J ATF *2
Rear final drive oil 1.75 3 3/4 pt 3 1/8 pt API GL-5 Synthetic 75W-90 Gear Oil
(Part No. 999MP-DF200p) or equivalent
*9
Transfer fluid 3.0 3 1/8 qt 2 5/8 qt Genuine NISSAN Matic D ATF (Conti-
nental U.S and Alaska) or Canada NIS-
SAN Automatic Transmission Fluid *7
Front final drive oil 1.6 3 3/8 pt 2 7/8 pt API GL-5 Viscosity SAE 80W-90 *6
Power steering fluid (PSF) 1.0 2 1/8 pt 1 3/4 pt Genuine NISSAN PSF or equivalent *3
Brake fluid ——— Genuine NISSAN Super Heavy Duty
Brake Fluid or equivalent,
DOT 3 (US FMVSS No. 116) *4
Brake grease ——— PBC (poly butyl cuprysil) grease or
equivalent
Multi-purpose grease ——— NLGI No. 2 (lithium soap base)
Windshield washer fluid 4.5 1 1/4 gal 1 gal Genuine NISSAN Windshield Washer
Concentrate Cleaner & Anti-freeze or
equivalent
Air conditioning system refrigerant 1.08 ± 0.05 kg 2.38 ± 0.11 lb 2.38 ± 0.11 lb HFC-134a (R-134a) *5
Air conditioning system oil 290 m9.8 fl oz 10.2 fl oz NISSAN A/C System Oil Type S or
equivalent *5
Page 2616 of 3383
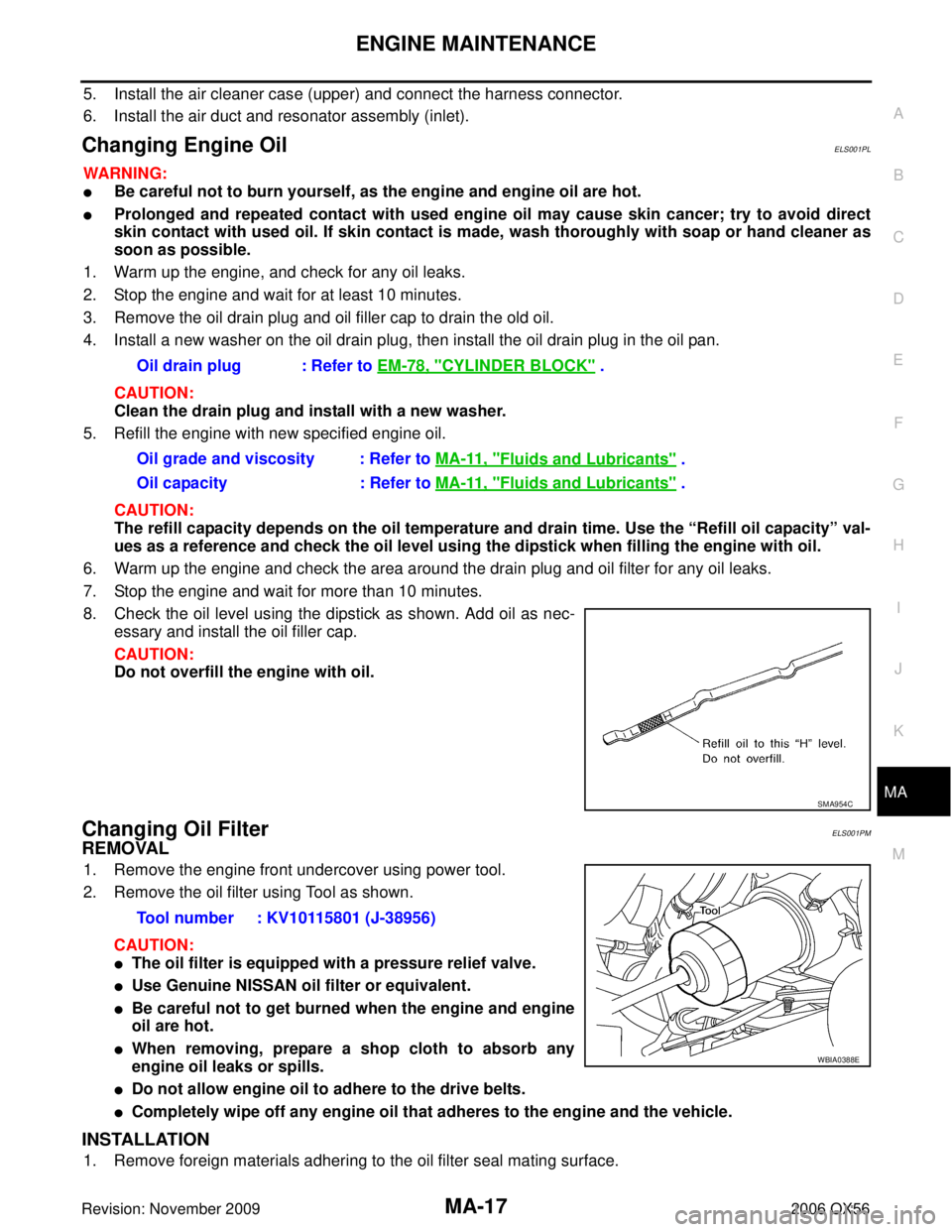
ENGINE MAINTENANCEMA-17
C
DE
F
G H
I
J
K
M A
B
MA
Revision: November 2009 2006 QX56
5. Install the air cleaner case (upper) and connect the harness connector.
6. Install the air duct and resonator assembly (inlet).
Changing Engine OilELS001PL
WARNING:
Be careful not to burn yourself, as the engine and engine oil are hot.
Prolonged and repeated contact with used engine oil may cause skin cancer; try to avoid direct
skin contact with used oil. If skin contact is made, wash thoroughly with soap or hand cleaner as
soon as possible.
1. Warm up the engine, and check for any oil leaks.
