reverse ISUZU TF SERIES 2004 Manual PDF
[x] Cancel search | Manufacturer: ISUZU, Model Year: 2004, Model line: TF SERIES, Model: ISUZU TF SERIES 2004Pages: 4264, PDF Size: 72.63 MB
Page 1962 of 4264
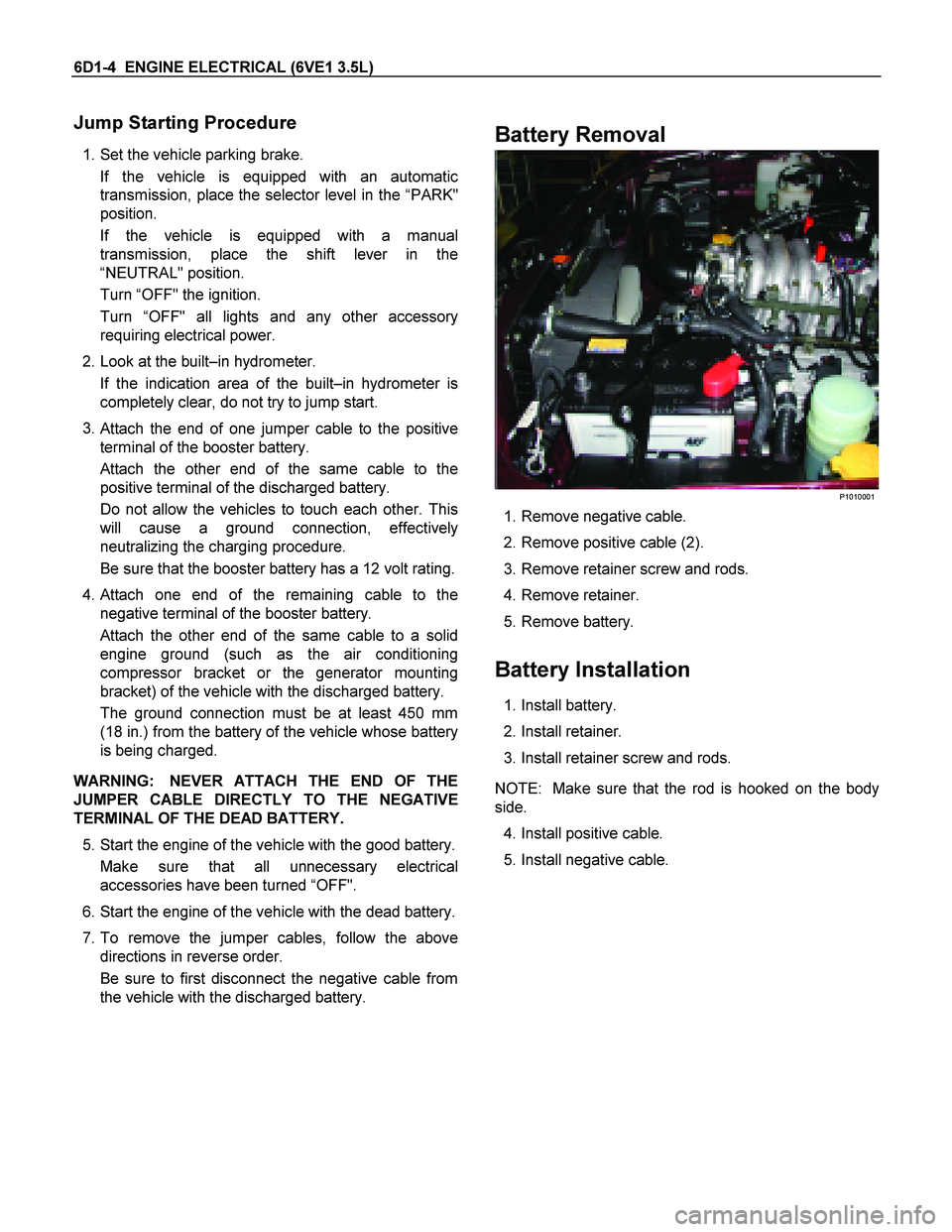
6D1-4 ENGINE ELECTRICAL (6VE1 3.5L)
Jump Starting Procedure
1. Set the vehicle parking brake.
If the vehicle is equipped with an automatic
transmission, place the selector level in the “PARK"
position.
If the vehicle is equipped with a manual
transmission, place the shift lever in the
“ NEUTRAL" position.
Turn “OFF" the ignition.
Turn “OFF" all lights and any other accessory
requiring electrical power.
2. Look at the built –in hydrometer.
If the indication area of the built –in hydrometer is
completely clear, do not try to jump start.
3.
Attach the end of one jumper cable to the positive
terminal of the booster battery.
Attach the other end of the same cable to the
positive terminal of the discharged battery.
Do not allow the vehicles to touch each other. This
will cause a ground connection, effectively
neutralizing the charging procedure.
Be sure that the booster battery has a 12 volt rating.
4. Attach one end of the remaining cable to the
negative terminal of the booster battery.
Attach the other end of the same cable to a solid
engine ground (such as the air conditioning
compressor bracket or the generator mounting
bracket) of the vehicle with the discharged battery.
The ground connection must be at least 450 mm
(18 in.) from the battery of the vehicle whose battery
is being charged.
WARNING: NEVER ATTACH THE END OF THE
JUMPER CABLE DIRECTLY TO THE NEGATIVE
TERMINAL OF THE DEAD BATTERY.
5. Start the engine of the vehicle with the good battery.
Make sure that all unnecessary electrical
accessories have been turned “OFF".
6. Start the engine of the vehicle with the dead battery.
7. To remove the jumper cables, follow the above directions in reverse order.
Be sure to first disconnect the negative cable from
the vehicle with the discharged battery.
Battery Removal
P1010001
1. Remove negative cable.
2. Remove positive cable (2).
3. Remove retainer screw and rods.
4. Remove retainer.
5. Remove battery.
Battery Installation
1. Install battery.
2. Install retainer.
3. Install retainer screw and rods.
NOTE: Make sure that the rod is hooked on the body
side.
