brake sensor JEEP GRAND CHEROKEE 2002 WJ / 2.G Owner's Manual
[x] Cancel search | Manufacturer: JEEP, Model Year: 2002, Model line: GRAND CHEROKEE, Model: JEEP GRAND CHEROKEE 2002 WJ / 2.GPages: 2199, PDF Size: 76.01 MB
Page 221 of 2199
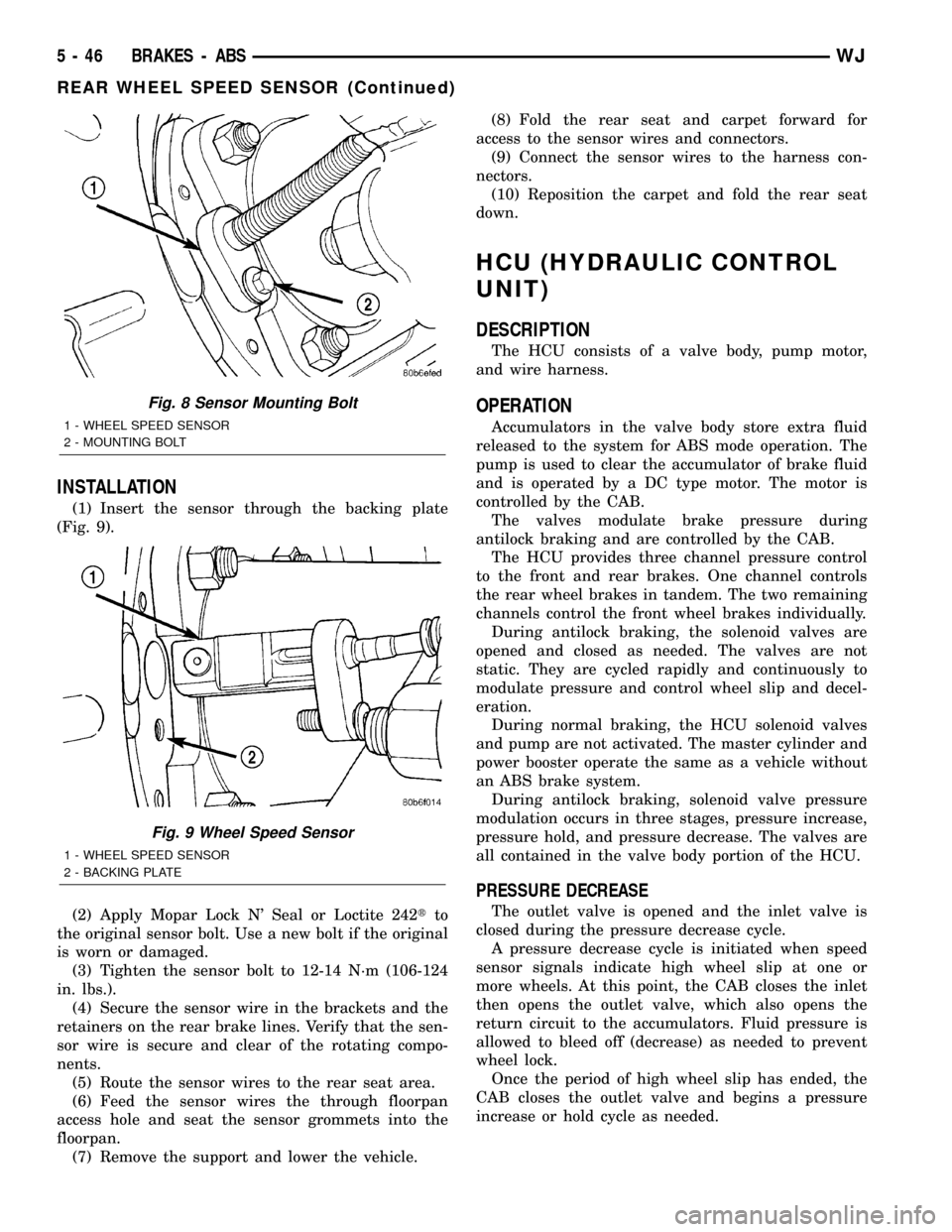
INSTALLATION
(1) Insert the sensor through the backing plate
(Fig. 9).
(2) Apply Mopar Lock N' Seal or Loctite 242tto
the original sensor bolt. Use a new bolt if the original
is worn or damaged.
(3) Tighten the sensor bolt to 12-14 N´m (106-124
in. lbs.).
(4) Secure the sensor wire in the brackets and the
retainers on the rear brake lines. Verify that the sen-
sor wire is secure and clear of the rotating compo-
nents.
(5) Route the sensor wires to the rear seat area.
(6) Feed the sensor wires the through floorpan
access hole and seat the sensor grommets into the
floorpan.
(7) Remove the support and lower the vehicle.(8) Fold the rear seat and carpet forward for
access to the sensor wires and connectors.
(9) Connect the sensor wires to the harness con-
nectors.
(10) Reposition the carpet and fold the rear seat
down.
HCU (HYDRAULIC CONTROL
UNIT)
DESCRIPTION
The HCU consists of a valve body, pump motor,
and wire harness.
OPERATION
Accumulators in the valve body store extra fluid
released to the system for ABS mode operation. The
pump is used to clear the accumulator of brake fluid
and is operated by a DC type motor. The motor is
controlled by the CAB.
The valves modulate brake pressure during
antilock braking and are controlled by the CAB.
The HCU provides three channel pressure control
to the front and rear brakes. One channel controls
the rear wheel brakes in tandem. The two remaining
channels control the front wheel brakes individually.
During antilock braking, the solenoid valves are
opened and closed as needed. The valves are not
static. They are cycled rapidly and continuously to
modulate pressure and control wheel slip and decel-
eration.
During normal braking, the HCU solenoid valves
and pump are not activated. The master cylinder and
power booster operate the same as a vehicle without
an ABS brake system.
During antilock braking, solenoid valve pressure
modulation occurs in three stages, pressure increase,
pressure hold, and pressure decrease. The valves are
all contained in the valve body portion of the HCU.
PRESSURE DECREASE
The outlet valve is opened and the inlet valve is
closed during the pressure decrease cycle.
A pressure decrease cycle is initiated when speed
sensor signals indicate high wheel slip at one or
more wheels. At this point, the CAB closes the inlet
then opens the outlet valve, which also opens the
return circuit to the accumulators. Fluid pressure is
allowed to bleed off (decrease) as needed to prevent
wheel lock.
Once the period of high wheel slip has ended, the
CAB closes the outlet valve and begins a pressure
increase or hold cycle as needed.
Fig. 8 Sensor Mounting Bolt
1 - WHEEL SPEED SENSOR
2 - MOUNTING BOLT
Fig. 9 Wheel Speed Sensor
1 - WHEEL SPEED SENSOR
2 - BACKING PLATE
5 - 46 BRAKES - ABSWJ
REAR WHEEL SPEED SENSOR (Continued)
Page 222 of 2199
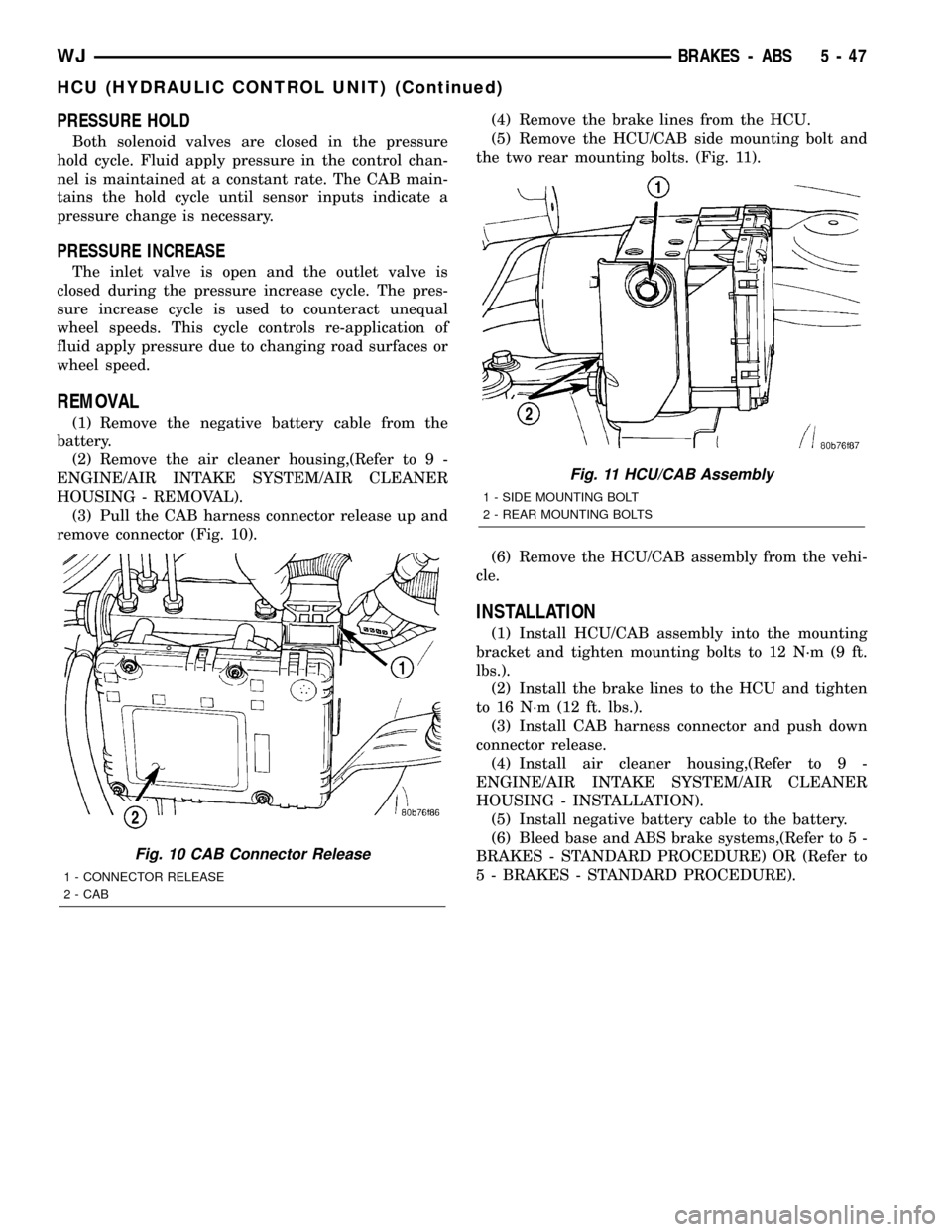
PRESSURE HOLD
Both solenoid valves are closed in the pressure
hold cycle. Fluid apply pressure in the control chan-
nel is maintained at a constant rate. The CAB main-
tains the hold cycle until sensor inputs indicate a
pressure change is necessary.
