o2 location JEEP GRAND CHEROKEE 2002 WJ / 2.G Workshop Manual
[x] Cancel search | Manufacturer: JEEP, Model Year: 2002, Model line: GRAND CHEROKEE, Model: JEEP GRAND CHEROKEE 2002 WJ / 2.GPages: 2199, PDF Size: 76.01 MB
Page 629 of 2199
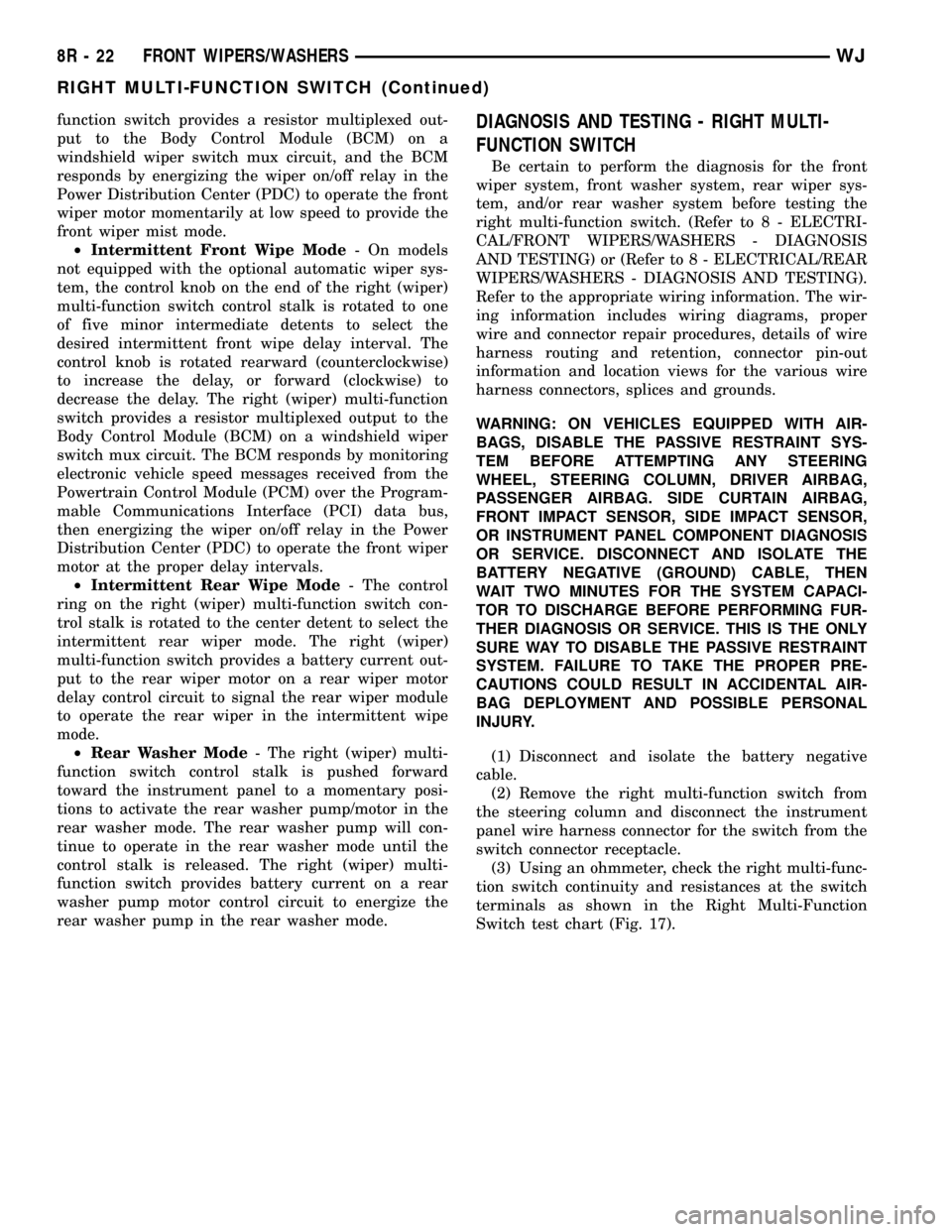
function switch provides a resistor multiplexed out-
put to the Body Control Module (BCM) on a
windshield wiper switch mux circuit, and the BCM
responds by energizing the wiper on/off relay in the
Power Distribution Center (PDC) to operate the front
wiper motor momentarily at low speed to provide the
front wiper mist mode.
²Intermittent Front Wipe Mode- On models
not equipped with the optional automatic wiper sys-
tem, the control knob on the end of the right (wiper)
multi-function switch control stalk is rotated to one
of five minor intermediate detents to select the
desired intermittent front wipe delay interval. The
control knob is rotated rearward (counterclockwise)
to increase the delay, or forward (clockwise) to
decrease the delay. The right (wiper) multi-function
switch provides a resistor multiplexed output to the
Body Control Module (BCM) on a windshield wiper
switch mux circuit. The BCM responds by monitoring
electronic vehicle speed messages received from the
Powertrain Control Module (PCM) over the Program-
mable Communications Interface (PCI) data bus,
then energizing the wiper on/off relay in the Power
Distribution Center (PDC) to operate the front wiper
motor at the proper delay intervals.
²Intermittent Rear Wipe Mode- The control
ring on the right (wiper) multi-function switch con-
trol stalk is rotated to the center detent to select the
intermittent rear wiper mode. The right (wiper)
multi-function switch provides a battery current out-
put to the rear wiper motor on a rear wiper motor
delay control circuit to signal the rear wiper module
to operate the rear wiper in the intermittent wipe
mode.
²Rear Washer Mode- The right (wiper) multi-
function switch control stalk is pushed forward
toward the instrument panel to a momentary posi-
tions to activate the rear washer pump/motor in the
rear washer mode. The rear washer pump will con-
tinue to operate in the rear washer mode until the
control stalk is released. The right (wiper) multi-
function switch provides battery current on a rear
washer pump motor control circuit to energize the
rear washer pump in the rear washer mode.DIAGNOSIS AND TESTING - RIGHT MULTI-
FUNCTION SWITCH
Be certain to perform the diagnosis for the front
wiper system, front washer system, rear wiper sys-
tem, and/or rear washer system before testing the
right multi-function switch. (Refer to 8 - ELECTRI-
CAL/FRONT WIPERS/WASHERS - DIAGNOSIS
AND TESTING) or (Refer to 8 - ELECTRICAL/REAR
WIPERS/WASHERS - DIAGNOSIS AND TESTING).
Refer to the appropriate wiring information. The wir-
ing information includes wiring diagrams, proper
wire and connector repair procedures, details of wire
harness routing and retention, connector pin-out
information and location views for the various wire
harness connectors, splices and grounds.
WARNING: ON VEHICLES EQUIPPED WITH AIR-
BAGS, DISABLE THE PASSIVE RESTRAINT SYS-
TEM BEFORE ATTEMPTING ANY STEERING
WHEEL, STEERING COLUMN, DRIVER AIRBAG,
PASSENGER AIRBAG. SIDE CURTAIN AIRBAG,
FRONT IMPACT SENSOR, SIDE IMPACT SENSOR,
OR INSTRUMENT PANEL COMPONENT DIAGNOSIS
OR SERVICE. DISCONNECT AND ISOLATE THE
BATTERY NEGATIVE (GROUND) CABLE, THEN
WAIT TWO MINUTES FOR THE SYSTEM CAPACI-
TOR TO DISCHARGE BEFORE PERFORMING FUR-
THER DIAGNOSIS OR SERVICE. THIS IS THE ONLY
SURE WAY TO DISABLE THE PASSIVE RESTRAINT
SYSTEM. FAILURE TO TAKE THE PROPER PRE-
CAUTIONS COULD RESULT IN ACCIDENTAL AIR-
BAG DEPLOYMENT AND POSSIBLE PERSONAL
INJURY.
(1) Disconnect and isolate the battery negative
cable.
(2) Remove the right multi-function switch from
the steering column and disconnect the instrument
panel wire harness connector for the switch from the
switch connector receptacle.
(3) Using an ohmmeter, check the right multi-func-
tion switch continuity and resistances at the switch
terminals as shown in the Right Multi-Function
Switch test chart (Fig. 17).
