spec JEEP GRAND CHEROKEE 2003 WJ / 2.G Workshop Manual
[x] Cancel search | Manufacturer: JEEP, Model Year: 2003, Model line: GRAND CHEROKEE, Model: JEEP GRAND CHEROKEE 2003 WJ / 2.GPages: 2199, PDF Size: 76.01 MB
Page 1588 of 2199
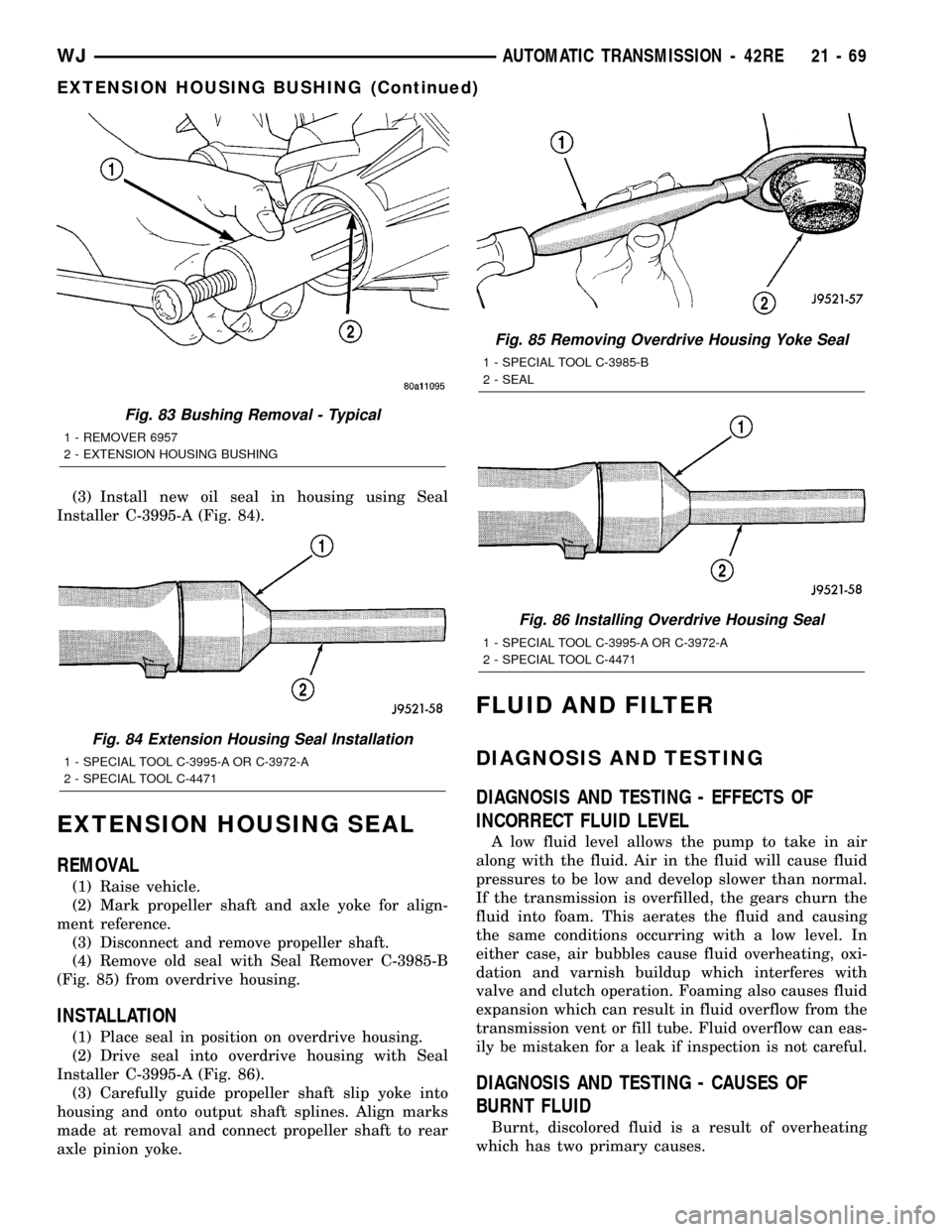
(3) Install new oil seal in housing using Seal
Installer C-3995-A (Fig. 84).
EXTENSION HOUSING SEAL
REMOVAL
(1) Raise vehicle.
(2) Mark propeller shaft and axle yoke for align-
ment reference.
(3) Disconnect and remove propeller shaft.
(4) Remove old seal with Seal Remover C-3985-B
(Fig. 85) from overdrive housing.
INSTALLATION
(1) Place seal in position on overdrive housing.
(2) Drive seal into overdrive housing with Seal
Installer C-3995-A (Fig. 86).
(3) Carefully guide propeller shaft slip yoke into
housing and onto output shaft splines. Align marks
made at removal and connect propeller shaft to rear
axle pinion yoke.
FLUID AND FILTER
DIAGNOSIS AND TESTING
DIAGNOSIS AND TESTING - EFFECTS OF
INCORRECT FLUID LEVEL
A low fluid level allows the pump to take in air
along with the fluid. Air in the fluid will cause fluid
pressures to be low and develop slower than normal.
If the transmission is overfilled, the gears churn the
fluid into foam. This aerates the fluid and causing
the same conditions occurring with a low level. In
either case, air bubbles cause fluid overheating, oxi-
dation and varnish buildup which interferes with
valve and clutch operation. Foaming also causes fluid
expansion which can result in fluid overflow from the
transmission vent or fill tube. Fluid overflow can eas-
ily be mistaken for a leak if inspection is not careful.
DIAGNOSIS AND TESTING - CAUSES OF
BURNT FLUID
Burnt, discolored fluid is a result of overheating
which has two primary causes.
