Electronic Control JEEP GRAND CHEROKEE 2002 WJ / 2.G Workshop Manual
[x] Cancel search | Manufacturer: JEEP, Model Year: 2002, Model line: GRAND CHEROKEE, Model: JEEP GRAND CHEROKEE 2002 WJ / 2.GPages: 2199, PDF Size: 76.01 MB
Page 1 of 2199
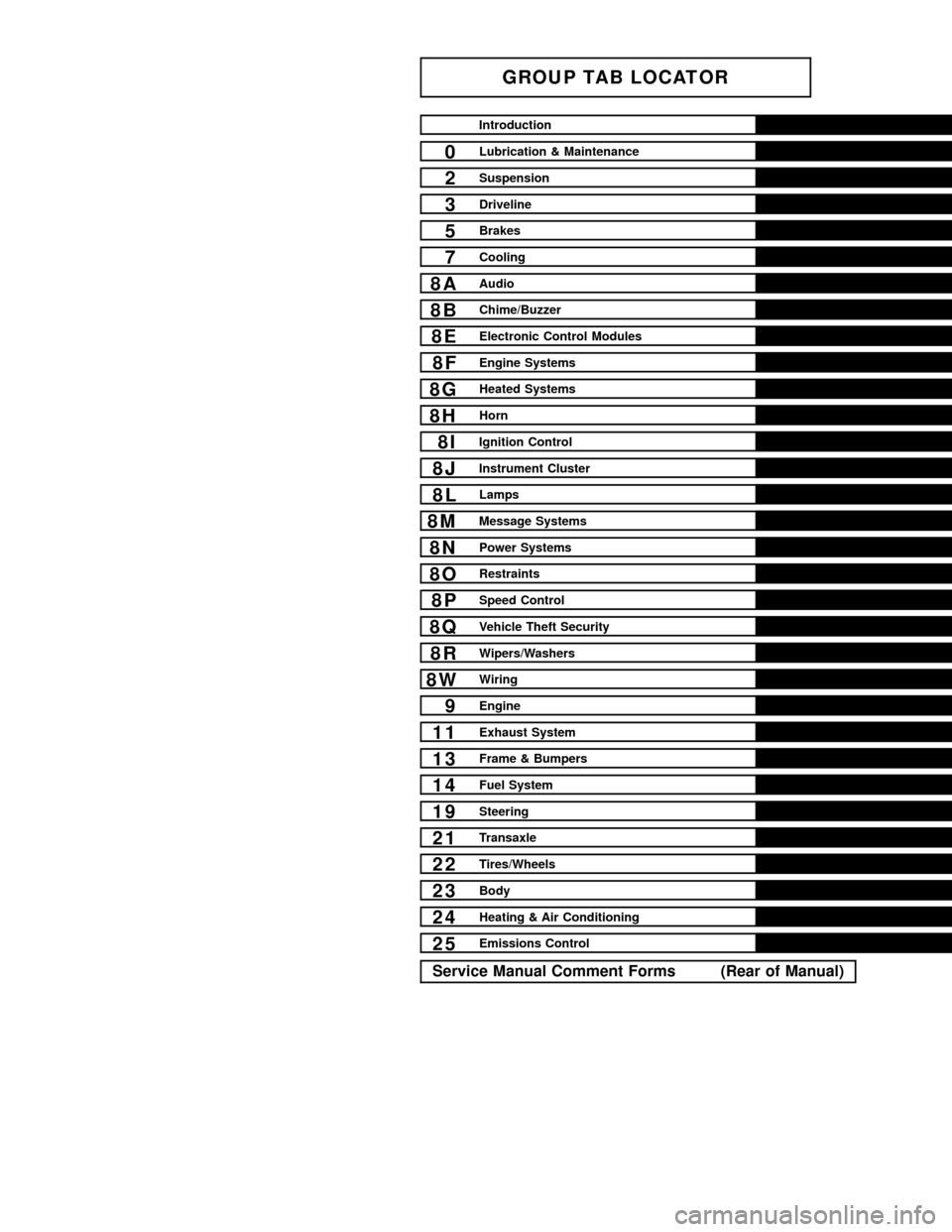
GROUP TAB LOCATOR
Introduction
0Lubrication & Maintenance
2Suspension
3Driveline
5Brakes
7Cooling
8AAudio
8BChime/Buzzer
8EElectronic Control Modules
8FEngine Systems
8GHeated Systems
8HHorn
8IIgnition Control
8JInstrument Cluster
8LLamps
8MMessage Systems
8NPower Systems
8ORestraints
8PSpeed Control
8QVehicle Theft Security
8RWipers/Washers
8WWiring
9Engine
11Exhaust System
13Frame & Bumpers
14Fuel System
19Steering
21Transaxle
22Tires/Wheels
23Body
24Heating & Air Conditioning
25Emissions Control
Service Manual Comment Forms (Rear of Manual)
Page 177 of 2199
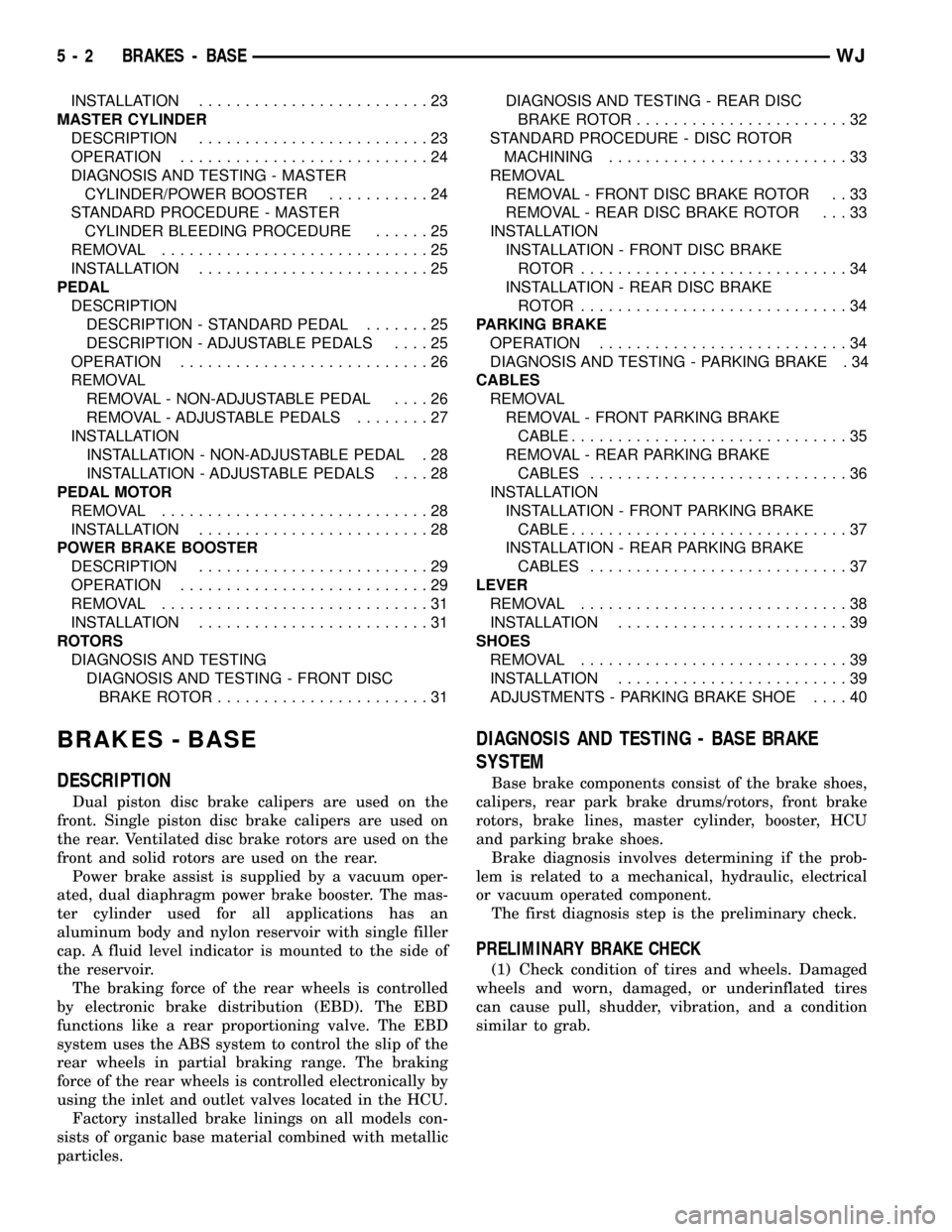
INSTALLATION.........................23
MASTER CYLINDER
DESCRIPTION.........................23
OPERATION...........................24
DIAGNOSIS AND TESTING - MASTER
CYLINDER/POWER BOOSTER...........24
STANDARD PROCEDURE - MASTER
CYLINDER BLEEDING PROCEDURE......25
REMOVAL.............................25
INSTALLATION.........................25
PEDAL
DESCRIPTION
DESCRIPTION - STANDARD PEDAL.......25
DESCRIPTION - ADJUSTABLE PEDALS....25
OPERATION...........................26
REMOVAL
REMOVAL - NON-ADJUSTABLE PEDAL....26
REMOVAL - ADJUSTABLE PEDALS........27
INSTALLATION
INSTALLATION - NON-ADJUSTABLE PEDAL . 28
INSTALLATION - ADJUSTABLE PEDALS....28
PEDAL MOTOR
REMOVAL.............................28
INSTALLATION.........................28
POWER BRAKE BOOSTER
DESCRIPTION.........................29
OPERATION...........................29
REMOVAL.............................31
INSTALLATION.........................31
ROTORS
DIAGNOSIS AND TESTING
DIAGNOSIS AND TESTING - FRONT DISC
BRAKE ROTOR.......................31DIAGNOSIS AND TESTING - REAR DISC
BRAKE ROTOR.......................32
STANDARD PROCEDURE - DISC ROTOR
MACHINING..........................33
REMOVAL
REMOVAL - FRONT DISC BRAKE ROTOR . . 33
REMOVAL - REAR DISC BRAKE ROTOR . . . 33
INSTALLATION
INSTALLATION - FRONT DISC BRAKE
ROTOR .............................34
INSTALLATION - REAR DISC BRAKE
ROTOR .............................34
PARKING BRAKE
OPERATION...........................34
DIAGNOSIS AND TESTING - PARKING BRAKE . 34
CABLES
REMOVAL
REMOVAL - FRONT PARKING BRAKE
CABLE..............................35
REMOVAL - REAR PARKING BRAKE
CABLES............................36
INSTALLATION
INSTALLATION - FRONT PARKING BRAKE
CABLE..............................37
INSTALLATION - REAR PARKING BRAKE
CABLES............................37
LEVER
REMOVAL.............................38
INSTALLATION.........................39
SHOES
REMOVAL.............................39
INSTALLATION.........................39
ADJUSTMENTS - PARKING BRAKE SHOE....40
BRAKES - BASE
DESCRIPTION
Dual piston disc brake calipers are used on the
front. Single piston disc brake calipers are used on
the rear. Ventilated disc brake rotors are used on the
front and solid rotors are used on the rear.
