trouble codes JEEP GRAND CHEROKEE 2002 WJ / 2.G Workshop Manual
[x] Cancel search | Manufacturer: JEEP, Model Year: 2002, Model line: GRAND CHEROKEE, Model: JEEP GRAND CHEROKEE 2002 WJ / 2.GPages: 2199, PDF Size: 76.01 MB
Page 226 of 2199
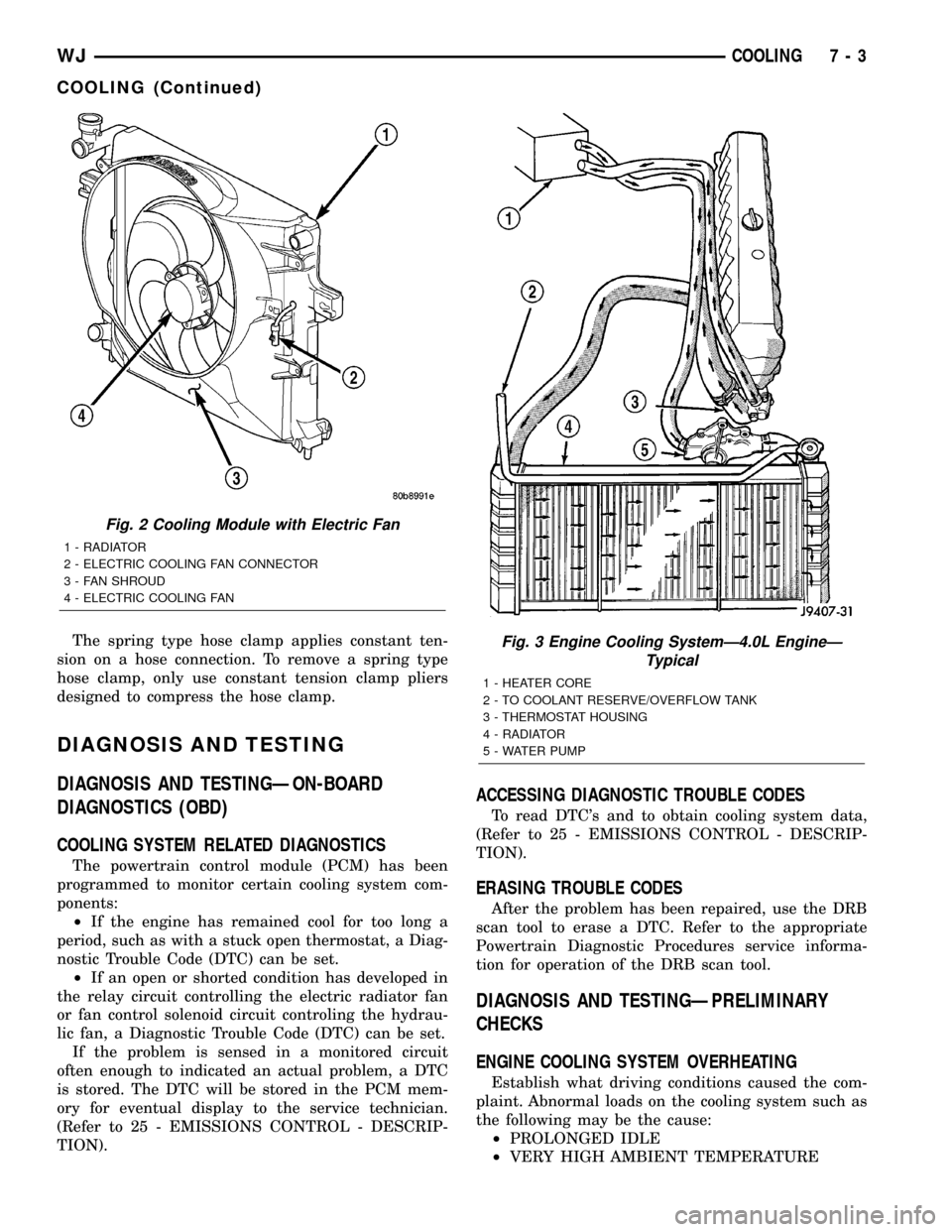
The spring type hose clamp applies constant ten-
sion on a hose connection. To remove a spring type
hose clamp, only use constant tension clamp pliers
designed to compress the hose clamp.
DIAGNOSIS AND TESTING
DIAGNOSIS AND TESTINGÐON-BOARD
DIAGNOSTICS (OBD)
COOLING SYSTEM RELATED DIAGNOSTICS
The powertrain control module (PCM) has been
programmed to monitor certain cooling system com-
ponents:
²If the engine has remained cool for too long a
period, such as with a stuck open thermostat, a Diag-
nostic Trouble Code (DTC) can be set.
²If an open or shorted condition has developed in
the relay circuit controlling the electric radiator fan
or fan control solenoid circuit controling the hydrau-
lic fan, a Diagnostic Trouble Code (DTC) can be set.
If the problem is sensed in a monitored circuit
often enough to indicated an actual problem, a DTC
is stored. The DTC will be stored in the PCM mem-
ory for eventual display to the service technician.
(Refer to 25 - EMISSIONS CONTROL - DESCRIP-
TION).
ACCESSING DIAGNOSTIC TROUBLE CODES
To read DTC's and to obtain cooling system data,
(Refer to 25 - EMISSIONS CONTROL - DESCRIP-
TION).
ERASING TROUBLE CODES
After the problem has been repaired, use the DRB
scan tool to erase a DTC. Refer to the appropriate
Powertrain Diagnostic Procedures service informa-
tion for operation of the DRB scan tool.
DIAGNOSIS AND TESTINGÐPRELIMINARY
CHECKS
ENGINE COOLING SYSTEM OVERHEATING
Establish what driving conditions caused the com-
plaint. Abnormal loads on the cooling system such as
the following may be the cause:
²PROLONGED IDLE
²VERY HIGH AMBIENT TEMPERATURE
Fig. 2 Cooling Module with Electric Fan
1 - RADIATOR
2 - ELECTRIC COOLING FAN CONNECTOR
3 - FAN SHROUD
4 - ELECTRIC COOLING FAN
Fig. 3 Engine Cooling SystemÐ4.0L EngineÐ
Typical
1 - HEATER CORE
2 - TO COOLANT RESERVE/OVERFLOW TANK
3 - THERMOSTAT HOUSING
4 - RADIATOR
5 - WATER PUMP
WJCOOLING 7 - 3
COOLING (Continued)
Page 327 of 2199
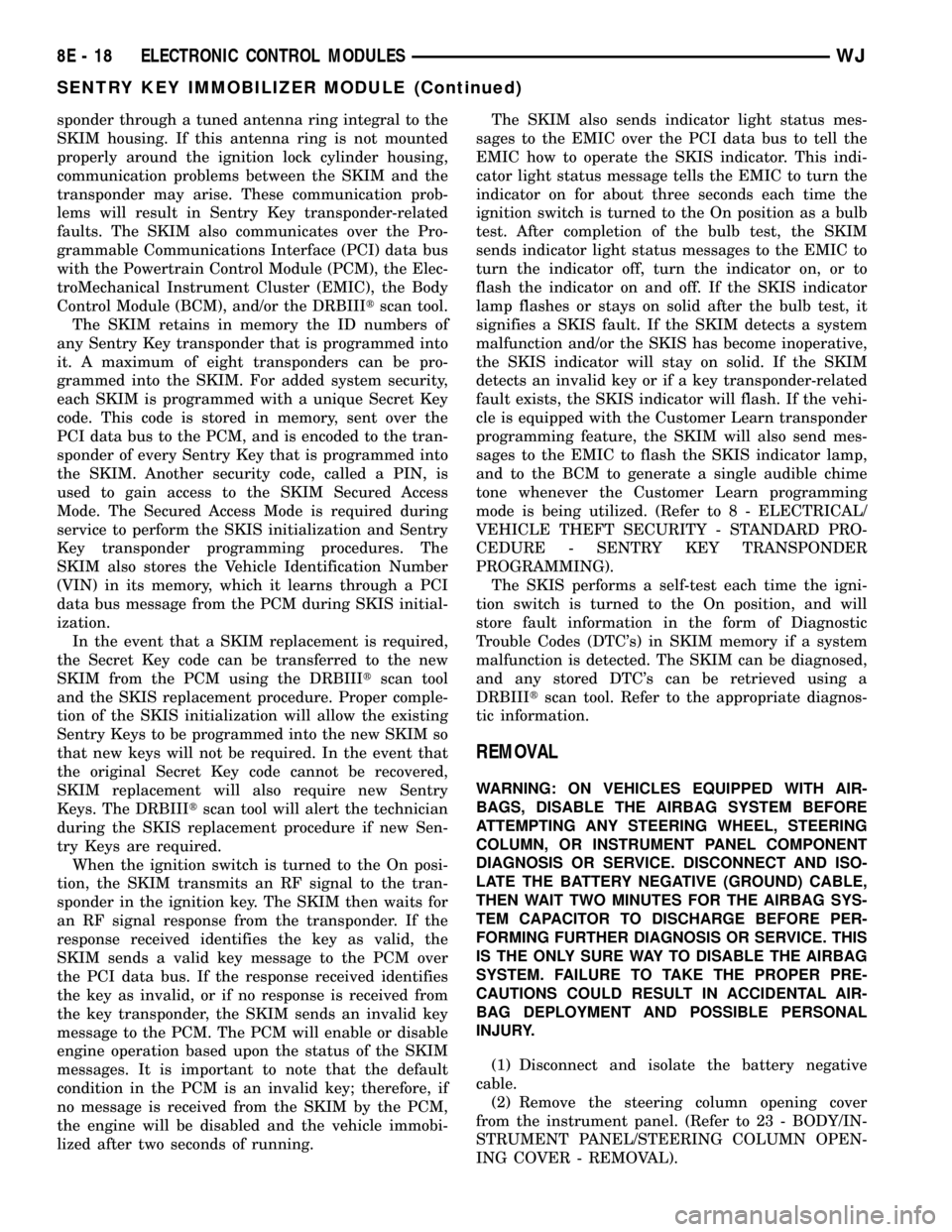
sponder through a tuned antenna ring integral to the
SKIM housing. If this antenna ring is not mounted
properly around the ignition lock cylinder housing,
communication problems between the SKIM and the
transponder may arise. These communication prob-
lems will result in Sentry Key transponder-related
faults. The SKIM also communicates over the Pro-
grammable Communications Interface (PCI) data bus
with the Powertrain Control Module (PCM), the Elec-
troMechanical Instrument Cluster (EMIC), the Body
Control Module (BCM), and/or the DRBIIItscan tool.