PRESSURE INCREASE
The inlet valve is open and the outlet valve is
closed during the pressure increase cycle. The pres-
sure increase cycle is used to counteract unequal
wheel speeds. This cycle controls re-application of
fluid apply pressure due to changing road surfaces or
wheel speed.
REMOVAL
(1) Remove the negative battery cable from the
battery.
(2) Remove the air cleaner housing,(Refer to 9 -
ENGINE/AIR INTAKE SYSTEM/AIR CLEANER
HOUSING - REMOVAL).
(3) Pull the CAB harness connector release up and
remove connector (Fig. 10).(4) Remove the brake lines from the HCU.
(5) Remove the HCU/CAB side mounting bolt and
the two rear mounting bolts. (Fig. 11).
(6) Remove the HCU/CAB assembly from the vehi-
cle.
INSTALLATION
(1) Install HCU/CAB assembly into the mounting
bracket and tighten mounting bolts to 12 N´m (9 ft.
lbs.).
(2) Install the brake lines to the HCU and tighten
to 16 N´m (12 ft. lbs.).
(3) Install CAB harness connector and push down
connector release.
(4) Install air cleaner housing,(Refer to 9 -
ENGINE/AIR INTAKE SYSTEM/AIR CLEANER
HOUSING - INSTALLATION).
(5) Install negative battery cable to the battery.
(6) Bleed base and ABS brake systems,(Refer to 5 -
BRAKES - STANDARD PROCEDURE) OR (Refer to
5 - BRAKES - STANDARD PROCEDURE).
Fig. 10 CAB Connector Release
1 - CONNECTOR RELEASE
2 - CAB
Fig. 11 HCU/CAB Assembly
1 - SIDE MOUNTING BOLT
2 - REAR MOUNTING BOLTS
WJBRAKES - ABS 5 - 47
HCU (HYDRAULIC CONTROL UNIT) (Continued)
Page 310 of 2199
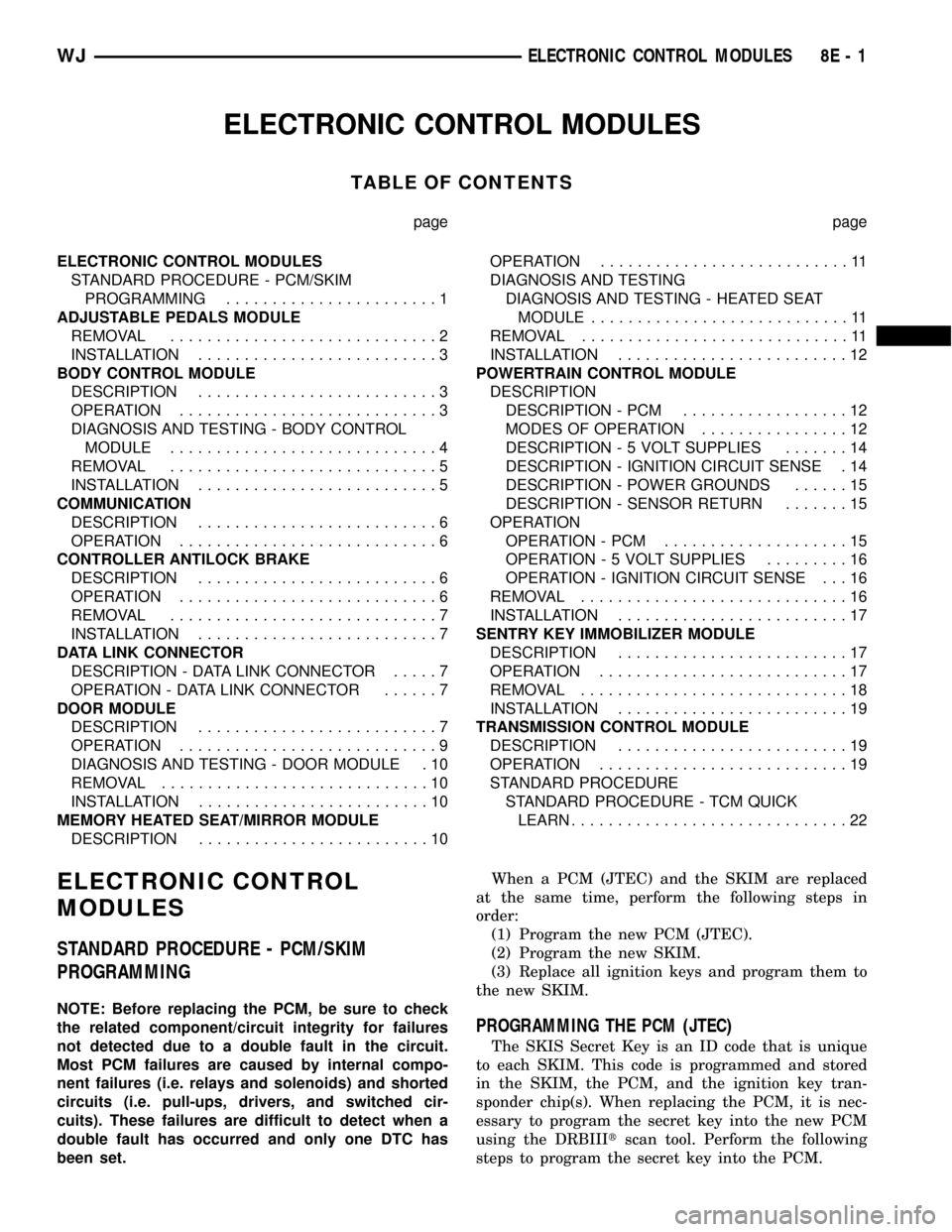
ELECTRONIC CONTROL MODULES
TABLE OF CONTENTS
page page
ELECTRONIC CONTROL MODULES
STANDARD PROCEDURE - PCM/SKIM
PROGRAMMING.......................1
ADJUSTABLE PEDALS MODULE
REMOVAL.............................2
INSTALLATION..........................3
BODY CONTROL MODULE
DESCRIPTION..........................3
OPERATION............................3
DIAGNOSIS AND TESTING - BODY CONTROL
MODULE.............................4
REMOVAL.............................5
INSTALLATION..........................5
COMMUNICATION
DESCRIPTION..........................6
OPERATION............................6
CONTROLLER ANTILOCK BRAKE
DESCRIPTION..........................6
OPERATION............................6
REMOVAL.............................7
INSTALLATION..........................7
DATA LINK CONNECTOR
DESCRIPTION - DATA LINK CONNECTOR.....7
OPERATION - DATA LINK CONNECTOR......7
DOOR MODULE
DESCRIPTION..........................7
OPERATION............................9
DIAGNOSIS AND TESTING - DOOR MODULE . 10
REMOVAL.............................10
INSTALLATION.........................10
MEMORY HEATED SEAT/MIRROR MODULE
DESCRIPTION.........................10OPERATION...........................11
DIAGNOSIS AND TESTING
DIAGNOSIS AND TESTING - HEATED SEAT
MODULE............................11
REMOVAL.............................11
INSTALLATION.........................12
POWERTRAIN CONTROL MODULE
DESCRIPTION
DESCRIPTION - PCM..................12
MODES OF OPERATION................12
DESCRIPTION - 5 VOLT SUPPLIES.......14
DESCRIPTION - IGNITION CIRCUIT SENSE . 14
DESCRIPTION - POWER GROUNDS......15
DESCRIPTION - SENSOR RETURN.......15
OPERATION
OPERATION - PCM....................15
OPERATION - 5 VOLT SUPPLIES.........16
OPERATION - IGNITION CIRCUIT SENSE . . . 16
REMOVAL.............................16
INSTALLATION.........................17
SENTRY KEY IMMOBILIZER MODULE
DESCRIPTION.........................17
OPERATION...........................17
REMOVAL.............................18
INSTALLATION.........................19
TRANSMISSION CONTROL MODULE
DESCRIPTION.........................19
OPERATION...........................19
STANDARD PROCEDURE
STANDARD PROCEDURE - TCM QUICK
LEARN..............................22
ELECTRONIC CONTROL
MODULES
STANDARD PROCEDURE - PCM/SKIM
PROGRAMMING
NOTE: Before replacing the PCM, be sure to check
the related component/circuit integrity for failures
not detected due to a double fault in the circuit.
