Instrument panel light bulb JEEP GRAND CHEROKEE 2002 WJ / 2.G Owner's Manual
[x] Cancel search | Manufacturer: JEEP, Model Year: 2002, Model line: GRAND CHEROKEE, Model: JEEP GRAND CHEROKEE 2002 WJ / 2.GPages: 2199, PDF Size: 76.01 MB
Page 458 of 2199
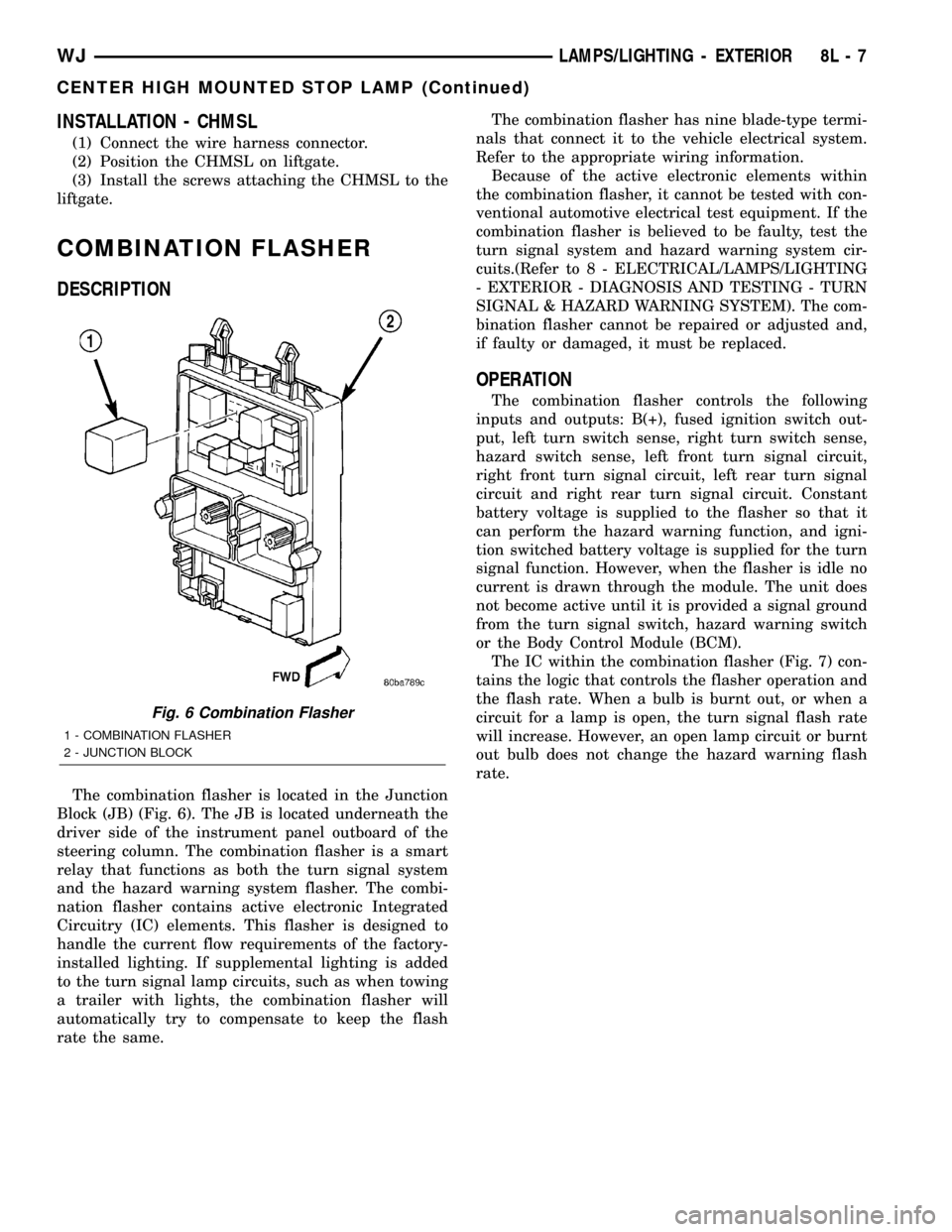
INSTALLATION - CHMSL
(1) Connect the wire harness connector.
(2) Position the CHMSL on liftgate.
(3) Install the screws attaching the CHMSL to the
liftgate.
COMBINATION FLASHER
DESCRIPTION
The combination flasher is located in the Junction
Block (JB) (Fig. 6). The JB is located underneath the
driver side of the instrument panel outboard of the
steering column. The combination flasher is a smart
relay that functions as both the turn signal system
and the hazard warning system flasher. The combi-
nation flasher contains active electronic Integrated
Circuitry (IC) elements. This flasher is designed to
handle the current flow requirements of the factory-
installed lighting. If supplemental lighting is added
to the turn signal lamp circuits, such as when towing
a trailer with lights, the combination flasher will
automatically try to compensate to keep the flash
rate the same.The combination flasher has nine blade-type termi-
nals that connect it to the vehicle electrical system.
Refer to the appropriate wiring information.
Because of the active electronic elements within
the combination flasher, it cannot be tested with con-
ventional automotive electrical test equipment. If the
combination flasher is believed to be faulty, test the
turn signal system and hazard warning system cir-
cuits.(Refer to 8 - ELECTRICAL/LAMPS/LIGHTING
- EXTERIOR - DIAGNOSIS AND TESTING - TURN
SIGNAL & HAZARD WARNING SYSTEM). The com-
bination flasher cannot be repaired or adjusted and,
if faulty or damaged, it must be replaced.
OPERATION
The combination flasher controls the following
inputs and outputs: B(+), fused ignition switch out-
put, left turn switch sense, right turn switch sense,
hazard switch sense, left front turn signal circuit,
right front turn signal circuit, left rear turn signal
circuit and right rear turn signal circuit. Constant
battery voltage is supplied to the flasher so that it
can perform the hazard warning function, and igni-
tion switched battery voltage is supplied for the turn
signal function. However, when the flasher is idle no
current is drawn through the module. The unit does
not become active until it is provided a signal ground
from the turn signal switch, hazard warning switch
or the Body Control Module (BCM).
