open gas tank ISUZU TF SERIES 2004 Workshop Manual
[x] Cancel search | Manufacturer: ISUZU, Model Year: 2004, Model line: TF SERIES, Model: ISUZU TF SERIES 2004Pages: 4264, PDF Size: 72.63 MB
Page 1829 of 4264
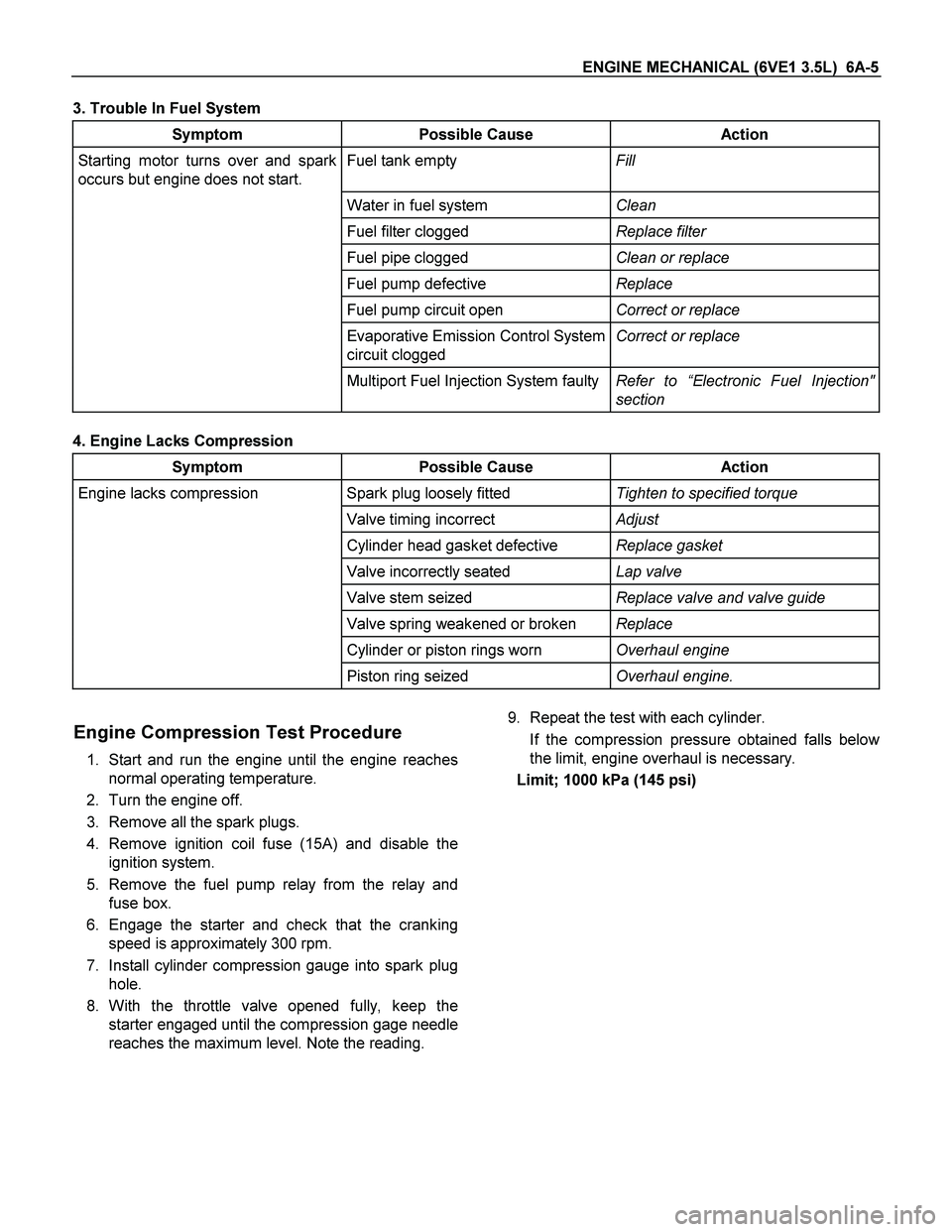
ENGINE MECHANICAL (6VE1 3.5L) 6A-5
3. Trouble In Fuel System
Symptom Possible Cause Action
Starting motor turns over and spark
occurs but engine does not start. Fuel tank empty Fill
Water in fuel system Clean
Fuel filter clogged Replace filter
Fuel pipe clogged Clean or replace
Fuel pump defective Replace
Fuel pump circuit open Correct or replace
Evaporative Emission Control System
circuit clogged Correct or replace
Multiport Fuel Injection System faultyRefer to “Electronic Fuel Injection"
section
4. Engine Lacks Compression
Symptom Possible Cause Action
Engine lacks compression Spark plug loosely fitted Tighten to specified torque
Valve timing incorrect Adjust
Cylinder head gasket defective Replace gasket
Valve incorrectly seated Lap valve
Valve stem seized Replace valve and valve guide
Valve spring weakened or broken Replace
Cylinder or piston rings worn Overhaul engine
Piston ring seized Overhaul engine.
Engine Compression Test Procedure
1. Start and run the engine until the engine reaches
normal operating temperature.
2. Turn the engine off.
3. Remove all the spark plugs.
4. Remove ignition coil fuse (15A) and disable the
ignition system.
5. Remove the fuel pump relay from the relay and
fuse box.
6. Engage the starter and check that the cranking
speed is approximately 300 rpm.
7. Install cylinder compression gauge into spark plug
hole.
8. With the throttle valve opened fully, keep the
starter engaged until the compression gage needle
reaches the maximum level. Note the reading.
9. Repeat the test with each cylinder.
If the compression pressure obtained falls belo
w
the limit, engine overhaul is necessary.
