Engine harness JEEP GRAND CHEROKEE 2003 WJ / 2.G User Guide
[x] Cancel search | Manufacturer: JEEP, Model Year: 2003, Model line: GRAND CHEROKEE, Model: JEEP GRAND CHEROKEE 2003 WJ / 2.GPages: 2199, PDF Size: 76.01 MB
Page 349 of 2199
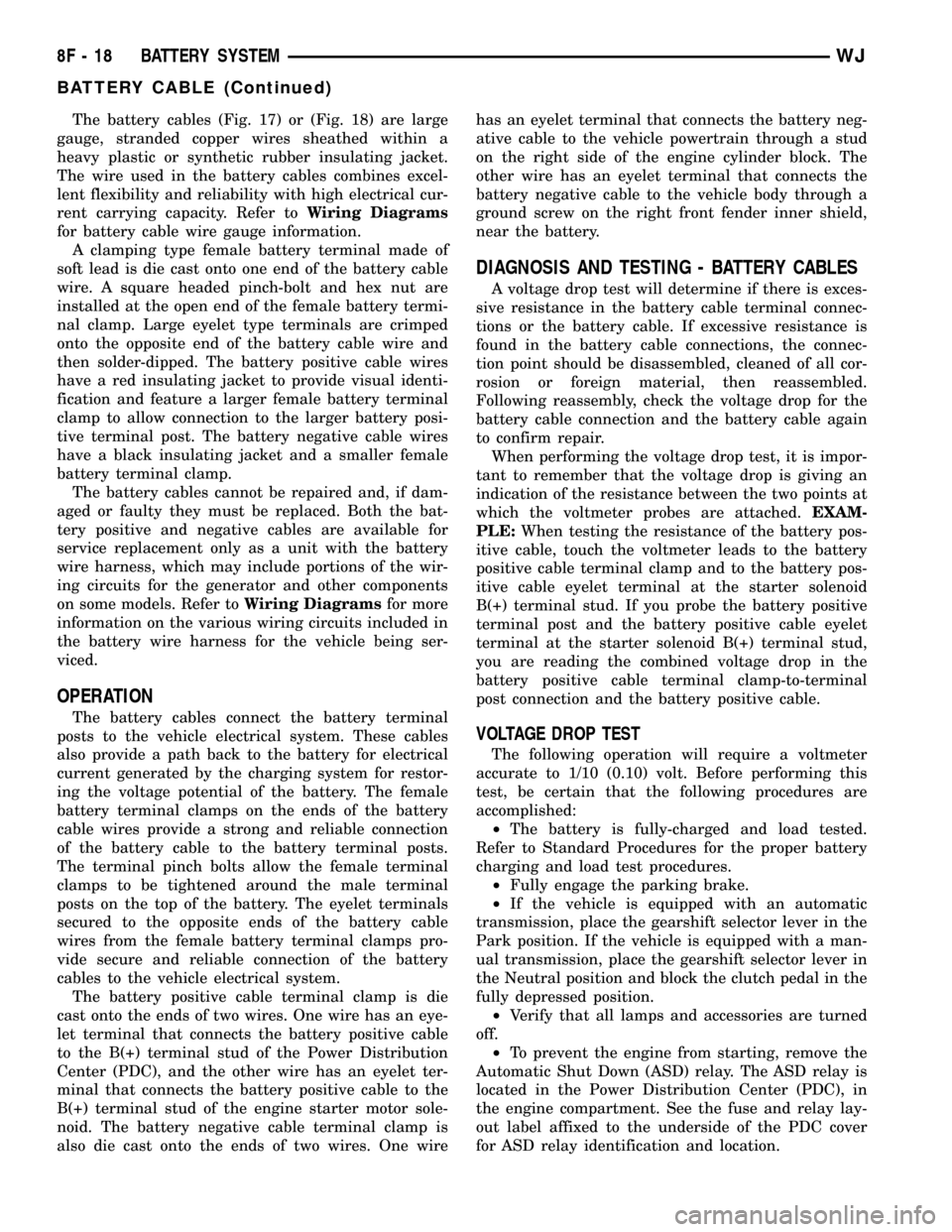
The battery cables (Fig. 17) or (Fig. 18) are large
gauge, stranded copper wires sheathed within a
heavy plastic or synthetic rubber insulating jacket.
The wire used in the battery cables combines excel-
lent flexibility and reliability with high electrical cur-
rent carrying capacity. Refer toWiring Diagrams
for battery cable wire gauge information.
A clamping type female battery terminal made of
soft lead is die cast onto one end of the battery cable
wire. A square headed pinch-bolt and hex nut are
installed at the open end of the female battery termi-
nal clamp. Large eyelet type terminals are crimped
onto the opposite end of the battery cable wire and
then solder-dipped. The battery positive cable wires
have a red insulating jacket to provide visual identi-
fication and feature a larger female battery terminal
clamp to allow connection to the larger battery posi-
tive terminal post. The battery negative cable wires
have a black insulating jacket and a smaller female
battery terminal clamp.
The battery cables cannot be repaired and, if dam-
aged or faulty they must be replaced. Both the bat-
tery positive and negative cables are available for
service replacement only as a unit with the battery
wire harness, which may include portions of the wir-
ing circuits for the generator and other components
on some models. Refer toWiring Diagramsfor more
information on the various wiring circuits included in
the battery wire harness for the vehicle being ser-
viced.
OPERATION
The battery cables connect the battery terminal
posts to the vehicle electrical system. These cables
also provide a path back to the battery for electrical
current generated by the charging system for restor-
ing the voltage potential of the battery. The female
battery terminal clamps on the ends of the battery
cable wires provide a strong and reliable connection
of the battery cable to the battery terminal posts.
The terminal pinch bolts allow the female terminal
clamps to be tightened around the male terminal
posts on the top of the battery. The eyelet terminals
secured to the opposite ends of the battery cable
wires from the female battery terminal clamps pro-
vide secure and reliable connection of the battery
cables to the vehicle electrical system.
The battery positive cable terminal clamp is die
cast onto the ends of two wires. One wire has an eye-
let terminal that connects the battery positive cable
to the B(+) terminal stud of the Power Distribution
Center (PDC), and the other wire has an eyelet ter-
minal that connects the battery positive cable to the
B(+) terminal stud of the engine starter motor sole-
noid. The battery negative cable terminal clamp is
also die cast onto the ends of two wires. One wirehas an eyelet terminal that connects the battery neg-
ative cable to the vehicle powertrain through a stud
on the right side of the engine cylinder block. The
other wire has an eyelet terminal that connects the
battery negative cable to the vehicle body through a
ground screw on the right front fender inner shield,
near the battery.
DIAGNOSIS AND TESTING - BATTERY CABLES
A voltage drop test will determine if there is exces-
sive resistance in the battery cable terminal connec-
tions or the battery cable. If excessive resistance is
found in the battery cable connections, the connec-
tion point should be disassembled, cleaned of all cor-
rosion or foreign material, then reassembled.
Following reassembly, check the voltage drop for the
battery cable connection and the battery cable again
to confirm repair.
When performing the voltage drop test, it is impor-
tant to remember that the voltage drop is giving an
indication of the resistance between the two points at
which the voltmeter probes are attached.EXAM-
PLE:When testing the resistance of the battery pos-
itive cable, touch the voltmeter leads to the battery
positive cable terminal clamp and to the battery pos-
itive cable eyelet terminal at the starter solenoid
B(+) terminal stud. If you probe the battery positive
terminal post and the battery positive cable eyelet
terminal at the starter solenoid B(+) terminal stud,
you are reading the combined voltage drop in the
battery positive cable terminal clamp-to-terminal
post connection and the battery positive cable.
VOLTAGE DROP TEST
The following operation will require a voltmeter
accurate to 1/10 (0.10) volt. Before performing this
test, be certain that the following procedures are
accomplished:
²The battery is fully-charged and load tested.
Refer to Standard Procedures for the proper battery
charging and load test procedures.
²Fully engage the parking brake.
²If the vehicle is equipped with an automatic
transmission, place the gearshift selector lever in the
Park position. If the vehicle is equipped with a man-
ual transmission, place the gearshift selector lever in
the Neutral position and block the clutch pedal in the
fully depressed position.
²Verify that all lamps and accessories are turned
off.
²To prevent the engine from starting, remove the
Automatic Shut Down (ASD) relay. The ASD relay is
located in the Power Distribution Center (PDC), in
the engine compartment. See the fuse and relay lay-
out label affixed to the underside of the PDC cover
for ASD relay identification and location.
