Ignition system JEEP GRAND CHEROKEE 2003 WJ / 2.G Workshop Manual
[x] Cancel search | Manufacturer: JEEP, Model Year: 2003, Model line: GRAND CHEROKEE, Model: JEEP GRAND CHEROKEE 2003 WJ / 2.GPages: 2199, PDF Size: 76.01 MB
Page 509 of 2199
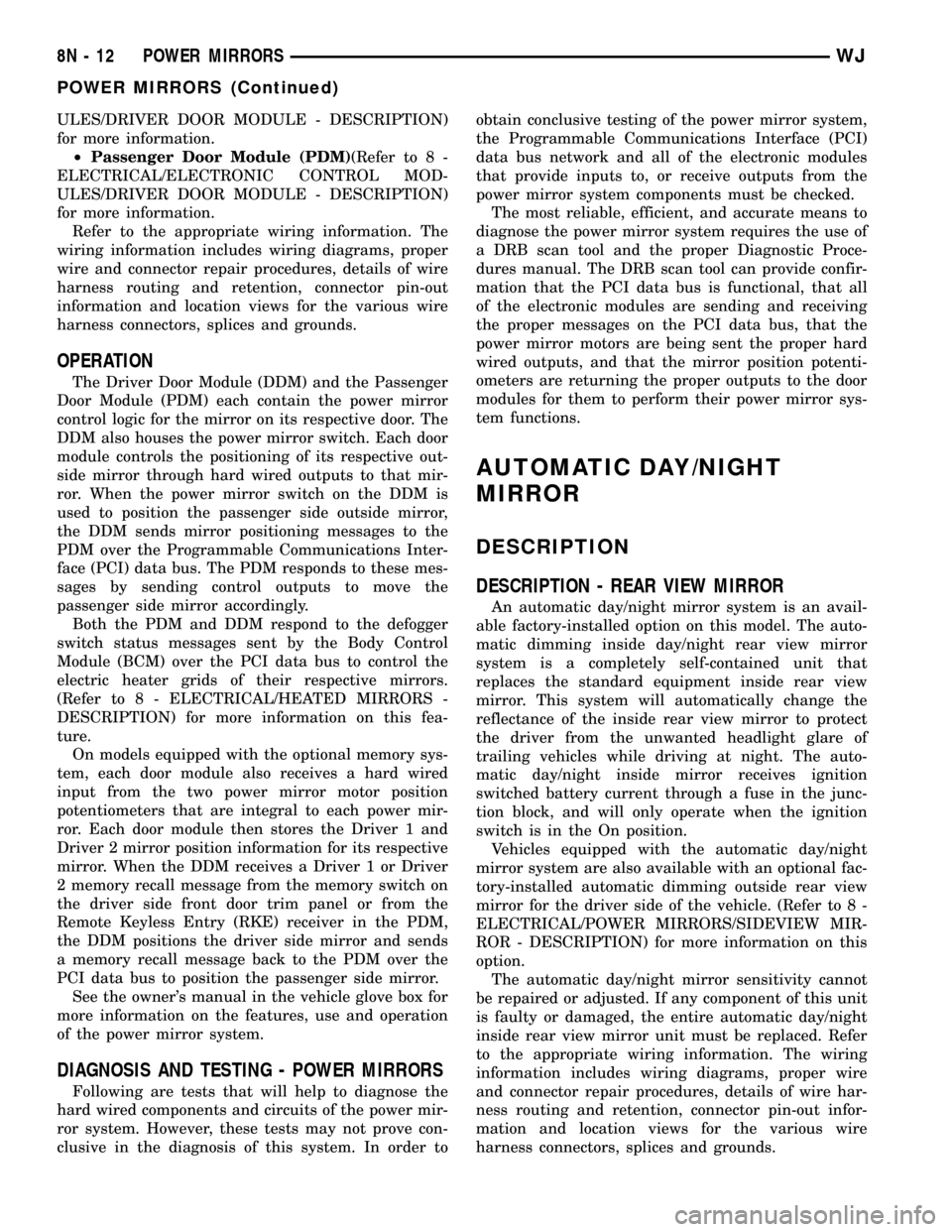
ULES/DRIVER DOOR MODULE - DESCRIPTION)
for more information.
²Passenger Door Module (PDM)(Refer to 8 -
ELECTRICAL/ELECTRONIC CONTROL MOD-
ULES/DRIVER DOOR MODULE - DESCRIPTION)
for more information.
Refer to the appropriate wiring information. The
wiring information includes wiring diagrams, proper
wire and connector repair procedures, details of wire
harness routing and retention, connector pin-out
information and location views for the various wire
harness connectors, splices and grounds.
OPERATION
The Driver Door Module (DDM) and the Passenger
Door Module (PDM) each contain the power mirror
control logic for the mirror on its respective door. The
DDM also houses the power mirror switch. Each door
module controls the positioning of its respective out-
side mirror through hard wired outputs to that mir-
ror. When the power mirror switch on the DDM is
used to position the passenger side outside mirror,
the DDM sends mirror positioning messages to the
PDM over the Programmable Communications Inter-
face (PCI) data bus. The PDM responds to these mes-
sages by sending control outputs to move the
passenger side mirror accordingly.
Both the PDM and DDM respond to the defogger
switch status messages sent by the Body Control
Module (BCM) over the PCI data bus to control the
electric heater grids of their respective mirrors.
(Refer to 8 - ELECTRICAL/HEATED MIRRORS -
DESCRIPTION) for more information on this fea-
ture.
On models equipped with the optional memory sys-
tem, each door module also receives a hard wired
input from the two power mirror motor position
potentiometers that are integral to each power mir-
ror. Each door module then stores the Driver 1 and
Driver 2 mirror position information for its respective
mirror. When the DDM receives a Driver 1 or Driver
2 memory recall message from the memory switch on
the driver side front door trim panel or from the
Remote Keyless Entry (RKE) receiver in the PDM,
the DDM positions the driver side mirror and sends
a memory recall message back to the PDM over the
PCI data bus to position the passenger side mirror.
See the owner's manual in the vehicle glove box for
more information on the features, use and operation
of the power mirror system.
DIAGNOSIS AND TESTING - POWER MIRRORS
Following are tests that will help to diagnose the
hard wired components and circuits of the power mir-
ror system. However, these tests may not prove con-
clusive in the diagnosis of this system. In order toobtain conclusive testing of the power mirror system,
the Programmable Communications Interface (PCI)
data bus network and all of the electronic modules
that provide inputs to, or receive outputs from the
power mirror system components must be checked.
The most reliable, efficient, and accurate means to
diagnose the power mirror system requires the use of
a DRB scan tool and the proper Diagnostic Proce-
dures manual. The DRB scan tool can provide confir-
mation that the PCI data bus is functional, that all
of the electronic modules are sending and receiving
the proper messages on the PCI data bus, that the
power mirror motors are being sent the proper hard
wired outputs, and that the mirror position potenti-
ometers are returning the proper outputs to the door
modules for them to perform their power mirror sys-
tem functions.
AUTOMATIC DAY/NIGHT
MIRROR
DESCRIPTION
DESCRIPTION - REAR VIEW MIRROR
An automatic day/night mirror system is an avail-
able factory-installed option on this model. The auto-
matic dimming inside day/night rear view mirror
system is a completely self-contained unit that
replaces the standard equipment inside rear view
mirror. This system will automatically change the
reflectance of the inside rear view mirror to protect
the driver from the unwanted headlight glare of
trailing vehicles while driving at night. The auto-
matic day/night inside mirror receives ignition
switched battery current through a fuse in the junc-
tion block, and will only operate when the ignition
switch is in the On position.
Vehicles equipped with the automatic day/night
mirror system are also available with an optional fac-
tory-installed automatic dimming outside rear view
mirror for the driver side of the vehicle. (Refer to 8 -
ELECTRICAL/POWER MIRRORS/SIDEVIEW MIR-
ROR - DESCRIPTION) for more information on this
option.
The automatic day/night mirror sensitivity cannot
be repaired or adjusted. If any component of this unit
is faulty or damaged, the entire automatic day/night
inside rear view mirror unit must be replaced. Refer
to the appropriate wiring information. The wiring
information includes wiring diagrams, proper wire
and connector repair procedures, details of wire har-
ness routing and retention, connector pin-out infor-
mation and location views for the various wire
harness connectors, splices and grounds.
