Manual control lever JEEP GRAND CHEROKEE 2003 WJ / 2.G User Guide
[x] Cancel search | Manufacturer: JEEP, Model Year: 2003, Model line: GRAND CHEROKEE, Model: JEEP GRAND CHEROKEE 2003 WJ / 2.GPages: 2199, PDF Size: 76.01 MB
Page 1780 of 2199
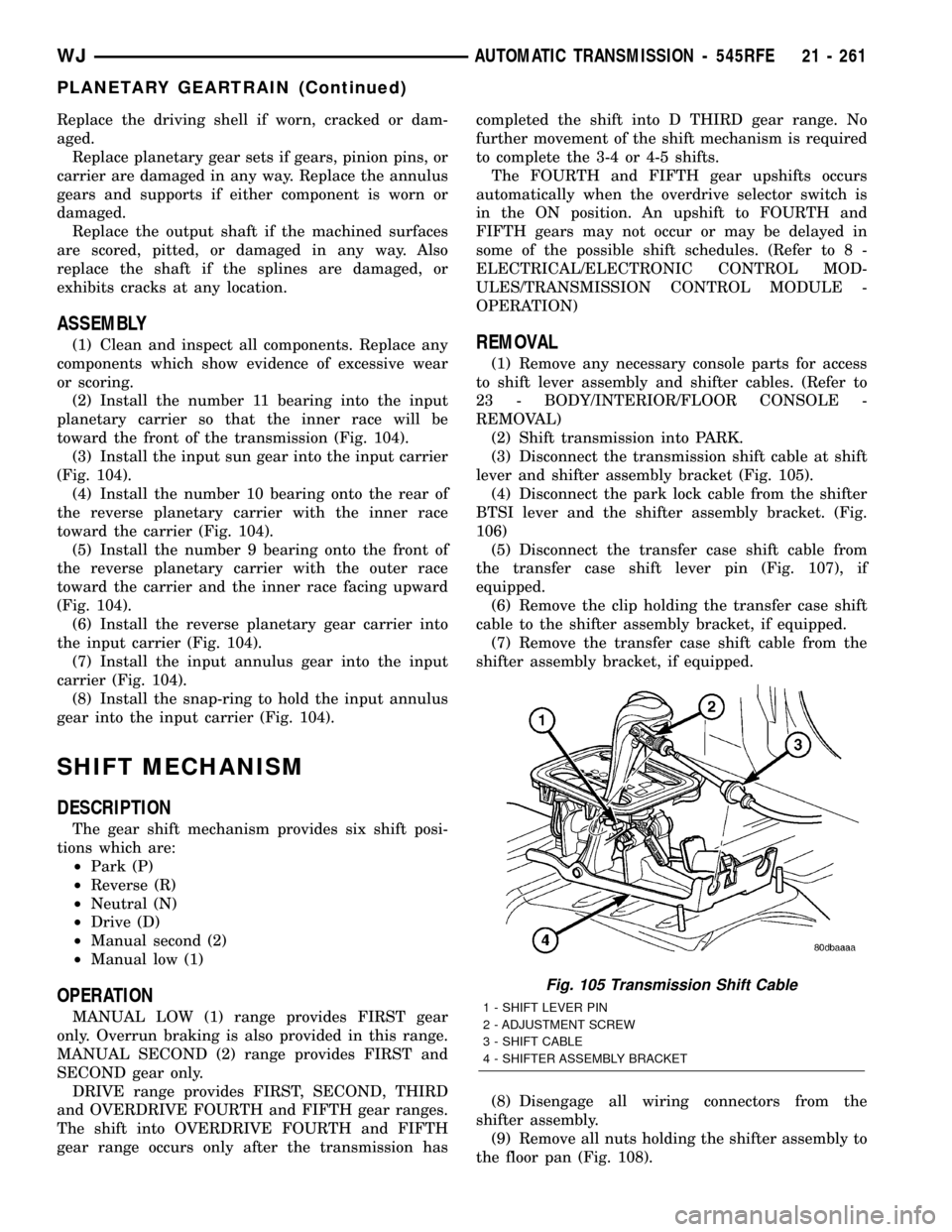
Replace the driving shell if worn, cracked or dam-
aged.
Replace planetary gear sets if gears, pinion pins, or
carrier are damaged in any way. Replace the annulus
gears and supports if either component is worn or
damaged.
Replace the output shaft if the machined surfaces
are scored, pitted, or damaged in any way. Also
replace the shaft if the splines are damaged, or
exhibits cracks at any location.
ASSEMBLY
(1) Clean and inspect all components. Replace any
components which show evidence of excessive wear
or scoring.
(2) Install the number 11 bearing into the input
planetary carrier so that the inner race will be
toward the front of the transmission (Fig. 104).
(3) Install the input sun gear into the input carrier
(Fig. 104).
(4) Install the number 10 bearing onto the rear of
the reverse planetary carrier with the inner race
toward the carrier (Fig. 104).
(5) Install the number 9 bearing onto the front of
the reverse planetary carrier with the outer race
toward the carrier and the inner race facing upward
(Fig. 104).
(6) Install the reverse planetary gear carrier into
the input carrier (Fig. 104).
(7) Install the input annulus gear into the input
carrier (Fig. 104).
(8) Install the snap-ring to hold the input annulus
gear into the input carrier (Fig. 104).
SHIFT MECHANISM
DESCRIPTION
The gear shift mechanism provides six shift posi-
tions which are:
²Park (P)
²Reverse (R)
²Neutral (N)
²Drive (D)
²Manual second (2)
²Manual low (1)
OPERATION
MANUAL LOW (1) range provides FIRST gear
only. Overrun braking is also provided in this range.
