torque JEEP GRAND CHEROKEE 2002 WJ / 2.G Owners Manual
[x] Cancel search | Manufacturer: JEEP, Model Year: 2002, Model line: GRAND CHEROKEE, Model: JEEP GRAND CHEROKEE 2002 WJ / 2.GPages: 2199, PDF Size: 76.01 MB
Page 411 of 2199
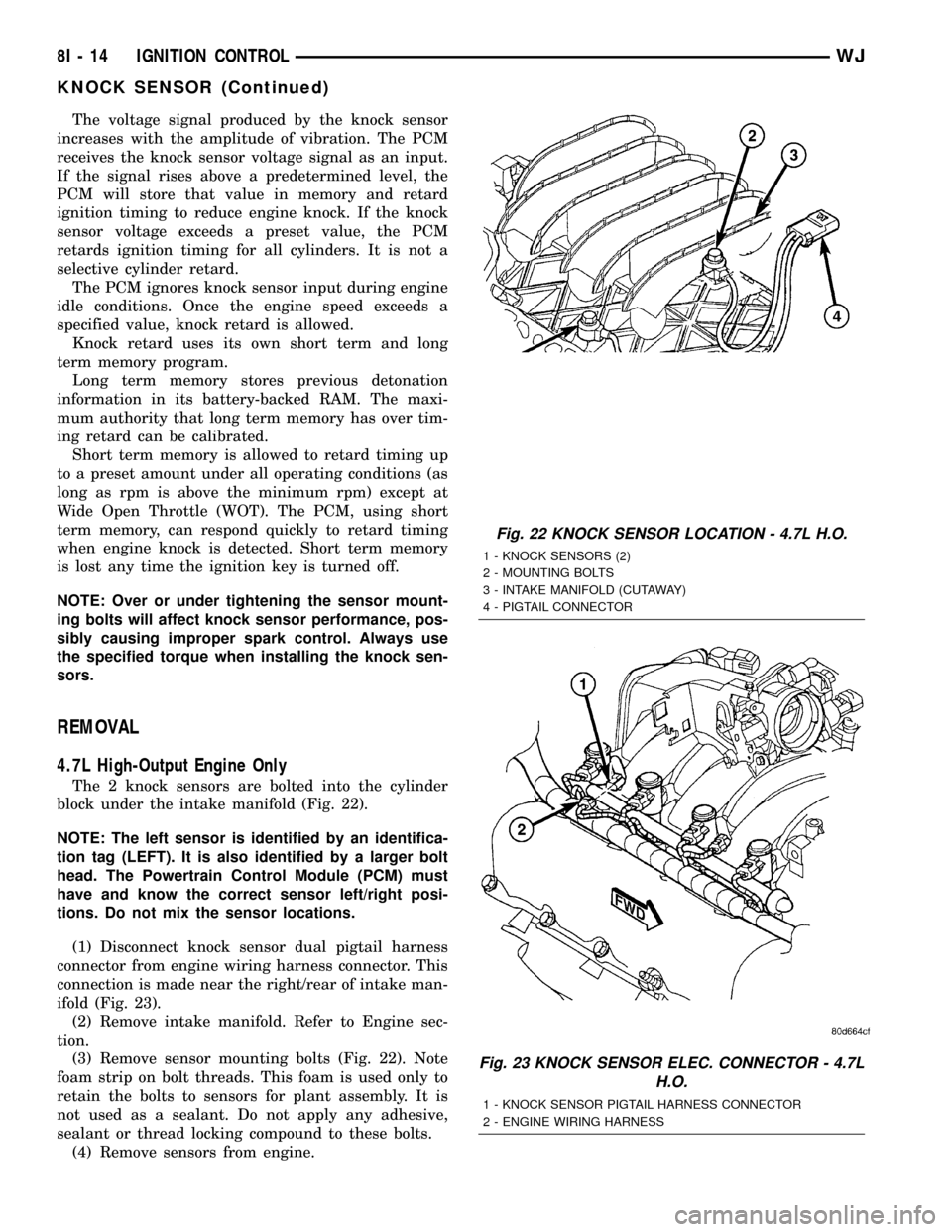
The voltage signal produced by the knock sensor
increases with the amplitude of vibration. The PCM
receives the knock sensor voltage signal as an input.
If the signal rises above a predetermined level, the
PCM will store that value in memory and retard
ignition timing to reduce engine knock. If the knock
sensor voltage exceeds a preset value, the PCM
retards ignition timing for all cylinders. It is not a
selective cylinder retard.
The PCM ignores knock sensor input during engine
idle conditions. Once the engine speed exceeds a
specified value, knock retard is allowed.
Knock retard uses its own short term and long
term memory program.
Long term memory stores previous detonation
information in its battery-backed RAM. The maxi-
mum authority that long term memory has over tim-
ing retard can be calibrated.
Short term memory is allowed to retard timing up
to a preset amount under all operating conditions (as
long as rpm is above the minimum rpm) except at
Wide Open Throttle (WOT). The PCM, using short
term memory, can respond quickly to retard timing
when engine knock is detected. Short term memory
is lost any time the ignition key is turned off.
NOTE: Over or under tightening the sensor mount-
ing bolts will affect knock sensor performance, pos-
sibly causing improper spark control. Always use
the specified torque when installing the knock sen-
sors.
REMOVAL
4.7L High-Output Engine Only
The 2 knock sensors are bolted into the cylinder
block under the intake manifold (Fig. 22).
NOTE: The left sensor is identified by an identifica-
tion tag (LEFT). It is also identified by a larger bolt
head. The Powertrain Control Module (PCM) must
have and know the correct sensor left/right posi-
tions. Do not mix the sensor locations.
(1) Disconnect knock sensor dual pigtail harness
connector from engine wiring harness connector. This
connection is made near the right/rear of intake man-
ifold (Fig. 23).
(2) Remove intake manifold. Refer to Engine sec-
tion.
(3) Remove sensor mounting bolts (Fig. 22). Note
foam strip on bolt threads. This foam is used only to
retain the bolts to sensors for plant assembly. It is
not used as a sealant. Do not apply any adhesive,
sealant or thread locking compound to these bolts.
(4) Remove sensors from engine.
Fig. 22 KNOCK SENSOR LOCATION - 4.7L H.O.
1 - KNOCK SENSORS (2)
2 - MOUNTING BOLTS
3 - INTAKE MANIFOLD (CUTAWAY)
4 - PIGTAIL CONNECTOR
Fig. 23 KNOCK SENSOR ELEC. CONNECTOR - 4.7L
H.O.
1 - KNOCK SENSOR PIGTAIL HARNESS CONNECTOR
2 - ENGINE WIRING HARNESS
8I - 14 IGNITION CONTROLWJ
KNOCK SENSOR (Continued)
Page 412 of 2199
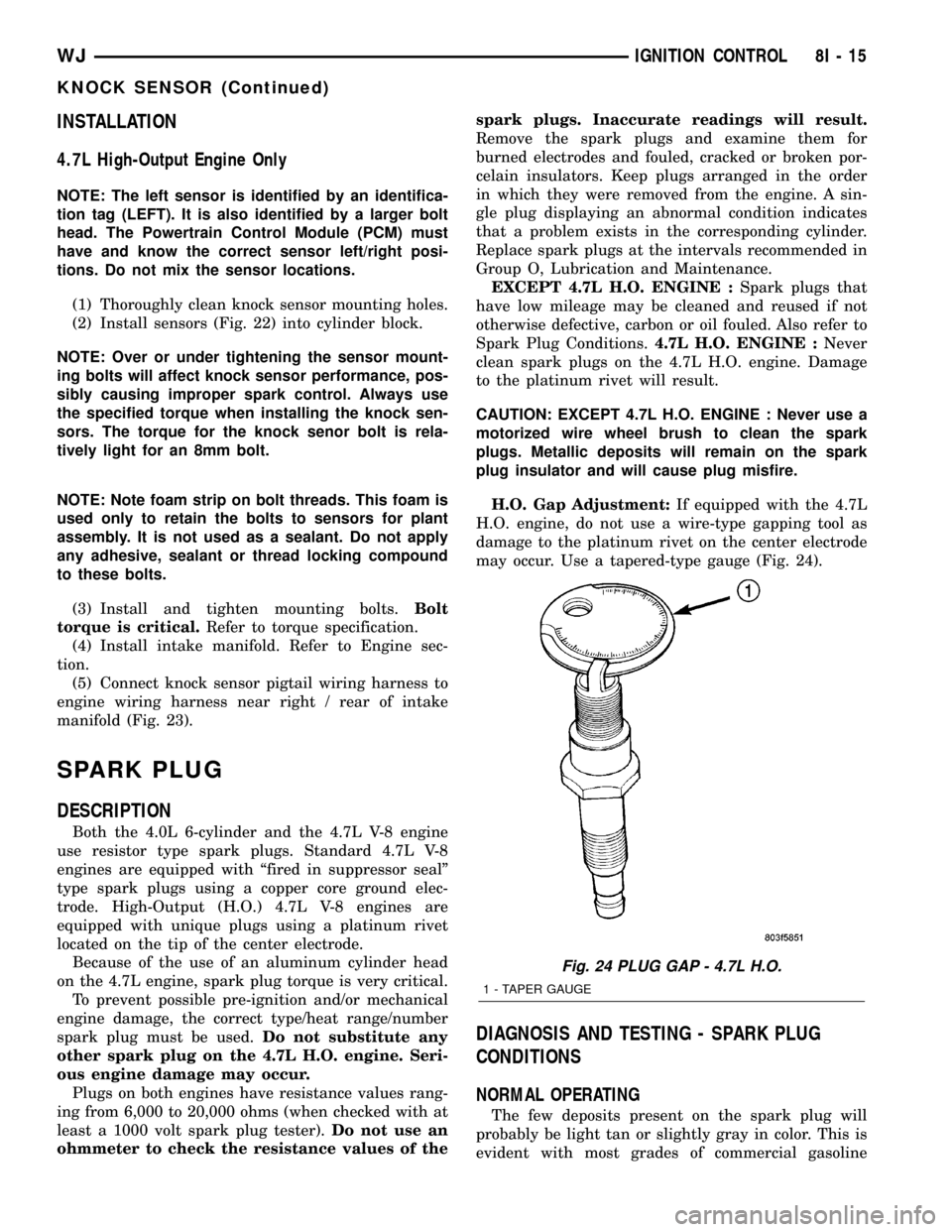
INSTALLATION
4.7L High-Output Engine Only
NOTE: The left sensor is identified by an identifica-
tion tag (LEFT). It is also identified by a larger bolt
head. The Powertrain Control Module (PCM) must
have and know the correct sensor left/right posi-
tions. Do not mix the sensor locations.