Power brake assist is supplied by a vacuum oper-
ated, dual diaphragm power brake booster. The mas-
ter cylinder used for all applications has an
aluminum body and nylon reservoir with single filler
cap. A fluid level indicator is mounted to the side of
the reservoir.
The braking force of the rear wheels is controlled
by electronic brake distribution (EBD). The EBD
functions like a rear proportioning valve. The EBD
system uses the ABS system to control the slip of the
rear wheels in partial braking range. The braking
force of the rear wheels is controlled electronically by
using the inlet and outlet valves located in the HCU.
Factory installed brake linings on all models con-
sists of organic base material combined with metallic
particles.
DIAGNOSIS AND TESTING - BASE BRAKE
SYSTEM
Base brake components consist of the brake shoes,
calipers, rear park brake drums/rotors, front brake
rotors, brake lines, master cylinder, booster, HCU
and parking brake shoes.
Brake diagnosis involves determining if the prob-
lem is related to a mechanical, hydraulic, electrical
or vacuum operated component.
The first diagnosis step is the preliminary check.
PRELIMINARY BRAKE CHECK
(1) Check condition of tires and wheels. Damaged
wheels and worn, damaged, or underinflated tires
can cause pull, shudder, vibration, and a condition
similar to grab.
5 - 2 BRAKES - BASEWJ
Page 209 of 2199
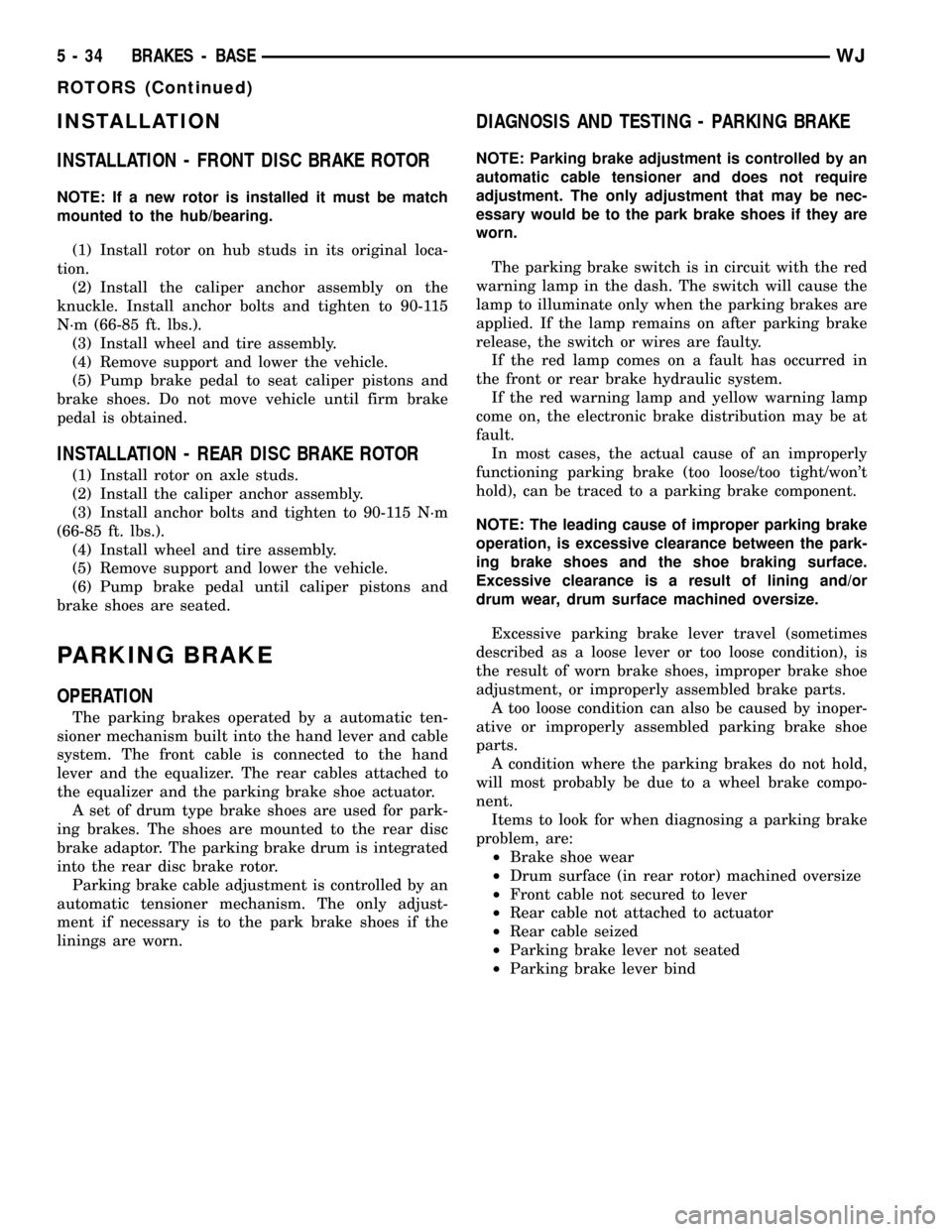
INSTALLATION
INSTALLATION - FRONT DISC BRAKE ROTOR
NOTE: If a new rotor is installed it must be match
mounted to the hub/bearing.
(1) Install rotor on hub studs in its original loca-
tion.
(2) Install the caliper anchor assembly on the
knuckle. Install anchor bolts and tighten to 90-115
N´m (66-85 ft. lbs.).
(3) Install wheel and tire assembly.
(4) Remove support and lower the vehicle.
(5) Pump brake pedal to seat caliper pistons and
brake shoes. Do not move vehicle until firm brake
pedal is obtained.
INSTALLATION - REAR DISC BRAKE ROTOR
(1) Install rotor on axle studs.
(2) Install the caliper anchor assembly.
(3) Install anchor bolts and tighten to 90-115 N´m
(66-85 ft. lbs.).
(4) Install wheel and tire assembly.
(5) Remove support and lower the vehicle.
(6) Pump brake pedal until caliper pistons and
brake shoes are seated.
PARKING BRAKE
OPERATION
The parking brakes operated by a automatic ten-
sioner mechanism built into the hand lever and cable
system. The front cable is connected to the hand
lever and the equalizer. The rear cables attached to
the equalizer and the parking brake shoe actuator.
A set of drum type brake shoes are used for park-
ing brakes. The shoes are mounted to the rear disc
brake adaptor. The parking brake drum is integrated
into the rear disc brake rotor.
Parking brake cable adjustment is controlled by an
automatic tensioner mechanism. The only adjust-
ment if necessary is to the park brake shoes if the
linings are worn.
DIAGNOSIS AND TESTING - PARKING BRAKE
NOTE: Parking brake adjustment is controlled by an
automatic cable tensioner and does not require
adjustment. The only adjustment that may be nec-
essary would be to the park brake shoes if they are
worn.