Most PCM failures are caused by internal compo-
nent failures (i.e. relays and solenoids) and shorted
circuits (i.e. pull-ups, drivers, and switched cir-
cuits). These failures are difficult to detect when a
double fault has occurred and only one DTC has
been set.When a PCM (JTEC) and the SKIM are replaced
at the same time, perform the following steps in
order:
(1) Program the new PCM (JTEC).
(2) Program the new SKIM.
(3) Replace all ignition keys and program them to
the new SKIM.
PROGRAMMING THE PCM (JTEC)
The SKIS Secret Key is an ID code that is unique
to each SKIM. This code is programmed and stored
in the SKIM, the PCM, and the ignition key tran-
sponder chip(s). When replacing the PCM, it is nec-
essary to program the secret key into the new PCM
using the DRBIIItscan tool. Perform the following
steps to program the secret key into the PCM.
WJELECTRONIC CONTROL MODULES 8E - 1
Page 312 of 2199
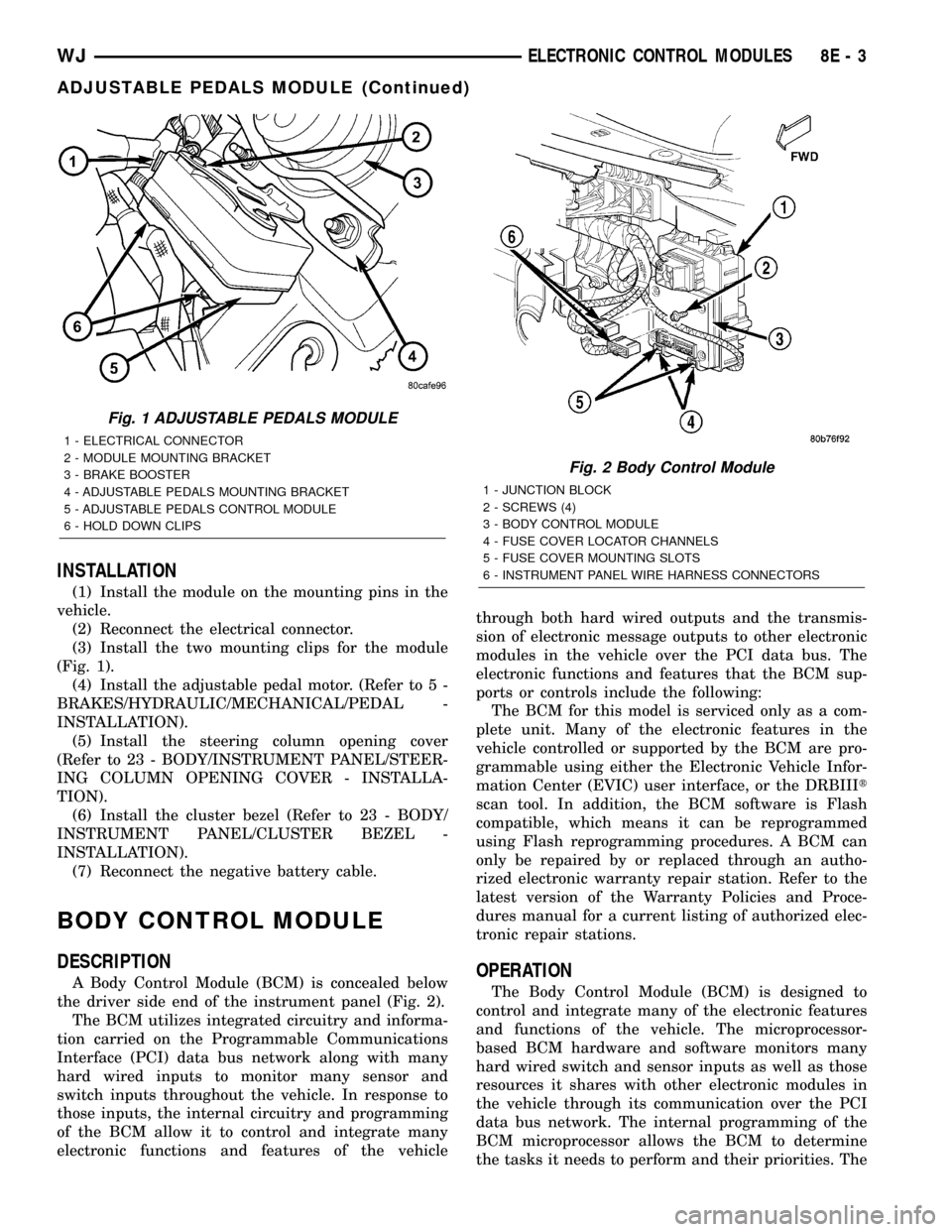
INSTALLATION
(1) Install the module on the mounting pins in the
vehicle.
(2) Reconnect the electrical connector.
(3) Install the two mounting clips for the module
(Fig. 1).
(4) Install the adjustable pedal motor. (Refer to 5 -
BRAKES/HYDRAULIC/MECHANICAL/PEDAL -
INSTALLATION).
(5) Install the steering column opening cover
(Refer to 23 - BODY/INSTRUMENT PANEL/STEER-
ING COLUMN OPENING COVER - INSTALLA-
TION).
(6) Install the cluster bezel (Refer to 23 - BODY/
INSTRUMENT PANEL/CLUSTER BEZEL -
INSTALLATION).
(7) Reconnect the negative battery cable.
BODY CONTROL MODULE
DESCRIPTION
A Body Control Module (BCM) is concealed below
the driver side end of the instrument panel (Fig. 2).
The BCM utilizes integrated circuitry and informa-
tion carried on the Programmable Communications
Interface (PCI) data bus network along with many
hard wired inputs to monitor many sensor and
switch inputs throughout the vehicle. In response to
those inputs, the internal circuitry and programming
of the BCM allow it to control and integrate many
electronic functions and features of the vehiclethrough both hard wired outputs and the transmis-
sion of electronic message outputs to other electronic
modules in the vehicle over the PCI data bus. The
electronic functions and features that the BCM sup-
ports or controls include the following:
The BCM for this model is serviced only as a com-
plete unit. Many of the electronic features in the
vehicle controlled or supported by the BCM are pro-
grammable using either the Electronic Vehicle Infor-
mation Center (EVIC) user interface, or the DRBIIIt
scan tool. In addition, the BCM software is Flash
compatible, which means it can be reprogrammed
using Flash reprogramming procedures. A BCM can
only be repaired by or replaced through an autho-
rized electronic warranty repair station. Refer to the
latest version of the Warranty Policies and Proce-
dures manual for a current listing of authorized elec-
tronic repair stations.OPERATION
The Body Control Module (BCM) is designed to
control and integrate many of the electronic features
and functions of the vehicle. The microprocessor-
based BCM hardware and software monitors many
hard wired switch and sensor inputs as well as those
resources it shares with other electronic modules in
the vehicle through its communication over the PCI
data bus network. The internal programming of the
BCM microprocessor allows the BCM to determine
the tasks it needs to perform and their priorities. The
Fig. 1 ADJUSTABLE PEDALS MODULE
1 - ELECTRICAL CONNECTOR
2 - MODULE MOUNTING BRACKET
3 - BRAKE BOOSTER
4 - ADJUSTABLE PEDALS MOUNTING BRACKET
5 - ADJUSTABLE PEDALS CONTROL MODULE
6 - HOLD DOWN CLIPS
Fig. 2 Body Control Module
1 - JUNCTION BLOCK
2 - SCREWS (4)
3 - BODY CONTROL MODULE
4 - FUSE COVER LOCATOR CHANNELS
5 - FUSE COVER MOUNTING SLOTS
6 - INSTRUMENT PANEL WIRE HARNESS CONNECTORS
WJELECTRONIC CONTROL MODULES 8E - 3
ADJUSTABLE PEDALS MODULE (Continued)
