Power control module JEEP GRAND CHEROKEE 2003 WJ / 2.G Owners Manual
[x] Cancel search | Manufacturer: JEEP, Model Year: 2003, Model line: GRAND CHEROKEE, Model: JEEP GRAND CHEROKEE 2003 WJ / 2.GPages: 2199, PDF Size: 76.01 MB
Page 530 of 2199
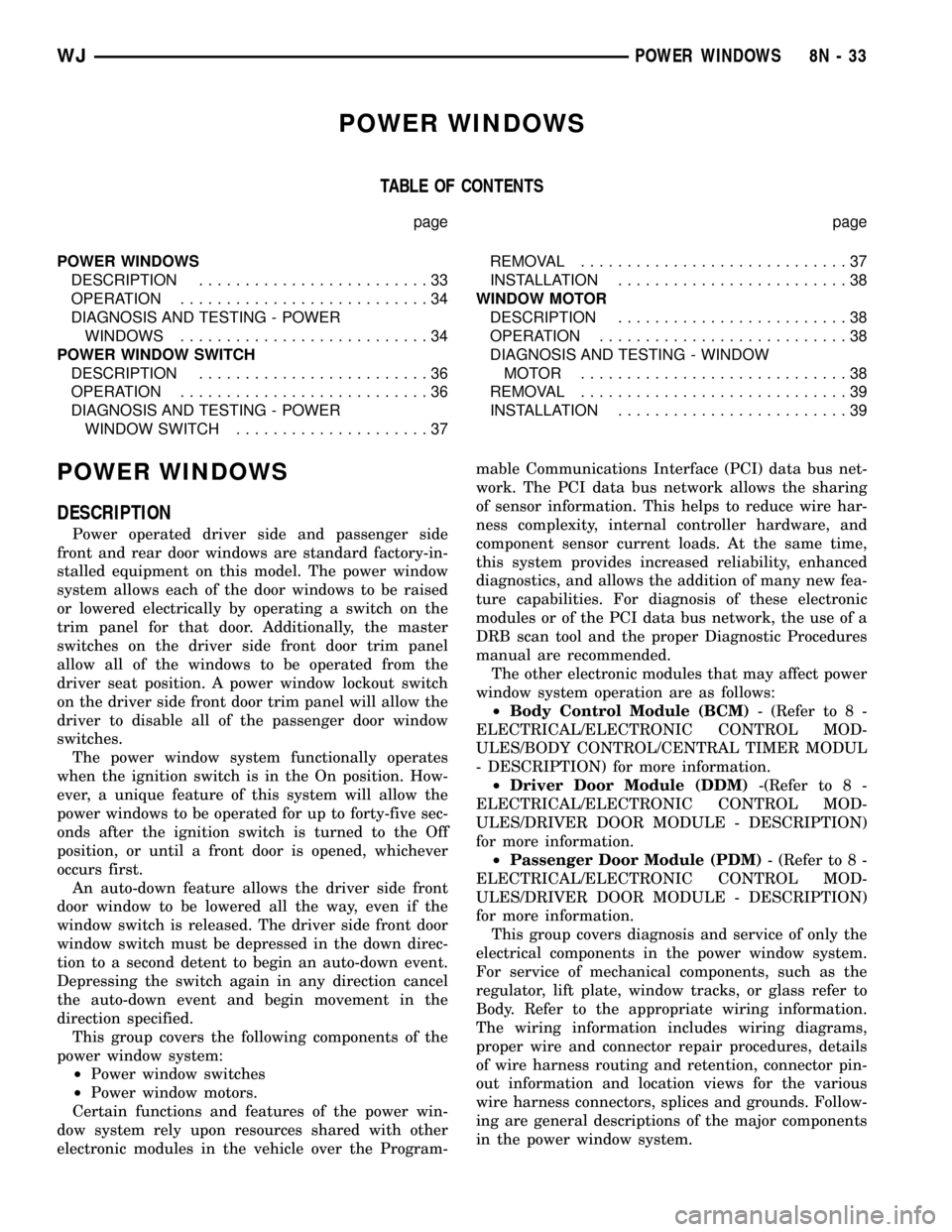
POWER WINDOWS
TABLE OF CONTENTS
page page
POWER WINDOWS
DESCRIPTION.........................33
OPERATION...........................34
DIAGNOSIS AND TESTING - POWER
WINDOWS...........................34
POWER WINDOW SWITCH
DESCRIPTION.........................36
OPERATION...........................36
DIAGNOSIS AND TESTING - POWER
WINDOW SWITCH.....................37REMOVAL.............................37
INSTALLATION.........................38
WINDOW MOTOR
DESCRIPTION.........................38
OPERATION...........................38
DIAGNOSIS AND TESTING - WINDOW
MOTOR .............................38
REMOVAL.............................39
INSTALLATION.........................39
POWER WINDOWS
DESCRIPTION
Power operated driver side and passenger side
front and rear door windows are standard factory-in-
stalled equipment on this model. The power window
system allows each of the door windows to be raised
or lowered electrically by operating a switch on the
trim panel for that door. Additionally, the master
switches on the driver side front door trim panel
allow all of the windows to be operated from the
driver seat position. A power window lockout switch
on the driver side front door trim panel will allow the
driver to disable all of the passenger door window
switches.
The power window system functionally operates
when the ignition switch is in the On position. How-
ever, a unique feature of this system will allow the
power windows to be operated for up to forty-five sec-
onds after the ignition switch is turned to the Off
position, or until a front door is opened, whichever
occurs first.
An auto-down feature allows the driver side front
door window to be lowered all the way, even if the
window switch is released. The driver side front door
window switch must be depressed in the down direc-
tion to a second detent to begin an auto-down event.
Depressing the switch again in any direction cancel
the auto-down event and begin movement in the
direction specified.
This group covers the following components of the
power window system:
²Power window switches
²Power window motors.
Certain functions and features of the power win-
dow system rely upon resources shared with other
electronic modules in the vehicle over the Program-mable Communications Interface (PCI) data bus net-
work. The PCI data bus network allows the sharing
of sensor information. This helps to reduce wire har-
ness complexity, internal controller hardware, and
component sensor current loads. At the same time,
this system provides increased reliability, enhanced
diagnostics, and allows the addition of many new fea-
ture capabilities. For diagnosis of these electronic
modules or of the PCI data bus network, the use of a
DRB scan tool and the proper Diagnostic Procedures
manual are recommended.
The other electronic modules that may affect power
window system operation are as follows:
²Body Control Module (BCM)- (Refer to 8 -
ELECTRICAL/ELECTRONIC CONTROL MOD-
ULES/BODY CONTROL/CENTRAL TIMER MODUL
- DESCRIPTION) for more information.
²Driver Door Module (DDM)-(Refer to 8 -
ELECTRICAL/ELECTRONIC CONTROL MOD-
ULES/DRIVER DOOR MODULE - DESCRIPTION)
for more information.
²Passenger Door Module (PDM)- (Refer to 8 -
ELECTRICAL/ELECTRONIC CONTROL MOD-
ULES/DRIVER DOOR MODULE - DESCRIPTION)
for more information.
This group covers diagnosis and service of only the
electrical components in the power window system.
For service of mechanical components, such as the
regulator, lift plate, window tracks, or glass refer to
Body. Refer to the appropriate wiring information.
The wiring information includes wiring diagrams,
proper wire and connector repair procedures, details
of wire harness routing and retention, connector pin-
out information and location views for the various
wire harness connectors, splices and grounds. Follow-
ing are general descriptions of the major components
in the power window system.
WJPOWER WINDOWS 8N - 33
Page 531 of 2199
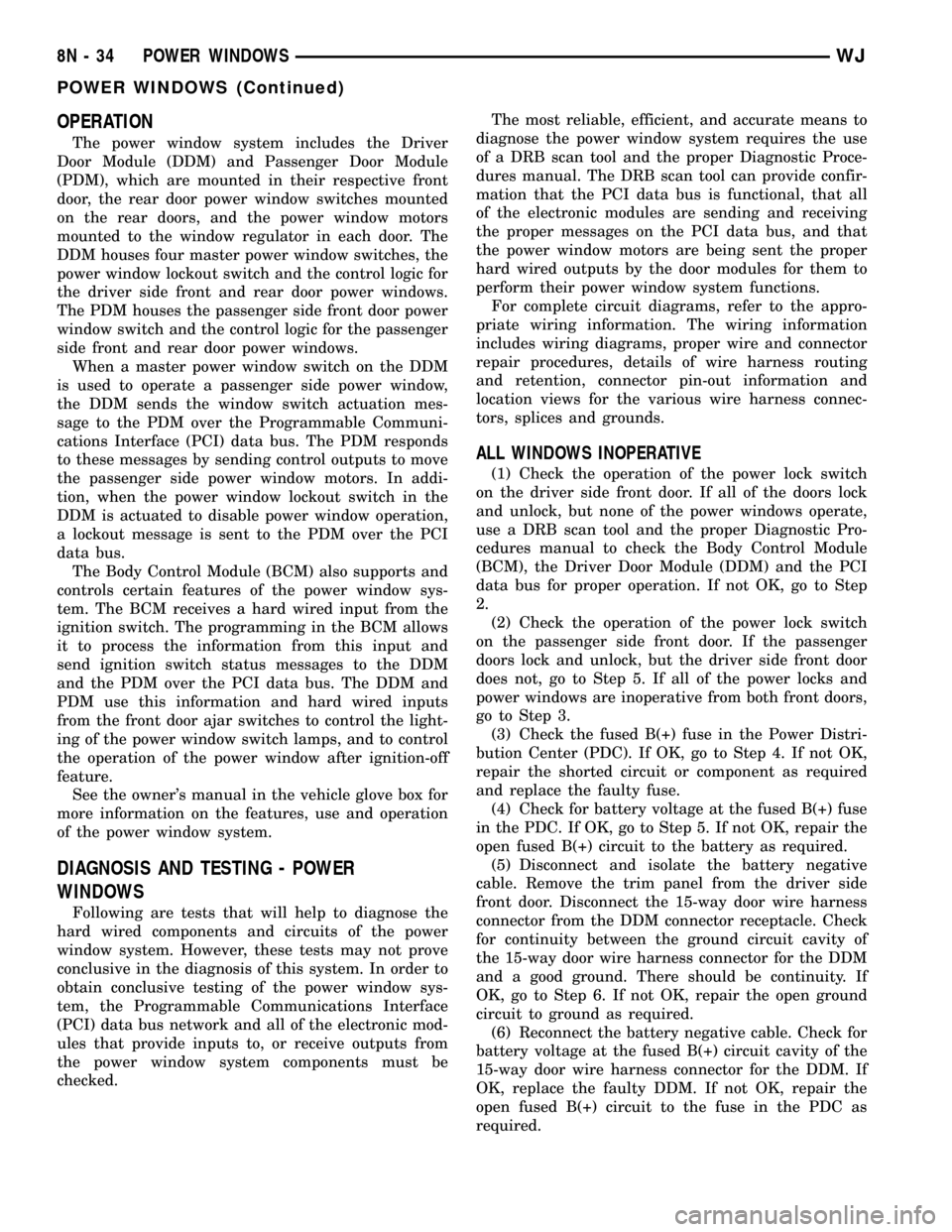
OPERATION
The power window system includes the Driver
Door Module (DDM) and Passenger Door Module
(PDM), which are mounted in their respective front
door, the rear door power window switches mounted
on the rear doors, and the power window motors
mounted to the window regulator in each door. The
DDM houses four master power window switches, the
power window lockout switch and the control logic for
the driver side front and rear door power windows.