The parking brake switch is in circuit with the red
warning lamp in the dash. The switch will cause the
lamp to illuminate only when the parking brakes are
applied. If the lamp remains on after parking brake
release, the switch or wires are faulty.
If the red lamp comes on a fault has occurred in
the front or rear brake hydraulic system.
If the red warning lamp and yellow warning lamp
come on, the electronic brake distribution may be at
fault.
In most cases, the actual cause of an improperly
functioning parking brake (too loose/too tight/won't
hold), can be traced to a parking brake component.
NOTE: The leading cause of improper parking brake
operation, is excessive clearance between the park-
ing brake shoes and the shoe braking surface.
Excessive clearance is a result of lining and/or
drum wear, drum surface machined oversize.
Excessive parking brake lever travel (sometimes
described as a loose lever or too loose condition), is
the result of worn brake shoes, improper brake shoe
adjustment, or improperly assembled brake parts.
A too loose condition can also be caused by inoper-
ative or improperly assembled parking brake shoe
parts.
A condition where the parking brakes do not hold,
will most probably be due to a wheel brake compo-
nent.
Items to look for when diagnosing a parking brake
problem, are:
²Brake shoe wear
²Drum surface (in rear rotor) machined oversize
²Front cable not secured to lever
²Rear cable not attached to actuator
²Rear cable seized
²Parking brake lever not seated
²Parking brake lever bind
5 - 34 BRAKES - BASEWJ
ROTORS (Continued)
Page 218 of 2199
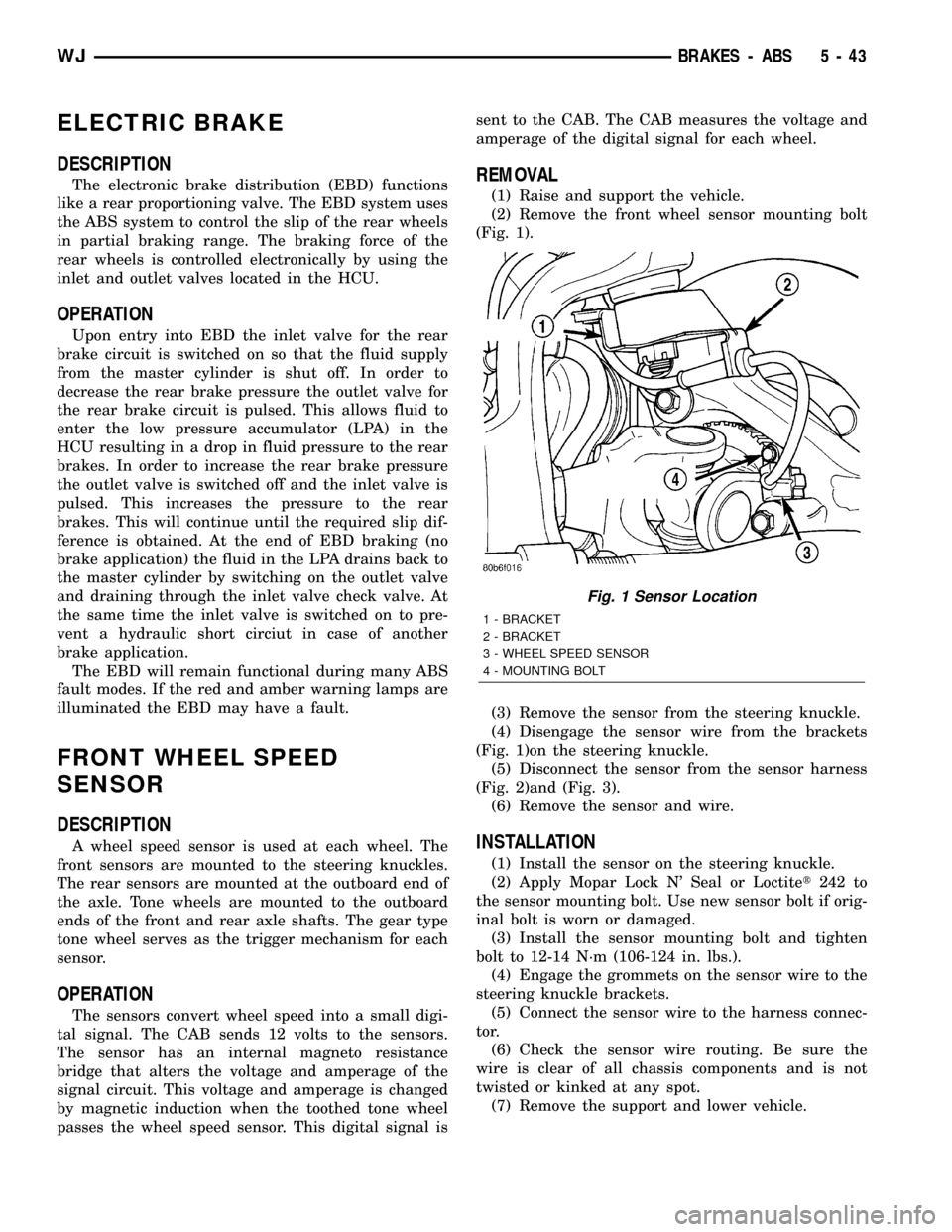
ELECTRIC BRAKE
DESCRIPTION
The electronic brake distribution (EBD) functions
like a rear proportioning valve. The EBD system uses
the ABS system to control the slip of the rear wheels
in partial braking range. The braking force of the
rear wheels is controlled electronically by using the
inlet and outlet valves located in the HCU.
OPERATION
Upon entry into EBD the inlet valve for the rear
brake circuit is switched on so that the fluid supply
from the master cylinder is shut off. In order to
decrease the rear brake pressure the outlet valve for
the rear brake circuit is pulsed. This allows fluid to
enter the low pressure accumulator (LPA) in the
HCU resulting in a drop in fluid pressure to the rear
brakes. In order to increase the rear brake pressure
the outlet valve is switched off and the inlet valve is
pulsed. This increases the pressure to the rear
brakes. This will continue until the required slip dif-
ference is obtained. At the end of EBD braking (no
brake application) the fluid in the LPA drains back to
the master cylinder by switching on the outlet valve
and draining through the inlet valve check valve. At
the same time the inlet valve is switched on to pre-
vent a hydraulic short circiut in case of another
brake application.
The EBD will remain functional during many ABS
fault modes. If the red and amber warning lamps are
illuminated the EBD may have a fault.
FRONT WHEEL SPEED
SENSOR
DESCRIPTION
A wheel speed sensor is used at each wheel. The
front sensors are mounted to the steering knuckles.
The rear sensors are mounted at the outboard end of
the axle. Tone wheels are mounted to the outboard
ends of the front and rear axle shafts. The gear type
tone wheel serves as the trigger mechanism for each
sensor.
OPERATION
The sensors convert wheel speed into a small digi-
tal signal. The CAB sends 12 volts to the sensors.
The sensor has an internal magneto resistance
bridge that alters the voltage and amperage of the
signal circuit. This voltage and amperage is changed
by magnetic induction when the toothed tone wheel
passes the wheel speed sensor. This digital signal issent to the CAB. The CAB measures the voltage and
amperage of the digital signal for each wheel.
REMOVAL
(1) Raise and support the vehicle.
(2) Remove the front wheel sensor mounting bolt
(Fig. 1).
(3) Remove the sensor from the steering knuckle.
(4) Disengage the sensor wire from the brackets
(Fig. 1)on the steering knuckle.
(5) Disconnect the sensor from the sensor harness
(Fig. 2)and (Fig. 3).
(6) Remove the sensor and wire.
INSTALLATION
(1) Install the sensor on the steering knuckle.
(2) Apply Mopar Lock N' Seal or Loctitet242 to
the sensor mounting bolt. Use new sensor bolt if orig-
inal bolt is worn or damaged.
(3) Install the sensor mounting bolt and tighten
bolt to 12-14 N´m (106-124 in. lbs.).
(4) Engage the grommets on the sensor wire to the
steering knuckle brackets.
(5) Connect the sensor wire to the harness connec-
tor.
(6) Check the sensor wire routing. Be sure the
wire is clear of all chassis components and is not
twisted or kinked at any spot.
(7) Remove the support and lower vehicle.
