relay JEEP GRAND CHEROKEE 2003 WJ / 2.G Service Manual
[x] Cancel search | Manufacturer: JEEP, Model Year: 2003, Model line: GRAND CHEROKEE, Model: JEEP GRAND CHEROKEE 2003 WJ / 2.GPages: 2199, PDF Size: 76.01 MB
Page 398 of 2199
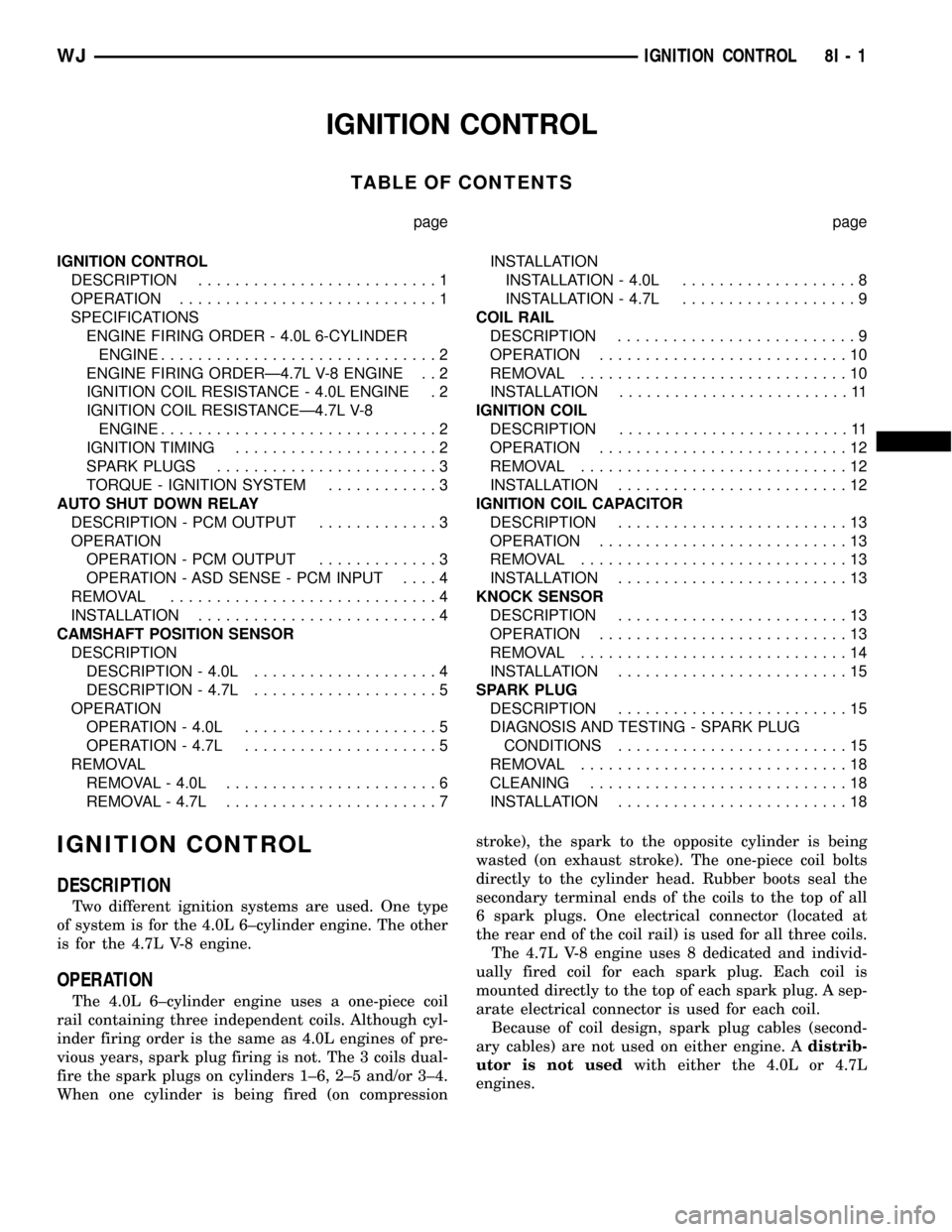
IGNITION CONTROL
TABLE OF CONTENTS
page page
IGNITION CONTROL
DESCRIPTION..........................1
OPERATION............................1
SPECIFICATIONS
ENGINE FIRING ORDER - 4.0L 6-CYLINDER
ENGINE..............................2
ENGINE FIRING ORDERÐ4.7L V-8 ENGINE . . 2
IGNITION COIL RESISTANCE - 4.0L ENGINE . 2
IGNITION COIL RESISTANCEÐ4.7L V-8
ENGINE..............................2
IGNITION TIMING......................2
SPARK PLUGS........................3
TORQUE - IGNITION SYSTEM............3
AUTO SHUT DOWN RELAY
DESCRIPTION - PCM OUTPUT.............3
OPERATION
OPERATION - PCM OUTPUT.............3
OPERATION - ASD SENSE - PCM INPUT....4
REMOVAL.............................4
INSTALLATION..........................4
CAMSHAFT POSITION SENSOR
DESCRIPTION
DESCRIPTION - 4.0L....................4
DESCRIPTION - 4.7L....................5
OPERATION
OPERATION - 4.0L.....................5
OPERATION - 4.7L.....................5
REMOVAL
REMOVAL - 4.0L.......................6
REMOVAL - 4.7L.......................7INSTALLATION
INSTALLATION - 4.0L...................8
INSTALLATION - 4.7L...................9
COIL RAIL
DESCRIPTION..........................9
OPERATION...........................10
REMOVAL.............................10
INSTALLATION.........................11
IGNITION COIL
DESCRIPTION.........................11
OPERATION...........................12
REMOVAL.............................12
INSTALLATION.........................12
IGNITION COIL CAPACITOR
DESCRIPTION.........................13
OPERATION...........................13
REMOVAL.............................13
INSTALLATION.........................13
KNOCK SENSOR
DESCRIPTION.........................13
OPERATION...........................13
REMOVAL.............................14
INSTALLATION.........................15
SPARK PLUG
DESCRIPTION.........................15
DIAGNOSIS AND TESTING - SPARK PLUG
CONDITIONS.........................15
REMOVAL.............................18
CLEANING............................18
INSTALLATION.........................18
IGNITION CONTROL
DESCRIPTION
Two different ignition systems are used. One type
of system is for the 4.0L 6±cylinder engine. The other
is for the 4.7L V-8 engine.
OPERATION
The 4.0L 6±cylinder engine uses a one-piece coil
rail containing three independent coils. Although cyl-
inder firing order is the same as 4.0L engines of pre-
vious years, spark plug firing is not. The 3 coils dual-
fire the spark plugs on cylinders 1±6, 2±5 and/or 3±4.
When one cylinder is being fired (on compressionstroke), the spark to the opposite cylinder is being
wasted (on exhaust stroke). The one-piece coil bolts
directly to the cylinder head. Rubber boots seal the
secondary terminal ends of the coils to the top of all
6 spark plugs. One electrical connector (located at
the rear end of the coil rail) is used for all three coils.
The 4.7L V-8 engine uses 8 dedicated and individ-
ually fired coil for each spark plug. Each coil is
mounted directly to the top of each spark plug. A sep-
arate electrical connector is used for each coil.
Because of coil design, spark plug cables (second-
ary cables) are not used on either engine. Adistrib-
utor is not usedwith either the 4.0L or 4.7L
engines.