(1) Thoroughly clean knock sensor mounting holes.
(2) Install sensors (Fig. 22) into cylinder block.
NOTE: Over or under tightening the sensor mount-
ing bolts will affect knock sensor performance, pos-
sibly causing improper spark control. Always use
the specified torque when installing the knock sen-
sors. The torque for the knock senor bolt is rela-
tively light for an 8mm bolt.
NOTE: Note foam strip on bolt threads. This foam is
used only to retain the bolts to sensors for plant
assembly. It is not used as a sealant. Do not apply
any adhesive, sealant or thread locking compound
to these bolts.
(3) Install and tighten mounting bolts.Bolt
torque is critical.Refer to torque specification.
(4) Install intake manifold. Refer to Engine sec-
tion.
(5) Connect knock sensor pigtail wiring harness to
engine wiring harness near right / rear of intake
manifold (Fig. 23).
SPARK PLUG
DESCRIPTION
Both the 4.0L 6-cylinder and the 4.7L V-8 engine
use resistor type spark plugs. Standard 4.7L V-8
engines are equipped with ªfired in suppressor sealº
type spark plugs using a copper core ground elec-
trode. High-Output (H.O.) 4.7L V-8 engines are
equipped with unique plugs using a platinum rivet
located on the tip of the center electrode.
Because of the use of an aluminum cylinder head
on the 4.7L engine, spark plug torque is very critical.
To prevent possible pre-ignition and/or mechanical
engine damage, the correct type/heat range/number
spark plug must be used.Do not substitute any
other spark plug on the 4.7L H.O. engine. Seri-
ous engine damage may occur.
Plugs on both engines have resistance values rang-
ing from 6,000 to 20,000 ohms (when checked with at
least a 1000 volt spark plug tester).Do not use an
ohmmeter to check the resistance values of thespark plugs. Inaccurate readings will result.
Remove the spark plugs and examine them for
burned electrodes and fouled, cracked or broken por-
celain insulators. Keep plugs arranged in the order
in which they were removed from the engine. A sin-
gle plug displaying an abnormal condition indicates
that a problem exists in the corresponding cylinder.
Replace spark plugs at the intervals recommended in
Group O, Lubrication and Maintenance.
EXCEPT 4.7L H.O. ENGINE :Spark plugs that
have low mileage may be cleaned and reused if not
otherwise defective, carbon or oil fouled. Also refer to
Spark Plug Conditions.4.7L H.O. ENGINE :Never
clean spark plugs on the 4.7L H.O. engine. Damage
to the platinum rivet will result.
CAUTION: EXCEPT 4.7L H.O. ENGINE : Never use a
motorized wire wheel brush to clean the spark
plugs. Metallic deposits will remain on the spark
plug insulator and will cause plug misfire.
H.O. Gap Adjustment:If equipped with the 4.7L
H.O. engine, do not use a wire-type gapping tool as
damage to the platinum rivet on the center electrode
may occur. Use a tapered-type gauge (Fig. 24).
DIAGNOSIS AND TESTING - SPARK PLUG
CONDITIONS
NORMAL OPERATING
The few deposits present on the spark plug will
probably be light tan or slightly gray in color. This is
evident with most grades of commercial gasoline
Fig. 24 PLUG GAP - 4.7L H.O.
1 - TAPER GAUGE
WJIGNITION CONTROL 8I - 15
KNOCK SENSOR (Continued)
Page 413 of 2199
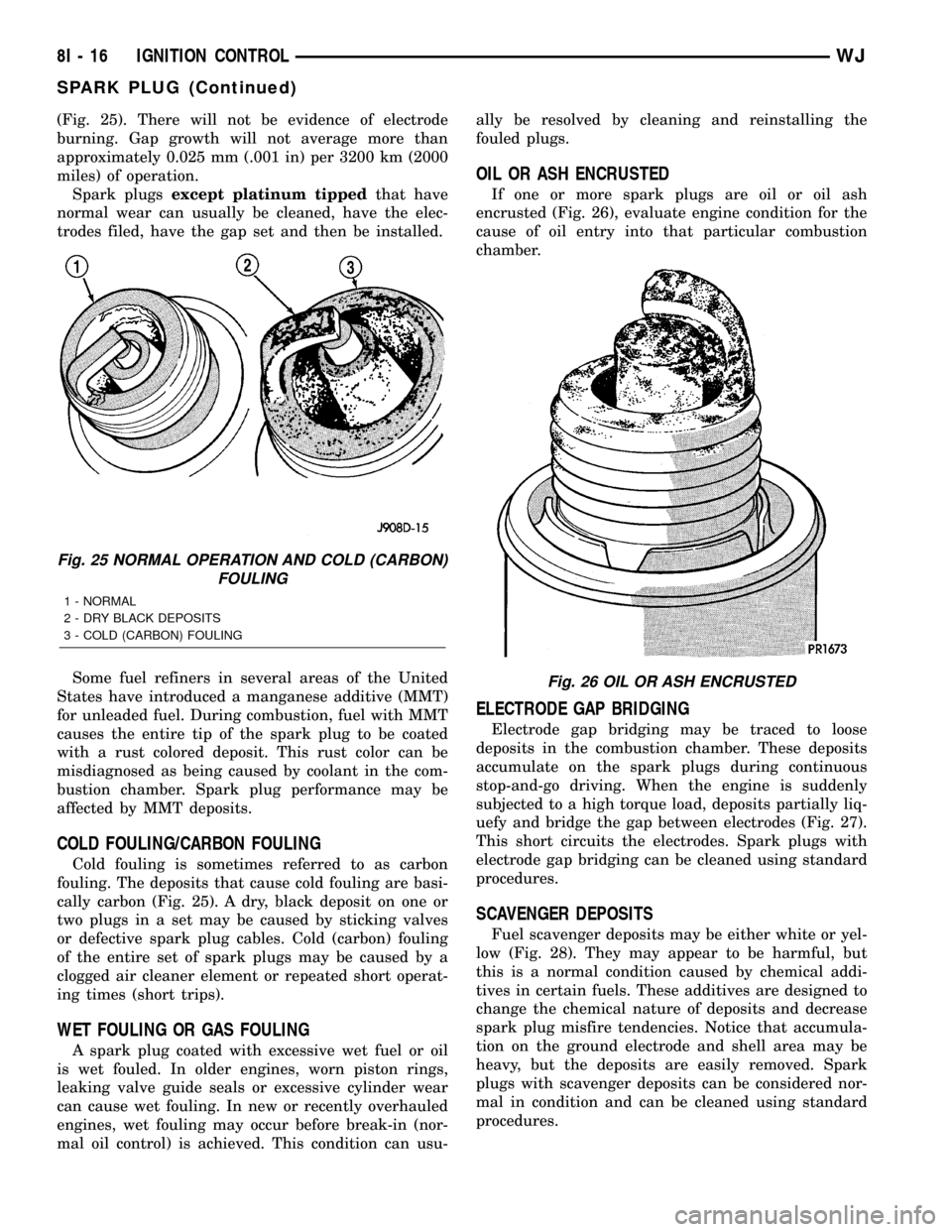
(Fig. 25). There will not be evidence of electrode
burning. Gap growth will not average more than
approximately 0.025 mm (.001 in) per 3200 km (2000
miles) of operation.
Spark plugsexcept platinum tippedthat have
normal wear can usually be cleaned, have the elec-
trodes filed, have the gap set and then be installed.
Some fuel refiners in several areas of the United
States have introduced a manganese additive (MMT)
for unleaded fuel. During combustion, fuel with MMT
causes the entire tip of the spark plug to be coated
with a rust colored deposit. This rust color can be
misdiagnosed as being caused by coolant in the com-
bustion chamber. Spark plug performance may be
affected by MMT deposits.
COLD FOULING/CARBON FOULING
Cold fouling is sometimes referred to as carbon
fouling. The deposits that cause cold fouling are basi-
cally carbon (Fig. 25). A dry, black deposit on one or
two plugs in a set may be caused by sticking valves
or defective spark plug cables. Cold (carbon) fouling
of the entire set of spark plugs may be caused by a
clogged air cleaner element or repeated short operat-
ing times (short trips).
WET FOULING OR GAS FOULING
A spark plug coated with excessive wet fuel or oil
is wet fouled. In older engines, worn piston rings,
leaking valve guide seals or excessive cylinder wear
can cause wet fouling. In new or recently overhauled
engines, wet fouling may occur before break-in (nor-
mal oil control) is achieved. This condition can usu-ally be resolved by cleaning and reinstalling the
fouled plugs.