The PDM houses the passenger side front door power
window switch and the control logic for the passenger
side front and rear door power windows.
When a master power window switch on the DDM
is used to operate a passenger side power window,
the DDM sends the window switch actuation mes-
sage to the PDM over the Programmable Communi-
cations Interface (PCI) data bus. The PDM responds
to these messages by sending control outputs to move
the passenger side power window motors. In addi-
tion, when the power window lockout switch in the
DDM is actuated to disable power window operation,
a lockout message is sent to the PDM over the PCI
data bus.
The Body Control Module (BCM) also supports and
controls certain features of the power window sys-
tem. The BCM receives a hard wired input from the
ignition switch. The programming in the BCM allows
it to process the information from this input and
send ignition switch status messages to the DDM
and the PDM over the PCI data bus. The DDM and
PDM use this information and hard wired inputs
from the front door ajar switches to control the light-
ing of the power window switch lamps, and to control
the operation of the power window after ignition-off
feature.
See the owner's manual in the vehicle glove box for
more information on the features, use and operation
of the power window system.
DIAGNOSIS AND TESTING - POWER
WINDOWS
Following are tests that will help to diagnose the
hard wired components and circuits of the power
window system. However, these tests may not prove
conclusive in the diagnosis of this system. In order to
obtain conclusive testing of the power window sys-
tem, the Programmable Communications Interface
(PCI) data bus network and all of the electronic mod-
ules that provide inputs to, or receive outputs from
the power window system components must be
checked.The most reliable, efficient, and accurate means to
diagnose the power window system requires the use
of a DRB scan tool and the proper Diagnostic Proce-
dures manual. The DRB scan tool can provide confir-
mation that the PCI data bus is functional, that all
of the electronic modules are sending and receiving
the proper messages on the PCI data bus, and that
the power window motors are being sent the proper
hard wired outputs by the door modules for them to
perform their power window system functions.
For complete circuit diagrams, refer to the appro-
priate wiring information. The wiring information
includes wiring diagrams, proper wire and connector
repair procedures, details of wire harness routing
and retention, connector pin-out information and
location views for the various wire harness connec-
tors, splices and grounds.
ALL WINDOWS INOPERATIVE
(1) Check the operation of the power lock switch
on the driver side front door. If all of the doors lock
and unlock, but none of the power windows operate,
use a DRB scan tool and the proper Diagnostic Pro-
cedures manual to check the Body Control Module
(BCM), the Driver Door Module (DDM) and the PCI
data bus for proper operation. If not OK, go to Step
2.
(2) Check the operation of the power lock switch
on the passenger side front door. If the passenger
doors lock and unlock, but the driver side front door
does not, go to Step 5. If all of the power locks and
power windows are inoperative from both front doors,
go to Step 3.
(3) Check the fused B(+) fuse in the Power Distri-
bution Center (PDC). If OK, go to Step 4. If not OK,
repair the shorted circuit or component as required
and replace the faulty fuse.
(4) Check for battery voltage at the fused B(+) fuse
in the PDC. If OK, go to Step 5. If not OK, repair the
open fused B(+) circuit to the battery as required.
(5) Disconnect and isolate the battery negative
cable. Remove the trim panel from the driver side
front door. Disconnect the 15-way door wire harness
connector from the DDM connector receptacle. Check
for continuity between the ground circuit cavity of
the 15-way door wire harness connector for the DDM
and a good ground. There should be continuity. If
OK, go to Step 6. If not OK, repair the open ground
circuit to ground as required.
(6) Reconnect the battery negative cable. Check for
battery voltage at the fused B(+) circuit cavity of the
15-way door wire harness connector for the DDM. If
OK, replace the faulty DDM. If not OK, repair the
open fused B(+) circuit to the fuse in the PDC as
required.
8N - 34 POWER WINDOWSWJ
POWER WINDOWS (Continued)
Page 533 of 2199
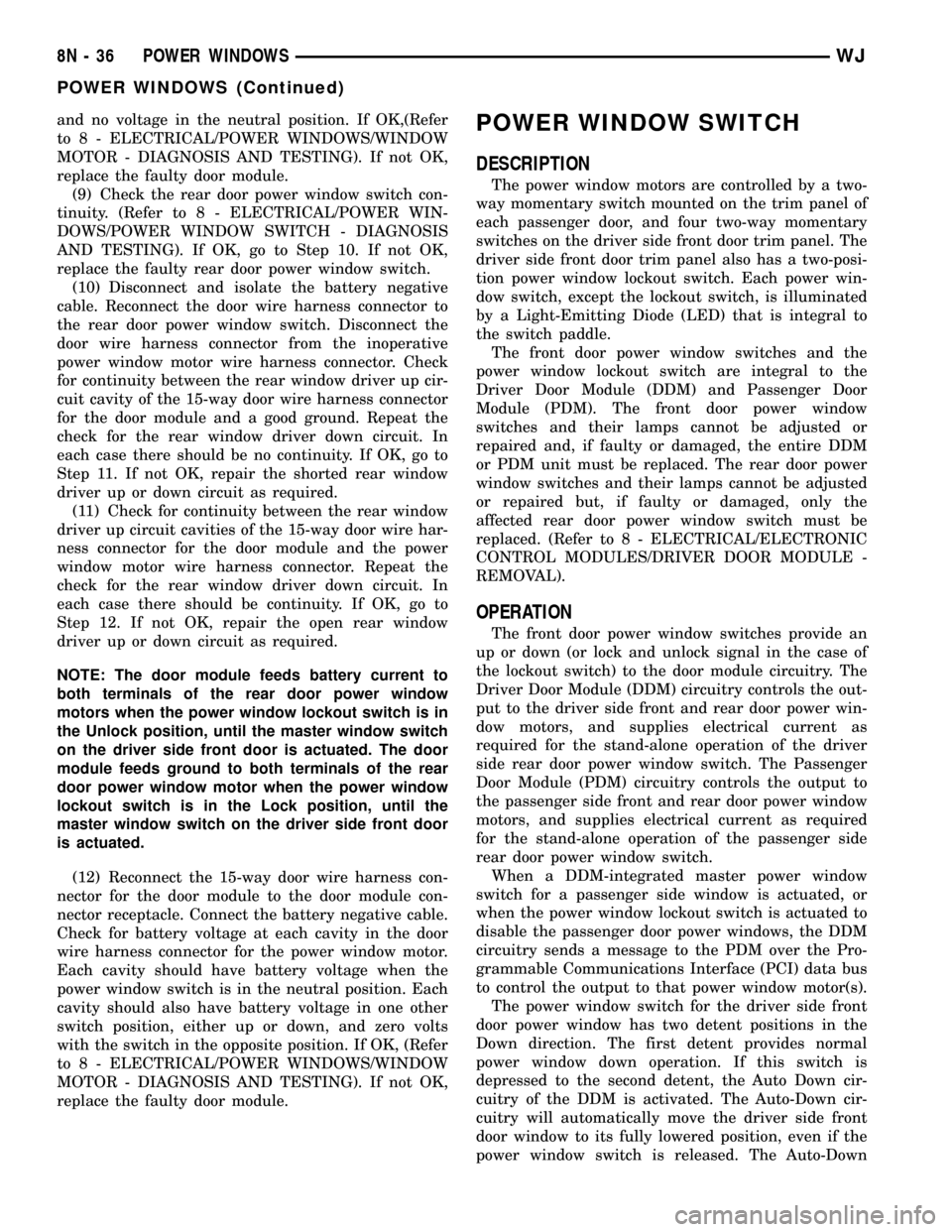
and no voltage in the neutral position. If OK,(Refer
to 8 - ELECTRICAL/POWER WINDOWS/WINDOW
MOTOR - DIAGNOSIS AND TESTING). If not OK,
replace the faulty door module.
(9) Check the rear door power window switch con-
tinuity. (Refer to 8 - ELECTRICAL/POWER WIN-
DOWS/POWER WINDOW SWITCH - DIAGNOSIS
AND TESTING). If OK, go to Step 10. If not OK,
replace the faulty rear door power window switch.
