check engine JAGUAR XJ 1994 2.G AJ16 Engine Manual
[x] Cancel search | Manufacturer: JAGUAR, Model Year: 1994, Model line: XJ, Model: JAGUAR XJ 1994 2.GPages: 73, PDF Size: 2.06 MB
Page 35 of 73
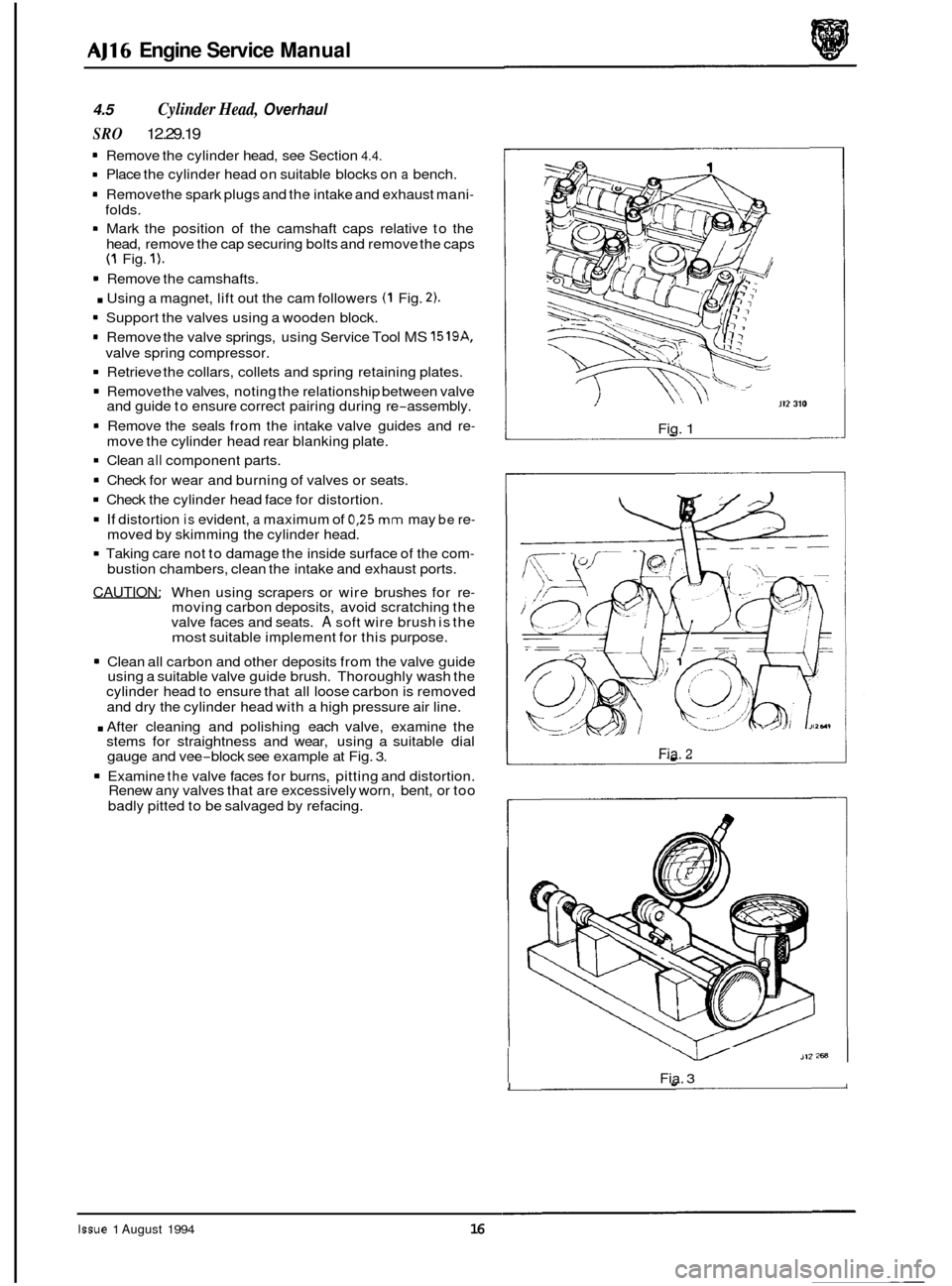
AJ16 Engine Service Manual
4.5 Cylinder Head, Overhaul
SRO 12.29.19
1 Remove the cylinder head, see Section 4.4.
1 Place the cylinder head on suitable blocks on a bench.
1 Remove the spark plugs and the intake and exhaust mani-
folds.
1 Mark the position of the camshaft caps relative to the
head, remove the cap securing bolts and remove the caps
(1 Fig. 1).
1 Remove the camshafts.
. Using a magnet, lift out the cam followers (1 Fig. 2).
1 Remove the valve springs, using Service Tool MS 1519A,
1 Retrieve the collars, collets and spring retaining plates.
1 Remove the valves, noting the relationship between valve
and guide to ensure correct pairing during re-assembly.
* Remove the seals from the intake valve guides and re- move the cylinder head rear blanking plate.
1 Clean all component parts.
1 Check for wear and burning of valves or seats.
1 Check the cylinder head face for distortion.
1 If distortion is evident, a maximum of 0,25 mm may be re- moved by skimming the cylinder head.
1 Taking care not to damage the inside surface of the com-
bustion chambers, clean the intake and exhaust ports.
CAUTION: When using scrapers or wire brushes for re- moving carbon deposits, avoid scratching the
valve faces and seats. A soft wire brush is the most suitable implement for this purpose.
1 Clean all carbon and other deposits from the valve guide
using a suitable valve guide brush. Thoroughly wash the
cylinder head to ensure that all loose carbon is removed
and dry the cylinder head with a high pressure air line.
. After cleaning and polishing each valve, examine the
stems for straightness and wear, using a suitable dial
gauge and vee
-block see example at Fig. 3.
1 Examine the valve faces for burns, pitting and distortion.
Renew any valves that are excessively worn, bent, or too
badly pitted to be salvaged by refacing.
Support the
valves using a wooden block.
valve spring compressor.