MANUAL SECOND (2) range provides FIRST and
SECOND gear only.
DRIVE range provides FIRST, SECOND, THIRD
and OVERDRIVE FOURTH and FIFTH gear ranges.
The shift into OVERDRIVE FOURTH and FIFTH
gear range occurs only after the transmission hascompleted the shift into D THIRD gear range. No
further movement of the shift mechanism is required
to complete the 3-4 or 4-5 shifts.
The FOURTH and FIFTH gear upshifts occurs
automatically when the overdrive selector switch is
in the ON position. An upshift to FOURTH and
FIFTH gears may not occur or may be delayed in
some of the possible shift schedules. (Refer to 8 -
ELECTRICAL/ELECTRONIC CONTROL MOD-
ULES/TRANSMISSION CONTROL MODULE -
OPERATION)
REMOVAL
(1) Remove any necessary console parts for access
to shift lever assembly and shifter cables. (Refer to
23 - BODY/INTERIOR/FLOOR CONSOLE -
REMOVAL)
(2) Shift transmission into PARK.
(3) Disconnect the transmission shift cable at shift
lever and shifter assembly bracket (Fig. 105).
(4) Disconnect the park lock cable from the shifter
BTSI lever and the shifter assembly bracket. (Fig.
106)
(5) Disconnect the transfer case shift cable from
the transfer case shift lever pin (Fig. 107), if
equipped.
(6) Remove the clip holding the transfer case shift
cable to the shifter assembly bracket, if equipped.
(7) Remove the transfer case shift cable from the
shifter assembly bracket, if equipped.
(8) Disengage all wiring connectors from the
shifter assembly.
(9) Remove all nuts holding the shifter assembly to
the floor pan (Fig. 108).
Fig. 105 Transmission Shift Cable
1 - SHIFT LEVER PIN
2 - ADJUSTMENT SCREW
3 - SHIFT CABLE
4 - SHIFTER ASSEMBLY BRACKET
WJAUTOMATIC TRANSMISSION - 545RFE 21 - 261
PLANETARY GEARTRAIN (Continued)
Page 1789 of 2199
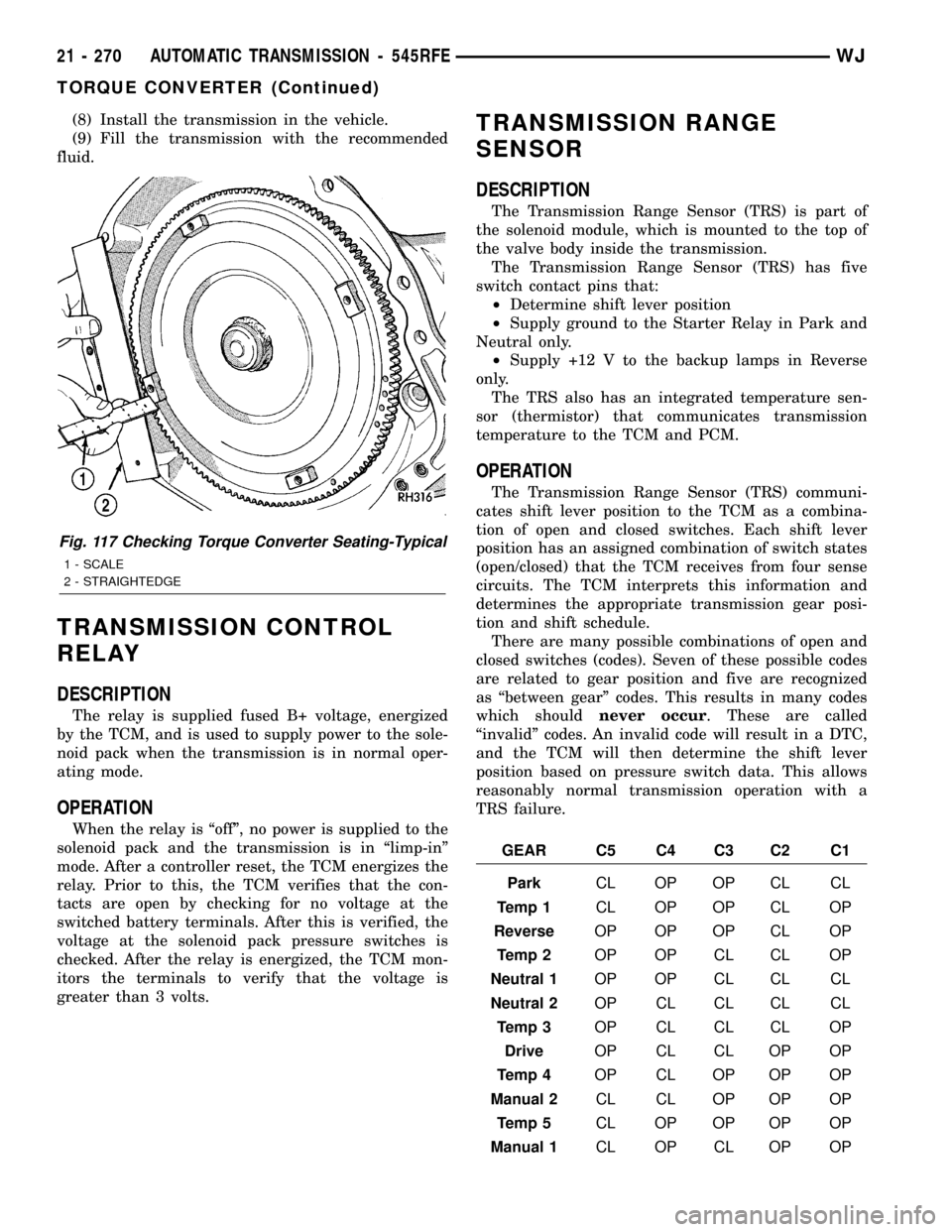
(8) Install the transmission in the vehicle.
