Turn signal JEEP GRAND CHEROKEE 2002 WJ / 2.G Service Manual
[x] Cancel search | Manufacturer: JEEP, Model Year: 2002, Model line: GRAND CHEROKEE, Model: JEEP GRAND CHEROKEE 2002 WJ / 2.GPages: 2199, PDF Size: 76.01 MB
Page 495 of 2199
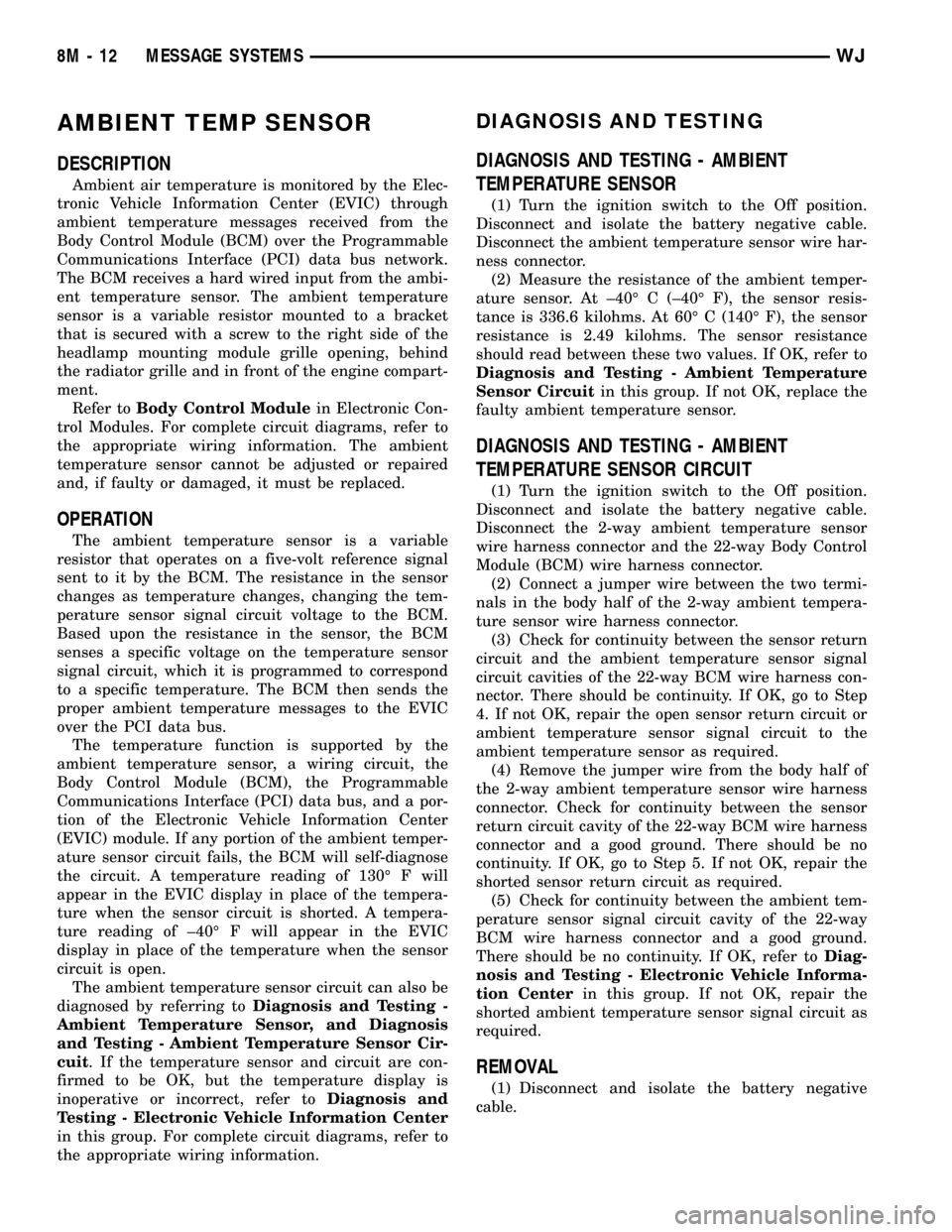
AMBIENT TEMP SENSOR
DESCRIPTION
Ambient air temperature is monitored by the Elec-
tronic Vehicle Information Center (EVIC) through
ambient temperature messages received from the
Body Control Module (BCM) over the Programmable
Communications Interface (PCI) data bus network.
The BCM receives a hard wired input from the ambi-
ent temperature sensor. The ambient temperature
sensor is a variable resistor mounted to a bracket
that is secured with a screw to the right side of the
headlamp mounting module grille opening, behind
the radiator grille and in front of the engine compart-
ment.
Refer toBody Control Modulein Electronic Con-
trol Modules. For complete circuit diagrams, refer to
the appropriate wiring information. The ambient
temperature sensor cannot be adjusted or repaired
and, if faulty or damaged, it must be replaced.
OPERATION
The ambient temperature sensor is a variable
resistor that operates on a five-volt reference signal
sent to it by the BCM. The resistance in the sensor
changes as temperature changes, changing the tem-
perature sensor signal circuit voltage to the BCM.
Based upon the resistance in the sensor, the BCM
senses a specific voltage on the temperature sensor
signal circuit, which it is programmed to correspond
to a specific temperature. The BCM then sends the
proper ambient temperature messages to the EVIC
over the PCI data bus.
The temperature function is supported by the
ambient temperature sensor, a wiring circuit, the
Body Control Module (BCM), the Programmable
Communications Interface (PCI) data bus, and a por-
tion of the Electronic Vehicle Information Center
(EVIC) module. If any portion of the ambient temper-
ature sensor circuit fails, the BCM will self-diagnose
the circuit. A temperature reading of 130É F will
appear in the EVIC display in place of the tempera-
ture when the sensor circuit is shorted. A tempera-
ture reading of ±40É F will appear in the EVIC
display in place of the temperature when the sensor
circuit is open.
The ambient temperature sensor circuit can also be
diagnosed by referring toDiagnosis and Testing -
Ambient Temperature Sensor, and Diagnosis
and Testing - Ambient Temperature Sensor Cir-
cuit. If the temperature sensor and circuit are con-
firmed to be OK, but the temperature display is
inoperative or incorrect, refer toDiagnosis and
Testing - Electronic Vehicle Information Center
in this group. For complete circuit diagrams, refer to
the appropriate wiring information.
DIAGNOSIS AND TESTING
DIAGNOSIS AND TESTING - AMBIENT
TEMPERATURE SENSOR
(1) Turn the ignition switch to the Off position.
Disconnect and isolate the battery negative cable.
Disconnect the ambient temperature sensor wire har-
ness connector.
(2) Measure the resistance of the ambient temper-
ature sensor. At ±40É C (±40É F), the sensor resis-
tance is 336.6 kilohms. At 60É C (140É F), the sensor
resistance is 2.49 kilohms. The sensor resistance
should read between these two values. If OK, refer to
Diagnosis and Testing - Ambient Temperature
Sensor Circuitin this group. If not OK, replace the
faulty ambient temperature sensor.
DIAGNOSIS AND TESTING - AMBIENT
TEMPERATURE SENSOR CIRCUIT
(1) Turn the ignition switch to the Off position.
Disconnect and isolate the battery negative cable.
Disconnect the 2-way ambient temperature sensor
wire harness connector and the 22-way Body Control
Module (BCM) wire harness connector.
(2) Connect a jumper wire between the two termi-
nals in the body half of the 2-way ambient tempera-
ture sensor wire harness connector.
(3) Check for continuity between the sensor return
circuit and the ambient temperature sensor signal
circuit cavities of the 22-way BCM wire harness con-
nector. There should be continuity. If OK, go to Step
4. If not OK, repair the open sensor return circuit or
ambient temperature sensor signal circuit to the
ambient temperature sensor as required.
(4) Remove the jumper wire from the body half of
the 2-way ambient temperature sensor wire harness
connector. Check for continuity between the sensor
return circuit cavity of the 22-way BCM wire harness
connector and a good ground. There should be no
continuity. If OK, go to Step 5. If not OK, repair the
shorted sensor return circuit as required.
(5) Check for continuity between the ambient tem-
perature sensor signal circuit cavity of the 22-way
BCM wire harness connector and a good ground.
There should be no continuity. If OK, refer toDiag-
nosis and Testing - Electronic Vehicle Informa-
tion Centerin this group. If not OK, repair the
shorted ambient temperature sensor signal circuit as
required.
REMOVAL
(1) Disconnect and isolate the battery negative
cable.