Fig. 1 Sensor Location
1 - BRACKET
2 - BRACKET
3 - WHEEL SPEED SENSOR
4 - MOUNTING BOLT
WJBRAKES - ABS 5 - 43
Page 281 of 2199
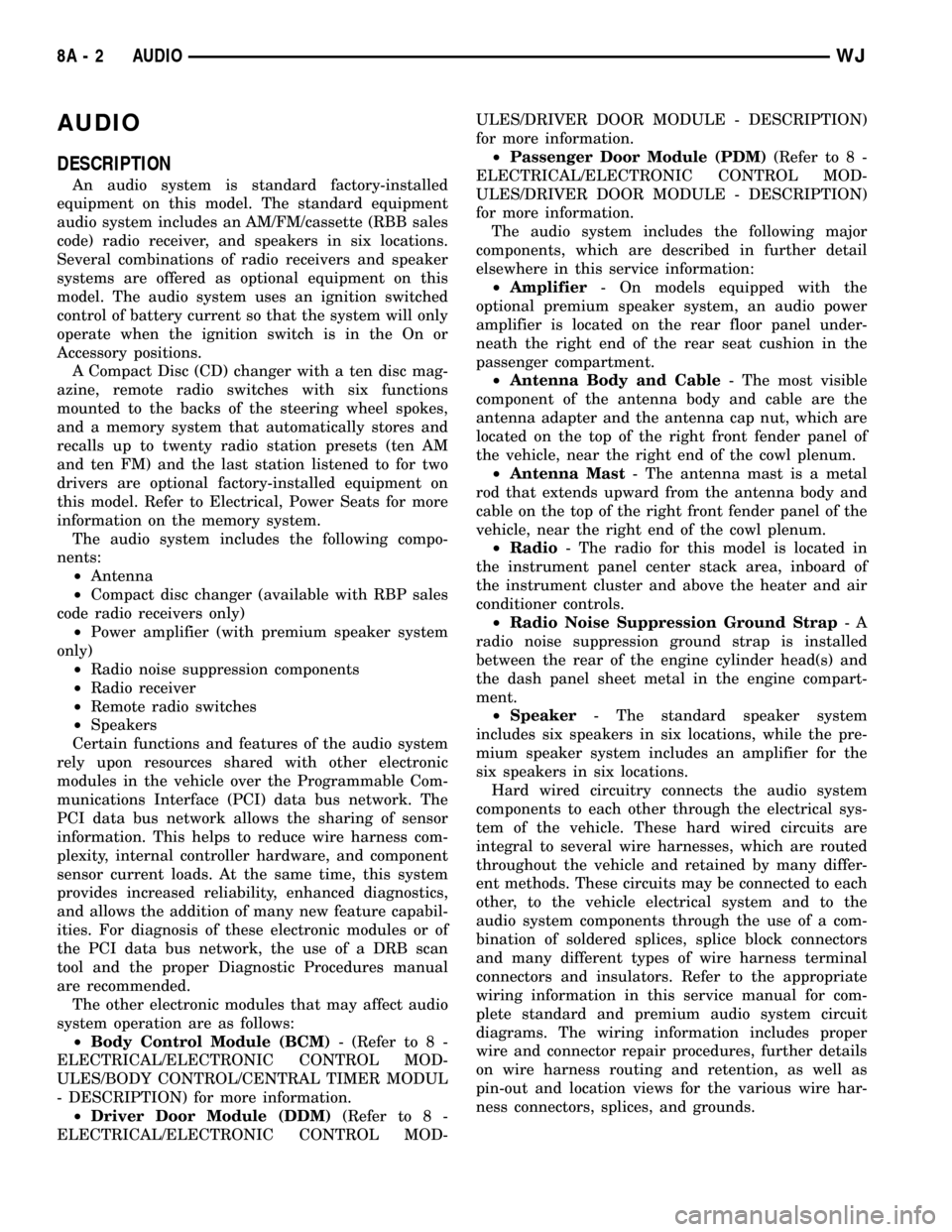
AUDIO
DESCRIPTION
An audio system is standard factory-installed
equipment on this model. The standard equipment
audio system includes an AM/FM/cassette (RBB sales
code) radio receiver, and speakers in six locations.
Several combinations of radio receivers and speaker
systems are offered as optional equipment on this
model. The audio system uses an ignition switched
control of battery current so that the system will only
operate when the ignition switch is in the On or
Accessory positions.
A Compact Disc (CD) changer with a ten disc mag-
azine, remote radio switches with six functions
mounted to the backs of the steering wheel spokes,
and a memory system that automatically stores and
recalls up to twenty radio station presets (ten AM
and ten FM) and the last station listened to for two
drivers are optional factory-installed equipment on
this model. Refer to Electrical, Power Seats for more
information on the memory system.
The audio system includes the following compo-
nents:
²Antenna
²Compact disc changer (available with RBP sales
code radio receivers only)
²Power amplifier (with premium speaker system
only)
²Radio noise suppression components
²Radio receiver
²Remote radio switches
²Speakers
Certain functions and features of the audio system
rely upon resources shared with other electronic
modules in the vehicle over the Programmable Com-
munications Interface (PCI) data bus network. The
PCI data bus network allows the sharing of sensor
information. This helps to reduce wire harness com-
plexity, internal controller hardware, and component
sensor current loads. At the same time, this system
provides increased reliability, enhanced diagnostics,
and allows the addition of many new feature capabil-
ities. For diagnosis of these electronic modules or of
the PCI data bus network, the use of a DRB scan
tool and the proper Diagnostic Procedures manual
are recommended.
The other electronic modules that may affect audio
system operation are as follows:
²Body Control Module (BCM)- (Refer to 8 -
ELECTRICAL/ELECTRONIC CONTROL MOD-
ULES/BODY CONTROL/CENTRAL TIMER MODUL
- DESCRIPTION) for more information.
²Driver Door Module (DDM)(Refer to 8 -
ELECTRICAL/ELECTRONIC CONTROL MOD-ULES/DRIVER DOOR MODULE - DESCRIPTION)
for more information.
²Passenger Door Module (PDM)(Refer to 8 -
ELECTRICAL/ELECTRONIC CONTROL MOD-
ULES/DRIVER DOOR MODULE - DESCRIPTION)
for more information.
The audio system includes the following major
components, which are described in further detail
elsewhere in this service information:
²Amplifier- On models equipped with the
optional premium speaker system, an audio power
amplifier is located on the rear floor panel under-
neath the right end of the rear seat cushion in the
passenger compartment.
²Antenna Body and Cable- The most visible
component of the antenna body and cable are the
antenna adapter and the antenna cap nut, which are
located on the top of the right front fender panel of
the vehicle, near the right end of the cowl plenum.
²Antenna Mast- The antenna mast is a metal
rod that extends upward from the antenna body and
cable on the top of the right front fender panel of the
vehicle, near the right end of the cowl plenum.
²Radio- The radio for this model is located in
the instrument panel center stack area, inboard of
the instrument cluster and above the heater and air
conditioner controls.
²Radio Noise Suppression Ground Strap-A
radio noise suppression ground strap is installed
between the rear of the engine cylinder head(s) and
the dash panel sheet metal in the engine compart-
ment.
²Speaker- The standard speaker system
includes six speakers in six locations, while the pre-
mium speaker system includes an amplifier for the
six speakers in six locations.
Hard wired circuitry connects the audio system
components to each other through the electrical sys-
tem of the vehicle. These hard wired circuits are
integral to several wire harnesses, which are routed
throughout the vehicle and retained by many differ-
ent methods. These circuits may be connected to each
other, to the vehicle electrical system and to the
audio system components through the use of a com-
bination of soldered splices, splice block connectors
and many different types of wire harness terminal
connectors and insulators. Refer to the appropriate
wiring information in this service manual for com-
plete standard and premium audio system circuit
diagrams. The wiring information includes proper
wire and connector repair procedures, further details
on wire harness routing and retention, as well as
pin-out and location views for the various wire har-
ness connectors, splices, and grounds.
