oil pressure ISUZU TF SERIES 2004 Repair Manual
[x] Cancel search | Manufacturer: ISUZU, Model Year: 2004, Model line: TF SERIES, Model: ISUZU TF SERIES 2004Pages: 4264, PDF Size: 72.63 MB
Page 1908 of 4264
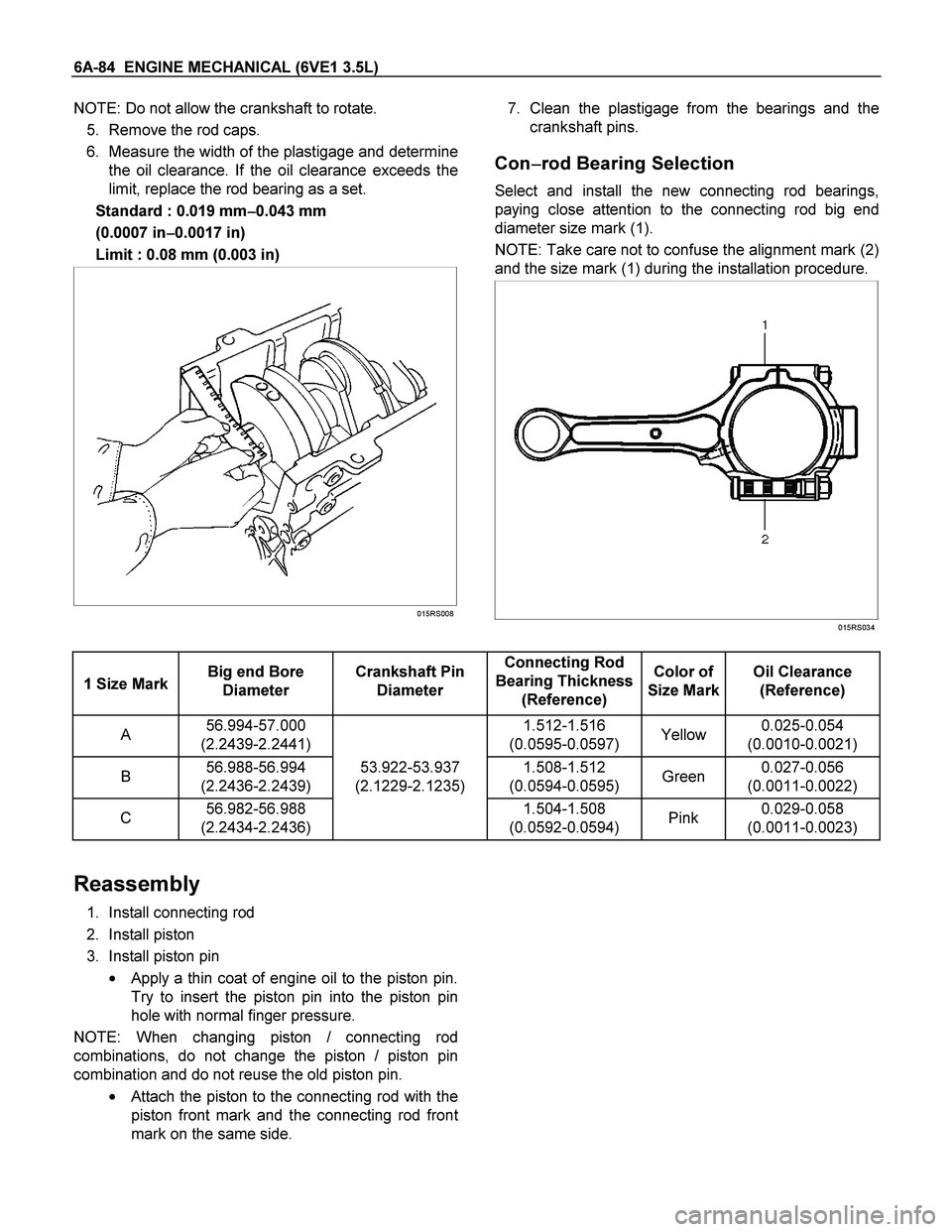
6A-84 ENGINE MECHANICAL (6VE1 3.5L)
NOTE: Do not allow the crankshaft to rotate.
5. Remove the rod caps.
6. Measure the width of the plastigage and determine
the oil clearance. If the oil clearance exceeds the
limit, replace the rod bearing as a set.
Standard : 0.019 mm
0.043 mm
(0.0007 in
0.0017 in)
Limit : 0.08 mm (0.003 in)
015RS008
7. Clean the plastigage from the bearings and the
crankshaft pins.
Con
rod Bearing Selection
Select and install the new connecting rod bearings,
paying close attention to the connecting rod big end
diameter size mark (1).
NOTE: Take care not to confuse the alignment mark (2)
and the size mark (1) during the installation procedure.
015RS034
1 Size Mark Big end Bore
Diameter Crankshaft Pin
Diameter Connecting Rod
Bearing Thickness
(Reference) Color of
Size Mark Oil Clearance
(Reference)
A 56.994-57.000
(2.2439-2.2441) 1.512-1.516
(0.0595-0.0597) Yellow 0.025-0.054
(0.0010-0.0021)
B 56.988-56.994
(2.2436-2.2439) 53.922-53.937
(2.1229-2.1235) 1.508-1.512
(0.0594-0.0595) Green 0.027-0.056
(0.0011-0.0022)
C 56.982-56.988
(2.2434-2.2436) 1.504-1.508
(0.0592-0.0594) Pink 0.029-0.058
(0.0011-0.0023)
Reassembly
1. Install connecting rod
2. Install piston
3. Install piston pin
Apply a thin coat of engine oil to the piston pin.
Try to insert the piston pin into the piston pin
hole with normal finger pressure.
NOTE: When changing piston / connecting rod
combinations, do not change the piston / piston pin
combination and do not reuse the old piston pin.
Attach the piston to the connecting rod with the
piston front mark and the connecting rod fron
t
mark on the same side.