8M - 12 MESSAGE SYSTEMSWJ
Page 500 of 2199
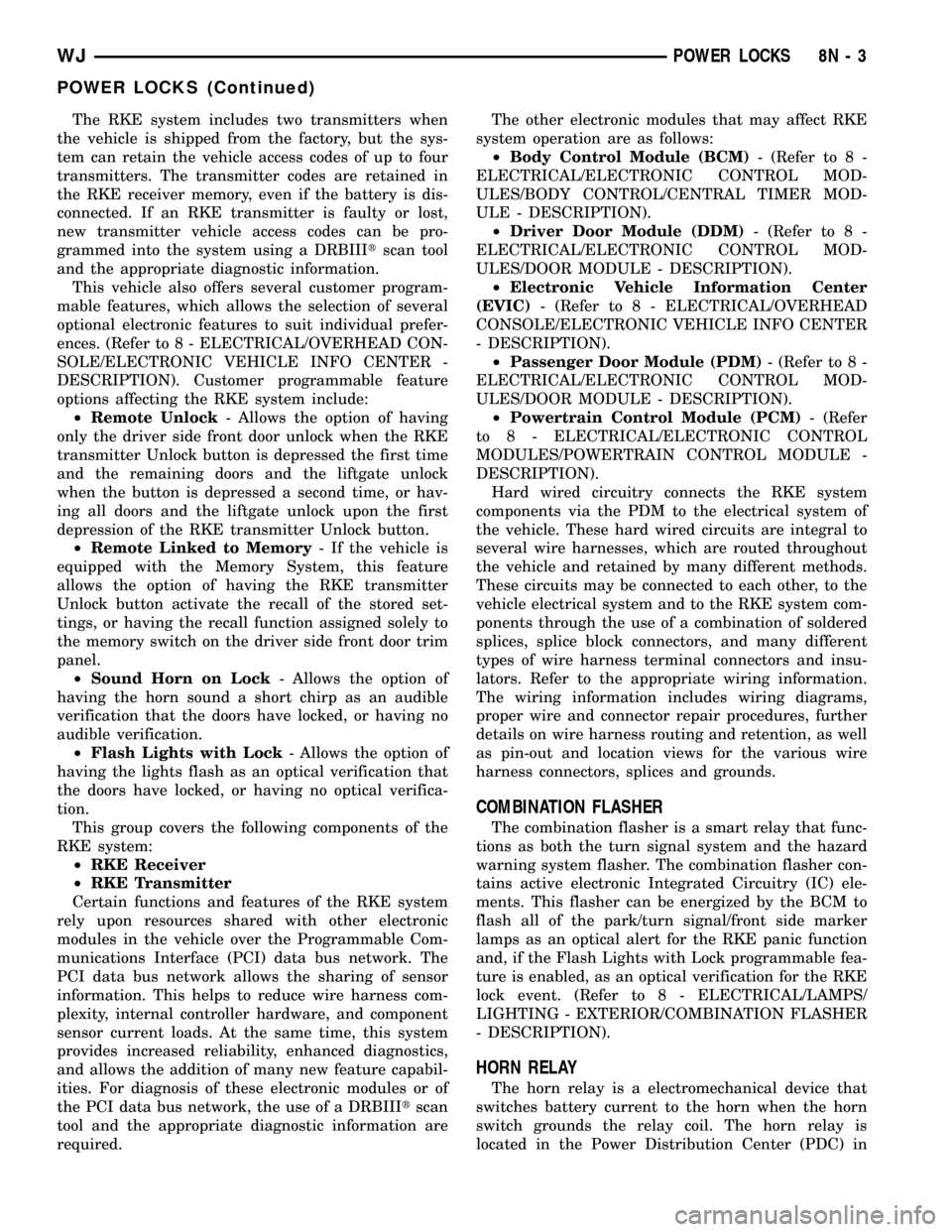
The RKE system includes two transmitters when
the vehicle is shipped from the factory, but the sys-
tem can retain the vehicle access codes of up to four
transmitters. The transmitter codes are retained in
the RKE receiver memory, even if the battery is dis-
connected. If an RKE transmitter is faulty or lost,
new transmitter vehicle access codes can be pro-
grammed into the system using a DRBIIItscan tool
and the appropriate diagnostic information.
This vehicle also offers several customer program-
mable features, which allows the selection of several
optional electronic features to suit individual prefer-
ences. (Refer to 8 - ELECTRICAL/OVERHEAD CON-
SOLE/ELECTRONIC VEHICLE INFO CENTER -
DESCRIPTION). Customer programmable feature
options affecting the RKE system include:
²Remote Unlock- Allows the option of having
only the driver side front door unlock when the RKE
transmitter Unlock button is depressed the first time
and the remaining doors and the liftgate unlock
when the button is depressed a second time, or hav-
ing all doors and the liftgate unlock upon the first
depression of the RKE transmitter Unlock button.
²Remote Linked to Memory- If the vehicle is
equipped with the Memory System, this feature
allows the option of having the RKE transmitter
Unlock button activate the recall of the stored set-
tings, or having the recall function assigned solely to
the memory switch on the driver side front door trim
panel.
²Sound Horn on Lock- Allows the option of
having the horn sound a short chirp as an audible
verification that the doors have locked, or having no
audible verification.
²Flash Lights with Lock- Allows the option of
having the lights flash as an optical verification that
the doors have locked, or having no optical verifica-
tion.
This group covers the following components of the
RKE system:
²RKE Receiver
²RKE Transmitter
Certain functions and features of the RKE system
rely upon resources shared with other electronic
modules in the vehicle over the Programmable Com-
munications Interface (PCI) data bus network. The
PCI data bus network allows the sharing of sensor
information. This helps to reduce wire harness com-
plexity, internal controller hardware, and component
sensor current loads. At the same time, this system
provides increased reliability, enhanced diagnostics,
and allows the addition of many new feature capabil-
ities. For diagnosis of these electronic modules or of
the PCI data bus network, the use of a DRBIIItscan
tool and the appropriate diagnostic information are
required.The other electronic modules that may affect RKE
system operation are as follows:
²Body Control Module (BCM)- (Refer to 8 -
ELECTRICAL/ELECTRONIC CONTROL MOD-
ULES/BODY CONTROL/CENTRAL TIMER MOD-
ULE - DESCRIPTION).
²Driver Door Module (DDM)- (Refer to 8 -
ELECTRICAL/ELECTRONIC CONTROL MOD-
ULES/DOOR MODULE - DESCRIPTION).
²Electronic Vehicle Information Center
(EVIC)- (Refer to 8 - ELECTRICAL/OVERHEAD
CONSOLE/ELECTRONIC VEHICLE INFO CENTER
- DESCRIPTION).
²Passenger Door Module (PDM)- (Refer to 8 -
ELECTRICAL/ELECTRONIC CONTROL MOD-
ULES/DOOR MODULE - DESCRIPTION).
²Powertrain Control Module (PCM)- (Refer
to 8 - ELECTRICAL/ELECTRONIC CONTROL
MODULES/POWERTRAIN CONTROL MODULE -
DESCRIPTION).
Hard wired circuitry connects the RKE system
components via the PDM to the electrical system of
the vehicle. These hard wired circuits are integral to
several wire harnesses, which are routed throughout
the vehicle and retained by many different methods.
These circuits may be connected to each other, to the
vehicle electrical system and to the RKE system com-
ponents through the use of a combination of soldered
splices, splice block connectors, and many different
types of wire harness terminal connectors and insu-
lators. Refer to the appropriate wiring information.
The wiring information includes wiring diagrams,
proper wire and connector repair procedures, further
details on wire harness routing and retention, as well
as pin-out and location views for the various wire
harness connectors, splices and grounds.
COMBINATION FLASHER
The combination flasher is a smart relay that func-
tions as both the turn signal system and the hazard
warning system flasher. The combination flasher con-
tains active electronic Integrated Circuitry (IC) ele-
ments. This flasher can be energized by the BCM to
flash all of the park/turn signal/front side marker
lamps as an optical alert for the RKE panic function
and, if the Flash Lights with Lock programmable fea-
ture is enabled, as an optical verification for the RKE
lock event. (Refer to 8 - ELECTRICAL/LAMPS/
LIGHTING - EXTERIOR/COMBINATION FLASHER
- DESCRIPTION).
HORN RELAY
The horn relay is a electromechanical device that
switches battery current to the horn when the horn
switch grounds the relay coil. The horn relay is
located in the Power Distribution Center (PDC) in
WJPOWER LOCKS 8N - 3
POWER LOCKS (Continued)
Page 502 of 2199
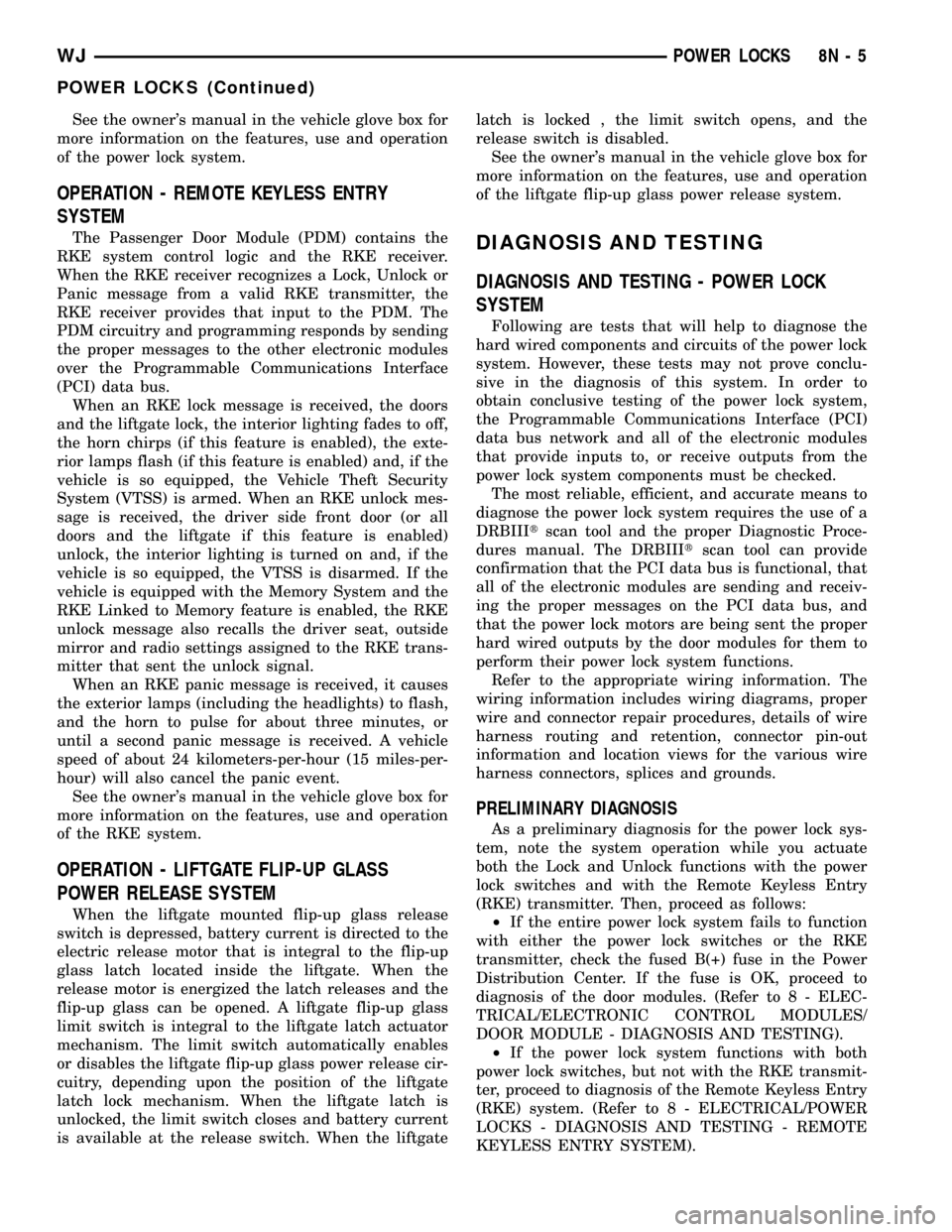
See the owner's manual in the vehicle glove box for
more information on the features, use and operation
of the power lock system.
