drain bolt ISUZU AXIOM 2002 Service Repair Manual
[x] Cancel search | Manufacturer: ISUZU, Model Year: 2002, Model line: AXIOM, Model: ISUZU AXIOM 2002Pages: 2100, PDF Size: 19.35 MB
Page 19 of 2100
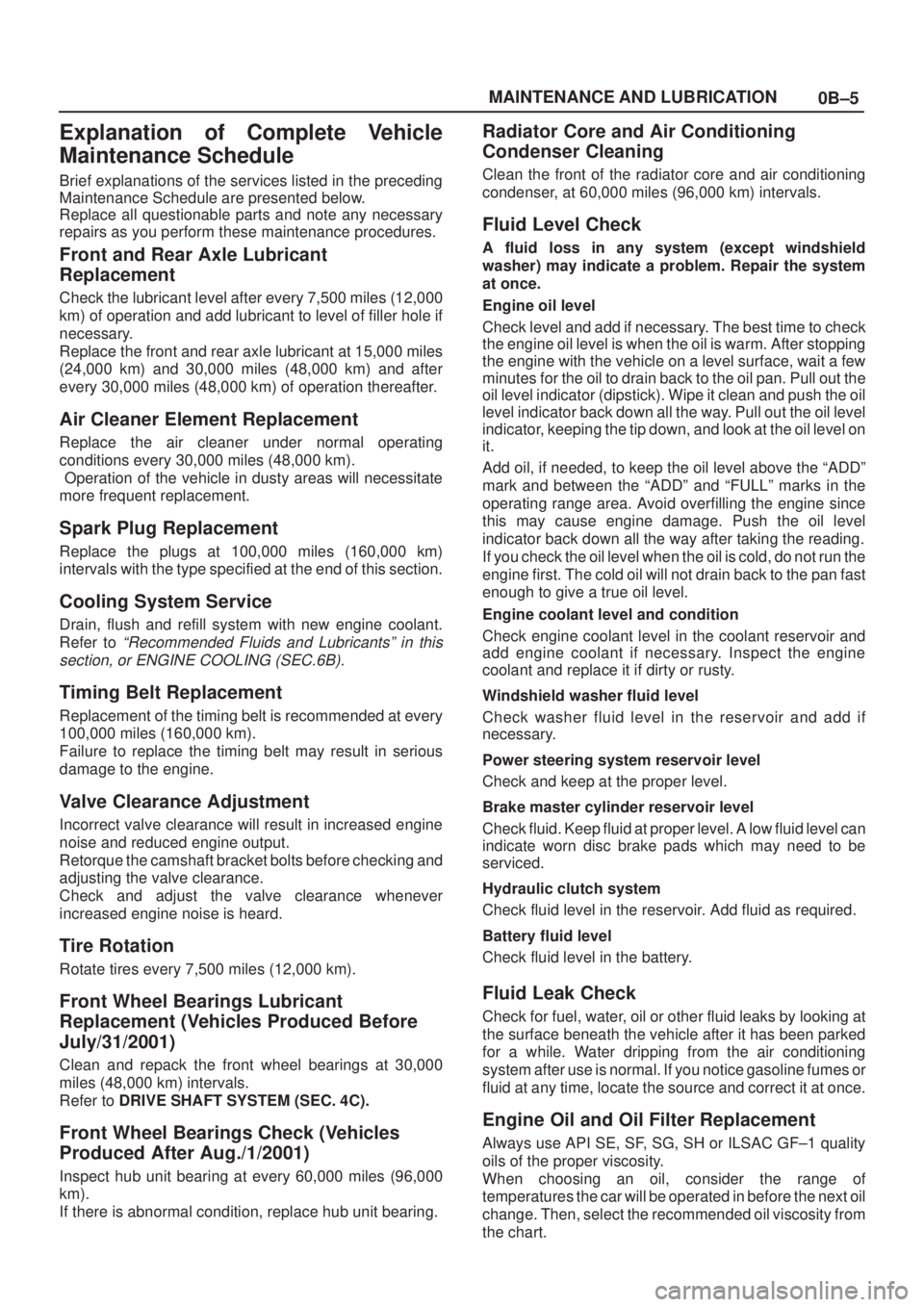
0B±5 MAINTENANCE AND LUBRICATION
Explanation of Complete Vehicle
Maintenance Schedule
Brief explanations of the services listed in the preceding
Maintenance Schedule are presented below.
Replace all questionable parts and note any necessary
repairs as you perform these maintenance procedures.
Front and Rear Axle Lubricant
Replacement
Check the lubricant level after every 7,500 miles (12,000
km) of operation and add lubricant to level of filler hole if
necessary.
Replace the front and rear axle lubricant at 15,000 miles
(24,000 km) and 30,000 miles (48,000 km) and after
every 30,000 miles (48,000 km) of operation thereafter.
Air Cleaner Element Replacement
Replace the air cleaner under normal operating
conditions every 30,000 miles (48,000 km).
Operation of the vehicle in dusty areas will necessitate
more frequent replacement.
Spark Plug Replacement
Replace the plugs at 100,000 miles (160,000 km)
intervals with the type specified at the end of this section.
Cooling System Service
Drain, flush and refill system with new engine coolant.
Refer to
ªRecommended Fluids and Lubricantsº in this
section, or ENGINE COOLING (SEC.6B).
Timing Belt Replacement
Replacement of the timing belt is recommended at every
100,000 miles (160,000 km).
Failure to replace the timing belt may result in serious
damage to the engine.
Valve Clearance Adjustment
Incorrect valve clearance will result in increased engine
noise and reduced engine output.
Retorque the camshaft bracket bolts before checking and
adjusting the valve clearance.
Check and adjust the valve clearance whenever
increased engine noise is heard.
Tire Rotation
Rotate tires every 7,500 miles (12,000 km).
Front Wheel Bearings Lubricant
Replacement (Vehicles Produced Before
July/31/2001)
Clean and repack the front wheel bearings at 30,000
miles (48,000 km) intervals.
Refer to DRIVE SHAFT SYSTEM (SEC. 4C).
Front Wheel Bearings Check (Vehicles
Produced After Aug./1/2001)
Inspect hub unit bearing at every 60,000 miles (96,000
km).
If there is abnormal condition, replace hub unit bearing.
Radiator Core and Air Conditioning
Condenser Cleaning
Clean the front of the radiator core and air conditioning
condenser, at 60,000 miles (96,000 km) intervals.
Fluid Level Check
A fluid loss in any system (except windshield
washer) may indicate a problem. Repair the system
at once.
Engine oil level
Check level and add if necessary. The best time to check
the engine oil level is when the oil is warm. After stopping
the engine with the vehicle on a level surface, wait a few
minutes for the oil to drain back to the oil pan. Pull out the
oil level indicator (dipstick). Wipe it clean and push the oil
level indicator back down all the way. Pull out the oil level
indicator, keeping the tip down, and look at the oil level on
it.
Add oil, if needed, to keep the oil level above the ªADDº
mark and between the ªADDº and ªFULLº marks in the
operating range area. Avoid overfilling the engine since
this may cause engine damage. Push the oil level
indicator back down all the way after taking the reading.
