Power train JEEP GRAND CHEROKEE 2002 WJ / 2.G Owner's Guide
[x] Cancel search | Manufacturer: JEEP, Model Year: 2002, Model line: GRAND CHEROKEE, Model: JEEP GRAND CHEROKEE 2002 WJ / 2.GPages: 2199, PDF Size: 76.01 MB
Page 388 of 2199
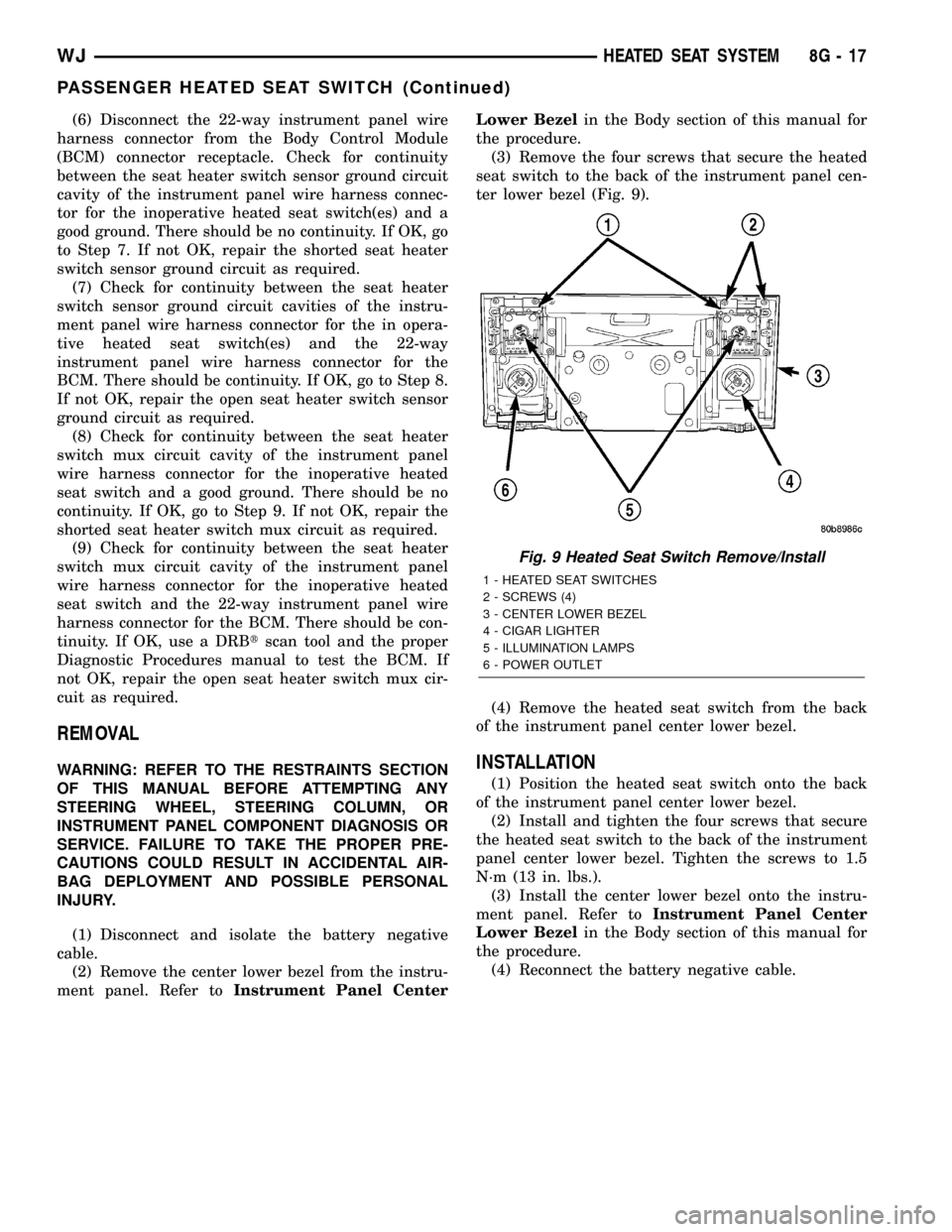
(6) Disconnect the 22-way instrument panel wire
harness connector from the Body Control Module
(BCM) connector receptacle. Check for continuity
between the seat heater switch sensor ground circuit
cavity of the instrument panel wire harness connec-
tor for the inoperative heated seat switch(es) and a
good ground. There should be no continuity. If OK, go
to Step 7. If not OK, repair the shorted seat heater
switch sensor ground circuit as required.
(7) Check for continuity between the seat heater
switch sensor ground circuit cavities of the instru-
ment panel wire harness connector for the in opera-
tive heated seat switch(es) and the 22-way
instrument panel wire harness connector for the
BCM. There should be continuity. If OK, go to Step 8.
If not OK, repair the open seat heater switch sensor
ground circuit as required.
(8) Check for continuity between the seat heater
switch mux circuit cavity of the instrument panel
wire harness connector for the inoperative heated
seat switch and a good ground. There should be no
continuity. If OK, go to Step 9. If not OK, repair the
shorted seat heater switch mux circuit as required.
(9) Check for continuity between the seat heater
switch mux circuit cavity of the instrument panel
wire harness connector for the inoperative heated
seat switch and the 22-way instrument panel wire
harness connector for the BCM. There should be con-
tinuity. If OK, use a DRBtscan tool and the proper
Diagnostic Procedures manual to test the BCM. If
not OK, repair the open seat heater switch mux cir-
cuit as required.
REMOVAL
WARNING: REFER TO THE RESTRAINTS SECTION
OF THIS MANUAL BEFORE ATTEMPTING ANY
STEERING WHEEL, STEERING COLUMN, OR
INSTRUMENT PANEL COMPONENT DIAGNOSIS OR
SERVICE. FAILURE TO TAKE THE PROPER PRE-
CAUTIONS COULD RESULT IN ACCIDENTAL AIR-
BAG DEPLOYMENT AND POSSIBLE PERSONAL
INJURY.
(1) Disconnect and isolate the battery negative
cable.
(2) Remove the center lower bezel from the instru-
ment panel. Refer toInstrument Panel CenterLower Bezelin the Body section of this manual for
the procedure.
(3) Remove the four screws that secure the heated
seat switch to the back of the instrument panel cen-
ter lower bezel (Fig. 9).
(4) Remove the heated seat switch from the back
of the instrument panel center lower bezel.INSTALLATION
(1) Position the heated seat switch onto the back
of the instrument panel center lower bezel.
(2) Install and tighten the four screws that secure
the heated seat switch to the back of the instrument
panel center lower bezel. Tighten the screws to 1.5
N´m (13 in. lbs.).
(3) Install the center lower bezel onto the instru-
ment panel. Refer toInstrument Panel Center
Lower Bezelin the Body section of this manual for
the procedure.
(4) Reconnect the battery negative cable.
Fig. 9 Heated Seat Switch Remove/Install
1 - HEATED SEAT SWITCHES
2 - SCREWS (4)
3 - CENTER LOWER BEZEL
4 - CIGAR LIGHTER
5 - ILLUMINATION LAMPS
6 - POWER OUTLET
WJHEATED SEAT SYSTEM 8G - 17
PASSENGER HEATED SEAT SWITCH (Continued)
Page 394 of 2199

WARNING: ON VEHICLES EQUIPPED WITH AIR-
BAGS, REFER TO ELECTRICAL, RESTRAINTS
BEFORE ATTEMPTING ANY STEERING WHEEL,
STEERING COLUMN, OR INSTRUMENT PANEL
COMPONENT DIAGNOSIS OR SERVICE. FAILURE
TO TAKE THE PROPER PRECAUTIONS COULD
RESULT IN ACCIDENTAL AIRBAG DEPLOYMENT
AND POSSIBLE PERSONAL INJURY.