2. Stop the engine and wait for at least 10 minutes.
3. Remove the oil drain plug and oil filler cap to drain the old oil.
4. Install a new washer on the oil drain plug, then install the oil drain plug in the oil pan.
CAUTION:
Clean the drain plug and install with a new washer.
5. Refill the engine with new specified engine oil.
CAUTION:
The refill capacity depends on the oil temperature and drain time. Use the “Refill oil capacity” val-
ues as a reference and check the oil level using the dipstick when filling the engine with oil.
6. Warm up the engine and check the area around the drain plug and oil filter for any oil leaks.
7. Stop the engine and wait for more than 10 minutes.
8. Check the oil level using the dipstick as shown. Add oil as nec- essary and install the oil filler cap.
CAUTION:
Do not overfill the engine with oil.
Changing Oil FilterELS001PM
REMOVAL
1. Remove the engine front undercover using power tool.
2. Remove the oil filter using Tool as shown.
CAUTION:
The oil filter is equipped with a pressure relief valve.
Use Genuine NISSAN oil filter or equivalent.
Be careful not to get burned when the engine and engine
oil are hot.
When removing, prepare a shop cloth to absorb any
engine oil leaks or spills.
Do not allow engine oil to adhere to the drive belts.
Completely wipe off any engine oil that adheres to the engine and the vehicle.
INSTALLATION
1. Remove foreign materials adhering to the oil filter seal mating surface. Oil drain plug : Refer to EM-78, "
CYLINDER BLOCK" .
Oil grade and viscosity : Refer to MA-11, "
Fluids and Lubricants" .
Oil capacity : Refer to MA-11, "
Fluids and Lubricants" .