4. Install positive cable.
5. Install negative cable.
Page 1966 of 4264
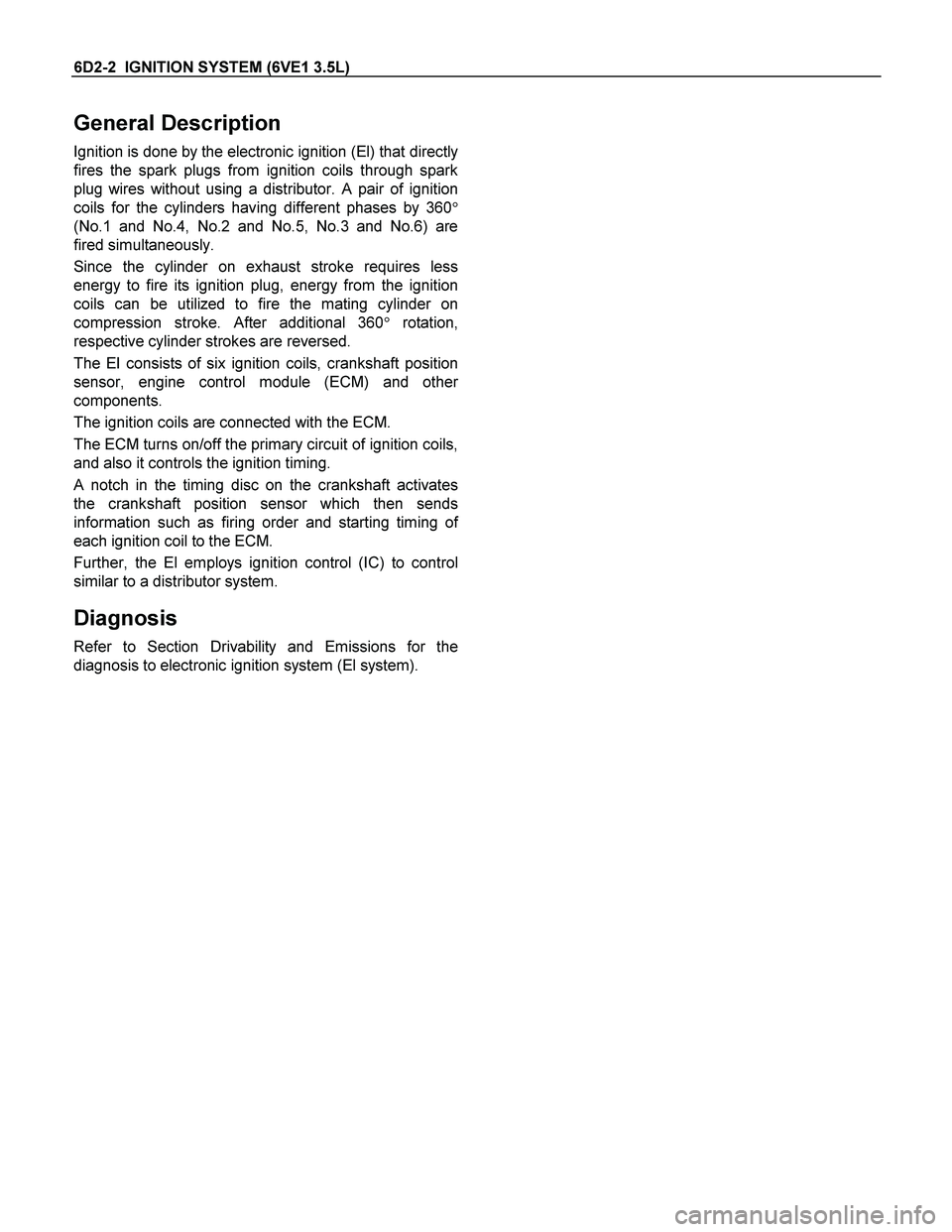
6D2-2 IGNITION SYSTEM (6VE1 3.5L)
General Description
Ignition is done by the electronic ignition (El) that directly
fires the spark plugs from ignition coils through spark
plug wires without using a distributor. A pair of ignition
coils for the cylinders having different phases by 360
(No.1 and No.4, No.2 and No.5, No.3 and No.6) are
fired simultaneously.
Since the cylinder on exhaust stroke requires less
energy to fire its ignition plug, energy from the ignition
coils can be utilized to fire the mating cylinder on
compression stroke. After additional 360rotation,
respective cylinder strokes are reversed.
The EI consists of six ignition coils, crankshaft position
sensor, engine control module (ECM) and othe
r
components.
The ignition coils are connected with the ECM.
The ECM turns on/off the primary circuit of ignition coils,
and also it controls the ignition timing.
A notch in the timing disc on the crankshaft activates
the crankshaft position sensor which then sends
information such as firing order and starting timing o
f
each ignition coil to the ECM.
Further, the El employs ignition control (IC) to control
similar to a distributor system.
Diagnosis
Refer to Section Drivability and Emissions for the
diagnosis to electronic ignition system (El system).
Page 1984 of 4264
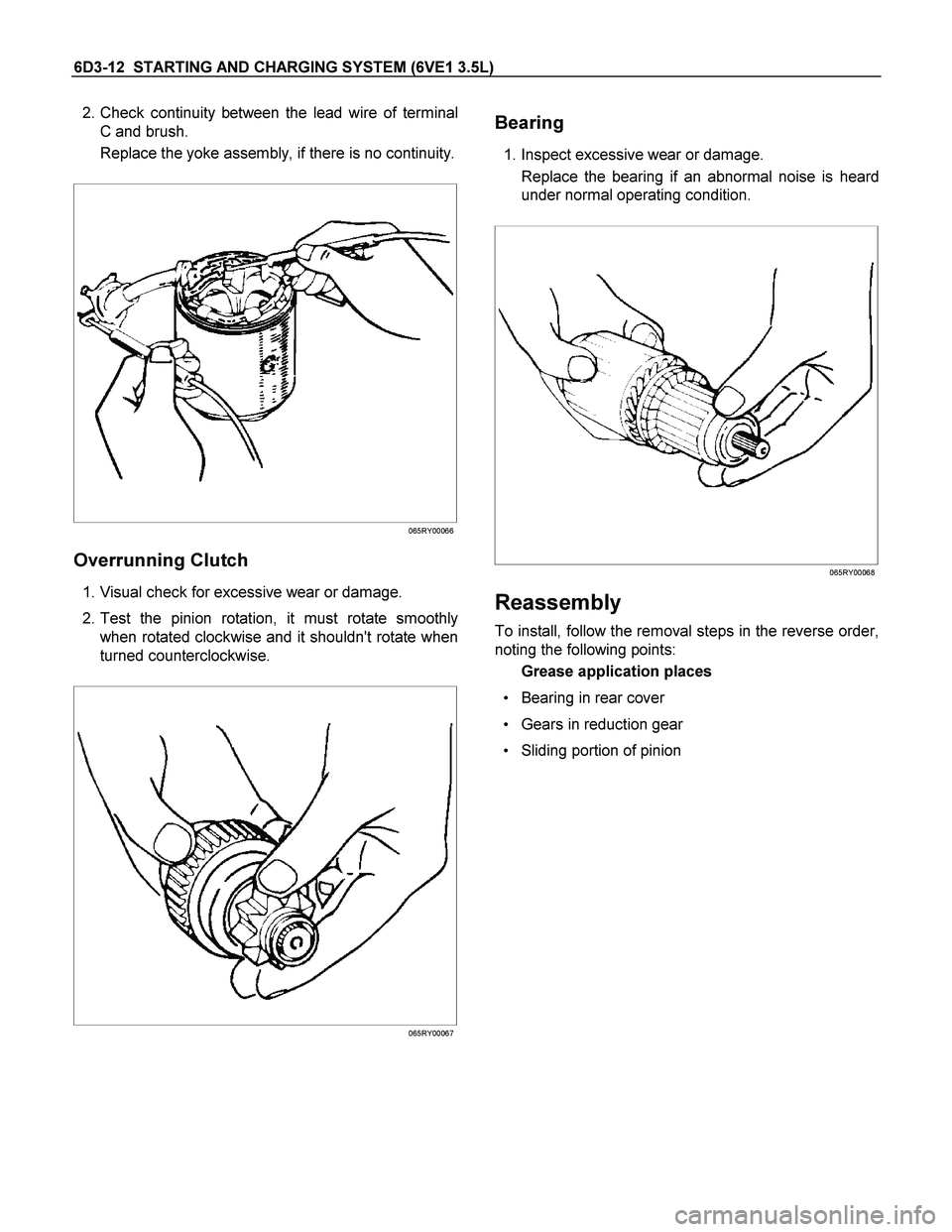
6D3-12 STARTING AND CHARGING SYSTEM (6VE1 3.5L)
2. Check continuity between the lead wire of terminal
C and brush.
