air conditioning ISUZU TF SERIES 2004 Workshop Manual
[x] Cancel search | Manufacturer: ISUZU, Model Year: 2004, Model line: TF SERIES, Model: ISUZU TF SERIES 2004Pages: 4264, PDF Size: 72.63 MB
Page 57 of 4264
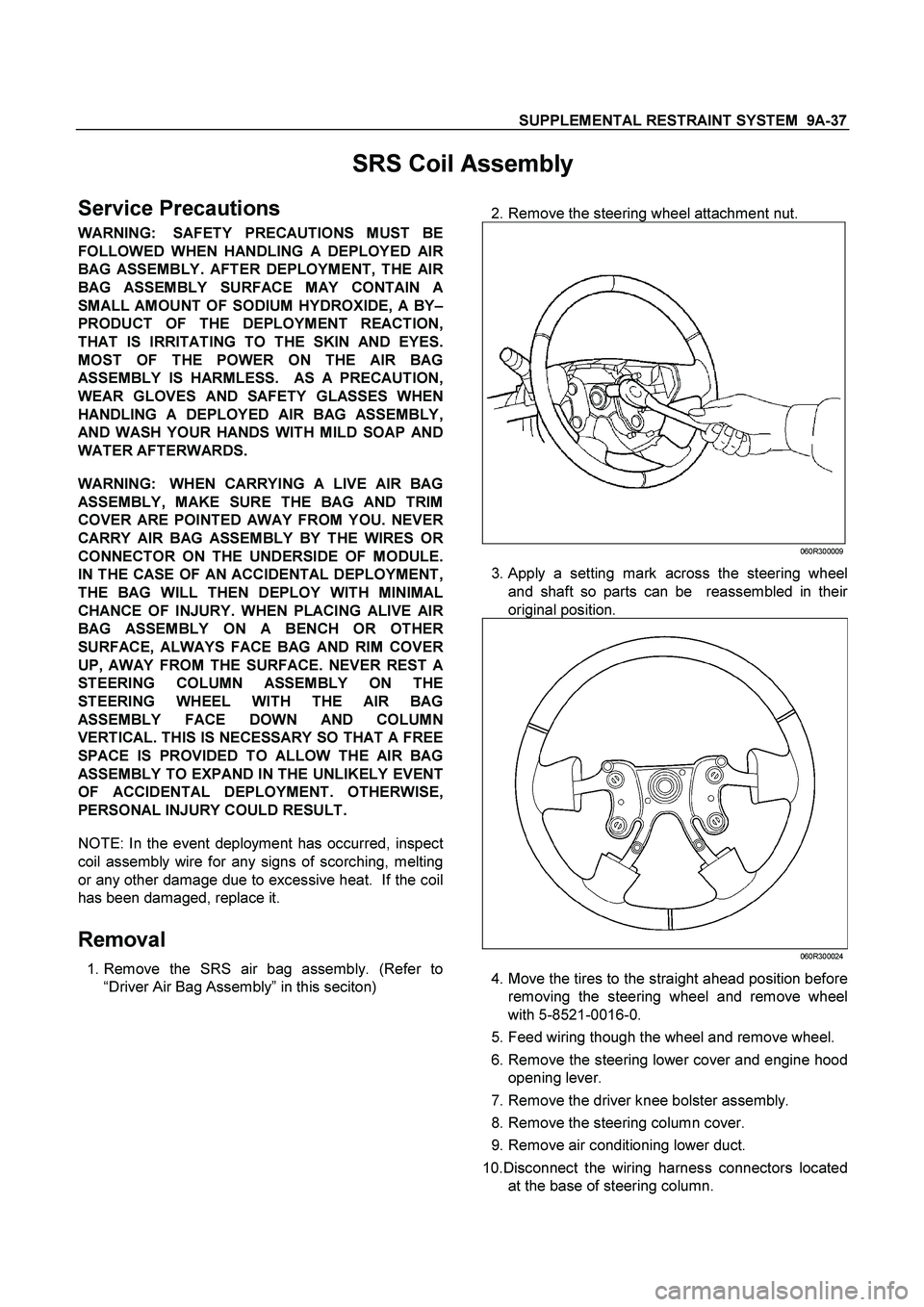
SUPPLEMENTAL RESTRAINT SYSTEM 9A-37
SRS Coil Assembly
Service Precautions
WARNING: SAFETY PRECAUTIONS MUST BE
FOLLOWED WHEN HANDLING A DEPLOYED AI
R
BAG ASSEMBLY. AFTER DEPLOYMENT, THE AIR
BAG ASSEMBLY SURFACE MAY CONTAIN A
SMALL AMOUNT OF SODIUM HYDROXIDE, A BY–
PRODUCT OF THE DEPLOYMENT REACTION,
THAT IS IRRITATING TO THE SKIN AND EYES.
MOST OF THE POWER ON THE AIR BAG
ASSEMBLY IS HARMLESS. AS A PRECAUTION,
WEAR GLOVES AND SAFETY GLASSES WHEN
HANDLING A DEPLOYED AIR BAG ASSEMBLY,
AND WASH YOUR HANDS WITH MILD SOAP AND
WATER AFTERWARDS.
WARNING: WHEN CARRYING A LIVE AIR BAG
ASSEMBLY, MAKE SURE THE BAG AND TRIM
COVER ARE POINTED AWAY FROM YOU. NEVE
R
CARRY AIR BAG ASSEMBLY BY THE WIRES OR
CONNECTOR ON THE UNDERSIDE OF MODULE.
IN THE CASE OF AN ACCIDENTAL DEPLOYMENT,
THE BAG WILL THEN DEPLOY WITH MINIMAL
CHANCE OF INJURY. WHEN PLACING ALIVE AI
R
BAG ASSEMBLY ON A BENCH OR OTHER
SURFACE, ALWAYS FACE BAG AND RIM COVER
UP, AWAY FROM THE SURFACE. NEVER REST A
STEERING COLUMN ASSEMBLY ON THE
STEERING WHEEL WITH THE AIR BAG
ASSEMBLY FACE DOWN AND COLUMN
VERTICAL. THIS IS NECESSARY SO THAT A FREE
SPACE IS PROVIDED TO ALLOW THE AIR BAG
ASSEMBLY TO EXPAND IN THE UNLIKELY EVENT
OF ACCIDENTAL DEPLOYMENT. OTHERWISE,
PERSONAL INJURY COULD RESULT.
NOTE: In the event deployment has occurred, inspec
t
coil assembly wire for any signs of scorching, melting
or any other damage due to excessive heat. If the coil
has been damaged, replace it.
Removal
1. Remove the SRS air bag assembly. (Refer to
“Driver Air Bag Assembly” in this seciton)
2. Remove the steering wheel attachment nut.
060R300009
3. Apply a setting mark across the steering wheel
and shaft so parts can be reassembled in thei
r
original position.
060R300024
4. Move the tires to the straight ahead position before
removing the steering wheel and remove wheel
with 5-8521-0016-0.
5. Feed wiring though the wheel and remove wheel.
6. Remove the steering lower cover and engine hood
opening lever.
7. Remove the driver knee bolster assembly.
8. Remove the steering column cover.
9. Remove air conditioning lower duct.
10.Disconnect the wiring harness connectors located
at the base of steering column.