OIL OR ASH ENCRUSTED
If one or more spark plugs are oil or oil ash
encrusted (Fig. 26), evaluate engine condition for the
cause of oil entry into that particular combustion
chamber.
ELECTRODE GAP BRIDGING
Electrode gap bridging may be traced to loose
deposits in the combustion chamber. These deposits
accumulate on the spark plugs during continuous
stop-and-go driving. When the engine is suddenly
subjected to a high torque load, deposits partially liq-
uefy and bridge the gap between electrodes (Fig. 27).
This short circuits the electrodes. Spark plugs with
electrode gap bridging can be cleaned using standard
procedures.
SCAVENGER DEPOSITS
Fuel scavenger deposits may be either white or yel-
low (Fig. 28). They may appear to be harmful, but
this is a normal condition caused by chemical addi-
tives in certain fuels. These additives are designed to
change the chemical nature of deposits and decrease
spark plug misfire tendencies. Notice that accumula-
tion on the ground electrode and shell area may be
heavy, but the deposits are easily removed. Spark
plugs with scavenger deposits can be considered nor-
mal in condition and can be cleaned using standard
procedures.
Fig. 25 NORMAL OPERATION AND COLD (CARBON)
FOULING
1 - NORMAL
2 - DRY BLACK DEPOSITS
3 - COLD (CARBON) FOULING
Fig. 26 OIL OR ASH ENCRUSTED
8I - 16 IGNITION CONTROLWJ
SPARK PLUG (Continued)
Page 415 of 2199
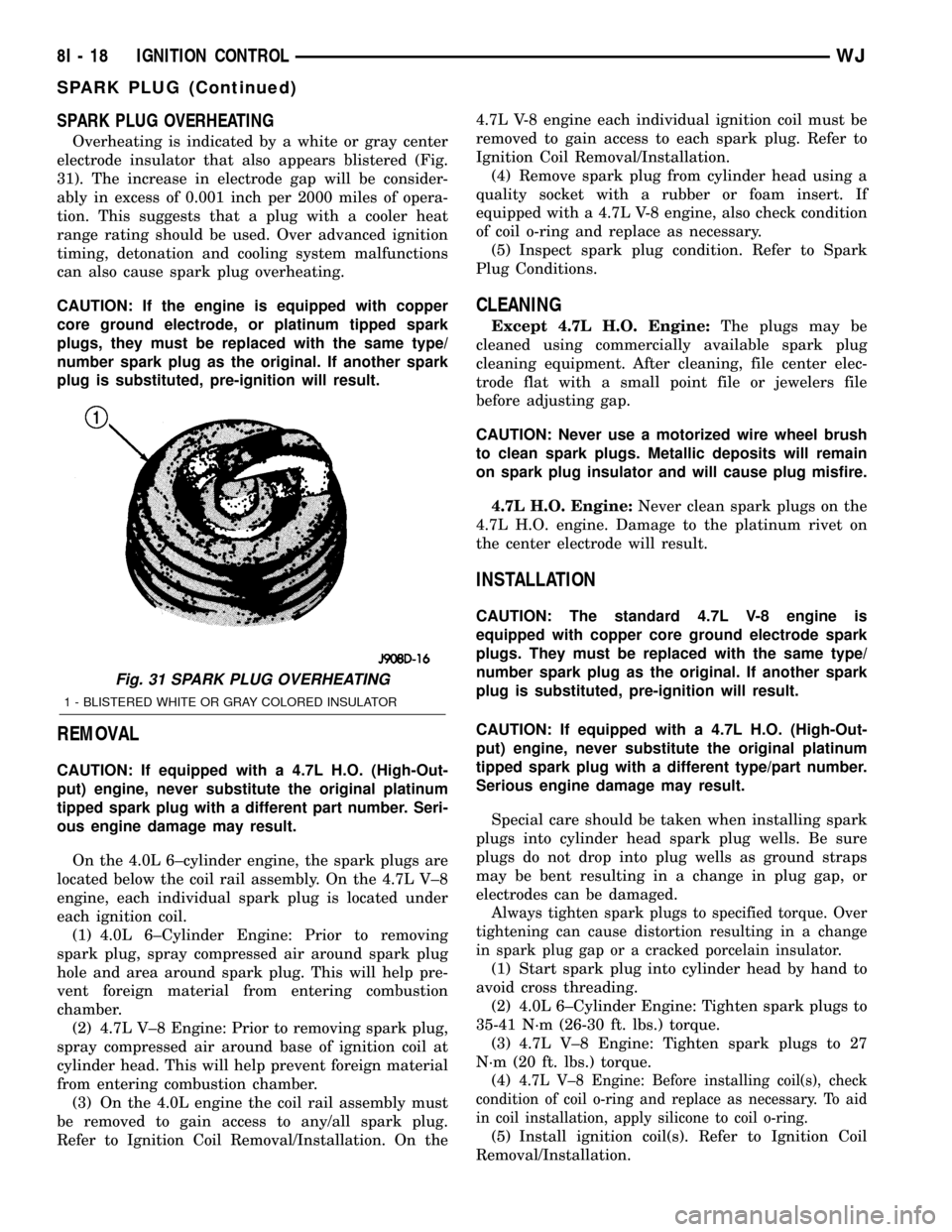
SPARK PLUG OVERHEATING
Overheating is indicated by a white or gray center
electrode insulator that also appears blistered (Fig.
31). The increase in electrode gap will be consider-
ably in excess of 0.001 inch per 2000 miles of opera-
tion. This suggests that a plug with a cooler heat
range rating should be used. Over advanced ignition
timing, detonation and cooling system malfunctions
can also cause spark plug overheating.
CAUTION: If the engine is equipped with copper
core ground electrode, or platinum tipped spark
plugs, they must be replaced with the same type/
number spark plug as the original. If another spark
plug is substituted, pre-ignition will result.
REMOVAL
CAUTION: If equipped with a 4.7L H.O. (High-Out-
put) engine, never substitute the original platinum
tipped spark plug with a different part number. Seri-
ous engine damage may result.
On the 4.0L 6±cylinder engine, the spark plugs are
located below the coil rail assembly. On the 4.7L V±8
engine, each individual spark plug is located under
each ignition coil.
(1) 4.0L 6±Cylinder Engine: Prior to removing
spark plug, spray compressed air around spark plug
hole and area around spark plug. This will help pre-
vent foreign material from entering combustion
chamber.
(2) 4.7L V±8 Engine: Prior to removing spark plug,
spray compressed air around base of ignition coil at
cylinder head. This will help prevent foreign material
from entering combustion chamber.
(3) On the 4.0L engine the coil rail assembly must
be removed to gain access to any/all spark plug.
Refer to Ignition Coil Removal/Installation. On the4.7L V-8 engine each individual ignition coil must be
removed to gain access to each spark plug. Refer to
Ignition Coil Removal/Installation.
(4) Remove spark plug from cylinder head using a
quality socket with a rubber or foam insert. If
equipped with a 4.7L V-8 engine, also check condition
of coil o-ring and replace as necessary.
(5) Inspect spark plug condition. Refer to Spark
Plug Conditions.
CLEANING
Except 4.7L H.O. Engine:The plugs may be
cleaned using commercially available spark plug
cleaning equipment. After cleaning, file center elec-
trode flat with a small point file or jewelers file
before adjusting gap.
CAUTION: Never use a motorized wire wheel brush
to clean spark plugs. Metallic deposits will remain
on spark plug insulator and will cause plug misfire.
4.7L H.O. Engine:Never clean spark plugs on the
4.7L H.O. engine. Damage to the platinum rivet on
the center electrode will result.
INSTALLATION
CAUTION: The standard 4.7L V-8 engine is
equipped with copper core ground electrode spark
plugs. They must be replaced with the same type/
number spark plug as the original. If another spark
plug is substituted, pre-ignition will result.
CAUTION: If equipped with a 4.7L H.O. (High-Out-
put) engine, never substitute the original platinum
tipped spark plug with a different type/part number.
Serious engine damage may result.
Special care should be taken when installing spark
plugs into cylinder head spark plug wells. Be sure
plugs do not drop into plug wells as ground straps
may be bent resulting in a change in plug gap, or
electrodes can be damaged.
Always tighten spark plugs to specified torque. Over
tightening can cause distortion resulting in a change
in spark plug gap or a cracked porcelain insulator.
(1) Start spark plug into cylinder head by hand to
avoid cross threading.
(2) 4.0L 6±Cylinder Engine: Tighten spark plugs to
35-41 N´m (26-30 ft. lbs.) torque.
(3) 4.7L V±8 Engine: Tighten spark plugs to 27
N´m (20 ft. lbs.) torque.
(4)
4.7L V±8 Engine: Before installing coil(s), check
condition of coil o-ring and replace as necessary. To aid
in coil installation, apply silicone to coil o-ring.
(5) Install ignition coil(s). Refer to Ignition Coil
Removal/Installation.