The SKIM retains in memory the ID numbers of
any Sentry Key transponder that is programmed into
it. A maximum of eight transponders can be pro-
grammed into the SKIM. For added system security,
each SKIM is programmed with a unique Secret Key
code. This code is stored in memory, sent over the
PCI data bus to the PCM, and is encoded to the tran-
sponder of every Sentry Key that is programmed into
the SKIM. Another security code, called a PIN, is
used to gain access to the SKIM Secured Access
Mode. The Secured Access Mode is required during
service to perform the SKIS initialization and Sentry
Key transponder programming procedures. The
SKIM also stores the Vehicle Identification Number
(VIN) in its memory, which it learns through a PCI
data bus message from the PCM during SKIS initial-
ization.
In the event that a SKIM replacement is required,
the Secret Key code can be transferred to the new
SKIM from the PCM using the DRBIIItscan tool
and the SKIS replacement procedure. Proper comple-
tion of the SKIS initialization will allow the existing
Sentry Keys to be programmed into the new SKIM so
that new keys will not be required. In the event that
the original Secret Key code cannot be recovered,
SKIM replacement will also require new Sentry
Keys. The DRBIIItscan tool will alert the technician
during the SKIS replacement procedure if new Sen-
try Keys are required.
When the ignition switch is turned to the On posi-
tion, the SKIM transmits an RF signal to the tran-
sponder in the ignition key. The SKIM then waits for
an RF signal response from the transponder. If the
response received identifies the key as valid, the
SKIM sends a valid key message to the PCM over
the PCI data bus. If the response received identifies
the key as invalid, or if no response is received from
the key transponder, the SKIM sends an invalid key
message to the PCM. The PCM will enable or disable
engine operation based upon the status of the SKIM
messages. It is important to note that the default
condition in the PCM is an invalid key; therefore, if
no message is received from the SKIM by the PCM,
the engine will be disabled and the vehicle immobi-
lized after two seconds of running.The SKIM also sends indicator light status mes-
sages to the EMIC over the PCI data bus to tell the
EMIC how to operate the SKIS indicator. This indi-
cator light status message tells the EMIC to turn the
indicator on for about three seconds each time the
ignition switch is turned to the On position as a bulb
test. After completion of the bulb test, the SKIM
sends indicator light status messages to the EMIC to
turn the indicator off, turn the indicator on, or to
flash the indicator on and off. If the SKIS indicator
lamp flashes or stays on solid after the bulb test, it
signifies a SKIS fault. If the SKIM detects a system
malfunction and/or the SKIS has become inoperative,
the SKIS indicator will stay on solid. If the SKIM
detects an invalid key or if a key transponder-related
fault exists, the SKIS indicator will flash. If the vehi-
cle is equipped with the Customer Learn transponder
programming feature, the SKIM will also send mes-
sages to the EMIC to flash the SKIS indicator lamp,
and to the BCM to generate a single audible chime
tone whenever the Customer Learn programming
mode is being utilized. (Refer to 8 - ELECTRICAL/
VEHICLE THEFT SECURITY - STANDARD PRO-
CEDURE - SENTRY KEY TRANSPONDER
PROGRAMMING).
The SKIS performs a self-test each time the igni-
tion switch is turned to the On position, and will
store fault information in the form of Diagnostic
Trouble Codes (DTC's) in SKIM memory if a system
malfunction is detected. The SKIM can be diagnosed,
and any stored DTC's can be retrieved using a
DRBIIItscan tool. Refer to the appropriate diagnos-
tic information.
REMOVAL
WARNING: ON VEHICLES EQUIPPED WITH AIR-
BAGS, DISABLE THE AIRBAG SYSTEM BEFORE
ATTEMPTING ANY STEERING WHEEL, STEERING
COLUMN, OR INSTRUMENT PANEL COMPONENT
DIAGNOSIS OR SERVICE. DISCONNECT AND ISO-
LATE THE BATTERY NEGATIVE (GROUND) CABLE,
THEN WAIT TWO MINUTES FOR THE AIRBAG SYS-
TEM CAPACITOR TO DISCHARGE BEFORE PER-
FORMING FURTHER DIAGNOSIS OR SERVICE. THIS
IS THE ONLY SURE WAY TO DISABLE THE AIRBAG
SYSTEM. FAILURE TO TAKE THE PROPER PRE-
CAUTIONS COULD RESULT IN ACCIDENTAL AIR-
BAG DEPLOYMENT AND POSSIBLE PERSONAL
INJURY.
(1) Disconnect and isolate the battery negative
cable.
(2) Remove the steering column opening cover
from the instrument panel. (Refer to 23 - BODY/IN-
STRUMENT PANEL/STEERING COLUMN OPEN-
ING COVER - REMOVAL).
8E - 18 ELECTRONIC CONTROL MODULESWJ
SENTRY KEY IMMOBILIZER MODULE (Continued)
Page 355 of 2199
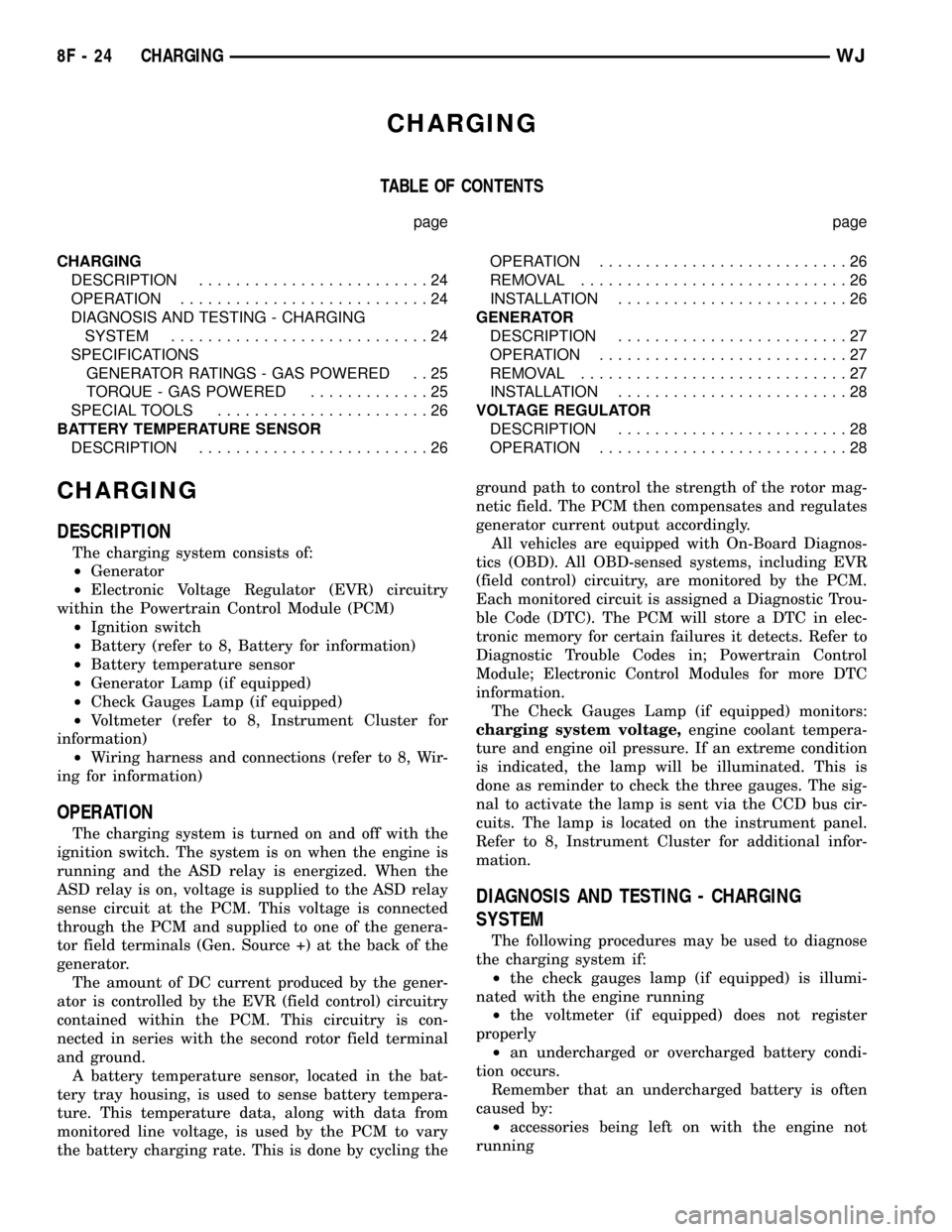
CHARGING
TABLE OF CONTENTS
page page
CHARGING
DESCRIPTION.........................24
OPERATION...........................24
DIAGNOSIS AND TESTING - CHARGING
SYSTEM............................24
SPECIFICATIONS
GENERATOR RATINGS - GAS POWERED . . 25
TORQUE - GAS POWERED.............25
SPECIAL TOOLS.......................26
BATTERY TEMPERATURE SENSOR
DESCRIPTION.........................26OPERATION...........................26
REMOVAL.............................26
INSTALLATION.........................26
GENERATOR
DESCRIPTION.........................27
OPERATION...........................27
REMOVAL.............................27
INSTALLATION.........................28
VOLTAGE REGULATOR
DESCRIPTION.........................28
OPERATION...........................28
CHARGING
DESCRIPTION
The charging system consists of:
²Generator
²Electronic Voltage Regulator (EVR) circuitry
within the Powertrain Control Module (PCM)
²Ignition switch
²Battery (refer to 8, Battery for information)
²Battery temperature sensor
²Generator Lamp (if equipped)
²Check Gauges Lamp (if equipped)
²Voltmeter (refer to 8, Instrument Cluster for
information)
²Wiring harness and connections (refer to 8, Wir-
ing for information)
OPERATION
The charging system is turned on and off with the
ignition switch. The system is on when the engine is
running and the ASD relay is energized. When the
ASD relay is on, voltage is supplied to the ASD relay
sense circuit at the PCM. This voltage is connected
through the PCM and supplied to one of the genera-
tor field terminals (Gen. Source +) at the back of the
generator.
