sensor ISUZU TROOPER 1998 Service Repair Manual
[x] Cancel search | Manufacturer: ISUZU, Model Year: 1998, Model line: TROOPER, Model: ISUZU TROOPER 1998Pages: 3573, PDF Size: 60.36 MB
Page 1681 of 3573
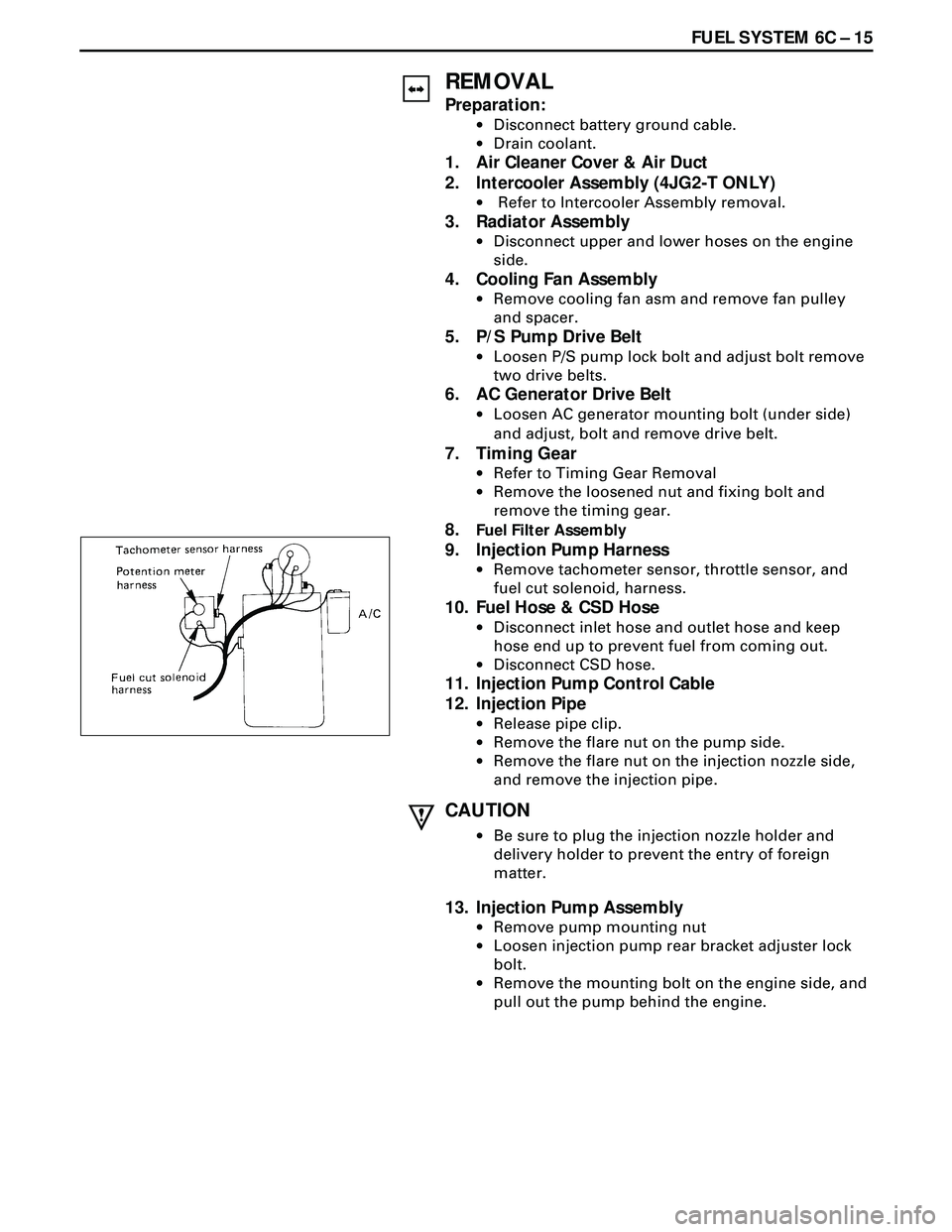
FUEL SYSTEM 6C Ð 15
REMOVAL
Preparation:
·Disconnect battery ground cable.
·Drain coolant.
1. Air Cleaner Cover & Air Duct
2. Intercooler Assembly (4JG2-T ONLY)
· Refer to Intercooler Assembly removal.
3. Radiator Assembly
·Disconnect upper and lower hoses on the engine
side.
4. Cooling Fan Assembly
·Remove cooling fan asm and remove fan pulley
and spacer.
5. P/S Pump Drive Belt
·Loosen P/S pump lock bolt and adjust bolt remove
two drive belts.
6. AC Generator Drive Belt
·Loosen AC generator mounting bolt (under side)
and adjust, bolt and remove drive belt.
7. Timing Gear
·Refer to Timing Gear Removal
·Remove the loosened nut and fixing bolt and
remove the timing gear.
8.Fuel Filter Assembly
9. Injection Pump Harness
·Remove tachometer sensor, throttle sensor, and
fuel cut solenoid, harness.
10. Fuel Hose & CSD Hose
·Disconnect inlet hose and outlet hose and keep
hose end up to prevent fuel from coming out.
·Disconnect CSD hose.
11. Injection Pump Control Cable
12. Injection Pipe
·Release pipe clip.
·Remove the flare nut on the pump side.
·Remove the flare nut on the injection nozzle side,
and remove the injection pipe.
CAUTION
·Be sure to plug the injection nozzle holder and
delivery holder to prevent the entry of foreign
matter.
13. Injection Pump Assembly
·Remove pump mounting nut
·Loosen injection pump rear bracket adjuster lock
bolt.
·Remove the mounting bolt on the engine side, and
pull out the pump behind the engine.