(1) Remove the horn relay from the PDC. (Refer to
8 - ELECTRICAL/HORN/HORN RELAY -
REMOVAL) for the procedures.
(2) A relay in the de-energized position should
have continuity between terminals 87A and 30, and
no continuity between terminals 87 and 30. If OK, go
to Step 3. If not OK, replace the faulty relay.
(3) Resistance between terminals 85 and 86 (elec-
tromagnet) should be 75 5 ohms. If OK, go to Step
4. If not OK, replace the faulty relay.
(4) Connect a battery to terminals 85 and 86.
There should now be continuity between terminals
30 and 87, and no continuity between terminals 87A
and 30. If OK, perform the Relay Circuit Test that
follows. If not OK, replace the faulty relay.
RELAY CIRCUIT TEST
(1) The relay common feed terminal cavity (30) is
connected to battery voltage and should be hot at all
times. If OK, go to Step 2. If not OK, repair the open
circuit to the fuse in the PDC as required.
(2) The relay normally closed terminal (87A) is
connected to terminal 30 in the de-energized position,
but is not used for this application. Go to Step 3.(3) The relay normally open terminal (87) is con-
nected to the common feed terminal (30) in the ener-
gized position. This terminal supplies battery voltage
to the horn(s). There should be continuity between
the cavity for relay terminal 87 and the horn relay
output circuit cavity of each horn wire harness con-
nector at all times. If OK, go to Step 4. If not OK,
repair the open circuit to the horn(s) as required.
(4) The coil battery terminal (86) is connected to
the electromagnet in the relay. It is connected to bat-
tery voltage and should be hot at all times. Check for
battery voltage at the cavity for relay terminal 86. If
OK, go to Step 5. If not OK, repair the open circuit to
the fuse in the PDC as required.
(5) The coil ground terminal (85) is connected to
the electromagnet in the relay. It is grounded
through the horn switch when the horn switch is
depressed. The horn relay coil ground terminal can
also be grounded by the Body Control Module (BCM)
in response to certain inputs related to the RKE sys-
tem or the Vehicle Theft Security System. Check for
continuity to ground at the cavity for relay terminal
85. There should be continuity with the horn switch
depressed, and no continuity with the horn switch
released. If not OK, (Refer to 8 - ELECTRICAL/
HORN/HORN SWITCH - DIAGNOSIS AND TEST-
ING).
REMOVAL
(1) Disconnect and isolate the battery negative
cable.
(2) Remove the cover from the Power Distribution
Center (PDC) (Fig. 3) .
(3) See the fuse and relay layout label affixed to
the underside of the PDC cover for horn relay iden-
tification and location.
(4) Remove the horn relay from the PDC.
INSTALLATION
(1) See the fuse and relay layout label affixed to
the underside of the PDC cover for the proper horn
relay location.
(2) Position the horn relay in the proper receptacle
in the PDC.
(3) Align the horn relay terminals with the termi-
nal cavities in the PDC receptacle.
(4) Push down firmly on the horn relay until the
terminals are fully seated in the terminal cavities in
the PDC receptacle.
(5) Install the cover onto the PDC.
(6) Reconnect the battery negative cable.
Fig. 2 Horn Relay
30 - COMMON FEED
85 - COIL GROUND
86 - COIL BATTERY
87 - NORMALLY OPEN
87A - NORMALLY CLOSED
WJHORN 8H - 5
HORN RELAY (Continued)
Page 395 of 2199
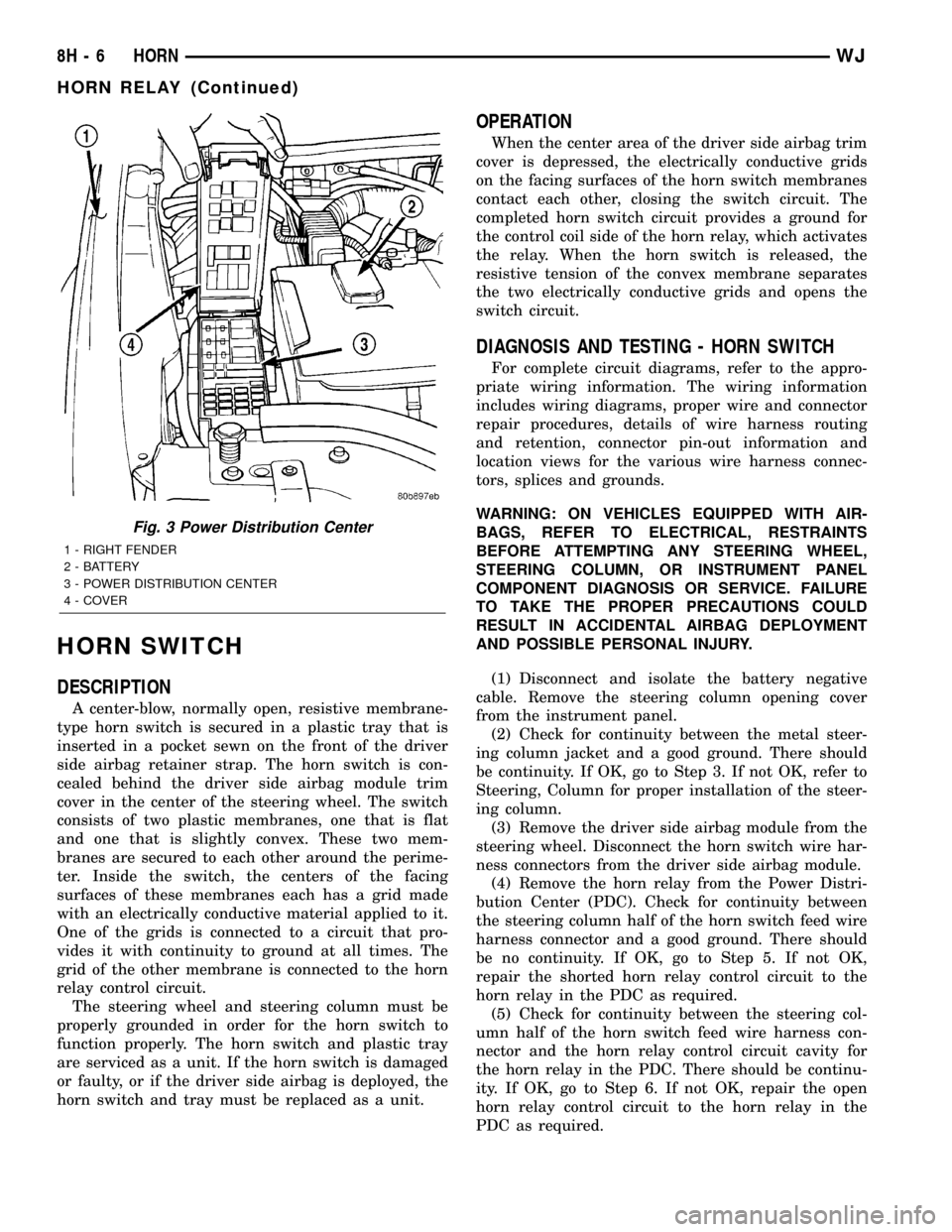
HORN SWITCH
DESCRIPTION
A center-blow, normally open, resistive membrane-
type horn switch is secured in a plastic tray that is
inserted in a pocket sewn on the front of the driver
side airbag retainer strap. The horn switch is con-
cealed behind the driver side airbag module trim
cover in the center of the steering wheel. The switch
consists of two plastic membranes, one that is flat
and one that is slightly convex. These two mem-
branes are secured to each other around the perime-
ter. Inside the switch, the centers of the facing
surfaces of these membranes each has a grid made
with an electrically conductive material applied to it.
