Ground strap JEEP GRAND CHEROKEE 2002 WJ / 2.G Owner's Manual
[x] Cancel search | Manufacturer: JEEP, Model Year: 2002, Model line: GRAND CHEROKEE, Model: JEEP GRAND CHEROKEE 2002 WJ / 2.GPages: 2199, PDF Size: 76.01 MB
Page 2104 of 2199
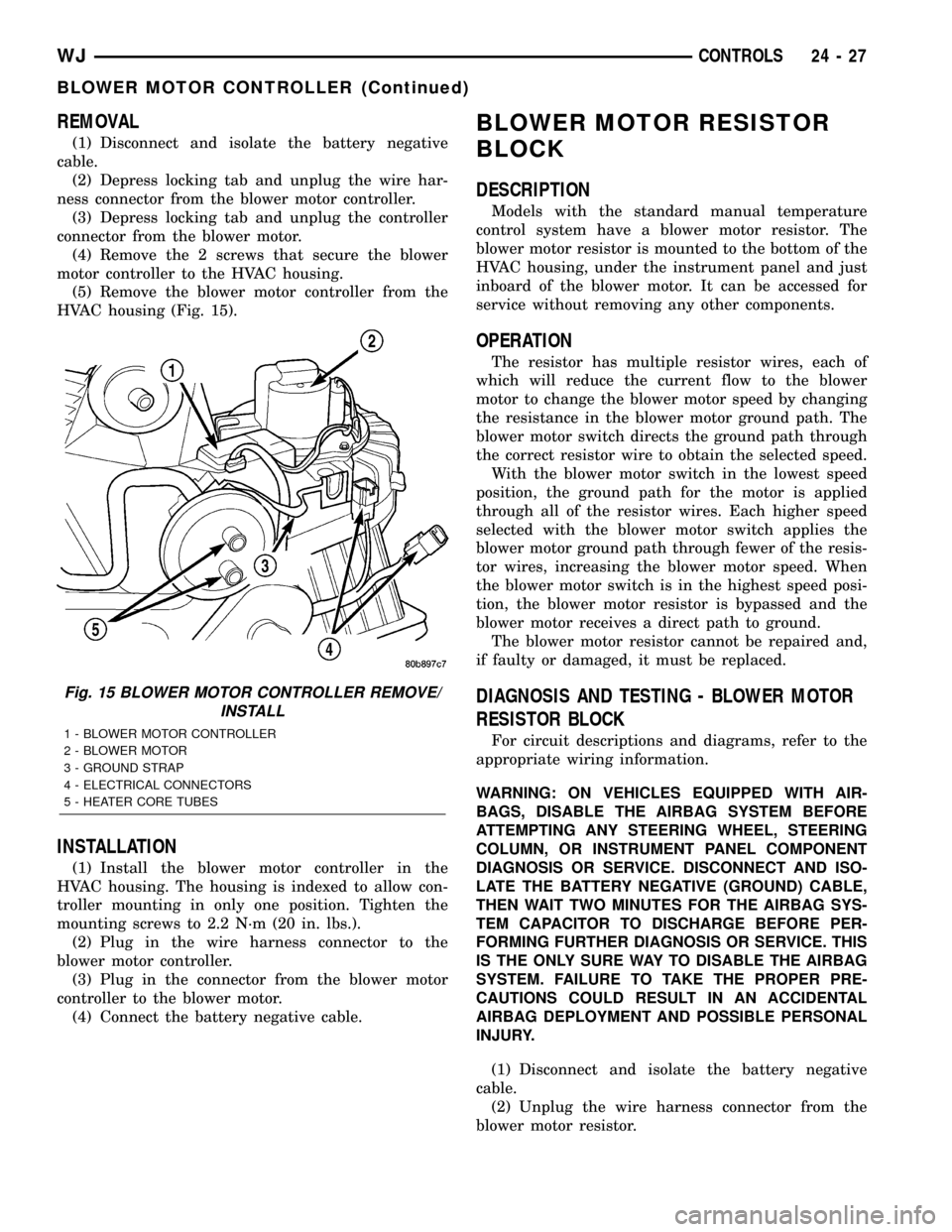
REMOVAL
(1) Disconnect and isolate the battery negative
cable.
(2) Depress locking tab and unplug the wire har-
ness connector from the blower motor controller.
(3) Depress locking tab and unplug the controller
connector from the blower motor.
(4) Remove the 2 screws that secure the blower
motor controller to the HVAC housing.
(5) Remove the blower motor controller from the
HVAC housing (Fig. 15).
INSTALLATION
(1) Install the blower motor controller in the
HVAC housing. The housing is indexed to allow con-
troller mounting in only one position. Tighten the
mounting screws to 2.2 N´m (20 in. lbs.).
(2) Plug in the wire harness connector to the
blower motor controller.
(3) Plug in the connector from the blower motor
controller to the blower motor.
(4) Connect the battery negative cable.
BLOWER MOTOR RESISTOR
BLOCK
DESCRIPTION
Models with the standard manual temperature
control system have a blower motor resistor. The
blower motor resistor is mounted to the bottom of the
HVAC housing, under the instrument panel and just
inboard of the blower motor. It can be accessed for
service without removing any other components.
OPERATION
The resistor has multiple resistor wires, each of
which will reduce the current flow to the blower
motor to change the blower motor speed by changing
the resistance in the blower motor ground path. The
blower motor switch directs the ground path through
the correct resistor wire to obtain the selected speed.
With the blower motor switch in the lowest speed
position, the ground path for the motor is applied
through all of the resistor wires. Each higher speed
selected with the blower motor switch applies the
blower motor ground path through fewer of the resis-
tor wires, increasing the blower motor speed. When
the blower motor switch is in the highest speed posi-
tion, the blower motor resistor is bypassed and the
blower motor receives a direct path to ground.
The blower motor resistor cannot be repaired and,
if faulty or damaged, it must be replaced.
DIAGNOSIS AND TESTING - BLOWER MOTOR
RESISTOR BLOCK
For circuit descriptions and diagrams, refer to the
appropriate wiring information.