8R - 22 FRONT WIPERS/WASHERSWJ
RIGHT MULTI-FUNCTION SWITCH (Continued)
Page 634 of 2199
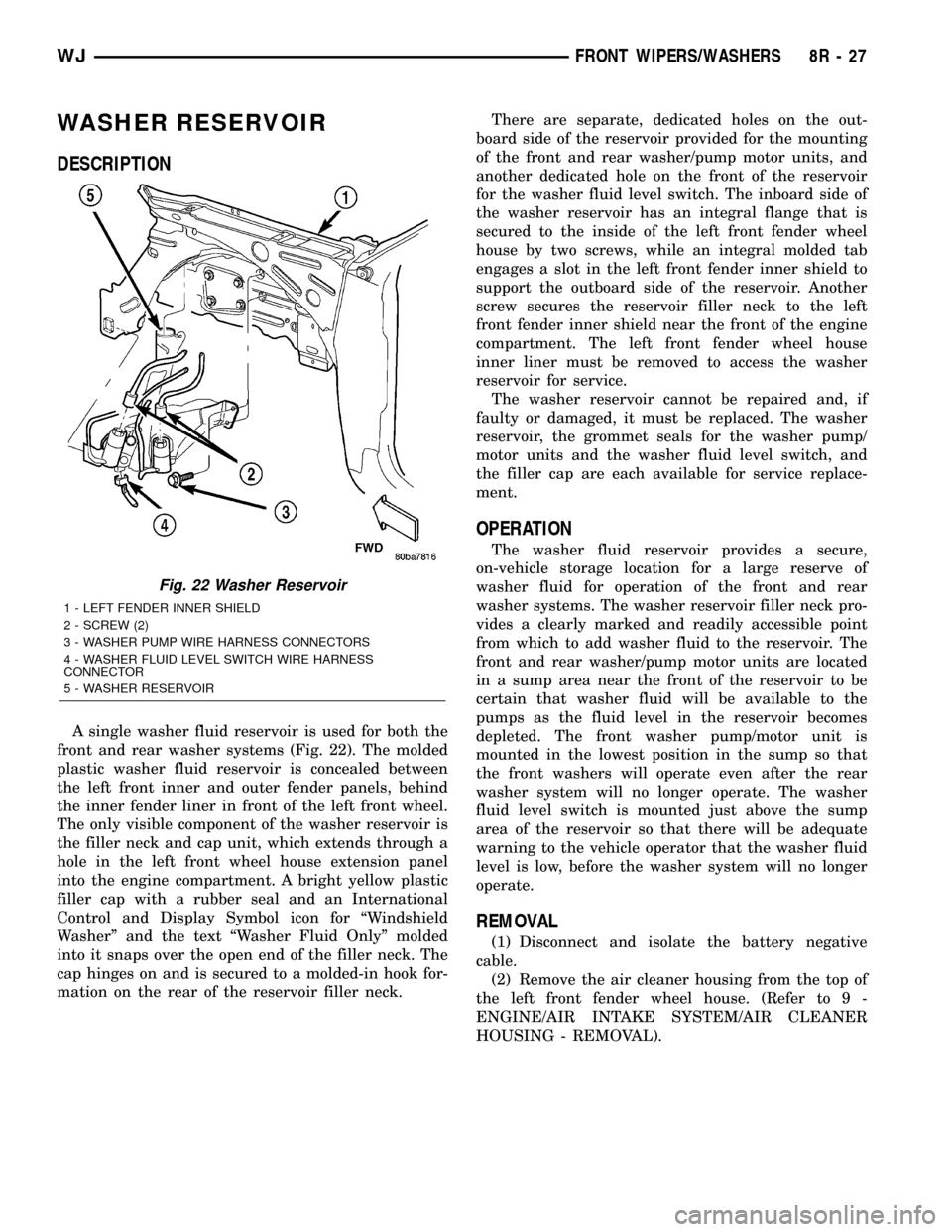
WASHER RESERVOIR
DESCRIPTION
A single washer fluid reservoir is used for both the
front and rear washer systems (Fig. 22). The molded
plastic washer fluid reservoir is concealed between
the left front inner and outer fender panels, behind
the inner fender liner in front of the left front wheel.
The only visible component of the washer reservoir is
the filler neck and cap unit, which extends through a
hole in the left front wheel house extension panel
into the engine compartment. A bright yellow plastic
filler cap with a rubber seal and an International
Control and Display Symbol icon for ªWindshield
Washerº and the text ªWasher Fluid Onlyº molded
into it snaps over the open end of the filler neck. The
cap hinges on and is secured to a molded-in hook for-
mation on the rear of the reservoir filler neck.There are separate, dedicated holes on the out-
board side of the reservoir provided for the mounting
of the front and rear washer/pump motor units, and
another dedicated hole on the front of the reservoir
for the washer fluid level switch. The inboard side of
the washer reservoir has an integral flange that is
secured to the inside of the left front fender wheel
house by two screws, while an integral molded tab
engages a slot in the left front fender inner shield to
support the outboard side of the reservoir. Another
screw secures the reservoir filler neck to the left
front fender inner shield near the front of the engine
compartment. The left front fender wheel house
inner liner must be removed to access the washer
reservoir for service.
The washer reservoir cannot be repaired and, if
faulty or damaged, it must be replaced. The washer
reservoir, the grommet seals for the washer pump/
motor units and the washer fluid level switch, and
the filler cap are each available for service replace-
ment.
OPERATION
The washer fluid reservoir provides a secure,
on-vehicle storage location for a large reserve of
washer fluid for operation of the front and rear
washer systems. The washer reservoir filler neck pro-
vides a clearly marked and readily accessible point
from which to add washer fluid to the reservoir. The
front and rear washer/pump motor units are located
in a sump area near the front of the reservoir to be
certain that washer fluid will be available to the
pumps as the fluid level in the reservoir becomes
depleted. The front washer pump/motor unit is
mounted in the lowest position in the sump so that
the front washers will operate even after the rear
washer system will no longer operate. The washer
fluid level switch is mounted just above the sump
area of the reservoir so that there will be adequate
warning to the vehicle operator that the washer fluid
level is low, before the washer system will no longer
operate.
REMOVAL
(1) Disconnect and isolate the battery negative
cable.
(2) Remove the air cleaner housing from the top of
the left front fender wheel house. (Refer to 9 -
ENGINE/AIR INTAKE SYSTEM/AIR CLEANER
HOUSING - REMOVAL).
Fig. 22 Washer Reservoir
1 - LEFT FENDER INNER SHIELD
2 - SCREW (2)
3 - WASHER PUMP WIRE HARNESS CONNECTORS
4 - WASHER FLUID LEVEL SWITCH WIRE HARNESS
CONNECTOR
5 - WASHER RESERVOIR
WJFRONT WIPERS/WASHERS 8R - 27
Page 637 of 2199
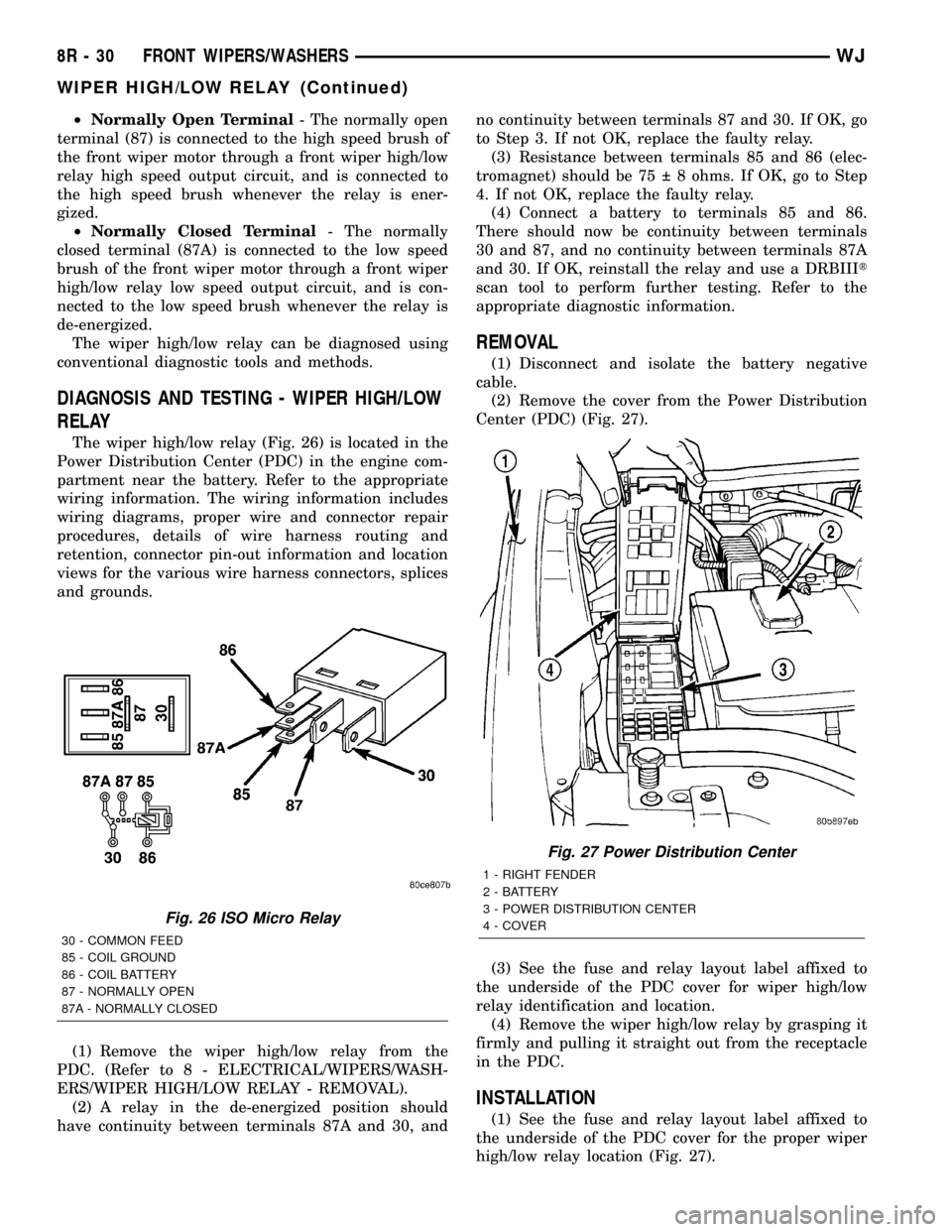
²Normally Open Terminal- The normally open
terminal (87) is connected to the high speed brush of
the front wiper motor through a front wiper high/low
relay high speed output circuit, and is connected to
the high speed brush whenever the relay is ener-
gized.