One of the grids is connected to a circuit that pro-
vides it with continuity to ground at all times. The
grid of the other membrane is connected to the horn
relay control circuit.
The steering wheel and steering column must be
properly grounded in order for the horn switch to
function properly. The horn switch and plastic tray
are serviced as a unit. If the horn switch is damaged
or faulty, or if the driver side airbag is deployed, the
horn switch and tray must be replaced as a unit.
OPERATION
When the center area of the driver side airbag trim
cover is depressed, the electrically conductive grids
on the facing surfaces of the horn switch membranes
contact each other, closing the switch circuit. The
completed horn switch circuit provides a ground for
the control coil side of the horn relay, which activates
the relay. When the horn switch is released, the
resistive tension of the convex membrane separates
the two electrically conductive grids and opens the
switch circuit.
DIAGNOSIS AND TESTING - HORN SWITCH
For complete circuit diagrams, refer to the appro-
priate wiring information. The wiring information
includes wiring diagrams, proper wire and connector
repair procedures, details of wire harness routing
and retention, connector pin-out information and
location views for the various wire harness connec-
tors, splices and grounds.
WARNING: ON VEHICLES EQUIPPED WITH AIR-
BAGS, REFER TO ELECTRICAL, RESTRAINTS
BEFORE ATTEMPTING ANY STEERING WHEEL,
STEERING COLUMN, OR INSTRUMENT PANEL
COMPONENT DIAGNOSIS OR SERVICE. FAILURE
TO TAKE THE PROPER PRECAUTIONS COULD
RESULT IN ACCIDENTAL AIRBAG DEPLOYMENT
AND POSSIBLE PERSONAL INJURY.
(1) Disconnect and isolate the battery negative
cable. Remove the steering column opening cover
from the instrument panel.
(2) Check for continuity between the metal steer-
ing column jacket and a good ground. There should
be continuity. If OK, go to Step 3. If not OK, refer to
Steering, Column for proper installation of the steer-
ing column.
(3) Remove the driver side airbag module from the
steering wheel. Disconnect the horn switch wire har-
ness connectors from the driver side airbag module.
(4) Remove the horn relay from the Power Distri-
bution Center (PDC). Check for continuity between
the steering column half of the horn switch feed wire
harness connector and a good ground. There should
be no continuity. If OK, go to Step 5. If not OK,
repair the shorted horn relay control circuit to the
horn relay in the PDC as required.
(5) Check for continuity between the steering col-
umn half of the horn switch feed wire harness con-
nector and the horn relay control circuit cavity for
the horn relay in the PDC. There should be continu-
ity. If OK, go to Step 6. If not OK, repair the open
horn relay control circuit to the horn relay in the
PDC as required.
Fig. 3 Power Distribution Center
1 - RIGHT FENDER
2 - BATTERY
3 - POWER DISTRIBUTION CENTER
4 - COVER
8H - 6 HORNWJ
HORN RELAY (Continued)
Page 399 of 2199
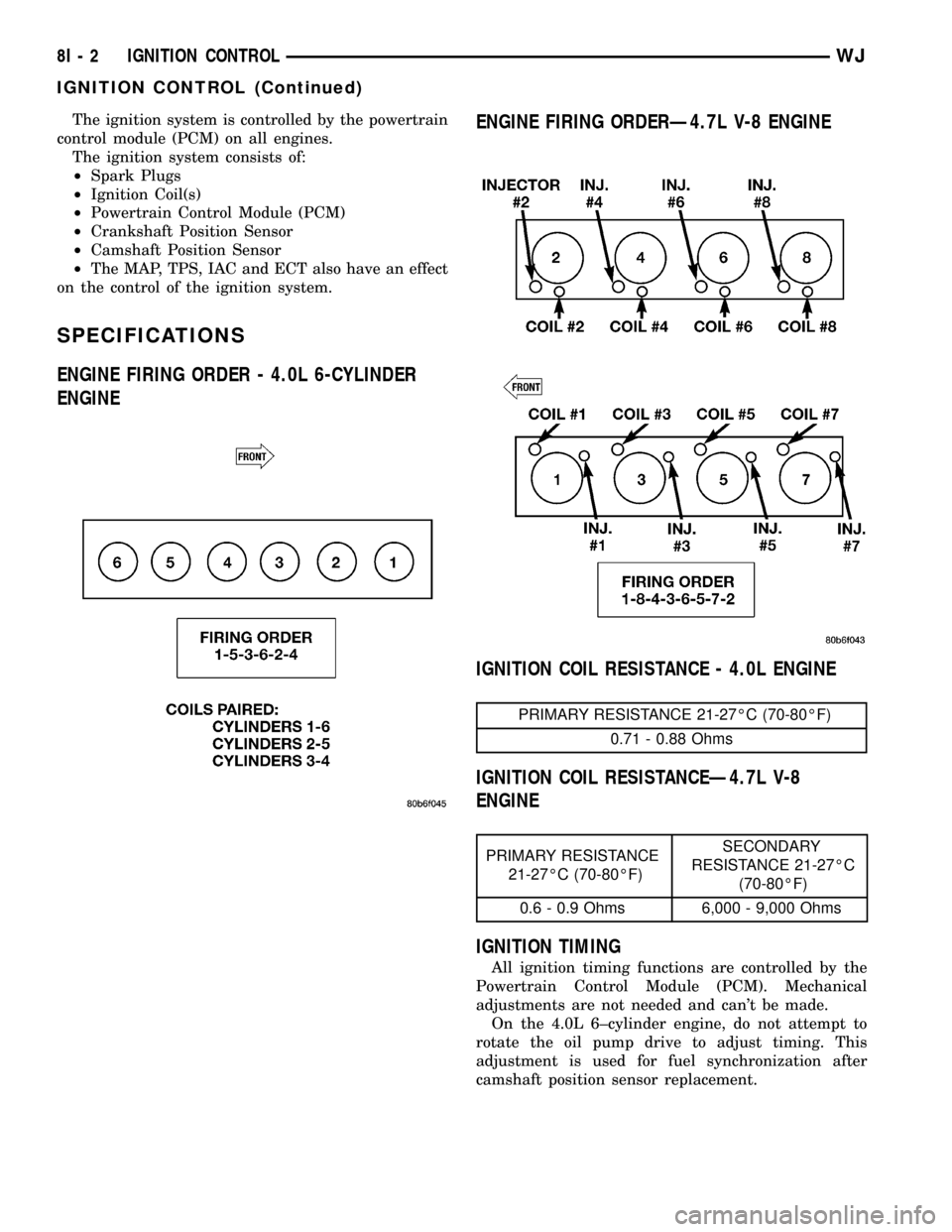
The ignition system is controlled by the powertrain
control module (PCM) on all engines.
The ignition system consists of:
²Spark Plugs
²Ignition Coil(s)
²Powertrain Control Module (PCM)
²Crankshaft Position Sensor
²Camshaft Position Sensor
²The MAP, TPS, IAC and ECT also have an effect
on the control of the ignition system.
SPECIFICATIONS
ENGINE FIRING ORDER - 4.0L 6-CYLINDER
ENGINEENGINE FIRING ORDERÐ4.7L V-8 ENGINE
IGNITION COIL RESISTANCE - 4.0L ENGINE
PRIMARY RESISTANCE 21-27ÉC (70-80ÉF)
0.71 - 0.88 Ohms
IGNITION COIL RESISTANCEÐ4.7L V-8
ENGINE
PRIMARY RESISTANCE
21-27ÉC (70-80ÉF)SECONDARY
RESISTANCE 21-27ÉC
(70-80ÉF)
0.6 - 0.9 Ohms 6,000 - 9,000 Ohms
IGNITION TIMING
All ignition timing functions are controlled by the
Powertrain Control Module (PCM). Mechanical
adjustments are not needed and can't be made.