8N - 12 POWER MIRRORSWJ
POWER MIRRORS (Continued)
Page 510 of 2199
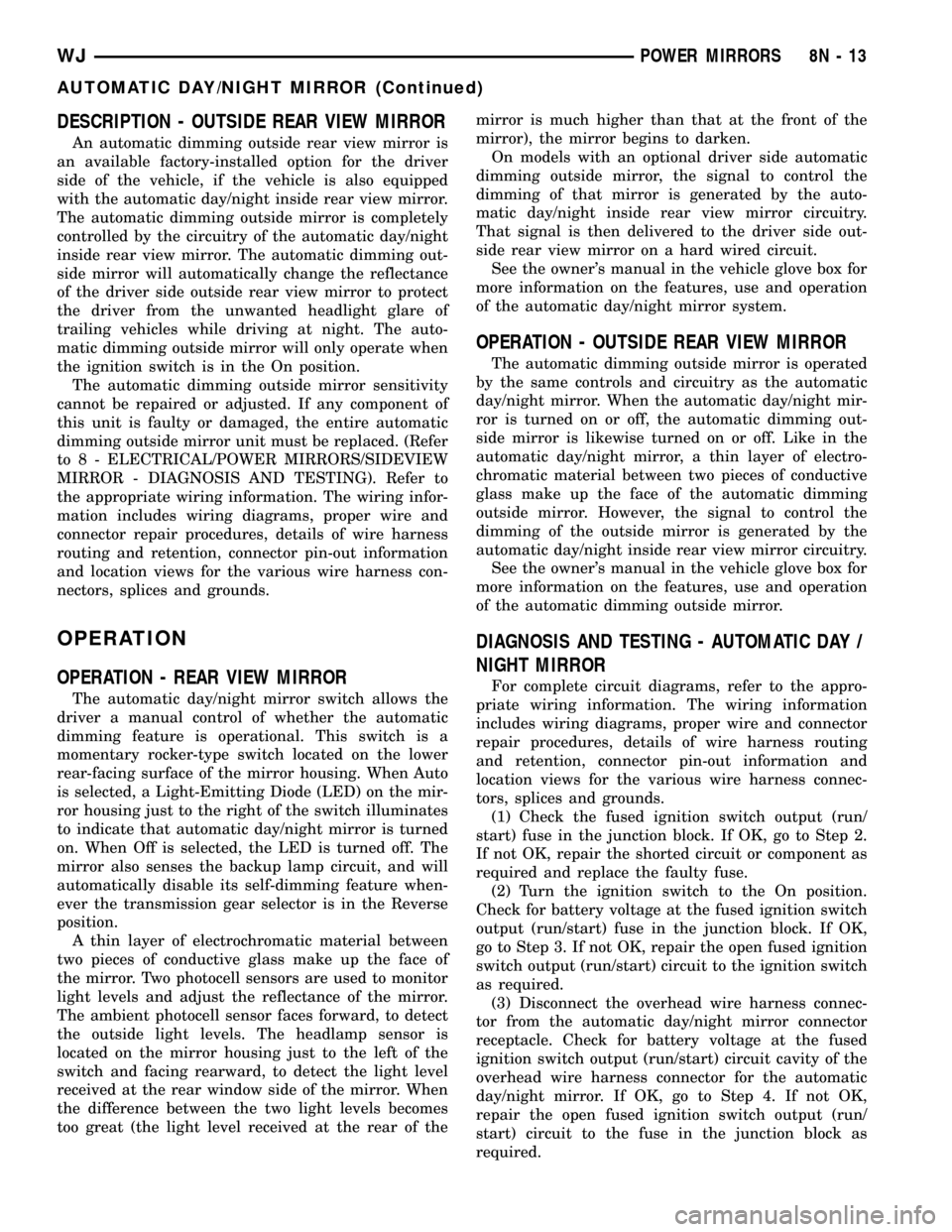
DESCRIPTION - OUTSIDE REAR VIEW MIRROR
An automatic dimming outside rear view mirror is
an available factory-installed option for the driver
side of the vehicle, if the vehicle is also equipped
with the automatic day/night inside rear view mirror.
The automatic dimming outside mirror is completely
controlled by the circuitry of the automatic day/night
inside rear view mirror. The automatic dimming out-
side mirror will automatically change the reflectance
of the driver side outside rear view mirror to protect
the driver from the unwanted headlight glare of
trailing vehicles while driving at night. The auto-
matic dimming outside mirror will only operate when
the ignition switch is in the On position.
The automatic dimming outside mirror sensitivity
cannot be repaired or adjusted. If any component of
this unit is faulty or damaged, the entire automatic
dimming outside mirror unit must be replaced. (Refer
to 8 - ELECTRICAL/POWER MIRRORS/SIDEVIEW
MIRROR - DIAGNOSIS AND TESTING). Refer to
the appropriate wiring information. The wiring infor-
mation includes wiring diagrams, proper wire and
connector repair procedures, details of wire harness
routing and retention, connector pin-out information
and location views for the various wire harness con-
nectors, splices and grounds.
OPERATION
OPERATION - REAR VIEW MIRROR
The automatic day/night mirror switch allows the
driver a manual control of whether the automatic
dimming feature is operational. This switch is a
momentary rocker-type switch located on the lower
rear-facing surface of the mirror housing. When Auto
is selected, a Light-Emitting Diode (LED) on the mir-
ror housing just to the right of the switch illuminates
to indicate that automatic day/night mirror is turned
on. When Off is selected, the LED is turned off. The
mirror also senses the backup lamp circuit, and will
automatically disable its self-dimming feature when-
ever the transmission gear selector is in the Reverse
position.
A thin layer of electrochromatic material between
two pieces of conductive glass make up the face of
the mirror. Two photocell sensors are used to monitor
light levels and adjust the reflectance of the mirror.
The ambient photocell sensor faces forward, to detect
the outside light levels. The headlamp sensor is
located on the mirror housing just to the left of the
switch and facing rearward, to detect the light level
received at the rear window side of the mirror. When
the difference between the two light levels becomes
too great (the light level received at the rear of themirror is much higher than that at the front of the
mirror), the mirror begins to darken.
On models with an optional driver side automatic
dimming outside mirror, the signal to control the
dimming of that mirror is generated by the auto-
matic day/night inside rear view mirror circuitry.
That signal is then delivered to the driver side out-
side rear view mirror on a hard wired circuit.
See the owner's manual in the vehicle glove box for
more information on the features, use and operation
of the automatic day/night mirror system.
OPERATION - OUTSIDE REAR VIEW MIRROR
The automatic dimming outside mirror is operated
by the same controls and circuitry as the automatic
day/night mirror. When the automatic day/night mir-
ror is turned on or off, the automatic dimming out-
side mirror is likewise turned on or off. Like in the
automatic day/night mirror, a thin layer of electro-
chromatic material between two pieces of conductive
glass make up the face of the automatic dimming
outside mirror. However, the signal to control the
dimming of the outside mirror is generated by the
automatic day/night inside rear view mirror circuitry.
See the owner's manual in the vehicle glove box for
more information on the features, use and operation
of the automatic dimming outside mirror.
DIAGNOSIS AND TESTING - AUTOMATIC DAY /
NIGHT MIRROR
For complete circuit diagrams, refer to the appro-
priate wiring information. The wiring information
includes wiring diagrams, proper wire and connector
repair procedures, details of wire harness routing
and retention, connector pin-out information and
location views for the various wire harness connec-
tors, splices and grounds.
(1) Check the fused ignition switch output (run/
start) fuse in the junction block. If OK, go to Step 2.
If not OK, repair the shorted circuit or component as
required and replace the faulty fuse.
(2) Turn the ignition switch to the On position.
Check for battery voltage at the fused ignition switch
output (run/start) fuse in the junction block. If OK,
go to Step 3. If not OK, repair the open fused ignition
switch output (run/start) circuit to the ignition switch
as required.
(3) Disconnect the overhead wire harness connec-
tor from the automatic day/night mirror connector
receptacle. Check for battery voltage at the fused
ignition switch output (run/start) circuit cavity of the
overhead wire harness connector for the automatic
day/night mirror. If OK, go to Step 4. If not OK,
repair the open fused ignition switch output (run/
start) circuit to the fuse in the junction block as
required.
WJPOWER MIRRORS 8N - 13
AUTOMATIC DAY/NIGHT MIRROR (Continued)
Page 511 of 2199
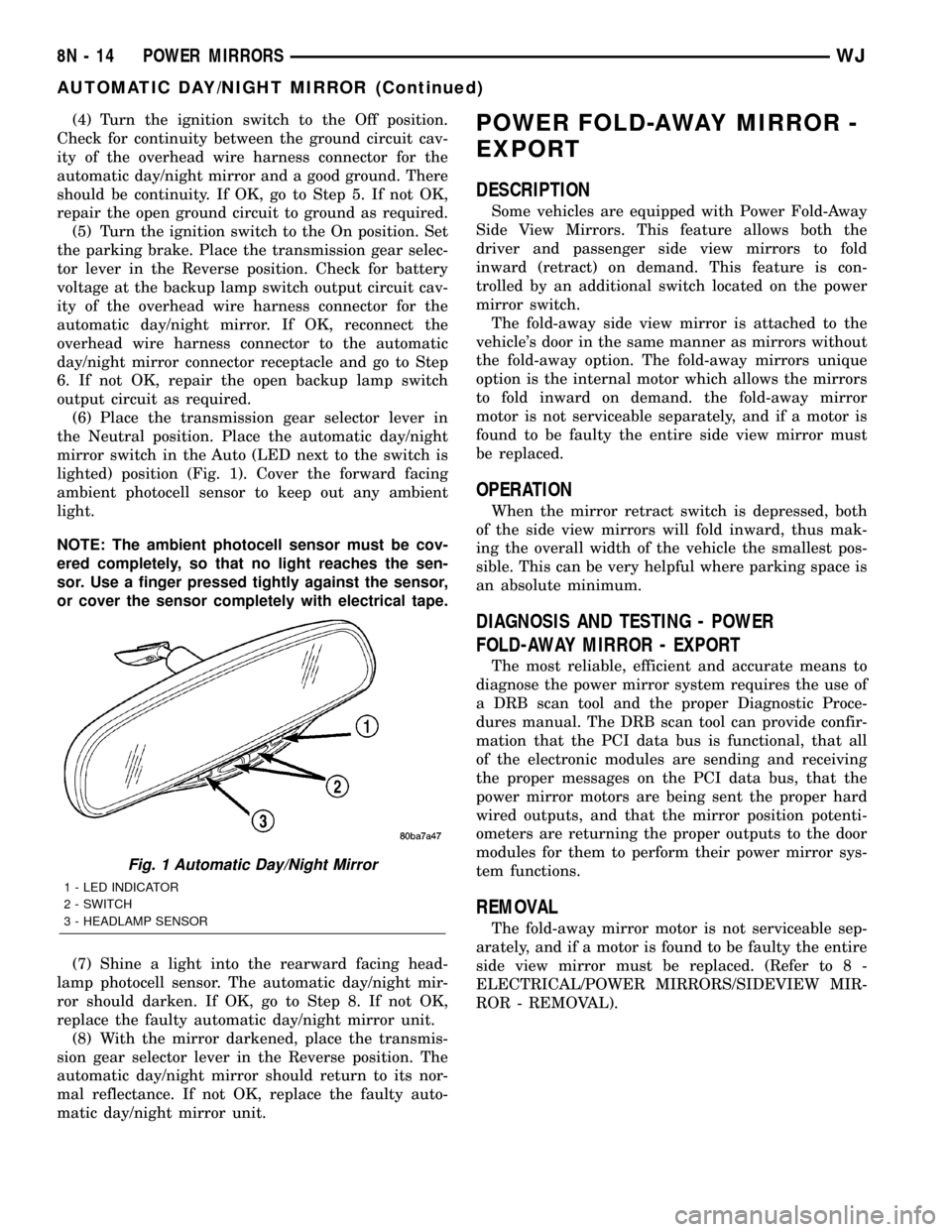
(4) Turn the ignition switch to the Off position.