Page 1912 of 4264
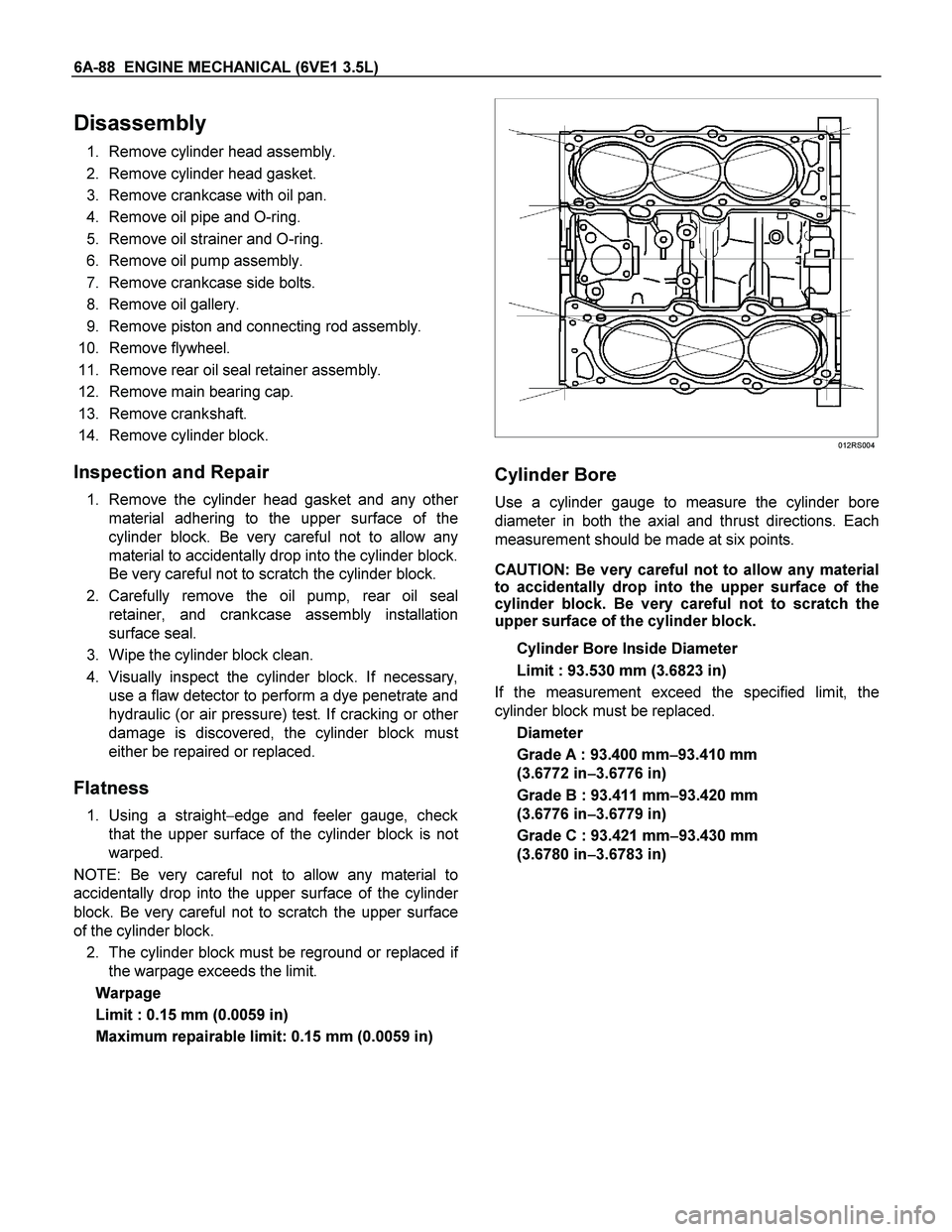
6A-88 ENGINE MECHANICAL (6VE1 3.5L)
Disassembly
1. Remove cylinder head assembly.
2. Remove cylinder head gasket.
3. Remove crankcase with oil pan.
4. Remove oil pipe and O-ring.
5. Remove oil strainer and O-ring.
6. Remove oil pump assembly.
7. Remove crankcase side bolts.
8. Remove oil gallery.
9. Remove piston and connecting rod assembly.
10. Remove flywheel.
11. Remove rear oil seal retainer assembly.
12. Remove main bearing cap.
13. Remove crankshaft.
14. Remove cylinder block.
Inspection and Repair
1. Remove the cylinder head gasket and any other
material adhering to the upper surface of the
cylinder block. Be very careful not to allow any
material to accidentally drop into the cylinder block.
Be very careful not to scratch the cylinder block.
2. Carefully remove the oil pump, rear oil seal
retainer, and crankcase assembly installation
surface seal.
3. Wipe the cylinder block clean.
4. Visually inspect the cylinder block. If necessary,
use a flaw detector to perform a dye penetrate and
hydraulic (or air pressure) test. If cracking or othe
r
damage is discovered, the cylinder block must
either be repaired or replaced.
Flatness
1. Using a straightedge and feeler gauge, check
that the upper surface of the cylinder block is no
t
warped.
NOTE: Be very careful not to allow any material to
accidentally drop into the upper surface of the cylinde
r
block. Be very careful not to scratch the upper surface
of the cylinder block.
2. The cylinder block must be reground or replaced i
f
the warpage exceeds the limit.
Warpage
Limit : 0.15 mm (0.0059 in)
Maximum repairable limit: 0.15 mm (0.0059 in)
012RS004
Cylinder Bore
Use a cylinder gauge to measure the cylinder bore
diameter in both the axial and thrust directions. Each
measurement should be made at six points.
CAUTION: Be very careful not to allow any material
to accidentally drop into the upper surface of the
cylinder block. Be very careful not to scratch the
upper surface of the cylinder block.
Cylinder Bore Inside Diameter
Limit : 93.530 mm (3.6823 in)
If the measurement exceed the specified limit, the
cylinder block must be replaced.