Fig. 83 Bushing Removal - Typical
1 - REMOVER 6957
2 - EXTENSION HOUSING BUSHING
Fig. 84 Extension Housing Seal Installation
1 - SPECIAL TOOL C-3995-A OR C-3972-A
2 - SPECIAL TOOL C-4471
Fig. 85 Removing Overdrive Housing Yoke Seal
1 - SPECIAL TOOL C-3985-B
2 - SEAL
Fig. 86 Installing Overdrive Housing Seal
1 - SPECIAL TOOL C-3995-A OR C-3972-A
2 - SPECIAL TOOL C-4471
WJAUTOMATIC TRANSMISSION - 42RE 21 - 69
EXTENSION HOUSING BUSHING (Continued)
Page 1591 of 2199
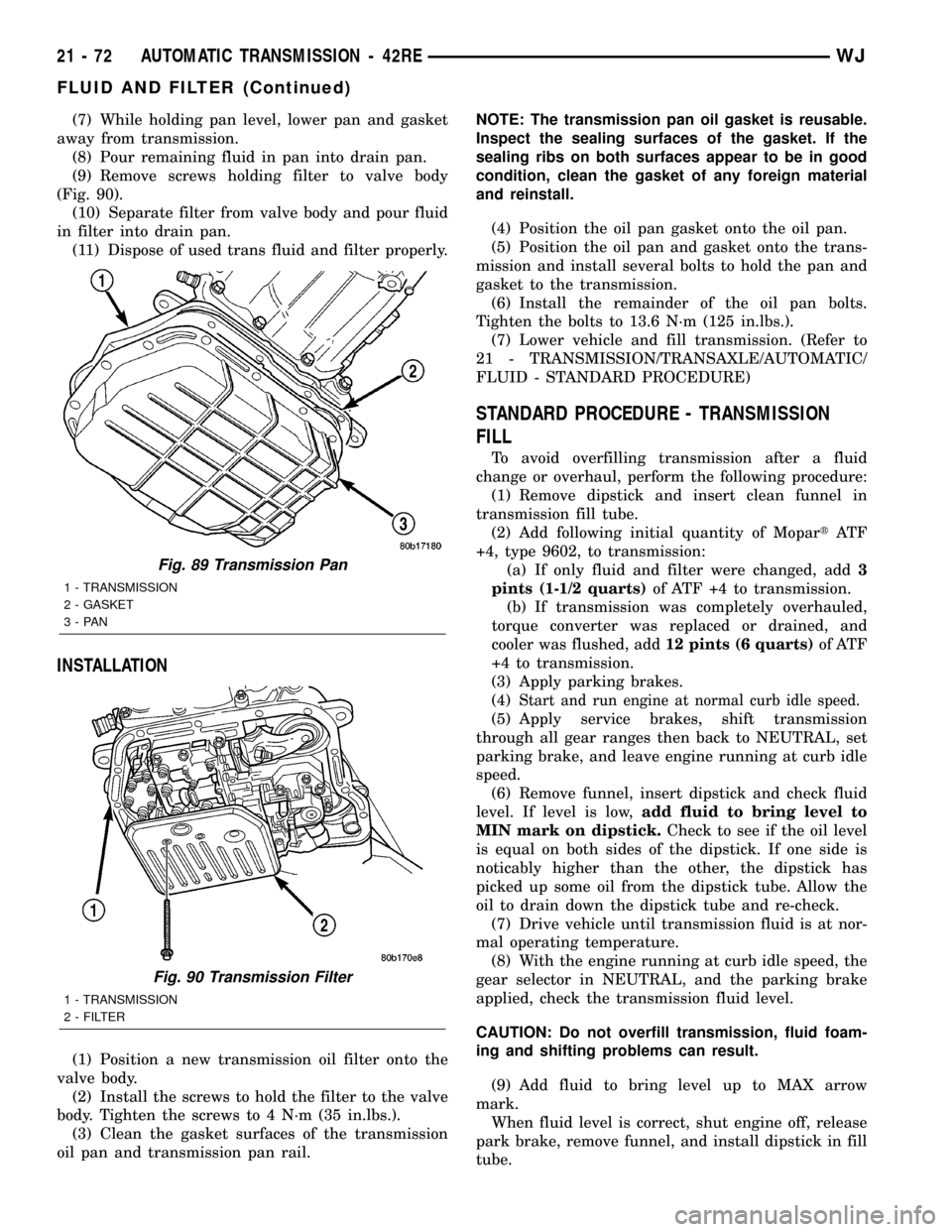
(7) While holding pan level, lower pan and gasket
away from transmission.
(8) Pour remaining fluid in pan into drain pan.
(9) Remove screws holding filter to valve body
(Fig. 90).
(10) Separate filter from valve body and pour fluid
in filter into drain pan.
(11) Dispose of used trans fluid and filter properly.
INSTALLATION
(1) Position a new transmission oil filter onto the
valve body.
(2) Install the screws to hold the filter to the valve
body. Tighten the screws to 4 N´m (35 in.lbs.).
(3) Clean the gasket surfaces of the transmission
oil pan and transmission pan rail.NOTE: The transmission pan oil gasket is reusable.
Inspect the sealing surfaces of the gasket. If the
sealing ribs on both surfaces appear to be in good
condition, clean the gasket of any foreign material
and reinstall.
(4) Position the oil pan gasket onto the oil pan.
(5) Position the oil pan and gasket onto the trans-
mission and install several bolts to hold the pan and
gasket to the transmission.
(6) Install the remainder of the oil pan bolts.
Tighten the bolts to 13.6 N´m (125 in.lbs.).
(7) Lower vehicle and fill transmission. (Refer to
21 - TRANSMISSION/TRANSAXLE/AUTOMATIC/
FLUID - STANDARD PROCEDURE)
STANDARD PROCEDURE - TRANSMISSION
FILL
To avoid overfilling transmission after a fluid
change or overhaul, perform the following procedure:
(1) Remove dipstick and insert clean funnel in
transmission fill tube.
(2) Add following initial quantity of MopartAT F
+4, type 9602, to transmission:
(a) If only fluid and filter were changed, add3
pints (1-1/2 quarts)of ATF +4 to transmission.
(b) If transmission was completely overhauled,
torque converter was replaced or drained, and
cooler was flushed, add12 pints (6 quarts)of ATF
+4 to transmission.
(3) Apply parking brakes.
(4)
Start and run engine at normal curb idle speed.
(5) Apply service brakes, shift transmission
through all gear ranges then back to NEUTRAL, set
parking brake, and leave engine running at curb idle
speed.
(6) Remove funnel, insert dipstick and check fluid
level. If level is low,add fluid to bring level to
MIN mark on dipstick.Check to see if the oil level
is equal on both sides of the dipstick. If one side is
noticably higher than the other, the dipstick has
picked up some oil from the dipstick tube. Allow the
oil to drain down the dipstick tube and re-check.
(7) Drive vehicle until transmission fluid is at nor-
mal operating temperature.
(8) With the engine running at curb idle speed, the
gear selector in NEUTRAL, and the parking brake
applied, check the transmission fluid level.
CAUTION: Do not overfill transmission, fluid foam-
ing and shifting problems can result.
(9) Add fluid to bring level up to MAX arrow
mark.
When fluid level is correct, shut engine off, release
park brake, remove funnel, and install dipstick in fill
tube.
