pressure testing JEEP GRAND CHEROKEE 2002 WJ / 2.G Owner's Manual
[x] Cancel search | Manufacturer: JEEP, Model Year: 2002, Model line: GRAND CHEROKEE, Model: JEEP GRAND CHEROKEE 2002 WJ / 2.GPages: 2199, PDF Size: 76.01 MB
Page 277 of 2199
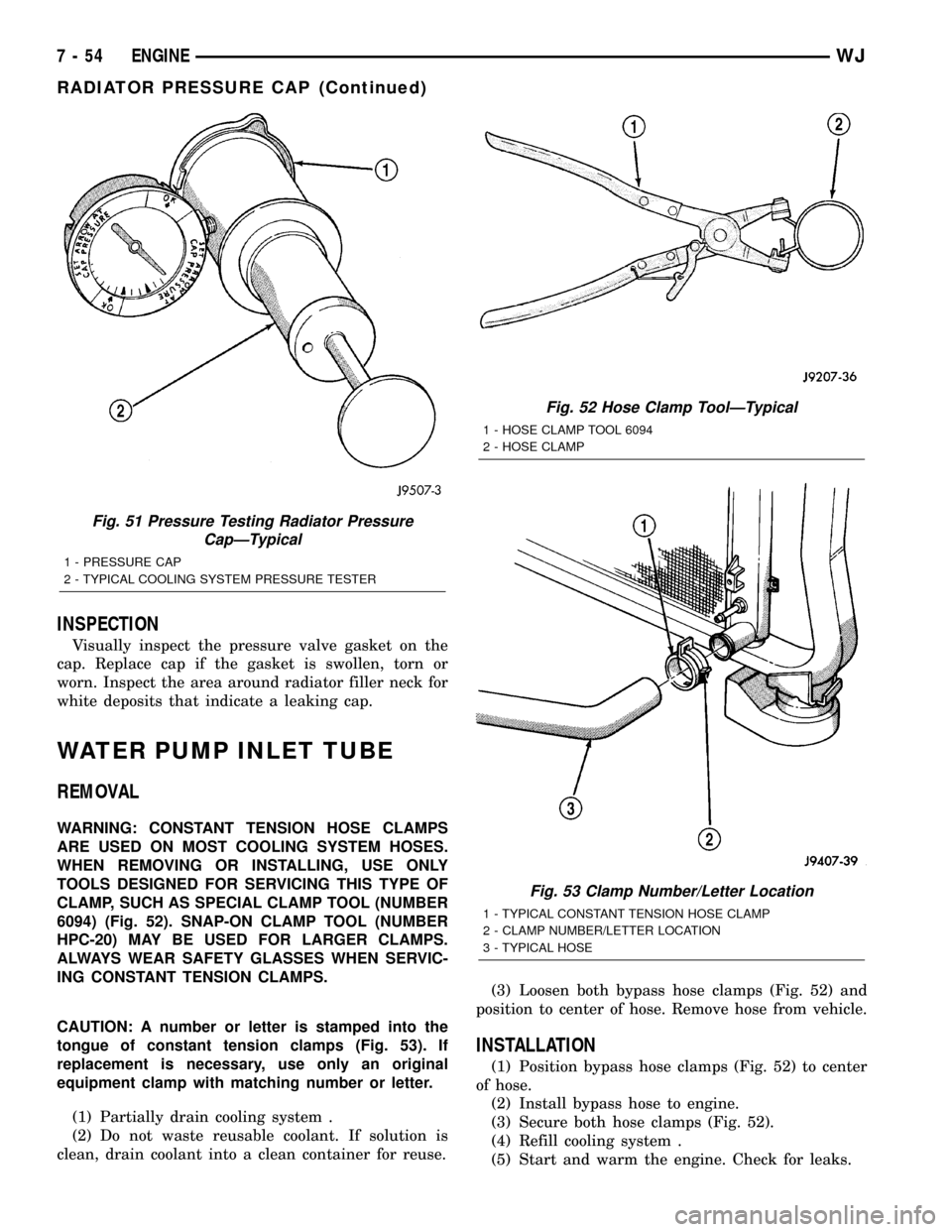
INSPECTION
Visually inspect the pressure valve gasket on the
cap. Replace cap if the gasket is swollen, torn or
worn. Inspect the area around radiator filler neck for
white deposits that indicate a leaking cap.
WATER PUMP INLET TUBE
REMOVAL
WARNING: CONSTANT TENSION HOSE CLAMPS
ARE USED ON MOST COOLING SYSTEM HOSES.
WHEN REMOVING OR INSTALLING, USE ONLY
TOOLS DESIGNED FOR SERVICING THIS TYPE OF
CLAMP, SUCH AS SPECIAL CLAMP TOOL (NUMBER
6094) (Fig. 52). SNAP-ON CLAMP TOOL (NUMBER
HPC-20) MAY BE USED FOR LARGER CLAMPS.
ALWAYS WEAR SAFETY GLASSES WHEN SERVIC-
ING CONSTANT TENSION CLAMPS.
CAUTION: A number or letter is stamped into the
tongue of constant tension clamps (Fig. 53). If
replacement is necessary, use only an original
equipment clamp with matching number or letter.
(1) Partially drain cooling system .
(2) Do not waste reusable coolant. If solution is
clean, drain coolant into a clean container for reuse.(3) Loosen both bypass hose clamps (Fig. 52) and
position to center of hose. Remove hose from vehicle.
INSTALLATION
(1) Position bypass hose clamps (Fig. 52) to center
of hose.
(2) Install bypass hose to engine.
(3) Secure both hose clamps (Fig. 52).
(4) Refill cooling system .
(5) Start and warm the engine. Check for leaks.
Fig. 51 Pressure Testing Radiator Pressure
CapÐTypical
1 - PRESSURE CAP
2 - TYPICAL COOLING SYSTEM PRESSURE TESTER
Fig. 52 Hose Clamp ToolÐTypical
1 - HOSE CLAMP TOOL 6094
2 - HOSE CLAMP
Fig. 53 Clamp Number/Letter Location
1 - TYPICAL CONSTANT TENSION HOSE CLAMP
2 - CLAMP NUMBER/LETTER LOCATION
3 - TYPICAL HOSE
7 - 54 ENGINEWJ
RADIATOR PRESSURE CAP (Continued)
Page 355 of 2199
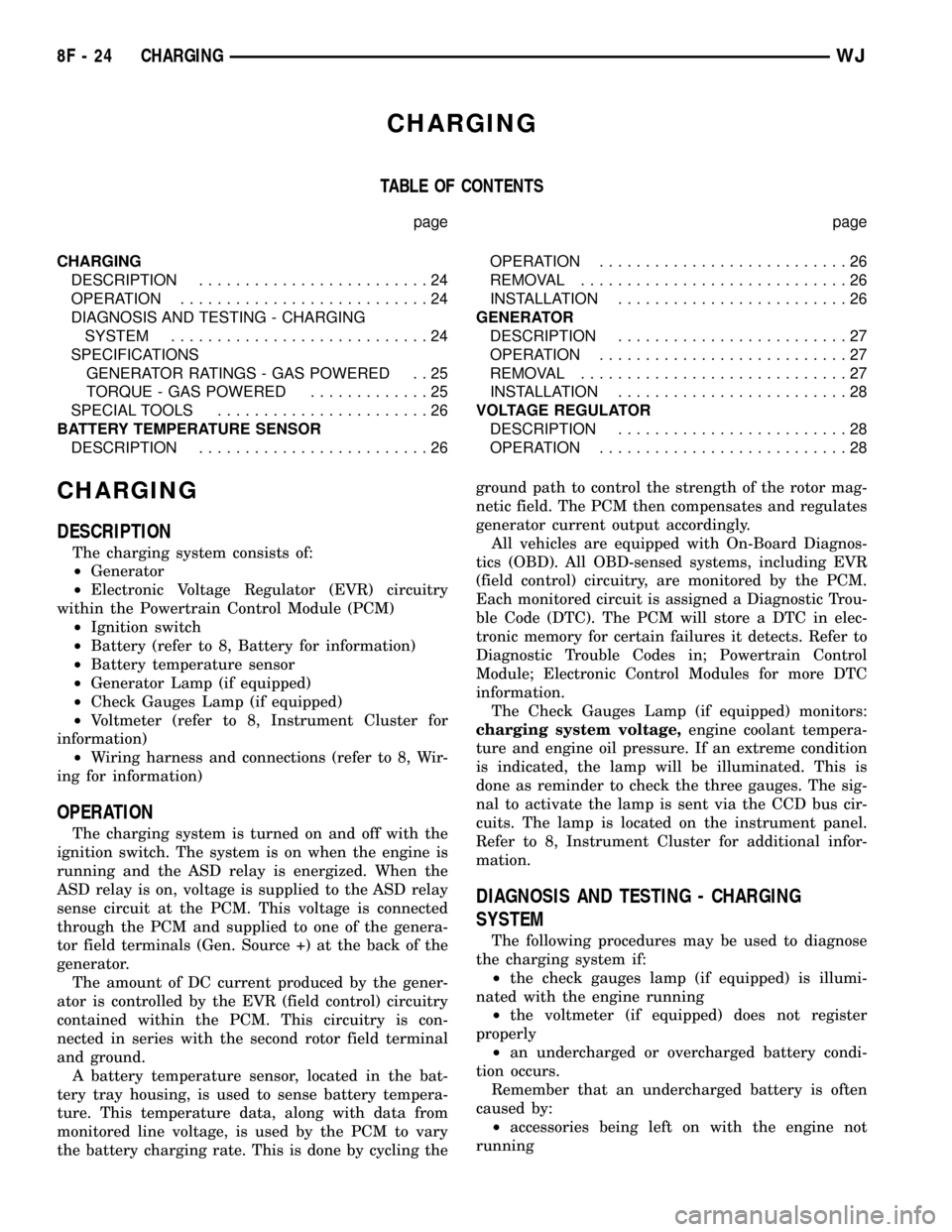
CHARGING
TABLE OF CONTENTS
page page
CHARGING
DESCRIPTION.........................24
OPERATION...........................24
DIAGNOSIS AND TESTING - CHARGING
SYSTEM............................24
SPECIFICATIONS
GENERATOR RATINGS - GAS POWERED . . 25
TORQUE - GAS POWERED.............25
SPECIAL TOOLS.......................26
BATTERY TEMPERATURE SENSOR
DESCRIPTION.........................26OPERATION...........................26
REMOVAL.............................26
INSTALLATION.........................26
GENERATOR
DESCRIPTION.........................27
OPERATION...........................27
REMOVAL.............................27
INSTALLATION.........................28
VOLTAGE REGULATOR
DESCRIPTION.........................28
OPERATION...........................28
CHARGING
DESCRIPTION
The charging system consists of:
²Generator
²Electronic Voltage Regulator (EVR) circuitry
within the Powertrain Control Module (PCM)
²Ignition switch
²Battery (refer to 8, Battery for information)
²Battery temperature sensor
²Generator Lamp (if equipped)
²Check Gauges Lamp (if equipped)
²Voltmeter (refer to 8, Instrument Cluster for
information)
²Wiring harness and connections (refer to 8, Wir-
ing for information)
OPERATION
The charging system is turned on and off with the
ignition switch. The system is on when the engine is
running and the ASD relay is energized. When the
ASD relay is on, voltage is supplied to the ASD relay
sense circuit at the PCM. This voltage is connected
through the PCM and supplied to one of the genera-
tor field terminals (Gen. Source +) at the back of the
generator.