Diameter
Grade A : 93.400 mm
93.410 mm
(3.6772 in
3.6776 in)
Grade B : 93.411 mm
93.420 mm
(3.6776 in
3.6779 in)
Grade C : 93.421 mm
93.430 mm
(3.6780 in
3.6783 in)
Page 1917 of 4264
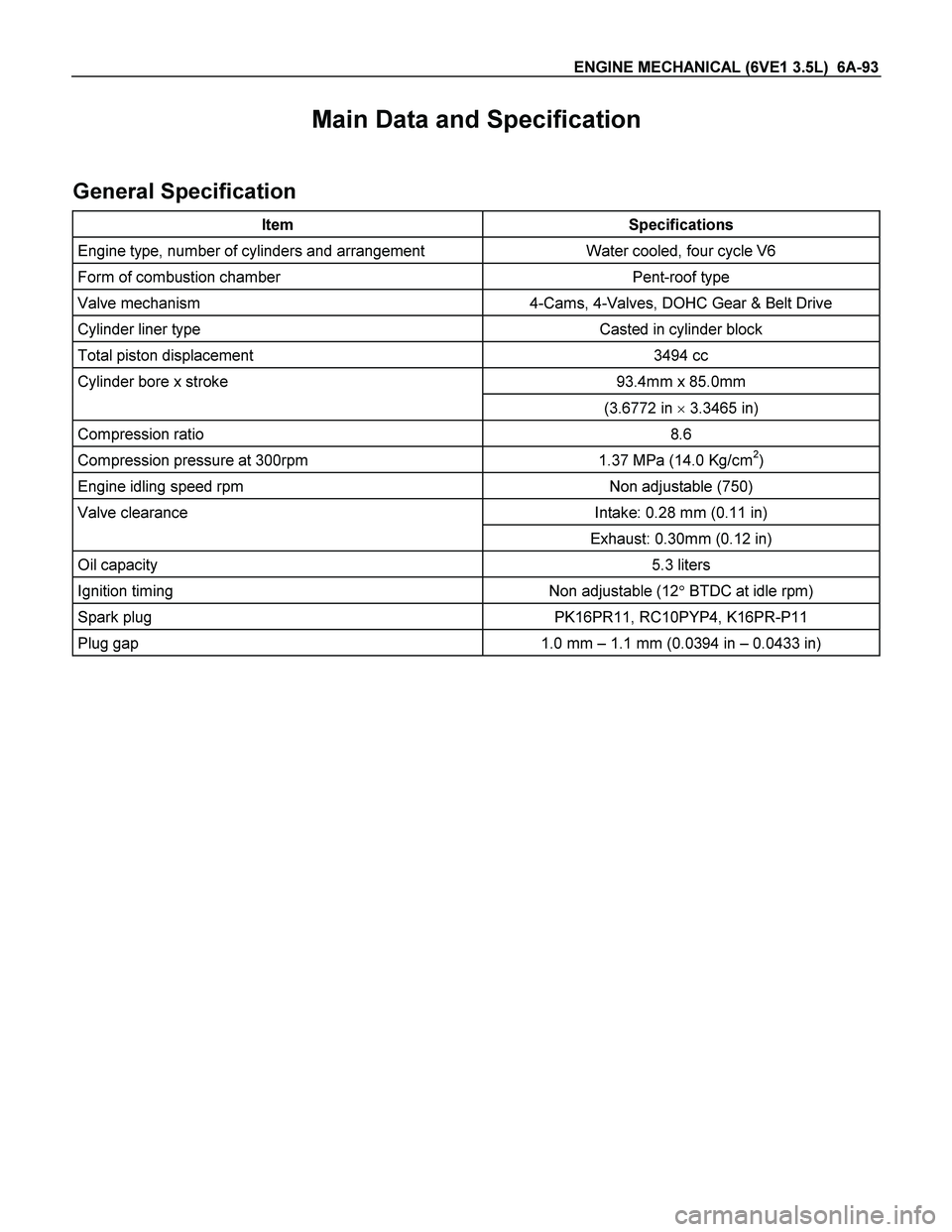
ENGINE MECHANICAL (6VE1 3.5L) 6A-93
Main Data and Specification
General Specification
Item Specifications
Engine type, number of cylinders and arrangement Water cooled, four cycle V6
Form of combustion chamber Pent-roof type
Valve mechanism 4-Cams, 4-Valves, DOHC Gear & Belt Drive
Cylinder liner type Casted in cylinder block
Total piston displacement 3494 cc
Cylinder bore x stroke 93.4mm x 85.0mm
(3.6772 in 3.3465 in)
Compression ratio 8.6
Compression pressure at 300rpm 1.37 MPa (14.0 Kg/cm2)
Engine idling speed rpm Non adjustable (750)
Valve clearance Intake: 0.28 mm (0.11 in)
Exhaust: 0.30mm (0.12 in)
Oil capacity 5.3 liters
Ignition timing
Non adjustable (12 BTDC at idle rpm)
Spark plug PK16PR11, RC10PYP4, K16PR-P11
Plug gap 1.0 mm – 1.1 mm (0.0394 in – 0.0433 in)
Page 1927 of 4264
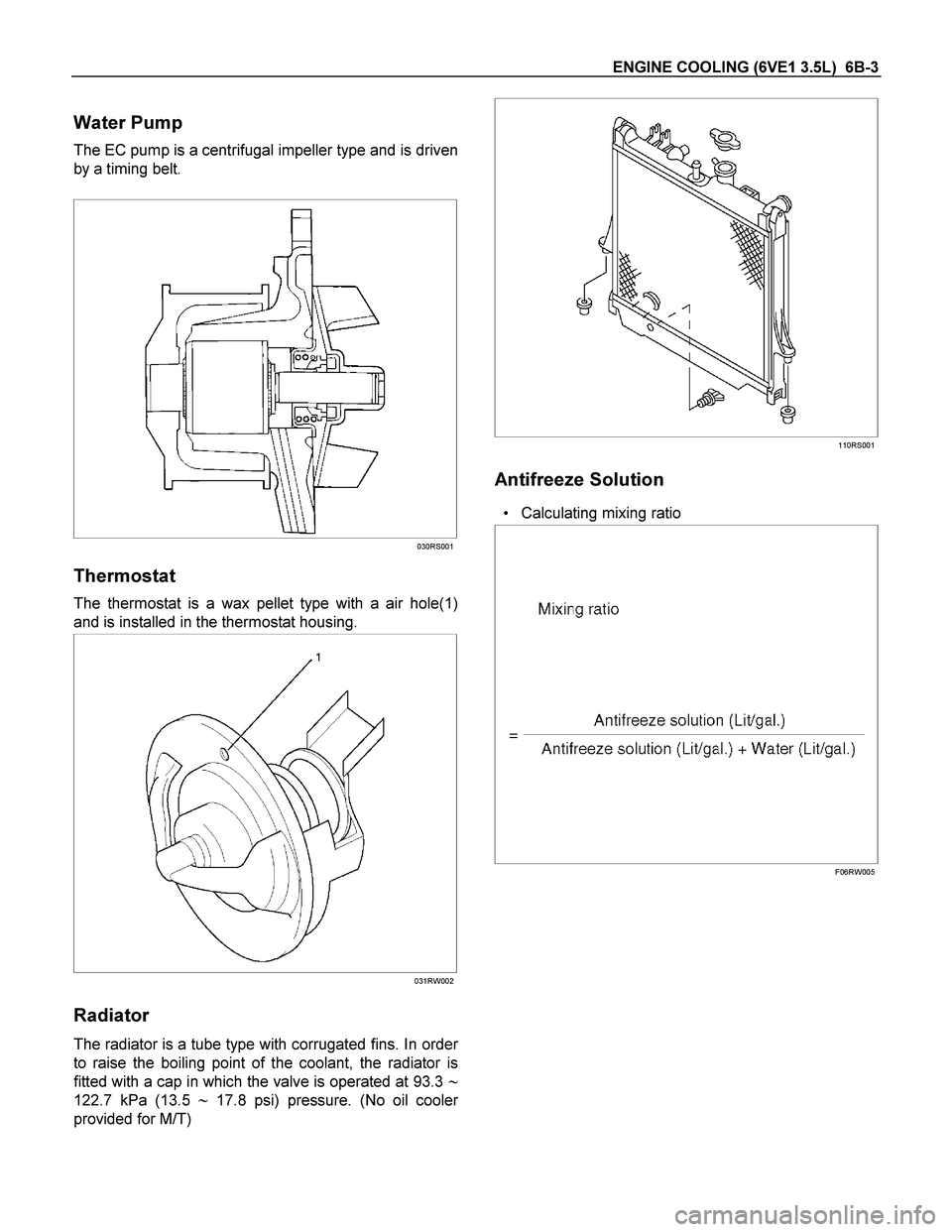
ENGINE COOLING (6VE1 3.5L) 6B-3
Water Pump
The EC pump is a centrifugal impeller type and is driven
by a timing belt.