The IC within the combination flasher (Fig. 7) con-
tains the logic that controls the flasher operation and
the flash rate. When a bulb is burnt out, or when a
circuit for a lamp is open, the turn signal flash rate
will increase. However, an open lamp circuit or burnt
out bulb does not change the hazard warning flash
rate.
Fig. 6 Combination Flasher
1 - COMBINATION FLASHER
2 - JUNCTION BLOCK
WJLAMPS/LIGHTING - EXTERIOR 8L - 7
CENTER HIGH MOUNTED STOP LAMP (Continued)
Page 466 of 2199

INSTALLATION - BULB
CAUTION: Do not touch the bulb glass with fingers
or other oily surfaces. Reduced bulb life will result.
(1) Position the bulb into socket and push into
place.
(2) Position the bulb socket in headlamp and turn
the bulb socket one quarter turn clockwise.
(3) Install the headlamp.
HEADLAMP SWITCH
DESCRIPTION
The headlamp switch is part of the left multi-func-
tion switch. A knob on the end of the multi-function
switch control stalk controls all of the exterior light-
ing switch functions. The exterior lighting switch is
hard wired to the Body Control Module (BCM).
The exterior lighting switch cannot be adjusted or
repaired and, if faulty or damaged, the entire left
multi-function switch unit must be replaced. (Refer
to 8 - ELECTRICAL/LAMPS/LIGHTING - EXTERI-
OR/TURN SIGNAL/HAZARD SWITCH - REMOVAL)
for the service procedures. (Refer to 8 - ELECTRI-
CAL/ELECTRONIC CONTROL MODULES/BODY
CONTROL/CENTRAL TIMER MODUL - DESCRIP-
TION) for more information on this component.
OPERATION
The exterior lighting switch uses a hard wired five
volt reference circuit from the BCM, resistor multi-
plexing and a hard wired switch output circuit to
provide the BCM with a zero to five volt signal thatindicates the status of all of the exterior lighting
switch settings. The BCM then uses control outputs
to energize the headlamp and park lamp relays that
activate the exterior lighting circuits.
The BCM monitors the exterior lighting switch sta-
tus, then sends the proper switch status messages to
other modules over the Programmable Communica-
tions Interface (PCI) data bus network. The exterior
lighting switch status is also used by the BCM as an
input for chime warning system operation.
DIAGNOSIS AND TESTING Ð HEADLAMP
SWITCH
Before testing the headlamp switch, turn on the
exterior lighting and open the driver side front door.
If the exterior lamps of the vehicle operate, but there
is no chime warning issued with the driver side front
door open, (Refer to 8 - ELECTRICAL/LAMPS/
LIGHTING - INTERIOR/DOOR AJAR SWITCH -
DIAGNOSIS AND TESTING). If the exterior lamps
of the vehicle are inoperative, but the chime warning
is issued, (Refer to 8 - ELECTRICAL/LAMPS/LIGHT-
ING - EXTERIOR - DIAGNOSIS AND TESTING).
If the exterior lamps and the chime warning are
both inoperative, test the left multi-function switch.
(Refer to 8 - ELECTRICAL/LAMPS/LIGHTING -
EXTERIOR - DIAGNOSIS AND TESTING). If the
multi-function switch tests OK, proceed as follows.
The following tests will help to locate a short or open
in the hard wired circuits between the multi-function
switch and the Body Control Module (BCM). For
complete circuit diagrams, refer to the appropriate
wiring information.
WARNING: ON VEHICLES EQUIPPED WITH AIR-
BAGS, REFER TO ELECTRICAL, RESTRAINTS
BEFORE ATTEMPTING ANY STEERING WHEEL,
STEERING COLUMN, OR INSTRUMENT PANEL
COMPONENT DIAGNOSIS OR SERVICE. FAILURE
TO TAKE THE PROPER PRECAUTIONS COULD
RESULT IN ACCIDENTAL AIRBAG DEPLOYMENT
AND POSSIBLE PERSONAL INJURY.
(1) Disconnect and isolate the battery negative
cable. Disconnect the instrument panel wire harness
connector from the left multi-function switch connec-
tor. Disconnect the instrument panel wire harness
connector from the Body Control Module (BCM).
Check for continuity between the headlamp switch
mux circuit of the instrument panel wire harness
connector for the multi-function switch and a good
ground. There should be no continuity. If OK, go to
Step 2. If not OK, repair the shorted headlamp
switch mux circuit.