8F - 18 BATTERY SYSTEMWJ
BATTERY CABLE (Continued)
Page 350 of 2199
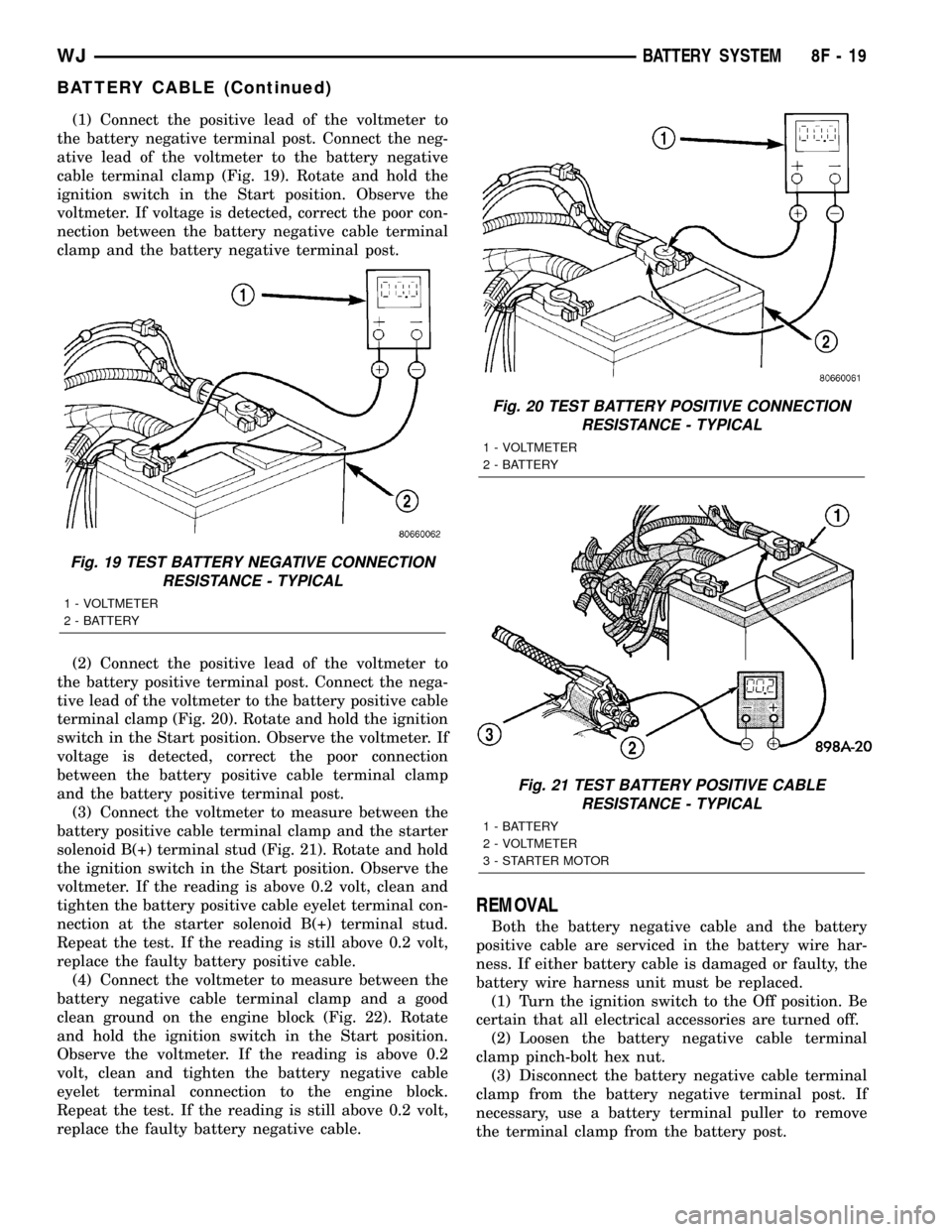
(1) Connect the positive lead of the voltmeter to
the battery negative terminal post. Connect the neg-
ative lead of the voltmeter to the battery negative
cable terminal clamp (Fig. 19). Rotate and hold the
ignition switch in the Start position. Observe the
voltmeter. If voltage is detected, correct the poor con-
nection between the battery negative cable terminal
clamp and the battery negative terminal post.
(2) Connect the positive lead of the voltmeter to
the battery positive terminal post. Connect the nega-
tive lead of the voltmeter to the battery positive cable
terminal clamp (Fig. 20). Rotate and hold the ignition
switch in the Start position. Observe the voltmeter. If
voltage is detected, correct the poor connection
between the battery positive cable terminal clamp
and the battery positive terminal post.
(3) Connect the voltmeter to measure between the
battery positive cable terminal clamp and the starter
solenoid B(+) terminal stud (Fig. 21). Rotate and hold
the ignition switch in the Start position. Observe the
voltmeter. If the reading is above 0.2 volt, clean and
tighten the battery positive cable eyelet terminal con-
nection at the starter solenoid B(+) terminal stud.
Repeat the test. If the reading is still above 0.2 volt,
replace the faulty battery positive cable.
(4) Connect the voltmeter to measure between the
battery negative cable terminal clamp and a good
clean ground on the engine block (Fig. 22). Rotate
and hold the ignition switch in the Start position.
Observe the voltmeter. If the reading is above 0.2
volt, clean and tighten the battery negative cable
eyelet terminal connection to the engine block.
Repeat the test. If the reading is still above 0.2 volt,
replace the faulty battery negative cable.
REMOVAL
Both the battery negative cable and the battery
positive cable are serviced in the battery wire har-
ness. If either battery cable is damaged or faulty, the
battery wire harness unit must be replaced.
(1) Turn the ignition switch to the Off position. Be
certain that all electrical accessories are turned off.
(2) Loosen the battery negative cable terminal
clamp pinch-bolt hex nut.
(3) Disconnect the battery negative cable terminal
clamp from the battery negative terminal post. If
necessary, use a battery terminal puller to remove
the terminal clamp from the battery post.
Fig. 19 TEST BATTERY NEGATIVE CONNECTION
RESISTANCE - TYPICAL
1 - VOLTMETER
2 - BATTERY
Fig. 20 TEST BATTERY POSITIVE CONNECTION
RESISTANCE - TYPICAL
1 - VOLTMETER
2 - BATTERY
Fig. 21 TEST BATTERY POSITIVE CABLE
RESISTANCE - TYPICAL
1 - BATTERY
2 - VOLTMETER
3 - STARTER MOTOR
WJBATTERY SYSTEM 8F - 19
BATTERY CABLE (Continued)
Page 351 of 2199
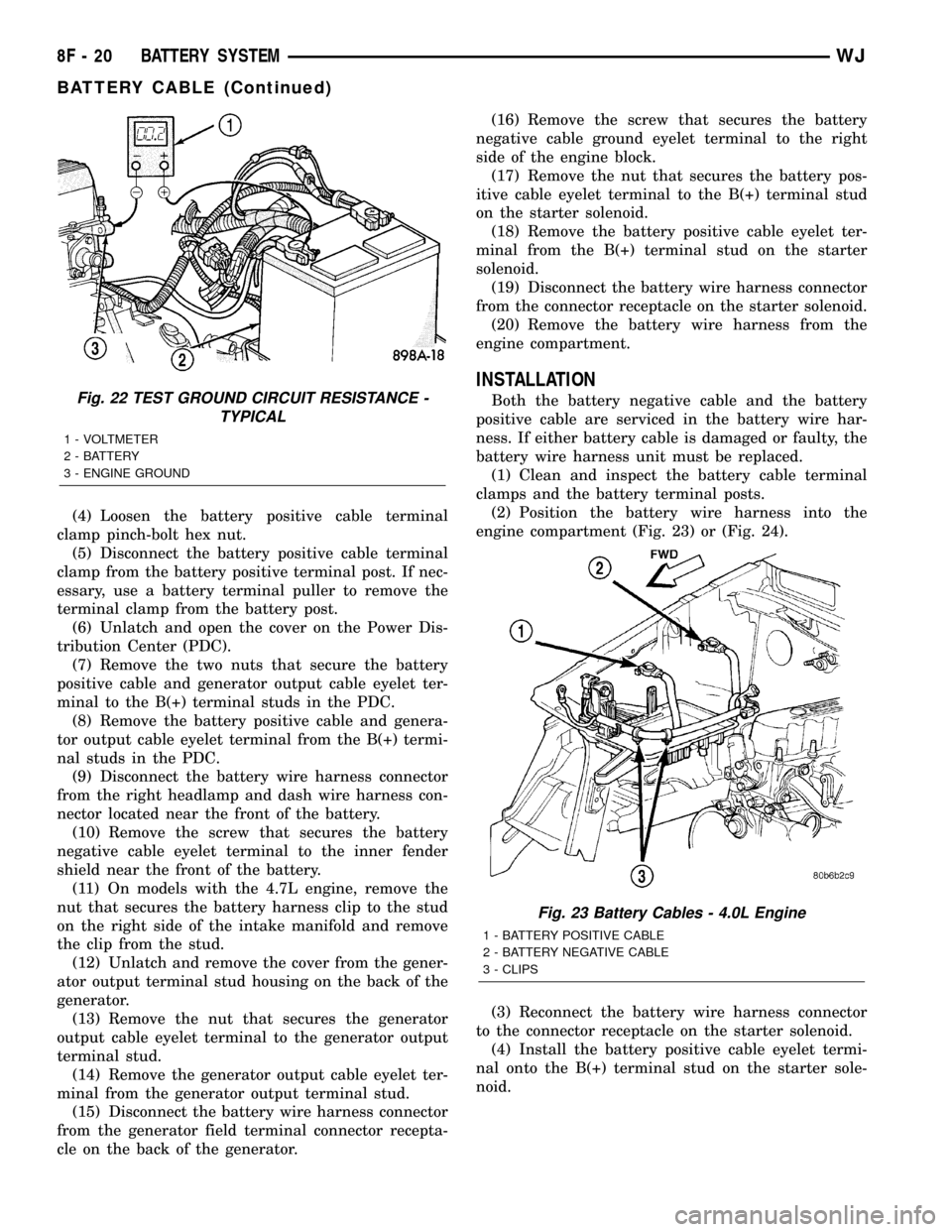
(4) Loosen the battery positive cable terminal
clamp pinch-bolt hex nut.