WJIGNITION CONTROL 8I - 1
Page 400 of 2199
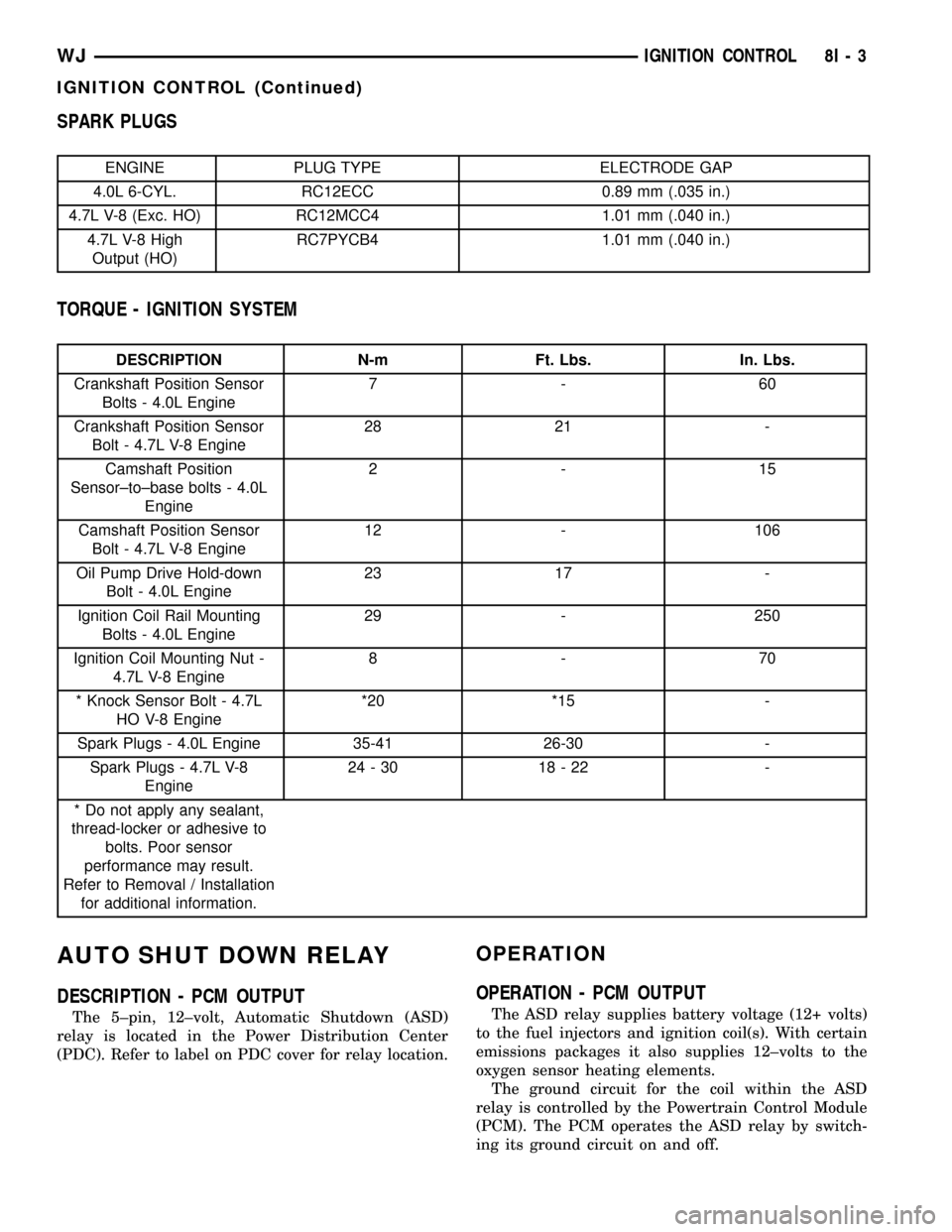
SPARK PLUGS
ENGINE PLUG TYPE ELECTRODE GAP
4.0L 6-CYL. RC12ECC 0.89 mm (.035 in.)
4.7L V-8 (Exc. HO) RC12MCC4 1.01 mm (.040 in.)
4.7L V-8 High
Output (HO)RC7PYCB4 1.01 mm (.040 in.)
TORQUE - IGNITION SYSTEM
DESCRIPTION N-m Ft. Lbs. In. Lbs.
Crankshaft Position Sensor
Bolts - 4.0L Engine7- 60
Crankshaft Position Sensor
Bolt - 4.7L V-8 Engine28 21 -
Camshaft Position
Sensor±to±base bolts - 4.0L
Engine2- 15
Camshaft Position Sensor
Bolt - 4.7L V-8 Engine12 - 106
Oil Pump Drive Hold-down
Bolt - 4.0L Engine23 17 -
Ignition Coil Rail Mounting
Bolts - 4.0L Engine29 - 250
Ignition Coil Mounting Nut -
4.7L V-8 Engine8- 70
* Knock Sensor Bolt - 4.7L
HO V-8 Engine*20 *15 -
Spark Plugs - 4.0L Engine 35-41 26-30 -
Spark Plugs - 4.7L V-8
Engine24-30 18-22 -
* Do not apply any sealant,
thread-locker or adhesive to
bolts. Poor sensor
performance may result.
Refer to Removal / Installation
for additional information.
AUTO SHUT DOWN RELAY
DESCRIPTION - PCM OUTPUT
The 5±pin, 12±volt, Automatic Shutdown (ASD)
relay is located in the Power Distribution Center
(PDC). Refer to label on PDC cover for relay location.
OPERATION
OPERATION - PCM OUTPUT
The ASD relay supplies battery voltage (12+ volts)
to the fuel injectors and ignition coil(s). With certain
emissions packages it also supplies 12±volts to the
oxygen sensor heating elements.
The ground circuit for the coil within the ASD
relay is controlled by the Powertrain Control Module
(PCM). The PCM operates the ASD relay by switch-
ing its ground circuit on and off.
WJIGNITION CONTROL 8I - 3
IGNITION CONTROL (Continued)
Page 401 of 2199
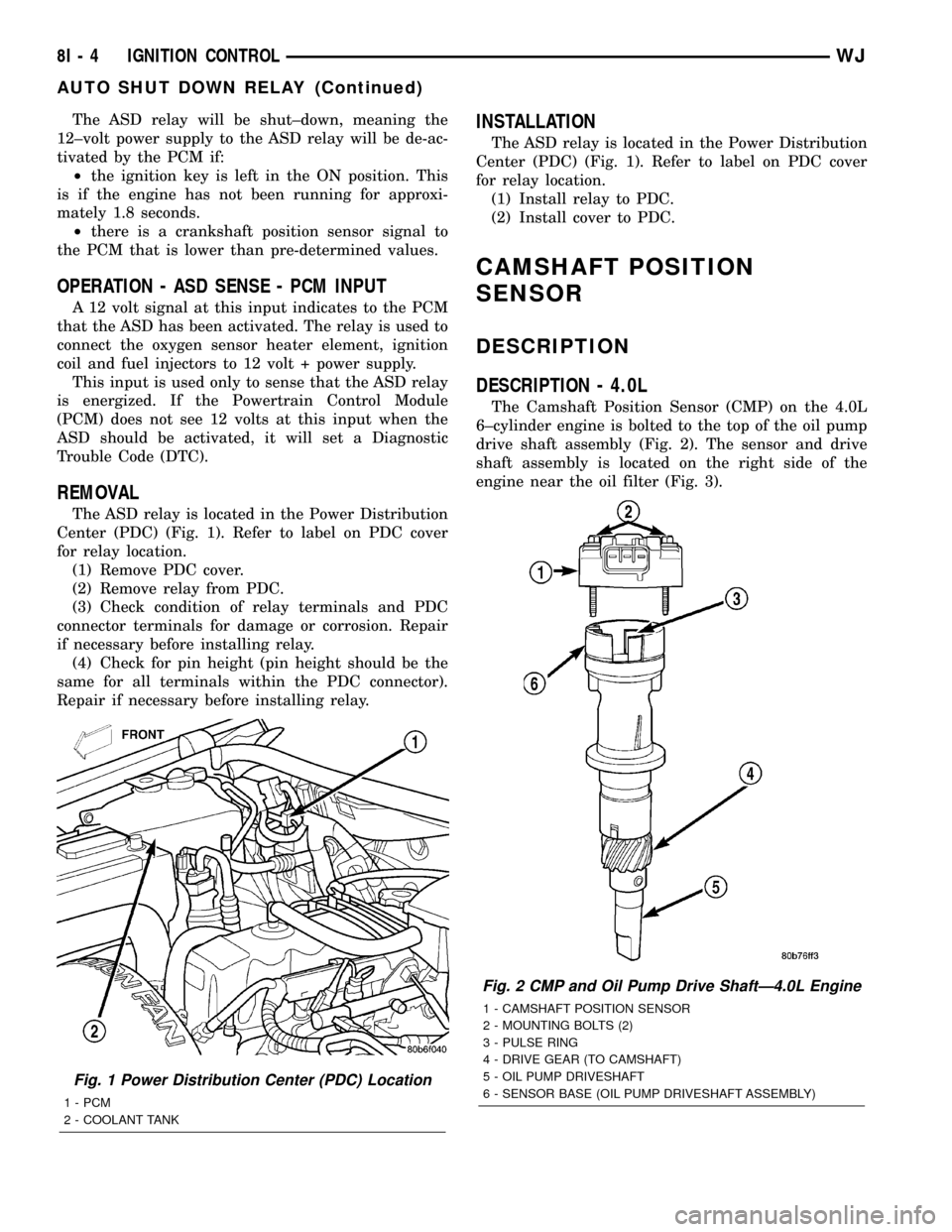
The ASD relay will be shut±down, meaning the
12±volt power supply to the ASD relay will be de-ac-
tivated by the PCM if:
²the ignition key is left in the ON position. This
is if the engine has not been running for approxi-
mately 1.8 seconds.