The amount of DC current produced by the gener-
ator is controlled by the EVR (field control) circuitry
contained within the PCM. This circuitry is con-
nected in series with the second rotor field terminal
and ground.
A battery temperature sensor, located in the bat-
tery tray housing, is used to sense battery tempera-
ture. This temperature data, along with data from
monitored line voltage, is used by the PCM to vary
the battery charging rate. This is done by cycling theground path to control the strength of the rotor mag-
netic field. The PCM then compensates and regulates
generator current output accordingly.
All vehicles are equipped with On-Board Diagnos-
tics (OBD). All OBD-sensed systems, including EVR
(field control) circuitry, are monitored by the PCM.
Each monitored circuit is assigned a Diagnostic Trou-
ble Code (DTC). The PCM will store a DTC in elec-
tronic memory for certain failures it detects. Refer to
Diagnostic Trouble Codes in; Powertrain Control
Module; Electronic Control Modules for more DTC
information.
The Check Gauges Lamp (if equipped) monitors:
charging system voltage,engine coolant tempera-
ture and engine oil pressure. If an extreme condition
is indicated, the lamp will be illuminated. This is
done as reminder to check the three gauges. The sig-
nal to activate the lamp is sent via the CCD bus cir-
cuits. The lamp is located on the instrument panel.
Refer to 8, Instrument Cluster for additional infor-
mation.
DIAGNOSIS AND TESTING - CHARGING
SYSTEM
The following procedures may be used to diagnose
the charging system if:
²the check gauges lamp (if equipped) is illumi-
nated with the engine running
²the voltmeter (if equipped) does not register
properly
²an undercharged or overcharged battery condi-
tion occurs.
Remember that an undercharged battery is often
caused by:
²accessories being left on with the engine not
running
8F - 24 CHARGINGWJ
Page 356 of 2199
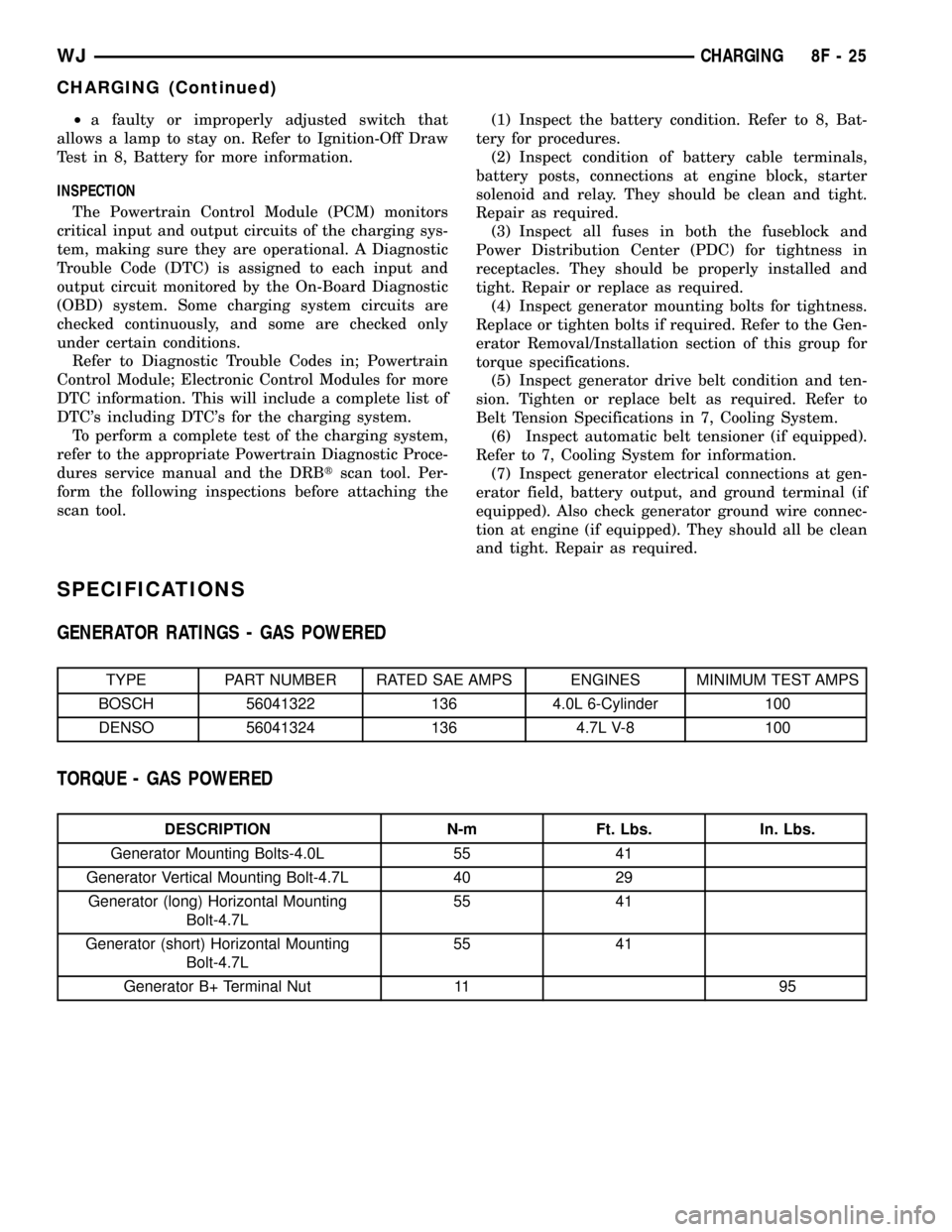
²a faulty or improperly adjusted switch that
allows a lamp to stay on. Refer to Ignition-Off Draw
Test in 8, Battery for more information.
INSPECTION
The Powertrain Control Module (PCM) monitors
critical input and output circuits of the charging sys-
tem, making sure they are operational. A Diagnostic
Trouble Code (DTC) is assigned to each input and
output circuit monitored by the On-Board Diagnostic
(OBD) system. Some charging system circuits are
checked continuously, and some are checked only
under certain conditions.
Refer to Diagnostic Trouble Codes in; Powertrain
Control Module; Electronic Control Modules for more
DTC information. This will include a complete list of
DTC's including DTC's for the charging system.
To perform a complete test of the charging system,
refer to the appropriate Powertrain Diagnostic Proce-
dures service manual and the DRBtscan tool. Per-
form the following inspections before attaching the
scan tool.(1) Inspect the battery condition. Refer to 8, Bat-
tery for procedures.
(2) Inspect condition of battery cable terminals,
battery posts, connections at engine block, starter
solenoid and relay. They should be clean and tight.
Repair as required.
(3) Inspect all fuses in both the fuseblock and
Power Distribution Center (PDC) for tightness in
receptacles. They should be properly installed and
tight. Repair or replace as required.
(4) Inspect generator mounting bolts for tightness.
Replace or tighten bolts if required. Refer to the Gen-
erator Removal/Installation section of this group for
torque specifications.
(5) Inspect generator drive belt condition and ten-
sion. Tighten or replace belt as required. Refer to
Belt Tension Specifications in 7, Cooling System.