SMA954C
Tool number : KV10115801 (J-38956)
WBIA0388E
Page 2739 of 3383
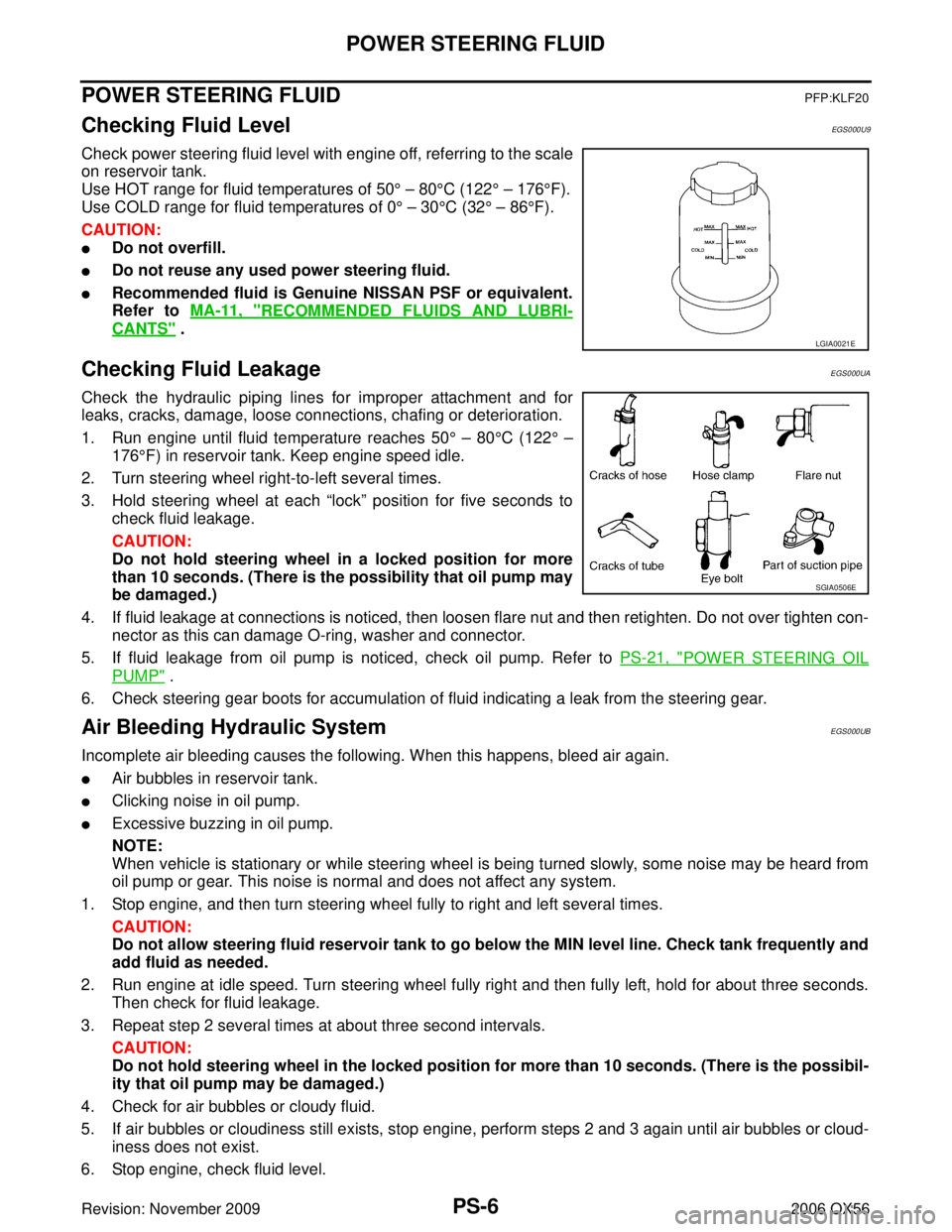
PS-6
POWER STEERING FLUID
Revision: November 20092006 QX56
POWER STEERING FLUIDPFP:KLF20
Checking Fluid LevelEGS000U9
Check power steering fluid level with engine off, referring to the scale
on reservoir tank.
Use HOT range for fluid temperatures of 50° – 80 °C (122 ° – 176° F).
Use COLD range for fluid temperatures of 0 ° – 30° C (32 ° – 86 °F).
CAUTION:
Do not overfill.
Do not reuse any used power steering fluid.
Recommended fluid is Genuine NISSAN PSF or equivalent.
Refer to MA-11, "
RECOMMENDED FLUIDS AND LUBRI-
CANTS" .