Page 58 of 4264
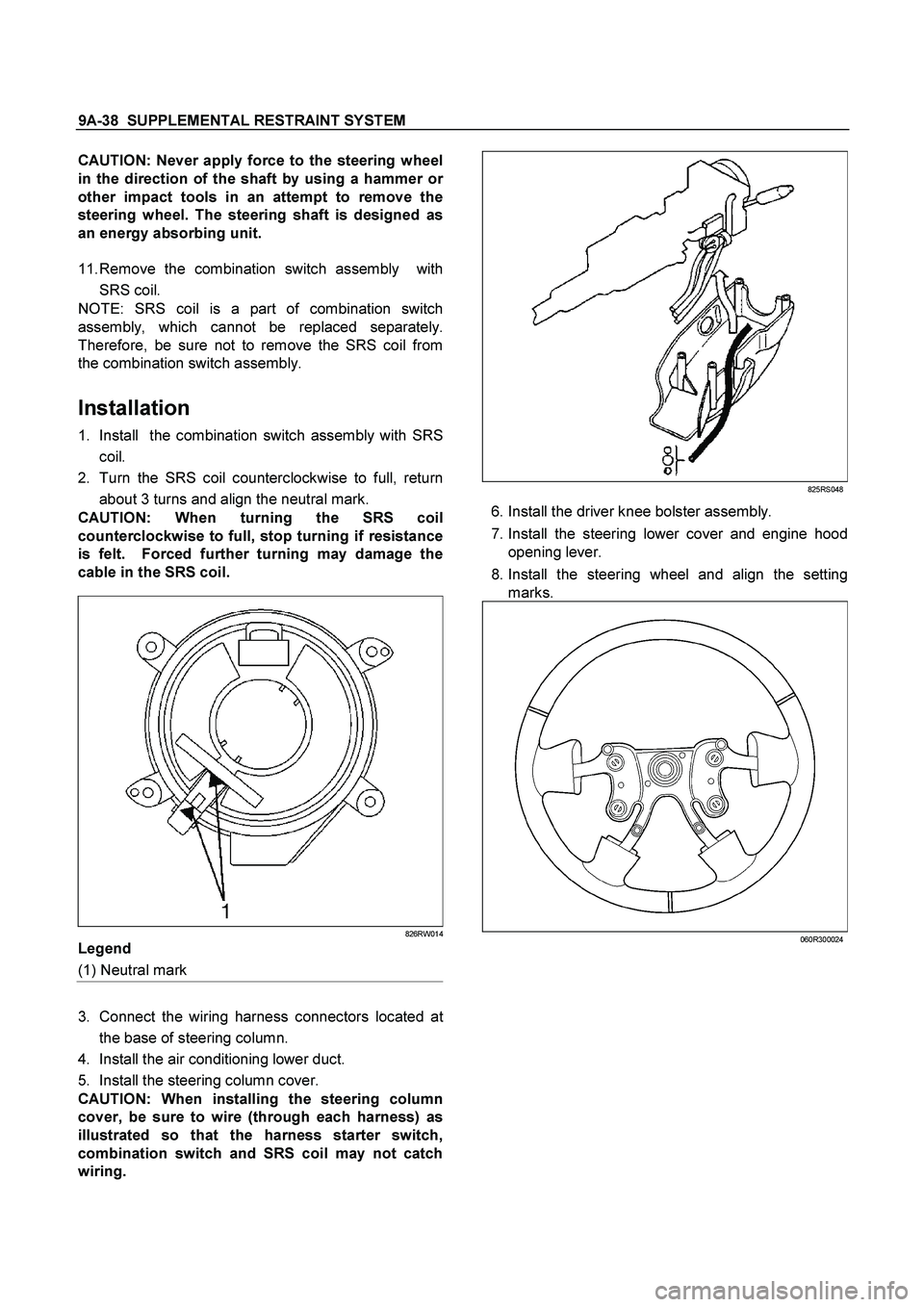
9A-38 SUPPLEMENTAL RESTRAINT SYSTEM
CAUTION: Never apply force to the steering wheel
in the direction of the shaft by using a hammer o
r
other impact tools in an attempt to remove the
steering wheel. The steering shaft is designed as
an energy absorbing unit.
11. Remove the combination switch assembly with
SRS coil.
NOTE: SRS coil is a part of combination switch
assembly, which cannot be replaced separately.
Therefore, be sure not to remove the SRS coil from
the combination switch assembly.
Installation
1. Install the combination switch assembly with SRS
coil.
2. Turn the SRS coil counterclockwise to full, return
about 3 turns and align the neutral mark.
CAUTION: When turning the SRS coil
counterclockwise to full, stop turning if resistance
is felt. Forced further turning may damage the
cable in the SRS coil.
826RW014
Legend
(1) Neutral mark
3. Connect the wiring harness connectors located at
the base of steering column.
4. Install the air conditioning lower duct.
5. Install the steering column cover.
CAUTION: When installing the steering column
cover, be sure to wire (through each harness) as
illustrated so that the harness starter switch,
combination switch and SRS coil may not catch
wiring.
825RS048
6. Install the driver knee bolster assembly.
7. Install the steering lower cover and engine hood
opening lever.
8. Install the steering wheel and align the setting
marks.
060R300024
Page 660 of 4264
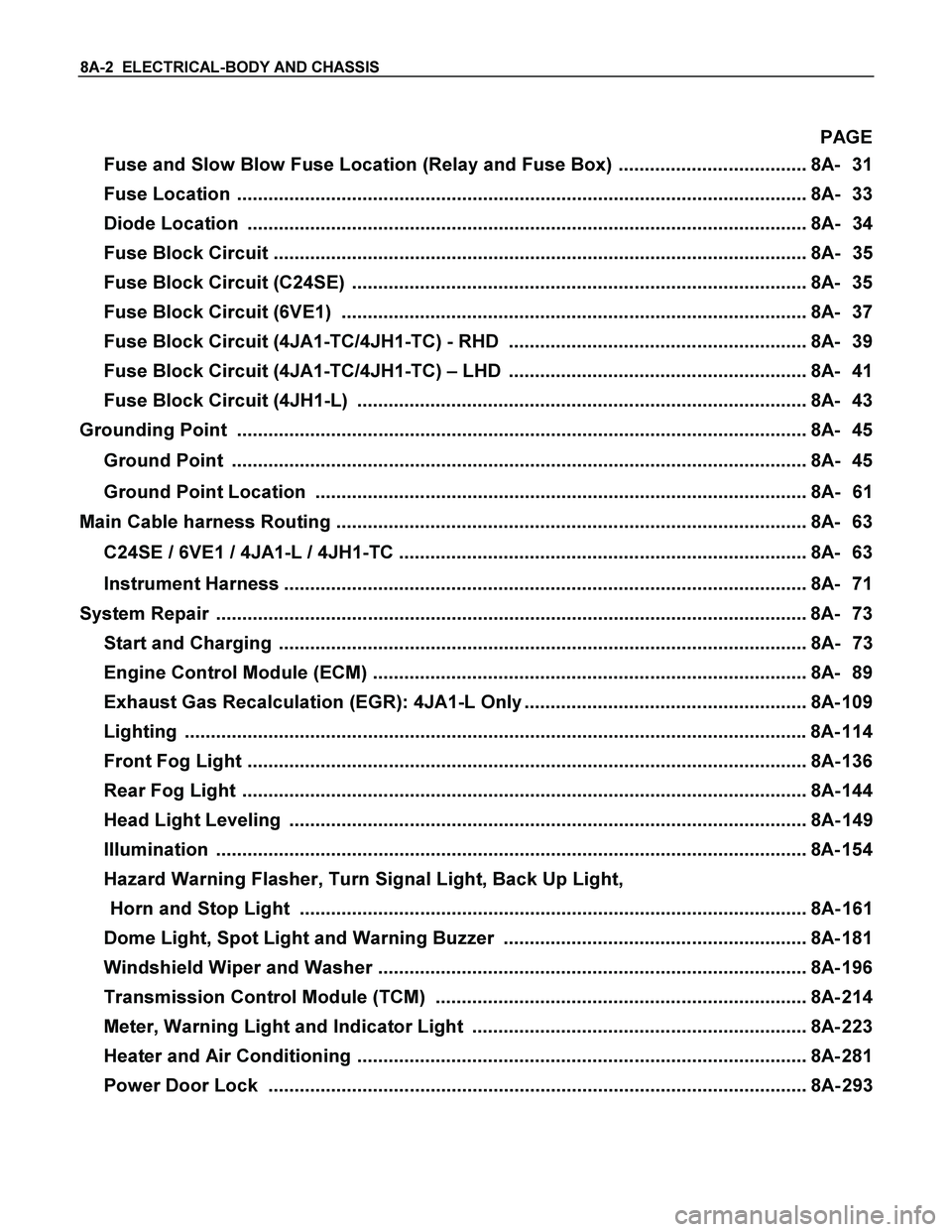
8A-2 ELECTRICAL-BODY AND CHASSIS
PAGE
Fuse and Slow Blow Fuse Location (Relay and Fuse Box) .................................... 8A- 31
Fuse Location ............................................................................................................. 8A- 33
Diode Location ........................................................................................................... 8A- 34
Fuse Block Circuit ...................................................................................................... 8A- 35
Fuse Block Circuit (C24SE) ....................................................................................... 8A- 35
Fuse Block Circuit (6VE1) ......................................................................................... 8A- 37
Fuse Block Circuit (4JA1-TC/4JH1-TC) - RHD ......................................................... 8A- 39
Fuse Block Circuit (4JA1-TC/4JH1-TC) – LHD ......................................................... 8A- 41
Fuse Block Circuit (4JH1-L) ...................................................................................... 8A- 43
Grounding Point ............................................................................................................. 8A- 45
Ground Point .............................................................................................................. 8A- 45
Ground Point Location .............................................................................................. 8A- 61
Main Cable harness Routing .......................................................................................... 8A- 63
C24SE / 6VE1 / 4JA1-L / 4JH1-TC .............................................................................. 8A- 63