(2) Check for continuity between the headlamp
switch mux circuit of the instrument panel wire har-
Fig. 13 Headlamp Bulb
1 - HIGH BEAM BULB
2 - LOW BEAM BULB
3 - MARKER BULB
4 - PARK/TURN SIGNAL BULB
WJLAMPS/LIGHTING - EXTERIOR 8L - 15
HEADLAMP (Continued)
Page 467 of 2199
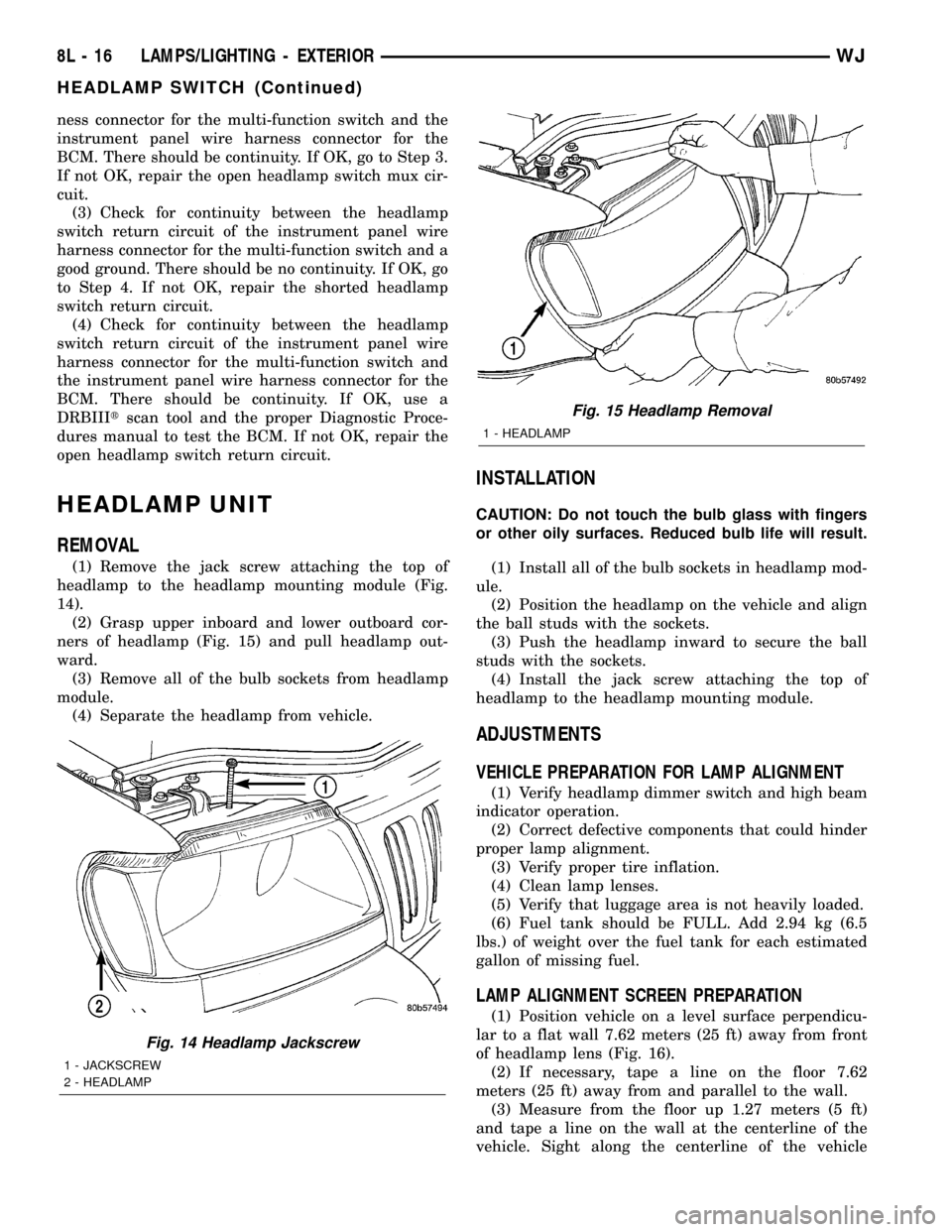
ness connector for the multi-function switch and the
instrument panel wire harness connector for the
BCM. There should be continuity. If OK, go to Step 3.
If not OK, repair the open headlamp switch mux cir-
cuit.
(3) Check for continuity between the headlamp
switch return circuit of the instrument panel wire
harness connector for the multi-function switch and a
good ground. There should be no continuity. If OK, go
to Step 4. If not OK, repair the shorted headlamp
switch return circuit.
(4) Check for continuity between the headlamp
switch return circuit of the instrument panel wire
harness connector for the multi-function switch and
the instrument panel wire harness connector for the
BCM. There should be continuity. If OK, use a
DRBIIItscan tool and the proper Diagnostic Proce-
dures manual to test the BCM. If not OK, repair the
open headlamp switch return circuit.
HEADLAMP UNIT
REMOVAL
(1) Remove the jack screw attaching the top of
headlamp to the headlamp mounting module (Fig.
14).
(2) Grasp upper inboard and lower outboard cor-
ners of headlamp (Fig. 15) and pull headlamp out-
ward.
(3) Remove all of the bulb sockets from headlamp
module.
(4) Separate the headlamp from vehicle.
INSTALLATION
CAUTION: Do not touch the bulb glass with fingers
or other oily surfaces. Reduced bulb life will result.
(1) Install all of the bulb sockets in headlamp mod-
ule.
(2) Position the headlamp on the vehicle and align
the ball studs with the sockets.
(3) Push the headlamp inward to secure the ball
studs with the sockets.
(4) Install the jack screw attaching the top of
headlamp to the headlamp mounting module.
ADJUSTMENTS
VEHICLE PREPARATION FOR LAMP ALIGNMENT
(1) Verify headlamp dimmer switch and high beam
indicator operation.
(2) Correct defective components that could hinder
proper lamp alignment.
(3) Verify proper tire inflation.
(4) Clean lamp lenses.
(5) Verify that luggage area is not heavily loaded.
(6) Fuel tank should be FULL. Add 2.94 kg (6.5
lbs.) of weight over the fuel tank for each estimated
gallon of missing fuel.
LAMP ALIGNMENT SCREEN PREPARATION
(1) Position vehicle on a level surface perpendicu-
lar to a flat wall 7.62 meters (25 ft) away from front
of headlamp lens (Fig. 16).
(2) If necessary, tape a line on the floor 7.62
meters (25 ft) away from and parallel to the wall.