(9) Fill the transmission with the recommended
fluid.
TRANSMISSION CONTROL
RELAY
DESCRIPTION
The relay is supplied fused B+ voltage, energized
by the TCM, and is used to supply power to the sole-
noid pack when the transmission is in normal oper-
ating mode.
OPERATION
When the relay is ªoffº, no power is supplied to the
solenoid pack and the transmission is in ªlimp-inº
mode. After a controller reset, the TCM energizes the
relay. Prior to this, the TCM verifies that the con-
tacts are open by checking for no voltage at the
switched battery terminals. After this is verified, the
voltage at the solenoid pack pressure switches is
checked. After the relay is energized, the TCM mon-
itors the terminals to verify that the voltage is
greater than 3 volts.
TRANSMISSION RANGE
SENSOR
DESCRIPTION
The Transmission Range Sensor (TRS) is part of
the solenoid module, which is mounted to the top of
the valve body inside the transmission.
The Transmission Range Sensor (TRS) has five
switch contact pins that:
²Determine shift lever position
²Supply ground to the Starter Relay in Park and
Neutral only.
²Supply +12 V to the backup lamps in Reverse
only.
The TRS also has an integrated temperature sen-
sor (thermistor) that communicates transmission
temperature to the TCM and PCM.
OPERATION
The Transmission Range Sensor (TRS) communi-
cates shift lever position to the TCM as a combina-
tion of open and closed switches. Each shift lever
position has an assigned combination of switch states
(open/closed) that the TCM receives from four sense
circuits. The TCM interprets this information and
determines the appropriate transmission gear posi-
tion and shift schedule.
There are many possible combinations of open and
closed switches (codes). Seven of these possible codes
are related to gear position and five are recognized
as ªbetween gearº codes. This results in many codes
which shouldnever occur. These are called
ªinvalidº codes. An invalid code will result in a DTC,
and the TCM will then determine the shift lever
position based on pressure switch data. This allows
reasonably normal transmission operation with a
TRS failure.
GEAR C5 C4 C3 C2 C1
ParkCL OP OP CL CL
Temp 1CL OP OP CL OP
ReverseOP OP OP CL OP
Temp 2OP OP CL CL OP
Neutral 1OP OP CL CL CL
Neutral 2OP CL CL CL CL
Temp 3OP CL CL CL OP
DriveOP CL CL OP OP
Temp 4OP CL OP OP OP
Manual 2CL CL OP OP OP
Temp 5CL OP OP OP OP
Manual 1CL OP CL OP OP
Fig. 117 Checking Torque Converter Seating-Typical
1 - SCALE
2 - STRAIGHTEDGE
21 - 270 AUTOMATIC TRANSMISSION - 545RFEWJ
TORQUE CONVERTER (Continued)