WARNING: ON VEHICLES EQUIPPED WITH AIR-
BAGS, DISABLE THE AIRBAG SYSTEM BEFORE
ATTEMPTING ANY STEERING WHEEL, STEERING
COLUMN, OR INSTRUMENT PANEL COMPONENT
DIAGNOSIS OR SERVICE. DISCONNECT AND ISO-
LATE THE BATTERY NEGATIVE (GROUND) CABLE,
THEN WAIT TWO MINUTES FOR THE AIRBAG SYS-
TEM CAPACITOR TO DISCHARGE BEFORE PER-
FORMING FURTHER DIAGNOSIS OR SERVICE. THIS
IS THE ONLY SURE WAY TO DISABLE THE AIRBAG
SYSTEM. FAILURE TO TAKE THE PROPER PRE-
CAUTIONS COULD RESULT IN AN ACCIDENTAL
AIRBAG DEPLOYMENT AND POSSIBLE PERSONAL
INJURY.
(1) Disconnect and isolate the battery negative
cable.
(2) Unplug the wire harness connector from the
blower motor resistor.
Fig. 15 BLOWER MOTOR CONTROLLER REMOVE/
INSTALL
1 - BLOWER MOTOR CONTROLLER
2 - BLOWER MOTOR
3 - GROUND STRAP
4 - ELECTRICAL CONNECTORS
5 - HEATER CORE TUBES
WJCONTROLS 24 - 27
BLOWER MOTOR CONTROLLER (Continued)
Page 2105 of 2199
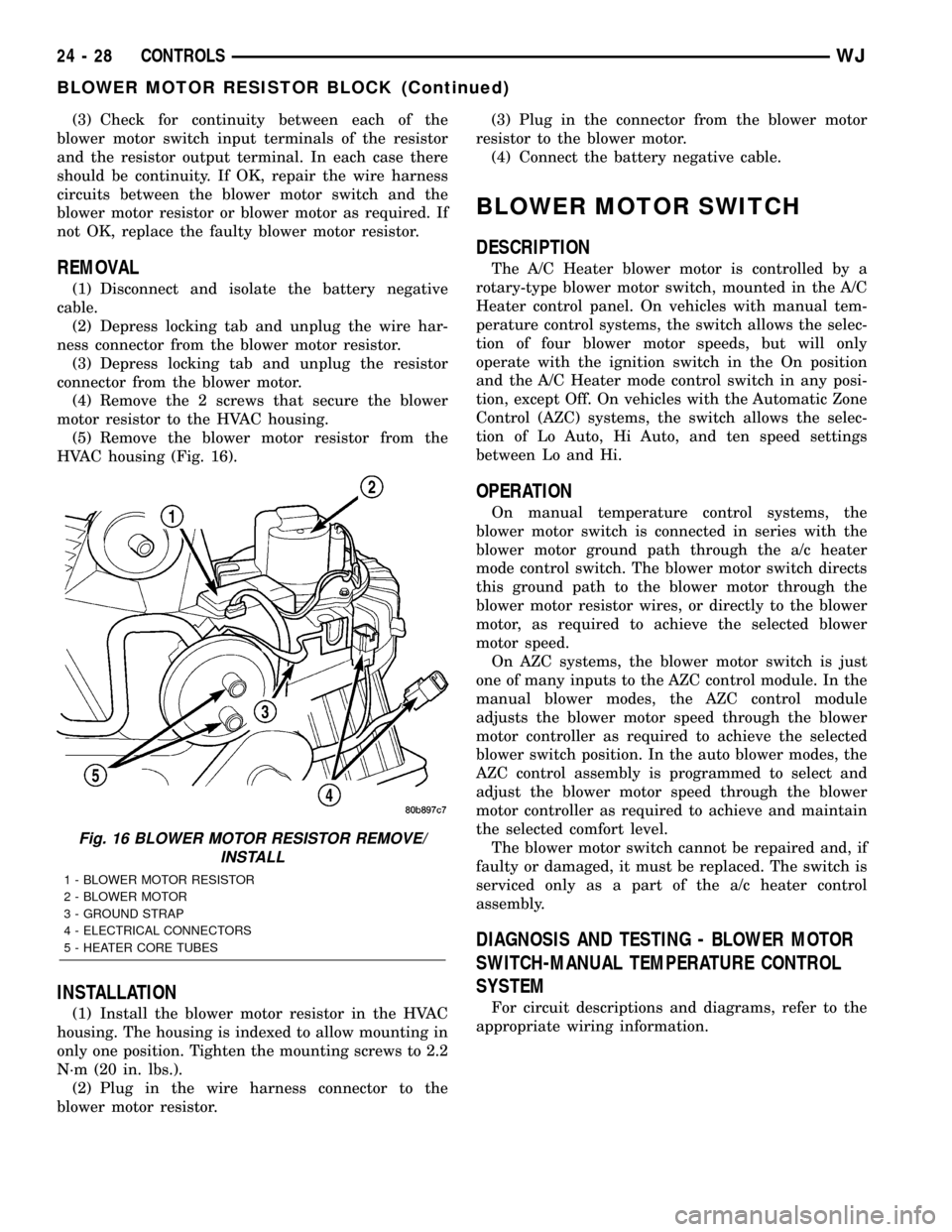
(3) Check for continuity between each of the
blower motor switch input terminals of the resistor
and the resistor output terminal. In each case there
should be continuity. If OK, repair the wire harness
circuits between the blower motor switch and the
blower motor resistor or blower motor as required. If
not OK, replace the faulty blower motor resistor.
REMOVAL
(1) Disconnect and isolate the battery negative
cable.
(2) Depress locking tab and unplug the wire har-
ness connector from the blower motor resistor.
(3) Depress locking tab and unplug the resistor
connector from the blower motor.
(4) Remove the 2 screws that secure the blower
motor resistor to the HVAC housing.
(5) Remove the blower motor resistor from the
HVAC housing (Fig. 16).