(5) Disconnect the battery positive cable terminal
clamp from the battery positive terminal post. If nec-
essary, use a battery terminal puller to remove the
terminal clamp from the battery post.
(6) Unlatch and open the cover on the Power Dis-
tribution Center (PDC).
(7) Remove the two nuts that secure the battery
positive cable and generator output cable eyelet ter-
minal to the B(+) terminal studs in the PDC.
(8) Remove the battery positive cable and genera-
tor output cable eyelet terminal from the B(+) termi-
nal studs in the PDC.
(9) Disconnect the battery wire harness connector
from the right headlamp and dash wire harness con-
nector located near the front of the battery.
(10) Remove the screw that secures the battery
negative cable eyelet terminal to the inner fender
shield near the front of the battery.
(11) On models with the 4.7L engine, remove the
nut that secures the battery harness clip to the stud
on the right side of the intake manifold and remove
the clip from the stud.
(12) Unlatch and remove the cover from the gener-
ator output terminal stud housing on the back of the
generator.
(13) Remove the nut that secures the generator
output cable eyelet terminal to the generator output
terminal stud.
(14) Remove the generator output cable eyelet ter-
minal from the generator output terminal stud.
(15) Disconnect the battery wire harness connector
from the generator field terminal connector recepta-
cle on the back of the generator.(16) Remove the screw that secures the battery
negative cable ground eyelet terminal to the right
side of the engine block.
(17) Remove the nut that secures the battery pos-
itive cable eyelet terminal to the B(+) terminal stud
on the starter solenoid.
(18) Remove the battery positive cable eyelet ter-
minal from the B(+) terminal stud on the starter
solenoid.
(19) Disconnect the battery wire harness connector
from the connector receptacle on the starter solenoid.
(20) Remove the battery wire harness from the
engine compartment.
INSTALLATION
Both the battery negative cable and the battery
positive cable are serviced in the battery wire har-
ness. If either battery cable is damaged or faulty, the
battery wire harness unit must be replaced.
(1) Clean and inspect the battery cable terminal
clamps and the battery terminal posts.
(2) Position the battery wire harness into the
engine compartment (Fig. 23) or (Fig. 24).
(3) Reconnect the battery wire harness connector
to the connector receptacle on the starter solenoid.
(4) Install the battery positive cable eyelet termi-
nal onto the B(+) terminal stud on the starter sole-
noid.Fig. 22 TEST GROUND CIRCUIT RESISTANCE -
TYPICAL
1 - VOLTMETER
2 - BATTERY
3 - ENGINE GROUND
Fig. 23 Battery Cables - 4.0L Engine
1 - BATTERY POSITIVE CABLE
2 - BATTERY NEGATIVE CABLE
3 - CLIPS
8F - 20 BATTERY SYSTEMWJ
BATTERY CABLE (Continued)
Page 352 of 2199
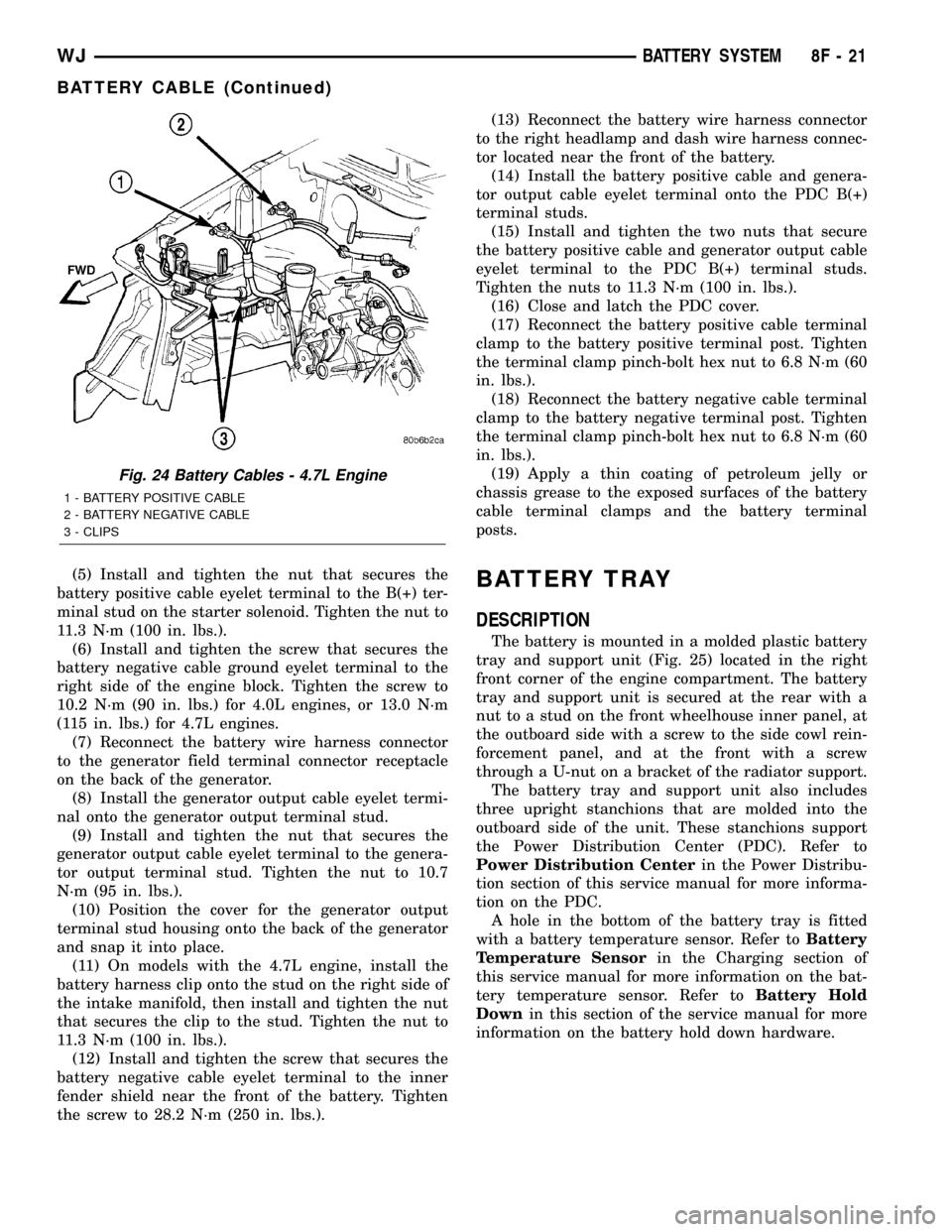
(5) Install and tighten the nut that secures the
battery positive cable eyelet terminal to the B(+) ter-
minal stud on the starter solenoid. Tighten the nut to
11.3 N´m (100 in. lbs.).
(6) Install and tighten the screw that secures the
battery negative cable ground eyelet terminal to the
right side of the engine block. Tighten the screw to
10.2 N´m (90 in. lbs.) for 4.0L engines, or 13.0 N´m
(115 in. lbs.) for 4.7L engines.