/ 112 310
Fig. 1
Fia. 2
I
JlZ 268
Fia. 3 I " 1
Issue 1 August 1994 16
Page 36 of 73
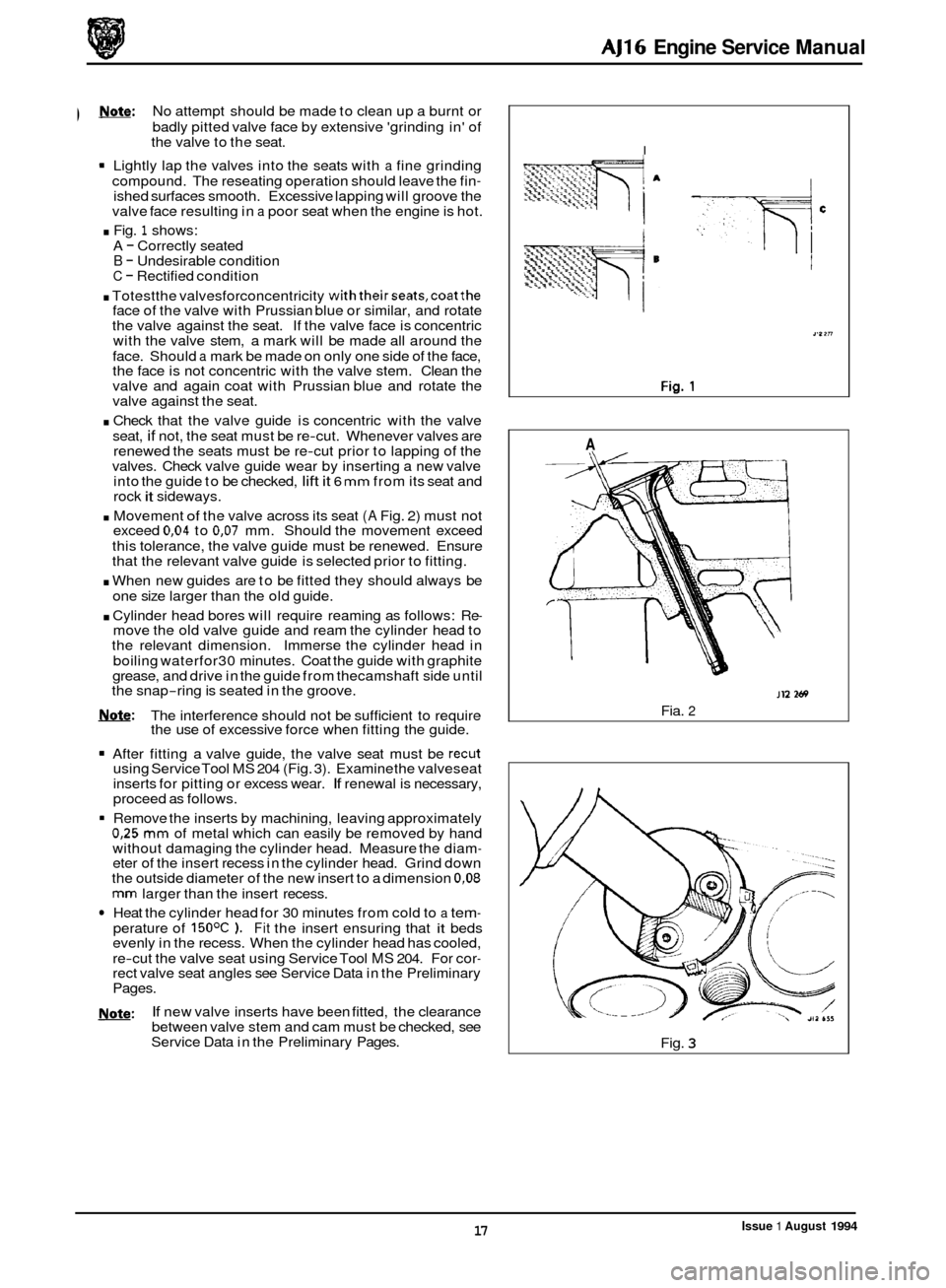
AJ16 Engine Service Manual
Note: No attempt should be made to clean up a burnt or
badly pitted valve face by extensive 'grinding in' of
the valve to the seat.
m Lightly lap the valves into the seats with a fine grinding
compound. The reseating operation should leave the fin- ished surfaces smooth. Excessive lapping will groove the
valve face resulting in a poor seat when the engine is hot.
A
- Correctly seated B - Undesirable condition C - Rectified condition
. Totestthe valvesforconcentricity withtheirseats,coatthe face of the valve with Prussian blue or similar, and rotate
the valve against the seat. If the valve face is concentric
with the valve stem, a mark will be made all around the
face. Should
a mark be made on only one side of the face,
the face is not concentric with the valve stem. Clean the
valve and again coat with Prussian blue and rotate the
valve against the seat.
. Check that the valve guide is concentric with the valve
seat,
if not, the seat must be re-cut. Whenever valves are
renewed the seats must be re-cut prior to lapping of the
valves. Check valve guide wear by inserting a new valve
into the guide to be checked,
lift it 6 mm from its seat and
rock it sideways.
. Movement of the valve across its seat (A Fig. 2) must not
exceed 0,04 to 0,07 mm. Should the movement exceed
this tolerance, the valve guide must be renewed. Ensure
that the relevant valve guide is selected prior to fitting.
. When new guides are to be fitted they should always be
one size larger than the old guide.
. Cylinder head bores will require reaming as follows: Re- move the old valve guide and ream the cylinder head to
the relevant dimension. Immerse the cylinder head in
boiling waterfor30 minutes. Coat the guide with graphite
grease, and drive in the guide from thecamshaft side until
the snap
-ring is seated in the groove.
b: The interference should not be sufficient to require
the use of excessive force when fitting the guide.
1 After fitting a valve guide, the valve seat must be recut using Service Tool MS 204 (Fig. 3). Examine the valveseat
inserts for pitting or excess wear. If renewal is necessary,
proceed as follows.
1 Remove the inserts by machining, leaving approximately 0,25 mm of metal which can easily be removed by hand
without damaging the cylinder head. Measure the diam- eter of the insert recess in the cylinder head. Grind down
the outside diameter of the new insert to a dimension 0,08
mm larger than the insert recess.
Heat the cylinder head for 30 minutes from cold to a tem- perature of 15OOC 1, Fit the insert ensuring that it beds
evenly in the recess. When the cylinder head has cooled,
re
-cut the valve seat using Service Tool MS 204. For cor- rect valve seat angles see Service Data in the Preliminary
Pages.
If new valve inserts have been fitted, the clearance
between valve stem and cam must be checked, see
Service Data in the Preliminary Pages.
