heater JEEP GRAND CHEROKEE 2002 WJ / 2.G Workshop Manual
[x] Cancel search | Manufacturer: JEEP, Model Year: 2002, Model line: GRAND CHEROKEE, Model: JEEP GRAND CHEROKEE 2002 WJ / 2.GPages: 2199, PDF Size: 76.01 MB
Page 2105 of 2199
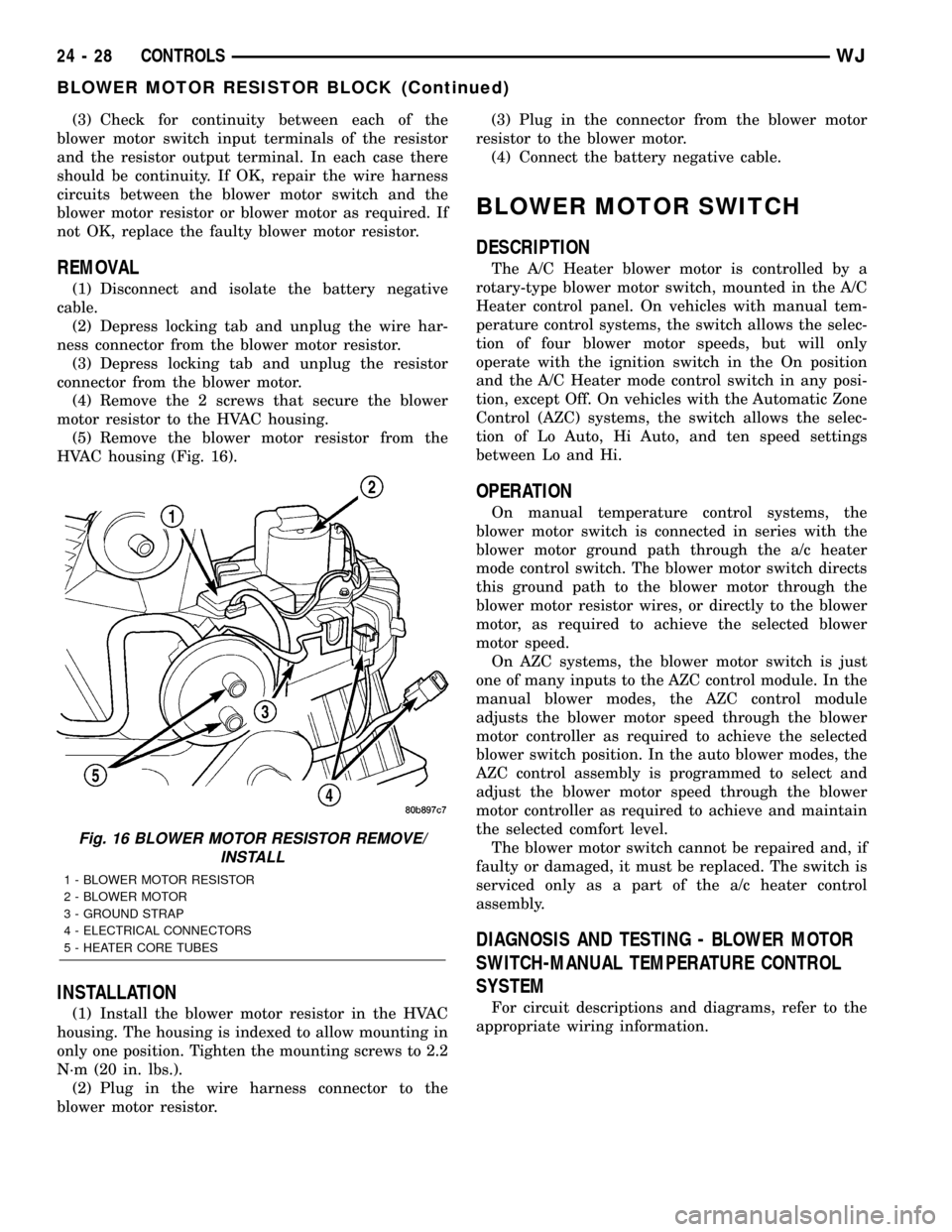
(3) Check for continuity between each of the
blower motor switch input terminals of the resistor
and the resistor output terminal. In each case there
should be continuity. If OK, repair the wire harness
circuits between the blower motor switch and the
blower motor resistor or blower motor as required. If
not OK, replace the faulty blower motor resistor.
REMOVAL
(1) Disconnect and isolate the battery negative
cable.
(2) Depress locking tab and unplug the wire har-
ness connector from the blower motor resistor.
(3) Depress locking tab and unplug the resistor
connector from the blower motor.
(4) Remove the 2 screws that secure the blower
motor resistor to the HVAC housing.
(5) Remove the blower motor resistor from the
HVAC housing (Fig. 16).
INSTALLATION
(1) Install the blower motor resistor in the HVAC
housing. The housing is indexed to allow mounting in
only one position. Tighten the mounting screws to 2.2
N´m (20 in. lbs.).
(2) Plug in the wire harness connector to the
blower motor resistor.(3) Plug in the connector from the blower motor
resistor to the blower motor.
(4) Connect the battery negative cable.
BLOWER MOTOR SWITCH
DESCRIPTION
The A/C Heater blower motor is controlled by a
rotary-type blower motor switch, mounted in the A/C
Heater control panel. On vehicles with manual tem-
perature control systems, the switch allows the selec-
tion of four blower motor speeds, but will only
operate with the ignition switch in the On position
and the A/C Heater mode control switch in any posi-
tion, except Off. On vehicles with the Automatic Zone
Control (AZC) systems, the switch allows the selec-
tion of Lo Auto, Hi Auto, and ten speed settings
between Lo and Hi.
OPERATION
On manual temperature control systems, the
blower motor switch is connected in series with the
blower motor ground path through the a/c heater
mode control switch. The blower motor switch directs
this ground path to the blower motor through the
blower motor resistor wires, or directly to the blower
motor, as required to achieve the selected blower
motor speed.
On AZC systems, the blower motor switch is just
one of many inputs to the AZC control module. In the
manual blower modes, the AZC control module
adjusts the blower motor speed through the blower
motor controller as required to achieve the selected
blower switch position. In the auto blower modes, the
AZC control assembly is programmed to select and
adjust the blower motor speed through the blower
motor controller as required to achieve and maintain
the selected comfort level.
The blower motor switch cannot be repaired and, if
faulty or damaged, it must be replaced. The switch is
serviced only as a part of the a/c heater control
assembly.
DIAGNOSIS AND TESTING - BLOWER MOTOR
SWITCH-MANUAL TEMPERATURE CONTROL
SYSTEM
For circuit descriptions and diagrams, refer to the
appropriate wiring information.