If you check the oil level when the oil is cold, do not run the
engine first. The cold oil will not drain back to the pan fast
enough to give a true oil level.
Engine coolant level and condition
Check engine coolant level in the coolant reservoir and
add engine coolant if necessary. Inspect the engine
coolant and replace it if dirty or rusty.
Windshield washer fluid level
Check washer fluid level in the reservoir and add if
necessary.
Power steering system reservoir level
Check and keep at the proper level.
Brake master cylinder reservoir level
Check fluid. Keep fluid at proper level. A low fluid level can
indicate worn disc brake pads which may need to be
serviced.
Hydraulic clutch system
Check fluid level in the reservoir. Add fluid as required.
Battery fluid level
Check fluid level in the battery.
Fluid Leak Check
Check for fuel, water, oil or other fluid leaks by looking at
the surface beneath the vehicle after it has been parked
for a while. Water dripping from the air conditioning
system after use is normal. If you notice gasoline fumes or
fluid at any time, locate the source and correct it at once.
Engine Oil and Oil Filter Replacement
Always use API SE, SF, SG, SH or ILSAC GF±1 quality
oils of the proper viscosity.
When choosing an oil, consider the range of
temperatures the car will be operated in before the next oil
change. Then, select the recommended oil viscosity from
the chart.
Page 20 of 2100
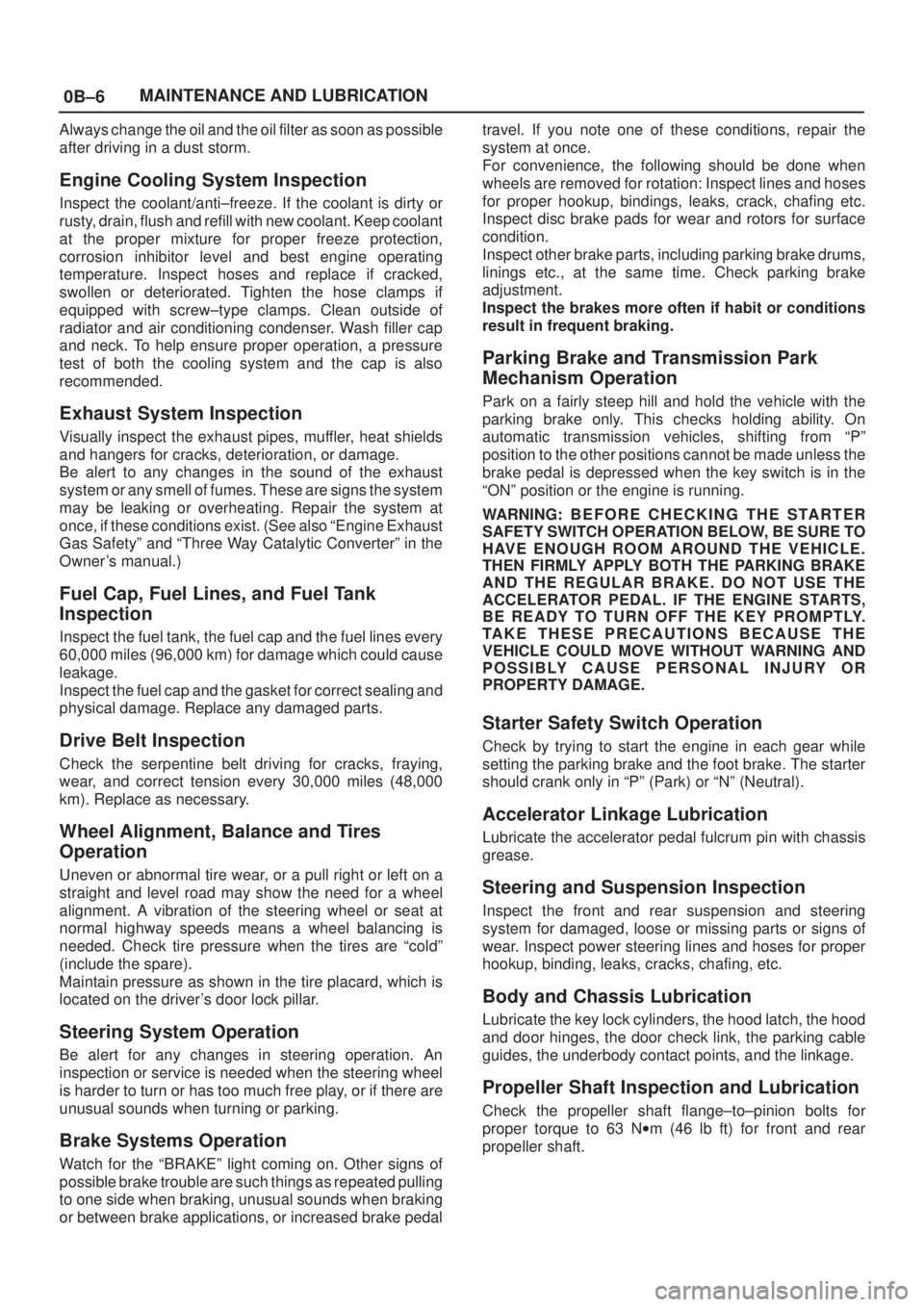
0B±6MAINTENANCE AND LUBRICATION
Always change the oil and the oil filter as soon as possible
after driving in a dust storm.
Engine Cooling System Inspection
Inspect the coolant/anti±freeze. If the coolant is dirty or
rusty, drain, flush and refill with new coolant. Keep coolant
at the proper mixture for proper freeze protection,
corrosion inhibitor level and best engine operating
temperature. Inspect hoses and replace if cracked,
swollen or deteriorated. Tighten the hose clamps if
equipped with screw±type clamps. Clean outside of
radiator and air conditioning condenser. Wash filler cap
and neck. To help ensure proper operation, a pressure
test of both the cooling system and the cap is also
recommended.
Exhaust System Inspection
Visually inspect the exhaust pipes, muffler, heat shields
and hangers for cracks, deterioration, or damage.
Be alert to any changes in the sound of the exhaust
system or any smell of fumes. These are signs the system
may be leaking or overheating. Repair the system at
once, if these conditions exist. (See also ªEngine Exhaust
Gas Safetyº and ªThree Way Catalytic Converterº in the
Owner's manual.)
Fuel Cap, Fuel Lines, and Fuel Tank
Inspection
Inspect the fuel tank, the fuel cap and the fuel lines every
60,000 miles (96,000 km) for damage which could cause
leakage.
Inspect the fuel cap and the gasket for correct sealing and
physical damage. Replace any damaged parts.
Drive Belt Inspection
Check the serpentine belt driving for cracks, fraying,
wear, and correct tension every 30,000 miles (48,000
km). Replace as necessary.
Wheel Alignment, Balance and Tires
Operation
Uneven or abnormal tire wear, or a pull right or left on a
straight and level road may show the need for a wheel
alignment. A vibration of the steering wheel or seat at
normal highway speeds means a wheel balancing is
needed. Check tire pressure when the tires are ªcoldº
(include the spare).
Maintain pressure as shown in the tire placard, which is
located on the driver's door lock pillar.
Steering System Operation
Be alert for any changes in steering operation. An
inspection or service is needed when the steering wheel
is harder to turn or has too much free play, or if there are
unusual sounds when turning or parking.