OPERATION - REMOTE KEYLESS ENTRY
SYSTEM
The Passenger Door Module (PDM) contains the
RKE system control logic and the RKE receiver.
When the RKE receiver recognizes a Lock, Unlock or
Panic message from a valid RKE transmitter, the
RKE receiver provides that input to the PDM. The
PDM circuitry and programming responds by sending
the proper messages to the other electronic modules
over the Programmable Communications Interface
(PCI) data bus.
When an RKE lock message is received, the doors
and the liftgate lock, the interior lighting fades to off,
the horn chirps (if this feature is enabled), the exte-
rior lamps flash (if this feature is enabled) and, if the
vehicle is so equipped, the Vehicle Theft Security
System (VTSS) is armed. When an RKE unlock mes-
sage is received, the driver side front door (or all
doors and the liftgate if this feature is enabled)
unlock, the interior lighting is turned on and, if the
vehicle is so equipped, the VTSS is disarmed. If the
vehicle is equipped with the Memory System and the
RKE Linked to Memory feature is enabled, the RKE
unlock message also recalls the driver seat, outside
mirror and radio settings assigned to the RKE trans-
mitter that sent the unlock signal.
When an RKE panic message is received, it causes
the exterior lamps (including the headlights) to flash,
and the horn to pulse for about three minutes, or
until a second panic message is received. A vehicle
speed of about 24 kilometers-per-hour (15 miles-per-
hour) will also cancel the panic event.
See the owner's manual in the vehicle glove box for
more information on the features, use and operation
of the RKE system.
OPERATION - LIFTGATE FLIP-UP GLASS
POWER RELEASE SYSTEM
When the liftgate mounted flip-up glass release
switch is depressed, battery current is directed to the
electric release motor that is integral to the flip-up
glass latch located inside the liftgate. When the
release motor is energized the latch releases and the
flip-up glass can be opened. A liftgate flip-up glass
limit switch is integral to the liftgate latch actuator
mechanism. The limit switch automatically enables
or disables the liftgate flip-up glass power release cir-
cuitry, depending upon the position of the liftgate
latch lock mechanism. When the liftgate latch is
unlocked, the limit switch closes and battery current
is available at the release switch. When the liftgatelatch is locked , the limit switch opens, and the
release switch is disabled.
See the owner's manual in the vehicle glove box for
more information on the features, use and operation
of the liftgate flip-up glass power release system.
DIAGNOSIS AND TESTING
DIAGNOSIS AND TESTING - POWER LOCK
SYSTEM
Following are tests that will help to diagnose the
hard wired components and circuits of the power lock
system. However, these tests may not prove conclu-
sive in the diagnosis of this system. In order to
obtain conclusive testing of the power lock system,
the Programmable Communications Interface (PCI)
data bus network and all of the electronic modules
that provide inputs to, or receive outputs from the
power lock system components must be checked.
The most reliable, efficient, and accurate means to
diagnose the power lock system requires the use of a
DRBIIItscan tool and the proper Diagnostic Proce-
dures manual. The DRBIIItscan tool can provide
confirmation that the PCI data bus is functional, that
all of the electronic modules are sending and receiv-
ing the proper messages on the PCI data bus, and
that the power lock motors are being sent the proper
hard wired outputs by the door modules for them to
perform their power lock system functions.
Refer to the appropriate wiring information. The
wiring information includes wiring diagrams, proper
wire and connector repair procedures, details of wire
harness routing and retention, connector pin-out
information and location views for the various wire
harness connectors, splices and grounds.
PRELIMINARY DIAGNOSIS
As a preliminary diagnosis for the power lock sys-
tem, note the system operation while you actuate
both the Lock and Unlock functions with the power
lock switches and with the Remote Keyless Entry
(RKE) transmitter. Then, proceed as follows:
²If the entire power lock system fails to function
with either the power lock switches or the RKE
transmitter, check the fused B(+) fuse in the Power
Distribution Center. If the fuse is OK, proceed to
diagnosis of the door modules. (Refer to 8 - ELEC-
TRICAL/ELECTRONIC CONTROL MODULES/
DOOR MODULE - DIAGNOSIS AND TESTING).
²If the power lock system functions with both
power lock switches, but not with the RKE transmit-
ter, proceed to diagnosis of the Remote Keyless Entry
(RKE) system. (Refer to 8 - ELECTRICAL/POWER
LOCKS - DIAGNOSIS AND TESTING - REMOTE
KEYLESS ENTRY SYSTEM).
WJPOWER LOCKS 8N - 5
POWER LOCKS (Continued)
Page 503 of 2199
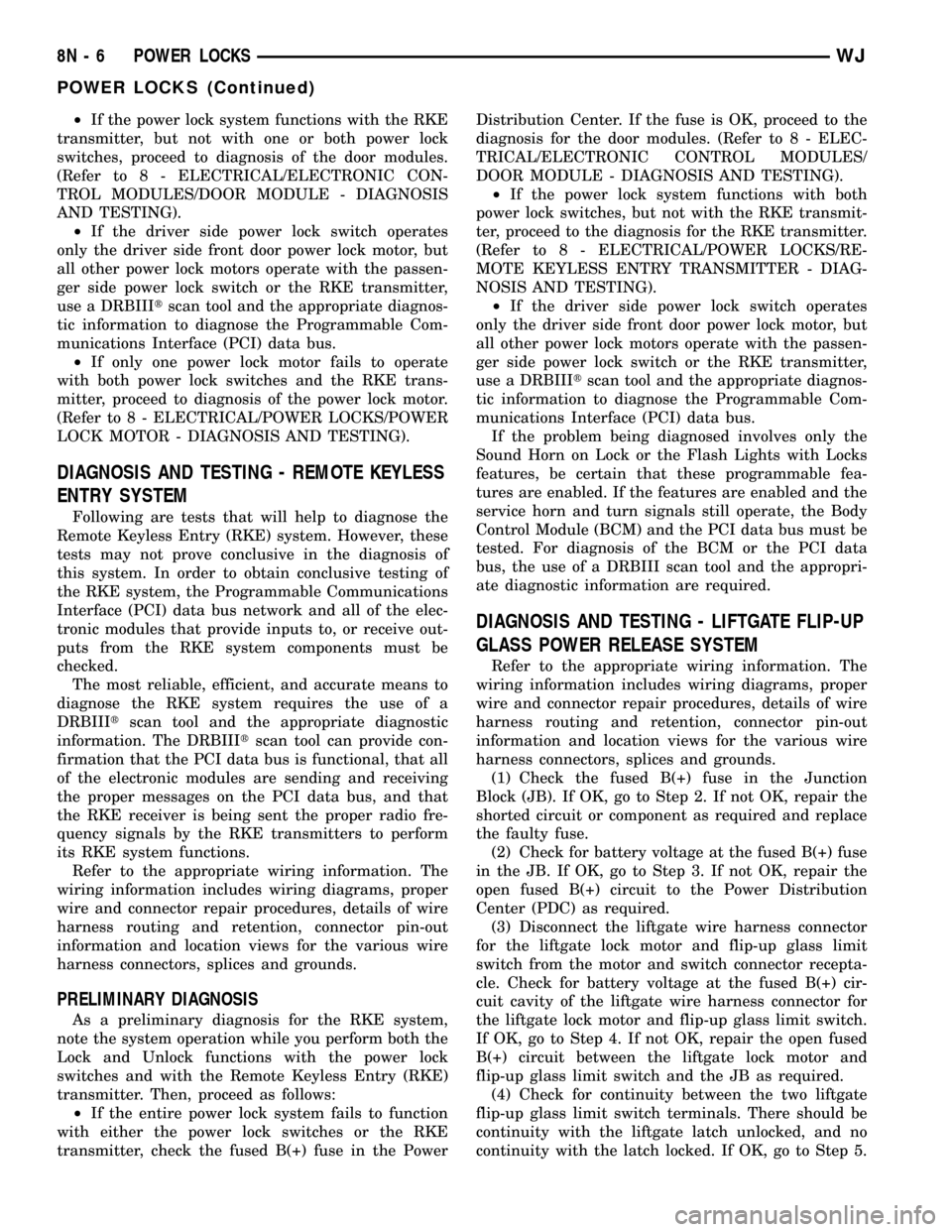
²If the power lock system functions with the RKE
transmitter, but not with one or both power lock
switches, proceed to diagnosis of the door modules.
(Refer to 8 - ELECTRICAL/ELECTRONIC CON-
TROL MODULES/DOOR MODULE - DIAGNOSIS
AND TESTING).
²If the driver side power lock switch operates
only the driver side front door power lock motor, but
all other power lock motors operate with the passen-
ger side power lock switch or the RKE transmitter,
use a DRBIIItscan tool and the appropriate diagnos-
tic information to diagnose the Programmable Com-
munications Interface (PCI) data bus.
²If only one power lock motor fails to operate
with both power lock switches and the RKE trans-
mitter, proceed to diagnosis of the power lock motor.
(Refer to 8 - ELECTRICAL/POWER LOCKS/POWER
LOCK MOTOR - DIAGNOSIS AND TESTING).