. Fig. 1 shows:
U:
I
A
JIZ 2M
Fia. 2
Fig. 3
Issue 1 August 1994 17
Page 37 of 73
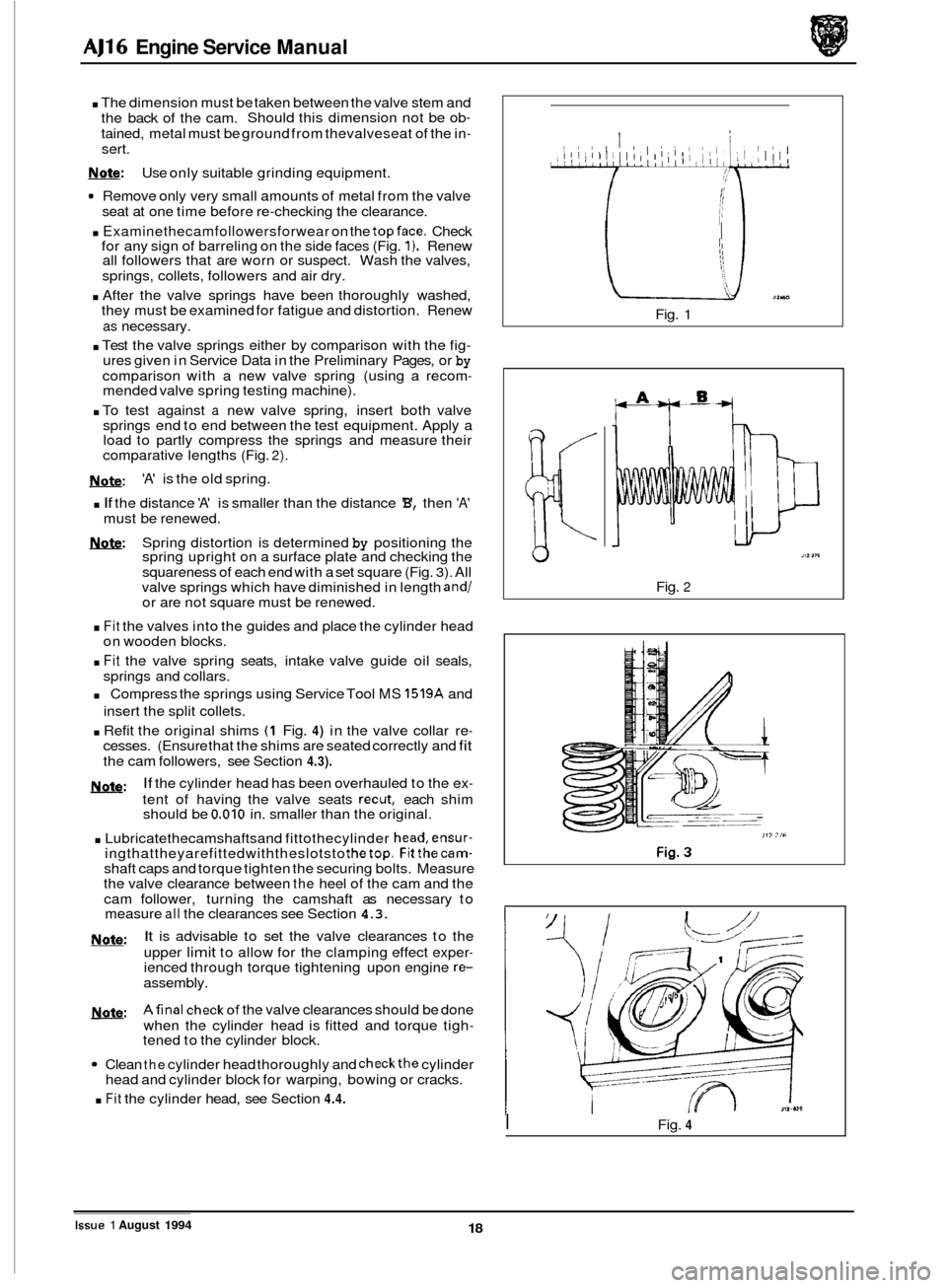
AJ16 Engine Service Manual
. The dimension must be taken between the valve stem and
the back of the cam. Should
this dimension not be ob-
tained, metal must be ground from thevalveseat of the in-
sert.
&&: Use only suitable grinding equipment.
* Remove only very small amounts of metal from the valve
seat at one time before re-checking the clearance.
. Examinethecamfollowersforwear on the topface. Check
for any sign of barreling on the side faces (Fig. 1). Renew
all followers that are worn or suspect. Wash the valves,
springs, collets, followers and air dry.
. After the valve springs have been thoroughly washed,
they must be examined for fatigue and distortion. Renew
as necessary.
. Test the valve springs either by comparison with the fig- ures given in Service Data in the Preliminary Pages, or by
comparison with a new valve spring (using a recom- mended valve spring testing machine).
. To test against a new valve spring, insert both valve
springs end to end between the test equipment. Apply a
load to partly compress the springs and measure their
comparative lengths (Fig.
2).
&@:
. If the distance 'A' is smaller than the distance 'B', then 'A'
b: Spring distortion is determined by positioning the
spring upright on a surface plate and checking the
squareness of each end with a set square (Fig.
3). All
valve springs which have diminished in length and/ or are not square must be renewed.
. Fit the valves into the guides and place the cylinder head
on wooden blocks.
. Fit the valve spring seats, intake valve guide oil seals,
springs and collars.
. Compress the springs using Service Tool MS 1519A and
insert the split collets.
. Refit the original shims (1 Fig. 4) in the valve collar re- cesses. (Ensure that the shims are seated correctly and fit
the cam followers, see Section 4.3).
If the cylinder head has been overhauled to the ex-
tent of having the valve seats recut, each shim
should be 0,010 in. smaller than the original.
. Lubricatethecamshaftsand fittothecylinder head,ensur- ingthattheyarefittedwiththeslotsto thetop. Fitthecam- shaft caps and torque tighten the securing bolts. Measure
the valve clearance between the heel of the cam and the
cam follower, turning the camshaft as necessary to
measure
all the clearances see Section 4.3.
It is advisable to set the valve clearances to the
upper
limit to allow for the clamping effect exper- ienced through torque tightening upon engine re- assembly.
Afinal checkof the valve clearances should be done
when the cylinder head is fitted and torque tigh
- tened to the cylinder block.
Clean the cylinder head thoroughly and checkthe cylinder
head and cylinder block for warping, bowing or cracks.
. Fit the cylinder head, see Section 4.4.
'A' is the old spring.
must be renewed.