Brake Systems Operation
Watch for the ªBRAKEº light coming on. Other signs of
possible brake trouble are such things as repeated pulling
to one side when braking, unusual sounds when braking
or between brake applications, or increased brake pedaltravel. If you note one of these conditions, repair the
system at once.
For convenience, the following should be done when
wheels are removed for rotation: Inspect lines and hoses
for proper hookup, bindings, leaks, crack, chafing etc.
Inspect disc brake pads for wear and rotors for surface
condition.
Inspect other brake parts, including parking brake drums,
linings etc., at the same time. Check parking brake
adjustment.
Inspect the brakes more often if habit or conditions
result in frequent braking.
Parking Brake and Transmission Park
Mechanism Operation
Park on a fairly steep hill and hold the vehicle with the
parking brake only. This checks holding ability. On
automatic transmission vehicles, shifting from ªPº
position to the other positions cannot be made unless the
brake pedal is depressed when the key switch is in the
ªONº position or the engine is running.
WARNING: B E F O R E C H E C K I N G T H E S TA R T E R
SAFETY SWITCH OPERATION BELOW, BE SURE TO
HAVE ENOUGH ROOM AROUND THE VEHICLE.
THEN FIRMLY APPLY BOTH THE PARKING BRAKE
AND THE REGULAR BRAKE. DO NOT USE THE
ACCELERATOR PEDAL. IF THE ENGINE STARTS,
BE READY TO TURN OFF THE KEY PROMPTLY.
TAKE THESE PRECAUTIONS BECAUSE THE
VEHICLE COULD MOVE WITHOUT WARNING AND
POSSIBLY CAUSE PERSONAL INJURY OR
PROPERTY DAMAGE.
Starter Safety Switch Operation
Check by trying to start the engine in each gear while
setting the parking brake and the foot brake. The starter
should crank only in ªPº (Park) or ªNº (Neutral).
Accelerator Linkage Lubrication
Lubricate the accelerator pedal fulcrum pin with chassis
grease.
Steering and Suspension Inspection
Inspect the front and rear suspension and steering
system for damaged, loose or missing parts or signs of
wear. Inspect power steering lines and hoses for proper
hookup, binding, leaks, cracks, chafing, etc.
Body and Chassis Lubrication
Lubricate the key lock cylinders, the hood latch, the hood
and door hinges, the door check link, the parking cable
guides, the underbody contact points, and the linkage.
Propeller Shaft Inspection and Lubrication
Check the propeller shaft flange±to±pinion bolts for
proper torque to 63 Nwm (46 lb ft) for front and rear
propeller shaft.
Page 174 of 2100
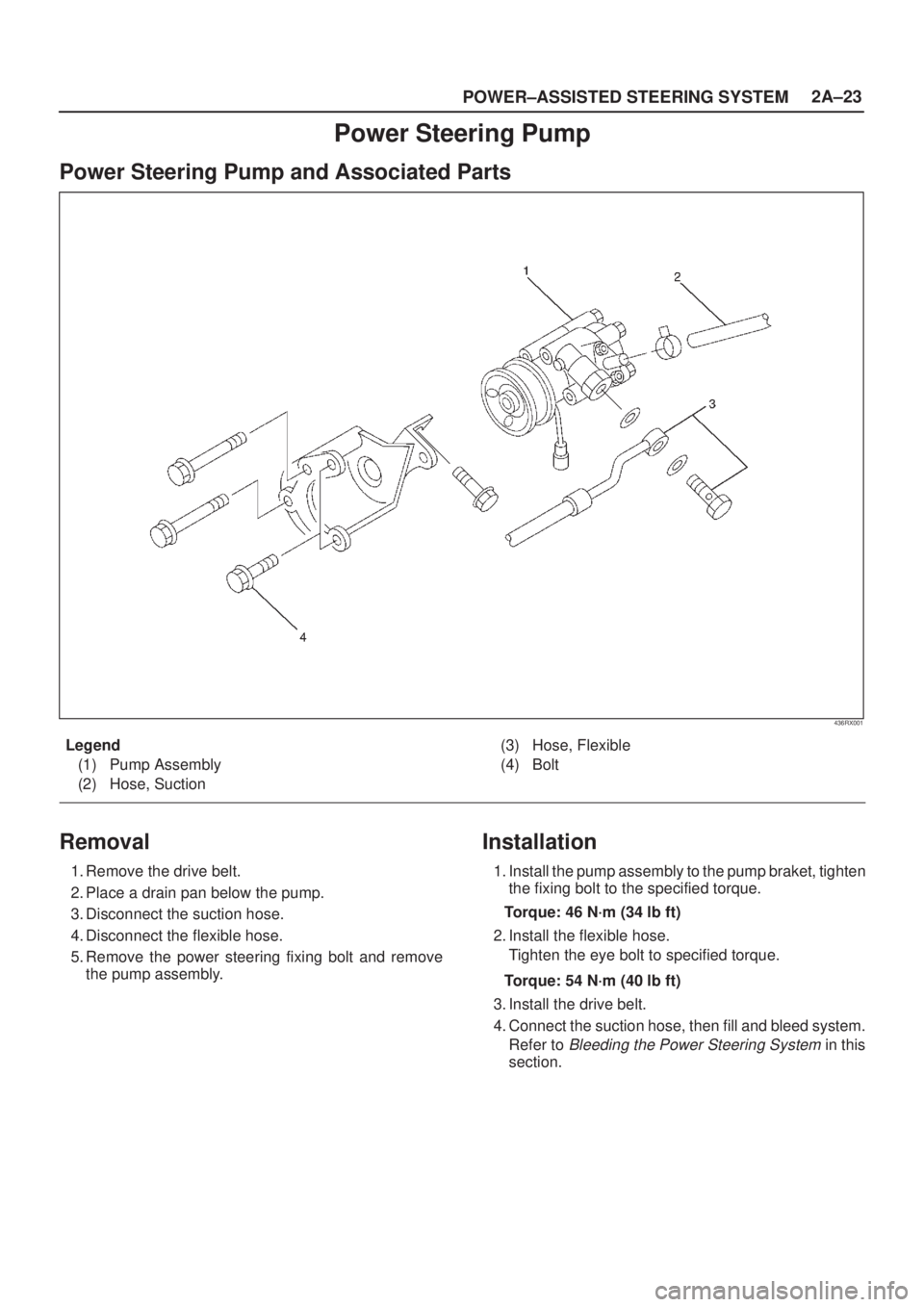
POWER±ASSISTED STEERING SYSTEM2A±23
Power Steering Pump
Power Steering Pump and Associated Parts
436RX001
Legend
(1) Pump Assembly
(2) Hose, Suction(3) Hose, Flexible
(4) Bolt
Removal
1. Remove the drive belt.
2. Place a drain pan below the pump.
3. Disconnect the suction hose.
4. Disconnect the flexible hose.
5. Remove the power steering fixing bolt and remove
the pump assembly.
Installation
1. Install the pump assembly to the pump braket, tighten
the fixing bolt to the specified torque.
Torque: 46 N´m (34 lb ft)
2. Install the flexible hose.
Tighten the eye bolt to specified torque.