Check for continuity between the ground circuit cav-
ity of the overhead wire harness connector for the
automatic day/night mirror and a good ground. There
should be continuity. If OK, go to Step 5. If not OK,
repair the open ground circuit to ground as required.
(5) Turn the ignition switch to the On position. Set
the parking brake. Place the transmission gear selec-
tor lever in the Reverse position. Check for battery
voltage at the backup lamp switch output circuit cav-
ity of the overhead wire harness connector for the
automatic day/night mirror. If OK, reconnect the
overhead wire harness connector to the automatic
day/night mirror connector receptacle and go to Step
6. If not OK, repair the open backup lamp switch
output circuit as required.
(6) Place the transmission gear selector lever in
the Neutral position. Place the automatic day/night
mirror switch in the Auto (LED next to the switch is
lighted) position (Fig. 1). Cover the forward facing
ambient photocell sensor to keep out any ambient
light.
NOTE: The ambient photocell sensor must be cov-
ered completely, so that no light reaches the sen-
sor. Use a finger pressed tightly against the sensor,
or cover the sensor completely with electrical tape.
(7) Shine a light into the rearward facing head-
lamp photocell sensor. The automatic day/night mir-
ror should darken. If OK, go to Step 8. If not OK,
replace the faulty automatic day/night mirror unit.
(8) With the mirror darkened, place the transmis-
sion gear selector lever in the Reverse position. The
automatic day/night mirror should return to its nor-
mal reflectance. If not OK, replace the faulty auto-
matic day/night mirror unit.POWER FOLD-AWAY MIRROR -
EXPORT
DESCRIPTION
Some vehicles are equipped with Power Fold-Away
Side View Mirrors. This feature allows both the
driver and passenger side view mirrors to fold
inward (retract) on demand. This feature is con-
trolled by an additional switch located on the power
mirror switch.
The fold-away side view mirror is attached to the
vehicle's door in the same manner as mirrors without
the fold-away option. The fold-away mirrors unique
option is the internal motor which allows the mirrors
to fold inward on demand. the fold-away mirror
motor is not serviceable separately, and if a motor is
found to be faulty the entire side view mirror must
be replaced.
OPERATION
When the mirror retract switch is depressed, both
of the side view mirrors will fold inward, thus mak-
ing the overall width of the vehicle the smallest pos-
sible. This can be very helpful where parking space is
an absolute minimum.
DIAGNOSIS AND TESTING - POWER
FOLD-AWAY MIRROR - EXPORT
The most reliable, efficient and accurate means to
diagnose the power mirror system requires the use of
a DRB scan tool and the proper Diagnostic Proce-
dures manual. The DRB scan tool can provide confir-
mation that the PCI data bus is functional, that all
of the electronic modules are sending and receiving
the proper messages on the PCI data bus, that the
power mirror motors are being sent the proper hard
wired outputs, and that the mirror position potenti-
ometers are returning the proper outputs to the door
modules for them to perform their power mirror sys-
tem functions.
REMOVAL
The fold-away mirror motor is not serviceable sep-
arately, and if a motor is found to be faulty the entire
side view mirror must be replaced. (Refer to 8 -
ELECTRICAL/POWER MIRRORS/SIDEVIEW MIR-
ROR - REMOVAL).
Fig. 1 Automatic Day/Night Mirror
1 - LED INDICATOR
2 - SWITCH
3 - HEADLAMP SENSOR
8N - 14 POWER MIRRORSWJ
AUTOMATIC DAY/NIGHT MIRROR (Continued)
Page 515 of 2199
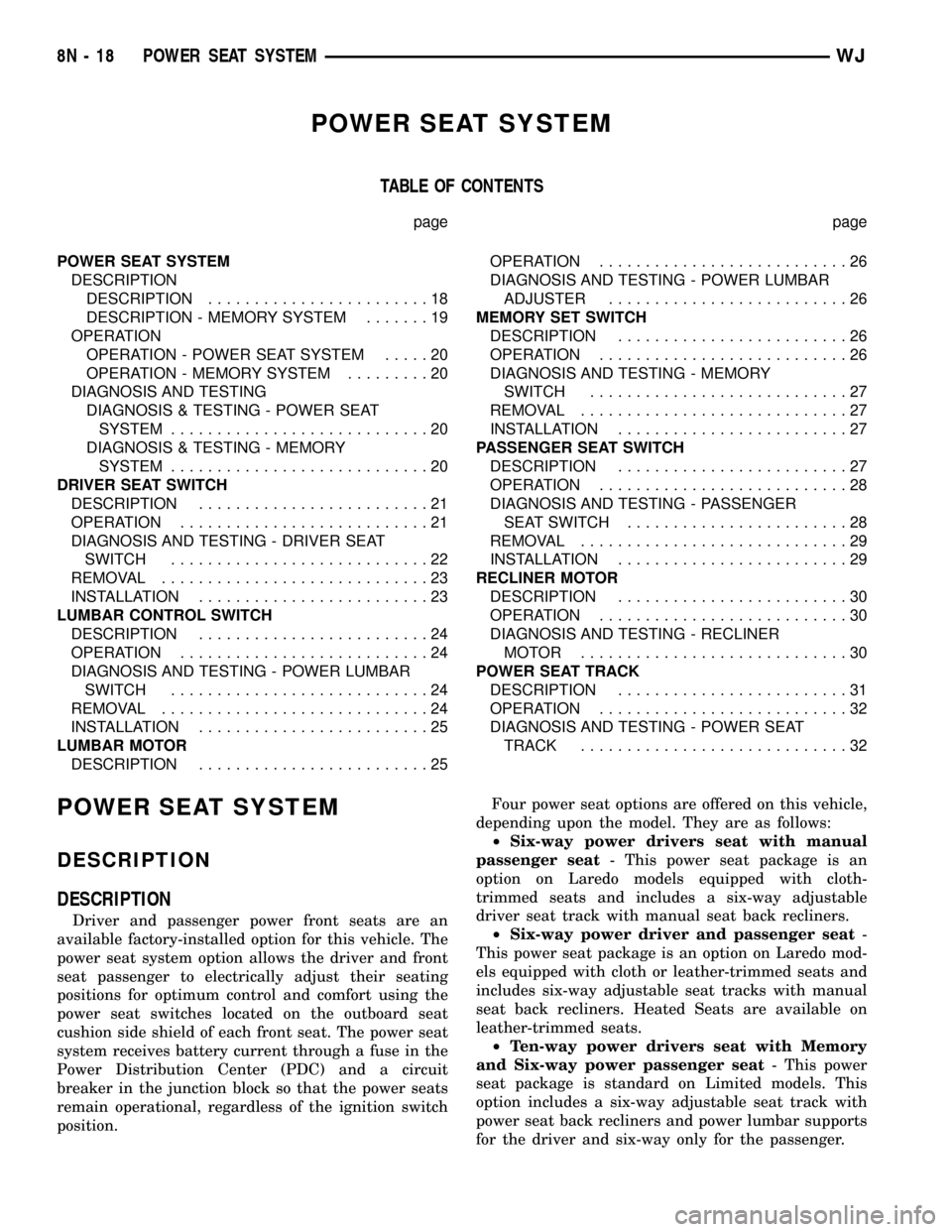
POWER SEAT SYSTEM
TABLE OF CONTENTS
page page
POWER SEAT SYSTEM
DESCRIPTION
DESCRIPTION........................18
DESCRIPTION - MEMORY SYSTEM.......19
OPERATION
OPERATION - POWER SEAT SYSTEM.....20
OPERATION - MEMORY SYSTEM.........20
DIAGNOSIS AND TESTING
DIAGNOSIS & TESTING - POWER SEAT
SYSTEM............................20
DIAGNOSIS & TESTING - MEMORY
SYSTEM............................20
DRIVER SEAT SWITCH
DESCRIPTION.........................21
OPERATION...........................21
DIAGNOSIS AND TESTING - DRIVER SEAT
SWITCH............................22
REMOVAL.............................23
INSTALLATION.........................23
LUMBAR CONTROL SWITCH
DESCRIPTION.........................24
OPERATION...........................24
DIAGNOSIS AND TESTING - POWER LUMBAR
SWITCH............................24
REMOVAL.............................24
INSTALLATION.........................25
LUMBAR MOTOR
DESCRIPTION.........................25OPERATION...........................26
DIAGNOSIS AND TESTING - POWER LUMBAR
ADJUSTER..........................26
MEMORY SET SWITCH
DESCRIPTION.........................26
OPERATION...........................26
DIAGNOSIS AND TESTING - MEMORY
SWITCH............................27
REMOVAL.............................27
INSTALLATION.........................27
PASSENGER SEAT SWITCH
DESCRIPTION.........................27
OPERATION...........................28
DIAGNOSIS AND TESTING - PASSENGER
SEAT SWITCH........................28
REMOVAL.............................29
INSTALLATION.........................29
RECLINER MOTOR
DESCRIPTION.........................30
OPERATION...........................30
DIAGNOSIS AND TESTING - RECLINER
MOTOR .............................30
POWER SEAT TRACK
DESCRIPTION.........................31
OPERATION...........................32
DIAGNOSIS AND TESTING - POWER SEAT
TRACK.............................32
POWER SEAT SYSTEM
DESCRIPTION
DESCRIPTION
Driver and passenger power front seats are an
available factory-installed option for this vehicle. The
power seat system option allows the driver and front
seat passenger to electrically adjust their seating
positions for optimum control and comfort using the
power seat switches located on the outboard seat
cushion side shield of each front seat. The power seat
system receives battery current through a fuse in the
Power Distribution Center (PDC) and a circuit
breaker in the junction block so that the power seats
remain operational, regardless of the ignition switch
position.Four power seat options are offered on this vehicle,
depending upon the model. They are as follows:
²Six-way power drivers seat with manual
passenger seat- This power seat package is an
option on Laredo models equipped with cloth-
trimmed seats and includes a six-way adjustable
driver seat track with manual seat back recliners.