Page 2108 of 2199
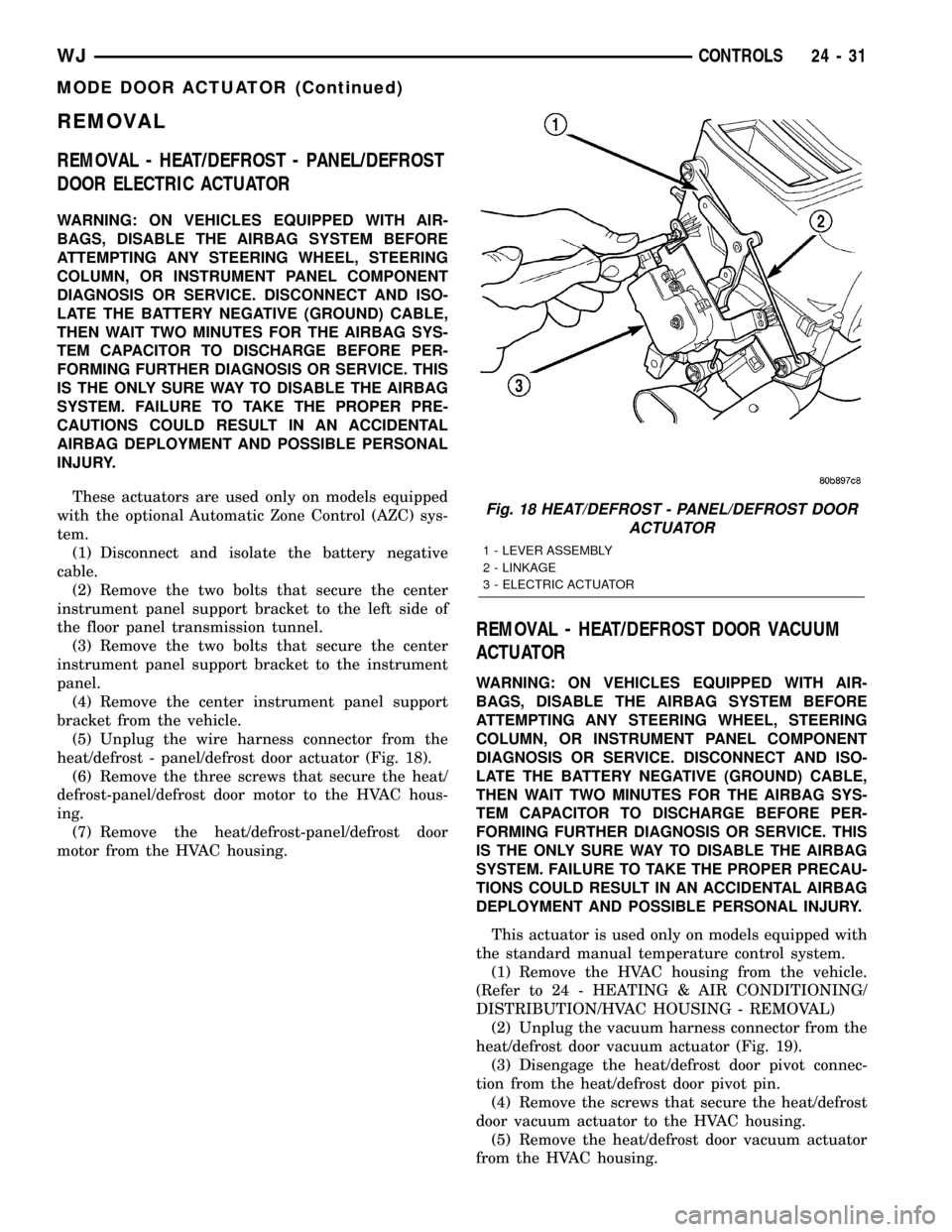
REMOVAL
REMOVAL - HEAT/DEFROST - PANEL/DEFROST
DOOR ELECTRIC ACTUATOR
WARNING: ON VEHICLES EQUIPPED WITH AIR-
BAGS, DISABLE THE AIRBAG SYSTEM BEFORE
ATTEMPTING ANY STEERING WHEEL, STEERING
COLUMN, OR INSTRUMENT PANEL COMPONENT
DIAGNOSIS OR SERVICE. DISCONNECT AND ISO-
LATE THE BATTERY NEGATIVE (GROUND) CABLE,
THEN WAIT TWO MINUTES FOR THE AIRBAG SYS-
TEM CAPACITOR TO DISCHARGE BEFORE PER-
FORMING FURTHER DIAGNOSIS OR SERVICE. THIS
IS THE ONLY SURE WAY TO DISABLE THE AIRBAG
SYSTEM. FAILURE TO TAKE THE PROPER PRE-
CAUTIONS COULD RESULT IN AN ACCIDENTAL
AIRBAG DEPLOYMENT AND POSSIBLE PERSONAL
INJURY.
These actuators are used only on models equipped
with the optional Automatic Zone Control (AZC) sys-
tem.
(1) Disconnect and isolate the battery negative
cable.
(2) Remove the two bolts that secure the center
instrument panel support bracket to the left side of
the floor panel transmission tunnel.
(3) Remove the two bolts that secure the center
instrument panel support bracket to the instrument
panel.
(4) Remove the center instrument panel support
bracket from the vehicle.
(5) Unplug the wire harness connector from the
heat/defrost - panel/defrost door actuator (Fig. 18).
(6) Remove the three screws that secure the heat/
defrost-panel/defrost door motor to the HVAC hous-
ing.
(7) Remove the heat/defrost-panel/defrost door
motor from the HVAC housing.
REMOVAL - HEAT/DEFROST DOOR VACUUM
ACTUATOR
WARNING: ON VEHICLES EQUIPPED WITH AIR-
BAGS, DISABLE THE AIRBAG SYSTEM BEFORE
ATTEMPTING ANY STEERING WHEEL, STEERING
COLUMN, OR INSTRUMENT PANEL COMPONENT
DIAGNOSIS OR SERVICE. DISCONNECT AND ISO-
LATE THE BATTERY NEGATIVE (GROUND) CABLE,
THEN WAIT TWO MINUTES FOR THE AIRBAG SYS-
TEM CAPACITOR TO DISCHARGE BEFORE PER-
FORMING FURTHER DIAGNOSIS OR SERVICE. THIS
IS THE ONLY SURE WAY TO DISABLE THE AIRBAG
SYSTEM. FAILURE TO TAKE THE PROPER PRECAU-
TIONS COULD RESULT IN AN ACCIDENTAL AIRBAG
DEPLOYMENT AND POSSIBLE PERSONAL INJURY.
This actuator is used only on models equipped with
the standard manual temperature control system.
(1) Remove the HVAC housing from the vehicle.
(Refer to 24 - HEATING & AIR CONDITIONING/
DISTRIBUTION/HVAC HOUSING - REMOVAL)
(2) Unplug the vacuum harness connector from the
heat/defrost door vacuum actuator (Fig. 19).
(3) Disengage the heat/defrost door pivot connec-
tion from the heat/defrost door pivot pin.
(4) Remove the screws that secure the heat/defrost
door vacuum actuator to the HVAC housing.
(5) Remove the heat/defrost door vacuum actuator
from the HVAC housing.