Replace the yoke assembly, if there is no continuity.
065RY00066
Overrunning Clutch
1. Visual check for excessive wear or damage.
2. Test the pinion rotation, it must rotate smoothly
when rotated clockwise and it shouldn't rotate when
turned counterclockwise.
065RY00067
Bearing
1. Inspect excessive wear or damage.
Replace the bearing if an abnormal noise is heard
under normal operating condition.
065RY00068
Reassembly
To install, follow the removal steps in the reverse order,
noting the following points:
Grease application places
Bearing in rear cover
Gears in reduction gear
Sliding portion of pinion
Page 1993 of 4264
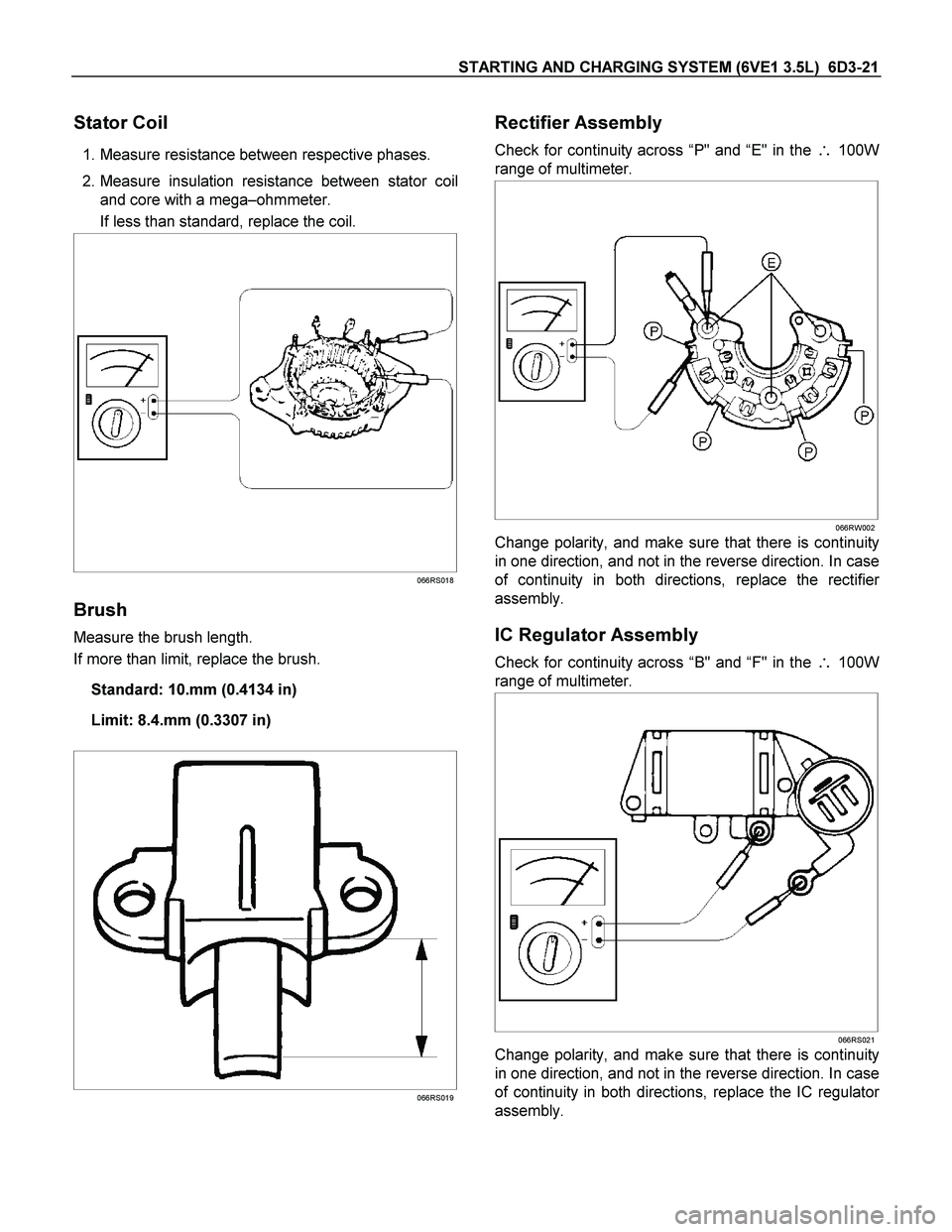
STARTING AND CHARGING SYSTEM (6VE1 3.5L) 6D3-21
Stator Coil
1. Measure resistance between respective phases.
2. Measure insulation resistance between stator coil
and core with a mega–ohmmeter.
If less than standard, replace the coil.
066RS018
Brush
Measure the brush length.