²Six-way power driver and passenger seat-
This power seat package is an option on Laredo mod-
els equipped with cloth or leather-trimmed seats and
includes six-way adjustable seat tracks with manual
seat back recliners. Heated Seats are available on
leather-trimmed seats.
²Ten-way power drivers seat with Memory
and Six-way power passenger seat- This power
seat package is standard on Limited models. This
option includes a six-way adjustable seat track with
power seat back recliners and power lumbar supports
for the driver and six-way only for the passenger.
8N - 18 POWER SEAT SYSTEMWJ
Page 516 of 2199
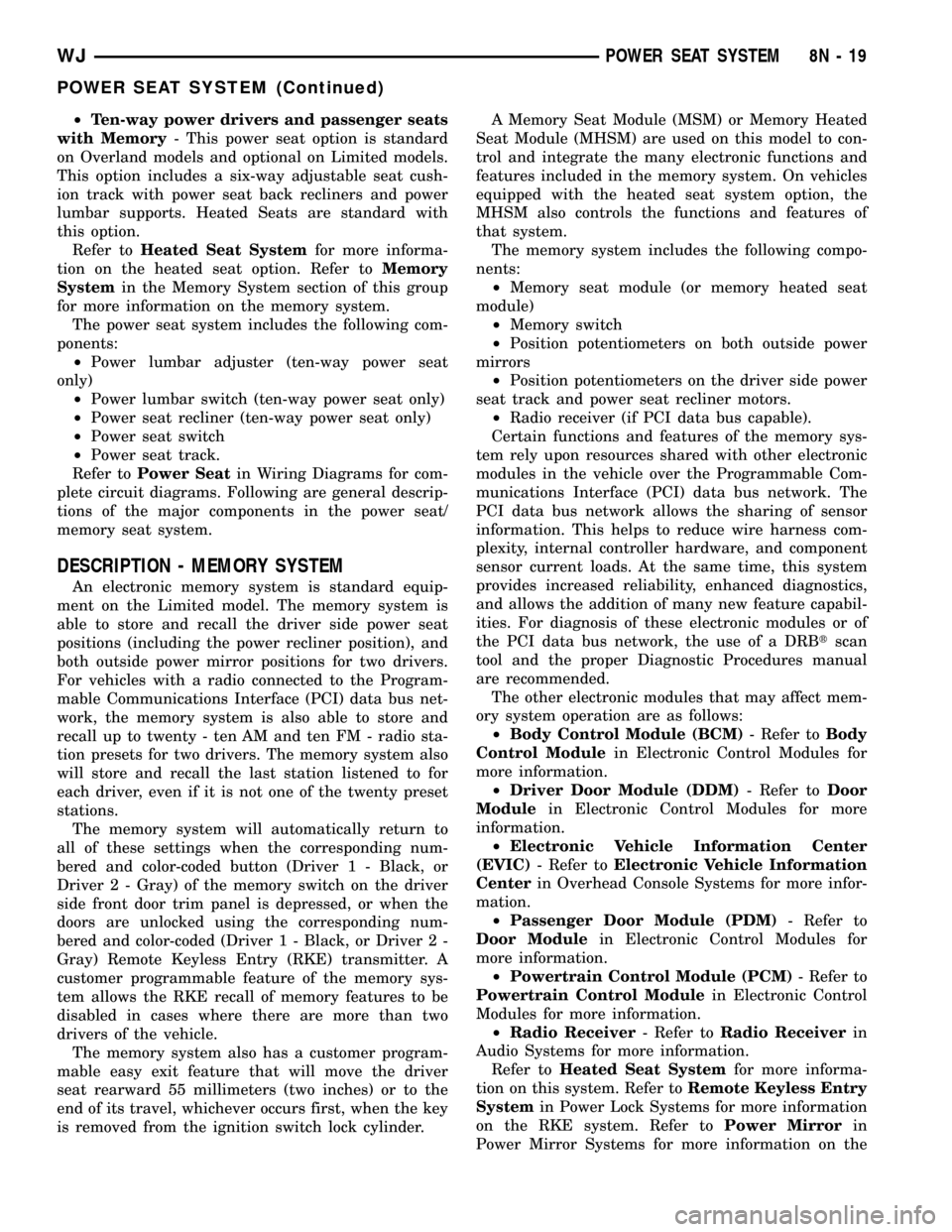
²Ten-way power drivers and passenger seats
with Memory- This power seat option is standard
on Overland models and optional on Limited models.
This option includes a six-way adjustable seat cush-
ion track with power seat back recliners and power
lumbar supports. Heated Seats are standard with
this option.
Refer toHeated Seat Systemfor more informa-
tion on the heated seat option. Refer toMemory
Systemin the Memory System section of this group
for more information on the memory system.
The power seat system includes the following com-
ponents:
²Power lumbar adjuster (ten-way power seat
only)
²Power lumbar switch (ten-way power seat only)
²Power seat recliner (ten-way power seat only)
²Power seat switch
²Power seat track.
Refer toPower Seatin Wiring Diagrams for com-
plete circuit diagrams. Following are general descrip-
tions of the major components in the power seat/
memory seat system.
DESCRIPTION - MEMORY SYSTEM
An electronic memory system is standard equip-
ment on the Limited model. The memory system is
able to store and recall the driver side power seat
positions (including the power recliner position), and
both outside power mirror positions for two drivers.
For vehicles with a radio connected to the Program-
mable Communications Interface (PCI) data bus net-
work, the memory system is also able to store and
recall up to twenty - ten AM and ten FM - radio sta-
tion presets for two drivers. The memory system also
will store and recall the last station listened to for
each driver, even if it is not one of the twenty preset
stations.
The memory system will automatically return to
all of these settings when the corresponding num-
bered and color-coded button (Driver 1 - Black, or
Driver 2 - Gray) of the memory switch on the driver
side front door trim panel is depressed, or when the
doors are unlocked using the corresponding num-
bered and color-coded (Driver 1 - Black, or Driver 2 -
Gray) Remote Keyless Entry (RKE) transmitter. A
customer programmable feature of the memory sys-
tem allows the RKE recall of memory features to be
disabled in cases where there are more than two
drivers of the vehicle.
The memory system also has a customer program-
mable easy exit feature that will move the driver
seat rearward 55 millimeters (two inches) or to the
end of its travel, whichever occurs first, when the key
is removed from the ignition switch lock cylinder.A Memory Seat Module (MSM) or Memory Heated
Seat Module (MHSM) are used on this model to con-
trol and integrate the many electronic functions and
features included in the memory system. On vehicles
equipped with the heated seat system option, the
MHSM also controls the functions and features of
that system.
The memory system includes the following compo-
nents:
²Memory seat module (or memory heated seat
module)
²Memory switch
²Position potentiometers on both outside power
mirrors
²Position potentiometers on the driver side power
seat track and power seat recliner motors.
²Radio receiver (if PCI data bus capable).
Certain functions and features of the memory sys-
tem rely upon resources shared with other electronic
modules in the vehicle over the Programmable Com-
munications Interface (PCI) data bus network. The
PCI data bus network allows the sharing of sensor
information. This helps to reduce wire harness com-
plexity, internal controller hardware, and component
sensor current loads. At the same time, this system
provides increased reliability, enhanced diagnostics,
and allows the addition of many new feature capabil-
ities. For diagnosis of these electronic modules or of
the PCI data bus network, the use of a DRBtscan
tool and the proper Diagnostic Procedures manual
are recommended.
The other electronic modules that may affect mem-
ory system operation are as follows:
²Body Control Module (BCM)- Refer toBody
Control Modulein Electronic Control Modules for
more information.
²Driver Door Module (DDM)- Refer toDoor
Modulein Electronic Control Modules for more
information.
²Electronic Vehicle Information Center
(EVIC)- Refer toElectronic Vehicle Information
Centerin Overhead Console Systems for more infor-
mation.
²Passenger Door Module (PDM)- Refer to
Door Modulein Electronic Control Modules for
more information.
²Powertrain Control Module (PCM)- Refer to
Powertrain Control Modulein Electronic Control
Modules for more information.