²Normally Closed Terminal- The normally
closed terminal (87A) is connected to the low speed
brush of the front wiper motor through a front wiper
high/low relay low speed output circuit, and is con-
nected to the low speed brush whenever the relay is
de-energized.
The wiper high/low relay can be diagnosed using
conventional diagnostic tools and methods.
DIAGNOSIS AND TESTING - WIPER HIGH/LOW
RELAY
The wiper high/low relay (Fig. 26) is located in the
Power Distribution Center (PDC) in the engine com-
partment near the battery. Refer to the appropriate
wiring information. The wiring information includes
wiring diagrams, proper wire and connector repair
procedures, details of wire harness routing and
retention, connector pin-out information and location
views for the various wire harness connectors, splices
and grounds.
(1) Remove the wiper high/low relay from the
PDC. (Refer to 8 - ELECTRICAL/WIPERS/WASH-
ERS/WIPER HIGH/LOW RELAY - REMOVAL).
(2) A relay in the de-energized position should
have continuity between terminals 87A and 30, andno continuity between terminals 87 and 30. If OK, go
to Step 3. If not OK, replace the faulty relay.
(3) Resistance between terminals 85 and 86 (elec-
tromagnet) should be 75 8 ohms. If OK, go to Step
4. If not OK, replace the faulty relay.
(4) Connect a battery to terminals 85 and 86.
There should now be continuity between terminals
30 and 87, and no continuity between terminals 87A
and 30. If OK, reinstall the relay and use a DRBIIIt
scan tool to perform further testing. Refer to the
appropriate diagnostic information.
REMOVAL
(1) Disconnect and isolate the battery negative
cable.
(2) Remove the cover from the Power Distribution
Center (PDC) (Fig. 27).
(3) See the fuse and relay layout label affixed to
the underside of the PDC cover for wiper high/low
relay identification and location.
(4) Remove the wiper high/low relay by grasping it
firmly and pulling it straight out from the receptacle
in the PDC.
INSTALLATION
(1) See the fuse and relay layout label affixed to
the underside of the PDC cover for the proper wiper
high/low relay location (Fig. 27).
Fig. 26 ISO Micro Relay
30 - COMMON FEED
85 - COIL GROUND
86 - COIL BATTERY
87 - NORMALLY OPEN
87A - NORMALLY CLOSED
Fig. 27 Power Distribution Center
1 - RIGHT FENDER
2 - BATTERY
3 - POWER DISTRIBUTION CENTER
4 - COVER
8R - 30 FRONT WIPERS/WASHERSWJ
WIPER HIGH/LOW RELAY (Continued)
Page 639 of 2199
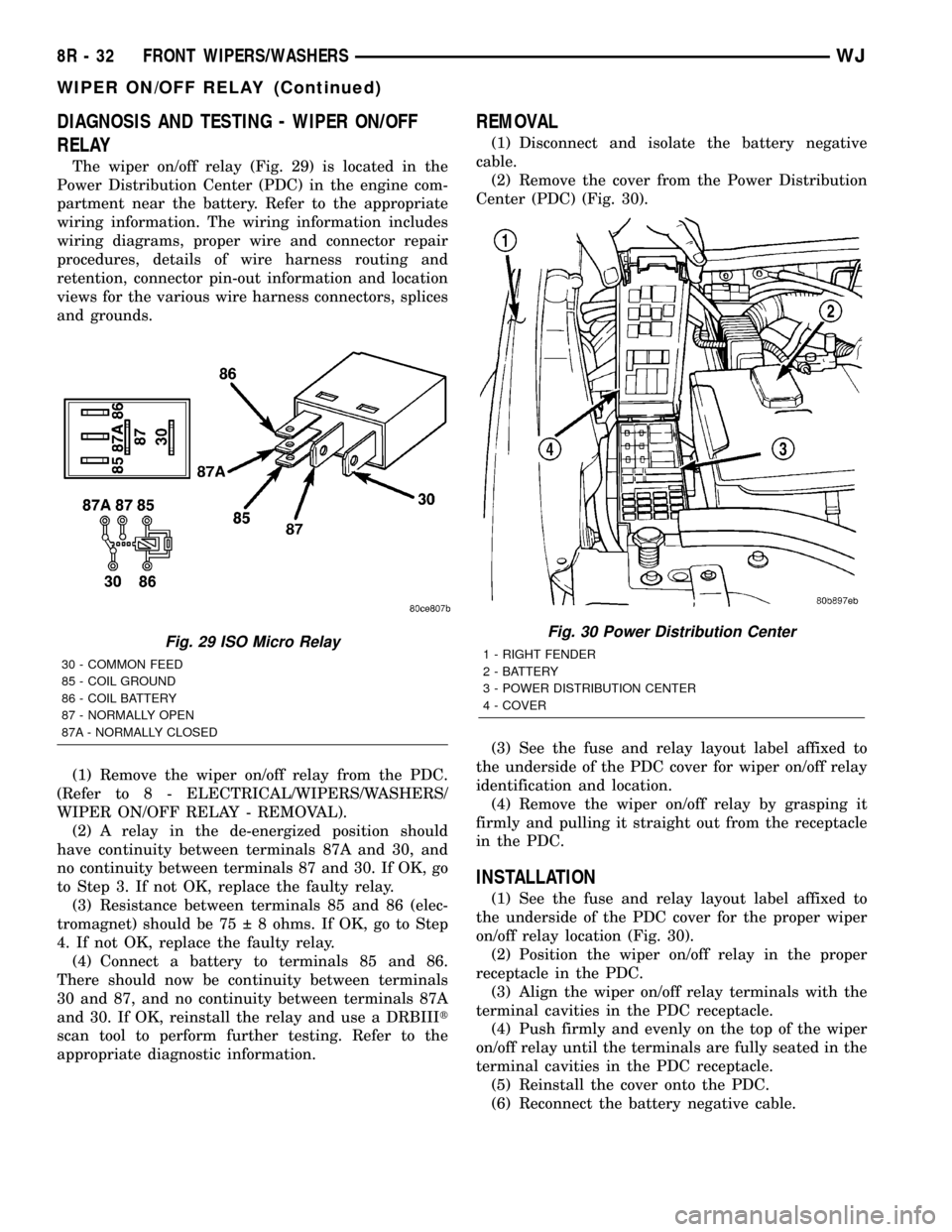
DIAGNOSIS AND TESTING - WIPER ON/OFF
RELAY
The wiper on/off relay (Fig. 29) is located in the
Power Distribution Center (PDC) in the engine com-
partment near the battery. Refer to the appropriate
wiring information. The wiring information includes
wiring diagrams, proper wire and connector repair
procedures, details of wire harness routing and
retention, connector pin-out information and location
views for the various wire harness connectors, splices
and grounds.
(1) Remove the wiper on/off relay from the PDC.
(Refer to 8 - ELECTRICAL/WIPERS/WASHERS/
WIPER ON/OFF RELAY - REMOVAL).
(2) A relay in the de-energized position should
have continuity between terminals 87A and 30, and
no continuity between terminals 87 and 30. If OK, go
to Step 3. If not OK, replace the faulty relay.
(3) Resistance between terminals 85 and 86 (elec-
tromagnet) should be 75 8 ohms. If OK, go to Step
4. If not OK, replace the faulty relay.
(4) Connect a battery to terminals 85 and 86.
There should now be continuity between terminals
30 and 87, and no continuity between terminals 87A
and 30. If OK, reinstall the relay and use a DRBIIIt
scan tool to perform further testing. Refer to the
appropriate diagnostic information.
REMOVAL
(1) Disconnect and isolate the battery negative
cable.
(2) Remove the cover from the Power Distribution
Center (PDC) (Fig. 30).
(3) See the fuse and relay layout label affixed to
the underside of the PDC cover for wiper on/off relay
identification and location.
(4) Remove the wiper on/off relay by grasping it
firmly and pulling it straight out from the receptacle
in the PDC.
INSTALLATION
(1) See the fuse and relay layout label affixed to
the underside of the PDC cover for the proper wiper
on/off relay location (Fig. 30).
(2) Position the wiper on/off relay in the proper
receptacle in the PDC.
(3) Align the wiper on/off relay terminals with the
terminal cavities in the PDC receptacle.
(4) Push firmly and evenly on the top of the wiper
on/off relay until the terminals are fully seated in the
terminal cavities in the PDC receptacle.
(5) Reinstall the cover onto the PDC.
(6) Reconnect the battery negative cable.