Fig. 31 SPARK PLUG OVERHEATING
1 - BLISTERED WHITE OR GRAY COLORED INSULATOR
8I - 18 IGNITION CONTROLWJ
SPARK PLUG (Continued)
Page 553 of 2199
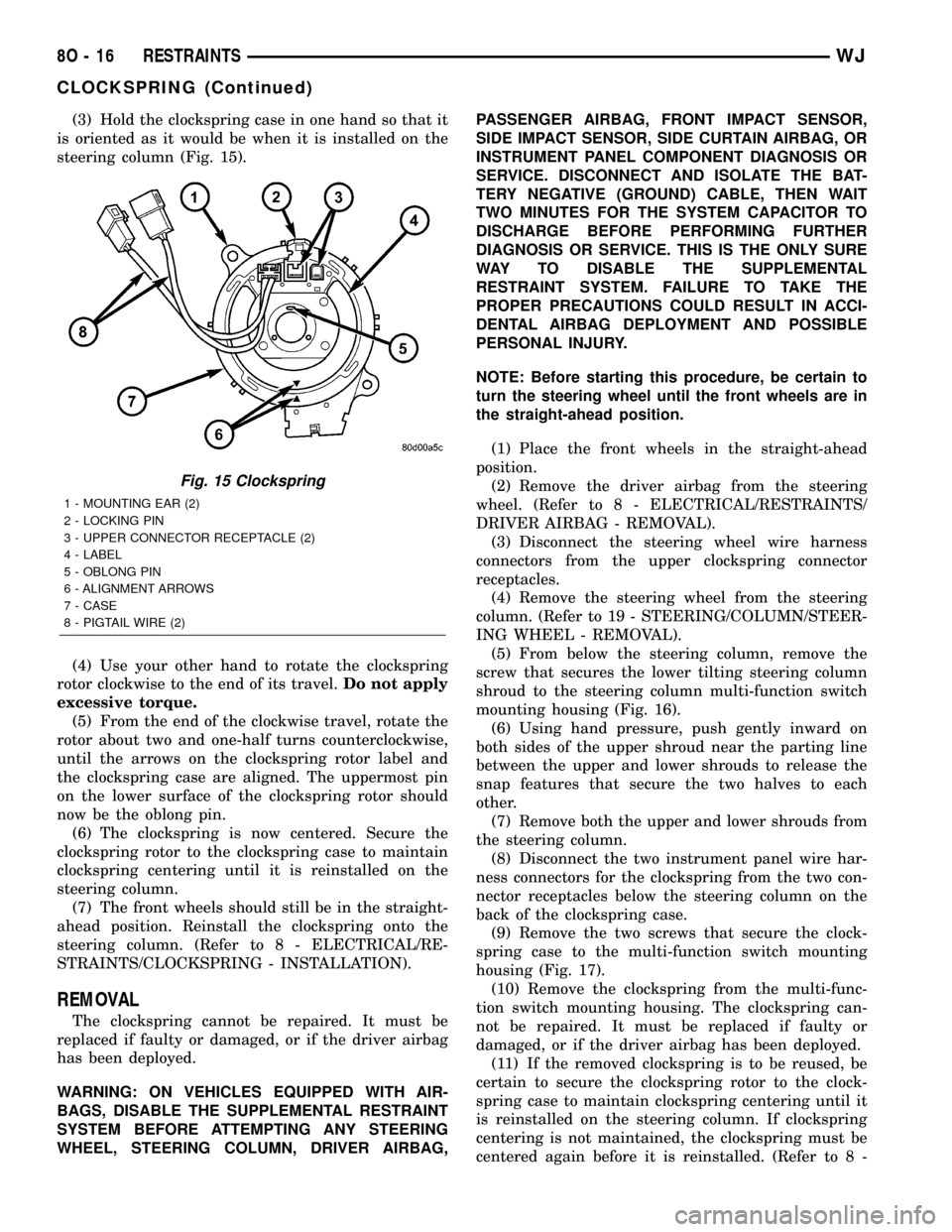
(3) Hold the clockspring case in one hand so that it
is oriented as it would be when it is installed on the
steering column (Fig. 15).
(4) Use your other hand to rotate the clockspring
rotor clockwise to the end of its travel.Do not apply
excessive torque.
(5) From the end of the clockwise travel, rotate the
rotor about two and one-half turns counterclockwise,
until the arrows on the clockspring rotor label and
the clockspring case are aligned. The uppermost pin
on the lower surface of the clockspring rotor should
now be the oblong pin.
(6) The clockspring is now centered. Secure the
clockspring rotor to the clockspring case to maintain
clockspring centering until it is reinstalled on the
steering column.
(7) The front wheels should still be in the straight-
ahead position. Reinstall the clockspring onto the
steering column. (Refer to 8 - ELECTRICAL/RE-
STRAINTS/CLOCKSPRING - INSTALLATION).
REMOVAL
The clockspring cannot be repaired. It must be
replaced if faulty or damaged, or if the driver airbag
has been deployed.
WARNING: ON VEHICLES EQUIPPED WITH AIR-
BAGS, DISABLE THE SUPPLEMENTAL RESTRAINT
SYSTEM BEFORE ATTEMPTING ANY STEERING
WHEEL, STEERING COLUMN, DRIVER AIRBAG,PASSENGER AIRBAG, FRONT IMPACT SENSOR,
SIDE IMPACT SENSOR, SIDE CURTAIN AIRBAG, OR
INSTRUMENT PANEL COMPONENT DIAGNOSIS OR
SERVICE. DISCONNECT AND ISOLATE THE BAT-
TERY NEGATIVE (GROUND) CABLE, THEN WAIT
TWO MINUTES FOR THE SYSTEM CAPACITOR TO
DISCHARGE BEFORE PERFORMING FURTHER
DIAGNOSIS OR SERVICE. THIS IS THE ONLY SURE
WAY TO DISABLE THE SUPPLEMENTAL
RESTRAINT SYSTEM. FAILURE TO TAKE THE
PROPER PRECAUTIONS COULD RESULT IN ACCI-
DENTAL AIRBAG DEPLOYMENT AND POSSIBLE
PERSONAL INJURY.
NOTE: Before starting this procedure, be certain to
turn the steering wheel until the front wheels are in
the straight-ahead position.
(1) Place the front wheels in the straight-ahead
position.
(2) Remove the driver airbag from the steering
wheel. (Refer to 8 - ELECTRICAL/RESTRAINTS/
DRIVER AIRBAG - REMOVAL).
(3) Disconnect the steering wheel wire harness
connectors from the upper clockspring connector
receptacles.
(4) Remove the steering wheel from the steering
column. (Refer to 19 - STEERING/COLUMN/STEER-
ING WHEEL - REMOVAL).
(5) From below the steering column, remove the
screw that secures the lower tilting steering column
shroud to the steering column multi-function switch
mounting housing (Fig. 16).
(6) Using hand pressure, push gently inward on
both sides of the upper shroud near the parting line
between the upper and lower shrouds to release the
snap features that secure the two halves to each
other.
(7) Remove both the upper and lower shrouds from
the steering column.
(8) Disconnect the two instrument panel wire har-
ness connectors for the clockspring from the two con-
nector receptacles below the steering column on the
back of the clockspring case.
(9) Remove the two screws that secure the clock-
spring case to the multi-function switch mounting
housing (Fig. 17).
(10) Remove the clockspring from the multi-func-
tion switch mounting housing. The clockspring can-
not be repaired. It must be replaced if faulty or
damaged, or if the driver airbag has been deployed.
(11) If the removed clockspring is to be reused, be
certain to secure the clockspring rotor to the clock-
spring case to maintain clockspring centering until it
is reinstalled on the steering column. If clockspring
centering is not maintained, the clockspring must be
centered again before it is reinstalled. (Refer to 8 -
Fig. 15 Clockspring
1 - MOUNTING EAR (2)
2 - LOCKING PIN
3 - UPPER CONNECTOR RECEPTACLE (2)
4 - LABEL
5 - OBLONG PIN
6 - ALIGNMENT ARROWS
7 - CASE
8 - PIGTAIL WIRE (2)
8O - 16 RESTRAINTSWJ
CLOCKSPRING (Continued)
Page 560 of 2199
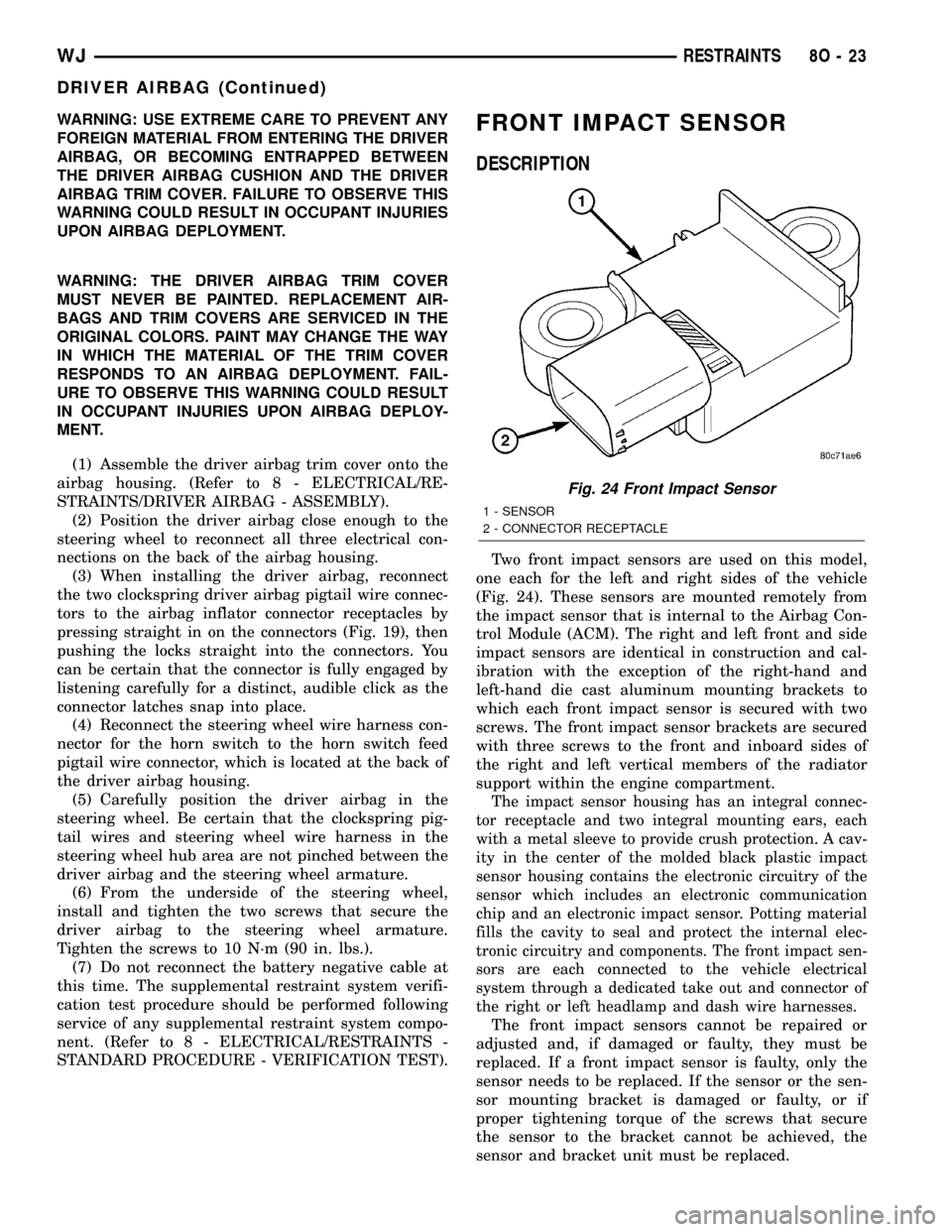
WARNING: USE EXTREME CARE TO PREVENT ANY
FOREIGN MATERIAL FROM ENTERING THE DRIVER
AIRBAG, OR BECOMING ENTRAPPED BETWEEN
THE DRIVER AIRBAG CUSHION AND THE DRIVER
AIRBAG TRIM COVER. FAILURE TO OBSERVE THIS
WARNING COULD RESULT IN OCCUPANT INJURIES
UPON AIRBAG DEPLOYMENT.