Page 315 of 2199
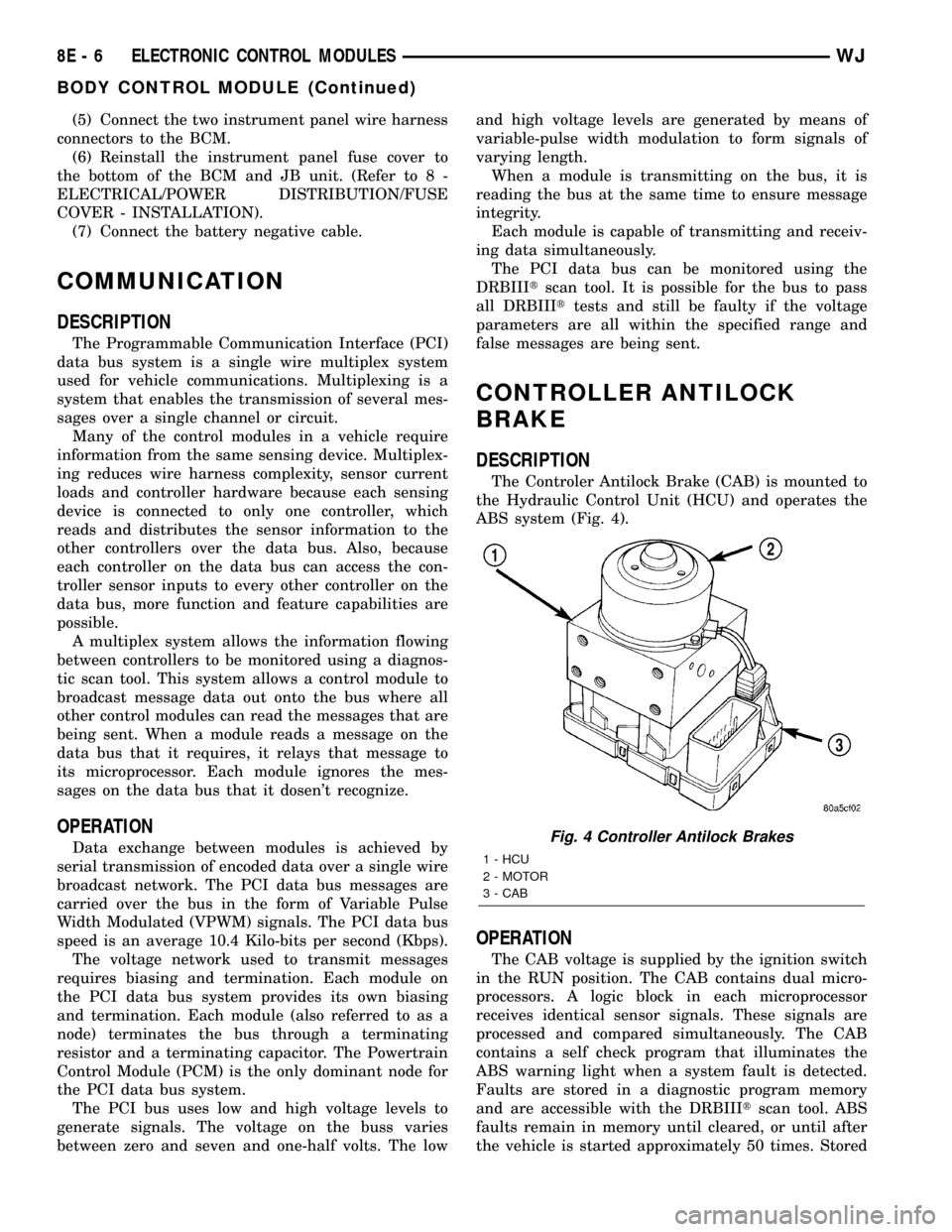
(5) Connect the two instrument panel wire harness
connectors to the BCM.
(6) Reinstall the instrument panel fuse cover to
the bottom of the BCM and JB unit. (Refer to 8 -
ELECTRICAL/POWER DISTRIBUTION/FUSE
COVER - INSTALLATION).
(7) Connect the battery negative cable.
COMMUNICATION
DESCRIPTION
The Programmable Communication Interface (PCI)
data bus system is a single wire multiplex system
used for vehicle communications. Multiplexing is a
system that enables the transmission of several mes-
sages over a single channel or circuit.
Many of the control modules in a vehicle require
information from the same sensing device. Multiplex-
ing reduces wire harness complexity, sensor current
loads and controller hardware because each sensing
device is connected to only one controller, which
reads and distributes the sensor information to the
other controllers over the data bus. Also, because
each controller on the data bus can access the con-
troller sensor inputs to every other controller on the
data bus, more function and feature capabilities are
possible.
A multiplex system allows the information flowing
between controllers to be monitored using a diagnos-
tic scan tool. This system allows a control module to
broadcast message data out onto the bus where all
other control modules can read the messages that are
being sent. When a module reads a message on the
data bus that it requires, it relays that message to
its microprocessor. Each module ignores the mes-
sages on the data bus that it dosen't recognize.
OPERATION
Data exchange between modules is achieved by
serial transmission of encoded data over a single wire
broadcast network. The PCI data bus messages are
carried over the bus in the form of Variable Pulse
Width Modulated (VPWM) signals. The PCI data bus
speed is an average 10.4 Kilo-bits per second (Kbps).
The voltage network used to transmit messages
requires biasing and termination. Each module on
the PCI data bus system provides its own biasing
and termination. Each module (also referred to as a
node) terminates the bus through a terminating
resistor and a terminating capacitor. The Powertrain
Control Module (PCM) is the only dominant node for
the PCI data bus system.
The PCI bus uses low and high voltage levels to
generate signals. The voltage on the buss varies
between zero and seven and one-half volts. The lowand high voltage levels are generated by means of
variable-pulse width modulation to form signals of
varying length.
When a module is transmitting on the bus, it is
reading the bus at the same time to ensure message
integrity.
Each module is capable of transmitting and receiv-
ing data simultaneously.
The PCI data bus can be monitored using the
DRBIIItscan tool. It is possible for the bus to pass
all DRBIIIttests and still be faulty if the voltage
parameters are all within the specified range and
false messages are being sent.
CONTROLLER ANTILOCK
BRAKE
DESCRIPTION
The Controler Antilock Brake (CAB) is mounted to
the Hydraulic Control Unit (HCU) and operates the
ABS system (Fig. 4).
OPERATION
The CAB voltage is supplied by the ignition switch
in the RUN position. The CAB contains dual micro-
processors. A logic block in each microprocessor
receives identical sensor signals. These signals are
processed and compared simultaneously. The CAB
contains a self check program that illuminates the
ABS warning light when a system fault is detected.
Faults are stored in a diagnostic program memory
and are accessible with the DRBIIItscan tool. ABS
faults remain in memory until cleared, or until after
the vehicle is started approximately 50 times. Stored
Fig. 4 Controller Antilock Brakes
1 - HCU
2 - MOTOR
3 - CAB
8E - 6 ELECTRONIC CONTROL MODULESWJ
BODY CONTROL MODULE (Continued)
Page 316 of 2199
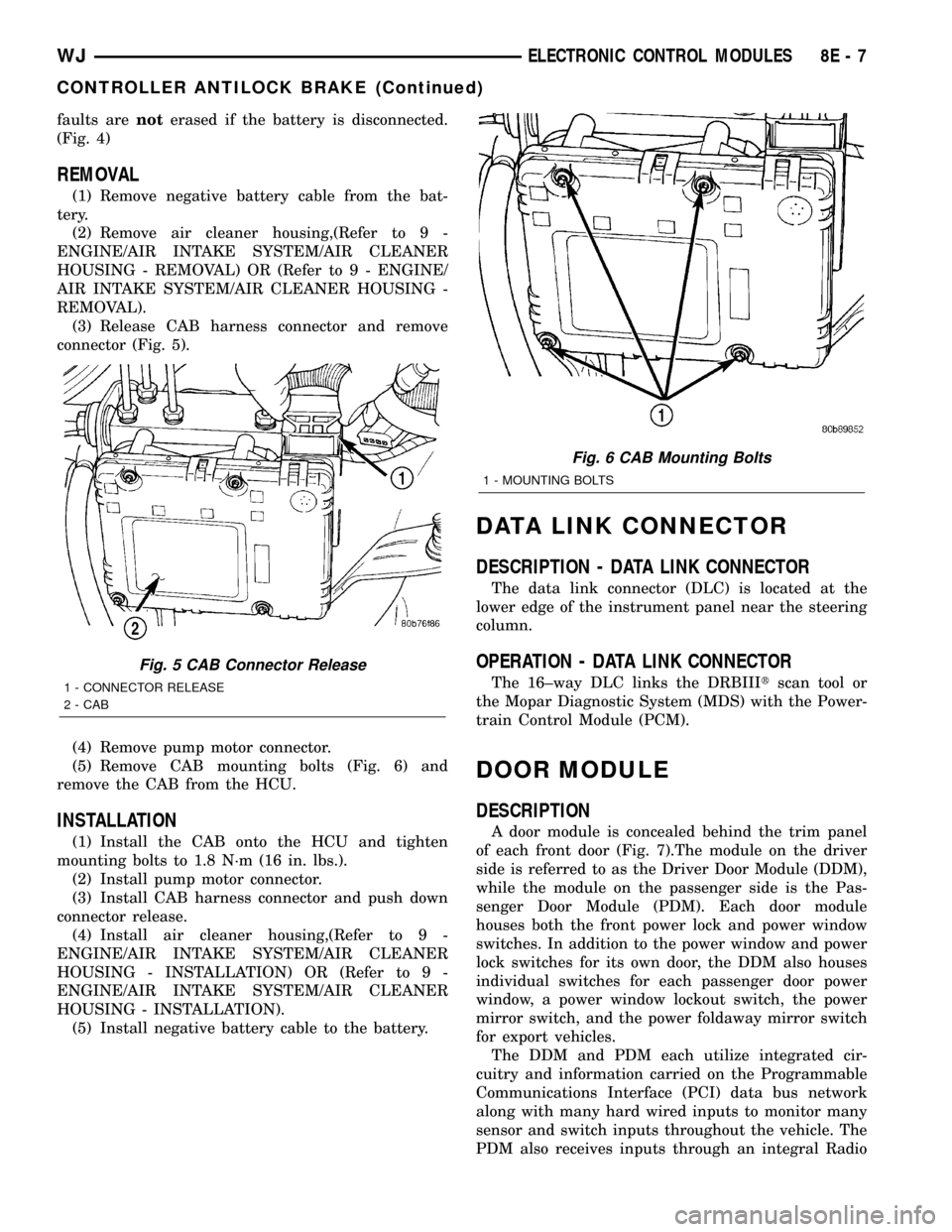
faults arenoterased if the battery is disconnected.
