warning light ISUZU AXIOM 2002 Service Repair Manual
[x] Cancel search | Manufacturer: ISUZU, Model Year: 2002, Model line: AXIOM, Model: ISUZU AXIOM 2002Pages: 2100, PDF Size: 19.35 MB
Page 2 of 2100
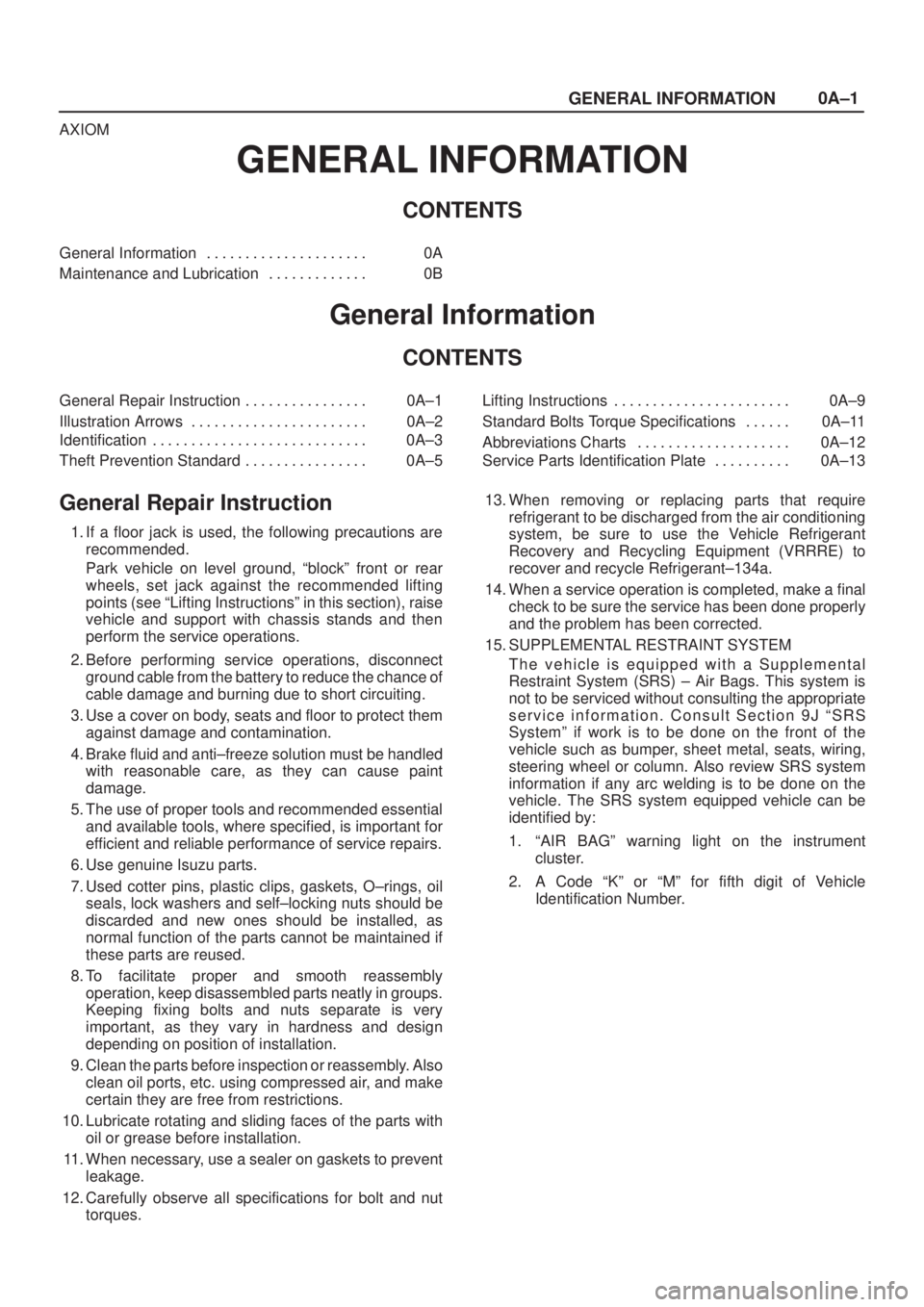
0A±1
GENERAL INFORMATION
AXIOM
GENERAL INFORMATION
CONTENTS
General Information 0A. . . . . . . . . . . . . . . . . . . . .
Maintenance and Lubrication 0B. . . . . . . . . . . . .
General Information
CONTENTS
General Repair Instruction 0A±1. . . . . . . . . . . . . . . .
Illustration Arrows 0A±2. . . . . . . . . . . . . . . . . . . . . . .
Identification 0A±3. . . . . . . . . . . . . . . . . . . . . . . . . . . .
Theft Prevention Standard 0A±5. . . . . . . . . . . . . . . . Lifting Instructions 0A±9. . . . . . . . . . . . . . . . . . . . . . .
Standard Bolts Torque Specifications 0A±11. . . . . .
Abbreviations Charts 0A±12. . . . . . . . . . . . . . . . . . . .
Service Parts Identification Plate 0A±13. . . . . . . . . .
General Repair Instruction
1. If a floor jack is used, the following precautions are
recommended.
Park vehicle on level ground, ªblockº front or rear
wheels, set jack against the recommended lifting
points (see ªLifting Instructionsº in this section), raise
vehicle and support with chassis stands and then
perform the service operations.
2. Before performing service operations, disconnect
ground cable from the battery to reduce the chance of
cable damage and burning due to short circuiting.
3. Use a cover on body, seats and floor to protect them
against damage and contamination.
4. Brake fluid and anti±freeze solution must be handled
with reasonable care, as they can cause paint
damage.
5. The use of proper tools and recommended essential
and available tools, where specified, is important for
efficient and reliable performance of service repairs.
6. Use genuine Isuzu parts.
7. Used cotter pins, plastic clips, gaskets, O±rings, oil
seals, lock washers and self±locking nuts should be
discarded and new ones should be installed, as
normal function of the parts cannot be maintained if
these parts are reused.
8. To facilitate proper and smooth reassembly
operation, keep disassembled parts neatly in groups.
Keeping fixing bolts and nuts separate is very
important, as they vary in hardness and design
depending on position of installation.
9. Clean the parts before inspection or reassembly. Also
clean oil ports, etc. using compressed air, and make
certain they are free from restrictions.
10. Lubricate rotating and sliding faces of the parts with
oil or grease before installation.
11. When necessary, use a sealer on gaskets to prevent
leakage.
12. Carefully observe all specifications for bolt and nut
torques.13. When removing or replacing parts that require
refrigerant to be discharged from the air conditioning
system, be sure to use the Vehicle Refrigerant
Recovery and Recycling Equipment (VRRRE) to
recover and recycle Refrigerant±134a.
14. When a service operation is completed, make a final
check to be sure the service has been done properly
and the problem has been corrected.
15. SUPPLEMENTAL RESTRAINT SYSTEM
The vehicle is equipped with a Supplemental
Restraint System (SRS) ± Air Bags. This system is
not to be serviced without consulting the appropriate
service information. Consult Section 9J ªSRS
Systemº if work is to be done on the front of the
vehicle such as bumper, sheet metal, seats, wiring,
steering wheel or column. Also review SRS system
information if any arc welding is to be done on the
vehicle. The SRS system equipped vehicle can be
identified by:
1. ªAIR BAGº warning light on the instrument
cluster.
2. A Code ªKº or ªMº for fifth digit of Vehicle
Identification Number.