Limit; 1000 kPa (145 psi)
Page 2052 of 4264
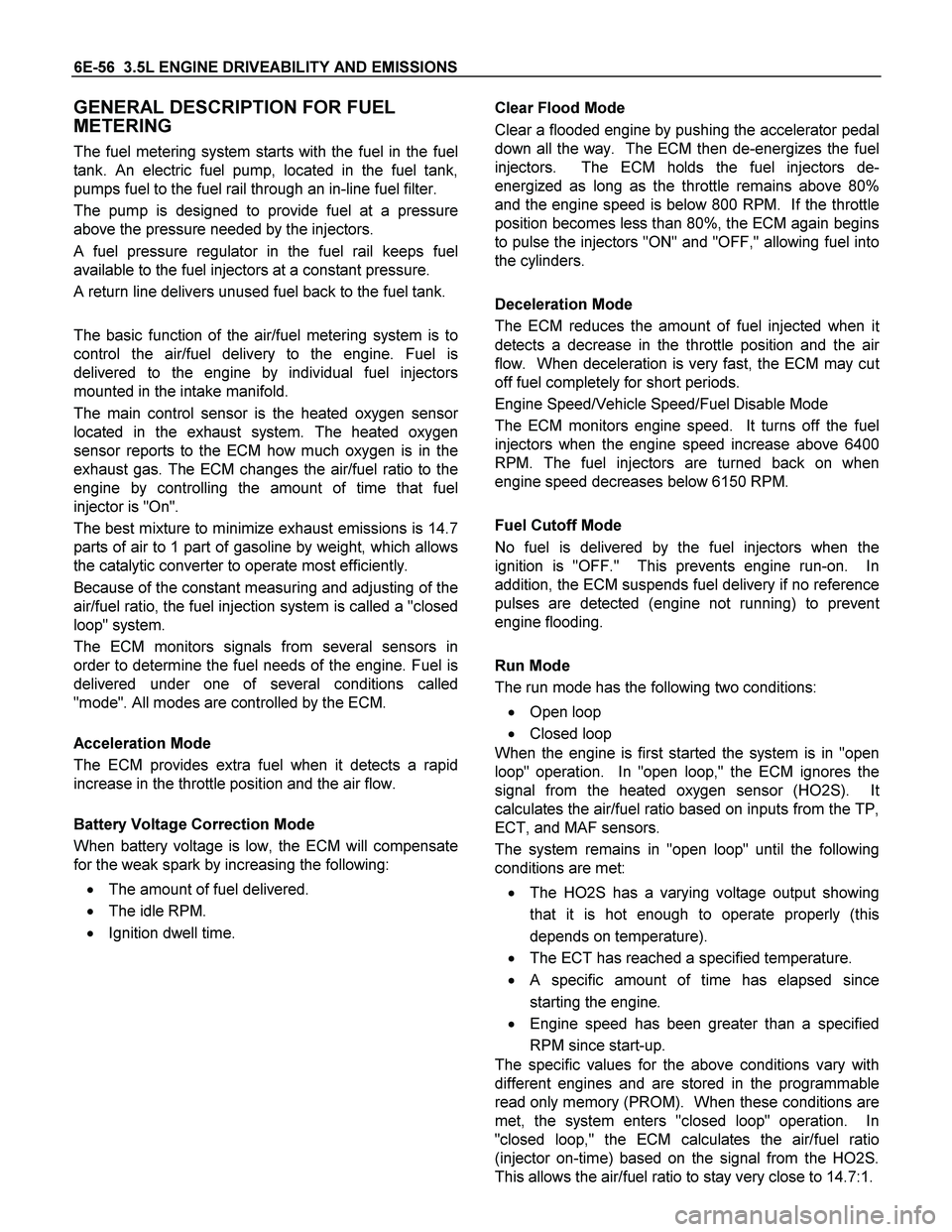
6E-56 3.5L ENGINE DRIVEABILITY AND EMISSIONS
GENERAL DESCRIPTION FOR FUEL
METERING
The fuel metering system starts with the fuel in the fuel
tank. An electric fuel pump, located in the fuel tank,
pumps fuel to the fuel rail through an in-line fuel filter.
The pump is designed to provide fuel at a pressure
above the pressure needed by the injectors.
A fuel pressure regulator in the fuel rail keeps fuel
available to the fuel injectors at a constant pressure.
A return line delivers unused fuel back to the fuel tank.
The basic function of the air/fuel metering system is to
control the air/fuel delivery to the engine. Fuel is
delivered to the engine by individual fuel injectors
mounted in the intake manifold.
The main control sensor is the heated oxygen senso
r
located in the exhaust system. The heated oxygen
sensor reports to the ECM how much oxygen is in the
exhaust gas. The ECM changes the air/fuel ratio to the
engine by controlling the amount of time that fuel
injector is "On".
The best mixture to minimize exhaust emissions is 14.7
parts of air to 1 part of gasoline by weight, which allows
the catalytic converter to operate most efficiently.
Because of the constant measuring and adjusting of the
air/fuel ratio, the fuel injection system is called a "closed
loop" system.
The ECM monitors signals from several sensors in
order to determine the fuel needs of the engine. Fuel is
delivered under one of several conditions called
"mode". All modes are controlled by the ECM.
Acceleration Mode
The ECM provides extra fuel when it detects a rapid
increase in the throttle position and the air flow.
Battery Voltage Correction Mode
When battery voltage is low, the ECM will compensate
for the weak spark by increasing the following:
The amount of fuel delivered.
The idle RPM.
Ignition dwell time.
Clear Flood Mode
Clear a flooded engine by pushing the accelerator pedal
down all the way. The ECM then de-energizes the fuel
injectors. The ECM holds the fuel injectors de-
energized as long as the throttle remains above 80%
and the engine speed is below 800 RPM. If the throttle
position becomes less than 80%, the ECM again begins
to pulse the injectors "ON" and "OFF," allowing fuel into
the cylinders.
Deceleration Mode
The ECM reduces the amount of fuel injected when i
t
detects a decrease in the throttle position and the air
flow. When deceleration is very fast, the ECM may cu
t
off fuel completely for short periods.
Engine Speed/Vehicle Speed/Fuel Disable Mode
The ECM monitors engine speed. It turns off the fuel
injectors when the engine speed increase above 6400
RPM. The fuel injectors are turned back on when
engine speed decreases below 6150 RPM.
Fuel Cutoff Mode
No fuel is delivered by the fuel injectors when the
ignition is "OFF." This prevents engine run-on. In
addition, the ECM suspends fuel delivery if no reference
pulses are detected (engine not running) to preven
t
engine flooding.
Run Mode
The run mode has the following two conditions:
Open loop
Closed loop
When the engine is first started the system is in "open
loop" operation. In "open loop," the ECM ignores the
signal from the heated oxygen sensor (HO2S). I
t
calculates the air/fuel ratio based on inputs from the TP,
ECT, and MAF sensors.
The system remains in "open loop" until the following
conditions are met:
The HO2S has a varying voltage output showing
that it is hot enough to operate properly (this
depends on temperature).