WARNING: THE DRIVER AIRBAG TRIM COVER
MUST NEVER BE PAINTED. REPLACEMENT AIR-
BAGS AND TRIM COVERS ARE SERVICED IN THE
ORIGINAL COLORS. PAINT MAY CHANGE THE WAY
IN WHICH THE MATERIAL OF THE TRIM COVER
RESPONDS TO AN AIRBAG DEPLOYMENT. FAIL-
URE TO OBSERVE THIS WARNING COULD RESULT
IN OCCUPANT INJURIES UPON AIRBAG DEPLOY-
MENT.
(1) Assemble the driver airbag trim cover onto the
airbag housing. (Refer to 8 - ELECTRICAL/RE-
STRAINTS/DRIVER AIRBAG - ASSEMBLY).
(2) Position the driver airbag close enough to the
steering wheel to reconnect all three electrical con-
nections on the back of the airbag housing.
(3) When installing the driver airbag, reconnect
the two clockspring driver airbag pigtail wire connec-
tors to the airbag inflator connector receptacles by
pressing straight in on the connectors (Fig. 19), then
pushing the locks straight into the connectors. You
can be certain that the connector is fully engaged by
listening carefully for a distinct, audible click as the
connector latches snap into place.
(4) Reconnect the steering wheel wire harness con-
nector for the horn switch to the horn switch feed
pigtail wire connector, which is located at the back of
the driver airbag housing.
(5) Carefully position the driver airbag in the
steering wheel. Be certain that the clockspring pig-
tail wires and steering wheel wire harness in the
steering wheel hub area are not pinched between the
driver airbag and the steering wheel armature.
(6) From the underside of the steering wheel,
install and tighten the two screws that secure the
driver airbag to the steering wheel armature.
Tighten the screws to 10 N´m (90 in. lbs.).
(7) Do not reconnect the battery negative cable at
this time. The supplemental restraint system verifi-
cation test procedure should be performed following
service of any supplemental restraint system compo-
nent. (Refer to 8 - ELECTRICAL/RESTRAINTS -
STANDARD PROCEDURE - VERIFICATION TEST).FRONT IMPACT SENSOR
DESCRIPTION
Two front impact sensors are used on this model,
one each for the left and right sides of the vehicle
(Fig. 24). These sensors are mounted remotely from
the impact sensor that is internal to the Airbag Con-
trol Module (ACM). The right and left front and side
impact sensors are identical in construction and cal-
ibration with the exception of the right-hand and
left-hand die cast aluminum mounting brackets to
which each front impact sensor is secured with two
screws. The front impact sensor brackets are secured
with three screws to the front and inboard sides of
the right and left vertical members of the radiator
support within the engine compartment.
The impact sensor housing has an integral connec-
tor receptacle and two integral mounting ears, each
with a metal sleeve to provide crush protection. A cav-
ity in the center of the molded black plastic impact
sensor housing contains the electronic circuitry of the
sensor which includes an electronic communication
chip and an electronic impact sensor. Potting material
fills the cavity to seal and protect the internal elec-
tronic circuitry and components. The front impact sen-
sors are each connected to the vehicle electrical
system through a dedicated take out and connector of
the right or left headlamp and dash wire harnesses.
The front impact sensors cannot be repaired or
adjusted and, if damaged or faulty, they must be
replaced. If a front impact sensor is faulty, only the
sensor needs to be replaced. If the sensor or the sen-
sor mounting bracket is damaged or faulty, or if
proper tightening torque of the screws that secure
the sensor to the bracket cannot be achieved, the
sensor and bracket unit must be replaced.
Fig. 24 Front Impact Sensor
1 - SENSOR
2 - CONNECTOR RECEPTACLE
WJRESTRAINTS 8O - 23
DRIVER AIRBAG (Continued)
Page 561 of 2199
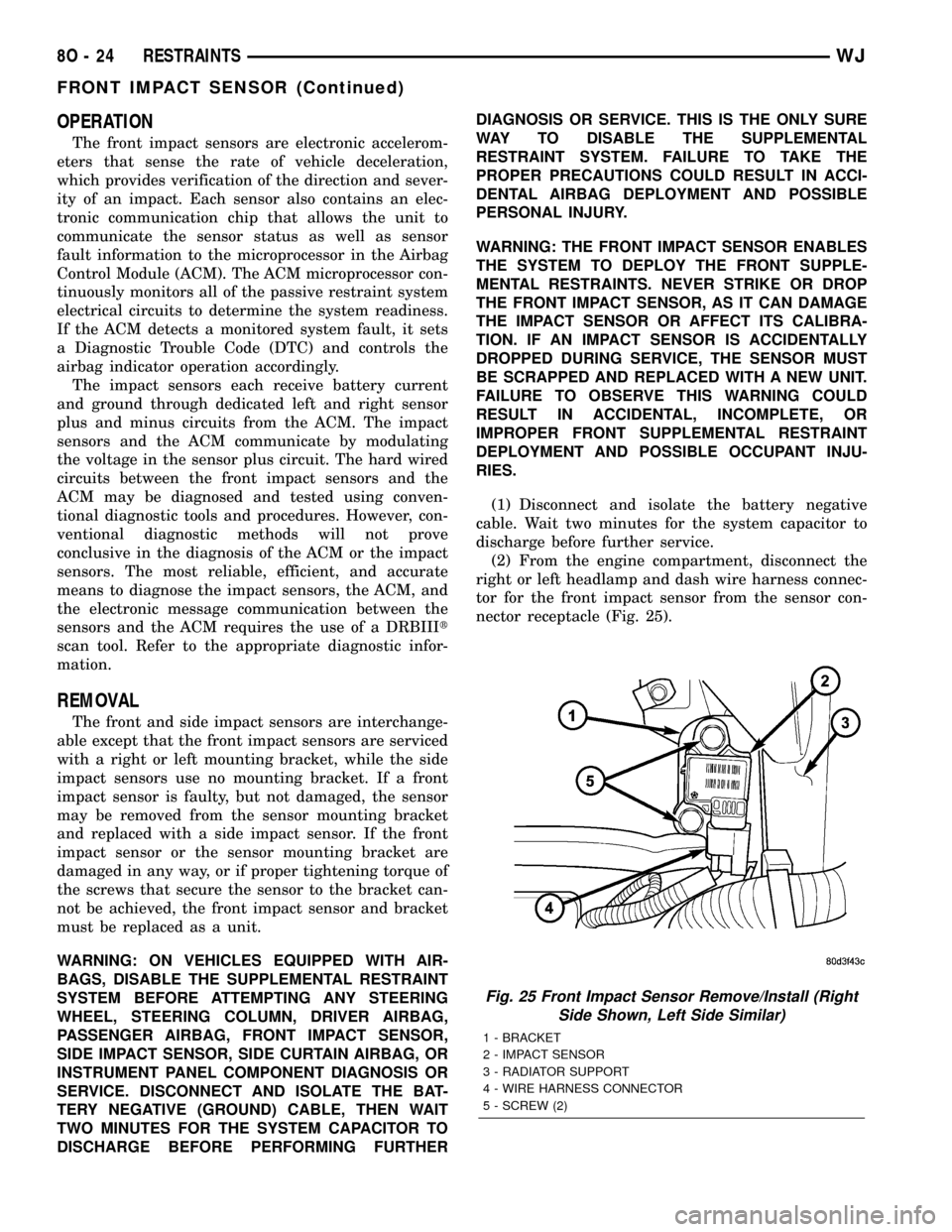
OPERATION
The front impact sensors are electronic accelerom-
eters that sense the rate of vehicle deceleration,
which provides verification of the direction and sever-
ity of an impact. Each sensor also contains an elec-
tronic communication chip that allows the unit to
communicate the sensor status as well as sensor
fault information to the microprocessor in the Airbag
Control Module (ACM). The ACM microprocessor con-
tinuously monitors all of the passive restraint system
electrical circuits to determine the system readiness.