Fig. 18 HEAT/DEFROST - PANEL/DEFROST DOOR
ACTUATOR
1 - LEVER ASSEMBLY
2 - LINKAGE
3 - ELECTRIC ACTUATOR
WJCONTROLS 24 - 31
MODE DOOR ACTUATOR (Continued)
Page 2109 of 2199
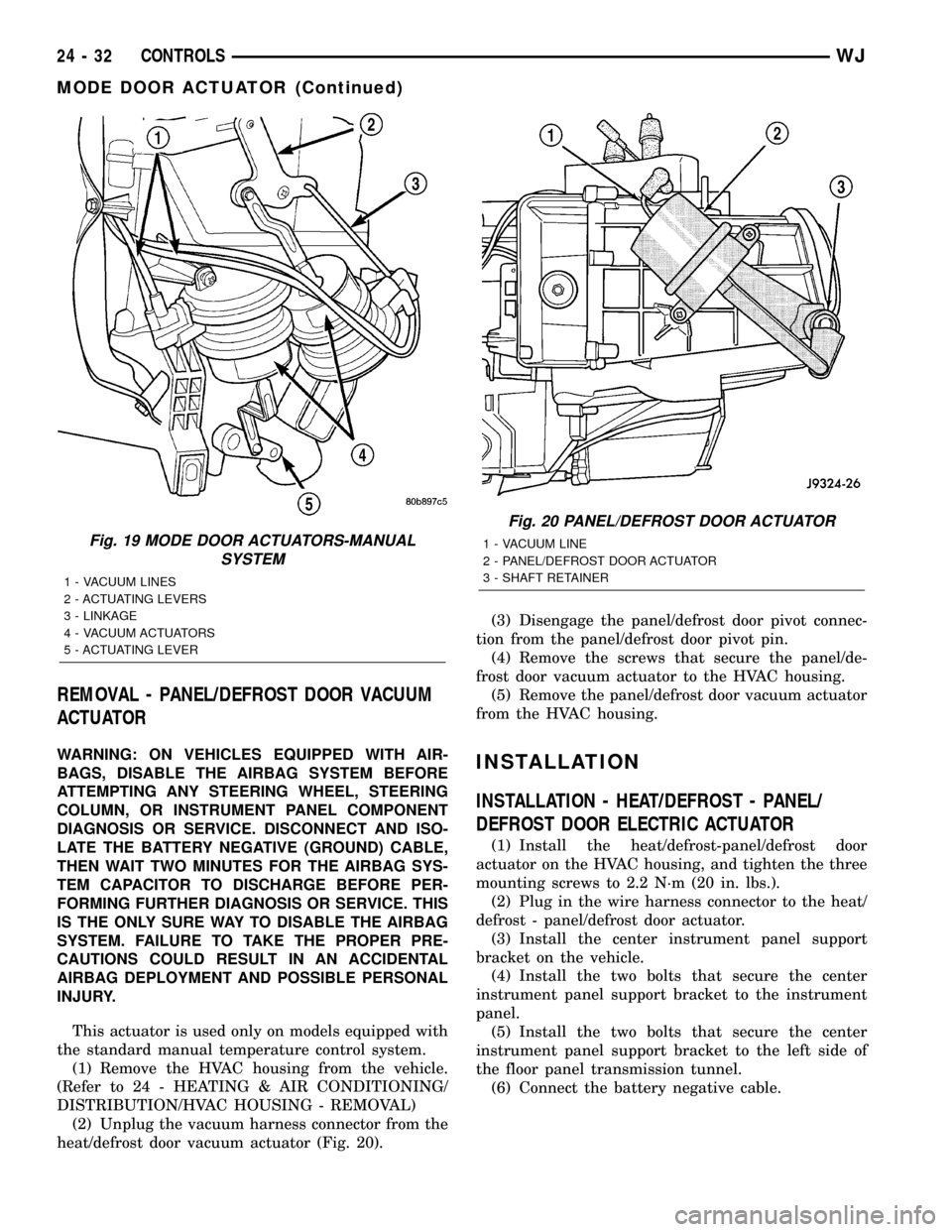
REMOVAL - PANEL/DEFROST DOOR VACUUM
ACTUATOR
WARNING: ON VEHICLES EQUIPPED WITH AIR-
BAGS, DISABLE THE AIRBAG SYSTEM BEFORE
ATTEMPTING ANY STEERING WHEEL, STEERING
COLUMN, OR INSTRUMENT PANEL COMPONENT
DIAGNOSIS OR SERVICE. DISCONNECT AND ISO-
LATE THE BATTERY NEGATIVE (GROUND) CABLE,
THEN WAIT TWO MINUTES FOR THE AIRBAG SYS-
TEM CAPACITOR TO DISCHARGE BEFORE PER-
FORMING FURTHER DIAGNOSIS OR SERVICE. THIS
IS THE ONLY SURE WAY TO DISABLE THE AIRBAG
SYSTEM. FAILURE TO TAKE THE PROPER PRE-
CAUTIONS COULD RESULT IN AN ACCIDENTAL
AIRBAG DEPLOYMENT AND POSSIBLE PERSONAL
INJURY.
This actuator is used only on models equipped with
the standard manual temperature control system.
(1) Remove the HVAC housing from the vehicle.
(Refer to 24 - HEATING & AIR CONDITIONING/
DISTRIBUTION/HVAC HOUSING - REMOVAL)
(2) Unplug the vacuum harness connector from the
heat/defrost door vacuum actuator (Fig. 20).(3) Disengage the panel/defrost door pivot connec-
tion from the panel/defrost door pivot pin.
(4) Remove the screws that secure the panel/de-
frost door vacuum actuator to the HVAC housing.
(5) Remove the panel/defrost door vacuum actuator
from the HVAC housing.INSTALLATION
INSTALLATION - HEAT/DEFROST - PANEL/
DEFROST DOOR ELECTRIC ACTUATOR
(1) Install the heat/defrost-panel/defrost door
actuator on the HVAC housing, and tighten the three
mounting screws to 2.2 N´m (20 in. lbs.).
(2) Plug in the wire harness connector to the heat/
defrost - panel/defrost door actuator.
(3) Install the center instrument panel support
bracket on the vehicle.
(4) Install the two bolts that secure the center
instrument panel support bracket to the instrument
panel.
(5) Install the two bolts that secure the center
instrument panel support bracket to the left side of
the floor panel transmission tunnel.
(6) Connect the battery negative cable.