The ECT has reached a specified temperature.
A specific amount of time has elapsed since
starting the engine.
Engine speed has been greater than a specified
RPM since start-up.
The specific values for the above conditions vary with
different engines and are stored in the programmable
read only memory (PROM). When these conditions are
met, the system enters "closed loop" operation. In
"closed loop," the ECM calculates the air/fuel ratio
(injector on-time) based on the signal from the HO2S.
This allows the air/fuel ratio to stay very close to 14.7:1.
Page 2352 of 4264
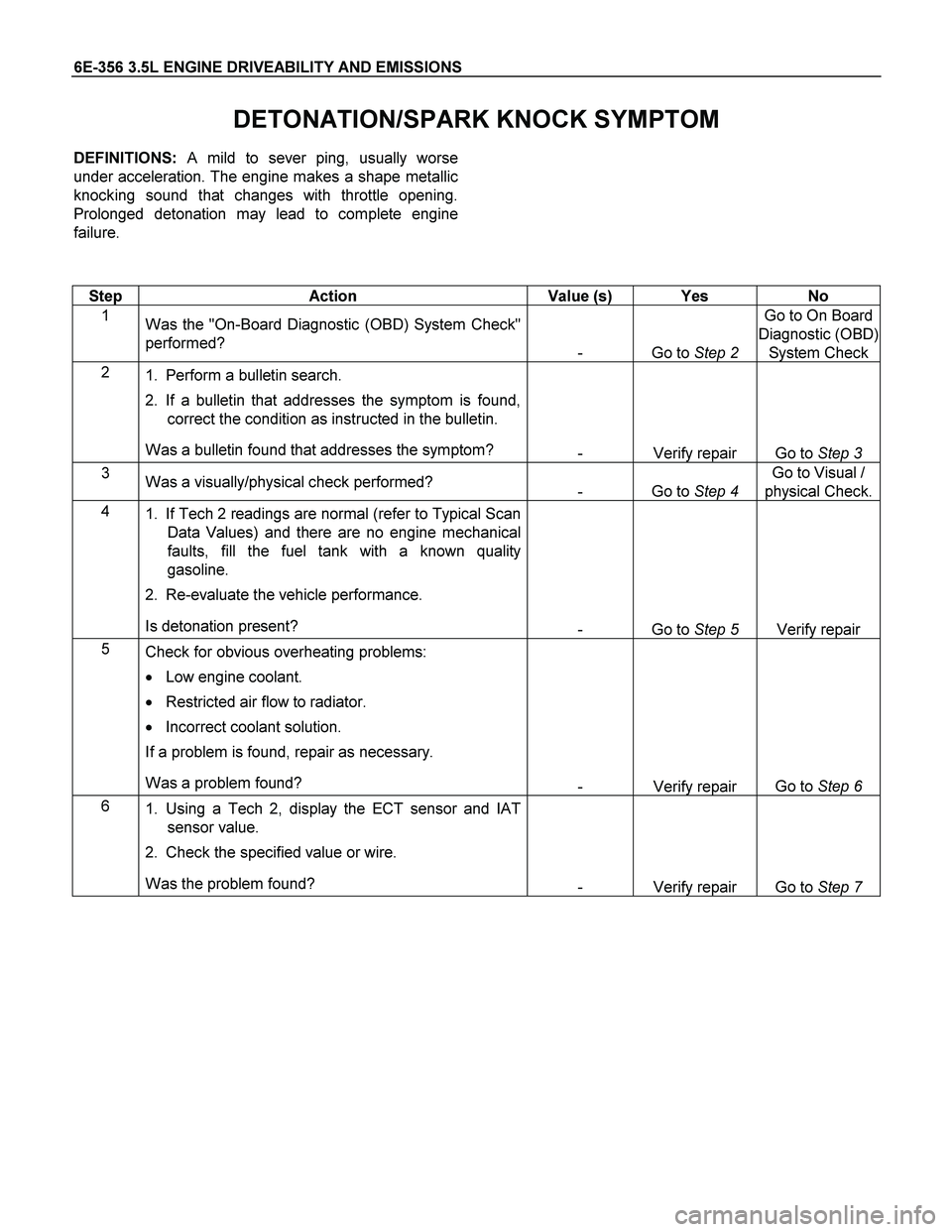
6E-356 3.5L ENGINE DRIVEABILITY AND EMISSIONS
DETONATION/SPARK KNOCK SYMPTOM
DEFINITIONS: A mild to sever ping, usually worse
under acceleration. The engine makes a shape metallic
knocking sound that changes with throttle opening.
Prolonged detonation may lead to complete engine
failure.
Step Action Value (s) Yes No
1
Was the "On-Board Diagnostic (OBD) System Check"
performed?
- Go to Step 2 Go to On Board
Diagnostic (OBD)
System Check
2
1. Perform a bulletin search.
2. If a bulletin that addresses the symptom is found,
correct the condition as instructed in the bulletin.
Was a bulletin found that addresses the symptom?
- Verify repair Go to Step 3
3
Was a visually/physical check performed?
- Go to Step 4 Go to Visual /
physical Check.
4
1. If Tech 2 readings are normal (refer to Typical Scan
Data Values) and there are no engine mechanical
faults, fill the fuel tank with a known quality
gasoline.
2. Re-evaluate the vehicle performance.
Is detonation present?
- Go to Step 5
Verify repair
5
Check for obvious overheating problems:
Low engine coolant.
Restricted air flow to radiator.
Incorrect coolant solution.
If a problem is found, repair as necessary.
Was a problem found?
- Verify repair Go to Step 6
6
1. Using a Tech 2, display the ECT sensor and IAT
sensor value.
2. Check the specified value or wire.
Was the problem found?