Page 20 of 2100
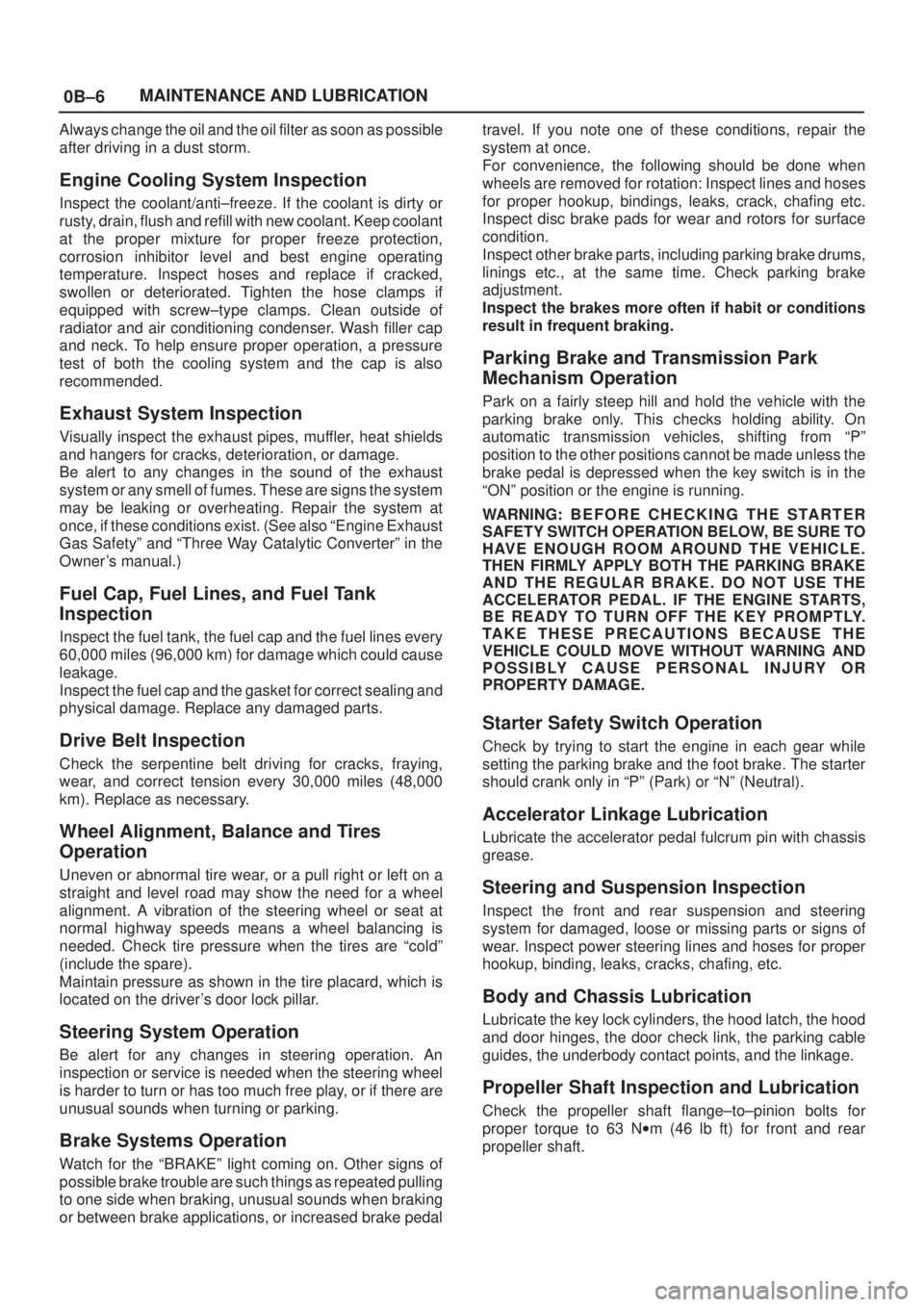
0B±6MAINTENANCE AND LUBRICATION
Always change the oil and the oil filter as soon as possible
after driving in a dust storm.
Engine Cooling System Inspection
Inspect the coolant/anti±freeze. If the coolant is dirty or
rusty, drain, flush and refill with new coolant. Keep coolant
at the proper mixture for proper freeze protection,
corrosion inhibitor level and best engine operating
temperature. Inspect hoses and replace if cracked,
swollen or deteriorated. Tighten the hose clamps if
equipped with screw±type clamps. Clean outside of
radiator and air conditioning condenser. Wash filler cap
and neck. To help ensure proper operation, a pressure
test of both the cooling system and the cap is also
recommended.
Exhaust System Inspection
Visually inspect the exhaust pipes, muffler, heat shields
and hangers for cracks, deterioration, or damage.
Be alert to any changes in the sound of the exhaust
system or any smell of fumes. These are signs the system
may be leaking or overheating. Repair the system at
once, if these conditions exist. (See also ªEngine Exhaust
Gas Safetyº and ªThree Way Catalytic Converterº in the
Owner's manual.)
Fuel Cap, Fuel Lines, and Fuel Tank
Inspection
Inspect the fuel tank, the fuel cap and the fuel lines every
60,000 miles (96,000 km) for damage which could cause
leakage.
Inspect the fuel cap and the gasket for correct sealing and
physical damage. Replace any damaged parts.
Drive Belt Inspection
Check the serpentine belt driving for cracks, fraying,
wear, and correct tension every 30,000 miles (48,000
km). Replace as necessary.
Wheel Alignment, Balance and Tires
Operation
Uneven or abnormal tire wear, or a pull right or left on a
straight and level road may show the need for a wheel
alignment. A vibration of the steering wheel or seat at
normal highway speeds means a wheel balancing is
needed. Check tire pressure when the tires are ªcoldº
(include the spare).
Maintain pressure as shown in the tire placard, which is
located on the driver's door lock pillar.
Steering System Operation
Be alert for any changes in steering operation. An
inspection or service is needed when the steering wheel
is harder to turn or has too much free play, or if there are
unusual sounds when turning or parking.
Brake Systems Operation
Watch for the ªBRAKEº light coming on. Other signs of
possible brake trouble are such things as repeated pulling
to one side when braking, unusual sounds when braking
or between brake applications, or increased brake pedaltravel. If you note one of these conditions, repair the
system at once.
For convenience, the following should be done when
wheels are removed for rotation: Inspect lines and hoses
for proper hookup, bindings, leaks, crack, chafing etc.
Inspect disc brake pads for wear and rotors for surface
condition.
Inspect other brake parts, including parking brake drums,
linings etc., at the same time. Check parking brake
adjustment.
Inspect the brakes more often if habit or conditions
result in frequent braking.
Parking Brake and Transmission Park
Mechanism Operation
Park on a fairly steep hill and hold the vehicle with the
parking brake only. This checks holding ability. On
automatic transmission vehicles, shifting from ªPº
position to the other positions cannot be made unless the
brake pedal is depressed when the key switch is in the
ªONº position or the engine is running.
WARNING: B E F O R E C H E C K I N G T H E S TA R T E R
SAFETY SWITCH OPERATION BELOW, BE SURE TO
HAVE ENOUGH ROOM AROUND THE VEHICLE.
THEN FIRMLY APPLY BOTH THE PARKING BRAKE
AND THE REGULAR BRAKE. DO NOT USE THE
ACCELERATOR PEDAL. IF THE ENGINE STARTS,
BE READY TO TURN OFF THE KEY PROMPTLY.
TAKE THESE PRECAUTIONS BECAUSE THE
VEHICLE COULD MOVE WITHOUT WARNING AND
POSSIBLY CAUSE PERSONAL INJURY OR
PROPERTY DAMAGE.
Starter Safety Switch Operation
Check by trying to start the engine in each gear while
setting the parking brake and the foot brake. The starter
should crank only in ªPº (Park) or ªNº (Neutral).
Accelerator Linkage Lubrication
Lubricate the accelerator pedal fulcrum pin with chassis
grease.
Steering and Suspension Inspection
Inspect the front and rear suspension and steering
system for damaged, loose or missing parts or signs of
wear. Inspect power steering lines and hoses for proper
hookup, binding, leaks, cracks, chafing, etc.
Body and Chassis Lubrication
Lubricate the key lock cylinders, the hood latch, the hood
and door hinges, the door check link, the parking cable
guides, the underbody contact points, and the linkage.
Propeller Shaft Inspection and Lubrication
Check the propeller shaft flange±to±pinion bolts for
proper torque to 63 Nwm (46 lb ft) for front and rear
propeller shaft.