(7) Reconnect the battery wire harness connector
to the generator field terminal connector receptacle
on the back of the generator.
(8) Install the generator output cable eyelet termi-
nal onto the generator output terminal stud.
(9) Install and tighten the nut that secures the
generator output cable eyelet terminal to the genera-
tor output terminal stud. Tighten the nut to 10.7
N´m (95 in. lbs.).
(10) Position the cover for the generator output
terminal stud housing onto the back of the generator
and snap it into place.
(11) On models with the 4.7L engine, install the
battery harness clip onto the stud on the right side of
the intake manifold, then install and tighten the nut
that secures the clip to the stud. Tighten the nut to
11.3 N´m (100 in. lbs.).
(12) Install and tighten the screw that secures the
battery negative cable eyelet terminal to the inner
fender shield near the front of the battery. Tighten
the screw to 28.2 N´m (250 in. lbs.).(13) Reconnect the battery wire harness connector
to the right headlamp and dash wire harness connec-
tor located near the front of the battery.
(14) Install the battery positive cable and genera-
tor output cable eyelet terminal onto the PDC B(+)
terminal studs.
(15) Install and tighten the two nuts that secure
the battery positive cable and generator output cable
eyelet terminal to the PDC B(+) terminal studs.
Tighten the nuts to 11.3 N´m (100 in. lbs.).
(16) Close and latch the PDC cover.
(17) Reconnect the battery positive cable terminal
clamp to the battery positive terminal post. Tighten
the terminal clamp pinch-bolt hex nut to 6.8 N´m (60
in. lbs.).
(18) Reconnect the battery negative cable terminal
clamp to the battery negative terminal post. Tighten
the terminal clamp pinch-bolt hex nut to 6.8 N´m (60
in. lbs.).
(19) Apply a thin coating of petroleum jelly or
chassis grease to the exposed surfaces of the battery
cable terminal clamps and the battery terminal
posts.BATTERY TRAY
DESCRIPTION
The battery is mounted in a molded plastic battery
tray and support unit (Fig. 25) located in the right
front corner of the engine compartment. The battery
tray and support unit is secured at the rear with a
nut to a stud on the front wheelhouse inner panel, at
the outboard side with a screw to the side cowl rein-
forcement panel, and at the front with a screw
through a U-nut on a bracket of the radiator support.
The battery tray and support unit also includes
three upright stanchions that are molded into the
outboard side of the unit. These stanchions support
the Power Distribution Center (PDC). Refer to
Power Distribution Centerin the Power Distribu-
tion section of this service manual for more informa-
tion on the PDC.
A hole in the bottom of the battery tray is fitted
with a battery temperature sensor. Refer toBattery
Temperature Sensorin the Charging section of
this service manual for more information on the bat-
tery temperature sensor. Refer toBattery Hold
Downin this section of the service manual for more
information on the battery hold down hardware.
Fig. 24 Battery Cables - 4.7L Engine
1 - BATTERY POSITIVE CABLE
2 - BATTERY NEGATIVE CABLE
3 - CLIPS
WJBATTERY SYSTEM 8F - 21
BATTERY CABLE (Continued)
Page 354 of 2199
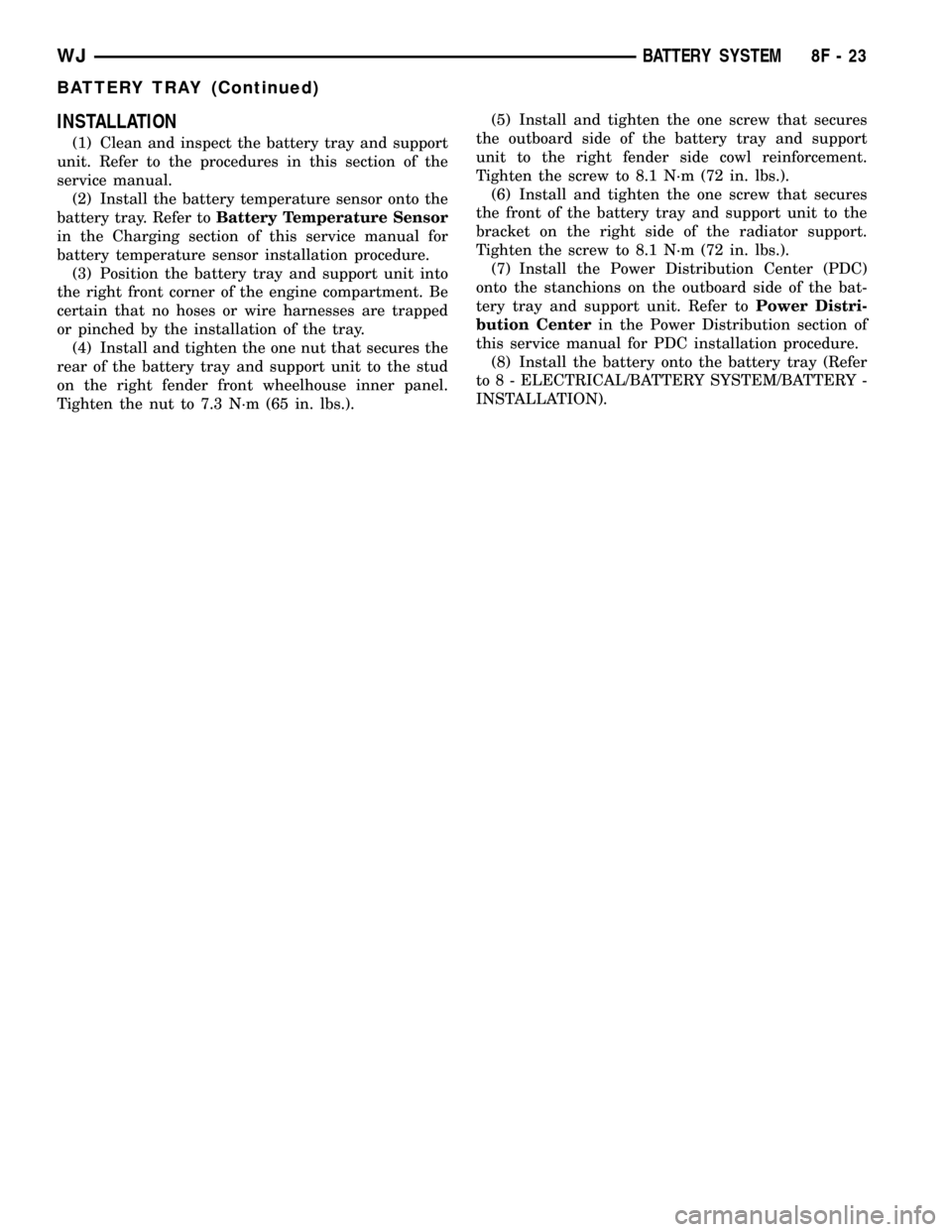
INSTALLATION
(1) Clean and inspect the battery tray and support
unit. Refer to the procedures in this section of the
service manual.
(2) Install the battery temperature sensor onto the
battery tray. Refer toBattery Temperature Sensor
in the Charging section of this service manual for
battery temperature sensor installation procedure.
(3) Position the battery tray and support unit into
the right front corner of the engine compartment. Be
certain that no hoses or wire harnesses are trapped
or pinched by the installation of the tray.
(4) Install and tighten the one nut that secures the
rear of the battery tray and support unit to the stud
on the right fender front wheelhouse inner panel.
Tighten the nut to 7.3 N´m (65 in. lbs.).(5) Install and tighten the one screw that secures
the outboard side of the battery tray and support
unit to the right fender side cowl reinforcement.
Tighten the screw to 8.1 N´m (72 in. lbs.).
(6) Install and tighten the one screw that secures
the front of the battery tray and support unit to the
bracket on the right side of the radiator support.
Tighten the screw to 8.1 N´m (72 in. lbs.).
(7) Install the Power Distribution Center (PDC)
onto the stanchions on the outboard side of the bat-
tery tray and support unit. Refer toPower Distri-
bution Centerin the Power Distribution section of
this service manual for PDC installation procedure.
(8) Install the battery onto the battery tray (Refer
to 8 - ELECTRICAL/BATTERY SYSTEM/BATTERY -
INSTALLATION).