- Verify repair Go to Step 7
Page 2409 of 4264
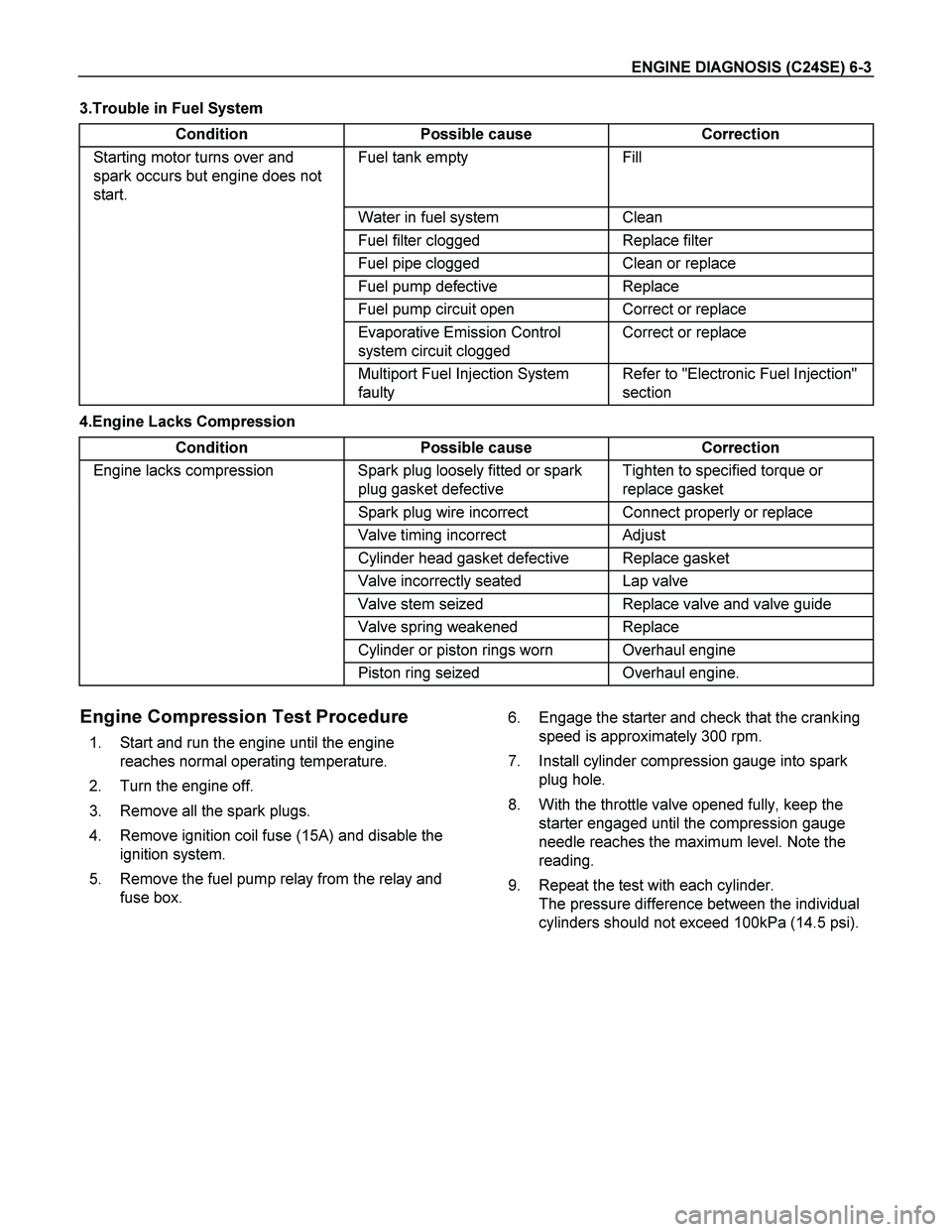
ENGINE DIAGNOSIS (C24SE) 6-3
3.Trouble in Fuel System
Condition Possible cause Correction
Starting motor turns over and
spark occurs but engine does not
start. Fuel tank empty Fill
Water in fuel system Clean
Fuel filter clogged Replace filter
Fuel pipe clogged Clean or replace
Fuel pump defective Replace
Fuel pump circuit open Correct or replace
Evaporative Emission Control
system circuit clogged Correct or replace
Multiport Fuel Injection System
faulty Refer to "Electronic Fuel Injection"
section
4.Engine Lacks Compression
Condition Possible cause Correction
Engine lacks compression Spark plug loosely fitted or spark
plug gasket defective Tighten to specified torque or
replace gasket
Spark plug wire incorrect Connect properly or replace
Valve timing incorrect Adjust
Cylinder head gasket defective Replace gasket
Valve incorrectly seated Lap valve
Valve stem seized Replace valve and valve guide
Valve spring weakened Replace
Cylinder or piston rings worn Overhaul engine
Piston ring seized Overhaul engine.
Engine Compression Test Procedure
1. Start and run the engine until the engine
reaches normal operating temperature.
2. Turn the engine off.
3. Remove all the spark plugs.
4. Remove ignition coil fuse (15A) and disable the
ignition system.
5. Remove the fuel pump relay from the relay and
fuse box. 6. Engage the starter and check that the cranking
speed is approximately 300 rpm.
7. Install cylinder compression gauge into spark
plug hole.
8. With the throttle valve opened fully, keep the
starter engaged until the compression gauge
needle reaches the maximum level. Note the
reading.
9. Repeat the test with each cylinder.
The pressure difference between the individual
cylinders should not exceed 100kPa (14.5 psi).