If more than limit, replace the brush.
Standard: 10.mm (0.4134 in)
Limit: 8.4.mm (0.3307 in)
066RS019
Rectifier Assembly
Check for continuity across “P" and “E" in the 100W
range of multimeter.
066RW002
Change polarity, and make sure that there is continuity
in one direction, and not in the reverse direction. In case
of continuity in both directions, replace the rectifie
r
assembly.
IC Regulator Assembly
Check for continuity across “B" and “F" in the 100W
range of multimeter.
066RS021
Change polarity, and make sure that there is continuity
in one direction, and not in the reverse direction. In case
of continuity in both directions, replace the IC regulato
r
assembly.
Page 1994 of 4264
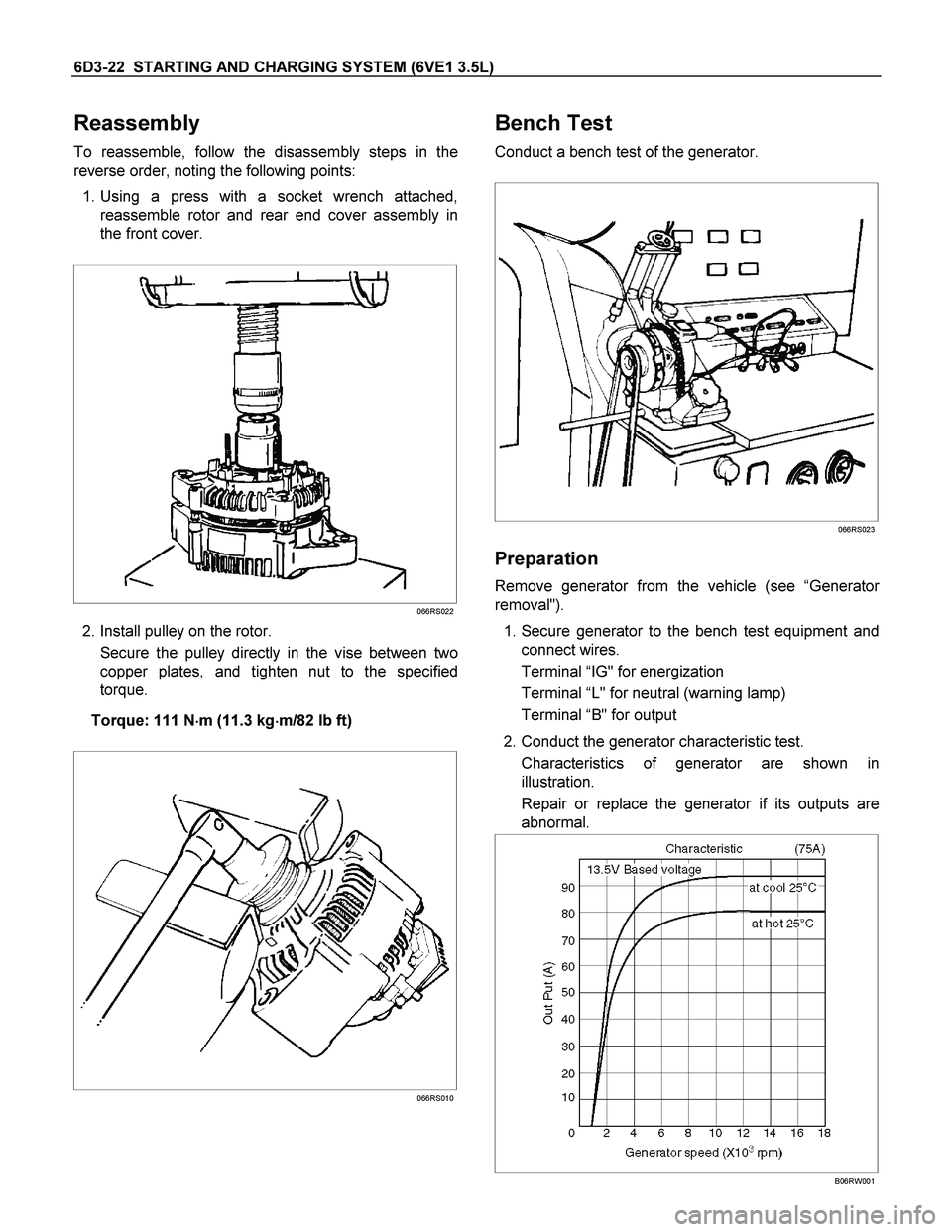
6D3-22 STARTING AND CHARGING SYSTEM (6VE1 3.5L)
Reassembly
To reassemble, follow the disassembly steps in the
reverse order, noting the following points:
1. Using a press with a socket wrench attached,
reassemble rotor and rear end cover assembly in
the front cover.
066RS022
2. Install pulley on the rotor.
Secure the pulley directly in the vise between two
copper plates, and tighten nut to the specified
torque.
Torque: 111 N
m (11.3 kg
m/82 lb ft)
066RS010
Bench Test
Conduct a bench test of the generator.
066RS023
Preparation
Remove generator from the vehicle (see “Generator
removal").
1. Secure generator to the bench test equipment and
connect wires.
Terminal “IG" for energization
Terminal “L" for neutral (warning lamp)
Terminal “B" for output
2. Conduct the generator characteristic test.
Characteristics of generator are shown in
illustration.
Repair or replace the generator if its outputs are
abnormal.