Instrument Harness .................................................................................................... 8A- 71
System Repair .................................................................................................................8A- 73
Start and Charging ..................................................................................................... 8A- 73
Engine Control Module (ECM) ................................................................................... 8A- 89
Exhaust Gas Recalculation (EGR): 4JA1-L Only ...................................................... 8A- 109
Lighting ....................................................................................................................... 8A- 114
Front Fog Light ........................................................................................................... 8A- 136
Rear Fog Light ............................................................................................................ 8A- 144
Head Light Leveling ................................................................................................... 8A- 149
Illumination ................................................................................................................. 8A- 154
Hazard Warning Flasher, Turn Signal Light, Back Up Light,
Horn and Stop Light ................................................................................................. 8A- 161
Dome Light, Spot Light and Warning Buzzer .......................................................... 8A- 181
Windshield Wiper and Washer .................................................................................. 8A- 196
Transmission Control Module (TCM) ....................................................................... 8A- 214
Meter, Warning Light and Indicator Light ................................................................ 8A- 223
Heater and Air Conditioning ...................................................................................... 8A- 281
Power Door Lock ....................................................................................................... 8A- 293
Page 939 of 4264
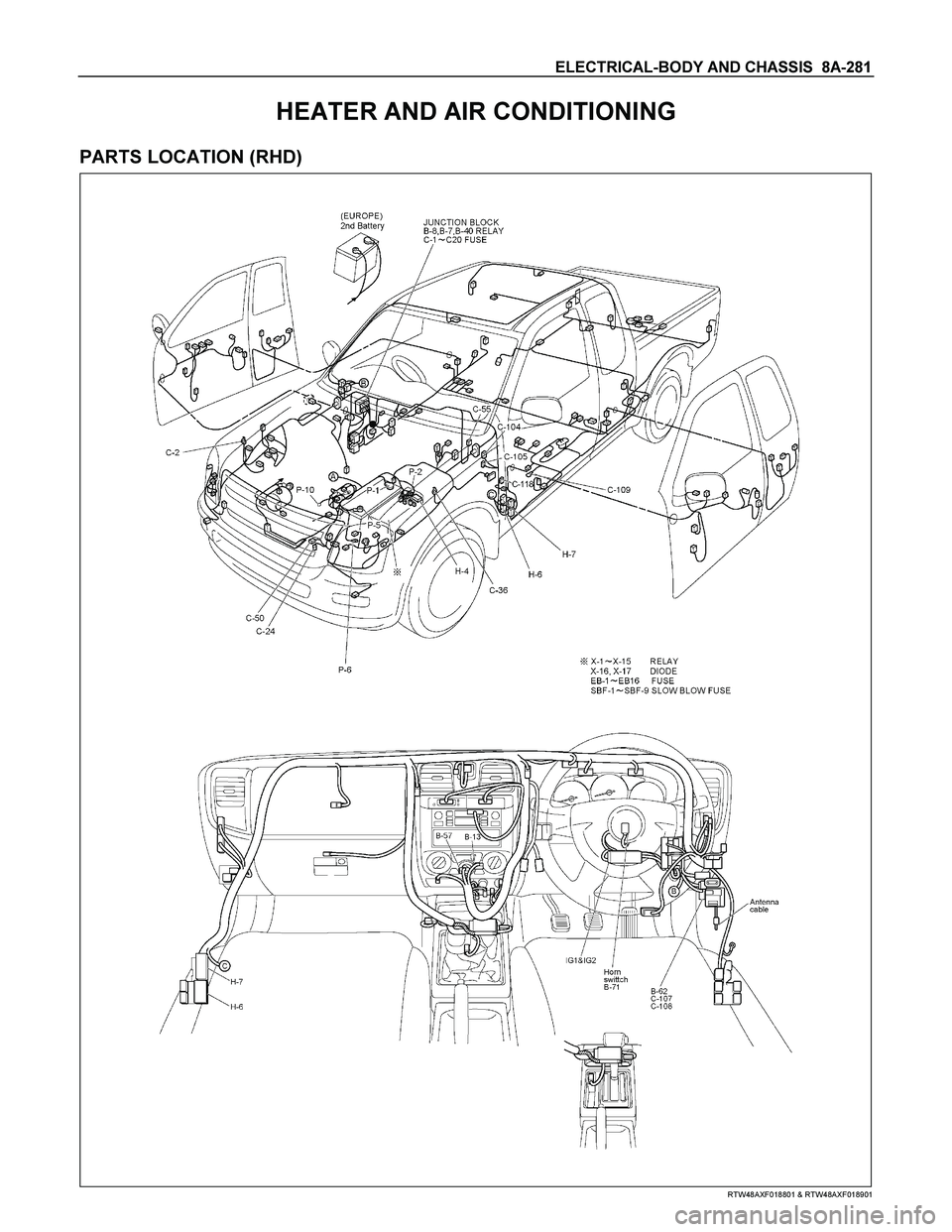
ELECTRICAL-BODY AND CHASSIS 8A-281
HEATER AND AIR CONDITIONING
PARTS LOCATION (RHD)
RTW48AXF018801 & RTW48AXF018901
Page 1460 of 4264
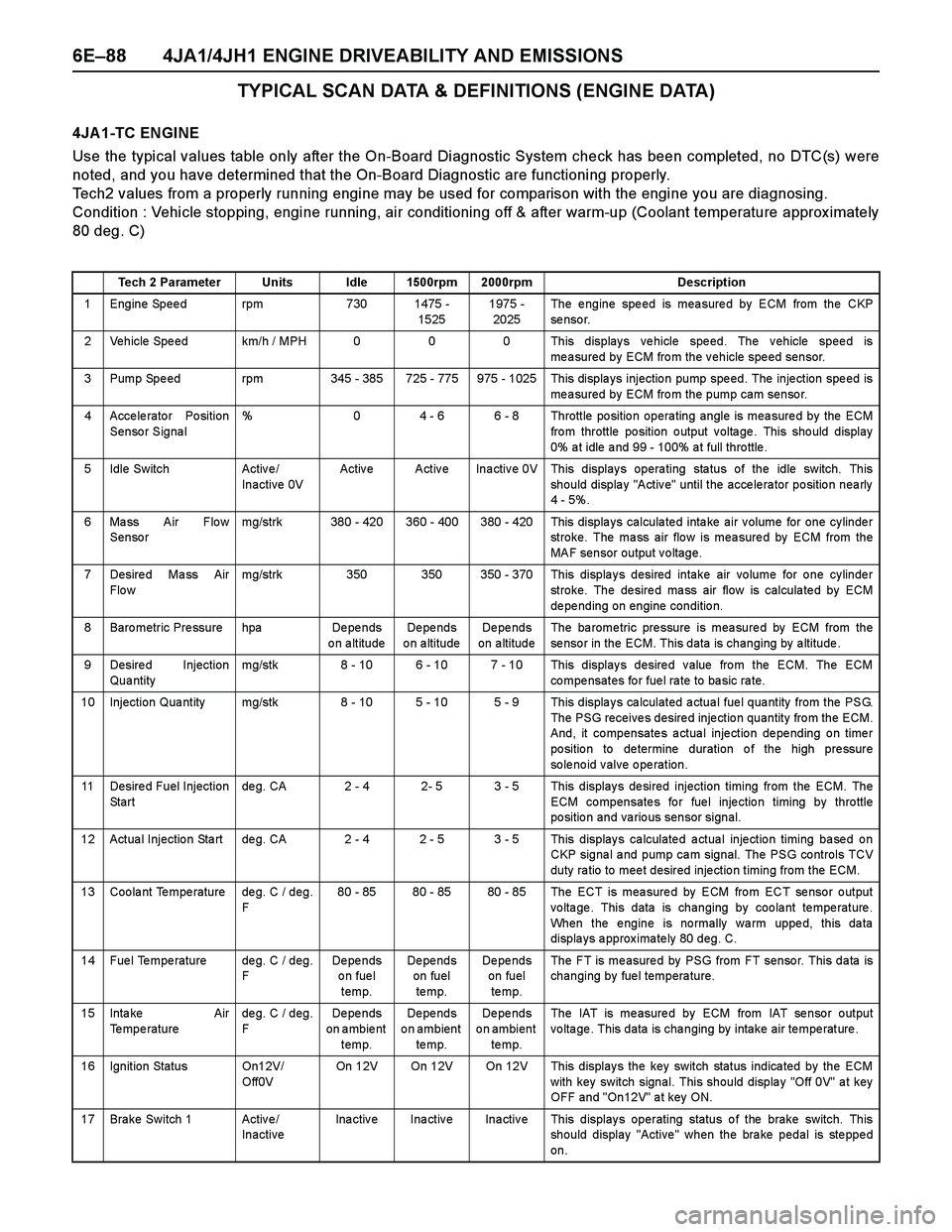
6E–88 4JA1/4JH1 ENGINE DRIVEABILITY AND EMISSIONS
TYPICAL SCAN DATA & DEFINITIONS (ENGINE DATA)
4JA 1-TC ENGINE
Use the typical values table only after the On-Board Diagnostic System check has been completed, no DTC(s) were
noted, and you have determined that the On-Board Diagnostic are functioning properly.
Tech2 values from a properly running engine may be used for comparison with the engine you are diagnosing.
Condition : Vehicle stopping, engine running, air conditioning off & after warm-up (Coolant temperature approx imately
80 deg. C)
Tech 2 Parameter Units Idle 1500rpm 2000rpm Description
1 Engine Speed rpm 730 1475 -
15251975 -
2025The engine speed is measured by ECM from the CKP
se nso r.
2 Vehicle Speed km/h / MPH 0 0 0 This displays vehicle speed. The vehicle speed is