If the ACM detects a monitored system fault, it sets
a Diagnostic Trouble Code (DTC) and controls the
airbag indicator operation accordingly.
The impact sensors each receive battery current
and ground through dedicated left and right sensor
plus and minus circuits from the ACM. The impact
sensors and the ACM communicate by modulating
the voltage in the sensor plus circuit. The hard wired
circuits between the front impact sensors and the
ACM may be diagnosed and tested using conven-
tional diagnostic tools and procedures. However, con-
ventional diagnostic methods will not prove
conclusive in the diagnosis of the ACM or the impact
sensors. The most reliable, efficient, and accurate
means to diagnose the impact sensors, the ACM, and
the electronic message communication between the
sensors and the ACM requires the use of a DRBIIIt
scan tool. Refer to the appropriate diagnostic infor-
mation.
REMOVAL
The front and side impact sensors are interchange-
able except that the front impact sensors are serviced
with a right or left mounting bracket, while the side
impact sensors use no mounting bracket. If a front
impact sensor is faulty, but not damaged, the sensor
may be removed from the sensor mounting bracket
and replaced with a side impact sensor. If the front
impact sensor or the sensor mounting bracket are
damaged in any way, or if proper tightening torque of
the screws that secure the sensor to the bracket can-
not be achieved, the front impact sensor and bracket
must be replaced as a unit.
WARNING: ON VEHICLES EQUIPPED WITH AIR-
BAGS, DISABLE THE SUPPLEMENTAL RESTRAINT
SYSTEM BEFORE ATTEMPTING ANY STEERING
WHEEL, STEERING COLUMN, DRIVER AIRBAG,
PASSENGER AIRBAG, FRONT IMPACT SENSOR,
SIDE IMPACT SENSOR, SIDE CURTAIN AIRBAG, OR
INSTRUMENT PANEL COMPONENT DIAGNOSIS OR
SERVICE. DISCONNECT AND ISOLATE THE BAT-
TERY NEGATIVE (GROUND) CABLE, THEN WAIT
TWO MINUTES FOR THE SYSTEM CAPACITOR TO
DISCHARGE BEFORE PERFORMING FURTHERDIAGNOSIS OR SERVICE. THIS IS THE ONLY SURE
WAY TO DISABLE THE SUPPLEMENTAL
RESTRAINT SYSTEM. FAILURE TO TAKE THE
PROPER PRECAUTIONS COULD RESULT IN ACCI-
DENTAL AIRBAG DEPLOYMENT AND POSSIBLE
PERSONAL INJURY.
WARNING: THE FRONT IMPACT SENSOR ENABLES
THE SYSTEM TO DEPLOY THE FRONT SUPPLE-
MENTAL RESTRAINTS. NEVER STRIKE OR DROP
THE FRONT IMPACT SENSOR, AS IT CAN DAMAGE
THE IMPACT SENSOR OR AFFECT ITS CALIBRA-
TION. IF AN IMPACT SENSOR IS ACCIDENTALLY
DROPPED DURING SERVICE, THE SENSOR MUST
BE SCRAPPED AND REPLACED WITH A NEW UNIT.
FAILURE TO OBSERVE THIS WARNING COULD
RESULT IN ACCIDENTAL, INCOMPLETE, OR
IMPROPER FRONT SUPPLEMENTAL RESTRAINT
DEPLOYMENT AND POSSIBLE OCCUPANT INJU-
RIES.
(1) Disconnect and isolate the battery negative
cable. Wait two minutes for the system capacitor to
discharge before further service.
(2) From the engine compartment, disconnect the
right or left headlamp and dash wire harness connec-
tor for the front impact sensor from the sensor con-
nector receptacle (Fig. 25).
Fig. 25 Front Impact Sensor Remove/Install (Right
Side Shown, Left Side Similar)
1 - BRACKET
2 - IMPACT SENSOR
3 - RADIATOR SUPPORT
4 - WIRE HARNESS CONNECTOR
5 - SCREW (2)
8O - 24 RESTRAINTSWJ
FRONT IMPACT SENSOR (Continued)
Page 562 of 2199
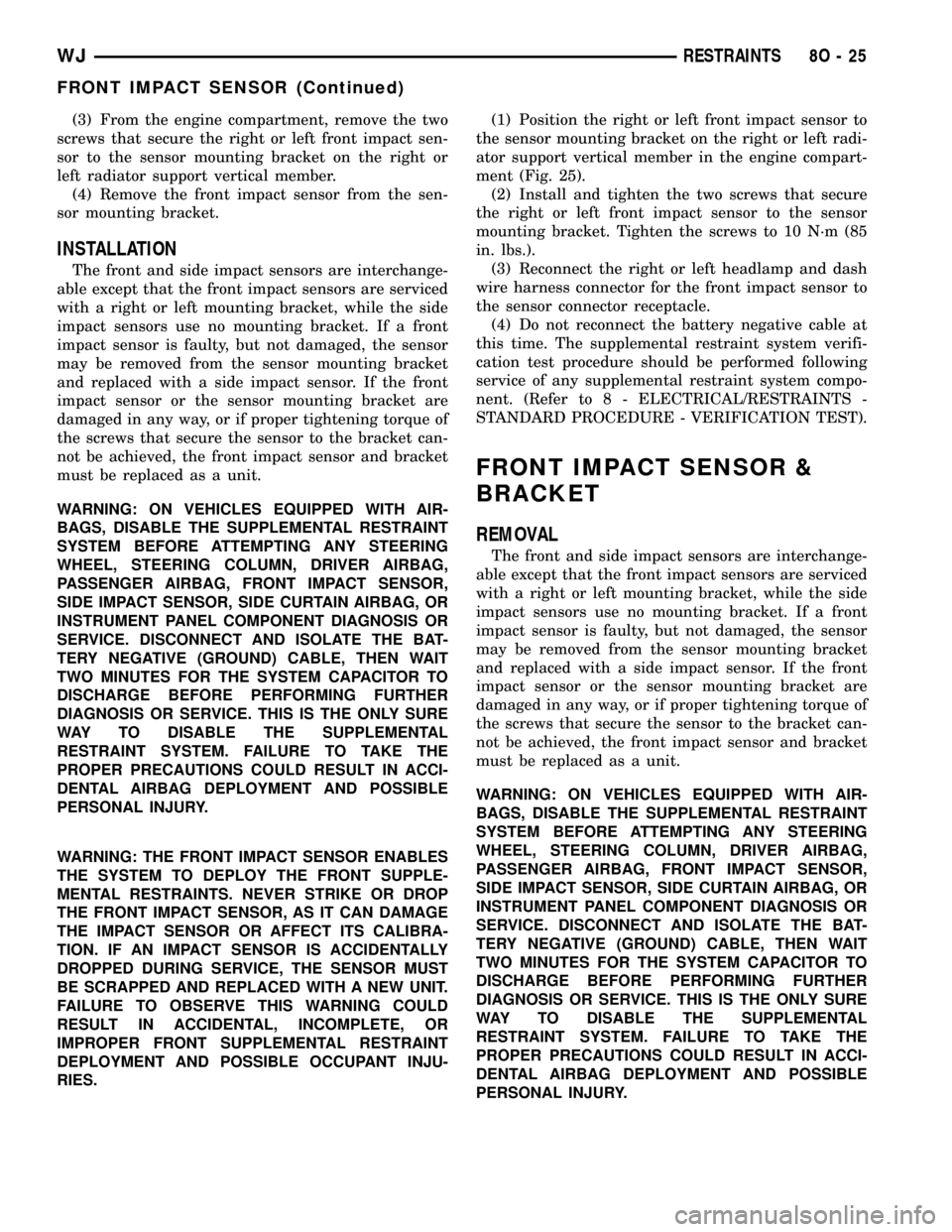
(3) From the engine compartment, remove the two
screws that secure the right or left front impact sen-
sor to the sensor mounting bracket on the right or
left radiator support vertical member.
(4) Remove the front impact sensor from the sen-
sor mounting bracket.
INSTALLATION
The front and side impact sensors are interchange-
able except that the front impact sensors are serviced
with a right or left mounting bracket, while the side
impact sensors use no mounting bracket. If a front
impact sensor is faulty, but not damaged, the sensor
may be removed from the sensor mounting bracket
and replaced with a side impact sensor. If the front
impact sensor or the sensor mounting bracket are
damaged in any way, or if proper tightening torque of
the screws that secure the sensor to the bracket can-
not be achieved, the front impact sensor and bracket
must be replaced as a unit.