Page 1719 of 3573
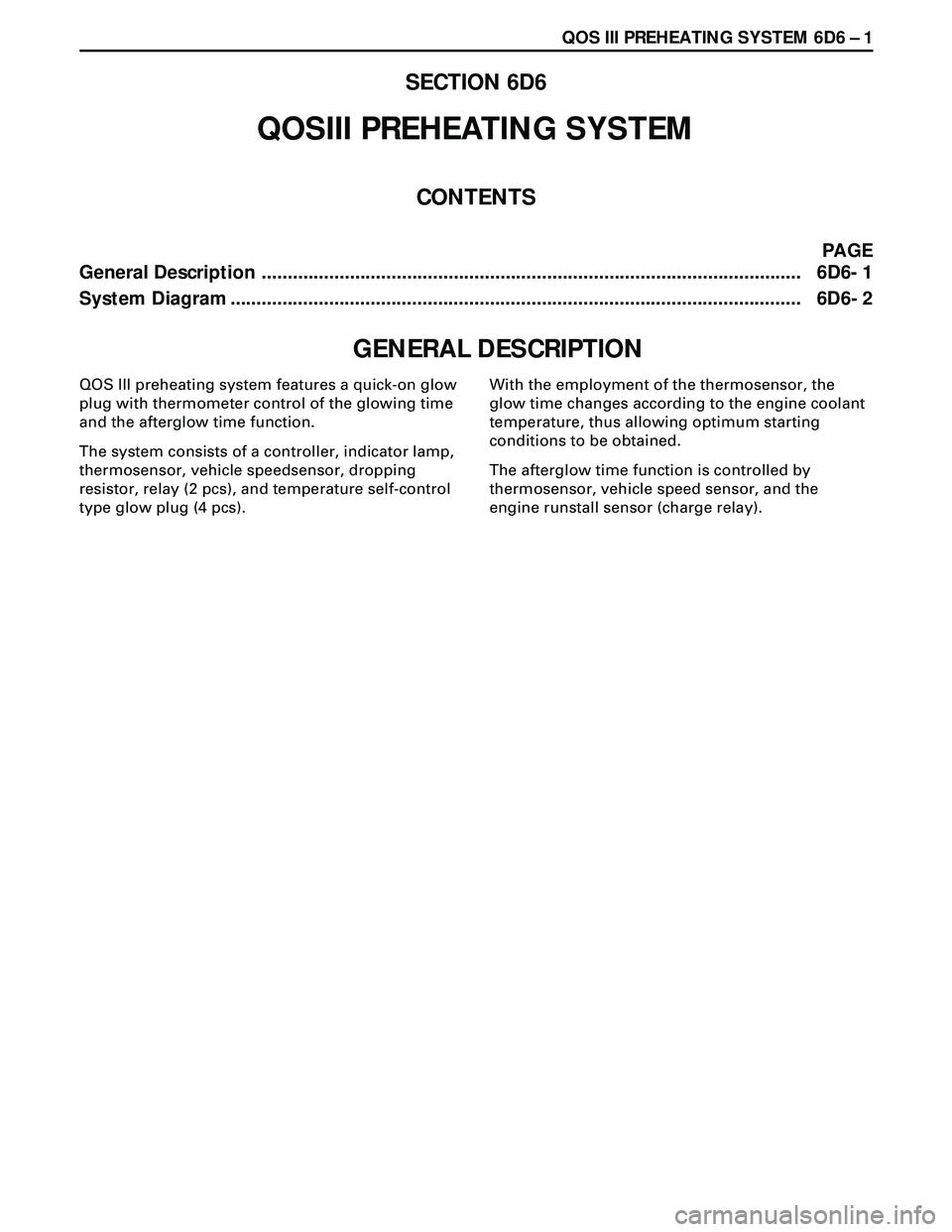
QOS III PREHEATING SYSTEM 6D6 Ð 1
PAGE
General Description ........................................................................................................ 6D6- 1
System Diagram .............................................................................................................. 6D6- 2
GENERAL DESCRIPTION
QOS III preheating system features a quick-on glow
plug with thermometer control of the glowing time
and the afterglow time function.
The system consists of a controller, indicator lamp,
thermosensor, vehicle speedsensor, dropping
resistor, relay (2 pcs), and temperature self-control
type glow plug (4 pcs).With the employment of the thermosensor, the
glow time changes according to the engine coolant
temperature, thus allowing optimum starting
conditions to be obtained.
The afterglow time function is controlled by
thermosensor, vehicle speed sensor, and the
engine runstall sensor (charge relay).
SECTION 6D6
QOSIII PREHEATING SYSTEM
CONTENTS
Page 1720 of 3573
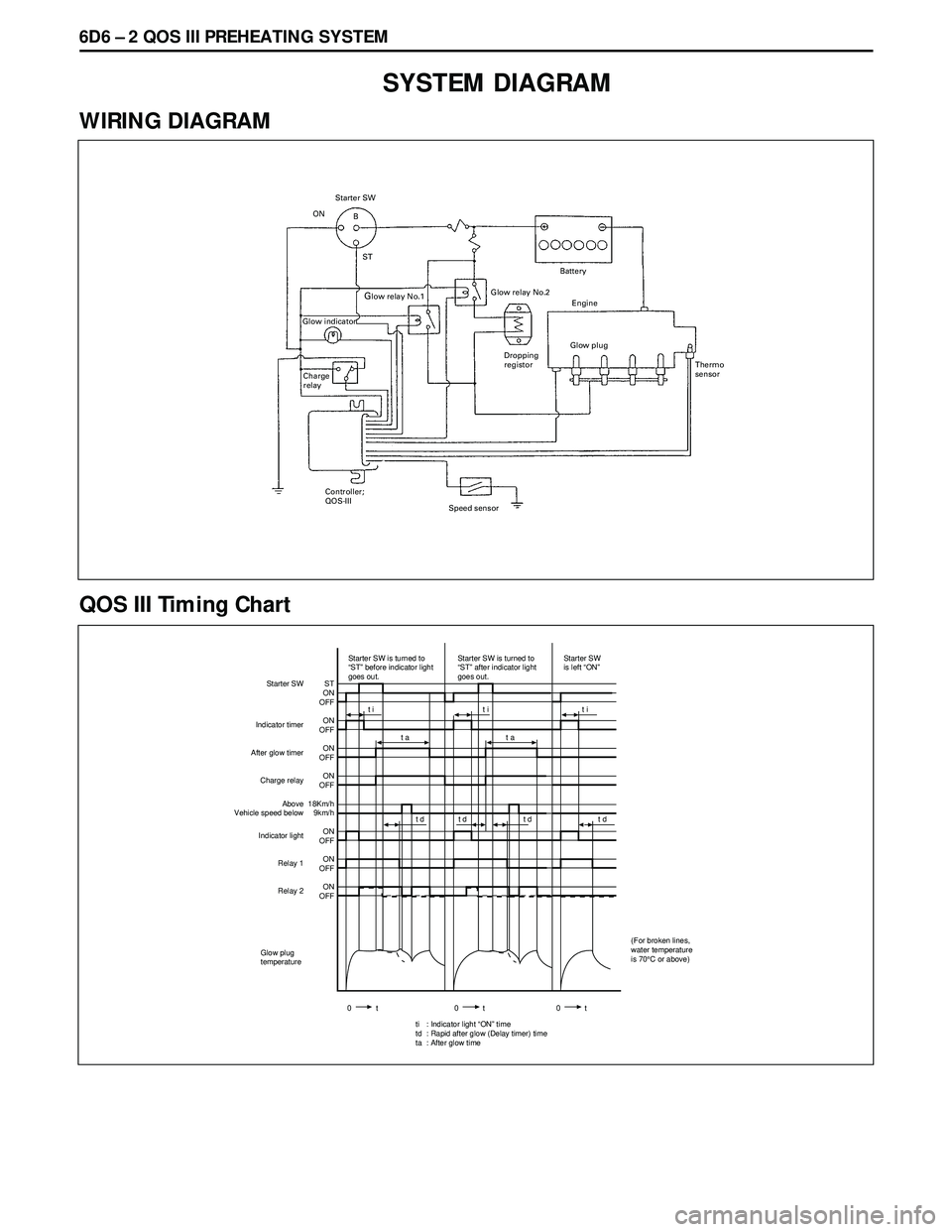
6D6 Ð 2 QOS III PREHEATING SYSTEM
SYSTEM DIAGRAM
WIRING DIAGRAM
ON
B
ST
Glow relay No.1 Starter SW
Battery
Engine Glow relay No.2
Glow indicator
Charge
relayGlow plug
Thermo
sensor
Controller;
QOS-III
Speed sensorDropping
registor
QOS III Timing Chart
ST
ON
OFF
ON
OFF
ON
OFF
ON
OFF
18Km/h
9km/h
ON
OFF
ON
OFF
ON
OFF Starter SW
