check engine ISUZU TF SERIES 2004 Workshop Manual
[x] Cancel search | Manufacturer: ISUZU, Model Year: 2004, Model line: TF SERIES, Model: ISUZU TF SERIES 2004Pages: 4264, PDF Size: 72.63 MB
Page 2101 of 4264
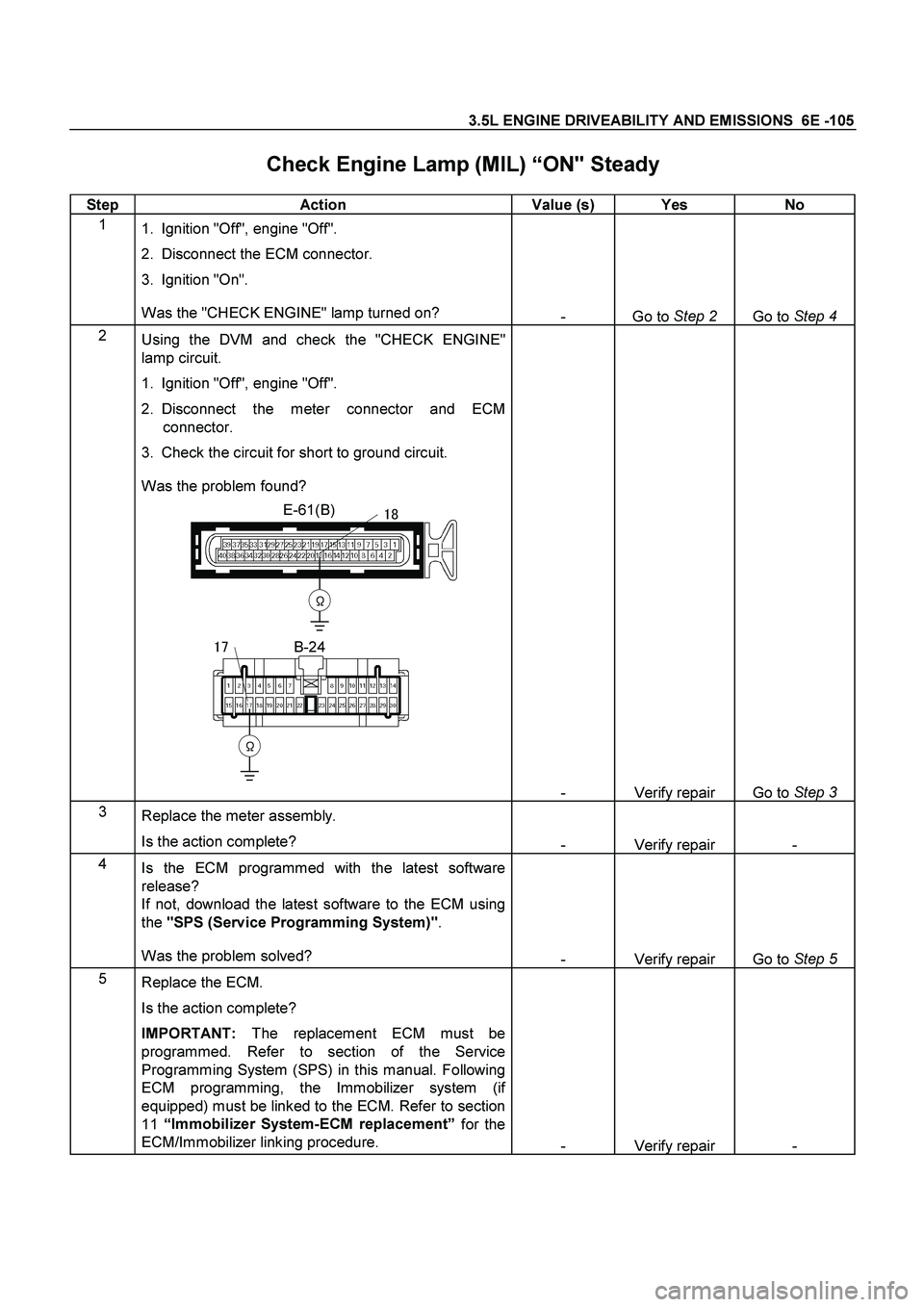
3.5L ENGINE DRIVEABILITY AND EMISSIONS 6E -105
Check Engine Lamp (MIL) “ON" Steady
Step Action Value (s) Yes No
1
1. Ignition "Off", engine "Off".
2. Disconnect the ECM connector.
3. Ignition "On".
Was the "CHECK ENGINE" lamp turned on?
- Go to Step 2
Go to Step 4
2
Using the DVM and check the "CHECK ENGINE"
lamp circuit.
1. Ignition "Off", engine "Off".
2. Disconnect the meter connector and ECM
connector.
3. Check the circuit for short to ground circuit.
Was the problem found?
B-24
E-61(B)
- Verify repair Go to Step 3
3
Replace the meter assembly.
Is the action complete?
- Verify repair -
4
Is the ECM programmed with the latest software
release?
If not, download the latest software to the ECM using
the "SPS (Service Programming System)"
.
Was the problem solved?
-
Verify repair
Go to Step 5
5
Replace the ECM.
Is the action complete?
IMPORTANT: The replacement ECM must be
programmed. Refer to section of the Service
Programming System (SPS) in this manual. Following
ECM programming, the Immobilizer system (if
equipped) must be linked to the ECM. Refer to section
11 “Immobilizer System-ECM replacement”
for the
ECM/Immobilizer linking procedure.