measured by ECM from the vehicle speed sensor.
3 Pump Spe ed rpm 345 - 385 725 - 775 975 - 1025 This displa ys injectio n pump spe ed. The inje ction spe ed is
measured by ECM from the pump cam sensor.
4 Accelerator Position
Sensor Signal% 0 4 - 6 6 - 8 Throttle position operating angle is measured by the ECM
fro m throttle po sition o utput v olta ge . This sho uld display
0% a t idle a nd 99 - 100% a t full thro ttle .
5 Idle Switch Activ e /
Inactive 0VActive Active Inactive 0V This displays operating status of the idle switch. This
should display "Active" until the accelerator position nearly
4 - 5%.
6 Mass Air Flow
Sensormg/strk 380 - 420 360 - 400 380 - 420 This displays calculated intake air volume for one cylinder
stroke. The mass air flow is measured by ECM from the
MAF sensor output voltage.
7 Desire d Ma ss Air
Flo wmg/strk 350 350 350 - 370 This displays desired intake air volume for one cylinder
stroke. The desired mass air flow is calculated by ECM
de pe nding on engine conditio n.
8 Baro metric Pre ssure hpa De pe nds
on altitudeDe pe nds
o n a ltitudeDe pe nds
on altitudeThe ba rome tric pre ssure is mea sure d by ECM from the
sensor in the ECM. This data is changing by altitude.
9 Desired Injection
Qua ntitymg/stk 8 - 10 6 - 10 7 - 10 This displays desired value from the ECM. The ECM
co mpe nsates fo r fue l ra te to ba sic ra te.
10 Injection Qua ntity mg/stk 8 - 10 5 - 10 5 - 9 This displa y s ca lculated a ctua l fue l qua ntity from the PSG.
The PSG receives desired injection quantity from the ECM.
And, it compensates actual injection depending on timer
po sitio n to de termine duration o f the high pre ssure
solenoid valve operation.
11 Desire d Fuel Injection
St a r tde g. CA 2 - 4 2- 5 3 - 5 This display s de sired injection timing from the ECM. The
ECM compensates for fuel injection timing by throttle
position and various sensor signal.
12 Actua l Injectio n Sta rt de g. CA 2 - 4 2 - 5 3 - 5 This display s ca lculate d a ctua l inje ctio n timing ba se d o n
CKP signa l a nd pump ca m signal. The PSG controls TCV
duty ra tio to mee t desired inje ctio n timing from the ECM.
13 Coolant Temperature deg. C / deg.
F80 - 85 80 - 85 80 - 85 The ECT is measured by ECM from ECT sensor output
voltage. This data is changing by coolant temperature.
When the engine is normally warm upped, this data
displays approximately 80 deg. C.
14 Fuel Temperature deg. C / deg.
FDe pe nds
on fuel
temp.De pe nds
on fuel
te mp.De pe nds
on fuel
te mp.The FT is measured by PSG from FT sensor. This data is
changing by fuel temperature.
15 Inta ke Air
Temperaturedeg. C / deg.
FDe pe nds
on ambient
temp.De pe nds
on ambient
te mp.De pe nds
on ambient
te mp.The IAT is measured by ECM from IAT sensor output
voltage. This data is changing by intake air temperature.
16 Ignition Status On12V/
Off0VOn 12V On 12V On 12V This displays the key switch status indicated by the ECM
with key switch signal. This should display "Off 0V" at key
OFF and "On12V" at key ON.
17 Brake Switch 1 Active/
InactiveInactive Inactive Inactive This displays operating status of the brake switch. This
should display "Active" when the brake pedal is stepped
on.