Starter SW is turned to
“ST” before indicator light
goes out.Starter SW is turned to
“ST” after indicator light
goes out.Starter SW
is left “ON”
Indicator timer
After glow timer
Charge relay
Indicator light
Relay 1
Relay 2Above
Vehicle speed below
t i t i t i
t a t a
t d t d t d t d
Glow plug
temperature
0t 0t 0t
: Indicator light “ON” time
: Rapid after glow (Delay timer) time
: After glow time
ti
td
ta
(For broken lines,
water temperature
is 70¡C or above)
Page 1722 of 3573
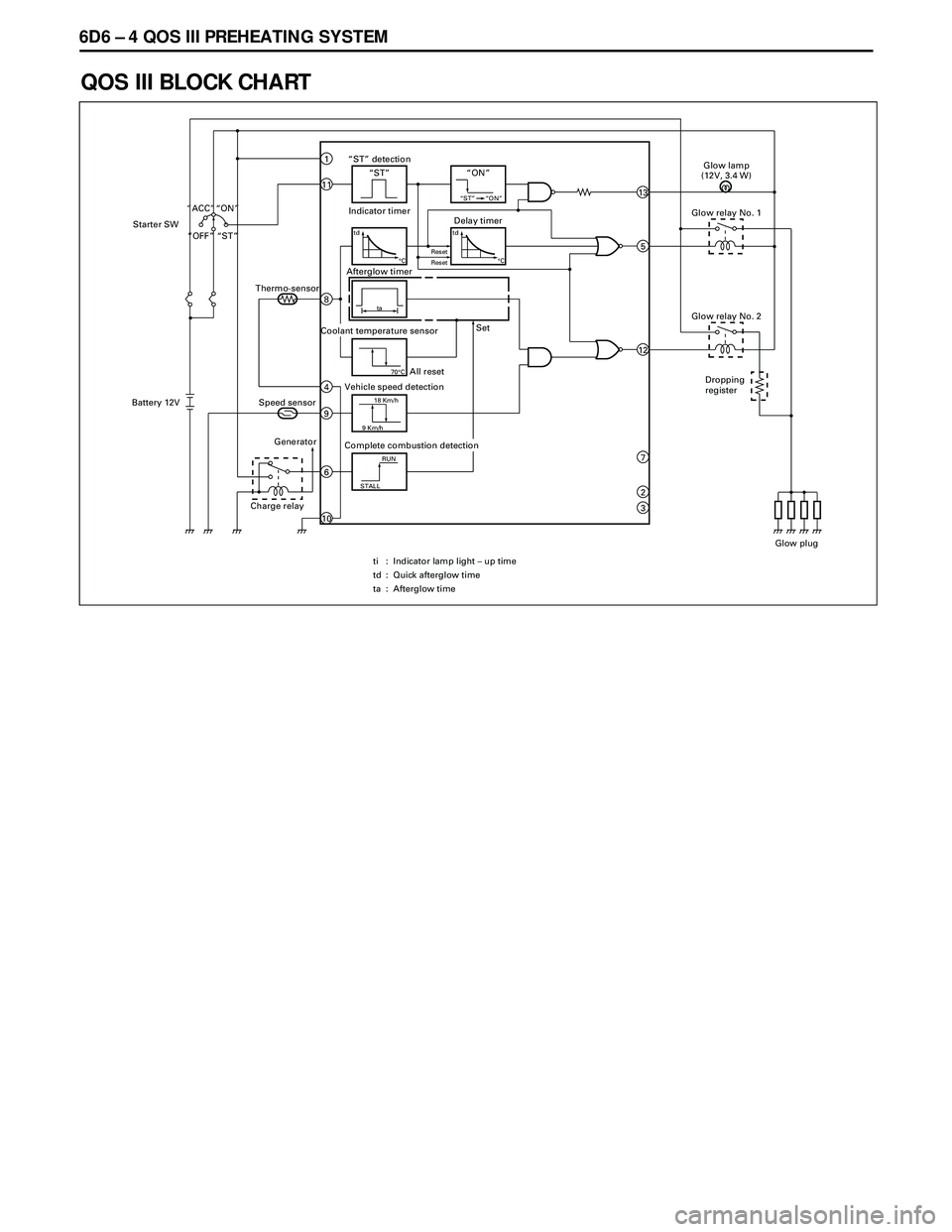
6D6 Ð 4 QOS III PREHEATING SYSTEM
QOS III BLOCK CHART
“ST” detection“ST”
Indicator timer
11
1“ON”
“ST” “ON”13
tdDelay timer
¡C
td
¡CResetReset5
ta
Afterglow timer
Coolant temperature sensor
70¡CAll reset
12
Vehicle speed detection
9 Km/h18 Km/h
Complete combustion detection
STALLRUN
Set 8
4
9
6
10
Thermo-sensor
Speed sensor
Generator
Charge relay
Glow relay No. 1
Glow lamp
(12V, 3.4 W)
Glow relay No. 2
Glow plug
Battery 12VStarter SW
“OFF” “ST” “ACC” “ON”
: Indicator lamp light – up time
: Quick afterglow time
: Afterglow time ti
td
ta7
2
3
Dropping
register
Page 1723 of 3573
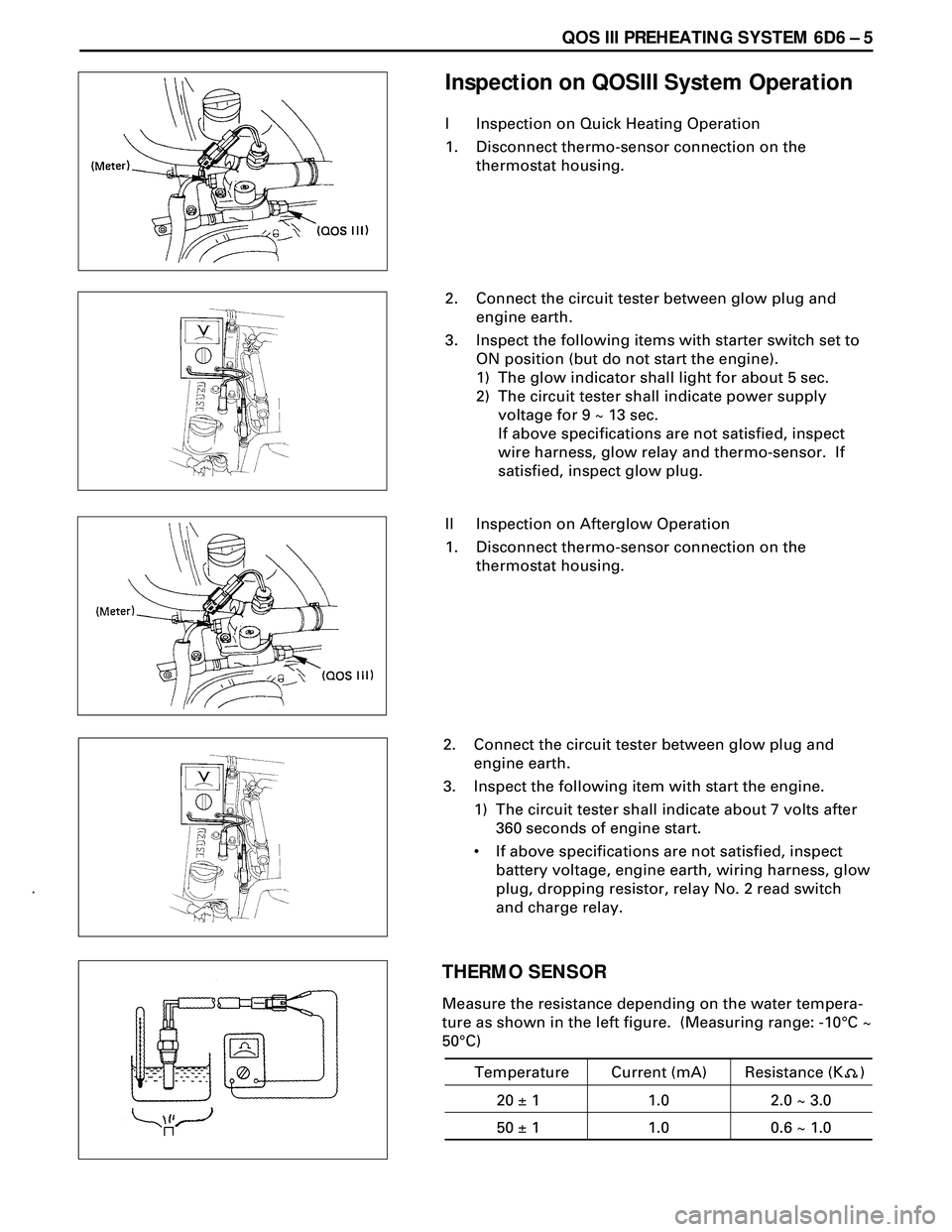
QOS III PREHEATING SYSTEM 6D6 Ð 5
Inspection on QOSIII System Operation
I Inspection on Quick Heating Operation
1. Disconnect thermo-sensor connection on the
thermostat housing.
2. Connect the circuit tester between glow plug and
engine earth.