Fig. 29 ISO Micro Relay
30 - COMMON FEED
85 - COIL GROUND
86 - COIL BATTERY
87 - NORMALLY OPEN
87A - NORMALLY CLOSED
Fig. 30 Power Distribution Center
1 - RIGHT FENDER
2 - BATTERY
3 - POWER DISTRIBUTION CENTER
4 - COVER
8R - 32 FRONT WIPERS/WASHERSWJ
WIPER ON/OFF RELAY (Continued)
Page 641 of 2199
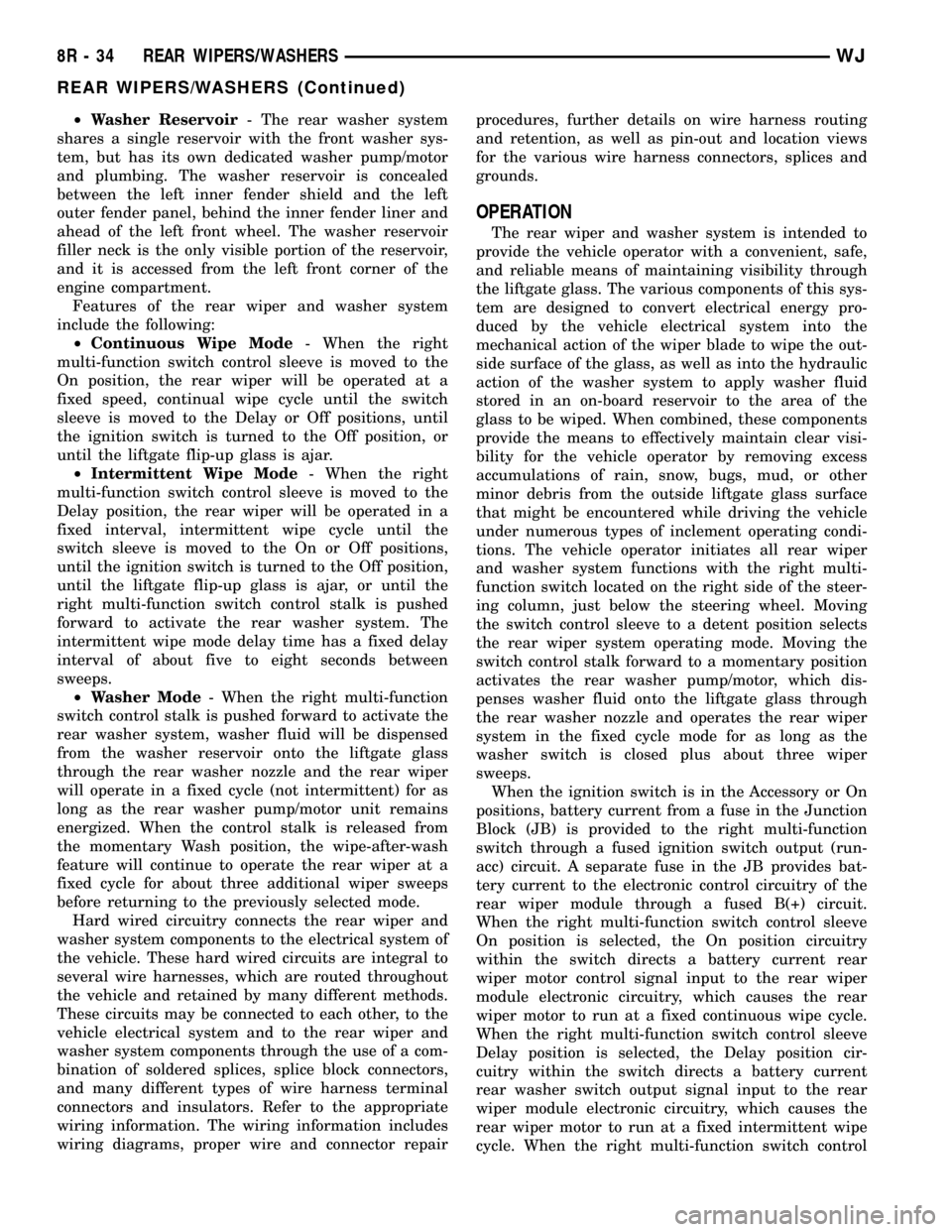
²Washer Reservoir- The rear washer system
shares a single reservoir with the front washer sys-
tem, but has its own dedicated washer pump/motor
and plumbing. The washer reservoir is concealed
between the left inner fender shield and the left
outer fender panel, behind the inner fender liner and
ahead of the left front wheel. The washer reservoir
filler neck is the only visible portion of the reservoir,
and it is accessed from the left front corner of the
engine compartment.
Features of the rear wiper and washer system
include the following:
²Continuous Wipe Mode- When the right
multi-function switch control sleeve is moved to the
On position, the rear wiper will be operated at a
fixed speed, continual wipe cycle until the switch
sleeve is moved to the Delay or Off positions, until
the ignition switch is turned to the Off position, or
until the liftgate flip-up glass is ajar.
²Intermittent Wipe Mode- When the right
multi-function switch control sleeve is moved to the
Delay position, the rear wiper will be operated in a
fixed interval, intermittent wipe cycle until the
switch sleeve is moved to the On or Off positions,
until the ignition switch is turned to the Off position,
until the liftgate flip-up glass is ajar, or until the
right multi-function switch control stalk is pushed
forward to activate the rear washer system. The
intermittent wipe mode delay time has a fixed delay
interval of about five to eight seconds between
sweeps.
²Washer Mode- When the right multi-function
switch control stalk is pushed forward to activate the
rear washer system, washer fluid will be dispensed
from the washer reservoir onto the liftgate glass
through the rear washer nozzle and the rear wiper
will operate in a fixed cycle (not intermittent) for as
long as the rear washer pump/motor unit remains
energized. When the control stalk is released from
the momentary Wash position, the wipe-after-wash
feature will continue to operate the rear wiper at a
fixed cycle for about three additional wiper sweeps
before returning to the previously selected mode.
Hard wired circuitry connects the rear wiper and
washer system components to the electrical system of
the vehicle. These hard wired circuits are integral to
several wire harnesses, which are routed throughout
the vehicle and retained by many different methods.
These circuits may be connected to each other, to the
vehicle electrical system and to the rear wiper and
washer system components through the use of a com-
bination of soldered splices, splice block connectors,
and many different types of wire harness terminal
connectors and insulators. Refer to the appropriate
wiring information. The wiring information includes
wiring diagrams, proper wire and connector repairprocedures, further details on wire harness routing
and retention, as well as pin-out and location views
for the various wire harness connectors, splices and
grounds.
OPERATION
The rear wiper and washer system is intended to
provide the vehicle operator with a convenient, safe,
and reliable means of maintaining visibility through
the liftgate glass. The various components of this sys-
tem are designed to convert electrical energy pro-
duced by the vehicle electrical system into the
mechanical action of the wiper blade to wipe the out-
side surface of the glass, as well as into the hydraulic
action of the washer system to apply washer fluid
stored in an on-board reservoir to the area of the
glass to be wiped. When combined, these components
provide the means to effectively maintain clear visi-
bility for the vehicle operator by removing excess
accumulations of rain, snow, bugs, mud, or other
minor debris from the outside liftgate glass surface
that might be encountered while driving the vehicle
under numerous types of inclement operating condi-
tions. The vehicle operator initiates all rear wiper
and washer system functions with the right multi-
function switch located on the right side of the steer-
ing column, just below the steering wheel. Moving
the switch control sleeve to a detent position selects
the rear wiper system operating mode. Moving the
switch control stalk forward to a momentary position
activates the rear washer pump/motor, which dis-
penses washer fluid onto the liftgate glass through
the rear washer nozzle and operates the rear wiper
system in the fixed cycle mode for as long as the
washer switch is closed plus about three wiper
sweeps.
When the ignition switch is in the Accessory or On
positions, battery current from a fuse in the Junction
Block (JB) is provided to the right multi-function
switch through a fused ignition switch output (run-
acc) circuit. A separate fuse in the JB provides bat-
tery current to the electronic control circuitry of the
rear wiper module through a fused B(+) circuit.
When the right multi-function switch control sleeve
On position is selected, the On position circuitry
within the switch directs a battery current rear
wiper motor control signal input to the rear wiper
module electronic circuitry, which causes the rear
wiper motor to run at a fixed continuous wipe cycle.