The amount of DC current produced by the gener-
ator is controlled by the EVR (field control) circuitry
contained within the PCM. This circuitry is con-
nected in series with the second rotor field terminal
and ground.
A battery temperature sensor, located in the bat-
tery tray housing, is used to sense battery tempera-
ture. This temperature data, along with data from
monitored line voltage, is used by the PCM to vary
the battery charging rate. This is done by cycling theground path to control the strength of the rotor mag-
netic field. The PCM then compensates and regulates
generator current output accordingly.
All vehicles are equipped with On-Board Diagnos-
tics (OBD). All OBD-sensed systems, including EVR
(field control) circuitry, are monitored by the PCM.
Each monitored circuit is assigned a Diagnostic Trou-
ble Code (DTC). The PCM will store a DTC in elec-
tronic memory for certain failures it detects. Refer to
Diagnostic Trouble Codes in; Powertrain Control
Module; Electronic Control Modules for more DTC
information.
The Check Gauges Lamp (if equipped) monitors:
charging system voltage,engine coolant tempera-
ture and engine oil pressure. If an extreme condition
is indicated, the lamp will be illuminated. This is
done as reminder to check the three gauges. The sig-
nal to activate the lamp is sent via the CCD bus cir-
cuits. The lamp is located on the instrument panel.
Refer to 8, Instrument Cluster for additional infor-
mation.
DIAGNOSIS AND TESTING - CHARGING
SYSTEM
The following procedures may be used to diagnose
the charging system if:
²the check gauges lamp (if equipped) is illumi-
nated with the engine running
²the voltmeter (if equipped) does not register
properly
²an undercharged or overcharged battery condi-
tion occurs.
Remember that an undercharged battery is often
caused by:
²accessories being left on with the engine not
running
8F - 24 CHARGINGWJ
Page 369 of 2199
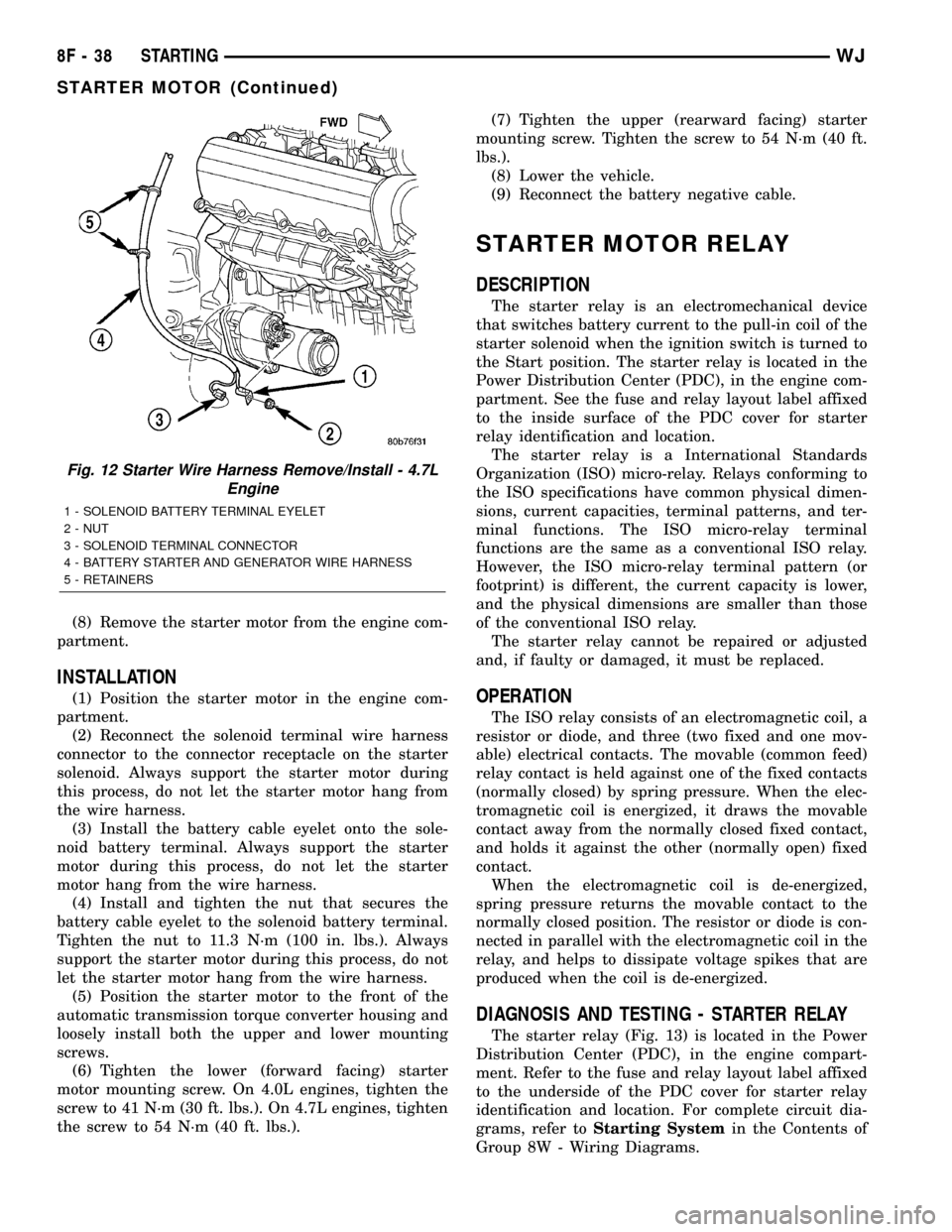
(8) Remove the starter motor from the engine com-
partment.
INSTALLATION
(1) Position the starter motor in the engine com-
partment.
(2) Reconnect the solenoid terminal wire harness
connector to the connector receptacle on the starter
solenoid. Always support the starter motor during
this process, do not let the starter motor hang from
the wire harness.
(3) Install the battery cable eyelet onto the sole-
noid battery terminal. Always support the starter
motor during this process, do not let the starter
motor hang from the wire harness.
(4) Install and tighten the nut that secures the
battery cable eyelet to the solenoid battery terminal.
Tighten the nut to 11.3 N´m (100 in. lbs.). Always
support the starter motor during this process, do not
let the starter motor hang from the wire harness.
(5) Position the starter motor to the front of the
automatic transmission torque converter housing and
loosely install both the upper and lower mounting
screws.
(6) Tighten the lower (forward facing) starter
motor mounting screw. On 4.0L engines, tighten the
screw to 41 N´m (30 ft. lbs.). On 4.7L engines, tighten
the screw to 54 N´m (40 ft. lbs.).(7) Tighten the upper (rearward facing) starter
mounting screw. Tighten the screw to 54 N´m (40 ft.
lbs.).
(8) Lower the vehicle.
(9) Reconnect the battery negative cable.
STARTER MOTOR RELAY
DESCRIPTION
The starter relay is an electromechanical device
that switches battery current to the pull-in coil of the
starter solenoid when the ignition switch is turned to
the Start position. The starter relay is located in the
Power Distribution Center (PDC), in the engine com-
partment. See the fuse and relay layout label affixed
to the inside surface of the PDC cover for starter
relay identification and location.