Checking Fluid LeakageEGS000UA
Check the hydraulic piping lines for improper attachment and for
leaks, cracks, damage, loose connections, chafing or deterioration.
1. Run engine until fluid temperature reaches 50 ° – 80 °C (122 ° –
176° F) in reservoir tank. Keep engine speed idle.
2. Turn steering wheel right-to-left several times.
3. Hold steering wheel at each “lock” position for five seconds to
check fluid leakage.
CAUTION:
Do not hold steering wheel in a locked position for more
than 10 seconds. (There is the possibility that oil pump may
be damaged.)
4. If fluid leakage at connections is noticed, then loosen flare nut and then retighten. Do not over tighten con- nector as this can damage O-ring, washer and connector.
5. If fluid leakage from oil pump is noticed, check oil pump. Refer to PS-21, "
POWER STEERING OIL
PUMP" .
6. Check steering gear boots for accumulation of fluid indicating a leak from the steering gear.
Air Bleeding Hydraulic SystemEGS000UB
Incomplete air bleeding causes the following. When this happens, bleed air again.
Air bubbles in reservoir tank.
Clicking noise in oil pump.
Excessive buzzing in oil pump.
NOTE:
When vehicle is stationary or while steering wheel is being turned slowly, some noise may be heard from
oil pump or gear. This noise is normal and does not affect any system.
1. Stop engine, and then turn steering wheel fully to right and left several times. CAUTION:
Do not allow steering fluid reservoir tank to go below the MIN level line. Check tank frequently and
add fluid as needed.
2. Run engine at idle speed. Turn steering wheel fully right and then fully left, hold for about three seconds. Then check for fluid leakage.
3. Repeat step 2 several times at about three second intervals. CAUTION:
Do not hold steering wheel in the locked position for more than 10 seconds. (There is the possibil-
ity that oil pump may be damaged.)
4. Check for air bubbles or cloudy fluid.
5. If air bubbles or cloudiness still exists, stop engine, perform steps 2 and 3 again until air bubbles or cloud- iness does not exist.
6. Stop engine, check fluid level.
LGIA0021E
SGIA0506E
Page 3328 of 3383
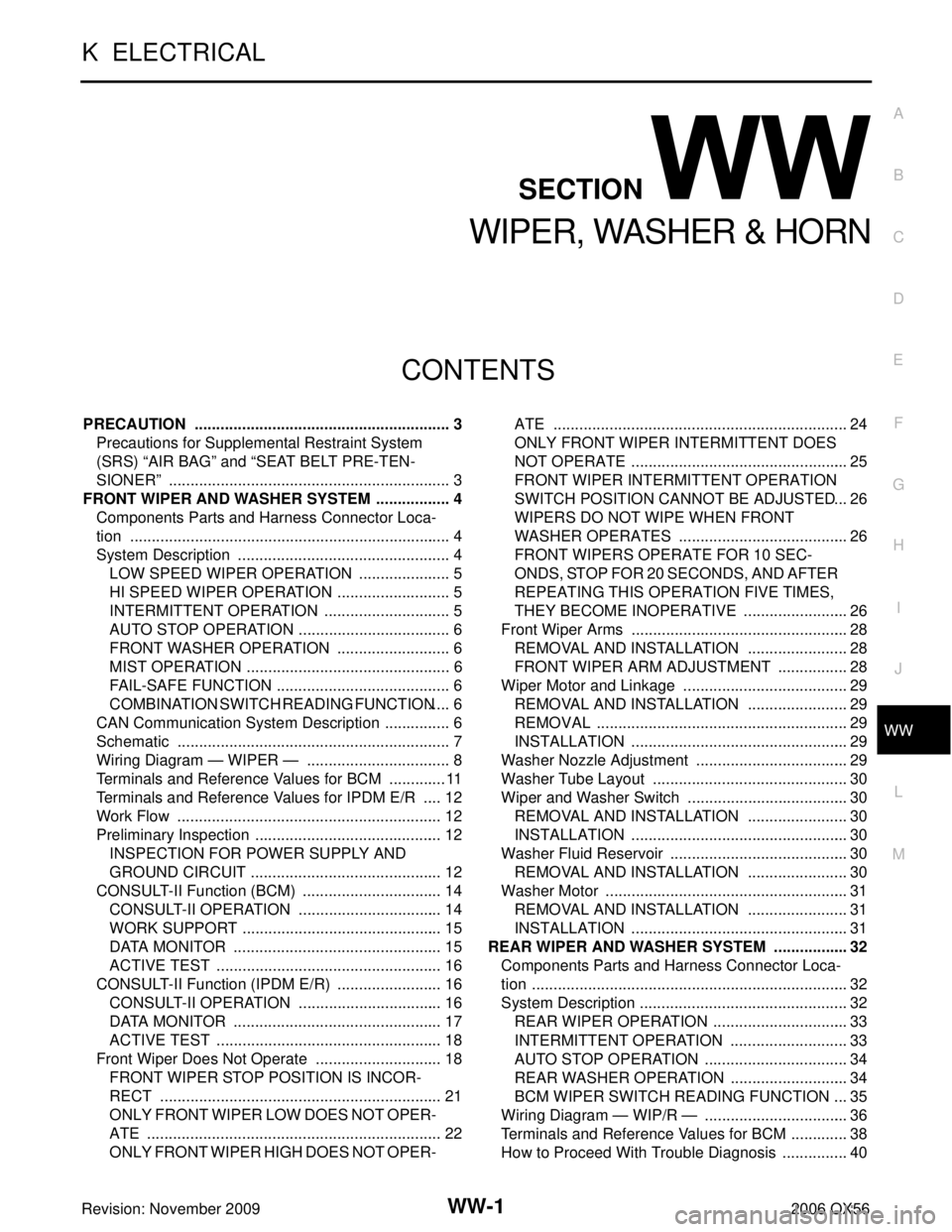
WW-1
WIPER, WASHER & HORN
K ELECTRICAL
CONTENTS
C
DE
F
G H
I
J
L
M
SECTION
A
B
WW
Revision: November 2009 2006 QX56
PRECAUTION .......................................................
..... 3