(3) Measure from the floor up 1.27 meters (5 ft)
and tape a line on the wall at the centerline of the
vehicle. Sight along the centerline of the vehicle
Fig. 14 Headlamp Jackscrew
1 - JACKSCREW
2 - HEADLAMP
Fig. 15 Headlamp Removal
1 - HEADLAMP
8L - 16 LAMPS/LIGHTING - EXTERIORWJ
HEADLAMP SWITCH (Continued)
Page 479 of 2199
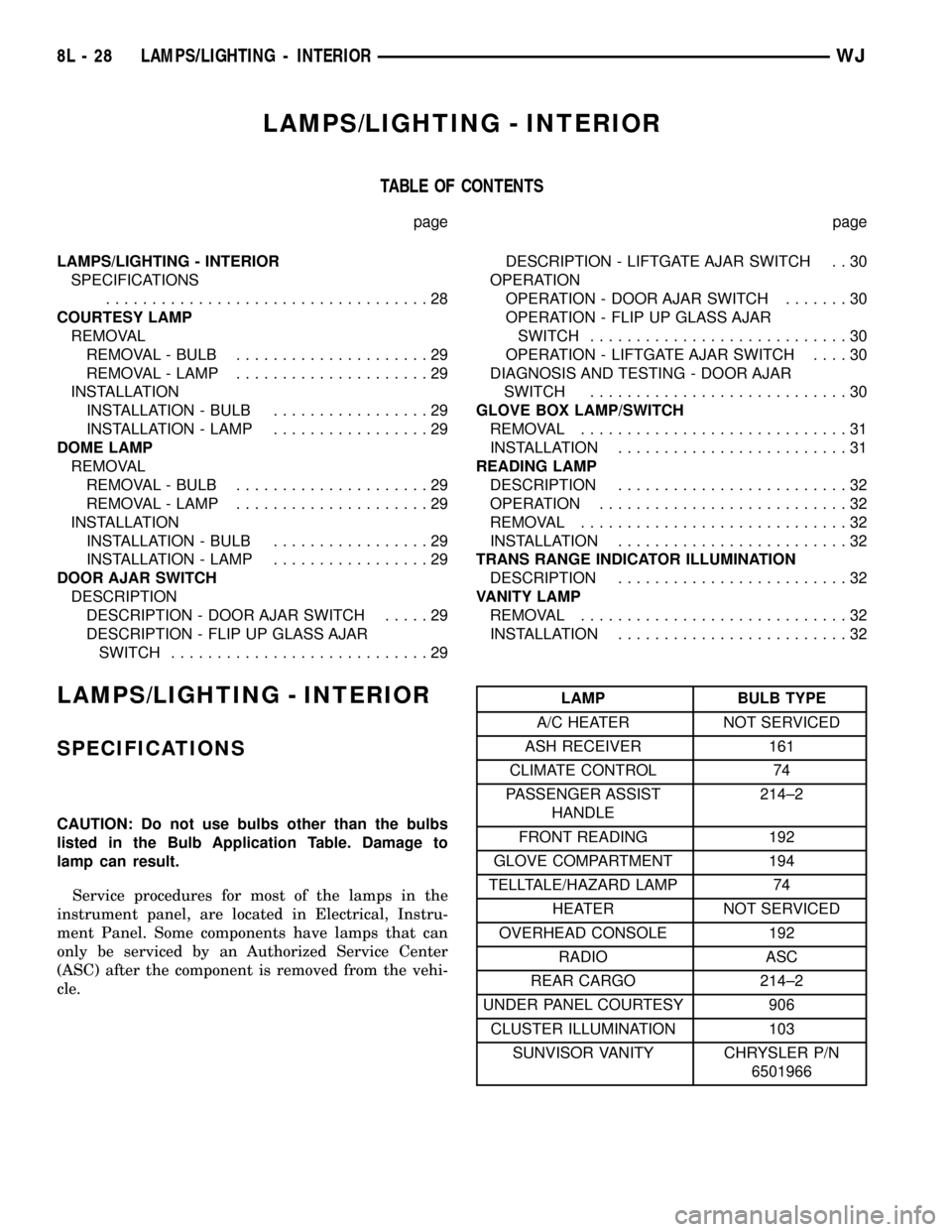
LAMPS/LIGHTING - INTERIOR
TABLE OF CONTENTS
page page
LAMPS/LIGHTING - INTERIOR
SPECIFICATIONS
...................................28
COURTESY LAMP
REMOVAL
REMOVAL - BULB.....................29
REMOVAL - LAMP.....................29
INSTALLATION
INSTALLATION - BULB.................29
INSTALLATION - LAMP.................29
DOME LAMP
REMOVAL
REMOVAL - BULB.....................29
REMOVAL - LAMP.....................29
INSTALLATION
INSTALLATION - BULB.................29
INSTALLATION - LAMP.................29
DOOR AJAR SWITCH
DESCRIPTION
DESCRIPTION - DOOR AJAR SWITCH.....29
DESCRIPTION - FLIP UP GLASS AJAR
SWITCH............................29DESCRIPTION - LIFTGATE AJAR SWITCH . . 30
OPERATION
OPERATION - DOOR AJAR SWITCH.......30
OPERATION - FLIP UP GLASS AJAR
SWITCH............................30
OPERATION - LIFTGATE AJAR SWITCH....30
DIAGNOSIS AND TESTING - DOOR AJAR
SWITCH............................30
GLOVE BOX LAMP/SWITCH
REMOVAL.............................31
INSTALLATION.........................31
READING LAMP
DESCRIPTION.........................32
OPERATION...........................32
REMOVAL.............................32
INSTALLATION.........................32
TRANS RANGE INDICATOR ILLUMINATION
DESCRIPTION.........................32
VANITY LAMP
REMOVAL.............................32
INSTALLATION.........................32
LAMPS/LIGHTING - INTERIOR
SPECIFICATIONS
CAUTION: Do not use bulbs other than the bulbs
listed in the Bulb Application Table. Damage to
lamp can result.
Service procedures for most of the lamps in the
instrument panel, are located in Electrical, Instru-
ment Panel. Some components have lamps that can
only be serviced by an Authorized Service Center
(ASC) after the component is removed from the vehi-
cle.