The starter relay is a International Standards
Organization (ISO) micro-relay. Relays conforming to
the ISO specifications have common physical dimen-
sions, current capacities, terminal patterns, and ter-
minal functions. The ISO micro-relay terminal
functions are the same as a conventional ISO relay.
However, the ISO micro-relay terminal pattern (or
footprint) is different, the current capacity is lower,
and the physical dimensions are smaller than those
of the conventional ISO relay.
The starter relay cannot be repaired or adjusted
and, if faulty or damaged, it must be replaced.
OPERATION
The ISO relay consists of an electromagnetic coil, a
resistor or diode, and three (two fixed and one mov-
able) electrical contacts. The movable (common feed)
relay contact is held against one of the fixed contacts
(normally closed) by spring pressure. When the elec-
tromagnetic coil is energized, it draws the movable
contact away from the normally closed fixed contact,
and holds it against the other (normally open) fixed
contact.
When the electromagnetic coil is de-energized,
spring pressure returns the movable contact to the
normally closed position. The resistor or diode is con-
nected in parallel with the electromagnetic coil in the
relay, and helps to dissipate voltage spikes that are
produced when the coil is de-energized.
DIAGNOSIS AND TESTING - STARTER RELAY
The starter relay (Fig. 13) is located in the Power
Distribution Center (PDC), in the engine compart-
ment. Refer to the fuse and relay layout label affixed
to the underside of the PDC cover for starter relay
identification and location. For complete circuit dia-
grams, refer toStarting Systemin the Contents of
Group 8W - Wiring Diagrams.
Fig. 12 Starter Wire Harness Remove/Install - 4.7L
Engine
1 - SOLENOID BATTERY TERMINAL EYELET
2 - NUT
3 - SOLENOID TERMINAL CONNECTOR
4 - BATTERY STARTER AND GENERATOR WIRE HARNESS
5 - RETAINERS
8F - 38 STARTINGWJ
STARTER MOTOR (Continued)
Page 376 of 2199
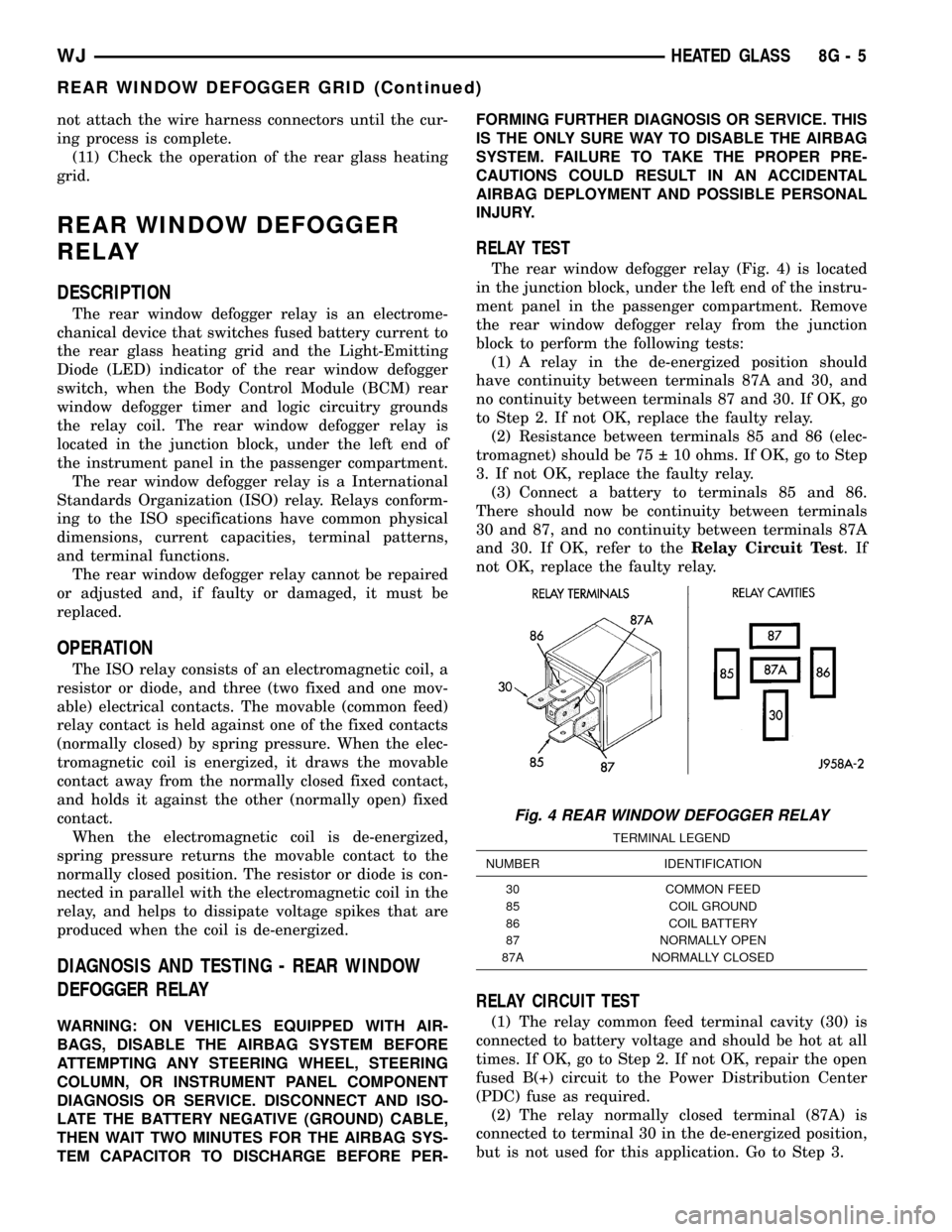
not attach the wire harness connectors until the cur-
ing process is complete.
(11) Check the operation of the rear glass heating
grid.
REAR WINDOW DEFOGGER
RELAY
DESCRIPTION
The rear window defogger relay is an electrome-
chanical device that switches fused battery current to
the rear glass heating grid and the Light-Emitting
Diode (LED) indicator of the rear window defogger
switch, when the Body Control Module (BCM) rear
window defogger timer and logic circuitry grounds
the relay coil. The rear window defogger relay is
located in the junction block, under the left end of
the instrument panel in the passenger compartment.
The rear window defogger relay is a International
Standards Organization (ISO) relay. Relays conform-
ing to the ISO specifications have common physical
dimensions, current capacities, terminal patterns,
and terminal functions.
The rear window defogger relay cannot be repaired
or adjusted and, if faulty or damaged, it must be
replaced.
OPERATION
The ISO relay consists of an electromagnetic coil, a
resistor or diode, and three (two fixed and one mov-
able) electrical contacts. The movable (common feed)
relay contact is held against one of the fixed contacts
(normally closed) by spring pressure. When the elec-
tromagnetic coil is energized, it draws the movable
contact away from the normally closed fixed contact,
and holds it against the other (normally open) fixed
contact.
When the electromagnetic coil is de-energized,
spring pressure returns the movable contact to the
normally closed position. The resistor or diode is con-
nected in parallel with the electromagnetic coil in the
relay, and helps to dissipate voltage spikes that are
produced when the coil is de-energized.
DIAGNOSIS AND TESTING - REAR WINDOW
DEFOGGER RELAY
WARNING: ON VEHICLES EQUIPPED WITH AIR-
BAGS, DISABLE THE AIRBAG SYSTEM BEFORE
ATTEMPTING ANY STEERING WHEEL, STEERING
COLUMN, OR INSTRUMENT PANEL COMPONENT
DIAGNOSIS OR SERVICE. DISCONNECT AND ISO-
LATE THE BATTERY NEGATIVE (GROUND) CABLE,
THEN WAIT TWO MINUTES FOR THE AIRBAG SYS-
TEM CAPACITOR TO DISCHARGE BEFORE PER-FORMING FURTHER DIAGNOSIS OR SERVICE. THIS
IS THE ONLY SURE WAY TO DISABLE THE AIRBAG
SYSTEM. FAILURE TO TAKE THE PROPER PRE-
CAUTIONS COULD RESULT IN AN ACCIDENTAL
AIRBAG DEPLOYMENT AND POSSIBLE PERSONAL
INJURY.
RELAY TEST
The rear window defogger relay (Fig. 4) is located
in the junction block, under the left end of the instru-
ment panel in the passenger compartment. Remove
the rear window defogger relay from the junction
block to perform the following tests:
(1) A relay in the de-energized position should
have continuity between terminals 87A and 30, and
no continuity between terminals 87 and 30. If OK, go
to Step 2. If not OK, replace the faulty relay.
(2) Resistance between terminals 85 and 86 (elec-
tromagnet) should be 75 10 ohms. If OK, go to Step
3. If not OK, replace the faulty relay.
(3) Connect a battery to terminals 85 and 86.
There should now be continuity between terminals
30 and 87, and no continuity between terminals 87A
and 30. If OK, refer to theRelay Circuit Test.If
not OK, replace the faulty relay.
RELAY CIRCUIT TEST
(1) The relay common feed terminal cavity (30) is
connected to battery voltage and should be hot at all
times. If OK, go to Step 2. If not OK, repair the open
fused B(+) circuit to the Power Distribution Center
(PDC) fuse as required.