-
Verify repair
-
Page 2102 of 4264
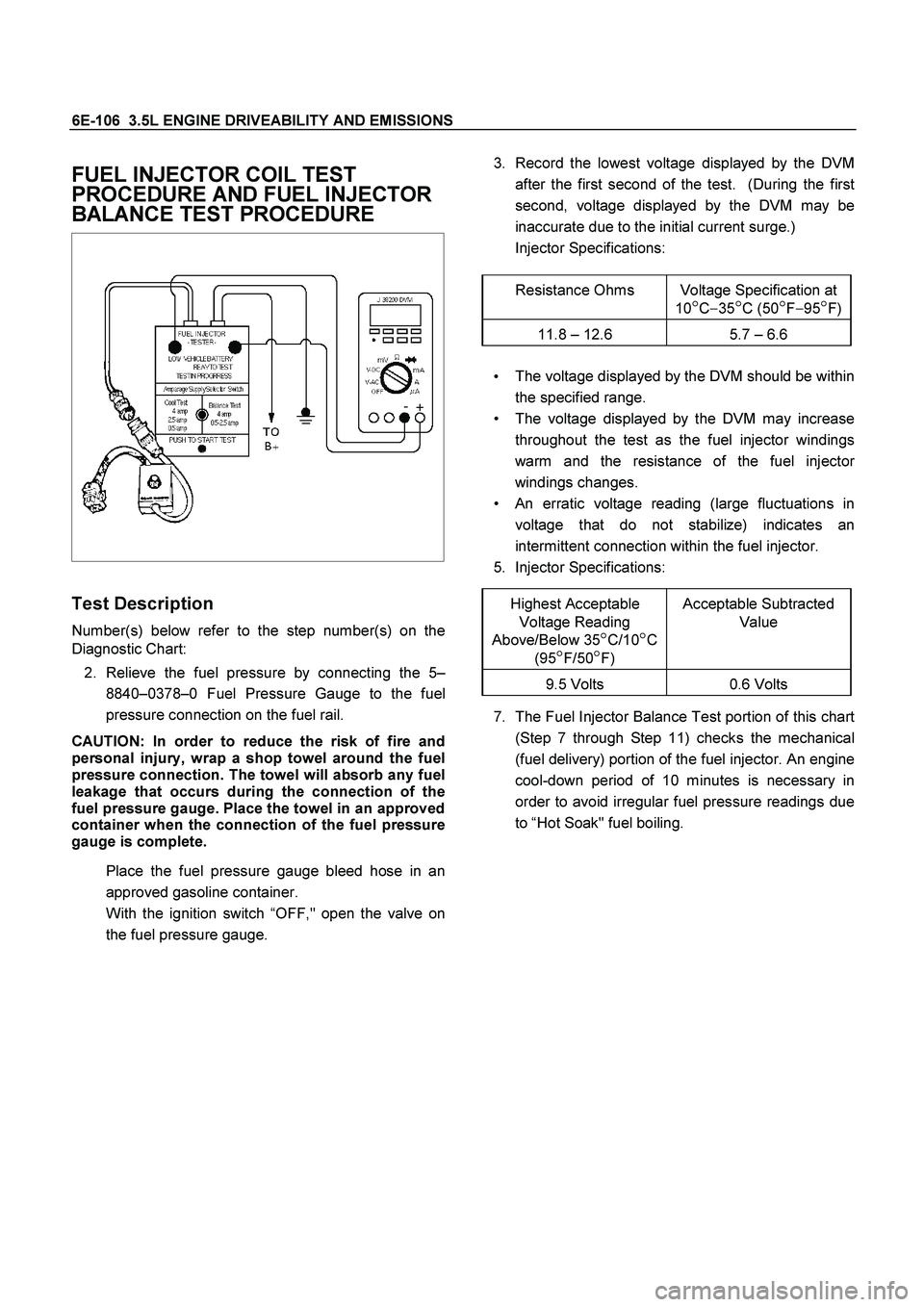
6E-106 3.5L ENGINE DRIVEABILITY AND EMISSIONS
FUEL INJECTOR COIL TEST
PROCEDURE AND FUEL INJECTOR
BALANCE TEST PROCEDURE
Test Description
Number(s) below refer to the step number(s) on the
Diagnostic Chart:
2.
Relieve the fuel pressure by connecting the 5–
8840–0378–0 Fuel Pressure Gauge to the fuel
pressure connection on the fuel rail.
CAUTION: In order to reduce the risk of fire and
personal injury, wrap a shop towel around the fuel
pressure connection. The towel will absorb any fuel
leakage that occurs during the connection of the
fuel pressure gauge. Place the towel in an approved
container when the connection of the fuel pressure
gauge is complete.
Place the fuel pressure gauge bleed hose in an
approved gasoline container.
With the ignition switch “OFF," open the valve on
the fuel pressure gauge.
3.
Record the lowest voltage displayed by the DVM
after the first second of the test. (During the first
second, voltage displayed by the DVM may be
inaccurate due to the initial current surge.)
Injector Specifications:
Resistance Ohms Voltage Specification at
10
C
35C (50F
95F)
11.8 – 12.6 5.7 – 6.6
The voltage displayed by the DVM should be within
the specified range.
The voltage displayed by the DVM may increase
throughout the test as the fuel injector windings
warm and the resistance of the fuel injecto
r
windings changes.
An erratic voltage reading (large fluctuations in
voltage that do not stabilize) indicates an
intermittent connection within the fuel injector.
5.
Injector Specifications:
Highest Acceptable
Voltage Reading
Above/Below 35
C/10C
(95
F/50F) Acceptable Subtracted
Value
9.5 Volts 0.6 Volts
7.
The Fuel Injector Balance Test portion of this chart
(Step 7 through Step 11) checks the mechanical
(fuel delivery) portion of the fuel injector. An engine
cool-down period of 10 minutes is necessary in
order to avoid irregular fuel pressure readings due
to “Hot Soak" fuel boiling.