Fig. 19 MODE DOOR ACTUATORS-MANUAL
SYSTEM
1 - VACUUM LINES
2 - ACTUATING LEVERS
3 - LINKAGE
4 - VACUUM ACTUATORS
5 - ACTUATING LEVER
Fig. 20 PANEL/DEFROST DOOR ACTUATOR
1 - VACUUM LINE
2 - PANEL/DEFROST DOOR ACTUATOR
3 - SHAFT RETAINER
24 - 32 CONTROLSWJ
MODE DOOR ACTUATOR (Continued)
Page 2110 of 2199
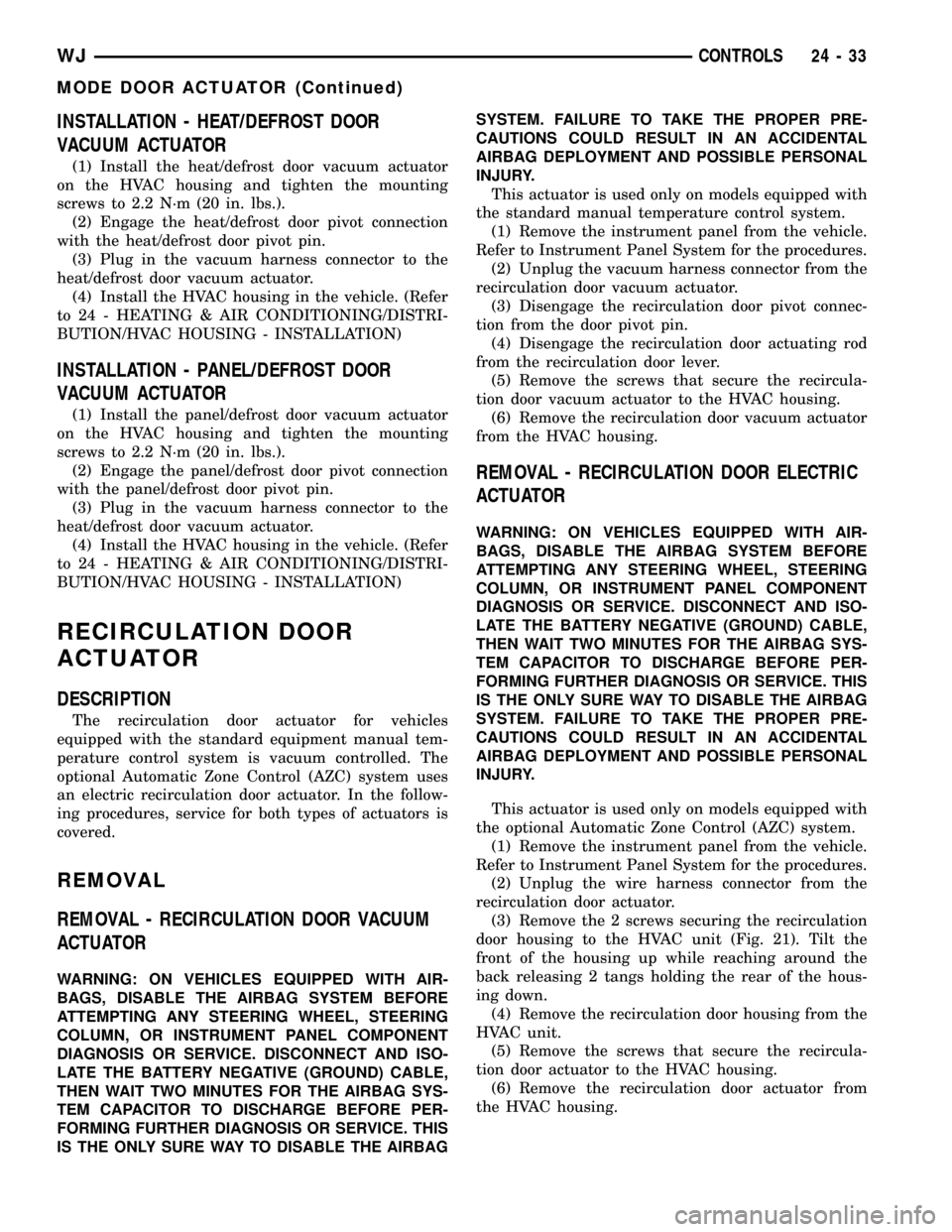
INSTALLATION - HEAT/DEFROST DOOR
VACUUM ACTUATOR
(1) Install the heat/defrost door vacuum actuator
on the HVAC housing and tighten the mounting
screws to 2.2 N´m (20 in. lbs.).
(2) Engage the heat/defrost door pivot connection
with the heat/defrost door pivot pin.
(3) Plug in the vacuum harness connector to the
heat/defrost door vacuum actuator.
(4) Install the HVAC housing in the vehicle. (Refer
to 24 - HEATING & AIR CONDITIONING/DISTRI-
BUTION/HVAC HOUSING - INSTALLATION)
INSTALLATION - PANEL/DEFROST DOOR
VACUUM ACTUATOR
(1) Install the panel/defrost door vacuum actuator
on the HVAC housing and tighten the mounting
screws to 2.2 N´m (20 in. lbs.).
(2) Engage the panel/defrost door pivot connection
with the panel/defrost door pivot pin.
(3) Plug in the vacuum harness connector to the
heat/defrost door vacuum actuator.
(4) Install the HVAC housing in the vehicle. (Refer
to 24 - HEATING & AIR CONDITIONING/DISTRI-
BUTION/HVAC HOUSING - INSTALLATION)
RECIRCULATION DOOR
ACTUATOR
DESCRIPTION
The recirculation door actuator for vehicles
equipped with the standard equipment manual tem-
perature control system is vacuum controlled. The
optional Automatic Zone Control (AZC) system uses
an electric recirculation door actuator. In the follow-
ing procedures, service for both types of actuators is
covered.