²Radio Receiver- Refer toRadio Receiverin
Audio Systems for more information.
Refer toHeated Seat Systemfor more informa-
tion on this system. Refer toRemote Keyless Entry
Systemin Power Lock Systems for more information
on the RKE system. Refer toPower Mirrorin
Power Mirror Systems for more information on the
WJPOWER SEAT SYSTEM 8N - 19
POWER SEAT SYSTEM (Continued)
Page 530 of 2199
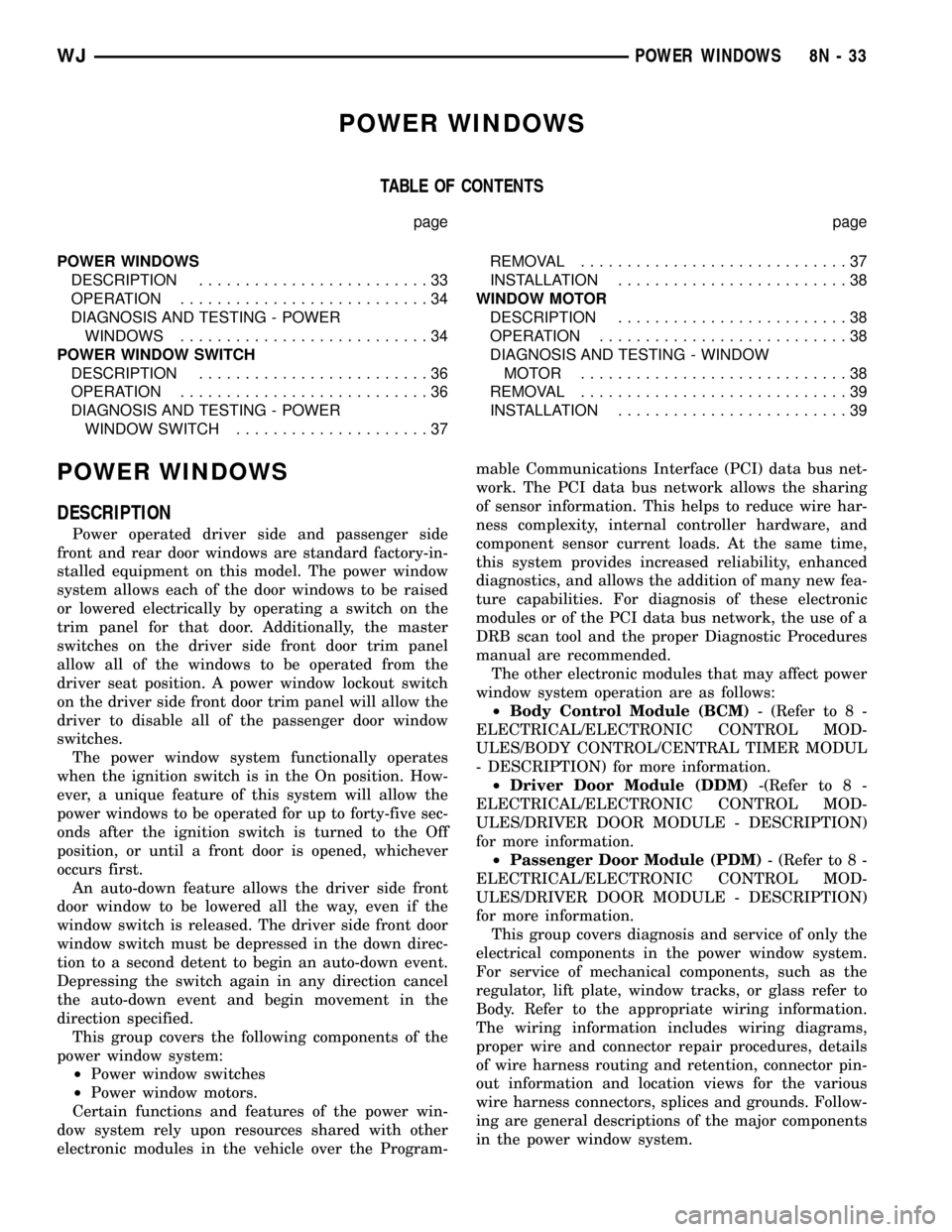
POWER WINDOWS
TABLE OF CONTENTS
page page
POWER WINDOWS
DESCRIPTION.........................33
OPERATION...........................34
DIAGNOSIS AND TESTING - POWER
WINDOWS...........................34
POWER WINDOW SWITCH
DESCRIPTION.........................36
OPERATION...........................36
DIAGNOSIS AND TESTING - POWER
WINDOW SWITCH.....................37REMOVAL.............................37
INSTALLATION.........................38
WINDOW MOTOR
DESCRIPTION.........................38
OPERATION...........................38
DIAGNOSIS AND TESTING - WINDOW
MOTOR .............................38
REMOVAL.............................39
INSTALLATION.........................39
POWER WINDOWS
DESCRIPTION
Power operated driver side and passenger side
front and rear door windows are standard factory-in-
stalled equipment on this model. The power window
system allows each of the door windows to be raised
or lowered electrically by operating a switch on the
trim panel for that door. Additionally, the master
switches on the driver side front door trim panel
allow all of the windows to be operated from the
driver seat position. A power window lockout switch
on the driver side front door trim panel will allow the
driver to disable all of the passenger door window
switches.
The power window system functionally operates
when the ignition switch is in the On position. How-
ever, a unique feature of this system will allow the
power windows to be operated for up to forty-five sec-
onds after the ignition switch is turned to the Off
position, or until a front door is opened, whichever
occurs first.
An auto-down feature allows the driver side front
door window to be lowered all the way, even if the
window switch is released. The driver side front door
window switch must be depressed in the down direc-
tion to a second detent to begin an auto-down event.
Depressing the switch again in any direction cancel
the auto-down event and begin movement in the
direction specified.
This group covers the following components of the
power window system:
²Power window switches
²Power window motors.
Certain functions and features of the power win-
dow system rely upon resources shared with other
electronic modules in the vehicle over the Program-mable Communications Interface (PCI) data bus net-
work. The PCI data bus network allows the sharing
of sensor information. This helps to reduce wire har-
ness complexity, internal controller hardware, and
component sensor current loads. At the same time,
this system provides increased reliability, enhanced
diagnostics, and allows the addition of many new fea-
ture capabilities. For diagnosis of these electronic
modules or of the PCI data bus network, the use of a
DRB scan tool and the proper Diagnostic Procedures
manual are recommended.
The other electronic modules that may affect power
window system operation are as follows:
²Body Control Module (BCM)- (Refer to 8 -
ELECTRICAL/ELECTRONIC CONTROL MOD-
ULES/BODY CONTROL/CENTRAL TIMER MODUL
- DESCRIPTION) for more information.
²Driver Door Module (DDM)-(Refer to 8 -
ELECTRICAL/ELECTRONIC CONTROL MOD-
ULES/DRIVER DOOR MODULE - DESCRIPTION)
for more information.
²Passenger Door Module (PDM)- (Refer to 8 -
ELECTRICAL/ELECTRONIC CONTROL MOD-
ULES/DRIVER DOOR MODULE - DESCRIPTION)
for more information.
This group covers diagnosis and service of only the
electrical components in the power window system.
For service of mechanical components, such as the
regulator, lift plate, window tracks, or glass refer to
Body. Refer to the appropriate wiring information.
The wiring information includes wiring diagrams,
proper wire and connector repair procedures, details
of wire harness routing and retention, connector pin-
out information and location views for the various
wire harness connectors, splices and grounds. Follow-
ing are general descriptions of the major components
in the power window system.