Page 2104 of 4264
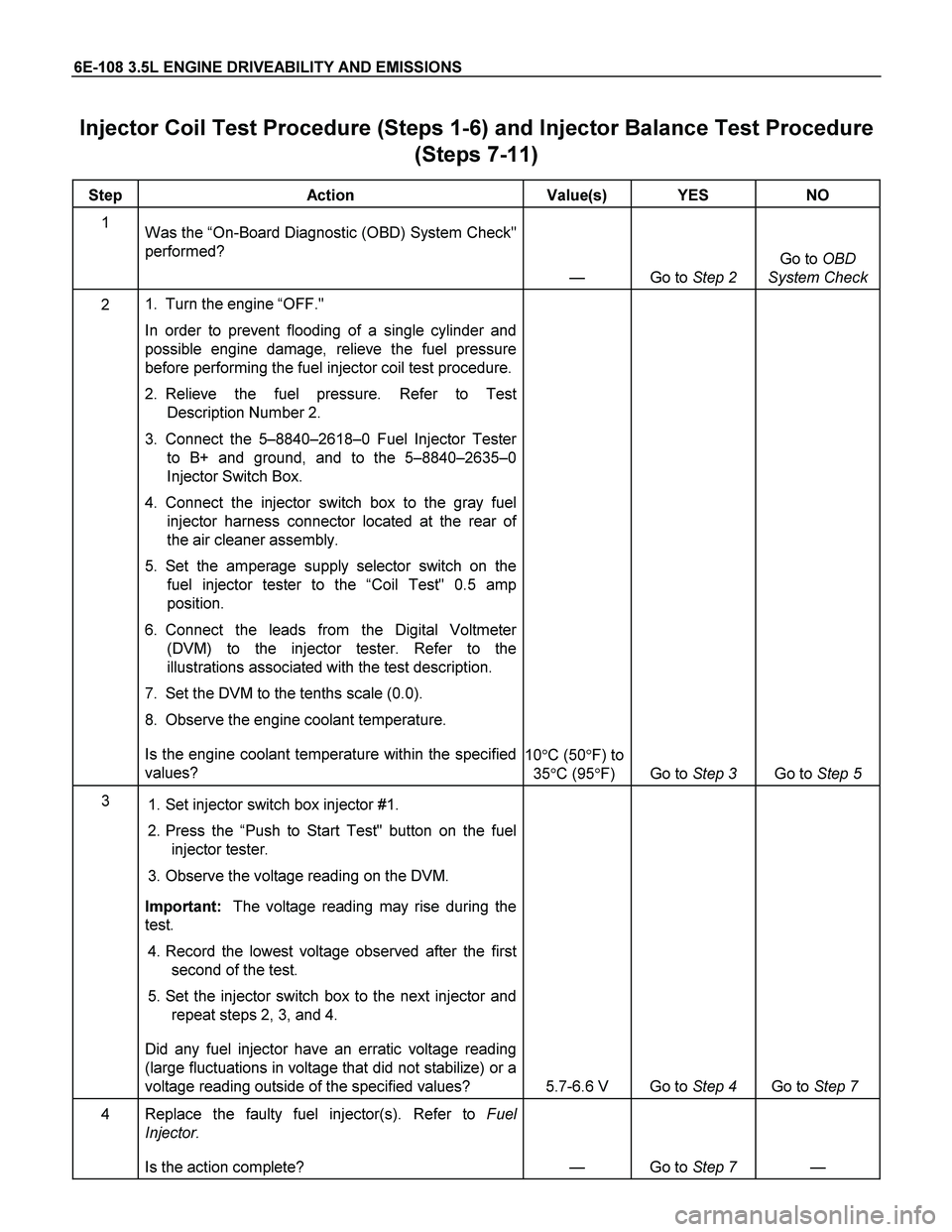
6E-108 3.5L ENGINE DRIVEABILITY AND EMISSIONS
Injector Coil Test Procedure (Steps 1-6) and Injector Balance Test Procedure
(Steps 7-11)
Step Action Value(s) YES NO
1
Was the “On-Board Diagnostic (OBD) System Check"
performed?
— Go to Step 2 Go to OBD
System Check
2 1. Turn the engine “OFF."
In order to prevent flooding of a single cylinder and
possible engine damage, relieve the fuel pressure
before performing the fuel injector coil test procedure.
2. Relieve the fuel pressure. Refer to Test
Description Number 2.
3. Connect the 5–8840–2618–0 Fuel Injector Tester
to B+ and ground, and to the 5–8840–2635–0
Injector Switch Box.
4. Connect the injector switch box to the gray fuel
injector harness connector located at the rear of
the air cleaner assembly.
5. Set the amperage supply selector switch on the
fuel injector tester to the “Coil Test" 0.5 amp
position.
6. Connect the leads from the Digital Voltmeter
(DVM) to the injector tester. Refer to the
illustrations associated with the test description.
7. Set the DVM to the tenths scale (0.0).
8. Observe the engine coolant temperature.
Is the engine coolant temperature within the specified
values? 10C (50F) to
35C (95F) Go to Step 3 Go to Step 5
3
1. Set injector switch box injector #1.
2. Press the “Push to Start Test" button on the fuel
injector tester.
3. Observe the voltage reading on the DVM.
Important: The voltage reading may rise during the
test.
4. Record the lowest voltage observed after the first
second of the test.
5. Set the injector switch box to the next injector and
repeat steps 2, 3, and 4.
Did any fuel injector have an erratic voltage reading
(large fluctuations in voltage that did not stabilize) or a
voltage reading outside of the specified values? 5.7-6.6 V Go to Step 4 Go to Step 7
4 Replace the faulty fuel injector(s). Refer to Fuel
Injector.