(6) Inspect automatic belt tensioner (if equipped).
Refer to 7, Cooling System for information.
(7) Inspect generator electrical connections at gen-
erator field, battery output, and ground terminal (if
equipped). Also check generator ground wire connec-
tion at engine (if equipped). They should all be clean
and tight. Repair as required.
SPECIFICATIONS
GENERATOR RATINGS - GAS POWERED
TYPE PART NUMBER RATED SAE AMPS ENGINES MINIMUM TEST AMPS
BOSCH 56041322 136 4.0L 6-Cylinder 100
DENSO 56041324 136 4.7L V-8 100
TORQUE - GAS POWERED
DESCRIPTION N-m Ft. Lbs. In. Lbs.
Generator Mounting Bolts-4.0L 55 41
Generator Vertical Mounting Bolt-4.7L 40 29
Generator (long) Horizontal Mounting
Bolt-4.7L55 41
Generator (short) Horizontal Mounting
Bolt-4.7L55 41
Generator B+ Terminal Nut 11 95
WJCHARGING 8F - 25
CHARGING (Continued)
Page 544 of 2199
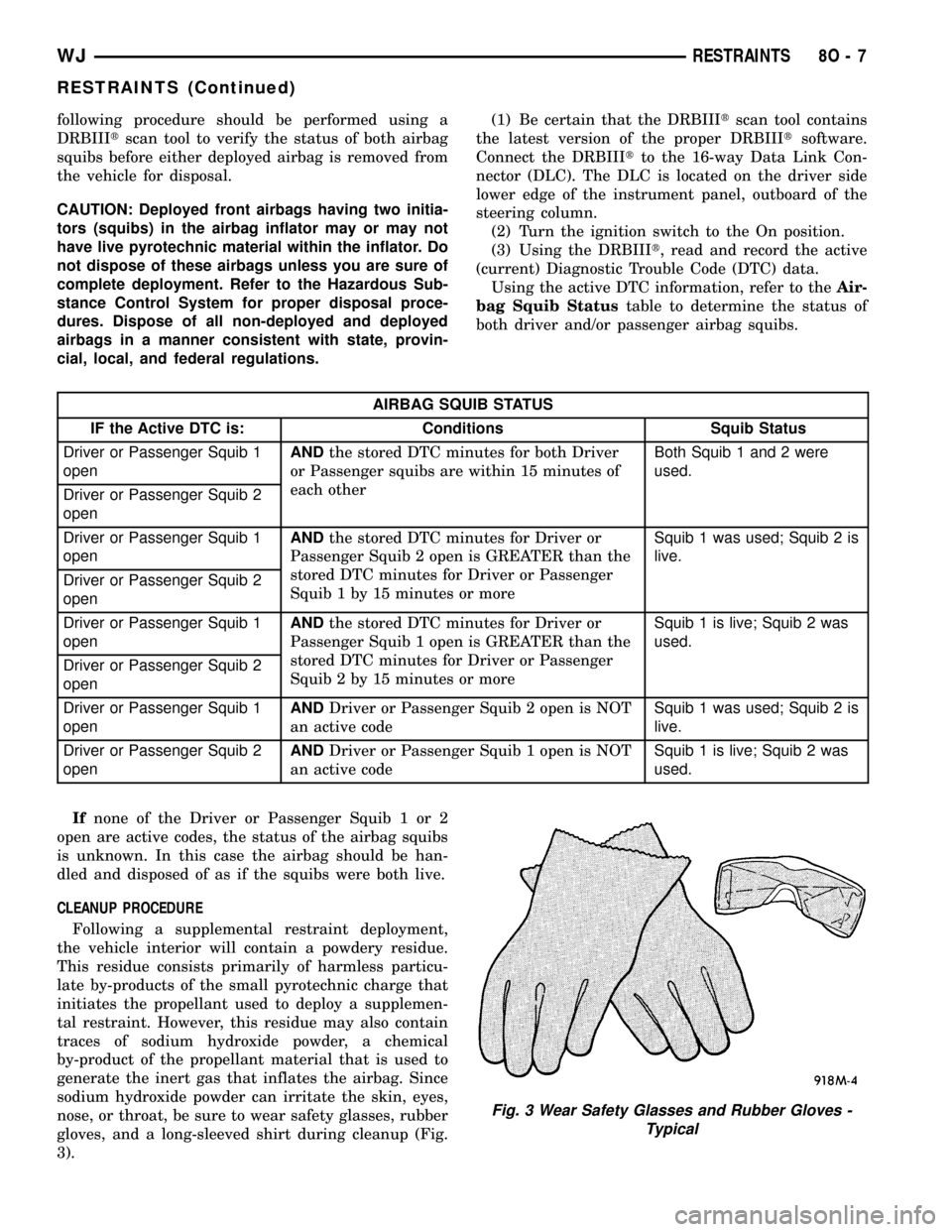
following procedure should be performed using a
DRBIIItscan tool to verify the status of both airbag
squibs before either deployed airbag is removed from
the vehicle for disposal.
CAUTION: Deployed front airbags having two initia-
tors (squibs) in the airbag inflator may or may not
have live pyrotechnic material within the inflator. Do
not dispose of these airbags unless you are sure of
complete deployment. Refer to the Hazardous Sub-
stance Control System for proper disposal proce-
dures. Dispose of all non-deployed and deployed
airbags in a manner consistent with state, provin-
cial, local, and federal regulations.(1) Be certain that the DRBIIItscan tool contains
the latest version of the proper DRBIIItsoftware.
Connect the DRBIIItto the 16-way Data Link Con-
nector (DLC). The DLC is located on the driver side
lower edge of the instrument panel, outboard of the
steering column.
(2) Turn the ignition switch to the On position.
(3) Using the DRBIIIt, read and record the active
(current) Diagnostic Trouble Code (DTC) data.
Using the active DTC information, refer to theAir-
bag Squib Statustable to determine the status of
both driver and/or passenger airbag squibs.
AIRBAG SQUIB STATUS
IF the Active DTC is: Conditions Squib Status
Driver or Passenger Squib 1
openANDthe stored DTC minutes for both Driver
or Passenger squibs are within 15 minutes of
each otherBoth Squib 1 and 2 were
used.
Driver or Passenger Squib 2
open
Driver or Passenger Squib 1
openANDthe stored DTC minutes for Driver or
Passenger Squib 2 open is GREATER than the
stored DTC minutes for Driver or Passenger
Squib 1 by 15 minutes or moreSquib 1 was used; Squib 2 is
live.
Driver or Passenger Squib 2
open
Driver or Passenger Squib 1
openANDthe stored DTC minutes for Driver or
Passenger Squib 1 open is GREATER than the
stored DTC minutes for Driver or Passenger
Squib 2 by 15 minutes or moreSquib 1 is live; Squib 2 was
used.
Driver or Passenger Squib 2
open
Driver or Passenger Squib 1
openANDDriver or Passenger Squib 2 open is NOT
an active codeSquib 1 was used; Squib 2 is
live.
Driver or Passenger Squib 2
openANDDriver or Passenger Squib 1 open is NOT
an active codeSquib 1 is live; Squib 2 was
used.
Ifnone of the Driver or Passenger Squib 1 or 2
open are active codes, the status of the airbag squibs
is unknown. In this case the airbag should be han-
dled and disposed of as if the squibs were both live.
CLEANUP PROCEDURE
Following a supplemental restraint deployment,
the vehicle interior will contain a powdery residue.
This residue consists primarily of harmless particu-
late by-products of the small pyrotechnic charge that
initiates the propellant used to deploy a supplemen-
tal restraint. However, this residue may also contain
traces of sodium hydroxide powder, a chemical
by-product of the propellant material that is used to
generate the inert gas that inflates the airbag. Since
sodium hydroxide powder can irritate the skin, eyes,
nose, or throat, be sure to wear safety glasses, rubber
gloves, and a long-sleeved shirt during cleanup (Fig.
3).