Precautions for Supplemental Restraint System
(SRS) “AIR BAG” and “SEAT BELT PRE-TEN-
SIONER” ............................................................. ..... 3
FRONT WIPER AND WASHER SYSTEM ............. ..... 4
Components Parts and Harness Connector Loca-
tion ...................................................................... ..... 4
System Description ............................................. ..... 4
LOW SPEED WIPER OPERATION ................. ..... 5
HI SPEED WIPER OPERATION ...................... ..... 5
INTERMITTENT OPERATION ......................... ..... 5
AUTO STOP OPERATION ............................... ..... 6
FRONT WASHER OPERATION ...................... ..... 6
MIST OPERATION ................................................ 6
FAIL-SAFE FUNCTION .................................... ..... 6
COMBINATION SWITCH READING FUNCTION ..... 6
CAN Communication System Description ........... ..... 6
Schematic ........................................................... ..... 7
Wiring Diagram — WIPER — ............................. ..... 8
Terminals and Reference Values for BCM .......... .... 11
Terminals and Reference Values for IPDM E/R .. ... 12
Work Flow ........................................................... ... 12
Preliminary Inspection ......................................... ... 12
INSPECTION FOR POWER SUPPLY AND
GROUND CIRCUIT .......................................... ... 12
CONSULT-II Function (BCM) .............................. ... 14
CONSULT-II OPERATION ............................... ... 14
WORK SUPPORT ............................................ ... 15
DATA MONITOR .............................................. ... 15
ACTIVE TEST .................................................. ... 16
CONSULT-II Function (IPDM E/R) ...................... ... 16
CONSULT-II OPERATION ............................... ... 16
DATA MONITOR .............................................. ... 17
ACTIVE TEST .................................................. ... 18
Front Wiper Does Not Operate ........................... ... 18
FRONT WIPER STOP POSITION IS INCOR-
RECT ............................................................... ... 21
ONLY FRONT WIPER LOW DOES NOT OPER-
ATE .................................................................. ... 22
ONLY FRONT WIPER HIGH DOES NOT OPER- ATE ..................................................................