Is the action complete? — Go to Step 7 —
Page 2106 of 4264
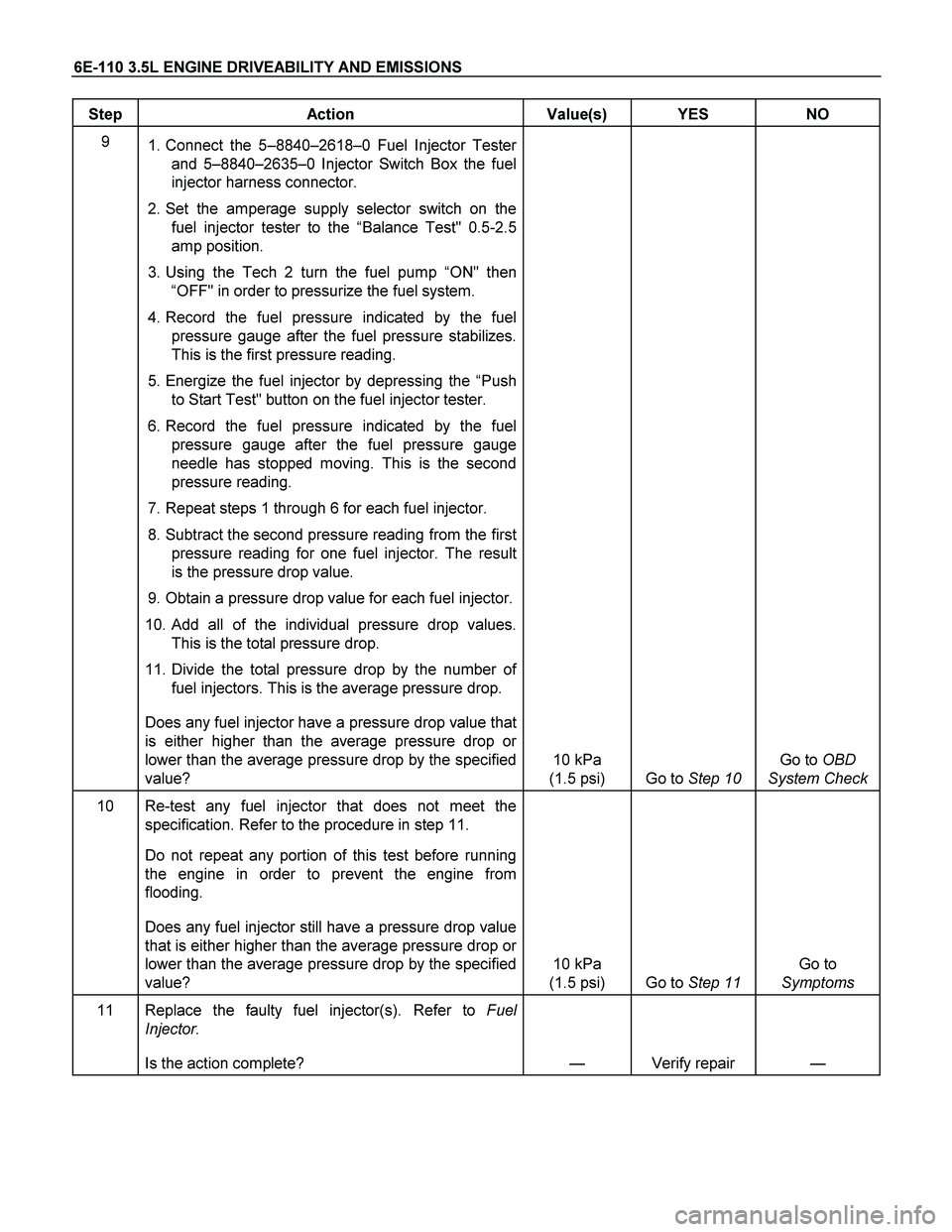
6E-110 3.5L ENGINE DRIVEABILITY AND EMISSIONS
Step Action Value(s) YES NO
9
1. Connect the 5–8840–2618–0 Fuel Injector Tester
and 5–8840–2635–0 Injector Switch Box the fuel
injector harness connector.
2. Set the amperage supply selector switch on the
fuel injector tester to the “Balance Test" 0.5-2.5
amp position.
3. Using the Tech 2 turn the fuel pump “ON" then
“OFF" in order to pressurize the fuel system.
4. Record the fuel pressure indicated by the fuel
pressure gauge after the fuel pressure stabilizes.
This is the first pressure reading.
5. Energize the fuel injector by depressing the “Push
to Start Test" button on the fuel injector tester.
6. Record the fuel pressure indicated by the fuel
pressure gauge after the fuel pressure gauge
needle has stopped moving. This is the second
pressure reading.
7. Repeat steps 1 through 6 for each fuel injector.
8. Subtract the second pressure reading from the first
pressure reading for one fuel injector. The result
is the pressure drop value.
9. Obtain a pressure drop value for each fuel injector.
10. Add all of the individual pressure drop values.
This is the total pressure drop.
11. Divide the total pressure drop by the number of
fuel injectors. This is the average pressure drop.
Does any fuel injector have a pressure drop value that
is either higher than the average pressure drop or
lower than the average pressure drop by the specified
value? 10 kPa
(1.5 psi) Go to Step 10 Go to OBD
System Check
10 Re-test any fuel injector that does not meet the
specification. Refer to the procedure in step 11.
Do not repeat any portion of this test before running
the engine in order to prevent the engine from
flooding.
Does any fuel injector still have a pressure drop value
that is either higher than the average pressure drop or
lower than the average pressure drop by the specified
value? 10 kPa
(1.5 psi) Go to Step 11 Go to
Symptoms
11 Replace the faulty fuel injector(s). Refer to Fuel
Injector.