²there is a crankshaft position sensor signal to
the PCM that is lower than pre-determined values.
OPERATION - ASD SENSE - PCM INPUT
A 12 volt signal at this input indicates to the PCM
that the ASD has been activated. The relay is used to
connect the oxygen sensor heater element, ignition
coil and fuel injectors to 12 volt + power supply.
This input is used only to sense that the ASD relay
is energized. If the Powertrain Control Module
(PCM) does not see 12 volts at this input when the
ASD should be activated, it will set a Diagnostic
Trouble Code (DTC).
REMOVAL
The ASD relay is located in the Power Distribution
Center (PDC) (Fig. 1). Refer to label on PDC cover
for relay location.
(1) Remove PDC cover.
(2) Remove relay from PDC.
(3) Check condition of relay terminals and PDC
connector terminals for damage or corrosion. Repair
if necessary before installing relay.
(4) Check for pin height (pin height should be the
same for all terminals within the PDC connector).
Repair if necessary before installing relay.
INSTALLATION
The ASD relay is located in the Power Distribution
Center (PDC) (Fig. 1). Refer to label on PDC cover
for relay location.
(1) Install relay to PDC.
(2) Install cover to PDC.
CAMSHAFT POSITION
SENSOR
DESCRIPTION
DESCRIPTION - 4.0L
The Camshaft Position Sensor (CMP) on the 4.0L
6±cylinder engine is bolted to the top of the oil pump
drive shaft assembly (Fig. 2). The sensor and drive
shaft assembly is located on the right side of the
engine near the oil filter (Fig. 3).
Fig. 1 Power Distribution Center (PDC) Location
1 - PCM
2 - COOLANT TANK
Fig. 2 CMP and Oil Pump Drive ShaftÐ4.0L Engine
1 - CAMSHAFT POSITION SENSOR
2 - MOUNTING BOLTS (2)
3 - PULSE RING
4 - DRIVE GEAR (TO CAMSHAFT)
5 - OIL PUMP DRIVESHAFT
6 - SENSOR BASE (OIL PUMP DRIVESHAFT ASSEMBLY)
8I - 4 IGNITION CONTROLWJ
AUTO SHUT DOWN RELAY (Continued)
Page 407 of 2199
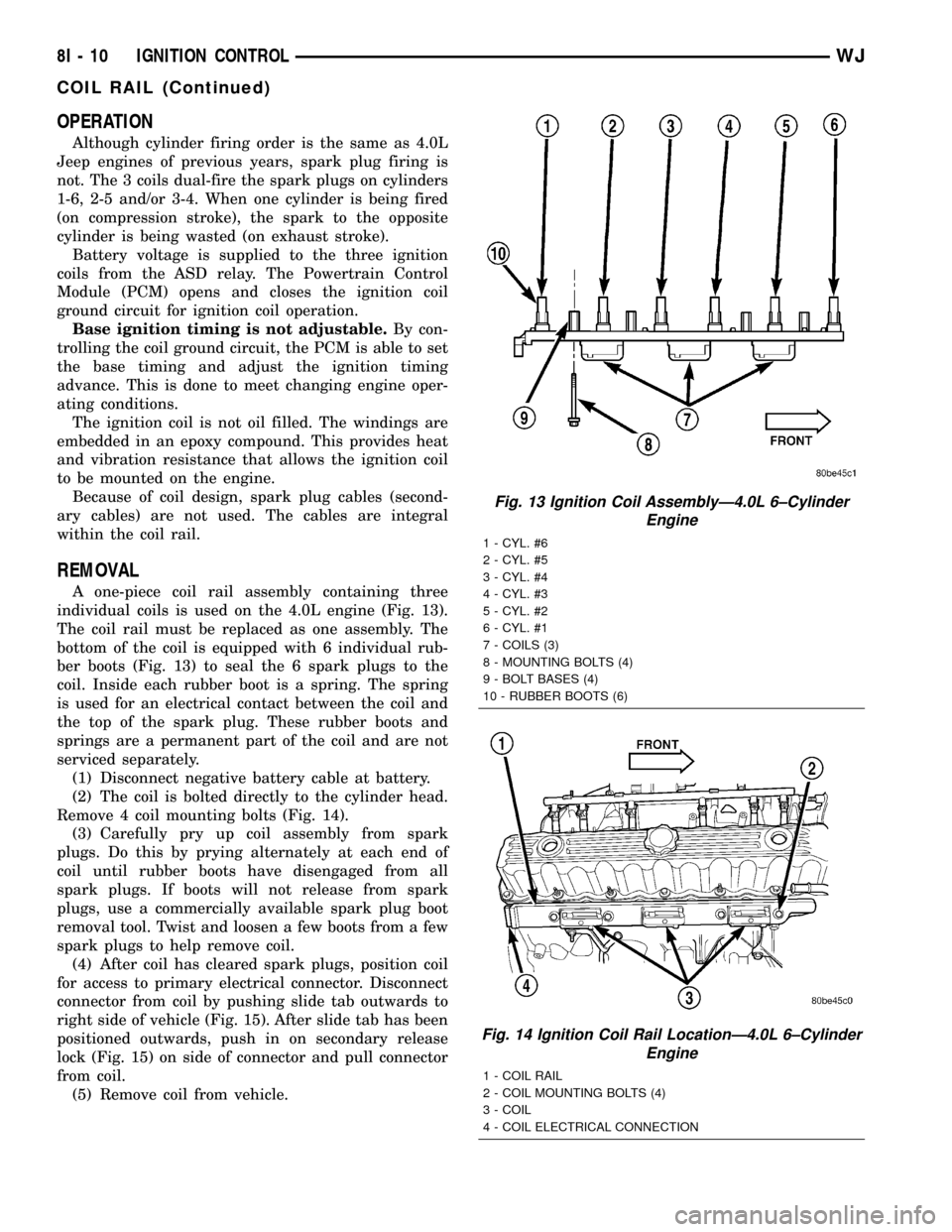
OPERATION
Although cylinder firing order is the same as 4.0L
Jeep engines of previous years, spark plug firing is
not. The 3 coils dual-fire the spark plugs on cylinders
1-6, 2-5 and/or 3-4. When one cylinder is being fired
(on compression stroke), the spark to the opposite
cylinder is being wasted (on exhaust stroke).
Battery voltage is supplied to the three ignition
coils from the ASD relay. The Powertrain Control
Module (PCM) opens and closes the ignition coil
ground circuit for ignition coil operation.
Base ignition timing is not adjustable.By con-
trolling the coil ground circuit, the PCM is able to set
the base timing and adjust the ignition timing
advance. This is done to meet changing engine oper-
ating conditions.
The ignition coil is not oil filled. The windings are
embedded in an epoxy compound. This provides heat
and vibration resistance that allows the ignition coil
to be mounted on the engine.
Because of coil design, spark plug cables (second-
ary cables) are not used. The cables are integral
within the coil rail.
REMOVAL
A one-piece coil rail assembly containing three
individual coils is used on the 4.0L engine (Fig. 13).
The coil rail must be replaced as one assembly. The
bottom of the coil is equipped with 6 individual rub-
ber boots (Fig. 13) to seal the 6 spark plugs to the
coil. Inside each rubber boot is a spring. The spring
is used for an electrical contact between the coil and
the top of the spark plug. These rubber boots and
springs are a permanent part of the coil and are not
serviced separately.
(1) Disconnect negative battery cable at battery.
(2) The coil is bolted directly to the cylinder head.
Remove 4 coil mounting bolts (Fig. 14).
(3) Carefully pry up coil assembly from spark
plugs. Do this by prying alternately at each end of
coil until rubber boots have disengaged from all
spark plugs. If boots will not release from spark
plugs, use a commercially available spark plug boot
removal tool. Twist and loosen a few boots from a few
spark plugs to help remove coil.