(10) Disconnect and isolate the battery negative
cable. Reconnect the door wire harness connector to
the rear door power window switch. Disconnect the
door wire harness connector from the inoperative
power window motor wire harness connector. Check
for continuity between the rear window driver up cir-
cuit cavity of the 15-way door wire harness connector
for the door module and a good ground. Repeat the
check for the rear window driver down circuit. In
each case there should be no continuity. If OK, go to
Step 11. If not OK, repair the shorted rear window
driver up or down circuit as required.
(11) Check for continuity between the rear window
driver up circuit cavities of the 15-way door wire har-
ness connector for the door module and the power
window motor wire harness connector. Repeat the
check for the rear window driver down circuit. In
each case there should be continuity. If OK, go to
Step 12. If not OK, repair the open rear window
driver up or down circuit as required.
NOTE: The door module feeds battery current to
both terminals of the rear door power window
motors when the power window lockout switch is in
the Unlock position, until the master window switch
on the driver side front door is actuated. The door
module feeds ground to both terminals of the rear
door power window motor when the power window
lockout switch is in the Lock position, until the
master window switch on the driver side front door
is actuated.
(12) Reconnect the 15-way door wire harness con-
nector for the door module to the door module con-
nector receptacle. Connect the battery negative cable.
Check for battery voltage at each cavity in the door
wire harness connector for the power window motor.
Each cavity should have battery voltage when the
power window switch is in the neutral position. Each
cavity should also have battery voltage in one other
switch position, either up or down, and zero volts
with the switch in the opposite position. If OK, (Refer
to 8 - ELECTRICAL/POWER WINDOWS/WINDOW
MOTOR - DIAGNOSIS AND TESTING). If not OK,
replace the faulty door module.POWER WINDOW SWITCH
DESCRIPTION
The power window motors are controlled by a two-
way momentary switch mounted on the trim panel of
each passenger door, and four two-way momentary
switches on the driver side front door trim panel. The
driver side front door trim panel also has a two-posi-
tion power window lockout switch. Each power win-
dow switch, except the lockout switch, is illuminated
by a Light-Emitting Diode (LED) that is integral to
the switch paddle.
The front door power window switches and the
power window lockout switch are integral to the
Driver Door Module (DDM) and Passenger Door
Module (PDM). The front door power window
switches and their lamps cannot be adjusted or
repaired and, if faulty or damaged, the entire DDM
or PDM unit must be replaced. The rear door power
window switches and their lamps cannot be adjusted
or repaired but, if faulty or damaged, only the
affected rear door power window switch must be
replaced. (Refer to 8 - ELECTRICAL/ELECTRONIC
CONTROL MODULES/DRIVER DOOR MODULE -
REMOVAL).
OPERATION
The front door power window switches provide an
up or down (or lock and unlock signal in the case of
the lockout switch) to the door module circuitry. The
Driver Door Module (DDM) circuitry controls the out-
put to the driver side front and rear door power win-
dow motors, and supplies electrical current as
required for the stand-alone operation of the driver
side rear door power window switch. The Passenger
Door Module (PDM) circuitry controls the output to
the passenger side front and rear door power window
motors, and supplies electrical current as required
for the stand-alone operation of the passenger side
rear door power window switch.
When a DDM-integrated master power window
switch for a passenger side window is actuated, or
when the power window lockout switch is actuated to
disable the passenger door power windows, the DDM
circuitry sends a message to the PDM over the Pro-
grammable Communications Interface (PCI) data bus
to control the output to that power window motor(s).
The power window switch for the driver side front
door power window has two detent positions in the
Down direction. The first detent provides normal
power window down operation. If this switch is
depressed to the second detent, the Auto Down cir-
cuitry of the DDM is activated. The Auto-Down cir-
cuitry will automatically move the driver side front
door window to its fully lowered position, even if the
power window switch is released. The Auto-Down
8N - 36 POWER WINDOWSWJ
POWER WINDOWS (Continued)
Page 535 of 2199
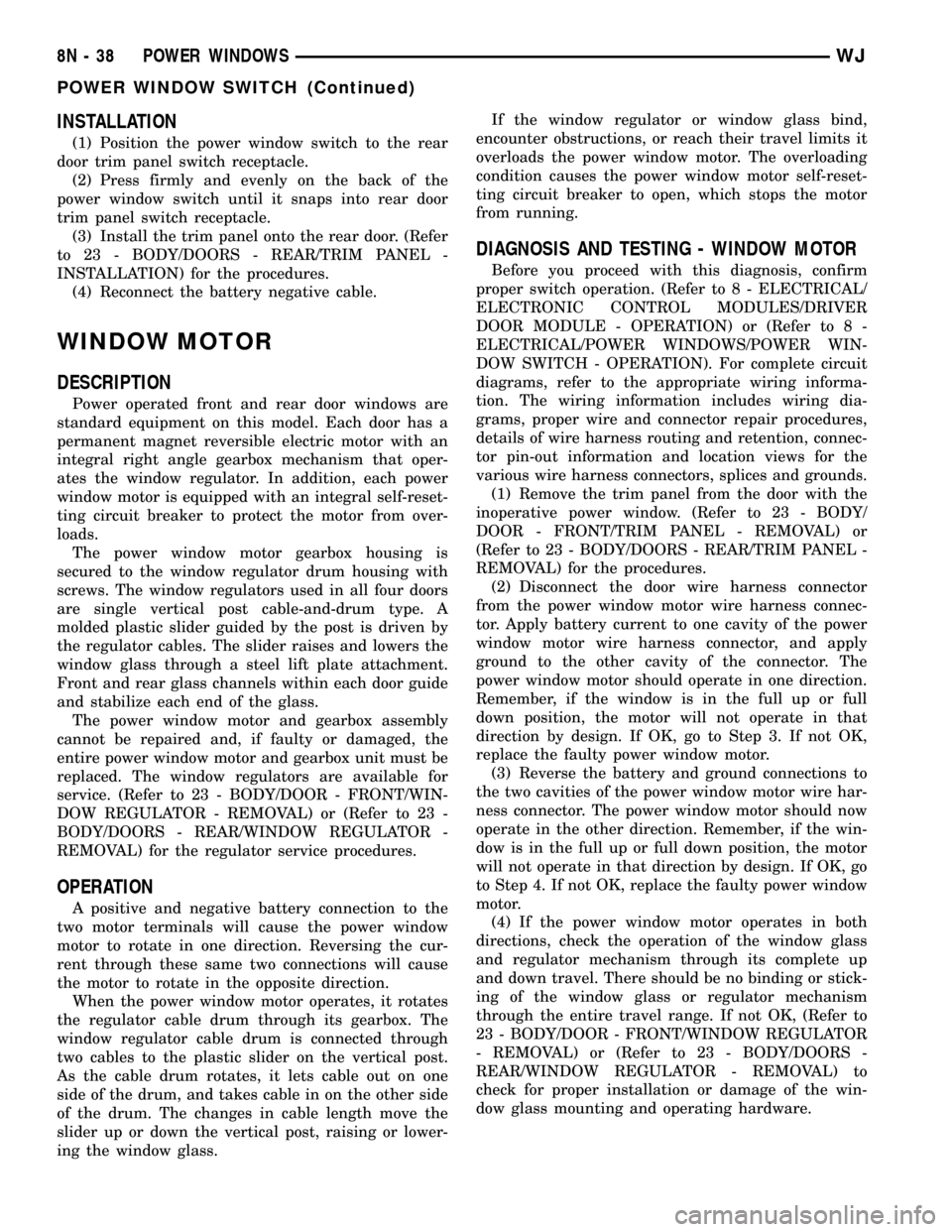
INSTALLATION
(1) Position the power window switch to the rear
door trim panel switch receptacle.
(2) Press firmly and evenly on the back of the
power window switch until it snaps into rear door
trim panel switch receptacle.
(3) Install the trim panel onto the rear door. (Refer
to 23 - BODY/DOORS - REAR/TRIM PANEL -
INSTALLATION) for the procedures.
(4) Reconnect the battery negative cable.
WINDOW MOTOR
DESCRIPTION
Power operated front and rear door windows are
standard equipment on this model. Each door has a
permanent magnet reversible electric motor with an
integral right angle gearbox mechanism that oper-
ates the window regulator. In addition, each power
window motor is equipped with an integral self-reset-
ting circuit breaker to protect the motor from over-
loads.
The power window motor gearbox housing is
secured to the window regulator drum housing with
screws. The window regulators used in all four doors
are single vertical post cable-and-drum type. A
molded plastic slider guided by the post is driven by
the regulator cables. The slider raises and lowers the
window glass through a steel lift plate attachment.
Front and rear glass channels within each door guide
and stabilize each end of the glass.
The power window motor and gearbox assembly
cannot be repaired and, if faulty or damaged, the
entire power window motor and gearbox unit must be
replaced. The window regulators are available for
service. (Refer to 23 - BODY/DOOR - FRONT/WIN-
DOW REGULATOR - REMOVAL) or (Refer to 23 -
BODY/DOORS - REAR/WINDOW REGULATOR -
REMOVAL) for the regulator service procedures.
OPERATION
A positive and negative battery connection to the
two motor terminals will cause the power window
motor to rotate in one direction. Reversing the cur-
rent through these same two connections will cause
the motor to rotate in the opposite direction.
When the power window motor operates, it rotates
the regulator cable drum through its gearbox. The
window regulator cable drum is connected through
two cables to the plastic slider on the vertical post.
As the cable drum rotates, it lets cable out on one
side of the drum, and takes cable in on the other side
of the drum. The changes in cable length move the
slider up or down the vertical post, raising or lower-
ing the window glass.If the window regulator or window glass bind,
encounter obstructions, or reach their travel limits it
overloads the power window motor. The overloading
condition causes the power window motor self-reset-
ting circuit breaker to open, which stops the motor
from running.