Fig. 16 BLOWER MOTOR RESISTOR REMOVE/
INSTALL
1 - BLOWER MOTOR RESISTOR
2 - BLOWER MOTOR
3 - GROUND STRAP
4 - ELECTRICAL CONNECTORS
5 - HEATER CORE TUBES
24 - 28 CONTROLSWJ
BLOWER MOTOR RESISTOR BLOCK (Continued)
Page 2106 of 2199
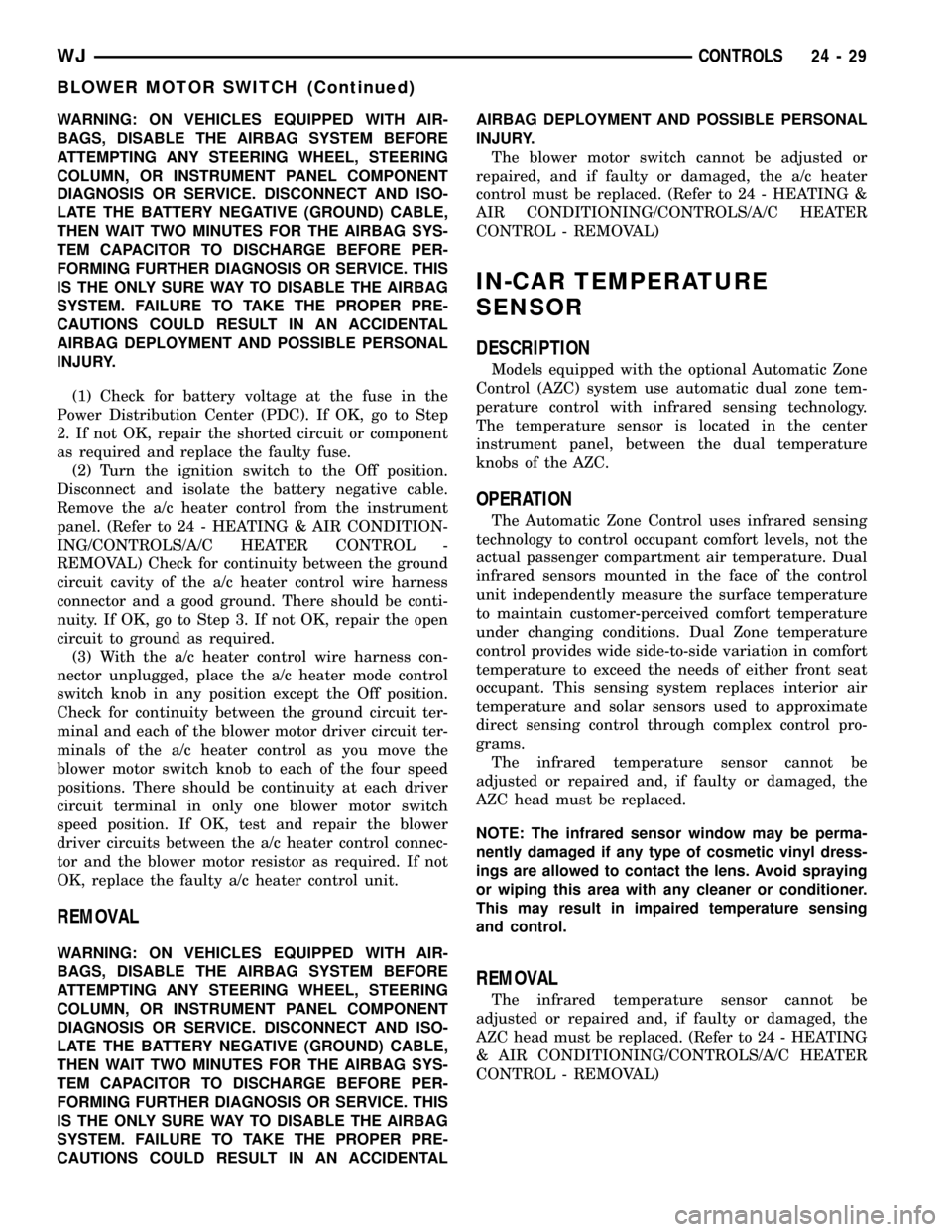
WARNING: ON VEHICLES EQUIPPED WITH AIR-
BAGS, DISABLE THE AIRBAG SYSTEM BEFORE
ATTEMPTING ANY STEERING WHEEL, STEERING
COLUMN, OR INSTRUMENT PANEL COMPONENT
DIAGNOSIS OR SERVICE. DISCONNECT AND ISO-
LATE THE BATTERY NEGATIVE (GROUND) CABLE,
THEN WAIT TWO MINUTES FOR THE AIRBAG SYS-
TEM CAPACITOR TO DISCHARGE BEFORE PER-
FORMING FURTHER DIAGNOSIS OR SERVICE. THIS
IS THE ONLY SURE WAY TO DISABLE THE AIRBAG
SYSTEM. FAILURE TO TAKE THE PROPER PRE-
CAUTIONS COULD RESULT IN AN ACCIDENTAL
AIRBAG DEPLOYMENT AND POSSIBLE PERSONAL
INJURY.
(1) Check for battery voltage at the fuse in the
Power Distribution Center (PDC). If OK, go to Step
2. If not OK, repair the shorted circuit or component
as required and replace the faulty fuse.
(2) Turn the ignition switch to the Off position.
Disconnect and isolate the battery negative cable.
Remove the a/c heater control from the instrument
panel. (Refer to 24 - HEATING & AIR CONDITION-
ING/CONTROLS/A/C HEATER CONTROL -
REMOVAL) Check for continuity between the ground
circuit cavity of the a/c heater control wire harness
connector and a good ground. There should be conti-
nuity. If OK, go to Step 3. If not OK, repair the open
circuit to ground as required.
(3) With the a/c heater control wire harness con-
nector unplugged, place the a/c heater mode control
switch knob in any position except the Off position.
Check for continuity between the ground circuit ter-
minal and each of the blower motor driver circuit ter-
minals of the a/c heater control as you move the
blower motor switch knob to each of the four speed
positions. There should be continuity at each driver
circuit terminal in only one blower motor switch
speed position. If OK, test and repair the blower
driver circuits between the a/c heater control connec-
tor and the blower motor resistor as required. If not
OK, replace the faulty a/c heater control unit.
REMOVAL
WARNING: ON VEHICLES EQUIPPED WITH AIR-
BAGS, DISABLE THE AIRBAG SYSTEM BEFORE
ATTEMPTING ANY STEERING WHEEL, STEERING
COLUMN, OR INSTRUMENT PANEL COMPONENT
DIAGNOSIS OR SERVICE. DISCONNECT AND ISO-
LATE THE BATTERY NEGATIVE (GROUND) CABLE,
THEN WAIT TWO MINUTES FOR THE AIRBAG SYS-
TEM CAPACITOR TO DISCHARGE BEFORE PER-
FORMING FURTHER DIAGNOSIS OR SERVICE. THIS
IS THE ONLY SURE WAY TO DISABLE THE AIRBAG
SYSTEM. FAILURE TO TAKE THE PROPER PRE-
CAUTIONS COULD RESULT IN AN ACCIDENTALAIRBAG DEPLOYMENT AND POSSIBLE PERSONAL
INJURY.
The blower motor switch cannot be adjusted or
repaired, and if faulty or damaged, the a/c heater
control must be replaced. (Refer to 24 - HEATING &
AIR CONDITIONING/CONTROLS/A/C HEATER
CONTROL - REMOVAL)
IN-CAR TEMPERATURE
SENSOR
DESCRIPTION
Models equipped with the optional Automatic Zone
Control (AZC) system use automatic dual zone tem-
perature control with infrared sensing technology.
The temperature sensor is located in the center
instrument panel, between the dual temperature
knobs of the AZC.
OPERATION
The Automatic Zone Control uses infrared sensing
technology to control occupant comfort levels, not the
actual passenger compartment air temperature. Dual
infrared sensors mounted in the face of the control
unit independently measure the surface temperature
to maintain customer-perceived comfort temperature
under changing conditions. Dual Zone temperature
control provides wide side-to-side variation in comfort
temperature to exceed the needs of either front seat
occupant. This sensing system replaces interior air
temperature and solar sensors used to approximate
direct sensing control through complex control pro-
grams.
The infrared temperature sensor cannot be
adjusted or repaired and, if faulty or damaged, the
AZC head must be replaced.
NOTE: The infrared sensor window may be perma-
nently damaged if any type of cosmetic vinyl dress-
ings are allowed to contact the lens. Avoid spraying
or wiping this area with any cleaner or conditioner.
This may result in impaired temperature sensing
and control.
REMOVAL
The infrared temperature sensor cannot be
adjusted or repaired and, if faulty or damaged, the
AZC head must be replaced. (Refer to 24 - HEATING
& AIR CONDITIONING/CONTROLS/A/C HEATER
CONTROL - REMOVAL)
WJCONTROLS 24 - 29
BLOWER MOTOR SWITCH (Continued)
Page 2111 of 2199

INSTALLATION
INSTALLATION - RECIRCULATION DOOR
VACUUM ACTUATOR
(1) Install the recirculation door vacuum actuator
on the HVAC housing and tighten the mounting
screws to 2.2 N´m (20 in. lbs.).
(2) Engage the recirculation door actuating rod
with the recirculation door lever.
(3) Engage the recirculation door pivot connection
with the door pivot pin.
(4) Plug in the vacuum harness connector to the
recirculation door vacuum actuator.
(5) Install the instrument panel in the vehicle.
Refer to Instrument Panel System for the procedures.
INSTALLATION - RECIRCULATION DOOR
ELECTRIC ACTUATOR
(1) Install the recirculation door actuator on the
recirculation door housing and tighten the mounting
screws to 2.2 N´m (20 in. lbs.).
(2) Install the recirculation door housing on the
HVAC unit and tighten the mounting screws to 2.2
N´m (20 in. lbs.).