Fig. 3 Wear Safety Glasses and Rubber Gloves -
Typical
WJRESTRAINTS 8O - 7
RESTRAINTS (Continued)
Page 595 of 2199
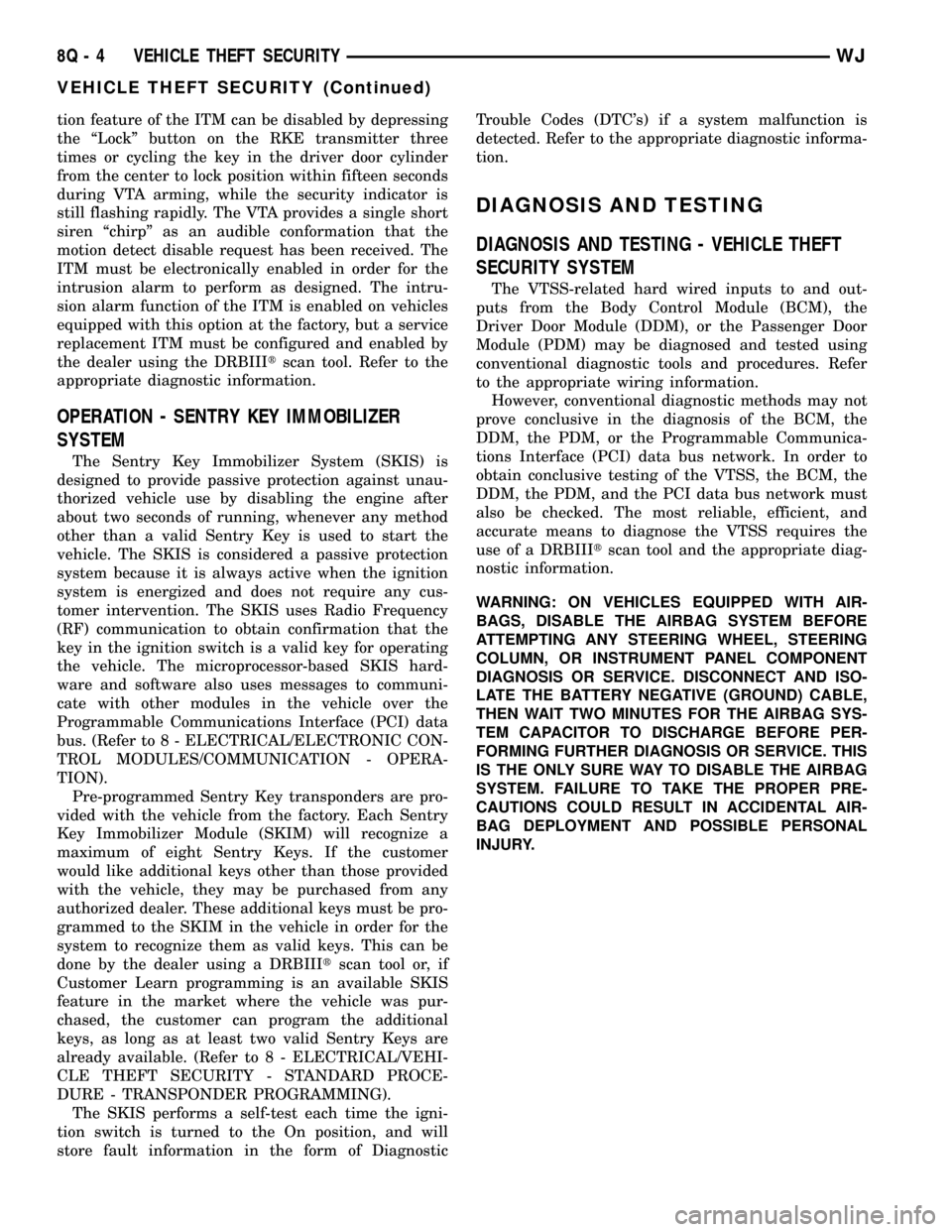
tion feature of the ITM can be disabled by depressing
the ªLockº button on the RKE transmitter three
times or cycling the key in the driver door cylinder
from the center to lock position within fifteen seconds
during VTA arming, while the security indicator is
still flashing rapidly. The VTA provides a single short
siren ªchirpº as an audible conformation that the
motion detect disable request has been received. The
ITM must be electronically enabled in order for the
intrusion alarm to perform as designed. The intru-
sion alarm function of the ITM is enabled on vehicles
equipped with this option at the factory, but a service
replacement ITM must be configured and enabled by
the dealer using the DRBIIItscan tool. Refer to the
appropriate diagnostic information.
OPERATION - SENTRY KEY IMMOBILIZER
SYSTEM
The Sentry Key Immobilizer System (SKIS) is
designed to provide passive protection against unau-
thorized vehicle use by disabling the engine after
about two seconds of running, whenever any method
other than a valid Sentry Key is used to start the
vehicle. The SKIS is considered a passive protection
system because it is always active when the ignition
system is energized and does not require any cus-
tomer intervention. The SKIS uses Radio Frequency
(RF) communication to obtain confirmation that the
key in the ignition switch is a valid key for operating
the vehicle. The microprocessor-based SKIS hard-
ware and software also uses messages to communi-
cate with other modules in the vehicle over the
Programmable Communications Interface (PCI) data
bus. (Refer to 8 - ELECTRICAL/ELECTRONIC CON-
TROL MODULES/COMMUNICATION - OPERA-
TION).
Pre-programmed Sentry Key transponders are pro-
vided with the vehicle from the factory. Each Sentry
Key Immobilizer Module (SKIM) will recognize a
maximum of eight Sentry Keys. If the customer
would like additional keys other than those provided
with the vehicle, they may be purchased from any
authorized dealer. These additional keys must be pro-
grammed to the SKIM in the vehicle in order for the
system to recognize them as valid keys. This can be
done by the dealer using a DRBIIItscan tool or, if
Customer Learn programming is an available SKIS
feature in the market where the vehicle was pur-
chased, the customer can program the additional
keys, as long as at least two valid Sentry Keys are
already available. (Refer to 8 - ELECTRICAL/VEHI-
CLE THEFT SECURITY - STANDARD PROCE-
DURE - TRANSPONDER PROGRAMMING).
The SKIS performs a self-test each time the igni-
tion switch is turned to the On position, and will
store fault information in the form of DiagnosticTrouble Codes (DTC's) if a system malfunction is
detected. Refer to the appropriate diagnostic informa-
tion.
DIAGNOSIS AND TESTING
DIAGNOSIS AND TESTING - VEHICLE THEFT
SECURITY SYSTEM
The VTSS-related hard wired inputs to and out-
puts from the Body Control Module (BCM), the
Driver Door Module (DDM), or the Passenger Door
Module (PDM) may be diagnosed and tested using
conventional diagnostic tools and procedures. Refer
to the appropriate wiring information.
However, conventional diagnostic methods may not
prove conclusive in the diagnosis of the BCM, the
DDM, the PDM, or the Programmable Communica-
tions Interface (PCI) data bus network. In order to
obtain conclusive testing of the VTSS, the BCM, the
DDM, the PDM, and the PCI data bus network must
also be checked. The most reliable, efficient, and
accurate means to diagnose the VTSS requires the
use of a DRBIIItscan tool and the appropriate diag-
nostic information.
WARNING: ON VEHICLES EQUIPPED WITH AIR-
BAGS, DISABLE THE AIRBAG SYSTEM BEFORE
ATTEMPTING ANY STEERING WHEEL, STEERING
COLUMN, OR INSTRUMENT PANEL COMPONENT
DIAGNOSIS OR SERVICE. DISCONNECT AND ISO-
LATE THE BATTERY NEGATIVE (GROUND) CABLE,
THEN WAIT TWO MINUTES FOR THE AIRBAG SYS-
TEM CAPACITOR TO DISCHARGE BEFORE PER-
FORMING FURTHER DIAGNOSIS OR SERVICE. THIS
IS THE ONLY SURE WAY TO DISABLE THE AIRBAG
SYSTEM. FAILURE TO TAKE THE PROPER PRE-
CAUTIONS COULD RESULT IN ACCIDENTAL AIR-
BAG DEPLOYMENT AND POSSIBLE PERSONAL
INJURY.
8Q - 4 VEHICLE THEFT SECURITYWJ
VEHICLE THEFT SECURITY (Continued)
Page 603 of 2199
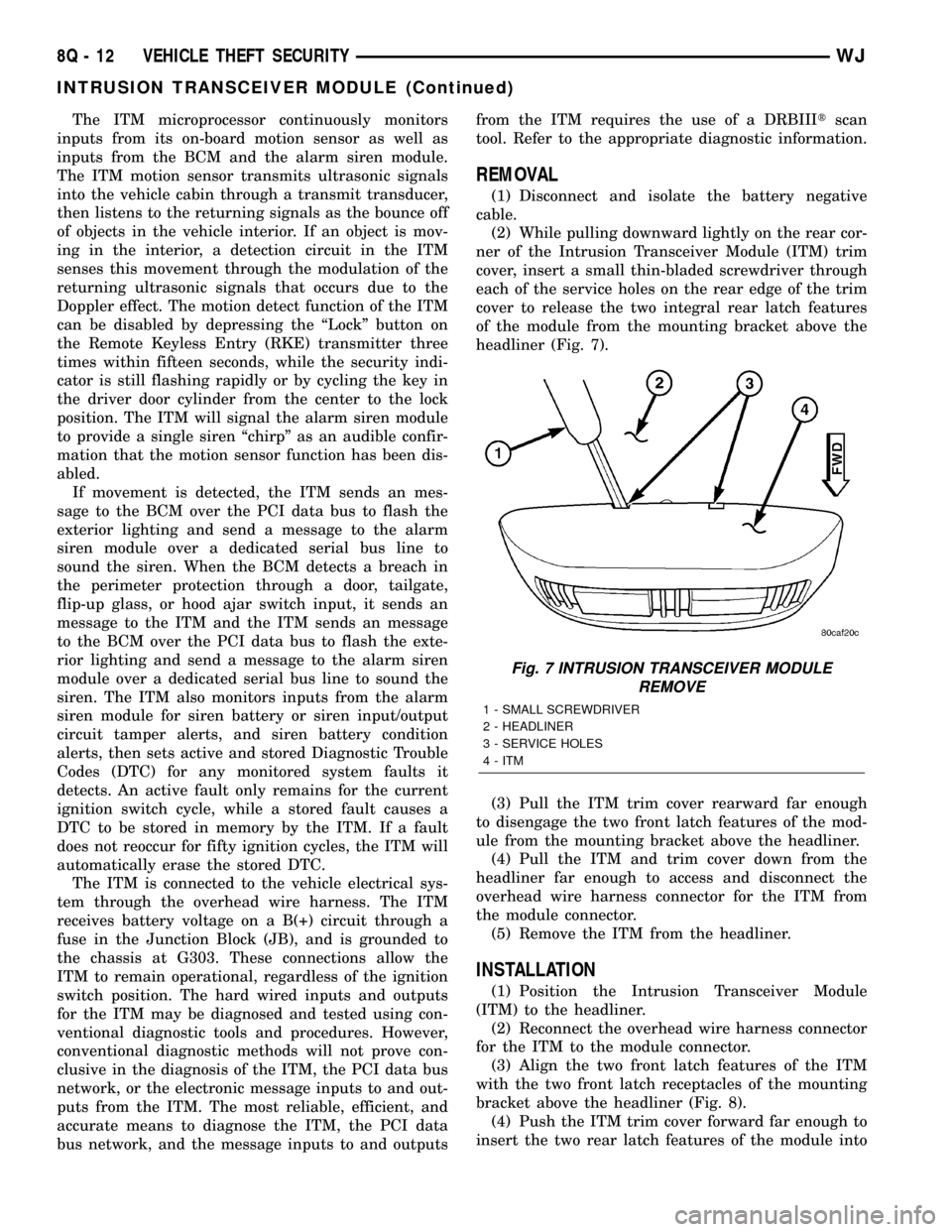
The ITM microprocessor continuously monitors
inputs from its on-board motion sensor as well as
inputs from the BCM and the alarm siren module.