INSTALLATION
(1) Install the blower motor resistor in the HVAC
housing. The housing is indexed to allow mounting in
only one position. Tighten the mounting screws to 2.2
N´m (20 in. lbs.).
(2) Plug in the wire harness connector to the
blower motor resistor.(3) Plug in the connector from the blower motor
resistor to the blower motor.
(4) Connect the battery negative cable.
BLOWER MOTOR SWITCH
DESCRIPTION
The A/C Heater blower motor is controlled by a
rotary-type blower motor switch, mounted in the A/C
Heater control panel. On vehicles with manual tem-
perature control systems, the switch allows the selec-
tion of four blower motor speeds, but will only
operate with the ignition switch in the On position
and the A/C Heater mode control switch in any posi-
tion, except Off. On vehicles with the Automatic Zone
Control (AZC) systems, the switch allows the selec-
tion of Lo Auto, Hi Auto, and ten speed settings
between Lo and Hi.
OPERATION
On manual temperature control systems, the
blower motor switch is connected in series with the
blower motor ground path through the a/c heater
mode control switch. The blower motor switch directs
this ground path to the blower motor through the
blower motor resistor wires, or directly to the blower
motor, as required to achieve the selected blower
motor speed.
On AZC systems, the blower motor switch is just
one of many inputs to the AZC control module. In the
manual blower modes, the AZC control module
adjusts the blower motor speed through the blower
motor controller as required to achieve the selected
blower switch position. In the auto blower modes, the
AZC control assembly is programmed to select and
adjust the blower motor speed through the blower
motor controller as required to achieve and maintain
the selected comfort level.
The blower motor switch cannot be repaired and, if
faulty or damaged, it must be replaced. The switch is
serviced only as a part of the a/c heater control
assembly.
DIAGNOSIS AND TESTING - BLOWER MOTOR
SWITCH-MANUAL TEMPERATURE CONTROL
SYSTEM
For circuit descriptions and diagrams, refer to the
appropriate wiring information.
Fig. 16 BLOWER MOTOR RESISTOR REMOVE/
INSTALL
1 - BLOWER MOTOR RESISTOR
2 - BLOWER MOTOR
3 - GROUND STRAP
4 - ELECTRICAL CONNECTORS
5 - HEATER CORE TUBES
24 - 28 CONTROLSWJ
BLOWER MOTOR RESISTOR BLOCK (Continued)
Page 2115 of 2199
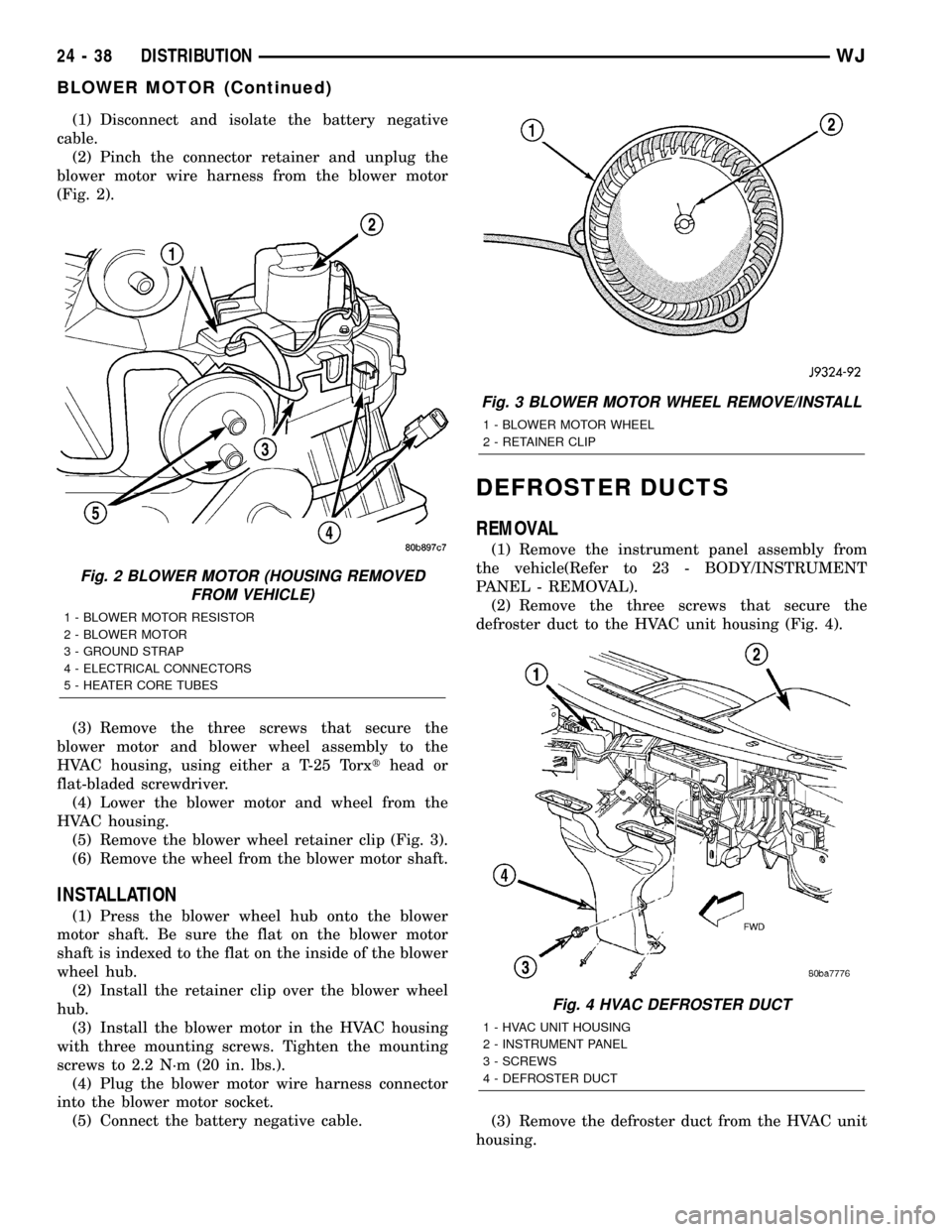
(1) Disconnect and isolate the battery negative
cable.