LAMP BULB TYPE
A/C HEATER NOT SERVICED
ASH RECEIVER 161
CLIMATE CONTROL 74
PASSENGER ASSIST
HANDLE214±2
FRONT READING 192
GLOVE COMPARTMENT 194
TELLTALE/HAZARD LAMP 74
HEATER NOT SERVICED
OVERHEAD CONSOLE 192
RADIO ASC
REAR CARGO 214±2
UNDER PANEL COURTESY 906
CLUSTER ILLUMINATION 103
SUNVISOR VANITY CHRYSLER P/N
6501966
8L - 28 LAMPS/LIGHTING - INTERIORWJ
Page 596 of 2199
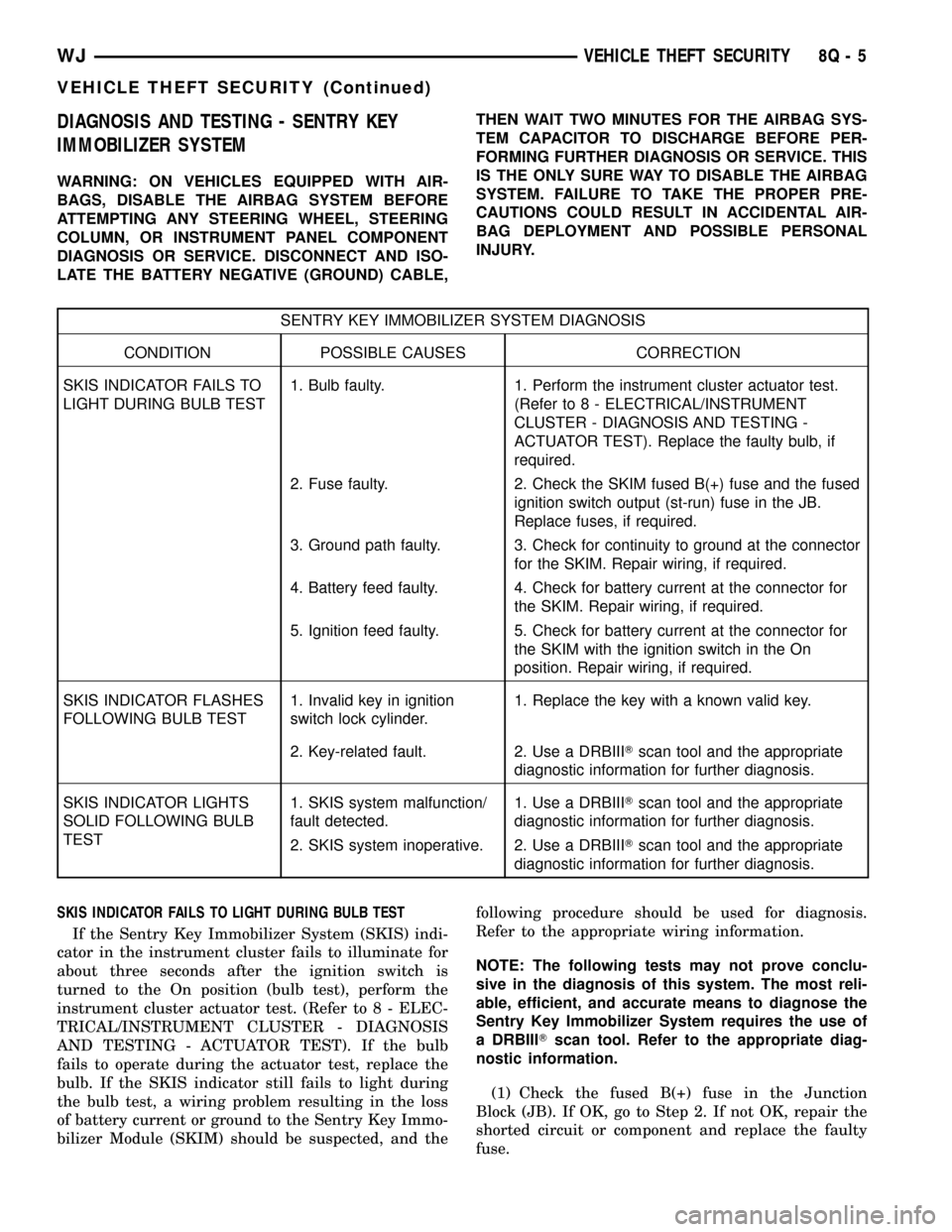
DIAGNOSIS AND TESTING - SENTRY KEY
IMMOBILIZER SYSTEM
WARNING: ON VEHICLES EQUIPPED WITH AIR-
BAGS, DISABLE THE AIRBAG SYSTEM BEFORE
ATTEMPTING ANY STEERING WHEEL, STEERING
COLUMN, OR INSTRUMENT PANEL COMPONENT
DIAGNOSIS OR SERVICE. DISCONNECT AND ISO-
LATE THE BATTERY NEGATIVE (GROUND) CABLE,THEN WAIT TWO MINUTES FOR THE AIRBAG SYS-
TEM CAPACITOR TO DISCHARGE BEFORE PER-
FORMING FURTHER DIAGNOSIS OR SERVICE. THIS
IS THE ONLY SURE WAY TO DISABLE THE AIRBAG
SYSTEM. FAILURE TO TAKE THE PROPER PRE-
CAUTIONS COULD RESULT IN ACCIDENTAL AIR-
BAG DEPLOYMENT AND POSSIBLE PERSONAL
INJURY.
SENTRY KEY IMMOBILIZER SYSTEM DIAGNOSIS
CONDITION POSSIBLE CAUSES CORRECTION
SKIS INDICATOR FAILS TO
LIGHT DURING BULB TEST1. Bulb faulty. 1. Perform the instrument cluster actuator test.
(Refer to 8 - ELECTRICAL/INSTRUMENT
CLUSTER - DIAGNOSIS AND TESTING -
ACTUATOR TEST). Replace the faulty bulb, if
required.
2. Fuse faulty. 2. Check the SKIM fused B(+) fuse and the fused
ignition switch output (st-run) fuse in the JB.
Replace fuses, if required.
3. Ground path faulty. 3. Check for continuity to ground at the connector
for the SKIM. Repair wiring, if required.
4. Battery feed faulty. 4. Check for battery current at the connector for
the SKIM. Repair wiring, if required.
5. Ignition feed faulty. 5. Check for battery current at the connector for
the SKIM with the ignition switch in the On
position. Repair wiring, if required.
SKIS INDICATOR FLASHES
FOLLOWING BULB TEST1. Invalid key in ignition
switch lock cylinder.1. Replace the key with a known valid key.
2. Key-related fault. 2. Use a DRBIIITscan tool and the appropriate
diagnostic information for further diagnosis.