... 24
ONLY FRONT WIPER INTERMITTENT DOES
NOT OPERATE ................................................ ... 25
FRONT WIPER INTERMITTENT OPERATION
SWITCH POSITION CANNOT BE ADJUSTED ... 26
WIPERS DO NOT WIPE WHEN FRONT
WASHER OPERATES ..................................... ... 26
FRONT WIPERS OPERATE FOR 10 SEC-
ONDS, STOP FOR 20 SECONDS, AND AFTER
REPEATING THIS OPERATION FIVE TIMES,
THEY BECOME INOPERATIVE ...................... ... 26
Front Wiper Arms ................................................ ... 28
REMOVAL AND INSTALLATION ..................... ... 28
FRONT WIPER ARM ADJUSTMENT .............. ... 28
Wiper Motor and Linkage .................................... ... 29
REMOVAL AND INSTALLATION ..................... ... 29
REMOVAL ........................................................ ... 29
INSTALLATION ................................................ ... 29
Washer Nozzle Adjustment ................................. ... 29
Washer Tube Layout ........................................... ... 30
Wiper and Washer Switch ................................... ... 30
REMOVAL AND INSTALLATION ..................... ... 30
INSTALLATION ................................................ ... 30
Washer Fluid Reservoir ....................................... ... 30
REMOVAL AND INSTALLATION ..................... ... 30
Washer Motor ...................................................... ... 31
REMOVAL AND INSTALLATION ..................... ... 31
INSTALLATION ................................................ ... 31
REAR WIPER AND WASHER SYSTEM ............... ... 32
Components Parts and Harness Connector Loca-
tion ....................................................................... ... 32
System Description .............................................. ... 32
REAR WIPER OPERATION ............................. ... 33
INTERMITTENT OPERATION ......................... ... 33
AUTO STOP OPERATION ............................... ... 34
REAR WASHER OPERATION ......................... ... 34
BCM WIPER SWITCH READING FUNCTION . ... 35
Wiring Diagram — WIP/R — .................................. 36
Terminals and Reference Values for BCM ........... ... 38
How to Proceed With Trouble Diagnosis ............. ... 40
Page 3329 of 3383
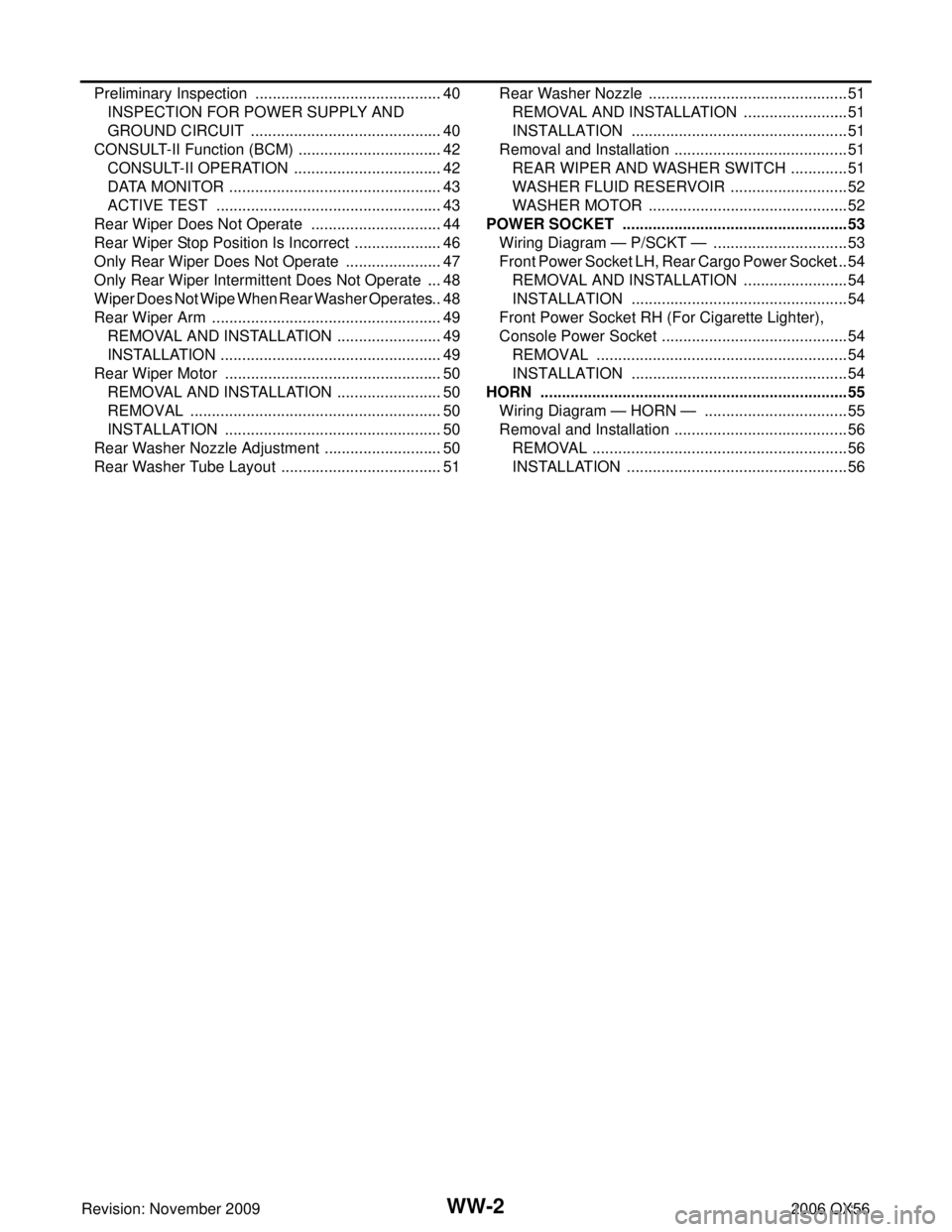
WW-2Revision: November 20092006 QX56
Preliminary Inspection .........................................
... 40
INSPECTION FOR POWER SUPPLY AND
GROUND CIRCUIT .......................................... ... 40