(Fig. 4)
REMOVAL
(1) Remove negative battery cable from the bat-
tery.
(2) Remove air cleaner housing,(Refer to 9 -
ENGINE/AIR INTAKE SYSTEM/AIR CLEANER
HOUSING - REMOVAL) OR (Refer to 9 - ENGINE/
AIR INTAKE SYSTEM/AIR CLEANER HOUSING -
REMOVAL).
(3) Release CAB harness connector and remove
connector (Fig. 5).
(4) Remove pump motor connector.
(5) Remove CAB mounting bolts (Fig. 6) and
remove the CAB from the HCU.
INSTALLATION
(1) Install the CAB onto the HCU and tighten
mounting bolts to 1.8 N´m (16 in. lbs.).
(2) Install pump motor connector.
(3) Install CAB harness connector and push down
connector release.
(4) Install air cleaner housing,(Refer to 9 -
ENGINE/AIR INTAKE SYSTEM/AIR CLEANER
HOUSING - INSTALLATION) OR (Refer to 9 -
ENGINE/AIR INTAKE SYSTEM/AIR CLEANER
HOUSING - INSTALLATION).
(5) Install negative battery cable to the battery.
DATA LINK CONNECTOR
DESCRIPTION - DATA LINK CONNECTOR
The data link connector (DLC) is located at the
lower edge of the instrument panel near the steering
column.
OPERATION - DATA LINK CONNECTOR
The 16±way DLC links the DRBIIItscan tool or
the Mopar Diagnostic System (MDS) with the Power-
train Control Module (PCM).
DOOR MODULE
DESCRIPTION
A door module is concealed behind the trim panel
of each front door (Fig. 7).The module on the driver
side is referred to as the Driver Door Module (DDM),
while the module on the passenger side is the Pas-
senger Door Module (PDM). Each door module
houses both the front power lock and power window
switches. In addition to the power window and power
lock switches for its own door, the DDM also houses
individual switches for each passenger door power
window, a power window lockout switch, the power
mirror switch, and the power foldaway mirror switch
for export vehicles.
The DDM and PDM each utilize integrated cir-
cuitry and information carried on the Programmable
Communications Interface (PCI) data bus network
along with many hard wired inputs to monitor many
sensor and switch inputs throughout the vehicle. The
PDM also receives inputs through an integral Radio
Fig. 5 CAB Connector Release
1 - CONNECTOR RELEASE
2 - CAB
Fig. 6 CAB Mounting Bolts
1 - MOUNTING BOLTS
WJELECTRONIC CONTROL MODULES 8E - 7
CONTROLLER ANTILOCK BRAKE (Continued)
Page 324 of 2199
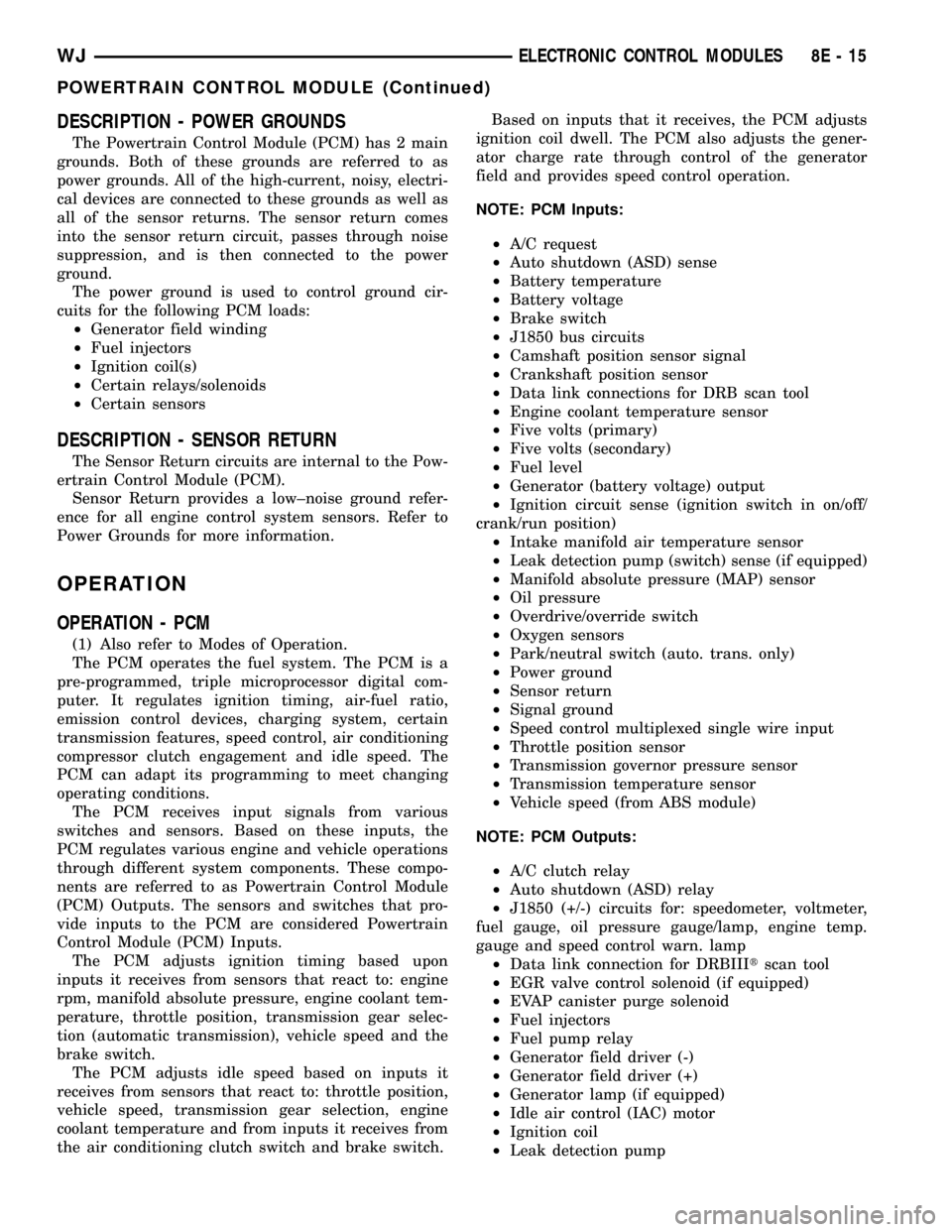
DESCRIPTION - POWER GROUNDS
The Powertrain Control Module (PCM) has 2 main
grounds. Both of these grounds are referred to as
power grounds. All of the high-current, noisy, electri-
cal devices are connected to these grounds as well as
all of the sensor returns. The sensor return comes
into the sensor return circuit, passes through noise
suppression, and is then connected to the power
ground.
The power ground is used to control ground cir-
cuits for the following PCM loads:
²Generator field winding
²Fuel injectors
²Ignition coil(s)
²Certain relays/solenoids
²Certain sensors
DESCRIPTION - SENSOR RETURN
The Sensor Return circuits are internal to the Pow-
ertrain Control Module (PCM).
Sensor Return provides a low±noise ground refer-
ence for all engine control system sensors. Refer to
Power Grounds for more information.
OPERATION
OPERATION - PCM
(1) Also refer to Modes of Operation.
The PCM operates the fuel system. The PCM is a
pre-programmed, triple microprocessor digital com-
puter. It regulates ignition timing, air-fuel ratio,
emission control devices, charging system, certain
transmission features, speed control, air conditioning
compressor clutch engagement and idle speed. The
PCM can adapt its programming to meet changing
operating conditions.
The PCM receives input signals from various
switches and sensors. Based on these inputs, the
PCM regulates various engine and vehicle operations
through different system components. These compo-
nents are referred to as Powertrain Control Module
(PCM) Outputs. The sensors and switches that pro-
vide inputs to the PCM are considered Powertrain
Control Module (PCM) Inputs.
The PCM adjusts ignition timing based upon
inputs it receives from sensors that react to: engine
rpm, manifold absolute pressure, engine coolant tem-
perature, throttle position, transmission gear selec-
tion (automatic transmission), vehicle speed and the
brake switch.
The PCM adjusts idle speed based on inputs it
receives from sensors that react to: throttle position,
vehicle speed, transmission gear selection, engine
coolant temperature and from inputs it receives from
the air conditioning clutch switch and brake switch.Based on inputs that it receives, the PCM adjusts
ignition coil dwell. The PCM also adjusts the gener-
ator charge rate through control of the generator
field and provides speed control operation.