030RS001
Thermostat
The thermostat is a wax pellet type with a air hole(1)
and is installed in the thermostat housing.
031RW002
Radiator
The radiator is a tube type with corrugated fins. In order
to raise the boiling point of the coolant, the radiator is
fitted with a cap in which the valve is operated at 93.3
122.7 kPa (13.5 17.8 psi) pressure. (No oil cooler
provided for M/T)
110RS001
Antifreeze Solution
Calculating mixing ratio
F06RW005
Page 1930 of 4264
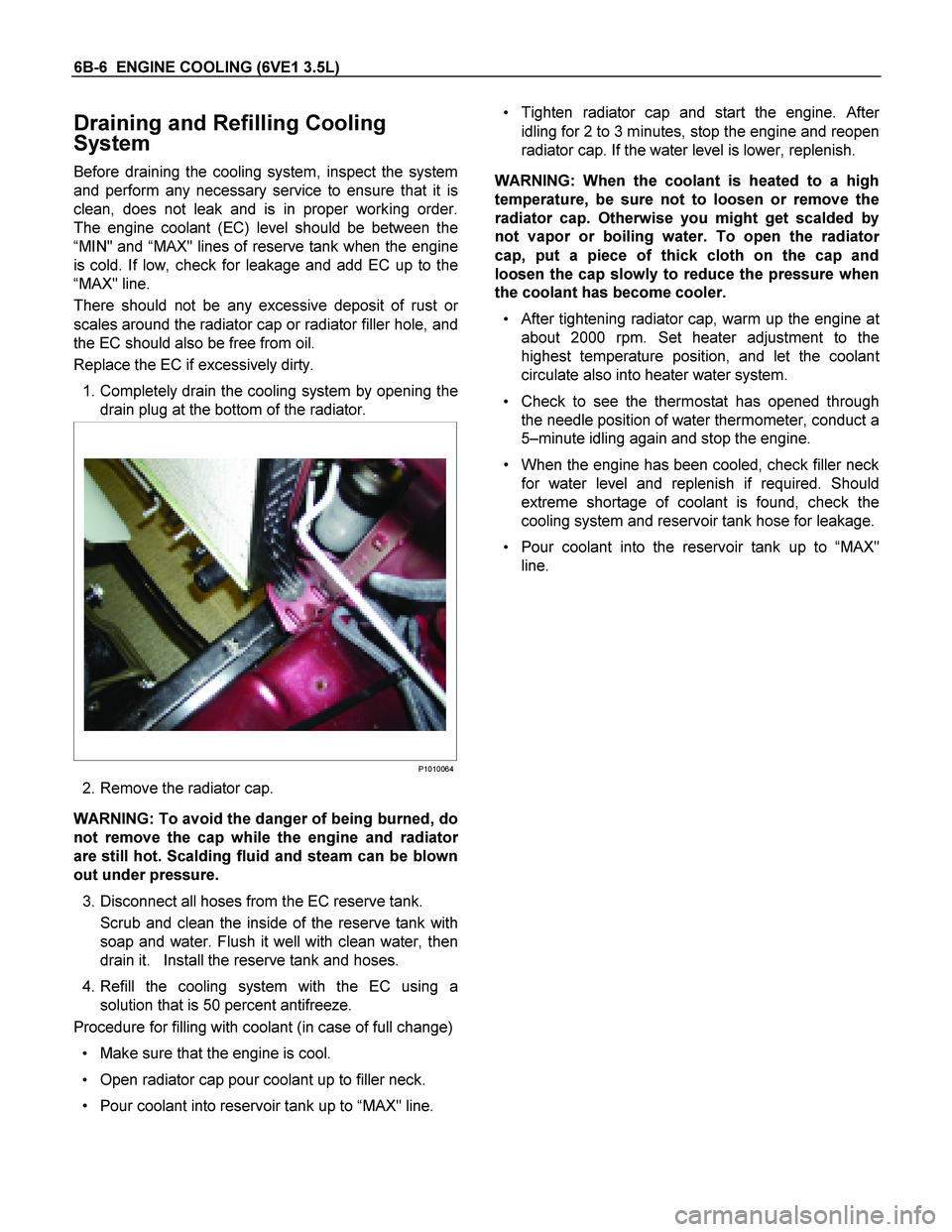
6B-6 ENGINE COOLING (6VE1 3.5L)
Draining and Refilling Cooling
System
Before draining the cooling system, inspect the system
and perform any necessary service to ensure that it is
clean, does not leak and is in proper working order.
The engine coolant (EC) level should be between the
“ MIN" and “MAX" lines of reserve tank when the engine
is cold. If low, check for leakage and add EC up to the
“ MAX" line.
There should not be any excessive deposit of rust o
r
scales around the radiator cap or radiator filler hole, and
the EC should also be free from oil.
Replace the EC if excessively dirty.
1. Completely drain the cooling system by opening the
drain plug at the bottom of the radiator.
P1010064
2. Remove the radiator cap.
WARNING: To avoid the danger of being burned, do
not remove the cap while the engine and radiato
r
are still hot. Scalding fluid and steam can be blown
out under pressure.
3. Disconnect all hoses from the EC reserve tank.
Scrub and clean the inside of the reserve tank with
soap and water. Flush it well with clean water, then
drain it. Install the reserve tank and hoses.
4. Refill the cooling system with the EC using a
solution that is 50 percent antifreeze.
Procedure for filling with coolant (in case of full change)
Make sure that the engine is cool.
Open radiator cap pour coolant up to filler neck.
Pour coolant into reservoir tank up to “MAX" line.
Tighten radiator cap and start the engine. Afte
r
idling for 2 to 3 minutes, stop the engine and reopen
radiator cap. If the water level is lower, replenish.
WARNING: When the coolant is heated to a high
temperature, be sure not to loosen or remove the
radiator cap. Otherwise you might get scalded by
not vapor or boiling water. To open the radiato
r
cap, put a piece of thick cloth on the cap and
loosen the cap slowly to reduce the pressure when
the coolant has become cooler.
After tightening radiator cap, warm up the engine at
about 2000 rpm. Set heater adjustment to the
highest temperature position, and let the coolan
t
circulate also into heater water system.
Check to see the thermostat has opened through
the needle position of water thermometer, conduct a
5 –minute idling again and stop the engine.
When the engine has been cooled, check filler neck
for water level and replenish if required. Should
extreme shortage of coolant is found, check the
cooling system and reservoir tank hose for leakage.
Pour coolant into the reservoir tank up to “MAX"
line.
