Message JEEP GRAND CHEROKEE 2002 WJ / 2.G User Guide
[x] Cancel search | Manufacturer: JEEP, Model Year: 2002, Model line: GRAND CHEROKEE, Model: JEEP GRAND CHEROKEE 2002 WJ / 2.GPages: 2199, PDF Size: 76.01 MB
Page 315 of 2199
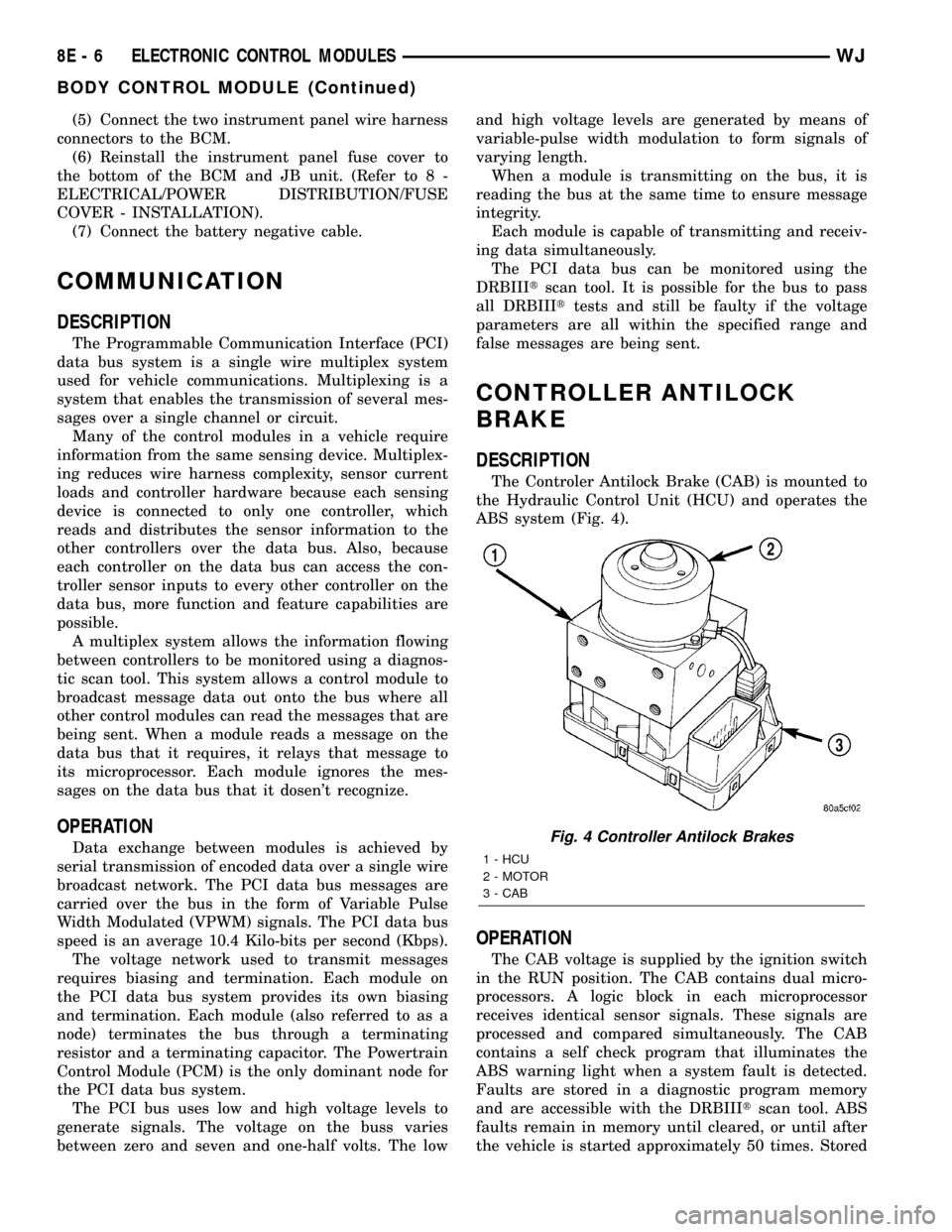
(5) Connect the two instrument panel wire harness
connectors to the BCM.
(6) Reinstall the instrument panel fuse cover to
the bottom of the BCM and JB unit. (Refer to 8 -
ELECTRICAL/POWER DISTRIBUTION/FUSE
COVER - INSTALLATION).
(7) Connect the battery negative cable.
COMMUNICATION
DESCRIPTION
The Programmable Communication Interface (PCI)
data bus system is a single wire multiplex system
used for vehicle communications. Multiplexing is a
system that enables the transmission of several mes-
sages over a single channel or circuit.
Many of the control modules in a vehicle require
information from the same sensing device. Multiplex-
ing reduces wire harness complexity, sensor current
loads and controller hardware because each sensing
device is connected to only one controller, which
reads and distributes the sensor information to the
other controllers over the data bus. Also, because
each controller on the data bus can access the con-
troller sensor inputs to every other controller on the
data bus, more function and feature capabilities are
possible.
A multiplex system allows the information flowing
between controllers to be monitored using a diagnos-
tic scan tool. This system allows a control module to
broadcast message data out onto the bus where all
other control modules can read the messages that are
being sent. When a module reads a message on the
data bus that it requires, it relays that message to
its microprocessor. Each module ignores the mes-
sages on the data bus that it dosen't recognize.
OPERATION
Data exchange between modules is achieved by
serial transmission of encoded data over a single wire
broadcast network. The PCI data bus messages are
carried over the bus in the form of Variable Pulse
Width Modulated (VPWM) signals. The PCI data bus
speed is an average 10.4 Kilo-bits per second (Kbps).
The voltage network used to transmit messages
requires biasing and termination. Each module on
the PCI data bus system provides its own biasing
and termination. Each module (also referred to as a
node) terminates the bus through a terminating
resistor and a terminating capacitor. The Powertrain
Control Module (PCM) is the only dominant node for
the PCI data bus system.
The PCI bus uses low and high voltage levels to
generate signals. The voltage on the buss varies
between zero and seven and one-half volts. The lowand high voltage levels are generated by means of
variable-pulse width modulation to form signals of
varying length.
When a module is transmitting on the bus, it is
reading the bus at the same time to ensure message
integrity.
Each module is capable of transmitting and receiv-
ing data simultaneously.
The PCI data bus can be monitored using the
DRBIIItscan tool. It is possible for the bus to pass
all DRBIIIttests and still be faulty if the voltage
parameters are all within the specified range and
false messages are being sent.
CONTROLLER ANTILOCK
BRAKE
DESCRIPTION
The Controler Antilock Brake (CAB) is mounted to
the Hydraulic Control Unit (HCU) and operates the
ABS system (Fig. 4).
OPERATION
The CAB voltage is supplied by the ignition switch
in the RUN position. The CAB contains dual micro-
processors. A logic block in each microprocessor
receives identical sensor signals. These signals are
processed and compared simultaneously. The CAB
contains a self check program that illuminates the
ABS warning light when a system fault is detected.
Faults are stored in a diagnostic program memory
and are accessible with the DRBIIItscan tool. ABS
faults remain in memory until cleared, or until after
the vehicle is started approximately 50 times. Stored
Fig. 4 Controller Antilock Brakes
1 - HCU
2 - MOTOR
3 - CAB
8E - 6 ELECTRONIC CONTROL MODULESWJ
BODY CONTROL MODULE (Continued)
Page 317 of 2199
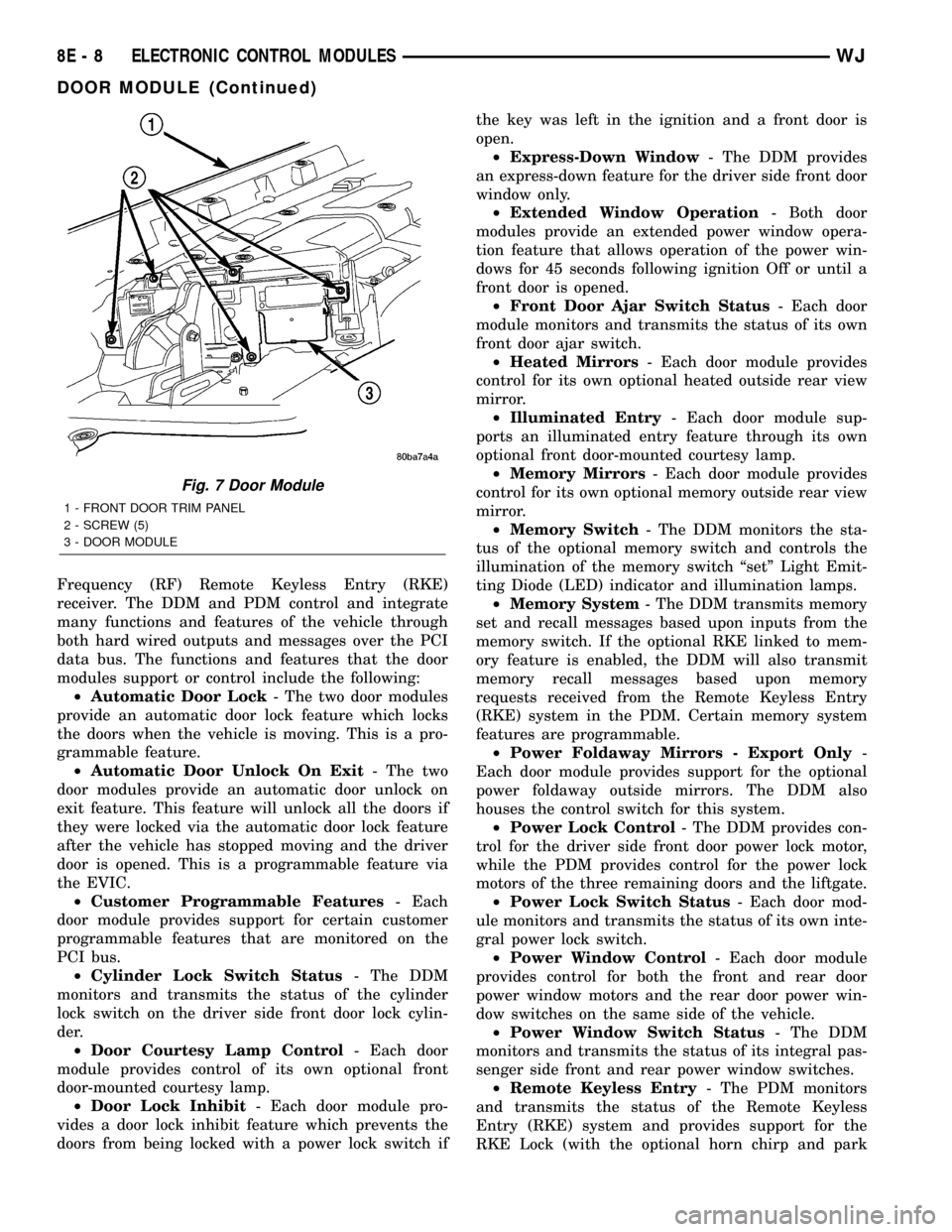
Frequency (RF) Remote Keyless Entry (RKE)
receiver. The DDM and PDM control and integrate
many functions and features of the vehicle through
both hard wired outputs and messages over the PCI
data bus. The functions and features that the door
modules support or control include the following:
²Automatic Door Lock- The two door modules
provide an automatic door lock feature which locks
the doors when the vehicle is moving. This is a pro-
grammable feature.