DIAGNOSIS AND TESTING - REMOTE KEYLESS
ENTRY SYSTEM
Following are tests that will help to diagnose the
Remote Keyless Entry (RKE) system. However, these
tests may not prove conclusive in the diagnosis of
this system. In order to obtain conclusive testing of
the RKE system, the Programmable Communications
Interface (PCI) data bus network and all of the elec-
tronic modules that provide inputs to, or receive out-
puts from the RKE system components must be
checked.
The most reliable, efficient, and accurate means to
diagnose the RKE system requires the use of a
DRBIIItscan tool and the appropriate diagnostic
information. The DRBIIItscan tool can provide con-
firmation that the PCI data bus is functional, that all
of the electronic modules are sending and receiving
the proper messages on the PCI data bus, and that
the RKE receiver is being sent the proper radio fre-
quency signals by the RKE transmitters to perform
its RKE system functions.
Refer to the appropriate wiring information. The
wiring information includes wiring diagrams, proper
wire and connector repair procedures, details of wire
harness routing and retention, connector pin-out
information and location views for the various wire
harness connectors, splices and grounds.
PRELIMINARY DIAGNOSIS
As a preliminary diagnosis for the RKE system,
note the system operation while you perform both the
Lock and Unlock functions with the power lock
switches and with the Remote Keyless Entry (RKE)
transmitter. Then, proceed as follows:
²If the entire power lock system fails to function
with either the power lock switches or the RKE
transmitter, check the fused B(+) fuse in the PowerDistribution Center. If the fuse is OK, proceed to the
diagnosis for the door modules. (Refer to 8 - ELEC-
TRICAL/ELECTRONIC CONTROL MODULES/
DOOR MODULE - DIAGNOSIS AND TESTING).
²If the power lock system functions with both
power lock switches, but not with the RKE transmit-
ter, proceed to the diagnosis for the RKE transmitter.
(Refer to 8 - ELECTRICAL/POWER LOCKS/RE-
MOTE KEYLESS ENTRY TRANSMITTER - DIAG-
NOSIS AND TESTING).
²If the driver side power lock switch operates
only the driver side front door power lock motor, but
all other power lock motors operate with the passen-
ger side power lock switch or the RKE transmitter,
use a DRBIIItscan tool and the appropriate diagnos-
tic information to diagnose the Programmable Com-
munications Interface (PCI) data bus.
If the problem being diagnosed involves only the
Sound Horn on Lock or the Flash Lights with Locks
features, be certain that these programmable fea-
tures are enabled. If the features are enabled and the
service horn and turn signals still operate, the Body
Control Module (BCM) and the PCI data bus must be
tested. For diagnosis of the BCM or the PCI data
bus, the use of a DRBIII scan tool and the appropri-
ate diagnostic information are required.
DIAGNOSIS AND TESTING - LIFTGATE FLIP-UP
GLASS POWER RELEASE SYSTEM
Refer to the appropriate wiring information. The
wiring information includes wiring diagrams, proper
wire and connector repair procedures, details of wire
harness routing and retention, connector pin-out
information and location views for the various wire
harness connectors, splices and grounds.
(1) Check the fused B(+) fuse in the Junction
Block (JB). If OK, go to Step 2. If not OK, repair the
shorted circuit or component as required and replace
the faulty fuse.
(2) Check for battery voltage at the fused B(+) fuse
in the JB. If OK, go to Step 3. If not OK, repair the
open fused B(+) circuit to the Power Distribution
Center (PDC) as required.
(3) Disconnect the liftgate wire harness connector
for the liftgate lock motor and flip-up glass limit
switch from the motor and switch connector recepta-
cle. Check for battery voltage at the fused B(+) cir-
cuit cavity of the liftgate wire harness connector for
the liftgate lock motor and flip-up glass limit switch.
If OK, go to Step 4. If not OK, repair the open fused
B(+) circuit between the liftgate lock motor and
flip-up glass limit switch and the JB as required.
(4) Check for continuity between the two liftgate
flip-up glass limit switch terminals. There should be
continuity with the liftgate latch unlocked, and no
continuity with the latch locked. If OK, go to Step 5.
8N - 6 POWER LOCKSWJ
POWER LOCKS (Continued)
Page 505 of 2199
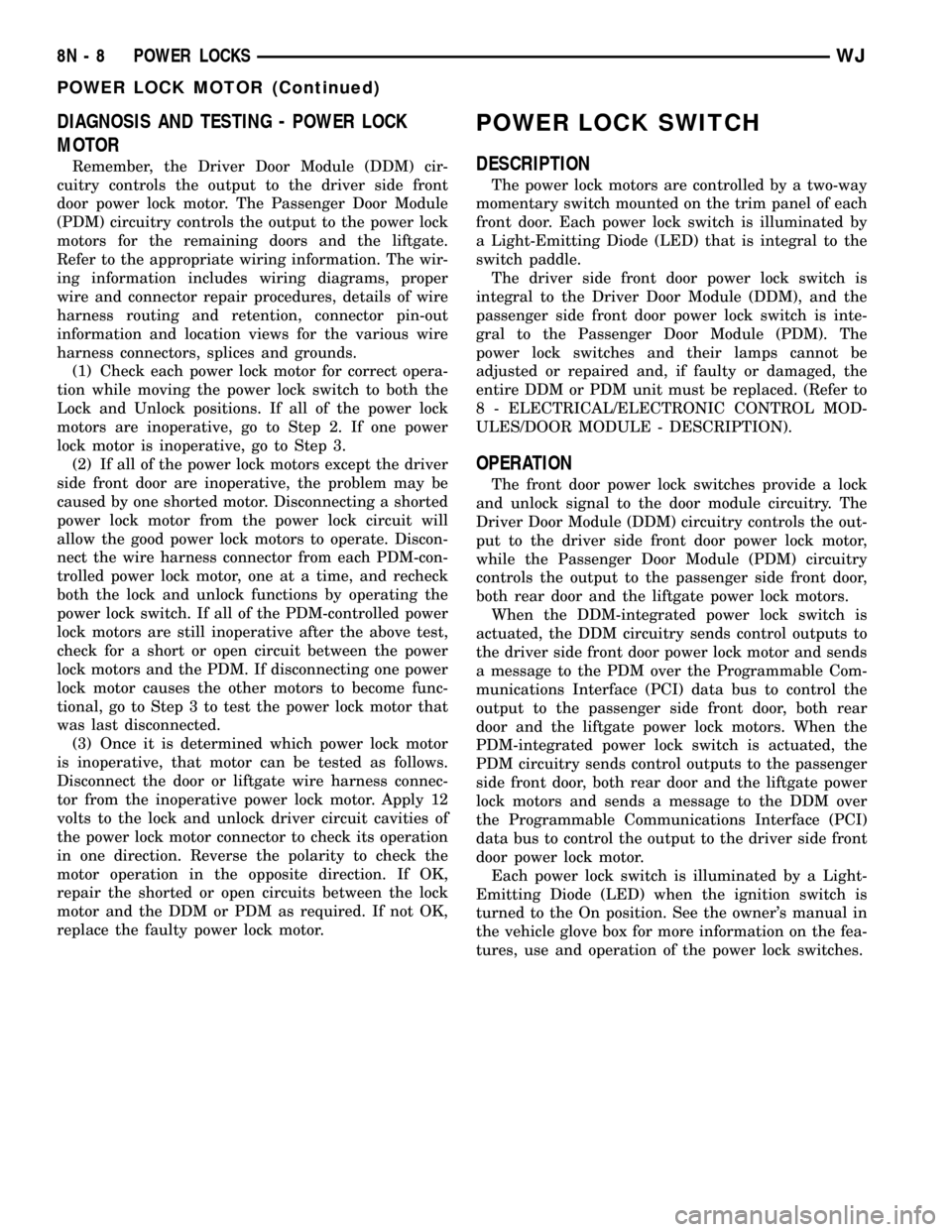
DIAGNOSIS AND TESTING - POWER LOCK
MOTOR
Remember, the Driver Door Module (DDM) cir-
cuitry controls the output to the driver side front
door power lock motor. The Passenger Door Module
(PDM) circuitry controls the output to the power lock
motors for the remaining doors and the liftgate.
Refer to the appropriate wiring information. The wir-
ing information includes wiring diagrams, proper
wire and connector repair procedures, details of wire
harness routing and retention, connector pin-out
information and location views for the various wire
harness connectors, splices and grounds.
(1) Check each power lock motor for correct opera-
tion while moving the power lock switch to both the
Lock and Unlock positions. If all of the power lock
motors are inoperative, go to Step 2. If one power
lock motor is inoperative, go to Step 3.
(2) If all of the power lock motors except the driver
side front door are inoperative, the problem may be
caused by one shorted motor. Disconnecting a shorted
power lock motor from the power lock circuit will
allow the good power lock motors to operate. Discon-
nect the wire harness connector from each PDM-con-
trolled power lock motor, one at a time, and recheck
both the lock and unlock functions by operating the
power lock switch. If all of the PDM-controlled power
lock motors are still inoperative after the above test,
check for a short or open circuit between the power
lock motors and the PDM. If disconnecting one power
lock motor causes the other motors to become func-
tional, go to Step 3 to test the power lock motor that
was last disconnected.
(3) Once it is determined which power lock motor
is inoperative, that motor can be tested as follows.
Disconnect the door or liftgate wire harness connec-
tor from the inoperative power lock motor. Apply 12
volts to the lock and unlock driver circuit cavities of
the power lock motor connector to check its operation
in one direction. Reverse the polarity to check the
motor operation in the opposite direction. If OK,
repair the shorted or open circuits between the lock
motor and the DDM or PDM as required. If not OK,
replace the faulty power lock motor.
POWER LOCK SWITCH
DESCRIPTION
The power lock motors are controlled by a two-way
momentary switch mounted on the trim panel of each
front door. Each power lock switch is illuminated by
a Light-Emitting Diode (LED) that is integral to the
switch paddle.
