front upper control arm JEEP GRAND CHEROKEE 2002 WJ / 2.G Workshop Manual
[x] Cancel search | Manufacturer: JEEP, Model Year: 2002, Model line: GRAND CHEROKEE, Model: JEEP GRAND CHEROKEE 2002 WJ / 2.GPages: 2199, PDF Size: 76.01 MB
Page 27 of 2199
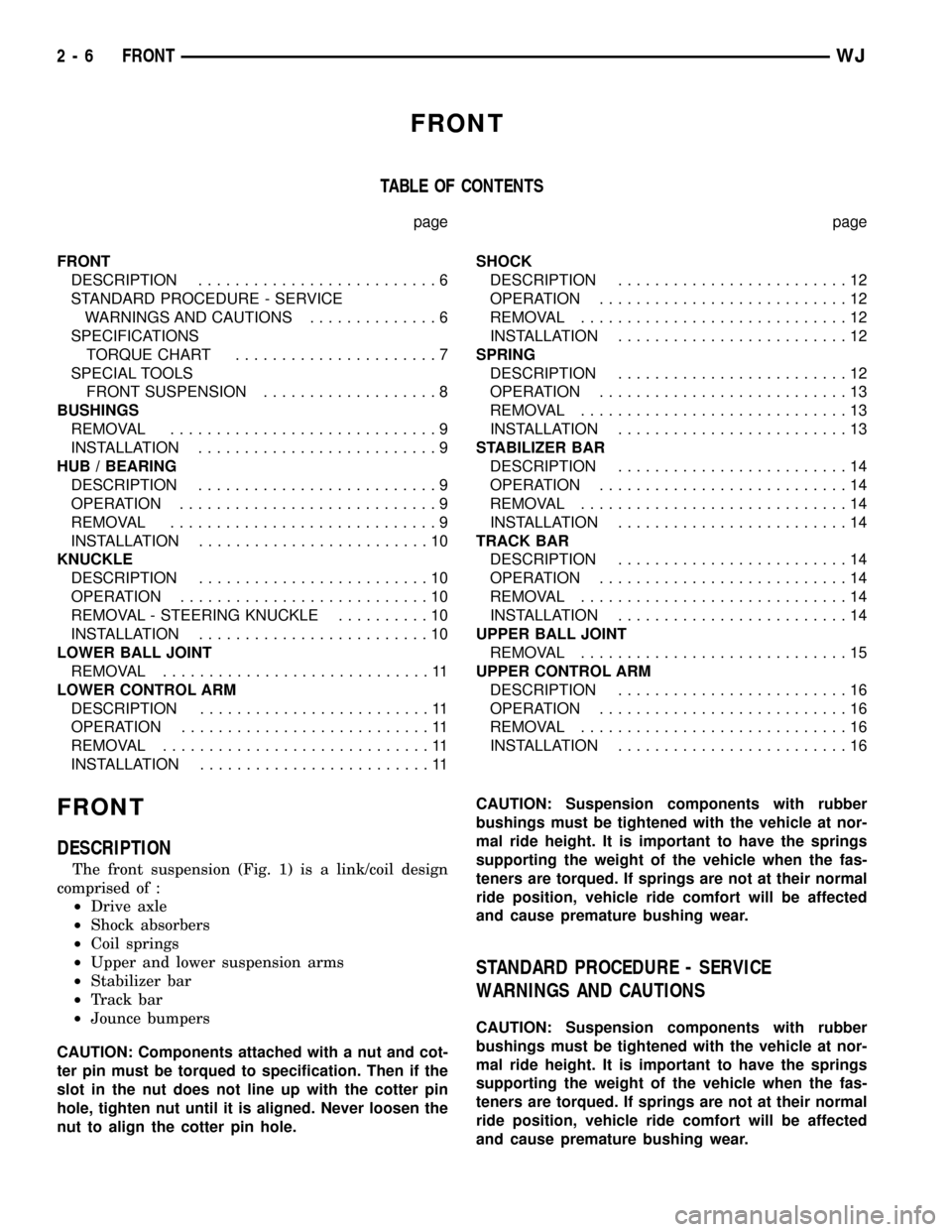
FRONT
TABLE OF CONTENTS
page page
FRONT
DESCRIPTION..........................6
STANDARD PROCEDURE - SERVICE
WARNINGS AND CAUTIONS..............6
SPECIFICATIONS
TORQUE CHART......................7
SPECIAL TOOLS
FRONT SUSPENSION...................8
BUSHINGS
REMOVAL.............................9
INSTALLATION..........................9
HUB / BEARING
DESCRIPTION..........................9
OPERATION............................9
REMOVAL.............................9
INSTALLATION.........................10
KNUCKLE
DESCRIPTION.........................10
OPERATION...........................10
REMOVAL - STEERING KNUCKLE..........10
INSTALLATION.........................10
LOWER BALL JOINT
REMOVAL.............................11
LOWER CONTROL ARM
DESCRIPTION.........................11
OPERATION...........................11
REMOVAL.............................11
INSTALLATION.........................11SHOCK
DESCRIPTION.........................12
OPERATION...........................12
REMOVAL.............................12
INSTALLATION.........................12
SPRING
DESCRIPTION.........................12
OPERATION...........................13
REMOVAL.............................13
INSTALLATION.........................13
STABILIZER BAR
DESCRIPTION.........................14
OPERATION...........................14
REMOVAL.............................14
INSTALLATION.........................14
TRACK BAR
DESCRIPTION.........................14
OPERATION...........................14
REMOVAL.............................14
INSTALLATION.........................14
UPPER BALL JOINT
REMOVAL.............................15
UPPER CONTROL ARM
DESCRIPTION.........................16
OPERATION...........................16
REMOVAL.............................16
INSTALLATION.........................16
FRONT
DESCRIPTION
The front suspension (Fig. 1) is a link/coil design
comprised of :
²Drive axle
²Shock absorbers
²Coil springs
²Upper and lower suspension arms
²Stabilizer bar
²Track bar
²Jounce bumpers
CAUTION: Components attached with a nut and cot-
ter pin must be torqued to specification. Then if the
slot in the nut does not line up with the cotter pin
hole, tighten nut until it is aligned. Never loosen the
nut to align the cotter pin hole.CAUTION: Suspension components with rubber
bushings must be tightened with the vehicle at nor-
mal ride height. It is important to have the springs
supporting the weight of the vehicle when the fas-
teners are torqued. If springs are not at their normal
ride position, vehicle ride comfort will be affected
and cause premature bushing wear.
STANDARD PROCEDURE - SERVICE
WARNINGS AND CAUTIONS
CAUTION: Suspension components with rubber
bushings must be tightened with the vehicle at nor-
mal ride height. It is important to have the springs
supporting the weight of the vehicle when the fas-
teners are torqued. If springs are not at their normal
ride position, vehicle ride comfort will be affected
and cause premature bushing wear.