²Automatic Door Unlock On Exit- The two
door modules provide an automatic door unlock on
exit feature. This feature will unlock all the doors if
they were locked via the automatic door lock feature
after the vehicle has stopped moving and the driver
door is opened. This is a programmable feature via
the EVIC.
²Customer Programmable Features- Each
door module provides support for certain customer
programmable features that are monitored on the
PCI bus.
²Cylinder Lock Switch Status- The DDM
monitors and transmits the status of the cylinder
lock switch on the driver side front door lock cylin-
der.
²Door Courtesy Lamp Control- Each door
module provides control of its own optional front
door-mounted courtesy lamp.
²Door Lock Inhibit- Each door module pro-
vides a door lock inhibit feature which prevents the
doors from being locked with a power lock switch ifthe key was left in the ignition and a front door is
open.
²Express-Down Window- The DDM provides
an express-down feature for the driver side front door
window only.
²Extended Window Operation- Both door
modules provide an extended power window opera-
tion feature that allows operation of the power win-
dows for 45 seconds following ignition Off or until a
front door is opened.
²Front Door Ajar Switch Status- Each door
module monitors and transmits the status of its own
front door ajar switch.
²Heated Mirrors- Each door module provides
control for its own optional heated outside rear view
mirror.
²Illuminated Entry- Each door module sup-
ports an illuminated entry feature through its own
optional front door-mounted courtesy lamp.
²Memory Mirrors- Each door module provides
control for its own optional memory outside rear view
mirror.
²Memory Switch- The DDM monitors the sta-
tus of the optional memory switch and controls the
illumination of the memory switch ªsetº Light Emit-
ting Diode (LED) indicator and illumination lamps.
²Memory System- The DDM transmits memory
set and recall messages based upon inputs from the
memory switch. If the optional RKE linked to mem-
ory feature is enabled, the DDM will also transmit
memory recall messages based upon memory
requests received from the Remote Keyless Entry
(RKE) system in the PDM. Certain memory system
features are programmable.
²Power Foldaway Mirrors - Export Only-
Each door module provides support for the optional
power foldaway outside mirrors. The DDM also
houses the control switch for this system.
²Power Lock Control- The DDM provides con-
trol for the driver side front door power lock motor,
while the PDM provides control for the power lock
motors of the three remaining doors and the liftgate.
²Power Lock Switch Status- Each door mod-
ule monitors and transmits the status of its own inte-
gral power lock switch.
²Power Window Control- Each door module
provides control for both the front and rear door
power window motors and the rear door power win-
dow switches on the same side of the vehicle.
²Power Window Switch Status- The DDM
monitors and transmits the status of its integral pas-
senger side front and rear power window switches.
²Remote Keyless Entry- The PDM monitors
and transmits the status of the Remote Keyless
Entry (RKE) system and provides support for the
RKE Lock (with the optional horn chirp and park
Fig. 7 Door Module
1 - FRONT DOOR TRIM PANEL
2 - SCREW (5)
3 - DOOR MODULE
8E - 8 ELECTRONIC CONTROL MODULESWJ
DOOR MODULE (Continued)
Page 318 of 2199
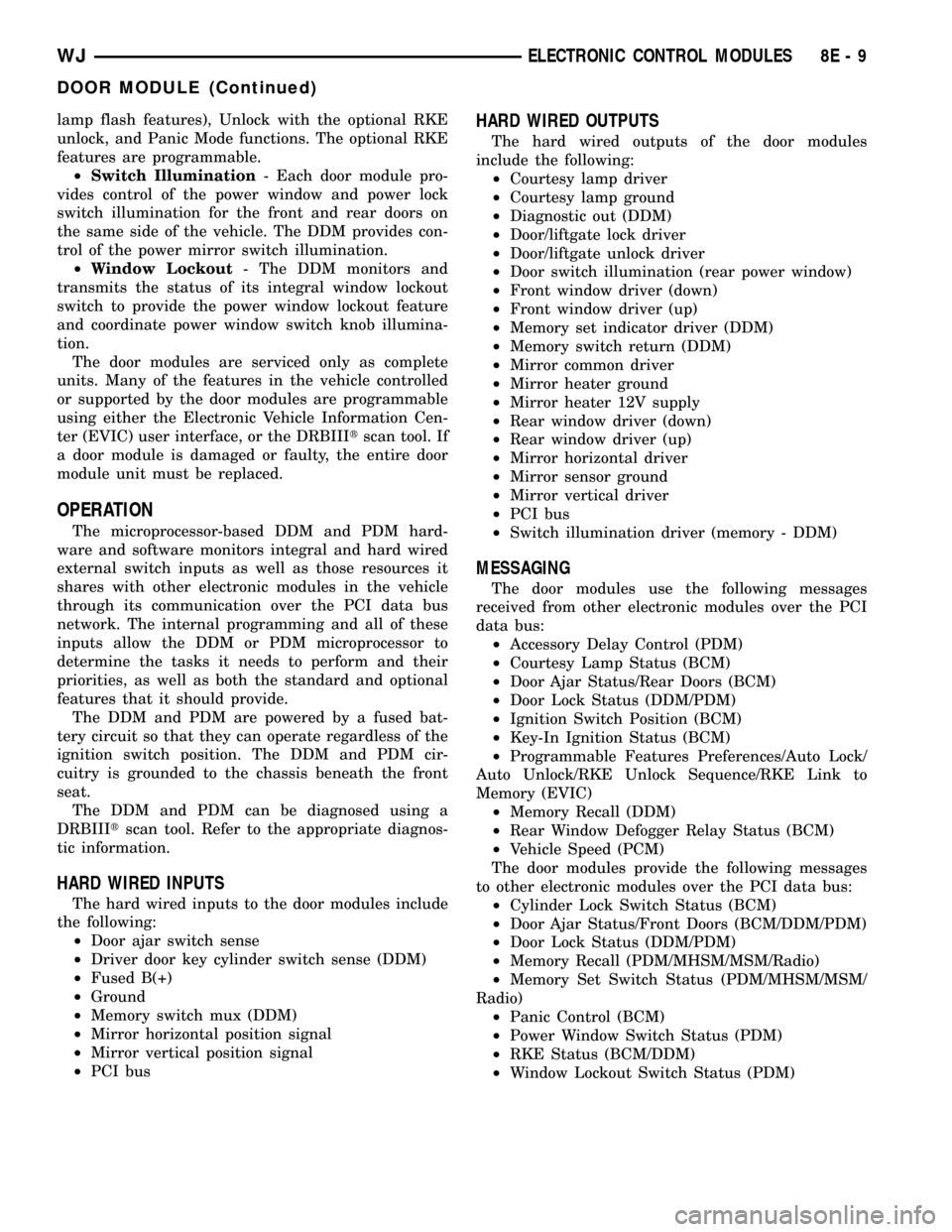
lamp flash features), Unlock with the optional RKE
unlock, and Panic Mode functions. The optional RKE
features are programmable.
²Switch Illumination- Each door module pro-
vides control of the power window and power lock
switch illumination for the front and rear doors on
the same side of the vehicle. The DDM provides con-
trol of the power mirror switch illumination.