Page 2628 of 4264
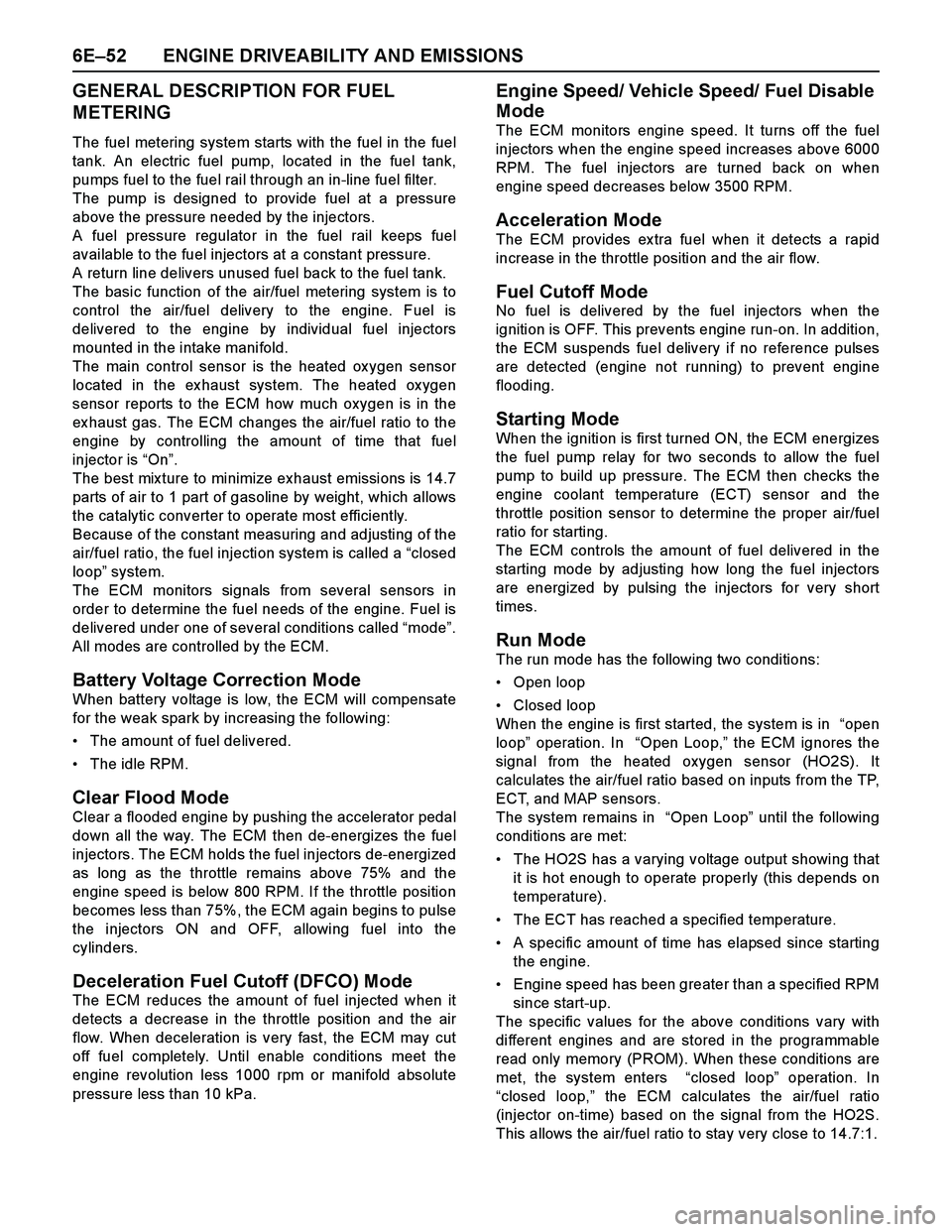
6E–52 ENGINE DRIVEABILITY AND EMISSIONS
GENERAL DESCRIPTION FOR FUEL
METERING
The fuel metering system starts with the fuel in the fuel
tank. An electric fuel pump, located in the fuel tank,
pumps fuel to the fuel rail through an in-line fuel filter.
The pump is designed to provide fuel at a pressure
above the pressure needed by the injectors.
A fuel pressure regulator in the fuel rail keeps fuel
available to the fuel injectors at a constant pressure.
A return line delivers unused fuel back to the fuel tank.
The basic function of the air/fuel metering system is to
control the air/fuel delivery to the engine. Fuel is
delivered to the engine by individual fuel injectors
mounted in the intake manifold.
The main control sensor is the heated ox ygen sensor
located in the ex haust system. The heated ox ygen
sensor reports to the ECM how much oxygen is in the
ex haust gas. The ECM changes the air/fuel ratio to the
engine by controlling the amount of time that fuel
injector is “On”.
The best mix ture to minimize exhaust emissions is 14.7
parts of air to 1 part of gasoline by weight, which allows
the catalytic converter to operate most efficiently.
Because of the constant measuring and adjusting of the
air/fuel ratio, the fuel injection system is called a “closed
loop” system.
The ECM monitors signals from several sensors in
order to determine the fuel needs of the engine. Fuel is
delivered under one of several conditions called “mode”.
All modes are controlled by the ECM.
Battery Voltage Correction Mode
When battery voltage is low, the ECM will compensate
for the weak spark by increasing the following:
The amount of fuel delivered.
The idle RPM.
Clear Flood Mode
Clear a flooded engine by pushing the accelerator pedal
down all the way. The ECM then de-energizes the fuel
injectors. The ECM holds the fuel injectors de-energized
as long as the throttle remains above 75% and the
engine speed is below 800 RPM. If the throttle position
becomes less than 75%, the ECM again begins to pulse
the injectors ON and OFF, allowing fuel into the
cylinders.
Deceleration Fuel Cutoff (DFCO) Mode
The ECM reduces the amount of fuel injected when it
detects a decrease in the throttle position and the air
flow. When deceleration is very fast, the ECM may cut
off fuel completely. Until enable conditions meet the
engine revolution less 1000 rpm or manifold absolute
pressure less than 10 kPa.
Engine Speed/ Vehicle Speed/ Fuel Disable
Mode
The ECM monitors engine speed. It turns off the fuel
injectors when the engine speed increases above 6000
RPM. The fuel injectors are turned back on when
engine speed decreases below 3500 RPM.
Acceleration Mode
The ECM provides ex tra fuel when it detects a rapid
increase in the throttle position and the air flow.
Fuel Cutoff Mode
No fuel is delivered by the fuel injectors when the
ignition is OFF. This prevents engine run-on. In addition,
the ECM suspends fuel delivery if no reference pulses
are detected (engine not running) to prevent engine
flooding.
Starting Mode
When the ignition is first turned ON, the ECM energizes
the fuel pump relay for two seconds to allow the fuel
pump to build up pressure. The ECM then checks the
engine coolant temperature (ECT) sensor and the
throttle position sensor to determine the proper air/fuel
ratio for starting.
The ECM controls the amount of fuel delivered in the
starting mode by adjusting how long the fuel injectors
are energized by pulsing the injectors for very short
times.
Run Mode
The run mode has the following two conditions:
Open loop
Closed loop
When the engine is first started, the system is in “open
loop” operation. In “Open Loop,” the ECM ignores the
signal from the heated oxygen sensor (HO2S). It
calculates the air/fuel ratio based on inputs from the TP,
ECT, and MAP sensors.
The system remains in “Open Loop” until the following
conditions are met:
The HO2S has a varying voltage output showing that
it is hot enough to operate properly (this depends on
temperature).
The ECT has reached a specified temperature.
A specific amount of time has elapsed since starting
the engine.
Engine speed has been greater than a specified RPM
since start-up.
The specific values for the above conditions vary with
different engines and are stored in the programmable
read only memory (PROM). When these conditions are
met, the system enters “closed loop” operation. In
“closed loop,” the ECM calculates the air/fuel ratio
(injector on-time) based on the signal from the HO2S.