8A - 2 AUDIOWJ
Page 282 of 2199
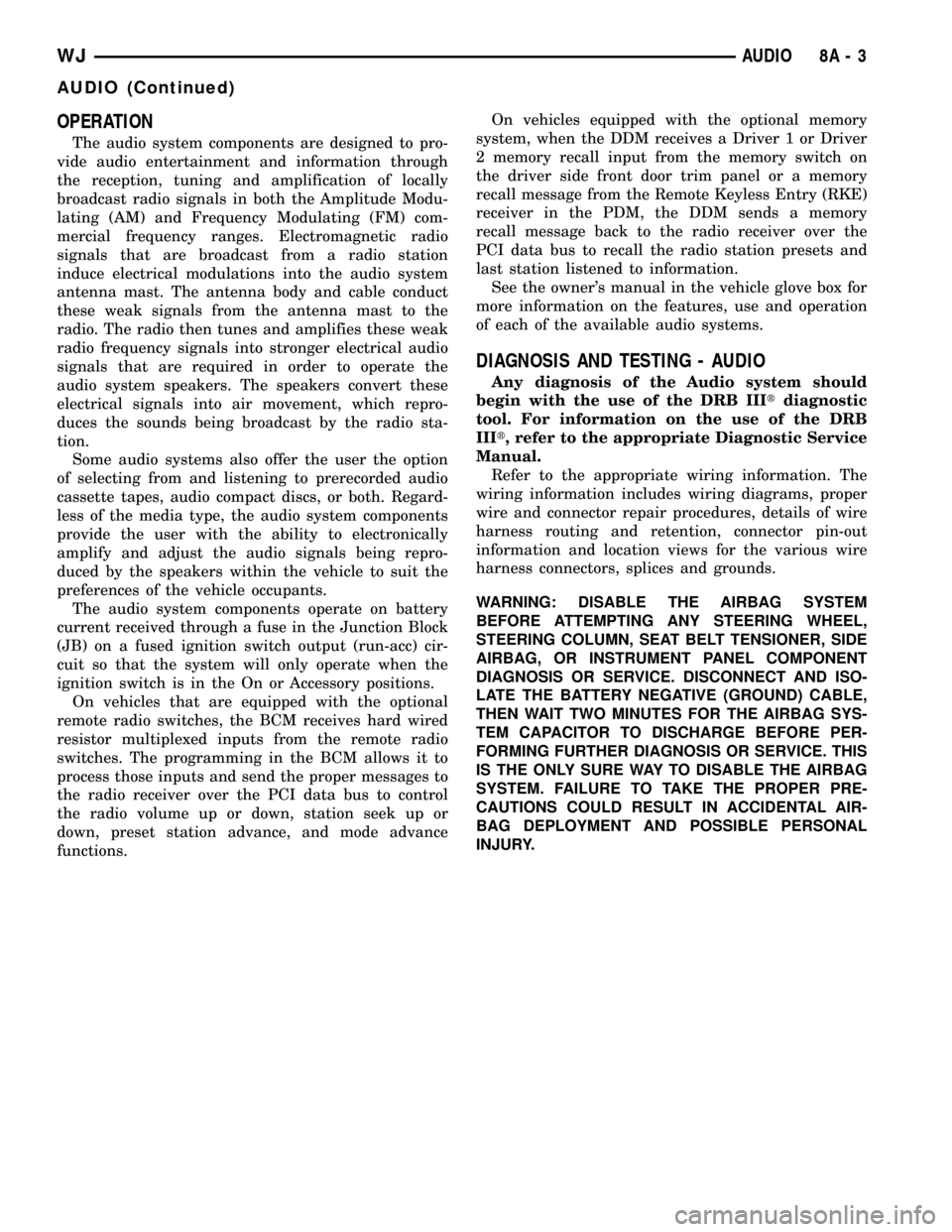
OPERATION
The audio system components are designed to pro-
vide audio entertainment and information through
the reception, tuning and amplification of locally
broadcast radio signals in both the Amplitude Modu-
lating (AM) and Frequency Modulating (FM) com-
mercial frequency ranges. Electromagnetic radio
signals that are broadcast from a radio station
induce electrical modulations into the audio system
antenna mast. The antenna body and cable conduct
these weak signals from the antenna mast to the
radio. The radio then tunes and amplifies these weak
radio frequency signals into stronger electrical audio
signals that are required in order to operate the
audio system speakers. The speakers convert these
electrical signals into air movement, which repro-
duces the sounds being broadcast by the radio sta-
tion.
Some audio systems also offer the user the option
of selecting from and listening to prerecorded audio
cassette tapes, audio compact discs, or both. Regard-
less of the media type, the audio system components
provide the user with the ability to electronically
amplify and adjust the audio signals being repro-
duced by the speakers within the vehicle to suit the
preferences of the vehicle occupants.
The audio system components operate on battery
current received through a fuse in the Junction Block
(JB) on a fused ignition switch output (run-acc) cir-
cuit so that the system will only operate when the
ignition switch is in the On or Accessory positions.
On vehicles that are equipped with the optional
remote radio switches, the BCM receives hard wired
resistor multiplexed inputs from the remote radio
switches. The programming in the BCM allows it to
process those inputs and send the proper messages to
the radio receiver over the PCI data bus to control
the radio volume up or down, station seek up or
down, preset station advance, and mode advance
functions.On vehicles equipped with the optional memory
system, when the DDM receives a Driver 1 or Driver
2 memory recall input from the memory switch on
the driver side front door trim panel or a memory
recall message from the Remote Keyless Entry (RKE)
receiver in the PDM, the DDM sends a memory
recall message back to the radio receiver over the
PCI data bus to recall the radio station presets and
last station listened to information.
See the owner's manual in the vehicle glove box for
more information on the features, use and operation
of each of the available audio systems.
DIAGNOSIS AND TESTING - AUDIO
Any diagnosis of the Audio system should
begin with the use of the DRB IIItdiagnostic
tool. For information on the use of the DRB
IIIt, refer to the appropriate Diagnostic Service
Manual.
Refer to the appropriate wiring information. The
wiring information includes wiring diagrams, proper
wire and connector repair procedures, details of wire
harness routing and retention, connector pin-out
information and location views for the various wire
harness connectors, splices and grounds.
WARNING: DISABLE THE AIRBAG SYSTEM
BEFORE ATTEMPTING ANY STEERING WHEEL,
STEERING COLUMN, SEAT BELT TENSIONER, SIDE
AIRBAG, OR INSTRUMENT PANEL COMPONENT
DIAGNOSIS OR SERVICE. DISCONNECT AND ISO-
LATE THE BATTERY NEGATIVE (GROUND) CABLE,
THEN WAIT TWO MINUTES FOR THE AIRBAG SYS-
TEM CAPACITOR TO DISCHARGE BEFORE PER-
FORMING FURTHER DIAGNOSIS OR SERVICE. THIS
IS THE ONLY SURE WAY TO DISABLE THE AIRBAG
SYSTEM. FAILURE TO TAKE THE PROPER PRE-
CAUTIONS COULD RESULT IN ACCIDENTAL AIR-
BAG DEPLOYMENT AND POSSIBLE PERSONAL
INJURY.
WJAUDIO 8A - 3
AUDIO (Continued)
Page 292 of 2199
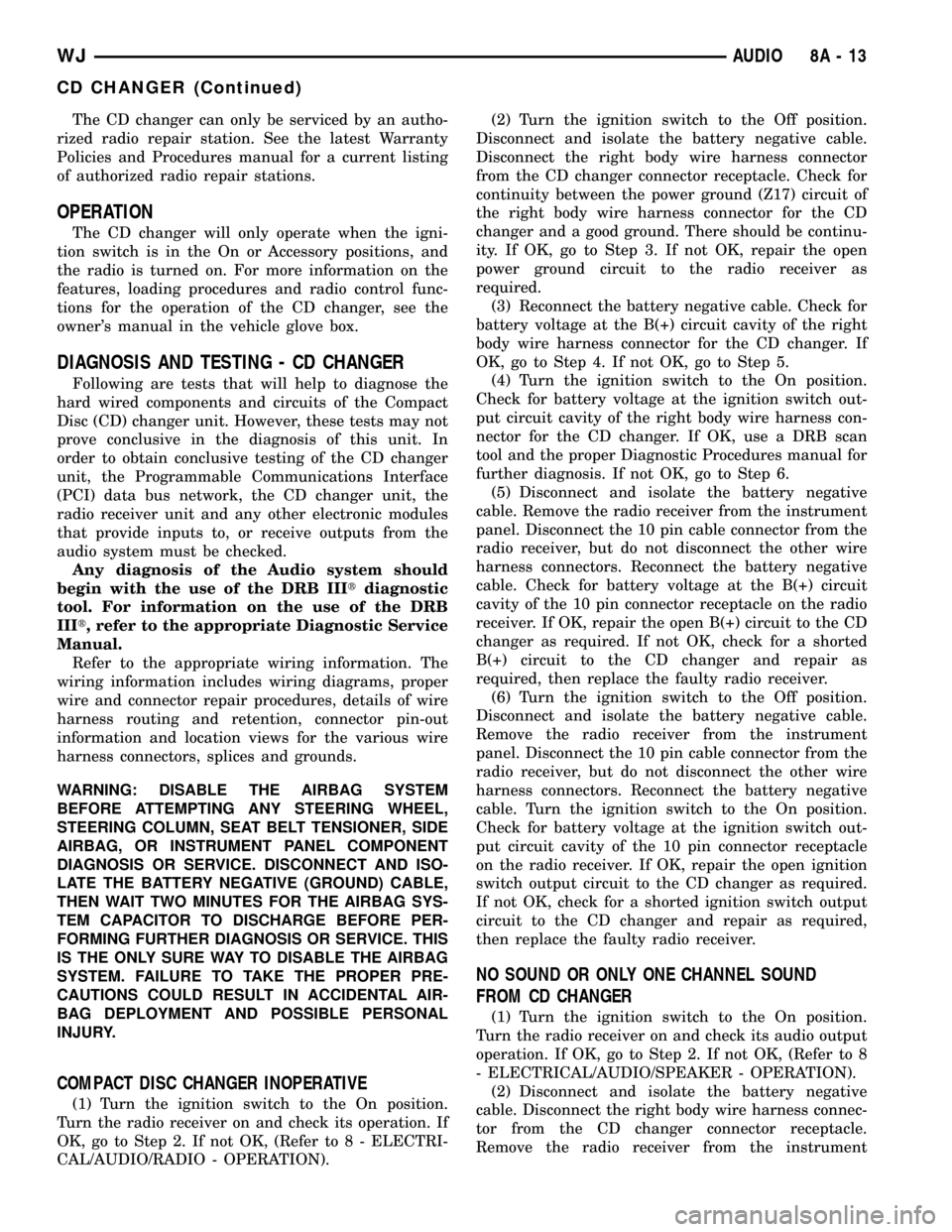
The CD changer can only be serviced by an autho-
rized radio repair station. See the latest Warranty
Policies and Procedures manual for a current listing
of authorized radio repair stations.