When the right multi-function switch control sleeve
Delay position is selected, the Delay position cir-
cuitry within the switch directs a battery current
rear washer switch output signal input to the rear
wiper module electronic circuitry, which causes the
rear wiper motor to run at a fixed intermittent wipe
cycle. When the right multi-function switch control
8R - 34 REAR WIPERS/WASHERSWJ
REAR WIPERS/WASHERS (Continued)
Page 642 of 2199
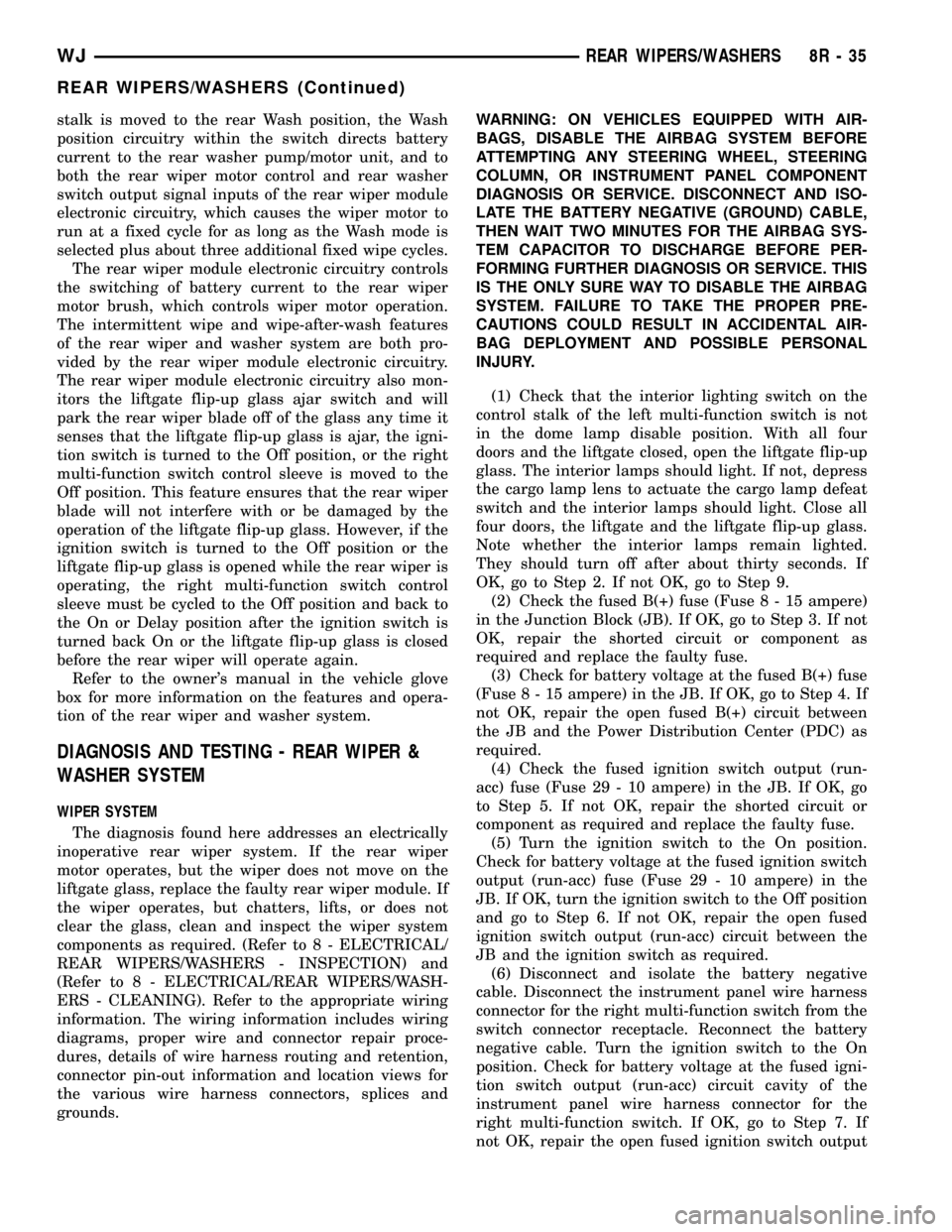
stalk is moved to the rear Wash position, the Wash
position circuitry within the switch directs battery
current to the rear washer pump/motor unit, and to
both the rear wiper motor control and rear washer
switch output signal inputs of the rear wiper module
electronic circuitry, which causes the wiper motor to
run at a fixed cycle for as long as the Wash mode is
selected plus about three additional fixed wipe cycles.
The rear wiper module electronic circuitry controls
the switching of battery current to the rear wiper
motor brush, which controls wiper motor operation.
The intermittent wipe and wipe-after-wash features
of the rear wiper and washer system are both pro-
vided by the rear wiper module electronic circuitry.
The rear wiper module electronic circuitry also mon-
itors the liftgate flip-up glass ajar switch and will
park the rear wiper blade off of the glass any time it
senses that the liftgate flip-up glass is ajar, the igni-
tion switch is turned to the Off position, or the right
multi-function switch control sleeve is moved to the
Off position. This feature ensures that the rear wiper
blade will not interfere with or be damaged by the
operation of the liftgate flip-up glass. However, if the
ignition switch is turned to the Off position or the
liftgate flip-up glass is opened while the rear wiper is
operating, the right multi-function switch control
sleeve must be cycled to the Off position and back to
the On or Delay position after the ignition switch is
turned back On or the liftgate flip-up glass is closed
before the rear wiper will operate again.
Refer to the owner's manual in the vehicle glove
box for more information on the features and opera-
tion of the rear wiper and washer system.
DIAGNOSIS AND TESTING - REAR WIPER &
WASHER SYSTEM
WIPER SYSTEM
The diagnosis found here addresses an electrically
inoperative rear wiper system. If the rear wiper
motor operates, but the wiper does not move on the
liftgate glass, replace the faulty rear wiper module. If
the wiper operates, but chatters, lifts, or does not
clear the glass, clean and inspect the wiper system
components as required. (Refer to 8 - ELECTRICAL/
REAR WIPERS/WASHERS - INSPECTION) and
(Refer to 8 - ELECTRICAL/REAR WIPERS/WASH-
ERS - CLEANING). Refer to the appropriate wiring
information. The wiring information includes wiring
diagrams, proper wire and connector repair proce-
dures, details of wire harness routing and retention,
connector pin-out information and location views for
the various wire harness connectors, splices and
grounds.WARNING: ON VEHICLES EQUIPPED WITH AIR-
BAGS, DISABLE THE AIRBAG SYSTEM BEFORE
ATTEMPTING ANY STEERING WHEEL, STEERING
COLUMN, OR INSTRUMENT PANEL COMPONENT
DIAGNOSIS OR SERVICE. DISCONNECT AND ISO-
LATE THE BATTERY NEGATIVE (GROUND) CABLE,
THEN WAIT TWO MINUTES FOR THE AIRBAG SYS-
TEM CAPACITOR TO DISCHARGE BEFORE PER-
FORMING FURTHER DIAGNOSIS OR SERVICE. THIS
IS THE ONLY SURE WAY TO DISABLE THE AIRBAG
SYSTEM. FAILURE TO TAKE THE PROPER PRE-
CAUTIONS COULD RESULT IN ACCIDENTAL AIR-
BAG DEPLOYMENT AND POSSIBLE PERSONAL
INJURY.
(1) Check that the interior lighting switch on the
control stalk of the left multi-function switch is not
in the dome lamp disable position. With all four
doors and the liftgate closed, open the liftgate flip-up
glass. The interior lamps should light. If not, depress
the cargo lamp lens to actuate the cargo lamp defeat
switch and the interior lamps should light. Close all
four doors, the liftgate and the liftgate flip-up glass.
Note whether the interior lamps remain lighted.
They should turn off after about thirty seconds. If
OK, go to Step 2. If not OK, go to Step 9.
(2) Check the fused B(+) fuse (Fuse8-15ampere)
in the Junction Block (JB). If OK, go to Step 3. If not
OK, repair the shorted circuit or component as
required and replace the faulty fuse.
(3) Check for battery voltage at the fused B(+) fuse
(Fuse8-15ampere) in the JB. If OK, go to Step 4. If
not OK, repair the open fused B(+) circuit between
the JB and the Power Distribution Center (PDC) as
required.
(4) Check the fused ignition switch output (run-
acc) fuse (Fuse 29 - 10 ampere) in the JB. If OK, go
to Step 5. If not OK, repair the shorted circuit or
component as required and replace the faulty fuse.
(5) Turn the ignition switch to the On position.
Check for battery voltage at the fused ignition switch
output (run-acc) fuse (Fuse 29 - 10 ampere) in the
JB. If OK, turn the ignition switch to the Off position
and go to Step 6. If not OK, repair the open fused
ignition switch output (run-acc) circuit between the
JB and the ignition switch as required.