WARNING: ON VEHICLES EQUIPPED WITH AIR-
BAGS, DISABLE THE SUPPLEMENTAL RESTRAINT
SYSTEM BEFORE ATTEMPTING ANY STEERING
WHEEL, STEERING COLUMN, DRIVER AIRBAG,
PASSENGER AIRBAG, FRONT IMPACT SENSOR,
SIDE IMPACT SENSOR, SIDE CURTAIN AIRBAG, OR
INSTRUMENT PANEL COMPONENT DIAGNOSIS OR
SERVICE. DISCONNECT AND ISOLATE THE BAT-
TERY NEGATIVE (GROUND) CABLE, THEN WAIT
TWO MINUTES FOR THE SYSTEM CAPACITOR TO
DISCHARGE BEFORE PERFORMING FURTHER
DIAGNOSIS OR SERVICE. THIS IS THE ONLY SURE
WAY TO DISABLE THE SUPPLEMENTAL
RESTRAINT SYSTEM. FAILURE TO TAKE THE
PROPER PRECAUTIONS COULD RESULT IN ACCI-
DENTAL AIRBAG DEPLOYMENT AND POSSIBLE
PERSONAL INJURY.
WARNING: THE FRONT IMPACT SENSOR ENABLES
THE SYSTEM TO DEPLOY THE FRONT SUPPLE-
MENTAL RESTRAINTS. NEVER STRIKE OR DROP
THE FRONT IMPACT SENSOR, AS IT CAN DAMAGE
THE IMPACT SENSOR OR AFFECT ITS CALIBRA-
TION. IF AN IMPACT SENSOR IS ACCIDENTALLY
DROPPED DURING SERVICE, THE SENSOR MUST
BE SCRAPPED AND REPLACED WITH A NEW UNIT.
FAILURE TO OBSERVE THIS WARNING COULD
RESULT IN ACCIDENTAL, INCOMPLETE, OR
IMPROPER FRONT SUPPLEMENTAL RESTRAINT
DEPLOYMENT AND POSSIBLE OCCUPANT INJU-
RIES.(1) Position the right or left front impact sensor to
the sensor mounting bracket on the right or left radi-
ator support vertical member in the engine compart-
ment (Fig. 25).
(2) Install and tighten the two screws that secure
the right or left front impact sensor to the sensor
mounting bracket. Tighten the screws to 10 N´m (85
in. lbs.).
(3) Reconnect the right or left headlamp and dash
wire harness connector for the front impact sensor to
the sensor connector receptacle.
(4) Do not reconnect the battery negative cable at
this time. The supplemental restraint system verifi-
cation test procedure should be performed following
service of any supplemental restraint system compo-
nent. (Refer to 8 - ELECTRICAL/RESTRAINTS -
STANDARD PROCEDURE - VERIFICATION TEST).
FRONT IMPACT SENSOR &
BRACKET
REMOVAL
The front and side impact sensors are interchange-
able except that the front impact sensors are serviced
with a right or left mounting bracket, while the side
impact sensors use no mounting bracket. If a front
impact sensor is faulty, but not damaged, the sensor
may be removed from the sensor mounting bracket
and replaced with a side impact sensor. If the front
impact sensor or the sensor mounting bracket are
damaged in any way, or if proper tightening torque of
the screws that secure the sensor to the bracket can-
not be achieved, the front impact sensor and bracket
must be replaced as a unit.
WARNING: ON VEHICLES EQUIPPED WITH AIR-
BAGS, DISABLE THE SUPPLEMENTAL RESTRAINT
SYSTEM BEFORE ATTEMPTING ANY STEERING
WHEEL, STEERING COLUMN, DRIVER AIRBAG,
PASSENGER AIRBAG, FRONT IMPACT SENSOR,
SIDE IMPACT SENSOR, SIDE CURTAIN AIRBAG, OR
INSTRUMENT PANEL COMPONENT DIAGNOSIS OR
SERVICE. DISCONNECT AND ISOLATE THE BAT-
TERY NEGATIVE (GROUND) CABLE, THEN WAIT
TWO MINUTES FOR THE SYSTEM CAPACITOR TO
DISCHARGE BEFORE PERFORMING FURTHER
DIAGNOSIS OR SERVICE. THIS IS THE ONLY SURE
WAY TO DISABLE THE SUPPLEMENTAL
RESTRAINT SYSTEM. FAILURE TO TAKE THE
PROPER PRECAUTIONS COULD RESULT IN ACCI-
DENTAL AIRBAG DEPLOYMENT AND POSSIBLE
PERSONAL INJURY.
WJRESTRAINTS 8O - 25
FRONT IMPACT SENSOR (Continued)
Page 563 of 2199
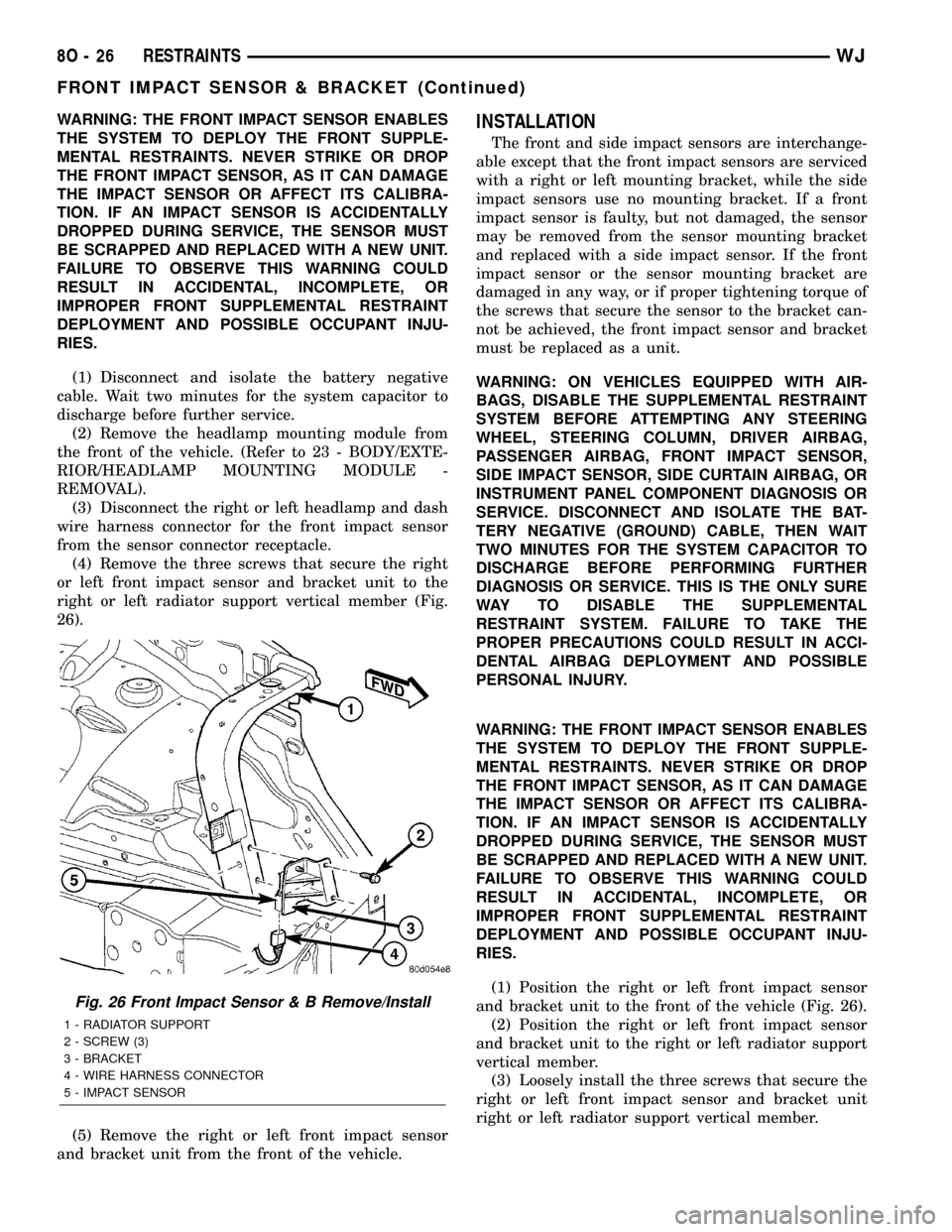
WARNING: THE FRONT IMPACT SENSOR ENABLES
THE SYSTEM TO DEPLOY THE FRONT SUPPLE-
MENTAL RESTRAINTS. NEVER STRIKE OR DROP
THE FRONT IMPACT SENSOR, AS IT CAN DAMAGE
THE IMPACT SENSOR OR AFFECT ITS CALIBRA-
TION. IF AN IMPACT SENSOR IS ACCIDENTALLY
DROPPED DURING SERVICE, THE SENSOR MUST
BE SCRAPPED AND REPLACED WITH A NEW UNIT.
FAILURE TO OBSERVE THIS WARNING COULD
RESULT IN ACCIDENTAL, INCOMPLETE, OR
IMPROPER FRONT SUPPLEMENTAL RESTRAINT
DEPLOYMENT AND POSSIBLE OCCUPANT INJU-
RIES.
(1) Disconnect and isolate the battery negative
cable. Wait two minutes for the system capacitor to
discharge before further service.
(2) Remove the headlamp mounting module from
the front of the vehicle. (Refer to 23 - BODY/EXTE-
RIOR/HEADLAMP MOUNTING MODULE -
REMOVAL).
(3) Disconnect the right or left headlamp and dash
wire harness connector for the front impact sensor
from the sensor connector receptacle.
(4) Remove the three screws that secure the right
or left front impact sensor and bracket unit to the
right or left radiator support vertical member (Fig.
26).
(5) Remove the right or left front impact sensor
and bracket unit from the front of the vehicle.INSTALLATION
The front and side impact sensors are interchange-
able except that the front impact sensors are serviced
with a right or left mounting bracket, while the side
impact sensors use no mounting bracket. If a front
impact sensor is faulty, but not damaged, the sensor
may be removed from the sensor mounting bracket
and replaced with a side impact sensor. If the front
impact sensor or the sensor mounting bracket are
damaged in any way, or if proper tightening torque of
the screws that secure the sensor to the bracket can-
not be achieved, the front impact sensor and bracket
must be replaced as a unit.