DIAGNOSIS AND TESTING - WINDOW MOTOR
Before you proceed with this diagnosis, confirm
proper switch operation. (Refer to 8 - ELECTRICAL/
ELECTRONIC CONTROL MODULES/DRIVER
DOOR MODULE - OPERATION) or (Refer to 8 -
ELECTRICAL/POWER WINDOWS/POWER WIN-
DOW SWITCH - OPERATION). For complete circuit
diagrams, refer to the appropriate wiring informa-
tion. The wiring information includes wiring dia-
grams, proper wire and connector repair procedures,
details of wire harness routing and retention, connec-
tor pin-out information and location views for the
various wire harness connectors, splices and grounds.
(1) Remove the trim panel from the door with the
inoperative power window. (Refer to 23 - BODY/
DOOR - FRONT/TRIM PANEL - REMOVAL) or
(Refer to 23 - BODY/DOORS - REAR/TRIM PANEL -
REMOVAL) for the procedures.
(2) Disconnect the door wire harness connector
from the power window motor wire harness connec-
tor. Apply battery current to one cavity of the power
window motor wire harness connector, and apply
ground to the other cavity of the connector. The
power window motor should operate in one direction.
Remember, if the window is in the full up or full
down position, the motor will not operate in that
direction by design. If OK, go to Step 3. If not OK,
replace the faulty power window motor.
(3) Reverse the battery and ground connections to
the two cavities of the power window motor wire har-
ness connector. The power window motor should now
operate in the other direction. Remember, if the win-
dow is in the full up or full down position, the motor
will not operate in that direction by design. If OK, go
to Step 4. If not OK, replace the faulty power window
motor.
(4) If the power window motor operates in both
directions, check the operation of the window glass
and regulator mechanism through its complete up
and down travel. There should be no binding or stick-
ing of the window glass or regulator mechanism
through the entire travel range. If not OK, (Refer to
23 - BODY/DOOR - FRONT/WINDOW REGULATOR
- REMOVAL) or (Refer to 23 - BODY/DOORS -
REAR/WINDOW REGULATOR - REMOVAL) to
check for proper installation or damage of the win-
dow glass mounting and operating hardware.
8N - 38 POWER WINDOWSWJ
POWER WINDOW SWITCH (Continued)
Page 574 of 2199
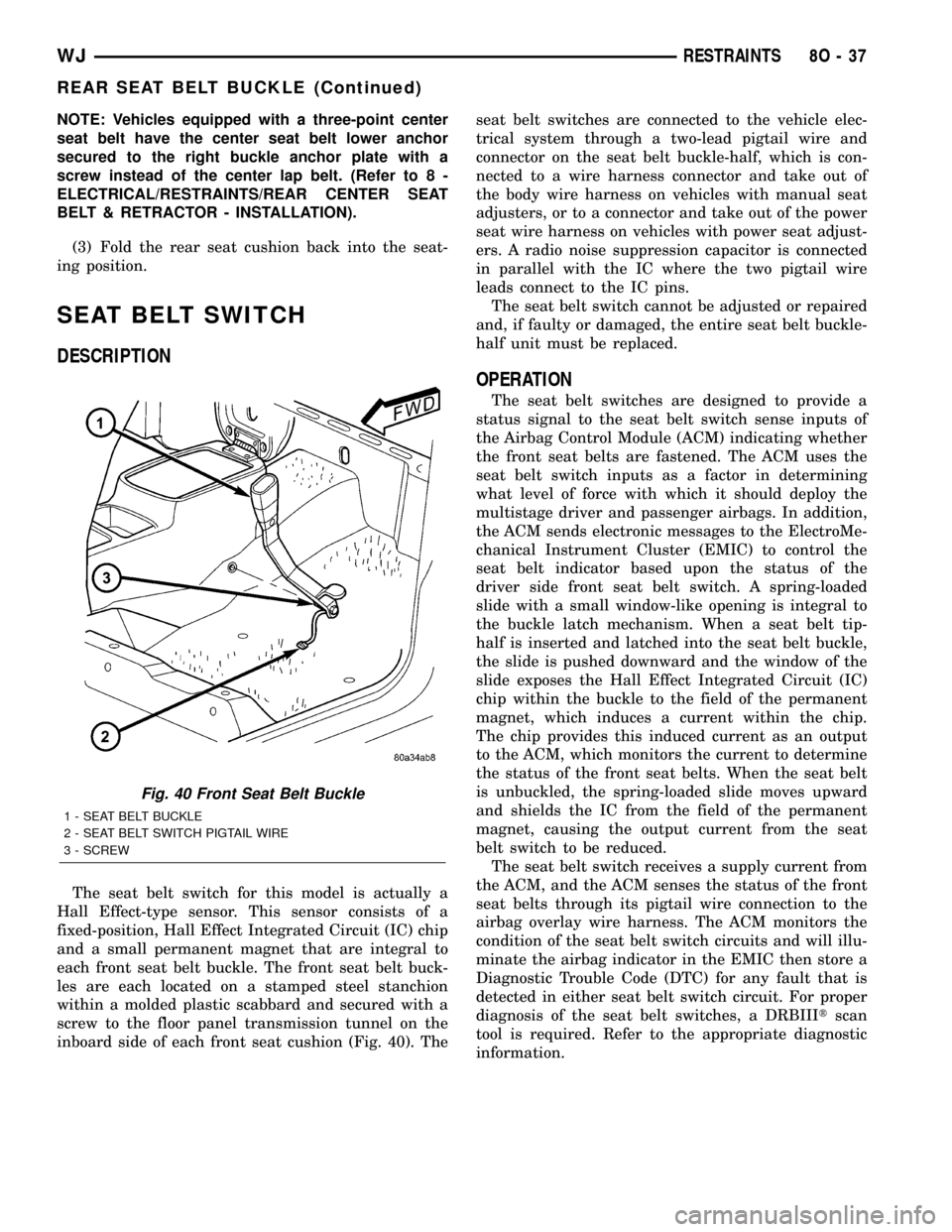
NOTE: Vehicles equipped with a three-point center
seat belt have the center seat belt lower anchor
secured to the right buckle anchor plate with a
screw instead of the center lap belt. (Refer to 8 -
ELECTRICAL/RESTRAINTS/REAR CENTER SEAT
BELT & RETRACTOR - INSTALLATION).
(3) Fold the rear seat cushion back into the seat-
ing position.
SEAT BELT SWITCH
DESCRIPTION
The seat belt switch for this model is actually a
Hall Effect-type sensor. This sensor consists of a
fixed-position, Hall Effect Integrated Circuit (IC) chip
and a small permanent magnet that are integral to
each front seat belt buckle. The front seat belt buck-
les are each located on a stamped steel stanchion
within a molded plastic scabbard and secured with a
screw to the floor panel transmission tunnel on the
inboard side of each front seat cushion (Fig. 40). Theseat belt switches are connected to the vehicle elec-
trical system through a two-lead pigtail wire and
connector on the seat belt buckle-half, which is con-
nected to a wire harness connector and take out of
the body wire harness on vehicles with manual seat
adjusters, or to a connector and take out of the power
seat wire harness on vehicles with power seat adjust-
ers. A radio noise suppression capacitor is connected
in parallel with the IC where the two pigtail wire
leads connect to the IC pins.
The seat belt switch cannot be adjusted or repaired
and, if faulty or damaged, the entire seat belt buckle-
half unit must be replaced.
OPERATION
The seat belt switches are designed to provide a
status signal to the seat belt switch sense inputs of
the Airbag Control Module (ACM) indicating whether
the front seat belts are fastened. The ACM uses the
seat belt switch inputs as a factor in determining
what level of force with which it should deploy the
multistage driver and passenger airbags. In addition,
the ACM sends electronic messages to the ElectroMe-
chanical Instrument Cluster (EMIC) to control the
seat belt indicator based upon the status of the
driver side front seat belt switch. A spring-loaded
slide with a small window-like opening is integral to
the buckle latch mechanism. When a seat belt tip-
half is inserted and latched into the seat belt buckle,
the slide is pushed downward and the window of the
slide exposes the Hall Effect Integrated Circuit (IC)
chip within the buckle to the field of the permanent
magnet, which induces a current within the chip.
The chip provides this induced current as an output
to the ACM, which monitors the current to determine
the status of the front seat belts. When the seat belt
is unbuckled, the spring-loaded slide moves upward
and shields the IC from the field of the permanent
magnet, causing the output current from the seat
belt switch to be reduced.
The seat belt switch receives a supply current from
the ACM, and the ACM senses the status of the front
seat belts through its pigtail wire connection to the
airbag overlay wire harness. The ACM monitors the
condition of the seat belt switch circuits and will illu-
minate the airbag indicator in the EMIC then store a
Diagnostic Trouble Code (DTC) for any fault that is
detected in either seat belt switch circuit. For proper
diagnosis of the seat belt switches, a DRBIIItscan
tool is required. Refer to the appropriate diagnostic
information.