(2) The relay normally closed terminal (87A) is
connected to terminal 30 in the de-energized position,
but is not used for this application. Go to Step 3.
Fig. 4 REAR WINDOW DEFOGGER RELAY
TERMINAL LEGEND
NUMBER IDENTIFICATION
30 COMMON FEED
85 COIL GROUND
86 COIL BATTERY
87 NORMALLY OPEN
87A NORMALLY CLOSED
WJHEATED GLASS 8G - 5
REAR WINDOW DEFOGGER GRID (Continued)
Page 393 of 2199
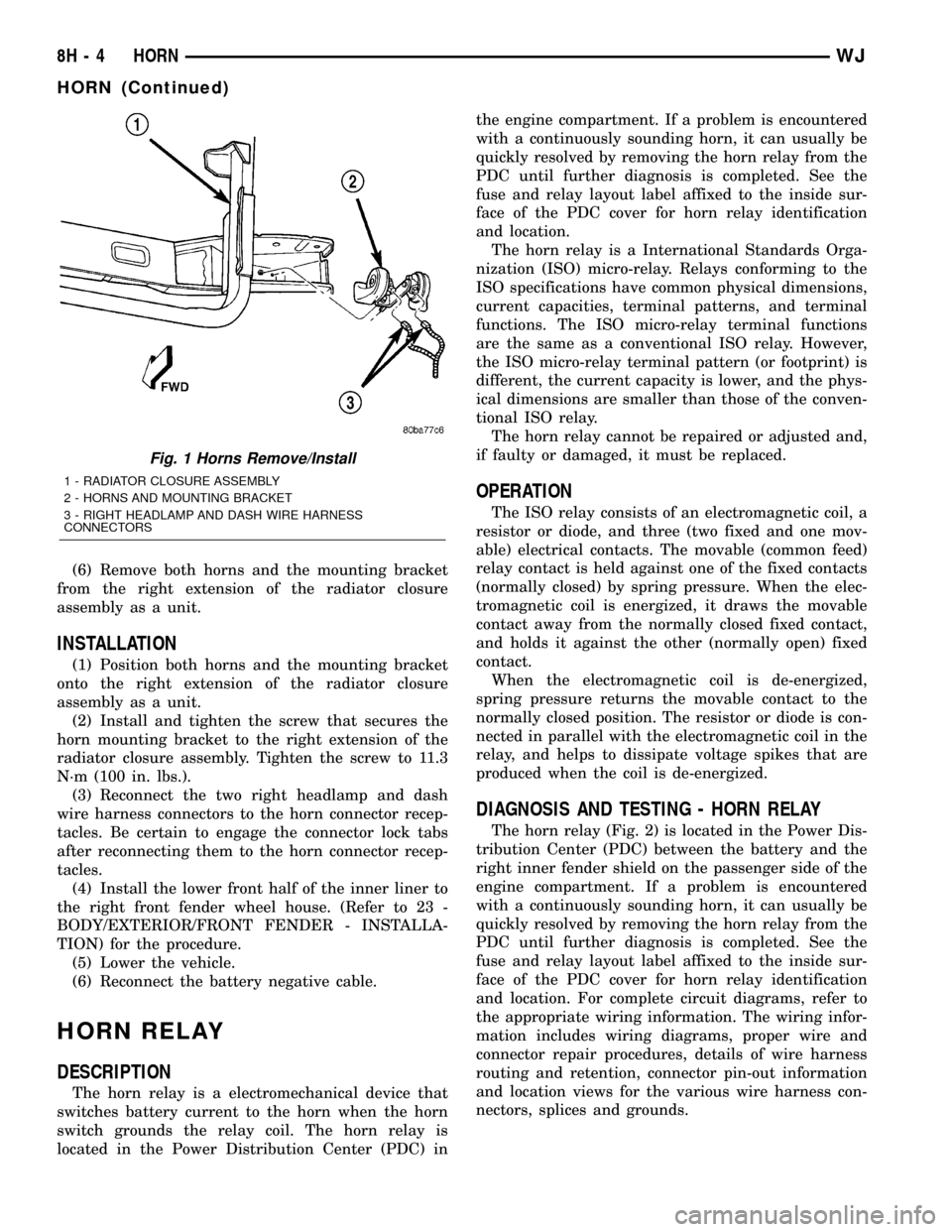
(6) Remove both horns and the mounting bracket
from the right extension of the radiator closure
assembly as a unit.
INSTALLATION
(1) Position both horns and the mounting bracket
onto the right extension of the radiator closure
assembly as a unit.
(2) Install and tighten the screw that secures the
horn mounting bracket to the right extension of the
radiator closure assembly. Tighten the screw to 11.3
N´m (100 in. lbs.).
(3) Reconnect the two right headlamp and dash
wire harness connectors to the horn connector recep-
tacles. Be certain to engage the connector lock tabs
after reconnecting them to the horn connector recep-
tacles.
(4) Install the lower front half of the inner liner to
the right front fender wheel house. (Refer to 23 -
BODY/EXTERIOR/FRONT FENDER - INSTALLA-
TION) for the procedure.
(5) Lower the vehicle.
(6) Reconnect the battery negative cable.
HORN RELAY
DESCRIPTION
The horn relay is a electromechanical device that
switches battery current to the horn when the horn
switch grounds the relay coil. The horn relay is
located in the Power Distribution Center (PDC) inthe engine compartment. If a problem is encountered
with a continuously sounding horn, it can usually be
quickly resolved by removing the horn relay from the
PDC until further diagnosis is completed. See the
fuse and relay layout label affixed to the inside sur-
face of the PDC cover for horn relay identification
and location.
The horn relay is a International Standards Orga-
nization (ISO) micro-relay. Relays conforming to the
ISO specifications have common physical dimensions,
current capacities, terminal patterns, and terminal
functions. The ISO micro-relay terminal functions
are the same as a conventional ISO relay. However,
the ISO micro-relay terminal pattern (or footprint) is
different, the current capacity is lower, and the phys-
ical dimensions are smaller than those of the conven-
tional ISO relay.
The horn relay cannot be repaired or adjusted and,
if faulty or damaged, it must be replaced.
OPERATION
The ISO relay consists of an electromagnetic coil, a
resistor or diode, and three (two fixed and one mov-
able) electrical contacts. The movable (common feed)
relay contact is held against one of the fixed contacts
(normally closed) by spring pressure. When the elec-
tromagnetic coil is energized, it draws the movable
contact away from the normally closed fixed contact,
and holds it against the other (normally open) fixed
contact.
When the electromagnetic coil is de-energized,
spring pressure returns the movable contact to the
normally closed position. The resistor or diode is con-
nected in parallel with the electromagnetic coil in the
relay, and helps to dissipate voltage spikes that are
produced when the coil is de-energized.
DIAGNOSIS AND TESTING - HORN RELAY
The horn relay (Fig. 2) is located in the Power Dis-
tribution Center (PDC) between the battery and the
right inner fender shield on the passenger side of the
engine compartment. If a problem is encountered
with a continuously sounding horn, it can usually be
quickly resolved by removing the horn relay from the
PDC until further diagnosis is completed. See the
fuse and relay layout label affixed to the inside sur-
face of the PDC cover for horn relay identification
and location. For complete circuit diagrams, refer to
the appropriate wiring information. The wiring infor-
mation includes wiring diagrams, proper wire and
connector repair procedures, details of wire harness
routing and retention, connector pin-out information
and location views for the various wire harness con-
nectors, splices and grounds.