SKIS INDICATOR LIGHTS
SOLID FOLLOWING BULB
TEST1. SKIS system malfunction/
fault detected.1. Use a DRBIIITscan tool and the appropriate
diagnostic information for further diagnosis.
2. SKIS system inoperative. 2. Use a DRBIIITscan tool and the appropriate
diagnostic information for further diagnosis.
SKIS INDICATOR FAILS TO LIGHT DURING BULB TEST
If the Sentry Key Immobilizer System (SKIS) indi-
cator in the instrument cluster fails to illuminate for
about three seconds after the ignition switch is
turned to the On position (bulb test), perform the
instrument cluster actuator test. (Refer to 8 - ELEC-
TRICAL/INSTRUMENT CLUSTER - DIAGNOSIS
AND TESTING - ACTUATOR TEST). If the bulb
fails to operate during the actuator test, replace the
bulb. If the SKIS indicator still fails to light during
the bulb test, a wiring problem resulting in the loss
of battery current or ground to the Sentry Key Immo-
bilizer Module (SKIM) should be suspected, and thefollowing procedure should be used for diagnosis.
Refer to the appropriate wiring information.
NOTE: The following tests may not prove conclu-
sive in the diagnosis of this system. The most reli-
able, efficient, and accurate means to diagnose the
Sentry Key Immobilizer System requires the use of
a DRBIIITscan tool. Refer to the appropriate diag-
nostic information.
(1) Check the fused B(+) fuse in the Junction
Block (JB). If OK, go to Step 2. If not OK, repair the
shorted circuit or component and replace the faulty
fuse.
WJVEHICLE THEFT SECURITY 8Q - 5
VEHICLE THEFT SECURITY (Continued)
Page 597 of 2199
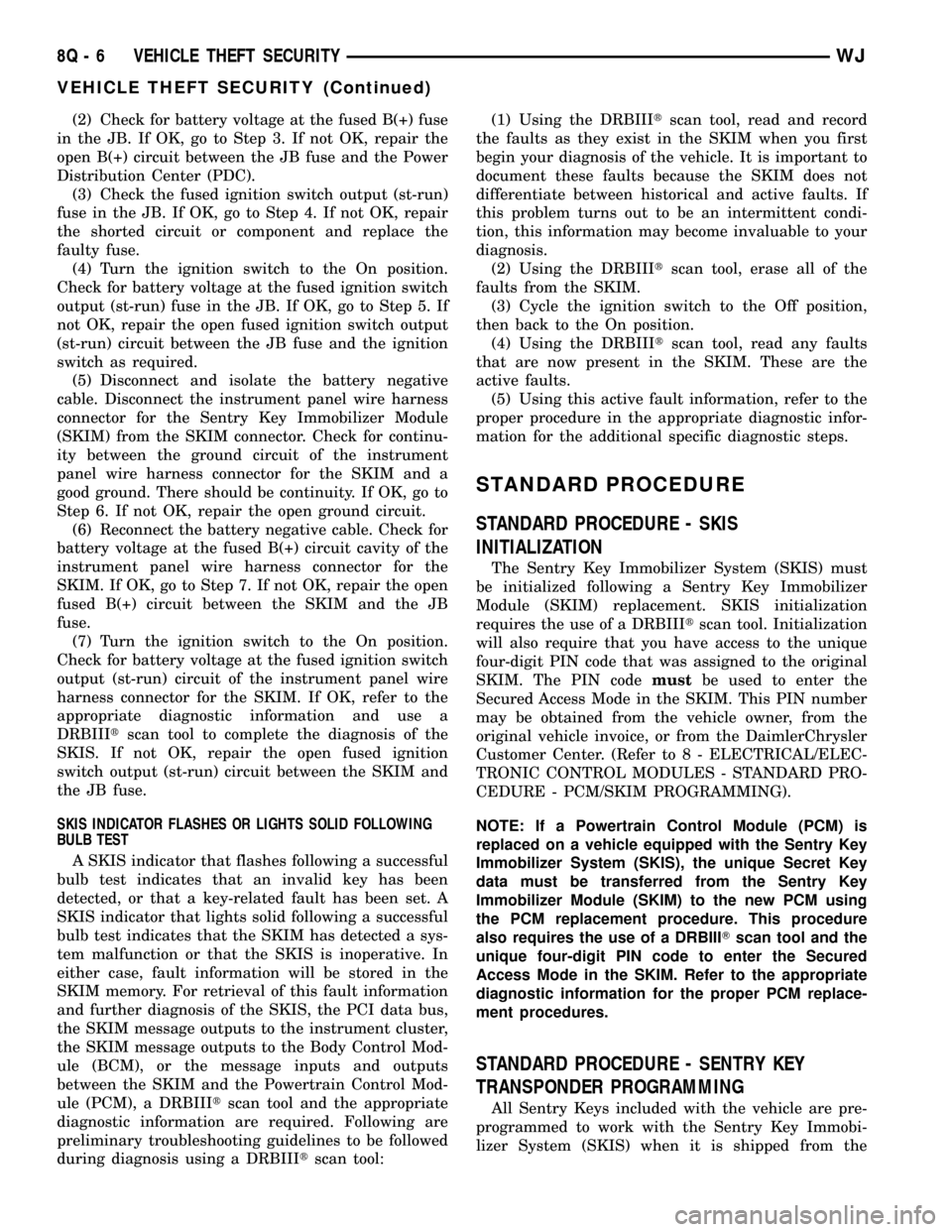
(2) Check for battery voltage at the fused B(+) fuse
in the JB. If OK, go to Step 3. If not OK, repair the
open B(+) circuit between the JB fuse and the Power
Distribution Center (PDC).
(3) Check the fused ignition switch output (st-run)
fuse in the JB. If OK, go to Step 4. If not OK, repair
the shorted circuit or component and replace the
faulty fuse.
(4) Turn the ignition switch to the On position.
Check for battery voltage at the fused ignition switch
output (st-run) fuse in the JB. If OK, go to Step 5. If
not OK, repair the open fused ignition switch output
(st-run) circuit between the JB fuse and the ignition
switch as required.