(2) Pinch the connector retainer and unplug the
blower motor wire harness from the blower motor
(Fig. 2).
(3) Remove the three screws that secure the
blower motor and blower wheel assembly to the
HVAC housing, using either a T-25 Torxthead or
flat-bladed screwdriver.
(4) Lower the blower motor and wheel from the
HVAC housing.
(5) Remove the blower wheel retainer clip (Fig. 3).
(6) Remove the wheel from the blower motor shaft.
INSTALLATION
(1) Press the blower wheel hub onto the blower
motor shaft. Be sure the flat on the blower motor
shaft is indexed to the flat on the inside of the blower
wheel hub.
(2) Install the retainer clip over the blower wheel
hub.
(3) Install the blower motor in the HVAC housing
with three mounting screws. Tighten the mounting
screws to 2.2 N´m (20 in. lbs.).
(4) Plug the blower motor wire harness connector
into the blower motor socket.
(5) Connect the battery negative cable.
DEFROSTER DUCTS
REMOVAL
(1) Remove the instrument panel assembly from
the vehicle(Refer to 23 - BODY/INSTRUMENT
PANEL - REMOVAL).
(2) Remove the three screws that secure the
defroster duct to the HVAC unit housing (Fig. 4).
(3) Remove the defroster duct from the HVAC unit
housing.
Fig. 2 BLOWER MOTOR (HOUSING REMOVED
FROM VEHICLE)
1 - BLOWER MOTOR RESISTOR
2 - BLOWER MOTOR
3 - GROUND STRAP
4 - ELECTRICAL CONNECTORS
5 - HEATER CORE TUBES
Fig. 3 BLOWER MOTOR WHEEL REMOVE/INSTALL
1 - BLOWER MOTOR WHEEL
2 - RETAINER CLIP
Fig. 4 HVAC DEFROSTER DUCT
1 - HVAC UNIT HOUSING
2 - INSTRUMENT PANEL
3 - SCREWS
4 - DEFROSTER DUCT
24 - 38 DISTRIBUTIONWJ
BLOWER MOTOR (Continued)
Page 2121 of 2199
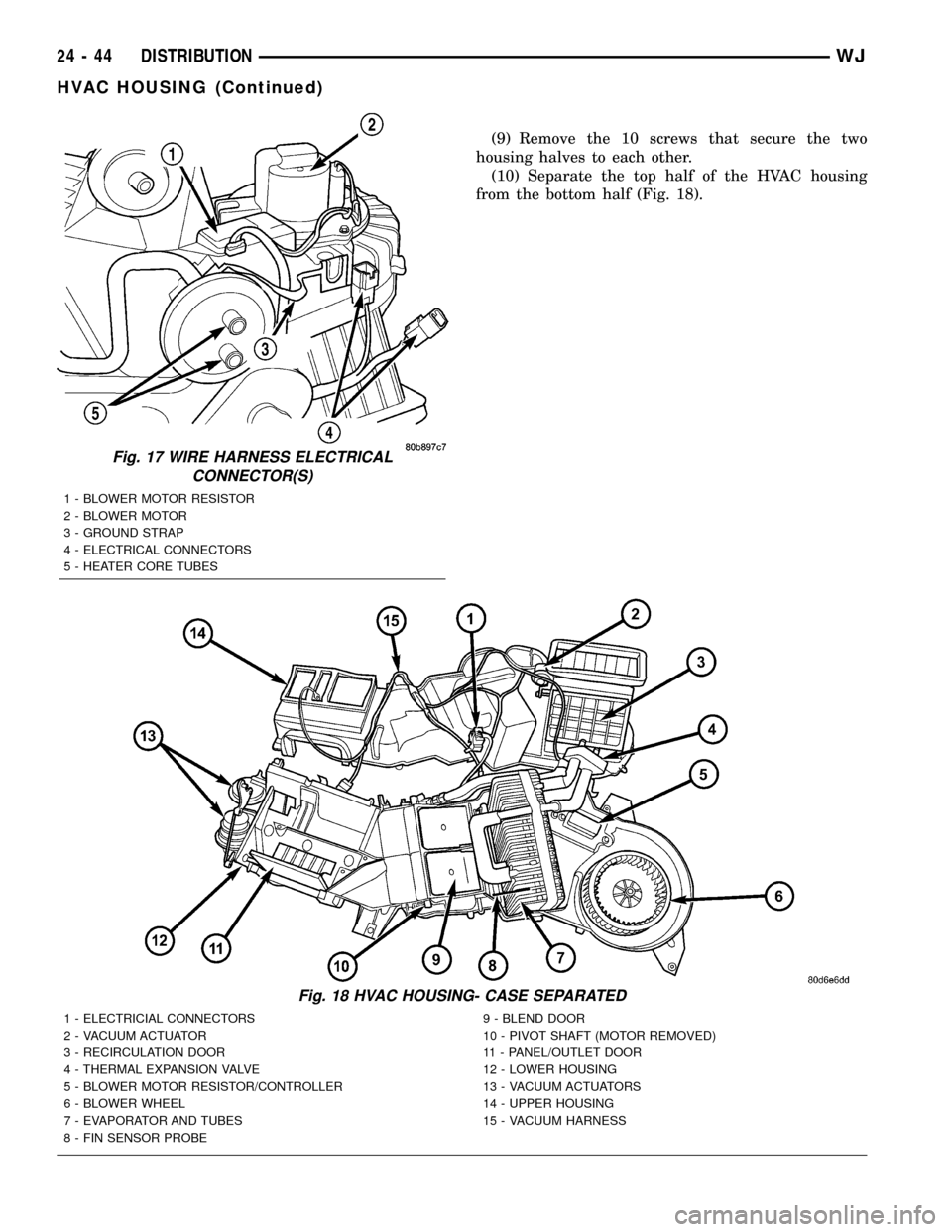
(9) Remove the 10 screws that secure the two
housing halves to each other.
(10) Separate the top half of the HVAC housing
from the bottom half (Fig. 18).