&&:
m:
&@:
Fig. 1
K
Fig. 2
I Fig. 4
Issue 1 August 1994 18
Page 39 of 73
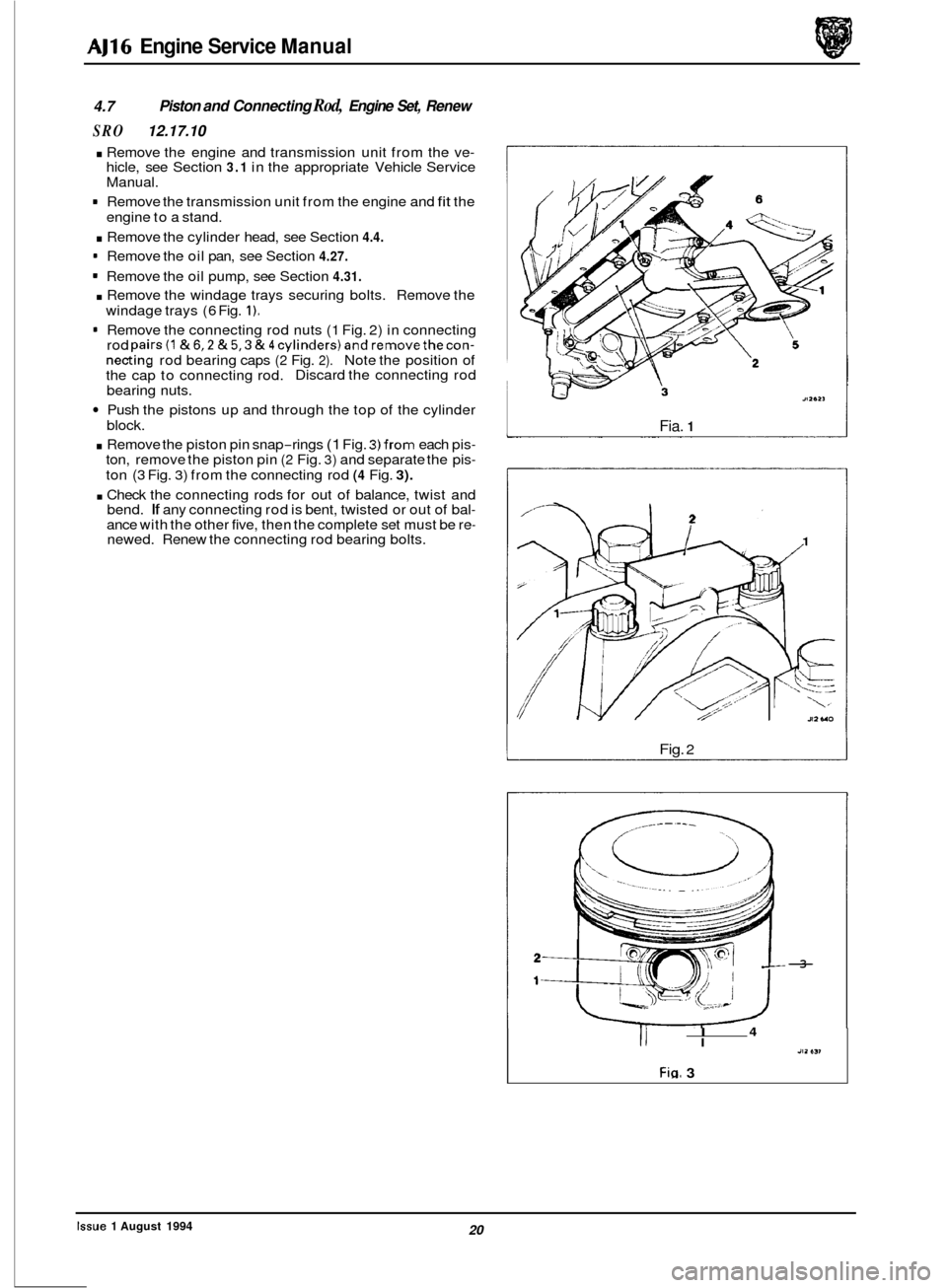
AJ16 Engine Service Manual
4.7 Piston
and Connecting Rod, Engine Set, Renew
SRO 12.17.10
. Remove the engine and transmission unit from the ve- hicle, see Section 3.1 in the appropriate Vehicle Service
Manual.
1 Remove the transmission unit from the engine and fit the
engine to a stand.
. Remove the cylinder head, see Section 4.4.
* Remove the oil pan, see Section 4.27.
1 Remove the oil pump, see Section 4.31.
. Remove the windage trays securing bolts. Remove the
windage trays (6 Fig. 1).
* Remove the connecting rod nuts (1 Fig. 2) in connecting
rod pairs(1 &6,2 &5,3&4cylinders)andremovethecon- necting rod bearing caps (2 Fig. 2). Note the position of
the cap to connecting rod. Discard
the connecting rod
bearing nuts.
Push the pistons up and through the top of the cylinder
block.
. Remove the piston pin snap-rings (1 Fig. 3)from each pis- ton, remove the piston pin (2 Fig. 3) and separate the pis-
ton (3 Fig. 3) from the connecting rod (4 Fig. 3).
. Check the connecting rods for out of balance, twist and
bend. If any connecting rod is bent, twisted or out of bal- ance with the other five, then the complete set must be re- newed. Renew
the connecting rod bearing bolts.
.a
Fia. 1
,11613
Fig. 2
I 4 Ii I
Fig. 3
-3
ill 631
Issue 1 August 1994 20
Page 40 of 73
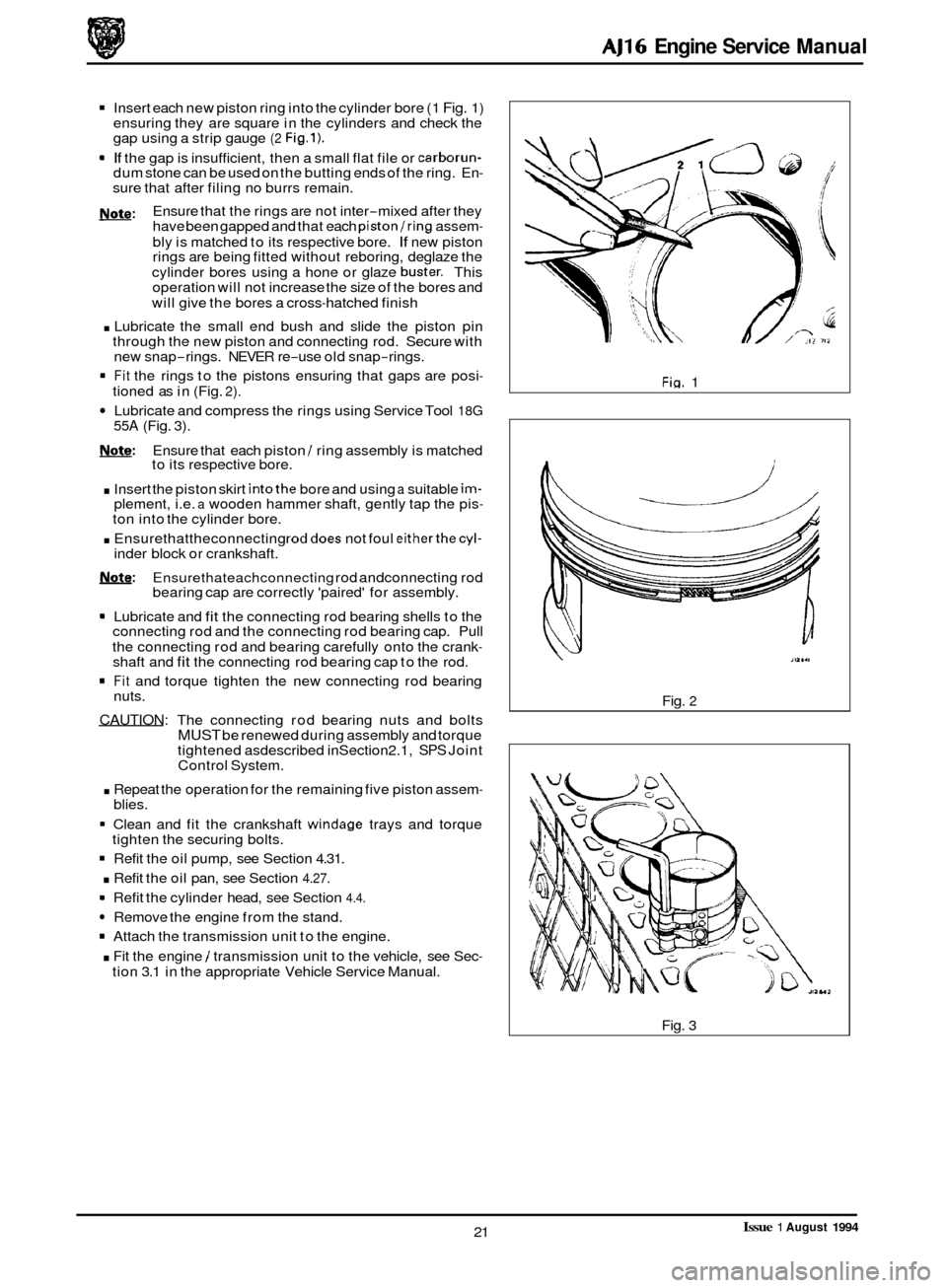
AJ16 Engine Service Manual
Insert each new piston ring into the cylinder bore (1 Fig. 1)
ensuring they are square in the cylinders and check the
gap using a strip gauge
(2 Fig.1).