Is the action complete? — Verify repair —
Page 2107 of 4264
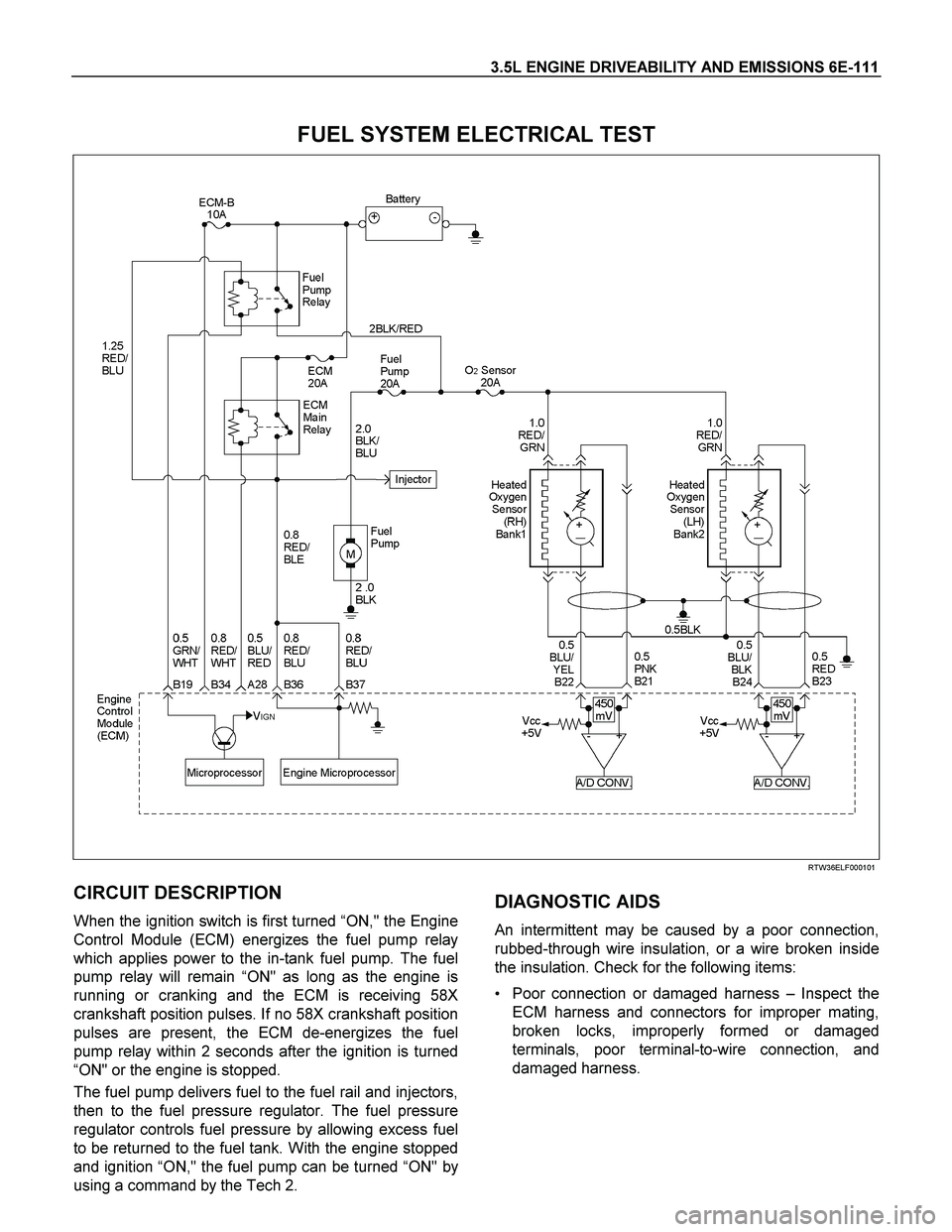
3.5L ENGINE DRIVEABILITY AND EMISSIONS 6E-111
FUEL SYSTEM ELECTRICAL TEST
RTW36ELF000101
CIRCUIT DESCRIPTION
When the ignition switch is first turned “ON," the Engine
Control Module (ECM) energizes the fuel pump relay
which applies power to the in-tank fuel pump. The fuel
pump relay will remain “ON" as long as the engine is
running or cranking and the ECM is receiving 58X
crankshaft position pulses. If no 58X crankshaft position
pulses are present, the ECM de-energizes the fuel
pump relay within 2 seconds after the ignition is turned
“ON" or the engine is stopped.
The fuel pump delivers fuel to the fuel rail and injectors,
then to the fuel pressure regulator. The fuel pressure
regulator controls fuel pressure by allowing excess fuel
to be returned to the fuel tank. With the engine stopped
and ignition “ON," the fuel pump can be turned “ON" by
using a command by the Tech 2.
DIAGNOSTIC AIDS
An intermittent may be caused by a poor connection,
rubbed-through wire insulation, or a wire broken inside
the insulation. Check for the following items:
Poor connection or damaged harness –Inspect the
ECM harness and connectors for improper mating,
broken locks, improperly formed or damaged
terminals, poor terminal-to-wire connection, and
damaged harness.
Page 2108 of 4264

6E-112 3.5L ENGINE DRIVEABILITY AND EMISSIONS
CAUTION: To reduce the risk of fire and personal
injury:
It is necessary to relieve fuel system pressure
before connecting a fuel pressure gauge. Refer to
Fuel Pressure Relief Procedure, below.
A small amount of fuel may be released when
disconnecting the fuel lines. Cover fuel line
fittings with a shop towel before disconnecting,
to catch any fuel that may leak out. Place the
towel in an approved container when the
disconnect is completed.
FUEL PRESSURE RELIEF PROCEDURE
1. Remove the fuel cap.
2. Remove the fuel pump relay from the underhood
relay center.
3. Start the engine and allow it to stall.
4. Crank the engine for an additional 3 seconds.
FUEL GAUGE INSTALLATION
1. Remove the fuel pressure fitting cap.
2. Install fuel gauge 5-8840-0378-0 to the fuel feed line
located in front of and above the right side valve
cover.
3. Reinstall the fuel pump relay.
Fuel System Electrical Test
Step Action Value (s) Yes No
1
Was the "On-Board Diagnostic (OBD) System Check"
performed?
- Go to Step 2 Go to On Board
Diagnostic (OBD)
System Check
2
1. Using the Tech 2, ignition "On" and engine "On".
2. Select the "Miscellaneous Test" and perform the
"Fuel Pump Relay" in the "Relays".
3. Operate the Tech 2 in accordance with procedure.
Was the fuel pump operated, when the Tech 2 is
operated?
- Test completed Go to Step 3
3
Check the "Fuel Pump" fuse (20A). If the fuse is burnt
out, repair as necessary.
Was the problem found?
- Verify repair Go to Step 4
4
Check for poor/faulty connection at the fuel pump, fuel
pump relay or ECM connector. If a poor/faulty
connection is found, repair as necessary.
E-61(B)
X-2
F-2
C-109
Was the problem found?