Fig. 40 Front Seat Belt Buckle
1 - SEAT BELT BUCKLE
2 - SEAT BELT SWITCH PIGTAIL WIRE
3 - SCREW
WJRESTRAINTS 8O - 37
REAR SEAT BELT BUCKLE (Continued)
Page 586 of 2199
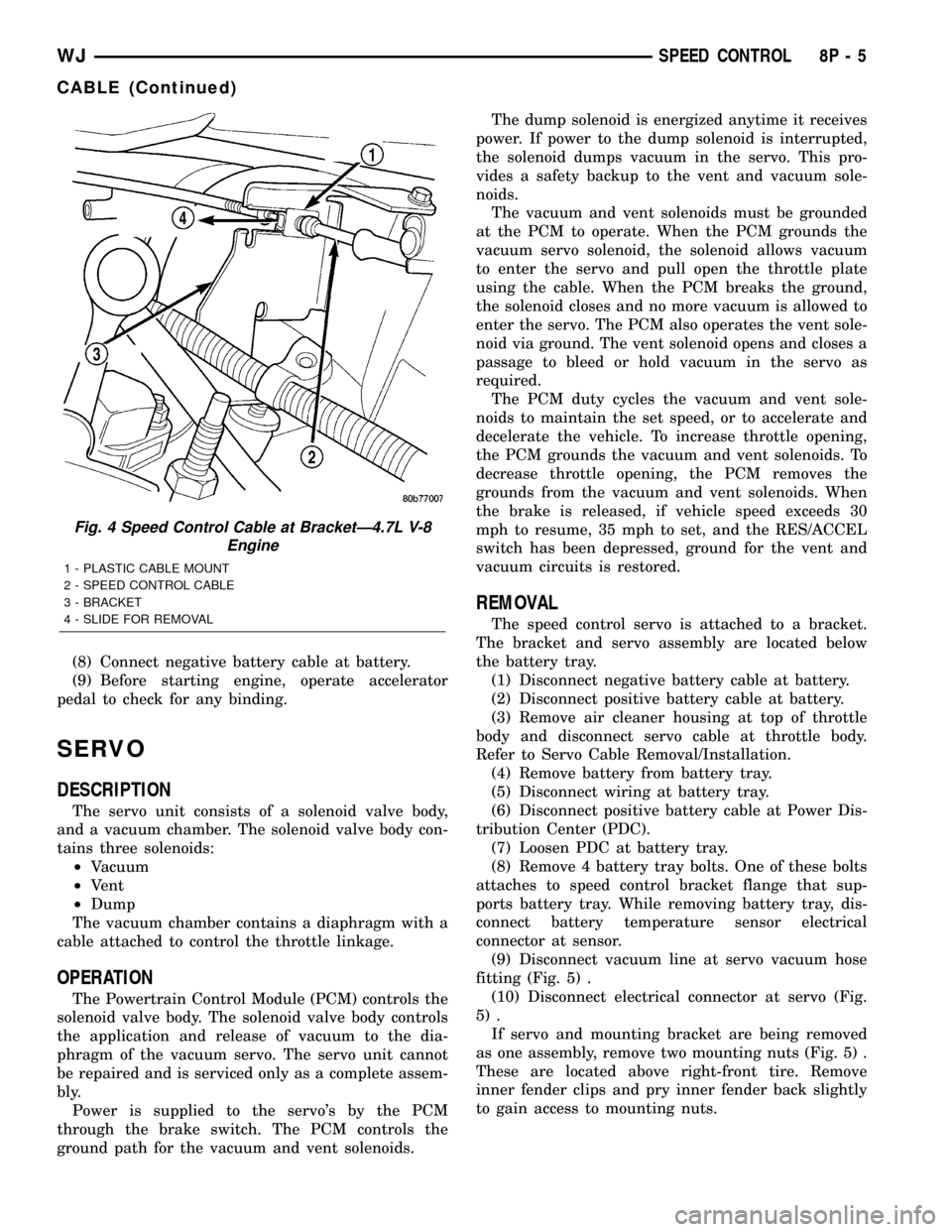
(8) Connect negative battery cable at battery.
(9) Before starting engine, operate accelerator
pedal to check for any binding.
SERVO
DESCRIPTION
The servo unit consists of a solenoid valve body,
and a vacuum chamber. The solenoid valve body con-
tains three solenoids:
²Vacuum
²Vent
²Dump
The vacuum chamber contains a diaphragm with a
cable attached to control the throttle linkage.
OPERATION
The Powertrain Control Module (PCM) controls the
solenoid valve body. The solenoid valve body controls
the application and release of vacuum to the dia-
phragm of the vacuum servo. The servo unit cannot
be repaired and is serviced only as a complete assem-
bly.
Power is supplied to the servo's by the PCM
through the brake switch. The PCM controls the
ground path for the vacuum and vent solenoids.The dump solenoid is energized anytime it receives
power. If power to the dump solenoid is interrupted,
the solenoid dumps vacuum in the servo. This pro-
vides a safety backup to the vent and vacuum sole-
noids.
The vacuum and vent solenoids must be grounded
at the PCM to operate. When the PCM grounds the
vacuum servo solenoid, the solenoid allows vacuum
to enter the servo and pull open the throttle plate
using the cable. When the PCM breaks the ground,
the solenoid closes and no more vacuum is allowed to
enter the servo. The PCM also operates the vent sole-
noid via ground. The vent solenoid opens and closes a
passage to bleed or hold vacuum in the servo as
required.
The PCM duty cycles the vacuum and vent sole-
noids to maintain the set speed, or to accelerate and
decelerate the vehicle. To increase throttle opening,
the PCM grounds the vacuum and vent solenoids. To
decrease throttle opening, the PCM removes the
grounds from the vacuum and vent solenoids. When
the brake is released, if vehicle speed exceeds 30
mph to resume, 35 mph to set, and the RES/ACCEL
switch has been depressed, ground for the vent and
vacuum circuits is restored.
REMOVAL
The speed control servo is attached to a bracket.
The bracket and servo assembly are located below
the battery tray.
(1) Disconnect negative battery cable at battery.
(2) Disconnect positive battery cable at battery.
(3) Remove air cleaner housing at top of throttle
body and disconnect servo cable at throttle body.
Refer to Servo Cable Removal/Installation.
(4) Remove battery from battery tray.
(5) Disconnect wiring at battery tray.
(6) Disconnect positive battery cable at Power Dis-
tribution Center (PDC).
(7) Loosen PDC at battery tray.
(8) Remove 4 battery tray bolts. One of these bolts
attaches to speed control bracket flange that sup-
ports battery tray. While removing battery tray, dis-
connect battery temperature sensor electrical
connector at sensor.
(9) Disconnect vacuum line at servo vacuum hose
fitting (Fig. 5) .
(10) Disconnect electrical connector at servo (Fig.
5) .
If servo and mounting bracket are being removed
as one assembly, remove two mounting nuts (Fig. 5) .
These are located above right-front tire. Remove
inner fender clips and pry inner fender back slightly
to gain access to mounting nuts.
Fig. 4 Speed Control Cable at BracketÐ4.7L V-8
Engine
1 - PLASTIC CABLE MOUNT
2 - SPEED CONTROL CABLE
3 - BRACKET
4 - SLIDE FOR REMOVAL
WJSPEED CONTROL 8P - 5
CABLE (Continued)
Page 588 of 2199
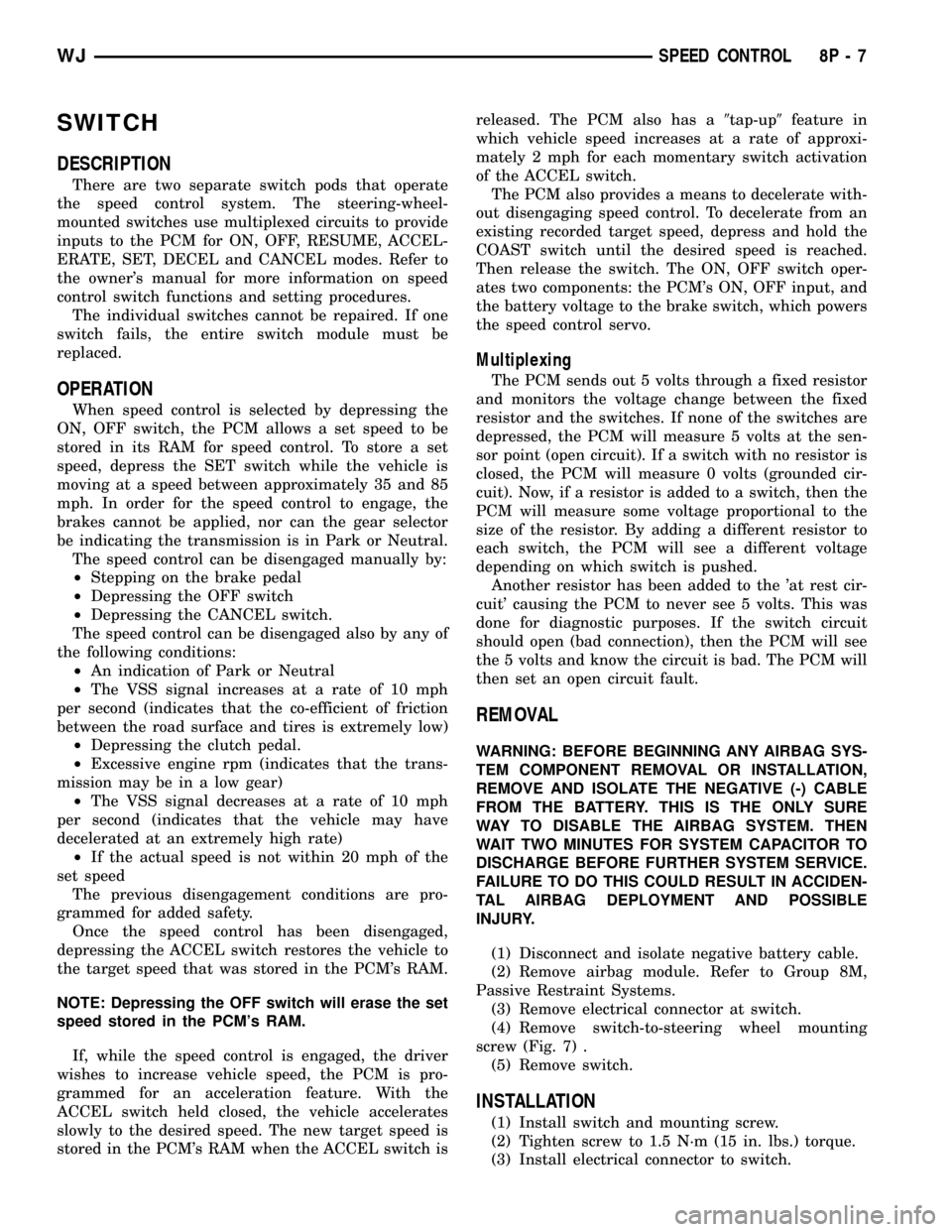
SWITCH
DESCRIPTION
There are two separate switch pods that operate
the speed control system. The steering-wheel-
mounted switches use multiplexed circuits to provide
inputs to the PCM for ON, OFF, RESUME, ACCEL-
ERATE, SET, DECEL and CANCEL modes. Refer to
the owner's manual for more information on speed
control switch functions and setting procedures.