(6) Disconnect and isolate the battery negative
cable. Disconnect the instrument panel wire harness
connector for the right multi-function switch from the
switch connector receptacle. Reconnect the battery
negative cable. Turn the ignition switch to the On
position. Check for battery voltage at the fused igni-
tion switch output (run-acc) circuit cavity of the
instrument panel wire harness connector for the
right multi-function switch. If OK, go to Step 7. If
not OK, repair the open fused ignition switch output
WJREAR WIPERS/WASHERS 8R - 35
REAR WIPERS/WASHERS (Continued)
Page 643 of 2199
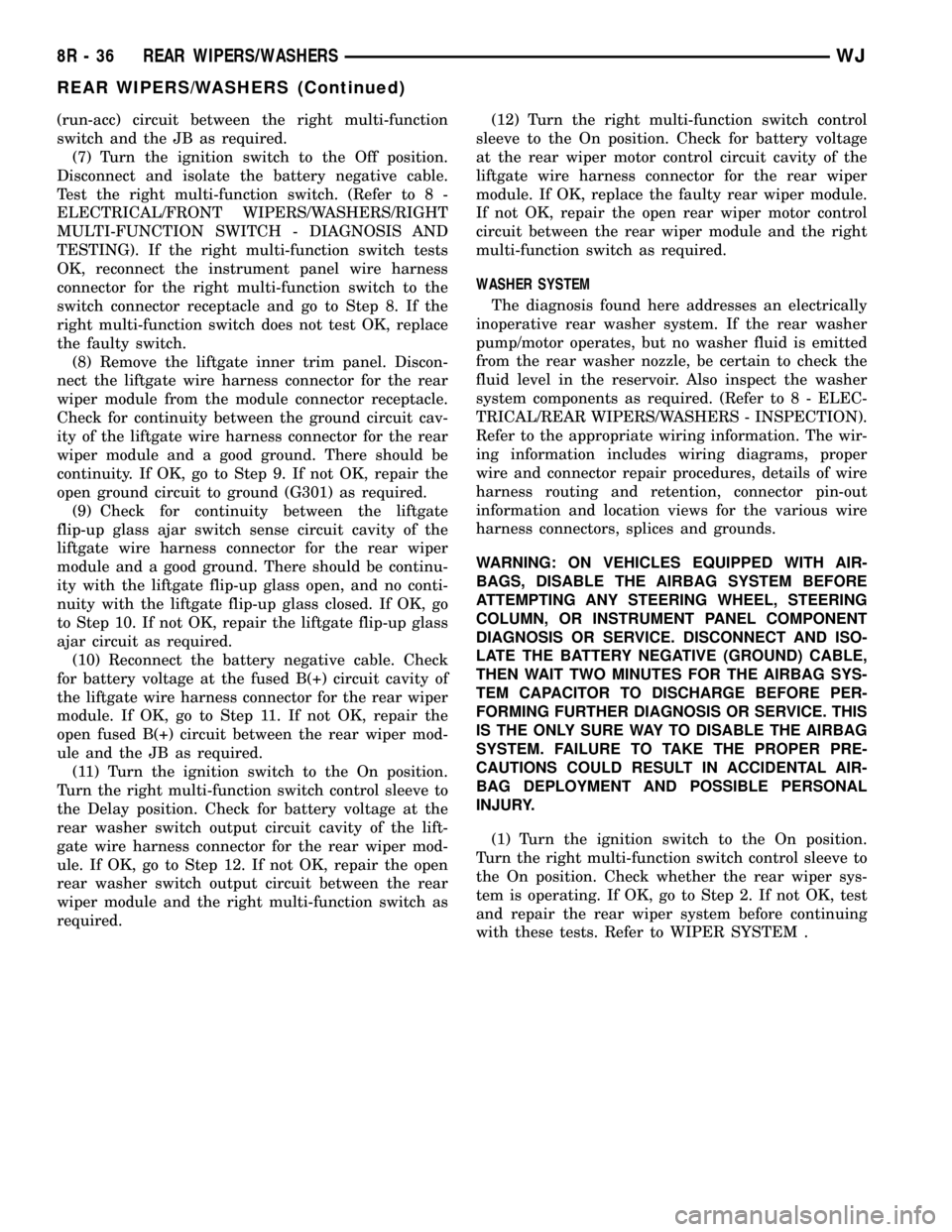
(run-acc) circuit between the right multi-function
switch and the JB as required.
(7) Turn the ignition switch to the Off position.
Disconnect and isolate the battery negative cable.
Test the right multi-function switch. (Refer to 8 -
ELECTRICAL/FRONT WIPERS/WASHERS/RIGHT
MULTI-FUNCTION SWITCH - DIAGNOSIS AND
TESTING). If the right multi-function switch tests
OK, reconnect the instrument panel wire harness
connector for the right multi-function switch to the
switch connector receptacle and go to Step 8. If the
right multi-function switch does not test OK, replace
the faulty switch.
(8) Remove the liftgate inner trim panel. Discon-
nect the liftgate wire harness connector for the rear
wiper module from the module connector receptacle.
Check for continuity between the ground circuit cav-
ity of the liftgate wire harness connector for the rear
wiper module and a good ground. There should be
continuity. If OK, go to Step 9. If not OK, repair the
open ground circuit to ground (G301) as required.
(9) Check for continuity between the liftgate
flip-up glass ajar switch sense circuit cavity of the
liftgate wire harness connector for the rear wiper
module and a good ground. There should be continu-
ity with the liftgate flip-up glass open, and no conti-
nuity with the liftgate flip-up glass closed. If OK, go
to Step 10. If not OK, repair the liftgate flip-up glass
ajar circuit as required.
(10) Reconnect the battery negative cable. Check
for battery voltage at the fused B(+) circuit cavity of
the liftgate wire harness connector for the rear wiper
module. If OK, go to Step 11. If not OK, repair the
open fused B(+) circuit between the rear wiper mod-
ule and the JB as required.
(11) Turn the ignition switch to the On position.
Turn the right multi-function switch control sleeve to
the Delay position. Check for battery voltage at the
rear washer switch output circuit cavity of the lift-
gate wire harness connector for the rear wiper mod-
ule. If OK, go to Step 12. If not OK, repair the open
rear washer switch output circuit between the rear
wiper module and the right multi-function switch as
required.(12) Turn the right multi-function switch control
sleeve to the On position. Check for battery voltage
at the rear wiper motor control circuit cavity of the
liftgate wire harness connector for the rear wiper
module. If OK, replace the faulty rear wiper module.
If not OK, repair the open rear wiper motor control
circuit between the rear wiper module and the right
multi-function switch as required.
WASHER SYSTEM
The diagnosis found here addresses an electrically
inoperative rear washer system. If the rear washer
pump/motor operates, but no washer fluid is emitted
from the rear washer nozzle, be certain to check the
fluid level in the reservoir. Also inspect the washer
system components as required. (Refer to 8 - ELEC-
TRICAL/REAR WIPERS/WASHERS - INSPECTION).
Refer to the appropriate wiring information. The wir-
ing information includes wiring diagrams, proper
wire and connector repair procedures, details of wire
harness routing and retention, connector pin-out
information and location views for the various wire
harness connectors, splices and grounds.
WARNING: ON VEHICLES EQUIPPED WITH AIR-
BAGS, DISABLE THE AIRBAG SYSTEM BEFORE
ATTEMPTING ANY STEERING WHEEL, STEERING
COLUMN, OR INSTRUMENT PANEL COMPONENT
DIAGNOSIS OR SERVICE. DISCONNECT AND ISO-
LATE THE BATTERY NEGATIVE (GROUND) CABLE,
THEN WAIT TWO MINUTES FOR THE AIRBAG SYS-
TEM CAPACITOR TO DISCHARGE BEFORE PER-
FORMING FURTHER DIAGNOSIS OR SERVICE. THIS
IS THE ONLY SURE WAY TO DISABLE THE AIRBAG
SYSTEM. FAILURE TO TAKE THE PROPER PRE-
CAUTIONS COULD RESULT IN ACCIDENTAL AIR-
BAG DEPLOYMENT AND POSSIBLE PERSONAL
INJURY.
(1) Turn the ignition switch to the On position.
Turn the right multi-function switch control sleeve to
the On position. Check whether the rear wiper sys-
tem is operating. If OK, go to Step 2. If not OK, test
and repair the rear wiper system before continuing
with these tests. Refer to WIPER SYSTEM .