Page 183 of 2100
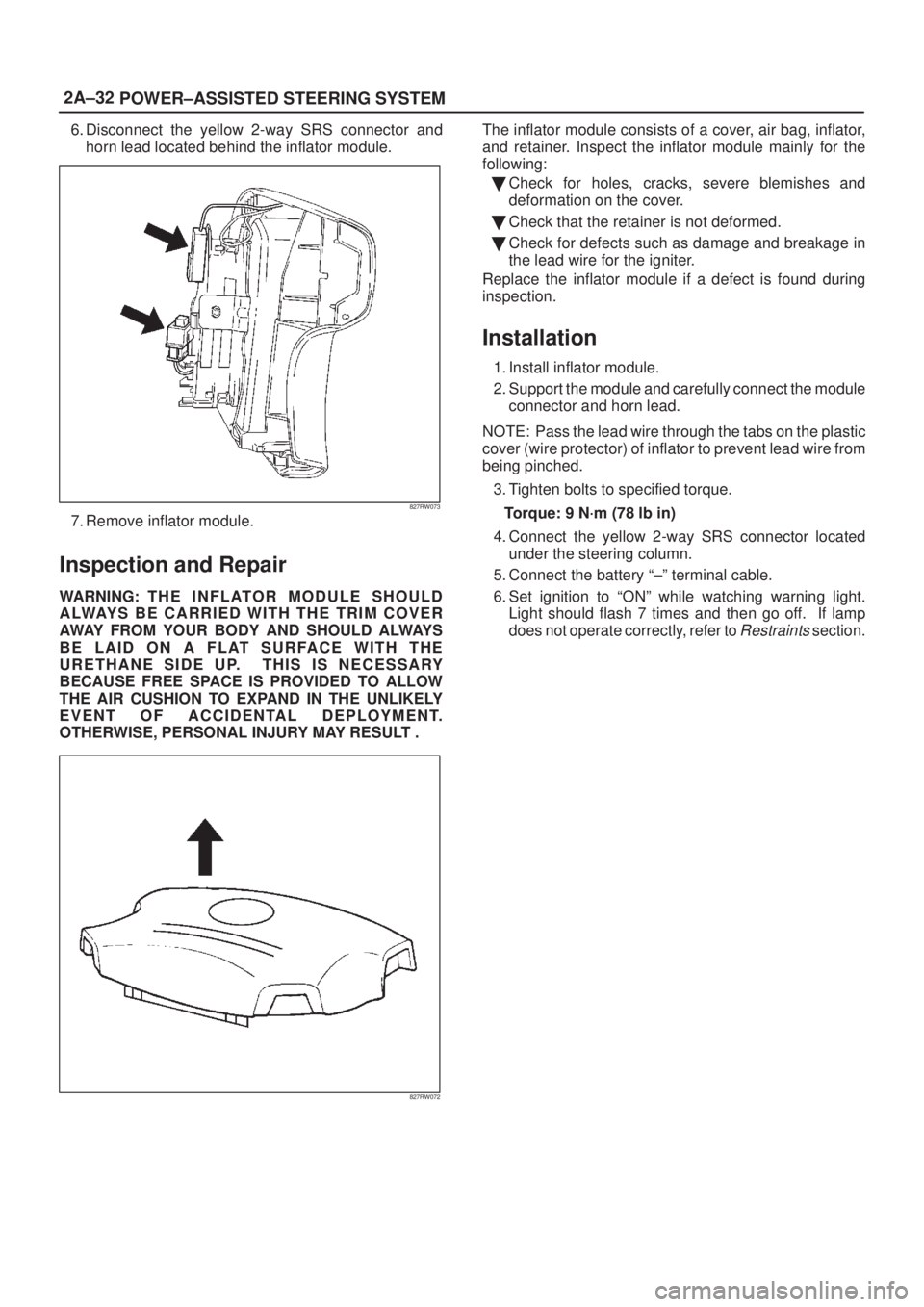
2A±32
POWER±ASSISTED STEERING SYSTEM
6. Disconnect the yellow 2-way SRS connector and
horn lead located behind the inflator module.
827RW073
7. Remove inflator module.
Inspection and Repair
WARNING: T H E I N F L AT O R M O D U L E S H O U L D
ALWAYS BE CARRIED WITH THE TRIM COVER
AWAY FROM YOUR BODY AND SHOULD ALWAYS
BE LAID ON A FLAT SURFACE WITH THE
URETHANE SIDE UP. THIS IS NECESSARY
BECAUSE FREE SPACE IS PROVIDED TO ALLOW
THE AIR CUSHION TO EXPAND IN THE UNLIKELY
EVENT OF ACCIDENTAL DEPLOYMENT.
OTHERWISE, PERSONAL INJURY MAY RESULT .
827RW072
The inflator module consists of a cover, air bag, inflator,
and retainer. Inspect the inflator module mainly for the
following:
Check for holes, cracks, severe blemishes and
deformation on the cover.
Check that the retainer is not deformed.
Check for defects such as damage and breakage in
the lead wire for the igniter.
Replace the inflator module if a defect is found during
inspection.
Installation
1. Install inflator module.
2. Support the module and carefully connect the module
connector and horn lead.
NOTE: Pass the lead wire through the tabs on the plastic
cover (wire protector) of inflator to prevent lead wire from
being pinched.
3. Tighten bolts to specified torque.
Torque: 9 N´m (78 lb in)
4. Connect the yellow 2-way SRS connector located
under the steering column.
5. Connect the battery ª±º terminal cable.
6. Set ignition to ªONº while watching warning light.
Light should flash 7 times and then go off. If lamp
does not operate correctly, refer to
Restraints section.
Page 274 of 2100
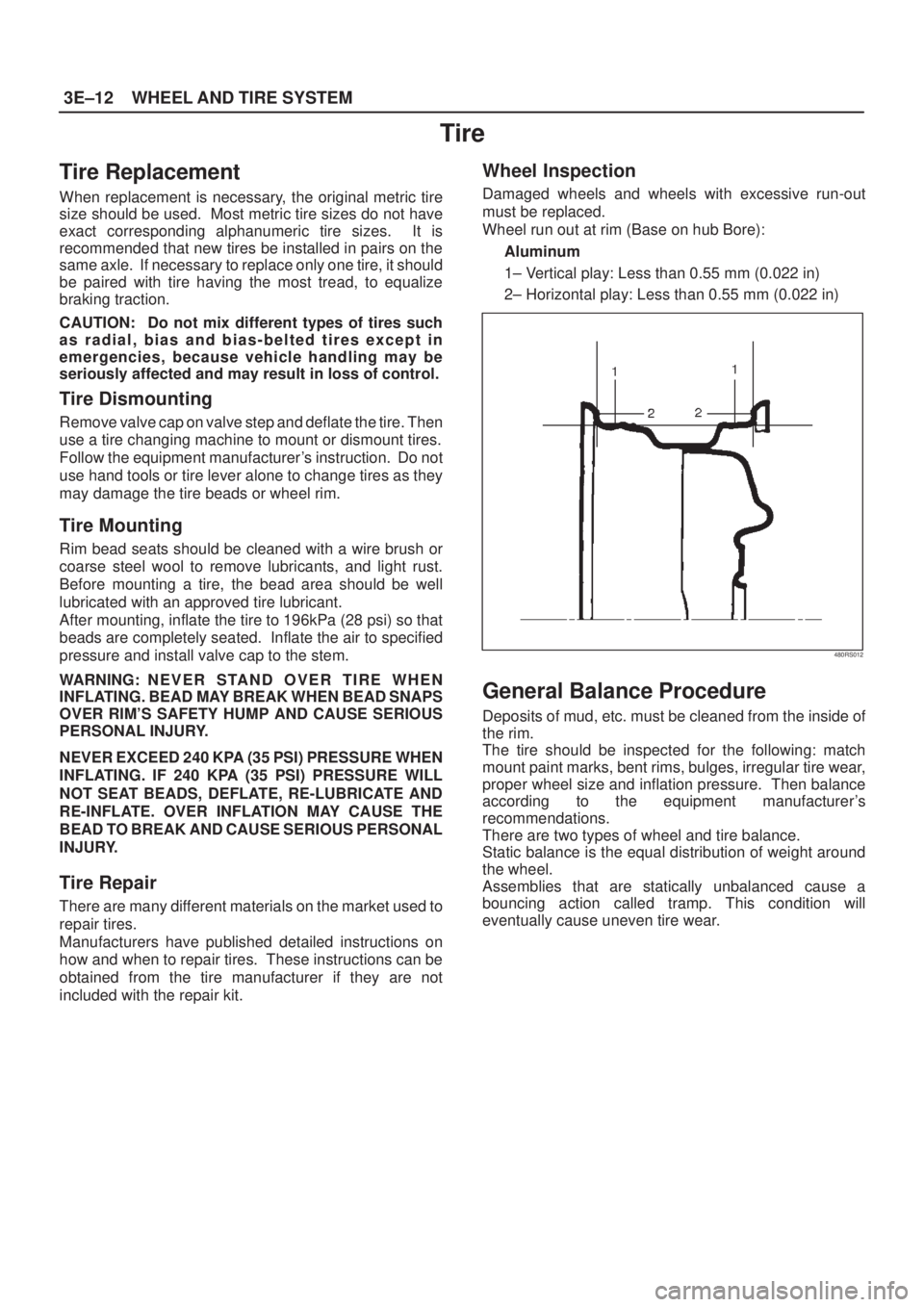
3E±12WHEEL AND TIRE SYSTEM
Tire
Tire Replacement
When replacement is necessary, the original metric tire
size should be used. Most metric tire sizes do not have
exact corresponding alphanumeric tire sizes. It is
recommended that new tires be installed in pairs on the
same axle. If necessary to replace only one tire, it should
be paired with tire having the most tread, to equalize
braking traction.
CAUTION: Do not mix different types of tires such
as radial, bias and bias-belted tires except in
emergencies, because vehicle handling may be
seriously affected and may result in loss of control.
Tire Dismounting
Remove valve cap on valve step and deflate the tire. Then
use a tire changing machine to mount or dismount tires.
Follow the equipment manufacturer's instruction. Do not
use hand tools or tire lever alone to change tires as they
may damage the tire beads or wheel rim.
Tire Mounting
Rim bead seats should be cleaned with a wire brush or
coarse steel wool to remove lubricants, and light rust.
Before mounting a tire, the bead area should be well
lubricated with an approved tire lubricant.
After mounting, inflate the tire to 196kPa (28 psi) so that
beads are completely seated. Inflate the air to specified
pressure and install valve cap to the stem.
WARNING: NEVER STAND OVER TIRE WHEN
INFLATING. BEAD MAY BREAK WHEN BEAD SNAPS
OVER RIM'S SAFETY HUMP AND CAUSE SERIOUS
PERSONAL INJURY.