- Verify repair Go to Step 5
Page 2109 of 4264
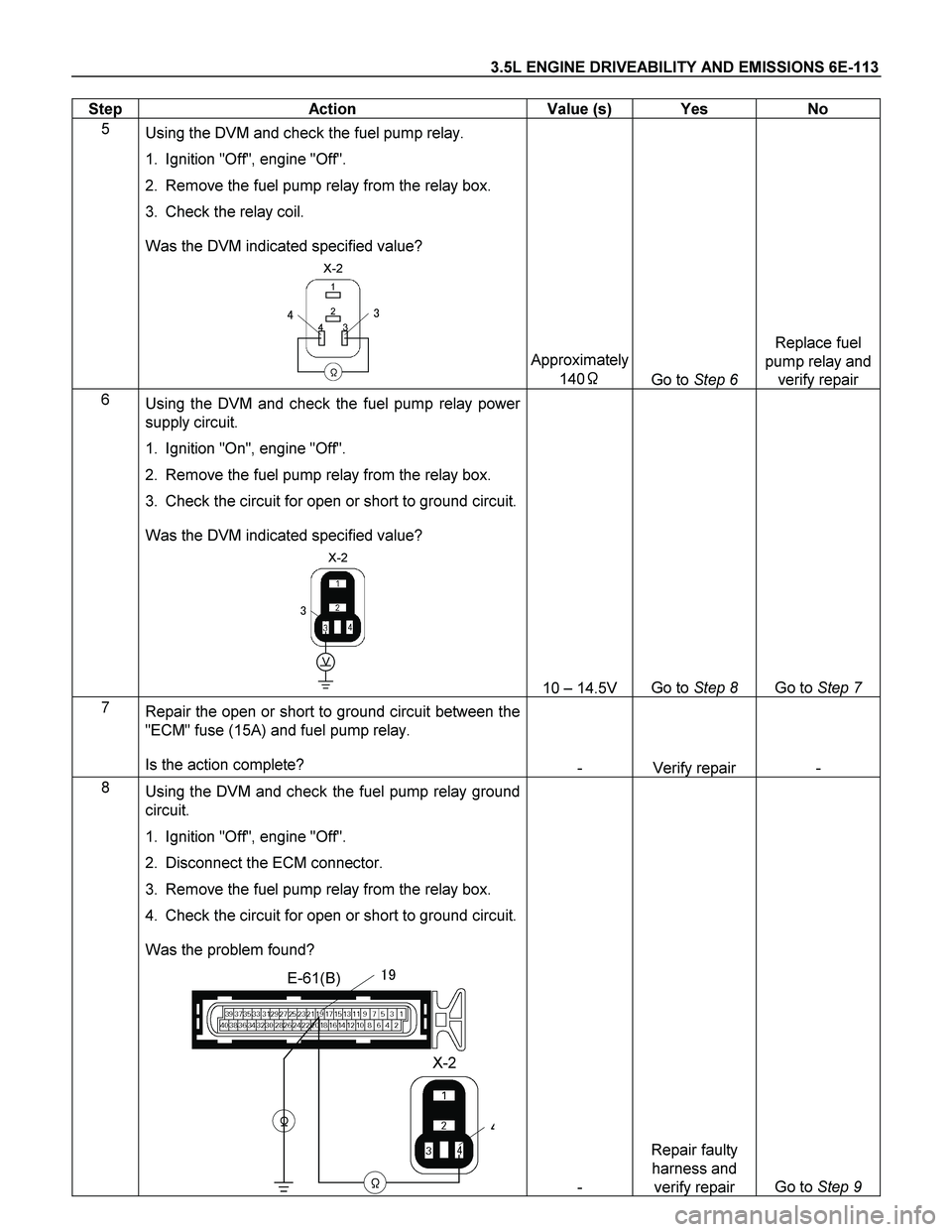
3.5L ENGINE DRIVEABILITY AND EMISSIONS 6E-113
Step Action Value (s) Yes No
5
Using the DVM and check the fuel pump relay.
1. Ignition "Off", engine "Off".
2. Remove the fuel pump relay from the relay box.
3. Check the relay coil.
Was the DVM indicated specified value?
X-2
1
3 2
4
Approximately
140
Go to Step 6 Replace fuel
pump relay and
verify repair
6
Using the DVM and check the fuel pump relay power
supply circuit.
1. Ignition "On", engine "Off".
2. Remove the fuel pump relay from the relay box.
3. Check the circuit for open or short to ground circuit.
Was the DVM indicated specified value?
X-2
V
10 – 14.5V Go to Step 8 Go to Step 7
7
Repair the open or short to ground circuit between the
"ECM" fuse (15A) and fuel pump relay.
Is the action complete?
- Verify repair -
8
Using the DVM and check the fuel pump relay ground
circuit.
1. Ignition "Off", engine "Off".
2. Disconnect the ECM connector.
3. Remove the fuel pump relay from the relay box.
4. Check the circuit for open or short to ground circuit.
Was the problem found?
E-61(B)
X-2
- Repair faulty