Fig. 89 Transmission Pan
1 - TRANSMISSION
2 - GASKET
3-PAN
Fig. 90 Transmission Filter
1 - TRANSMISSION
2 - FILTER
21 - 72 AUTOMATIC TRANSMISSION - 42REWJ
FLUID AND FILTER (Continued)
Page 1593 of 2199
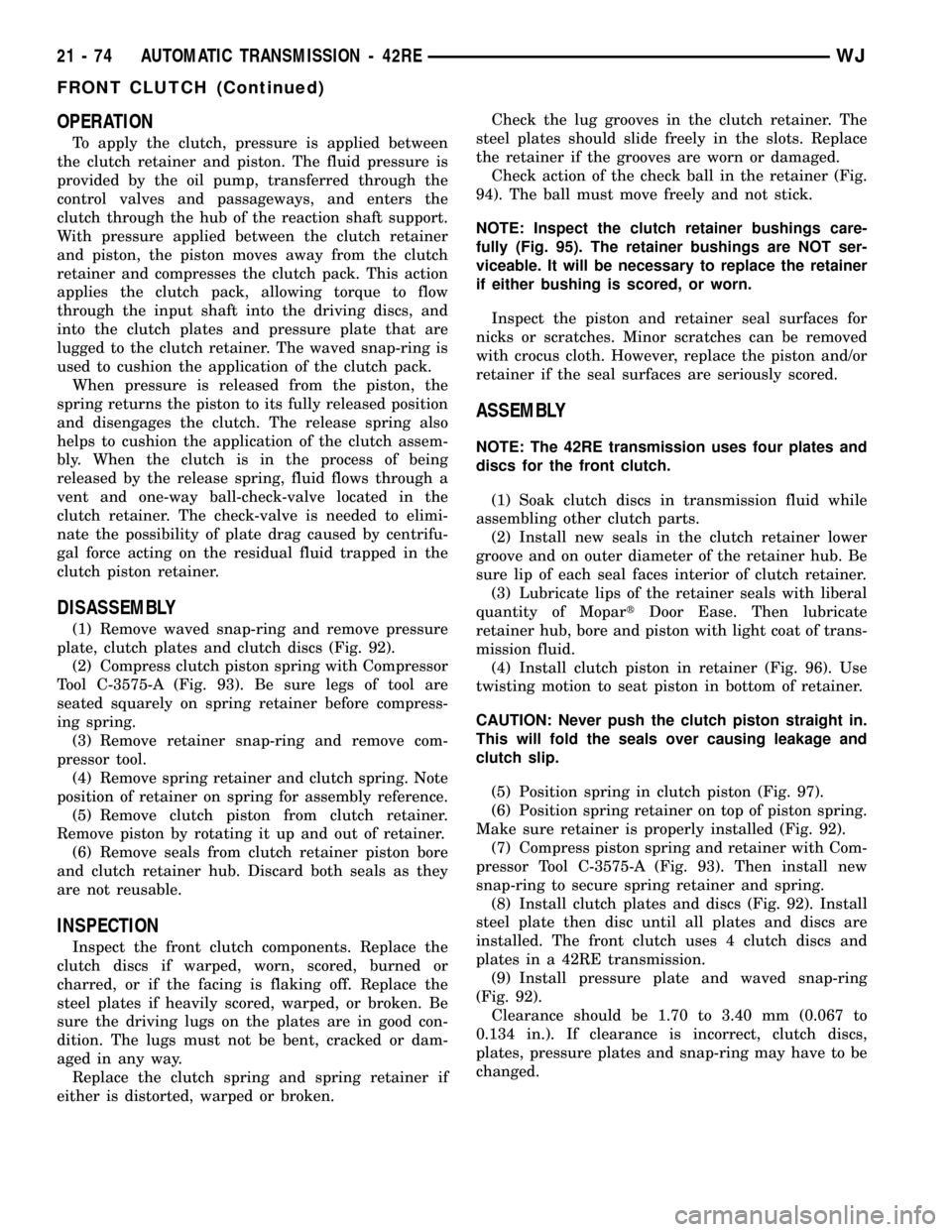
OPERATION
To apply the clutch, pressure is applied between
the clutch retainer and piston. The fluid pressure is
provided by the oil pump, transferred through the
control valves and passageways, and enters the
clutch through the hub of the reaction shaft support.
With pressure applied between the clutch retainer
and piston, the piston moves away from the clutch
retainer and compresses the clutch pack. This action
applies the clutch pack, allowing torque to flow
through the input shaft into the driving discs, and
into the clutch plates and pressure plate that are
lugged to the clutch retainer. The waved snap-ring is
used to cushion the application of the clutch pack.
When pressure is released from the piston, the
spring returns the piston to its fully released position
and disengages the clutch. The release spring also
helps to cushion the application of the clutch assem-
bly. When the clutch is in the process of being
released by the release spring, fluid flows through a
vent and one-way ball-check-valve located in the
clutch retainer. The check-valve is needed to elimi-
nate the possibility of plate drag caused by centrifu-
gal force acting on the residual fluid trapped in the
clutch piston retainer.
DISASSEMBLY
(1) Remove waved snap-ring and remove pressure
plate, clutch plates and clutch discs (Fig. 92).
(2) Compress clutch piston spring with Compressor
Tool C-3575-A (Fig. 93). Be sure legs of tool are
seated squarely on spring retainer before compress-
ing spring.
(3) Remove retainer snap-ring and remove com-
pressor tool.
(4) Remove spring retainer and clutch spring. Note
position of retainer on spring for assembly reference.
(5) Remove clutch piston from clutch retainer.
Remove piston by rotating it up and out of retainer.
(6) Remove seals from clutch retainer piston bore
and clutch retainer hub. Discard both seals as they
are not reusable.
INSPECTION
Inspect the front clutch components. Replace the
clutch discs if warped, worn, scored, burned or
charred, or if the facing is flaking off. Replace the
steel plates if heavily scored, warped, or broken. Be
sure the driving lugs on the plates are in good con-
dition. The lugs must not be bent, cracked or dam-
aged in any way.
Replace the clutch spring and spring retainer if
either is distorted, warped or broken.Check the lug grooves in the clutch retainer. The
steel plates should slide freely in the slots. Replace
the retainer if the grooves are worn or damaged.
Check action of the check ball in the retainer (Fig.
94). The ball must move freely and not stick.
NOTE: Inspect the clutch retainer bushings care-
fully (Fig. 95). The retainer bushings are NOT ser-
viceable. It will be necessary to replace the retainer
if either bushing is scored, or worn.
Inspect the piston and retainer seal surfaces for
nicks or scratches. Minor scratches can be removed
with crocus cloth. However, replace the piston and/or
retainer if the seal surfaces are seriously scored.
ASSEMBLY
NOTE: The 42RE transmission uses four plates and
discs for the front clutch.
(1) Soak clutch discs in transmission fluid while
assembling other clutch parts.
(2) Install new seals in the clutch retainer lower
groove and on outer diameter of the retainer hub. Be
sure lip of each seal faces interior of clutch retainer.
(3) Lubricate lips of the retainer seals with liberal
quantity of MopartDoor Ease. Then lubricate
retainer hub, bore and piston with light coat of trans-
mission fluid.
(4) Install clutch piston in retainer (Fig. 96). Use
twisting motion to seat piston in bottom of retainer.
CAUTION: Never push the clutch piston straight in.
This will fold the seals over causing leakage and
clutch slip.
(5) Position spring in clutch piston (Fig. 97).
(6) Position spring retainer on top of piston spring.
Make sure retainer is properly installed (Fig. 92).
(7) Compress piston spring and retainer with Com-
pressor Tool C-3575-A (Fig. 93). Then install new
snap-ring to secure spring retainer and spring.
(8) Install clutch plates and discs (Fig. 92). Install
steel plate then disc until all plates and discs are
installed. The front clutch uses 4 clutch discs and
plates in a 42RE transmission.
(9) Install pressure plate and waved snap-ring
(Fig. 92).
Clearance should be 1.70 to 3.40 mm (0.067 to
0.134 in.). If clearance is incorrect, clutch discs,
plates, pressure plates and snap-ring may have to be
changed.