Page 1462 of 4264
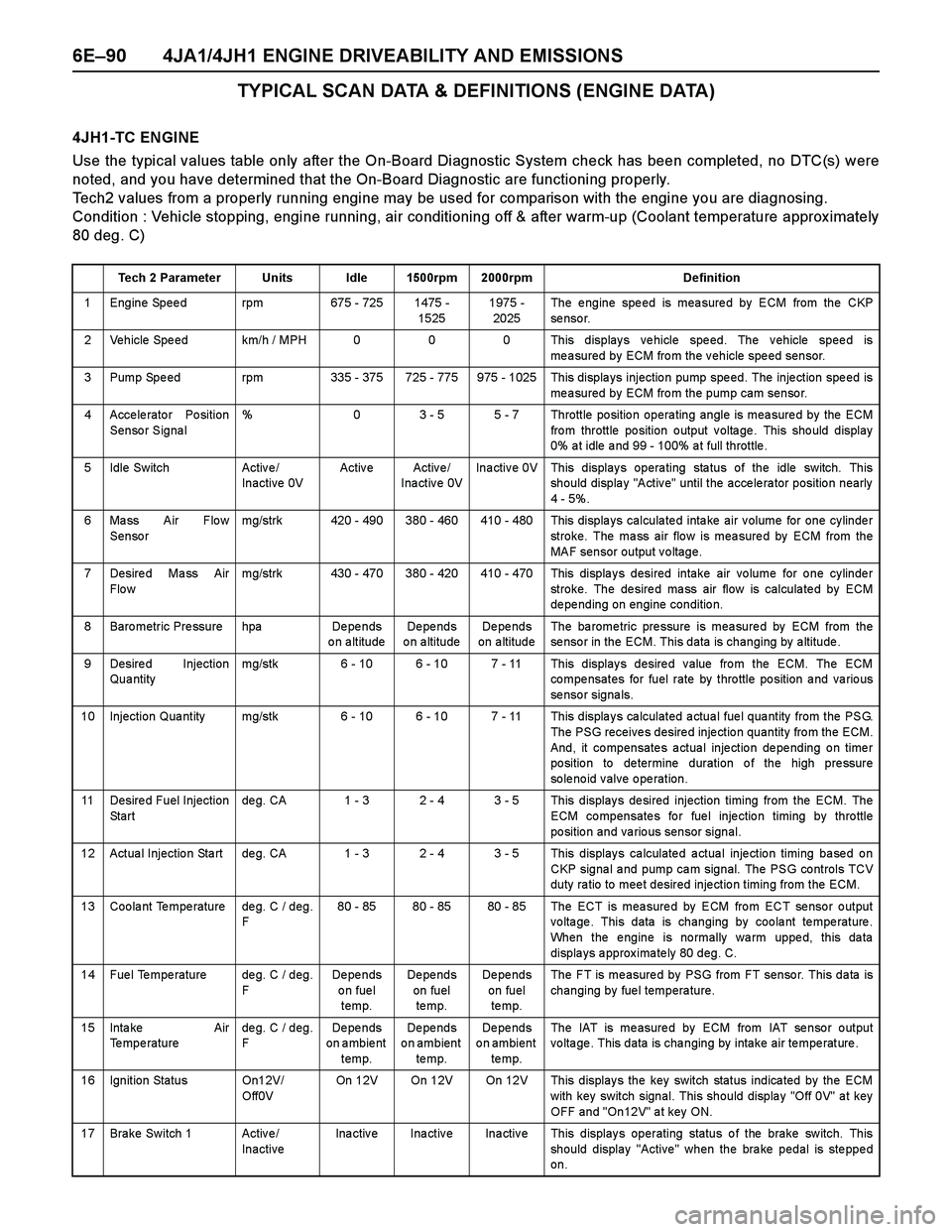
6E–90 4JA1/4JH1 ENGINE DRIVEABILITY AND EMISSIONS
TYPICAL SCAN DATA & DEFINITIONS (ENGINE DATA)
4JH1-TC ENGINE
Use the typical values table only after the On-Board Diagnostic System check has been completed, no DTC(s) were
noted, and you have determined that the On-Board Diagnostic are functioning properly.
Tech2 values from a properly running engine may be used for comparison with the engine you are diagnosing.
Condition : Vehicle stopping, engine running, air conditioning off & after warm-up (Coolant temperature approx imately
80 deg. C)
Tech 2 Parameter Units Idle 1500rpm 2000rpm Definition
1 Engine Speed rpm 675 - 725 1475 -
15251975 -
2025The engine speed is measured by ECM from the CKP
se nso r.
2 Vehicle Speed km/h / MPH 0 0 0 This displays vehicle speed. The vehicle speed is
measured by ECM from the vehicle speed sensor.
3 Pump Spe ed rpm 335 - 375 725 - 775 975 - 1025 This displa ys injectio n pump spe ed. The inje ction spe ed is
measured by ECM from the pump cam sensor.
4 Accelerator Position
Sensor Signal% 0 3 - 5 5 - 7 Throttle position operating angle is measured by the ECM
fro m throttle po sition o utput v olta ge . This sho uld display
0% a t idle a nd 99 - 100% a t full throttle .
5 Idle Switch Activ e /
Inactive 0VActive Active/
Inactive 0VInactive 0V This displays operating status of the idle switch. This
should display "Active" until the accelerator position nearly
4 - 5%.
6 Mass Air Flow
Sensormg/strk 420 - 490 380 - 460 410 - 480 This displays calculated intake air volume for one cylinder
stroke. The mass air flow is measured by ECM from the
MAF sensor output voltage.
7 Desire d Ma ss Air
Flo wmg/strk 430 - 470 380 - 420 410 - 470 This displays desired intake air volume for one cylinder
stroke. The desired mass air flow is calculated by ECM
de pe nding on engine conditio n.
8 Baro metric Pre ssure hpa De pe nds
on altitudeDe pe nds
o n a ltitudeDe pe nds
on altitudeThe ba rome tric pre ssure is mea sure d by ECM from the
sensor in the ECM. This data is changing by altitude.
9 Desired Injection
Qua ntitymg/stk 6 - 10 6 - 10 7 - 11 This displays desired value from the ECM. The ECM
co mpe nsates for fuel rate by thro ttle po sition a nd va rio us
se nso r signa ls.
10 Injection Qua ntity mg/stk 6 - 10 6 - 10 7 - 11 This displa y s ca lculated a ctua l fue l qua ntity from the PSG.
The PSG receives desired injection quantity from the ECM.
And, it compensates actual injection depending on timer
po sitio n to de termine duration o f the high pre ssure
solenoid valve operation.
11 Desire d Fuel Injection
St a r tde g. CA 1 - 3 2 - 4 3 - 5 This display s de sired injection timing from the ECM. The
ECM compensates for fuel injection timing by throttle
position and various sensor signal.
12 Actua l Injectio n Sta rt de g. CA 1 - 3 2 - 4 3 - 5 This display s ca lculate d a ctua l inje ctio n timing ba se d o n
CKP signa l a nd pump ca m signal. The PSG controls TCV
duty ra tio to mee t desired inje ctio n timing from the ECM.
13 Coolant Temperature deg. C / deg.
F80 - 85 80 - 85 80 - 85 The ECT is measured by ECM from ECT sensor output
voltage. This data is changing by coolant temperature.
When the engine is normally warm upped, this data
displays approximately 80 deg. C.
14 Fuel Temperature deg. C / deg.
FDe pe nds
on fuel
temp.De pe nds
on fuel
te mp.De pe nds
on fuel
te mp.The FT is measured by PSG from FT sensor. This data is
changing by fuel temperature.
15 Inta ke Air
Temperaturedeg. C / deg.
FDe pe nds
on ambient
temp.De pe nds
on ambient
te mp.De pe nds
on ambient
te mp.The IAT is measured by ECM from IAT sensor output
voltage. This data is changing by intake air temperature.
16 Ignition Status On12V/
Off0VOn 12V On 12V On 12V This displays the key switch status indicated by the ECM
with key switch signal. This should display "Off 0V" at key
OFF and "On12V" at key ON.
17 Brake Switch 1 Active/
InactiveInactive Inactive Inactive This displays operating status of the brake switch. This
should display "Active" when the brake pedal is stepped
on.