The ITM motion sensor transmits ultrasonic signals
into the vehicle cabin through a transmit transducer,
then listens to the returning signals as the bounce off
of objects in the vehicle interior. If an object is mov-
ing in the interior, a detection circuit in the ITM
senses this movement through the modulation of the
returning ultrasonic signals that occurs due to the
Doppler effect. The motion detect function of the ITM
can be disabled by depressing the ªLockº button on
the Remote Keyless Entry (RKE) transmitter three
times within fifteen seconds, while the security indi-
cator is still flashing rapidly or by cycling the key in
the driver door cylinder from the center to the lock
position. The ITM will signal the alarm siren module
to provide a single siren ªchirpº as an audible confir-
mation that the motion sensor function has been dis-
abled.
If movement is detected, the ITM sends an mes-
sage to the BCM over the PCI data bus to flash the
exterior lighting and send a message to the alarm
siren module over a dedicated serial bus line to
sound the siren. When the BCM detects a breach in
the perimeter protection through a door, tailgate,
flip-up glass, or hood ajar switch input, it sends an
message to the ITM and the ITM sends an message
to the BCM over the PCI data bus to flash the exte-
rior lighting and send a message to the alarm siren
module over a dedicated serial bus line to sound the
siren. The ITM also monitors inputs from the alarm
siren module for siren battery or siren input/output
circuit tamper alerts, and siren battery condition
alerts, then sets active and stored Diagnostic Trouble
Codes (DTC) for any monitored system faults it
detects. An active fault only remains for the current
ignition switch cycle, while a stored fault causes a
DTC to be stored in memory by the ITM. If a fault
does not reoccur for fifty ignition cycles, the ITM will
automatically erase the stored DTC.
The ITM is connected to the vehicle electrical sys-
tem through the overhead wire harness. The ITM
receives battery voltage on a B(+) circuit through a
fuse in the Junction Block (JB), and is grounded to
the chassis at G303. These connections allow the
ITM to remain operational, regardless of the ignition
switch position. The hard wired inputs and outputs
for the ITM may be diagnosed and tested using con-
ventional diagnostic tools and procedures. However,
conventional diagnostic methods will not prove con-
clusive in the diagnosis of the ITM, the PCI data bus
network, or the electronic message inputs to and out-
puts from the ITM. The most reliable, efficient, and
accurate means to diagnose the ITM, the PCI data
bus network, and the message inputs to and outputsfrom the ITM requires the use of a DRBIIItscan
tool. Refer to the appropriate diagnostic information.
REMOVAL
(1) Disconnect and isolate the battery negative
cable.
(2) While pulling downward lightly on the rear cor-
ner of the Intrusion Transceiver Module (ITM) trim
cover, insert a small thin-bladed screwdriver through
each of the service holes on the rear edge of the trim
cover to release the two integral rear latch features
of the module from the mounting bracket above the
headliner (Fig. 7).
(3) Pull the ITM trim cover rearward far enough
to disengage the two front latch features of the mod-
ule from the mounting bracket above the headliner.
(4) Pull the ITM and trim cover down from the
headliner far enough to access and disconnect the
overhead wire harness connector for the ITM from
the module connector.
(5) Remove the ITM from the headliner.
INSTALLATION
(1) Position the Intrusion Transceiver Module
(ITM) to the headliner.
(2) Reconnect the overhead wire harness connector
for the ITM to the module connector.
(3) Align the two front latch features of the ITM
with the two front latch receptacles of the mounting
bracket above the headliner (Fig. 8).
(4) Push the ITM trim cover forward far enough to
insert the two rear latch features of the module into
Fig. 7 INTRUSION TRANSCEIVER MODULE
REMOVE
1 - SMALL SCREWDRIVER
2 - HEADLINER
3 - SERVICE HOLES
4 - ITM
8Q - 12 VEHICLE THEFT SECURITYWJ
INTRUSION TRANSCEIVER MODULE (Continued)
Page 1423 of 2199
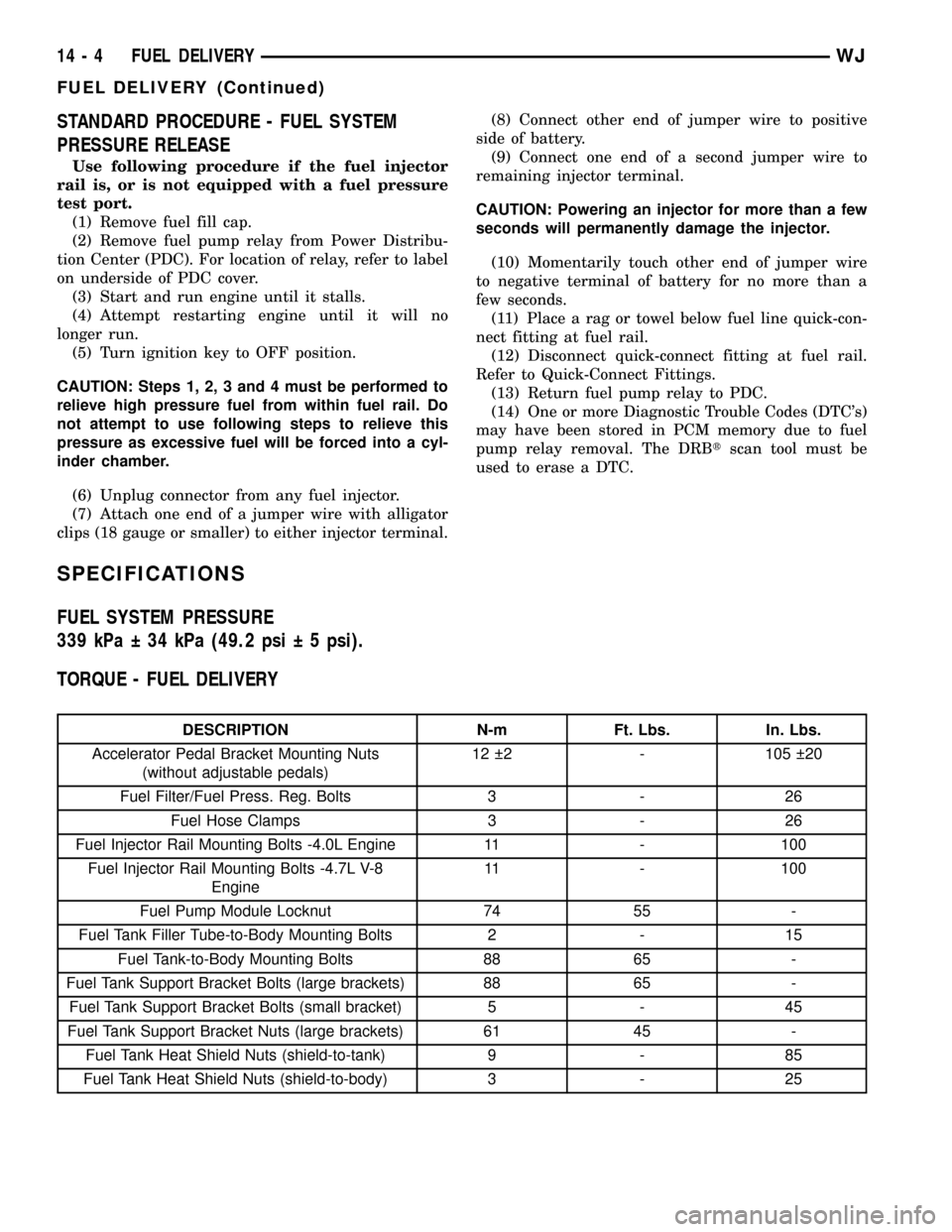
STANDARD PROCEDURE - FUEL SYSTEM
PRESSURE RELEASE
Use following procedure if the fuel injector
rail is, or is not equipped with a fuel pressure
test port.