21 - 74 AUTOMATIC TRANSMISSION - 42REWJ
FRONT CLUTCH (Continued)
Page 1595 of 2199
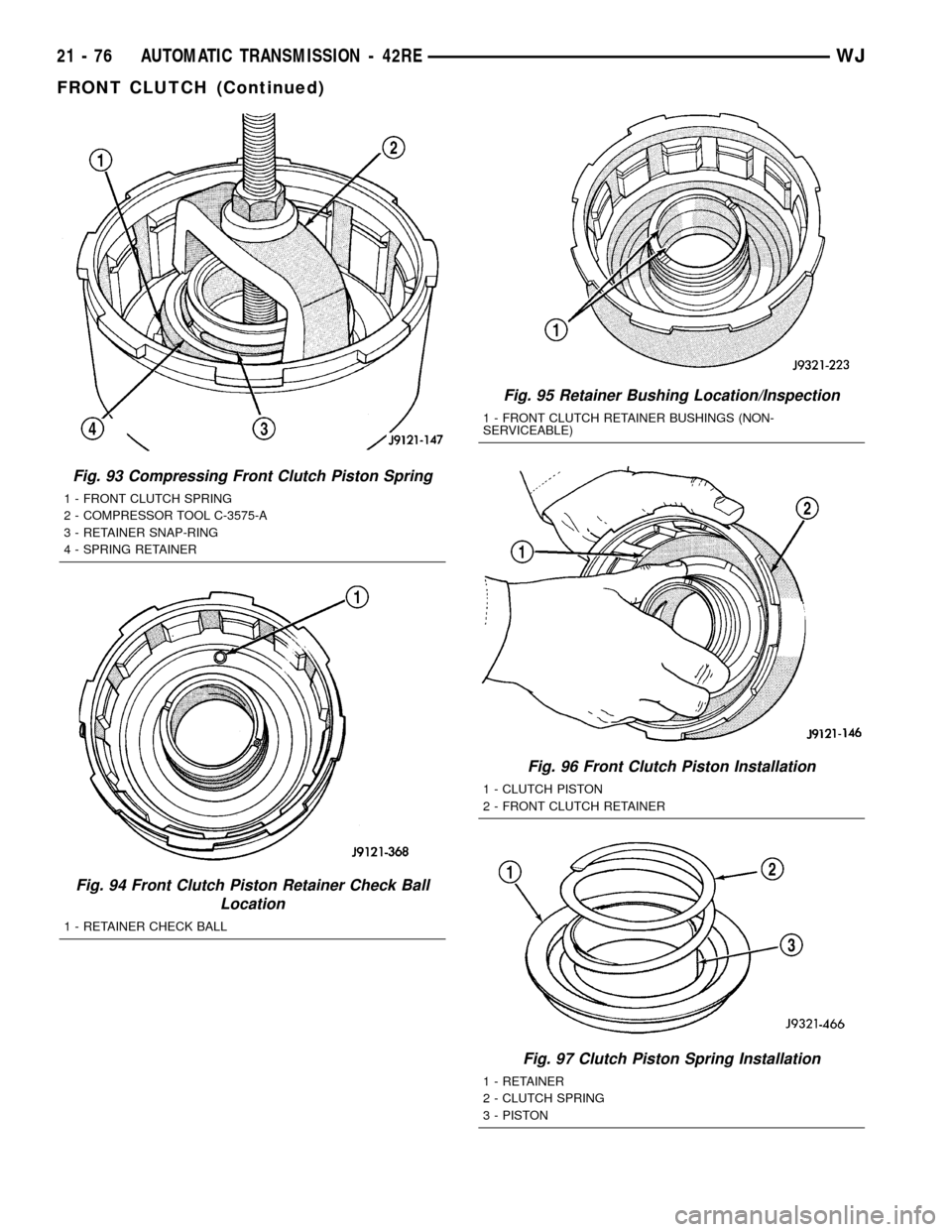
Fig. 93 Compressing Front Clutch Piston Spring
1 - FRONT CLUTCH SPRING
2 - COMPRESSOR TOOL C-3575-A
3 - RETAINER SNAP-RING
4 - SPRING RETAINER
Fig. 94 Front Clutch Piston Retainer Check Ball
Location
1 - RETAINER CHECK BALL
Fig. 95 Retainer Bushing Location/Inspection
1 - FRONT CLUTCH RETAINER BUSHINGS (NON-
SERVICEABLE)
Fig. 96 Front Clutch Piston Installation
1 - CLUTCH PISTON
2 - FRONT CLUTCH RETAINER
Fig. 97 Clutch Piston Spring Installation
1 - RETAINER
2 - CLUTCH SPRING
3 - PISTON
21 - 76 AUTOMATIC TRANSMISSION - 42REWJ
FRONT CLUTCH (Continued)
Page 1596 of 2199
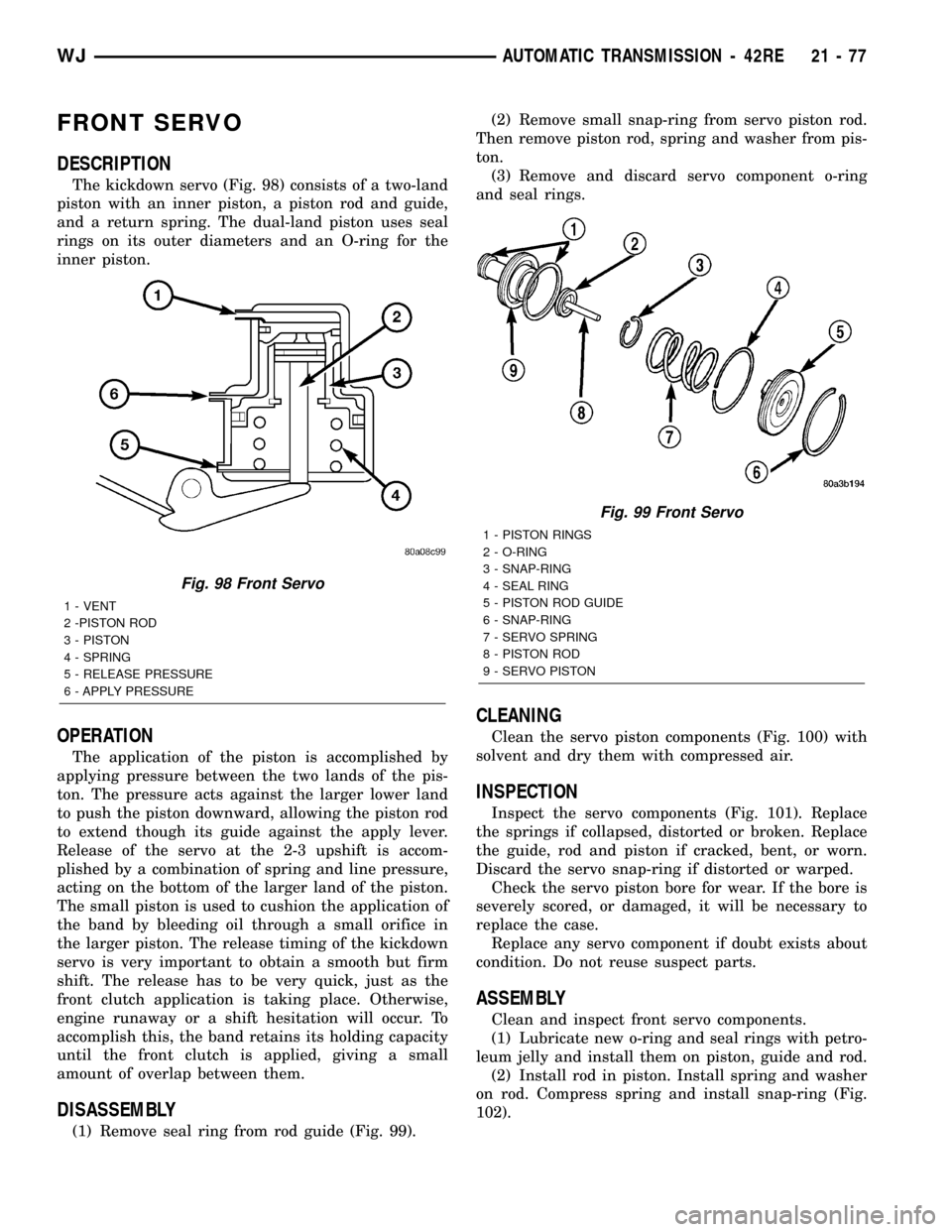
FRONT SERVO
DESCRIPTION
The kickdown servo (Fig. 98) consists of a two-land
piston with an inner piston, a piston rod and guide,
and a return spring. The dual-land piston uses seal
rings on its outer diameters and an O-ring for the
inner piston.