²Window Lockout- The DDM monitors and
transmits the status of its integral window lockout
switch to provide the power window lockout feature
and coordinate power window switch knob illumina-
tion.
The door modules are serviced only as complete
units. Many of the features in the vehicle controlled
or supported by the door modules are programmable
using either the Electronic Vehicle Information Cen-
ter (EVIC) user interface, or the DRBIIItscan tool. If
a door module is damaged or faulty, the entire door
module unit must be replaced.
OPERATION
The microprocessor-based DDM and PDM hard-
ware and software monitors integral and hard wired
external switch inputs as well as those resources it
shares with other electronic modules in the vehicle
through its communication over the PCI data bus
network. The internal programming and all of these
inputs allow the DDM or PDM microprocessor to
determine the tasks it needs to perform and their
priorities, as well as both the standard and optional
features that it should provide.
The DDM and PDM are powered by a fused bat-
tery circuit so that they can operate regardless of the
ignition switch position. The DDM and PDM cir-
cuitry is grounded to the chassis beneath the front
seat.
The DDM and PDM can be diagnosed using a
DRBIIItscan tool. Refer to the appropriate diagnos-
tic information.
HARD WIRED INPUTS
The hard wired inputs to the door modules include
the following:
²Door ajar switch sense
²Driver door key cylinder switch sense (DDM)
²Fused B(+)
²Ground
²Memory switch mux (DDM)
²Mirror horizontal position signal
²Mirror vertical position signal
²PCI bus
HARD WIRED OUTPUTS
The hard wired outputs of the door modules
include the following:
²Courtesy lamp driver
²Courtesy lamp ground
²Diagnostic out (DDM)
²Door/liftgate lock driver
²Door/liftgate unlock driver
²Door switch illumination (rear power window)
²Front window driver (down)
²Front window driver (up)
²Memory set indicator driver (DDM)
²Memory switch return (DDM)
²Mirror common driver
²Mirror heater ground
²Mirror heater 12V supply
²Rear window driver (down)
²Rear window driver (up)
²Mirror horizontal driver
²Mirror sensor ground
²Mirror vertical driver
²PCI bus
²Switch illumination driver (memory - DDM)
MESSAGING
The door modules use the following messages
received from other electronic modules over the PCI
data bus:
²Accessory Delay Control (PDM)
²Courtesy Lamp Status (BCM)
²Door Ajar Status/Rear Doors (BCM)
²Door Lock Status (DDM/PDM)
²Ignition Switch Position (BCM)
²Key-In Ignition Status (BCM)
²Programmable Features Preferences/Auto Lock/
Auto Unlock/RKE Unlock Sequence/RKE Link to
Memory (EVIC)
²Memory Recall (DDM)
²Rear Window Defogger Relay Status (BCM)
²Vehicle Speed (PCM)
The door modules provide the following messages
to other electronic modules over the PCI data bus:
²Cylinder Lock Switch Status (BCM)
²Door Ajar Status/Front Doors (BCM/DDM/PDM)
²Door Lock Status (DDM/PDM)
²Memory Recall (PDM/MHSM/MSM/Radio)
²Memory Set Switch Status (PDM/MHSM/MSM/
Radio)
²Panic Control (BCM)
²Power Window Switch Status (PDM)
²RKE Status (BCM/DDM)
²Window Lockout Switch Status (PDM)
WJELECTRONIC CONTROL MODULES 8E - 9
DOOR MODULE (Continued)
Page 320 of 2199
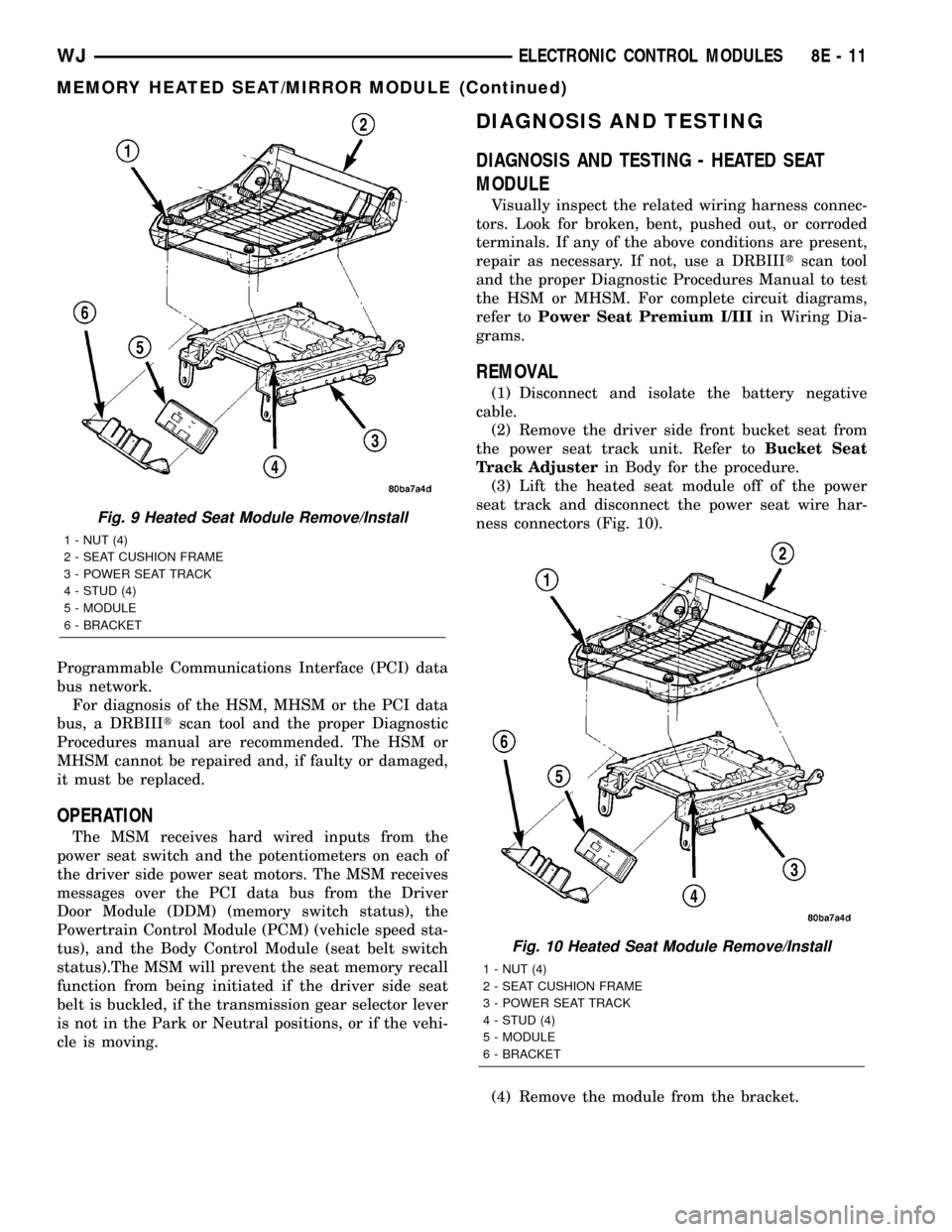
Programmable Communications Interface (PCI) data
bus network.
For diagnosis of the HSM, MHSM or the PCI data
bus, a DRBIIItscan tool and the proper Diagnostic
Procedures manual are recommended. The HSM or
MHSM cannot be repaired and, if faulty or damaged,
it must be replaced.
OPERATION
The MSM receives hard wired inputs from the
power seat switch and the potentiometers on each of
the driver side power seat motors. The MSM receives
messages over the PCI data bus from the Driver
Door Module (DDM) (memory switch status), the
Powertrain Control Module (PCM) (vehicle speed sta-
tus), and the Body Control Module (seat belt switch
status).The MSM will prevent the seat memory recall
function from being initiated if the driver side seat
belt is buckled, if the transmission gear selector lever
is not in the Park or Neutral positions, or if the vehi-
cle is moving.
DIAGNOSIS AND TESTING
DIAGNOSIS AND TESTING - HEATED SEAT
MODULE
Visually inspect the related wiring harness connec-
tors. Look for broken, bent, pushed out, or corroded
terminals. If any of the above conditions are present,
repair as necessary. If not, use a DRBIIItscan tool
and the proper Diagnostic Procedures Manual to test
the HSM or MHSM. For complete circuit diagrams,
refer toPower Seat Premium I/IIIin Wiring Dia-
grams.
REMOVAL
(1) Disconnect and isolate the battery negative
cable.
(2) Remove the driver side front bucket seat from
the power seat track unit. Refer toBucket Seat
Track Adjusterin Body for the procedure.
(3) Lift the heated seat module off of the power
seat track and disconnect the power seat wire har-
ness connectors (Fig. 10).
(4) Remove the module from the bracket.