REMOVAL
REMOVAL - RECIRCULATION DOOR VACUUM
ACTUATOR
WARNING: ON VEHICLES EQUIPPED WITH AIR-
BAGS, DISABLE THE AIRBAG SYSTEM BEFORE
ATTEMPTING ANY STEERING WHEEL, STEERING
COLUMN, OR INSTRUMENT PANEL COMPONENT
DIAGNOSIS OR SERVICE. DISCONNECT AND ISO-
LATE THE BATTERY NEGATIVE (GROUND) CABLE,
THEN WAIT TWO MINUTES FOR THE AIRBAG SYS-
TEM CAPACITOR TO DISCHARGE BEFORE PER-
FORMING FURTHER DIAGNOSIS OR SERVICE. THIS
IS THE ONLY SURE WAY TO DISABLE THE AIRBAGSYSTEM. FAILURE TO TAKE THE PROPER PRE-
CAUTIONS COULD RESULT IN AN ACCIDENTAL
AIRBAG DEPLOYMENT AND POSSIBLE PERSONAL
INJURY.
This actuator is used only on models equipped with
the standard manual temperature control system.
(1) Remove the instrument panel from the vehicle.
Refer to Instrument Panel System for the procedures.
(2) Unplug the vacuum harness connector from the
recirculation door vacuum actuator.
(3) Disengage the recirculation door pivot connec-
tion from the door pivot pin.
(4) Disengage the recirculation door actuating rod
from the recirculation door lever.
(5) Remove the screws that secure the recircula-
tion door vacuum actuator to the HVAC housing.
(6) Remove the recirculation door vacuum actuator
from the HVAC housing.
REMOVAL - RECIRCULATION DOOR ELECTRIC
ACTUATOR
WARNING: ON VEHICLES EQUIPPED WITH AIR-
BAGS, DISABLE THE AIRBAG SYSTEM BEFORE
ATTEMPTING ANY STEERING WHEEL, STEERING
COLUMN, OR INSTRUMENT PANEL COMPONENT
DIAGNOSIS OR SERVICE. DISCONNECT AND ISO-
LATE THE BATTERY NEGATIVE (GROUND) CABLE,
THEN WAIT TWO MINUTES FOR THE AIRBAG SYS-
TEM CAPACITOR TO DISCHARGE BEFORE PER-
FORMING FURTHER DIAGNOSIS OR SERVICE. THIS
IS THE ONLY SURE WAY TO DISABLE THE AIRBAG
SYSTEM. FAILURE TO TAKE THE PROPER PRE-
CAUTIONS COULD RESULT IN AN ACCIDENTAL
AIRBAG DEPLOYMENT AND POSSIBLE PERSONAL
INJURY.
This actuator is used only on models equipped with
the optional Automatic Zone Control (AZC) system.
(1) Remove the instrument panel from the vehicle.
Refer to Instrument Panel System for the procedures.
(2) Unplug the wire harness connector from the
recirculation door actuator.
(3) Remove the 2 screws securing the recirculation
door housing to the HVAC unit (Fig. 21). Tilt the
front of the housing up while reaching around the
back releasing 2 tangs holding the rear of the hous-
ing down.
(4) Remove the recirculation door housing from the
HVAC unit.
(5) Remove the screws that secure the recircula-
tion door actuator to the HVAC housing.
(6) Remove the recirculation door actuator from
the HVAC housing.
WJCONTROLS 24 - 33
MODE DOOR ACTUATOR (Continued)
Page 2122 of 2199
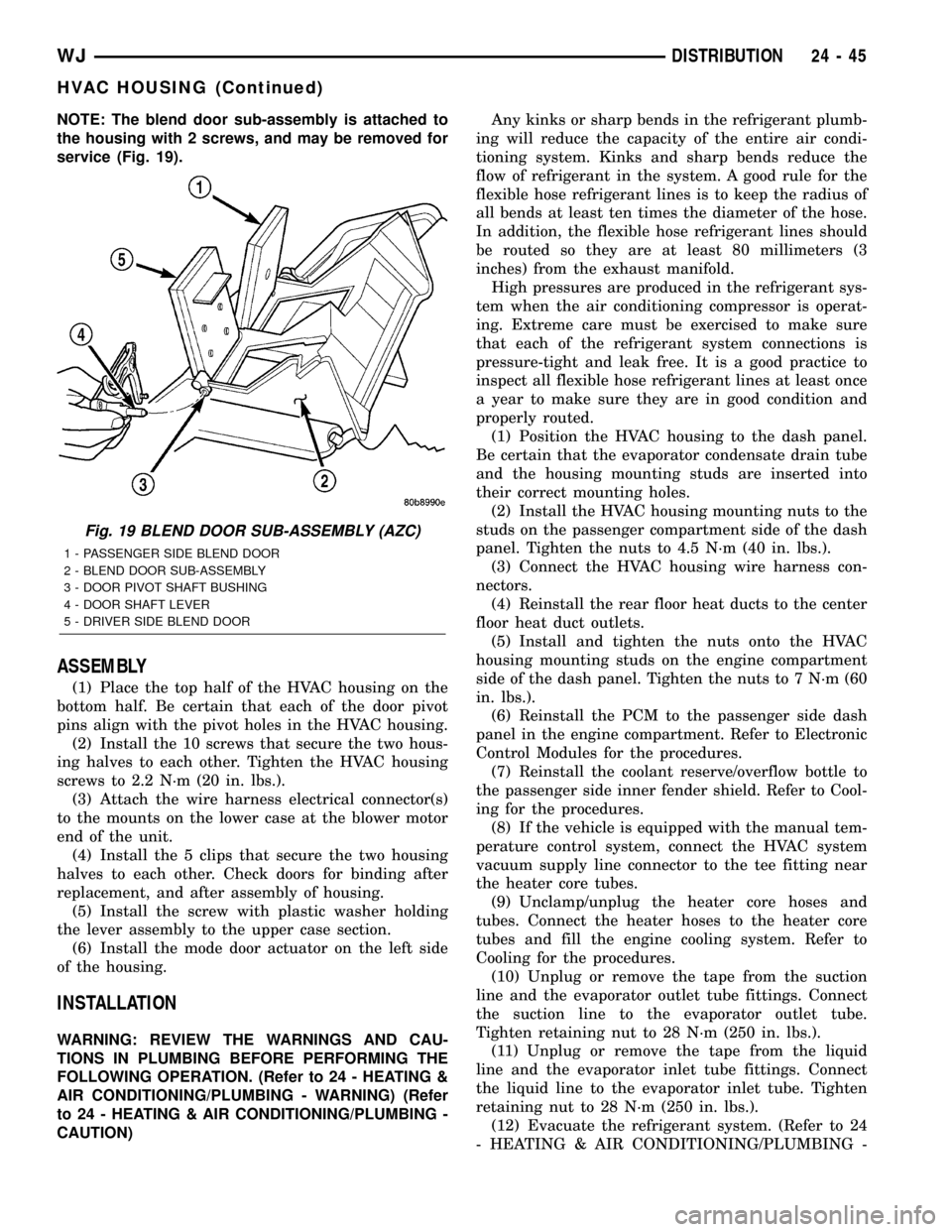
NOTE: The blend door sub-assembly is attached to
the housing with 2 screws, and may be removed for
service (Fig. 19).