This allows the air/fuel ratio to stay very close to 14.7:1.
Page 2633 of 4264
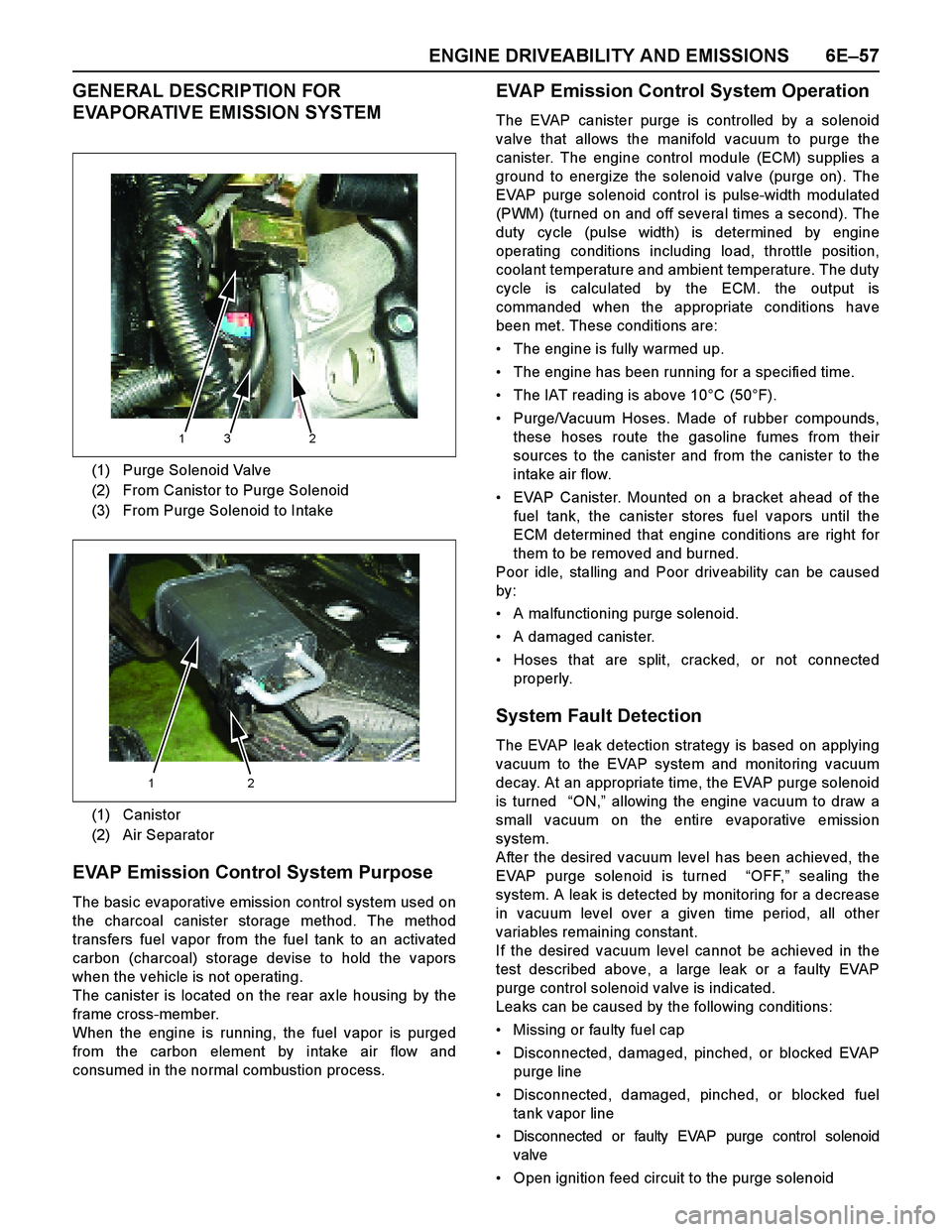
ENGINE DRIVEABILITY AND EMISSIONS 6E–57
GENERAL DESCRIPTION FOR
EVAPORATIVE EMISSION SYSTEM
EVAP Emission Control System Purpose
The basic evaporative emission control system used on
the charcoal canister storage method. The method
transfers fuel vapor from the fuel tank to an activated
carbon (charcoal) storage devise to hold the vapors
when the vehicle is not operating.
The canister is located on the rear ax le housing by the
frame cross-member.
When the engine is running, the fuel vapor is purged
from the carbon element by intake air flow and
consumed in the normal combustion process.
EVAP Emission Control System Operation
The EVAP canister purge is controlled by a solenoid
valve that allows the manifold vacuum to purge the
canister. The engine control module (ECM) supplies a
ground to energize the solenoid valve (purge on). The
EVAP purge solenoid control is pulse-width modulated
(PWM) (turned on and off several times a second). The
duty cycle (pulse width) is determined by engine
operating conditions including load, throttle position,
coolant temperature and ambient temperature. The duty
cycle is calculated by the ECM. the output is
commanded when the appropriate conditions have
been met. These conditions are:
The engine is fully warmed up.
The engine has been running for a specified time.
The IAT reading is above 10°C (50°F).
Purge/Vacuum Hoses. Made of rubber compounds,
these hoses route the gasoline fumes from their
sources to the canister and from the canister to the
intake air flow.
EVAP Canister. Mounted on a bracket ahead of the
fuel tank, the canister stores fuel vapors until the
ECM determined that engine conditions are right for
them to be removed and burned.
Poor idle, stalling and Poor driveability can be caused
by:
A malfunctioning purge solenoid.
A damaged canister.
Hoses that are split, cracked, or not connected
properly.
System Fault Detection
The EVAP leak detection strategy is based on applying
vacuum to the EVAP system and monitoring vacuum
decay. At an appropriate time, the EVAP purge solenoid
is turned “ON,” allowing the engine vacuum to draw a
small vacuum on the entire evaporative emission
system.
After the desired vacuum level has been achieved, the
EVAP purge solenoid is turned “OFF,” sealing the
system. A leak is detected by monitoring for a decrease
in vacuum level over a given time period, all other
variables remaining constant.
If the desired vacuum level cannot be achieved in the
test described above, a large leak or a faulty EVAP
purge control solenoid valve is indicated.