Fig. 1 Horns Remove/Install
1 - RADIATOR CLOSURE ASSEMBLY
2 - HORNS AND MOUNTING BRACKET
3 - RIGHT HEADLAMP AND DASH WIRE HARNESS
CONNECTORS
8H - 4 HORNWJ
HORN (Continued)
Page 416 of 2199
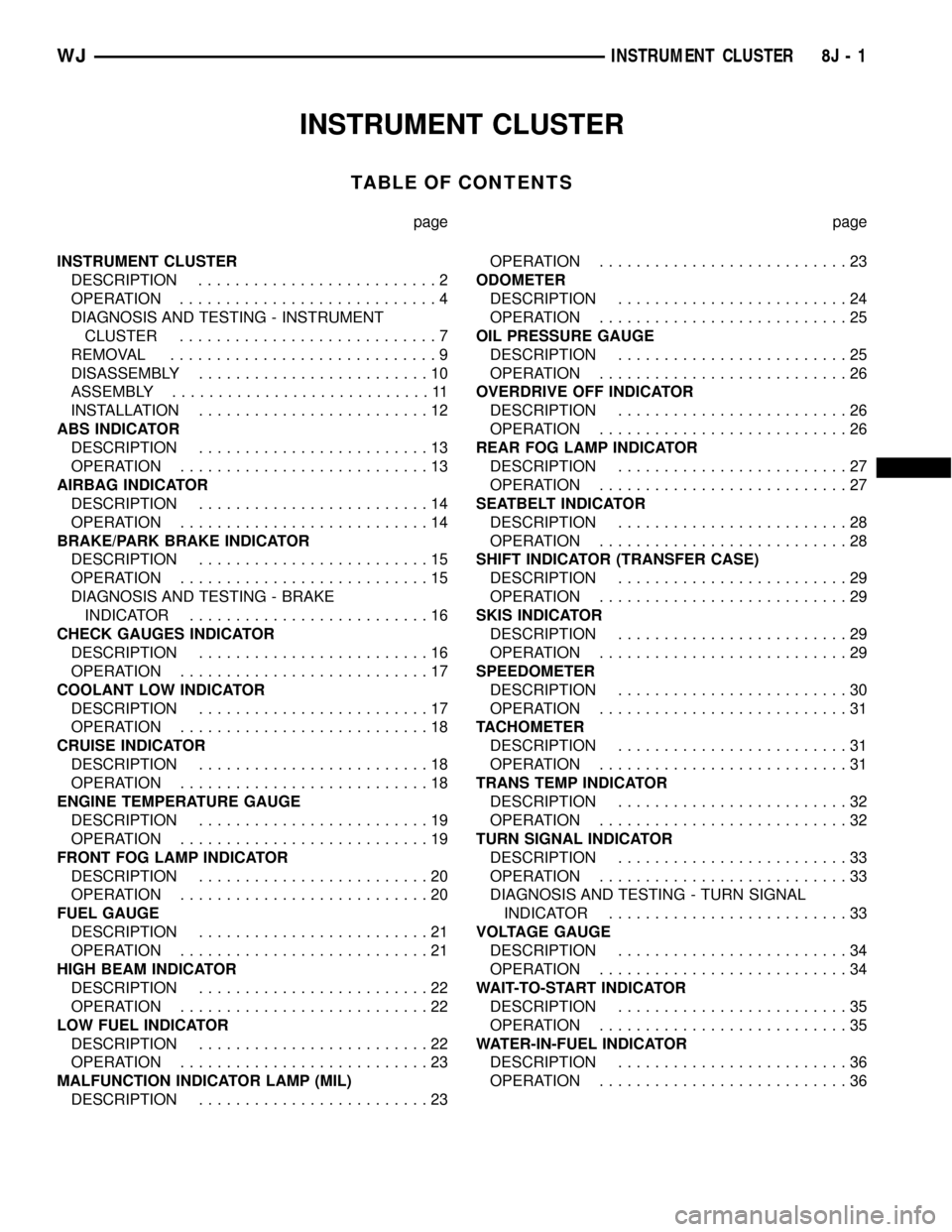
INSTRUMENT CLUSTER
TABLE OF CONTENTS
page page
INSTRUMENT CLUSTER
DESCRIPTION..........................2
OPERATION............................4
DIAGNOSIS AND TESTING - INSTRUMENT
CLUSTER............................7
REMOVAL.............................9
DISASSEMBLY.........................10
ASSEMBLY............................11
INSTALLATION.........................12
ABS INDICATOR
DESCRIPTION.........................13
OPERATION...........................13
AIRBAG INDICATOR
DESCRIPTION.........................14
OPERATION...........................14
BRAKE/PARK BRAKE INDICATOR
DESCRIPTION.........................15
OPERATION...........................15
DIAGNOSIS AND TESTING - BRAKE
INDICATOR..........................16
CHECK GAUGES INDICATOR
DESCRIPTION.........................16
OPERATION...........................17
COOLANT LOW INDICATOR
DESCRIPTION.........................17
OPERATION...........................18
CRUISE INDICATOR
DESCRIPTION.........................18
OPERATION...........................18
ENGINE TEMPERATURE GAUGE
DESCRIPTION.........................19
OPERATION...........................19
FRONT FOG LAMP INDICATOR
DESCRIPTION.........................20
OPERATION...........................20
FUEL GAUGE
DESCRIPTION.........................21
OPERATION...........................21
HIGH BEAM INDICATOR
DESCRIPTION.........................22
OPERATION...........................22
LOW FUEL INDICATOR
DESCRIPTION.........................22
OPERATION...........................23
MALFUNCTION INDICATOR LAMP (MIL)
DESCRIPTION.........................23OPERATION...........................23
ODOMETER
DESCRIPTION.........................24
OPERATION...........................25
OIL PRESSURE GAUGE
DESCRIPTION.........................25
OPERATION...........................26
OVERDRIVE OFF INDICATOR
DESCRIPTION.........................26
OPERATION...........................26
REAR FOG LAMP INDICATOR
DESCRIPTION.........................27
OPERATION...........................27
SEATBELT INDICATOR
DESCRIPTION.........................28
OPERATION...........................28
SHIFT INDICATOR (TRANSFER CASE)
DESCRIPTION.........................29
OPERATION...........................29
SKIS INDICATOR
DESCRIPTION.........................29
OPERATION...........................29
SPEEDOMETER
DESCRIPTION.........................30
OPERATION...........................31
TACHOMETER
DESCRIPTION.........................31
OPERATION...........................31
TRANS TEMP INDICATOR
DESCRIPTION.........................32
OPERATION...........................32
TURN SIGNAL INDICATOR
DESCRIPTION.........................33
OPERATION...........................33
DIAGNOSIS AND TESTING - TURN SIGNAL
INDICATOR..........................33
VOLTAGE GAUGE
DESCRIPTION.........................34
OPERATION...........................34
WAIT-TO-START INDICATOR
DESCRIPTION.........................35
OPERATION...........................35
WATER-IN-FUEL INDICATOR
DESCRIPTION.........................36
OPERATION...........................36
WJINSTRUMENT CLUSTER 8J - 1
Page 432 of 2199
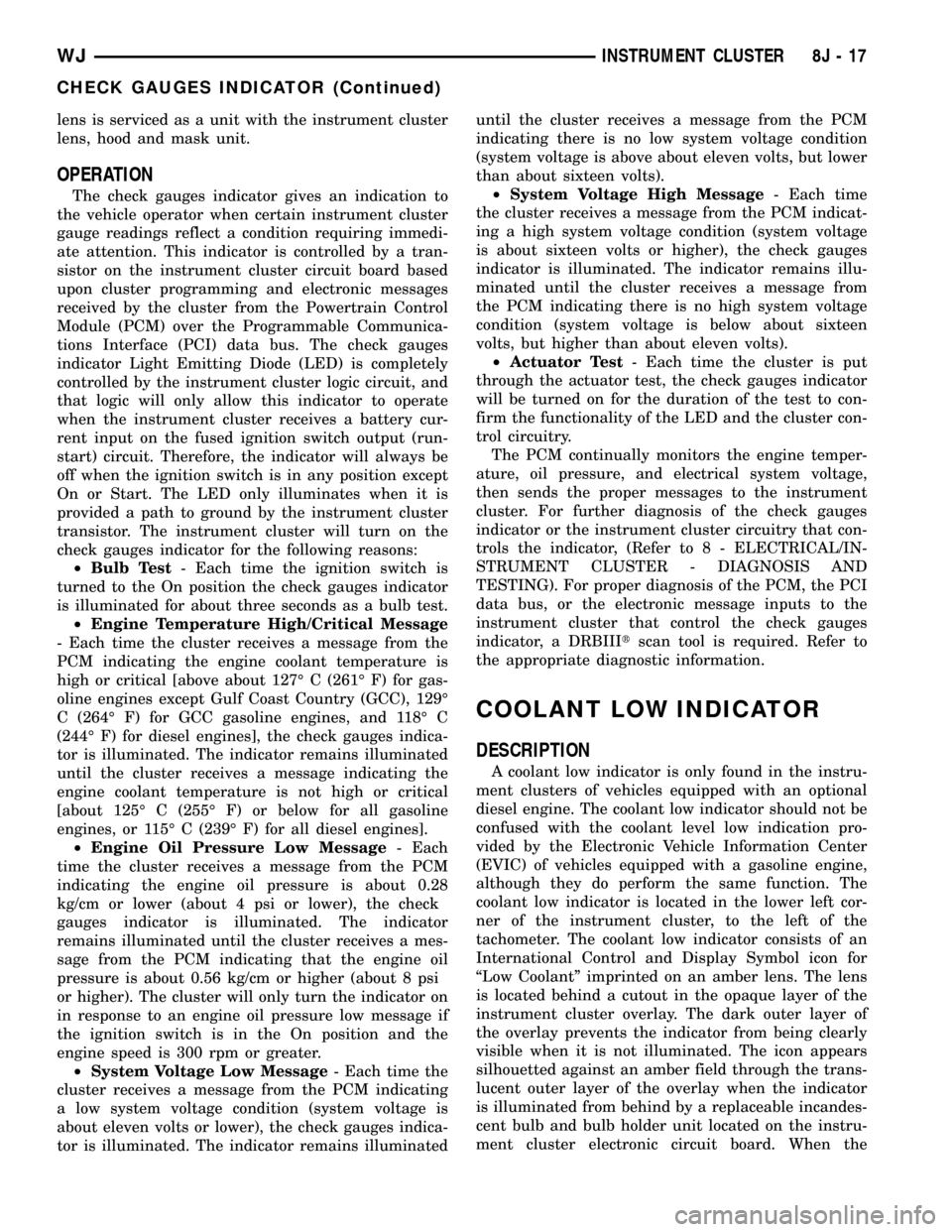
lens is serviced as a unit with the instrument cluster
lens, hood and mask unit.