Fig. 17 WIRE HARNESS ELECTRICAL
CONNECTOR(S)
1 - BLOWER MOTOR RESISTOR
2 - BLOWER MOTOR
3 - GROUND STRAP
4 - ELECTRICAL CONNECTORS
5 - HEATER CORE TUBES
Fig. 18 HVAC HOUSING- CASE SEPARATED
1 - ELECTRICIAL CONNECTORS
2 - VACUUM ACTUATOR
3 - RECIRCULATION DOOR
4 - THERMAL EXPANSION VALVE
5 - BLOWER MOTOR RESISTOR/CONTROLLER
6 - BLOWER WHEEL
7 - EVAPORATOR AND TUBES
8 - FIN SENSOR PROBE9 - BLEND DOOR
10 - PIVOT SHAFT (MOTOR REMOVED)
11 - PANEL/OUTLET DOOR
12 - LOWER HOUSING
13 - VACUUM ACTUATORS
14 - UPPER HOUSING
15 - VACUUM HARNESS
24 - 44 DISTRIBUTIONWJ
HVAC HOUSING (Continued)
Page 2146 of 2199
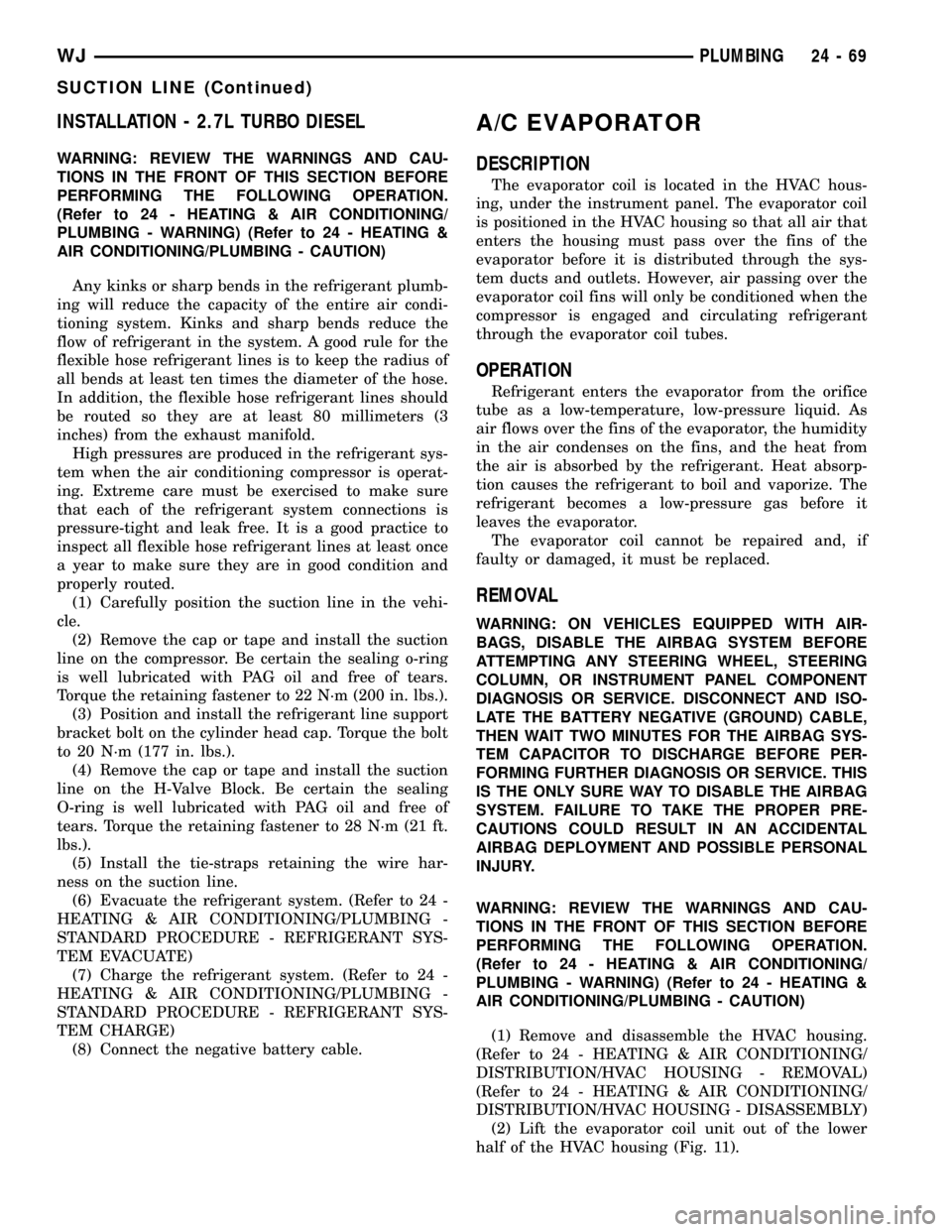
INSTALLATION - 2.7L TURBO DIESEL
WARNING: REVIEW THE WARNINGS AND CAU-
TIONS IN THE FRONT OF THIS SECTION BEFORE
PERFORMING THE FOLLOWING OPERATION.
(Refer to 24 - HEATING & AIR CONDITIONING/
PLUMBING - WARNING) (Refer to 24 - HEATING &
AIR CONDITIONING/PLUMBING - CAUTION)
Any kinks or sharp bends in the refrigerant plumb-
ing will reduce the capacity of the entire air condi-
tioning system. Kinks and sharp bends reduce the
flow of refrigerant in the system. A good rule for the
flexible hose refrigerant lines is to keep the radius of
all bends at least ten times the diameter of the hose.
In addition, the flexible hose refrigerant lines should
be routed so they are at least 80 millimeters (3
inches) from the exhaust manifold.
High pressures are produced in the refrigerant sys-
tem when the air conditioning compressor is operat-
ing. Extreme care must be exercised to make sure
that each of the refrigerant system connections is
pressure-tight and leak free. It is a good practice to
inspect all flexible hose refrigerant lines at least once
a year to make sure they are in good condition and
properly routed.