OPERATION
The application of the piston is accomplished by
applying pressure between the two lands of the pis-
ton. The pressure acts against the larger lower land
to push the piston downward, allowing the piston rod
to extend though its guide against the apply lever.
Release of the servo at the 2-3 upshift is accom-
plished by a combination of spring and line pressure,
acting on the bottom of the larger land of the piston.
The small piston is used to cushion the application of
the band by bleeding oil through a small orifice in
the larger piston. The release timing of the kickdown
servo is very important to obtain a smooth but firm
shift. The release has to be very quick, just as the
front clutch application is taking place. Otherwise,
engine runaway or a shift hesitation will occur. To
accomplish this, the band retains its holding capacity
until the front clutch is applied, giving a small
amount of overlap between them.
DISASSEMBLY
(1) Remove seal ring from rod guide (Fig. 99).(2) Remove small snap-ring from servo piston rod.
Then remove piston rod, spring and washer from pis-
ton.
(3) Remove and discard servo component o-ring
and seal rings.
CLEANING
Clean the servo piston components (Fig. 100) with
solvent and dry them with compressed air.
INSPECTION
Inspect the servo components (Fig. 101). Replace
the springs if collapsed, distorted or broken. Replace
the guide, rod and piston if cracked, bent, or worn.
Discard the servo snap-ring if distorted or warped.
Check the servo piston bore for wear. If the bore is
severely scored, or damaged, it will be necessary to
replace the case.
Replace any servo component if doubt exists about
condition. Do not reuse suspect parts.
ASSEMBLY
Clean and inspect front servo components.
(1) Lubricate new o-ring and seal rings with petro-
leum jelly and install them on piston, guide and rod.
(2) Install rod in piston. Install spring and washer
on rod. Compress spring and install snap-ring (Fig.
102).
Fig. 98 Front Servo
1 - VENT
2 -PISTON ROD
3 - PISTON
4 - SPRING
5 - RELEASE PRESSURE
6 - APPLY PRESSURE
Fig. 99 Front Servo
1 - PISTON RINGS
2 - O-RING
3 - SNAP-RING
4 - SEAL RING
5 - PISTON ROD GUIDE
6 - SNAP-RING
7 - SERVO SPRING
8 - PISTON ROD
9 - SERVO PISTON
WJAUTOMATIC TRANSMISSION - 42RE 21 - 77
Page 1601 of 2199
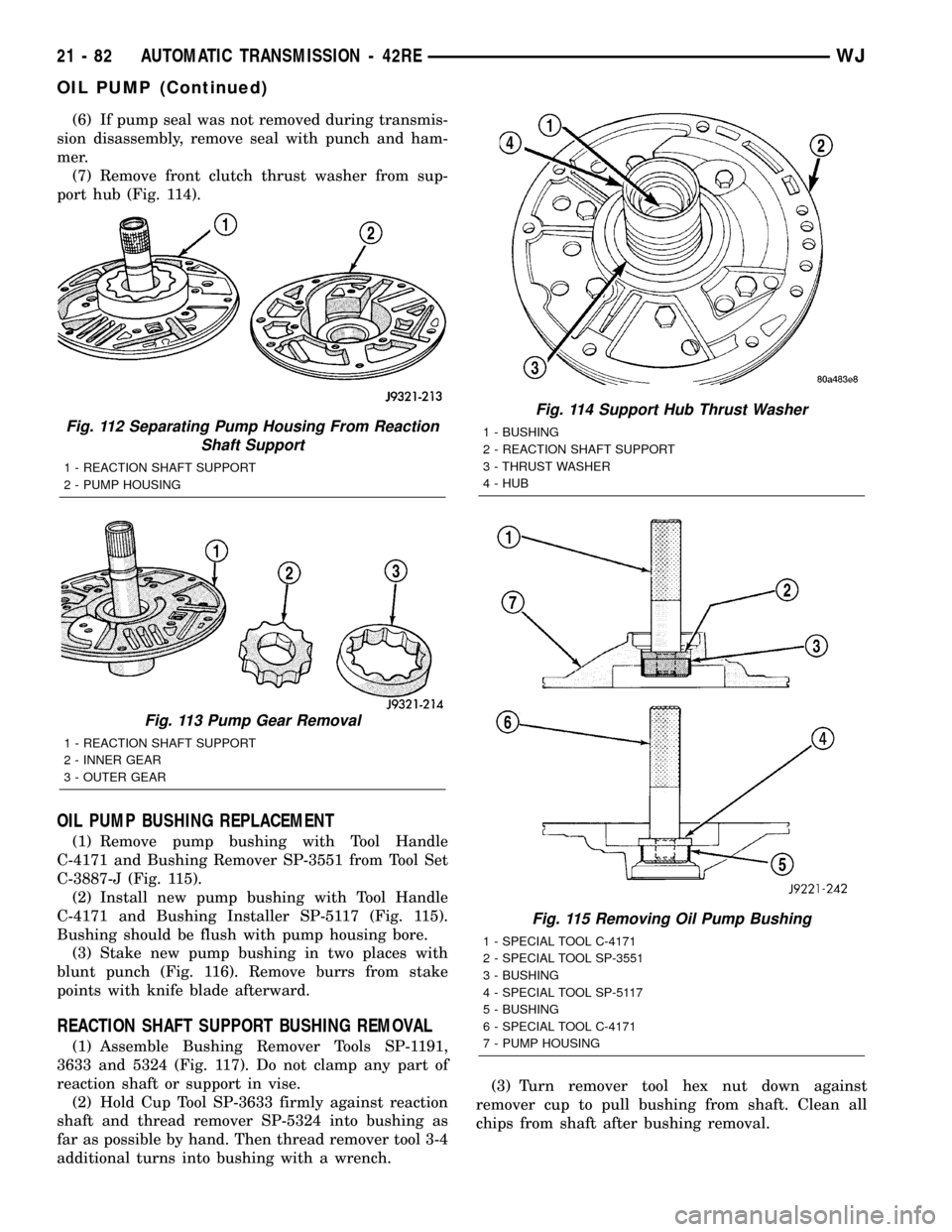
(6) If pump seal was not removed during transmis-
sion disassembly, remove seal with punch and ham-
mer.
(7) Remove front clutch thrust washer from sup-
port hub (Fig. 114).
OIL PUMP BUSHING REPLACEMENT
(1) Remove pump bushing with Tool Handle
C-4171 and Bushing Remover SP-3551 from Tool Set
C-3887-J (Fig. 115).
(2) Install new pump bushing with Tool Handle
C-4171 and Bushing Installer SP-5117 (Fig. 115).
Bushing should be flush with pump housing bore.
(3) Stake new pump bushing in two places with
blunt punch (Fig. 116). Remove burrs from stake
points with knife blade afterward.