Page 1873 of 4264
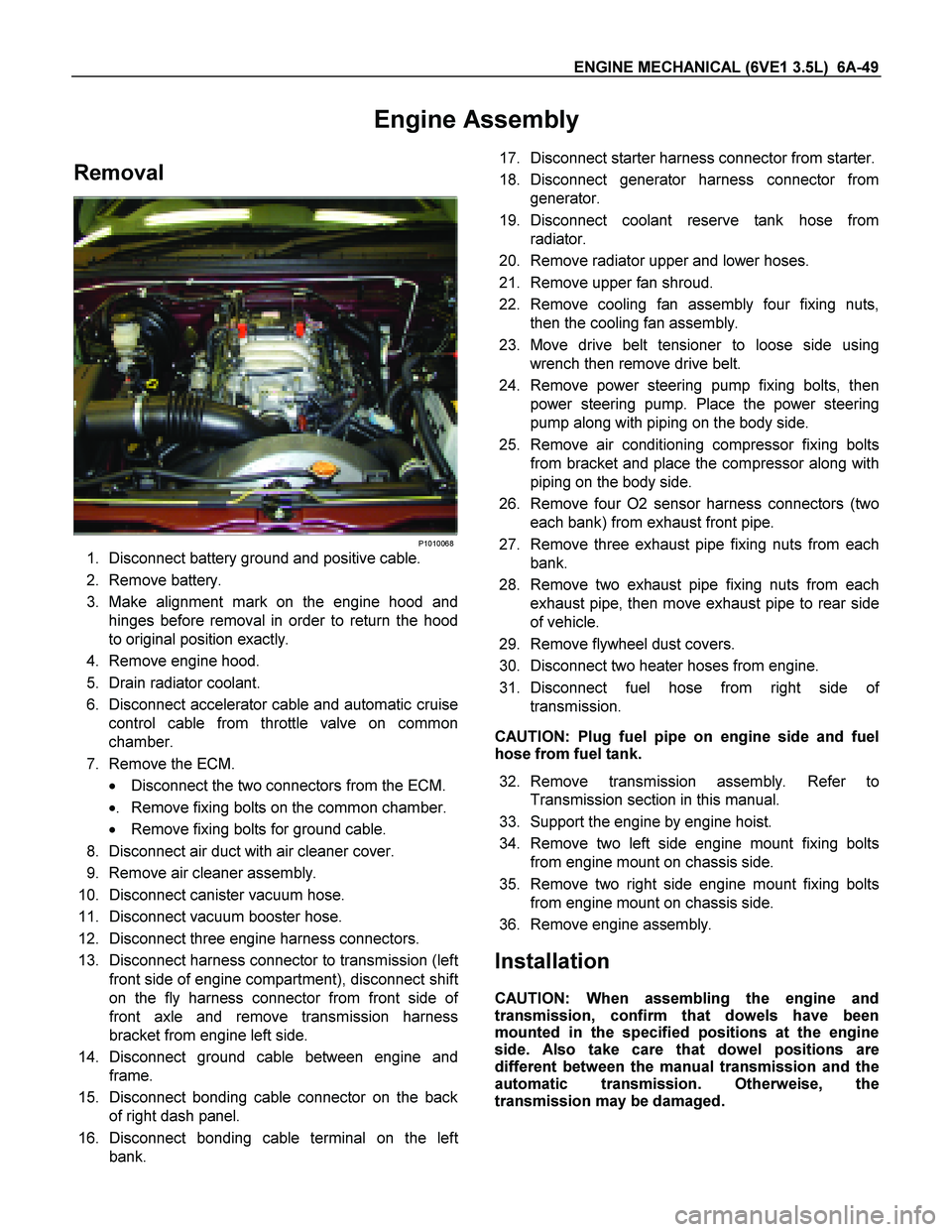
ENGINE MECHANICAL (6VE1 3.5L) 6A-49
Engine Assembly
Removal
P1010068
1. Disconnect battery ground and positive cable.
2. Remove battery.
3. Make alignment mark on the engine hood and
hinges before removal in order to return the hood
to original position exactly.
4. Remove engine hood.
5. Drain radiator coolant.
6. Disconnect accelerator cable and automatic cruise
control cable from throttle valve on common
chamber.
7. Remove the ECM.
Disconnect the two connectors from the ECM.
. Remove fixing bolts on the common chamber.
Remove fixing bolts for ground cable.
8. Disconnect air duct with air cleaner cover.
9. Remove air cleaner assembly.
10. Disconnect canister vacuum hose.
11. Disconnect vacuum booster hose.
12. Disconnect three engine harness connectors.
13. Disconnect harness connector to transmission (lef
t
front side of engine compartment), disconnect shift
on the fly harness connector from front side o
f
front axle and remove transmission harness
bracket from engine left side.
14. Disconnect ground cable between engine and
frame.
15. Disconnect bonding cable connector on the back
of right dash panel.
16. Disconnect bonding cable terminal on the lef
t
bank.
17. Disconnect starter harness connector from starter.
18. Disconnect generator harness connector from
generator.
19. Disconnect coolant reserve tank hose from
radiator.
20. Remove radiator upper and lower hoses.
21. Remove upper fan shroud.
22. Remove cooling fan assembly four fixing nuts,
then the cooling fan assembly.
23. Move drive belt tensioner to loose side using
wrench then remove drive belt.
24. Remove power steering pump fixing bolts, then
power steering pump. Place the power steering
pump along with piping on the body side.
25. Remove air conditioning compressor fixing bolts
from bracket and place the compressor along with
piping on the body side.
26. Remove four O2 sensor harness connectors (two
each bank) from exhaust front pipe.
27. Remove three exhaust pipe fixing nuts from each
bank.
28. Remove two exhaust pipe fixing nuts from each
exhaust pipe, then move exhaust pipe to rear side
of vehicle.
29. Remove flywheel dust covers.
30. Disconnect two heater hoses from engine.
31. Disconnect fuel hose from right side o
f
transmission.
CAUTION: Plug fuel pipe on engine side and fuel
hose from fuel tank.
32. Remove transmission assembly. Refer to
Transmission section in this manual.
33. Support the engine by engine hoist.
34. Remove two left side engine mount fixing bolts
from engine mount on chassis side.
35. Remove two right side engine mount fixing bolts
from engine mount on chassis side.
36. Remove engine assembly.
Installation
CAUTION: When assembling the engine and
transmission, confirm that dowels have been
mounted in the specified positions at the engine
side. Also take care that dowel positions are
different between the manual transmission and the
automatic transmission. Otherweise, the
transmission may be damaged.