Fig. 9 Heated Seat Module Remove/Install
1 - NUT (4)
2 - SEAT CUSHION FRAME
3 - POWER SEAT TRACK
4 - STUD (4)
5 - MODULE
6 - BRACKET
Fig. 10 Heated Seat Module Remove/Install
1 - NUT (4)
2 - SEAT CUSHION FRAME
3 - POWER SEAT TRACK
4 - STUD (4)
5 - MODULE
6 - BRACKET
WJELECTRONIC CONTROL MODULES 8E - 11
MEMORY HEATED SEAT/MIRROR MODULE (Continued)
Page 327 of 2199
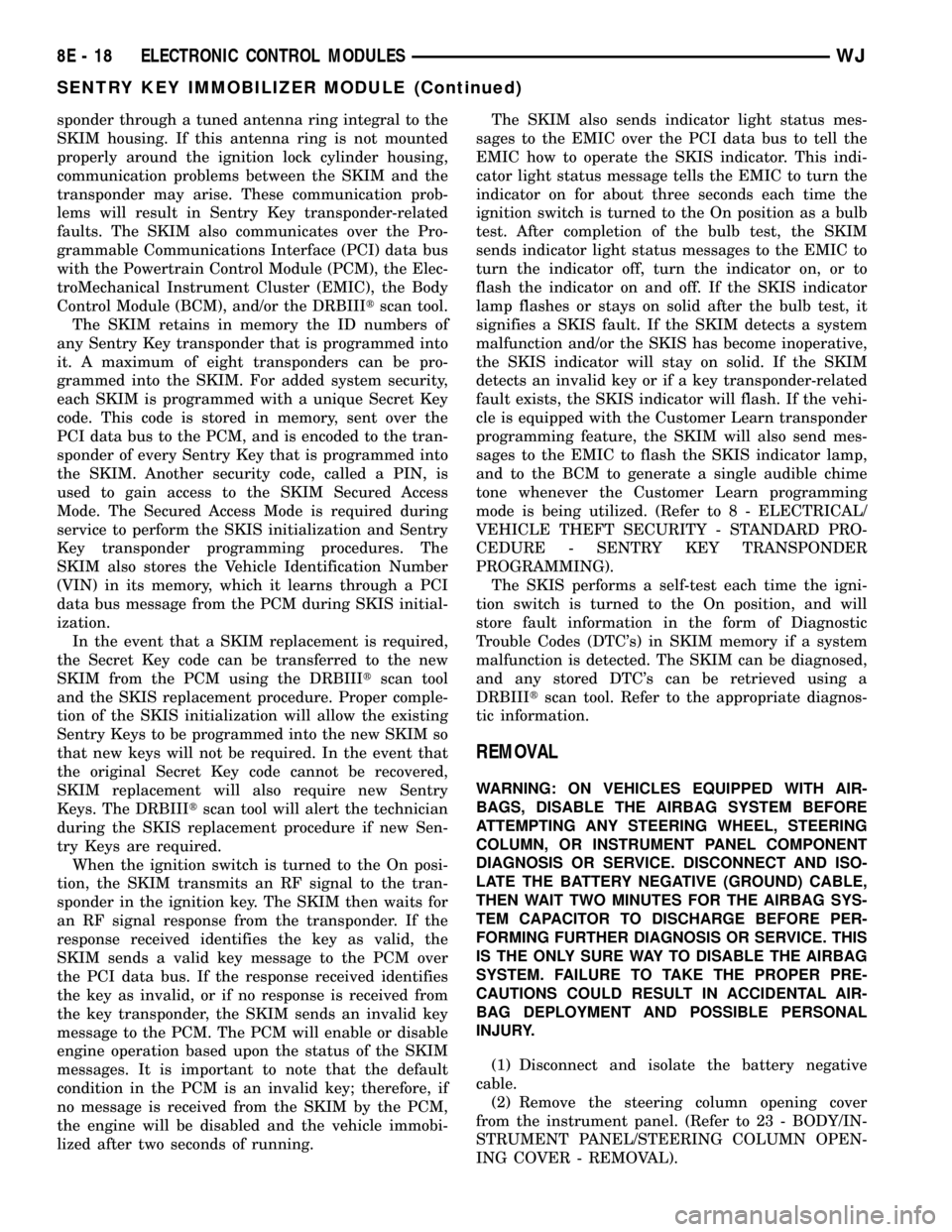
sponder through a tuned antenna ring integral to the
SKIM housing. If this antenna ring is not mounted
properly around the ignition lock cylinder housing,
communication problems between the SKIM and the
transponder may arise. These communication prob-
lems will result in Sentry Key transponder-related
faults. The SKIM also communicates over the Pro-
grammable Communications Interface (PCI) data bus
with the Powertrain Control Module (PCM), the Elec-
troMechanical Instrument Cluster (EMIC), the Body
Control Module (BCM), and/or the DRBIIItscan tool.
The SKIM retains in memory the ID numbers of
any Sentry Key transponder that is programmed into
it. A maximum of eight transponders can be pro-
grammed into the SKIM. For added system security,
each SKIM is programmed with a unique Secret Key
code. This code is stored in memory, sent over the
PCI data bus to the PCM, and is encoded to the tran-
sponder of every Sentry Key that is programmed into
the SKIM. Another security code, called a PIN, is
used to gain access to the SKIM Secured Access
Mode. The Secured Access Mode is required during
service to perform the SKIS initialization and Sentry
Key transponder programming procedures. The
SKIM also stores the Vehicle Identification Number
(VIN) in its memory, which it learns through a PCI
data bus message from the PCM during SKIS initial-
ization.
In the event that a SKIM replacement is required,
the Secret Key code can be transferred to the new
SKIM from the PCM using the DRBIIItscan tool
and the SKIS replacement procedure. Proper comple-
tion of the SKIS initialization will allow the existing
Sentry Keys to be programmed into the new SKIM so
that new keys will not be required. In the event that
the original Secret Key code cannot be recovered,
SKIM replacement will also require new Sentry
Keys. The DRBIIItscan tool will alert the technician
during the SKIS replacement procedure if new Sen-
try Keys are required.
When the ignition switch is turned to the On posi-
tion, the SKIM transmits an RF signal to the tran-
sponder in the ignition key. The SKIM then waits for
an RF signal response from the transponder. If the
response received identifies the key as valid, the
SKIM sends a valid key message to the PCM over
the PCI data bus. If the response received identifies
the key as invalid, or if no response is received from
the key transponder, the SKIM sends an invalid key
message to the PCM. The PCM will enable or disable
engine operation based upon the status of the SKIM
messages. It is important to note that the default
condition in the PCM is an invalid key; therefore, if
no message is received from the SKIM by the PCM,
the engine will be disabled and the vehicle immobi-
lized after two seconds of running.The SKIM also sends indicator light status mes-
sages to the EMIC over the PCI data bus to tell the
EMIC how to operate the SKIS indicator. This indi-
cator light status message tells the EMIC to turn the
indicator on for about three seconds each time the
ignition switch is turned to the On position as a bulb
test. After completion of the bulb test, the SKIM
sends indicator light status messages to the EMIC to
turn the indicator off, turn the indicator on, or to
flash the indicator on and off. If the SKIS indicator
lamp flashes or stays on solid after the bulb test, it
signifies a SKIS fault. If the SKIM detects a system
malfunction and/or the SKIS has become inoperative,
the SKIS indicator will stay on solid. If the SKIM
detects an invalid key or if a key transponder-related
fault exists, the SKIS indicator will flash. If the vehi-
cle is equipped with the Customer Learn transponder
programming feature, the SKIM will also send mes-
sages to the EMIC to flash the SKIS indicator lamp,
and to the BCM to generate a single audible chime
tone whenever the Customer Learn programming
mode is being utilized. (Refer to 8 - ELECTRICAL/
VEHICLE THEFT SECURITY - STANDARD PRO-
CEDURE - SENTRY KEY TRANSPONDER
PROGRAMMING).
The SKIS performs a self-test each time the igni-
tion switch is turned to the On position, and will
store fault information in the form of Diagnostic
Trouble Codes (DTC's) in SKIM memory if a system
malfunction is detected. The SKIM can be diagnosed,
and any stored DTC's can be retrieved using a
DRBIIItscan tool. Refer to the appropriate diagnos-
tic information.
REMOVAL
WARNING: ON VEHICLES EQUIPPED WITH AIR-
BAGS, DISABLE THE AIRBAG SYSTEM BEFORE
ATTEMPTING ANY STEERING WHEEL, STEERING
COLUMN, OR INSTRUMENT PANEL COMPONENT
DIAGNOSIS OR SERVICE. DISCONNECT AND ISO-
LATE THE BATTERY NEGATIVE (GROUND) CABLE,
THEN WAIT TWO MINUTES FOR THE AIRBAG SYS-
TEM CAPACITOR TO DISCHARGE BEFORE PER-
FORMING FURTHER DIAGNOSIS OR SERVICE. THIS
IS THE ONLY SURE WAY TO DISABLE THE AIRBAG
SYSTEM. FAILURE TO TAKE THE PROPER PRE-
CAUTIONS COULD RESULT IN ACCIDENTAL AIR-
BAG DEPLOYMENT AND POSSIBLE PERSONAL
INJURY.
(1) Disconnect and isolate the battery negative
cable.
(2) Remove the steering column opening cover
from the instrument panel. (Refer to 23 - BODY/IN-
STRUMENT PANEL/STEERING COLUMN OPEN-
ING COVER - REMOVAL).