NEVER EXCEED 240 KPA (35 PSI) PRESSURE WHEN
INFLATING. IF 240 KPA (35 PSI) PRESSURE WILL
NOT SEAT BEADS, DEFLATE, RE-LUBRICATE AND
RE-INFLATE. OVER INFLATION MAY CAUSE THE
BEAD TO BREAK AND CAUSE SERIOUS PERSONAL
INJURY.
Tire Repair
There are many different materials on the market used to
repair tires.
Manufacturers have published detailed instructions on
how and when to repair tires. These instructions can be
obtained from the tire manufacturer if they are not
included with the repair kit.
Wheel Inspection
Damaged wheels and wheels with excessive run-out
must be replaced.
Wheel run out at rim (Base on hub Bore):
Aluminum
1± Vertical play: Less than 0.55 mm (0.022 in)
2± Horizontal play: Less than 0.55 mm (0.022 in)
480RS012
General Balance Procedure
Deposits of mud, etc. must be cleaned from the inside of
the rim.
The tire should be inspected for the following: match
mount paint marks, bent rims, bulges, irregular tire wear,
proper wheel size and inflation pressure. Then balance
according to the equipment manufacturer's
recommendations.
There are two types of wheel and tire balance.
Static balance is the equal distribution of weight around
the wheel.
Assemblies that are statically unbalanced cause a
bouncing action called tramp. This condition will
eventually cause uneven tire wear.
Page 284 of 2100
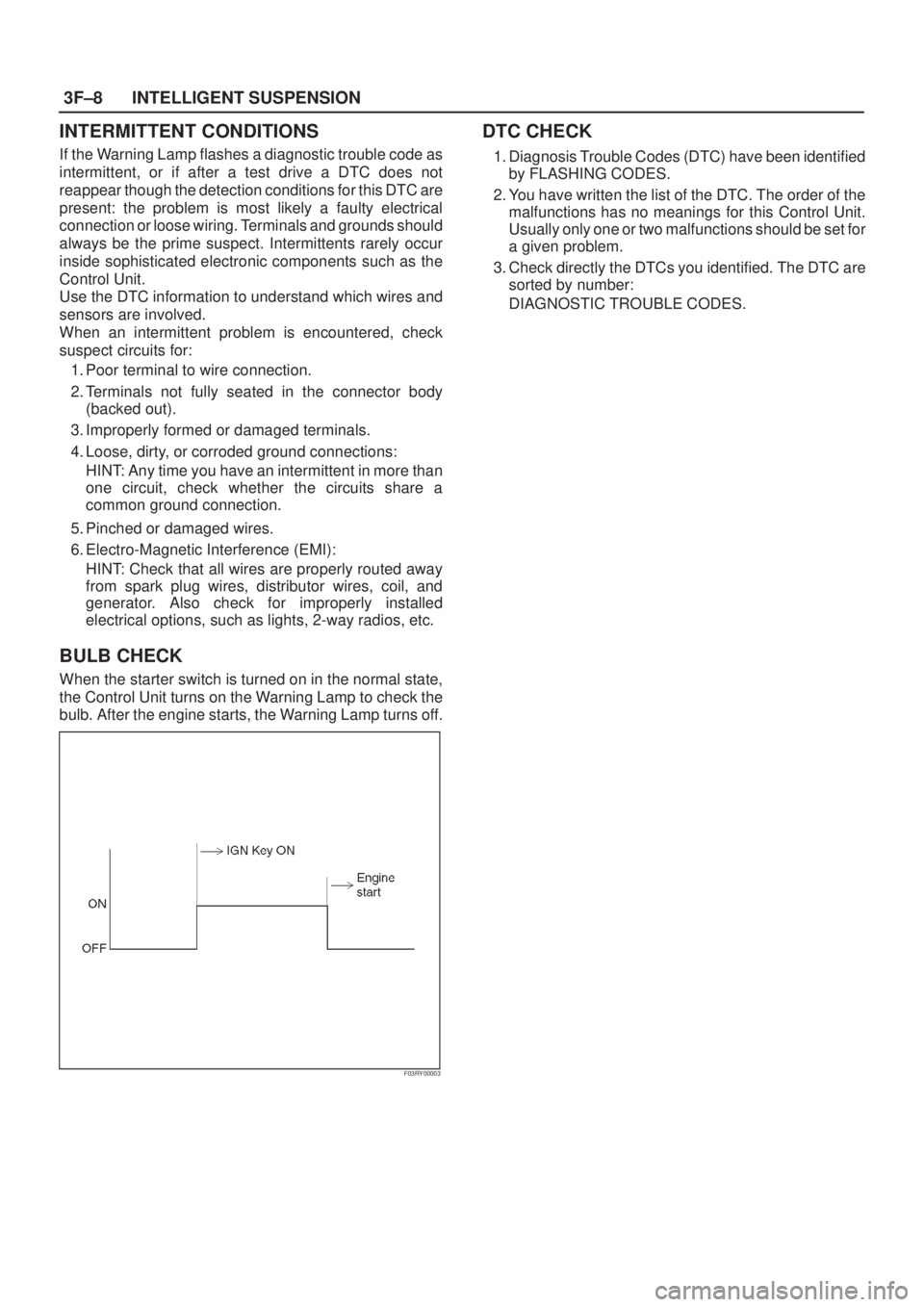
3F±8INTELLIGENT SUSPENSION
INTERMITTENT CONDITIONS
If the Warning Lamp flashes a diagnostic trouble code as
intermittent, or if after a test drive a DTC does not
reappear though the detection conditions for this DTC are
present: the problem is most likely a faulty electrical
connection or loose wiring. Terminals and grounds should
always be the prime suspect. Intermittents rarely occur
inside sophisticated electronic components such as the
Control Unit.
Use the DTC information to understand which wires and
sensors are involved.
When an intermittent problem is encountered, check
suspect circuits for:
1. Poor terminal to wire connection.
2. Terminals not fully seated in the connector body
(backed out).
3. Improperly formed or damaged terminals.
4. Loose, dirty, or corroded ground connections:
HINT: Any time you have an intermittent in more than
one circuit, check whether the circuits share a
common ground connection.
5. Pinched or damaged wires.
6. Electro-Magnetic Interference (EMI):
HINT: Check that all wires are properly routed away
from spark plug wires, distributor wires, coil, and
generator. Also check for improperly installed
electrical options, such as lights, 2-way radios, etc.
BULB CHECK
When the starter switch is turned on in the normal state,
the Control Unit turns on the Warning Lamp to check the
bulb. After the engine starts, the Warning Lamp turns off.
F03RY00003
DTC CHECK
1. Diagnosis Trouble Codes (DTC) have been identified
by FLASHING CODES.
2. You have written the list of the DTC. The order of the
malfunctions has no meanings for this Control Unit.
Usually only one or two malfunctions should be set for
a given problem.
3. Check directly the DTCs you identified. The DTC are
sorted by number:
DIAGNOSTIC TROUBLE CODES.
Page 620 of 2100
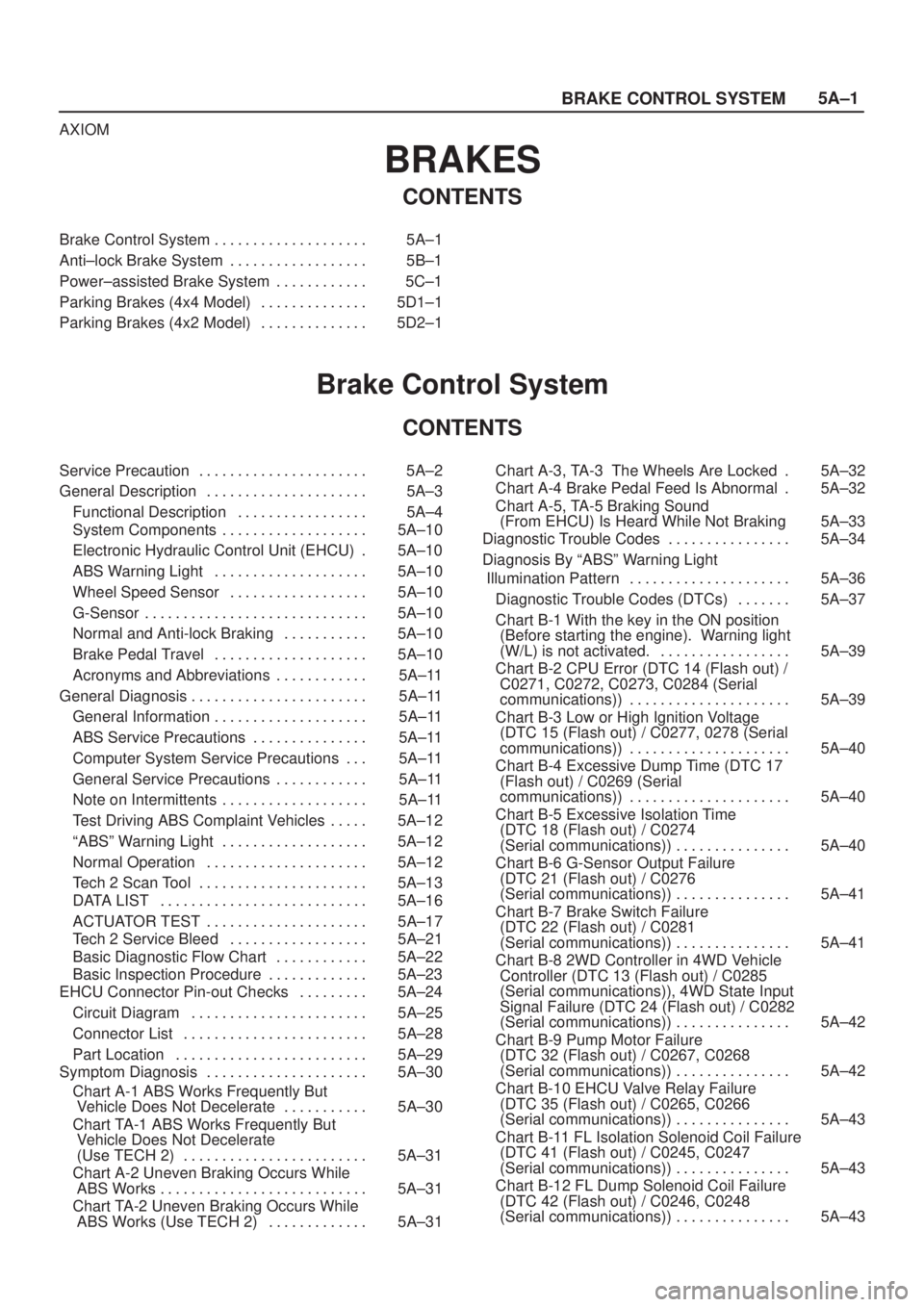
5A±1
BRAKE CONTROL SYSTEM
AXIOM
BRAKES
CONTENTS
Brake Control System 5A±1. . . . . . . . . . . . . . . . . . . .