2 - 6 FRONTWJ
Page 32 of 2199
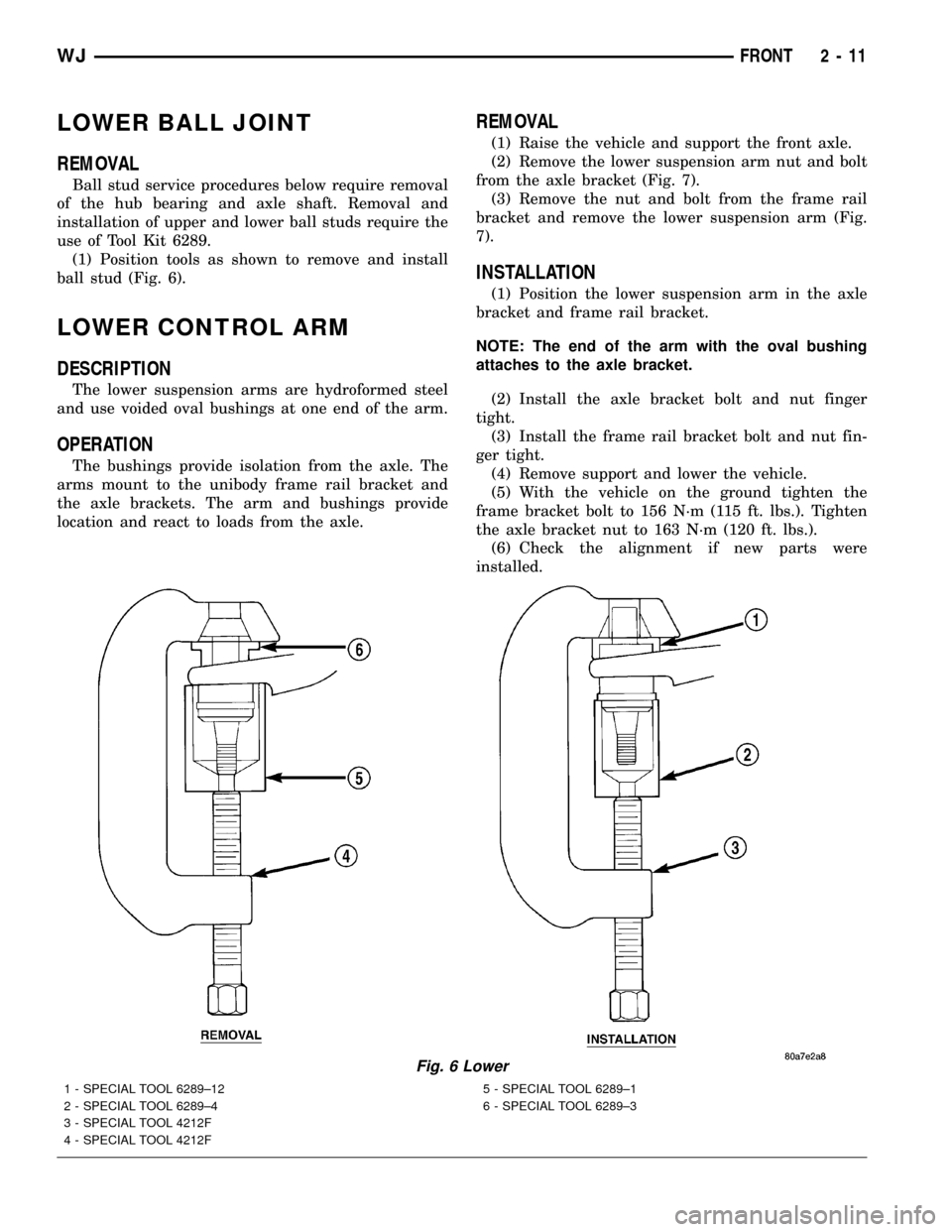
LOWER BALL JOINT
REMOVAL
Ball stud service procedures below require removal
of the hub bearing and axle shaft. Removal and
installation of upper and lower ball studs require the
use of Tool Kit 6289.
(1) Position tools as shown to remove and install
ball stud (Fig. 6).
LOWER CONTROL ARM
DESCRIPTION
The lower suspension arms are hydroformed steel
and use voided oval bushings at one end of the arm.
OPERATION
The bushings provide isolation from the axle. The
arms mount to the unibody frame rail bracket and
the axle brackets. The arm and bushings provide
location and react to loads from the axle.
REMOVAL
(1) Raise the vehicle and support the front axle.
(2) Remove the lower suspension arm nut and bolt
from the axle bracket (Fig. 7).
(3) Remove the nut and bolt from the frame rail
bracket and remove the lower suspension arm (Fig.
7).
INSTALLATION
(1) Position the lower suspension arm in the axle
bracket and frame rail bracket.
NOTE: The end of the arm with the oval bushing
attaches to the axle bracket.
(2) Install the axle bracket bolt and nut finger
tight.
(3) Install the frame rail bracket bolt and nut fin-
ger tight.
(4) Remove support and lower the vehicle.
(5) With the vehicle on the ground tighten the
frame bracket bolt to 156 N´m (115 ft. lbs.). Tighten
the axle bracket nut to 163 N´m (120 ft. lbs.).
(6) Check the alignment if new parts were
installed.
Fig. 6 Lower
1 - SPECIAL TOOL 6289±12
2 - SPECIAL TOOL 6289±4
3 - SPECIAL TOOL 4212F
4 - SPECIAL TOOL 4212F5 - SPECIAL TOOL 6289±1
6 - SPECIAL TOOL 6289±3
WJFRONT 2 - 11
Page 33 of 2199
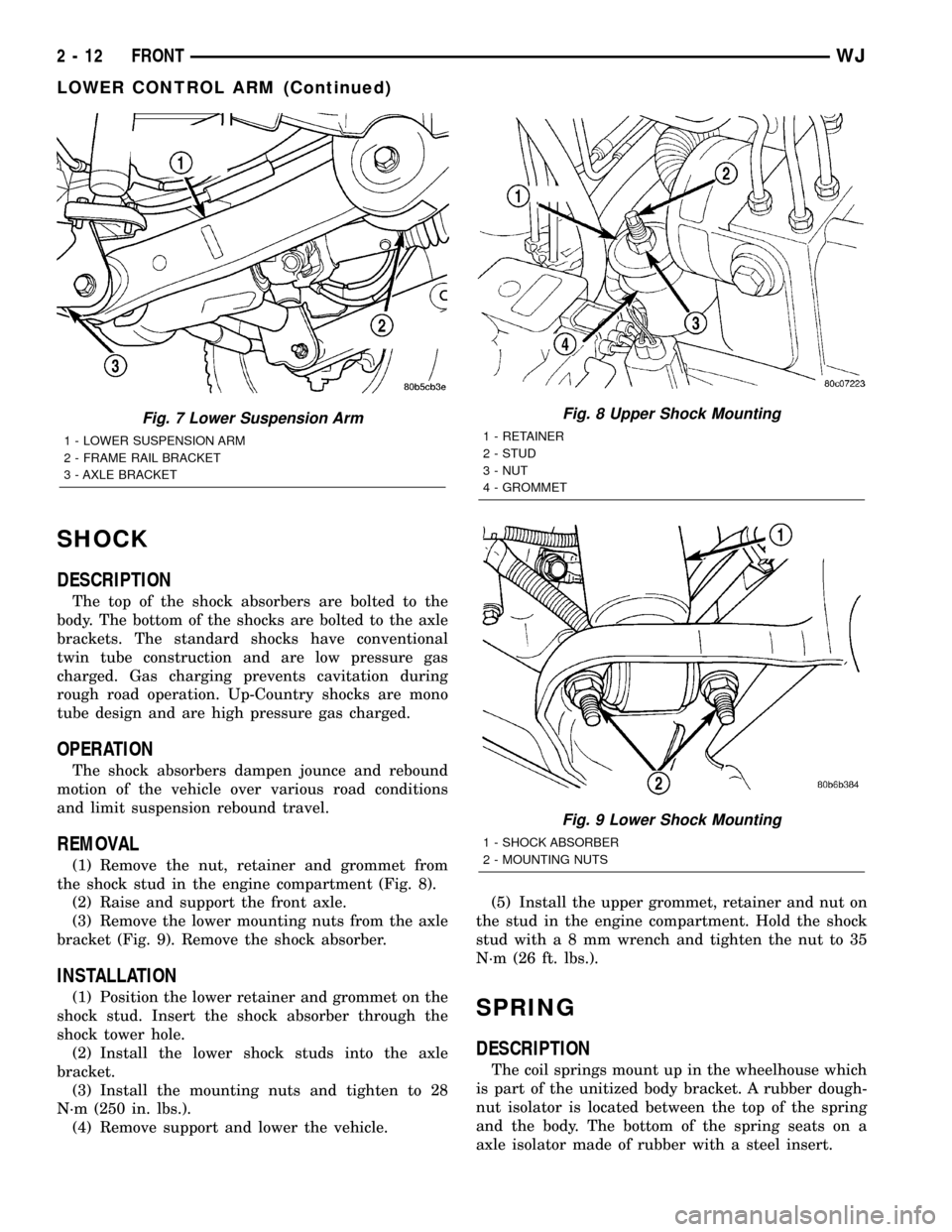
SHOCK
DESCRIPTION
The top of the shock absorbers are bolted to the
body. The bottom of the shocks are bolted to the axle
brackets. The standard shocks have conventional
twin tube construction and are low pressure gas
charged. Gas charging prevents cavitation during
rough road operation. Up-Country shocks are mono
tube design and are high pressure gas charged.
OPERATION
The shock absorbers dampen jounce and rebound
motion of the vehicle over various road conditions
and limit suspension rebound travel.
REMOVAL
(1) Remove the nut, retainer and grommet from
the shock stud in the engine compartment (Fig. 8).
(2) Raise and support the front axle.
(3) Remove the lower mounting nuts from the axle
bracket (Fig. 9). Remove the shock absorber.
INSTALLATION
(1) Position the lower retainer and grommet on the
shock stud. Insert the shock absorber through the
shock tower hole.
(2) Install the lower shock studs into the axle
bracket.
(3) Install the mounting nuts and tighten to 28
N´m (250 in. lbs.).