3. Inspect the following items with starter switch set to
ON position (but do not start the engine).
1) The glow indicator shall light for about 5 sec.
2) The circuit tester shall indicate power supply
voltage for 9 ~ 13 sec.
If above specifications are not satisfied, inspect
wire harness, glow relay and thermo-sensor. If
satisfied, inspect glow plug.
II Inspection on Afterglow Operation
1. Disconnect thermo-sensor connection on the
thermostat housing.
2. Connect the circuit tester between glow plug and
engine earth.
3. Inspect the following item with start the engine.
1) The circuit tester shall indicate about 7 volts after
360 seconds of engine start.
¥ If above specifications are not satisfied, inspect
battery voltage, engine earth, wiring harness, glow
plug, dropping resistor, relay No. 2 read switch
and charge relay.
THERMO SENSOR
Measure the resistance depending on the water tempera-
ture as shown in the left figure. (Measuring range: -10¡C ~
50¡C)
Current (mA)
20 ± 1 1.0
50 ± 1Resistance (K )
1.0
2.0 ~ 3.0
0.6 ~ 1.0 Temperature
Page 1724 of 3573
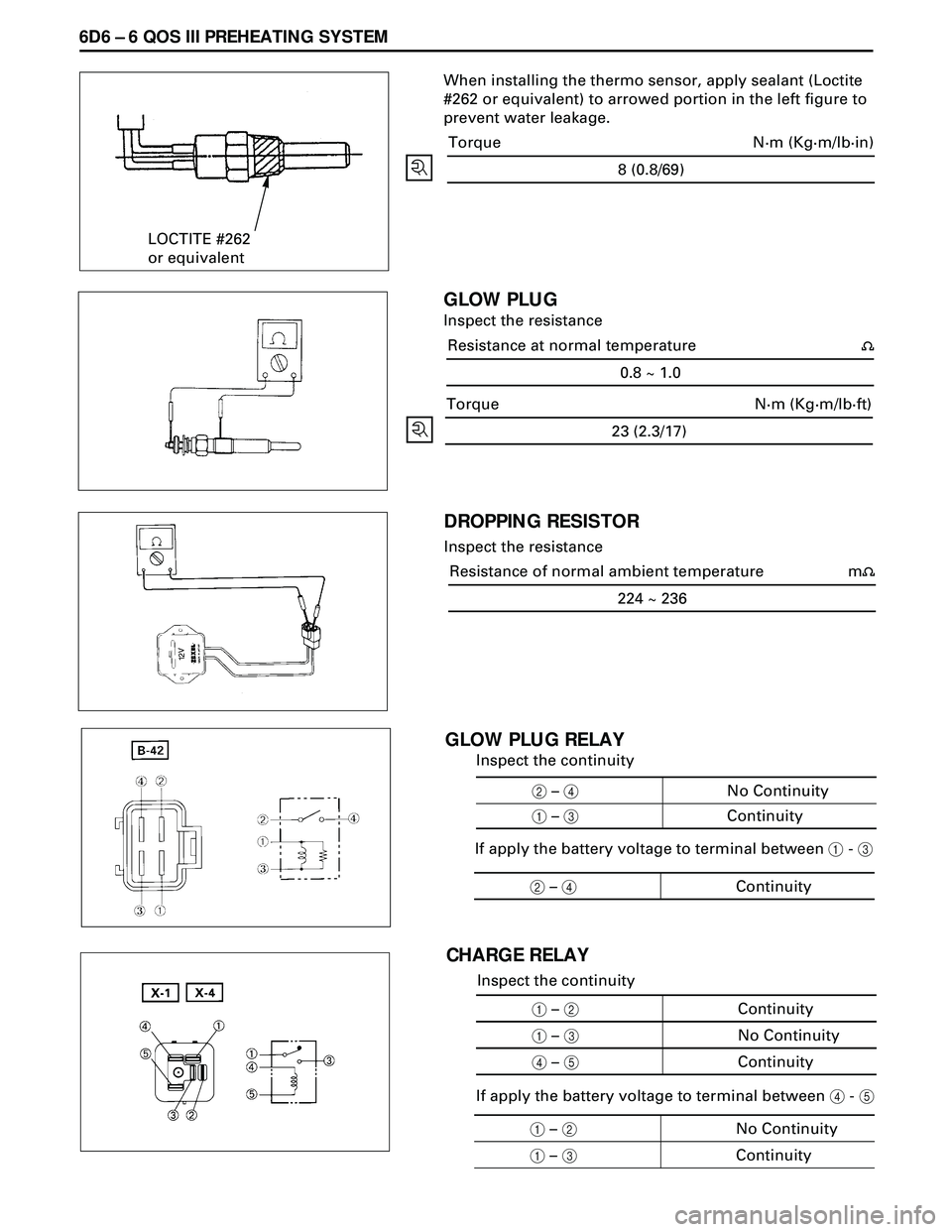
6D6 Ð 6 QOS III PREHEATING SYSTEM
8 (0.8/69)
Torque N·m (Kg·m/lb·in)
23 (2.3/17)
Torque N·m (Kg·m/lb·ft)
0.8 ~ 1.0
Resistance at normal temperature
LOCTITE #262
or equivalentWhen installing the thermo sensor, apply sealant (Loctite
#262 or equivalent) to arrowed portion in the left figure to
prevent water leakage.