(4) After coil has cleared spark plugs, position coil
for access to primary electrical connector. Disconnect
connector from coil by pushing slide tab outwards to
right side of vehicle (Fig. 15). After slide tab has been
positioned outwards, push in on secondary release
lock (Fig. 15) on side of connector and pull connector
from coil.
(5) Remove coil from vehicle.
Fig. 13 Ignition Coil AssemblyÐ4.0L 6±Cylinder
Engine
1 - CYL. #6
2 - CYL. #5
3 - CYL. #4
4 - CYL. #3
5 - CYL. #2
6 - CYL. #1
7 - COILS (3)
8 - MOUNTING BOLTS (4)
9 - BOLT BASES (4)
10 - RUBBER BOOTS (6)
Fig. 14 Ignition Coil Rail LocationÐ4.0L 6±Cylinder
Engine
1 - COIL RAIL
2 - COIL MOUNTING BOLTS (4)
3 - COIL
4 - COIL ELECTRICAL CONNECTION
8I - 10 IGNITION CONTROLWJ
COIL RAIL (Continued)
Page 409 of 2199
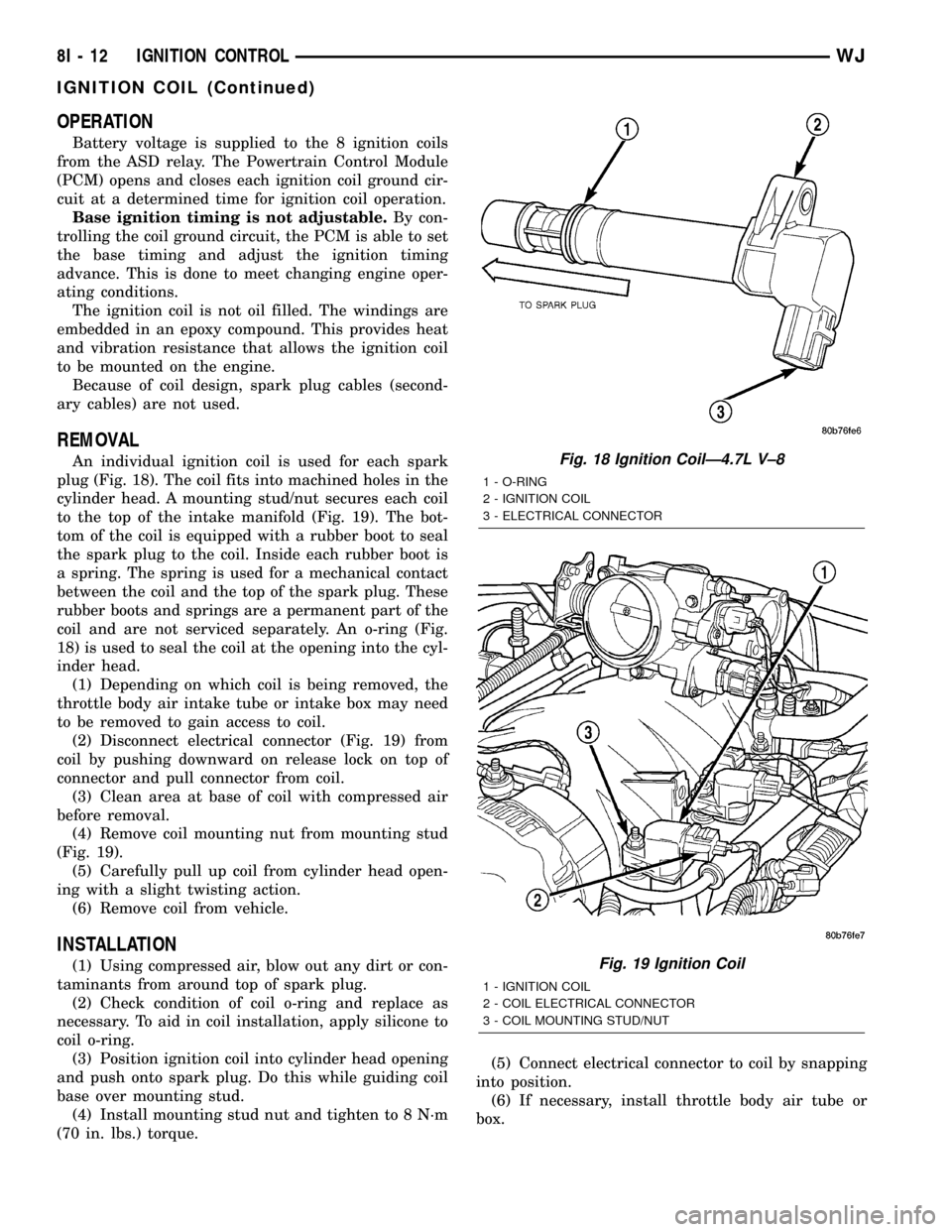
OPERATION
Battery voltage is supplied to the 8 ignition coils
from the ASD relay. The Powertrain Control Module
(PCM) opens and closes each ignition coil ground cir-
cuit at a determined time for ignition coil operation.
Base ignition timing is not adjustable.By con-
trolling the coil ground circuit, the PCM is able to set
the base timing and adjust the ignition timing
advance. This is done to meet changing engine oper-
ating conditions.
The ignition coil is not oil filled. The windings are
embedded in an epoxy compound. This provides heat
and vibration resistance that allows the ignition coil
to be mounted on the engine.
Because of coil design, spark plug cables (second-
ary cables) are not used.
REMOVAL
An individual ignition coil is used for each spark
plug (Fig. 18). The coil fits into machined holes in the
cylinder head. A mounting stud/nut secures each coil
to the top of the intake manifold (Fig. 19). The bot-
tom of the coil is equipped with a rubber boot to seal
the spark plug to the coil. Inside each rubber boot is
a spring. The spring is used for a mechanical contact
between the coil and the top of the spark plug. These
rubber boots and springs are a permanent part of the
coil and are not serviced separately. An o-ring (Fig.
18) is used to seal the coil at the opening into the cyl-
inder head.
(1) Depending on which coil is being removed, the
throttle body air intake tube or intake box may need
to be removed to gain access to coil.
(2) Disconnect electrical connector (Fig. 19) from
coil by pushing downward on release lock on top of
connector and pull connector from coil.
(3) Clean area at base of coil with compressed air
before removal.
(4) Remove coil mounting nut from mounting stud
(Fig. 19).
(5) Carefully pull up coil from cylinder head open-
ing with a slight twisting action.
(6) Remove coil from vehicle.
INSTALLATION
(1) Using compressed air, blow out any dirt or con-
taminants from around top of spark plug.
(2) Check condition of coil o-ring and replace as
necessary. To aid in coil installation, apply silicone to
coil o-ring.
(3) Position ignition coil into cylinder head opening
and push onto spark plug. Do this while guiding coil
base over mounting stud.
(4) Install mounting stud nut and tighten to 8 N´m
(70 in. lbs.) torque.(5) Connect electrical connector to coil by snapping
into position.
(6) If necessary, install throttle body air tube or
box.