The driver side front door power lock switch is
integral to the Driver Door Module (DDM), and the
passenger side front door power lock switch is inte-
gral to the Passenger Door Module (PDM). The
power lock switches and their lamps cannot be
adjusted or repaired and, if faulty or damaged, the
entire DDM or PDM unit must be replaced. (Refer to
8 - ELECTRICAL/ELECTRONIC CONTROL MOD-
ULES/DOOR MODULE - DESCRIPTION).
OPERATION
The front door power lock switches provide a lock
and unlock signal to the door module circuitry. The
Driver Door Module (DDM) circuitry controls the out-
put to the driver side front door power lock motor,
while the Passenger Door Module (PDM) circuitry
controls the output to the passenger side front door,
both rear door and the liftgate power lock motors.
When the DDM-integrated power lock switch is
actuated, the DDM circuitry sends control outputs to
the driver side front door power lock motor and sends
a message to the PDM over the Programmable Com-
munications Interface (PCI) data bus to control the
output to the passenger side front door, both rear
door and the liftgate power lock motors. When the
PDM-integrated power lock switch is actuated, the
PDM circuitry sends control outputs to the passenger
side front door, both rear door and the liftgate power
lock motors and sends a message to the DDM over
the Programmable Communications Interface (PCI)
data bus to control the output to the driver side front
door power lock motor.
Each power lock switch is illuminated by a Light-
Emitting Diode (LED) when the ignition switch is
turned to the On position. See the owner's manual in
the vehicle glove box for more information on the fea-
tures, use and operation of the power lock switches.
8N - 8 POWER LOCKSWJ
POWER LOCK MOTOR (Continued)
Page 510 of 2199
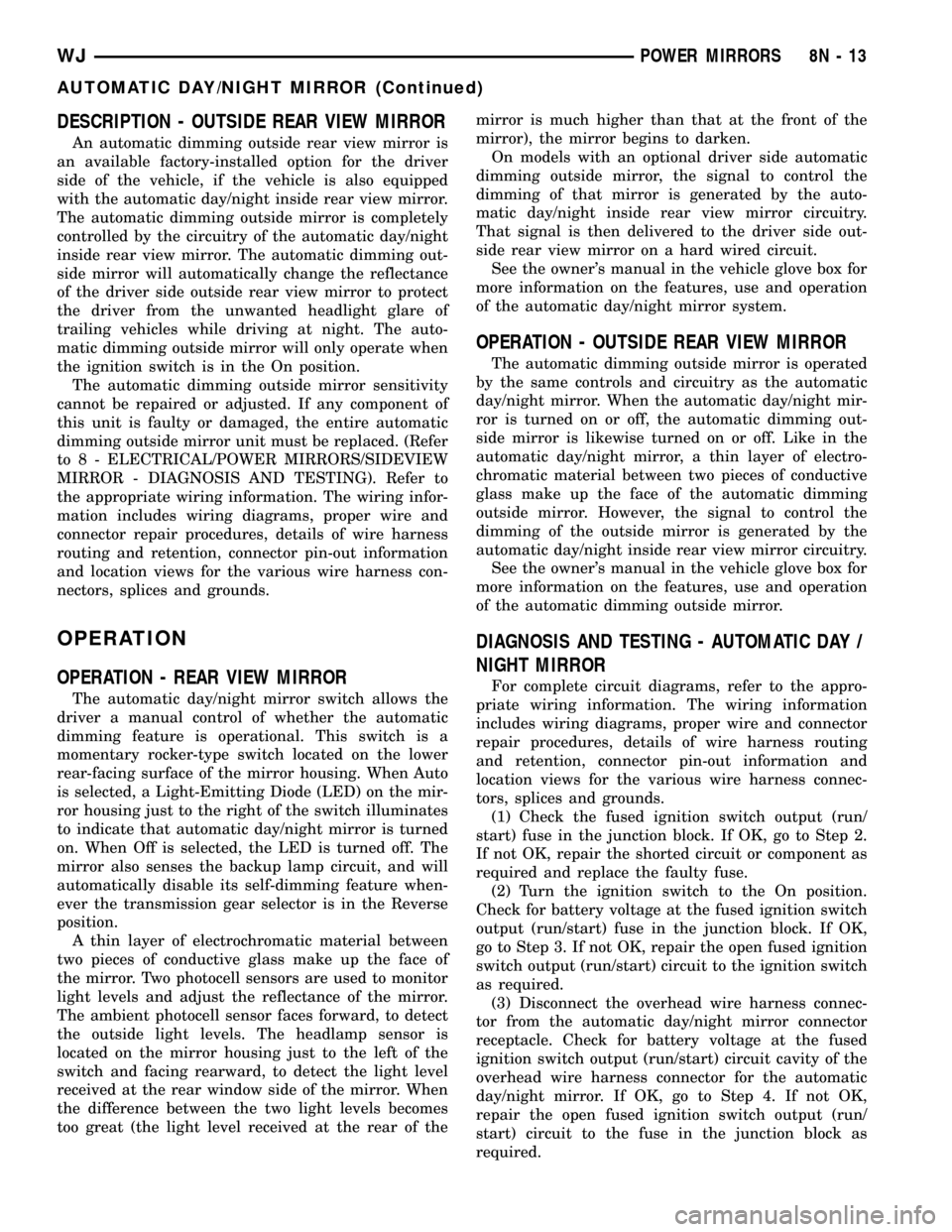
DESCRIPTION - OUTSIDE REAR VIEW MIRROR
An automatic dimming outside rear view mirror is
an available factory-installed option for the driver
side of the vehicle, if the vehicle is also equipped
with the automatic day/night inside rear view mirror.
The automatic dimming outside mirror is completely
controlled by the circuitry of the automatic day/night
inside rear view mirror. The automatic dimming out-
side mirror will automatically change the reflectance
of the driver side outside rear view mirror to protect
the driver from the unwanted headlight glare of
trailing vehicles while driving at night. The auto-
matic dimming outside mirror will only operate when
the ignition switch is in the On position.
The automatic dimming outside mirror sensitivity
cannot be repaired or adjusted. If any component of
this unit is faulty or damaged, the entire automatic
dimming outside mirror unit must be replaced. (Refer
to 8 - ELECTRICAL/POWER MIRRORS/SIDEVIEW
MIRROR - DIAGNOSIS AND TESTING). Refer to
the appropriate wiring information. The wiring infor-
mation includes wiring diagrams, proper wire and
connector repair procedures, details of wire harness
routing and retention, connector pin-out information
and location views for the various wire harness con-
nectors, splices and grounds.
OPERATION
OPERATION - REAR VIEW MIRROR
The automatic day/night mirror switch allows the
driver a manual control of whether the automatic
dimming feature is operational. This switch is a
momentary rocker-type switch located on the lower
rear-facing surface of the mirror housing. When Auto
is selected, a Light-Emitting Diode (LED) on the mir-
ror housing just to the right of the switch illuminates
to indicate that automatic day/night mirror is turned
on. When Off is selected, the LED is turned off. The
mirror also senses the backup lamp circuit, and will
automatically disable its self-dimming feature when-
ever the transmission gear selector is in the Reverse
position.
A thin layer of electrochromatic material between
two pieces of conductive glass make up the face of
the mirror. Two photocell sensors are used to monitor
light levels and adjust the reflectance of the mirror.
The ambient photocell sensor faces forward, to detect
the outside light levels. The headlamp sensor is
located on the mirror housing just to the left of the
switch and facing rearward, to detect the light level
received at the rear window side of the mirror. When
the difference between the two light levels becomes
too great (the light level received at the rear of themirror is much higher than that at the front of the
mirror), the mirror begins to darken.
On models with an optional driver side automatic
dimming outside mirror, the signal to control the
dimming of that mirror is generated by the auto-
matic day/night inside rear view mirror circuitry.
That signal is then delivered to the driver side out-
side rear view mirror on a hard wired circuit.
See the owner's manual in the vehicle glove box for
more information on the features, use and operation
of the automatic day/night mirror system.
OPERATION - OUTSIDE REAR VIEW MIRROR
The automatic dimming outside mirror is operated
by the same controls and circuitry as the automatic
day/night mirror. When the automatic day/night mir-
ror is turned on or off, the automatic dimming out-
side mirror is likewise turned on or off. Like in the
automatic day/night mirror, a thin layer of electro-
chromatic material between two pieces of conductive
glass make up the face of the automatic dimming
outside mirror. However, the signal to control the
dimming of the outside mirror is generated by the
automatic day/night inside rear view mirror circuitry.
See the owner's manual in the vehicle glove box for
more information on the features, use and operation
of the automatic dimming outside mirror.
DIAGNOSIS AND TESTING - AUTOMATIC DAY /
NIGHT MIRROR
For complete circuit diagrams, refer to the appro-
priate wiring information. The wiring information
includes wiring diagrams, proper wire and connector
repair procedures, details of wire harness routing
and retention, connector pin-out information and
location views for the various wire harness connec-
tors, splices and grounds.
(1) Check the fused ignition switch output (run/
start) fuse in the junction block. If OK, go to Step 2.
If not OK, repair the shorted circuit or component as
required and replace the faulty fuse.
(2) Turn the ignition switch to the On position.
Check for battery voltage at the fused ignition switch
output (run/start) fuse in the junction block. If OK,
go to Step 3. If not OK, repair the open fused ignition
switch output (run/start) circuit to the ignition switch
as required.
(3) Disconnect the overhead wire harness connec-
tor from the automatic day/night mirror connector
receptacle. Check for battery voltage at the fused
ignition switch output (run/start) circuit cavity of the
overhead wire harness connector for the automatic
day/night mirror. If OK, go to Step 4. If not OK,
repair the open fused ignition switch output (run/
start) circuit to the fuse in the junction block as
required.