(4) Remove support and lower the vehicle.(5) Install the upper grommet, retainer and nut on
the stud in the engine compartment. Hold the shock
stud witha8mmwrench and tighten the nut to 35
N´m (26 ft. lbs.).SPRING
DESCRIPTION
The coil springs mount up in the wheelhouse which
is part of the unitized body bracket. A rubber dough-
nut isolator is located between the top of the spring
and the body. The bottom of the spring seats on a
axle isolator made of rubber with a steel insert.
Fig. 7 Lower Suspension Arm
1 - LOWER SUSPENSION ARM
2 - FRAME RAIL BRACKET
3 - AXLE BRACKET
Fig. 8 Upper Shock Mounting
1 - RETAINER
2 - STUD
3 - NUT
4 - GROMMET
Fig. 9 Lower Shock Mounting
1 - SHOCK ABSORBER
2 - MOUNTING NUTS
2 - 12 FRONTWJ
LOWER CONTROL ARM (Continued)
Page 37 of 2199
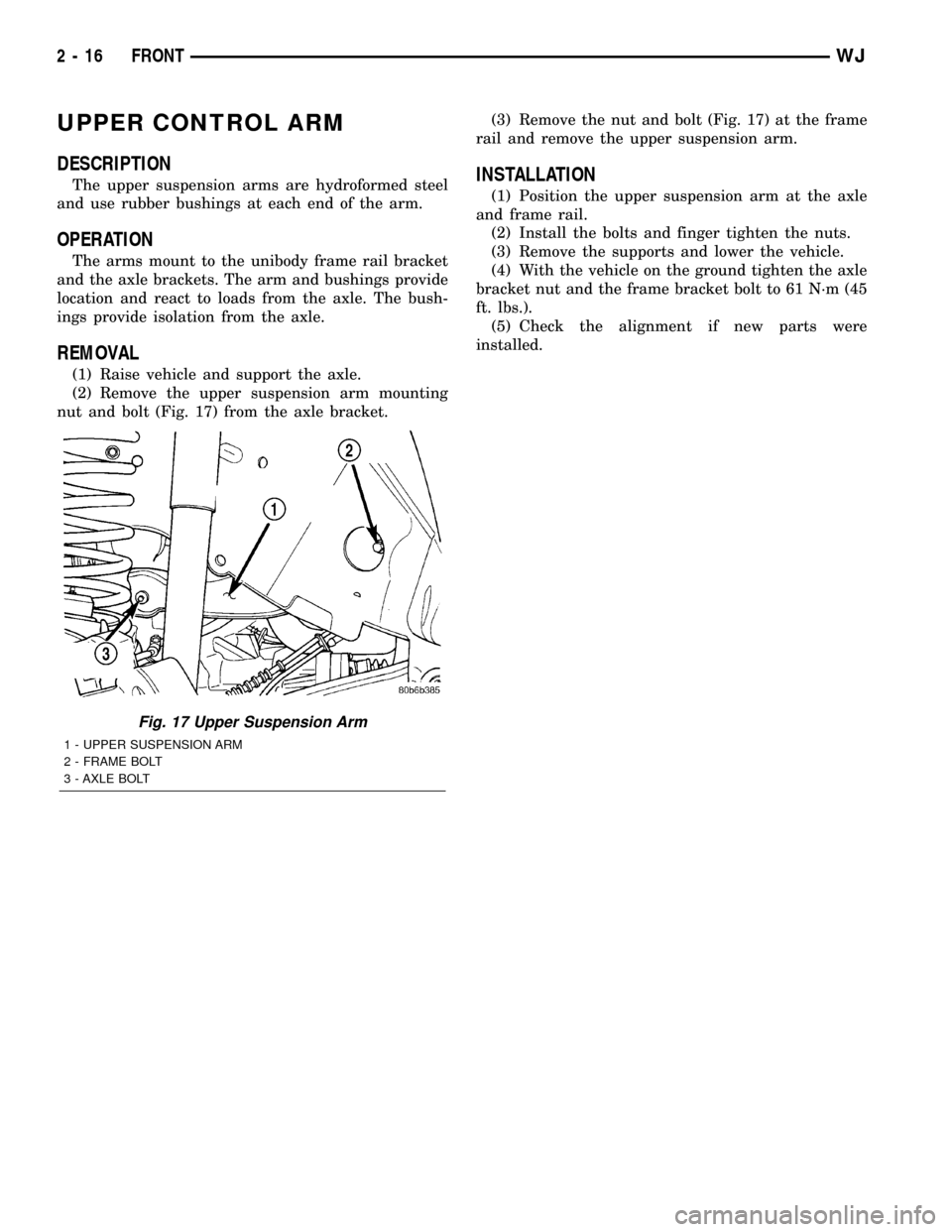
UPPER CONTROL ARM
DESCRIPTION
The upper suspension arms are hydroformed steel
and use rubber bushings at each end of the arm.
OPERATION
The arms mount to the unibody frame rail bracket
and the axle brackets. The arm and bushings provide
location and react to loads from the axle. The bush-
ings provide isolation from the axle.
REMOVAL
(1) Raise vehicle and support the axle.
(2) Remove the upper suspension arm mounting
nut and bolt (Fig. 17) from the axle bracket.(3) Remove the nut and bolt (Fig. 17) at the frame
rail and remove the upper suspension arm.
INSTALLATION
(1) Position the upper suspension arm at the axle
and frame rail.
(2) Install the bolts and finger tighten the nuts.
(3) Remove the supports and lower the vehicle.
(4) With the vehicle on the ground tighten the axle
bracket nut and the frame bracket bolt to 61 N´m (45
ft. lbs.).
(5) Check the alignment if new parts were
installed.
Fig. 17 Upper Suspension Arm
1 - UPPER SUSPENSION ARM
2 - FRAME BOLT
3 - AXLE BOLT
2 - 16 FRONTWJ
Page 270 of 2199
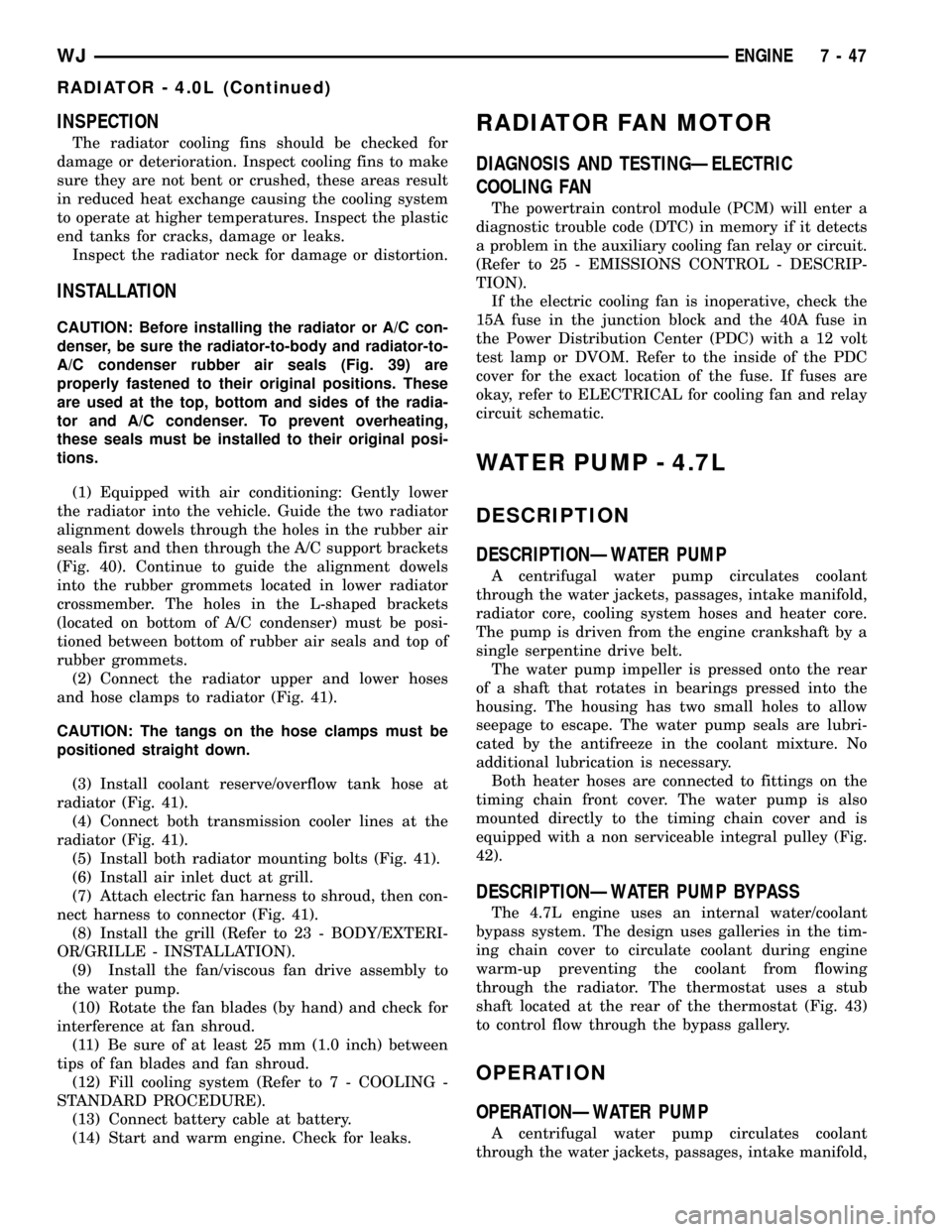
INSPECTION
The radiator cooling fins should be checked for
damage or deterioration. Inspect cooling fins to make
sure they are not bent or crushed, these areas result
in reduced heat exchange causing the cooling system
to operate at higher temperatures. Inspect the plastic
end tanks for cracks, damage or leaks.