Page 1935 of 4264
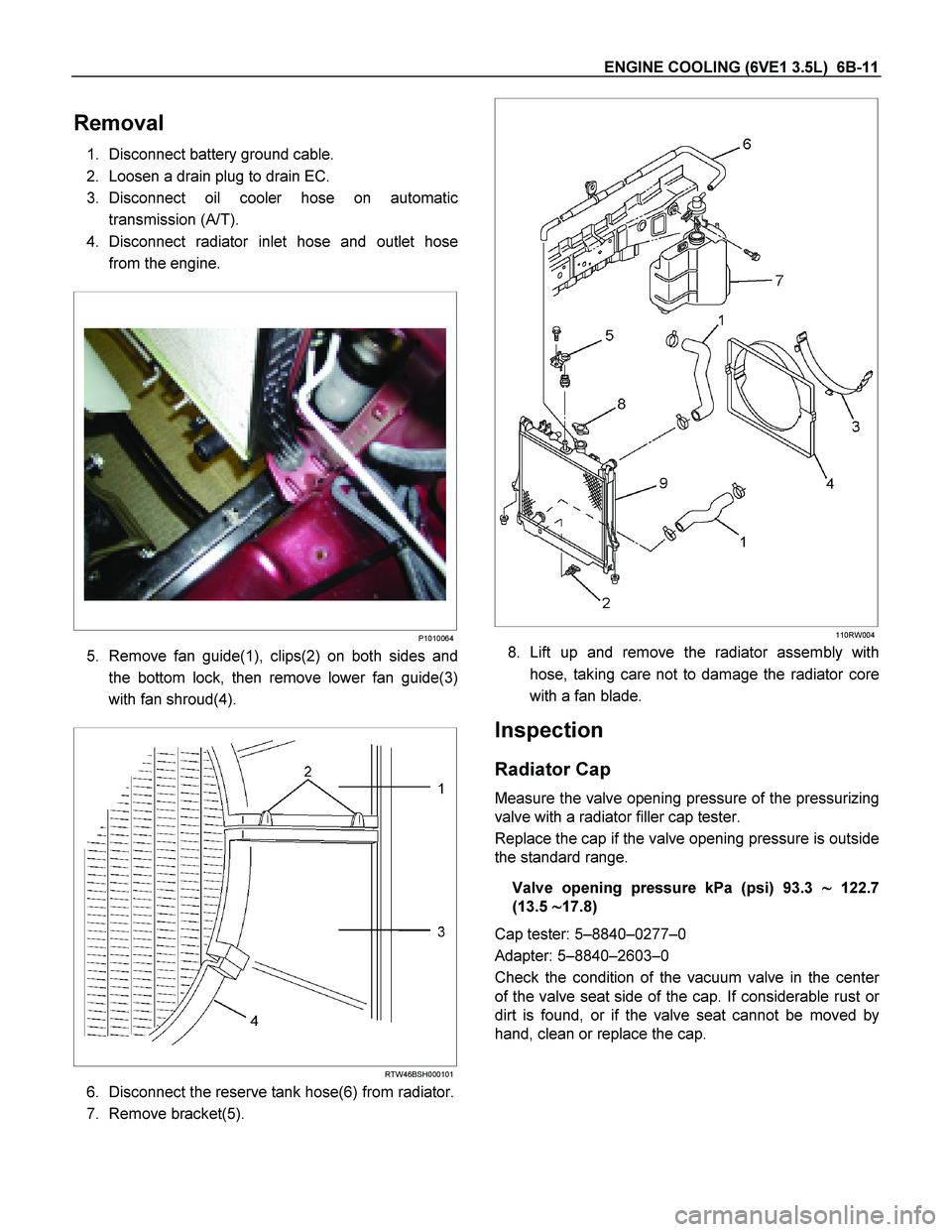
ENGINE COOLING (6VE1 3.5L) 6B-11
Removal
1. Disconnect battery ground cable.
2. Loosen a drain plug to drain EC.
3. Disconnect oil cooler hose on automatic transmission (A/T).
4. Disconnect radiator inlet hose and outlet hose from the engine.
P1010064
5. Remove fan guide(1), clips(2) on both sides and
the bottom lock, then remove lower fan guide(3)
with fan shroud(4).
RTW46BSH000101
6. Disconnect the reserve tank hose(6) from radiator.
7. Remove bracket(5).
110RW004
8. Lift up and remove the radiator assembly with
hose, taking care not to damage the radiator core
with a fan blade.
Inspection
Radiator Cap
Measure the valve opening pressure of the pressurizing
valve with a radiator filler cap tester.
Replace the cap if the valve opening pressure is outside
the standard range.
Valve opening pressure kPa (psi) 93.3
122.7
(13.5
17.8)
Cap tester: 5 –8840 –0277 –0
Adapter: 5 –8840 –2603 –0
Check the condition of the vacuum valve in the cente
r
of the valve seat side of the cap. If considerable rust or
dirt is found, or if the valve seat cannot be moved by
hand, clean or replace the cap.