WJPOWER MIRRORS 8N - 13
AUTOMATIC DAY/NIGHT MIRROR (Continued)
Page 514 of 2199
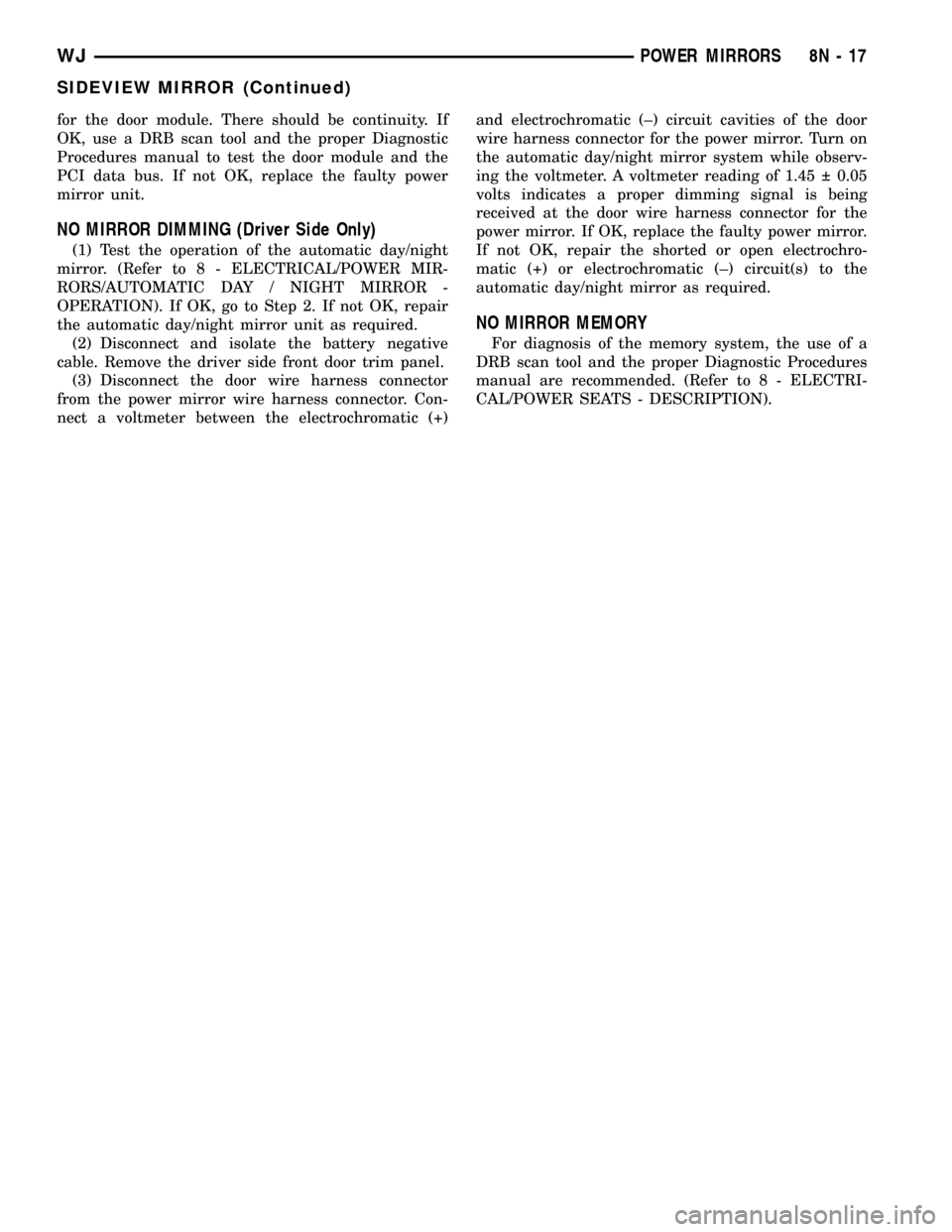
for the door module. There should be continuity. If
OK, use a DRB scan tool and the proper Diagnostic
Procedures manual to test the door module and the
PCI data bus. If not OK, replace the faulty power
mirror unit.
NO MIRROR DIMMING (Driver Side Only)
(1) Test the operation of the automatic day/night
mirror. (Refer to 8 - ELECTRICAL/POWER MIR-
RORS/AUTOMATIC DAY / NIGHT MIRROR -
OPERATION). If OK, go to Step 2. If not OK, repair
the automatic day/night mirror unit as required.
(2) Disconnect and isolate the battery negative
cable. Remove the driver side front door trim panel.
(3) Disconnect the door wire harness connector
from the power mirror wire harness connector. Con-
nect a voltmeter between the electrochromatic (+)and electrochromatic (±) circuit cavities of the door
wire harness connector for the power mirror. Turn on
the automatic day/night mirror system while observ-
ing the voltmeter. A voltmeter reading of 1.45 0.05
volts indicates a proper dimming signal is being
received at the door wire harness connector for the
power mirror. If OK, replace the faulty power mirror.
If not OK, repair the shorted or open electrochro-
matic (+) or electrochromatic (±) circuit(s) to the
automatic day/night mirror as required.
NO MIRROR MEMORY
For diagnosis of the memory system, the use of a
DRB scan tool and the proper Diagnostic Procedures
manual are recommended. (Refer to 8 - ELECTRI-
CAL/POWER SEATS - DESCRIPTION).
WJPOWER MIRRORS 8N - 17
SIDEVIEW MIRROR (Continued)
Page 541 of 2199
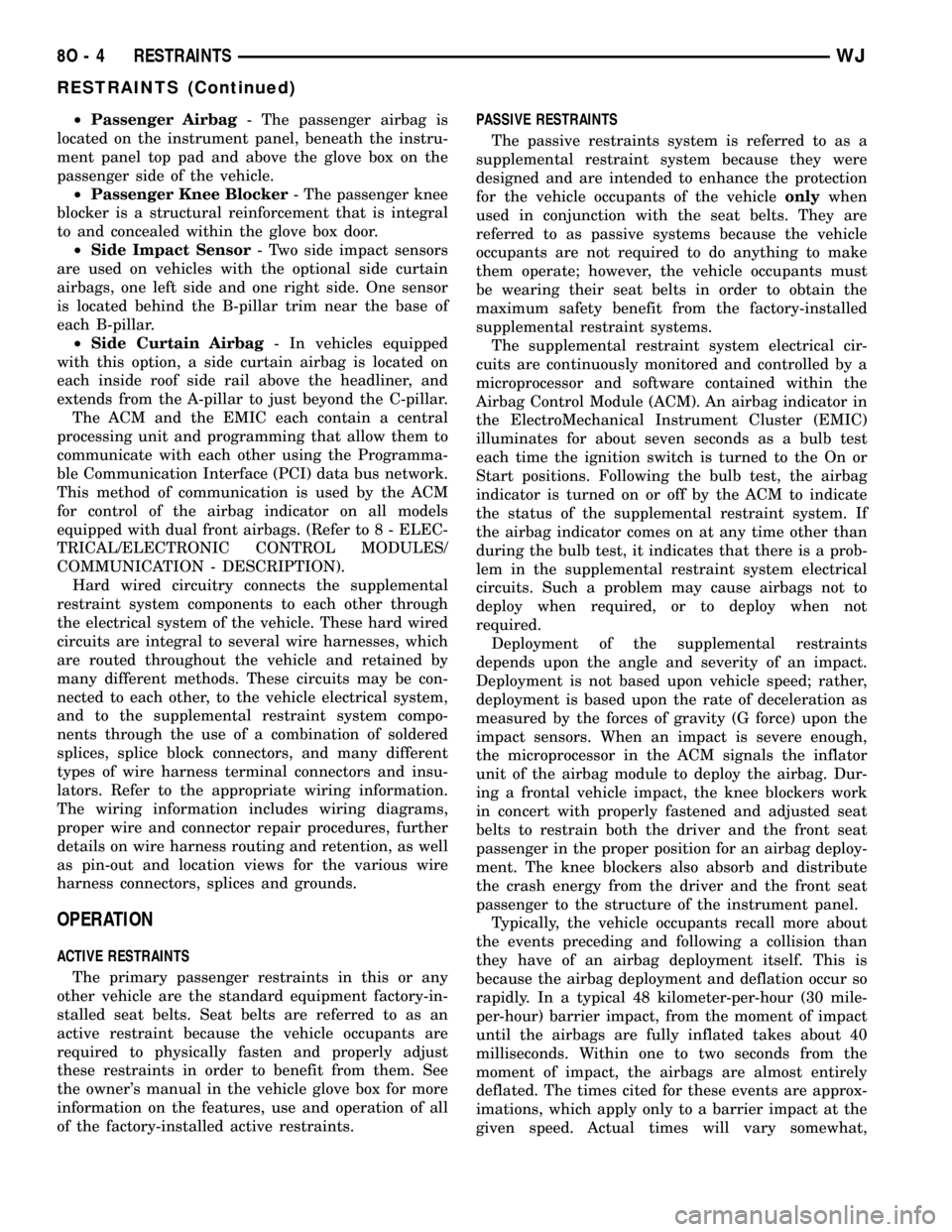
²Passenger Airbag- The passenger airbag is
located on the instrument panel, beneath the instru-
ment panel top pad and above the glove box on the
passenger side of the vehicle.
²Passenger Knee Blocker- The passenger knee
blocker is a structural reinforcement that is integral
to and concealed within the glove box door.
²Side Impact Sensor- Two side impact sensors
are used on vehicles with the optional side curtain
airbags, one left side and one right side. One sensor
is located behind the B-pillar trim near the base of
each B-pillar.
²Side Curtain Airbag- In vehicles equipped
with this option, a side curtain airbag is located on
each inside roof side rail above the headliner, and
extends from the A-pillar to just beyond the C-pillar.
The ACM and the EMIC each contain a central
processing unit and programming that allow them to
communicate with each other using the Programma-
ble Communication Interface (PCI) data bus network.
This method of communication is used by the ACM
for control of the airbag indicator on all models
equipped with dual front airbags. (Refer to 8 - ELEC-
TRICAL/ELECTRONIC CONTROL MODULES/
COMMUNICATION - DESCRIPTION).