GLOW PLUG
Inspect the resistance
No Continuity 2 –4
Continuity 1 –3
Continuity 2 –4
Continuity 1 –2
No Continuity 1 –3
Continuity 4 –5
No Continuity 1 –2
Continuity 1 –3
224 ~ 236
Resistance of normal ambient temperature m
DROPPING RESISTOR
Inspect the resistance
GLOW PLUG RELAY
Inspect the continuity
If apply the battery voltage to terminal between 1 - 3
CHARGE RELAY
Inspect the continuity
If apply the battery voltage to terminal between 4 - 5
Page 1746 of 3573
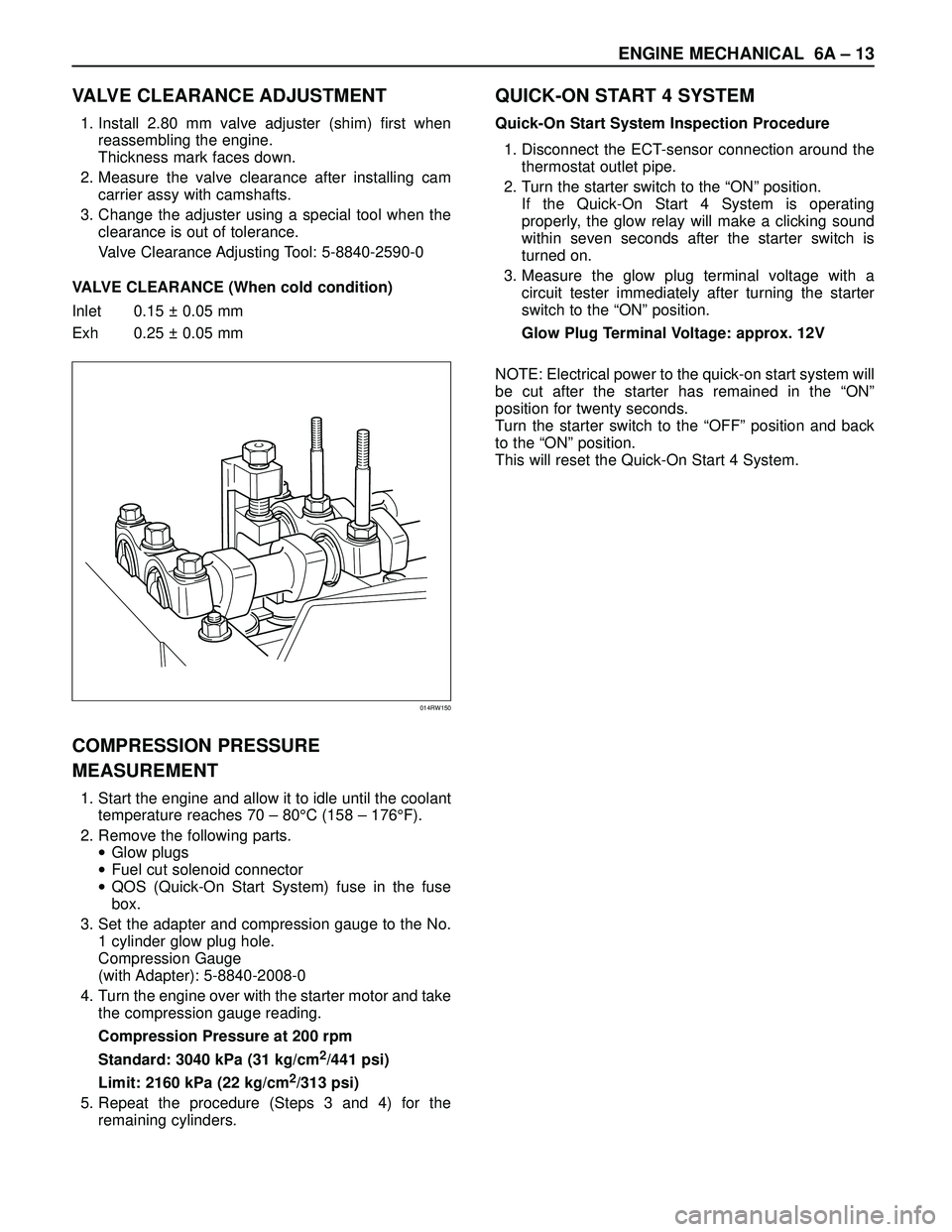
ENGINE MECHANICAL 6A – 13
VALVE CLEARANCE ADJUSTMENT
1. Install 2.80 mm valve adjuster (shim) first when
reassembling the engine.
Thickness mark faces down.
2. Measure the valve clearance after installing cam
carrier assy with camshafts.
3. Change the adjuster using a special tool when the
clearance is out of tolerance.
Valve Clearance Adjusting Tool: 5-8840-2590-0
VALVE CLEARANCE (When cold condition)
Inlet 0.15 ± 0.05 mm
Exh 0.25 ± 0.05 mm
COMPRESSION PRESSURE
MEASUREMENT
1. Start the engine and allow it to idle until the coolant
temperature reaches 70 – 80°C (158 – 176°F).