(3) Plug in the wire harness connector to the recir-
culation door actuator.
(4) Install the instrument panel in the vehicle.
Refer to Instrument Panel System for the procedures.
VACUUM CHECK VALVE
DESCRIPTION
Two vacuum check valves (non AZC only) are
installed on the vacuum supply system. One is on the
accessory vacuum supply line in the engine compart-
ment, near the vacuum tap on the engine intake
manifold. A second vacuum check valve is located on
the bottom of the HVAC unit behind the passenger
front floor duct on the black vacuum line. The vac-
uum check valves are designed to allow vacuum to
flow in only one direction through the accessory vac-
uum supply circuits.
OPERATION
The use of a vacuum check valve helps to maintain
the system vacuum needed to retain the selected A/C
Heater mode settings. The check valve will prevent
the engine from bleeding down system vacuum
through the intake manifold during extended heavy
engine load (low engine vacuum) operation.
The vacuum check valve cannot be repaired and, if
faulty or damaged, it must be replaced.
REMOVAL
(1) Unplug the HVAC vacuum supply line connec-
tor at the vacuum check valve near the engine intake
manifold vacuum adapter fitting.
(2) Note the orientation of the check valve in the
vacuum supply line for correct installation.
(3) Unplug the vacuum check valve from the vac-
uum supply line fittings.
INSTALLATION
(1) Plug in the vacuum check valve at the vacuum
supply line fittings, noting the orientation of the
check valve in the vacuum supply line for correct
installation.
(2) Plug in the HVAC vacuum supply line connec-
tor at the vacuum check valve near the engine intake
manifold vacuum adapter fitting.
VACUUM RESERVOIR
DESCRIPTION
The vacuum reservoir is mounted in the right front
of the vehicle behind the headlamp mounting module
(Fig. 22). The headlamp mounting module and head-
lamp assembly must be removed from the vehicle to
access the vacuum reservoir for service. Refer to
Lamps/Lighting for the procedures.
OPERATION
Engine vacuum is stored in the vacuum reservoir.
The stored vacuum is used to operate the vacuum-
Fig. 21 RECIRCULATION DOOR HOUSING
1 - RECIRCULATION DOOR HOUSING
2 - ATTACHING SCREWS
24 - 34 CONTROLSWJ
RECIRCULATION DOOR ACTUATOR (Continued)
Page 2114 of 2199
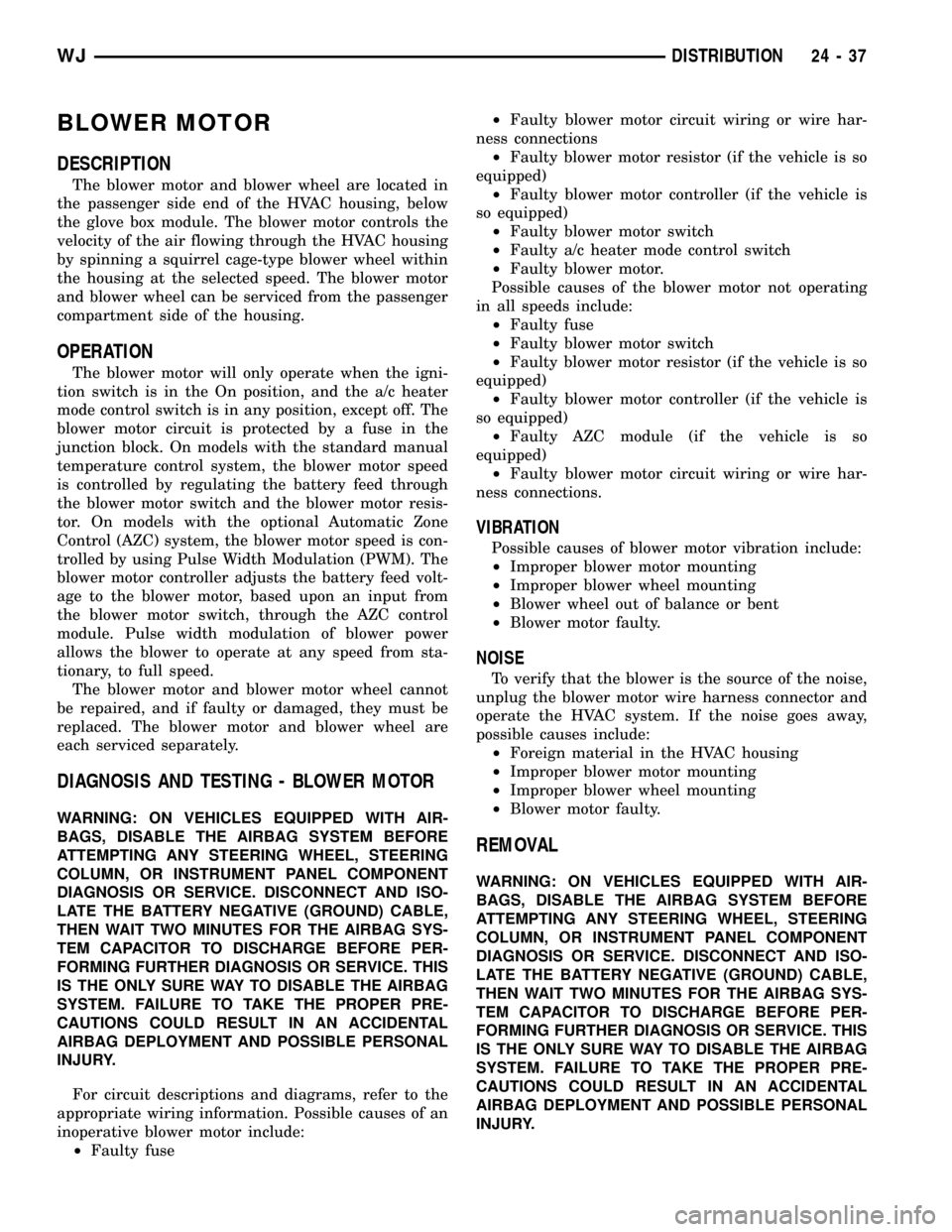
BLOWER MOTOR
DESCRIPTION
The blower motor and blower wheel are located in
the passenger side end of the HVAC housing, below
the glove box module. The blower motor controls the
velocity of the air flowing through the HVAC housing
by spinning a squirrel cage-type blower wheel within
the housing at the selected speed. The blower motor
and blower wheel can be serviced from the passenger
compartment side of the housing.
OPERATION
The blower motor will only operate when the igni-
tion switch is in the On position, and the a/c heater
mode control switch is in any position, except off. The
blower motor circuit is protected by a fuse in the
junction block. On models with the standard manual
temperature control system, the blower motor speed
is controlled by regulating the battery feed through
the blower motor switch and the blower motor resis-
tor. On models with the optional Automatic Zone
Control (AZC) system, the blower motor speed is con-
trolled by using Pulse Width Modulation (PWM). The
blower motor controller adjusts the battery feed volt-
age to the blower motor, based upon an input from
the blower motor switch, through the AZC control
module. Pulse width modulation of blower power
allows the blower to operate at any speed from sta-
tionary, to full speed.
The blower motor and blower motor wheel cannot
be repaired, and if faulty or damaged, they must be
replaced. The blower motor and blower wheel are
each serviced separately.
DIAGNOSIS AND TESTING - BLOWER MOTOR
WARNING: ON VEHICLES EQUIPPED WITH AIR-
BAGS, DISABLE THE AIRBAG SYSTEM BEFORE
ATTEMPTING ANY STEERING WHEEL, STEERING
COLUMN, OR INSTRUMENT PANEL COMPONENT
DIAGNOSIS OR SERVICE. DISCONNECT AND ISO-
LATE THE BATTERY NEGATIVE (GROUND) CABLE,
THEN WAIT TWO MINUTES FOR THE AIRBAG SYS-
TEM CAPACITOR TO DISCHARGE BEFORE PER-
FORMING FURTHER DIAGNOSIS OR SERVICE. THIS
IS THE ONLY SURE WAY TO DISABLE THE AIRBAG
SYSTEM. FAILURE TO TAKE THE PROPER PRE-
CAUTIONS COULD RESULT IN AN ACCIDENTAL
AIRBAG DEPLOYMENT AND POSSIBLE PERSONAL
INJURY.