Torque: 54 N´m (40 lb ft)
3. Install the drive belt.
4. Connect the suction hose, then fill and bleed system.
Refer to
Bleeding the Power Steering System in this
section.
Page 343 of 2100
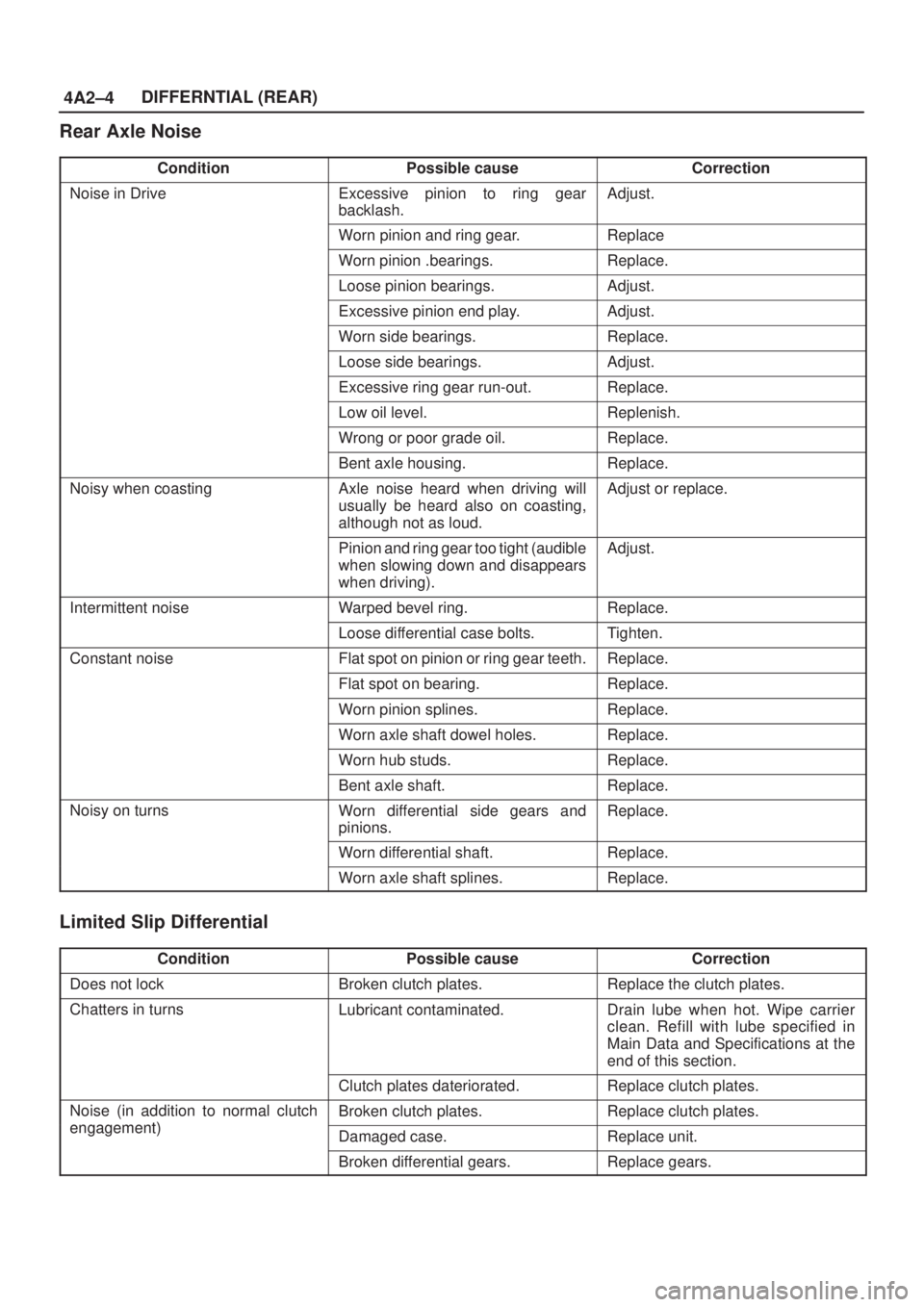
4A2±4DIFFERNTIAL (REAR)
Rear Axle Noise
ConditionPossible causeCorrection
Noise in DriveExcessive pinion to ring gear
backlash.Adjust.
Worn pinion and ring gear.Replace
Worn pinion .bearings.Replace.
Loose pinion bearings.Adjust.
Excessive pinion end play.Adjust.
Worn side bearings.Replace.
Loose side bearings.Adjust.
Excessive ring gear run-out.Replace.
Low oil level.Replenish.
Wrong or poor grade oil.Replace.
Bent axle housing.Replace.
Noisy when coastingAxle noise heard when driving will
usually be heard also on coasting,
although not as loud.Adjust or replace.
Pinion and ring gear too tight (audible
when slowing down and disappears
when driving).Adjust.
Intermittent noiseWarped bevel ring.Replace.
Loose differential case bolts.Tighten.
Constant noiseFlat spot on pinion or ring gear teeth.Replace.
Flat spot on bearing.Replace.
Worn pinion splines.Replace.
Worn axle shaft dowel holes.Replace.
Worn hub studs.Replace.
Bent axle shaft.Replace.
Noisy on turnsWorn differential side gears and
pinions.Replace.
Worn differential shaft.Replace.
Worn axle shaft splines.Replace.
Limited Slip Differential
ConditionPossible causeCorrection
Does not lockBroken clutch plates.Replace the clutch plates.
Chatters in turnsLubricant contaminated.Drain lube when hot. Wipe carrier
clean. Refill with lube specified in
Main Data and Specifications at the
end of this section.
Clutch plates dateriorated.Replace clutch plates.
Noise (in addition to normal clutch
engagement)
Broken clutch plates.Replace clutch plates.
engagement)Damaged case.Replace unit.
Broken differential gears.Replace gears.