Inspect the radiator neck for damage or distortion.
INSTALLATION
CAUTION: Before installing the radiator or A/C con-
denser, be sure the radiator-to-body and radiator-to-
A/C condenser rubber air seals (Fig. 39) are
properly fastened to their original positions. These
are used at the top, bottom and sides of the radia-
tor and A/C condenser. To prevent overheating,
these seals must be installed to their original posi-
tions.
(1) Equipped with air conditioning: Gently lower
the radiator into the vehicle. Guide the two radiator
alignment dowels through the holes in the rubber air
seals first and then through the A/C support brackets
(Fig. 40). Continue to guide the alignment dowels
into the rubber grommets located in lower radiator
crossmember. The holes in the L-shaped brackets
(located on bottom of A/C condenser) must be posi-
tioned between bottom of rubber air seals and top of
rubber grommets.
(2) Connect the radiator upper and lower hoses
and hose clamps to radiator (Fig. 41).
CAUTION: The tangs on the hose clamps must be
positioned straight down.
(3) Install coolant reserve/overflow tank hose at
radiator (Fig. 41).
(4) Connect both transmission cooler lines at the
radiator (Fig. 41).
(5) Install both radiator mounting bolts (Fig. 41).
(6) Install air inlet duct at grill.
(7) Attach electric fan harness to shroud, then con-
nect harness to connector (Fig. 41).
(8) Install the grill (Refer to 23 - BODY/EXTERI-
OR/GRILLE - INSTALLATION).
(9) Install the fan/viscous fan drive assembly to
the water pump.
(10) Rotate the fan blades (by hand) and check for
interference at fan shroud.
(11) Be sure of at least 25 mm (1.0 inch) between
tips of fan blades and fan shroud.
(12) Fill cooling system (Refer to 7 - COOLING -
STANDARD PROCEDURE).
(13) Connect battery cable at battery.
(14) Start and warm engine. Check for leaks.
RADIATOR FAN MOTOR
DIAGNOSIS AND TESTINGÐELECTRIC
COOLING FAN
The powertrain control module (PCM) will enter a
diagnostic trouble code (DTC) in memory if it detects
a problem in the auxiliary cooling fan relay or circuit.
(Refer to 25 - EMISSIONS CONTROL - DESCRIP-
TION).
If the electric cooling fan is inoperative, check the
15A fuse in the junction block and the 40A fuse in
the Power Distribution Center (PDC) with a 12 volt
test lamp or DVOM. Refer to the inside of the PDC
cover for the exact location of the fuse. If fuses are
okay, refer to ELECTRICAL for cooling fan and relay
circuit schematic.
WATER PUMP - 4.7L
DESCRIPTION
DESCRIPTIONÐWATER PUMP
A centrifugal water pump circulates coolant
through the water jackets, passages, intake manifold,
radiator core, cooling system hoses and heater core.
The pump is driven from the engine crankshaft by a
single serpentine drive belt.
The water pump impeller is pressed onto the rear
of a shaft that rotates in bearings pressed into the
housing. The housing has two small holes to allow
seepage to escape. The water pump seals are lubri-
cated by the antifreeze in the coolant mixture. No
additional lubrication is necessary.
Both heater hoses are connected to fittings on the
timing chain front cover. The water pump is also
mounted directly to the timing chain cover and is
equipped with a non serviceable integral pulley (Fig.
42).
DESCRIPTIONÐWATER PUMP BYPASS
The 4.7L engine uses an internal water/coolant
bypass system. The design uses galleries in the tim-
ing chain cover to circulate coolant during engine
warm-up preventing the coolant from flowing
through the radiator. The thermostat uses a stub
shaft located at the rear of the thermostat (Fig. 43)
to control flow through the bypass gallery.
OPERATION
OPERATIONÐWATER PUMP
A centrifugal water pump circulates coolant
through the water jackets, passages, intake manifold,
WJENGINE 7 - 47
RADIATOR - 4.0L (Continued)
Page 543 of 2199
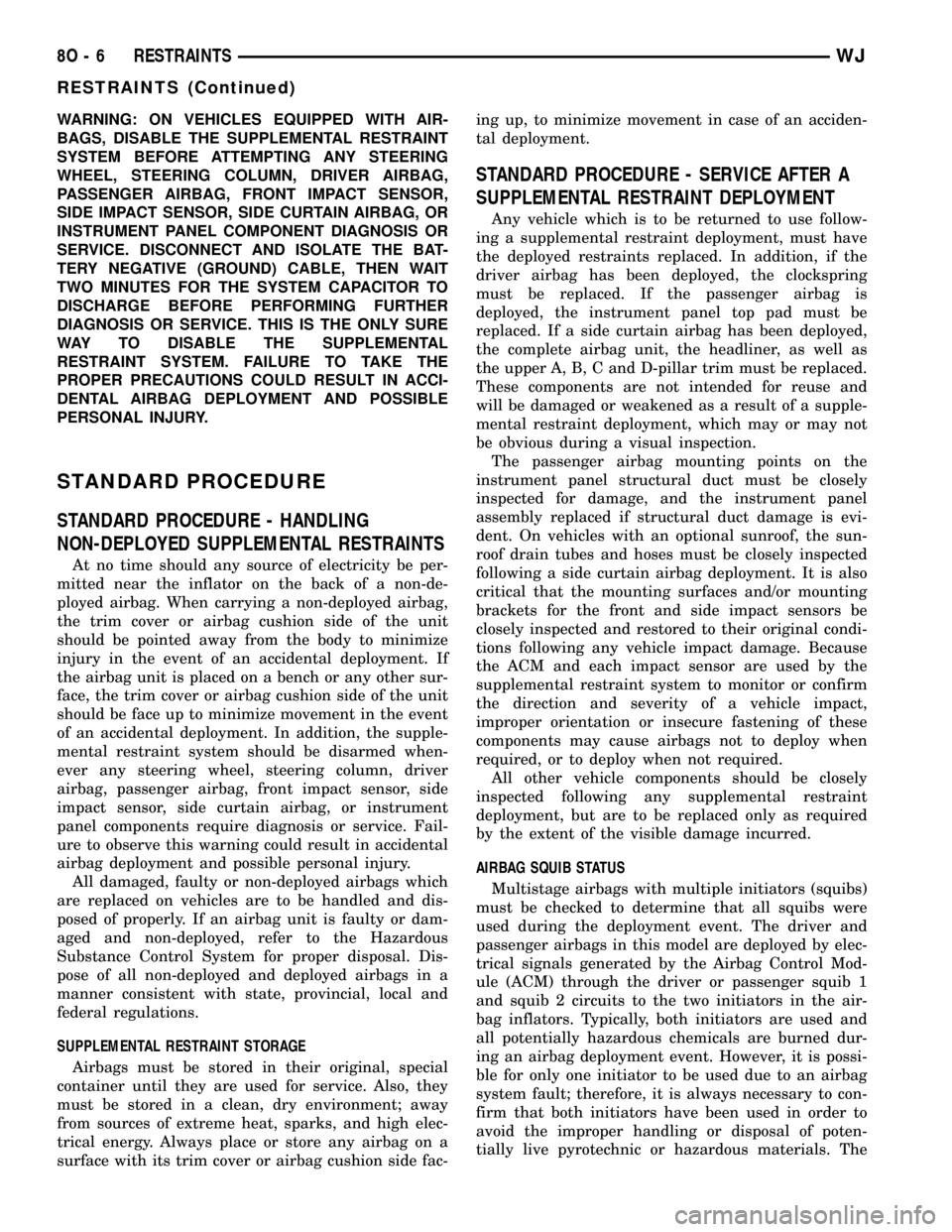
WARNING: ON VEHICLES EQUIPPED WITH AIR-
BAGS, DISABLE THE SUPPLEMENTAL RESTRAINT
SYSTEM BEFORE ATTEMPTING ANY STEERING
WHEEL, STEERING COLUMN, DRIVER AIRBAG,
PASSENGER AIRBAG, FRONT IMPACT SENSOR,
SIDE IMPACT SENSOR, SIDE CURTAIN AIRBAG, OR
INSTRUMENT PANEL COMPONENT DIAGNOSIS OR
SERVICE. DISCONNECT AND ISOLATE THE BAT-
TERY NEGATIVE (GROUND) CABLE, THEN WAIT
TWO MINUTES FOR THE SYSTEM CAPACITOR TO
DISCHARGE BEFORE PERFORMING FURTHER
DIAGNOSIS OR SERVICE. THIS IS THE ONLY SURE
WAY TO DISABLE THE SUPPLEMENTAL
RESTRAINT SYSTEM. FAILURE TO TAKE THE
PROPER PRECAUTIONS COULD RESULT IN ACCI-
DENTAL AIRBAG DEPLOYMENT AND POSSIBLE
PERSONAL INJURY.