Hard wired circuitry connects the supplemental
restraint system components to each other through
the electrical system of the vehicle. These hard wired
circuits are integral to several wire harnesses, which
are routed throughout the vehicle and retained by
many different methods. These circuits may be con-
nected to each other, to the vehicle electrical system,
and to the supplemental restraint system compo-
nents through the use of a combination of soldered
splices, splice block connectors, and many different
types of wire harness terminal connectors and insu-
lators. Refer to the appropriate wiring information.
The wiring information includes wiring diagrams,
proper wire and connector repair procedures, further
details on wire harness routing and retention, as well
as pin-out and location views for the various wire
harness connectors, splices and grounds.
OPERATION
ACTIVE RESTRAINTS
The primary passenger restraints in this or any
other vehicle are the standard equipment factory-in-
stalled seat belts. Seat belts are referred to as an
active restraint because the vehicle occupants are
required to physically fasten and properly adjust
these restraints in order to benefit from them. See
the owner's manual in the vehicle glove box for more
information on the features, use and operation of all
of the factory-installed active restraints.PASSIVE RESTRAINTS
The passive restraints system is referred to as a
supplemental restraint system because they were
designed and are intended to enhance the protection
for the vehicle occupants of the vehicleonlywhen
used in conjunction with the seat belts. They are
referred to as passive systems because the vehicle
occupants are not required to do anything to make
them operate; however, the vehicle occupants must
be wearing their seat belts in order to obtain the
maximum safety benefit from the factory-installed
supplemental restraint systems.
The supplemental restraint system electrical cir-
cuits are continuously monitored and controlled by a
microprocessor and software contained within the
Airbag Control Module (ACM). An airbag indicator in
the ElectroMechanical Instrument Cluster (EMIC)
illuminates for about seven seconds as a bulb test
each time the ignition switch is turned to the On or
Start positions. Following the bulb test, the airbag
indicator is turned on or off by the ACM to indicate
the status of the supplemental restraint system. If
the airbag indicator comes on at any time other than
during the bulb test, it indicates that there is a prob-
lem in the supplemental restraint system electrical
circuits. Such a problem may cause airbags not to
deploy when required, or to deploy when not
required.
Deployment of the supplemental restraints
depends upon the angle and severity of an impact.
Deployment is not based upon vehicle speed; rather,
deployment is based upon the rate of deceleration as
measured by the forces of gravity (G force) upon the
impact sensors. When an impact is severe enough,
the microprocessor in the ACM signals the inflator
unit of the airbag module to deploy the airbag. Dur-
ing a frontal vehicle impact, the knee blockers work
in concert with properly fastened and adjusted seat
belts to restrain both the driver and the front seat
passenger in the proper position for an airbag deploy-
ment. The knee blockers also absorb and distribute
the crash energy from the driver and the front seat
passenger to the structure of the instrument panel.
Typically, the vehicle occupants recall more about
the events preceding and following a collision than
they have of an airbag deployment itself. This is
because the airbag deployment and deflation occur so
rapidly. In a typical 48 kilometer-per-hour (30 mile-
per-hour) barrier impact, from the moment of impact
until the airbags are fully inflated takes about 40
milliseconds. Within one to two seconds from the
moment of impact, the airbags are almost entirely
deflated. The times cited for these events are approx-
imations, which apply only to a barrier impact at the
given speed. Actual times will vary somewhat,
8O - 4 RESTRAINTSWJ
RESTRAINTS (Continued)
Page 543 of 2199
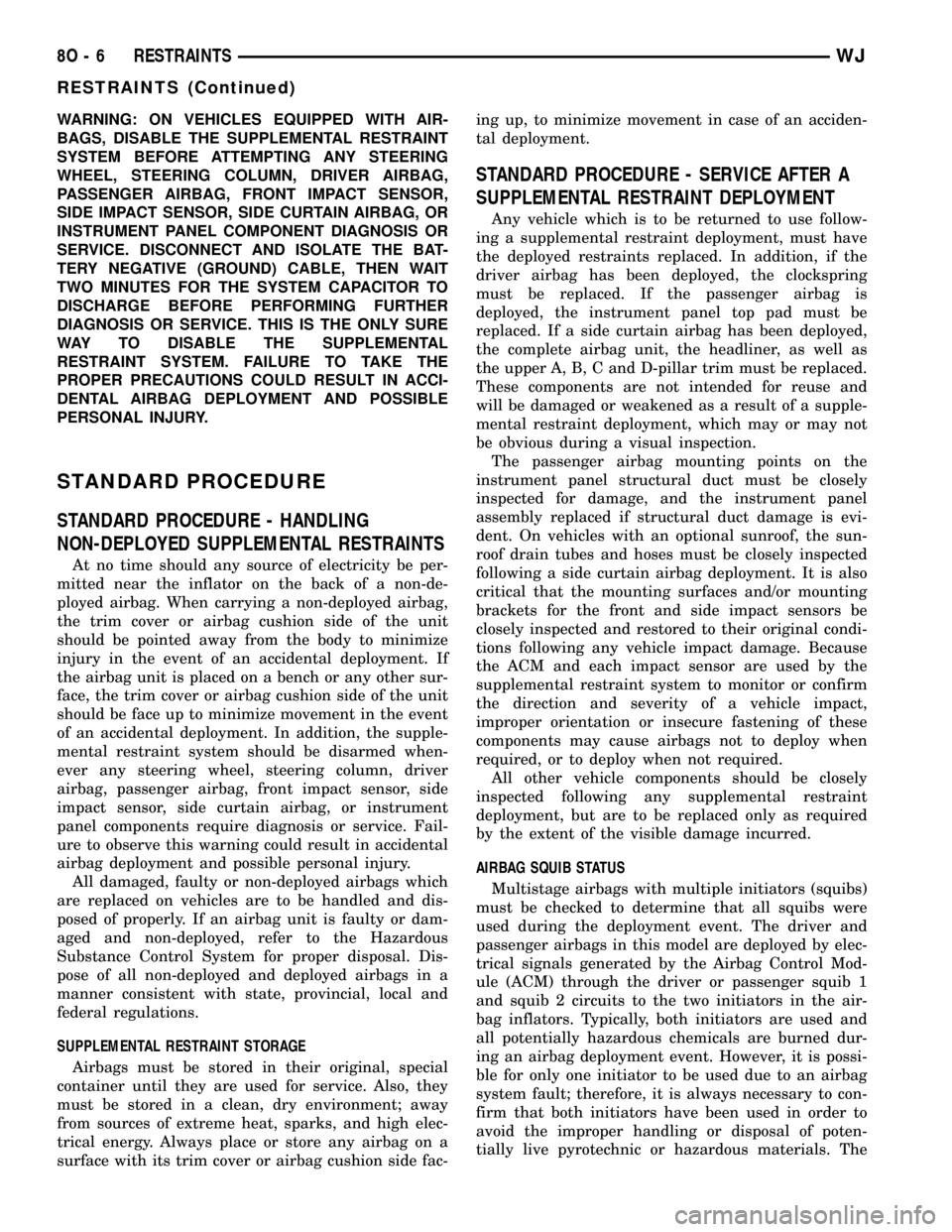
WARNING: ON VEHICLES EQUIPPED WITH AIR-
BAGS, DISABLE THE SUPPLEMENTAL RESTRAINT
SYSTEM BEFORE ATTEMPTING ANY STEERING
WHEEL, STEERING COLUMN, DRIVER AIRBAG,
PASSENGER AIRBAG, FRONT IMPACT SENSOR,
SIDE IMPACT SENSOR, SIDE CURTAIN AIRBAG, OR
INSTRUMENT PANEL COMPONENT DIAGNOSIS OR
SERVICE. DISCONNECT AND ISOLATE THE BAT-
TERY NEGATIVE (GROUND) CABLE, THEN WAIT
TWO MINUTES FOR THE SYSTEM CAPACITOR TO
DISCHARGE BEFORE PERFORMING FURTHER
DIAGNOSIS OR SERVICE. THIS IS THE ONLY SURE
WAY TO DISABLE THE SUPPLEMENTAL
RESTRAINT SYSTEM. FAILURE TO TAKE THE
PROPER PRECAUTIONS COULD RESULT IN ACCI-
DENTAL AIRBAG DEPLOYMENT AND POSSIBLE
PERSONAL INJURY.
STANDARD PROCEDURE
STANDARD PROCEDURE - HANDLING
NON-DEPLOYED SUPPLEMENTAL RESTRAINTS
At no time should any source of electricity be per-
mitted near the inflator on the back of a non-de-
ployed airbag. When carrying a non-deployed airbag,
the trim cover or airbag cushion side of the unit
should be pointed away from the body to minimize
injury in the event of an accidental deployment. If
the airbag unit is placed on a bench or any other sur-
face, the trim cover or airbag cushion side of the unit
should be face up to minimize movement in the event
of an accidental deployment. In addition, the supple-
mental restraint system should be disarmed when-
ever any steering wheel, steering column, driver
airbag, passenger airbag, front impact sensor, side
impact sensor, side curtain airbag, or instrument
panel components require diagnosis or service. Fail-
ure to observe this warning could result in accidental
airbag deployment and possible personal injury.
All damaged, faulty or non-deployed airbags which
are replaced on vehicles are to be handled and dis-
posed of properly. If an airbag unit is faulty or dam-
aged and non-deployed, refer to the Hazardous
Substance Control System for proper disposal. Dis-
pose of all non-deployed and deployed airbags in a
manner consistent with state, provincial, local and
federal regulations.
SUPPLEMENTAL RESTRAINT STORAGE
Airbags must be stored in their original, special
container until they are used for service. Also, they
must be stored in a clean, dry environment; away
from sources of extreme heat, sparks, and high elec-
trical energy. Always place or store any airbag on a
surface with its trim cover or airbag cushion side fac-ing up, to minimize movement in case of an acciden-
tal deployment.
STANDARD PROCEDURE - SERVICE AFTER A
SUPPLEMENTAL RESTRAINT DEPLOYMENT
Any vehicle which is to be returned to use follow-
ing a supplemental restraint deployment, must have
the deployed restraints replaced. In addition, if the
driver airbag has been deployed, the clockspring
must be replaced. If the passenger airbag is
deployed, the instrument panel top pad must be
replaced. If a side curtain airbag has been deployed,
the complete airbag unit, the headliner, as well as
the upper A, B, C and D-pillar trim must be replaced.