The individual switches cannot be repaired. If one
switch fails, the entire switch module must be
replaced.
OPERATION
When speed control is selected by depressing the
ON, OFF switch, the PCM allows a set speed to be
stored in its RAM for speed control. To store a set
speed, depress the SET switch while the vehicle is
moving at a speed between approximately 35 and 85
mph. In order for the speed control to engage, the
brakes cannot be applied, nor can the gear selector
be indicating the transmission is in Park or Neutral.
The speed control can be disengaged manually by:
²Stepping on the brake pedal
²Depressing the OFF switch
²Depressing the CANCEL switch.
The speed control can be disengaged also by any of
the following conditions:
²An indication of Park or Neutral
²The VSS signal increases at a rate of 10 mph
per second (indicates that the co-efficient of friction
between the road surface and tires is extremely low)
²Depressing the clutch pedal.
²Excessive engine rpm (indicates that the trans-
mission may be in a low gear)
²The VSS signal decreases at a rate of 10 mph
per second (indicates that the vehicle may have
decelerated at an extremely high rate)
²If the actual speed is not within 20 mph of the
set speed
The previous disengagement conditions are pro-
grammed for added safety.
Once the speed control has been disengaged,
depressing the ACCEL switch restores the vehicle to
the target speed that was stored in the PCM's RAM.
NOTE: Depressing the OFF switch will erase the set
speed stored in the PCM's RAM.
If, while the speed control is engaged, the driver
wishes to increase vehicle speed, the PCM is pro-
grammed for an acceleration feature. With the
ACCEL switch held closed, the vehicle accelerates
slowly to the desired speed. The new target speed is
stored in the PCM's RAM when the ACCEL switch isreleased. The PCM also has a9tap-up9feature in
which vehicle speed increases at a rate of approxi-
mately 2 mph for each momentary switch activation
of the ACCEL switch.
The PCM also provides a means to decelerate with-
out disengaging speed control. To decelerate from an
existing recorded target speed, depress and hold the
COAST switch until the desired speed is reached.
Then release the switch. The ON, OFF switch oper-
ates two components: the PCM's ON, OFF input, and
the battery voltage to the brake switch, which powers
the speed control servo.
Multiplexing
The PCM sends out 5 volts through a fixed resistor
and monitors the voltage change between the fixed
resistor and the switches. If none of the switches are
depressed, the PCM will measure 5 volts at the sen-
sor point (open circuit). If a switch with no resistor is
closed, the PCM will measure 0 volts (grounded cir-
cuit). Now, if a resistor is added to a switch, then the
PCM will measure some voltage proportional to the
size of the resistor. By adding a different resistor to
each switch, the PCM will see a different voltage
depending on which switch is pushed.
Another resistor has been added to the 'at rest cir-
cuit' causing the PCM to never see 5 volts. This was
done for diagnostic purposes. If the switch circuit
should open (bad connection), then the PCM will see
the 5 volts and know the circuit is bad. The PCM will
then set an open circuit fault.
REMOVAL
WARNING: BEFORE BEGINNING ANY AIRBAG SYS-
TEM COMPONENT REMOVAL OR INSTALLATION,
REMOVE AND ISOLATE THE NEGATIVE (-) CABLE
FROM THE BATTERY. THIS IS THE ONLY SURE
WAY TO DISABLE THE AIRBAG SYSTEM. THEN
WAIT TWO MINUTES FOR SYSTEM CAPACITOR TO
DISCHARGE BEFORE FURTHER SYSTEM SERVICE.
FAILURE TO DO THIS COULD RESULT IN ACCIDEN-
TAL AIRBAG DEPLOYMENT AND POSSIBLE
INJURY.
(1) Disconnect and isolate negative battery cable.
(2) Remove airbag module. Refer to Group 8M,
Passive Restraint Systems.
(3) Remove electrical connector at switch.
(4) Remove switch-to-steering wheel mounting
screw (Fig. 7) .
(5) Remove switch.
INSTALLATION
(1) Install switch and mounting screw.
(2) Tighten screw to 1.5 N´m (15 in. lbs.) torque.
(3) Install electrical connector to switch.
WJSPEED CONTROL 8P - 7
Page 593 of 2199
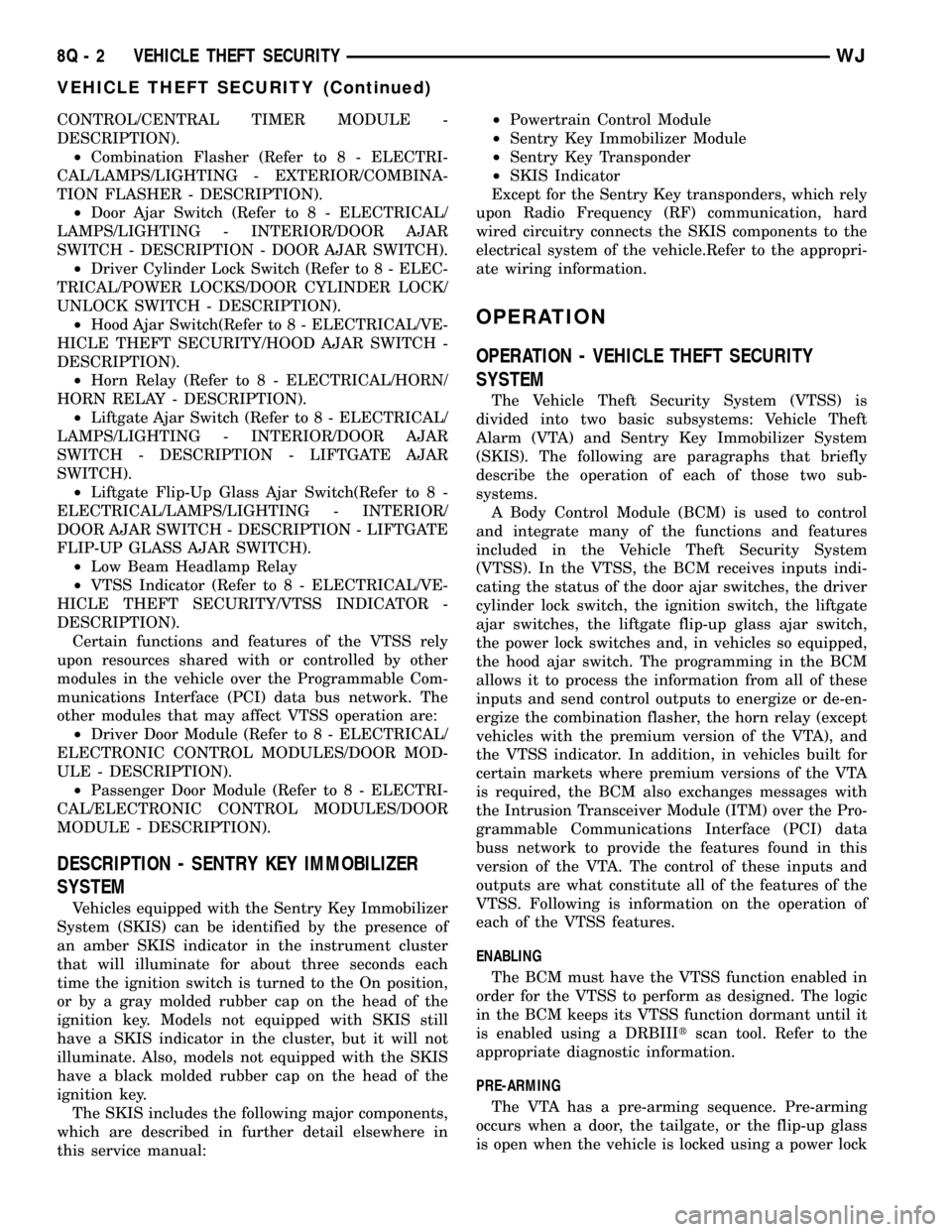
CONTROL/CENTRAL TIMER MODULE -
DESCRIPTION).
²Combination Flasher (Refer to 8 - ELECTRI-
CAL/LAMPS/LIGHTING - EXTERIOR/COMBINA-
TION FLASHER - DESCRIPTION).
²Door Ajar Switch (Refer to 8 - ELECTRICAL/
LAMPS/LIGHTING - INTERIOR/DOOR AJAR
SWITCH - DESCRIPTION - DOOR AJAR SWITCH).
²Driver Cylinder Lock Switch (Refer to 8 - ELEC-
TRICAL/POWER LOCKS/DOOR CYLINDER LOCK/
UNLOCK SWITCH - DESCRIPTION).
²Hood Ajar Switch(Refer to 8 - ELECTRICAL/VE-
HICLE THEFT SECURITY/HOOD AJAR SWITCH -
DESCRIPTION).
²Horn Relay (Refer to 8 - ELECTRICAL/HORN/
HORN RELAY - DESCRIPTION).
²Liftgate Ajar Switch (Refer to 8 - ELECTRICAL/
LAMPS/LIGHTING - INTERIOR/DOOR AJAR
SWITCH - DESCRIPTION - LIFTGATE AJAR
SWITCH).
²Liftgate Flip-Up Glass Ajar Switch(Refer to 8 -
ELECTRICAL/LAMPS/LIGHTING - INTERIOR/
DOOR AJAR SWITCH - DESCRIPTION - LIFTGATE
FLIP-UP GLASS AJAR SWITCH).