2. Remove the following parts.
•Glow plugs
•Fuel cut solenoid connector
•QOS (Quick-On Start System) fuse in the fuse
box.
3. Set the adapter and compression gauge to the No.
1 cylinder glow plug hole.
Compression Gauge
(with Adapter): 5-8840-2008-0
4. Turn the engine over with the starter motor and take
the compression gauge reading.
Compression Pressure at 200 rpm
Standard: 3040 kPa (31 kg/cm
2/441 psi)
Limit: 2160 kPa (22 kg/cm
2/313 psi)
5. Repeat the procedure (Steps 3 and 4) for the
remaining cylinders.
QUICK-ON START 4 SYSTEM
Quick-On Start System Inspection Procedure
1. Disconnect the ECT-sensor connection around the
thermostat outlet pipe.
2. Turn the starter switch to the “ON” position.
If the Quick-On Start 4 System is operating
properly, the glow relay will make a clicking sound
within seven seconds after the starter switch is
turned on.
3. Measure the glow plug terminal voltage with a
circuit tester immediately after turning the starter
switch to the “ON” position.
Glow Plug Terminal Voltage: approx. 12V
NOTE: Electrical power to the quick-on start system will
be cut after the starter has remained in the “ON”
position for twenty seconds.
Turn the starter switch to the “OFF” position and back
to the “ON” position.
This will reset the Quick-On Start 4 System.
014RW150
Page 1768 of 3573
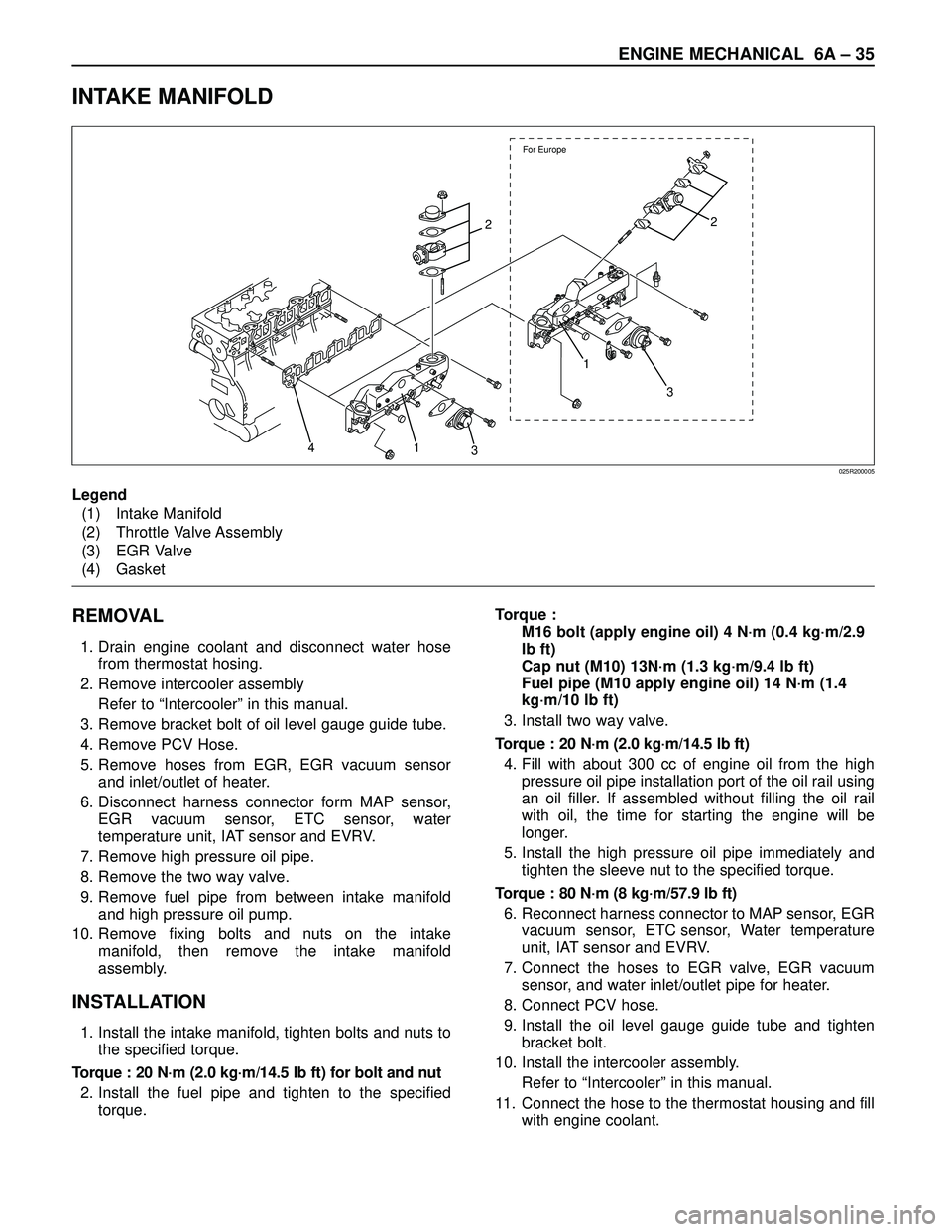
ENGINE MECHANICAL 6A – 35
INTAKE MANIFOLD
REMOVAL
1. Drain engine coolant and disconnect water hose
from thermostat hosing.
2. Remove intercooler assembly
Refer to “Intercooler” in this manual.
3. Remove bracket bolt of oil level gauge guide tube.
4. Remove PCV Hose.
5. Remove hoses from EGR, EGR vacuum sensor
and inlet/outlet of heater.
6. Disconnect harness connector form MAP sensor,
EGR vacuum sensor, ETC sensor, water
temperature unit, IAT sensor and EVRV.
7. Remove high pressure oil pipe.
8. Remove the two way valve.
9. Remove fuel pipe from between intake manifold
and high pressure oil pump.
10. Remove fixing bolts and nuts on the intake
manifold, then remove the intake manifold
assembly.
INSTALLATION
1. Install the intake manifold, tighten bolts and nuts to
the specified torque.
Torque : 20 N·m (2.0 kg·m/14.5 lb ft) for bolt and nut
2. Install the fuel pipe and tighten to the specified
torque.Torque :
M16 bolt (apply engine oil) 4 N·m (0.4 kg·m/2.9
lb ft)
Cap nut (M10) 13N·m (1.3 kg·m/9.4 lb ft)
Fuel pipe (M10 apply engine oil) 14 N·m (1.4
kg·m/10 lb ft)
3. Install two way valve.
Torque : 20 N·m (2.0 kg·m/14.5 lb ft)
4. Fill with about 300 cc of engine oil from the high
pressure oil pipe installation port of the oil rail using
an oil filler. If assembled without filling the oil rail
with oil, the time for starting the engine will be
longer.