Leaks can be caused by the following conditions:
Missing or faulty fuel cap
Disconnected, damaged, pinched, or blocked EVAP
purge line
Disconnected, damaged, pinched, or blocked fuel
tank vapor line
Disconnected or faulty EVAP purge control solenoid
valve
Open ignition feed circuit to the purge solenoid (1) Purge Solenoid Valve
(2) From Canistor to Purge Solenoid
(3) From Purge Solenoid to Intake
(1) Canistor
(2) Air Separator
132
12
Page 2687 of 4264
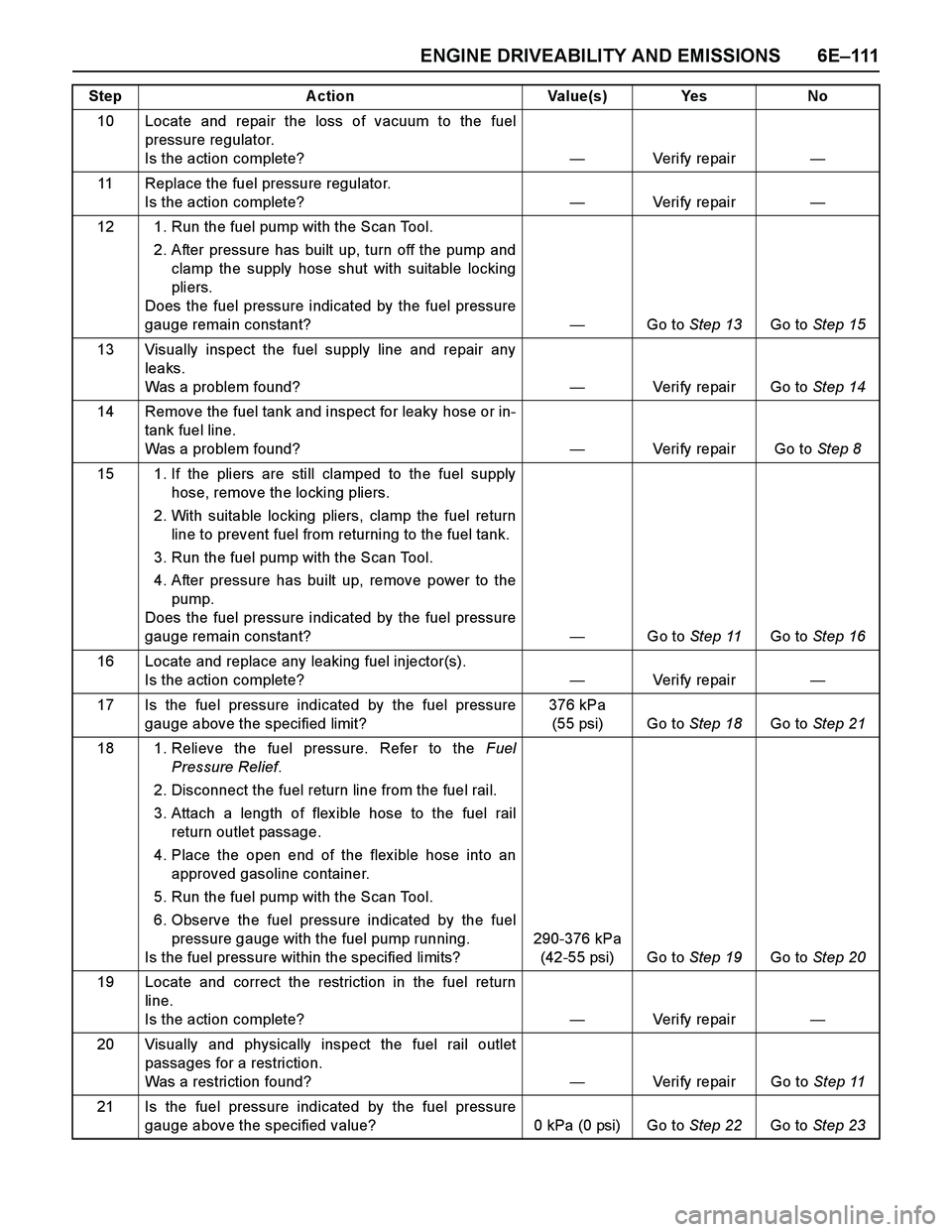
ENGINE DRIVEABILITY AND EMISSIONS 6E–111
10 Locate and repair the loss of vacuum to the fuel
pressure regulator.
Is the action complete?—Veri fy repai r—
11 Replace the fuel pressure regulator.
Is the action complete?—Veri fy repai r—
12 1. Run the fuel pump with the Scan Tool.
2. After pressure has built up, turn off the pump and
clamp the supply hose shut with suitable locking
pliers.
Does the fuel pressure indicated by the fuel pressure
gauge remain constant?—Go to Step 13Go to Step 15
13 Visually inspect the fuel supply line and repair any
leaks.
Was a problem found?—Verify repair Go to Step 14
14 Remove the fuel tank and inspect for leaky hose or in-
tank fuel line.
Was a problem found?—Verify repair Go to Step 8
15 1. If the pliers are still clamped to the fuel supply
hose, remove the locking pliers.
2. With suitable locking pliers, clamp the fuel return
line to prevent fuel from returning to the fuel tank.
3. Run the fuel pump with the Scan Tool.
4. After pressure has built up, remove power to the
pump.
Does the fuel pressure indicated by the fuel pressure
gauge remain constant?—Go to Step 11Go to Step 16
16 Locate and replace any leaking fuel injector(s).
Is the action complete?—Veri fy repai r—
17 Is the fuel pressure indicated by the fuel pressure
gauge above the specified limit?376 kPa
(55 psi) Go to Step 18Go to Step 21
18 1. Relieve the fuel pressure. Refer to the Fuel
Pressure Relief.
2. Disconnect the fuel return line from the fuel rail.
3. Attach a length of flex ible hose to the fuel rail
return outlet passage.
4. Place the open end of the flex ible hose into an
approved gasoline container.
5. Run the fuel pump with the Scan Tool.
6. Observe the fuel pressure indicated by the fuel
pressure gauge with the fuel pump running.
Is the fuel pressure within the specified limits?290-376 kPa
(42-55 psi) Go to Step 19Go to Step 20
19 Locate and correct the restriction in the fuel return
line.
Is the action complete?—Veri fy repai r—
20 Visually and physically inspect the fuel rail outlet
passages for a restriction.