WJPOWER WINDOWS 8N - 33
Page 531 of 2199
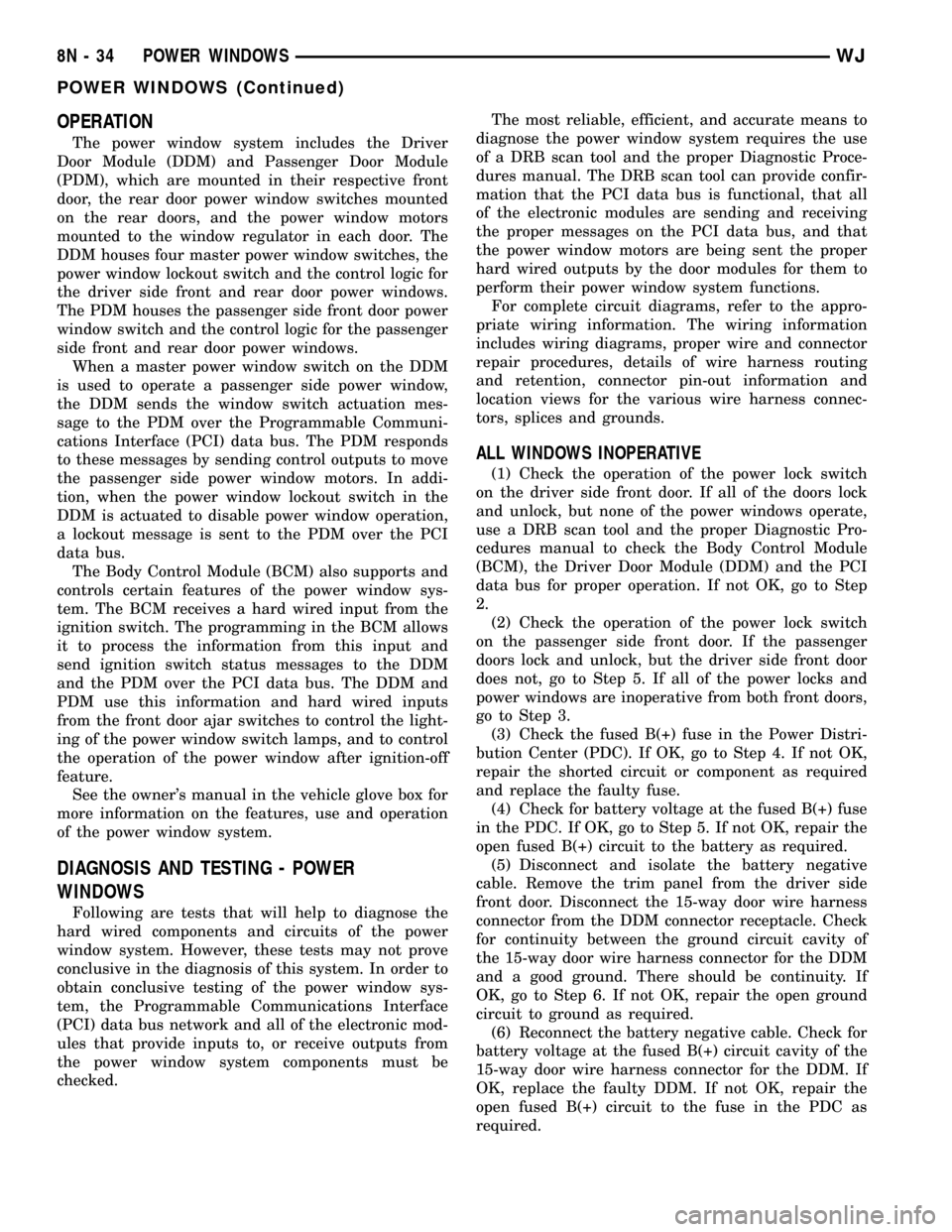
OPERATION
The power window system includes the Driver
Door Module (DDM) and Passenger Door Module
(PDM), which are mounted in their respective front
door, the rear door power window switches mounted
on the rear doors, and the power window motors
mounted to the window regulator in each door. The
DDM houses four master power window switches, the
power window lockout switch and the control logic for
the driver side front and rear door power windows.
The PDM houses the passenger side front door power
window switch and the control logic for the passenger
side front and rear door power windows.
When a master power window switch on the DDM
is used to operate a passenger side power window,
the DDM sends the window switch actuation mes-
sage to the PDM over the Programmable Communi-
cations Interface (PCI) data bus. The PDM responds
to these messages by sending control outputs to move
the passenger side power window motors. In addi-
tion, when the power window lockout switch in the
DDM is actuated to disable power window operation,
a lockout message is sent to the PDM over the PCI
data bus.
The Body Control Module (BCM) also supports and
controls certain features of the power window sys-
tem. The BCM receives a hard wired input from the
ignition switch. The programming in the BCM allows
it to process the information from this input and
send ignition switch status messages to the DDM
and the PDM over the PCI data bus. The DDM and
PDM use this information and hard wired inputs
from the front door ajar switches to control the light-
ing of the power window switch lamps, and to control
the operation of the power window after ignition-off
feature.
See the owner's manual in the vehicle glove box for
more information on the features, use and operation
of the power window system.
DIAGNOSIS AND TESTING - POWER
WINDOWS
Following are tests that will help to diagnose the
hard wired components and circuits of the power
window system. However, these tests may not prove
conclusive in the diagnosis of this system. In order to
obtain conclusive testing of the power window sys-
tem, the Programmable Communications Interface
(PCI) data bus network and all of the electronic mod-
ules that provide inputs to, or receive outputs from
the power window system components must be
checked.The most reliable, efficient, and accurate means to
diagnose the power window system requires the use
of a DRB scan tool and the proper Diagnostic Proce-
dures manual. The DRB scan tool can provide confir-
mation that the PCI data bus is functional, that all
of the electronic modules are sending and receiving
the proper messages on the PCI data bus, and that
the power window motors are being sent the proper
hard wired outputs by the door modules for them to
perform their power window system functions.
For complete circuit diagrams, refer to the appro-
priate wiring information. The wiring information
includes wiring diagrams, proper wire and connector
repair procedures, details of wire harness routing
and retention, connector pin-out information and
location views for the various wire harness connec-
tors, splices and grounds.
ALL WINDOWS INOPERATIVE
(1) Check the operation of the power lock switch
on the driver side front door. If all of the doors lock
and unlock, but none of the power windows operate,
use a DRB scan tool and the proper Diagnostic Pro-
cedures manual to check the Body Control Module
(BCM), the Driver Door Module (DDM) and the PCI
data bus for proper operation. If not OK, go to Step
2.
(2) Check the operation of the power lock switch
on the passenger side front door. If the passenger
doors lock and unlock, but the driver side front door
does not, go to Step 5. If all of the power locks and
power windows are inoperative from both front doors,
go to Step 3.
(3) Check the fused B(+) fuse in the Power Distri-
bution Center (PDC). If OK, go to Step 4. If not OK,
repair the shorted circuit or component as required
and replace the faulty fuse.
(4) Check for battery voltage at the fused B(+) fuse
in the PDC. If OK, go to Step 5. If not OK, repair the
open fused B(+) circuit to the battery as required.
(5) Disconnect and isolate the battery negative
cable. Remove the trim panel from the driver side
front door. Disconnect the 15-way door wire harness
connector from the DDM connector receptacle. Check
for continuity between the ground circuit cavity of
the 15-way door wire harness connector for the DDM
and a good ground. There should be continuity. If
OK, go to Step 6. If not OK, repair the open ground
circuit to ground as required.
(6) Reconnect the battery negative cable. Check for
battery voltage at the fused B(+) circuit cavity of the
15-way door wire harness connector for the DDM. If
OK, replace the faulty DDM. If not OK, repair the
open fused B(+) circuit to the fuse in the PDC as
required.
8N - 34 POWER WINDOWSWJ
POWER WINDOWS (Continued)
Page 540 of 2199
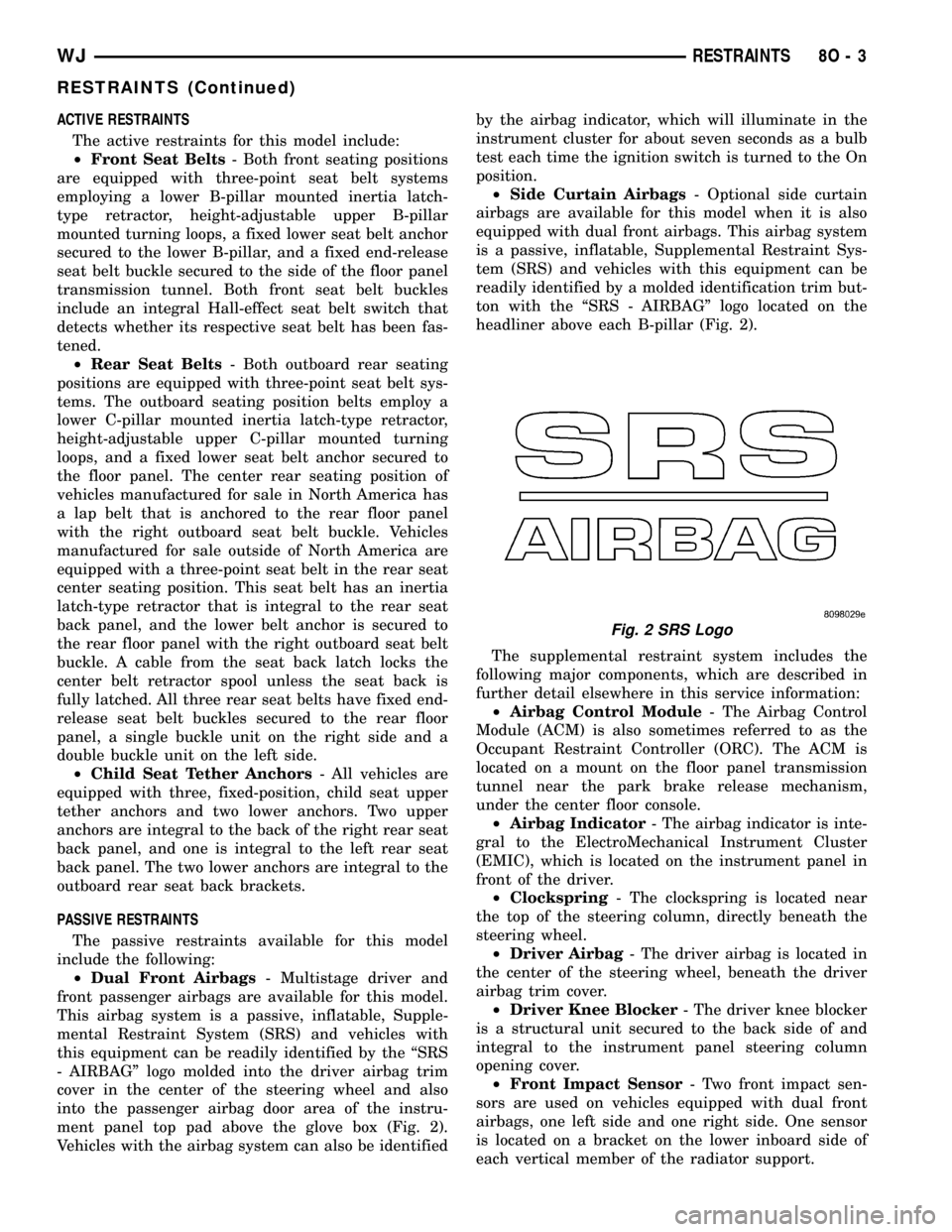
ACTIVE RESTRAINTS
The active restraints for this model include:
²Front Seat Belts- Both front seating positions
are equipped with three-point seat belt systems
employing a lower B-pillar mounted inertia latch-
type retractor, height-adjustable upper B-pillar
mounted turning loops, a fixed lower seat belt anchor
secured to the lower B-pillar, and a fixed end-release
seat belt buckle secured to the side of the floor panel
transmission tunnel. Both front seat belt buckles
include an integral Hall-effect seat belt switch that
detects whether its respective seat belt has been fas-
tened.