WJBATTERY SYSTEM 8F - 23
BATTERY TRAY (Continued)
Page 355 of 2199
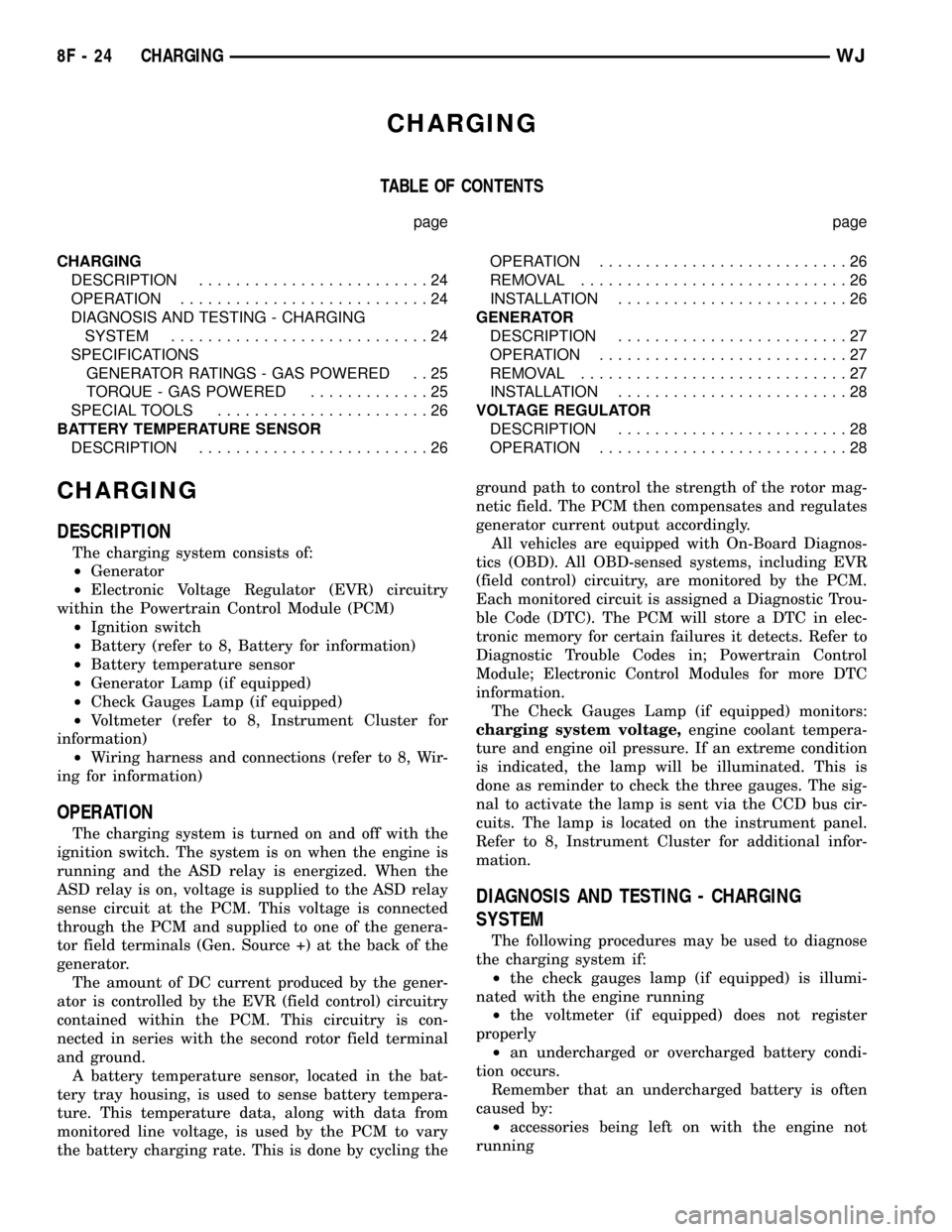
CHARGING
TABLE OF CONTENTS
page page
CHARGING
DESCRIPTION.........................24
OPERATION...........................24
DIAGNOSIS AND TESTING - CHARGING
SYSTEM............................24
SPECIFICATIONS
GENERATOR RATINGS - GAS POWERED . . 25
TORQUE - GAS POWERED.............25
SPECIAL TOOLS.......................26
BATTERY TEMPERATURE SENSOR
DESCRIPTION.........................26OPERATION...........................26
REMOVAL.............................26
INSTALLATION.........................26
GENERATOR
DESCRIPTION.........................27
OPERATION...........................27
REMOVAL.............................27
INSTALLATION.........................28
VOLTAGE REGULATOR
DESCRIPTION.........................28
OPERATION...........................28
CHARGING
DESCRIPTION
The charging system consists of:
²Generator
²Electronic Voltage Regulator (EVR) circuitry
within the Powertrain Control Module (PCM)
²Ignition switch
²Battery (refer to 8, Battery for information)
²Battery temperature sensor
²Generator Lamp (if equipped)
²Check Gauges Lamp (if equipped)
²Voltmeter (refer to 8, Instrument Cluster for
information)
²Wiring harness and connections (refer to 8, Wir-
ing for information)
OPERATION
The charging system is turned on and off with the
ignition switch. The system is on when the engine is
running and the ASD relay is energized. When the
ASD relay is on, voltage is supplied to the ASD relay
sense circuit at the PCM. This voltage is connected
through the PCM and supplied to one of the genera-
tor field terminals (Gen. Source +) at the back of the
generator.
The amount of DC current produced by the gener-
ator is controlled by the EVR (field control) circuitry
contained within the PCM. This circuitry is con-
nected in series with the second rotor field terminal
and ground.
A battery temperature sensor, located in the bat-
tery tray housing, is used to sense battery tempera-
ture. This temperature data, along with data from
monitored line voltage, is used by the PCM to vary
the battery charging rate. This is done by cycling theground path to control the strength of the rotor mag-
netic field. The PCM then compensates and regulates
generator current output accordingly.
All vehicles are equipped with On-Board Diagnos-
tics (OBD). All OBD-sensed systems, including EVR
(field control) circuitry, are monitored by the PCM.
Each monitored circuit is assigned a Diagnostic Trou-
ble Code (DTC). The PCM will store a DTC in elec-
tronic memory for certain failures it detects. Refer to
Diagnostic Trouble Codes in; Powertrain Control
Module; Electronic Control Modules for more DTC
information.
The Check Gauges Lamp (if equipped) monitors:
charging system voltage,engine coolant tempera-
ture and engine oil pressure. If an extreme condition
is indicated, the lamp will be illuminated. This is
done as reminder to check the three gauges. The sig-
nal to activate the lamp is sent via the CCD bus cir-
cuits. The lamp is located on the instrument panel.
Refer to 8, Instrument Cluster for additional infor-
mation.
DIAGNOSIS AND TESTING - CHARGING
SYSTEM
The following procedures may be used to diagnose
the charging system if:
²the check gauges lamp (if equipped) is illumi-
nated with the engine running
²the voltmeter (if equipped) does not register
properly
²an undercharged or overcharged battery condi-
tion occurs.