(1) Remove fuel fill cap.
(2) Remove fuel pump relay from Power Distribu-
tion Center (PDC). For location of relay, refer to label
on underside of PDC cover.
(3) Start and run engine until it stalls.
(4) Attempt restarting engine until it will no
longer run.
(5) Turn ignition key to OFF position.
CAUTION: Steps 1, 2, 3 and 4 must be performed to
relieve high pressure fuel from within fuel rail. Do
not attempt to use following steps to relieve this
pressure as excessive fuel will be forced into a cyl-
inder chamber.
(6) Unplug connector from any fuel injector.
(7) Attach one end of a jumper wire with alligator
clips (18 gauge or smaller) to either injector terminal.(8) Connect other end of jumper wire to positive
side of battery.
(9) Connect one end of a second jumper wire to
remaining injector terminal.
CAUTION: Powering an injector for more than a few
seconds will permanently damage the injector.
(10) Momentarily touch other end of jumper wire
to negative terminal of battery for no more than a
few seconds.
(11) Place a rag or towel below fuel line quick-con-
nect fitting at fuel rail.
(12) Disconnect quick-connect fitting at fuel rail.
Refer to Quick-Connect Fittings.
(13) Return fuel pump relay to PDC.
(14) One or more Diagnostic Trouble Codes (DTC's)
may have been stored in PCM memory due to fuel
pump relay removal. The DRBtscan tool must be
used to erase a DTC.
SPECIFICATIONS
FUEL SYSTEM PRESSURE
339 kPa 34 kPa (49.2 psi 5 psi).
TORQUE - FUEL DELIVERY
DESCRIPTION N-m Ft. Lbs. In. Lbs.
Accelerator Pedal Bracket Mounting Nuts
(without adjustable pedals)12 2 - 105 20
Fuel Filter/Fuel Press. Reg. Bolts 3 - 26
Fuel Hose Clamps 3 - 26
Fuel Injector Rail Mounting Bolts -4.0L Engine 11 - 100
Fuel Injector Rail Mounting Bolts -4.7L V-8
Engine11 - 100
Fuel Pump Module Locknut 74 55 -
Fuel Tank Filler Tube-to-Body Mounting Bolts 2 - 15
Fuel Tank-to-Body Mounting Bolts 88 65 -
Fuel Tank Support Bracket Bolts (large brackets) 88 65 -
Fuel Tank Support Bracket Bolts (small bracket) 5 - 45
Fuel Tank Support Bracket Nuts (large brackets) 61 45 -
Fuel Tank Heat Shield Nuts (shield-to-tank) 9 - 85
Fuel Tank Heat Shield Nuts (shield-to-body) 3 - 25
14 - 4 FUEL DELIVERYWJ
FUEL DELIVERY (Continued)
Page 1426 of 2199
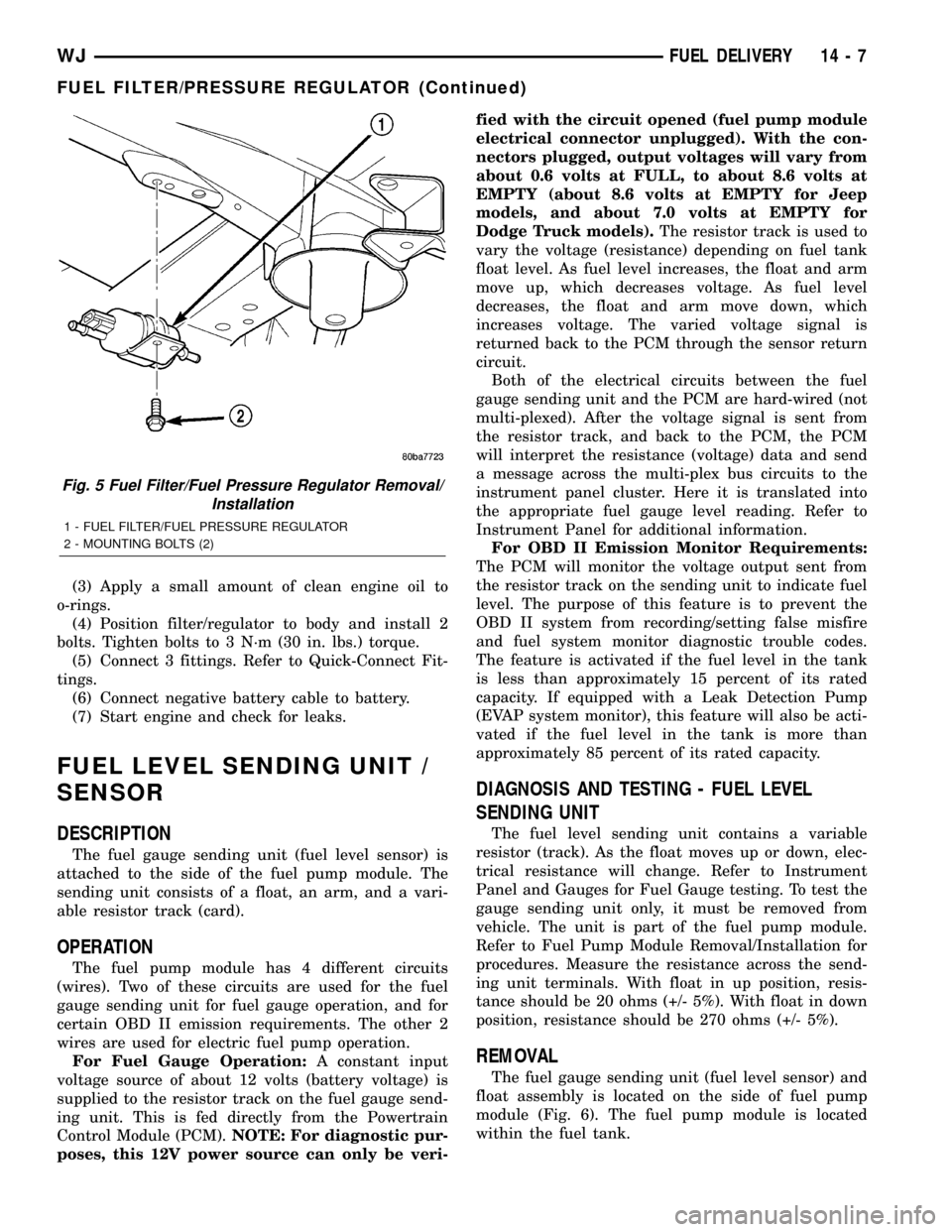
(3) Apply a small amount of clean engine oil to
o-rings.
(4) Position filter/regulator to body and install 2
bolts. Tighten bolts to 3 N´m (30 in. lbs.) torque.
(5) Connect 3 fittings. Refer to Quick-Connect Fit-
tings.
(6) Connect negative battery cable to battery.
(7) Start engine and check for leaks.
FUEL LEVEL SENDING UNIT /
SENSOR
DESCRIPTION
The fuel gauge sending unit (fuel level sensor) is
attached to the side of the fuel pump module. The
sending unit consists of a float, an arm, and a vari-
able resistor track (card).
OPERATION
The fuel pump module has 4 different circuits
(wires). Two of these circuits are used for the fuel
gauge sending unit for fuel gauge operation, and for
certain OBD II emission requirements. The other 2
wires are used for electric fuel pump operation.
For Fuel Gauge Operation:A constant input
voltage source of about 12 volts (battery voltage) is
supplied to the resistor track on the fuel gauge send-
ing unit. This is fed directly from the Powertrain
Control Module (PCM).NOTE: For diagnostic pur-
poses, this 12V power source can only be veri-fied with the circuit opened (fuel pump module
electrical connector unplugged). With the con-
nectors plugged, output voltages will vary from
about 0.6 volts at FULL, to about 8.6 volts at
EMPTY (about 8.6 volts at EMPTY for Jeep
models, and about 7.0 volts at EMPTY for
Dodge Truck models).The resistor track is used to
vary the voltage (resistance) depending on fuel tank
float level. As fuel level increases, the float and arm
move up, which decreases voltage. As fuel level
decreases, the float and arm move down, which
increases voltage. The varied voltage signal is
returned back to the PCM through the sensor return
circuit.
Both of the electrical circuits between the fuel
gauge sending unit and the PCM are hard-wired (not
multi-plexed). After the voltage signal is sent from
the resistor track, and back to the PCM, the PCM
will interpret the resistance (voltage) data and send
a message across the multi-plex bus circuits to the
instrument panel cluster. Here it is translated into
the appropriate fuel gauge level reading. Refer to
Instrument Panel for additional information.
For OBD II Emission Monitor Requirements:
The PCM will monitor the voltage output sent from
the resistor track on the sending unit to indicate fuel
level. The purpose of this feature is to prevent the
OBD II system from recording/setting false misfire
and fuel system monitor diagnostic trouble codes.
The feature is activated if the fuel level in the tank
is less than approximately 15 percent of its rated
capacity. If equipped with a Leak Detection Pump
(EVAP system monitor), this feature will also be acti-
vated if the fuel level in the tank is more than
approximately 85 percent of its rated capacity.