STANDARD PROCEDURE
STANDARD PROCEDURE - HANDLING
NON-DEPLOYED SUPPLEMENTAL RESTRAINTS
At no time should any source of electricity be per-
mitted near the inflator on the back of a non-de-
ployed airbag. When carrying a non-deployed airbag,
the trim cover or airbag cushion side of the unit
should be pointed away from the body to minimize
injury in the event of an accidental deployment. If
the airbag unit is placed on a bench or any other sur-
face, the trim cover or airbag cushion side of the unit
should be face up to minimize movement in the event
of an accidental deployment. In addition, the supple-
mental restraint system should be disarmed when-
ever any steering wheel, steering column, driver
airbag, passenger airbag, front impact sensor, side
impact sensor, side curtain airbag, or instrument
panel components require diagnosis or service. Fail-
ure to observe this warning could result in accidental
airbag deployment and possible personal injury.
All damaged, faulty or non-deployed airbags which
are replaced on vehicles are to be handled and dis-
posed of properly. If an airbag unit is faulty or dam-
aged and non-deployed, refer to the Hazardous
Substance Control System for proper disposal. Dis-
pose of all non-deployed and deployed airbags in a
manner consistent with state, provincial, local and
federal regulations.
SUPPLEMENTAL RESTRAINT STORAGE
Airbags must be stored in their original, special
container until they are used for service. Also, they
must be stored in a clean, dry environment; away
from sources of extreme heat, sparks, and high elec-
trical energy. Always place or store any airbag on a
surface with its trim cover or airbag cushion side fac-ing up, to minimize movement in case of an acciden-
tal deployment.
STANDARD PROCEDURE - SERVICE AFTER A
SUPPLEMENTAL RESTRAINT DEPLOYMENT
Any vehicle which is to be returned to use follow-
ing a supplemental restraint deployment, must have
the deployed restraints replaced. In addition, if the
driver airbag has been deployed, the clockspring
must be replaced. If the passenger airbag is
deployed, the instrument panel top pad must be
replaced. If a side curtain airbag has been deployed,
the complete airbag unit, the headliner, as well as
the upper A, B, C and D-pillar trim must be replaced.
These components are not intended for reuse and
will be damaged or weakened as a result of a supple-
mental restraint deployment, which may or may not
be obvious during a visual inspection.
The passenger airbag mounting points on the
instrument panel structural duct must be closely
inspected for damage, and the instrument panel
assembly replaced if structural duct damage is evi-
dent. On vehicles with an optional sunroof, the sun-
roof drain tubes and hoses must be closely inspected
following a side curtain airbag deployment. It is also
critical that the mounting surfaces and/or mounting
brackets for the front and side impact sensors be
closely inspected and restored to their original condi-
tions following any vehicle impact damage. Because
the ACM and each impact sensor are used by the
supplemental restraint system to monitor or confirm
the direction and severity of a vehicle impact,
improper orientation or insecure fastening of these
components may cause airbags not to deploy when
required, or to deploy when not required.
All other vehicle components should be closely
inspected following any supplemental restraint
deployment, but are to be replaced only as required
by the extent of the visible damage incurred.
AIRBAG SQUIB STATUS
Multistage airbags with multiple initiators (squibs)
must be checked to determine that all squibs were
used during the deployment event. The driver and
passenger airbags in this model are deployed by elec-
trical signals generated by the Airbag Control Mod-
ule (ACM) through the driver or passenger squib 1
and squib 2 circuits to the two initiators in the air-
bag inflators. Typically, both initiators are used and
all potentially hazardous chemicals are burned dur-
ing an airbag deployment event. However, it is possi-
ble for only one initiator to be used due to an airbag
system fault; therefore, it is always necessary to con-
firm that both initiators have been used in order to
avoid the improper handling or disposal of poten-
tially live pyrotechnic or hazardous materials. The
8O - 6 RESTRAINTSWJ
RESTRAINTS (Continued)
Page 567 of 2199
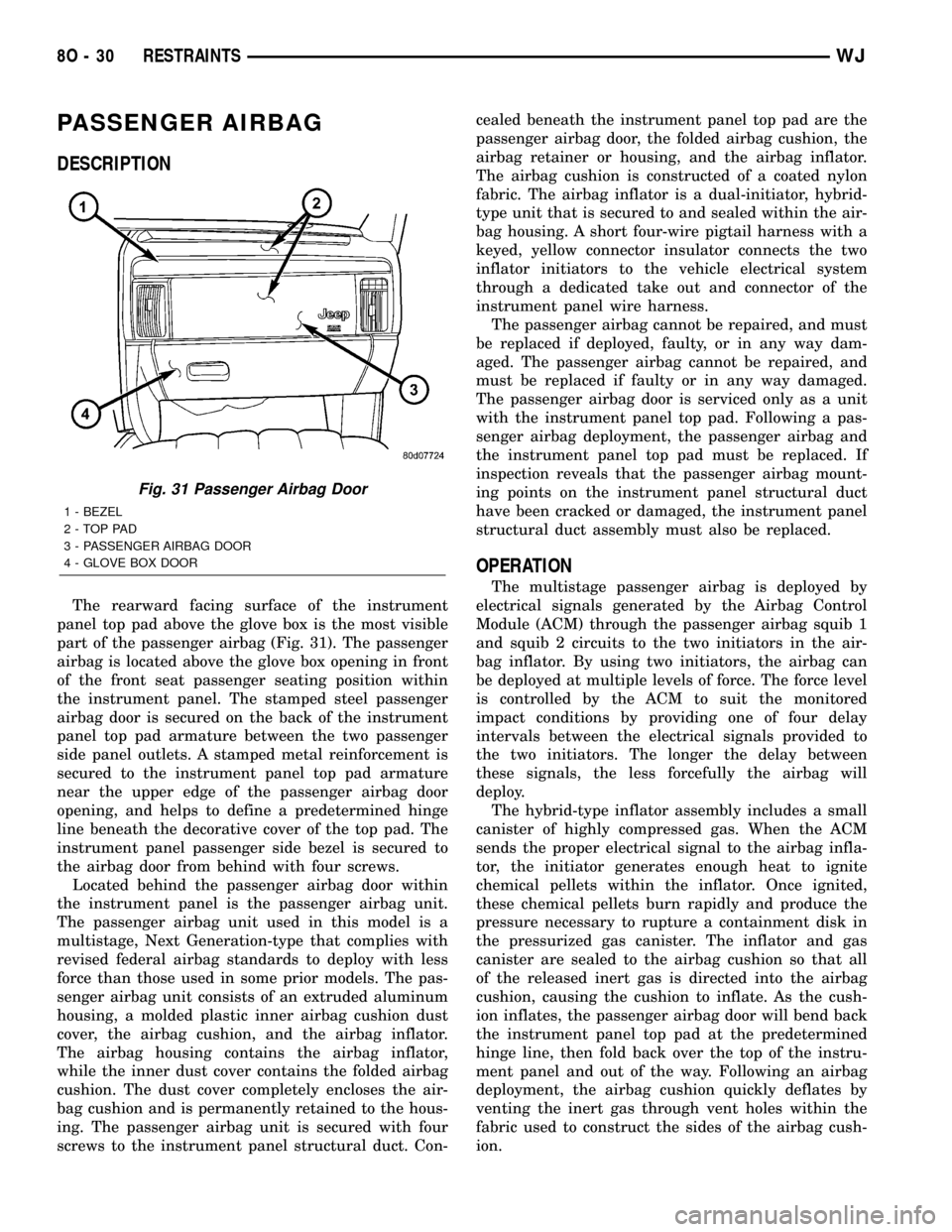
PASSENGER AIRBAG
DESCRIPTION
The rearward facing surface of the instrument
panel top pad above the glove box is the most visible
part of the passenger airbag (Fig. 31). The passenger
airbag is located above the glove box opening in front
of the front seat passenger seating position within
the instrument panel. The stamped steel passenger
airbag door is secured on the back of the instrument
panel top pad armature between the two passenger
side panel outlets. A stamped metal reinforcement is
secured to the instrument panel top pad armature
near the upper edge of the passenger airbag door
opening, and helps to define a predetermined hinge
line beneath the decorative cover of the top pad. The
instrument panel passenger side bezel is secured to
the airbag door from behind with four screws.