Remember that an undercharged battery is often
caused by:
²accessories being left on with the engine not
running
8F - 24 CHARGINGWJ
Page 357 of 2199
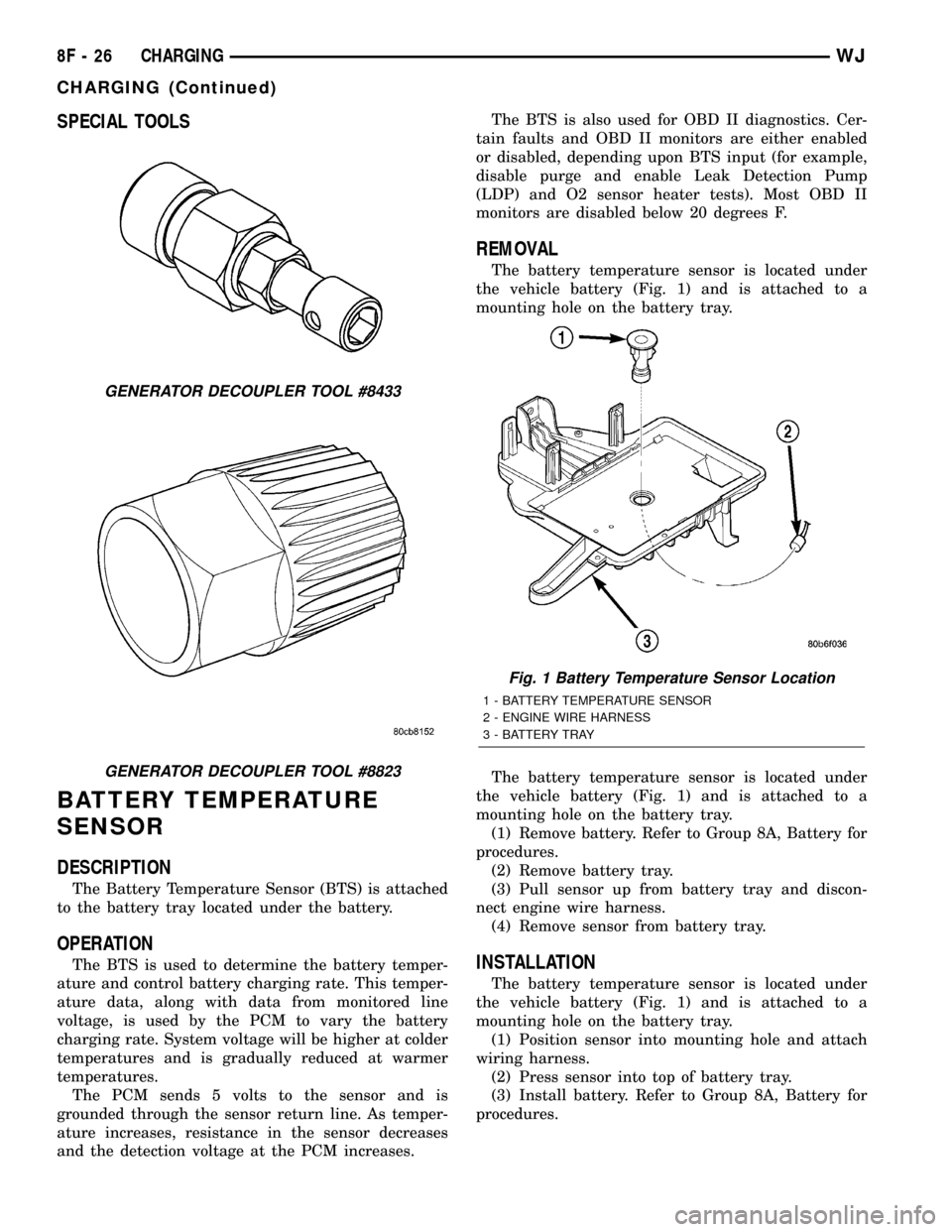
SPECIAL TOOLS
BATTERY TEMPERATURE
SENSOR
DESCRIPTION
The Battery Temperature Sensor (BTS) is attached
to the battery tray located under the battery.
OPERATION
The BTS is used to determine the battery temper-
ature and control battery charging rate. This temper-
ature data, along with data from monitored line
voltage, is used by the PCM to vary the battery
charging rate. System voltage will be higher at colder
temperatures and is gradually reduced at warmer
temperatures.
The PCM sends 5 volts to the sensor and is
grounded through the sensor return line. As temper-
ature increases, resistance in the sensor decreases
and the detection voltage at the PCM increases.The BTS is also used for OBD II diagnostics. Cer-
tain faults and OBD II monitors are either enabled
or disabled, depending upon BTS input (for example,
disable purge and enable Leak Detection Pump
(LDP) and O2 sensor heater tests). Most OBD II
monitors are disabled below 20 degrees F.
REMOVAL
The battery temperature sensor is located under
the vehicle battery (Fig. 1) and is attached to a
mounting hole on the battery tray.
The battery temperature sensor is located under
the vehicle battery (Fig. 1) and is attached to a
mounting hole on the battery tray.
(1) Remove battery. Refer to Group 8A, Battery for
procedures.
(2) Remove battery tray.
(3) Pull sensor up from battery tray and discon-
nect engine wire harness.
(4) Remove sensor from battery tray.
INSTALLATION
The battery temperature sensor is located under
the vehicle battery (Fig. 1) and is attached to a
mounting hole on the battery tray.
(1) Position sensor into mounting hole and attach
wiring harness.
(2) Press sensor into top of battery tray.
(3) Install battery. Refer to Group 8A, Battery for
procedures.
GENERATOR DECOUPLER TOOL #8433
GENERATOR DECOUPLER TOOL #8823
Fig. 1 Battery Temperature Sensor Location
1 - BATTERY TEMPERATURE SENSOR
2 - ENGINE WIRE HARNESS
3 - BATTERY TRAY
8F - 26 CHARGINGWJ
CHARGING (Continued)
Page 360 of 2199
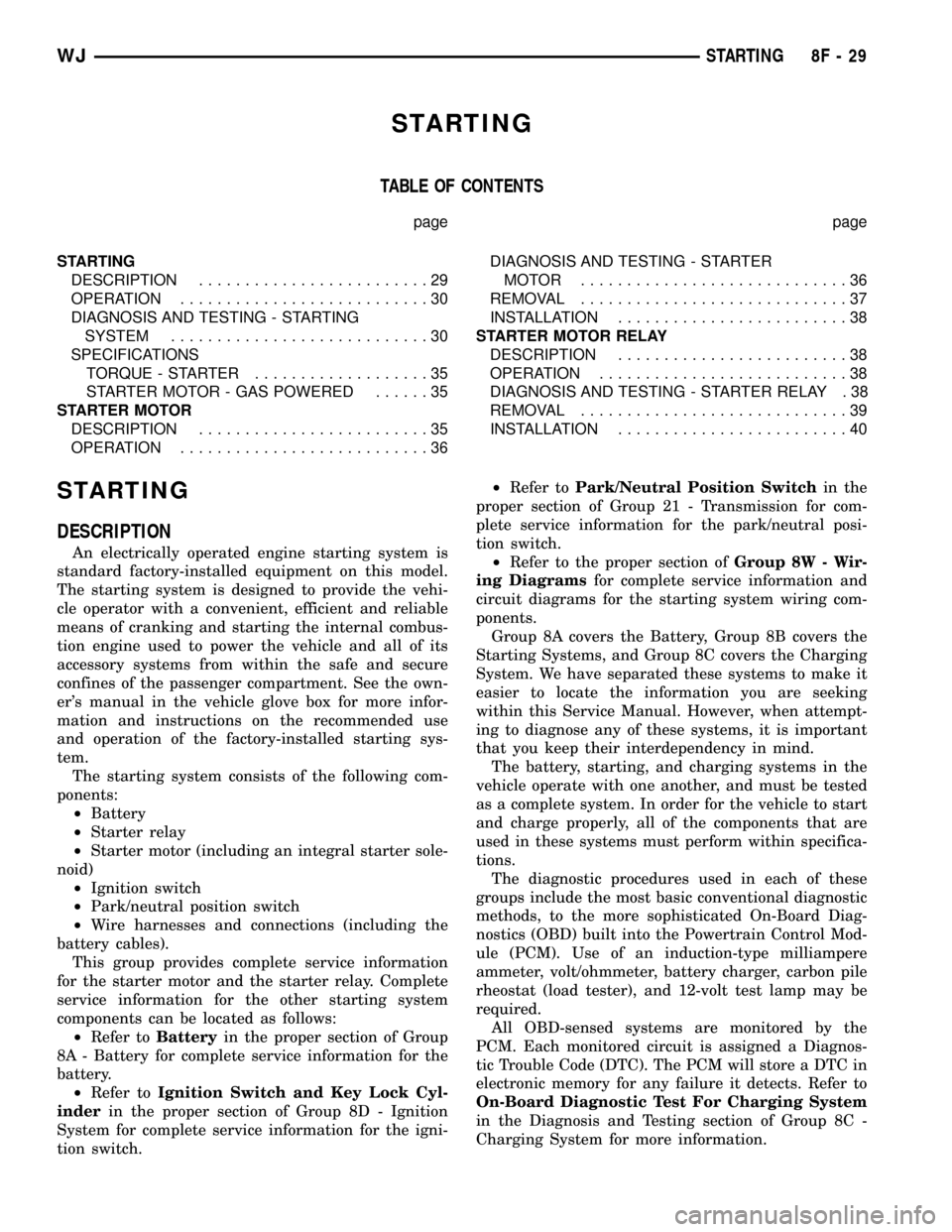
STARTING
TABLE OF CONTENTS
page page
STARTING
DESCRIPTION.........................29
OPERATION...........................30
DIAGNOSIS AND TESTING - STARTING
SYSTEM............................30
SPECIFICATIONS
TORQUE - STARTER...................35
STARTER MOTOR - GAS POWERED......35
STARTER MOTOR
DESCRIPTION.........................35
OPERATION...........................36DIAGNOSIS AND TESTING - STARTER
MOTOR .............................36
REMOVAL.............................37
INSTALLATION.........................38
STARTER MOTOR RELAY
DESCRIPTION.........................38
OPERATION...........................38
DIAGNOSIS AND TESTING - STARTER RELAY . 38
REMOVAL.............................39
INSTALLATION.........................40
STARTING
DESCRIPTION
An electrically operated engine starting system is
standard factory-installed equipment on this model.