OPERATION
The CD changer will only operate when the igni-
tion switch is in the On or Accessory positions, and
the radio is turned on. For more information on the
features, loading procedures and radio control func-
tions for the operation of the CD changer, see the
owner's manual in the vehicle glove box.
DIAGNOSIS AND TESTING - CD CHANGER
Following are tests that will help to diagnose the
hard wired components and circuits of the Compact
Disc (CD) changer unit. However, these tests may not
prove conclusive in the diagnosis of this unit. In
order to obtain conclusive testing of the CD changer
unit, the Programmable Communications Interface
(PCI) data bus network, the CD changer unit, the
radio receiver unit and any other electronic modules
that provide inputs to, or receive outputs from the
audio system must be checked.
Any diagnosis of the Audio system should
begin with the use of the DRB IIItdiagnostic
tool. For information on the use of the DRB
IIIt, refer to the appropriate Diagnostic Service
Manual.
Refer to the appropriate wiring information. The
wiring information includes wiring diagrams, proper
wire and connector repair procedures, details of wire
harness routing and retention, connector pin-out
information and location views for the various wire
harness connectors, splices and grounds.
WARNING: DISABLE THE AIRBAG SYSTEM
BEFORE ATTEMPTING ANY STEERING WHEEL,
STEERING COLUMN, SEAT BELT TENSIONER, SIDE
AIRBAG, OR INSTRUMENT PANEL COMPONENT
DIAGNOSIS OR SERVICE. DISCONNECT AND ISO-
LATE THE BATTERY NEGATIVE (GROUND) CABLE,
THEN WAIT TWO MINUTES FOR THE AIRBAG SYS-
TEM CAPACITOR TO DISCHARGE BEFORE PER-
FORMING FURTHER DIAGNOSIS OR SERVICE. THIS
IS THE ONLY SURE WAY TO DISABLE THE AIRBAG
SYSTEM. FAILURE TO TAKE THE PROPER PRE-
CAUTIONS COULD RESULT IN ACCIDENTAL AIR-
BAG DEPLOYMENT AND POSSIBLE PERSONAL
INJURY.
COMPACT DISC CHANGER INOPERATIVE
(1) Turn the ignition switch to the On position.
Turn the radio receiver on and check its operation. If
OK, go to Step 2. If not OK, (Refer to 8 - ELECTRI-
CAL/AUDIO/RADIO - OPERATION).(2) Turn the ignition switch to the Off position.
Disconnect and isolate the battery negative cable.
Disconnect the right body wire harness connector
from the CD changer connector receptacle. Check for
continuity between the power ground (Z17) circuit of
the right body wire harness connector for the CD
changer and a good ground. There should be continu-
ity. If OK, go to Step 3. If not OK, repair the open
power ground circuit to the radio receiver as
required.
(3) Reconnect the battery negative cable. Check for
battery voltage at the B(+) circuit cavity of the right
body wire harness connector for the CD changer. If
OK, go to Step 4. If not OK, go to Step 5.
(4) Turn the ignition switch to the On position.
Check for battery voltage at the ignition switch out-
put circuit cavity of the right body wire harness con-
nector for the CD changer. If OK, use a DRB scan
tool and the proper Diagnostic Procedures manual for
further diagnosis. If not OK, go to Step 6.
(5) Disconnect and isolate the battery negative
cable. Remove the radio receiver from the instrument
panel. Disconnect the 10 pin cable connector from the
radio receiver, but do not disconnect the other wire
harness connectors. Reconnect the battery negative
cable. Check for battery voltage at the B(+) circuit
cavity of the 10 pin connector receptacle on the radio
receiver. If OK, repair the open B(+) circuit to the CD
changer as required. If not OK, check for a shorted
B(+) circuit to the CD changer and repair as
required, then replace the faulty radio receiver.
(6) Turn the ignition switch to the Off position.
Disconnect and isolate the battery negative cable.
Remove the radio receiver from the instrument
panel. Disconnect the 10 pin cable connector from the
radio receiver, but do not disconnect the other wire
harness connectors. Reconnect the battery negative
cable. Turn the ignition switch to the On position.
Check for battery voltage at the ignition switch out-
put circuit cavity of the 10 pin connector receptacle
on the radio receiver. If OK, repair the open ignition
switch output circuit to the CD changer as required.
If not OK, check for a shorted ignition switch output
circuit to the CD changer and repair as required,
then replace the faulty radio receiver.
NO SOUND OR ONLY ONE CHANNEL SOUND
FROM CD CHANGER
(1) Turn the ignition switch to the On position.
Turn the radio receiver on and check its audio output
operation. If OK, go to Step 2. If not OK, (Refer to 8
- ELECTRICAL/AUDIO/SPEAKER - OPERATION).
(2) Disconnect and isolate the battery negative
cable. Disconnect the right body wire harness connec-
tor from the CD changer connector receptacle.
Remove the radio receiver from the instrument
WJAUDIO 8A - 13
CD CHANGER (Continued)
Page 295 of 2199
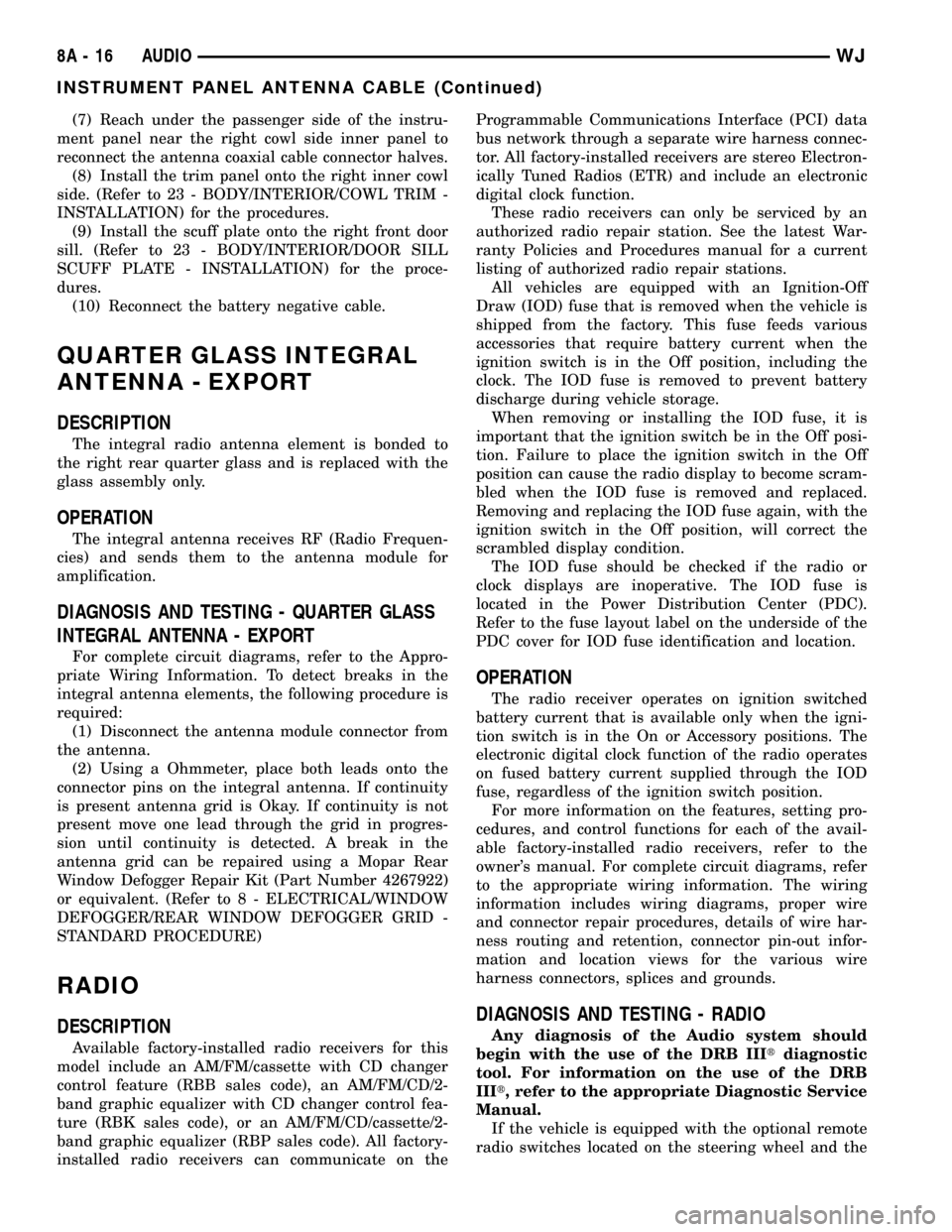
(7) Reach under the passenger side of the instru-
ment panel near the right cowl side inner panel to
reconnect the antenna coaxial cable connector halves.