REACTION SHAFT SUPPORT BUSHING REMOVAL
(1) Assemble Bushing Remover Tools SP-1191,
3633 and 5324 (Fig. 117). Do not clamp any part of
reaction shaft or support in vise.
(2) Hold Cup Tool SP-3633 firmly against reaction
shaft and thread remover SP-5324 into bushing as
far as possible by hand. Then thread remover tool 3-4
additional turns into bushing with a wrench.(3) Turn remover tool hex nut down against
remover cup to pull bushing from shaft. Clean all
chips from shaft after bushing removal.
Fig. 112 Separating Pump Housing From Reaction
Shaft Support
1 - REACTION SHAFT SUPPORT
2 - PUMP HOUSING
Fig. 113 Pump Gear Removal
1 - REACTION SHAFT SUPPORT
2 - INNER GEAR
3 - OUTER GEAR
Fig. 114 Support Hub Thrust Washer
1 - BUSHING
2 - REACTION SHAFT SUPPORT
3 - THRUST WASHER
4 - HUB
Fig. 115 Removing Oil Pump Bushing
1 - SPECIAL TOOL C-4171
2 - SPECIAL TOOL SP-3551
3 - BUSHING
4 - SPECIAL TOOL SP-5117
5 - BUSHING
6 - SPECIAL TOOL C-4171
7 - PUMP HOUSING
21 - 82 AUTOMATIC TRANSMISSION - 42REWJ
OIL PUMP (Continued)
Page 1602 of 2199
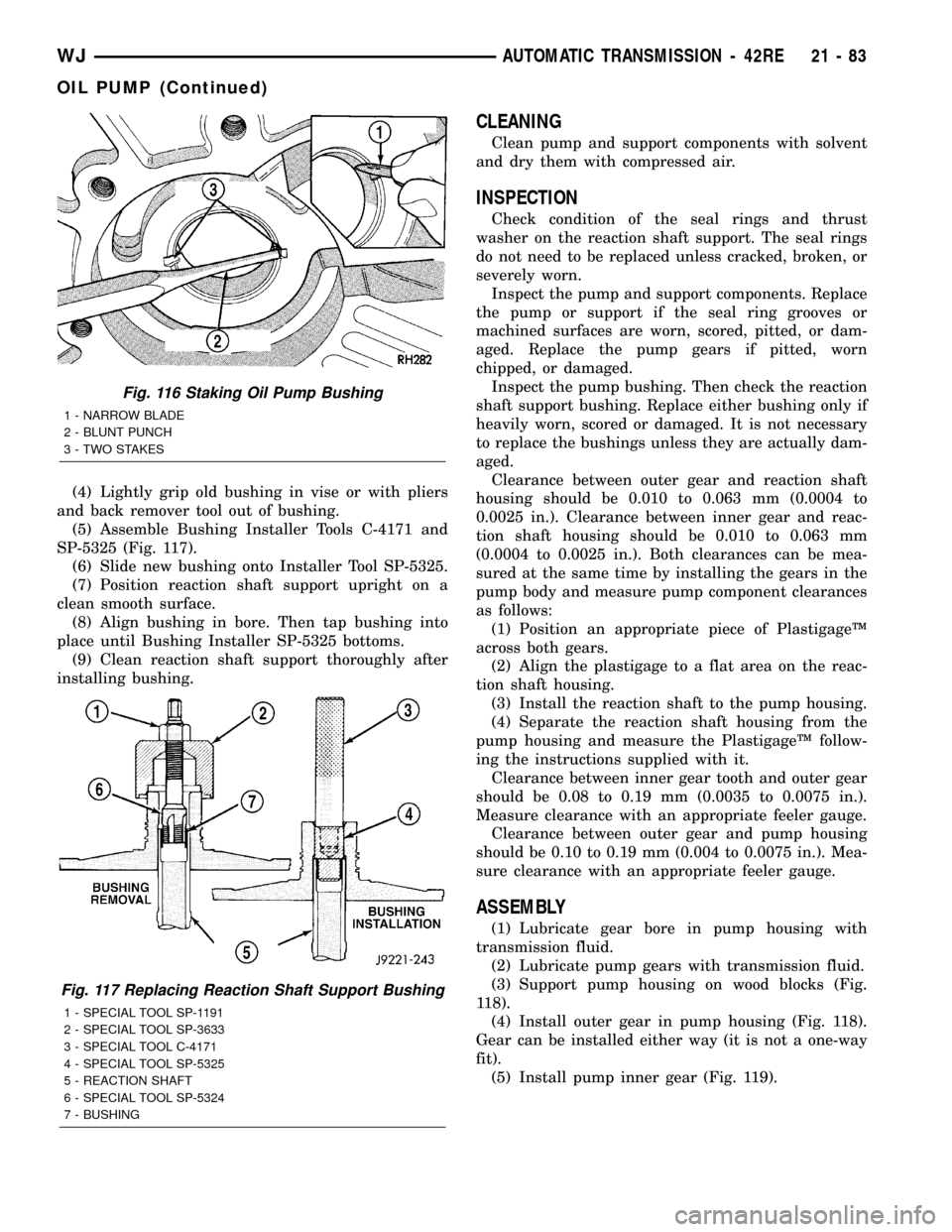
(4) Lightly grip old bushing in vise or with pliers
and back remover tool out of bushing.
(5) Assemble Bushing Installer Tools C-4171 and
SP-5325 (Fig. 117).
(6) Slide new bushing onto Installer Tool SP-5325.
(7) Position reaction shaft support upright on a
clean smooth surface.
(8) Align bushing in bore. Then tap bushing into
place until Bushing Installer SP-5325 bottoms.
(9) Clean reaction shaft support thoroughly after
installing bushing.
CLEANING
Clean pump and support components with solvent
and dry them with compressed air.
INSPECTION
Check condition of the seal rings and thrust
washer on the reaction shaft support. The seal rings
do not need to be replaced unless cracked, broken, or
severely worn.
Inspect the pump and support components. Replace
the pump or support if the seal ring grooves or
machined surfaces are worn, scored, pitted, or dam-
aged. Replace the pump gears if pitted, worn
chipped, or damaged.
Inspect the pump bushing. Then check the reaction
shaft support bushing. Replace either bushing only if
heavily worn, scored or damaged. It is not necessary
to replace the bushings unless they are actually dam-
aged.
Clearance between outer gear and reaction shaft
housing should be 0.010 to 0.063 mm (0.0004 to
0.0025 in.). Clearance between inner gear and reac-
tion shaft housing should be 0.010 to 0.063 mm
(0.0004 to 0.0025 in.). Both clearances can be mea-
sured at the same time by installing the gears in the
pump body and measure pump component clearances
as follows:
(1) Position an appropriate piece of PlastigageŸ
across both gears.
(2) Align the plastigage to a flat area on the reac-
tion shaft housing.
(3) Install the reaction shaft to the pump housing.
(4) Separate the reaction shaft housing from the
pump housing and measure the PlastigageŸ follow-
ing the instructions supplied with it.
Clearance between inner gear tooth and outer gear
should be 0.08 to 0.19 mm (0.0035 to 0.0075 in.).
Measure clearance with an appropriate feeler gauge.
Clearance between outer gear and pump housing
should be 0.10 to 0.19 mm (0.004 to 0.0075 in.). Mea-
sure clearance with an appropriate feeler gauge.