9 If the gap is insufficient, then a small flat file or carborun- dum stone can be used on the butting ends of the ring. En- sure that after filing no burrs remain.
Ensure that the rings are not inter
-mixed after they
have been gapped and that each piston/ring assem-
bly is matched to its respective bore. If new piston
rings are being fitted without reboring, deglaze the
cylinder bores using a hone or glaze
buster. This
operation will not increase the size of the bores and
will give the bores a cross
-hatched finish
. Lubricate the small end bush and slide the piston pin
through the new piston and connecting rod. Secure with
new snap
-rings. NEVER re-use old snap-rings.
Fit the rings to the pistons ensuring that gaps are posi- tioned as in (Fig. 2).
Lubricate and compress the rings using Service Tool 18G 55A (Fig. 3).
w:
b: Ensure that each piston / ring assembly is matched
to its respective bore.
. Insert the piston skirt intothe bore and using a suitable im- 0
plement, i.e. a wooden hammer shaft, gently tap the pis- ton into the cylinder bore.
. Ensurethattheconnecting roddoes not foul eitherthecyl- inder block or crankshaft.
Note: Ensurethateachconnecting rod andconnecting rod
m Lubricate and fit the connecting rod bearing shells to the
connecting rod and the connecting rod bearing cap. Pull
the connecting rod and bearing carefully onto the crank
- shaft and fit the connecting rod bearing cap to the rod.
Fit and torque tighten the new connecting rod bearing
nuts.
CAUTION: The connecting rod bearing nuts and bolts MUST be renewed during assembly and torque
tightened asdescribed inSection2.1, SPS Joint
Control System.
. Repeat the operation for the remaining five piston assem-
bearing cap are correctly 'paired' for assembly.
blies.
Clean and fit the crankshaft
windage trays and torque
-
0 - - tighten the securing bolts.
Refit the oil pump, see Section 4.31.
. Refit the oil pan, see Section 4.27.
Refit the cylinder head, see Section 4.4.
Remove the engine from the stand.
Attach the transmission unit to the engine.
. Fit the engine / transmission unit to the vehicle, see Sec- tion 3.1 in the appropriate Vehicle Service Manual.
Fin. 1
itl6.l
Fig. 2
Fig. 3
Issue 1 August 1994 21
Page 42 of 73
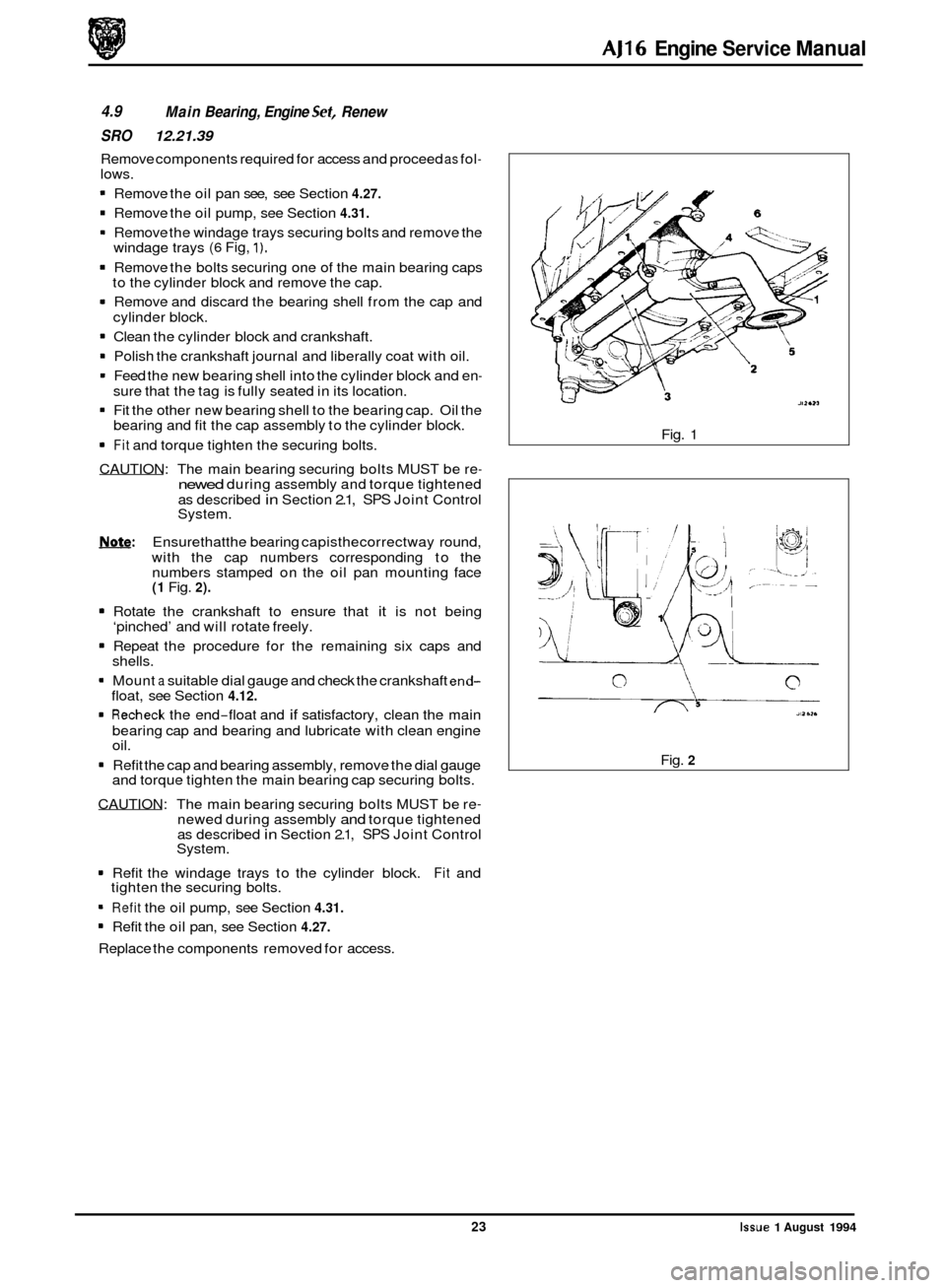
AJ16 Engine Service Manual
4.9
SRO 12.21.39
Main Bearing, Engine Set, Renew
Remove components required for access and proceed as fol- lows.