NOTE: PCM Inputs:
²A/C request
²Auto shutdown (ASD) sense
²Battery temperature
²Battery voltage
²Brake switch
²J1850 bus circuits
²Camshaft position sensor signal
²Crankshaft position sensor
²Data link connections for DRB scan tool
²Engine coolant temperature sensor
²Five volts (primary)
²Five volts (secondary)
²Fuel level
²Generator (battery voltage) output
²Ignition circuit sense (ignition switch in on/off/
crank/run position)
²Intake manifold air temperature sensor
²Leak detection pump (switch) sense (if equipped)
²Manifold absolute pressure (MAP) sensor
²Oil pressure
²Overdrive/override switch
²Oxygen sensors
²Park/neutral switch (auto. trans. only)
²Power ground
²Sensor return
²Signal ground
²Speed control multiplexed single wire input
²Throttle position sensor
²Transmission governor pressure sensor
²Transmission temperature sensor
²Vehicle speed (from ABS module)
NOTE: PCM Outputs:
²A/C clutch relay
²Auto shutdown (ASD) relay
²J1850 (+/-) circuits for: speedometer, voltmeter,
fuel gauge, oil pressure gauge/lamp, engine temp.
gauge and speed control warn. lamp
²Data link connection for DRBIIItscan tool
²EGR valve control solenoid (if equipped)
²EVAP canister purge solenoid
²Fuel injectors
²Fuel pump relay
²Generator field driver (-)
²Generator field driver (+)
²Generator lamp (if equipped)
²Idle air control (IAC) motor
²Ignition coil
²Leak detection pump
WJELECTRONIC CONTROL MODULES 8E - 15
POWERTRAIN CONTROL MODULE (Continued)
Page 423 of 2199
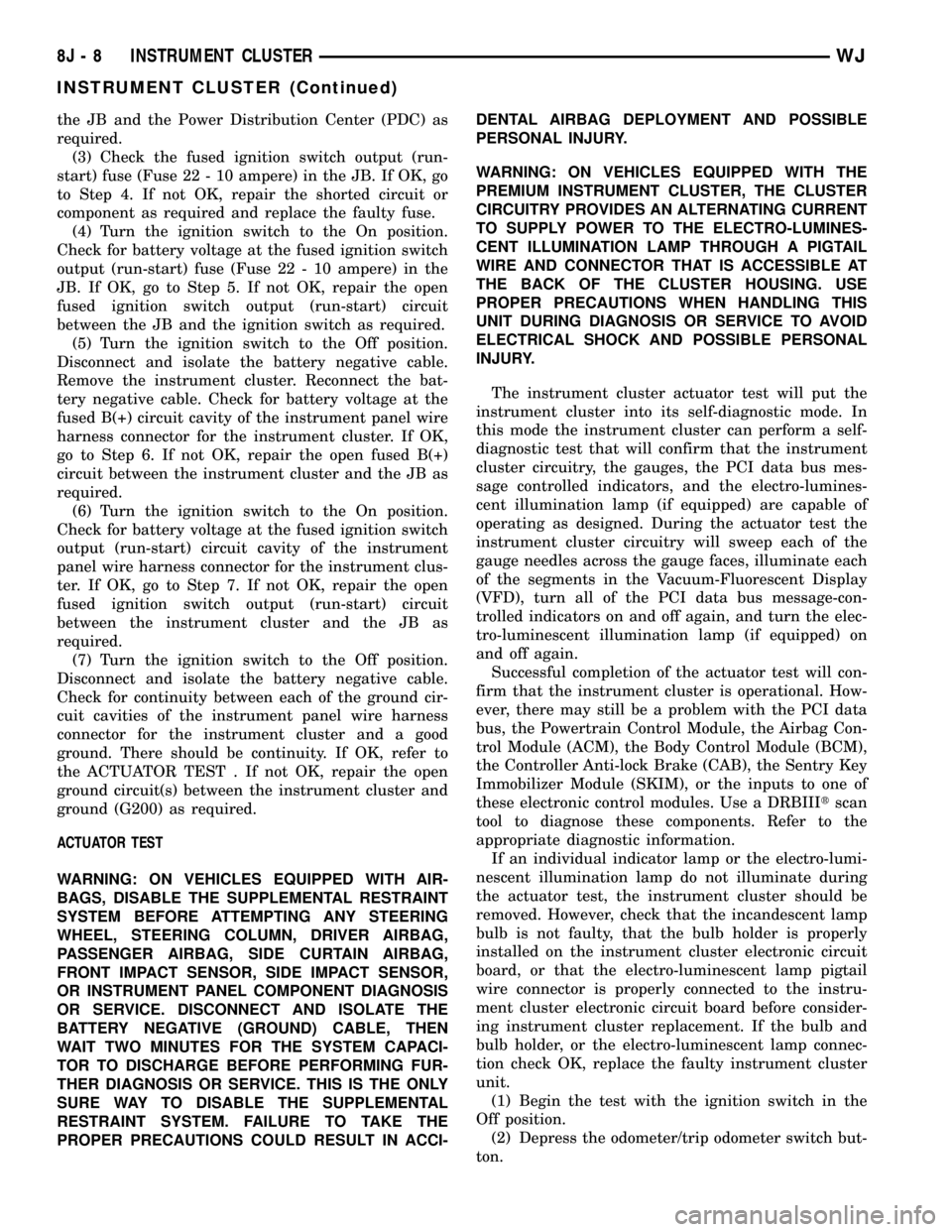
the JB and the Power Distribution Center (PDC) as
required.
(3) Check the fused ignition switch output (run-
start) fuse (Fuse 22 - 10 ampere) in the JB. If OK, go
to Step 4. If not OK, repair the shorted circuit or
component as required and replace the faulty fuse.
(4) Turn the ignition switch to the On position.
Check for battery voltage at the fused ignition switch
output (run-start) fuse (Fuse 22 - 10 ampere) in the
JB. If OK, go to Step 5. If not OK, repair the open
fused ignition switch output (run-start) circuit
between the JB and the ignition switch as required.
(5) Turn the ignition switch to the Off position.
Disconnect and isolate the battery negative cable.
Remove the instrument cluster. Reconnect the bat-
tery negative cable. Check for battery voltage at the
fused B(+) circuit cavity of the instrument panel wire
harness connector for the instrument cluster. If OK,
go to Step 6. If not OK, repair the open fused B(+)
circuit between the instrument cluster and the JB as
required.
(6) Turn the ignition switch to the On position.
Check for battery voltage at the fused ignition switch
output (run-start) circuit cavity of the instrument
panel wire harness connector for the instrument clus-
ter. If OK, go to Step 7. If not OK, repair the open
fused ignition switch output (run-start) circuit
between the instrument cluster and the JB as
required.
(7) Turn the ignition switch to the Off position.
Disconnect and isolate the battery negative cable.
Check for continuity between each of the ground cir-
cuit cavities of the instrument panel wire harness
connector for the instrument cluster and a good
ground. There should be continuity. If OK, refer to
the ACTUATOR TEST . If not OK, repair the open
ground circuit(s) between the instrument cluster and
ground (G200) as required.
ACTUATOR TEST
WARNING: ON VEHICLES EQUIPPED WITH AIR-
BAGS, DISABLE THE SUPPLEMENTAL RESTRAINT
SYSTEM BEFORE ATTEMPTING ANY STEERING
WHEEL, STEERING COLUMN, DRIVER AIRBAG,
PASSENGER AIRBAG, SIDE CURTAIN AIRBAG,
FRONT IMPACT SENSOR, SIDE IMPACT SENSOR,
OR INSTRUMENT PANEL COMPONENT DIAGNOSIS
OR SERVICE. DISCONNECT AND ISOLATE THE
BATTERY NEGATIVE (GROUND) CABLE, THEN
WAIT TWO MINUTES FOR THE SYSTEM CAPACI-
TOR TO DISCHARGE BEFORE PERFORMING FUR-
THER DIAGNOSIS OR SERVICE. THIS IS THE ONLY
SURE WAY TO DISABLE THE SUPPLEMENTAL
RESTRAINT SYSTEM. FAILURE TO TAKE THE
PROPER PRECAUTIONS COULD RESULT IN ACCI-DENTAL AIRBAG DEPLOYMENT AND POSSIBLE
PERSONAL INJURY.
WARNING: ON VEHICLES EQUIPPED WITH THE
PREMIUM INSTRUMENT CLUSTER, THE CLUSTER
CIRCUITRY PROVIDES AN ALTERNATING CURRENT
TO SUPPLY POWER TO THE ELECTRO-LUMINES-
CENT ILLUMINATION LAMP THROUGH A PIGTAIL
WIRE AND CONNECTOR THAT IS ACCESSIBLE AT
THE BACK OF THE CLUSTER HOUSING. USE
PROPER PRECAUTIONS WHEN HANDLING THIS
UNIT DURING DIAGNOSIS OR SERVICE TO AVOID
ELECTRICAL SHOCK AND POSSIBLE PERSONAL
INJURY.
The instrument cluster actuator test will put the
instrument cluster into its self-diagnostic mode. In
this mode the instrument cluster can perform a self-
diagnostic test that will confirm that the instrument
cluster circuitry, the gauges, the PCI data bus mes-
sage controlled indicators, and the electro-lumines-
cent illumination lamp (if equipped) are capable of
operating as designed. During the actuator test the
instrument cluster circuitry will sweep each of the
gauge needles across the gauge faces, illuminate each
of the segments in the Vacuum-Fluorescent Display
(VFD), turn all of the PCI data bus message-con-
trolled indicators on and off again, and turn the elec-
tro-luminescent illumination lamp (if equipped) on
and off again.