CONSULT-II Function (BCM) ............................... ... 42
CONSULT-II OPERATION ................................ ... 42
DATA MONITOR ............................................... ... 43
ACTIVE TEST .................................................. ... 43
Rear Wiper Does Not Operate ............................... 44
Rear Wiper Stop Position Is Incorrect .................. ... 46
Only Rear Wiper Does Not Operate ....................... 47
Only Rear Wiper Intermittent Does Not Operate . ... 48
Wiper Does Not Wipe When Rear Washer Operates ... 48
Rear Wiper Arm ................................................... ... 49
REMOVAL AND INSTALLATION ...................... ... 49
INSTALLATION ................................................. ... 49
Rear Wiper Motor ................................................... 50 REMOVAL AND INSTALLATION ...................... ... 50
REMOVAL ........................................................ ... 50
INSTALLATION ................................................ ... 50
Rear Washer Nozzle Adjustment ......................... ... 50
Rear Washer Tube Layout ................................... ... 51Rear Washer Nozzle ............................................
... 51
REMOVAL AND INSTALLATION ...................... ... 51
INSTALLATION ................................................ ... 51
Removal and Installation ...................................... ... 51
REAR WIPER AND WASHER SWITCH ........... ... 51
WASHER FLUID RESERVOIR ......................... ... 52
WASHER MOTOR ............................................ ... 52
POWER SOCKET .................................................. ... 53
Wiring Diagram — P/SCKT — ............................. ... 53
Front Power Socket LH, Rear Cargo Power Socket ... 54
REMOVAL AND INSTALLATION ...................... ... 54
INSTALLATION ................................................ ... 54
Front Power Socket RH (For Cigarette Lighter),
Console Power Socket ......................................... ... 54
REMOVAL ........................................................ ... 54
INSTALLATION ................................................ ... 54
HORN ..................................................................... ... 55
Wiring Diagram — HORN — ............................... ... 55
Removal and Installation ...................................... ... 56
REMOVAL ......................................................... ... 56
INSTALLATION ................................................. ... 56