(1) Carefully position the suction line in the vehi-
cle.
(2) Remove the cap or tape and install the suction
line on the compressor. Be certain the sealing o-ring
is well lubricated with PAG oil and free of tears.
Torque the retaining fastener to 22 N´m (200 in. lbs.).
(3) Position and install the refrigerant line support
bracket bolt on the cylinder head cap. Torque the bolt
to 20 N´m (177 in. lbs.).
(4) Remove the cap or tape and install the suction
line on the H-Valve Block. Be certain the sealing
O-ring is well lubricated with PAG oil and free of
tears. Torque the retaining fastener to 28 N´m (21 ft.
lbs.).
(5) Install the tie-straps retaining the wire har-
ness on the suction line.
(6) Evacuate the refrigerant system. (Refer to 24 -
HEATING & AIR CONDITIONING/PLUMBING -
STANDARD PROCEDURE - REFRIGERANT SYS-
TEM EVACUATE)
(7) Charge the refrigerant system. (Refer to 24 -
HEATING & AIR CONDITIONING/PLUMBING -
STANDARD PROCEDURE - REFRIGERANT SYS-
TEM CHARGE)
(8) Connect the negative battery cable.
A/C EVAPORATOR
DESCRIPTION
The evaporator coil is located in the HVAC hous-
ing, under the instrument panel. The evaporator coil
is positioned in the HVAC housing so that all air that
enters the housing must pass over the fins of the
evaporator before it is distributed through the sys-
tem ducts and outlets. However, air passing over the
evaporator coil fins will only be conditioned when the
compressor is engaged and circulating refrigerant
through the evaporator coil tubes.
OPERATION
Refrigerant enters the evaporator from the orifice
tube as a low-temperature, low-pressure liquid. As
air flows over the fins of the evaporator, the humidity
in the air condenses on the fins, and the heat from
the air is absorbed by the refrigerant. Heat absorp-
tion causes the refrigerant to boil and vaporize. The
refrigerant becomes a low-pressure gas before it
leaves the evaporator.
The evaporator coil cannot be repaired and, if
faulty or damaged, it must be replaced.
REMOVAL
WARNING: ON VEHICLES EQUIPPED WITH AIR-
BAGS, DISABLE THE AIRBAG SYSTEM BEFORE
ATTEMPTING ANY STEERING WHEEL, STEERING
COLUMN, OR INSTRUMENT PANEL COMPONENT
DIAGNOSIS OR SERVICE. DISCONNECT AND ISO-
LATE THE BATTERY NEGATIVE (GROUND) CABLE,
THEN WAIT TWO MINUTES FOR THE AIRBAG SYS-
TEM CAPACITOR TO DISCHARGE BEFORE PER-
FORMING FURTHER DIAGNOSIS OR SERVICE. THIS
IS THE ONLY SURE WAY TO DISABLE THE AIRBAG
SYSTEM. FAILURE TO TAKE THE PROPER PRE-
CAUTIONS COULD RESULT IN AN ACCIDENTAL
AIRBAG DEPLOYMENT AND POSSIBLE PERSONAL
INJURY.
WARNING: REVIEW THE WARNINGS AND CAU-
TIONS IN THE FRONT OF THIS SECTION BEFORE
PERFORMING THE FOLLOWING OPERATION.
(Refer to 24 - HEATING & AIR CONDITIONING/
PLUMBING - WARNING) (Refer to 24 - HEATING &
AIR CONDITIONING/PLUMBING - CAUTION)
(1) Remove and disassemble the HVAC housing.
(Refer to 24 - HEATING & AIR CONDITIONING/
DISTRIBUTION/HVAC HOUSING - REMOVAL)
(Refer to 24 - HEATING & AIR CONDITIONING/
DISTRIBUTION/HVAC HOUSING - DISASSEMBLY)
(2) Lift the evaporator coil unit out of the lower
half of the HVAC housing (Fig. 11).
WJPLUMBING 24 - 69
SUCTION LINE (Continued)
Page 2148 of 2199
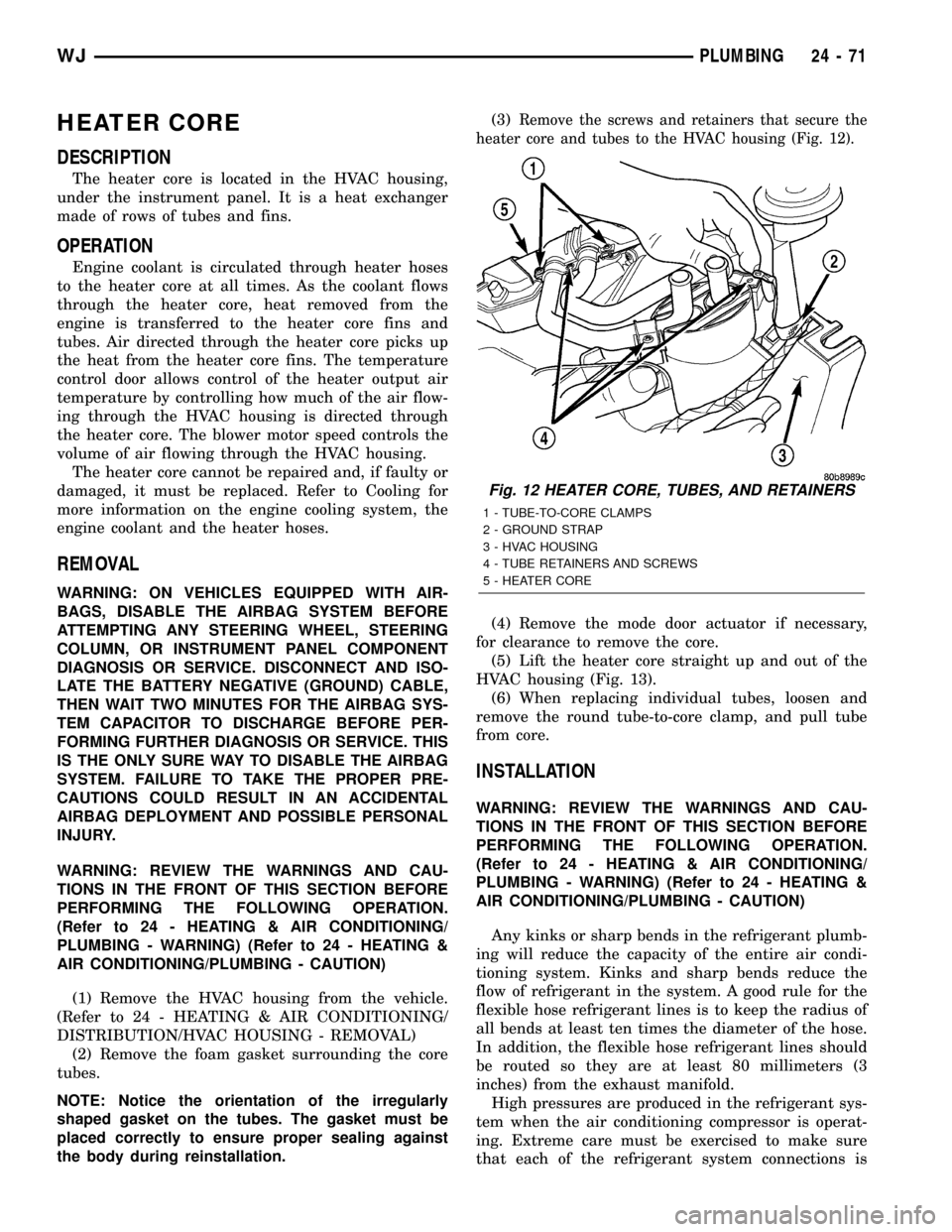