Successful completion of the actuator test will con-
firm that the instrument cluster is operational. How-
ever, there may still be a problem with the PCI data
bus, the Powertrain Control Module, the Airbag Con-
trol Module (ACM), the Body Control Module (BCM),
the Controller Anti-lock Brake (CAB), the Sentry Key
Immobilizer Module (SKIM), or the inputs to one of
these electronic control modules. Use a DRBIIItscan
tool to diagnose these components. Refer to the
appropriate diagnostic information.
If an individual indicator lamp or the electro-lumi-
nescent illumination lamp do not illuminate during
the actuator test, the instrument cluster should be
removed. However, check that the incandescent lamp
bulb is not faulty, that the bulb holder is properly
installed on the instrument cluster electronic circuit
board, or that the electro-luminescent lamp pigtail
wire connector is properly connected to the instru-
ment cluster electronic circuit board before consider-
ing instrument cluster replacement. If the bulb and
bulb holder, or the electro-luminescent lamp connec-
tion check OK, replace the faulty instrument cluster
unit.
(1) Begin the test with the ignition switch in the
Off position.
(2) Depress the odometer/trip odometer switch but-
ton.
8J - 8 INSTRUMENT CLUSTERWJ
INSTRUMENT CLUSTER (Continued)
Page 429 of 2199
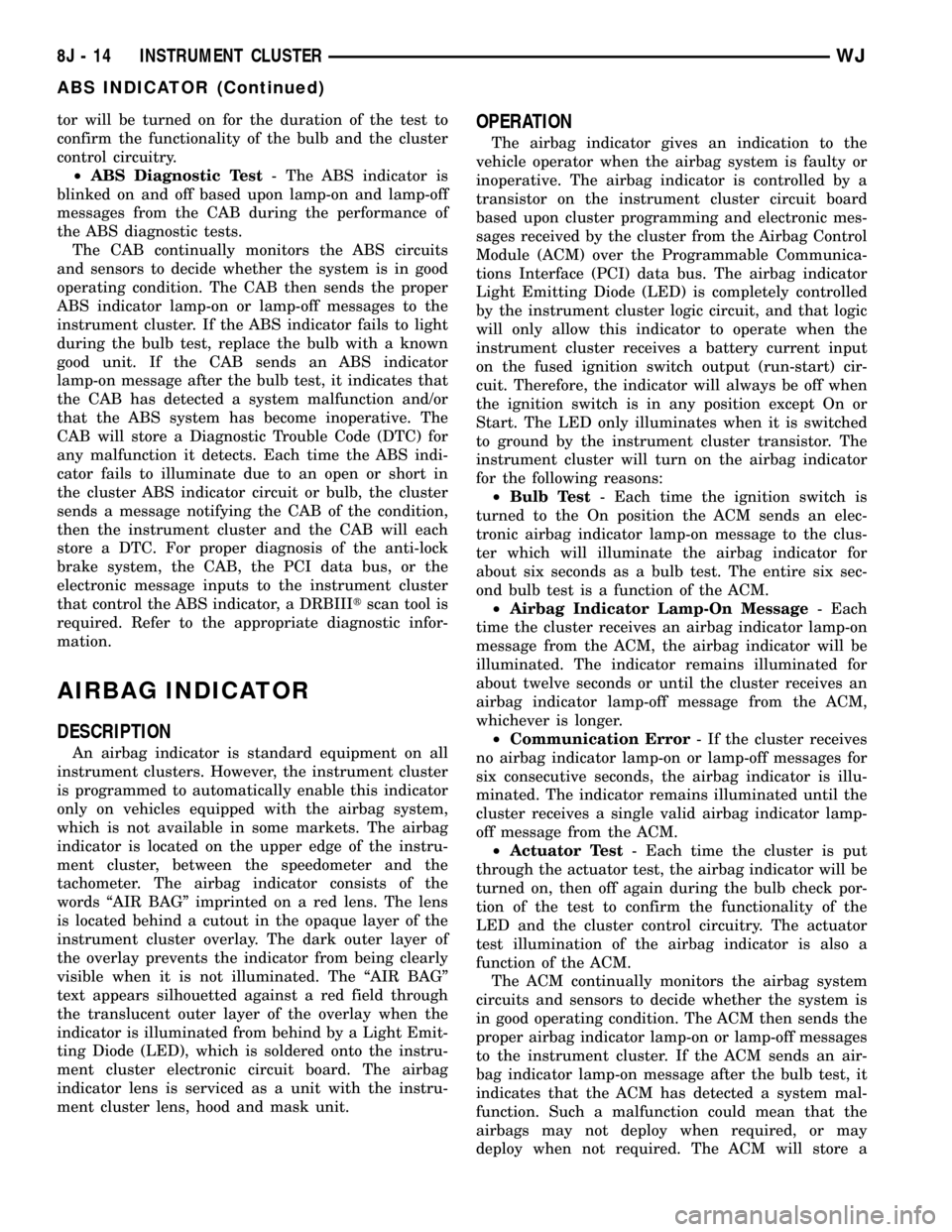
tor will be turned on for the duration of the test to
confirm the functionality of the bulb and the cluster
control circuitry.
²ABS Diagnostic Test- The ABS indicator is
blinked on and off based upon lamp-on and lamp-off
messages from the CAB during the performance of
the ABS diagnostic tests.
The CAB continually monitors the ABS circuits
and sensors to decide whether the system is in good
operating condition. The CAB then sends the proper
ABS indicator lamp-on or lamp-off messages to the
instrument cluster. If the ABS indicator fails to light
during the bulb test, replace the bulb with a known
good unit. If the CAB sends an ABS indicator
lamp-on message after the bulb test, it indicates that
the CAB has detected a system malfunction and/or
that the ABS system has become inoperative. The
CAB will store a Diagnostic Trouble Code (DTC) for
any malfunction it detects. Each time the ABS indi-
cator fails to illuminate due to an open or short in
the cluster ABS indicator circuit or bulb, the cluster
sends a message notifying the CAB of the condition,
then the instrument cluster and the CAB will each
store a DTC. For proper diagnosis of the anti-lock
brake system, the CAB, the PCI data bus, or the
electronic message inputs to the instrument cluster
that control the ABS indicator, a DRBIIItscan tool is
required. Refer to the appropriate diagnostic infor-
mation.
AIRBAG INDICATOR
DESCRIPTION
An airbag indicator is standard equipment on all
instrument clusters. However, the instrument cluster
is programmed to automatically enable this indicator
only on vehicles equipped with the airbag system,
which is not available in some markets. The airbag
indicator is located on the upper edge of the instru-
ment cluster, between the speedometer and the
tachometer. The airbag indicator consists of the
words ªAIR BAGº imprinted on a red lens. The lens
is located behind a cutout in the opaque layer of the
instrument cluster overlay. The dark outer layer of
the overlay prevents the indicator from being clearly
visible when it is not illuminated. The ªAIR BAGº
text appears silhouetted against a red field through
the translucent outer layer of the overlay when the
indicator is illuminated from behind by a Light Emit-
ting Diode (LED), which is soldered onto the instru-
ment cluster electronic circuit board. The airbag
indicator lens is serviced as a unit with the instru-
ment cluster lens, hood and mask unit.
OPERATION
The airbag indicator gives an indication to the
vehicle operator when the airbag system is faulty or
inoperative. The airbag indicator is controlled by a
transistor on the instrument cluster circuit board
based upon cluster programming and electronic mes-
sages received by the cluster from the Airbag Control
Module (ACM) over the Programmable Communica-
tions Interface (PCI) data bus. The airbag indicator
Light Emitting Diode (LED) is completely controlled
by the instrument cluster logic circuit, and that logic
will only allow this indicator to operate when the
instrument cluster receives a battery current input
on the fused ignition switch output (run-start) cir-
cuit. Therefore, the indicator will always be off when
the ignition switch is in any position except On or
Start. The LED only illuminates when it is switched
to ground by the instrument cluster transistor. The
instrument cluster will turn on the airbag indicator
for the following reasons:
²Bulb Test- Each time the ignition switch is
turned to the On position the ACM sends an elec-
tronic airbag indicator lamp-on message to the clus-
ter which will illuminate the airbag indicator for
about six seconds as a bulb test. The entire six sec-
ond bulb test is a function of the ACM.
²Airbag Indicator Lamp-On Message- Each
time the cluster receives an airbag indicator lamp-on
message from the ACM, the airbag indicator will be
illuminated. The indicator remains illuminated for
about twelve seconds or until the cluster receives an
airbag indicator lamp-off message from the ACM,
whichever is longer.
²Communication Error- If the cluster receives
no airbag indicator lamp-on or lamp-off messages for
six consecutive seconds, the airbag indicator is illu-
minated. The indicator remains illuminated until the
cluster receives a single valid airbag indicator lamp-
off message from the ACM.
²Actuator Test- Each time the cluster is put
through the actuator test, the airbag indicator will be
turned on, then off again during the bulb check por-
tion of the test to confirm the functionality of the
LED and the cluster control circuitry. The actuator
test illumination of the airbag indicator is also a
function of the ACM.