(5) Disconnect and isolate the battery negative
cable. Disconnect the instrument panel wire harness
connector for the Sentry Key Immobilizer Module
(SKIM) from the SKIM connector. Check for continu-
ity between the ground circuit of the instrument
panel wire harness connector for the SKIM and a
good ground. There should be continuity. If OK, go to
Step 6. If not OK, repair the open ground circuit.
(6) Reconnect the battery negative cable. Check for
battery voltage at the fused B(+) circuit cavity of the
instrument panel wire harness connector for the
SKIM. If OK, go to Step 7. If not OK, repair the open
fused B(+) circuit between the SKIM and the JB
fuse.
(7) Turn the ignition switch to the On position.
Check for battery voltage at the fused ignition switch
output (st-run) circuit of the instrument panel wire
harness connector for the SKIM. If OK, refer to the
appropriate diagnostic information and use a
DRBIIItscan tool to complete the diagnosis of the
SKIS. If not OK, repair the open fused ignition
switch output (st-run) circuit between the SKIM and
the JB fuse.
SKIS INDICATOR FLASHES OR LIGHTS SOLID FOLLOWING
BULB TEST
A SKIS indicator that flashes following a successful
bulb test indicates that an invalid key has been
detected, or that a key-related fault has been set. A
SKIS indicator that lights solid following a successful
bulb test indicates that the SKIM has detected a sys-
tem malfunction or that the SKIS is inoperative. In
either case, fault information will be stored in the
SKIM memory. For retrieval of this fault information
and further diagnosis of the SKIS, the PCI data bus,
the SKIM message outputs to the instrument cluster,
the SKIM message outputs to the Body Control Mod-
ule (BCM), or the message inputs and outputs
between the SKIM and the Powertrain Control Mod-
ule (PCM), a DRBIIItscan tool and the appropriate
diagnostic information are required. Following are
preliminary troubleshooting guidelines to be followed
during diagnosis using a DRBIIItscan tool:(1) Using the DRBIIItscan tool, read and record
the faults as they exist in the SKIM when you first
begin your diagnosis of the vehicle. It is important to
document these faults because the SKIM does not
differentiate between historical and active faults. If
this problem turns out to be an intermittent condi-
tion, this information may become invaluable to your
diagnosis.
(2) Using the DRBIIItscan tool, erase all of the
faults from the SKIM.
(3) Cycle the ignition switch to the Off position,
then back to the On position.
(4) Using the DRBIIItscan tool, read any faults
that are now present in the SKIM. These are the
active faults.
(5) Using this active fault information, refer to the
proper procedure in the appropriate diagnostic infor-
mation for the additional specific diagnostic steps.
STANDARD PROCEDURE
STANDARD PROCEDURE - SKIS
INITIALIZATION
The Sentry Key Immobilizer System (SKIS) must
be initialized following a Sentry Key Immobilizer
Module (SKIM) replacement. SKIS initialization
requires the use of a DRBIIItscan tool. Initialization
will also require that you have access to the unique
four-digit PIN code that was assigned to the original
SKIM. The PIN codemustbe used to enter the
Secured Access Mode in the SKIM. This PIN number
may be obtained from the vehicle owner, from the
original vehicle invoice, or from the DaimlerChrysler
Customer Center. (Refer to 8 - ELECTRICAL/ELEC-
TRONIC CONTROL MODULES - STANDARD PRO-
CEDURE - PCM/SKIM PROGRAMMING).
NOTE: If a Powertrain Control Module (PCM) is
replaced on a vehicle equipped with the Sentry Key
Immobilizer System (SKIS), the unique Secret Key
data must be transferred from the Sentry Key
Immobilizer Module (SKIM) to the new PCM using
the PCM replacement procedure. This procedure
also requires the use of a DRBIIITscan tool and the
unique four-digit PIN code to enter the Secured
Access Mode in the SKIM. Refer to the appropriate
diagnostic information for the proper PCM replace-
ment procedures.
STANDARD PROCEDURE - SENTRY KEY
TRANSPONDER PROGRAMMING