For circuit descriptions and diagrams, refer to the
appropriate wiring information. Possible causes of an
inoperative blower motor include:
²Faulty fuse²Faulty blower motor circuit wiring or wire har-
ness connections
²Faulty blower motor resistor (if the vehicle is so
equipped)
²Faulty blower motor controller (if the vehicle is
so equipped)
²Faulty blower motor switch
²Faulty a/c heater mode control switch
²Faulty blower motor.
Possible causes of the blower motor not operating
in all speeds include:
²Faulty fuse
²Faulty blower motor switch
²Faulty blower motor resistor (if the vehicle is so
equipped)
²Faulty blower motor controller (if the vehicle is
so equipped)
²Faulty AZC module (if the vehicle is so
equipped)
²Faulty blower motor circuit wiring or wire har-
ness connections.
VIBRATION
Possible causes of blower motor vibration include:
²Improper blower motor mounting
²Improper blower wheel mounting
²Blower wheel out of balance or bent
²Blower motor faulty.
NOISE
To verify that the blower is the source of the noise,
unplug the blower motor wire harness connector and
operate the HVAC system. If the noise goes away,
possible causes include:
²Foreign material in the HVAC housing
²Improper blower motor mounting
²Improper blower wheel mounting
²Blower motor faulty.
REMOVAL
WARNING: ON VEHICLES EQUIPPED WITH AIR-
BAGS, DISABLE THE AIRBAG SYSTEM BEFORE
ATTEMPTING ANY STEERING WHEEL, STEERING
COLUMN, OR INSTRUMENT PANEL COMPONENT
DIAGNOSIS OR SERVICE. DISCONNECT AND ISO-
LATE THE BATTERY NEGATIVE (GROUND) CABLE,
THEN WAIT TWO MINUTES FOR THE AIRBAG SYS-
TEM CAPACITOR TO DISCHARGE BEFORE PER-
FORMING FURTHER DIAGNOSIS OR SERVICE. THIS
IS THE ONLY SURE WAY TO DISABLE THE AIRBAG
SYSTEM. FAILURE TO TAKE THE PROPER PRE-
CAUTIONS COULD RESULT IN AN ACCIDENTAL
AIRBAG DEPLOYMENT AND POSSIBLE PERSONAL
INJURY.
WJDISTRIBUTION 24 - 37
Page 2115 of 2199
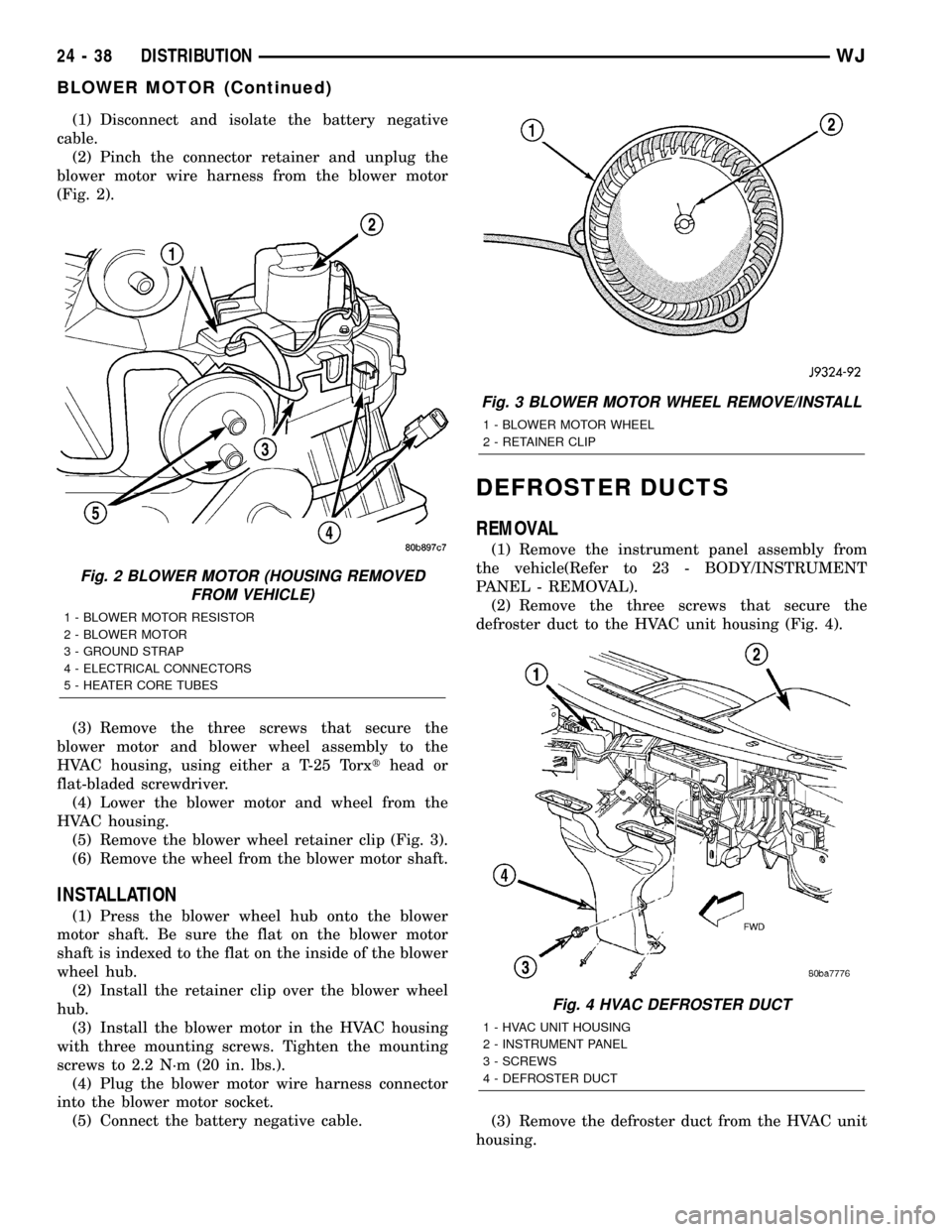
(1) Disconnect and isolate the battery negative
cable.
(2) Pinch the connector retainer and unplug the
blower motor wire harness from the blower motor
(Fig. 2).
(3) Remove the three screws that secure the
blower motor and blower wheel assembly to the
HVAC housing, using either a T-25 Torxthead or
flat-bladed screwdriver.
(4) Lower the blower motor and wheel from the
HVAC housing.
(5) Remove the blower wheel retainer clip (Fig. 3).
(6) Remove the wheel from the blower motor shaft.
INSTALLATION
(1) Press the blower wheel hub onto the blower
motor shaft. Be sure the flat on the blower motor
shaft is indexed to the flat on the inside of the blower
wheel hub.
(2) Install the retainer clip over the blower wheel
hub.
(3) Install the blower motor in the HVAC housing
with three mounting screws. Tighten the mounting
screws to 2.2 N´m (20 in. lbs.).
(4) Plug the blower motor wire harness connector
into the blower motor socket.
(5) Connect the battery negative cable.
DEFROSTER DUCTS
REMOVAL
(1) Remove the instrument panel assembly from
the vehicle(Refer to 23 - BODY/INSTRUMENT
PANEL - REMOVAL).
(2) Remove the three screws that secure the
defroster duct to the HVAC unit housing (Fig. 4).
(3) Remove the defroster duct from the HVAC unit
housing.