Fig. 18 Ignition CoilÐ4.7L V±8
1 - O-RING
2 - IGNITION COIL
3 - ELECTRICAL CONNECTOR
Fig. 19 Ignition Coil
1 - IGNITION COIL
2 - COIL ELECTRICAL CONNECTOR
3 - COIL MOUNTING STUD/NUT
8I - 12 IGNITION CONTROLWJ
IGNITION COIL (Continued)
Page 435 of 2199
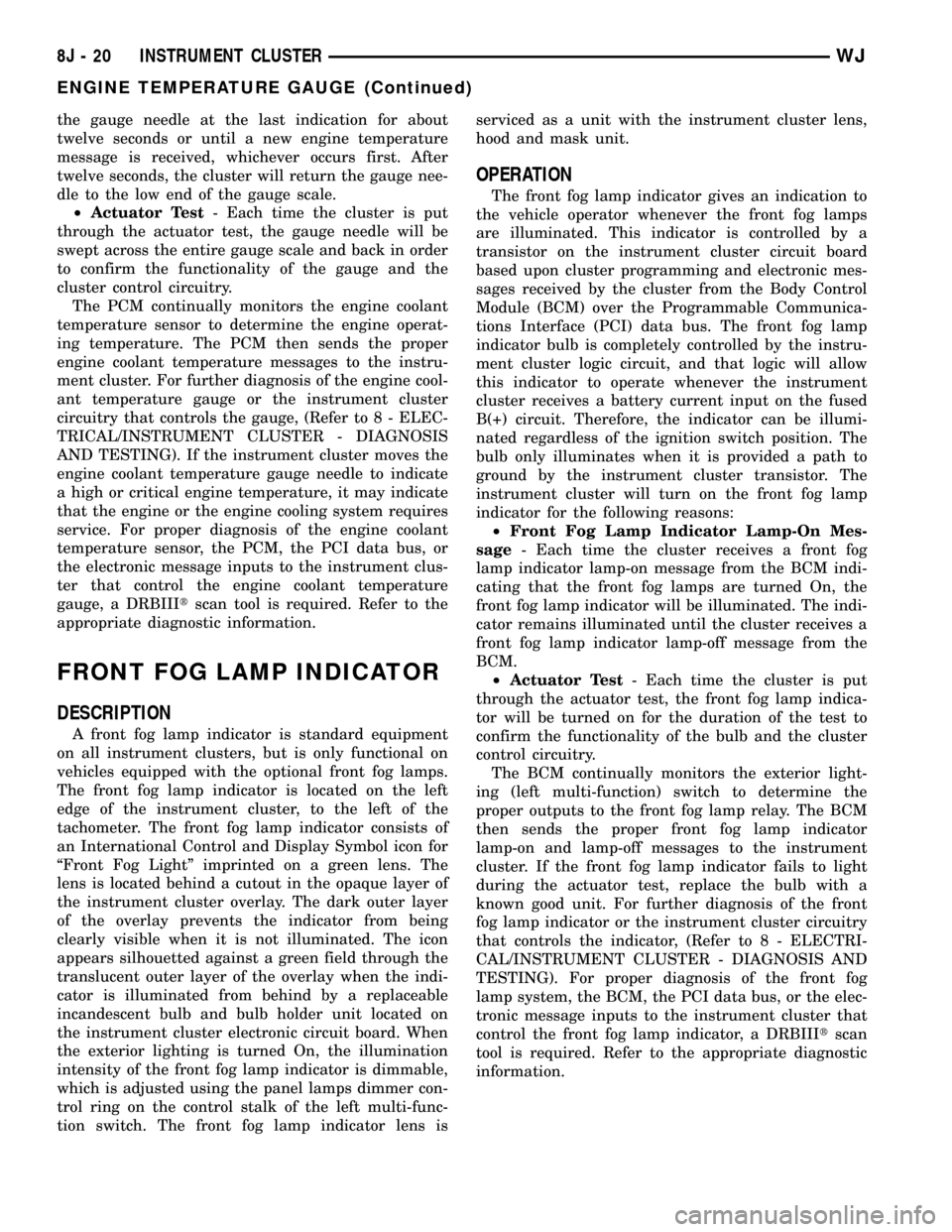
the gauge needle at the last indication for about
twelve seconds or until a new engine temperature
message is received, whichever occurs first. After
twelve seconds, the cluster will return the gauge nee-
dle to the low end of the gauge scale.
²Actuator Test- Each time the cluster is put
through the actuator test, the gauge needle will be
swept across the entire gauge scale and back in order
to confirm the functionality of the gauge and the
cluster control circuitry.
The PCM continually monitors the engine coolant
temperature sensor to determine the engine operat-
ing temperature. The PCM then sends the proper
engine coolant temperature messages to the instru-
ment cluster. For further diagnosis of the engine cool-
ant temperature gauge or the instrument cluster
circuitry that controls the gauge, (Refer to 8 - ELEC-
TRICAL/INSTRUMENT CLUSTER - DIAGNOSIS
AND TESTING). If the instrument cluster moves the
engine coolant temperature gauge needle to indicate
a high or critical engine temperature, it may indicate
that the engine or the engine cooling system requires
service. For proper diagnosis of the engine coolant
temperature sensor, the PCM, the PCI data bus, or
the electronic message inputs to the instrument clus-
ter that control the engine coolant temperature
gauge, a DRBIIItscan tool is required. Refer to the
appropriate diagnostic information.
FRONT FOG LAMP INDICATOR
DESCRIPTION
A front fog lamp indicator is standard equipment
on all instrument clusters, but is only functional on
vehicles equipped with the optional front fog lamps.
The front fog lamp indicator is located on the left
edge of the instrument cluster, to the left of the
tachometer. The front fog lamp indicator consists of
an International Control and Display Symbol icon for
ªFront Fog Lightº imprinted on a green lens. The
lens is located behind a cutout in the opaque layer of
the instrument cluster overlay. The dark outer layer
of the overlay prevents the indicator from being
clearly visible when it is not illuminated. The icon
appears silhouetted against a green field through the
translucent outer layer of the overlay when the indi-
cator is illuminated from behind by a replaceable
incandescent bulb and bulb holder unit located on
the instrument cluster electronic circuit board. When
the exterior lighting is turned On, the illumination
intensity of the front fog lamp indicator is dimmable,
which is adjusted using the panel lamps dimmer con-
trol ring on the control stalk of the left multi-func-
tion switch. The front fog lamp indicator lens isserviced as a unit with the instrument cluster lens,
hood and mask unit.
OPERATION
The front fog lamp indicator gives an indication to
the vehicle operator whenever the front fog lamps
are illuminated. This indicator is controlled by a
transistor on the instrument cluster circuit board
based upon cluster programming and electronic mes-
sages received by the cluster from the Body Control
Module (BCM) over the Programmable Communica-
tions Interface (PCI) data bus. The front fog lamp
indicator bulb is completely controlled by the instru-
ment cluster logic circuit, and that logic will allow
this indicator to operate whenever the instrument
cluster receives a battery current input on the fused
B(+) circuit. Therefore, the indicator can be illumi-
nated regardless of the ignition switch position. The
bulb only illuminates when it is provided a path to
ground by the instrument cluster transistor. The
instrument cluster will turn on the front fog lamp
indicator for the following reasons:
²Front Fog Lamp Indicator Lamp-On Mes-
sage- Each time the cluster receives a front fog
lamp indicator lamp-on message from the BCM indi-
cating that the front fog lamps are turned On, the
front fog lamp indicator will be illuminated. The indi-
cator remains illuminated until the cluster receives a
front fog lamp indicator lamp-off message from the
BCM.
²Actuator Test- Each time the cluster is put
through the actuator test, the front fog lamp indica-
tor will be turned on for the duration of the test to
confirm the functionality of the bulb and the cluster
control circuitry.
The BCM continually monitors the exterior light-
ing (left multi-function) switch to determine the
proper outputs to the front fog lamp relay. The BCM
then sends the proper front fog lamp indicator
lamp-on and lamp-off messages to the instrument
cluster. If the front fog lamp indicator fails to light
during the actuator test, replace the bulb with a
known good unit. For further diagnosis of the front
fog lamp indicator or the instrument cluster circuitry
that controls the indicator, (Refer to 8 - ELECTRI-
CAL/INSTRUMENT CLUSTER - DIAGNOSIS AND
TESTING). For proper diagnosis of the front fog
lamp system, the BCM, the PCI data bus, or the elec-
tronic message inputs to the instrument cluster that
control the front fog lamp indicator, a DRBIIItscan
tool is required. Refer to the appropriate diagnostic
information.