Located behind the passenger airbag door within
the instrument panel is the passenger airbag unit.
The passenger airbag unit used in this model is a
multistage, Next Generation-type that complies with
revised federal airbag standards to deploy with less
force than those used in some prior models. The pas-
senger airbag unit consists of an extruded aluminum
housing, a molded plastic inner airbag cushion dust
cover, the airbag cushion, and the airbag inflator.
The airbag housing contains the airbag inflator,
while the inner dust cover contains the folded airbag
cushion. The dust cover completely encloses the air-
bag cushion and is permanently retained to the hous-
ing. The passenger airbag unit is secured with four
screws to the instrument panel structural duct. Con-cealed beneath the instrument panel top pad are the
passenger airbag door, the folded airbag cushion, the
airbag retainer or housing, and the airbag inflator.
The airbag cushion is constructed of a coated nylon
fabric. The airbag inflator is a dual-initiator, hybrid-
type unit that is secured to and sealed within the air-
bag housing. A short four-wire pigtail harness with a
keyed, yellow connector insulator connects the two
inflator initiators to the vehicle electrical system
through a dedicated take out and connector of the
instrument panel wire harness.
The passenger airbag cannot be repaired, and must
be replaced if deployed, faulty, or in any way dam-
aged. The passenger airbag cannot be repaired, and
must be replaced if faulty or in any way damaged.
The passenger airbag door is serviced only as a unit
with the instrument panel top pad. Following a pas-
senger airbag deployment, the passenger airbag and
the instrument panel top pad must be replaced. If
inspection reveals that the passenger airbag mount-
ing points on the instrument panel structural duct
have been cracked or damaged, the instrument panel
structural duct assembly must also be replaced.
OPERATION
The multistage passenger airbag is deployed by
electrical signals generated by the Airbag Control
Module (ACM) through the passenger airbag squib 1
and squib 2 circuits to the two initiators in the air-
bag inflator. By using two initiators, the airbag can
be deployed at multiple levels of force. The force level
is controlled by the ACM to suit the monitored
impact conditions by providing one of four delay
intervals between the electrical signals provided to
the two initiators. The longer the delay between
these signals, the less forcefully the airbag will
deploy.
The hybrid-type inflator assembly includes a small
canister of highly compressed gas. When the ACM
sends the proper electrical signal to the airbag infla-
tor, the initiator generates enough heat to ignite
chemical pellets within the inflator. Once ignited,
these chemical pellets burn rapidly and produce the
pressure necessary to rupture a containment disk in
the pressurized gas canister. The inflator and gas
canister are sealed to the airbag cushion so that all
of the released inert gas is directed into the airbag
cushion, causing the cushion to inflate. As the cush-
ion inflates, the passenger airbag door will bend back
the instrument panel top pad at the predetermined
hinge line, then fold back over the top of the instru-
ment panel and out of the way. Following an airbag
deployment, the airbag cushion quickly deflates by
venting the inert gas through vent holes within the
fabric used to construct the sides of the airbag cush-
ion.
Fig. 31 Passenger Airbag Door
1 - BEZEL
2-TOPPAD
3 - PASSENGER AIRBAG DOOR
4 - GLOVE BOX DOOR
8O - 30 RESTRAINTSWJ
Page 623 of 2199
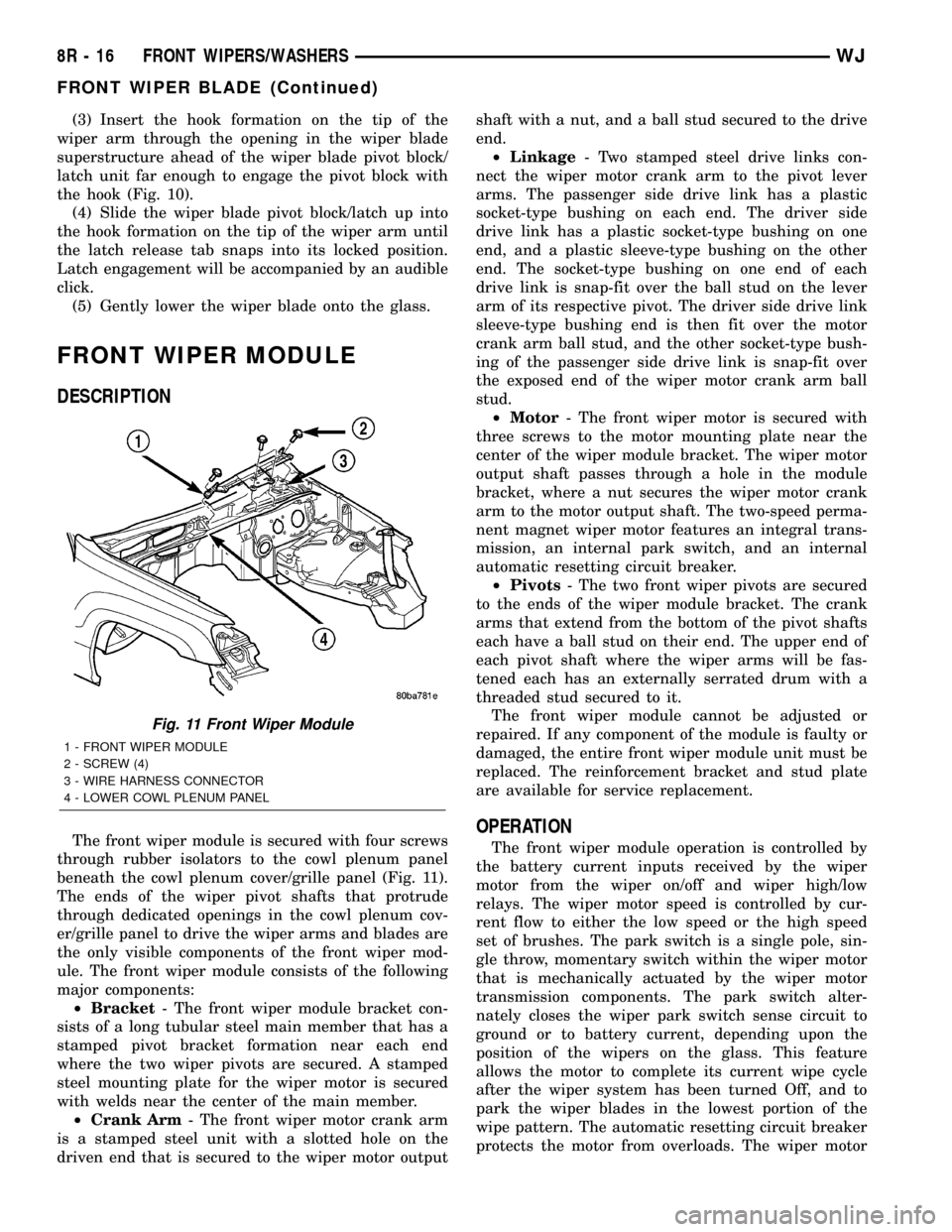
(3) Insert the hook formation on the tip of the
wiper arm through the opening in the wiper blade
superstructure ahead of the wiper blade pivot block/
latch unit far enough to engage the pivot block with
the hook (Fig. 10).
(4) Slide the wiper blade pivot block/latch up into
the hook formation on the tip of the wiper arm until
the latch release tab snaps into its locked position.
Latch engagement will be accompanied by an audible
click.
(5) Gently lower the wiper blade onto the glass.