B06RW001
Page 2293 of 4264
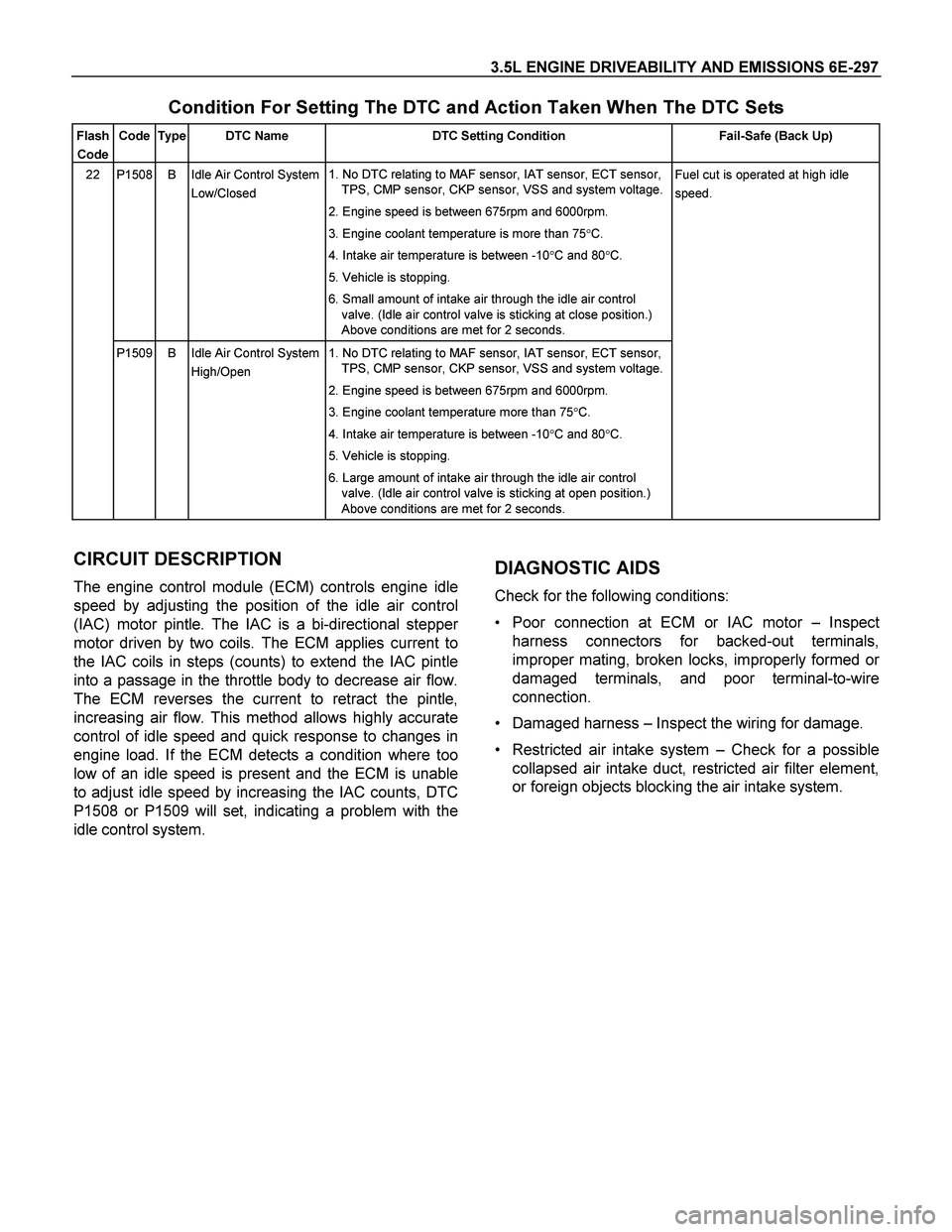
3.5L ENGINE DRIVEABILITY AND EMISSIONS 6E-297
Condition For Setting The DTC and Action Taken When The DTC Sets
Flash
Code Code Type DTC Name DTC Setting Condition Fail-Safe (Back Up)
P1508 B Idle Air Control System
Low/Closed 1. No DTC relating to MAF sensor, IAT sensor, ECT sensor,
TPS, CMP sensor, CKP sensor, VSS and system voltage.
2. Engine speed is between 675rpm and 6000rpm.
3. Engine coolant temperature is more than 75C.
4. Intake air temperature is between -10C and 80C.
5. Vehicle is stopping.
6. Small amount of intake air through the idle air control
valve. (Idle air control valve is sticking at close position.)
Above conditions are met for 2 seconds. 22
P1509 B Idle Air Control System
High/Open 1. No DTC relating to MAF sensor, IAT sensor, ECT sensor,
TPS, CMP sensor, CKP sensor, VSS and system voltage.
2. Engine speed is between 675rpm and 6000rpm.
3. Engine coolant temperature more than 75C.
4. Intake air temperature is between -10C and 80C.
5. Vehicle is stopping.
6. Large amount of intake air through the idle air control
valve. (Idle air control valve is sticking at open position.)
Above conditions are met for 2 seconds. Fuel cut is operated at high idle
speed.
CIRCUIT DESCRIPTION
The engine control module (ECM) controls engine idle
speed by adjusting the position of the idle air control
(IAC) motor pintle. The IAC is a bi-directional steppe
r
motor driven by two coils. The ECM applies current to
the IAC coils in steps (counts) to extend the IAC pintle
into a passage in the throttle body to decrease air flow.
The ECM reverses the current to retract the pintle,
increasing air flow. This method allows highly accurate
control of idle speed and quick response to changes in
engine load. If the ECM detects a condition where too
low of an idle speed is present and the ECM is unable
to adjust idle speed by increasing the IAC counts, DTC
P1508 or P1509 will set, indicating a problem with the
idle control system.
DIAGNOSTIC AIDS
Check for the following conditions:
Poor connection at ECM or IAC motor –Inspec
t
harness connectors for backed-out terminals,
improper mating, broken locks, improperly formed o
r
damaged terminals, and poor terminal-to-wire
connection.
Damaged harness – Inspect the wiring for damage.
Restricted air intake system – Check for a possible
collapsed air intake duct, restricted air filter element,
or foreign objects blocking the air intake system.