Anti±lock Brake System 5B±1. . . . . . . . . . . . . . . . . .
Power±assisted Brake System 5C±1. . . . . . . . . . . .
Parking Brakes (4x4 Model) 5D1±1. . . . . . . . . . . . . .
Parking Brakes (4x2 Model) 5D2±1. . . . . . . . . . . . . .
Brake Control System
CONTENTS
Service Precaution 5A±2. . . . . . . . . . . . . . . . . . . . . .
General Description 5A±3. . . . . . . . . . . . . . . . . . . . .
Functional Description 5A±4. . . . . . . . . . . . . . . . .
System Components 5A±10. . . . . . . . . . . . . . . . . . .
Electronic Hydraulic Control Unit (EHCU) 5A±10.
ABS Warning Light 5A±10. . . . . . . . . . . . . . . . . . . .
Wheel Speed Sensor 5A±10. . . . . . . . . . . . . . . . . .
G-Sensor 5A±10. . . . . . . . . . . . . . . . . . . . . . . . . . . . .
Normal and Anti-lock Braking 5A±10. . . . . . . . . . .
Brake Pedal Travel 5A±10. . . . . . . . . . . . . . . . . . . .
Acronyms and Abbreviations 5A±11. . . . . . . . . . . .
General Diagnosis 5A±11. . . . . . . . . . . . . . . . . . . . . . .
General Information 5A±11. . . . . . . . . . . . . . . . . . . .
ABS Service Precautions 5A±11. . . . . . . . . . . . . . .
Computer System Service Precautions 5A±11. . .
General Service Precautions 5A±11. . . . . . . . . . . .
Note on Intermittents 5A±11. . . . . . . . . . . . . . . . . . .
Test Driving ABS Complaint Vehicles 5A±12. . . . .
ªABSº Warning Light 5A±12. . . . . . . . . . . . . . . . . . .
Normal Operation 5A±12. . . . . . . . . . . . . . . . . . . . .
Tech 2 Scan Tool 5A±13. . . . . . . . . . . . . . . . . . . . . .
DATA LIST 5A±16. . . . . . . . . . . . . . . . . . . . . . . . . . .
ACTUATOR TEST 5A±17. . . . . . . . . . . . . . . . . . . . .
Tech 2 Service Bleed 5A±21. . . . . . . . . . . . . . . . . .
Basic Diagnostic Flow Chart 5A±22. . . . . . . . . . . .
Basic Inspection Procedure 5A±23. . . . . . . . . . . . .
EHCU Connector Pin-out Checks 5A±24. . . . . . . . .
Circuit Diagram 5A±25. . . . . . . . . . . . . . . . . . . . . . .
Connector List 5A±28. . . . . . . . . . . . . . . . . . . . . . . .
Part Location 5A±29. . . . . . . . . . . . . . . . . . . . . . . . .
Symptom Diagnosis 5A±30. . . . . . . . . . . . . . . . . . . . .
Chart A-1 ABS Works Frequently But
Vehicle Does Not Decelerate 5A±30. . . . . . . . . . .
Chart TA-1 ABS Works Frequently But
Vehicle Does Not Decelerate
(Use TECH 2) 5A±31. . . . . . . . . . . . . . . . . . . . . . . .
Chart A-2 Uneven Braking Occurs While
ABS Works 5A±31. . . . . . . . . . . . . . . . . . . . . . . . . . .
Chart TA-2 Uneven Braking Occurs While
ABS Works (Use TECH 2) 5A±31. . . . . . . . . . . . . Chart A-3, TA-3 The Wheels Are Locked 5A±32.
Chart A-4 Brake Pedal Feed Is Abnormal 5A±32.
Chart A-5, TA-5 Braking Sound
(From EHCU) Is Heard While Not Braking 5A±33
Diagnostic Trouble Codes 5A±34. . . . . . . . . . . . . . . .
Diagnosis By ªABSº Warning Light
Illumination Pattern 5A±36. . . . . . . . . . . . . . . . . . . . .
Diagnostic Trouble Codes (DTCs) 5A±37. . . . . . .
Chart B-1 With the key in the ON position
(Before starting the engine). Warning light
(W/L) is not activated. 5A±39. . . . . . . . . . . . . . . . .
Chart B-2 CPU Error (DTC 14 (Flash out) /
C0271, C0272, C0273, C0284 (Serial
communications)) 5A±39. . . . . . . . . . . . . . . . . . . . .
Chart B-3 Low or High Ignition Voltage
(DTC 15 (Flash out) / C0277, 0278 (Serial
communications)) 5A±40. . . . . . . . . . . . . . . . . . . . .
Chart B-4 Excessive Dump Time (DTC 17
(Flash out) / C0269 (Serial
communications)) 5A±40. . . . . . . . . . . . . . . . . . . . .
Chart B-5 Excessive Isolation Time
(DTC 18 (Flash out) / C0274
(Serial communications)) 5A±40. . . . . . . . . . . . . . .
Chart B-6 G-Sensor Output Failure
(DTC 21 (Flash out) / C0276
(Serial communications)) 5A±41. . . . . . . . . . . . . . .
Chart B-7 Brake Switch Failure
(DTC 22 (Flash out) / C0281
(Serial communications)) 5A±41. . . . . . . . . . . . . . .
Chart B-8 2WD Controller in 4WD Vehicle
Controller (DTC 13 (Flash out) / C0285
(Serial communications)), 4WD State Input
Signal Failure (DTC 24 (Flash out) / C0282
(Serial communications)) 5A±42. . . . . . . . . . . . . . .
Chart B-9 Pump Motor Failure
(DTC 32 (Flash out) / C0267, C0268
(Serial communications)) 5A±42. . . . . . . . . . . . . . .
Chart B-10 EHCU Valve Relay Failure
(DTC 35 (Flash out) / C0265, C0266
(Serial communications)) 5A±43. . . . . . . . . . . . . . .
Chart B-11 FL Isolation Solenoid Coil Failure
(DTC 41 (Flash out) / C0245, C0247
(Serial communications)) 5A±43. . . . . . . . . . . . . . .
Chart B-12 FL Dump Solenoid Coil Failure
(DTC 42 (Flash out) / C0246, C0248
(Serial communications)) 5A±43. . . . . . . . . . . . . . .