Fig. 2 BLOWER MOTOR (HOUSING REMOVED
FROM VEHICLE)
1 - BLOWER MOTOR RESISTOR
2 - BLOWER MOTOR
3 - GROUND STRAP
4 - ELECTRICAL CONNECTORS
5 - HEATER CORE TUBES
Fig. 3 BLOWER MOTOR WHEEL REMOVE/INSTALL
1 - BLOWER MOTOR WHEEL
2 - RETAINER CLIP
Fig. 4 HVAC DEFROSTER DUCT
1 - HVAC UNIT HOUSING
2 - INSTRUMENT PANEL
3 - SCREWS
4 - DEFROSTER DUCT
24 - 38 DISTRIBUTIONWJ
BLOWER MOTOR (Continued)
Page 2118 of 2199
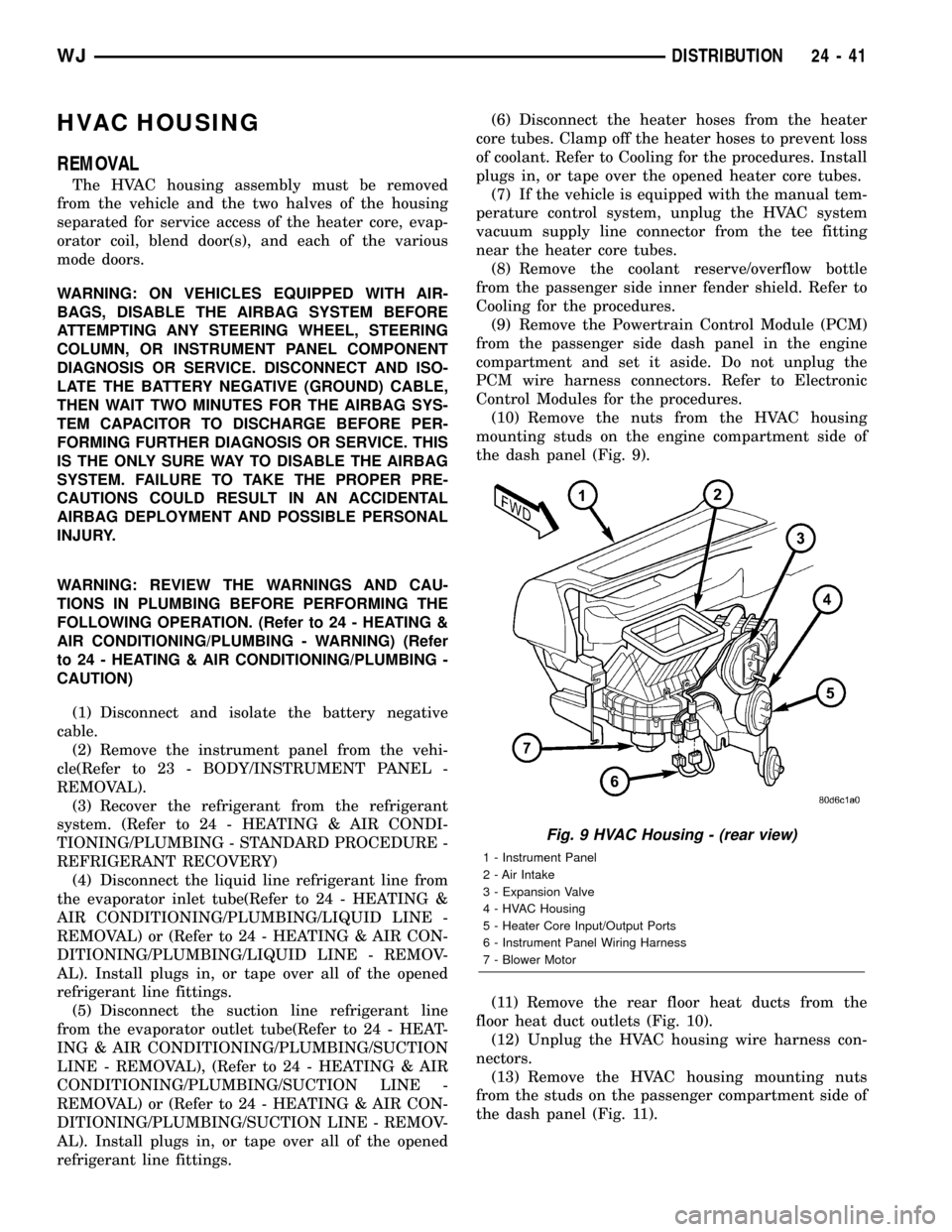
HVAC HOUSING
REMOVAL
The HVAC housing assembly must be removed
from the vehicle and the two halves of the housing
separated for service access of the heater core, evap-
orator coil, blend door(s), and each of the various
mode doors.
WARNING: ON VEHICLES EQUIPPED WITH AIR-
BAGS, DISABLE THE AIRBAG SYSTEM BEFORE
ATTEMPTING ANY STEERING WHEEL, STEERING
COLUMN, OR INSTRUMENT PANEL COMPONENT
DIAGNOSIS OR SERVICE. DISCONNECT AND ISO-
LATE THE BATTERY NEGATIVE (GROUND) CABLE,
THEN WAIT TWO MINUTES FOR THE AIRBAG SYS-
TEM CAPACITOR TO DISCHARGE BEFORE PER-
FORMING FURTHER DIAGNOSIS OR SERVICE. THIS
IS THE ONLY SURE WAY TO DISABLE THE AIRBAG
SYSTEM. FAILURE TO TAKE THE PROPER PRE-
CAUTIONS COULD RESULT IN AN ACCIDENTAL
AIRBAG DEPLOYMENT AND POSSIBLE PERSONAL
INJURY.
WARNING: REVIEW THE WARNINGS AND CAU-
TIONS IN PLUMBING BEFORE PERFORMING THE
FOLLOWING OPERATION. (Refer to 24 - HEATING &
AIR CONDITIONING/PLUMBING - WARNING) (Refer
to 24 - HEATING & AIR CONDITIONING/PLUMBING -
CAUTION)
(1) Disconnect and isolate the battery negative
cable.
(2) Remove the instrument panel from the vehi-
cle(Refer to 23 - BODY/INSTRUMENT PANEL -
REMOVAL).
(3) Recover the refrigerant from the refrigerant
system. (Refer to 24 - HEATING & AIR CONDI-
TIONING/PLUMBING - STANDARD PROCEDURE -
REFRIGERANT RECOVERY)
(4) Disconnect the liquid line refrigerant line from
the evaporator inlet tube(Refer to 24 - HEATING &
AIR CONDITIONING/PLUMBING/LIQUID LINE -
REMOVAL) or (Refer to 24 - HEATING & AIR CON-
DITIONING/PLUMBING/LIQUID LINE - REMOV-
AL). Install plugs in, or tape over all of the opened
refrigerant line fittings.
(5) Disconnect the suction line refrigerant line
from the evaporator outlet tube(Refer to 24 - HEAT-
ING & AIR CONDITIONING/PLUMBING/SUCTION
LINE - REMOVAL), (Refer to 24 - HEATING & AIR
CONDITIONING/PLUMBING/SUCTION LINE -
REMOVAL) or (Refer to 24 - HEATING & AIR CON-
DITIONING/PLUMBING/SUCTION LINE - REMOV-
AL). Install plugs in, or tape over all of the opened
refrigerant line fittings.(6) Disconnect the heater hoses from the heater
core tubes. Clamp off the heater hoses to prevent loss
of coolant. Refer to Cooling for the procedures. Install
plugs in, or tape over the opened heater core tubes.
(7) If the vehicle is equipped with the manual tem-
perature control system, unplug the HVAC system
vacuum supply line connector from the tee fitting
near the heater core tubes.
(8) Remove the coolant reserve/overflow bottle
from the passenger side inner fender shield. Refer to
Cooling for the procedures.
(9) Remove the Powertrain Control Module (PCM)
from the passenger side dash panel in the engine
compartment and set it aside. Do not unplug the
PCM wire harness connectors. Refer to Electronic
Control Modules for the procedures.
(10) Remove the nuts from the HVAC housing
mounting studs on the engine compartment side of
the dash panel (Fig. 9).
(11) Remove the rear floor heat ducts from the
floor heat duct outlets (Fig. 10).
(12) Unplug the HVAC housing wire harness con-
nectors.
(13) Remove the HVAC housing mounting nuts
from the studs on the passenger compartment side of
the dash panel (Fig. 11).