²Rear Seat Belts- Both outboard rear seating
positions are equipped with three-point seat belt sys-
tems. The outboard seating position belts employ a
lower C-pillar mounted inertia latch-type retractor,
height-adjustable upper C-pillar mounted turning
loops, and a fixed lower seat belt anchor secured to
the floor panel. The center rear seating position of
vehicles manufactured for sale in North America has
a lap belt that is anchored to the rear floor panel
with the right outboard seat belt buckle. Vehicles
manufactured for sale outside of North America are
equipped with a three-point seat belt in the rear seat
center seating position. This seat belt has an inertia
latch-type retractor that is integral to the rear seat
back panel, and the lower belt anchor is secured to
the rear floor panel with the right outboard seat belt
buckle. A cable from the seat back latch locks the
center belt retractor spool unless the seat back is
fully latched. All three rear seat belts have fixed end-
release seat belt buckles secured to the rear floor
panel, a single buckle unit on the right side and a
double buckle unit on the left side.
²Child Seat Tether Anchors- All vehicles are
equipped with three, fixed-position, child seat upper
tether anchors and two lower anchors. Two upper
anchors are integral to the back of the right rear seat
back panel, and one is integral to the left rear seat
back panel. The two lower anchors are integral to the
outboard rear seat back brackets.
PASSIVE RESTRAINTS
The passive restraints available for this model
include the following:
²Dual Front Airbags- Multistage driver and
front passenger airbags are available for this model.
This airbag system is a passive, inflatable, Supple-
mental Restraint System (SRS) and vehicles with
this equipment can be readily identified by the ªSRS
- AIRBAGº logo molded into the driver airbag trim
cover in the center of the steering wheel and also
into the passenger airbag door area of the instru-
ment panel top pad above the glove box (Fig. 2).
Vehicles with the airbag system can also be identifiedby the airbag indicator, which will illuminate in the
instrument cluster for about seven seconds as a bulb
test each time the ignition switch is turned to the On
position.
²Side Curtain Airbags- Optional side curtain
airbags are available for this model when it is also
equipped with dual front airbags. This airbag system
is a passive, inflatable, Supplemental Restraint Sys-
tem (SRS) and vehicles with this equipment can be
readily identified by a molded identification trim but-
ton with the ªSRS - AIRBAGº logo located on the
headliner above each B-pillar (Fig. 2).
The supplemental restraint system includes the
following major components, which are described in
further detail elsewhere in this service information:
²Airbag Control Module- The Airbag Control
Module (ACM) is also sometimes referred to as the
Occupant Restraint Controller (ORC). The ACM is
located on a mount on the floor panel transmission
tunnel near the park brake release mechanism,
under the center floor console.
²Airbag Indicator- The airbag indicator is inte-
gral to the ElectroMechanical Instrument Cluster
(EMIC), which is located on the instrument panel in
front of the driver.
²Clockspring- The clockspring is located near
the top of the steering column, directly beneath the
steering wheel.
²Driver Airbag- The driver airbag is located in
the center of the steering wheel, beneath the driver
airbag trim cover.
²Driver Knee Blocker- The driver knee blocker
is a structural unit secured to the back side of and
integral to the instrument panel steering column
opening cover.
²Front Impact Sensor- Two front impact sen-
sors are used on vehicles equipped with dual front
airbags, one left side and one right side. One sensor
is located on a bracket on the lower inboard side of
each vertical member of the radiator support.
Fig. 2 SRS Logo
WJRESTRAINTS 8O - 3
RESTRAINTS (Continued)
Page 541 of 2199
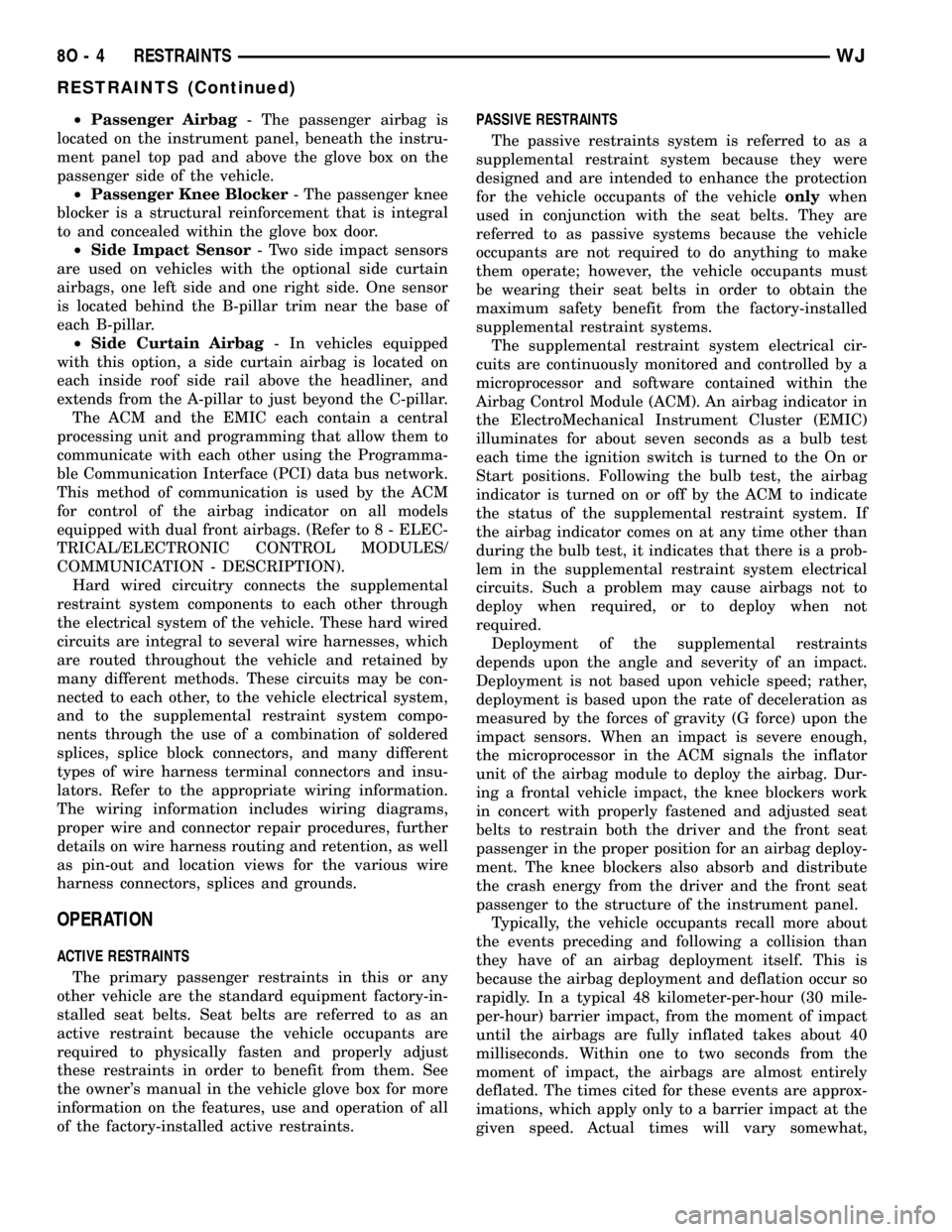
²Passenger Airbag- The passenger airbag is
located on the instrument panel, beneath the instru-
ment panel top pad and above the glove box on the
passenger side of the vehicle.
²Passenger Knee Blocker- The passenger knee
blocker is a structural reinforcement that is integral
to and concealed within the glove box door.
²Side Impact Sensor- Two side impact sensors
are used on vehicles with the optional side curtain
airbags, one left side and one right side. One sensor
is located behind the B-pillar trim near the base of
each B-pillar.
²Side Curtain Airbag- In vehicles equipped
with this option, a side curtain airbag is located on
each inside roof side rail above the headliner, and
extends from the A-pillar to just beyond the C-pillar.
The ACM and the EMIC each contain a central
processing unit and programming that allow them to
communicate with each other using the Programma-
ble Communication Interface (PCI) data bus network.
This method of communication is used by the ACM
for control of the airbag indicator on all models
equipped with dual front airbags. (Refer to 8 - ELEC-
TRICAL/ELECTRONIC CONTROL MODULES/
COMMUNICATION - DESCRIPTION).
Hard wired circuitry connects the supplemental
restraint system components to each other through
the electrical system of the vehicle. These hard wired
circuits are integral to several wire harnesses, which
are routed throughout the vehicle and retained by
many different methods. These circuits may be con-
nected to each other, to the vehicle electrical system,
and to the supplemental restraint system compo-
nents through the use of a combination of soldered
splices, splice block connectors, and many different
types of wire harness terminal connectors and insu-
lators. Refer to the appropriate wiring information.
The wiring information includes wiring diagrams,
proper wire and connector repair procedures, further
details on wire harness routing and retention, as well
as pin-out and location views for the various wire
harness connectors, splices and grounds.