²Low Beam Headlamp Relay
²VTSS Indicator (Refer to 8 - ELECTRICAL/VE-
HICLE THEFT SECURITY/VTSS INDICATOR -
DESCRIPTION).
Certain functions and features of the VTSS rely
upon resources shared with or controlled by other
modules in the vehicle over the Programmable Com-
munications Interface (PCI) data bus network. The
other modules that may affect VTSS operation are:
²Driver Door Module (Refer to 8 - ELECTRICAL/
ELECTRONIC CONTROL MODULES/DOOR MOD-
ULE - DESCRIPTION).
²Passenger Door Module (Refer to 8 - ELECTRI-
CAL/ELECTRONIC CONTROL MODULES/DOOR
MODULE - DESCRIPTION).
DESCRIPTION - SENTRY KEY IMMOBILIZER
SYSTEM
Vehicles equipped with the Sentry Key Immobilizer
System (SKIS) can be identified by the presence of
an amber SKIS indicator in the instrument cluster
that will illuminate for about three seconds each
time the ignition switch is turned to the On position,
or by a gray molded rubber cap on the head of the
ignition key. Models not equipped with SKIS still
have a SKIS indicator in the cluster, but it will not
illuminate. Also, models not equipped with the SKIS
have a black molded rubber cap on the head of the
ignition key.
The SKIS includes the following major components,
which are described in further detail elsewhere in
this service manual:²Powertrain Control Module
²Sentry Key Immobilizer Module
²Sentry Key Transponder
²SKIS Indicator
Except for the Sentry Key transponders, which rely
upon Radio Frequency (RF) communication, hard
wired circuitry connects the SKIS components to the
electrical system of the vehicle.Refer to the appropri-
ate wiring information.
OPERATION
OPERATION - VEHICLE THEFT SECURITY
SYSTEM
The Vehicle Theft Security System (VTSS) is
divided into two basic subsystems: Vehicle Theft
Alarm (VTA) and Sentry Key Immobilizer System
(SKIS). The following are paragraphs that briefly
describe the operation of each of those two sub-
systems.
A Body Control Module (BCM) is used to control
and integrate many of the functions and features
included in the Vehicle Theft Security System
(VTSS). In the VTSS, the BCM receives inputs indi-
cating the status of the door ajar switches, the driver
cylinder lock switch, the ignition switch, the liftgate
ajar switches, the liftgate flip-up glass ajar switch,
the power lock switches and, in vehicles so equipped,
the hood ajar switch. The programming in the BCM
allows it to process the information from all of these
inputs and send control outputs to energize or de-en-
ergize the combination flasher, the horn relay (except
vehicles with the premium version of the VTA), and
the VTSS indicator. In addition, in vehicles built for
certain markets where premium versions of the VTA
is required, the BCM also exchanges messages with
the Intrusion Transceiver Module (ITM) over the Pro-
grammable Communications Interface (PCI) data
buss network to provide the features found in this
version of the VTA. The control of these inputs and
outputs are what constitute all of the features of the
VTSS. Following is information on the operation of
each of the VTSS features.
ENABLING
The BCM must have the VTSS function enabled in
order for the VTSS to perform as designed. The logic
in the BCM keeps its VTSS function dormant until it
is enabled using a DRBIIItscan tool. Refer to the
appropriate diagnostic information.
PRE-ARMING
The VTA has a pre-arming sequence. Pre-arming
occurs when a door, the tailgate, or the flip-up glass
is open when the vehicle is locked using a power lock
8Q - 2 VEHICLE THEFT SECURITYWJ
VEHICLE THEFT SECURITY (Continued)
Page 597 of 2199
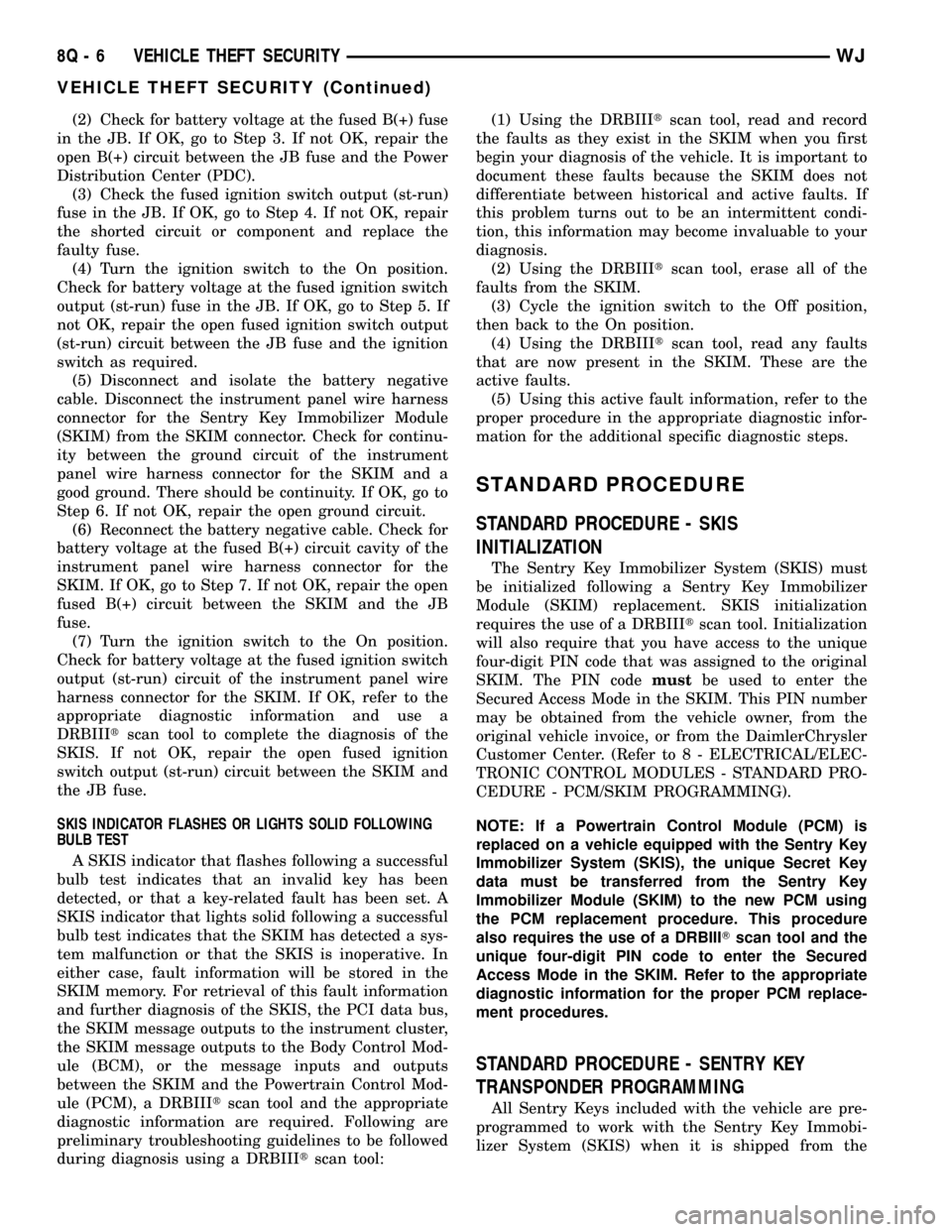
(2) Check for battery voltage at the fused B(+) fuse
in the JB. If OK, go to Step 3. If not OK, repair the
open B(+) circuit between the JB fuse and the Power
Distribution Center (PDC).
(3) Check the fused ignition switch output (st-run)
fuse in the JB. If OK, go to Step 4. If not OK, repair
the shorted circuit or component and replace the
faulty fuse.
(4) Turn the ignition switch to the On position.
Check for battery voltage at the fused ignition switch
output (st-run) fuse in the JB. If OK, go to Step 5. If
not OK, repair the open fused ignition switch output
(st-run) circuit between the JB fuse and the ignition
switch as required.
(5) Disconnect and isolate the battery negative
cable. Disconnect the instrument panel wire harness
connector for the Sentry Key Immobilizer Module
(SKIM) from the SKIM connector. Check for continu-
ity between the ground circuit of the instrument
panel wire harness connector for the SKIM and a
good ground. There should be continuity. If OK, go to
Step 6. If not OK, repair the open ground circuit.
(6) Reconnect the battery negative cable. Check for
battery voltage at the fused B(+) circuit cavity of the
instrument panel wire harness connector for the
SKIM. If OK, go to Step 7. If not OK, repair the open
fused B(+) circuit between the SKIM and the JB
fuse.
(7) Turn the ignition switch to the On position.
Check for battery voltage at the fused ignition switch
output (st-run) circuit of the instrument panel wire
harness connector for the SKIM. If OK, refer to the
appropriate diagnostic information and use a
DRBIIItscan tool to complete the diagnosis of the
SKIS. If not OK, repair the open fused ignition
switch output (st-run) circuit between the SKIM and
the JB fuse.
SKIS INDICATOR FLASHES OR LIGHTS SOLID FOLLOWING
BULB TEST
A SKIS indicator that flashes following a successful
bulb test indicates that an invalid key has been
detected, or that a key-related fault has been set. A
SKIS indicator that lights solid following a successful
bulb test indicates that the SKIM has detected a sys-
tem malfunction or that the SKIS is inoperative. In
either case, fault information will be stored in the
SKIM memory. For retrieval of this fault information
and further diagnosis of the SKIS, the PCI data bus,
the SKIM message outputs to the instrument cluster,
the SKIM message outputs to the Body Control Mod-
ule (BCM), or the message inputs and outputs
between the SKIM and the Powertrain Control Mod-
ule (PCM), a DRBIIItscan tool and the appropriate
diagnostic information are required. Following are
preliminary troubleshooting guidelines to be followed
during diagnosis using a DRBIIItscan tool:(1) Using the DRBIIItscan tool, read and record
the faults as they exist in the SKIM when you first
begin your diagnosis of the vehicle. It is important to
document these faults because the SKIM does not
differentiate between historical and active faults. If
this problem turns out to be an intermittent condi-
tion, this information may become invaluable to your
diagnosis.