1 Remove the oil pan see, see Section 4.27.
1 Remove the oil pump, see Section 4.31.
* Remove the windage trays securing bolts and remove the
1 Remove the bolts securing one of the main bearing caps
1 Remove and discard the bearing shell from the cap and
1 Clean the cylinder block and crankshaft.
1 Polish the crankshaft journal and liberally coat with oil.
1 Feed the new bearing shell into the cylinder block and en- sure that the tag is fully seated in its location.
1 Fit the other new bearing shell to the bearing cap. Oil the
bearing and fit the cap assembly to the cylinder block.
1 Fit and torque tighten the securing bolts.
CAUTION: The main bearing securing bolts MUST be re
- newed during assembly and torque tightened
as described
in Section 2.1, SPS Joint Control
System.
Note: Ensurethatthe bearing capisthecorrectway round,
with the cap numbers corresponding to the
numbers stamped on the oil pan mounting face
(1 Fig. 2).
1 Rotate the crankshaft to ensure that it is not being
‘pinched’ and will rotate freely.
1 Repeat the procedure for the remaining six caps and
shells.
1 Mount a suitable dial gauge and check the crankshaft end- float, see Section 4.12.
1 Recheck the end-float and if satisfactory, clean the main
bearing cap and bearing and lubricate with clean engine
oil.
1 Refit the cap and bearing assembly, remove the dial gauge
and torque tighten the main bearing cap securing bolts.
CAUTION: The main bearing securing bolts MUST be re
- newed during assembly and torque tightened
as described in Section 2.1, SPS Joint Control
System.
1 Refit the windage trays to the cylinder block. Fit and
1 Refit the oil pump, see Section 4.31.
1 Refit the oil pan, see Section 4.27.
Replace the components removed for access.
windage trays
(6 Fig, 1).
to
the cylinder block and remove the cap.
cylinder block.
0
tighten the securing bolts. Fig.
1
Fig. 2
23
Issue 1 August 1994
Page 44 of 73

AJ16 Engine Service Manual
1 Clean and polish the crankshaft journals, lubricate and
carefully assemble the crankshaft into the cylinder block,
fit the thrust washers ensuring that the steel side of the
washer is mated to the cylinder block (1 Fig. 1).
1 Rotate the crankshaft to ensure that it turns freely.
1 Fit the main bearing shells into the main bearing caps, lu- bricate and fit to the cylinder block.
1 Start the securing bolts and carefullytap the main bearing
caps to ensure they are seated to the cylinder block.
1 Rotate thecrankshaft to ensurethat it still turnsfreely, pull
down each bearing cap individuallyand torque tighten the
securing bolts.
1 Rotate the crankshaft between pulling down each bearing
cap.
1 Check and if necessary adjust the crankshaft end-float in
accordance with Section 4.12.
1 Renew the crankshaft rear oil seal, see Section 4.14.
1 Fit a new bearing shell to the connecting rod, lubricate
1 Fit a bearing shell to theconnecting rod bearing cap, lubri-
with clean engine oil and fit to the crankshaft.
cate and fit to the connecting rod.
Fit and torque tighten
1 Turn the crankshaft over ensuring that there are no 'tiaht'
the nuts.
spots, and that the crankshaft rotates freely.
-
1 Repeat this procedure for the remaining five cylinders.
WUTION: The connecting rod bearing nuts, bolts and
main bearing securing bolts MUST be renewed during assembly and torque tightened as de- scribed in Section 2.1, SPS Joint Control Sys- tem.
1 Clean and inspect for wear or damage all the timing gears,
chains, guides and tensioners.
1 Renew any suspect component.
1 Fit and seat the crankshaft sprocket woodruff key and fit the sprocket to the crankshaft.
1 Refit the timing chains - upper and lower; and the upper
and lower tensioners, see Section 4.19.
1 Fit a dial gauge to the top ofthe cylinder blockand turn the
engine over until No.1 and 6 pistons are at TDC (Fig. 2).
1 Lubricate the upper chain and fit it to the intermediate
sprocket.
0 1 Fit an elastic band to retain the upper dampers and chain.
. Lubricate the oil pump drive chain, fit the chain to the
crankshaft sprocket and lodge in the correct position.
1 Renew the timing cover oil seal and refit the timing cover.
. Lubricate and fit the oil seal distance piece. Fit and seatthe
1 Refit the oil pump, see Section 4.31.
1 Refit the flywheel (Manual), see Section 4.15, or refit the
1 Refit the oil pan, see Section 4.27.
1 Refit the crankshaft damper /pulley assembly, see Section
1 Refit the cylinder head, see Section 4.4.
1 Remove the engine from the stand and refit the trans-
1 Refit the engine/transmission unitto thevehicle, see Sec-
damper woodruff key.
drive
-plate (Automatic), see Section 4.16.
4.11.
mission unit.
tion
3.1 in the appropriate Vehicle Service Manual.. Fig.
1
Fig. 2
Issue 1 August 1994 25
Page 46 of 73
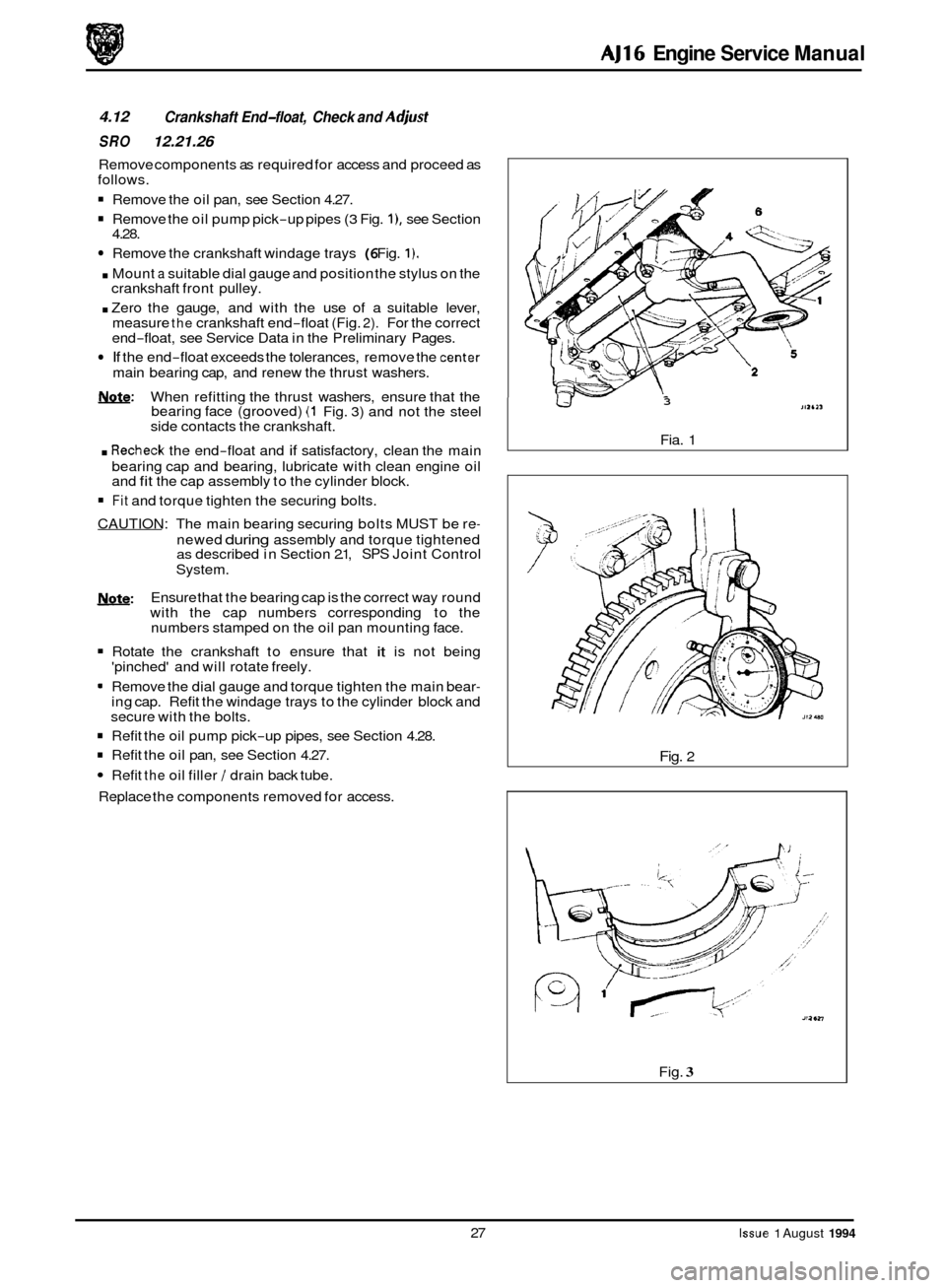
AJ16 Engine Service Manual
4.12
SRO 12.21.26
Crankshaft End-float, Check and A4ust
Remove components as required for access and proceed as
follows.