Page 1937 of 4264
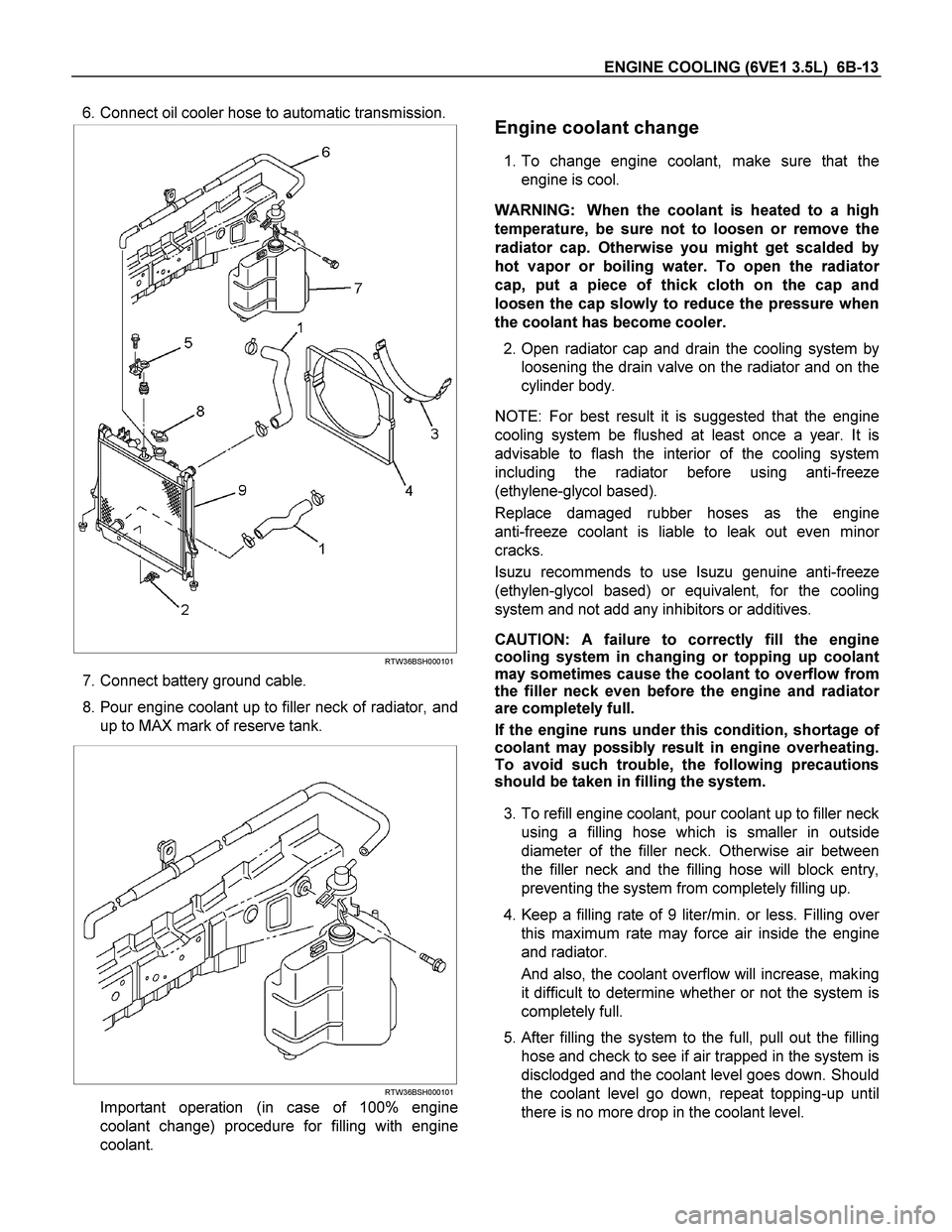
ENGINE COOLING (6VE1 3.5L) 6B-13
6. Connect oil cooler hose to automatic transmission.
RTW36BSH000101
7. Connect battery ground cable.
8. Pour engine coolant up to filler neck of radiator, and
up to MAX mark of reserve tank.
RTW36BSH000101
Important operation (in case of 100% engine
coolant change) procedure for filling with engine
coolant.
Engine coolant change
1. To change engine coolant, make sure that the
engine is cool.
WARNING: When the coolant is heated to a high
temperature, be sure not to loosen or remove the
radiator cap. Otherwise you might get scalded by
hot vapor or boiling water. To open the radiato
r
cap, put a piece of thick cloth on the cap and
loosen the cap slowly to reduce the pressure when
the coolant has become cooler.
2. Open radiator cap and drain the cooling system by
loosening the drain valve on the radiator and on the
cylinder body.
NOTE: For best result it is suggested that the engine
cooling system be flushed at least once a year. It is
advisable to flash the interior of the cooling system
including the radiator before using anti-freeze
(ethylene-glycol based).
Replace damaged rubber hoses as the engine
anti-freeze coolant is liable to leak out even mino
r
cracks.
Isuzu recommends to use Isuzu genuine anti-freeze
(ethylen-glycol based) or equivalent, for the cooling
system and not add any inhibitors or additives.
CAUTION: A failure to correctly fill the engine
cooling system in changing or topping up coolant
may sometimes cause the coolant to overflow from
the filler neck even before the engine and radiato
r
are completely full.
If the engine runs under this condition, shortage o
f
coolant may possibly result in engine overheating.
To avoid such trouble, the following precautions
should be taken in filling the system.
3. To refill engine coolant, pour coolant up to filler neck
using a filling hose which is smaller in outside
diameter of the filler neck. Otherwise air between
the filler neck and the filling hose will block entry,
preventing the system from completely filling up.
4. Keep a filling rate of 9 liter/min. or less. Filling ove
r
this maximum rate may force air inside the engine
and radiator.
And also, the coolant overflow will increase, making
it difficult to determine whether or not the system is
completely full.
5.
After filling the system to the full, pull out the filling
hose and check to see if air trapped in the system is
disclodged and the coolant level goes down. Should
the coolant level go down, repeat topping-up until
there is no more drop in the coolant level.
Page 1938 of 4264
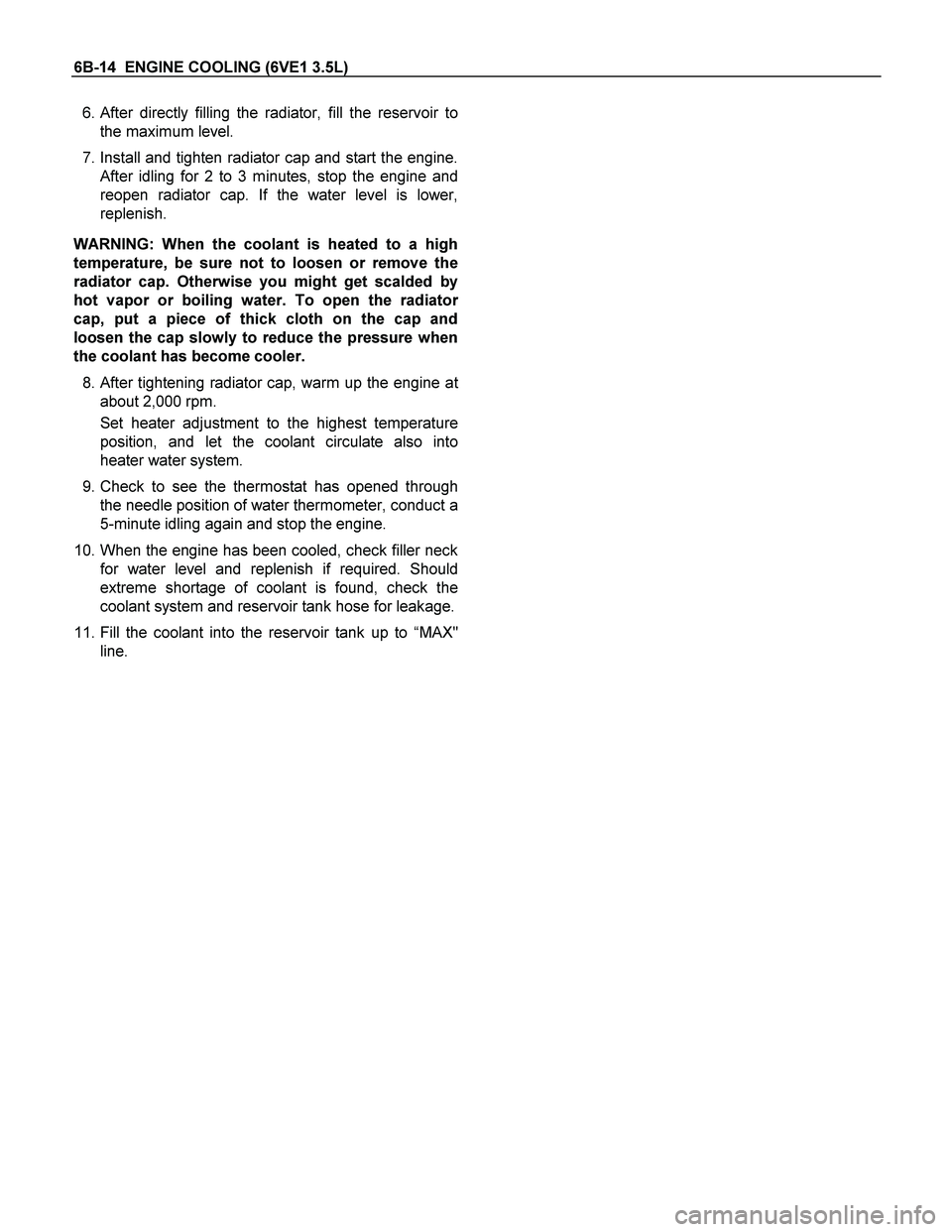
6B-14 ENGINE COOLING (6VE1 3.5L)
6. After directly filling the radiator, fill the reservoir to
the maximum level.