Fig. 9 HVAC Housing - (rear view)
1 - Instrument Panel
2 - Air Intake
3 - Expansion Valve
4 - HVAC Housing
5 - Heater Core Input/Output Ports
6 - Instrument Panel Wiring Harness
7 - Blower Motor
WJDISTRIBUTION 24 - 41
Page 2119 of 2199
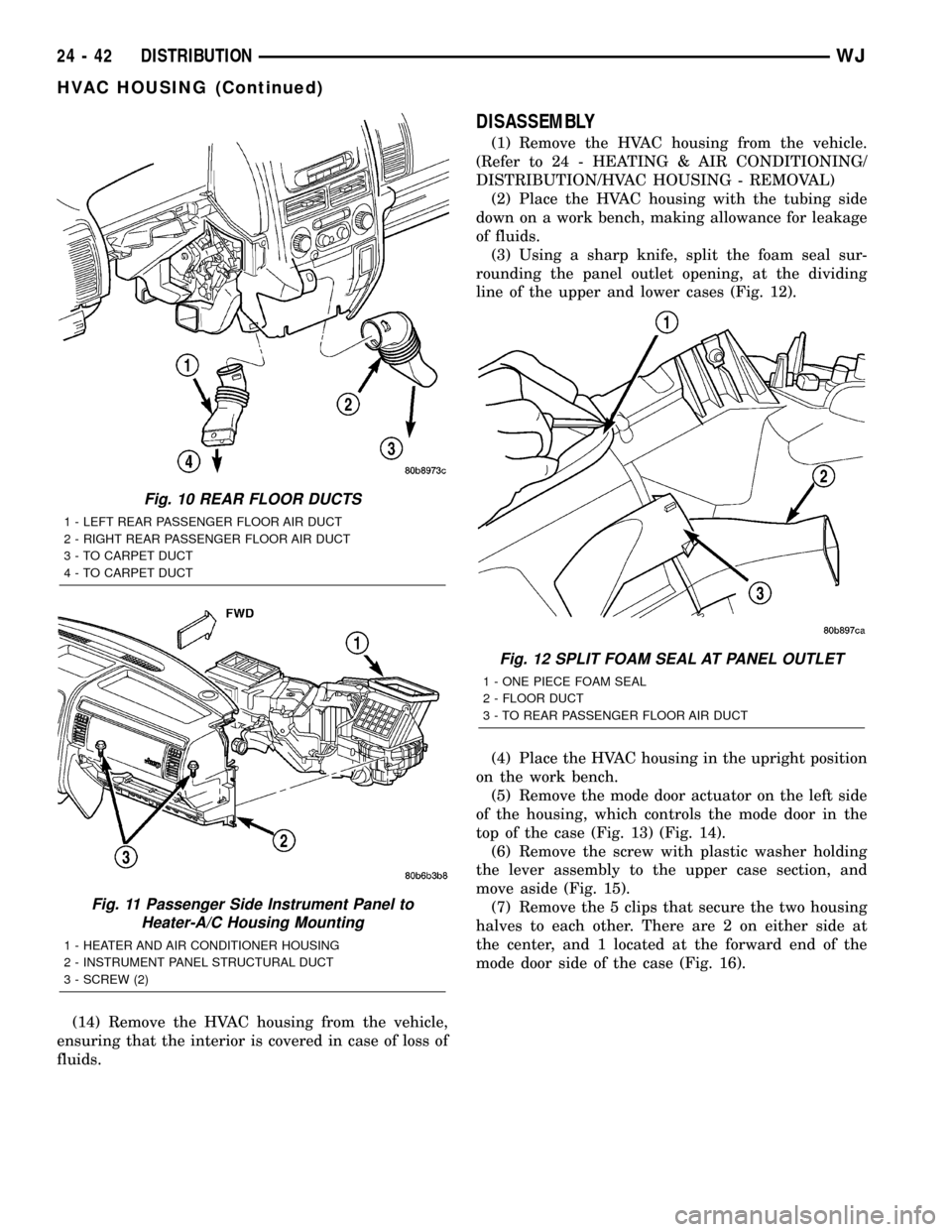
(14) Remove the HVAC housing from the vehicle,
ensuring that the interior is covered in case of loss of
fluids.
DISASSEMBLY
(1) Remove the HVAC housing from the vehicle.
(Refer to 24 - HEATING & AIR CONDITIONING/
DISTRIBUTION/HVAC HOUSING - REMOVAL)
(2) Place the HVAC housing with the tubing side
down on a work bench, making allowance for leakage
of fluids.
(3) Using a sharp knife, split the foam seal sur-
rounding the panel outlet opening, at the dividing
line of the upper and lower cases (Fig. 12).
(4) Place the HVAC housing in the upright position
on the work bench.
(5) Remove the mode door actuator on the left side
of the housing, which controls the mode door in the
top of the case (Fig. 13) (Fig. 14).
(6) Remove the screw with plastic washer holding
the lever assembly to the upper case section, and
move aside (Fig. 15).
(7) Remove the 5 clips that secure the two housing
halves to each other. There are 2 on either side at
the center, and 1 located at the forward end of the
mode door side of the case (Fig. 16).
Fig. 10 REAR FLOOR DUCTS
1 - LEFT REAR PASSENGER FLOOR AIR DUCT
2 - RIGHT REAR PASSENGER FLOOR AIR DUCT
3 - TO CARPET DUCT
4 - TO CARPET DUCT
Fig. 11 Passenger Side Instrument Panel to
Heater-A/C Housing Mounting
1 - HEATER AND AIR CONDITIONER HOUSING
2 - INSTRUMENT PANEL STRUCTURAL DUCT
3 - SCREW (2)
Fig. 12 SPLIT FOAM SEAL AT PANEL OUTLET
1 - ONE PIECE FOAM SEAL
2 - FLOOR DUCT
3 - TO REAR PASSENGER FLOOR AIR DUCT
24 - 42 DISTRIBUTIONWJ
HVAC HOUSING (Continued)
Page 2121 of 2199
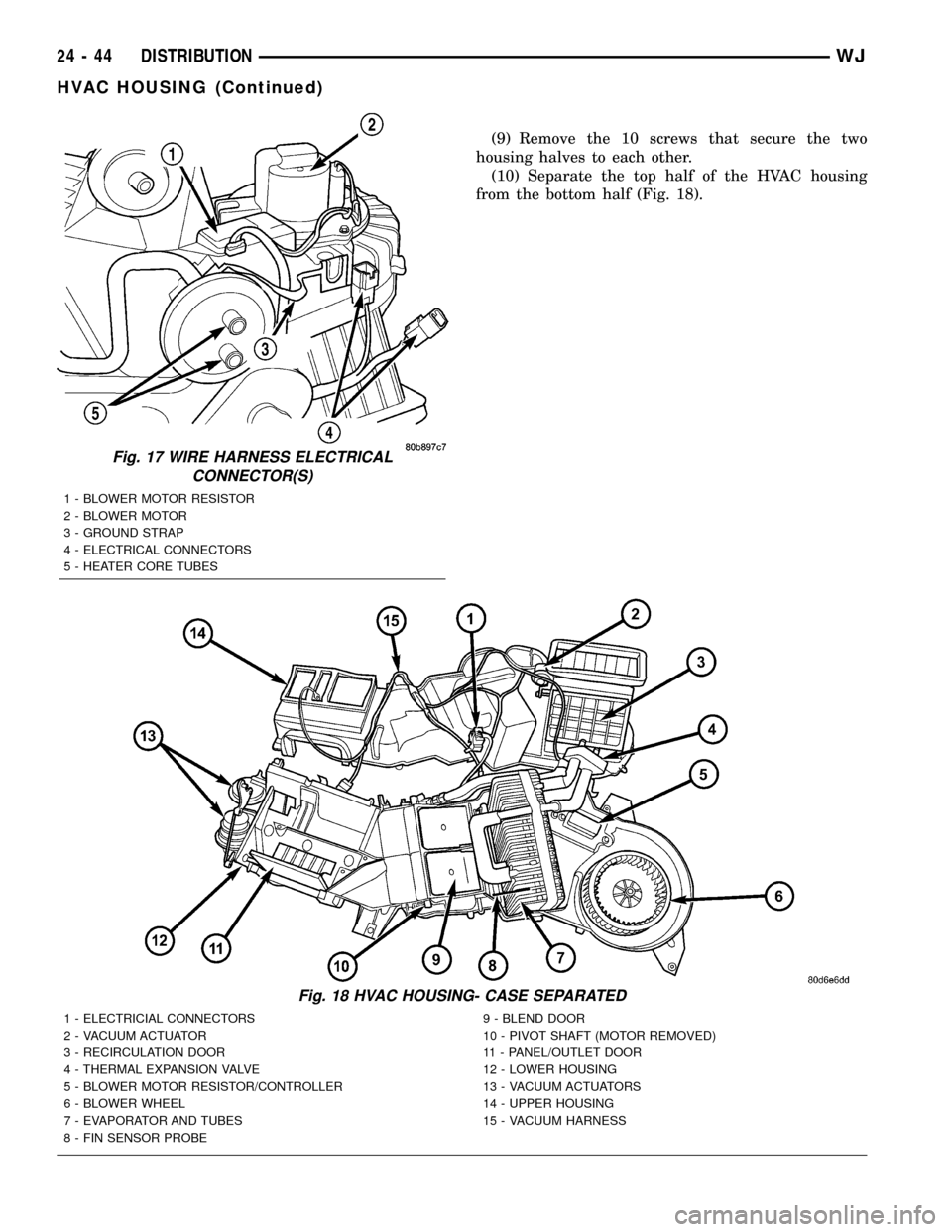
(9) Remove the 10 screws that secure the two
housing halves to each other.