On the 4.0L 6±cylinder engine, do not attempt to
rotate the oil pump drive to adjust timing. This
adjustment is used for fuel synchronization after
camshaft position sensor replacement.
8I - 2 IGNITION CONTROLWJ
IGNITION CONTROL (Continued)
Page 400 of 2199
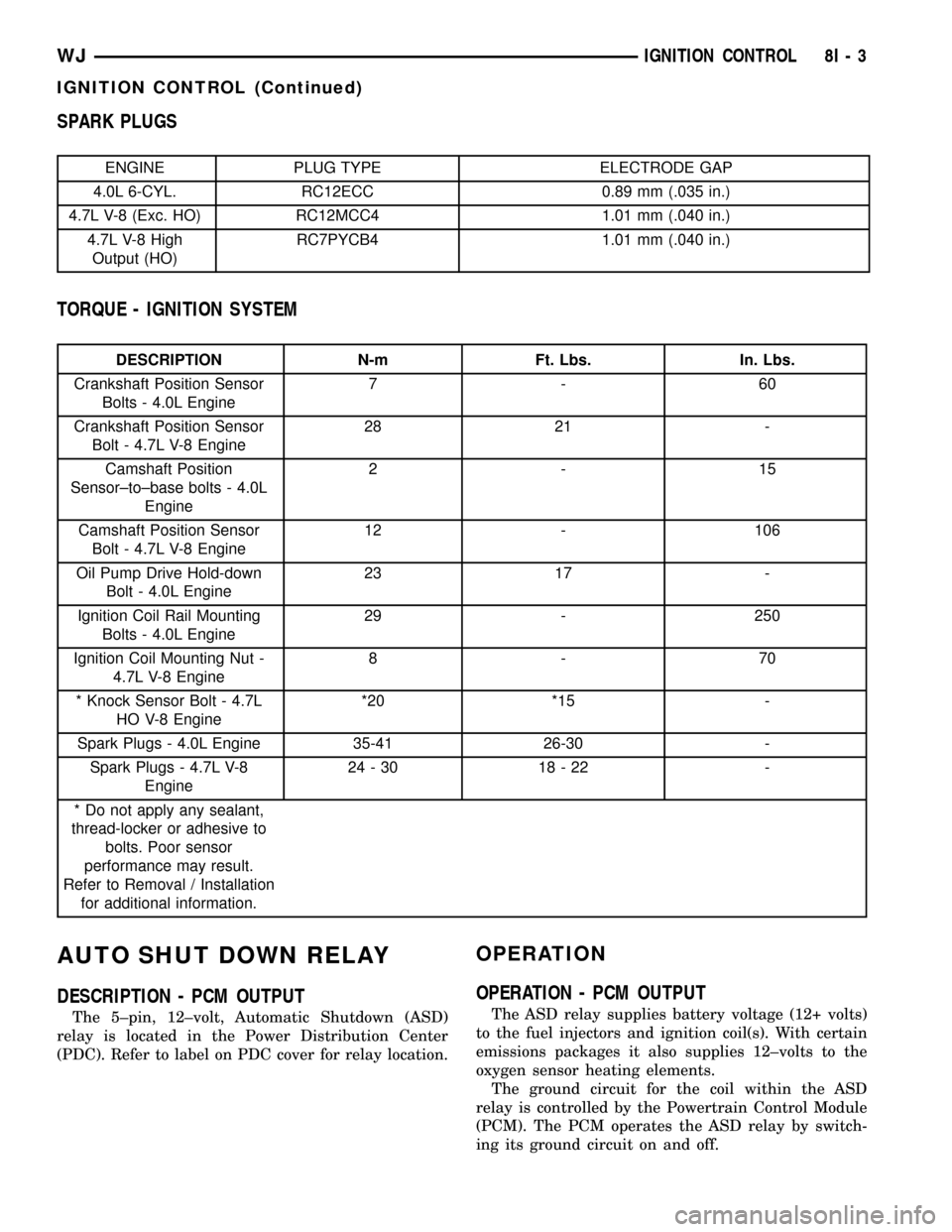
SPARK PLUGS
ENGINE PLUG TYPE ELECTRODE GAP
4.0L 6-CYL. RC12ECC 0.89 mm (.035 in.)
4.7L V-8 (Exc. HO) RC12MCC4 1.01 mm (.040 in.)
4.7L V-8 High
Output (HO)RC7PYCB4 1.01 mm (.040 in.)
TORQUE - IGNITION SYSTEM
DESCRIPTION N-m Ft. Lbs. In. Lbs.
Crankshaft Position Sensor
Bolts - 4.0L Engine7- 60
Crankshaft Position Sensor
Bolt - 4.7L V-8 Engine28 21 -
Camshaft Position
Sensor±to±base bolts - 4.0L
Engine2- 15
Camshaft Position Sensor
Bolt - 4.7L V-8 Engine12 - 106
Oil Pump Drive Hold-down
Bolt - 4.0L Engine23 17 -
Ignition Coil Rail Mounting
Bolts - 4.0L Engine29 - 250
Ignition Coil Mounting Nut -
4.7L V-8 Engine8- 70
* Knock Sensor Bolt - 4.7L
HO V-8 Engine*20 *15 -
Spark Plugs - 4.0L Engine 35-41 26-30 -
Spark Plugs - 4.7L V-8
Engine24-30 18-22 -
* Do not apply any sealant,
thread-locker or adhesive to
bolts. Poor sensor
performance may result.
Refer to Removal / Installation
for additional information.
AUTO SHUT DOWN RELAY
DESCRIPTION - PCM OUTPUT
The 5±pin, 12±volt, Automatic Shutdown (ASD)
relay is located in the Power Distribution Center
(PDC). Refer to label on PDC cover for relay location.
OPERATION
OPERATION - PCM OUTPUT
The ASD relay supplies battery voltage (12+ volts)
to the fuel injectors and ignition coil(s). With certain
emissions packages it also supplies 12±volts to the
oxygen sensor heating elements.
The ground circuit for the coil within the ASD
relay is controlled by the Powertrain Control Module
(PCM). The PCM operates the ASD relay by switch-
ing its ground circuit on and off.