8J - 20 INSTRUMENT CLUSTERWJ
ENGINE TEMPERATURE GAUGE (Continued)
Page 437 of 2199
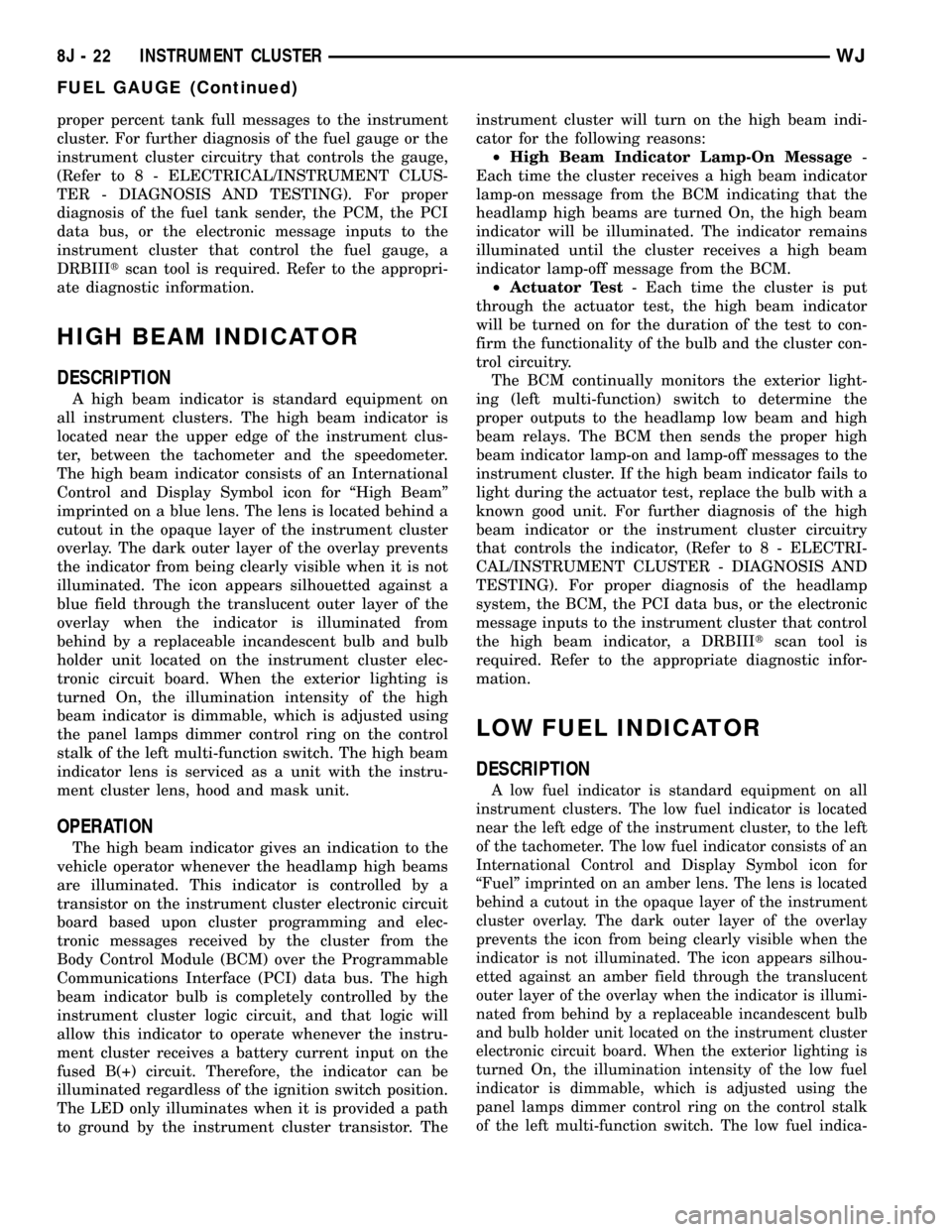
proper percent tank full messages to the instrument
cluster. For further diagnosis of the fuel gauge or the
instrument cluster circuitry that controls the gauge,
(Refer to 8 - ELECTRICAL/INSTRUMENT CLUS-
TER - DIAGNOSIS AND TESTING). For proper
diagnosis of the fuel tank sender, the PCM, the PCI
data bus, or the electronic message inputs to the
instrument cluster that control the fuel gauge, a
DRBIIItscan tool is required. Refer to the appropri-
ate diagnostic information.
HIGH BEAM INDICATOR
DESCRIPTION
A high beam indicator is standard equipment on
all instrument clusters. The high beam indicator is
located near the upper edge of the instrument clus-
ter, between the tachometer and the speedometer.
The high beam indicator consists of an International
Control and Display Symbol icon for ªHigh Beamº
imprinted on a blue lens. The lens is located behind a
cutout in the opaque layer of the instrument cluster
overlay. The dark outer layer of the overlay prevents
the indicator from being clearly visible when it is not
illuminated. The icon appears silhouetted against a
blue field through the translucent outer layer of the
overlay when the indicator is illuminated from
behind by a replaceable incandescent bulb and bulb
holder unit located on the instrument cluster elec-
tronic circuit board. When the exterior lighting is
turned On, the illumination intensity of the high
beam indicator is dimmable, which is adjusted using
the panel lamps dimmer control ring on the control
stalk of the left multi-function switch. The high beam
indicator lens is serviced as a unit with the instru-
ment cluster lens, hood and mask unit.
OPERATION
The high beam indicator gives an indication to the
vehicle operator whenever the headlamp high beams
are illuminated. This indicator is controlled by a
transistor on the instrument cluster electronic circuit
board based upon cluster programming and elec-
tronic messages received by the cluster from the
Body Control Module (BCM) over the Programmable
Communications Interface (PCI) data bus. The high
beam indicator bulb is completely controlled by the
instrument cluster logic circuit, and that logic will
allow this indicator to operate whenever the instru-
ment cluster receives a battery current input on the
fused B(+) circuit. Therefore, the indicator can be
illuminated regardless of the ignition switch position.
The LED only illuminates when it is provided a path
to ground by the instrument cluster transistor. Theinstrument cluster will turn on the high beam indi-
cator for the following reasons:
²High Beam Indicator Lamp-On Message-
Each time the cluster receives a high beam indicator
lamp-on message from the BCM indicating that the
headlamp high beams are turned On, the high beam
indicator will be illuminated. The indicator remains
illuminated until the cluster receives a high beam
indicator lamp-off message from the BCM.
²Actuator Test- Each time the cluster is put
through the actuator test, the high beam indicator
will be turned on for the duration of the test to con-
firm the functionality of the bulb and the cluster con-
trol circuitry.
The BCM continually monitors the exterior light-
ing (left multi-function) switch to determine the
proper outputs to the headlamp low beam and high
beam relays. The BCM then sends the proper high
beam indicator lamp-on and lamp-off messages to the
instrument cluster. If the high beam indicator fails to
light during the actuator test, replace the bulb with a
known good unit. For further diagnosis of the high
beam indicator or the instrument cluster circuitry
that controls the indicator, (Refer to 8 - ELECTRI-
CAL/INSTRUMENT CLUSTER - DIAGNOSIS AND
TESTING). For proper diagnosis of the headlamp
system, the BCM, the PCI data bus, or the electronic
message inputs to the instrument cluster that control
the high beam indicator, a DRBIIItscan tool is
required. Refer to the appropriate diagnostic infor-
mation.
LOW FUEL INDICATOR
DESCRIPTION
A low fuel indicator is standard equipment on all
instrument clusters. The low fuel indicator is located
near the left edge of the instrument cluster, to the left
of the tachometer. The low fuel indicator consists of an
International Control and Display Symbol icon for
ªFuelº imprinted on an amber lens. The lens is located
behind a cutout in the opaque layer of the instrument
cluster overlay. The dark outer layer of the overlay
prevents the icon from being clearly visible when the
indicator is not illuminated. The icon appears silhou-
etted against an amber field through the translucent
outer layer of the overlay when the indicator is illumi-
nated from behind by a replaceable incandescent bulb
and bulb holder unit located on the instrument cluster
electronic circuit board. When the exterior lighting is
turned On, the illumination intensity of the low fuel
indicator is dimmable, which is adjusted using the
panel lamps dimmer control ring on the control stalk
of the left multi-function switch. The low fuel indica-
8J - 22 INSTRUMENT CLUSTERWJ
FUEL GAUGE (Continued)
Page 442 of 2199

pletely controlled by the instrument cluster logic cir-
cuit, and that logic will only allow this indicator to
operate when the instrument cluster receives a bat-
tery current input on the fused ignition switch out-
put (run-start) circuit. Therefore, the indicator will
always be off when the ignition switch is in any posi-
tion except On or Start. The bulb only illuminates
when it is provided a path to ground by the instru-
ment cluster transistor. The instrument cluster will
turn on the overdrive off indicator for the following
reasons:
²Bulb Test- Each time the ignition switch is
turned to the On position the overdrive off indicator
is illuminated for about three seconds as a bulb test.
²Overdrive Off Indicator Lamp-On Message-
Each time the cluster receives an overdrive off indi-
cator lamp-on message from the PCM or TCM indi-
cating that the Off position of the overdrive off
switch has been selected, the overdrive off indicator
will be illuminated. The indicator remains illumi-
nated until the cluster receives an overdrive off indi-
cator lamp-off message from the PCM or TCM, or
until the ignition switch is turned to the Off position,
whichever occurs first.