Page 353 of 2100
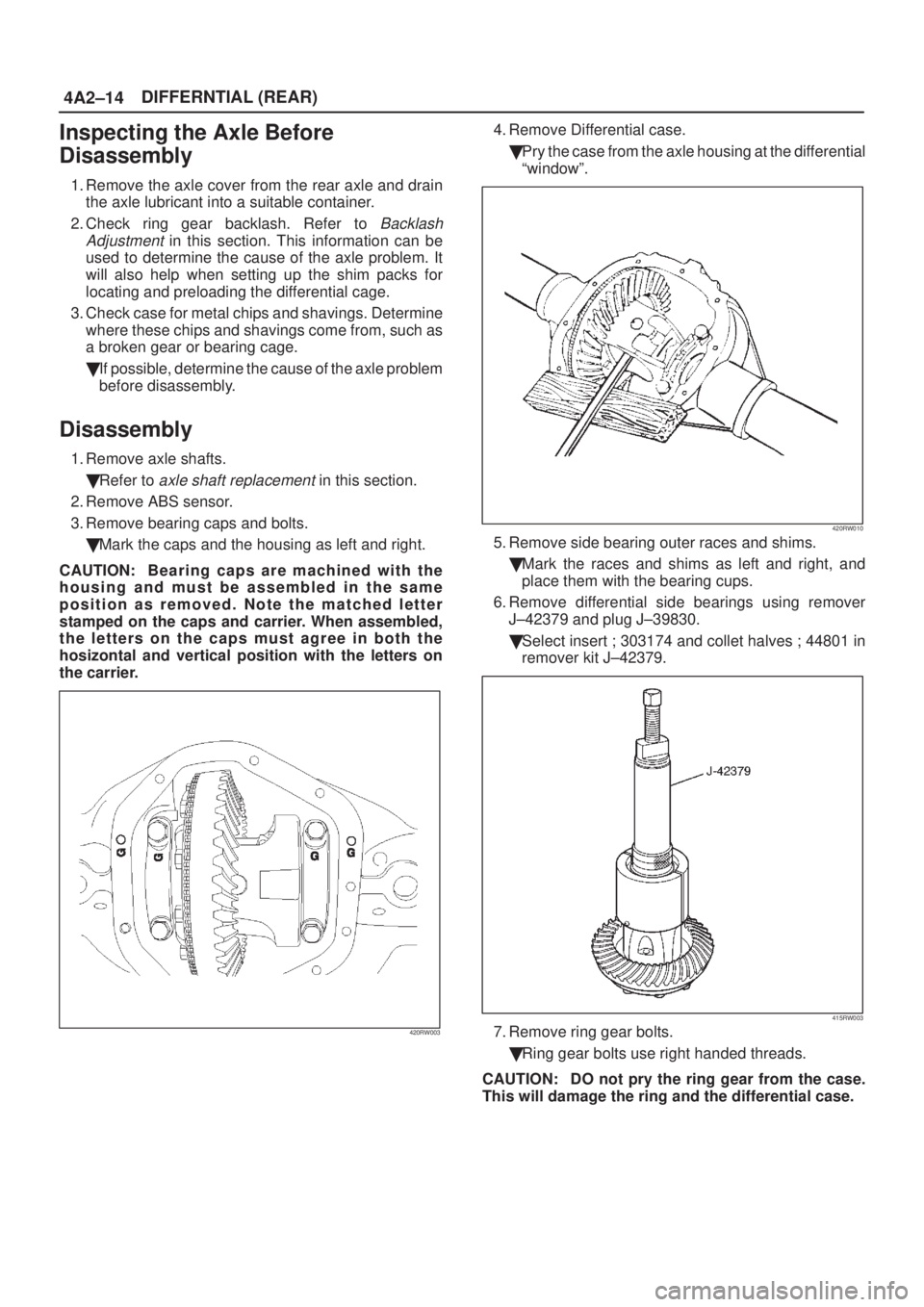
4A2±14DIFFERNTIAL (REAR)
Inspecting the Axle Before
Disassembly
1. Remove the axle cover from the rear axle and drain
the axle lubricant into a suitable container.
2. Check ring gear backlash. Refer to
Backlash
Adjustment
in this section. This information can be
used to determine the cause of the axle problem. It
will also help when setting up the shim packs for
locating and preloading the differential cage.
3. Check case for metal chips and shavings. Determine
where these chips and shavings come from, such as
a broken gear or bearing cage.
If possible, determine the cause of the axle problem
before disassembly.
Disassembly
1. Remove axle shafts.
Refer to
axle shaft replacement in this section.
2. Remove ABS sensor.
3. Remove bearing caps and bolts.
Mark the caps and the housing as left and right.
CAUTION: Be a ri n g c a p s a re machined with the
housing and must be assembled in the same
position as removed. Note the matched letter
stamped on the caps and carrier. When assembled,
the letters on the caps must agree in both the
hosizontal and vertical position with the letters on
the carrier.
420RW003
4. Remove Differential case.
Pry the case from the axle housing at the differential
ªwindowº.
420RW010
5. Remove side bearing outer races and shims.
Mark the races and shims as left and right, and
place them with the bearing cups.
6. Remove differential side bearings using remover
J±42379 and plug J±39830.
Select insert ; 303174 and collet halves ; 44801 in
remover kit J±42379.
415RW003
7. Remove ring gear bolts.
Ring gear bolts use right handed threads.
CAUTION: DO not pry the ring gear from the case.
This will damage the ring and the differential case.
Page 517 of 2100
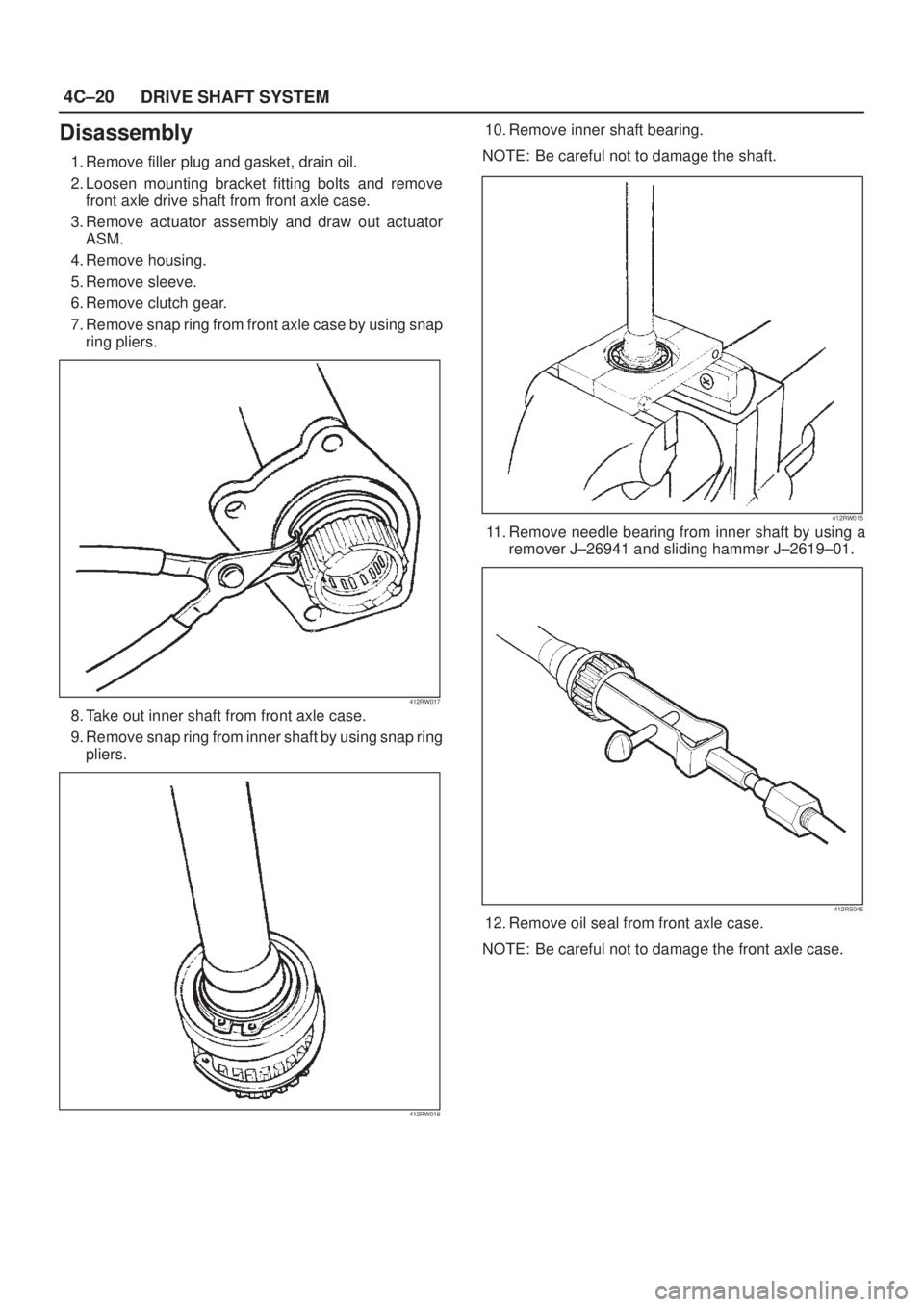
4C±20
DRIVE SHAFT SYSTEM
Disassembly
1. Remove filler plug and gasket, drain oil.
2. Loosen mounting bracket fitting bolts and remove
front axle drive shaft from front axle case.