8R - 36 REAR WIPERS/WASHERSWJ
REAR WIPERS/WASHERS (Continued)
Page 654 of 2199
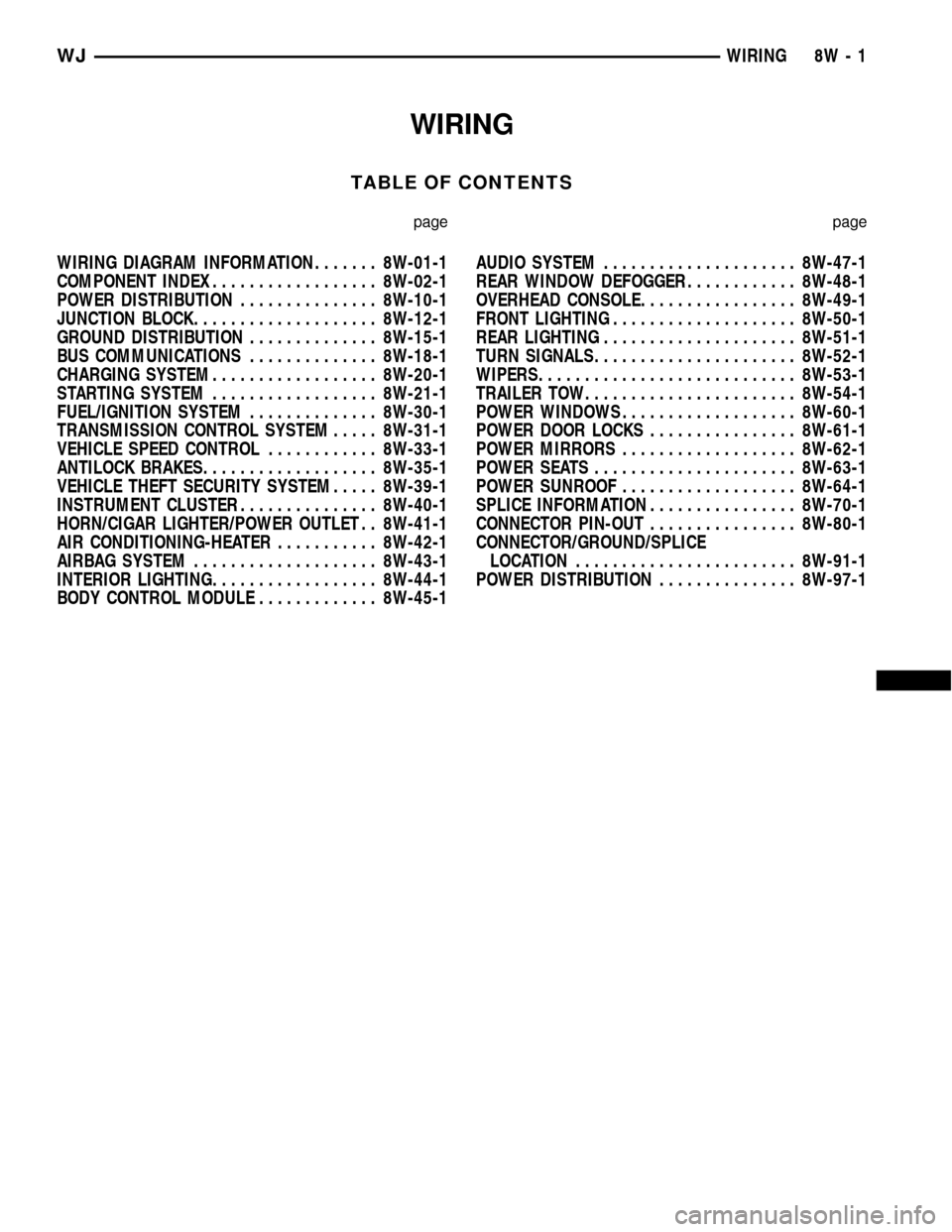
WIRING
TABLE OF CONTENTS
page page
WIRING DIAGRAM INFORMATION....... 8W-01-1
COMPONENT INDEX.................. 8W-02-1
POWER DISTRIBUTION............... 8W-10-1
JUNCTION BLOCK.................... 8W-12-1
GROUND DISTRIBUTION.............. 8W-15-1
BUS COMMUNICATIONS.............. 8W-18-1
CHARGING SYSTEM.................. 8W-20-1
STARTING SYSTEM.................. 8W-21-1
FUEL/IGNITION SYSTEM.............. 8W-30-1
TRANSMISSION CONTROL SYSTEM..... 8W-31-1
VEHICLE SPEED CONTROL............ 8W-33-1
ANTILOCK BRAKES................... 8W-35-1
VEHICLE THEFT SECURITY SYSTEM..... 8W-39-1
INSTRUMENT CLUSTER............... 8W-40-1
HORN/CIGAR LIGHTER/POWER OUTLET . . 8W-41-1
AIR CONDITIONING-HEATER........... 8W-42-1
AIRBAG SYSTEM.................... 8W-43-1
INTERIOR LIGHTING.................. 8W-44-1
BODY CONTROL MODULE............. 8W-45-1AUDIO SYSTEM..................... 8W-47-1
REAR WINDOW DEFOGGER............ 8W-48-1
OVERHEAD CONSOLE................. 8W-49-1
FRONT LIGHTING.................... 8W-50-1
REAR LIGHTING..................... 8W-51-1
TURN SIGNALS...................... 8W-52-1
WIPERS............................ 8W-53-1
TRAILER TOW....................... 8W-54-1
POWER WINDOWS................... 8W-60-1
POWER DOOR LOCKS................ 8W-61-1
POWER MIRRORS................... 8W-62-1
POWER SEATS...................... 8W-63-1
POWER SUNROOF................... 8W-64-1
SPLICE INFORMATION................ 8W-70-1
CONNECTOR PIN-OUT................ 8W-80-1
CONNECTOR/GROUND/SPLICE
LOCATION........................ 8W-91-1
POWER DISTRIBUTION............... 8W-97-1 WJWIRING 8W - 1
Page 661 of 2199
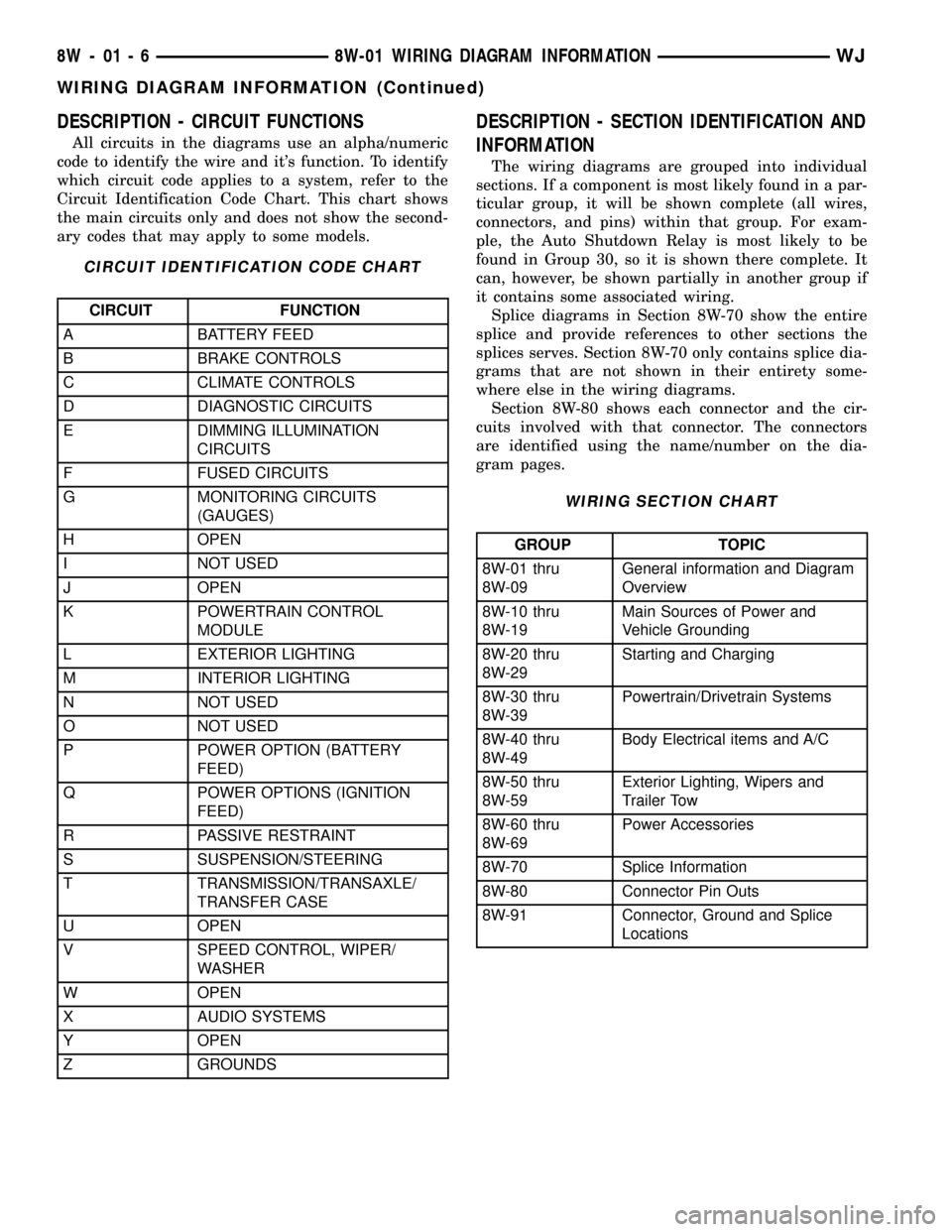
DESCRIPTION - CIRCUIT FUNCTIONS
All circuits in the diagrams use an alpha/numeric
code to identify the wire and it's function. To identify
which circuit code applies to a system, refer to the
Circuit Identification Code Chart. This chart shows
the main circuits only and does not show the second-
ary codes that may apply to some models.
CIRCUIT IDENTIFICATION CODE CHART
CIRCUIT FUNCTION
A BATTERY FEED
B BRAKE CONTROLS
C CLIMATE CONTROLS
D DIAGNOSTIC CIRCUITS
E DIMMING ILLUMINATION
CIRCUITS
F FUSED CIRCUITS
G MONITORING CIRCUITS
(GAUGES)
H OPEN
I NOT USED
J OPEN
K POWERTRAIN CONTROL
MODULE
L EXTERIOR LIGHTING
M INTERIOR LIGHTING
N NOT USED
O NOT USED
P POWER OPTION (BATTERY
FEED)
Q POWER OPTIONS (IGNITION
FEED)
R PASSIVE RESTRAINT
S SUSPENSION/STEERING
T TRANSMISSION/TRANSAXLE/
TRANSFER CASE
U OPEN
V SPEED CONTROL, WIPER/
WASHER
W OPEN
X AUDIO SYSTEMS
Y OPEN
Z GROUNDS
DESCRIPTION - SECTION IDENTIFICATION AND
INFORMATION
The wiring diagrams are grouped into individual
sections. If a component is most likely found in a par-
ticular group, it will be shown complete (all wires,
connectors, and pins) within that group. For exam-
ple, the Auto Shutdown Relay is most likely to be
found in Group 30, so it is shown there complete. It
can, however, be shown partially in another group if
it contains some associated wiring.