Page 2486 of 4264
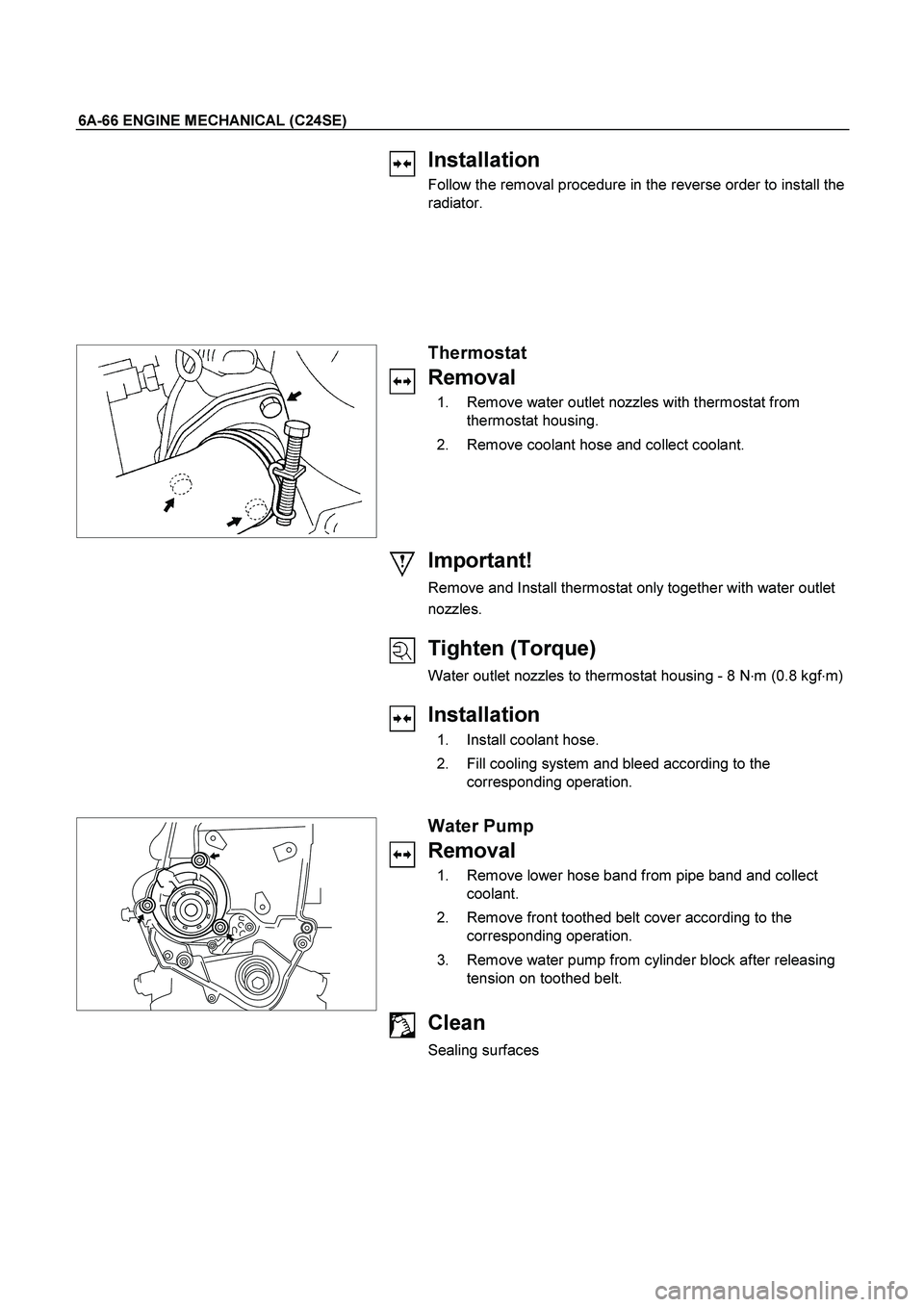
6A-66 ENGINE MECHANICAL (C24SE)
Installation
Follow the removal procedure in the reverse order to install the
radiator.
Thermostat
Removal
1. Remove water outlet nozzles with thermostat from
thermostat housing.
2. Remove coolant hose and collect coolant.
Important!
Remove and Install thermostat only together with water outlet
nozzles.
Tighten (Torque)
Water outlet nozzles to thermostat housing - 8 N
m (0.8 kgf
m)
Installation
1. Install coolant hose.
2. Fill cooling system and bleed according to the
corresponding operation.
Water Pump
Removal
1. Remove lower hose band from pipe band and collect
coolant.
2. Remove front toothed belt cover according to the
corresponding operation.
3. Remove water pump from cylinder block after releasing
tension on toothed belt.
Clean
Sealing surfaces
Page 2547 of 4264
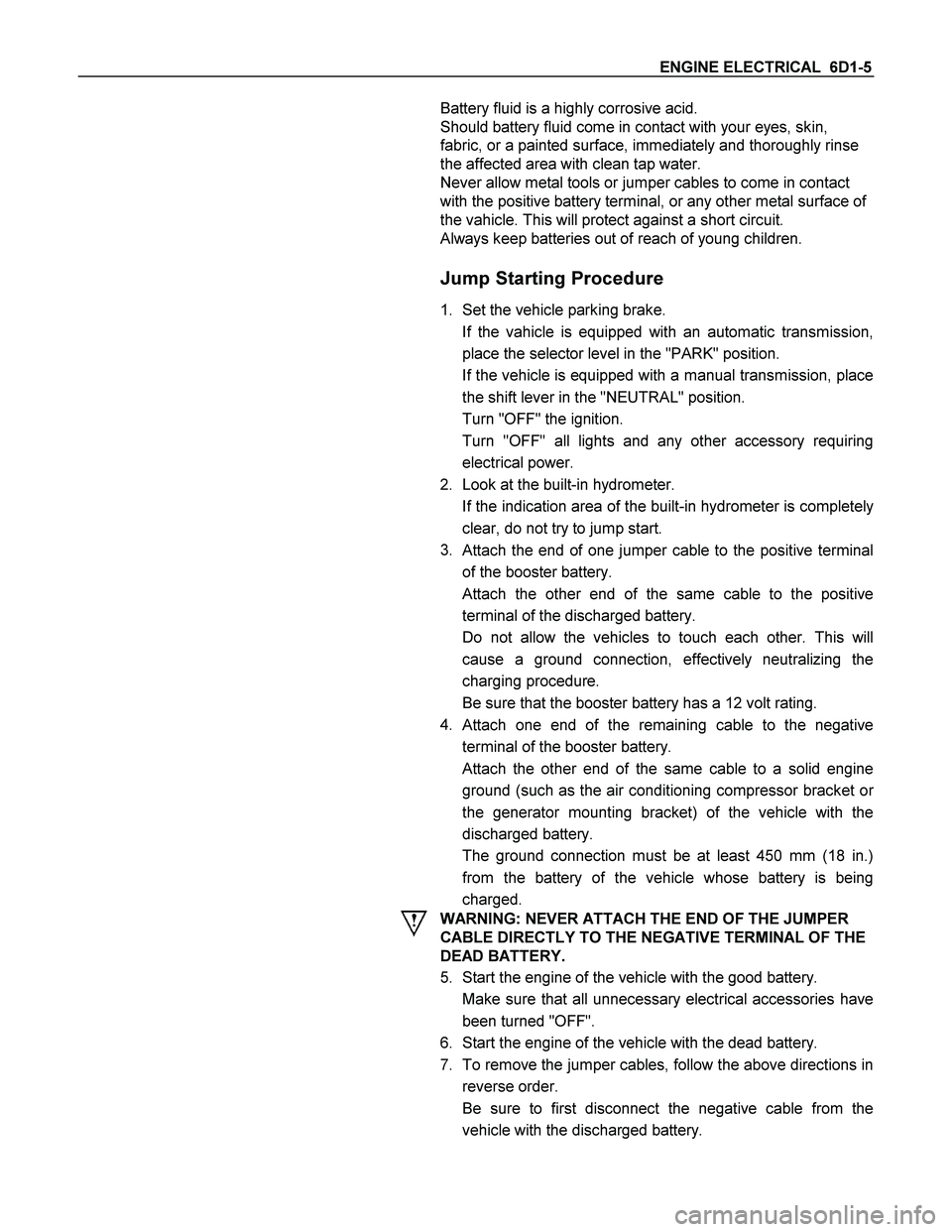
ENGINE ELECTRICAL 6D1-5
Battery fluid is a highly corrosive acid.