(8) Install the trim panel onto the right inner cowl
side. (Refer to 23 - BODY/INTERIOR/COWL TRIM -
INSTALLATION) for the procedures.
(9) Install the scuff plate onto the right front door
sill. (Refer to 23 - BODY/INTERIOR/DOOR SILL
SCUFF PLATE - INSTALLATION) for the proce-
dures.
(10) Reconnect the battery negative cable.
QUARTER GLASS INTEGRAL
ANTENNA - EXPORT
DESCRIPTION
The integral radio antenna element is bonded to
the right rear quarter glass and is replaced with the
glass assembly only.
OPERATION
The integral antenna receives RF (Radio Frequen-
cies) and sends them to the antenna module for
amplification.
DIAGNOSIS AND TESTING - QUARTER GLASS
INTEGRAL ANTENNA - EXPORT
For complete circuit diagrams, refer to the Appro-
priate Wiring Information. To detect breaks in the
integral antenna elements, the following procedure is
required:
(1) Disconnect the antenna module connector from
the antenna.
(2) Using a Ohmmeter, place both leads onto the
connector pins on the integral antenna. If continuity
is present antenna grid is Okay. If continuity is not
present move one lead through the grid in progres-
sion until continuity is detected. A break in the
antenna grid can be repaired using a Mopar Rear
Window Defogger Repair Kit (Part Number 4267922)
or equivalent. (Refer to 8 - ELECTRICAL/WINDOW
DEFOGGER/REAR WINDOW DEFOGGER GRID -
STANDARD PROCEDURE)
RADIO
DESCRIPTION
Available factory-installed radio receivers for this
model include an AM/FM/cassette with CD changer
control feature (RBB sales code), an AM/FM/CD/2-
band graphic equalizer with CD changer control fea-
ture (RBK sales code), or an AM/FM/CD/cassette/2-
band graphic equalizer (RBP sales code). All factory-
installed radio receivers can communicate on theProgrammable Communications Interface (PCI) data
bus network through a separate wire harness connec-
tor. All factory-installed receivers are stereo Electron-
ically Tuned Radios (ETR) and include an electronic
digital clock function.
These radio receivers can only be serviced by an
authorized radio repair station. See the latest War-
ranty Policies and Procedures manual for a current
listing of authorized radio repair stations.
All vehicles are equipped with an Ignition-Off
Draw (IOD) fuse that is removed when the vehicle is
shipped from the factory. This fuse feeds various
accessories that require battery current when the
ignition switch is in the Off position, including the
clock. The IOD fuse is removed to prevent battery
discharge during vehicle storage.
When removing or installing the IOD fuse, it is
important that the ignition switch be in the Off posi-
tion. Failure to place the ignition switch in the Off
position can cause the radio display to become scram-
bled when the IOD fuse is removed and replaced.
Removing and replacing the IOD fuse again, with the
ignition switch in the Off position, will correct the
scrambled display condition.
The IOD fuse should be checked if the radio or
clock displays are inoperative. The IOD fuse is
located in the Power Distribution Center (PDC).
Refer to the fuse layout label on the underside of the
PDC cover for IOD fuse identification and location.
OPERATION
The radio receiver operates on ignition switched
battery current that is available only when the igni-
tion switch is in the On or Accessory positions. The
electronic digital clock function of the radio operates
on fused battery current supplied through the IOD
fuse, regardless of the ignition switch position.
For more information on the features, setting pro-
cedures, and control functions for each of the avail-
able factory-installed radio receivers, refer to the
owner's manual. For complete circuit diagrams, refer
to the appropriate wiring information. The wiring
information includes wiring diagrams, proper wire
and connector repair procedures, details of wire har-
ness routing and retention, connector pin-out infor-
mation and location views for the various wire
harness connectors, splices and grounds.
DIAGNOSIS AND TESTING - RADIO
Any diagnosis of the Audio system should
begin with the use of the DRB IIItdiagnostic
tool. For information on the use of the DRB
IIIt, refer to the appropriate Diagnostic Service
Manual.
If the vehicle is equipped with the optional remote
radio switches located on the steering wheel and the
8A - 16 AUDIOWJ
INSTRUMENT PANEL ANTENNA CABLE (Continued)
Page 299 of 2199
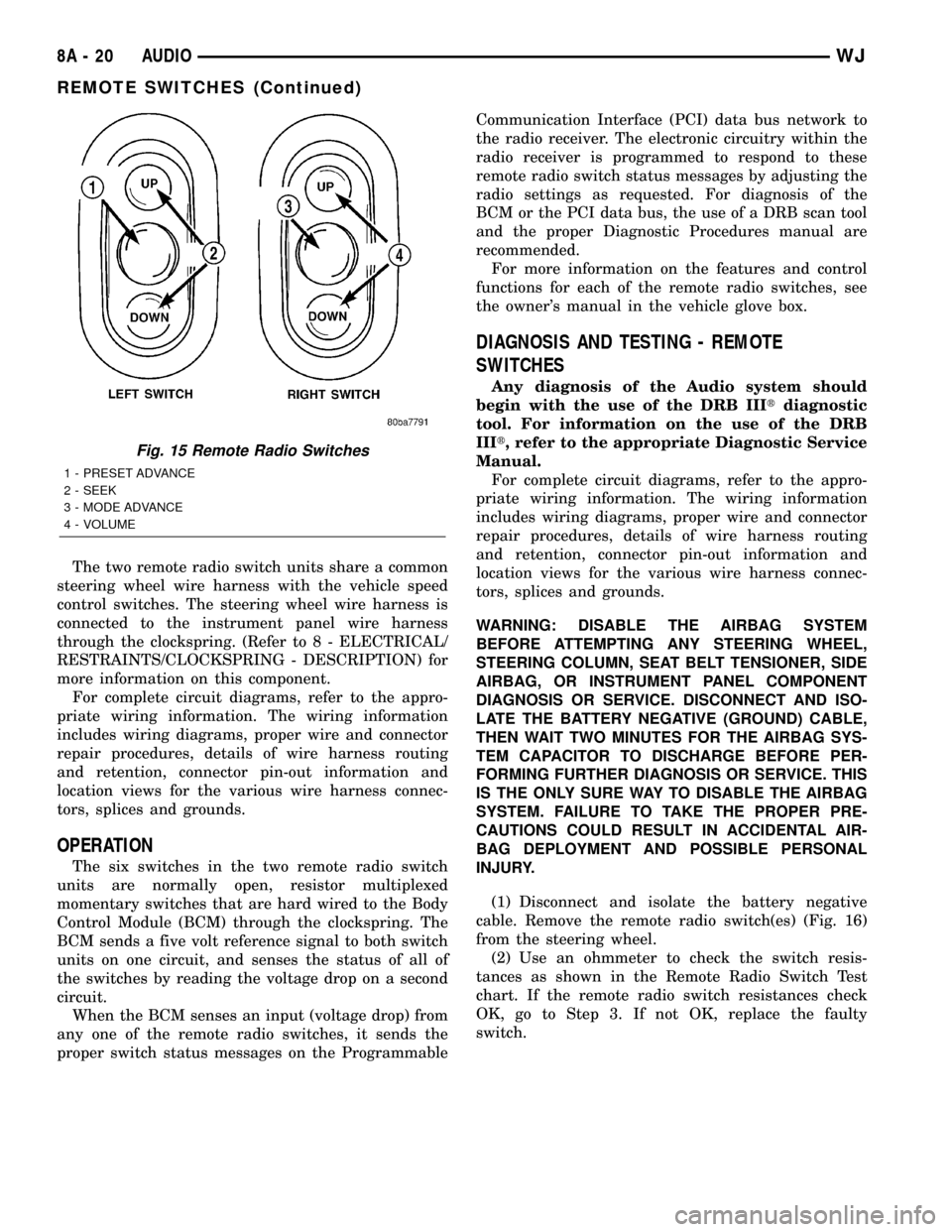
The two remote radio switch units share a common
steering wheel wire harness with the vehicle speed
control switches. The steering wheel wire harness is
connected to the instrument panel wire harness
through the clockspring. (Refer to 8 - ELECTRICAL/
RESTRAINTS/CLOCKSPRING - DESCRIPTION) for
more information on this component.
For complete circuit diagrams, refer to the appro-
priate wiring information. The wiring information
includes wiring diagrams, proper wire and connector
repair procedures, details of wire harness routing
and retention, connector pin-out information and
location views for the various wire harness connec-
tors, splices and grounds.
OPERATION
The six switches in the two remote radio switch
units are normally open, resistor multiplexed
momentary switches that are hard wired to the Body
Control Module (BCM) through the clockspring. The
BCM sends a five volt reference signal to both switch
units on one circuit, and senses the status of all of
the switches by reading the voltage drop on a second
circuit.
When the BCM senses an input (voltage drop) from
any one of the remote radio switches, it sends the
proper switch status messages on the ProgrammableCommunication Interface (PCI) data bus network to
the radio receiver. The electronic circuitry within the
radio receiver is programmed to respond to these
remote radio switch status messages by adjusting the
radio settings as requested. For diagnosis of the
BCM or the PCI data bus, the use of a DRB scan tool
and the proper Diagnostic Procedures manual are
recommended.