8E - 18 ELECTRONIC CONTROL MODULESWJ
SENTRY KEY IMMOBILIZER MODULE (Continued)
Page 373 of 2199
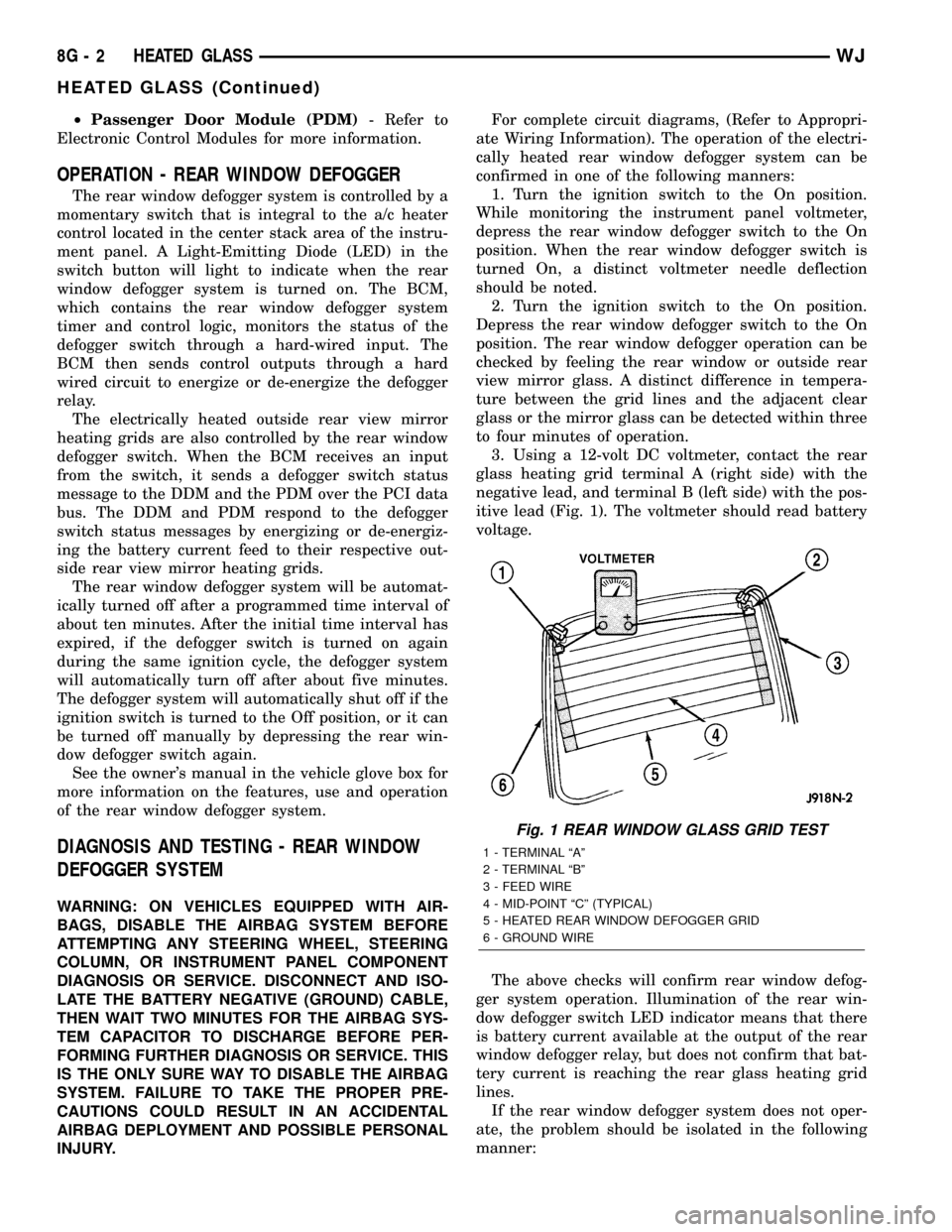
²Passenger Door Module (PDM)- Refer to
Electronic Control Modules for more information.
OPERATION - REAR WINDOW DEFOGGER
The rear window defogger system is controlled by a
momentary switch that is integral to the a/c heater
control located in the center stack area of the instru-
ment panel. A Light-Emitting Diode (LED) in the
switch button will light to indicate when the rear
window defogger system is turned on. The BCM,
which contains the rear window defogger system
timer and control logic, monitors the status of the
defogger switch through a hard-wired input. The
BCM then sends control outputs through a hard
wired circuit to energize or de-energize the defogger
relay.
The electrically heated outside rear view mirror
heating grids are also controlled by the rear window
defogger switch. When the BCM receives an input
from the switch, it sends a defogger switch status
message to the DDM and the PDM over the PCI data
bus. The DDM and PDM respond to the defogger
switch status messages by energizing or de-energiz-
ing the battery current feed to their respective out-
side rear view mirror heating grids.
The rear window defogger system will be automat-
ically turned off after a programmed time interval of
about ten minutes. After the initial time interval has
expired, if the defogger switch is turned on again
during the same ignition cycle, the defogger system
will automatically turn off after about five minutes.
The defogger system will automatically shut off if the
ignition switch is turned to the Off position, or it can
be turned off manually by depressing the rear win-
dow defogger switch again.
See the owner's manual in the vehicle glove box for
more information on the features, use and operation
of the rear window defogger system.
DIAGNOSIS AND TESTING - REAR WINDOW
DEFOGGER SYSTEM
WARNING: ON VEHICLES EQUIPPED WITH AIR-
BAGS, DISABLE THE AIRBAG SYSTEM BEFORE
ATTEMPTING ANY STEERING WHEEL, STEERING
COLUMN, OR INSTRUMENT PANEL COMPONENT
DIAGNOSIS OR SERVICE. DISCONNECT AND ISO-
LATE THE BATTERY NEGATIVE (GROUND) CABLE,
THEN WAIT TWO MINUTES FOR THE AIRBAG SYS-
TEM CAPACITOR TO DISCHARGE BEFORE PER-
FORMING FURTHER DIAGNOSIS OR SERVICE. THIS
IS THE ONLY SURE WAY TO DISABLE THE AIRBAG
SYSTEM. FAILURE TO TAKE THE PROPER PRE-
CAUTIONS COULD RESULT IN AN ACCIDENTAL
AIRBAG DEPLOYMENT AND POSSIBLE PERSONAL
INJURY.For complete circuit diagrams, (Refer to Appropri-
ate Wiring Information). The operation of the electri-
cally heated rear window defogger system can be
confirmed in one of the following manners:
1. Turn the ignition switch to the On position.
While monitoring the instrument panel voltmeter,
depress the rear window defogger switch to the On
position. When the rear window defogger switch is
turned On, a distinct voltmeter needle deflection
should be noted.
2. Turn the ignition switch to the On position.
Depress the rear window defogger switch to the On
position. The rear window defogger operation can be
checked by feeling the rear window or outside rear
view mirror glass. A distinct difference in tempera-
ture between the grid lines and the adjacent clear
glass or the mirror glass can be detected within three
to four minutes of operation.
3. Using a 12-volt DC voltmeter, contact the rear
glass heating grid terminal A (right side) with the
negative lead, and terminal B (left side) with the pos-
itive lead (Fig. 1). The voltmeter should read battery
voltage.
The above checks will confirm rear window defog-
ger system operation. Illumination of the rear win-
dow defogger switch LED indicator means that there
is battery current available at the output of the rear
window defogger relay, but does not confirm that bat-
tery current is reaching the rear glass heating grid
lines.