OPERATION
The check gauges indicator gives an indication to
the vehicle operator when certain instrument cluster
gauge readings reflect a condition requiring immedi-
ate attention. This indicator is controlled by a tran-
sistor on the instrument cluster circuit board based
upon cluster programming and electronic messages
received by the cluster from the Powertrain Control
Module (PCM) over the Programmable Communica-
tions Interface (PCI) data bus. The check gauges
indicator Light Emitting Diode (LED) is completely
controlled by the instrument cluster logic circuit, and
that logic will only allow this indicator to operate
when the instrument cluster receives a battery cur-
rent input on the fused ignition switch output (run-
start) circuit. Therefore, the indicator will always be
off when the ignition switch is in any position except
On or Start. The LED only illuminates when it is
provided a path to ground by the instrument cluster
transistor. The instrument cluster will turn on the
check gauges indicator for the following reasons:
²Bulb Test- Each time the ignition switch is
turned to the On position the check gauges indicator
is illuminated for about three seconds as a bulb test.
²Engine Temperature High/Critical Message
- Each time the cluster receives a message from the
PCM indicating the engine coolant temperature is
high or critical [above about 127É C (261É F) for gas-
oline engines except Gulf Coast Country (GCC), 129É
C (264É F) for GCC gasoline engines, and 118É C
(244É F) for diesel engines], the check gauges indica-
tor is illuminated. The indicator remains illuminated
until the cluster receives a message indicating the
engine coolant temperature is not high or critical
[about 125É C (255É F) or below for all gasoline
engines, or 115É C (239É F) for all diesel engines].
²Engine Oil Pressure Low Message- Each
time the cluster receives a message from the PCM
indicating the engine oil pressure is about 0.28
kg/cm or lower (about 4 psi or lower), the check
gauges indicator is illuminated. The indicator
remains illuminated until the cluster receives a mes-
sage from the PCM indicating that the engine oil
pressure is about 0.56 kg/cm or higher (about 8 psi
or higher). The cluster will only turn the indicator on
in response to an engine oil pressure low message if
the ignition switch is in the On position and the
engine speed is 300 rpm or greater.
²System Voltage Low Message- Each time the
cluster receives a message from the PCM indicating
a low system voltage condition (system voltage is
about eleven volts or lower), the check gauges indica-
tor is illuminated. The indicator remains illuminateduntil the cluster receives a message from the PCM
indicating there is no low system voltage condition
(system voltage is above about eleven volts, but lower
than about sixteen volts).
²System Voltage High Message- Each time
the cluster receives a message from the PCM indicat-
ing a high system voltage condition (system voltage
is about sixteen volts or higher), the check gauges
indicator is illuminated. The indicator remains illu-
minated until the cluster receives a message from
the PCM indicating there is no high system voltage
condition (system voltage is below about sixteen
volts, but higher than about eleven volts).
²Actuator Test- Each time the cluster is put
through the actuator test, the check gauges indicator
will be turned on for the duration of the test to con-
firm the functionality of the LED and the cluster con-
trol circuitry.
The PCM continually monitors the engine temper-
ature, oil pressure, and electrical system voltage,
then sends the proper messages to the instrument
cluster. For further diagnosis of the check gauges
indicator or the instrument cluster circuitry that con-
trols the indicator, (Refer to 8 - ELECTRICAL/IN-
STRUMENT CLUSTER - DIAGNOSIS AND
TESTING). For proper diagnosis of the PCM, the PCI
data bus, or the electronic message inputs to the
instrument cluster that control the check gauges
indicator, a DRBIIItscan tool is required. Refer to
the appropriate diagnostic information.
COOLANT LOW INDICATOR
DESCRIPTION
A coolant low indicator is only found in the instru-
ment clusters of vehicles equipped with an optional
diesel engine. The coolant low indicator should not be
confused with the coolant level low indication pro-
vided by the Electronic Vehicle Information Center
(EVIC) of vehicles equipped with a gasoline engine,
although they do perform the same function. The
coolant low indicator is located in the lower left cor-
ner of the instrument cluster, to the left of the
tachometer. The coolant low indicator consists of an
International Control and Display Symbol icon for
ªLow Coolantº imprinted on an amber lens. The lens
is located behind a cutout in the opaque layer of the
instrument cluster overlay. The dark outer layer of
the overlay prevents the indicator from being clearly
visible when it is not illuminated. The icon appears
silhouetted against an amber field through the trans-
lucent outer layer of the overlay when the indicator
is illuminated from behind by a replaceable incandes-
cent bulb and bulb holder unit located on the instru-
ment cluster electronic circuit board. When the
WJINSTRUMENT CLUSTER 8J - 17
CHECK GAUGES INDICATOR (Continued)
Page 440 of 2199
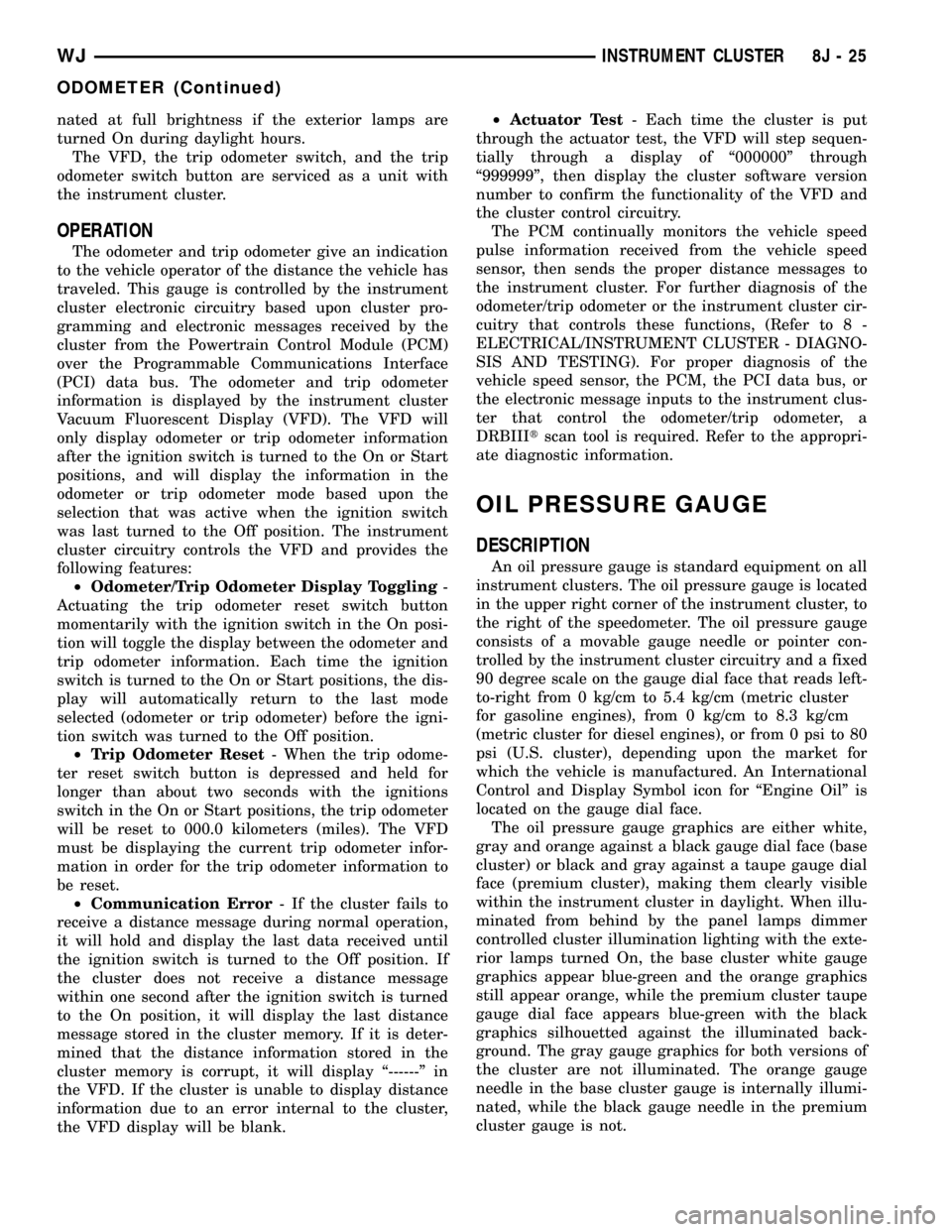
nated at full brightness if the exterior lamps are
turned On during daylight hours.
The VFD, the trip odometer switch, and the trip
odometer switch button are serviced as a unit with
the instrument cluster.
OPERATION
The odometer and trip odometer give an indication
to the vehicle operator of the distance the vehicle has
traveled. This gauge is controlled by the instrument
cluster electronic circuitry based upon cluster pro-
gramming and electronic messages received by the
cluster from the Powertrain Control Module (PCM)
over the Programmable Communications Interface
(PCI) data bus. The odometer and trip odometer
information is displayed by the instrument cluster
Vacuum Fluorescent Display (VFD). The VFD will
only display odometer or trip odometer information
after the ignition switch is turned to the On or Start
positions, and will display the information in the
odometer or trip odometer mode based upon the
selection that was active when the ignition switch
was last turned to the Off position. The instrument
cluster circuitry controls the VFD and provides the
following features:
²Odometer/Trip Odometer Display Toggling-
Actuating the trip odometer reset switch button
momentarily with the ignition switch in the On posi-
tion will toggle the display between the odometer and
trip odometer information. Each time the ignition
switch is turned to the On or Start positions, the dis-
play will automatically return to the last mode
selected (odometer or trip odometer) before the igni-
tion switch was turned to the Off position.