(10) Separate the top half of the HVAC housing
from the bottom half (Fig. 18).
Fig. 17 WIRE HARNESS ELECTRICAL
CONNECTOR(S)
1 - BLOWER MOTOR RESISTOR
2 - BLOWER MOTOR
3 - GROUND STRAP
4 - ELECTRICAL CONNECTORS
5 - HEATER CORE TUBES
Fig. 18 HVAC HOUSING- CASE SEPARATED
1 - ELECTRICIAL CONNECTORS
2 - VACUUM ACTUATOR
3 - RECIRCULATION DOOR
4 - THERMAL EXPANSION VALVE
5 - BLOWER MOTOR RESISTOR/CONTROLLER
6 - BLOWER WHEEL
7 - EVAPORATOR AND TUBES
8 - FIN SENSOR PROBE9 - BLEND DOOR
10 - PIVOT SHAFT (MOTOR REMOVED)
11 - PANEL/OUTLET DOOR
12 - LOWER HOUSING
13 - VACUUM ACTUATORS
14 - UPPER HOUSING
15 - VACUUM HARNESS
24 - 44 DISTRIBUTIONWJ
HVAC HOUSING (Continued)
Page 2122 of 2199
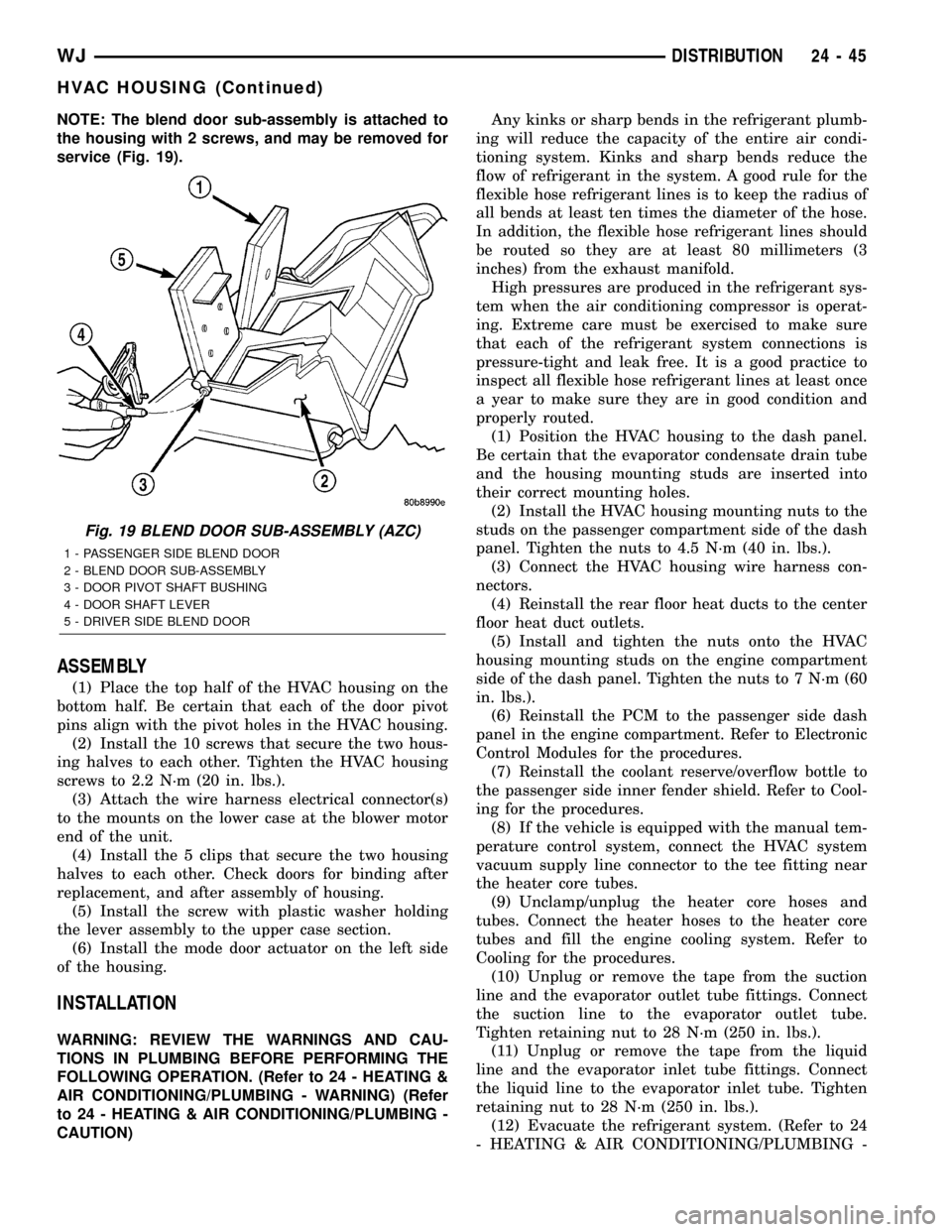
NOTE: The blend door sub-assembly is attached to
the housing with 2 screws, and may be removed for
service (Fig. 19).
ASSEMBLY
(1) Place the top half of the HVAC housing on the
bottom half. Be certain that each of the door pivot
pins align with the pivot holes in the HVAC housing.
(2) Install the 10 screws that secure the two hous-
ing halves to each other. Tighten the HVAC housing
screws to 2.2 N´m (20 in. lbs.).
(3) Attach the wire harness electrical connector(s)
to the mounts on the lower case at the blower motor
end of the unit.
(4) Install the 5 clips that secure the two housing
halves to each other. Check doors for binding after
replacement, and after assembly of housing.
(5) Install the screw with plastic washer holding
the lever assembly to the upper case section.
(6) Install the mode door actuator on the left side
of the housing.
INSTALLATION
WARNING: REVIEW THE WARNINGS AND CAU-
TIONS IN PLUMBING BEFORE PERFORMING THE
FOLLOWING OPERATION. (Refer to 24 - HEATING &
AIR CONDITIONING/PLUMBING - WARNING) (Refer
to 24 - HEATING & AIR CONDITIONING/PLUMBING -
CAUTION)Any kinks or sharp bends in the refrigerant plumb-
ing will reduce the capacity of the entire air condi-
tioning system. Kinks and sharp bends reduce the
flow of refrigerant in the system. A good rule for the
flexible hose refrigerant lines is to keep the radius of
all bends at least ten times the diameter of the hose.
In addition, the flexible hose refrigerant lines should
be routed so they are at least 80 millimeters (3
inches) from the exhaust manifold.
High pressures are produced in the refrigerant sys-
tem when the air conditioning compressor is operat-
ing. Extreme care must be exercised to make sure
that each of the refrigerant system connections is
pressure-tight and leak free. It is a good practice to
inspect all flexible hose refrigerant lines at least once
a year to make sure they are in good condition and
properly routed.
(1) Position the HVAC housing to the dash panel.
Be certain that the evaporator condensate drain tube
and the housing mounting studs are inserted into
their correct mounting holes.
(2) Install the HVAC housing mounting nuts to the
studs on the passenger compartment side of the dash
panel. Tighten the nuts to 4.5 N´m (40 in. lbs.).
(3) Connect the HVAC housing wire harness con-
nectors.
(4) Reinstall the rear floor heat ducts to the center
floor heat duct outlets.
(5) Install and tighten the nuts onto the HVAC
housing mounting studs on the engine compartment
side of the dash panel. Tighten the nuts to 7 N´m (60
in. lbs.).
(6) Reinstall the PCM to the passenger side dash
panel in the engine compartment. Refer to Electronic
Control Modules for the procedures.
(7) Reinstall the coolant reserve/overflow bottle to
the passenger side inner fender shield. Refer to Cool-
ing for the procedures.
(8) If the vehicle is equipped with the manual tem-
perature control system, connect the HVAC system
vacuum supply line connector to the tee fitting near
the heater core tubes.