Page 1962 of 4264
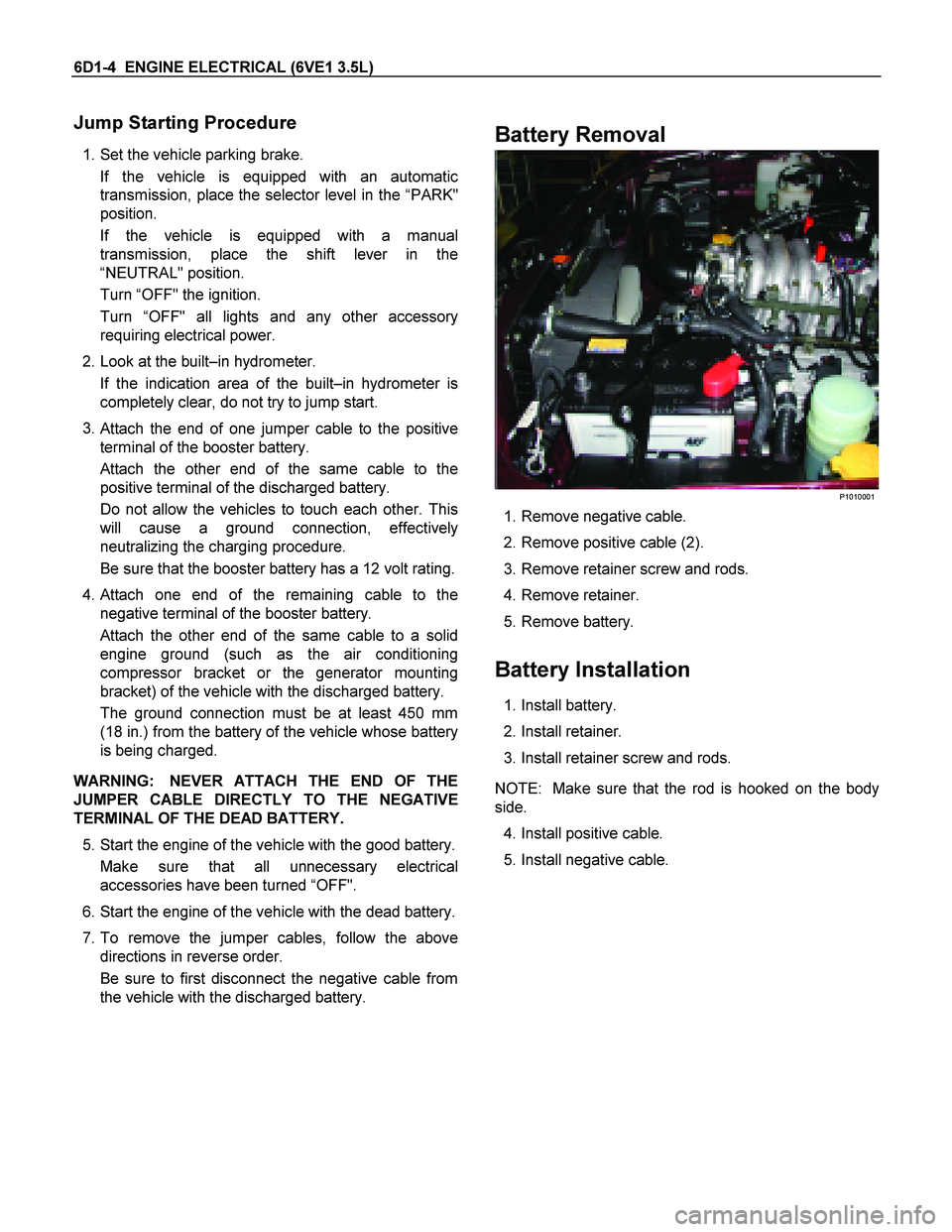
6D1-4 ENGINE ELECTRICAL (6VE1 3.5L)
Jump Starting Procedure
1. Set the vehicle parking brake.
If the vehicle is equipped with an automatic
transmission, place the selector level in the “PARK"
position.
If the vehicle is equipped with a manual
transmission, place the shift lever in the
“ NEUTRAL" position.
Turn “OFF" the ignition.
Turn “OFF" all lights and any other accessory
requiring electrical power.
2. Look at the built –in hydrometer.
If the indication area of the built –in hydrometer is
completely clear, do not try to jump start.
3.
Attach the end of one jumper cable to the positive
terminal of the booster battery.
Attach the other end of the same cable to the
positive terminal of the discharged battery.
Do not allow the vehicles to touch each other. This
will cause a ground connection, effectively
neutralizing the charging procedure.
Be sure that the booster battery has a 12 volt rating.
4. Attach one end of the remaining cable to the
negative terminal of the booster battery.
Attach the other end of the same cable to a solid
engine ground (such as the air conditioning
compressor bracket or the generator mounting
bracket) of the vehicle with the discharged battery.
The ground connection must be at least 450 mm
(18 in.) from the battery of the vehicle whose battery
is being charged.
WARNING: NEVER ATTACH THE END OF THE
JUMPER CABLE DIRECTLY TO THE NEGATIVE
TERMINAL OF THE DEAD BATTERY.
5. Start the engine of the vehicle with the good battery.
Make sure that all unnecessary electrical
accessories have been turned “OFF".
6. Start the engine of the vehicle with the dead battery.
7. To remove the jumper cables, follow the above directions in reverse order.
Be sure to first disconnect the negative cable from
the vehicle with the discharged battery.
Battery Removal
P1010001
1. Remove negative cable.
2. Remove positive cable (2).
3. Remove retainer screw and rods.
4. Remove retainer.
5. Remove battery.
Battery Installation
1. Install battery.
2. Install retainer.
3. Install retainer screw and rods.
NOTE: Make sure that the rod is hooked on the body
side.
4. Install positive cable.
5. Install negative cable.
Page 2047 of 4264
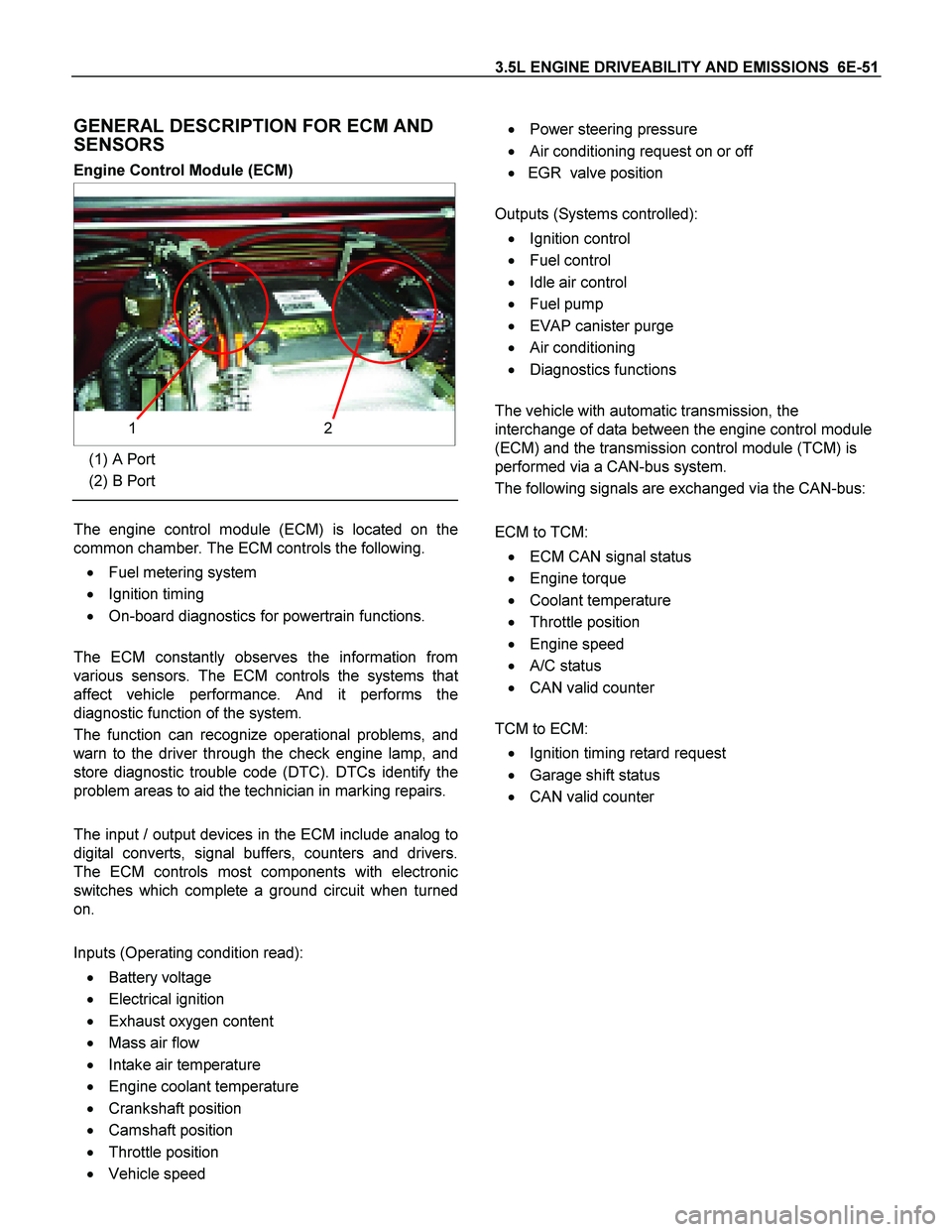
3.5L ENGINE DRIVEABILITY AND EMISSIONS 6E-51
GENERAL DESCRIPTION FOR ECM AND
SENSORS
Engine Control Module (ECM)
1 2
(1) A Port
(2) B Port
The engine control module (ECM) is located on the
common chamber. The ECM controls the following.