The ACM continually monitors the airbag system
circuits and sensors to decide whether the system is
in good operating condition. The ACM then sends the
proper airbag indicator lamp-on or lamp-off messages
to the instrument cluster. If the ACM sends an air-
bag indicator lamp-on message after the bulb test, it
indicates that the ACM has detected a system mal-
function. Such a malfunction could mean that the
airbags may not deploy when required, or may
deploy when not required. The ACM will store a
8J - 14 INSTRUMENT CLUSTERWJ
ABS INDICATOR (Continued)
Page 431 of 2199
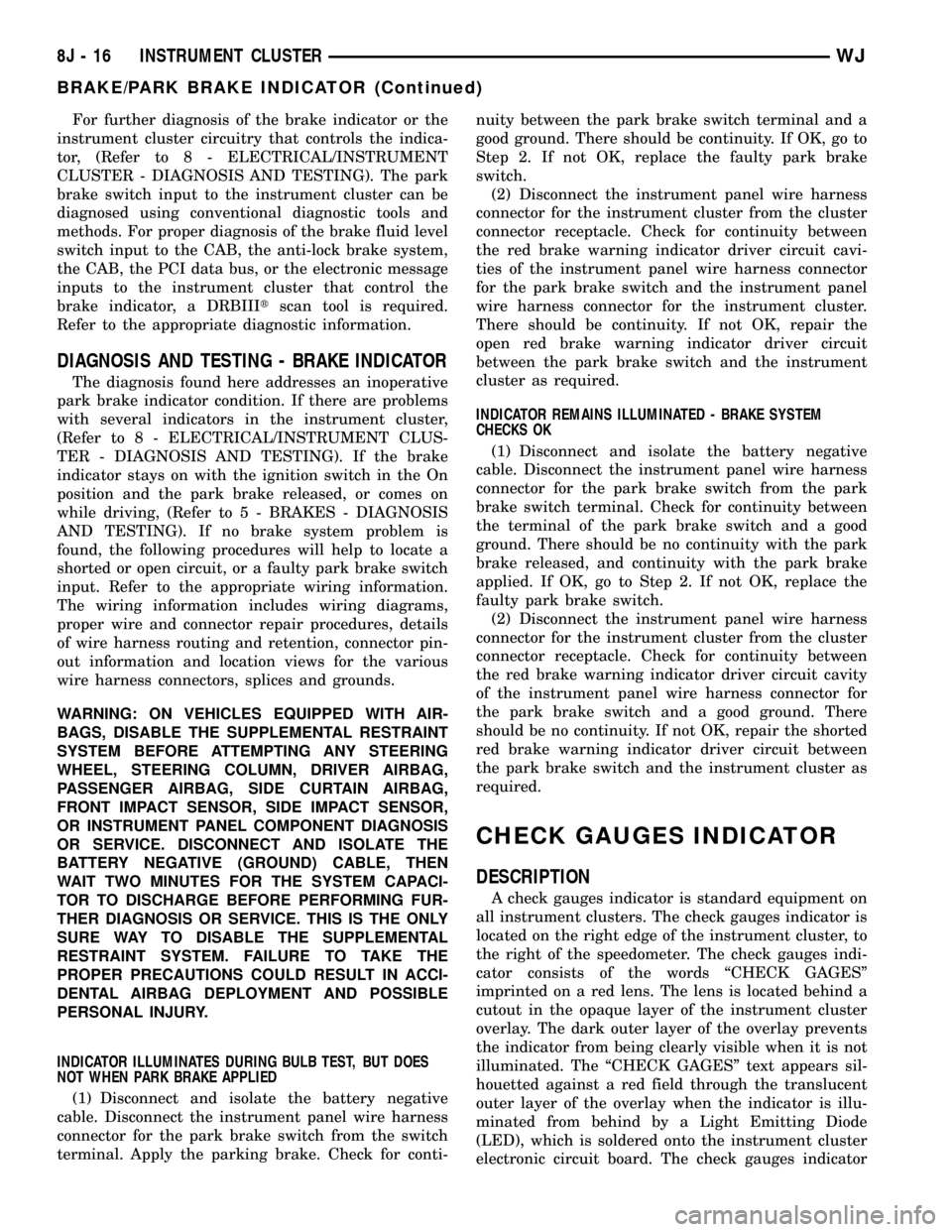
For further diagnosis of the brake indicator or the
instrument cluster circuitry that controls the indica-
tor, (Refer to 8 - ELECTRICAL/INSTRUMENT
CLUSTER - DIAGNOSIS AND TESTING). The park
brake switch input to the instrument cluster can be
diagnosed using conventional diagnostic tools and
methods. For proper diagnosis of the brake fluid level
switch input to the CAB, the anti-lock brake system,
the CAB, the PCI data bus, or the electronic message
inputs to the instrument cluster that control the
brake indicator, a DRBIIItscan tool is required.
Refer to the appropriate diagnostic information.
DIAGNOSIS AND TESTING - BRAKE INDICATOR
The diagnosis found here addresses an inoperative
park brake indicator condition. If there are problems
with several indicators in the instrument cluster,
(Refer to 8 - ELECTRICAL/INSTRUMENT CLUS-
TER - DIAGNOSIS AND TESTING). If the brake
indicator stays on with the ignition switch in the On
position and the park brake released, or comes on
while driving, (Refer to 5 - BRAKES - DIAGNOSIS
AND TESTING). If no brake system problem is
found, the following procedures will help to locate a
shorted or open circuit, or a faulty park brake switch
input. Refer to the appropriate wiring information.
The wiring information includes wiring diagrams,
proper wire and connector repair procedures, details
of wire harness routing and retention, connector pin-
out information and location views for the various
wire harness connectors, splices and grounds.
WARNING: ON VEHICLES EQUIPPED WITH AIR-
BAGS, DISABLE THE SUPPLEMENTAL RESTRAINT
SYSTEM BEFORE ATTEMPTING ANY STEERING
WHEEL, STEERING COLUMN, DRIVER AIRBAG,
PASSENGER AIRBAG, SIDE CURTAIN AIRBAG,
FRONT IMPACT SENSOR, SIDE IMPACT SENSOR,
OR INSTRUMENT PANEL COMPONENT DIAGNOSIS
OR SERVICE. DISCONNECT AND ISOLATE THE
BATTERY NEGATIVE (GROUND) CABLE, THEN
WAIT TWO MINUTES FOR THE SYSTEM CAPACI-
TOR TO DISCHARGE BEFORE PERFORMING FUR-
THER DIAGNOSIS OR SERVICE. THIS IS THE ONLY
SURE WAY TO DISABLE THE SUPPLEMENTAL
RESTRAINT SYSTEM. FAILURE TO TAKE THE
PROPER PRECAUTIONS COULD RESULT IN ACCI-
DENTAL AIRBAG DEPLOYMENT AND POSSIBLE
PERSONAL INJURY.
INDICATOR ILLUMINATES DURING BULB TEST, BUT DOES
NOT WHEN PARK BRAKE APPLIED
(1) Disconnect and isolate the battery negative
cable. Disconnect the instrument panel wire harness
connector for the park brake switch from the switch
terminal. Apply the parking brake. Check for conti-nuity between the park brake switch terminal and a
good ground. There should be continuity. If OK, go to
Step 2. If not OK, replace the faulty park brake
switch.
(2) Disconnect the instrument panel wire harness
connector for the instrument cluster from the cluster
connector receptacle. Check for continuity between
the red brake warning indicator driver circuit cavi-
ties of the instrument panel wire harness connector
for the park brake switch and the instrument panel
wire harness connector for the instrument cluster.
There should be continuity. If not OK, repair the
open red brake warning indicator driver circuit
between the park brake switch and the instrument
cluster as required.
INDICATOR REMAINS ILLUMINATED - BRAKE SYSTEM
CHECKS OK
(1) Disconnect and isolate the battery negative
cable. Disconnect the instrument panel wire harness
connector for the park brake switch from the park
brake switch terminal. Check for continuity between
the terminal of the park brake switch and a good
ground. There should be no continuity with the park
brake released, and continuity with the park brake
applied. If OK, go to Step 2. If not OK, replace the
faulty park brake switch.
(2) Disconnect the instrument panel wire harness
connector for the instrument cluster from the cluster
connector receptacle. Check for continuity between
the red brake warning indicator driver circuit cavity
of the instrument panel wire harness connector for
the park brake switch and a good ground. There
should be no continuity. If not OK, repair the shorted
red brake warning indicator driver circuit between
the park brake switch and the instrument cluster as
required.
CHECK GAUGES INDICATOR
DESCRIPTION
A check gauges indicator is standard equipment on
all instrument clusters. The check gauges indicator is
located on the right edge of the instrument cluster, to
the right of the speedometer. The check gauges indi-
cator consists of the words ªCHECK GAGESº
imprinted on a red lens. The lens is located behind a
cutout in the opaque layer of the instrument cluster
overlay. The dark outer layer of the overlay prevents
the indicator from being clearly visible when it is not
illuminated. The ªCHECK GAGESº text appears sil-
houetted against a red field through the translucent
outer layer of the overlay when the indicator is illu-
minated from behind by a Light Emitting Diode
(LED), which is soldered onto the instrument cluster
electronic circuit board. The check gauges indicator
8J - 16 INSTRUMENT CLUSTERWJ
BRAKE/PARK BRAKE INDICATOR (Continued)