These components are not intended for reuse and
will be damaged or weakened as a result of a supple-
mental restraint deployment, which may or may not
be obvious during a visual inspection.
The passenger airbag mounting points on the
instrument panel structural duct must be closely
inspected for damage, and the instrument panel
assembly replaced if structural duct damage is evi-
dent. On vehicles with an optional sunroof, the sun-
roof drain tubes and hoses must be closely inspected
following a side curtain airbag deployment. It is also
critical that the mounting surfaces and/or mounting
brackets for the front and side impact sensors be
closely inspected and restored to their original condi-
tions following any vehicle impact damage. Because
the ACM and each impact sensor are used by the
supplemental restraint system to monitor or confirm
the direction and severity of a vehicle impact,
improper orientation or insecure fastening of these
components may cause airbags not to deploy when
required, or to deploy when not required.
All other vehicle components should be closely
inspected following any supplemental restraint
deployment, but are to be replaced only as required
by the extent of the visible damage incurred.
AIRBAG SQUIB STATUS
Multistage airbags with multiple initiators (squibs)
must be checked to determine that all squibs were
used during the deployment event. The driver and
passenger airbags in this model are deployed by elec-
trical signals generated by the Airbag Control Mod-
ule (ACM) through the driver or passenger squib 1
and squib 2 circuits to the two initiators in the air-
bag inflators. Typically, both initiators are used and
all potentially hazardous chemicals are burned dur-
ing an airbag deployment event. However, it is possi-
ble for only one initiator to be used due to an airbag
system fault; therefore, it is always necessary to con-
firm that both initiators have been used in order to
avoid the improper handling or disposal of poten-
tially live pyrotechnic or hazardous materials. The
8O - 6 RESTRAINTSWJ
RESTRAINTS (Continued)
Page 547 of 2199
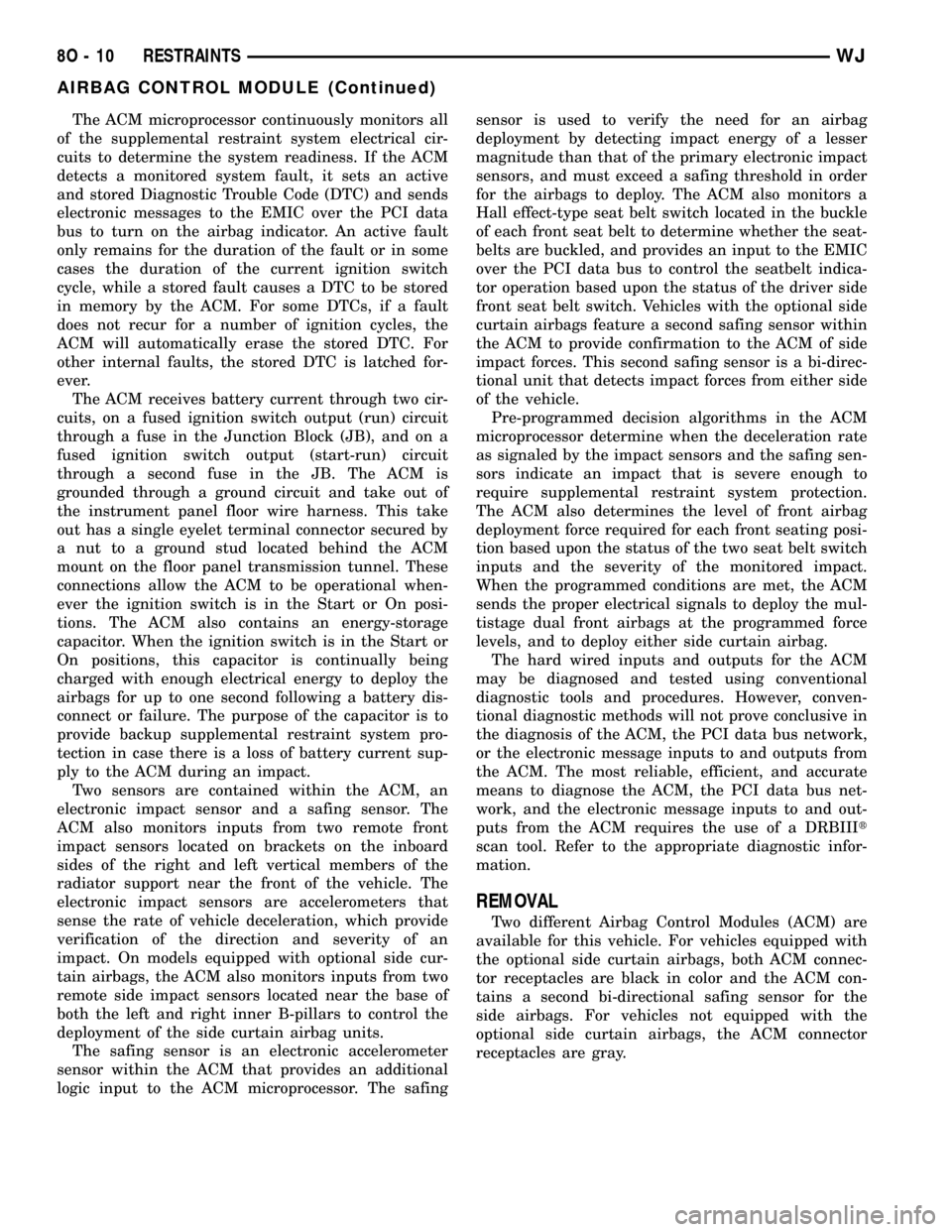
The ACM microprocessor continuously monitors all
of the supplemental restraint system electrical cir-
cuits to determine the system readiness. If the ACM
detects a monitored system fault, it sets an active
and stored Diagnostic Trouble Code (DTC) and sends
electronic messages to the EMIC over the PCI data
bus to turn on the airbag indicator. An active fault
only remains for the duration of the fault or in some
cases the duration of the current ignition switch
cycle, while a stored fault causes a DTC to be stored
in memory by the ACM. For some DTCs, if a fault
does not recur for a number of ignition cycles, the
ACM will automatically erase the stored DTC. For
other internal faults, the stored DTC is latched for-
ever.
The ACM receives battery current through two cir-
cuits, on a fused ignition switch output (run) circuit
through a fuse in the Junction Block (JB), and on a
fused ignition switch output (start-run) circuit
through a second fuse in the JB. The ACM is
grounded through a ground circuit and take out of
the instrument panel floor wire harness. This take
out has a single eyelet terminal connector secured by
a nut to a ground stud located behind the ACM
mount on the floor panel transmission tunnel. These
connections allow the ACM to be operational when-
ever the ignition switch is in the Start or On posi-
tions. The ACM also contains an energy-storage
capacitor. When the ignition switch is in the Start or
On positions, this capacitor is continually being
charged with enough electrical energy to deploy the
airbags for up to one second following a battery dis-
connect or failure. The purpose of the capacitor is to
provide backup supplemental restraint system pro-
tection in case there is a loss of battery current sup-
ply to the ACM during an impact.
Two sensors are contained within the ACM, an
electronic impact sensor and a safing sensor. The
ACM also monitors inputs from two remote front
impact sensors located on brackets on the inboard
sides of the right and left vertical members of the
radiator support near the front of the vehicle. The
electronic impact sensors are accelerometers that
sense the rate of vehicle deceleration, which provide
verification of the direction and severity of an
impact. On models equipped with optional side cur-
tain airbags, the ACM also monitors inputs from two
remote side impact sensors located near the base of
both the left and right inner B-pillars to control the
deployment of the side curtain airbag units.
The safing sensor is an electronic accelerometer
sensor within the ACM that provides an additional
logic input to the ACM microprocessor. The safingsensor is used to verify the need for an airbag
deployment by detecting impact energy of a lesser
magnitude than that of the primary electronic impact
sensors, and must exceed a safing threshold in order
for the airbags to deploy. The ACM also monitors a
Hall effect-type seat belt switch located in the buckle
of each front seat belt to determine whether the seat-
belts are buckled, and provides an input to the EMIC
over the PCI data bus to control the seatbelt indica-
tor operation based upon the status of the driver side
front seat belt switch. Vehicles with the optional side
curtain airbags feature a second safing sensor within
the ACM to provide confirmation to the ACM of side
impact forces. This second safing sensor is a bi-direc-
tional unit that detects impact forces from either side
of the vehicle.
Pre-programmed decision algorithms in the ACM
microprocessor determine when the deceleration rate
as signaled by the impact sensors and the safing sen-
sors indicate an impact that is severe enough to
require supplemental restraint system protection.
The ACM also determines the level of front airbag
deployment force required for each front seating posi-
tion based upon the status of the two seat belt switch
inputs and the severity of the monitored impact.
When the programmed conditions are met, the ACM
sends the proper electrical signals to deploy the mul-
tistage dual front airbags at the programmed force
levels, and to deploy either side curtain airbag.
The hard wired inputs and outputs for the ACM
may be diagnosed and tested using conventional
diagnostic tools and procedures. However, conven-
tional diagnostic methods will not prove conclusive in
the diagnosis of the ACM, the PCI data bus network,
or the electronic message inputs to and outputs from
the ACM. The most reliable, efficient, and accurate
means to diagnose the ACM, the PCI data bus net-
work, and the electronic message inputs to and out-
puts from the ACM requires the use of a DRBIIIt
scan tool. Refer to the appropriate diagnostic infor-
mation.
REMOVAL
Two different Airbag Control Modules (ACM) are
available for this vehicle. For vehicles equipped with
the optional side curtain airbags, both ACM connec-
tor receptacles are black in color and the ACM con-
tains a second bi-directional safing sensor for the
side airbags. For vehicles not equipped with the
optional side curtain airbags, the ACM connector
receptacles are gray.
8O - 10 RESTRAINTSWJ
AIRBAG CONTROL MODULE (Continued)