Should battery fluid come in contact with your eyes, skin,
fabric, or a painted surface, immediately and thoroughly rinse
the affected area with clean tap water.
Never allow metal tools or jumper cables to come in contact
with the positive battery terminal, or any other metal surface of
the vahicle. This will protect against a short circuit.
Always keep batteries out of reach of young children.
Jump Starting Procedure
1. Set the vehicle parking brake.
If the vahicle is equipped with an automatic transmission,
place the selector level in the "PARK" position.
If the vehicle is equipped with a manual transmission, place
the shift lever in the "NEUTRAL" position.
Turn "OFF" the ignition.
Turn "OFF" all lights and any other accessory requiring
electrical power.
2. Look at the built-in hydrometer.
If the indication area of the built-in hydrometer is completely
clear, do not try to jump start.
3.
Attach the end of one jumper cable to the positive terminal
of the booster battery.
Attach the other end of the same cable to the positive
terminal of the discharged battery.
Do not allow the vehicles to touch each other. This will
cause a ground connection, effectively neutralizing the
charging procedure.
Be sure that the booster battery has a 12 volt rating.
4.
Attach one end of the remaining cable to the negative
terminal of the booster battery.
Attach the other end of the same cable to a solid engine
ground (such as the air conditioning compressor bracket o
r
the generator mounting bracket) of the vehicle with the
discharged battery.
The ground connection must be at least 450 mm (18 in.)
from the battery of the vehicle whose battery is being
charged.
WARNING: NEVER ATTACH THE END OF THE JUMPER
CABLE DIRECTLY TO THE NEGATIVE TERMINAL OF THE
DEAD BATTERY.
5. Start the engine of the vehicle with the good battery.
Make sure that all unnecessary electrical accessories have
been turned "OFF".
6. Start the engine of the vehicle with the dead battery.
7. To remove the jumper cables, follow the above directions in
reverse order.
Be sure to first disconnect the negative cable from the
vehicle with the discharged battery.
Page 2560 of 4264
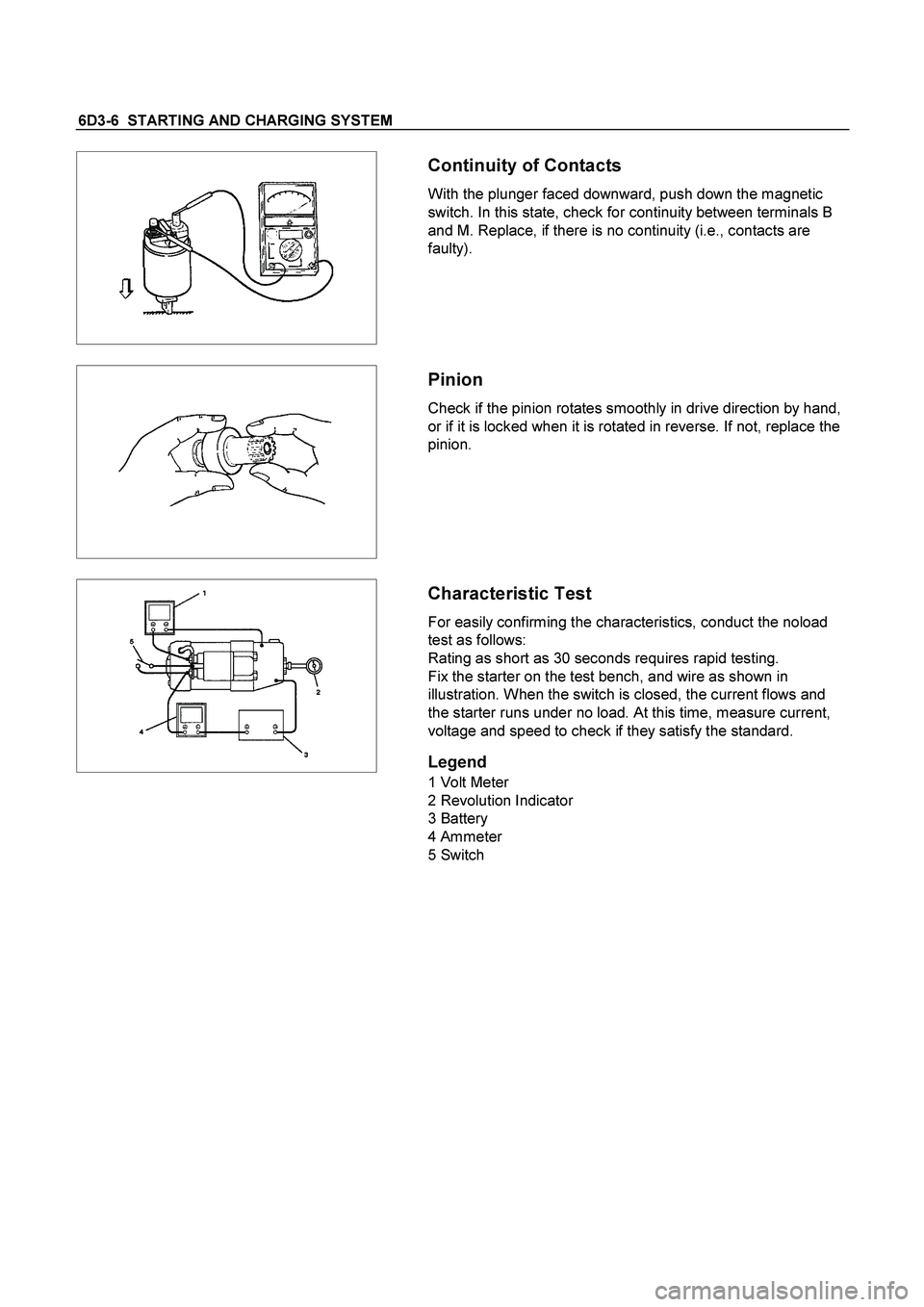
6D3-6 STARTING AND CHARGING SYSTEM
Continuity of Contacts
With the plunger faced downward, push down the magnetic
switch. In this state, check for continuity between terminals B
and M. Replace, if there is no continuity (i.e., contacts are
faulty).