If the rear window defogger system does not oper-
ate, the problem should be isolated in the following
manner:
Fig. 1 REAR WINDOW GLASS GRID TEST
1 - TERMINAL ªAº
2 - TERMINAL ªBº
3 - FEED WIRE
4 - MID-POINT ªCº (TYPICAL)
5 - HEATED REAR WINDOW DEFOGGER GRID
6 - GROUND WIRE
8G - 2 HEATED GLASSWJ
HEATED GLASS (Continued)
Page 379 of 2199
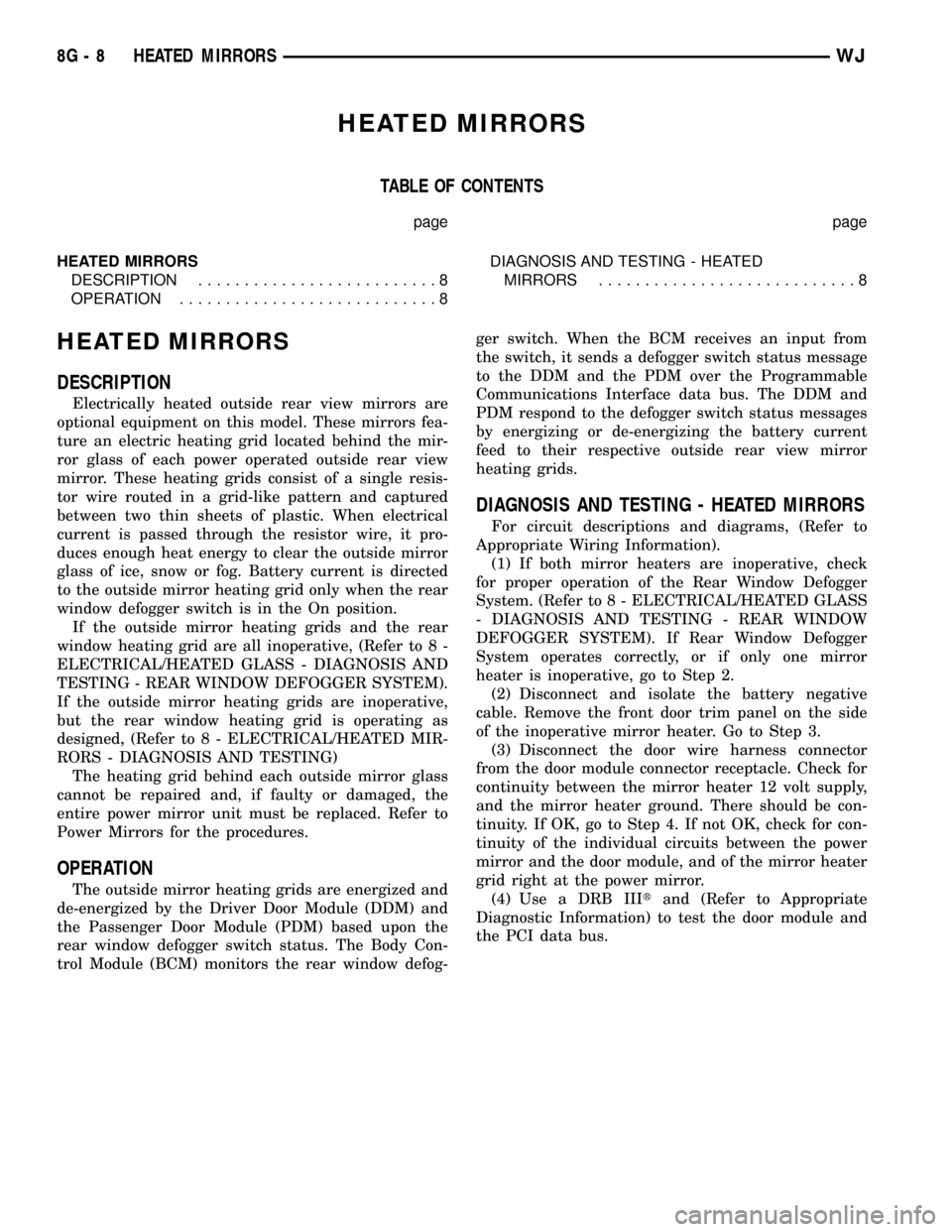
HEATED MIRRORS
TABLE OF CONTENTS
page page
HEATED MIRRORS
DESCRIPTION..........................8
OPERATION............................8DIAGNOSIS AND TESTING - HEATED
MIRRORS............................8
HEATED MIRRORS
DESCRIPTION
Electrically heated outside rear view mirrors are
optional equipment on this model. These mirrors fea-
ture an electric heating grid located behind the mir-
ror glass of each power operated outside rear view
mirror. These heating grids consist of a single resis-
tor wire routed in a grid-like pattern and captured
between two thin sheets of plastic. When electrical
current is passed through the resistor wire, it pro-
duces enough heat energy to clear the outside mirror
glass of ice, snow or fog. Battery current is directed
to the outside mirror heating grid only when the rear
window defogger switch is in the On position.
If the outside mirror heating grids and the rear
window heating grid are all inoperative, (Refer to 8 -
ELECTRICAL/HEATED GLASS - DIAGNOSIS AND
TESTING - REAR WINDOW DEFOGGER SYSTEM).
If the outside mirror heating grids are inoperative,
but the rear window heating grid is operating as
designed, (Refer to 8 - ELECTRICAL/HEATED MIR-
RORS - DIAGNOSIS AND TESTING)
The heating grid behind each outside mirror glass
cannot be repaired and, if faulty or damaged, the
entire power mirror unit must be replaced. Refer to
Power Mirrors for the procedures.
OPERATION
The outside mirror heating grids are energized and
de-energized by the Driver Door Module (DDM) and
the Passenger Door Module (PDM) based upon the
rear window defogger switch status. The Body Con-
trol Module (BCM) monitors the rear window defog-ger switch. When the BCM receives an input from
the switch, it sends a defogger switch status message
to the DDM and the PDM over the Programmable
Communications Interface data bus. The DDM and
PDM respond to the defogger switch status messages
by energizing or de-energizing the battery current
feed to their respective outside rear view mirror
heating grids.
DIAGNOSIS AND TESTING - HEATED MIRRORS
For circuit descriptions and diagrams, (Refer to
Appropriate Wiring Information).
(1) If both mirror heaters are inoperative, check
for proper operation of the Rear Window Defogger
System. (Refer to 8 - ELECTRICAL/HEATED GLASS
- DIAGNOSIS AND TESTING - REAR WINDOW
DEFOGGER SYSTEM). If Rear Window Defogger
System operates correctly, or if only one mirror
heater is inoperative, go to Step 2.
(2) Disconnect and isolate the battery negative
cable. Remove the front door trim panel on the side
of the inoperative mirror heater. Go to Step 3.
(3) Disconnect the door wire harness connector
from the door module connector receptacle. Check for
continuity between the mirror heater 12 volt supply,
and the mirror heater ground. There should be con-
tinuity. If OK, go to Step 4. If not OK, check for con-
tinuity of the individual circuits between the power
mirror and the door module, and of the mirror heater
grid right at the power mirror.
(4) Use a DRB IIItand (Refer to Appropriate
Diagnostic Information) to test the door module and
the PCI data bus.
8G - 8 HEATED MIRRORSWJ
Page 381 of 2199
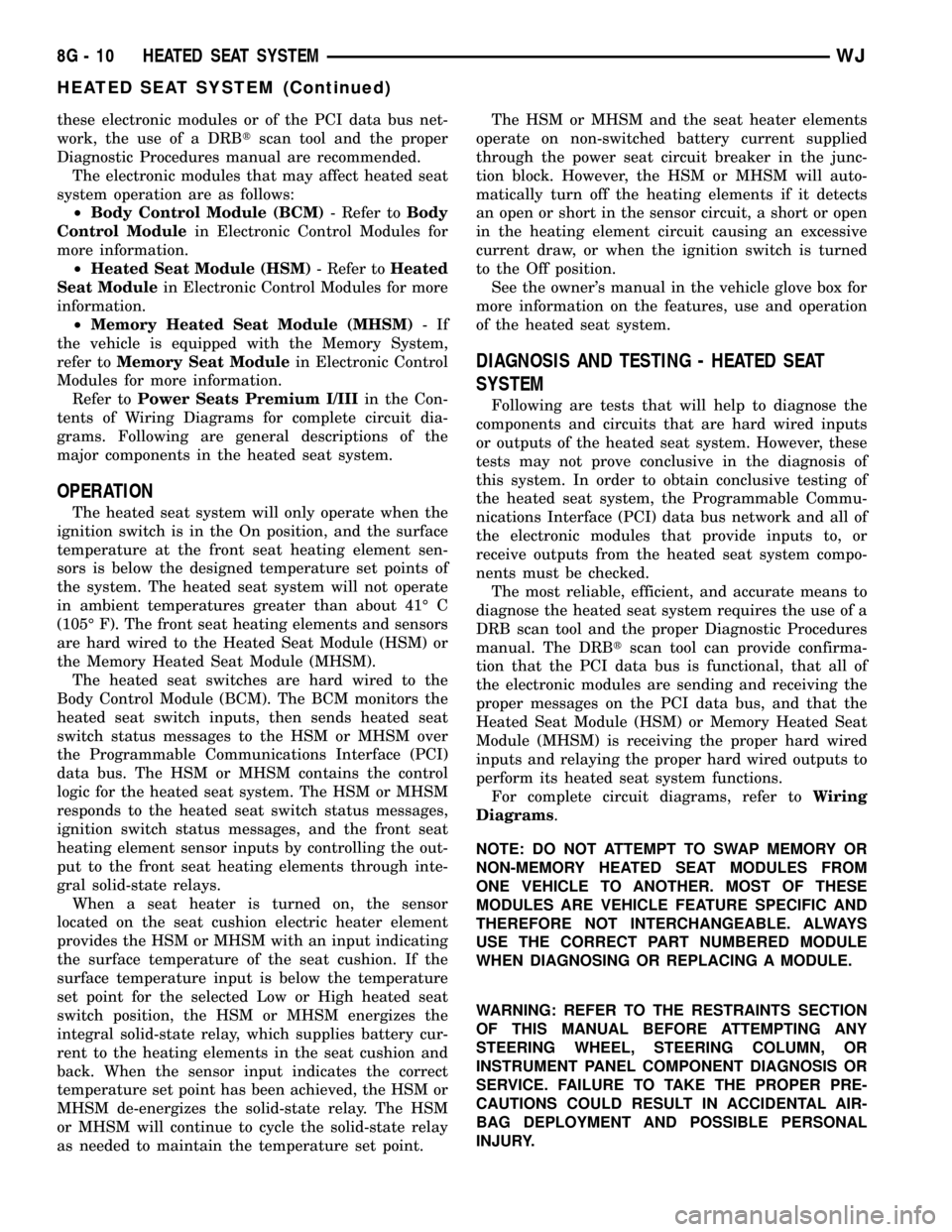
these electronic modules or of the PCI data bus net-
work, the use of a DRBtscan tool and the proper
Diagnostic Procedures manual are recommended.
The electronic modules that may affect heated seat
system operation are as follows:
²Body Control Module (BCM)- Refer toBody
Control Modulein Electronic Control Modules for
more information.
²Heated Seat Module (HSM)- Refer toHeated
Seat Modulein Electronic Control Modules for more
information.
²Memory Heated Seat Module (MHSM)-If
the vehicle is equipped with the Memory System,
refer toMemory Seat Modulein Electronic Control
Modules for more information.