5. Install the high pressure oil pipe immediately and
tighten the sleeve nut to the specified torque.
Torque : 80 N·m (8 kg·m/57.9 lb ft)
6. Reconnect harness connector to MAP sensor, EGR
vacuum sensor, ETC sensor, Water temperature
unit, IAT sensor and EVRV.
7. Connect the hoses to EGR valve, EGR vacuum
sensor, and water inlet/outlet pipe for heater.
8. Connect PCV hose.
9. Install the oil level gauge guide tube and tighten
bracket bolt.
10. Install the intercooler assembly.
Refer to “Intercooler” in this manual.
11. Connect the hose to the thermostat housing and fill
with engine coolant.
For Europe
2
1
3
3 1 42
025R200005
Legend
(1) Intake Manifold
(2) Throttle Valve Assembly
(3) EGR Valve
(4) Gasket
Page 1777 of 3573
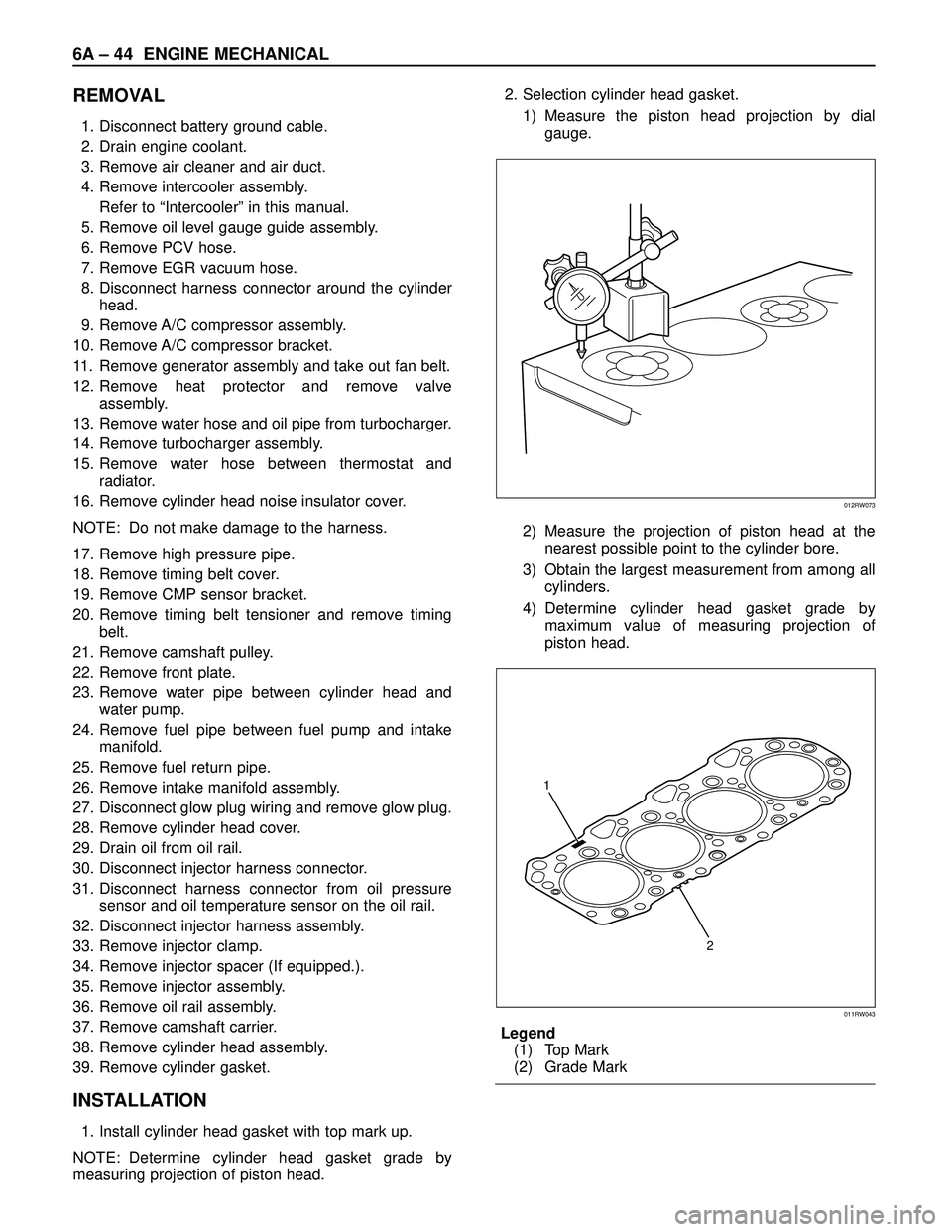
6A – 44 ENGINE MECHANICAL
REMOVAL
1. Disconnect battery ground cable.
2. Drain engine coolant.
3. Remove air cleaner and air duct.
4. Remove intercooler assembly.
Refer to “Intercooler” in this manual.
5. Remove oil level gauge guide assembly.
6. Remove PCV hose.
7. Remove EGR vacuum hose.
8. Disconnect harness connector around the cylinder
head.
9. Remove A/C compressor assembly.
10. Remove A/C compressor bracket.
11. Remove generator assembly and take out fan belt.
12. Remove heat protector and remove valve
assembly.
13. Remove water hose and oil pipe from turbocharger.
14. Remove turbocharger assembly.
15. Remove water hose between thermostat and
radiator.
16. Remove cylinder head noise insulator cover.
NOTE: Do not make damage to the harness.
17. Remove high pressure pipe.
18. Remove timing belt cover.
19. Remove CMP sensor bracket.
20. Remove timing belt tensioner and remove timing
belt.
21. Remove camshaft pulley.
22. Remove front plate.
23. Remove water pipe between cylinder head and
water pump.
24. Remove fuel pipe between fuel pump and intake
manifold.
25. Remove fuel return pipe.
26. Remove intake manifold assembly.
27. Disconnect glow plug wiring and remove glow plug.
28. Remove cylinder head cover.
29. Drain oil from oil rail.
30. Disconnect injector harness connector.
31. Disconnect harness connector from oil pressure
sensor and oil temperature sensor on the oil rail.
32. Disconnect injector harness assembly.
33. Remove injector clamp.
34. Remove injector spacer (If equipped.).
35. Remove injector assembly.
36. Remove oil rail assembly.
37. Remove camshaft carrier.
38. Remove cylinder head assembly.
39. Remove cylinder gasket.
INSTALLATION
1. Install cylinder head gasket with top mark up.
NOTE: Determine cylinder head gasket grade by
measuring projection of piston head.2. Selection cylinder head gasket.
1) Measure the piston head projection by dial
gauge.
2) Measure the projection of piston head at the
nearest possible point to the cylinder bore.
3) Obtain the largest measurement from among all
cylinders.
4) Determine cylinder head gasket grade by
maximum value of measuring projection of
piston head.