ASSEMBLY
(1) Lubricate gear bore in pump housing with
transmission fluid.
(2) Lubricate pump gears with transmission fluid.
(3) Support pump housing on wood blocks (Fig.
118).
(4) Install outer gear in pump housing (Fig. 118).
Gear can be installed either way (it is not a one-way
fit).
(5) Install pump inner gear (Fig. 119).
Fig. 116 Staking Oil Pump Bushing
1 - NARROW BLADE
2 - BLUNT PUNCH
3 - TWO STAKES
Fig. 117 Replacing Reaction Shaft Support Bushing
1 - SPECIAL TOOL SP-1191
2 - SPECIAL TOOL SP-3633
3 - SPECIAL TOOL C-4171
4 - SPECIAL TOOL SP-5325
5 - REACTION SHAFT
6 - SPECIAL TOOL SP-5324
7 - BUSHING
WJAUTOMATIC TRANSMISSION - 42RE 21 - 83
OIL PUMP (Continued)
Page 1604 of 2199
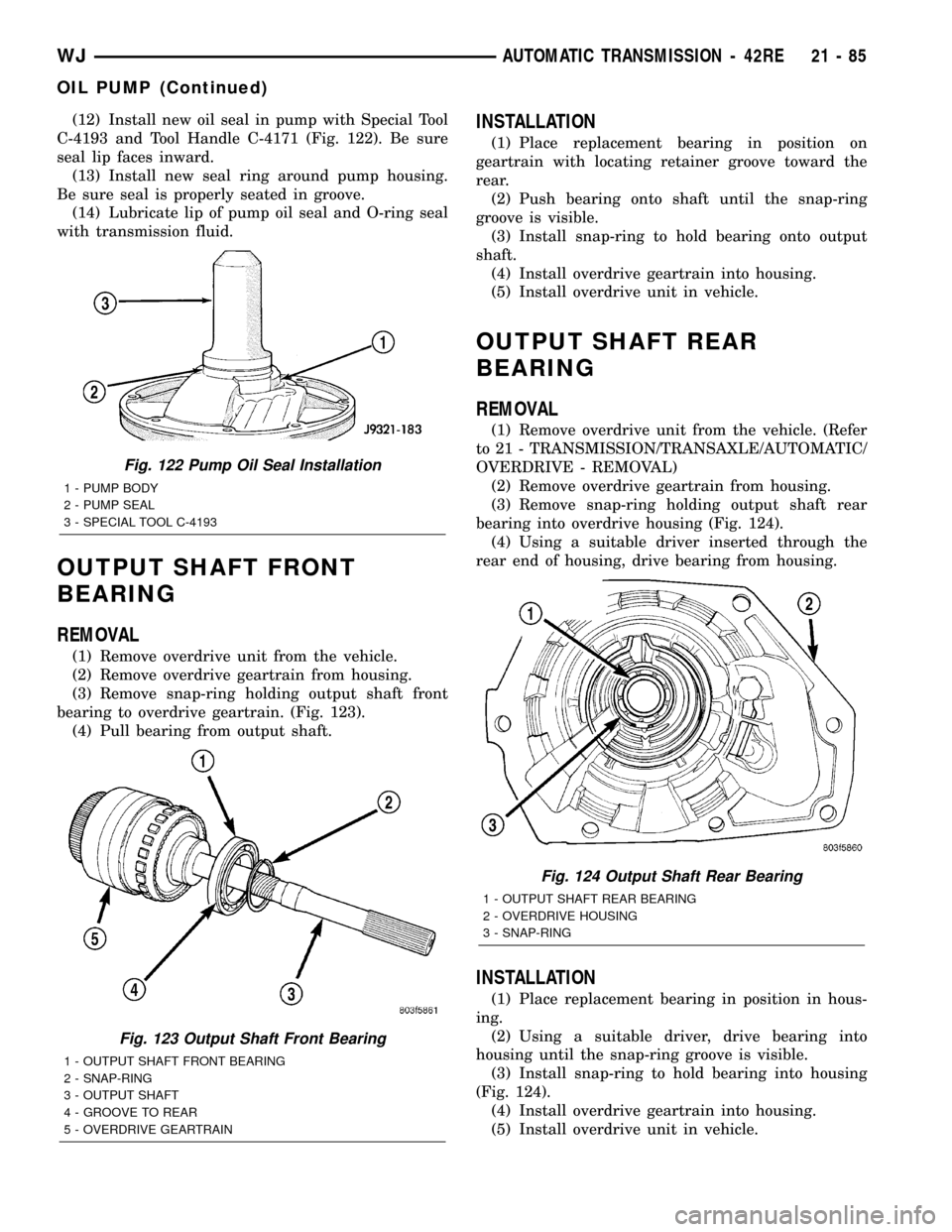
(12) Install new oil seal in pump with Special Tool
C-4193 and Tool Handle C-4171 (Fig. 122). Be sure
seal lip faces inward.
(13) Install new seal ring around pump housing.
Be sure seal is properly seated in groove.
(14) Lubricate lip of pump oil seal and O-ring seal
with transmission fluid.
OUTPUT SHAFT FRONT
BEARING
REMOVAL
(1) Remove overdrive unit from the vehicle.
(2) Remove overdrive geartrain from housing.
(3) Remove snap-ring holding output shaft front
bearing to overdrive geartrain. (Fig. 123).
(4) Pull bearing from output shaft.
INSTALLATION
(1) Place replacement bearing in position on
geartrain with locating retainer groove toward the
rear.
(2) Push bearing onto shaft until the snap-ring
groove is visible.
(3) Install snap-ring to hold bearing onto output
shaft.
(4) Install overdrive geartrain into housing.
(5) Install overdrive unit in vehicle.
OUTPUT SHAFT REAR
BEARING
REMOVAL
(1) Remove overdrive unit from the vehicle. (Refer
to 21 - TRANSMISSION/TRANSAXLE/AUTOMATIC/
OVERDRIVE - REMOVAL)
(2) Remove overdrive geartrain from housing.
(3) Remove snap-ring holding output shaft rear
bearing into overdrive housing (Fig. 124).
(4) Using a suitable driver inserted through the
rear end of housing, drive bearing from housing.
INSTALLATION
(1) Place replacement bearing in position in hous-
ing.
(2) Using a suitable driver, drive bearing into
housing until the snap-ring groove is visible.
(3) Install snap-ring to hold bearing into housing
(Fig. 124).
(4) Install overdrive geartrain into housing.
(5) Install overdrive unit in vehicle.