²Actuator Test- Each time the cluster is put
through the actuator test, the overdrive off indicator
will be turned on for the duration of the test to con-
firm the functionality of the bulb and the cluster con-
trol circuitry.
The PCM or TCM continually monitors the over-
drive off switch to determine the proper outputs to
the automatic transmission. The PCM or TCM then
sends the proper overdrive off indicator lamp-on or
lamp-off messages to the instrument cluster. If the
overdrive off indicator fails to light during the bulb
test, replace the bulb with a known good unit. For
further diagnosis of the overdrive off indicator or the
instrument cluster circuitry that controls the indica-
tor, (Refer to 8 - ELECTRICAL/INSTRUMENT
CLUSTER - DIAGNOSIS AND TESTING). For
proper diagnosis of the overdrive control system, the
PCM, the TCM, the PCI data bus, or the electronic
message inputs to the instrument cluster that control
the overdrive off indicator, a DRBIIItscan tool is
required. Refer to the appropriate diagnostic infor-
mation.
REAR FOG LAMP INDICATOR
DESCRIPTION
A rear fog lamp indicator is standard equipment on
all instrument clusters, but is only functional on
vehicles equipped with optional rear fog lamps,
which are available only in certain international
markets where they are required. The rear fog lampindicator is located on the left edge of the instrument
cluster, to the left of the tachometer. The rear fog
lamp indicator consists of an International Control
and Display Symbol icon for ªRear Fog Lightº
imprinted on an amber lens. The lens is located
behind a cutout in the opaque layer of the instru-
ment cluster overlay. The dark outer layer of the
overlay prevents the indicator from being clearly vis-
ible when it is not illuminated. The icon appears sil-
houetted against an amber field through the
translucent outer layer of the overlay when the indi-
cator is illuminated from behind by a replaceable
incandescent bulb and bulb holder unit located on
the instrument cluster electronic circuit board. When
the exterior lighting is turned On, the illumination
intensity of the rear fog lamp indicator is dimmable,
which is adjusted using the panel lamps dimmer con-
trol ring on the control stalk of the left multi-func-
tion switch. The rear fog lamp indicator lens is
serviced as a unit with the instrument cluster lens,
hood and mask unit.
OPERATION
The rear fog lamp indicator gives an indication to
the vehicle operator whenever the rear fog lamps are
illuminated. This indicator is controlled by a transis-
tor on the instrument cluster electronic circuit board
based upon cluster programming and electronic mes-
sages received by the cluster from the Body Control
Module (BCM) over the Programmable Communica-
tions Interface (PCI) data bus. The rear fog lamp
indicator bulb is completely controlled by the instru-
ment cluster logic circuit, and that logic will allow
this indicator to operate whenever the instrument
cluster receives a battery current input on the fused
B(+) circuit. Therefore, the indicator can be illumi-
nated regardless of the ignition switch position. The
bulb only illuminates when it is provided a path to
ground by the instrument cluster transistor. The
instrument cluster will turn on the rear fog lamp
indicator for the following reasons:
²Rear Fog Lamp Indicator Lamp-On Mes-
sage- Each time the cluster receives a rear fog lamp
indicator lamp-on message from the BCM indicating
that the rear fog lamps are turned On, the rear fog
lamp indicator will be illuminated. The indicator
remains illuminated until the cluster receives a rear
fog lamp indicator lamp-off message from the BCM.
²Actuator Test- Each time the cluster is put
through the actuator test, the rear fog lamp indicator
will be turned on for the duration of the test to con-
firm the functionality of the bulb and the cluster con-
trol circuitry.
The BCM continually monitors the exterior light-
ing (left multi-function) switch to determine the
proper outputs to the rear fog lamp relay. The BCM
WJINSTRUMENT CLUSTER 8J - 27
OVERDRIVE OFF INDICATOR (Continued)
Page 458 of 2199
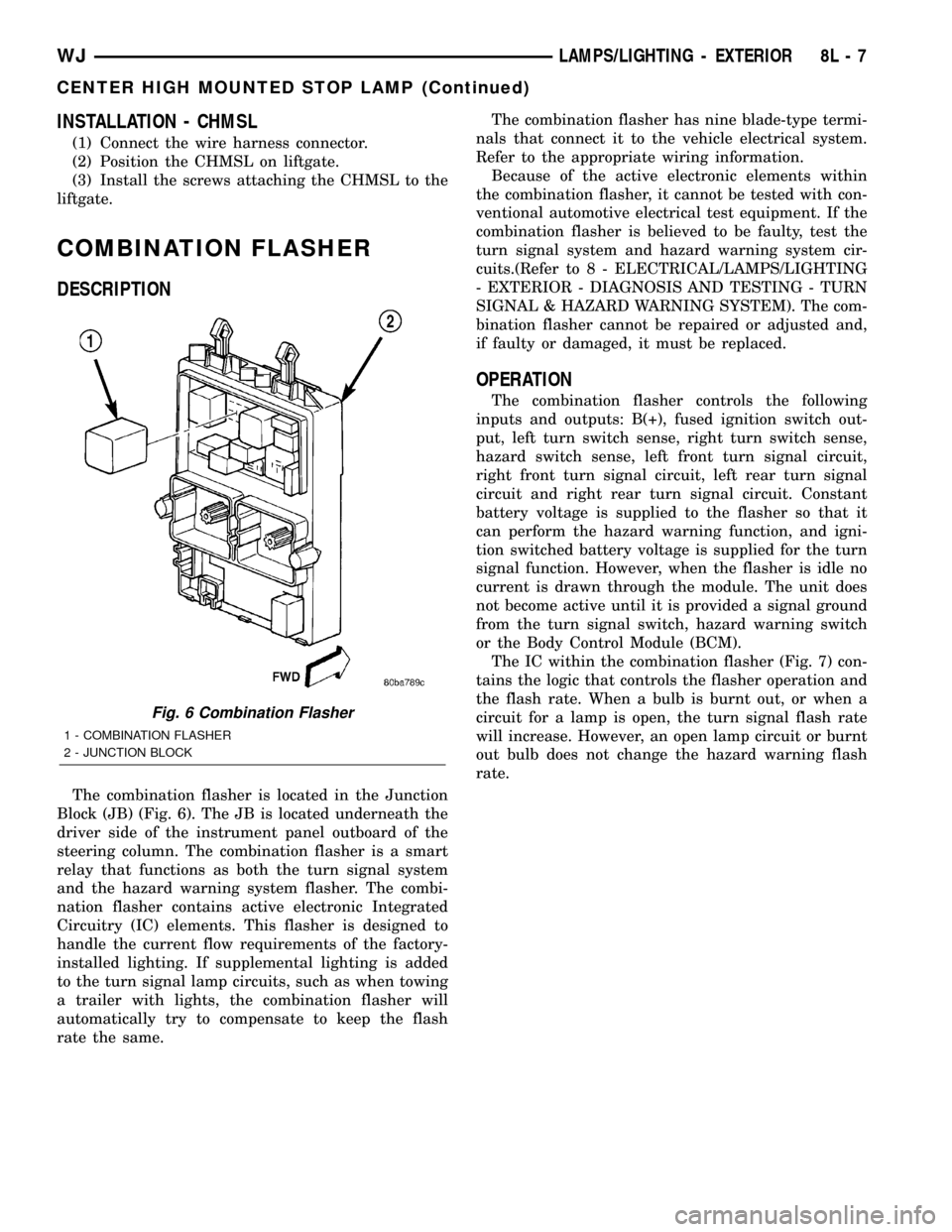
INSTALLATION - CHMSL
(1) Connect the wire harness connector.
(2) Position the CHMSL on liftgate.
(3) Install the screws attaching the CHMSL to the
liftgate.
COMBINATION FLASHER
DESCRIPTION
The combination flasher is located in the Junction
Block (JB) (Fig. 6). The JB is located underneath the
driver side of the instrument panel outboard of the
steering column. The combination flasher is a smart
relay that functions as both the turn signal system
and the hazard warning system flasher. The combi-
nation flasher contains active electronic Integrated
Circuitry (IC) elements. This flasher is designed to
handle the current flow requirements of the factory-
installed lighting. If supplemental lighting is added
to the turn signal lamp circuits, such as when towing
a trailer with lights, the combination flasher will
automatically try to compensate to keep the flash
rate the same.The combination flasher has nine blade-type termi-
nals that connect it to the vehicle electrical system.