Legend
(1) Top Mark
(2) Grade Mark
012RW073
2 1
011RW043
Page 1778 of 3573
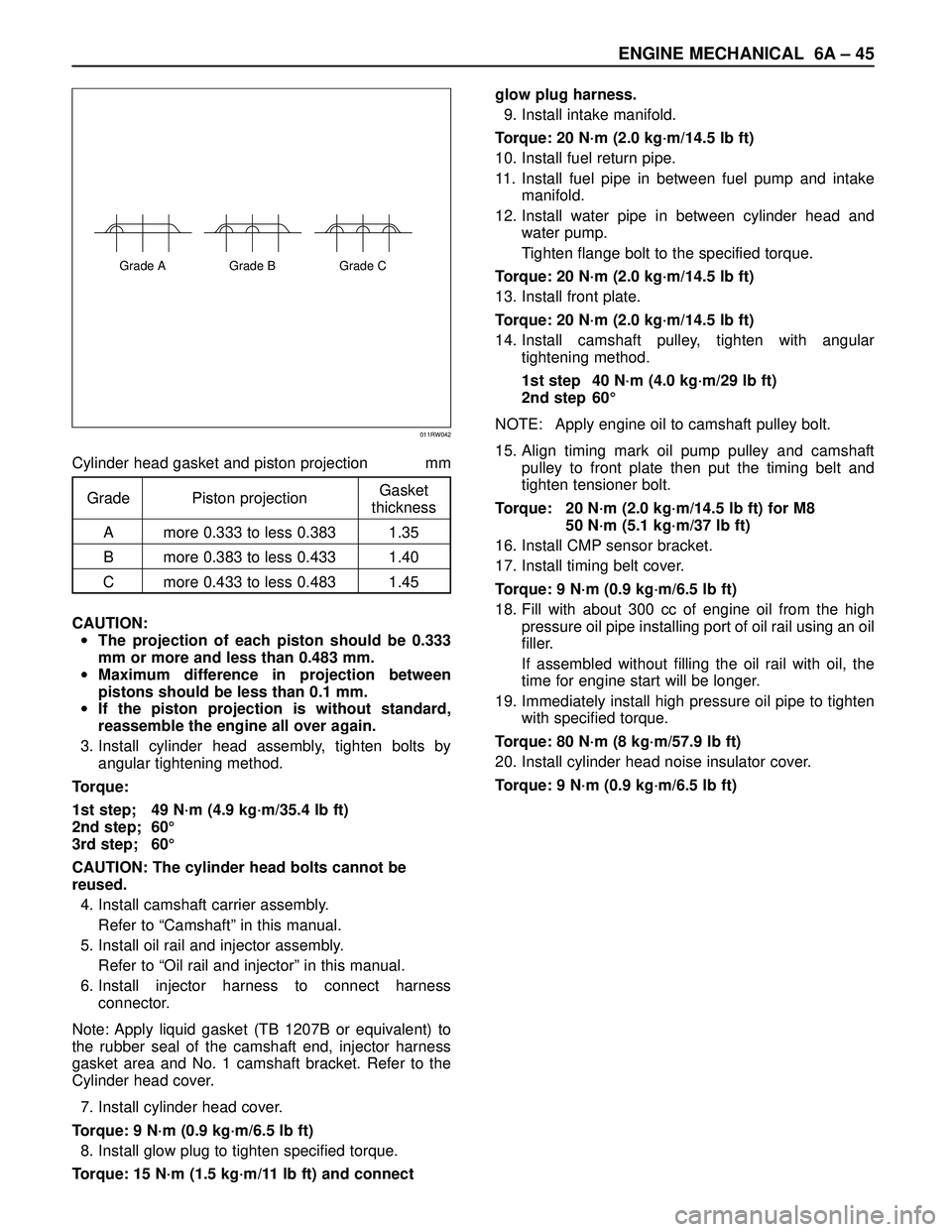
ENGINE MECHANICAL 6A – 45
Cylinder head gasket and piston projection mm
CAUTION:
•The projection of each piston should be 0.333
mm or more and less than 0.483 mm.
•Maximum difference in projection between
pistons should be less than 0.1 mm.
•If the piston projection is without standard,
reassemble the engine all over again.
3. Install cylinder head assembly, tighten bolts by
angular tightening method.
Torque:
1st step; 49 N·m (4.9 kg·m/35.4 lb ft)
2nd step; 60°
3rd step; 60°
CAUTION: The cylinder head bolts cannot be
reused.
4. Install camshaft carrier assembly.
Refer to “Camshaft” in this manual.
5. Install oil rail and injector assembly.
Refer to “Oil rail and injector” in this manual.
6. Install injector harness to connect harness
connector.
Note: Apply liquid gasket (TB 1207B or equivalent) to
the rubber seal of the camshaft end, injector harness
gasket area and No. 1 camshaft bracket. Refer to the
Cylinder head cover.
7. Install cylinder head cover.
Torque: 9 N·m (0.9 kg·m/6.5 lb ft)
8. Install glow plug to tighten specified torque.
Torque: 15 N·m (1.5 kg·m/11 lb ft) and connectglow plug harness.
9. Install intake manifold.
Torque: 20 N·m (2.0 kg·m/14.5 lb ft)
10. Install fuel return pipe.
11. Install fuel pipe in between fuel pump and intake
manifold.
12. Install water pipe in between cylinder head and
water pump.
Tighten flange bolt to the specified torque.
Torque: 20 N·m (2.0 kg·m/14.5 lb ft)
13. Install front plate.
Torque: 20 N·m (2.0 kg·m/14.5 lb ft)
14. Install camshaft pulley, tighten with angular
tightening method.
1st step 40 N·m (4.0 kg·m/29 lb ft)
2nd step 60°
NOTE: Apply engine oil to camshaft pulley bolt.
15. Align timing mark oil pump pulley and camshaft
pulley to front plate then put the timing belt and
tighten tensioner bolt.
Torque: 20 N·m (2.0 kg·m/14.5 lb ft) for M8
50 N·m (5.1 kg·m/37 lb ft)
16. Install CMP sensor bracket.
17. Install timing belt cover.
Torque: 9 N·m (0.9 kg·m/6.5 lb ft)
18. Fill with about 300 cc of engine oil from the high
pressure oil pipe installing port of oil rail using an oil
filler.
If assembled without filling the oil rail with oil, the
time for engine start will be longer.
19. Immediately install high pressure oil pipe to tighten
with specified torque.
Torque: 80 N·m (8 kg·m/57.9 lb ft)
20. Install cylinder head noise insulator cover.
Torque: 9 N·m (0.9 kg·m/6.5 lb ft)
Grade A Grade B Grade C
011RW042
Grade Piston projectionGasket
thickness
A more 0.333 to less 0.383 1.35
B more 0.383 to less 0.433 1.40
C more 0.433 to less 0.483 1.45