3. Remove actuator assembly and draw out actuator
ASM.
4. Remove housing.
5. Remove sleeve.
6. Remove clutch gear.
7. Remove snap ring from front axle case by using snap
ring pliers.
412RW017
8. Take out inner shaft from front axle case.
9. Remove snap ring from inner shaft by using snap ring
pliers.
412RW016
10. Remove inner shaft bearing.
NOTE: Be careful not to damage the shaft.
412RW015
11. Remove needle bearing from inner shaft by using a
remover J±26941 and sliding hammer J±2619±01.
412RS045
12. Remove oil seal from front axle case.
NOTE: Be careful not to damage the front axle case.
Page 556 of 2100
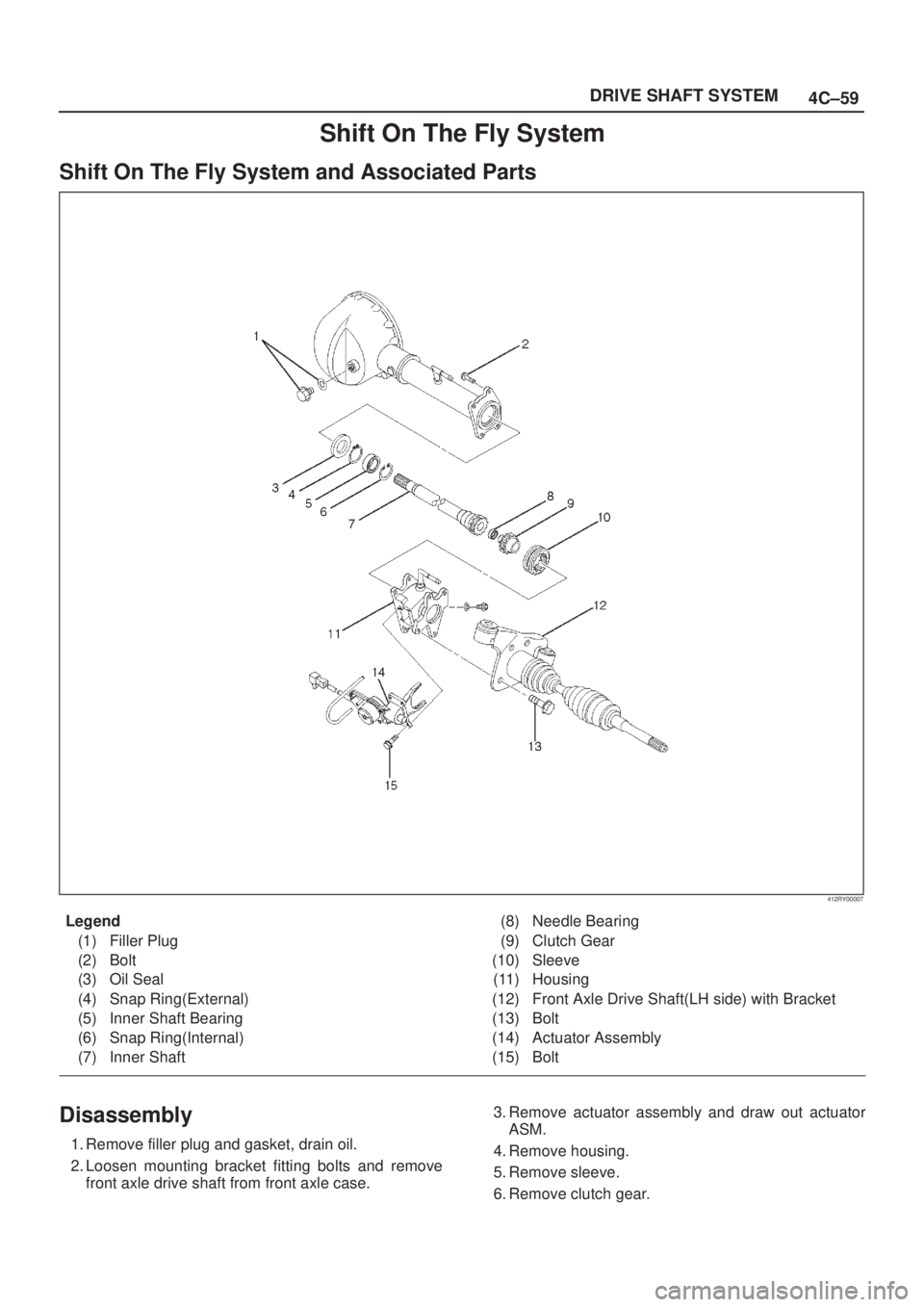
4C±59 DRIVE SHAFT SYSTEM
Shift On The Fly System
Shift On The Fly System and Associated Parts
412RY00007
Legend
(1) Filler Plug
(2) Bolt
(3) Oil Seal
(4) Snap Ring(External)
(5) Inner Shaft Bearing
(6) Snap Ring(Internal)
(7) Inner Shaft(8) Needle Bearing
(9) Clutch Gear
(10) Sleeve
(11) Housing
(12) Front Axle Drive Shaft(LH side) with Bracket
(13) Bolt
(14) Actuator Assembly
(15) Bolt
Disassembly
1. Remove filler plug and gasket, drain oil.
2. Loosen mounting bracket fitting bolts and remove
front axle drive shaft from front axle case.3. Remove actuator assembly and draw out actuator
ASM.