(2) Using the DRBIIItscan tool, erase all of the
faults from the SKIM.
(3) Cycle the ignition switch to the Off position,
then back to the On position.
(4) Using the DRBIIItscan tool, read any faults
that are now present in the SKIM. These are the
active faults.
(5) Using this active fault information, refer to the
proper procedure in the appropriate diagnostic infor-
mation for the additional specific diagnostic steps.
STANDARD PROCEDURE
STANDARD PROCEDURE - SKIS
INITIALIZATION
The Sentry Key Immobilizer System (SKIS) must
be initialized following a Sentry Key Immobilizer
Module (SKIM) replacement. SKIS initialization
requires the use of a DRBIIItscan tool. Initialization
will also require that you have access to the unique
four-digit PIN code that was assigned to the original
SKIM. The PIN codemustbe used to enter the
Secured Access Mode in the SKIM. This PIN number
may be obtained from the vehicle owner, from the
original vehicle invoice, or from the DaimlerChrysler
Customer Center. (Refer to 8 - ELECTRICAL/ELEC-
TRONIC CONTROL MODULES - STANDARD PRO-
CEDURE - PCM/SKIM PROGRAMMING).
NOTE: If a Powertrain Control Module (PCM) is
replaced on a vehicle equipped with the Sentry Key
Immobilizer System (SKIS), the unique Secret Key
data must be transferred from the Sentry Key
Immobilizer Module (SKIM) to the new PCM using
the PCM replacement procedure. This procedure
also requires the use of a DRBIIITscan tool and the
unique four-digit PIN code to enter the Secured
Access Mode in the SKIM. Refer to the appropriate
diagnostic information for the proper PCM replace-
ment procedures.
STANDARD PROCEDURE - SENTRY KEY
TRANSPONDER PROGRAMMING
All Sentry Keys included with the vehicle are pre-
programmed to work with the Sentry Key Immobi-
lizer System (SKIS) when it is shipped from the
8Q - 6 VEHICLE THEFT SECURITYWJ
VEHICLE THEFT SECURITY (Continued)
Page 606 of 2199
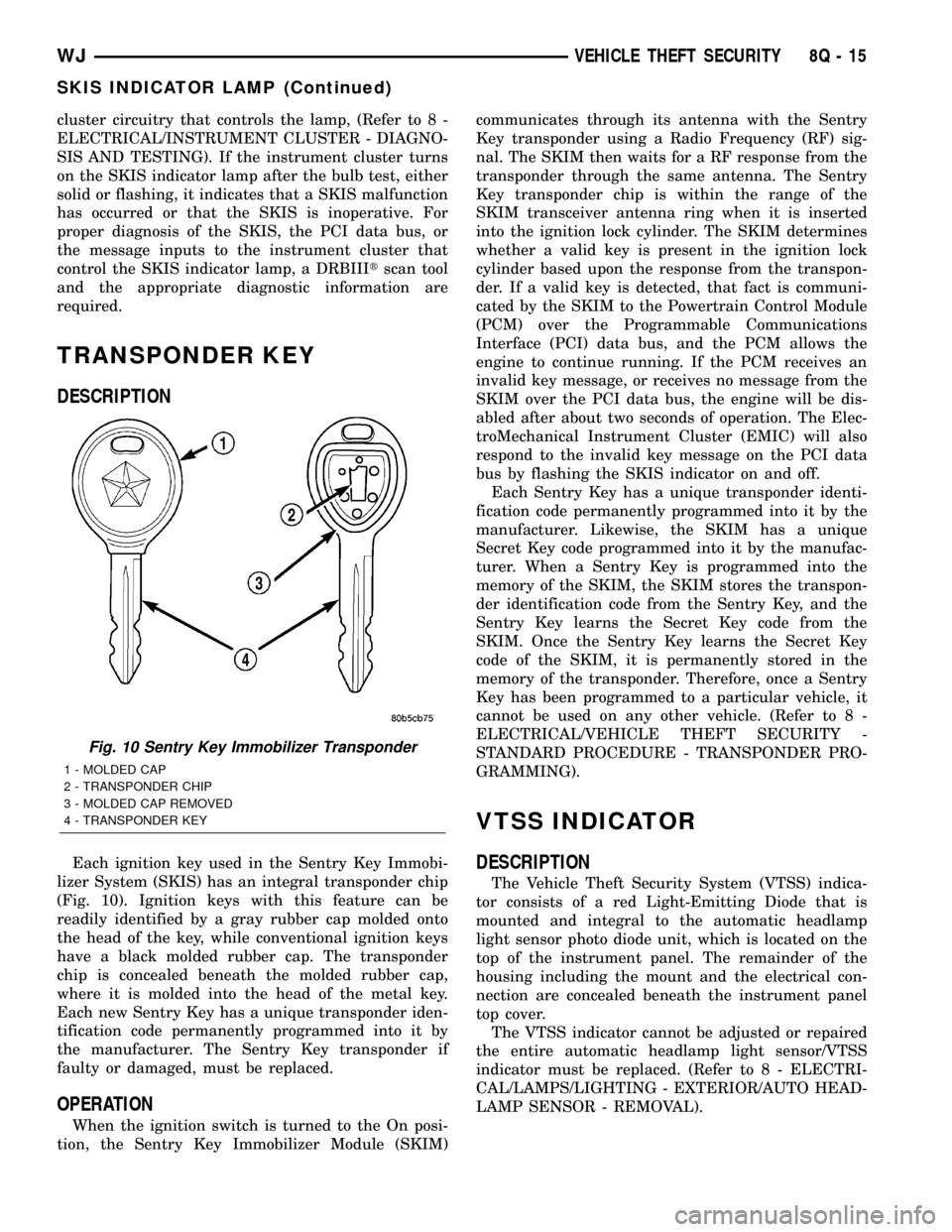
cluster circuitry that controls the lamp, (Refer to 8 -
ELECTRICAL/INSTRUMENT CLUSTER - DIAGNO-
SIS AND TESTING). If the instrument cluster turns
on the SKIS indicator lamp after the bulb test, either
solid or flashing, it indicates that a SKIS malfunction
has occurred or that the SKIS is inoperative. For
proper diagnosis of the SKIS, the PCI data bus, or
the message inputs to the instrument cluster that
control the SKIS indicator lamp, a DRBIIItscan tool
and the appropriate diagnostic information are
required.
TRANSPONDER KEY
DESCRIPTION
Each ignition key used in the Sentry Key Immobi-
lizer System (SKIS) has an integral transponder chip
(Fig. 10). Ignition keys with this feature can be
readily identified by a gray rubber cap molded onto
the head of the key, while conventional ignition keys
have a black molded rubber cap. The transponder
chip is concealed beneath the molded rubber cap,
where it is molded into the head of the metal key.
Each new Sentry Key has a unique transponder iden-
tification code permanently programmed into it by
the manufacturer. The Sentry Key transponder if
faulty or damaged, must be replaced.
OPERATION
When the ignition switch is turned to the On posi-
tion, the Sentry Key Immobilizer Module (SKIM)communicates through its antenna with the Sentry
Key transponder using a Radio Frequency (RF) sig-
nal. The SKIM then waits for a RF response from the
transponder through the same antenna. The Sentry
Key transponder chip is within the range of the
SKIM transceiver antenna ring when it is inserted
into the ignition lock cylinder. The SKIM determines
whether a valid key is present in the ignition lock
cylinder based upon the response from the transpon-
der. If a valid key is detected, that fact is communi-
cated by the SKIM to the Powertrain Control Module
(PCM) over the Programmable Communications
Interface (PCI) data bus, and the PCM allows the
engine to continue running. If the PCM receives an
invalid key message, or receives no message from the
SKIM over the PCI data bus, the engine will be dis-
abled after about two seconds of operation. The Elec-
troMechanical Instrument Cluster (EMIC) will also
respond to the invalid key message on the PCI data
bus by flashing the SKIS indicator on and off.
Each Sentry Key has a unique transponder identi-
fication code permanently programmed into it by the
manufacturer. Likewise, the SKIM has a unique
Secret Key code programmed into it by the manufac-
turer. When a Sentry Key is programmed into the
memory of the SKIM, the SKIM stores the transpon-
der identification code from the Sentry Key, and the
Sentry Key learns the Secret Key code from the
SKIM. Once the Sentry Key learns the Secret Key
code of the SKIM, it is permanently stored in the
memory of the transponder. Therefore, once a Sentry
Key has been programmed to a particular vehicle, it
cannot be used on any other vehicle. (Refer to 8 -
ELECTRICAL/VEHICLE THEFT SECURITY -
STANDARD PROCEDURE - TRANSPONDER PRO-
GRAMMING).
VTSS INDICATOR
DESCRIPTION
The Vehicle Theft Security System (VTSS) indica-
tor consists of a red Light-Emitting Diode that is
mounted and integral to the automatic headlamp
light sensor photo diode unit, which is located on the
top of the instrument panel. The remainder of the
housing including the mount and the electrical con-
nection are concealed beneath the instrument panel
top cover.
The VTSS indicator cannot be adjusted or repaired
the entire automatic headlamp light sensor/VTSS
indicator must be replaced. (Refer to 8 - ELECTRI-
CAL/LAMPS/LIGHTING - EXTERIOR/AUTO HEAD-
LAMP SENSOR - REMOVAL).
Fig. 10 Sentry Key Immobilizer Transponder
1 - MOLDED CAP
2 - TRANSPONDER CHIP
3 - MOLDED CAP REMOVED
4 - TRANSPONDER KEY
WJVEHICLE THEFT SECURITY 8Q - 15
SKIS INDICATOR LAMP (Continued)