WARNING: ON VEHICLES EQUIPPED WITH AIR-
BAGS, DISABLE THE SUPPLEMENTAL RESTRAINT
SYSTEM BEFORE ATTEMPTING ANY STEERING
WHEEL, STEERING COLUMN, DRIVER AIRBAG,
PASSENGER AIRBAG, FRONT IMPACT SENSOR,
SIDE IMPACT SENSOR, SIDE CURTAIN AIRBAG, OR
INSTRUMENT PANEL COMPONENT DIAGNOSIS OR
SERVICE. DISCONNECT AND ISOLATE THE BAT-
TERY NEGATIVE (GROUND) CABLE, THEN WAIT
TWO MINUTES FOR THE SYSTEM CAPACITOR TO
DISCHARGE BEFORE PERFORMING FURTHER
DIAGNOSIS OR SERVICE. THIS IS THE ONLY SURE
WAY TO DISABLE THE SUPPLEMENTAL
RESTRAINT SYSTEM. FAILURE TO TAKE THE
PROPER PRECAUTIONS COULD RESULT IN ACCI-
DENTAL AIRBAG DEPLOYMENT AND POSSIBLE
PERSONAL INJURY.
WARNING: THE FRONT IMPACT SENSOR ENABLES
THE SYSTEM TO DEPLOY THE FRONT SUPPLE-
MENTAL RESTRAINTS. NEVER STRIKE OR DROP
THE FRONT IMPACT SENSOR, AS IT CAN DAMAGE
THE IMPACT SENSOR OR AFFECT ITS CALIBRA-
TION. IF AN IMPACT SENSOR IS ACCIDENTALLY
DROPPED DURING SERVICE, THE SENSOR MUST
BE SCRAPPED AND REPLACED WITH A NEW UNIT.
FAILURE TO OBSERVE THIS WARNING COULD
RESULT IN ACCIDENTAL, INCOMPLETE, OR
IMPROPER FRONT SUPPLEMENTAL RESTRAINT
DEPLOYMENT AND POSSIBLE OCCUPANT INJU-
RIES.
(1) Position the right or left front impact sensor
and bracket unit to the front of the vehicle (Fig. 26).
(2) Position the right or left front impact sensor
and bracket unit to the right or left radiator support
vertical member.
(3) Loosely install the three screws that secure the
right or left front impact sensor and bracket unit
right or left radiator support vertical member.
Fig. 26 Front Impact Sensor & B Remove/Install
1 - RADIATOR SUPPORT
2 - SCREW (3)
3 - BRACKET
4 - WIRE HARNESS CONNECTOR
5 - IMPACT SENSOR
8O - 26 RESTRAINTSWJ
FRONT IMPACT SENSOR & BRACKET (Continued)
Page 582 of 2199
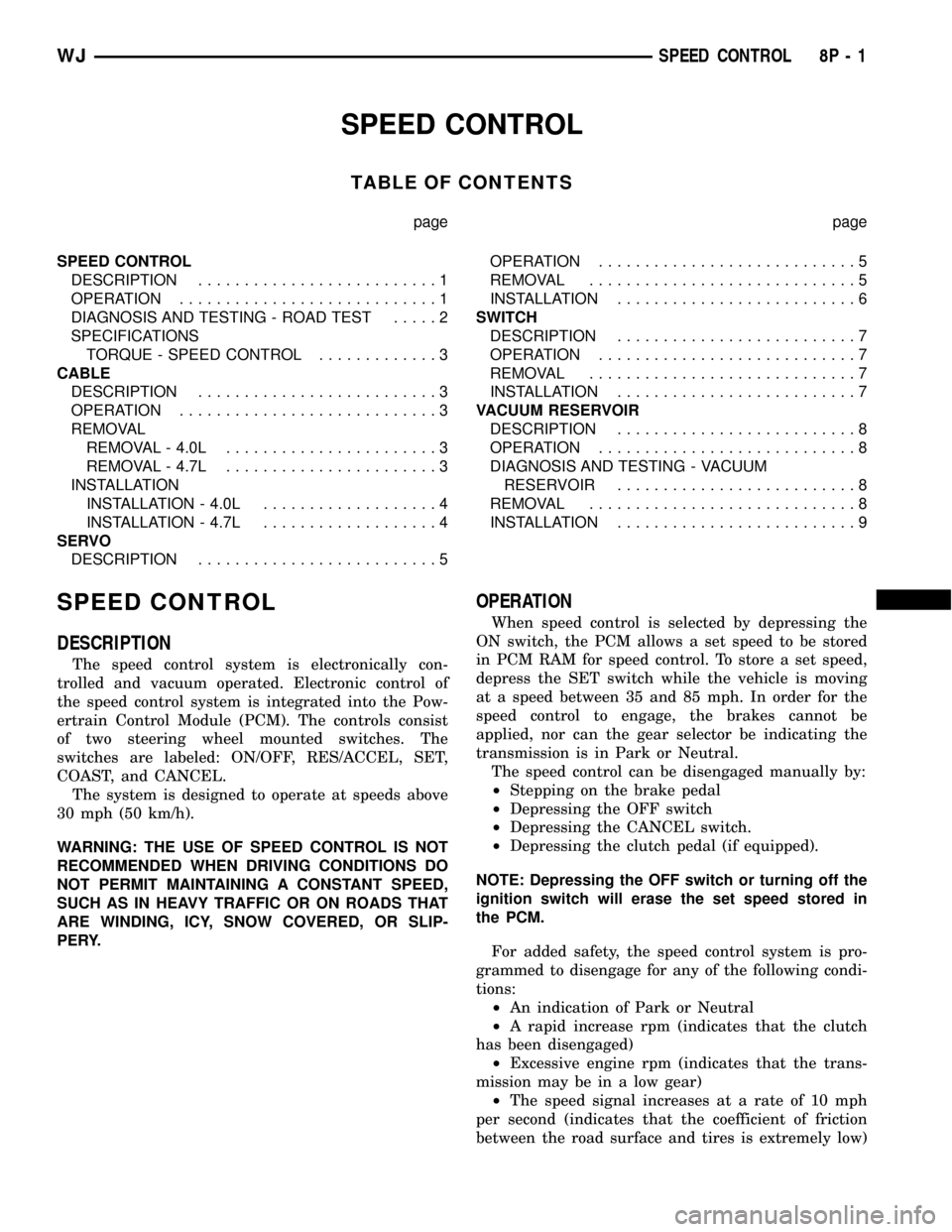
SPEED CONTROL
TABLE OF CONTENTS
page page
SPEED CONTROL
DESCRIPTION..........................1
OPERATION............................1
DIAGNOSIS AND TESTING - ROAD TEST.....2
SPECIFICATIONS
TORQUE - SPEED CONTROL.............3
CABLE
DESCRIPTION..........................3
OPERATION............................3
REMOVAL
REMOVAL - 4.0L.......................3
REMOVAL - 4.7L.......................3
INSTALLATION
INSTALLATION - 4.0L...................4
INSTALLATION - 4.7L...................4
SERVO
DESCRIPTION..........................5OPERATION............................5
REMOVAL.............................5
INSTALLATION..........................6
SWITCH
DESCRIPTION..........................7
OPERATION............................7
REMOVAL.............................7
INSTALLATION..........................7
VACUUM RESERVOIR
DESCRIPTION..........................8
OPERATION............................8
DIAGNOSIS AND TESTING - VACUUM
RESERVOIR..........................8
REMOVAL.............................8
INSTALLATION..........................9
SPEED CONTROL
DESCRIPTION
The speed control system is electronically con-
trolled and vacuum operated. Electronic control of
the speed control system is integrated into the Pow-
ertrain Control Module (PCM). The controls consist
of two steering wheel mounted switches. The
switches are labeled: ON/OFF, RES/ACCEL, SET,
COAST, and CANCEL.
The system is designed to operate at speeds above
30 mph (50 km/h).
WARNING: THE USE OF SPEED CONTROL IS NOT
RECOMMENDED WHEN DRIVING CONDITIONS DO
NOT PERMIT MAINTAINING A CONSTANT SPEED,
SUCH AS IN HEAVY TRAFFIC OR ON ROADS THAT
ARE WINDING, ICY, SNOW COVERED, OR SLIP-
PERY.
OPERATION
When speed control is selected by depressing the
ON switch, the PCM allows a set speed to be stored
in PCM RAM for speed control. To store a set speed,
depress the SET switch while the vehicle is moving
at a speed between 35 and 85 mph. In order for the
speed control to engage, the brakes cannot be
applied, nor can the gear selector be indicating the
transmission is in Park or Neutral.
The speed control can be disengaged manually by:
²Stepping on the brake pedal
²Depressing the OFF switch
²Depressing the CANCEL switch.
²Depressing the clutch pedal (if equipped).
NOTE: Depressing the OFF switch or turning off the
ignition switch will erase the set speed stored in
the PCM.
For added safety, the speed control system is pro-
grammed to disengage for any of the following condi-
tions:
²An indication of Park or Neutral
²A rapid increase rpm (indicates that the clutch
has been disengaged)
²Excessive engine rpm (indicates that the trans-
mission may be in a low gear)
²The speed signal increases at a rate of 10 mph
per second (indicates that the coefficient of friction
between the road surface and tires is extremely low)
WJSPEED CONTROL 8P - 1