4. Remove housing.
5. Remove sleeve.
6. Remove clutch gear.
Page 593 of 2100
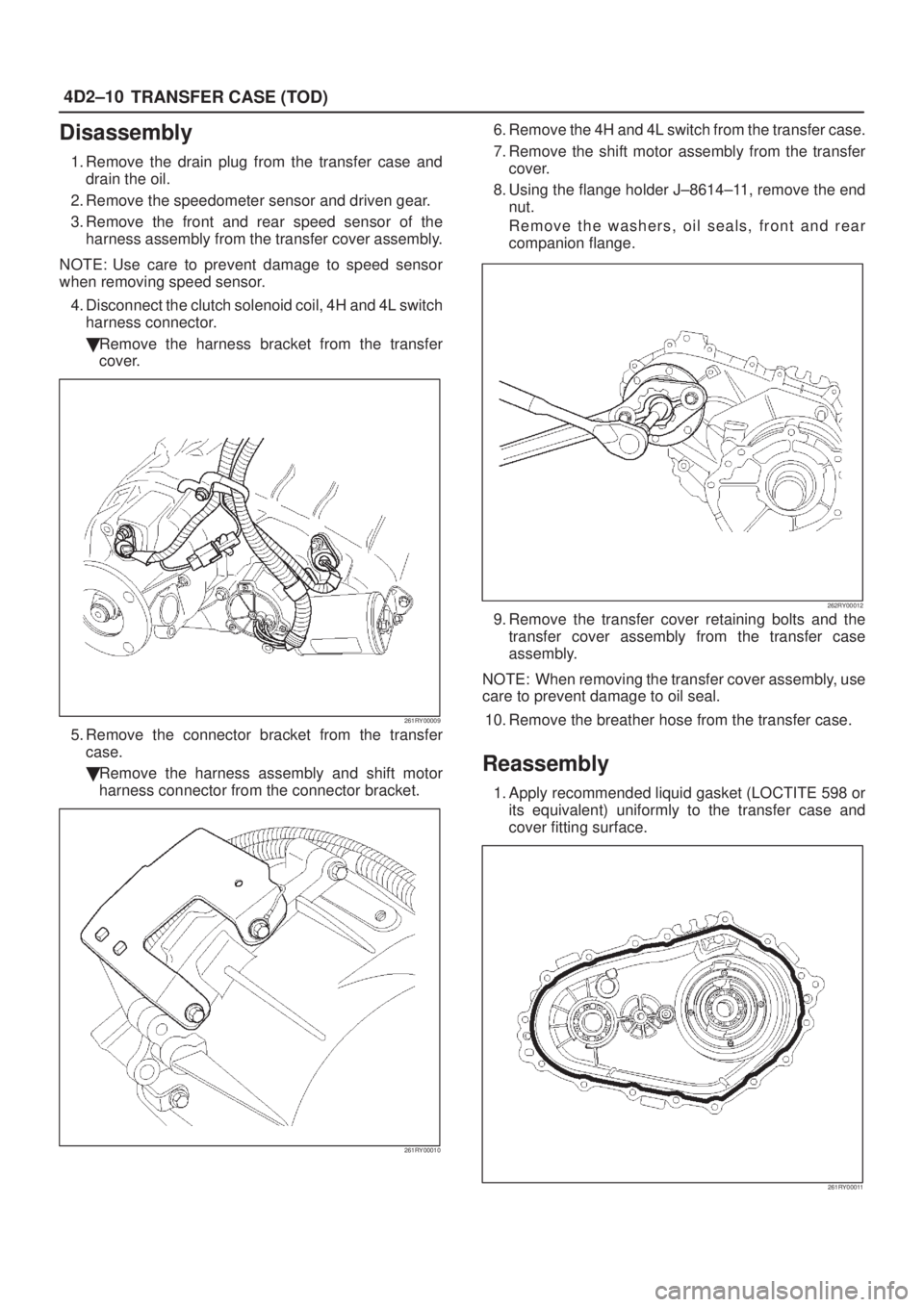
4D2±10
TRANSFER CASE (TOD)
Disassembly
1. Remove the drain plug from the transfer case and
drain the oil.
2. Remove the speedometer sensor and driven gear.
3. Remove the front and rear speed sensor of the
harness assembly from the transfer cover assembly.
NOTE: Use care to prevent damage to speed sensor
when removing speed sensor.
4. Disconnect the clutch solenoid coil, 4H and 4L switch
harness connector.
Remove the harness bracket from the transfer
cover.
261RY00009
5. Remove the connector bracket from the transfer
case.
Remove the harness assembly and shift motor
harness connector from the connector bracket.
261RY00010
6. Remove the 4H and 4L switch from the transfer case.
7. Remove the shift motor assembly from the transfer
cover.
8. Using the flange holder J±8614±11, remove the end
nut.
Remove the washers, oil seals, front and rear
companion flange.
262RY00012
9. Remove the transfer cover retaining bolts and the
transfer cover assembly from the transfer case
assembly.
NOTE: When removing the transfer cover assembly, use
care to prevent damage to oil seal.
10. Remove the breather hose from the transfer case.
Reassembly
1. Apply recommended liquid gasket (LOCTITE 598 or
its equivalent) uniformly to the transfer case and
cover fitting surface.
261RY00011
Page 717 of 2100
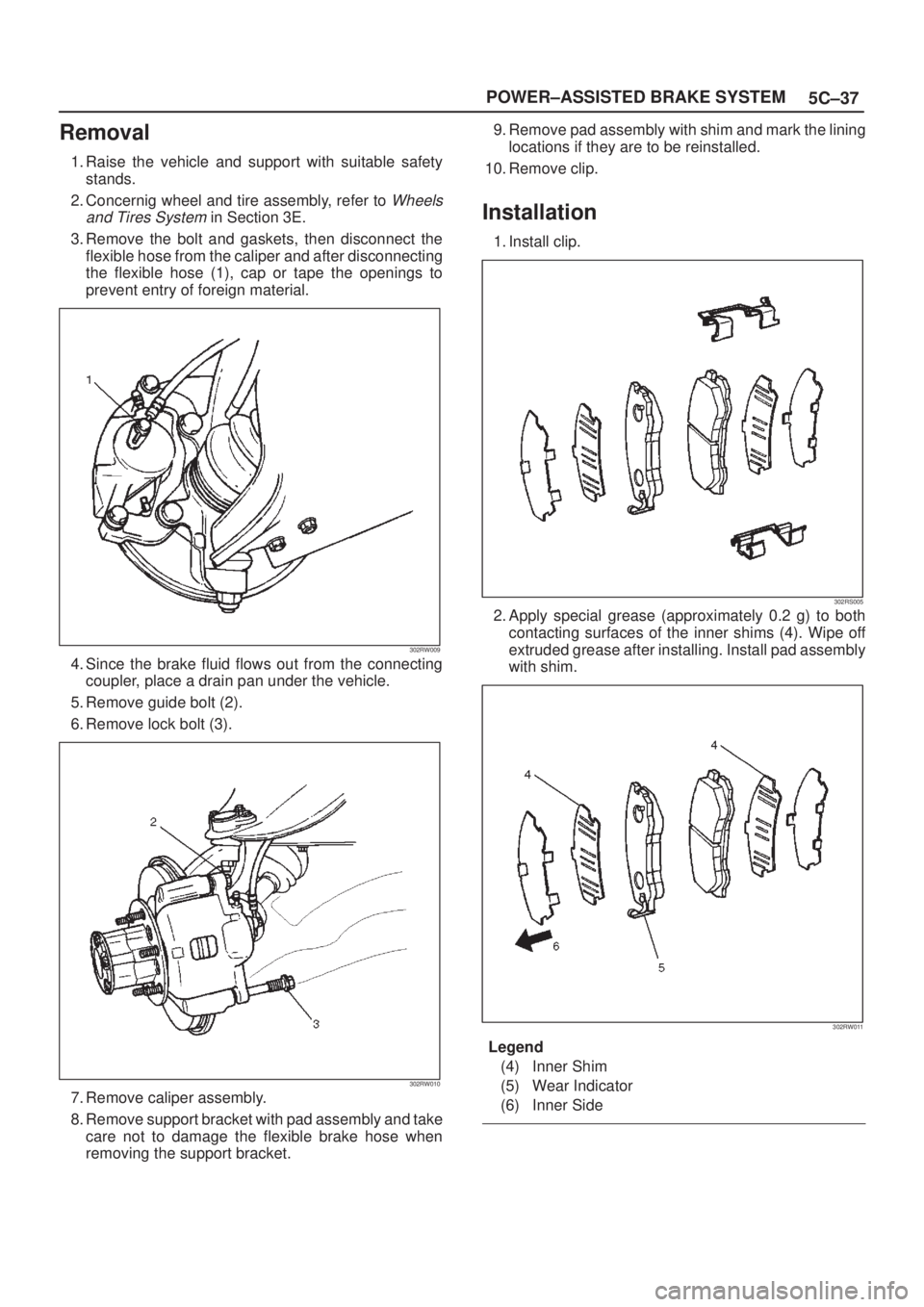
5C±37 POWER±ASSISTED BRAKE SYSTEM
Removal
1. Raise the vehicle and support with suitable safety
stands.