WJIGNITION CONTROL 8I - 3
IGNITION CONTROL (Continued)
Page 401 of 2199
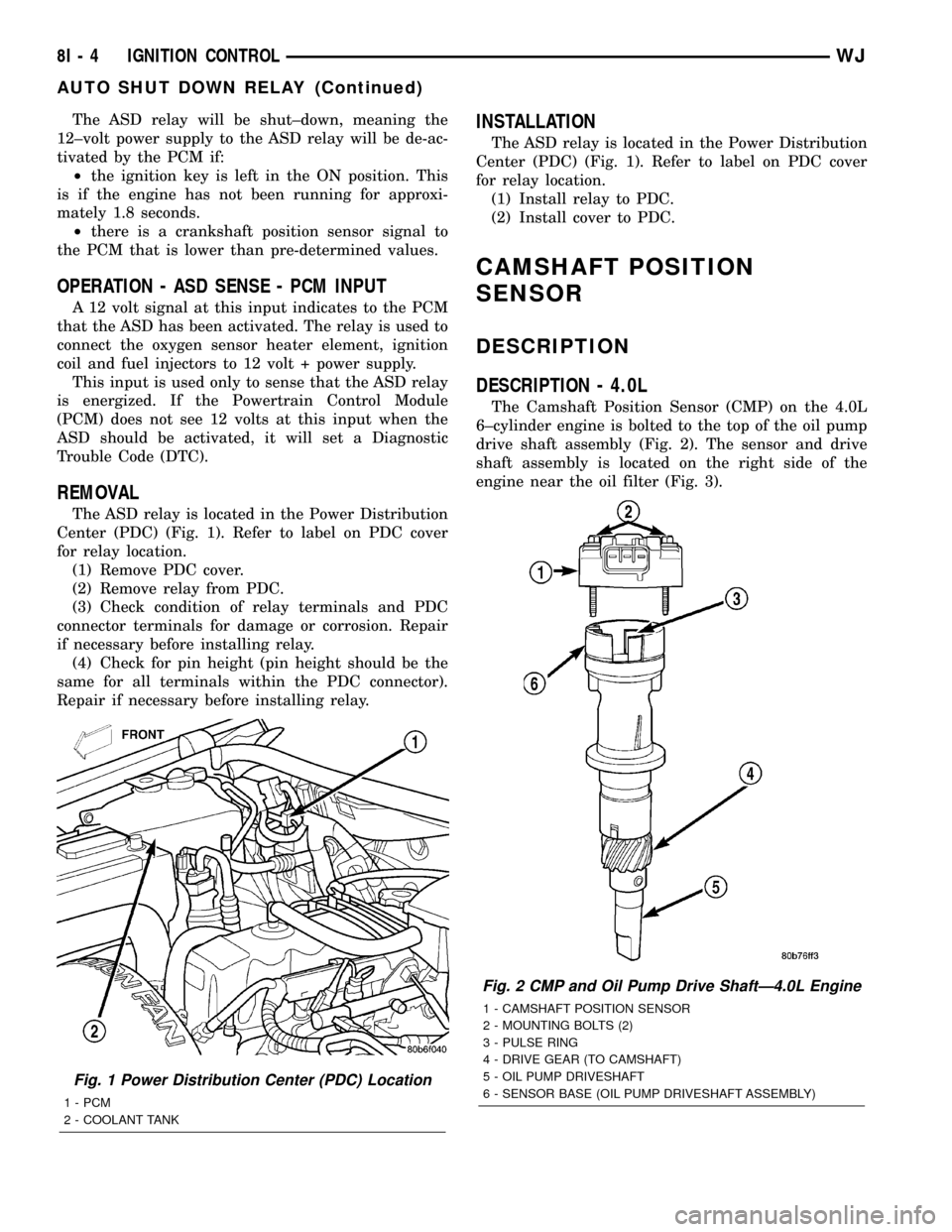
The ASD relay will be shut±down, meaning the
12±volt power supply to the ASD relay will be de-ac-
tivated by the PCM if:
²the ignition key is left in the ON position. This
is if the engine has not been running for approxi-
mately 1.8 seconds.
²there is a crankshaft position sensor signal to
the PCM that is lower than pre-determined values.
OPERATION - ASD SENSE - PCM INPUT
A 12 volt signal at this input indicates to the PCM
that the ASD has been activated. The relay is used to
connect the oxygen sensor heater element, ignition
coil and fuel injectors to 12 volt + power supply.
This input is used only to sense that the ASD relay
is energized. If the Powertrain Control Module
(PCM) does not see 12 volts at this input when the
ASD should be activated, it will set a Diagnostic
Trouble Code (DTC).
REMOVAL
The ASD relay is located in the Power Distribution
Center (PDC) (Fig. 1). Refer to label on PDC cover
for relay location.
(1) Remove PDC cover.
(2) Remove relay from PDC.
(3) Check condition of relay terminals and PDC
connector terminals for damage or corrosion. Repair
if necessary before installing relay.
(4) Check for pin height (pin height should be the
same for all terminals within the PDC connector).
Repair if necessary before installing relay.
INSTALLATION
The ASD relay is located in the Power Distribution
Center (PDC) (Fig. 1). Refer to label on PDC cover
for relay location.
(1) Install relay to PDC.
(2) Install cover to PDC.
CAMSHAFT POSITION
SENSOR
DESCRIPTION
DESCRIPTION - 4.0L
The Camshaft Position Sensor (CMP) on the 4.0L
6±cylinder engine is bolted to the top of the oil pump
drive shaft assembly (Fig. 2). The sensor and drive
shaft assembly is located on the right side of the
engine near the oil filter (Fig. 3).
Fig. 1 Power Distribution Center (PDC) Location
1 - PCM
2 - COOLANT TANK
Fig. 2 CMP and Oil Pump Drive ShaftÐ4.0L Engine
1 - CAMSHAFT POSITION SENSOR
2 - MOUNTING BOLTS (2)
3 - PULSE RING
4 - DRIVE GEAR (TO CAMSHAFT)
5 - OIL PUMP DRIVESHAFT
6 - SENSOR BASE (OIL PUMP DRIVESHAFT ASSEMBLY)
8I - 4 IGNITION CONTROLWJ
AUTO SHUT DOWN RELAY (Continued)
Page 406 of 2199
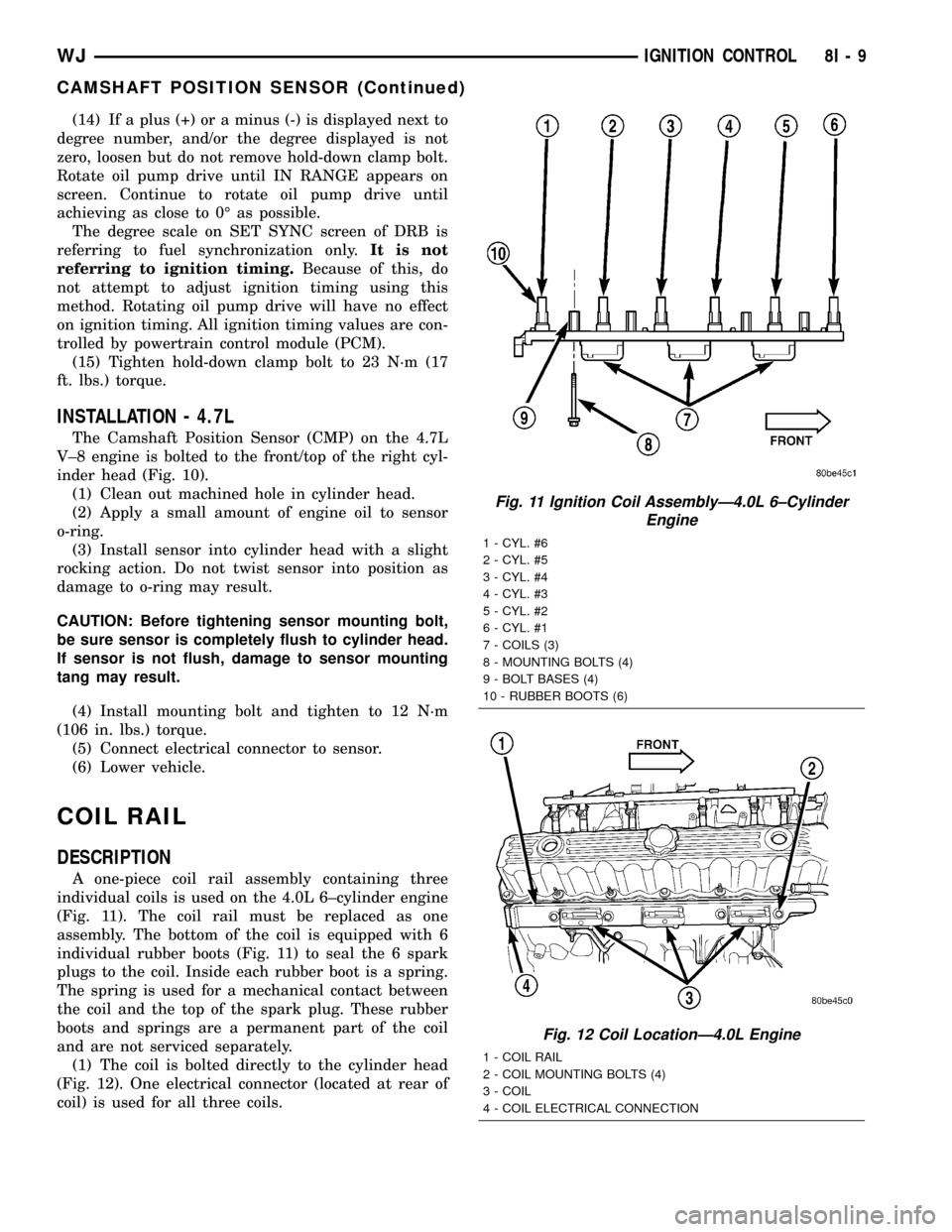
(14) If a plus (+) or a minus (-) is displayed next to
degree number, and/or the degree displayed is not
zero, loosen but do not remove hold-down clamp bolt.