The starting system is designed to provide the vehi-
cle operator with a convenient, efficient and reliable
means of cranking and starting the internal combus-
tion engine used to power the vehicle and all of its
accessory systems from within the safe and secure
confines of the passenger compartment. See the own-
er's manual in the vehicle glove box for more infor-
mation and instructions on the recommended use
and operation of the factory-installed starting sys-
tem.
The starting system consists of the following com-
ponents:
²Battery
²Starter relay
²Starter motor (including an integral starter sole-
noid)
²Ignition switch
²Park/neutral position switch
²Wire harnesses and connections (including the
battery cables).
This group provides complete service information
for the starter motor and the starter relay. Complete
service information for the other starting system
components can be located as follows:
²Refer toBatteryin the proper section of Group
8A - Battery for complete service information for the
battery.
²Refer toIgnition Switch and Key Lock Cyl-
inderin the proper section of Group 8D - Ignition
System for complete service information for the igni-
tion switch.²Refer toPark/Neutral Position Switchin the
proper section of Group 21 - Transmission for com-
plete service information for the park/neutral posi-
tion switch.
²Refer to the proper section ofGroup 8W - Wir-
ing Diagramsfor complete service information and
circuit diagrams for the starting system wiring com-
ponents.
Group 8A covers the Battery, Group 8B covers the
Starting Systems, and Group 8C covers the Charging
System. We have separated these systems to make it
easier to locate the information you are seeking
within this Service Manual. However, when attempt-
ing to diagnose any of these systems, it is important
that you keep their interdependency in mind.
The battery, starting, and charging systems in the
vehicle operate with one another, and must be tested
as a complete system. In order for the vehicle to start
and charge properly, all of the components that are
used in these systems must perform within specifica-
tions.
The diagnostic procedures used in each of these
groups include the most basic conventional diagnostic
methods, to the more sophisticated On-Board Diag-
nostics (OBD) built into the Powertrain Control Mod-
ule (PCM). Use of an induction-type milliampere
ammeter, volt/ohmmeter, battery charger, carbon pile
rheostat (load tester), and 12-volt test lamp may be
required.
All OBD-sensed systems are monitored by the
PCM. Each monitored circuit is assigned a Diagnos-
tic Trouble Code (DTC). The PCM will store a DTC in
electronic memory for any failure it detects. Refer to
On-Board Diagnostic Test For Charging System
in the Diagnosis and Testing section of Group 8C -
Charging System for more information.
WJSTARTING 8F - 29
Page 361 of 2199
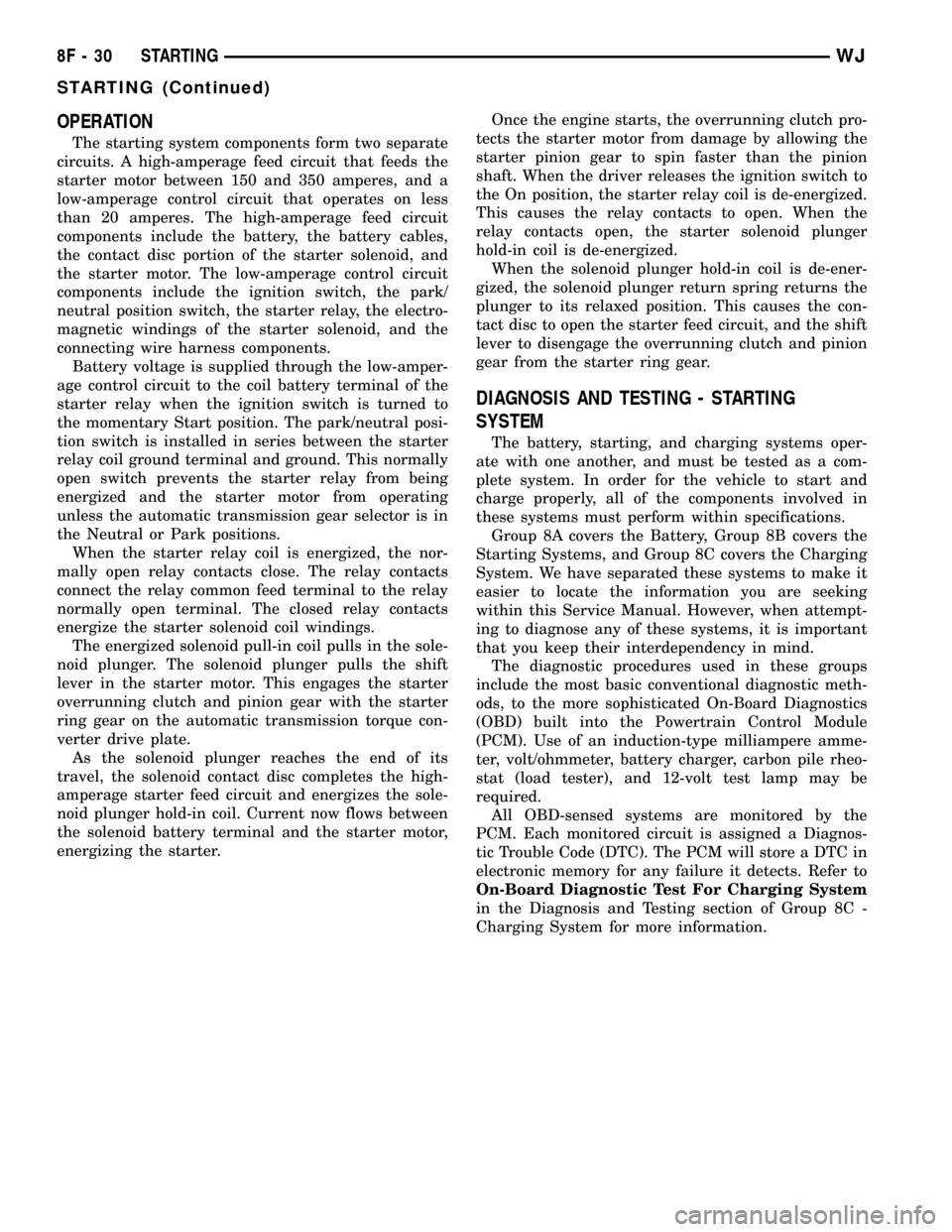
OPERATION
The starting system components form two separate
circuits. A high-amperage feed circuit that feeds the
starter motor between 150 and 350 amperes, and a
low-amperage control circuit that operates on less
than 20 amperes. The high-amperage feed circuit
components include the battery, the battery cables,
the contact disc portion of the starter solenoid, and
the starter motor. The low-amperage control circuit
components include the ignition switch, the park/
neutral position switch, the starter relay, the electro-
magnetic windings of the starter solenoid, and the
connecting wire harness components.
Battery voltage is supplied through the low-amper-
age control circuit to the coil battery terminal of the
starter relay when the ignition switch is turned to
the momentary Start position. The park/neutral posi-
tion switch is installed in series between the starter
relay coil ground terminal and ground. This normally
open switch prevents the starter relay from being
energized and the starter motor from operating
unless the automatic transmission gear selector is in
the Neutral or Park positions.
When the starter relay coil is energized, the nor-
mally open relay contacts close. The relay contacts
connect the relay common feed terminal to the relay
normally open terminal. The closed relay contacts
energize the starter solenoid coil windings.
The energized solenoid pull-in coil pulls in the sole-
noid plunger. The solenoid plunger pulls the shift
lever in the starter motor. This engages the starter
overrunning clutch and pinion gear with the starter
ring gear on the automatic transmission torque con-
verter drive plate.
As the solenoid plunger reaches the end of its
travel, the solenoid contact disc completes the high-
amperage starter feed circuit and energizes the sole-
noid plunger hold-in coil. Current now flows between
the solenoid battery terminal and the starter motor,
energizing the starter.Once the engine starts, the overrunning clutch pro-
tects the starter motor from damage by allowing the
starter pinion gear to spin faster than the pinion
shaft. When the driver releases the ignition switch to
the On position, the starter relay coil is de-energized.
This causes the relay contacts to open. When the
relay contacts open, the starter solenoid plunger
hold-in coil is de-energized.
When the solenoid plunger hold-in coil is de-ener-
gized, the solenoid plunger return spring returns the
plunger to its relaxed position. This causes the con-
tact disc to open the starter feed circuit, and the shift
lever to disengage the overrunning clutch and pinion
gear from the starter ring gear.
DIAGNOSIS AND TESTING - STARTING
SYSTEM
The battery, starting, and charging systems oper-
ate with one another, and must be tested as a com-
plete system. In order for the vehicle to start and
charge properly, all of the components involved in
these systems must perform within specifications.