Fuel metering system
Ignition timing
On-board diagnostics for powertrain functions.
The ECM constantly observes the information from
various sensors. The ECM controls the systems tha
t
affect vehicle performance. And it performs the
diagnostic function of the system.
The function can recognize operational problems, and
warn to the driver through the check engine lamp, and
store diagnostic trouble code (DTC). DTCs identify the
problem areas to aid the technician in marking repairs.
The input / output devices in the ECM include analog to
digital converts, signal buffers, counters and drivers.
The ECM controls most components with electronic
switches which complete a ground circuit when turned
on.
Inputs (Operating condition read):
Battery voltage
Electrical ignition
Exhaust oxygen content
Mass air flow
Intake air temperature
Engine coolant temperature
Crankshaft position
Camshaft position
Throttle position
Vehicle speed
Power steering pressure
Air conditioning request on or off
EGR valve position
Outputs (Systems controlled):
Ignition control
Fuel control
Idle air control
Fuel pump
EVAP canister purge
Air conditioning
Diagnostics functions
The vehicle with automatic transmission, the
interchange of data between the engine control module
(ECM) and the transmission control module (TCM) is
performed via a CAN-bus system.
The following signals are exchanged via the CAN-bus:
ECM to TCM:
ECM CAN signal status
Engine torque
Coolant temperature
Throttle position
Engine speed
A/C status
CAN valid counter
TCM to ECM:
Ignition timing retard request
Garage shift status
CAN valid counter
Page 2049 of 4264
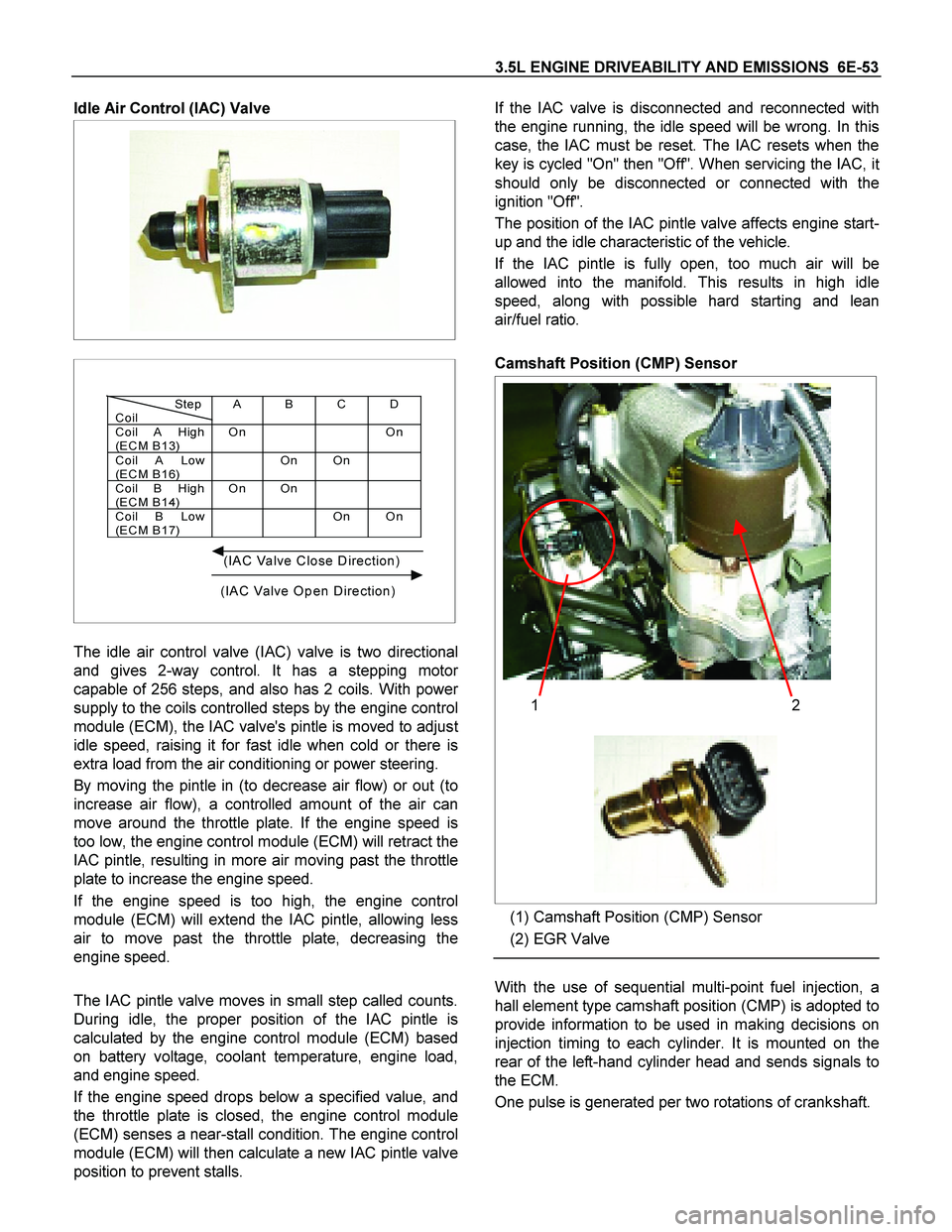
3.5L ENGINE DRIVEABILITY AND EMISSIONS 6E-53
Idle Air Control (IAC) Valve
Step
CoilAB CD
Coil A High
(EC M B13)On On
Coil A Low
(EC M B16)On On
Coil B High
(EC M B14)On On
Coil B Low
(EC M B17)On On
(IAC Valve Close Direction)
(IAC Valve Open Direction)
The idle air control valve (IAC) valve is two directional
and gives 2-way control. It has a stepping moto
r
capable of 256 steps, and also has 2 coils. With power
supply to the coils controlled steps by the engine control
module (ECM), the IAC valve's pintle is moved to adjus
t
idle speed, raising it for fast idle when cold or there is
extra load from the air conditioning or power steering.
By moving the pintle in (to decrease air flow) or out (to
increase air flow), a controlled amount of the air can
move around the throttle plate. If the engine speed is
too low, the engine control module (ECM) will retract the
IAC pintle, resulting in more air moving past the throttle
plate to increase the engine speed.
If the engine speed is too high, the engine control
module (ECM) will extend the IAC pintle, allowing less
air to move past the throttle plate, decreasing the
engine speed.
The IAC pintle valve moves in small step called counts.
During idle, the proper position of the IAC pintle is
calculated by the engine control module (ECM) based
on battery voltage, coolant temperature, engine load,
and engine speed.
If the engine speed drops below a specified value, and
the throttle plate is closed, the engine control module
(ECM) senses a near-stall condition. The engine control
module (ECM) will then calculate a new IAC pintle valve
position to prevent stalls. If the IAC valve is disconnected and reconnected with
the engine running, the idle speed will be wrong. In this
case, the IAC must be reset. The IAC resets when the
key is cycled "On" then "Off". When servicing the IAC, i
t
should only be disconnected or connected with the
ignition "Off".
The position of the IAC pintle valve affects engine start-
up and the idle characteristic of the vehicle.
If the IAC pintle is fully open, too much air will be
allowed into the manifold. This results in high idle
speed, along with possible hard starting and lean
air/fuel ratio.
Camshaft Position (CMP) Sensor
12
(1) Camshaft Position (CMP) Sensor
(2) EGR Valve
With the use of sequential multi-point fuel injection, a
hall element type camshaft position (CMP) is adopted to
provide information to be used in making decisions on
injection timing to each cylinder. It is mounted on the
rear of the left-hand cylinder head and sends signals to
the ECM.
One pulse is generated per two rotations of crankshaft.