Remove the oil pan, see Section 4.27.
Remove the oil pump pick-up pipes (3 Fig. I), see Section
Remove the crankshaft windage trays (6 Fig. 1).
. Mount a suitable dial gauge and position the stylus on the
crankshaft front pulley.
. Zero the gauge, and with the use of a suitable lever,
measure the crankshaft end-float (Fig. 2). For the correct
end-float, see Service Data in the Preliminary Pages.
If the end-float exceeds the tolerances, remove the center
main bearing cap, and renew the thrust washers.
&&: When refitting the thrust washers, ensure that the
bearing face (grooved) (1 Fig. 3) and not the steel
side contacts the crankshaft.
. Recheck the end-float and if satisfactory, clean the main
bearing cap and bearing, lubricate with clean engine oil
and
fit the cap assembly to the cylinder block.
4.28. 0
Fit and
torque tighten the securing bolts.
CAUTION: The main bearing securing bolts MUST be re
-
newed during assembly and torque tightened as described in Section 2.1, SPS Joint Control
System.
Ensure that the bearing cap is the correct way round
with the cap numbers corresponding to the
numbers stamped on the oil pan mounting face.
Rotate the crankshaft to ensure that it is not being
'pinched' and will rotate freely.
m Remove the dial gauge and torque tighten the main bear- ing cap. Refit the windage trays to the cylinder block and
secure with the bolts.
w:
Refit the oil pump pick-up pipes, see Section 4.28.
Refit the oil pan, see Section 4.27.
Refit the oil filler / drain back tube.
Replace the components removed for access.
0
3
Fia. 1
Fig. 2
Fig.
3
27 Issue 1 August 1994
Page 50 of 73
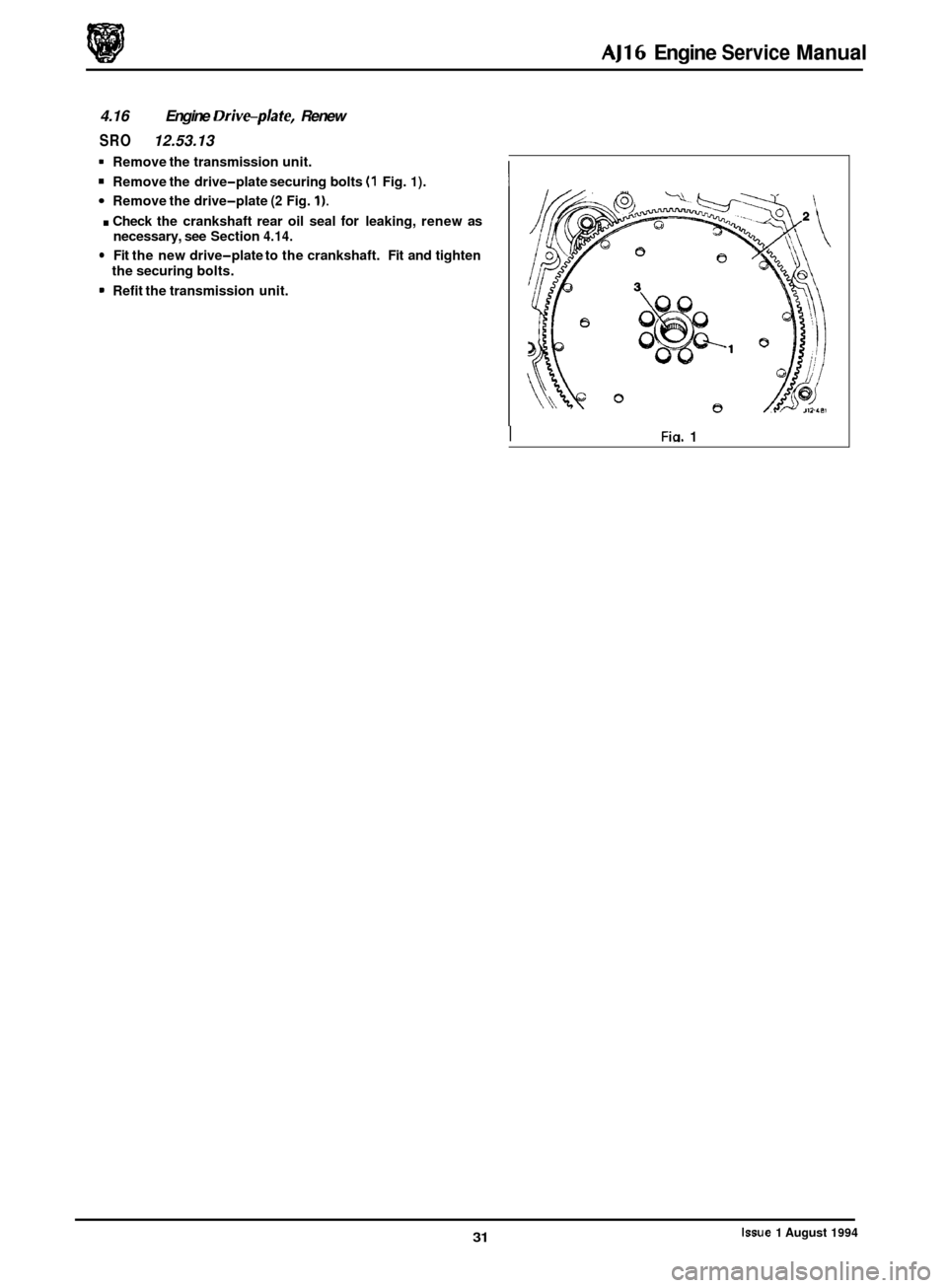
AJ16 Engine Service Manual
4.16 Engine Driveplate, Renew
SRO 12.53.13
1 Remove the transmission unit.
Remove the drive-plate securing bolts (1 Fig. 1).