FRONT WIPER MODULE
DESCRIPTION
The front wiper module is secured with four screws
through rubber isolators to the cowl plenum panel
beneath the cowl plenum cover/grille panel (Fig. 11).
The ends of the wiper pivot shafts that protrude
through dedicated openings in the cowl plenum cov-
er/grille panel to drive the wiper arms and blades are
the only visible components of the front wiper mod-
ule. The front wiper module consists of the following
major components:
²Bracket- The front wiper module bracket con-
sists of a long tubular steel main member that has a
stamped pivot bracket formation near each end
where the two wiper pivots are secured. A stamped
steel mounting plate for the wiper motor is secured
with welds near the center of the main member.
²Crank Arm- The front wiper motor crank arm
is a stamped steel unit with a slotted hole on the
driven end that is secured to the wiper motor outputshaft with a nut, and a ball stud secured to the drive
end.
²Linkage- Two stamped steel drive links con-
nect the wiper motor crank arm to the pivot lever
arms. The passenger side drive link has a plastic
socket-type bushing on each end. The driver side
drive link has a plastic socket-type bushing on one
end, and a plastic sleeve-type bushing on the other
end. The socket-type bushing on one end of each
drive link is snap-fit over the ball stud on the lever
arm of its respective pivot. The driver side drive link
sleeve-type bushing end is then fit over the motor
crank arm ball stud, and the other socket-type bush-
ing of the passenger side drive link is snap-fit over
the exposed end of the wiper motor crank arm ball
stud.
²Motor- The front wiper motor is secured with
three screws to the motor mounting plate near the
center of the wiper module bracket. The wiper motor
output shaft passes through a hole in the module
bracket, where a nut secures the wiper motor crank
arm to the motor output shaft. The two-speed perma-
nent magnet wiper motor features an integral trans-
mission, an internal park switch, and an internal
automatic resetting circuit breaker.
²Pivots- The two front wiper pivots are secured
to the ends of the wiper module bracket. The crank
arms that extend from the bottom of the pivot shafts
each have a ball stud on their end. The upper end of
each pivot shaft where the wiper arms will be fas-
tened each has an externally serrated drum with a
threaded stud secured to it.
The front wiper module cannot be adjusted or
repaired. If any component of the module is faulty or
damaged, the entire front wiper module unit must be
replaced. The reinforcement bracket and stud plate
are available for service replacement.OPERATION
The front wiper module operation is controlled by
the battery current inputs received by the wiper
motor from the wiper on/off and wiper high/low
relays. The wiper motor speed is controlled by cur-
rent flow to either the low speed or the high speed
set of brushes. The park switch is a single pole, sin-
gle throw, momentary switch within the wiper motor
that is mechanically actuated by the wiper motor
transmission components. The park switch alter-
nately closes the wiper park switch sense circuit to
ground or to battery current, depending upon the
position of the wipers on the glass. This feature
allows the motor to complete its current wipe cycle
after the wiper system has been turned Off, and to
park the wiper blades in the lowest portion of the
wipe pattern. The automatic resetting circuit breaker
protects the motor from overloads. The wiper motor
Fig. 11 Front Wiper Module
1 - FRONT WIPER MODULE
2 - SCREW (4)
3 - WIRE HARNESS CONNECTOR
4 - LOWER COWL PLENUM PANEL
8R - 16 FRONT WIPERS/WASHERSWJ
FRONT WIPER BLADE (Continued)
Page 625 of 2199
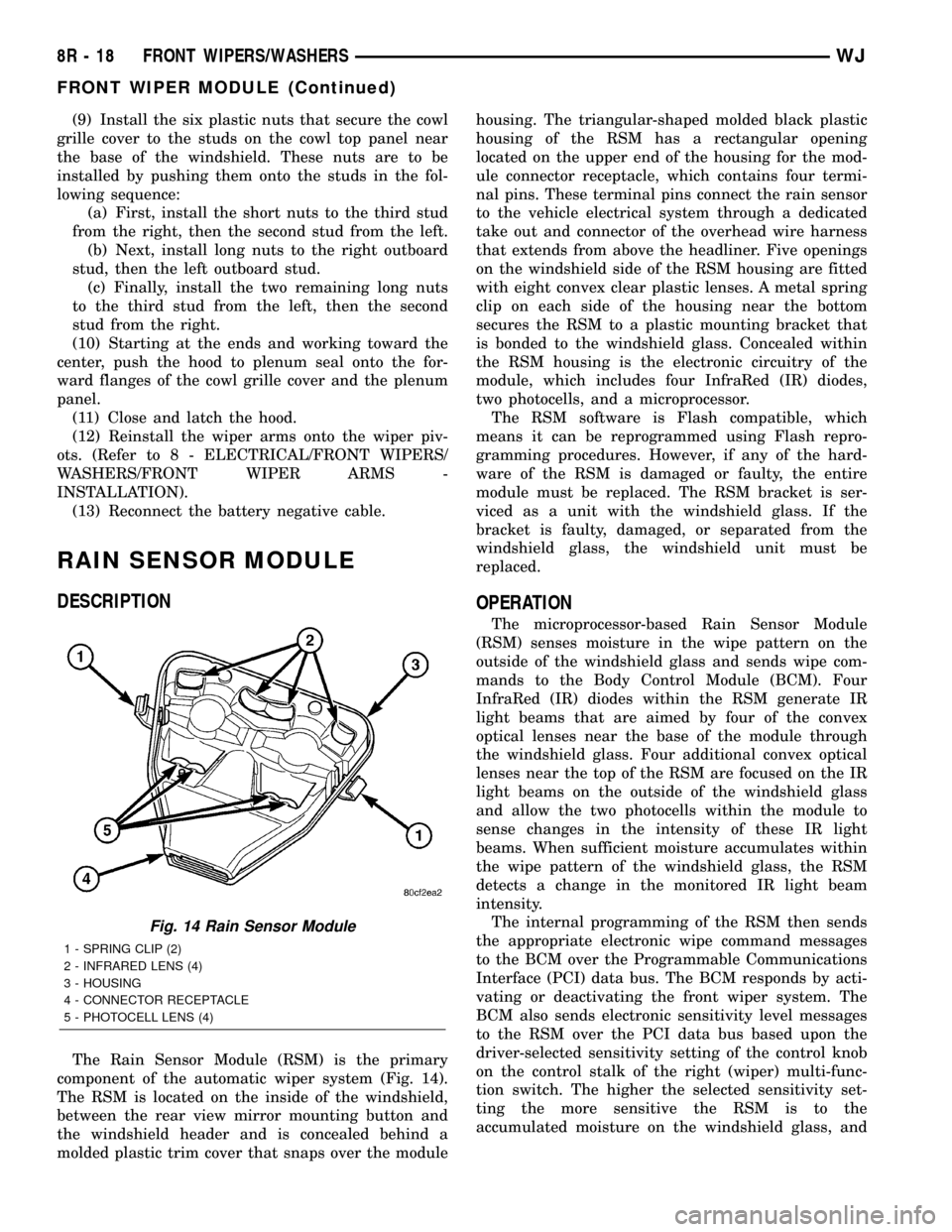
(9) Install the six plastic nuts that secure the cowl
grille cover to the studs on the cowl top panel near
the base of the windshield. These nuts are to be
installed by pushing them onto the studs in the fol-
lowing sequence:
(a) First, install the short nuts to the third stud
from the right, then the second stud from the left.
(b) Next, install long nuts to the right outboard
stud, then the left outboard stud.
(c) Finally, install the two remaining long nuts
to the third stud from the left, then the second
stud from the right.
(10) Starting at the ends and working toward the
center, push the hood to plenum seal onto the for-
ward flanges of the cowl grille cover and the plenum
panel.
(11) Close and latch the hood.
(12) Reinstall the wiper arms onto the wiper piv-
ots. (Refer to 8 - ELECTRICAL/FRONT WIPERS/
WASHERS/FRONT WIPER ARMS -
INSTALLATION).
(13) Reconnect the battery negative cable.
RAIN SENSOR MODULE
DESCRIPTION
The Rain Sensor Module (RSM) is the primary
component of the automatic wiper system (Fig. 14).
The RSM is located on the inside of the windshield,
between the rear view mirror mounting button and
the windshield header and is concealed behind a
molded plastic trim cover that snaps over the modulehousing. The triangular-shaped molded black plastic
housing of the RSM has a rectangular opening
located on the upper end of the housing for the mod-
ule connector receptacle, which contains four termi-
nal pins. These terminal pins connect the rain sensor
to the vehicle electrical system through a dedicated
take out and connector of the overhead wire harness
that extends from above the headliner. Five openings
on the windshield side of the RSM housing are fitted
with eight convex clear plastic lenses. A metal spring
clip on each side of the housing near the bottom
secures the RSM to a plastic mounting bracket that
is bonded to the windshield glass. Concealed within
the RSM housing is the electronic circuitry of the
module, which includes four InfraRed (IR) diodes,
two photocells, and a microprocessor.