Rotate oil pump drive until IN RANGE appears on
screen. Continue to rotate oil pump drive until
achieving as close to 0É as possible.
The degree scale on SET SYNC screen of DRB is
referring to fuel synchronization only.It is not
referring to ignition timing.Because of this, do
not attempt to adjust ignition timing using this
method. Rotating oil pump drive will have no effect
on ignition timing. All ignition timing values are con-
trolled by powertrain control module (PCM).
(15) Tighten hold-down clamp bolt to 23 N´m (17
ft. lbs.) torque.
INSTALLATION - 4.7L
The Camshaft Position Sensor (CMP) on the 4.7L
V±8 engine is bolted to the front/top of the right cyl-
inder head (Fig. 10).
(1) Clean out machined hole in cylinder head.
(2) Apply a small amount of engine oil to sensor
o-ring.
(3) Install sensor into cylinder head with a slight
rocking action. Do not twist sensor into position as
damage to o-ring may result.
CAUTION: Before tightening sensor mounting bolt,
be sure sensor is completely flush to cylinder head.
If sensor is not flush, damage to sensor mounting
tang may result.
(4) Install mounting bolt and tighten to 12 N´m
(106 in. lbs.) torque.
(5) Connect electrical connector to sensor.
(6) Lower vehicle.
COIL RAIL
DESCRIPTION
A one-piece coil rail assembly containing three
individual coils is used on the 4.0L 6±cylinder engine
(Fig. 11). The coil rail must be replaced as one
assembly. The bottom of the coil is equipped with 6
individual rubber boots (Fig. 11) to seal the 6 spark
plugs to the coil. Inside each rubber boot is a spring.
The spring is used for a mechanical contact between
the coil and the top of the spark plug. These rubber
boots and springs are a permanent part of the coil
and are not serviced separately.
(1) The coil is bolted directly to the cylinder head
(Fig. 12). One electrical connector (located at rear of
coil) is used for all three coils.
Fig. 11 Ignition Coil AssemblyÐ4.0L 6±Cylinder
Engine
1 - CYL. #6
2 - CYL. #5
3 - CYL. #4
4 - CYL. #3
5 - CYL. #2
6 - CYL. #1
7 - COILS (3)
8 - MOUNTING BOLTS (4)
9 - BOLT BASES (4)
10 - RUBBER BOOTS (6)
Fig. 12 Coil LocationÐ4.0L Engine
1 - COIL RAIL
2 - COIL MOUNTING BOLTS (4)
3 - COIL
4 - COIL ELECTRICAL CONNECTION
WJIGNITION CONTROL 8I - 9
CAMSHAFT POSITION SENSOR (Continued)
Page 407 of 2199
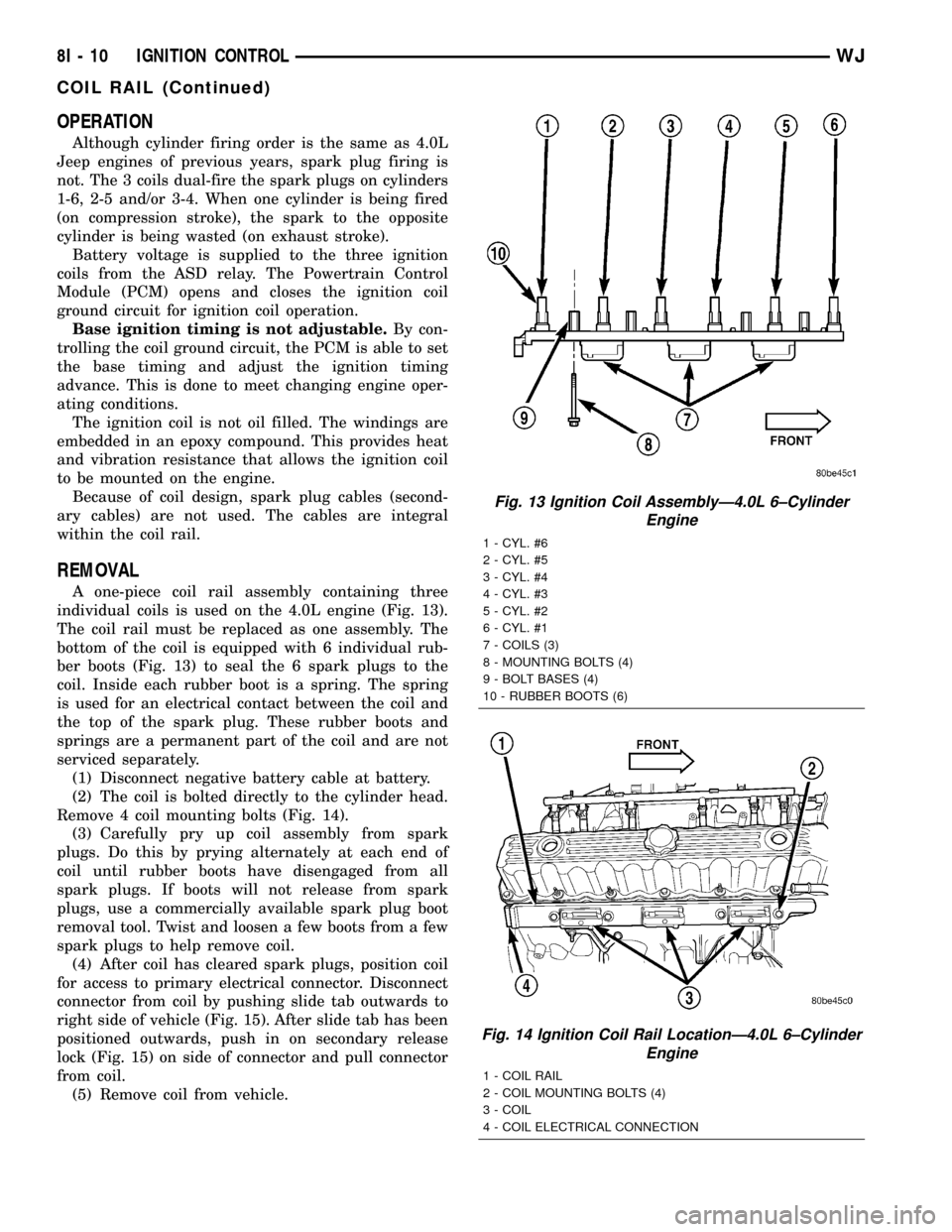
OPERATION
Although cylinder firing order is the same as 4.0L
Jeep engines of previous years, spark plug firing is
not. The 3 coils dual-fire the spark plugs on cylinders
1-6, 2-5 and/or 3-4. When one cylinder is being fired
(on compression stroke), the spark to the opposite
cylinder is being wasted (on exhaust stroke).