For more information on the features and control
functions for each of the remote radio switches, see
the owner's manual in the vehicle glove box.
DIAGNOSIS AND TESTING - REMOTE
SWITCHES
Any diagnosis of the Audio system should
begin with the use of the DRB IIItdiagnostic
tool. For information on the use of the DRB
IIIt, refer to the appropriate Diagnostic Service
Manual.
For complete circuit diagrams, refer to the appro-
priate wiring information. The wiring information
includes wiring diagrams, proper wire and connector
repair procedures, details of wire harness routing
and retention, connector pin-out information and
location views for the various wire harness connec-
tors, splices and grounds.
WARNING: DISABLE THE AIRBAG SYSTEM
BEFORE ATTEMPTING ANY STEERING WHEEL,
STEERING COLUMN, SEAT BELT TENSIONER, SIDE
AIRBAG, OR INSTRUMENT PANEL COMPONENT
DIAGNOSIS OR SERVICE. DISCONNECT AND ISO-
LATE THE BATTERY NEGATIVE (GROUND) CABLE,
THEN WAIT TWO MINUTES FOR THE AIRBAG SYS-
TEM CAPACITOR TO DISCHARGE BEFORE PER-
FORMING FURTHER DIAGNOSIS OR SERVICE. THIS
IS THE ONLY SURE WAY TO DISABLE THE AIRBAG
SYSTEM. FAILURE TO TAKE THE PROPER PRE-
CAUTIONS COULD RESULT IN ACCIDENTAL AIR-
BAG DEPLOYMENT AND POSSIBLE PERSONAL
INJURY.
(1) Disconnect and isolate the battery negative
cable. Remove the remote radio switch(es) (Fig. 16)
from the steering wheel.
(2) Use an ohmmeter to check the switch resis-
tances as shown in the Remote Radio Switch Test
chart. If the remote radio switch resistances check
OK, go to Step 3. If not OK, replace the faulty
switch.
Fig. 15 Remote Radio Switches
1 - PRESET ADVANCE
2 - SEEK
3 - MODE ADVANCE
4 - VOLUME
8A - 20 AUDIOWJ
REMOTE SWITCHES (Continued)
Page 307 of 2199
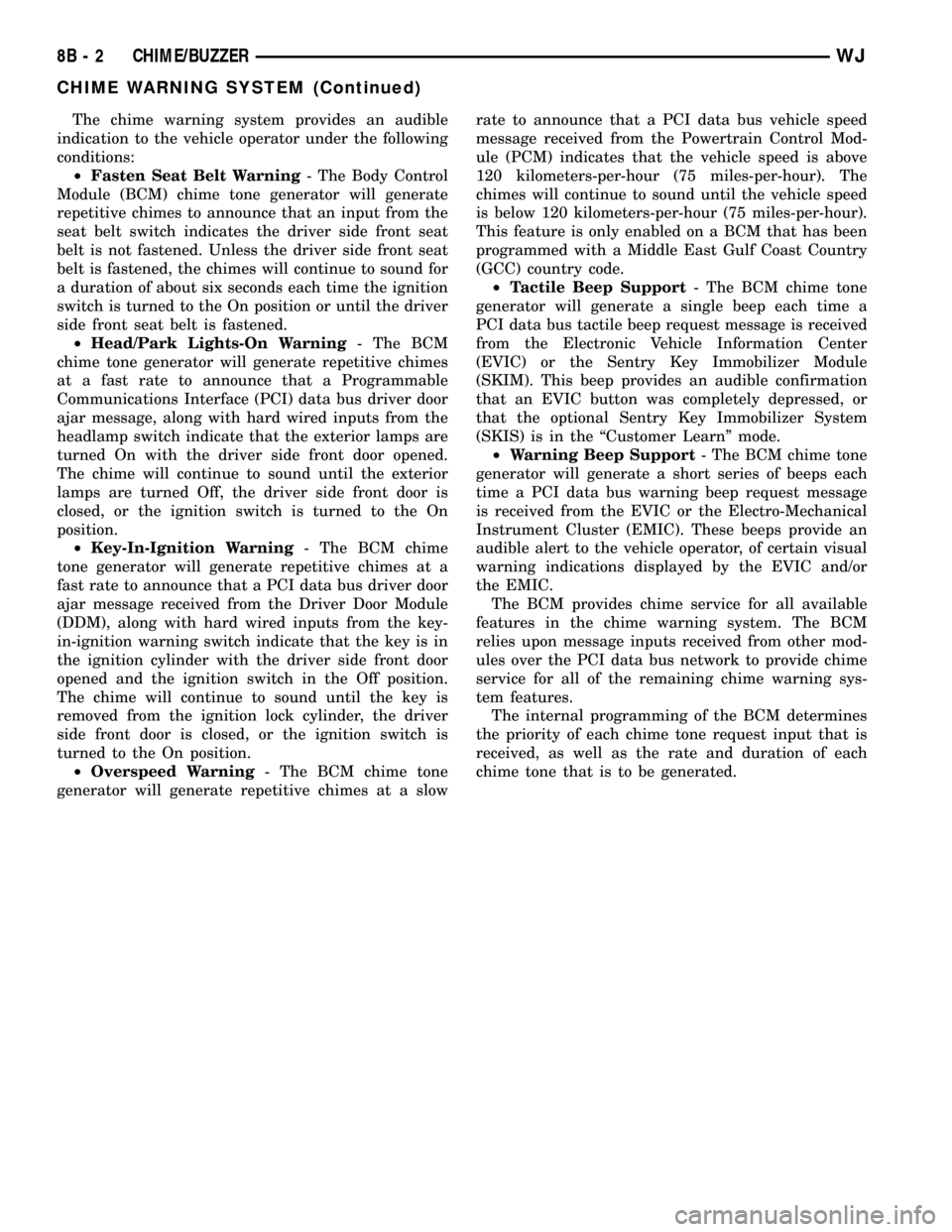
The chime warning system provides an audible
indication to the vehicle operator under the following
conditions:
²Fasten Seat Belt Warning- The Body Control
Module (BCM) chime tone generator will generate
repetitive chimes to announce that an input from the
seat belt switch indicates the driver side front seat
belt is not fastened. Unless the driver side front seat
belt is fastened, the chimes will continue to sound for
a duration of about six seconds each time the ignition
switch is turned to the On position or until the driver
side front seat belt is fastened.
²Head/Park Lights-On Warning- The BCM
chime tone generator will generate repetitive chimes
at a fast rate to announce that a Programmable
Communications Interface (PCI) data bus driver door
ajar message, along with hard wired inputs from the
headlamp switch indicate that the exterior lamps are
turned On with the driver side front door opened.
The chime will continue to sound until the exterior
lamps are turned Off, the driver side front door is
closed, or the ignition switch is turned to the On
position.
²Key-In-Ignition Warning- The BCM chime
tone generator will generate repetitive chimes at a
fast rate to announce that a PCI data bus driver door
ajar message received from the Driver Door Module
(DDM), along with hard wired inputs from the key-
in-ignition warning switch indicate that the key is in
the ignition cylinder with the driver side front door
opened and the ignition switch in the Off position.
The chime will continue to sound until the key is
removed from the ignition lock cylinder, the driver
side front door is closed, or the ignition switch is
turned to the On position.
²Overspeed Warning- The BCM chime tone
generator will generate repetitive chimes at a slowrate to announce that a PCI data bus vehicle speed
message received from the Powertrain Control Mod-
ule (PCM) indicates that the vehicle speed is above
120 kilometers-per-hour (75 miles-per-hour). The
chimes will continue to sound until the vehicle speed
is below 120 kilometers-per-hour (75 miles-per-hour).
This feature is only enabled on a BCM that has been
programmed with a Middle East Gulf Coast Country
(GCC) country code.
²Tactile Beep Support- The BCM chime tone
generator will generate a single beep each time a
PCI data bus tactile beep request message is received
from the Electronic Vehicle Information Center
(EVIC) or the Sentry Key Immobilizer Module
(SKIM). This beep provides an audible confirmation
that an EVIC button was completely depressed, or
that the optional Sentry Key Immobilizer System
(SKIS) is in the ªCustomer Learnº mode.
²Warning Beep Support- The BCM chime tone
generator will generate a short series of beeps each
time a PCI data bus warning beep request message
is received from the EVIC or the Electro-Mechanical
Instrument Cluster (EMIC). These beeps provide an
audible alert to the vehicle operator, of certain visual
warning indications displayed by the EVIC and/or
the EMIC.
The BCM provides chime service for all available
features in the chime warning system. The BCM
relies upon message inputs received from other mod-
ules over the PCI data bus network to provide chime
service for all of the remaining chime warning sys-
tem features.
The internal programming of the BCM determines
the priority of each chime tone request input that is
received, as well as the rate and duration of each
chime tone that is to be generated.
8B - 2 CHIME/BUZZERWJ
CHIME WARNING SYSTEM (Continued)