Pinion
Check if the pinion rotates smoothly in drive direction by hand,
or if it is locked when it is rotated in reverse. If not, replace the
pinion.
Characteristic Test
For easily confirming the characteristics, conduct the noload
test as follows:
Rating as short as 30 seconds requires rapid testing.
Fix the starter on the test bench, and wire as shown in
illustration. When the switch is closed, the current flows and
the starter runs under no load. At this time, measure current,
voltage and speed to check if they satisfy the standard.
Legend
1 Volt Meter
2 Revolution Indicator
3 Battery
4 Ammeter
5 Switch
Page 2565 of 4264
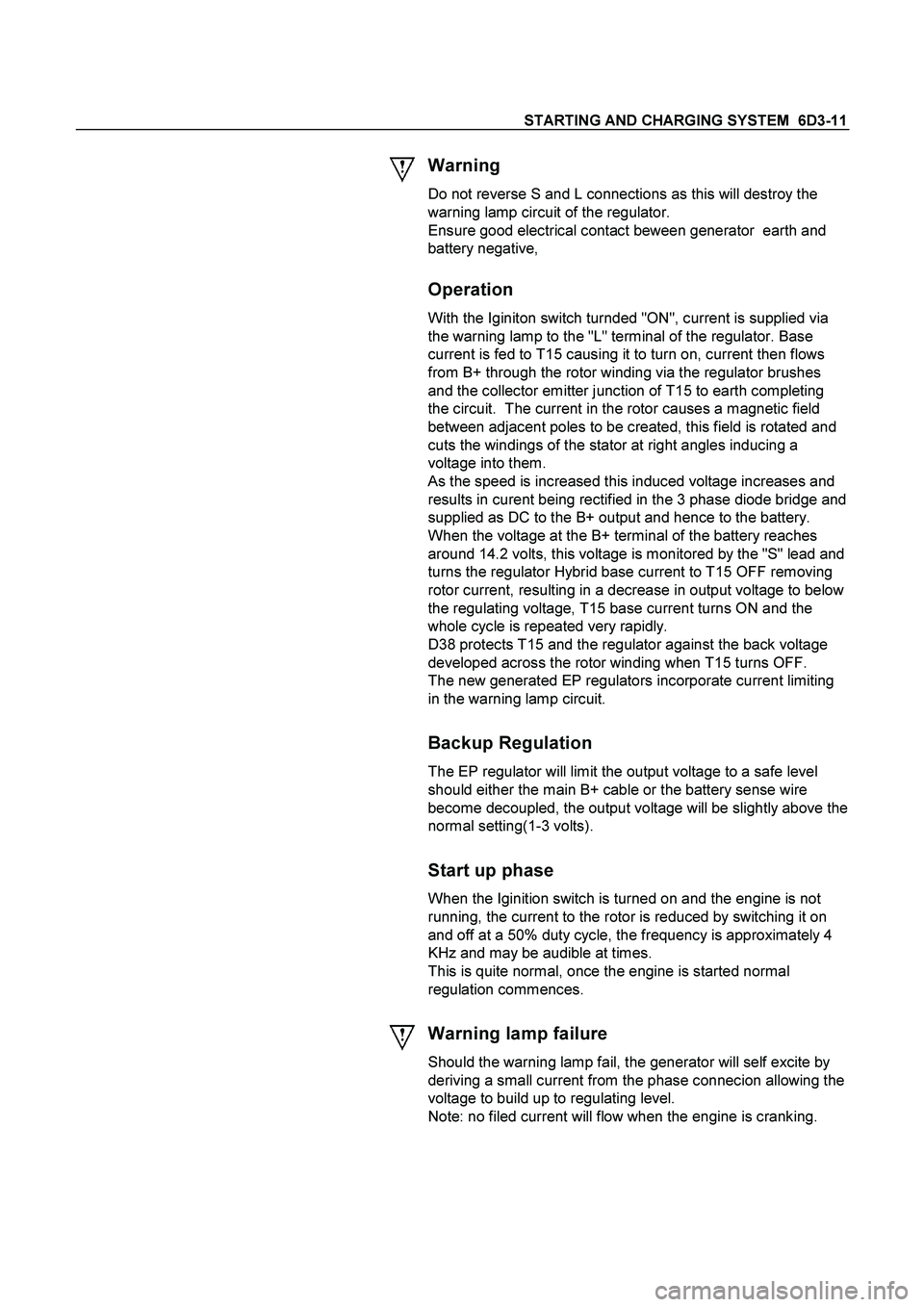
STARTING AND CHARGING SYSTEM 6D3-11
Warning
Do not reverse S and L connections as this will destroy the
warning lamp circuit of the regulator.
Ensure good electrical contact beween generator earth and
battery negative,
Operation
With the Iginiton switch turnded "ON", current is supplied via
the warning lamp to the "L" terminal of the regulator. Base
current is fed to T15 causing it to turn on, current then flows
from B+ through the rotor winding via the regulator brushes
and the collector emitter junction of T15 to earth completing
the circuit. The current in the rotor causes a magnetic field
between adjacent poles to be created, this field is rotated and
cuts the windings of the stator at right angles inducing a
voltage into them.
As the speed is increased this induced voltage increases and
results in curent being rectified in the 3 phase diode bridge and
supplied as DC to the B+ output and hence to the battery.
When the voltage at the B+ terminal of the battery reaches
around 14.2 volts, this voltage is monitored by the "S" lead and
turns the regulator Hybrid base current to T15 OFF removing
rotor current, resulting in a decrease in output voltage to below
the regulating voltage, T15 base current turns ON and the
whole cycle is repeated very rapidly.
D38 protects T15 and the regulator against the back voltage
developed across the rotor winding when T15 turns OFF.
The new generated EP regulators incorporate current limiting
in the warning lamp circuit.
Backup Regulation
The EP regulator will limit the output voltage to a safe level
should either the main B+ cable or the battery sense wire
become decoupled, the output voltage will be slightly above the
normal setting(1-3 volts).
Start up phase
When the Iginition switch is turned on and the engine is not
running, the current to the rotor is reduced by switching it on
and off at a 50% duty cycle, the frequency is approximately 4
KHz and may be audible at times.
This is quite normal, once the engine is started normal
regulation commences.
Warning lamp failure
Should the warning lamp fail, the generator will self excite by
deriving a small current from the phase connecion allowing the
voltage to build up to regulating level.
Note: no filed current will flow when the engine is cranking.