Was a restriction found?—Verify repair Go to Step 11
21 Is the fuel pressure indicated by the fuel pressure
gauge above the specified value? 0 kPa (0 psi) Go to Step 22Go to Step 23 Step Action Value(s) Yes No
Page 2830 of 4264
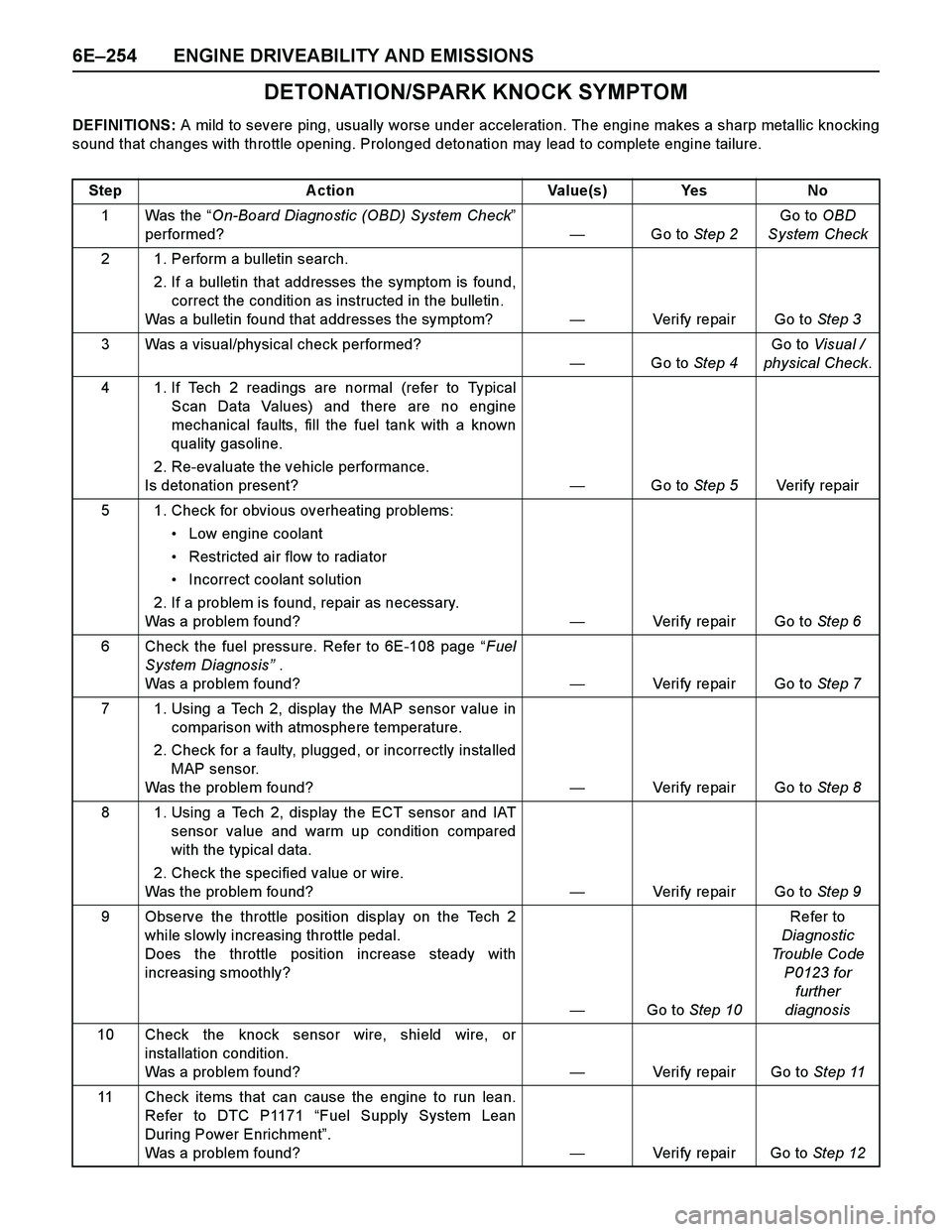
6E–254 ENGINE DRIVEABILITY AND EMISSIONS
DETONATION/SPARK KNOCK SYMPTOM
DEFINITIONS: A mild to severe ping, usually worse under acceleration. The engine makes a sharp metallic knocking
sound that changes with throttle opening. Prolonged detonation may lead to complete engine tailure.
Step Action Value(s) Yes No
1Was the “On-Board Diagnostic (OBD) System Check”
performed?—Go to Step 2Go to OBD
System Check
2 1. Perform a bulletin search.
2. If a bulletin that addresses the symptom is found,
correct the condition as instructed in the bulletin.
Was a bulletin found that addresses the symptom?—Verify repair Go to Step 3
3 Was a visual/physical check performed?
—Go to Step 4Go to Visual /
physical Check.
4 1. If Tech 2 readings are normal (refer to Typical
Scan Data Values) and there are no engine
mechanical faults, fill the fuel tank with a known
quality gasoline.
2. Re-evaluate the vehicle performance.
Is detonation present?—Go to Step 5Verify repair
5 1. Check for obvious overheating problems:
Low engine coolant
Restricted air flow to radiator
Incorrect coolant solution
2. If a problem is found, repair as necessary.
Was a problem found?—Verify repair Go to Step 6
6 Check the fuel pressure. Refer to 6E-108 page “Fuel
System Diagnosis” .
Was a problem found?—Verify repair Go to Step 7
7 1. Using a Tech 2, display the MAP sensor value in
comparison with atmosphere temperature.
2. Check for a faulty, plugged, or incorrectly installed
MAP sensor.
Was the problem found?—Verify repair Go to Step 8
8 1. Using a Tech 2, display the ECT sensor and IAT
sensor value and warm up condition compared
with the typical data.
2. Check the specified value or wire.
Was the problem found?—Verify repair Go to Step 9
9 Observe the throttle position display on the Tech 2
while slowly increasing throttle pedal.
Does the throttle position increase steady with
increasing smoothly?
—Go to Step 10Refer to
Diagnostic
Trouble Code
P0123 for
further
diagnosis
10 Check the knock sensor wire, shield wire, or
installation condition.
Was a problem found?—Verify repair Go to Step 11
11 Check items that can cause the engine to run lean.
Refer to DTC P1171 “Fuel Supply System Lean
During Power Enrichment”.
Was a problem found?—Verify repair Go to Step 12