Page 629 of 2100
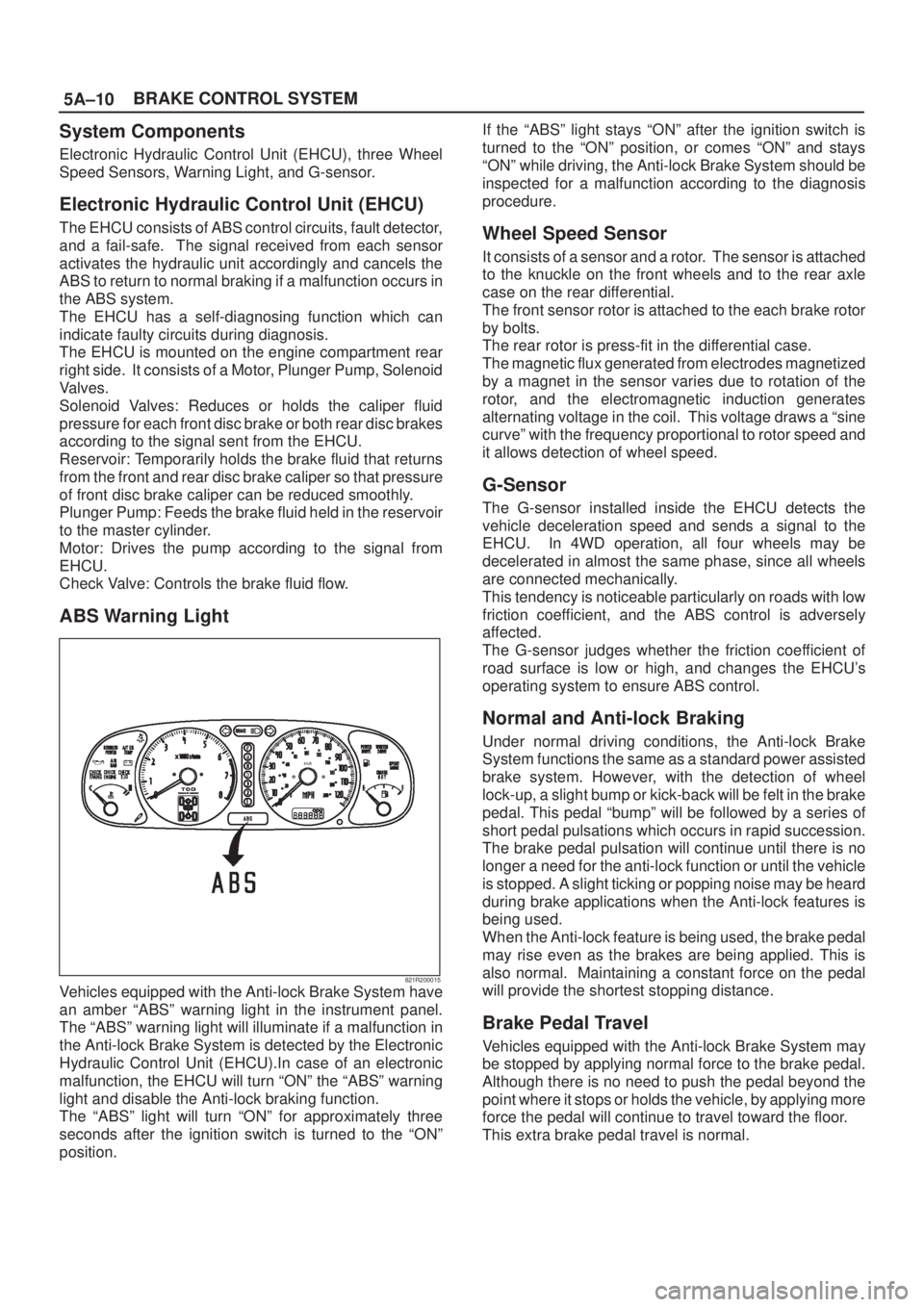
5A±10BRAKE CONTROL SYSTEM
System Components
Electronic Hydraulic Control Unit (EHCU), three Wheel
Speed Sensors, Warning Light, and G-sensor.
Electronic Hydraulic Control Unit (EHCU)
The EHCU consists of ABS control circuits, fault detector,
and a fail-safe. The signal received from each sensor
activates the hydraulic unit accordingly and cancels the
ABS to return to normal braking if a malfunction occurs in
the ABS system.
The EHCU has a self-diagnosing function which can
indicate faulty circuits during diagnosis.
The EHCU is mounted on the engine compartment rear
right side. It consists of a Motor, Plunger Pump, Solenoid
Valves.
Solenoid Valves: Reduces or holds the caliper fluid
pressure for each front disc brake or both rear disc brakes
according to the signal sent from the EHCU.
Reservoir: Temporarily holds the brake fluid that returns
from the front and rear disc brake caliper so that pressure
of front disc brake caliper can be reduced smoothly.
Plunger Pump: Feeds the brake fluid held in the reservoir
to the master cylinder.
Motor: Drives the pump according to the signal from
EHCU.
Check Valve: Controls the brake fluid flow.
ABS Warning Light
821R200015Vehicles equipped with the Anti-lock Brake System have
an amber ªABSº warning light in the instrument panel.
The ªABSº warning light will illuminate if a malfunction in
the Anti-lock Brake System is detected by the Electronic
Hydraulic Control Unit (EHCU).In case of an electronic
malfunction, the EHCU will turn ªONº the ªABSº warning
light and disable the Anti-lock braking function.
The ªABSº light will turn ªONº for approximately three
seconds after the ignition switch is turned to the ªONº
position.If the ªABSº light stays ªONº after the ignition switch is
turned to the ªONº position, or comes ªONº and stays
ªONº while driving, the Anti-lock Brake System should be
inspected for a malfunction according to the diagnosis
procedure.
Wheel Speed Sensor
It consists of a sensor and a rotor. The sensor is attached
to the knuckle on the front wheels and to the rear axle
case on the rear differential.
The front sensor rotor is attached to the each brake rotor
by bolts.
The rear rotor is press-fit in the differential case.
The magnetic flux generated from electrodes magnetized
by a magnet in the sensor varies due to rotation of the
rotor, and the electromagnetic induction generates
alternating voltage in the coil. This voltage draws a ªsine
curveº with the frequency proportional to rotor speed and
it allows detection of wheel speed.
G-Sensor
The G-sensor installed inside the EHCU detects the
vehicle deceleration speed and sends a signal to the
EHCU. In 4WD operation, all four wheels may be
decelerated in almost the same phase, since all wheels
are connected mechanically.
This tendency is noticeable particularly on roads with low
friction coefficient, and the ABS control is adversely
affected.
The G-sensor judges whether the friction coefficient of
road surface is low or high, and changes the EHCU's
operating system to ensure ABS control.
Normal and Anti-lock Braking
Under normal driving conditions, the Anti-lock Brake
System functions the same as a standard power assisted
brake system. However, with the detection of wheel
lock-up, a slight bump or kick-back will be felt in the brake
pedal. This pedal ªbumpº will be followed by a series of
short pedal pulsations which occurs in rapid succession.
The brake pedal pulsation will continue until there is no
longer a need for the anti-lock function or until the vehicle
is stopped. A slight ticking or popping noise may be heard
during brake applications when the Anti-lock features is
being used.
When the Anti-lock feature is being used, the brake pedal
may rise even as the brakes are being applied. This is
also normal. Maintaining a constant force on the pedal
will provide the shortest stopping distance.
Brake Pedal Travel
Vehicles equipped with the Anti-lock Brake System may
be stopped by applying normal force to the brake pedal.
Although there is no need to push the pedal beyond the
point where it stops or holds the vehicle, by applying more
force the pedal will continue to travel toward the floor.
This extra brake pedal travel is normal.