harness and
verify repair Go to Step 9
Page 2110 of 4264
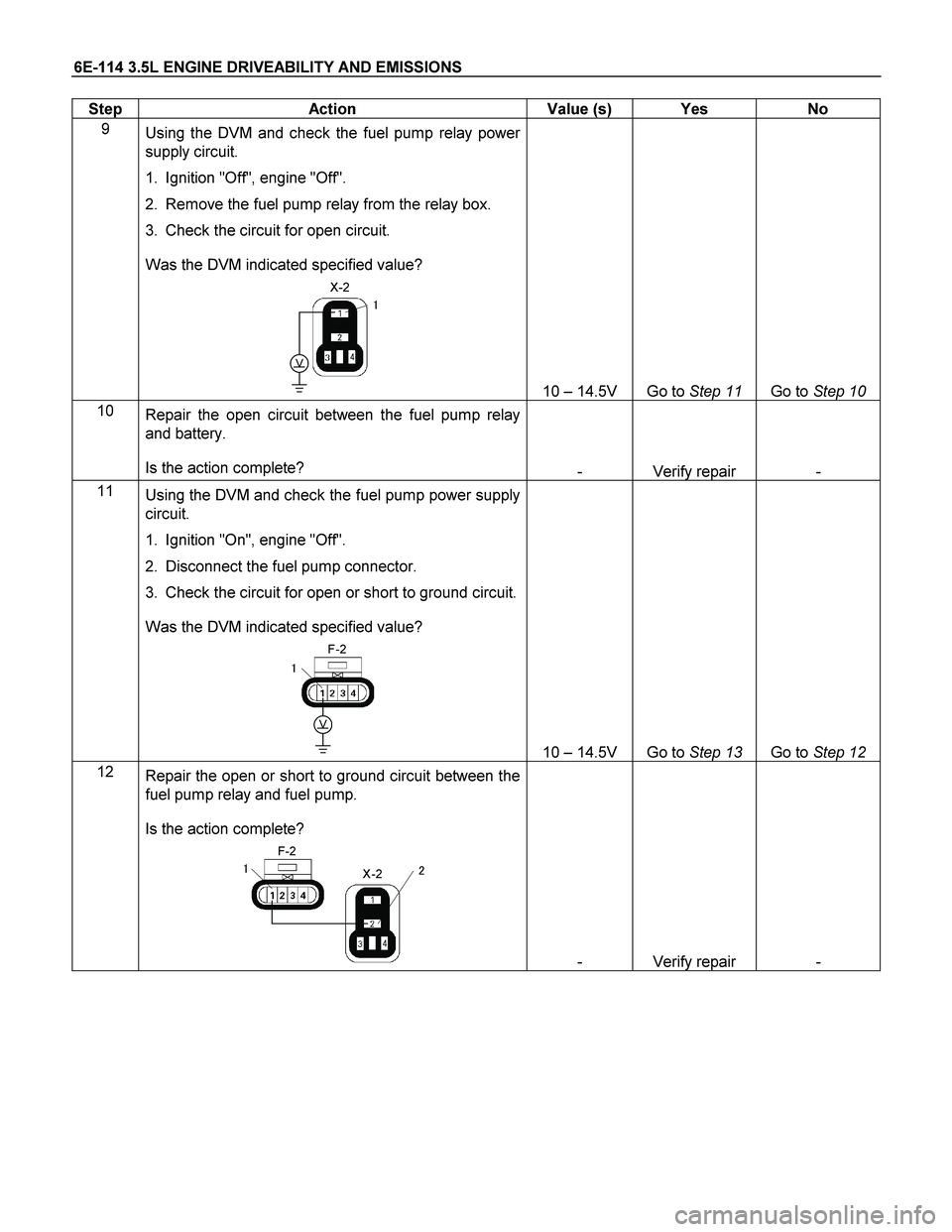
6E-114 3.5L ENGINE DRIVEABILITY AND EMISSIONS
Step Action Value (s) Yes No
9
Using the DVM and check the fuel pump relay power
supply circuit.
1. Ignition "Off", engine "Off".
2. Remove the fuel pump relay from the relay box.
3. Check the circuit for open circuit.
Was the DVM indicated specified value?
X-2
V
10 – 14.5V Go to Step 11 Go to Step 10
10
Repair the open circuit between the fuel pump relay
and battery.
Is the action complete?
- Verify repair -
11
Using the DVM and check the fuel pump power supply
circuit.
1. Ignition "On", engine "Off".
2. Disconnect the fuel pump connector.
3. Check the circuit for open or short to ground circuit.
Was the DVM indicated specified value?
F-2
V
10 – 14.5V Go to Step 13 Go to Step 12
12
Repair the open or short to ground circuit between the
fuel pump relay and fuel pump.
Is the action complete?
F-2
X-2
- Verify repair -
Page 2111 of 4264
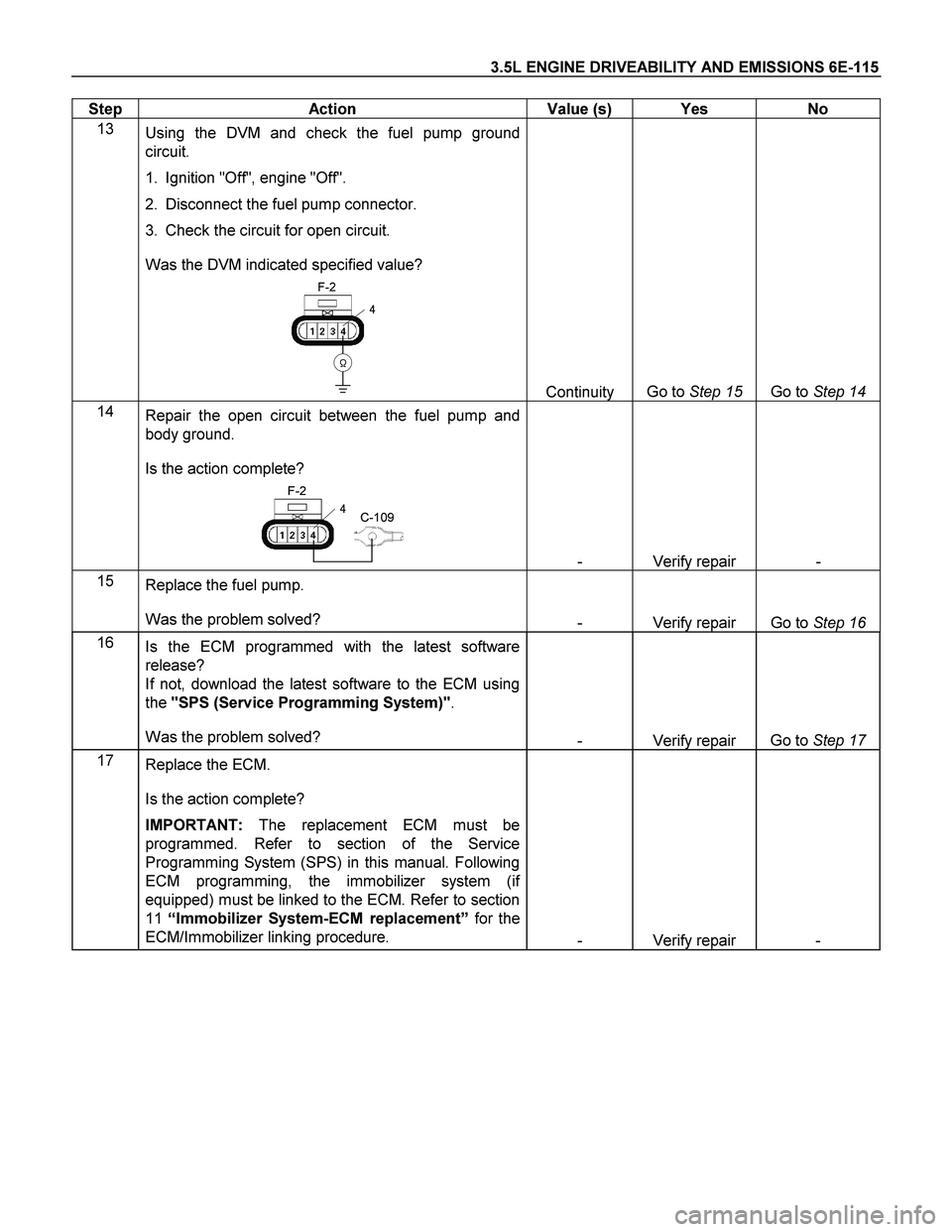
3.5L ENGINE DRIVEABILITY AND EMISSIONS 6E-115
Step Action Value (s) Yes No
13
Using the DVM and check the fuel pump ground
circuit.