Refer to the appropriate wiring information.
Because of the active electronic elements within
the combination flasher, it cannot be tested with con-
ventional automotive electrical test equipment. If the
combination flasher is believed to be faulty, test the
turn signal system and hazard warning system cir-
cuits.(Refer to 8 - ELECTRICAL/LAMPS/LIGHTING
- EXTERIOR - DIAGNOSIS AND TESTING - TURN
SIGNAL & HAZARD WARNING SYSTEM). The com-
bination flasher cannot be repaired or adjusted and,
if faulty or damaged, it must be replaced.
OPERATION
The combination flasher controls the following
inputs and outputs: B(+), fused ignition switch out-
put, left turn switch sense, right turn switch sense,
hazard switch sense, left front turn signal circuit,
right front turn signal circuit, left rear turn signal
circuit and right rear turn signal circuit. Constant
battery voltage is supplied to the flasher so that it
can perform the hazard warning function, and igni-
tion switched battery voltage is supplied for the turn
signal function. However, when the flasher is idle no
current is drawn through the module. The unit does
not become active until it is provided a signal ground
from the turn signal switch, hazard warning switch
or the Body Control Module (BCM).
The IC within the combination flasher (Fig. 7) con-
tains the logic that controls the flasher operation and
the flash rate. When a bulb is burnt out, or when a
circuit for a lamp is open, the turn signal flash rate
will increase. However, an open lamp circuit or burnt
out bulb does not change the hazard warning flash
rate.
Fig. 6 Combination Flasher
1 - COMBINATION FLASHER
2 - JUNCTION BLOCK
WJLAMPS/LIGHTING - EXTERIOR 8L - 7
CENTER HIGH MOUNTED STOP LAMP (Continued)
Page 465 of 2199
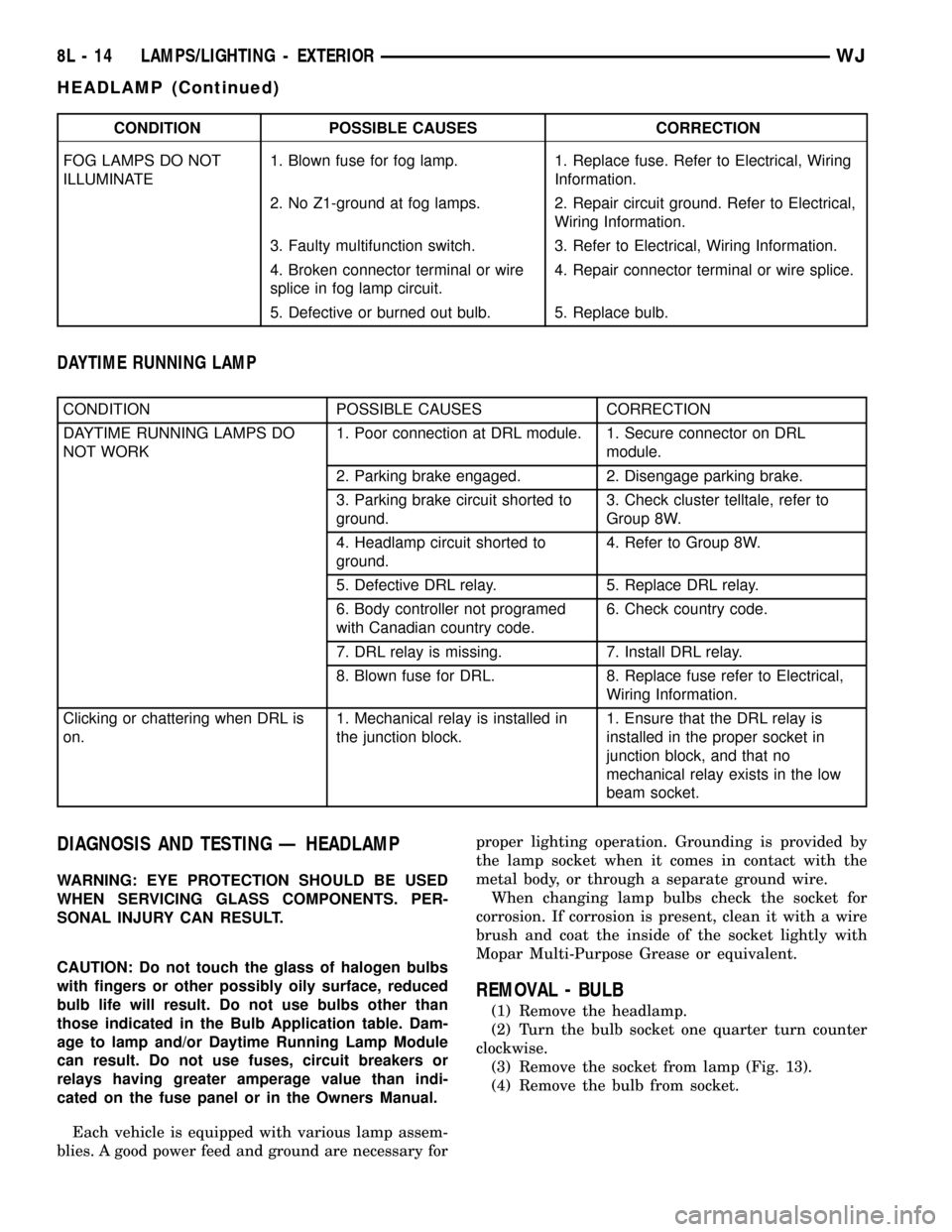
CONDITION POSSIBLE CAUSES CORRECTION
FOG LAMPS DO NOT
ILLUMINATE1. Blown fuse for fog lamp. 1. Replace fuse. Refer to Electrical, Wiring
Information.
2. No Z1-ground at fog lamps. 2. Repair circuit ground. Refer to Electrical,
Wiring Information.
3. Faulty multifunction switch. 3. Refer to Electrical, Wiring Information.
4. Broken connector terminal or wire
splice in fog lamp circuit.4. Repair connector terminal or wire splice.
5. Defective or burned out bulb. 5. Replace bulb.
DAYTIME RUNNING LAMP
CONDITION POSSIBLE CAUSES CORRECTION
DAYTIME RUNNING LAMPS DO
NOT WORK1. Poor connection at DRL module. 1. Secure connector on DRL
module.
2. Parking brake engaged. 2. Disengage parking brake.
3. Parking brake circuit shorted to
ground.3. Check cluster telltale, refer to
Group 8W.
4. Headlamp circuit shorted to
ground.4. Refer to Group 8W.
5. Defective DRL relay. 5. Replace DRL relay.
6. Body controller not programed
with Canadian country code.6. Check country code.
7. DRL relay is missing. 7. Install DRL relay.
8. Blown fuse for DRL. 8. Replace fuse refer to Electrical,
Wiring Information.
Clicking or chattering when DRL is
on.1. Mechanical relay is installed in
the junction block.1. Ensure that the DRL relay is
installed in the proper socket in
junction block, and that no
mechanical relay exists in the low
beam socket.
DIAGNOSIS AND TESTING Ð HEADLAMP
WARNING: EYE PROTECTION SHOULD BE USED
WHEN SERVICING GLASS COMPONENTS. PER-
SONAL INJURY CAN RESULT.
CAUTION: Do not touch the glass of halogen bulbs
with fingers or other possibly oily surface, reduced
bulb life will result. Do not use bulbs other than
those indicated in the Bulb Application table. Dam-
age to lamp and/or Daytime Running Lamp Module
can result. Do not use fuses, circuit breakers or
relays having greater amperage value than indi-
cated on the fuse panel or in the Owners Manual.
Each vehicle is equipped with various lamp assem-
blies. A good power feed and ground are necessary forproper lighting operation. Grounding is provided by
the lamp socket when it comes in contact with the
metal body, or through a separate ground wire.
When changing lamp bulbs check the socket for
corrosion. If corrosion is present, clean it with a wire
brush and coat the inside of the socket lightly with
Mopar Multi-Purpose Grease or equivalent.
REMOVAL - BULB
(1) Remove the headlamp.
(2) Turn the bulb socket one quarter turn counter
clockwise.
(3) Remove the socket from lamp (Fig. 13).
(4) Remove the bulb from socket.
8L - 14 LAMPS/LIGHTING - EXTERIORWJ
HEADLAMP (Continued)