OPERATION
ACTIVE RESTRAINTS
The primary passenger restraints in this or any
other vehicle are the standard equipment factory-in-
stalled seat belts. Seat belts are referred to as an
active restraint because the vehicle occupants are
required to physically fasten and properly adjust
these restraints in order to benefit from them. See
the owner's manual in the vehicle glove box for more
information on the features, use and operation of all
of the factory-installed active restraints.PASSIVE RESTRAINTS
The passive restraints system is referred to as a
supplemental restraint system because they were
designed and are intended to enhance the protection
for the vehicle occupants of the vehicleonlywhen
used in conjunction with the seat belts. They are
referred to as passive systems because the vehicle
occupants are not required to do anything to make
them operate; however, the vehicle occupants must
be wearing their seat belts in order to obtain the
maximum safety benefit from the factory-installed
supplemental restraint systems.
The supplemental restraint system electrical cir-
cuits are continuously monitored and controlled by a
microprocessor and software contained within the
Airbag Control Module (ACM). An airbag indicator in
the ElectroMechanical Instrument Cluster (EMIC)
illuminates for about seven seconds as a bulb test
each time the ignition switch is turned to the On or
Start positions. Following the bulb test, the airbag
indicator is turned on or off by the ACM to indicate
the status of the supplemental restraint system. If
the airbag indicator comes on at any time other than
during the bulb test, it indicates that there is a prob-
lem in the supplemental restraint system electrical
circuits. Such a problem may cause airbags not to
deploy when required, or to deploy when not
required.
Deployment of the supplemental restraints
depends upon the angle and severity of an impact.
Deployment is not based upon vehicle speed; rather,
deployment is based upon the rate of deceleration as
measured by the forces of gravity (G force) upon the
impact sensors. When an impact is severe enough,
the microprocessor in the ACM signals the inflator
unit of the airbag module to deploy the airbag. Dur-
ing a frontal vehicle impact, the knee blockers work
in concert with properly fastened and adjusted seat
belts to restrain both the driver and the front seat
passenger in the proper position for an airbag deploy-
ment. The knee blockers also absorb and distribute
the crash energy from the driver and the front seat
passenger to the structure of the instrument panel.
Typically, the vehicle occupants recall more about
the events preceding and following a collision than
they have of an airbag deployment itself. This is
because the airbag deployment and deflation occur so
rapidly. In a typical 48 kilometer-per-hour (30 mile-
per-hour) barrier impact, from the moment of impact
until the airbags are fully inflated takes about 40
milliseconds. Within one to two seconds from the
moment of impact, the airbags are almost entirely
deflated. The times cited for these events are approx-
imations, which apply only to a barrier impact at the
given speed. Actual times will vary somewhat,
8O - 4 RESTRAINTSWJ
RESTRAINTS (Continued)
Page 544 of 2199
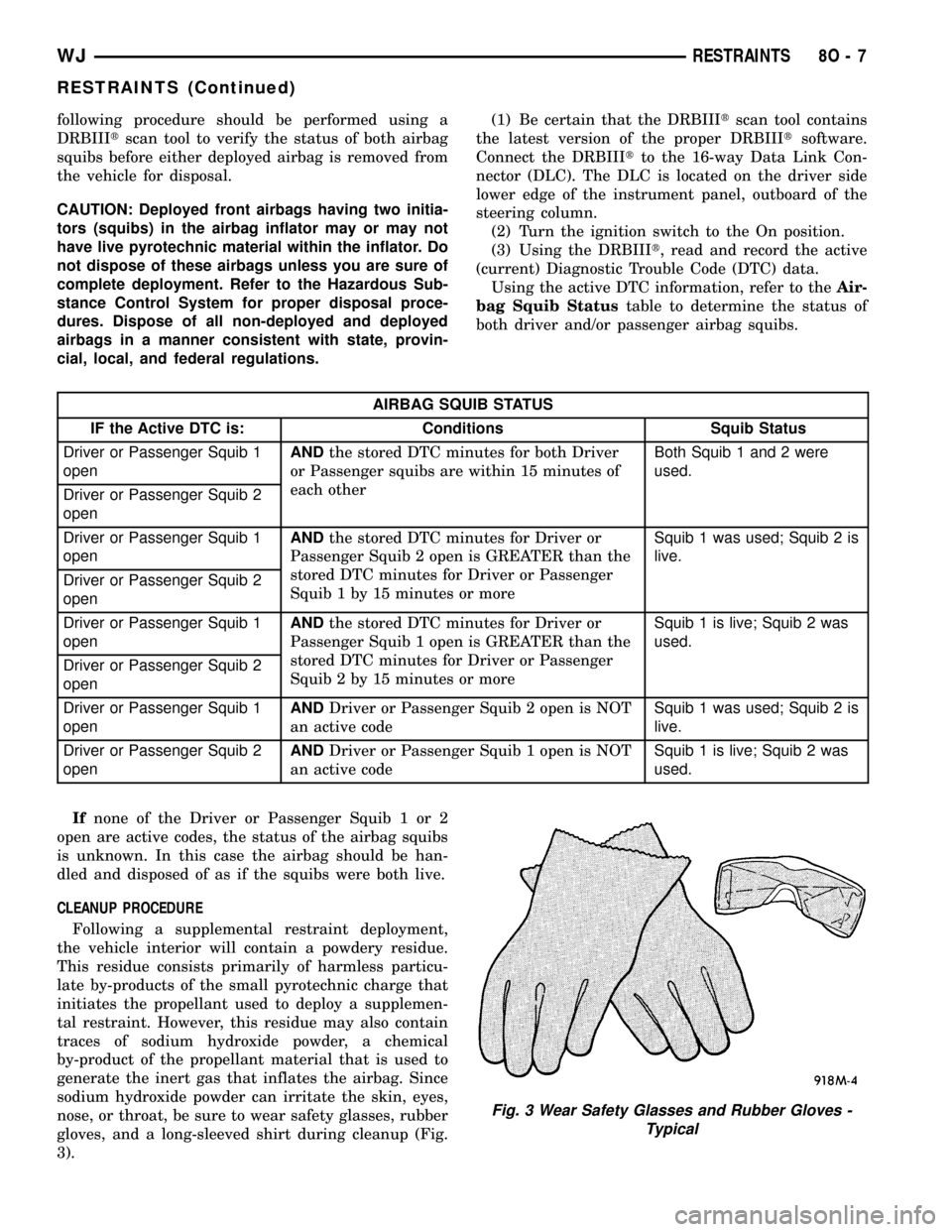
following procedure should be performed using a
DRBIIItscan tool to verify the status of both airbag
squibs before either deployed airbag is removed from
the vehicle for disposal.
CAUTION: Deployed front airbags having two initia-
tors (squibs) in the airbag inflator may or may not
have live pyrotechnic material within the inflator. Do
not dispose of these airbags unless you are sure of
complete deployment. Refer to the Hazardous Sub-
stance Control System for proper disposal proce-
dures. Dispose of all non-deployed and deployed
airbags in a manner consistent with state, provin-
cial, local, and federal regulations.(1) Be certain that the DRBIIItscan tool contains
the latest version of the proper DRBIIItsoftware.
Connect the DRBIIItto the 16-way Data Link Con-
nector (DLC). The DLC is located on the driver side
lower edge of the instrument panel, outboard of the
steering column.
(2) Turn the ignition switch to the On position.
(3) Using the DRBIIIt, read and record the active
(current) Diagnostic Trouble Code (DTC) data.
Using the active DTC information, refer to theAir-
bag Squib Statustable to determine the status of
both driver and/or passenger airbag squibs.
AIRBAG SQUIB STATUS
IF the Active DTC is: Conditions Squib Status
Driver or Passenger Squib 1
openANDthe stored DTC minutes for both Driver
or Passenger squibs are within 15 minutes of
each otherBoth Squib 1 and 2 were
used.
Driver or Passenger Squib 2
open
Driver or Passenger Squib 1
openANDthe stored DTC minutes for Driver or
Passenger Squib 2 open is GREATER than the
stored DTC minutes for Driver or Passenger
Squib 1 by 15 minutes or moreSquib 1 was used; Squib 2 is
live.
Driver or Passenger Squib 2
open
Driver or Passenger Squib 1
openANDthe stored DTC minutes for Driver or
Passenger Squib 1 open is GREATER than the
stored DTC minutes for Driver or Passenger
Squib 2 by 15 minutes or moreSquib 1 is live; Squib 2 was
used.
Driver or Passenger Squib 2
open
Driver or Passenger Squib 1
openANDDriver or Passenger Squib 2 open is NOT
an active codeSquib 1 was used; Squib 2 is
live.
Driver or Passenger Squib 2
openANDDriver or Passenger Squib 1 open is NOT
an active codeSquib 1 is live; Squib 2 was
used.
Ifnone of the Driver or Passenger Squib 1 or 2
open are active codes, the status of the airbag squibs
is unknown. In this case the airbag should be han-
dled and disposed of as if the squibs were both live.
CLEANUP PROCEDURE
Following a supplemental restraint deployment,
the vehicle interior will contain a powdery residue.
This residue consists primarily of harmless particu-
late by-products of the small pyrotechnic charge that
initiates the propellant used to deploy a supplemen-
tal restraint. However, this residue may also contain
traces of sodium hydroxide powder, a chemical
by-product of the propellant material that is used to
generate the inert gas that inflates the airbag. Since
sodium hydroxide powder can irritate the skin, eyes,
nose, or throat, be sure to wear safety glasses, rubber
gloves, and a long-sleeved shirt during cleanup (Fig.
3).
Fig. 3 Wear Safety Glasses and Rubber Gloves -
Typical
WJRESTRAINTS 8O - 7
RESTRAINTS (Continued)