7. Install and tighten radiator cap and start the engine.
After idling for 2 to 3 minutes, stop the engine and
reopen radiator cap. If the water level is lower,
replenish.
WARNING: When the coolant is heated to a high
temperature, be sure not to loosen or remove the
radiator cap. Otherwise you might get scalded by
hot vapor or boiling water. To open the radiato
r
cap, put a piece of thick cloth on the cap and
loosen the cap slowly to reduce the pressure when
the coolant has become cooler.
8.
After tightening radiator cap, warm up the engine at
about 2,000 rpm.
Set heater adjustment to the highest temperature
position, and let the coolant circulate also into
heater water system.
9. Check to see the thermostat has opened through
the needle position of water thermometer, conduct a
5-minute idling again and stop the engine.
10. When the engine has been cooled, check filler neck
for water level and replenish if required. Should
extreme shortage of coolant is found, check the
coolant system and reservoir tank hose for leakage.
11. Fill the coolant into the reservoir tank up to “MAX"
line.
Page 1943 of 4264
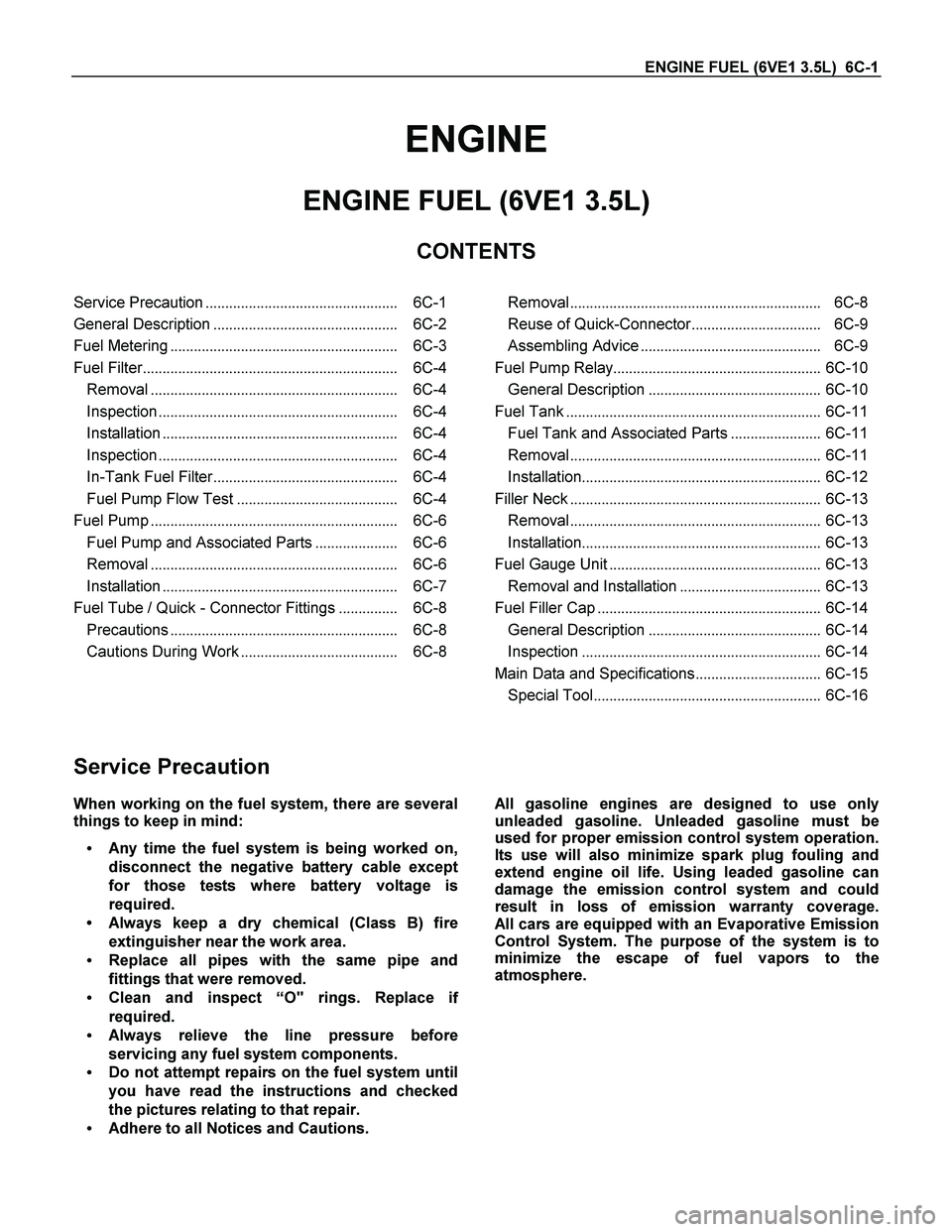
ENGINE FUEL (6VE1 3.5L) 6C-1
ENGINE
ENGINE FUEL (6VE1 3.5L)
CONTENTS
Service Precaution................................................. 6C-1
General Description............................................... 6C-2
Fuel Metering.......................................................... 6C-3
Fuel Filter................................................................. 6C-4
Removal............................................................... 6C-4
Inspection............................................................. 6C-4
Installation............................................................ 6C-4
Inspection............................................................. 6C-4
In-Tank Fuel Filter............................................... 6C-4
Fuel Pump Flow Test......................................... 6C-4
Fuel Pump............................................................... 6C-6
Fuel Pump and Associated Parts..................... 6C-6
Removal............................................................... 6C-6
Installation............................................................ 6C-7
Fuel Tube / Quick - Connector Fittings............... 6C-8
Precautions.......................................................... 6C-8
Cautions During Work........................................ 6C-8
Removal................................................................ 6C-8
Reuse of Quick-Connector................................. 6C-9
Assembling Advice.............................................. 6C-9
Fuel Pump Relay..................................................... 6C-10
General Description............................................ 6C-10
Fuel Tank................................................................. 6C-11
Fuel Tank and Associated Parts....................... 6C-11
Removal................................................................ 6C-11
Installation............................................................. 6C-12
Filler Neck................................................................ 6C-13
Removal................................................................ 6C-13
Installation............................................................. 6C-13
Fuel Gauge Unit...................................................... 6C-13
Removal and Installation.................................... 6C-13
Fuel Filler Cap......................................................... 6C-14
General Description............................................ 6C-14
Inspection............................................................. 6C-14
Main Data and Specifications................................ 6C-15
Special Tool.......................................................... 6C-16
Service Precaution
When working on the fuel system, there are several
things to keep in mind:
Any time the fuel system is being worked on,
disconnect the negative battery cable except
for those tests where battery voltage is
required.