Battery voltage is supplied to the three ignition
coils from the ASD relay. The Powertrain Control
Module (PCM) opens and closes the ignition coil
ground circuit for ignition coil operation.
Base ignition timing is not adjustable.By con-
trolling the coil ground circuit, the PCM is able to set
the base timing and adjust the ignition timing
advance. This is done to meet changing engine oper-
ating conditions.
The ignition coil is not oil filled. The windings are
embedded in an epoxy compound. This provides heat
and vibration resistance that allows the ignition coil
to be mounted on the engine.
Because of coil design, spark plug cables (second-
ary cables) are not used. The cables are integral
within the coil rail.
REMOVAL
A one-piece coil rail assembly containing three
individual coils is used on the 4.0L engine (Fig. 13).
The coil rail must be replaced as one assembly. The
bottom of the coil is equipped with 6 individual rub-
ber boots (Fig. 13) to seal the 6 spark plugs to the
coil. Inside each rubber boot is a spring. The spring
is used for an electrical contact between the coil and
the top of the spark plug. These rubber boots and
springs are a permanent part of the coil and are not
serviced separately.
(1) Disconnect negative battery cable at battery.
(2) The coil is bolted directly to the cylinder head.
Remove 4 coil mounting bolts (Fig. 14).
(3) Carefully pry up coil assembly from spark
plugs. Do this by prying alternately at each end of
coil until rubber boots have disengaged from all
spark plugs. If boots will not release from spark
plugs, use a commercially available spark plug boot
removal tool. Twist and loosen a few boots from a few
spark plugs to help remove coil.
(4) After coil has cleared spark plugs, position coil
for access to primary electrical connector. Disconnect
connector from coil by pushing slide tab outwards to
right side of vehicle (Fig. 15). After slide tab has been
positioned outwards, push in on secondary release
lock (Fig. 15) on side of connector and pull connector
from coil.
(5) Remove coil from vehicle.
Fig. 13 Ignition Coil AssemblyÐ4.0L 6±Cylinder
Engine
1 - CYL. #6
2 - CYL. #5
3 - CYL. #4
4 - CYL. #3
5 - CYL. #2
6 - CYL. #1
7 - COILS (3)
8 - MOUNTING BOLTS (4)
9 - BOLT BASES (4)
10 - RUBBER BOOTS (6)
Fig. 14 Ignition Coil Rail LocationÐ4.0L 6±Cylinder
Engine
1 - COIL RAIL
2 - COIL MOUNTING BOLTS (4)
3 - COIL
4 - COIL ELECTRICAL CONNECTION
8I - 10 IGNITION CONTROLWJ
COIL RAIL (Continued)
Page 409 of 2199
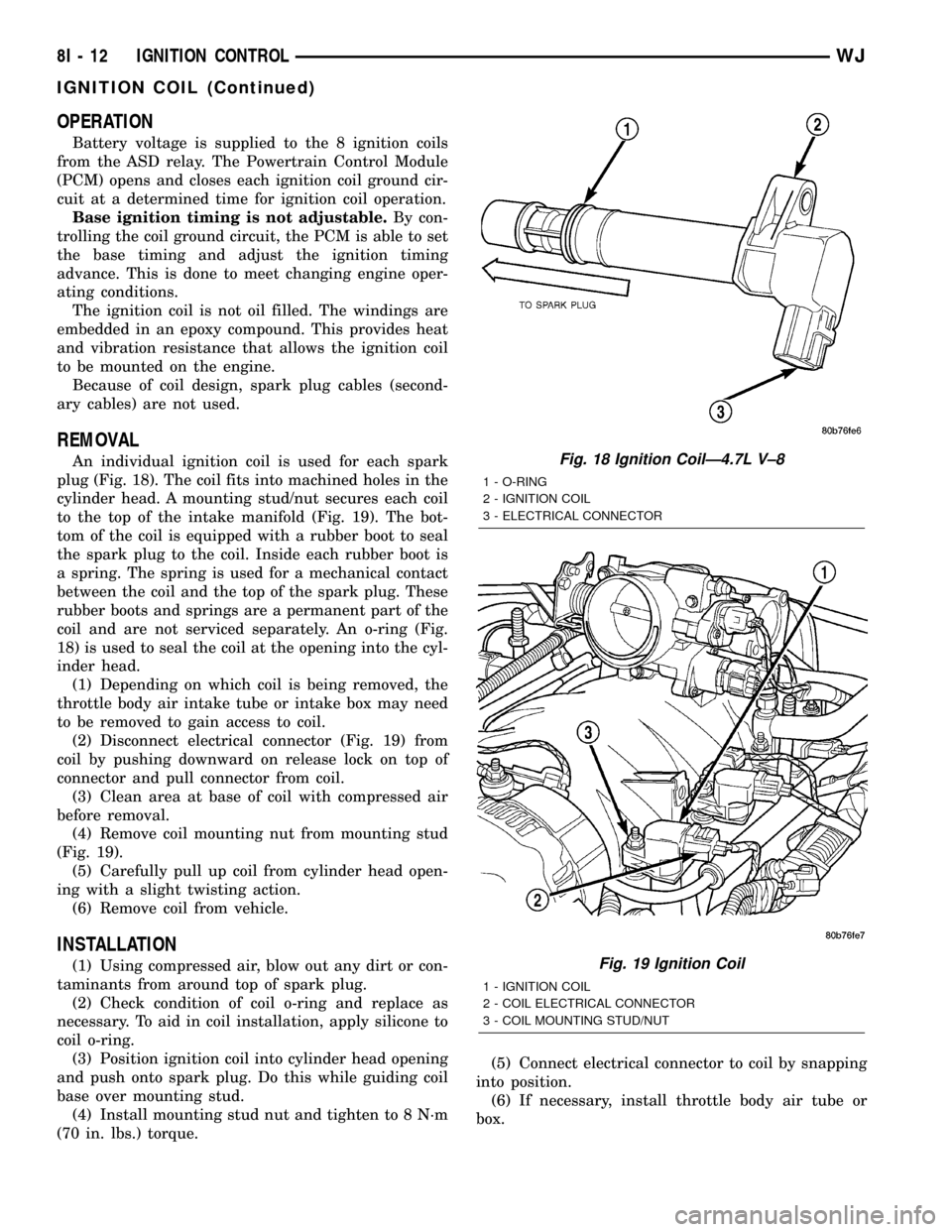
OPERATION
Battery voltage is supplied to the 8 ignition coils
from the ASD relay. The Powertrain Control Module
(PCM) opens and closes each ignition coil ground cir-
cuit at a determined time for ignition coil operation.
Base ignition timing is not adjustable.By con-
trolling the coil ground circuit, the PCM is able to set
the base timing and adjust the ignition timing
advance. This is done to meet changing engine oper-
ating conditions.
The ignition coil is not oil filled. The windings are
embedded in an epoxy compound. This provides heat
and vibration resistance that allows the ignition coil
to be mounted on the engine.
Because of coil design, spark plug cables (second-
ary cables) are not used.