Fig. 122 Pump Oil Seal Installation
1 - PUMP BODY
2 - PUMP SEAL
3 - SPECIAL TOOL C-4193
Fig. 123 Output Shaft Front Bearing
1 - OUTPUT SHAFT FRONT BEARING
2 - SNAP-RING
3 - OUTPUT SHAFT
4 - GROOVE TO REAR
5 - OVERDRIVE GEARTRAIN
Fig. 124 Output Shaft Rear Bearing
1 - OUTPUT SHAFT REAR BEARING
2 - OVERDRIVE HOUSING
3 - SNAP-RING
WJAUTOMATIC TRANSMISSION - 42RE 21 - 85
OIL PUMP (Continued)
Page 1610 of 2199
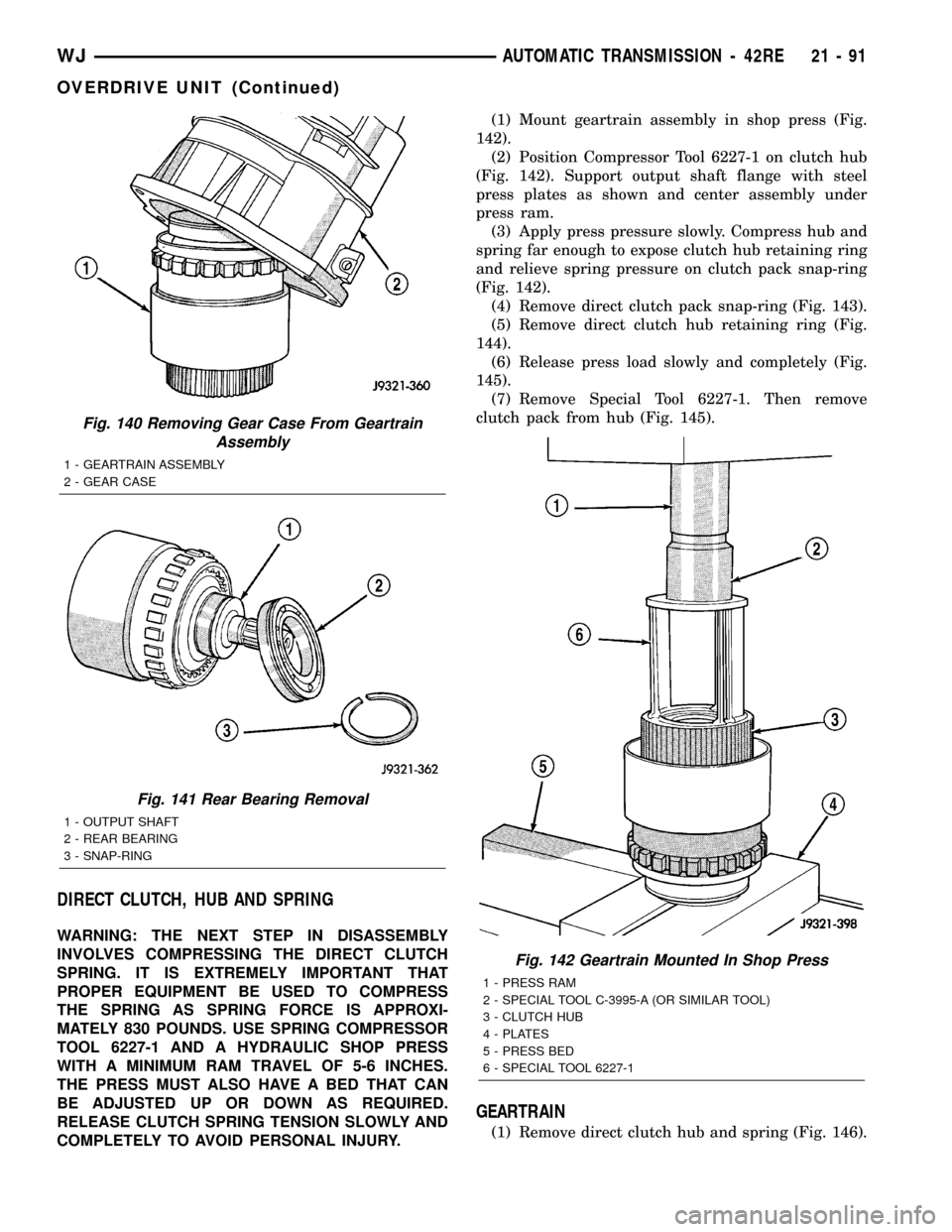
DIRECT CLUTCH, HUB AND SPRING
WARNING: THE NEXT STEP IN DISASSEMBLY
INVOLVES COMPRESSING THE DIRECT CLUTCH
SPRING. IT IS EXTREMELY IMPORTANT THAT
PROPER EQUIPMENT BE USED TO COMPRESS
THE SPRING AS SPRING FORCE IS APPROXI-
MATELY 830 POUNDS. USE SPRING COMPRESSOR
TOOL 6227-1 AND A HYDRAULIC SHOP PRESS
WITH A MINIMUM RAM TRAVEL OF 5-6 INCHES.
THE PRESS MUST ALSO HAVE A BED THAT CAN
BE ADJUSTED UP OR DOWN AS REQUIRED.
RELEASE CLUTCH SPRING TENSION SLOWLY AND
COMPLETELY TO AVOID PERSONAL INJURY.(1) Mount geartrain assembly in shop press (Fig.
142).
(2) Position Compressor Tool 6227-1 on clutch hub
(Fig. 142). Support output shaft flange with steel
press plates as shown and center assembly under
press ram.
(3) Apply press pressure slowly. Compress hub and
spring far enough to expose clutch hub retaining ring
and relieve spring pressure on clutch pack snap-ring
(Fig. 142).
(4) Remove direct clutch pack snap-ring (Fig. 143).
(5) Remove direct clutch hub retaining ring (Fig.
144).
(6) Release press load slowly and completely (Fig.
145).
(7) Remove Special Tool 6227-1. Then remove
clutch pack from hub (Fig. 145).
GEARTRAIN
(1) Remove direct clutch hub and spring (Fig. 146).
Fig. 140 Removing Gear Case From Geartrain
Assembly
1 - GEARTRAIN ASSEMBLY
2 - GEAR CASE
Fig. 141 Rear Bearing Removal
1 - OUTPUT SHAFT
2 - REAR BEARING
3 - SNAP-RING
Fig. 142 Geartrain Mounted In Shop Press
1 - PRESS RAM
2 - SPECIAL TOOL C-3995-A (OR SIMILAR TOOL)
3 - CLUTCH HUB
4 - PLATES
5 - PRESS BED
6 - SPECIAL TOOL 6227-1
WJAUTOMATIC TRANSMISSION - 42RE 21 - 91
OVERDRIVE UNIT (Continued)
Page 1611 of 2199

(2) Remove sun gear and spring plate. Then
remove planetary thrust bearing and planetary gear
(Fig. 147).
(3) Remove overrunning clutch assembly with
expanding type snap-ring pliers (Fig. 148). Insert pli-
ers into clutch hub. Expand pliers to grip hub splines
and remove clutch with counterclockwise, twisting
motion.
(4) Remove thrust bearing from overrunning
clutch hub.
Fig. 143 Direct Clutch Pack Snap-Ring Removal
1 - CLUTCH HUB
2 - SPECIAL TOOL 6227-1
3 - DIRECT CLUTCH PACK SNAP-RING
4 - PRESS PLATES
5 - CLUTCH DRUM
Fig. 144 Direct Clutch Hub Retaining Ring Removal
1 - SPECIAL TOOL 6227-1
2 - CLUTCH HUB RETAINING RING
3 - PRESS BED
4 - PRESS PLATES
Fig. 145 Direct Clutch Pack Removal
1 - SPECIAL TOOL 6227-1
2 - DIRECT CLUTCH HUB
3 - DIRECT CLUTCH PACK
Fig. 146 Direct Clutch Hub And Spring Removal
1 - DIRECT CLUTCH SPRING
2 - DIRECT CLUTCH HUB
21 - 92 AUTOMATIC TRANSMISSION - 42REWJ
OVERDRIVE UNIT (Continued)