HEATER CORE
DESCRIPTION
The heater core is located in the HVAC housing,
under the instrument panel. It is a heat exchanger
made of rows of tubes and fins.
OPERATION
Engine coolant is circulated through heater hoses
to the heater core at all times. As the coolant flows
through the heater core, heat removed from the
engine is transferred to the heater core fins and
tubes. Air directed through the heater core picks up
the heat from the heater core fins. The temperature
control door allows control of the heater output air
temperature by controlling how much of the air flow-
ing through the HVAC housing is directed through
the heater core. The blower motor speed controls the
volume of air flowing through the HVAC housing.
The heater core cannot be repaired and, if faulty or
damaged, it must be replaced. Refer to Cooling for
more information on the engine cooling system, the
engine coolant and the heater hoses.
REMOVAL
WARNING: ON VEHICLES EQUIPPED WITH AIR-
BAGS, DISABLE THE AIRBAG SYSTEM BEFORE
ATTEMPTING ANY STEERING WHEEL, STEERING
COLUMN, OR INSTRUMENT PANEL COMPONENT
DIAGNOSIS OR SERVICE. DISCONNECT AND ISO-
LATE THE BATTERY NEGATIVE (GROUND) CABLE,
THEN WAIT TWO MINUTES FOR THE AIRBAG SYS-
TEM CAPACITOR TO DISCHARGE BEFORE PER-
FORMING FURTHER DIAGNOSIS OR SERVICE. THIS
IS THE ONLY SURE WAY TO DISABLE THE AIRBAG
SYSTEM. FAILURE TO TAKE THE PROPER PRE-
CAUTIONS COULD RESULT IN AN ACCIDENTAL
AIRBAG DEPLOYMENT AND POSSIBLE PERSONAL
INJURY.
WARNING: REVIEW THE WARNINGS AND CAU-
TIONS IN THE FRONT OF THIS SECTION BEFORE
PERFORMING THE FOLLOWING OPERATION.
(Refer to 24 - HEATING & AIR CONDITIONING/
PLUMBING - WARNING) (Refer to 24 - HEATING &
AIR CONDITIONING/PLUMBING - CAUTION)
(1) Remove the HVAC housing from the vehicle.
(Refer to 24 - HEATING & AIR CONDITIONING/
DISTRIBUTION/HVAC HOUSING - REMOVAL)
(2) Remove the foam gasket surrounding the core
tubes.
NOTE: Notice the orientation of the irregularly
shaped gasket on the tubes. The gasket must be
placed correctly to ensure proper sealing against
the body during reinstallation.(3)
Remove the screws and retainers that secure the
heater core and tubes to the HVAC housing (Fig. 12).
(4) Remove the mode door actuator if necessary,
for clearance to remove the core.
(5) Lift the heater core straight up and out of the
HVAC housing (Fig. 13).
(6) When replacing individual tubes, loosen and
remove the round tube-to-core clamp, and pull tube
from core.
INSTALLATION
WARNING: REVIEW THE WARNINGS AND CAU-
TIONS IN THE FRONT OF THIS SECTION BEFORE
PERFORMING THE FOLLOWING OPERATION.
(Refer to 24 - HEATING & AIR CONDITIONING/
PLUMBING - WARNING) (Refer to 24 - HEATING &
AIR CONDITIONING/PLUMBING - CAUTION)
Any kinks or sharp bends in the refrigerant plumb-
ing will reduce the capacity of the entire air condi-
tioning system. Kinks and sharp bends reduce the
flow of refrigerant in the system. A good rule for the
flexible hose refrigerant lines is to keep the radius of
all bends at least ten times the diameter of the hose.
In addition, the flexible hose refrigerant lines should
be routed so they are at least 80 millimeters (3
inches) from the exhaust manifold.