Refer toPower Seats Premium I/IIIin the Con-
tents of Wiring Diagrams for complete circuit dia-
grams. Following are general descriptions of the
major components in the heated seat system.
OPERATION
The heated seat system will only operate when the
ignition switch is in the On position, and the surface
temperature at the front seat heating element sen-
sors is below the designed temperature set points of
the system. The heated seat system will not operate
in ambient temperatures greater than about 41É C
(105É F). The front seat heating elements and sensors
are hard wired to the Heated Seat Module (HSM) or
the Memory Heated Seat Module (MHSM).
The heated seat switches are hard wired to the
Body Control Module (BCM). The BCM monitors the
heated seat switch inputs, then sends heated seat
switch status messages to the HSM or MHSM over
the Programmable Communications Interface (PCI)
data bus. The HSM or MHSM contains the control
logic for the heated seat system. The HSM or MHSM
responds to the heated seat switch status messages,
ignition switch status messages, and the front seat
heating element sensor inputs by controlling the out-
put to the front seat heating elements through inte-
gral solid-state relays.
When a seat heater is turned on, the sensor
located on the seat cushion electric heater element
provides the HSM or MHSM with an input indicating
the surface temperature of the seat cushion. If the
surface temperature input is below the temperature
set point for the selected Low or High heated seat
switch position, the HSM or MHSM energizes the
integral solid-state relay, which supplies battery cur-
rent to the heating elements in the seat cushion and
back. When the sensor input indicates the correct
temperature set point has been achieved, the HSM or
MHSM de-energizes the solid-state relay. The HSM
or MHSM will continue to cycle the solid-state relay
as needed to maintain the temperature set point.The HSM or MHSM and the seat heater elements
operate on non-switched battery current supplied
through the power seat circuit breaker in the junc-
tion block. However, the HSM or MHSM will auto-
matically turn off the heating elements if it detects
an open or short in the sensor circuit, a short or open
in the heating element circuit causing an excessive
current draw, or when the ignition switch is turned
to the Off position.
See the owner's manual in the vehicle glove box for
more information on the features, use and operation
of the heated seat system.
DIAGNOSIS AND TESTING - HEATED SEAT
SYSTEM
Following are tests that will help to diagnose the
components and circuits that are hard wired inputs
or outputs of the heated seat system. However, these
tests may not prove conclusive in the diagnosis of
this system. In order to obtain conclusive testing of
the heated seat system, the Programmable Commu-
nications Interface (PCI) data bus network and all of
the electronic modules that provide inputs to, or
receive outputs from the heated seat system compo-
nents must be checked.
The most reliable, efficient, and accurate means to
diagnose the heated seat system requires the use of a
DRB scan tool and the proper Diagnostic Procedures
manual. The DRBtscan tool can provide confirma-
tion that the PCI data bus is functional, that all of
the electronic modules are sending and receiving the
proper messages on the PCI data bus, and that the
Heated Seat Module (HSM) or Memory Heated Seat
Module (MHSM) is receiving the proper hard wired
inputs and relaying the proper hard wired outputs to
perform its heated seat system functions.
For complete circuit diagrams, refer toWiring
Diagrams.
NOTE: DO NOT ATTEMPT TO SWAP MEMORY OR
NON-MEMORY HEATED SEAT MODULES FROM
ONE VEHICLE TO ANOTHER. MOST OF THESE
MODULES ARE VEHICLE FEATURE SPECIFIC AND
THEREFORE NOT INTERCHANGEABLE. ALWAYS
USE THE CORRECT PART NUMBERED MODULE
WHEN DIAGNOSING OR REPLACING A MODULE.
WARNING: REFER TO THE RESTRAINTS SECTION
OF THIS MANUAL BEFORE ATTEMPTING ANY
STEERING WHEEL, STEERING COLUMN, OR
INSTRUMENT PANEL COMPONENT DIAGNOSIS OR
SERVICE. FAILURE TO TAKE THE PROPER PRE-
CAUTIONS COULD RESULT IN ACCIDENTAL AIR-
BAG DEPLOYMENT AND POSSIBLE PERSONAL
INJURY.
8G - 10 HEATED SEAT SYSTEMWJ
HEATED SEAT SYSTEM (Continued)
Page 382 of 2199
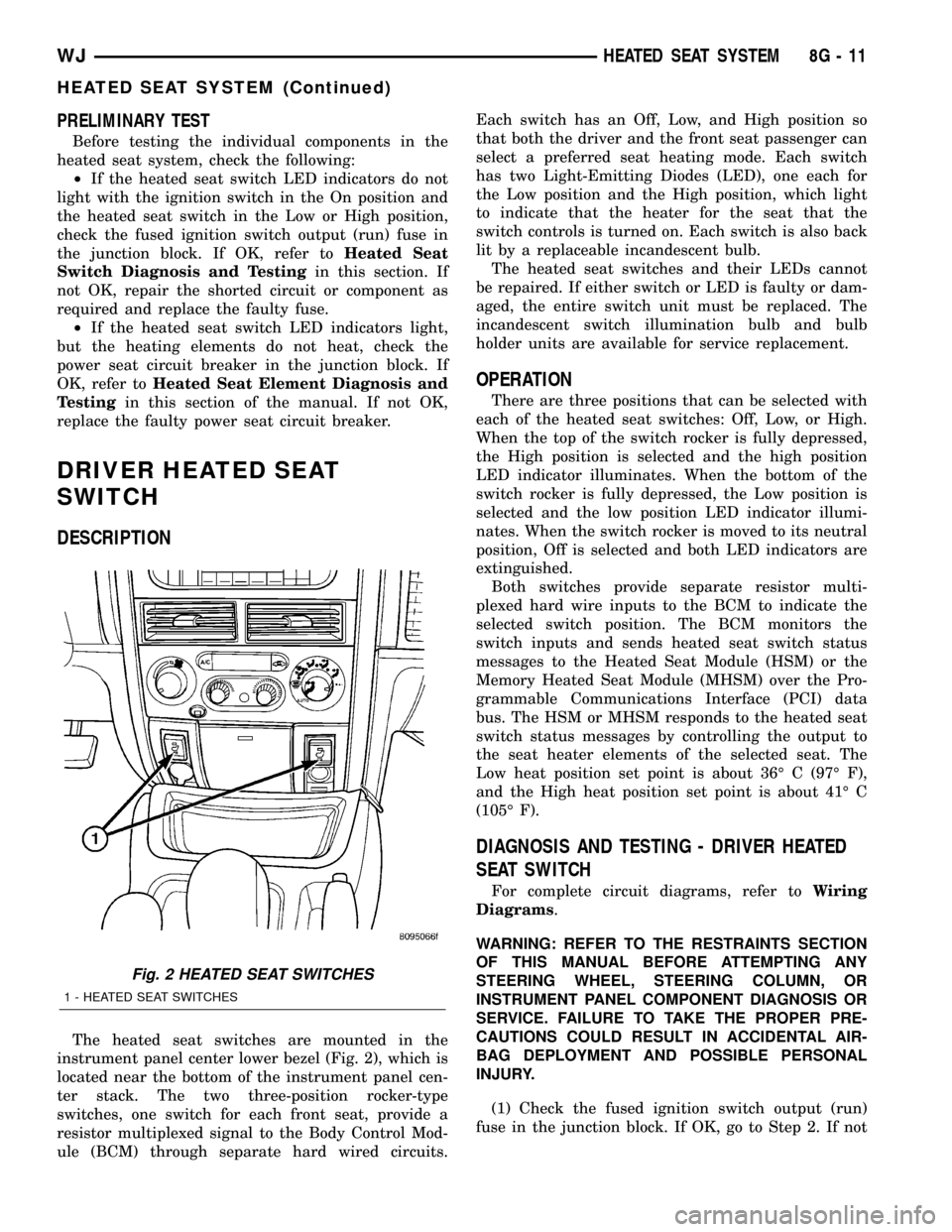
PRELIMINARY TEST
Before testing the individual components in the
heated seat system, check the following:
²If the heated seat switch LED indicators do not
light with the ignition switch in the On position and
the heated seat switch in the Low or High position,
check the fused ignition switch output (run) fuse in
the junction block. If OK, refer toHeated Seat
Switch Diagnosis and Testingin this section. If
not OK, repair the shorted circuit or component as
required and replace the faulty fuse.
²If the heated seat switch LED indicators light,
but the heating elements do not heat, check the
power seat circuit breaker in the junction block. If
OK, refer toHeated Seat Element Diagnosis and
Testingin this section of the manual. If not OK,
replace the faulty power seat circuit breaker.
DRIVER HEATED SEAT
SWITCH
DESCRIPTION
The heated seat switches are mounted in the
instrument panel center lower bezel (Fig. 2), which is
located near the bottom of the instrument panel cen-
ter stack. The two three-position rocker-type
switches, one switch for each front seat, provide a
resistor multiplexed signal to the Body Control Mod-
ule (BCM) through separate hard wired circuits.Each switch has an Off, Low, and High position so
that both the driver and the front seat passenger can
select a preferred seat heating mode. Each switch
has two Light-Emitting Diodes (LED), one each for
the Low position and the High position, which light
to indicate that the heater for the seat that the
switch controls is turned on. Each switch is also back
lit by a replaceable incandescent bulb.
The heated seat switches and their LEDs cannot
be repaired. If either switch or LED is faulty or dam-
aged, the entire switch unit must be replaced. The
incandescent switch illumination bulb and bulb
holder units are available for service replacement.