The RSM software is Flash compatible, which
means it can be reprogrammed using Flash repro-
gramming procedures. However, if any of the hard-
ware of the RSM is damaged or faulty, the entire
module must be replaced. The RSM bracket is ser-
viced as a unit with the windshield glass. If the
bracket is faulty, damaged, or separated from the
windshield glass, the windshield unit must be
replaced.
OPERATION
The microprocessor-based Rain Sensor Module
(RSM) senses moisture in the wipe pattern on the
outside of the windshield glass and sends wipe com-
mands to the Body Control Module (BCM). Four
InfraRed (IR) diodes within the RSM generate IR
light beams that are aimed by four of the convex
optical lenses near the base of the module through
the windshield glass. Four additional convex optical
lenses near the top of the RSM are focused on the IR
light beams on the outside of the windshield glass
and allow the two photocells within the module to
sense changes in the intensity of these IR light
beams. When sufficient moisture accumulates within
the wipe pattern of the windshield glass, the RSM
detects a change in the monitored IR light beam
intensity.
The internal programming of the RSM then sends
the appropriate electronic wipe command messages
to the BCM over the Programmable Communications
Interface (PCI) data bus. The BCM responds by acti-
vating or deactivating the front wiper system. The
BCM also sends electronic sensitivity level messages
to the RSM over the PCI data bus based upon the
driver-selected sensitivity setting of the control knob
on the control stalk of the right (wiper) multi-func-
tion switch. The higher the selected sensitivity set-
ting the more sensitive the RSM is to the
accumulated moisture on the windshield glass, and
Fig. 14 Rain Sensor Module
1 - SPRING CLIP (2)
2 - INFRARED LENS (4)
3 - HOUSING
4 - CONNECTOR RECEPTACLE
5 - PHOTOCELL LENS (4)
8R - 18 FRONT WIPERS/WASHERSWJ
FRONT WIPER MODULE (Continued)
Page 1474 of 2199
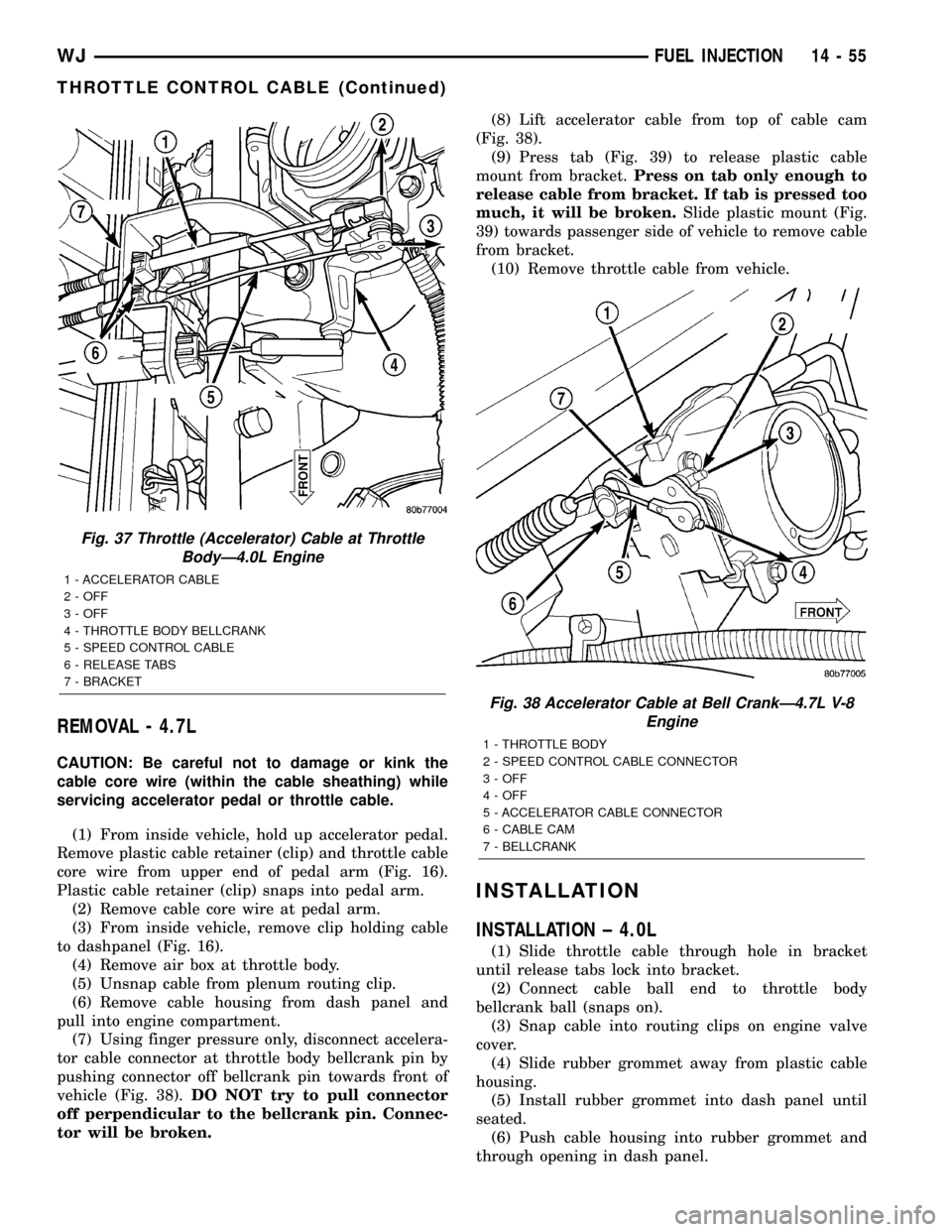
REMOVAL - 4.7L
CAUTION: Be careful not to damage or kink the
cable core wire (within the cable sheathing) while
servicing accelerator pedal or throttle cable.
(1) From inside vehicle, hold up accelerator pedal.
Remove plastic cable retainer (clip) and throttle cable
core wire from upper end of pedal arm (Fig. 16).
Plastic cable retainer (clip) snaps into pedal arm.
(2) Remove cable core wire at pedal arm.
(3) From inside vehicle, remove clip holding cable
to dashpanel (Fig. 16).
(4) Remove air box at throttle body.
(5) Unsnap cable from plenum routing clip.
(6) Remove cable housing from dash panel and
pull into engine compartment.
(7) Using finger pressure only, disconnect accelera-
tor cable connector at throttle body bellcrank pin by
pushing connector off bellcrank pin towards front of
vehicle (Fig. 38).DO NOT try to pull connector
off perpendicular to the bellcrank pin. Connec-
tor will be broken.(8) Lift accelerator cable from top of cable cam
(Fig. 38).
(9) Press tab (Fig. 39) to release plastic cable
mount from bracket.Press on tab only enough to
release cable from bracket. If tab is pressed too
much, it will be broken.Slide plastic mount (Fig.
39) towards passenger side of vehicle to remove cable
from bracket.
(10) Remove throttle cable from vehicle.
INSTALLATION
INSTALLATION ± 4.0L
(1) Slide throttle cable through hole in bracket
until release tabs lock into bracket.
(2) Connect cable ball end to throttle body
bellcrank ball (snaps on).
(3) Snap cable into routing clips on engine valve
cover.
(4) Slide rubber grommet away from plastic cable
housing.
(5) Install rubber grommet into dash panel until
seated.
(6) Push cable housing into rubber grommet and
through opening in dash panel.
Fig. 37 Throttle (Accelerator) Cable at Throttle
BodyÐ4.0L Engine
1 - ACCELERATOR CABLE
2 - OFF
3 - OFF
4 - THROTTLE BODY BELLCRANK
5 - SPEED CONTROL CABLE
6 - RELEASE TABS
7 - BRACKET
Fig. 38 Accelerator Cable at Bell CrankÐ4.7L V-8
Engine
1 - THROTTLE BODY
2 - SPEED CONTROL CABLE CONNECTOR
3 - OFF
4 - OFF
5 - ACCELERATOR CABLE CONNECTOR
6 - CABLE CAM
7 - BELLCRANK
WJFUEL INJECTION 14 - 55
THROTTLE CONTROL CABLE (Continued)