High pressures are produced in the refrigerant sys-
tem when the air conditioning compressor is operat-
ing. Extreme care must be exercised to make sure
that each of the refrigerant system connections is
Fig. 12 HEATER CORE, TUBES, AND RETAINERS
1 - TUBE-TO-CORE CLAMPS
2 - GROUND STRAP
3 - HVAC HOUSING
4 - TUBE RETAINERS AND SCREWS
5 - HEATER CORE
WJPLUMBING 24 - 71
Page 2149 of 2199
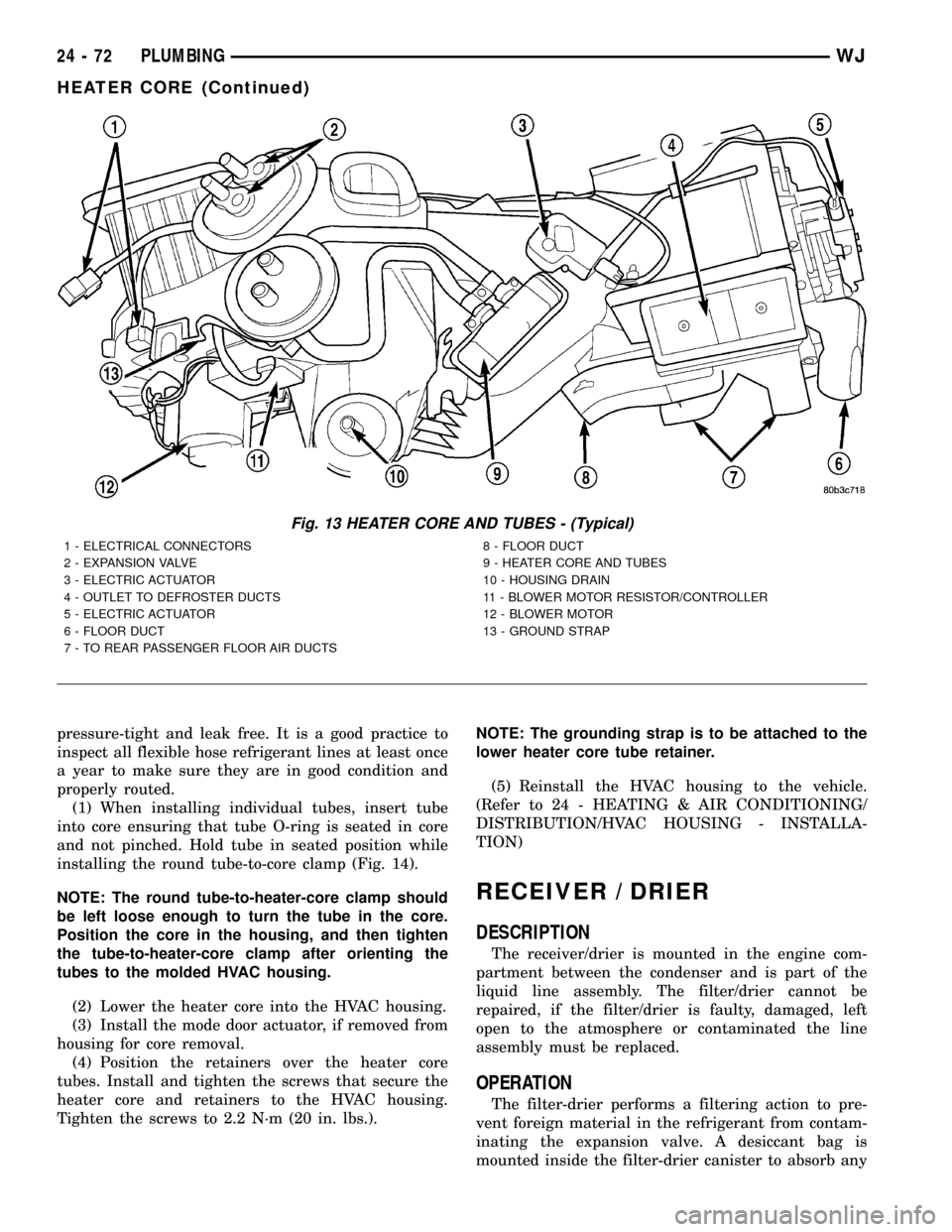
pressure-tight and leak free. It is a good practice to
inspect all flexible hose refrigerant lines at least once
a year to make sure they are in good condition and
properly routed.
(1) When installing individual tubes, insert tube
into core ensuring that tube O-ring is seated in core
and not pinched. Hold tube in seated position while
installing the round tube-to-core clamp (Fig. 14).
NOTE: The round tube-to-heater-core clamp should
be left loose enough to turn the tube in the core.
Position the core in the housing, and then tighten
the tube-to-heater-core clamp after orienting the
tubes to the molded HVAC housing.
(2) Lower the heater core into the HVAC housing.
(3) Install the mode door actuator, if removed from
housing for core removal.
(4) Position the retainers over the heater core
tubes. Install and tighten the screws that secure the
heater core and retainers to the HVAC housing.
Tighten the screws to 2.2 N´m (20 in. lbs.).NOTE: The grounding strap is to be attached to the
lower heater core tube retainer.
(5) Reinstall the HVAC housing to the vehicle.
(Refer to 24 - HEATING & AIR CONDITIONING/
DISTRIBUTION/HVAC HOUSING - INSTALLA-
TION)
RECEIVER / DRIER
DESCRIPTION
The receiver/drier is mounted in the engine com-
partment between the condenser and is part of the
liquid line assembly. The filter/drier cannot be
repaired, if the filter/drier is faulty, damaged, left
open to the atmosphere or contaminated the line
assembly must be replaced.
OPERATION
The filter-drier performs a filtering action to pre-
vent foreign material in the refrigerant from contam-
inating the expansion valve. A desiccant bag is
mounted inside the filter-drier canister to absorb any
Fig. 13 HEATER CORE AND TUBES - (Typical)
1 - ELECTRICAL CONNECTORS
2 - EXPANSION VALVE
3 - ELECTRIC ACTUATOR
4 - OUTLET TO DEFROSTER DUCTS
5 - ELECTRIC ACTUATOR
6 - FLOOR DUCT
7 - TO REAR PASSENGER FLOOR AIR DUCTS8 - FLOOR DUCT
9 - HEATER CORE AND TUBES
10 - HOUSING DRAIN
11 - BLOWER MOTOR RESISTOR/CONTROLLER
12 - BLOWER MOTOR
13 - GROUND STRAP
24 - 72 PLUMBINGWJ
HEATER CORE (Continued)