²Trip Odometer Reset- When the trip odome-
ter reset switch button is depressed and held for
longer than about two seconds with the ignitions
switch in the On or Start positions, the trip odometer
will be reset to 000.0 kilometers (miles). The VFD
must be displaying the current trip odometer infor-
mation in order for the trip odometer information to
be reset.
²Communication Error- If the cluster fails to
receive a distance message during normal operation,
it will hold and display the last data received until
the ignition switch is turned to the Off position. If
the cluster does not receive a distance message
within one second after the ignition switch is turned
to the On position, it will display the last distance
message stored in the cluster memory. If it is deter-
mined that the distance information stored in the
cluster memory is corrupt, it will display ª------º in
the VFD. If the cluster is unable to display distance
information due to an error internal to the cluster,
the VFD display will be blank.²Actuator Test- Each time the cluster is put
through the actuator test, the VFD will step sequen-
tially through a display of ª000000º through
ª999999º, then display the cluster software version
number to confirm the functionality of the VFD and
the cluster control circuitry.
The PCM continually monitors the vehicle speed
pulse information received from the vehicle speed
sensor, then sends the proper distance messages to
the instrument cluster. For further diagnosis of the
odometer/trip odometer or the instrument cluster cir-
cuitry that controls these functions, (Refer to 8 -
ELECTRICAL/INSTRUMENT CLUSTER - DIAGNO-
SIS AND TESTING). For proper diagnosis of the
vehicle speed sensor, the PCM, the PCI data bus, or
the electronic message inputs to the instrument clus-
ter that control the odometer/trip odometer, a
DRBIIItscan tool is required. Refer to the appropri-
ate diagnostic information.
OIL PRESSURE GAUGE
DESCRIPTION
An oil pressure gauge is standard equipment on all
instrument clusters. The oil pressure gauge is located
in the upper right corner of the instrument cluster, to
the right of the speedometer. The oil pressure gauge
consists of a movable gauge needle or pointer con-
trolled by the instrument cluster circuitry and a fixed
90 degree scale on the gauge dial face that reads left-
to-right from 0 kg/cm to 5.4 kg/cm (metric cluster
for gasoline engines), from 0 kg/cm to 8.3 kg/cm
(metric cluster for diesel engines), or from 0 psi to 80
psi (U.S. cluster), depending upon the market for
which the vehicle is manufactured. An International
Control and Display Symbol icon for ªEngine Oilº is
located on the gauge dial face.
The oil pressure gauge graphics are either white,
gray and orange against a black gauge dial face (base
cluster) or black and gray against a taupe gauge dial
face (premium cluster), making them clearly visible
within the instrument cluster in daylight. When illu-
minated from behind by the panel lamps dimmer
controlled cluster illumination lighting with the exte-
rior lamps turned On, the base cluster white gauge
graphics appear blue-green and the orange graphics
still appear orange, while the premium cluster taupe
gauge dial face appears blue-green with the black
graphics silhouetted against the illuminated back-
ground. The gray gauge graphics for both versions of
the cluster are not illuminated. The orange gauge
needle in the base cluster gauge is internally illumi-
nated, while the black gauge needle in the premium
cluster gauge is not.
WJINSTRUMENT CLUSTER 8J - 25
ODOMETER (Continued)
Page 441 of 2199
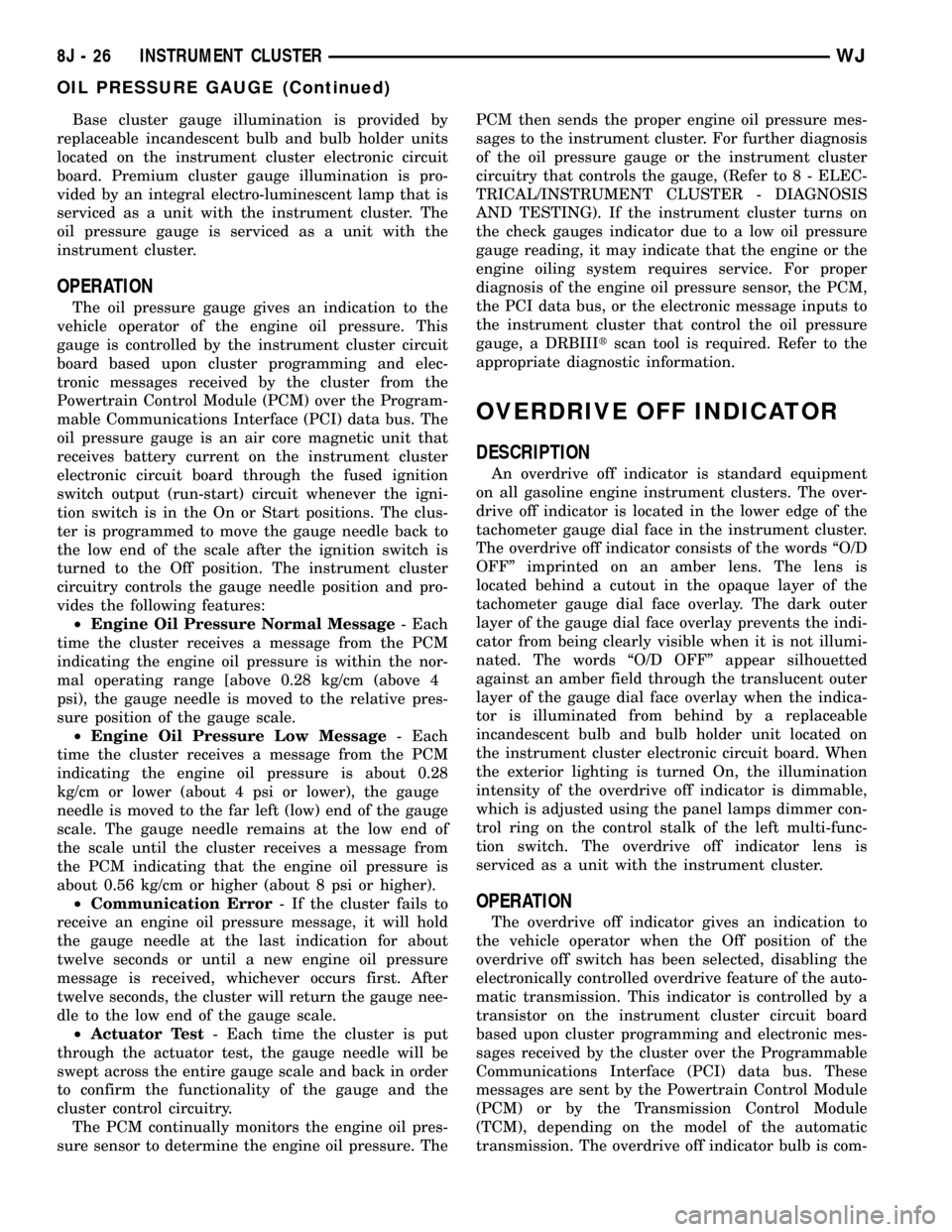
Base cluster gauge illumination is provided by
replaceable incandescent bulb and bulb holder units
located on the instrument cluster electronic circuit
board. Premium cluster gauge illumination is pro-
vided by an integral electro-luminescent lamp that is
serviced as a unit with the instrument cluster. The
oil pressure gauge is serviced as a unit with the
instrument cluster.
OPERATION
The oil pressure gauge gives an indication to the
vehicle operator of the engine oil pressure. This
gauge is controlled by the instrument cluster circuit
board based upon cluster programming and elec-
tronic messages received by the cluster from the
Powertrain Control Module (PCM) over the Program-
mable Communications Interface (PCI) data bus. The
oil pressure gauge is an air core magnetic unit that
receives battery current on the instrument cluster
electronic circuit board through the fused ignition
switch output (run-start) circuit whenever the igni-
tion switch is in the On or Start positions. The clus-
ter is programmed to move the gauge needle back to
the low end of the scale after the ignition switch is
turned to the Off position. The instrument cluster
circuitry controls the gauge needle position and pro-
vides the following features:
²Engine Oil Pressure Normal Message- Each
time the cluster receives a message from the PCM
indicating the engine oil pressure is within the nor-
mal operating range [above 0.28 kg/cm (above 4
psi), the gauge needle is moved to the relative pres-
sure position of the gauge scale.
²Engine Oil Pressure Low Message- Each
time the cluster receives a message from the PCM
indicating the engine oil pressure is about 0.28
kg/cm or lower (about 4 psi or lower), the gauge
needle is moved to the far left (low) end of the gauge
scale. The gauge needle remains at the low end of
the scale until the cluster receives a message from
the PCM indicating that the engine oil pressure is
about 0.56 kg/cm or higher (about 8 psi or higher).
²Communication Error- If the cluster fails to
receive an engine oil pressure message, it will hold
the gauge needle at the last indication for about
twelve seconds or until a new engine oil pressure
message is received, whichever occurs first. After
twelve seconds, the cluster will return the gauge nee-
dle to the low end of the gauge scale.
²Actuator Test- Each time the cluster is put
through the actuator test, the gauge needle will be
swept across the entire gauge scale and back in order
to confirm the functionality of the gauge and the
cluster control circuitry.