Group 8A covers the Battery, Group 8B covers the
Starting Systems, and Group 8C covers the Charging
System. We have separated these systems to make it
easier to locate the information you are seeking
within this Service Manual. However, when attempt-
ing to diagnose any of these systems, it is important
that you keep their interdependency in mind.
The diagnostic procedures used in these groups
include the most basic conventional diagnostic meth-
ods, to the more sophisticated On-Board Diagnostics
(OBD) built into the Powertrain Control Module
(PCM). Use of an induction-type milliampere amme-
ter, volt/ohmmeter, battery charger, carbon pile rheo-
stat (load tester), and 12-volt test lamp may be
required.
All OBD-sensed systems are monitored by the
PCM. Each monitored circuit is assigned a Diagnos-
tic Trouble Code (DTC). The PCM will store a DTC in
electronic memory for any failure it detects. Refer to
On-Board Diagnostic Test For Charging System
in the Diagnosis and Testing section of Group 8C -
Charging System for more information.
8F - 30 STARTINGWJ
STARTING (Continued)
Page 363 of 2199
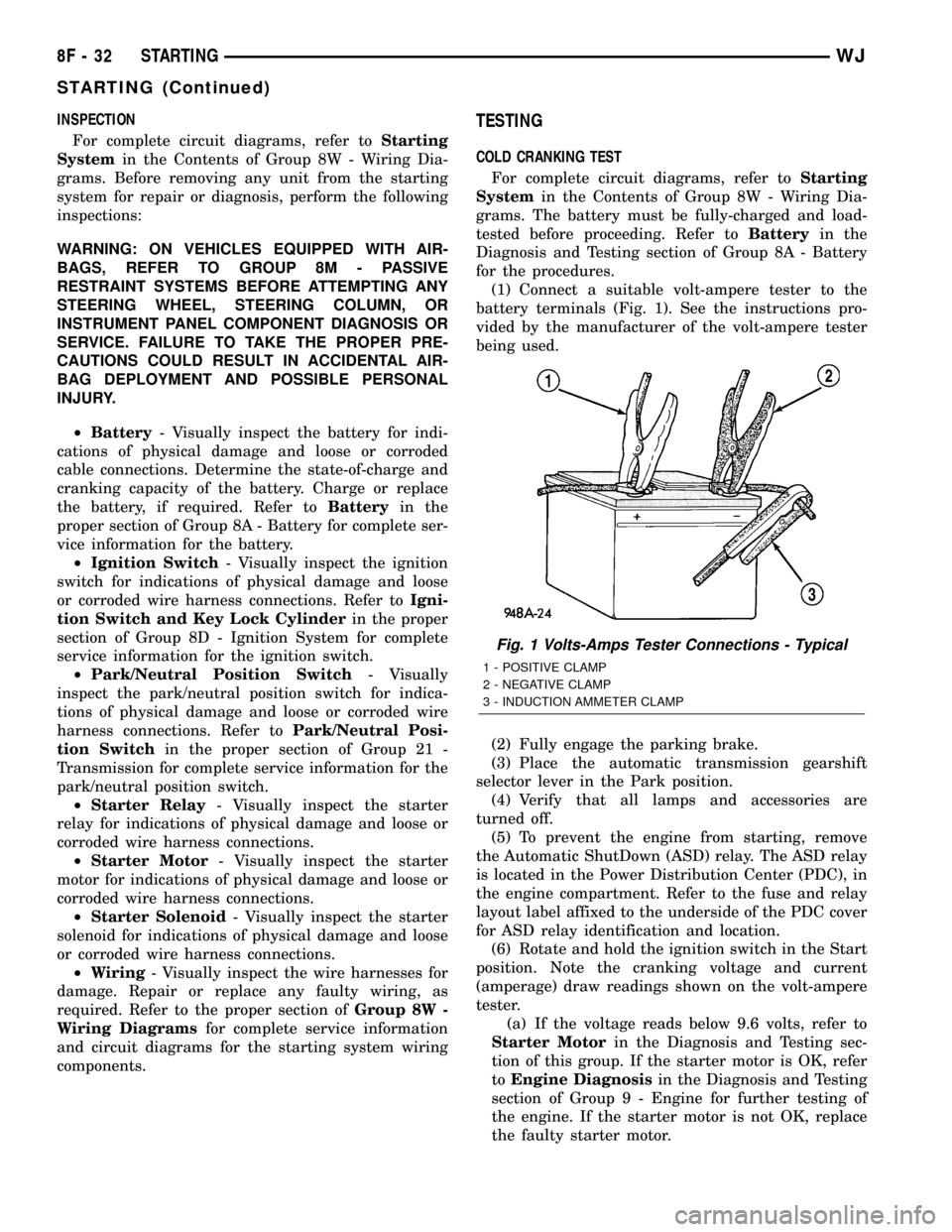
INSPECTION
For complete circuit diagrams, refer toStarting
Systemin the Contents of Group 8W - Wiring Dia-
grams. Before removing any unit from the starting
system for repair or diagnosis, perform the following
inspections:
WARNING: ON VEHICLES EQUIPPED WITH AIR-
BAGS, REFER TO GROUP 8M - PASSIVE
RESTRAINT SYSTEMS BEFORE ATTEMPTING ANY
STEERING WHEEL, STEERING COLUMN, OR
INSTRUMENT PANEL COMPONENT DIAGNOSIS OR
SERVICE. FAILURE TO TAKE THE PROPER PRE-
CAUTIONS COULD RESULT IN ACCIDENTAL AIR-
BAG DEPLOYMENT AND POSSIBLE PERSONAL
INJURY.
²Battery- Visually inspect the battery for indi-
cations of physical damage and loose or corroded
cable connections. Determine the state-of-charge and
cranking capacity of the battery. Charge or replace
the battery, if required. Refer toBatteryin the
proper section of Group 8A - Battery for complete ser-
vice information for the battery.
²Ignition Switch- Visually inspect the ignition
switch for indications of physical damage and loose
or corroded wire harness connections. Refer toIgni-
tion Switch and Key Lock Cylinderin the proper
section of Group 8D - Ignition System for complete
service information for the ignition switch.
²Park/Neutral Position Switch- Visually
inspect the park/neutral position switch for indica-
tions of physical damage and loose or corroded wire
harness connections. Refer toPark/Neutral Posi-
tion Switchin the proper section of Group 21 -
Transmission for complete service information for the
park/neutral position switch.
²Starter Relay- Visually inspect the starter
relay for indications of physical damage and loose or
corroded wire harness connections.
²Starter Motor- Visually inspect the starter
motor for indications of physical damage and loose or
corroded wire harness connections.
²Starter Solenoid- Visually inspect the starter
solenoid for indications of physical damage and loose
or corroded wire harness connections.
²Wiring- Visually inspect the wire harnesses for
damage. Repair or replace any faulty wiring, as
required. Refer to the proper section ofGroup 8W -
Wiring Diagramsfor complete service information
and circuit diagrams for the starting system wiring
components.TESTING
COLD CRANKING TEST
For complete circuit diagrams, refer toStarting
Systemin the Contents of Group 8W - Wiring Dia-
grams. The battery must be fully-charged and load-
tested before proceeding. Refer toBatteryin the
Diagnosis and Testing section of Group 8A - Battery
for the procedures.
(1) Connect a suitable volt-ampere tester to the
battery terminals (Fig. 1). See the instructions pro-
vided by the manufacturer of the volt-ampere tester
being used.
(2) Fully engage the parking brake.
(3) Place the automatic transmission gearshift
selector lever in the Park position.
(4) Verify that all lamps and accessories are
turned off.
(5) To prevent the engine from starting, remove
the Automatic ShutDown (ASD) relay. The ASD relay
is located in the Power Distribution Center (PDC), in
the engine compartment. Refer to the fuse and relay
layout label affixed to the underside of the PDC cover
for ASD relay identification and location.
(6) Rotate and hold the ignition switch in the Start
position. Note the cranking voltage and current
(amperage) draw readings shown on the volt-ampere
tester.
(a) If the voltage reads below 9.6 volts, refer to
Starter Motorin the Diagnosis and Testing sec-
tion of this group. If the starter motor is OK, refer
toEngine Diagnosisin the Diagnosis and Testing
section of Group 9 - Engine for further testing of
the engine. If the starter motor is not OK, replace
the faulty starter motor.
Fig. 1 Volts-Amps Tester Connections - Typical
1 - POSITIVE CLAMP
2 - NEGATIVE CLAMP
3 - INDUCTION AMMETER CLAMP
8F - 32 STARTINGWJ
STARTING (Continued)