Page 630 of 2100
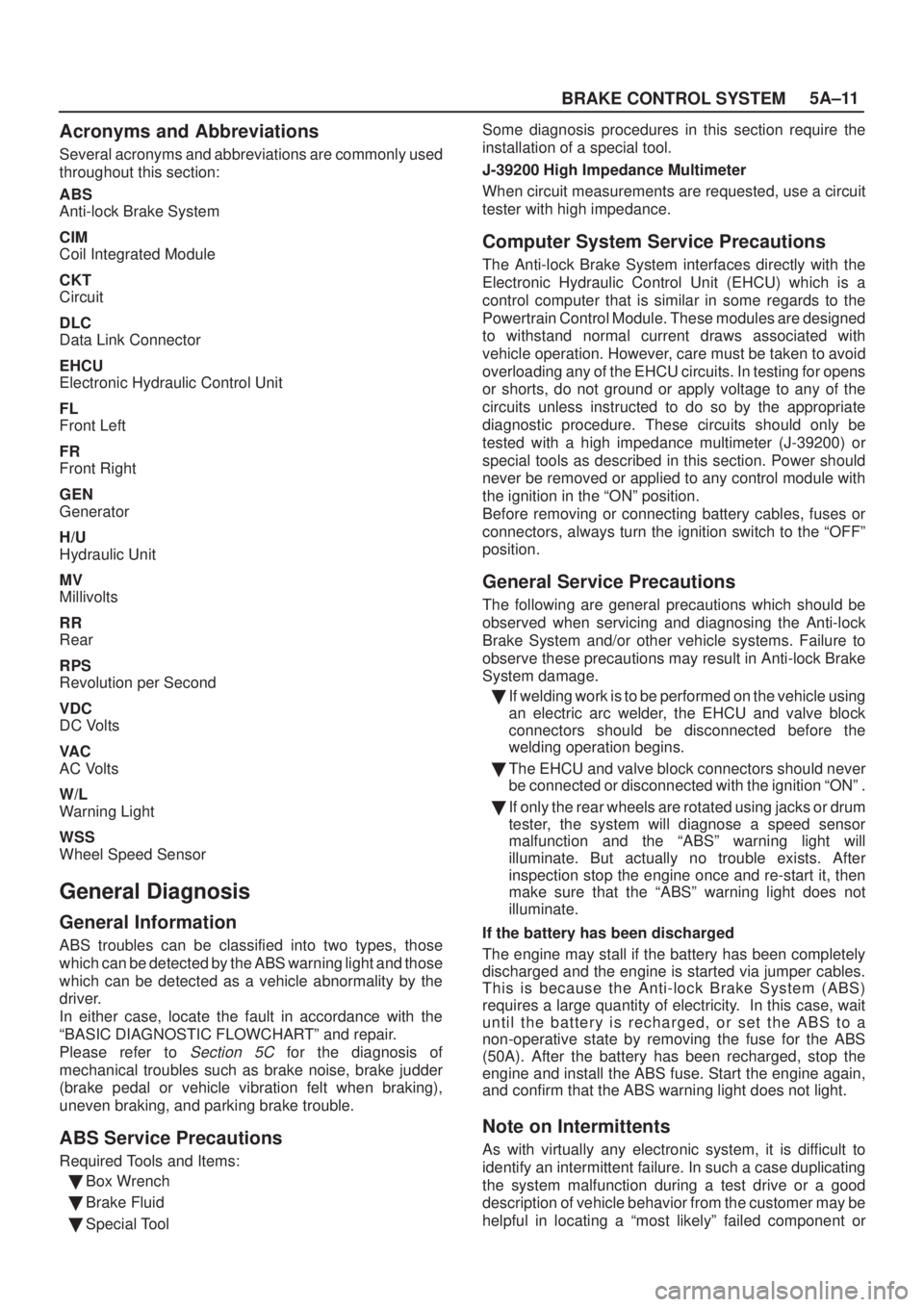
5A±11
BRAKE CONTROL SYSTEM
Acronyms and Abbreviations
Several acronyms and abbreviations are commonly used
throughout this section:
ABS
Anti-lock Brake System
CIM
Coil Integrated Module
CKT
Circuit
DLC
Data Link Connector
EHCU
Electronic Hydraulic Control Unit
FL
Front Left
FR
Front Right
GEN
Generator
H/U
Hydraulic Unit
MV
Millivolts
RR
Rear
RPS
Revolution per Second
VDC
DC Volts
VA C
AC Volts
W/L
Warning Light
WSS
Wheel Speed Sensor
General Diagnosis
General Information
ABS troubles can be classified into two types, those
which can be detected by the ABS warning light and those
which can be detected as a vehicle abnormality by the
driver.
In either case, locate the fault in accordance with the
ªBASIC DIAGNOSTIC FLOWCHARTº and repair.
Please refer to
Section 5C for the diagnosis of
mechanical troubles such as brake noise, brake judder
(brake pedal or vehicle vibration felt when braking),
uneven braking, and parking brake trouble.
ABS Service Precautions
Required Tools and Items:
Box Wrench
Brake Fluid
Special ToolSome diagnosis procedures in this section require the
installation of a special tool.
J-39200 High Impedance Multimeter
When circuit measurements are requested, use a circuit
tester with high impedance.
Computer System Service Precautions
The Anti-lock Brake System interfaces directly with the
Electronic Hydraulic Control Unit (EHCU) which is a
control computer that is similar in some regards to the
Powertrain Control Module. These modules are designed
to withstand normal current draws associated with
vehicle operation. However, care must be taken to avoid
overloading any of the EHCU circuits. In testing for opens
or shorts, do not ground or apply voltage to any of the
circuits unless instructed to do so by the appropriate
diagnostic procedure. These circuits should only be
tested with a high impedance multimeter (J-39200) or
special tools as described in this section. Power should
never be removed or applied to any control module with
the ignition in the ªONº position.
Before removing or connecting battery cables, fuses or
connectors, always turn the ignition switch to the ªOFFº
position.
General Service Precautions
The following are general precautions which should be
observed when servicing and diagnosing the Anti-lock
Brake System and/or other vehicle systems. Failure to
observe these precautions may result in Anti-lock Brake
System damage.
If welding work is to be performed on the vehicle using
an electric arc welder, the EHCU and valve block
connectors should be disconnected before the
welding operation begins.
The EHCU and valve block connectors should never
be connected or disconnected with the ignition ªONº .
If only the rear wheels are rotated using jacks or drum
tester, the system will diagnose a speed sensor
malfunction and the ªABSº warning light will
illuminate. But actually no trouble exists. After
inspection stop the engine once and re-start it, then
make sure that the ªABSº warning light does not
illuminate.
If the battery has been discharged
The engine may stall if the battery has been completely
discharged and the engine is started via jumper cables.
This is because the Anti-lock Brake System (ABS)
requires a large quantity of electricity. In this case, wait
until the battery is recharged, or set the ABS to a
non-operative state by removing the fuse for the ABS
(50A). After the battery has been recharged, stop the
engine and install the ABS fuse. Start the engine again,
and confirm that the ABS warning light does not light.
Note on Intermittents
As with virtually any electronic system, it is difficult to
identify an intermittent failure. In such a case duplicating
the system malfunction during a test drive or a good
description of vehicle behavior from the customer may be
helpful in locating a ªmost likelyº failed component or
Page 631 of 2100
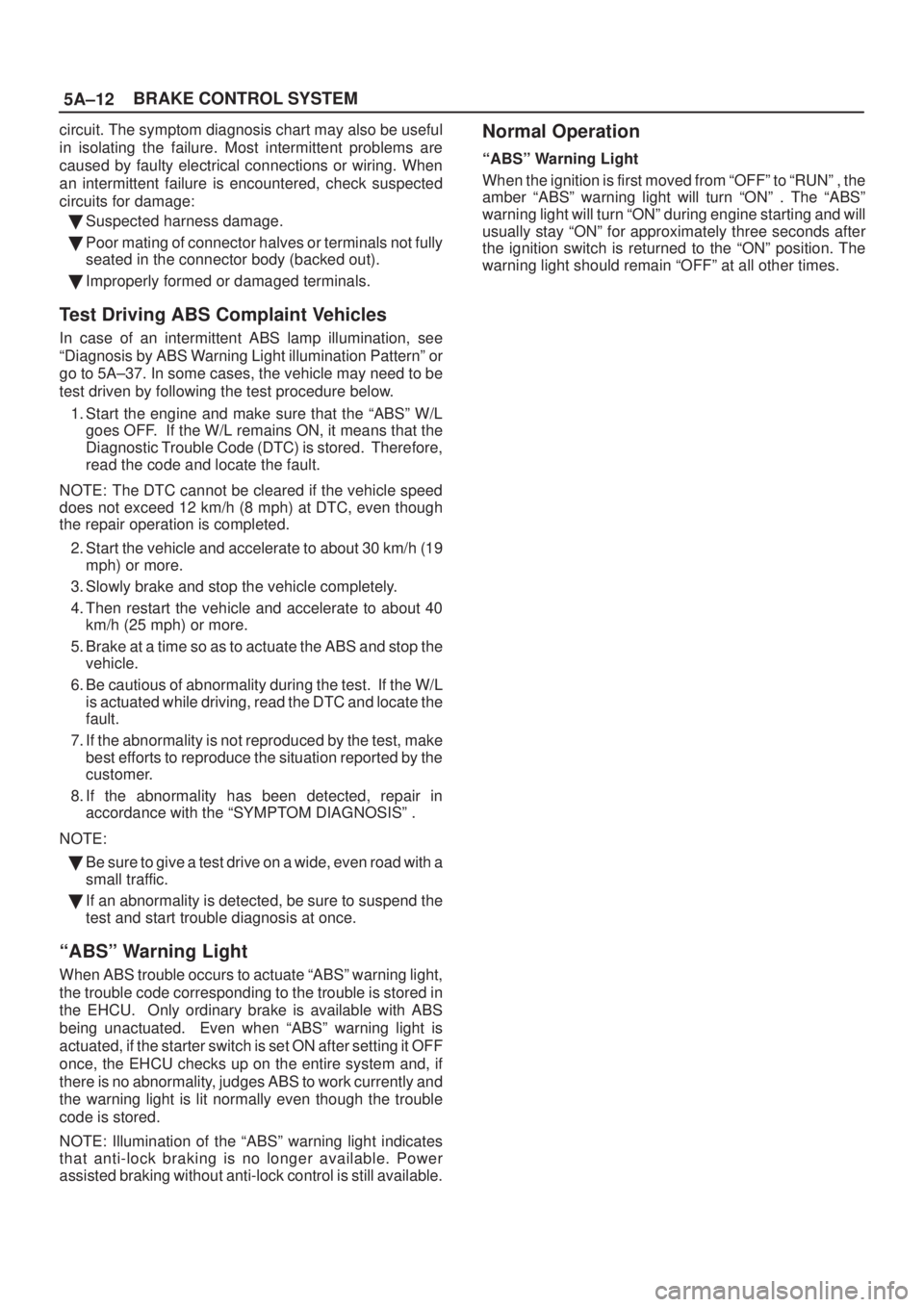
5A±12BRAKE CONTROL SYSTEM
circuit. The symptom diagnosis chart may also be useful
in isolating the failure. Most intermittent problems are
caused by faulty electrical connections or wiring. When
an intermittent failure is encountered, check suspected
circuits for damage:
Suspected harness damage.