Always keep a dry chemical (Class B) fire
extinguisher near the work area.
Replace all pipes with the same pipe and
fittings that were removed.
Clean and inspect “O" rings. Replace i
f
required.
Always relieve the line pressure before
servicing any fuel system components.
Do not attempt repairs on the fuel system until
you have read the instructions and checked
the pictures relating to that repair.
Adhere to all Notices and Cautions.
All gasoline engines are designed to use only
unleaded gasoline. Unleaded gasoline must be
used for proper emission control system operation.
Its use will also minimize spark plug fouling and
extend engine oil life. Using leaded gasoline can
damage the emission control system and could
result in loss of emission warranty coverage.
All cars are equipped with an Evaporative Emission
Control System. The purpose of the system is to
minimize the escape of fuel vapors to the
atmosphere.
Page 1950 of 4264
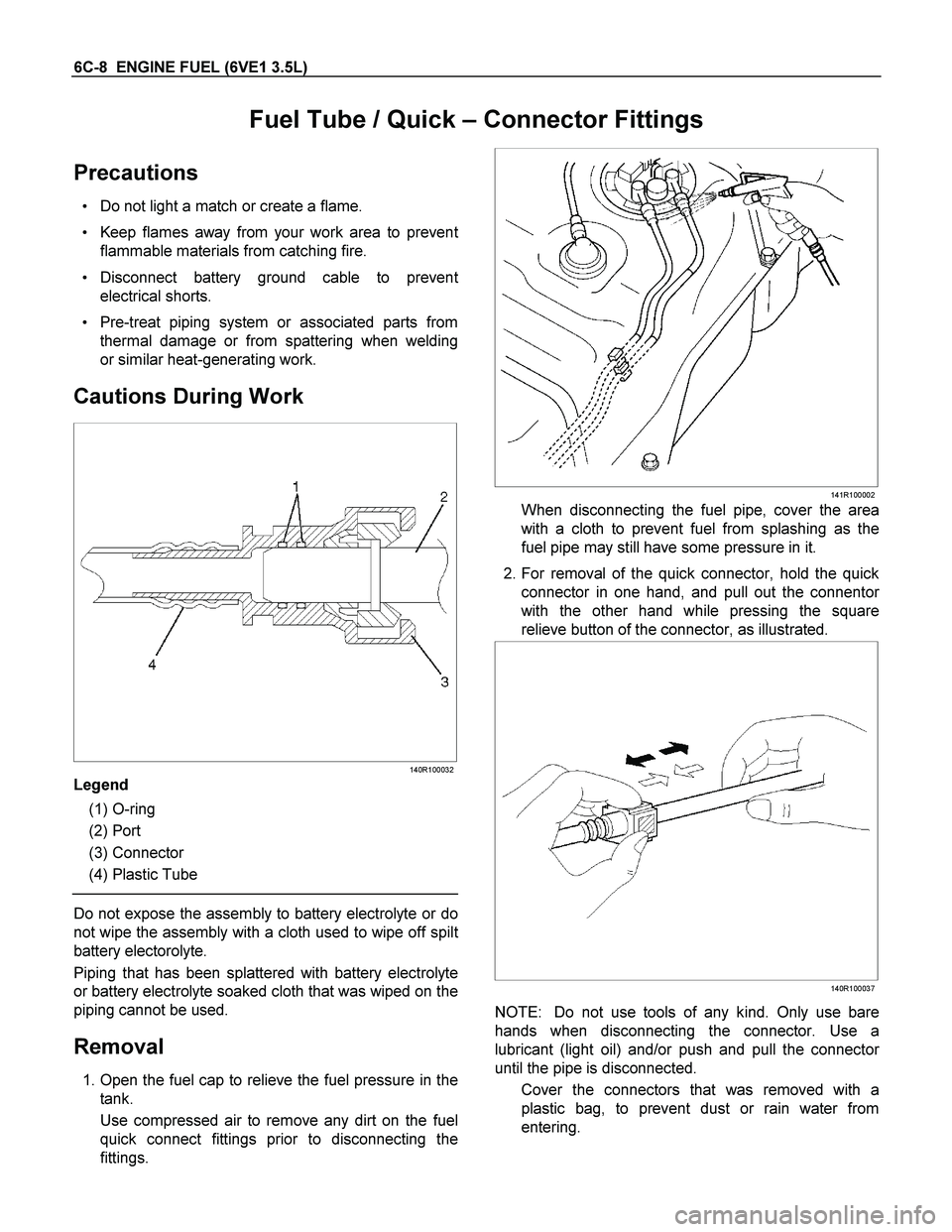
6C-8 ENGINE FUEL (6VE1 3.5L)
Fuel Tube / Quick – Connector Fittings
Precautions
Do not light a match or create a flame.
Keep flames away from your work area to preven
t
flammable materials from catching fire.
Disconnect battery ground cable to preven
t
electrical shorts.
Pre-treat piping system or associated parts from
thermal damage or from spattering when welding
or similar heat-generating work.
Cautions During Work
140R100032
Legend
(1) O-ring
(2) Port
(3) Connector
(4) Plastic Tube
Do not expose the assembly to battery electrolyte or do
not wipe the assembly with a cloth used to wipe off spil
t
battery electorolyte.
Piping that has been splattered with battery electrolyte
or battery electrolyte soaked cloth that was wiped on the
piping cannot be used.
Removal
1. Open the fuel cap to relieve the fuel pressure in the
tank.
Use compressed air to remove any dirt on the fuel
quick connect fittings prior to disconnecting the
fittings.
141R100002
When disconnecting the fuel pipe, cover the area
with a cloth to prevent fuel from splashing as the
fuel pipe may still have some pressure in it.
2. For removal of the quick connector, hold the quick
connector in one hand, and pull out the connento
r
with the other hand while pressing the square
relieve button of the connector, as illustrated.
140R100037
NOTE: Do not use tools of any kind. Only use bare
hands when disconnecting the connector. Use a
lubricant (light oil) and/or push and pull the connecto
r
until the pipe is disconnected.
Cover the connectors that was removed with a
plastic bag, to prevent dust or rain water from
entering.