ASSEMBLY
(1) Place the top half of the HVAC housing on the
bottom half. Be certain that each of the door pivot
pins align with the pivot holes in the HVAC housing.
(2) Install the 10 screws that secure the two hous-
ing halves to each other. Tighten the HVAC housing
screws to 2.2 N´m (20 in. lbs.).
(3) Attach the wire harness electrical connector(s)
to the mounts on the lower case at the blower motor
end of the unit.
(4) Install the 5 clips that secure the two housing
halves to each other. Check doors for binding after
replacement, and after assembly of housing.
(5) Install the screw with plastic washer holding
the lever assembly to the upper case section.
(6) Install the mode door actuator on the left side
of the housing.
INSTALLATION
WARNING: REVIEW THE WARNINGS AND CAU-
TIONS IN PLUMBING BEFORE PERFORMING THE
FOLLOWING OPERATION. (Refer to 24 - HEATING &
AIR CONDITIONING/PLUMBING - WARNING) (Refer
to 24 - HEATING & AIR CONDITIONING/PLUMBING -
CAUTION)Any kinks or sharp bends in the refrigerant plumb-
ing will reduce the capacity of the entire air condi-
tioning system. Kinks and sharp bends reduce the
flow of refrigerant in the system. A good rule for the
flexible hose refrigerant lines is to keep the radius of
all bends at least ten times the diameter of the hose.
In addition, the flexible hose refrigerant lines should
be routed so they are at least 80 millimeters (3
inches) from the exhaust manifold.
High pressures are produced in the refrigerant sys-
tem when the air conditioning compressor is operat-
ing. Extreme care must be exercised to make sure
that each of the refrigerant system connections is
pressure-tight and leak free. It is a good practice to
inspect all flexible hose refrigerant lines at least once
a year to make sure they are in good condition and
properly routed.
(1) Position the HVAC housing to the dash panel.
Be certain that the evaporator condensate drain tube
and the housing mounting studs are inserted into
their correct mounting holes.
(2) Install the HVAC housing mounting nuts to the
studs on the passenger compartment side of the dash
panel. Tighten the nuts to 4.5 N´m (40 in. lbs.).
(3) Connect the HVAC housing wire harness con-
nectors.
(4) Reinstall the rear floor heat ducts to the center
floor heat duct outlets.
(5) Install and tighten the nuts onto the HVAC
housing mounting studs on the engine compartment
side of the dash panel. Tighten the nuts to 7 N´m (60
in. lbs.).
(6) Reinstall the PCM to the passenger side dash
panel in the engine compartment. Refer to Electronic
Control Modules for the procedures.
(7) Reinstall the coolant reserve/overflow bottle to
the passenger side inner fender shield. Refer to Cool-
ing for the procedures.
(8) If the vehicle is equipped with the manual tem-
perature control system, connect the HVAC system
vacuum supply line connector to the tee fitting near
the heater core tubes.
(9) Unclamp/unplug the heater core hoses and
tubes. Connect the heater hoses to the heater core
tubes and fill the engine cooling system. Refer to
Cooling for the procedures.
(10) Unplug or remove the tape from the suction
line and the evaporator outlet tube fittings. Connect
the suction line to the evaporator outlet tube.
Tighten retaining nut to 28 N´m (250 in. lbs.).
(11) Unplug or remove the tape from the liquid
line and the evaporator inlet tube fittings. Connect
the liquid line to the evaporator inlet tube. Tighten
retaining nut to 28 N´m (250 in. lbs.).
(12) Evacuate the refrigerant system. (Refer to 24
- HEATING & AIR CONDITIONING/PLUMBING -
Fig. 19 BLEND DOOR SUB-ASSEMBLY (AZC)
1 - PASSENGER SIDE BLEND DOOR
2 - BLEND DOOR SUB-ASSEMBLY
3 - DOOR PIVOT SHAFT BUSHING
4 - DOOR SHAFT LEVER
5 - DRIVER SIDE BLEND DOOR
WJDISTRIBUTION 24 - 45
HVAC HOUSING (Continued)