Poor mating of connector halves or terminals not fully
seated in the connector body (backed out).
Improperly formed or damaged terminals.
Test Driving ABS Complaint Vehicles
In case of an intermittent ABS lamp illumination, see
ªDiagnosis by ABS Warning Light illumination Patternº or
go to 5A±37. In some cases, the vehicle may need to be
test driven by following the test procedure below.
1. Start the engine and make sure that the ªABSº W/L
goes OFF. If the W/L remains ON, it means that the
Diagnostic Trouble Code (DTC) is stored. Therefore,
read the code and locate the fault.
NOTE: The DTC cannot be cleared if the vehicle speed
does not exceed 12 km/h (8 mph) at DTC, even though
the repair operation is completed.
2. Start the vehicle and accelerate to about 30 km/h (19
mph) or more.
3. Slowly brake and stop the vehicle completely.
4. Then restart the vehicle and accelerate to about 40
km/h (25 mph) or more.
5. Brake at a time so as to actuate the ABS and stop the
vehicle.
6. Be cautious of abnormality during the test. If the W/L
is actuated while driving, read the DTC and locate the
fault.
7. If the abnormality is not reproduced by the test, make
best efforts to reproduce the situation reported by the
customer.
8. If the abnormality has been detected, repair in
accordance with the ªSYMPTOM DIAGNOSISº .
NOTE:
Be sure to give a test drive on a wide, even road with a
small traffic.
If an abnormality is detected, be sure to suspend the
test and start trouble diagnosis at once.
ªABSº Warning Light
When ABS trouble occurs to actuate ªABSº warning light,
the trouble code corresponding to the trouble is stored in
the EHCU. Only ordinary brake is available with ABS
being unactuated. Even when ªABSº warning light is
actuated, if the starter switch is set ON after setting it OFF
once, the EHCU checks up on the entire system and, if
there is no abnormality, judges ABS to work currently and
the warning light is lit normally even though the trouble
code is stored.
NOTE: Illumination of the ªABSº warning light indicates
that anti-lock braking is no longer available. Power
assisted braking without anti-lock control is still available.
Normal Operation
ªABSº Warning Light
When the ignition is first moved from ªOFFº to ªRUNº , the
amber ªABSº warning light will turn ªONº . The ªABSº
warning light will turn ªONº during engine starting and will
usually stay ªONº for approximately three seconds after
the ignition switch is returned to the ªONº position. The
warning light should remain ªOFFº at all other times.
Page 649 of 2100
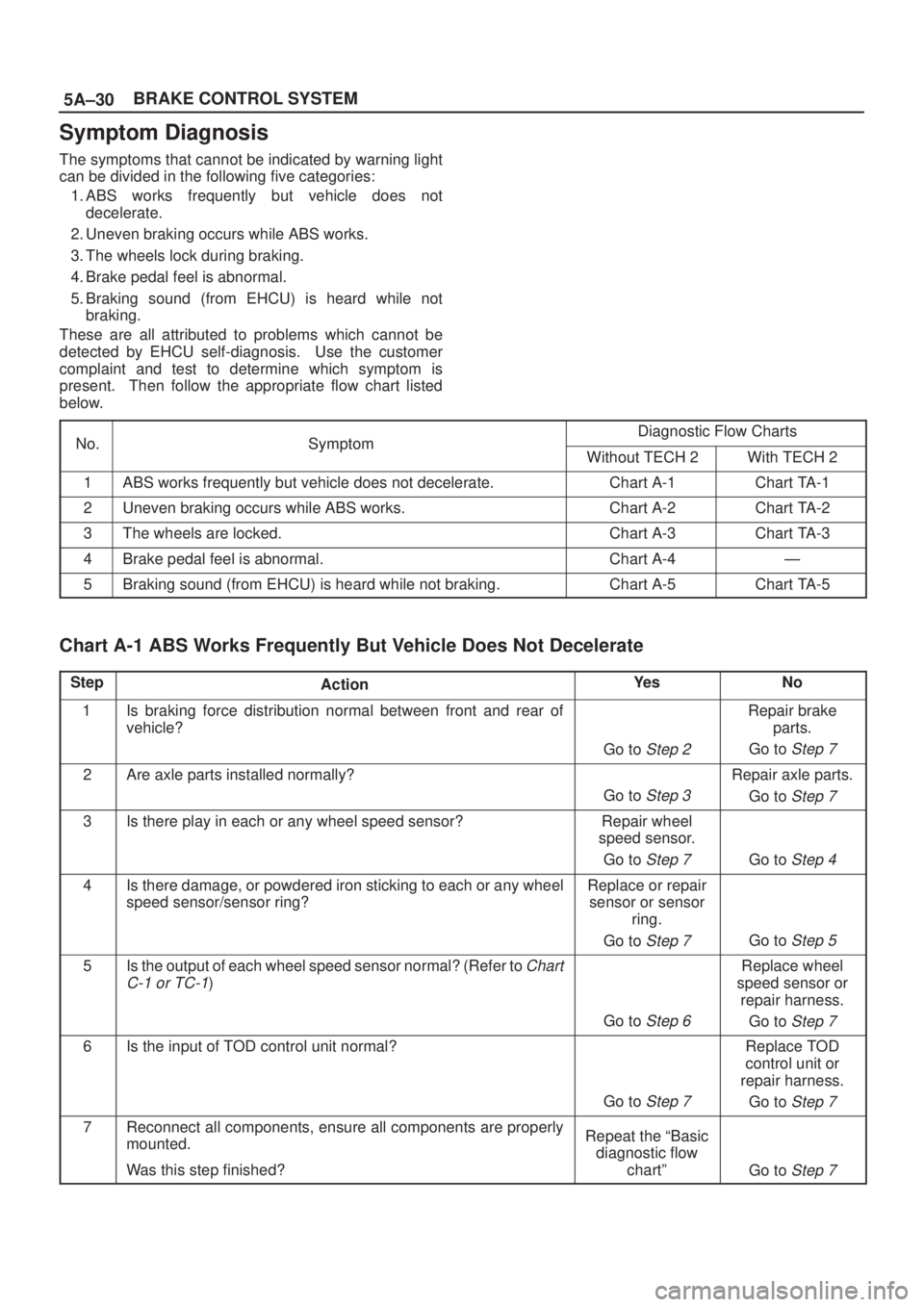
5A±30BRAKE CONTROL SYSTEM
Symptom Diagnosis
The symptoms that cannot be indicated by warning light
can be divided in the following five categories:
1. ABS works frequently but vehicle does not
decelerate.
2. Uneven braking occurs while ABS works.
3. The wheels lock during braking.
4. Brake pedal feel is abnormal.
5. Braking sound (from EHCU) is heard while not
braking.
These are all attributed to problems which cannot be
detected by EHCU self-diagnosis. Use the customer
complaint and test to determine which symptom is
present. Then follow the appropriate flow chart listed
below.
NoSymptomDiagnostic Flow ChartsNo.Sym tomWithout TECH 2With TECH 2
1ABS works frequently but vehicle does not decelerate.Chart A-1Chart TA-1
2Uneven braking occurs while ABS works.Chart A-2Chart TA-2
3The wheels are locked.Chart A-3Chart TA-3
4Brake pedal feel is abnormal.Chart A-4Ð
5Braking sound (from EHCU) is heard while not braking. Chart A-5Chart TA-5
Chart A-1 ABS Works Frequently But Vehicle Does Not Decelerate
StepActionYe sNo
1Is braking force distribution normal between front and rear of
vehicle?
Go to Step 2
Repair brake
parts.
Go to
Step 7
2Are axle parts installed normally?
Go to Step 3
Repair axle parts.
Go to
Step 7
3Is there play in each or any wheel speed sensor?Repair wheel
speed sensor.
Go to
Step 7Go to Step 4
4Is there damage, or powdered iron sticking to each or any wheel
speed sensor/sensor ring?Replace or repair
sensor or sensor
ring.
Go to
Step 7Go to Step 5
5Is the output of each wheel speed sensor normal? (Refer to Chart
C-1 or TC-1
)
Go to Step 6
Replace wheel
speed sensor or
repair harness.
Go to
Step 7
6Is the input of TOD control unit normal?
Go to Step 7
Replace TOD
control unit or
repair harness.
Go to
Step 7
7Reconnect all components, ensure all components are properly
mounted.
Was this step finished?Repeat the ªBasic
diagnostic flow
chartº
Go to Step 7