OPERATION
There are three positions that can be selected with
each of the heated seat switches: Off, Low, or High.
When the top of the switch rocker is fully depressed,
the High position is selected and the high position
LED indicator illuminates. When the bottom of the
switch rocker is fully depressed, the Low position is
selected and the low position LED indicator illumi-
nates. When the switch rocker is moved to its neutral
position, Off is selected and both LED indicators are
extinguished.
Both switches provide separate resistor multi-
plexed hard wire inputs to the BCM to indicate the
selected switch position. The BCM monitors the
switch inputs and sends heated seat switch status
messages to the Heated Seat Module (HSM) or the
Memory Heated Seat Module (MHSM) over the Pro-
grammable Communications Interface (PCI) data
bus. The HSM or MHSM responds to the heated seat
switch status messages by controlling the output to
the seat heater elements of the selected seat. The
Low heat position set point is about 36É C (97É F),
and the High heat position set point is about 41É C
(105É F).
DIAGNOSIS AND TESTING - DRIVER HEATED
SEAT SWITCH
For complete circuit diagrams, refer toWiring
Diagrams.
WARNING: REFER TO THE RESTRAINTS SECTION
OF THIS MANUAL BEFORE ATTEMPTING ANY
STEERING WHEEL, STEERING COLUMN, OR
INSTRUMENT PANEL COMPONENT DIAGNOSIS OR
SERVICE. FAILURE TO TAKE THE PROPER PRE-
CAUTIONS COULD RESULT IN ACCIDENTAL AIR-
BAG DEPLOYMENT AND POSSIBLE PERSONAL
INJURY.
(1) Check the fused ignition switch output (run)
fuse in the junction block. If OK, go to Step 2. If not
Fig. 2 HEATED SEAT SWITCHES
1 - HEATED SEAT SWITCHES
WJHEATED SEAT SYSTEM 8G - 11
HEATED SEAT SYSTEM (Continued)
Page 387 of 2199
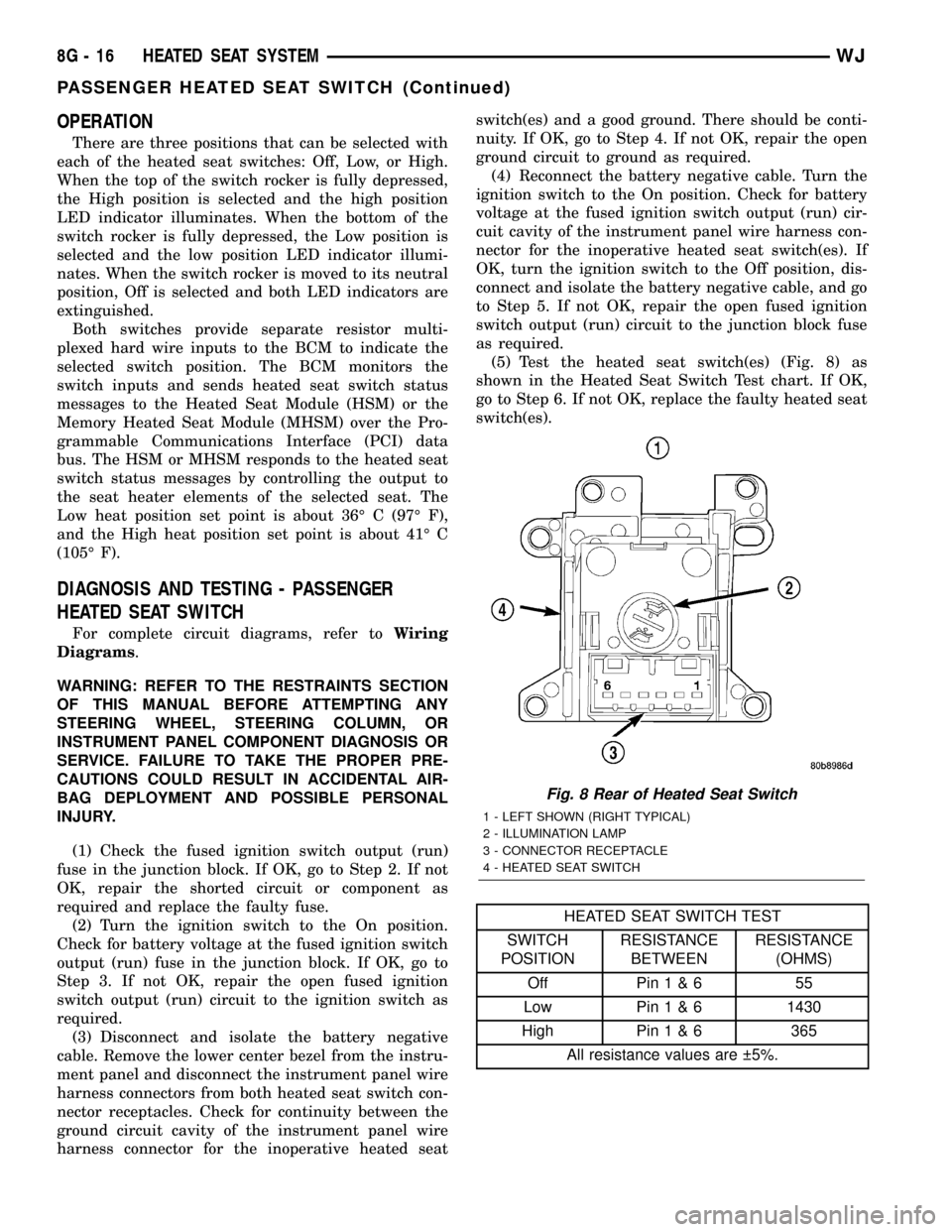
OPERATION
There are three positions that can be selected with
each of the heated seat switches: Off, Low, or High.
When the top of the switch rocker is fully depressed,
the High position is selected and the high position
LED indicator illuminates. When the bottom of the
switch rocker is fully depressed, the Low position is
selected and the low position LED indicator illumi-
nates. When the switch rocker is moved to its neutral
position, Off is selected and both LED indicators are
extinguished.
Both switches provide separate resistor multi-
plexed hard wire inputs to the BCM to indicate the
selected switch position. The BCM monitors the
switch inputs and sends heated seat switch status
messages to the Heated Seat Module (HSM) or the
Memory Heated Seat Module (MHSM) over the Pro-
grammable Communications Interface (PCI) data
bus. The HSM or MHSM responds to the heated seat
switch status messages by controlling the output to
the seat heater elements of the selected seat. The
Low heat position set point is about 36É C (97É F),
and the High heat position set point is about 41É C
(105É F).
DIAGNOSIS AND TESTING - PASSENGER
HEATED SEAT SWITCH
For complete circuit diagrams, refer toWiring
Diagrams.
WARNING: REFER TO THE RESTRAINTS SECTION
OF THIS MANUAL BEFORE ATTEMPTING ANY
STEERING WHEEL, STEERING COLUMN, OR
INSTRUMENT PANEL COMPONENT DIAGNOSIS OR
SERVICE. FAILURE TO TAKE THE PROPER PRE-
CAUTIONS COULD RESULT IN ACCIDENTAL AIR-
BAG DEPLOYMENT AND POSSIBLE PERSONAL
INJURY.
(1) Check the fused ignition switch output (run)
fuse in the junction block. If OK, go to Step 2. If not
OK, repair the shorted circuit or component as
required and replace the faulty fuse.
(2) Turn the ignition switch to the On position.
Check for battery voltage at the fused ignition switch
output (run) fuse in the junction block. If OK, go to
Step 3. If not OK, repair the open fused ignition
switch output (run) circuit to the ignition switch as
required.
(3) Disconnect and isolate the battery negative
cable. Remove the lower center bezel from the instru-
ment panel and disconnect the instrument panel wire
harness connectors from both heated seat switch con-
nector receptacles. Check for continuity between the
ground circuit cavity of the instrument panel wire
harness connector for the inoperative heated seatswitch(es) and a good ground. There should be conti-
nuity. If OK, go to Step 4. If not OK, repair the open
ground circuit to ground as required.
(4) Reconnect the battery negative cable. Turn the
ignition switch to the On position. Check for battery
voltage at the fused ignition switch output (run) cir-
cuit cavity of the instrument panel wire harness con-
nector for the inoperative heated seat switch(es). If
OK, turn the ignition switch to the Off position, dis-
connect and isolate the battery negative cable, and go
to Step 5. If not OK, repair the open fused ignition
switch output (run) circuit to the junction block fuse
as required.
(5) Test the heated seat switch(es) (Fig. 8) as
shown in the Heated Seat Switch Test chart. If OK,
go to Step 6. If not OK, replace the faulty heated seat
switch(es).
HEATED SEAT SWITCH TEST
SWITCH
POSITIONRESISTANCE
BETWEENRESISTANCE
(OHMS)
Off Pin1&6 55
Low Pin1&61430
High Pin1&6 365
All resistance values are 5%.
Fig. 8 Rear of Heated Seat Switch
1 - LEFT SHOWN (RIGHT TYPICAL)
2 - ILLUMINATION LAMP
3 - CONNECTOR RECEPTACLE
4 - HEATED SEAT SWITCH
8G - 16 HEATED SEAT SYSTEMWJ
PASSENGER HEATED SEAT SWITCH (Continued)