Remove the drive-plate (2 Fig. 1).
. Check the crankshaft rear oil seal for leaking, renew as
Fit the new drive-plate to the crankshaft. Fit and tighten
1 Refit the transmission unit.
necessary,
see Section
4.14.
the securing bolts.
I Fin. 1
Issue 1 August 1994 31
Page 52 of 73
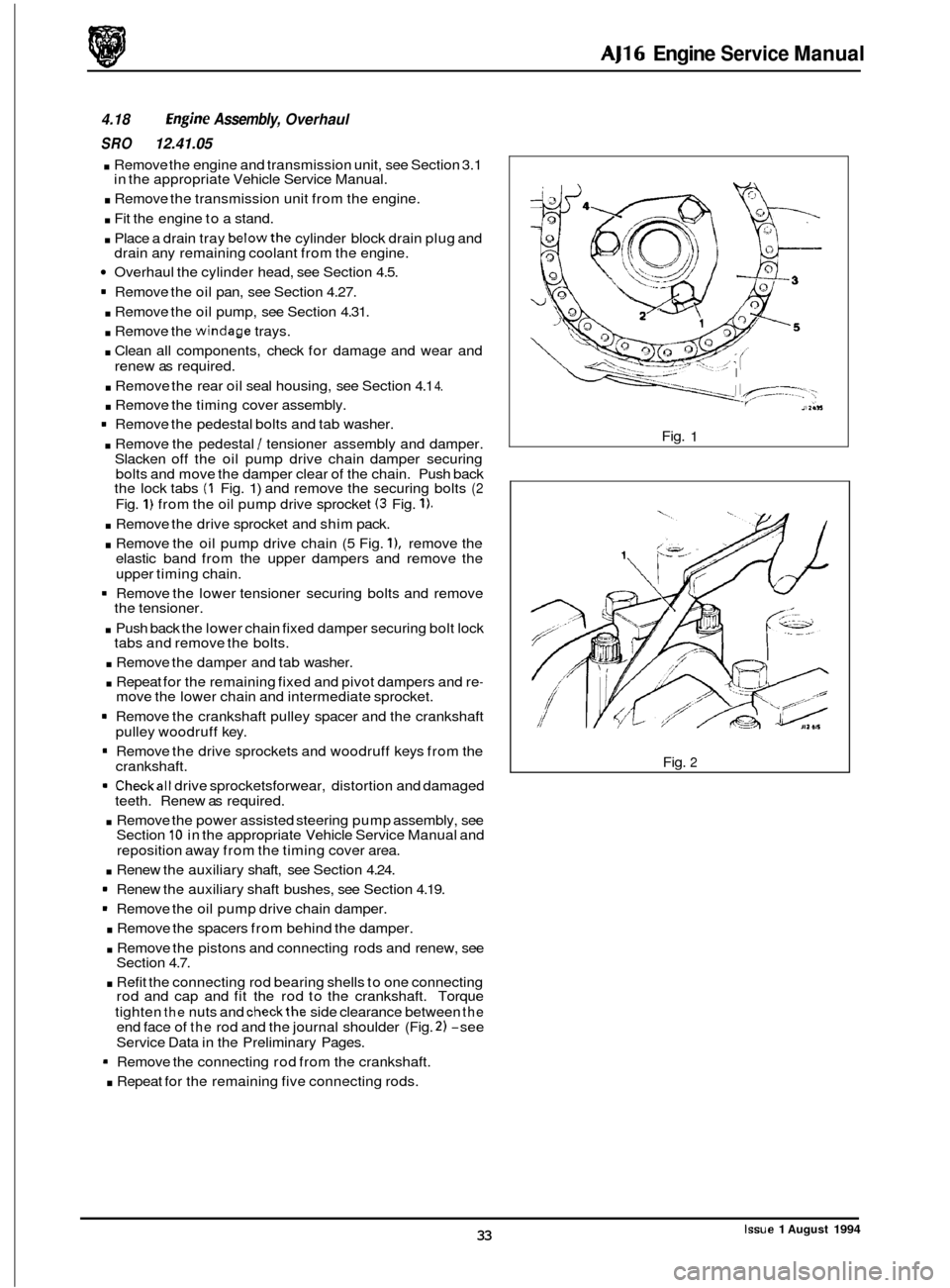
AJ16 Engine Service Manual
4.18 &;ne Assembly, Overhaul
SRO 12.41.05
. Remove the engine and transmission unit, see Section 3.1
. Remove the transmission unit from the engine.
. Fit the engine to a stand.
. Place a drain tray belowthe cylinder block drain plug and
Overhaul the cylinder head, see Section 4.5.
1 Remove the oil pan, see Section 4.27.
. Remove the oil pump, see Section 4.31.
. Remove the windage trays.
. Clean all components, check for damage and wear and
. Remove the rear oil seal housing, see Section 4.1 4.
. Remove the timing cover assembly.
1 Remove the pedestal bolts and tab washer.
. Remove the pedestal / tensioner assembly and damper.
Slacken off the oil pump drive chain damper securing
bolts and move the damper clear of the chain. Push back
the lock tabs
(1 Fig. 1) and remove the securing bolts (2
Fig. 1) from the oil pump drive sprocket (3 Fig. 1).
in the appropriate Vehicle Service Manual.
drain any remaining coolant from the engine.
renew as required.
. Remove the drive sprocket and shim pack.
. Remove the oil pump drive chain (5 Fig. l), remove the
elastic band from the upper dampers and remove the
upper timing chain.
1 Remove the lower tensioner securing bolts and remove
the tensioner.
. Push back the lower chain fixed damper securing bolt lock
tabs and remove the bolts.
. Remove the damper and tab washer.
. Repeat for the remaining fixed and pivot dampers and re- move the lower chain and intermediate sprocket.
Remove the crankshaft pulley spacer and the crankshaft
pulley woodruff key.
= Remove the drive sprockets and woodruff keys from the
crankshaft.
1 Checkall drive sprocketsforwear, distortion and damaged
teeth. Renew as required.
. Remove the power assisted steering pump assembly, see
Section 10 in the appropriate Vehicle Service Manual and
reposition away from the timing cover area.
. Renew the auxiliary shaft, see Section 4.24.
1 Renew the auxiliary shaft bushes, see Section 4.19.
1 Remove the oil pump drive chain damper.
. Remove the spacers from behind the damper.
. Remove the pistons and connecting rods and renew, see
Section 4.7.
. Refit the connecting rod bearing shells to one connecting
rod and cap and fit the rod to the crankshaft. Torque
tighten
the nuts and checkthe side clearance between the end face of the rod and the journal shoulder (Fig. 2) -see
Service Data in the Preliminary Pages.
Remove the connecting rod from the crankshaft.
. Repeat for the remaining five connecting rods. Fig.
1
Fig. 2
Issue 1 August 1994 33