(9) Unclamp/unplug the heater core hoses and
tubes. Connect the heater hoses to the heater core
tubes and fill the engine cooling system. Refer to
Cooling for the procedures.
(10) Unplug or remove the tape from the suction
line and the evaporator outlet tube fittings. Connect
the suction line to the evaporator outlet tube.
Tighten retaining nut to 28 N´m (250 in. lbs.).
(11) Unplug or remove the tape from the liquid
line and the evaporator inlet tube fittings. Connect
the liquid line to the evaporator inlet tube. Tighten
retaining nut to 28 N´m (250 in. lbs.).
(12) Evacuate the refrigerant system. (Refer to 24
- HEATING & AIR CONDITIONING/PLUMBING -
Fig. 19 BLEND DOOR SUB-ASSEMBLY (AZC)
1 - PASSENGER SIDE BLEND DOOR
2 - BLEND DOOR SUB-ASSEMBLY
3 - DOOR PIVOT SHAFT BUSHING
4 - DOOR SHAFT LEVER
5 - DRIVER SIDE BLEND DOOR
WJDISTRIBUTION 24 - 45
HVAC HOUSING (Continued)
Page 2128 of 2199
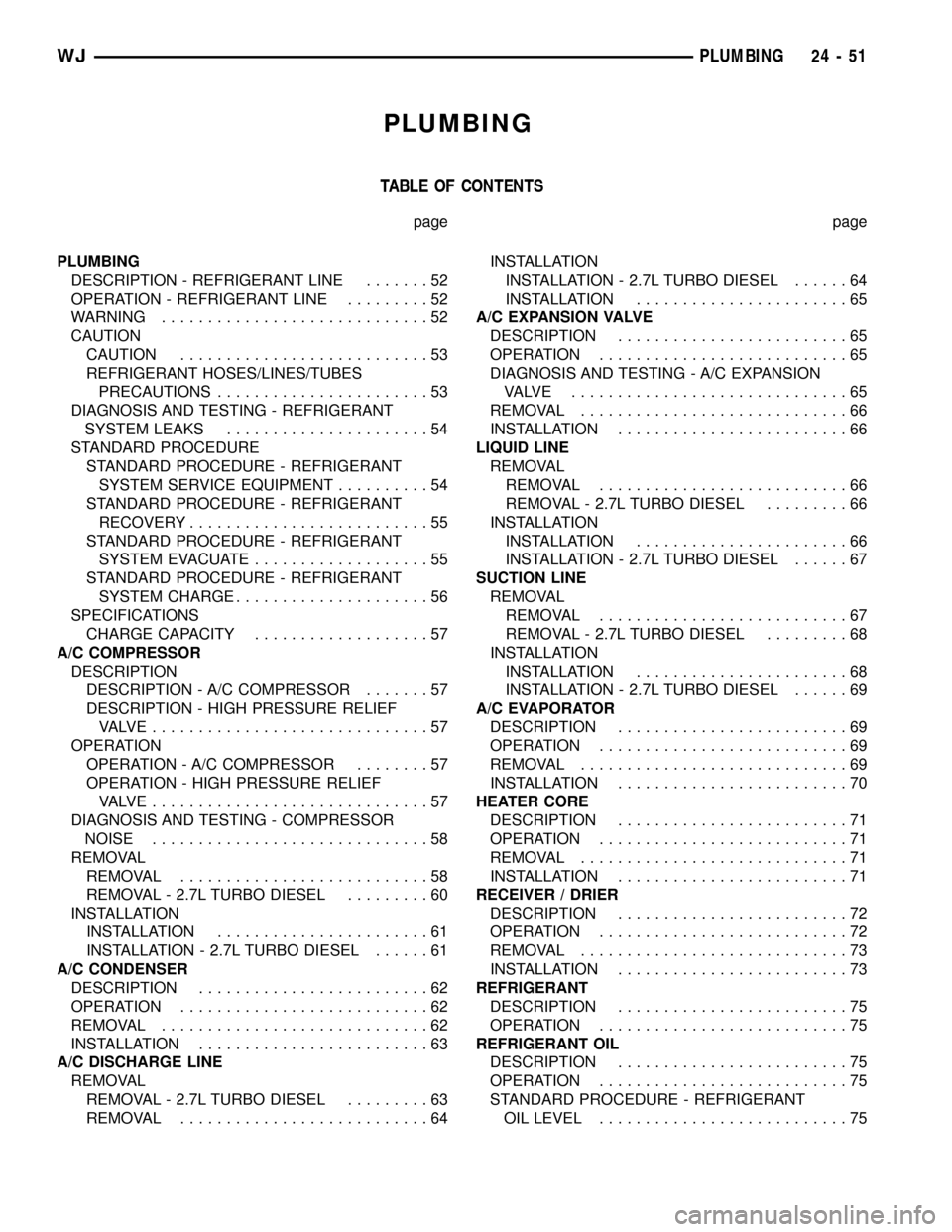
PLUMBING
TABLE OF CONTENTS
page page
PLUMBING
DESCRIPTION - REFRIGERANT LINE.......52
OPERATION - REFRIGERANT LINE.........52
WARNING.............................52
CAUTION
CAUTION...........................53
REFRIGERANT HOSES/LINES/TUBES
PRECAUTIONS.......................53
DIAGNOSIS AND TESTING - REFRIGERANT
SYSTEM LEAKS......................54
STANDARD PROCEDURE
STANDARD PROCEDURE - REFRIGERANT
SYSTEM SERVICE EQUIPMENT..........54
STANDARD PROCEDURE - REFRIGERANT
RECOVERY..........................55
STANDARD PROCEDURE - REFRIGERANT
SYSTEM EVACUATE...................55
STANDARD PROCEDURE - REFRIGERANT
SYSTEM CHARGE.....................56
SPECIFICATIONS
CHARGE CAPACITY...................57
A/C COMPRESSOR
DESCRIPTION
DESCRIPTION - A/C COMPRESSOR.......57
DESCRIPTION - HIGH PRESSURE RELIEF
VALVE..............................57
OPERATION
OPERATION - A/C COMPRESSOR........57
OPERATION - HIGH PRESSURE RELIEF
VALVE..............................57
DIAGNOSIS AND TESTING - COMPRESSOR
NOISE..............................58
REMOVAL
REMOVAL...........................58
REMOVAL - 2.7L TURBO DIESEL.........60
INSTALLATION
INSTALLATION.......................61
INSTALLATION - 2.7L TURBO DIESEL......61
A/C CONDENSER
DESCRIPTION.........................62
OPERATION...........................62
REMOVAL.............................62
INSTALLATION.........................63
A/C DISCHARGE LINE
REMOVAL
REMOVAL - 2.7L TURBO DIESEL.........63
REMOVAL...........................64INSTALLATION
INSTALLATION - 2.7L TURBO DIESEL......64
INSTALLATION.......................65
A/C EXPANSION VALVE
DESCRIPTION.........................65
OPERATION...........................65
DIAGNOSIS AND TESTING - A/C EXPANSION
VALVE ..............................65
REMOVAL.............................66
INSTALLATION.........................66
LIQUID LINE
REMOVAL
REMOVAL...........................66
REMOVAL - 2.7L TURBO DIESEL.........66
INSTALLATION
INSTALLATION.......................66
INSTALLATION - 2.7L TURBO DIESEL......67
SUCTION LINE
REMOVAL
REMOVAL...........................67
REMOVAL - 2.7L TURBO DIESEL.........68
INSTALLATION
INSTALLATION.......................68
INSTALLATION - 2.7L TURBO DIESEL......69
A/C EVAPORATOR
DESCRIPTION.........................69
OPERATION...........................69
REMOVAL.............................69
INSTALLATION.........................70
HEATER CORE
DESCRIPTION.........................71
OPERATION...........................71
REMOVAL.............................71
INSTALLATION.........................71
RECEIVER / DRIER
DESCRIPTION.........................72
OPERATION...........................72
REMOVAL.............................73
INSTALLATION.........................73
REFRIGERANT
DESCRIPTION.........................75
OPERATION...........................75
REFRIGERANT OIL
DESCRIPTION.........................75
OPERATION...........................75
STANDARD PROCEDURE - REFRIGERANT
OIL LEVEL...........................75
WJPLUMBING 24 - 51