REMOVAL
An individual ignition coil is used for each spark
plug (Fig. 18). The coil fits into machined holes in the
cylinder head. A mounting stud/nut secures each coil
to the top of the intake manifold (Fig. 19). The bot-
tom of the coil is equipped with a rubber boot to seal
the spark plug to the coil. Inside each rubber boot is
a spring. The spring is used for a mechanical contact
between the coil and the top of the spark plug. These
rubber boots and springs are a permanent part of the
coil and are not serviced separately. An o-ring (Fig.
18) is used to seal the coil at the opening into the cyl-
inder head.
(1) Depending on which coil is being removed, the
throttle body air intake tube or intake box may need
to be removed to gain access to coil.
(2) Disconnect electrical connector (Fig. 19) from
coil by pushing downward on release lock on top of
connector and pull connector from coil.
(3) Clean area at base of coil with compressed air
before removal.
(4) Remove coil mounting nut from mounting stud
(Fig. 19).
(5) Carefully pull up coil from cylinder head open-
ing with a slight twisting action.
(6) Remove coil from vehicle.
INSTALLATION
(1) Using compressed air, blow out any dirt or con-
taminants from around top of spark plug.
(2) Check condition of coil o-ring and replace as
necessary. To aid in coil installation, apply silicone to
coil o-ring.
(3) Position ignition coil into cylinder head opening
and push onto spark plug. Do this while guiding coil
base over mounting stud.
(4) Install mounting stud nut and tighten to 8 N´m
(70 in. lbs.) torque.(5) Connect electrical connector to coil by snapping
into position.
(6) If necessary, install throttle body air tube or
box.
Fig. 18 Ignition CoilÐ4.7L V±8
1 - O-RING
2 - IGNITION COIL
3 - ELECTRICAL CONNECTOR
Fig. 19 Ignition Coil
1 - IGNITION COIL
2 - COIL ELECTRICAL CONNECTOR
3 - COIL MOUNTING STUD/NUT
8I - 12 IGNITION CONTROLWJ
IGNITION COIL (Continued)
Page 410 of 2199
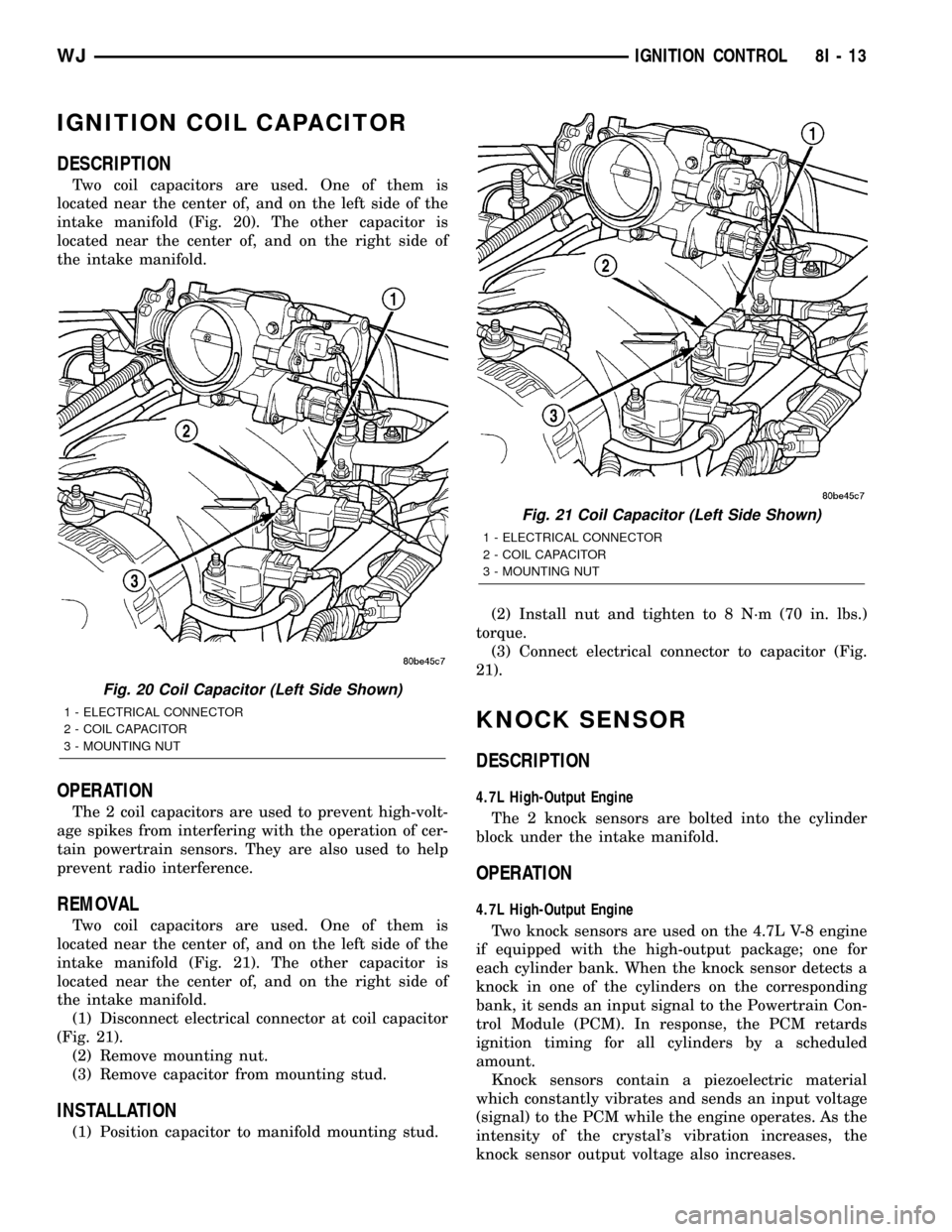
IGNITION COIL CAPACITOR
DESCRIPTION
Two coil capacitors are used. One of them is
located near the center of, and on the left side of the
intake manifold (Fig. 20). The other capacitor is
located near the center of, and on the right side of
the intake manifold.
OPERATION
The 2 coil capacitors are used to prevent high-volt-
age spikes from interfering with the operation of cer-
tain powertrain sensors. They are also used to help
prevent radio interference.
REMOVAL
Two coil capacitors are used. One of them is
located near the center of, and on the left side of the
intake manifold (Fig. 21). The other capacitor is
located near the center of, and on the right side of
the intake manifold.
(1) Disconnect electrical connector at coil capacitor
(Fig. 21).
(2) Remove mounting nut.
(3) Remove capacitor from mounting stud.
INSTALLATION
(1) Position capacitor to manifold mounting stud.(2) Install nut and tighten to 8 N´m (70 in. lbs.)
torque.
(3) Connect electrical connector to capacitor (Fig.
21).
KNOCK SENSOR
DESCRIPTION
4.7L High-Output Engine
The 2 knock sensors are bolted into the cylinder
block under the intake manifold.
OPERATION
4.7L High-Output Engine
Two knock sensors are used on the 4.7L V-8 engine
if equipped with the high-output package; one for
each cylinder bank. When the knock sensor detects a
knock in one of the cylinders on the corresponding
bank, it sends an input signal to the Powertrain Con-
trol Module (PCM). In response, the PCM retards
ignition timing for all cylinders by a scheduled
amount.
Knock sensors contain a piezoelectric material
which constantly vibrates and sends an input voltage
(signal) to the PCM while the engine operates. As the
intensity of the crystal's vibration increases, the
knock sensor output voltage also increases.
Fig. 20 Coil Capacitor (Left Side Shown)
1 - ELECTRICAL CONNECTOR
2 - COIL CAPACITOR
3 - MOUNTING NUT
Fig. 21 Coil Capacitor (Left Side Shown)
1 - ELECTRICAL CONNECTOR
2 - COIL CAPACITOR
3 - MOUNTING NUT
WJIGNITION CONTROL 8I - 13