All Sentry Keys included with the vehicle are pre-
programmed to work with the Sentry Key Immobi-
lizer System (SKIS) when it is shipped from the
8Q - 6 VEHICLE THEFT SECURITYWJ
VEHICLE THEFT SECURITY (Continued)
Page 606 of 2199
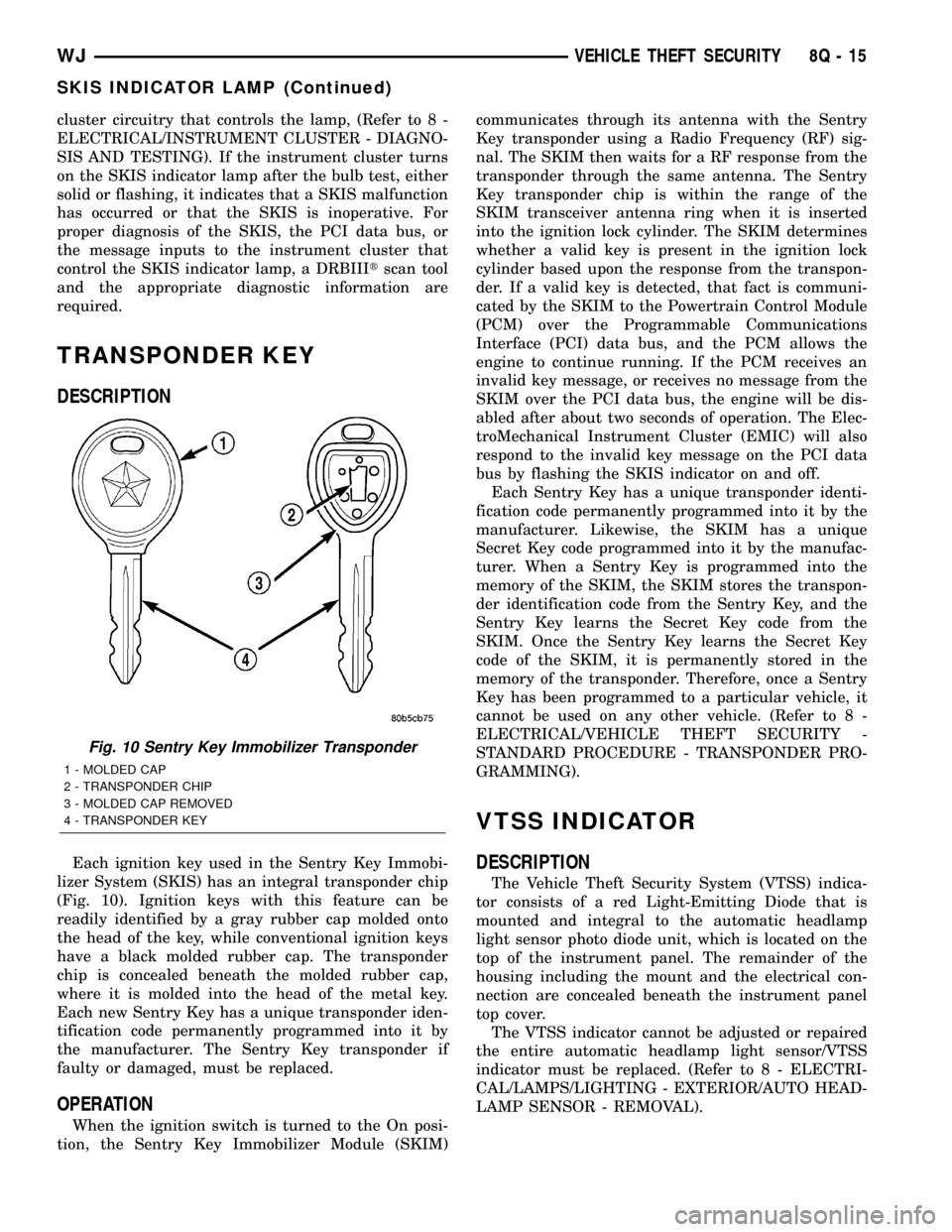
cluster circuitry that controls the lamp, (Refer to 8 -
ELECTRICAL/INSTRUMENT CLUSTER - DIAGNO-
SIS AND TESTING). If the instrument cluster turns
on the SKIS indicator lamp after the bulb test, either
solid or flashing, it indicates that a SKIS malfunction
has occurred or that the SKIS is inoperative. For
proper diagnosis of the SKIS, the PCI data bus, or
the message inputs to the instrument cluster that
control the SKIS indicator lamp, a DRBIIItscan tool
and the appropriate diagnostic information are
required.
TRANSPONDER KEY
DESCRIPTION
Each ignition key used in the Sentry Key Immobi-
lizer System (SKIS) has an integral transponder chip
(Fig. 10). Ignition keys with this feature can be
readily identified by a gray rubber cap molded onto
the head of the key, while conventional ignition keys
have a black molded rubber cap. The transponder
chip is concealed beneath the molded rubber cap,
where it is molded into the head of the metal key.
Each new Sentry Key has a unique transponder iden-
tification code permanently programmed into it by
the manufacturer. The Sentry Key transponder if
faulty or damaged, must be replaced.
OPERATION
When the ignition switch is turned to the On posi-
tion, the Sentry Key Immobilizer Module (SKIM)communicates through its antenna with the Sentry
Key transponder using a Radio Frequency (RF) sig-
nal. The SKIM then waits for a RF response from the
transponder through the same antenna. The Sentry
Key transponder chip is within the range of the
SKIM transceiver antenna ring when it is inserted
into the ignition lock cylinder. The SKIM determines
whether a valid key is present in the ignition lock
cylinder based upon the response from the transpon-
der. If a valid key is detected, that fact is communi-
cated by the SKIM to the Powertrain Control Module
(PCM) over the Programmable Communications
Interface (PCI) data bus, and the PCM allows the
engine to continue running. If the PCM receives an
invalid key message, or receives no message from the
SKIM over the PCI data bus, the engine will be dis-
abled after about two seconds of operation. The Elec-
troMechanical Instrument Cluster (EMIC) will also
respond to the invalid key message on the PCI data
bus by flashing the SKIS indicator on and off.
Each Sentry Key has a unique transponder identi-
fication code permanently programmed into it by the
manufacturer. Likewise, the SKIM has a unique
Secret Key code programmed into it by the manufac-
turer. When a Sentry Key is programmed into the
memory of the SKIM, the SKIM stores the transpon-
der identification code from the Sentry Key, and the
Sentry Key learns the Secret Key code from the
SKIM. Once the Sentry Key learns the Secret Key
code of the SKIM, it is permanently stored in the
memory of the transponder. Therefore, once a Sentry
Key has been programmed to a particular vehicle, it
cannot be used on any other vehicle. (Refer to 8 -
ELECTRICAL/VEHICLE THEFT SECURITY -
STANDARD PROCEDURE - TRANSPONDER PRO-
GRAMMING).
VTSS INDICATOR
DESCRIPTION
The Vehicle Theft Security System (VTSS) indica-
tor consists of a red Light-Emitting Diode that is
mounted and integral to the automatic headlamp
light sensor photo diode unit, which is located on the
top of the instrument panel. The remainder of the
housing including the mount and the electrical con-
nection are concealed beneath the instrument panel
top cover.
The VTSS indicator cannot be adjusted or repaired
the entire automatic headlamp light sensor/VTSS
indicator must be replaced. (Refer to 8 - ELECTRI-
CAL/LAMPS/LIGHTING - EXTERIOR/AUTO HEAD-
LAMP SENSOR - REMOVAL).
Fig. 10 Sentry Key Immobilizer Transponder
1 - MOLDED CAP
2 - TRANSPONDER CHIP
3 - MOLDED CAP REMOVED
4 - TRANSPONDER KEY
WJVEHICLE THEFT SECURITY 8Q - 15
SKIS INDICATOR LAMP (Continued)