1. Ignition "Off", engine "Off".
2. Disconnect the fuel pump connector.
3. Check the circuit for open circuit.
Was the DVM indicated specified value?
F-2
Continuity Go to Step 15 Go to Step 14
14
Repair the open circuit between the fuel pump and
body ground.
Is the action complete?
F-2
C-109
- Verify repair -
15
Replace the fuel pump.
Was the problem solved?
- Verify repair Go to Step 16
16
Is the ECM programmed with the latest software
release?
If not, download the latest software to the ECM using
the "SPS (Service Programming System)".
Was the problem solved?
- Verify repair Go to Step 17
17
Replace the ECM.
Is the action complete?
IMPORTANT: The replacement ECM must be
programmed. Refer to section of the Service
Programming System (SPS) in this manual. Following
ECM programming, the immobilizer system (if
equipped) must be linked to the ECM. Refer to section
11 “Immobilizer System-ECM replacement” for the
ECM/Immobilizer linking procedure.
- Verify repair -
Page 2112 of 4264
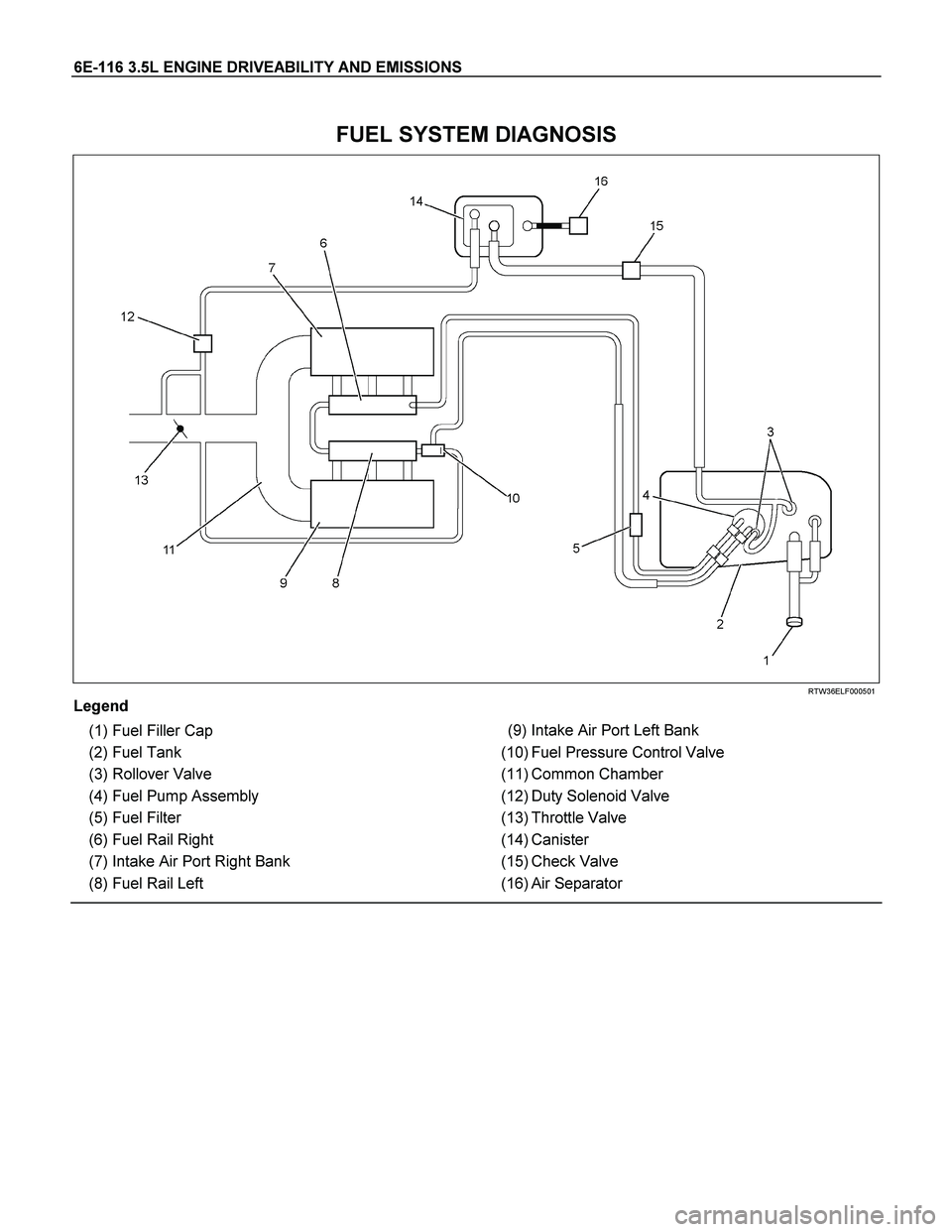
6E-116 3.5L ENGINE DRIVEABILITY AND EMISSIONS
FUEL SYSTEM DIAGNOSIS
RTW36ELF000501
Legend
(1) Fuel Filler Cap
(2) Fuel Tank
(3) Rollover Valve
(4) Fuel Pump Assembly
(5) Fuel Filter
(6) Fuel Rail Right
(7) Intake Air Port Right Bank
(8) Fuel Rail Left
(9) Intake Air Port Left Bank
(10) Fuel Pressure Control Valve
(11) Common Chamber
(12) Duty Solenoid Valve
(13) Throttle Valve
(14) Canister
(15) Check Valve
(16) Air Separator