2. Concernig wheel and tire assembly, refer to
Wheels
and Tires System
in Section 3E.
3. Remove the bolt and gaskets, then disconnect the
flexible hose from the caliper and after disconnecting
the flexible hose (1), cap or tape the openings to
prevent entry of foreign material.
302RW009
4. Since the brake fluid flows out from the connecting
coupler, place a drain pan under the vehicle.
5. Remove guide bolt (2).
6. Remove lock bolt (3).
302RW010
7. Remove caliper assembly.
8. Remove support bracket with pad assembly and take
care not to damage the flexible brake hose when
removing the support bracket.9. Remove pad assembly with shim and mark the lining
locations if they are to be reinstalled.
10. Remove clip.
Installation
1. Install clip.
302RS005
2. Apply special grease (approximately 0.2 g) to both
contacting surfaces of the inner shims (4). Wipe off
extruded grease after installing. Install pad assembly
with shim.
302RW011
Legend
(4) Inner Shim
(5) Wear Indicator
(6) Inner Side
Page 728 of 2100
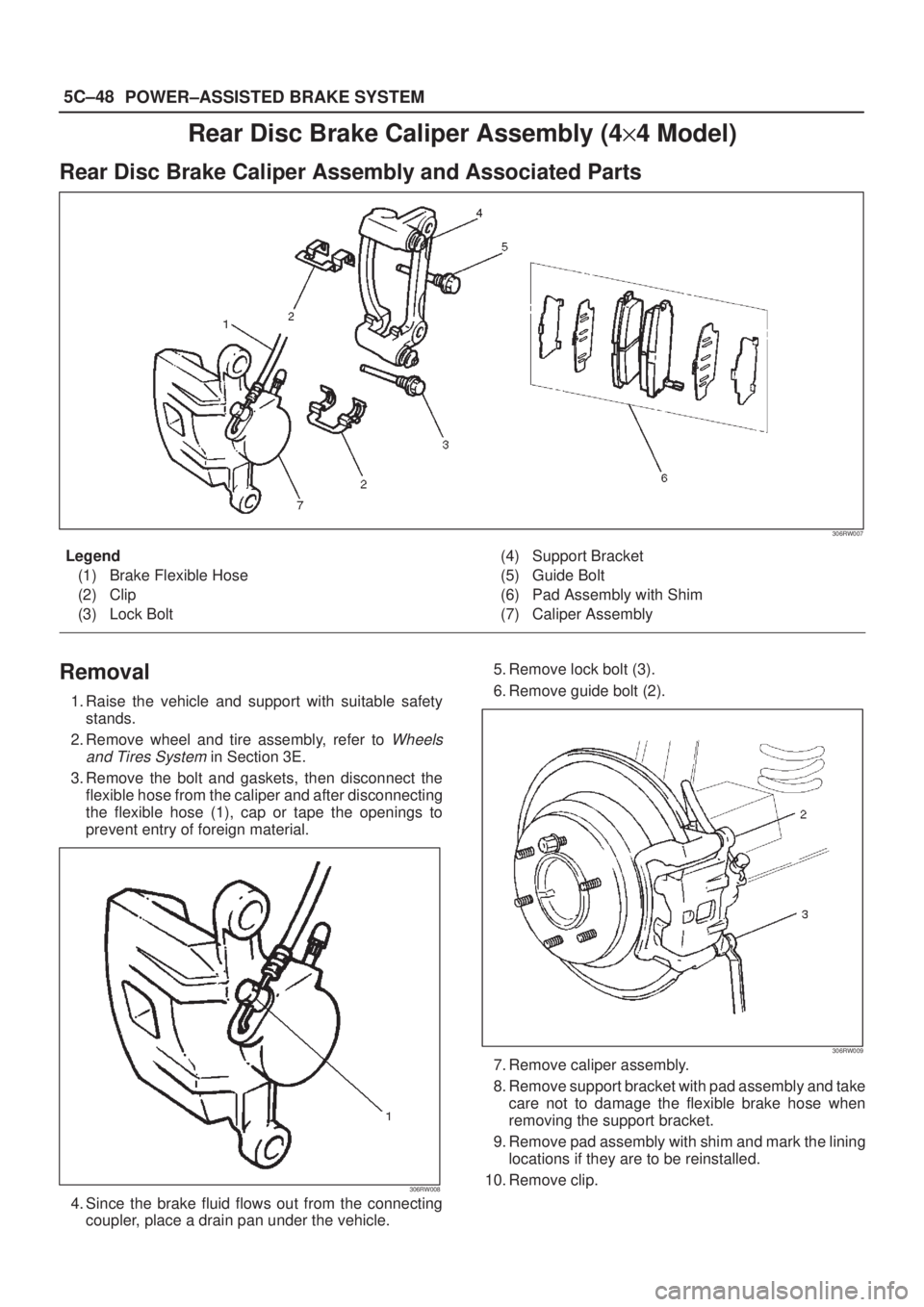
5C±48
POWER±ASSISTED BRAKE SYSTEM
Rear Disc Brake Caliper Assembly (4y4 Model)
Rear Disc Brake Caliper Assembly and Associated Parts
306RW007
Legend
(1) Brake Flexible Hose
(2) Clip
(3) Lock Bolt(4) Support Bracket
(5) Guide Bolt
(6) Pad Assembly with Shim
(7) Caliper Assembly
Removal
1. Raise the vehicle and support with suitable safety
stands.
2. Remove wheel and tire assembly, refer to
Wheels
and Tires System
in Section 3E.
3. Remove the bolt and gaskets, then disconnect the
flexible hose from the caliper and after disconnecting
the flexible hose (1), cap or tape the openings to
prevent entry of foreign material.
306RW008
4. Since the brake fluid flows out from the connecting
coupler, place a drain pan under the vehicle.5. Remove lock bolt (3).
6. Remove guide bolt (2).
306RW009
7. Remove caliper assembly.
8. Remove support bracket with pad assembly and take
care not to damage the flexible brake hose when
removing the support bracket.
9. Remove pad assembly with shim and mark the lining
locations if they are to be reinstalled.
10. Remove clip.