Splice diagrams in Section 8W-70 show the entire
splice and provide references to other sections the
splices serves. Section 8W-70 only contains splice dia-
grams that are not shown in their entirety some-
where else in the wiring diagrams.
Section 8W-80 shows each connector and the cir-
cuits involved with that connector. The connectors
are identified using the name/number on the dia-
gram pages.
WIRING SECTION CHART
GROUP TOPIC
8W-01 thru
8W-09General information and Diagram
Overview
8W-10 thru
8W-19Main Sources of Power and
Vehicle Grounding
8W-20 thru
8W-29Starting and Charging
8W-30 thru
8W-39Powertrain/Drivetrain Systems
8W-40 thru
8W-49Body Electrical items and A/C
8W-50 thru
8W-59Exterior Lighting, Wipers and
Trailer Tow
8W-60 thru
8W-69Power Accessories
8W-70 Splice Information
8W-80 Connector Pin Outs
8W-91 Connector, Ground and Splice
Locations
8W - 01 - 6 8W-01 WIRING DIAGRAM INFORMATIONWJ
WIRING DIAGRAM INFORMATION (Continued)
Page 662 of 2199
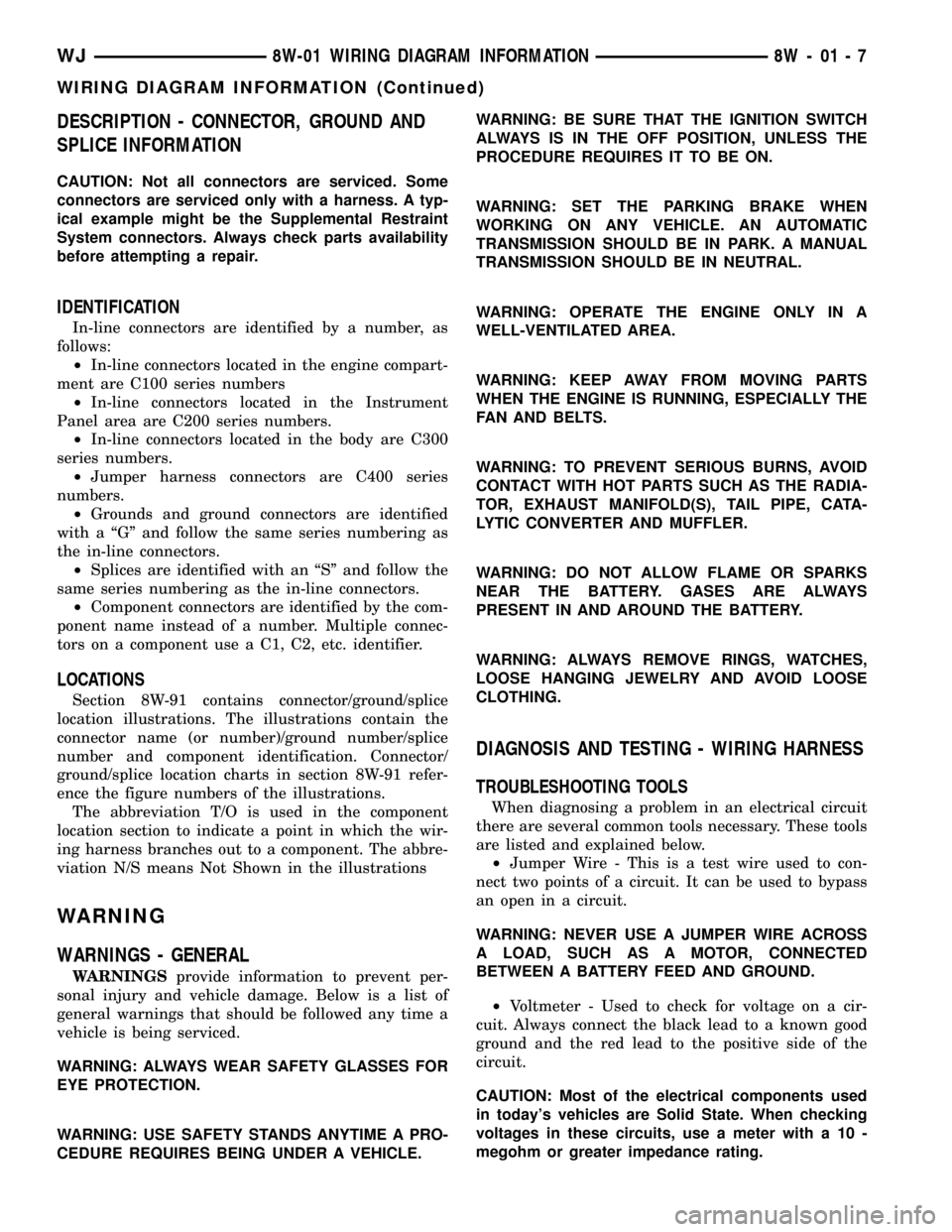
DESCRIPTION - CONNECTOR, GROUND AND
SPLICE INFORMATION
CAUTION: Not all connectors are serviced. Some
connectors are serviced only with a harness. A typ-
ical example might be the Supplemental Restraint
System connectors. Always check parts availability
before attempting a repair.
IDENTIFICATION
In-line connectors are identified by a number, as
follows:
²In-line connectors located in the engine compart-
ment are C100 series numbers
²In-line connectors located in the Instrument
Panel area are C200 series numbers.
²In-line connectors located in the body are C300
series numbers.
²Jumper harness connectors are C400 series
numbers.
²Grounds and ground connectors are identified
with a ªGº and follow the same series numbering as
the in-line connectors.
²Splices are identified with an ªSº and follow the
same series numbering as the in-line connectors.
²Component connectors are identified by the com-
ponent name instead of a number. Multiple connec-
tors on a component use a C1, C2, etc. identifier.
LOCATIONS
Section 8W-91 contains connector/ground/splice
location illustrations. The illustrations contain the
connector name (or number)/ground number/splice
number and component identification. Connector/
ground/splice location charts in section 8W-91 refer-
ence the figure numbers of the illustrations.
The abbreviation T/O is used in the component
location section to indicate a point in which the wir-
ing harness branches out to a component. The abbre-
viation N/S means Not Shown in the illustrations
WARNING
WARNINGS - GENERAL
WARNINGSprovide information to prevent per-
sonal injury and vehicle damage. Below is a list of
general warnings that should be followed any time a
vehicle is being serviced.
WARNING: ALWAYS WEAR SAFETY GLASSES FOR
EYE PROTECTION.
WARNING: USE SAFETY STANDS ANYTIME A PRO-
CEDURE REQUIRES BEING UNDER A VEHICLE.WARNING: BE SURE THAT THE IGNITION SWITCH
ALWAYS IS IN THE OFF POSITION, UNLESS THE
PROCEDURE REQUIRES IT TO BE ON.
WARNING: SET THE PARKING BRAKE WHEN
WORKING ON ANY VEHICLE. AN AUTOMATIC
TRANSMISSION SHOULD BE IN PARK. A MANUAL
TRANSMISSION SHOULD BE IN NEUTRAL.
WARNING: OPERATE THE ENGINE ONLY IN A
WELL-VENTILATED AREA.
WARNING: KEEP AWAY FROM MOVING PARTS
WHEN THE ENGINE IS RUNNING, ESPECIALLY THE
FAN AND BELTS.
WARNING: TO PREVENT SERIOUS BURNS, AVOID
CONTACT WITH HOT PARTS SUCH AS THE RADIA-
TOR, EXHAUST MANIFOLD(S), TAIL PIPE, CATA-
LYTIC CONVERTER AND MUFFLER.
WARNING: DO NOT ALLOW FLAME OR SPARKS
NEAR THE BATTERY. GASES ARE ALWAYS
PRESENT IN AND AROUND THE BATTERY.
WARNING: ALWAYS REMOVE RINGS, WATCHES,
LOOSE HANGING JEWELRY AND AVOID LOOSE
CLOTHING.
DIAGNOSIS AND TESTING - WIRING HARNESS
TROUBLESHOOTING TOOLS
When diagnosing a problem in an electrical circuit
there are several common tools necessary. These tools
are listed and explained below.
²Jumper Wire - This is a test wire used to con-
nect two points of a circuit. It can be used to bypass
an open in a circuit.
WARNING: NEVER USE A JUMPER WIRE ACROSS
A LOAD, SUCH AS A MOTOR, CONNECTED
BETWEEN A BATTERY FEED AND GROUND.
²Voltmeter - Used to check for voltage on a cir-
cuit. Always connect the black lead to a known good
ground and the red lead to the positive side of the
circuit.
CAUTION: Most of the electrical components used
in today's vehicles are Solid State. When checking
voltages in these circuits, use a meter with a 10 -
megohm or greater impedance rating.
WJ8W-01 WIRING DIAGRAM INFORMATION 8W - 01 - 7
WIRING DIAGRAM INFORMATION (Continued)