DIAGNOSIS AND TESTING - FUEL LEVEL
SENDING UNIT
The fuel level sending unit contains a variable
resistor (track). As the float moves up or down, elec-
trical resistance will change. Refer to Instrument
Panel and Gauges for Fuel Gauge testing. To test the
gauge sending unit only, it must be removed from
vehicle. The unit is part of the fuel pump module.
Refer to Fuel Pump Module Removal/Installation for
procedures. Measure the resistance across the send-
ing unit terminals. With float in up position, resis-
tance should be 20 ohms (+/- 5%). With float in down
position, resistance should be 270 ohms (+/- 5%).
REMOVAL
The fuel gauge sending unit (fuel level sensor) and
float assembly is located on the side of fuel pump
module (Fig. 6). The fuel pump module is located
within the fuel tank.
Fig. 5 Fuel Filter/Fuel Pressure Regulator Removal/
Installation
1 - FUEL FILTER/FUEL PRESSURE REGULATOR
2 - MOUNTING BOLTS (2)
WJFUEL DELIVERY 14 - 7
FUEL FILTER/PRESSURE REGULATOR (Continued)
Page 1530 of 2199
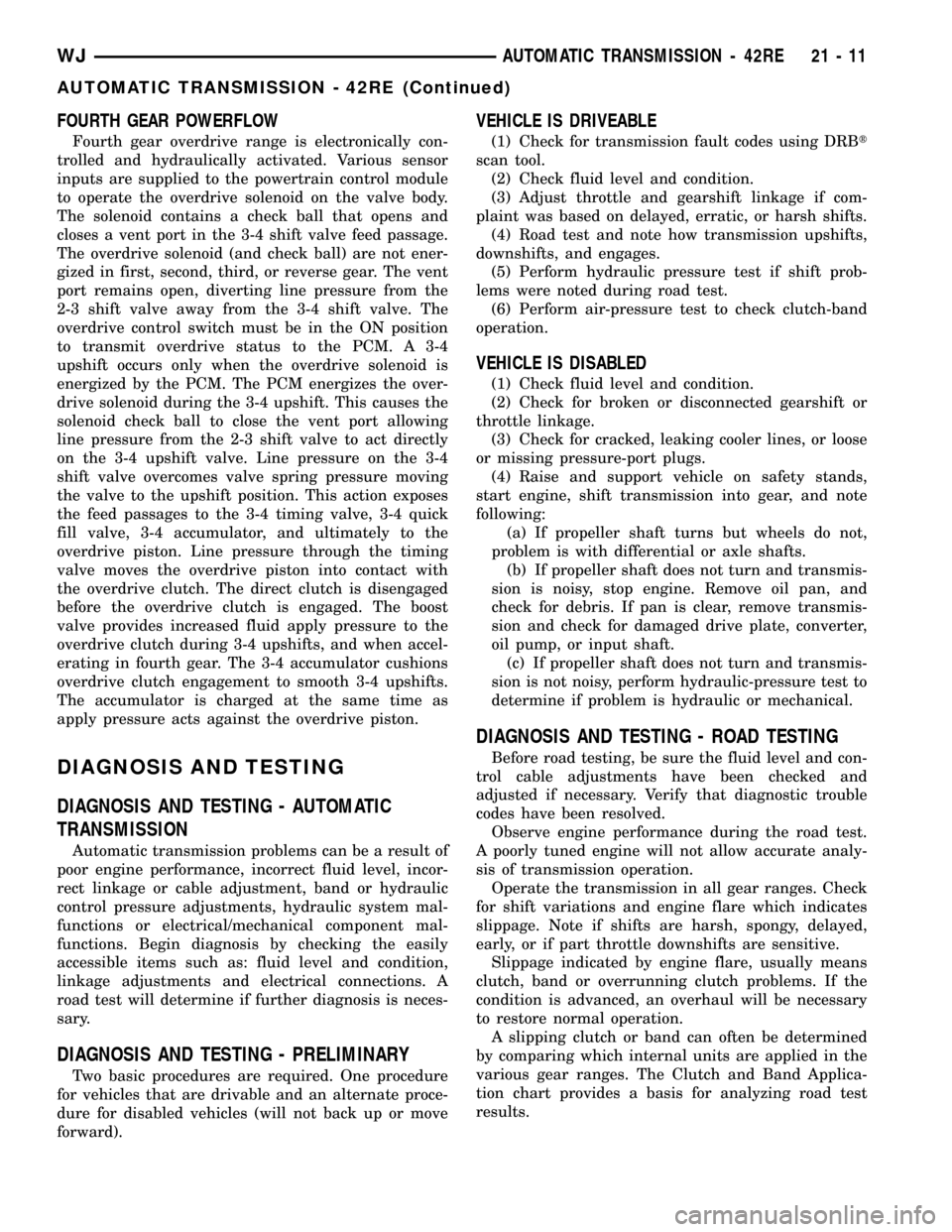
FOURTH GEAR POWERFLOW
Fourth gear overdrive range is electronically con-
trolled and hydraulically activated. Various sensor
inputs are supplied to the powertrain control module
to operate the overdrive solenoid on the valve body.
The solenoid contains a check ball that opens and
closes a vent port in the 3-4 shift valve feed passage.
The overdrive solenoid (and check ball) are not ener-
gized in first, second, third, or reverse gear. The vent
port remains open, diverting line pressure from the
2-3 shift valve away from the 3-4 shift valve. The
overdrive control switch must be in the ON position
to transmit overdrive status to the PCM. A 3-4
upshift occurs only when the overdrive solenoid is
energized by the PCM. The PCM energizes the over-
drive solenoid during the 3-4 upshift. This causes the
solenoid check ball to close the vent port allowing
line pressure from the 2-3 shift valve to act directly
on the 3-4 upshift valve. Line pressure on the 3-4
shift valve overcomes valve spring pressure moving
the valve to the upshift position. This action exposes
the feed passages to the 3-4 timing valve, 3-4 quick
fill valve, 3-4 accumulator, and ultimately to the
overdrive piston. Line pressure through the timing
valve moves the overdrive piston into contact with
the overdrive clutch. The direct clutch is disengaged
before the overdrive clutch is engaged. The boost
valve provides increased fluid apply pressure to the
overdrive clutch during 3-4 upshifts, and when accel-
erating in fourth gear. The 3-4 accumulator cushions
overdrive clutch engagement to smooth 3-4 upshifts.
The accumulator is charged at the same time as
apply pressure acts against the overdrive piston.
DIAGNOSIS AND TESTING
DIAGNOSIS AND TESTING - AUTOMATIC
TRANSMISSION
Automatic transmission problems can be a result of
poor engine performance, incorrect fluid level, incor-
rect linkage or cable adjustment, band or hydraulic
control pressure adjustments, hydraulic system mal-
functions or electrical/mechanical component mal-
functions. Begin diagnosis by checking the easily
accessible items such as: fluid level and condition,
linkage adjustments and electrical connections. A
road test will determine if further diagnosis is neces-
sary.
DIAGNOSIS AND TESTING - PRELIMINARY
Two basic procedures are required. One procedure
for vehicles that are drivable and an alternate proce-
dure for disabled vehicles (will not back up or move
forward).
VEHICLE IS DRIVEABLE
(1) Check for transmission fault codes using DRBt
scan tool.
(2) Check fluid level and condition.
(3) Adjust throttle and gearshift linkage if com-
plaint was based on delayed, erratic, or harsh shifts.
(4) Road test and note how transmission upshifts,
downshifts, and engages.
(5) Perform hydraulic pressure test if shift prob-
lems were noted during road test.
(6) Perform air-pressure test to check clutch-band
operation.
VEHICLE IS DISABLED
(1) Check fluid level and condition.
(2) Check for broken or disconnected gearshift or
throttle linkage.
(3) Check for cracked, leaking cooler lines, or loose
or missing pressure-port plugs.
(4) Raise and support vehicle on safety stands,
start engine, shift transmission into gear, and note
following:
(a) If propeller shaft turns but wheels do not,
problem is with differential or axle shafts.
(b) If propeller shaft does not turn and transmis-
sion is noisy, stop engine. Remove oil pan, and
check for debris. If pan is clear, remove transmis-
sion and check for damaged drive plate, converter,
oil pump, or input shaft.
(c) If propeller shaft does not turn and transmis-
sion is not noisy, perform hydraulic-pressure test to
determine if problem is hydraulic or mechanical.
DIAGNOSIS AND TESTING - ROAD TESTING
Before road testing, be sure the fluid level and con-
trol cable adjustments have been checked and
adjusted if necessary. Verify that diagnostic trouble
codes have been resolved.
Observe engine performance during the road test.
A poorly tuned engine will not allow accurate analy-
sis of transmission operation.
Operate the transmission in all gear ranges. Check
for shift variations and engine flare which indicates
slippage. Note if shifts are harsh, spongy, delayed,
early, or if part throttle downshifts are sensitive.
Slippage indicated by engine flare, usually means
clutch, band or overrunning clutch problems. If the
condition is advanced, an overhaul will be necessary
to restore normal operation.
A slipping clutch or band can often be determined
by comparing which internal units are applied in the
various gear ranges. The Clutch and Band Applica-
tion chart provides a basis for analyzing road test
results.
WJAUTOMATIC TRANSMISSION - 42RE 21 - 11
AUTOMATIC TRANSMISSION - 42RE (Continued)