The PCM continually monitors the engine oil pres-
sure sensor to determine the engine oil pressure. ThePCM then sends the proper engine oil pressure mes-
sages to the instrument cluster. For further diagnosis
of the oil pressure gauge or the instrument cluster
circuitry that controls the gauge, (Refer to 8 - ELEC-
TRICAL/INSTRUMENT CLUSTER - DIAGNOSIS
AND TESTING). If the instrument cluster turns on
the check gauges indicator due to a low oil pressure
gauge reading, it may indicate that the engine or the
engine oiling system requires service. For proper
diagnosis of the engine oil pressure sensor, the PCM,
the PCI data bus, or the electronic message inputs to
the instrument cluster that control the oil pressure
gauge, a DRBIIItscan tool is required. Refer to the
appropriate diagnostic information.
OVERDRIVE OFF INDICATOR
DESCRIPTION
An overdrive off indicator is standard equipment
on all gasoline engine instrument clusters. The over-
drive off indicator is located in the lower edge of the
tachometer gauge dial face in the instrument cluster.
The overdrive off indicator consists of the words ªO/D
OFFº imprinted on an amber lens. The lens is
located behind a cutout in the opaque layer of the
tachometer gauge dial face overlay. The dark outer
layer of the gauge dial face overlay prevents the indi-
cator from being clearly visible when it is not illumi-
nated. The words ªO/D OFFº appear silhouetted
against an amber field through the translucent outer
layer of the gauge dial face overlay when the indica-
tor is illuminated from behind by a replaceable
incandescent bulb and bulb holder unit located on
the instrument cluster electronic circuit board. When
the exterior lighting is turned On, the illumination
intensity of the overdrive off indicator is dimmable,
which is adjusted using the panel lamps dimmer con-
trol ring on the control stalk of the left multi-func-
tion switch. The overdrive off indicator lens is
serviced as a unit with the instrument cluster.
OPERATION
The overdrive off indicator gives an indication to
the vehicle operator when the Off position of the
overdrive off switch has been selected, disabling the
electronically controlled overdrive feature of the auto-
matic transmission. This indicator is controlled by a
transistor on the instrument cluster circuit board
based upon cluster programming and electronic mes-
sages received by the cluster over the Programmable
Communications Interface (PCI) data bus. These
messages are sent by the Powertrain Control Module
(PCM) or by the Transmission Control Module
(TCM), depending on the model of the automatic
transmission. The overdrive off indicator bulb is com-
8J - 26 INSTRUMENT CLUSTERWJ
OIL PRESSURE GAUGE (Continued)
Page 484 of 2199
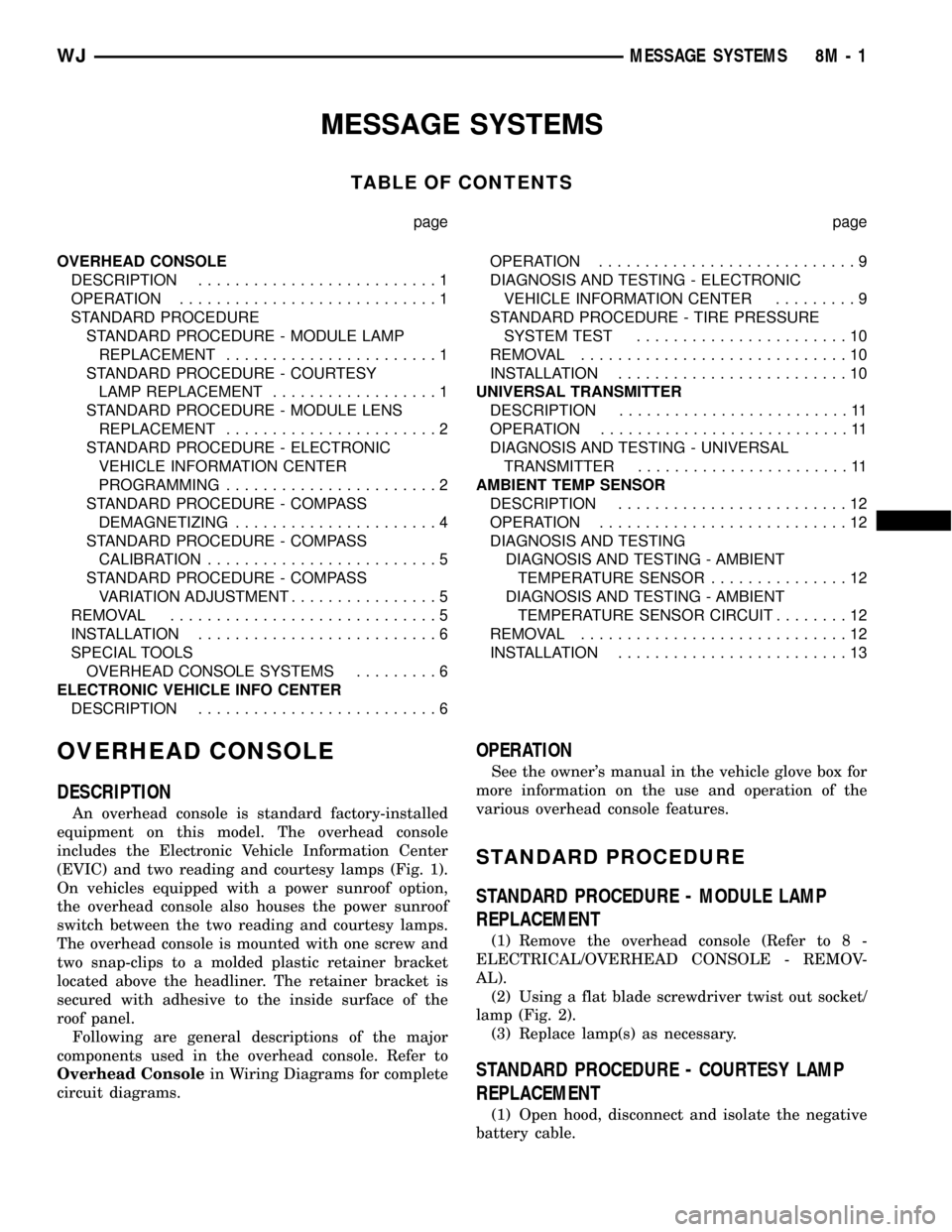
MESSAGE SYSTEMS
TABLE OF CONTENTS
page page
OVERHEAD CONSOLE
DESCRIPTION..........................1
OPERATION............................1
STANDARD PROCEDURE
STANDARD PROCEDURE - MODULE LAMP
REPLACEMENT.......................1
STANDARD PROCEDURE - COURTESY
LAMP REPLACEMENT..................1
STANDARD PROCEDURE - MODULE LENS
REPLACEMENT.......................2
STANDARD PROCEDURE - ELECTRONIC
VEHICLE INFORMATION CENTER
PROGRAMMING.......................2
STANDARD PROCEDURE - COMPASS
DEMAGNETIZING......................4
STANDARD PROCEDURE - COMPASS
CALIBRATION.........................5
STANDARD PROCEDURE - COMPASS
VARIATION ADJUSTMENT................5
REMOVAL.............................5
INSTALLATION..........................6
SPECIAL TOOLS
OVERHEAD CONSOLE SYSTEMS.........6
ELECTRONIC VEHICLE INFO CENTER
DESCRIPTION..........................6OPERATION............................9
DIAGNOSIS AND TESTING - ELECTRONIC
VEHICLE INFORMATION CENTER.........9
STANDARD PROCEDURE - TIRE PRESSURE
SYSTEM TEST.......................10
REMOVAL.............................10
INSTALLATION.........................10
UNIVERSAL TRANSMITTER
DESCRIPTION.........................11
OPERATION...........................11
DIAGNOSIS AND TESTING - UNIVERSAL
TRANSMITTER.......................11
AMBIENT TEMP SENSOR
DESCRIPTION.........................12
OPERATION...........................12
DIAGNOSIS AND TESTING
DIAGNOSIS AND TESTING - AMBIENT
TEMPERATURE SENSOR...............12
DIAGNOSIS AND TESTING - AMBIENT
TEMPERATURE SENSOR CIRCUIT........12
REMOVAL.............................12
INSTALLATION.........................13
OVERHEAD CONSOLE
DESCRIPTION
An overhead console is standard factory-installed
equipment on this model. The overhead console
includes the Electronic Vehicle Information Center
(EVIC) and two reading and courtesy lamps (Fig. 1).
On vehicles equipped with a power sunroof option,
the overhead console also houses the power sunroof
switch between the two reading and courtesy lamps.
The overhead console is mounted with one screw and
two snap-clips to a molded plastic retainer bracket
located above the headliner. The retainer bracket is
secured with adhesive to the inside surface of the
roof panel.
Following are general descriptions of the major
components used in the overhead console. Refer to
Overhead Consolein Wiring Diagrams for complete
circuit diagrams.
OPERATION
See the owner's manual in the vehicle glove box for
more information on the use and operation of the
various overhead console features.
STANDARD PROCEDURE
STANDARD PROCEDURE - MODULE LAMP
REPLACEMENT
(1) Remove the overhead console (Refer to 8 -
ELECTRICAL/OVERHEAD CONSOLE - REMOV-
AL).
(2) Using a flat blade screwdriver twist out socket/
lamp (Fig. 2).
(3) Replace lamp(s) as necessary.
STANDARD PROCEDURE - COURTESY LAMP
REPLACEMENT
(1) Open hood, disconnect and isolate the negative
battery cable.
WJMESSAGE SYSTEMS 8M - 1