Obd JEEP GRAND CHEROKEE 2003 WJ / 2.G Workshop Manual
[x] Cancel search | Manufacturer: JEEP, Model Year: 2003, Model line: GRAND CHEROKEE, Model: JEEP GRAND CHEROKEE 2003 WJ / 2.GPages: 2199, PDF Size: 76.01 MB
Page 224 of 2199
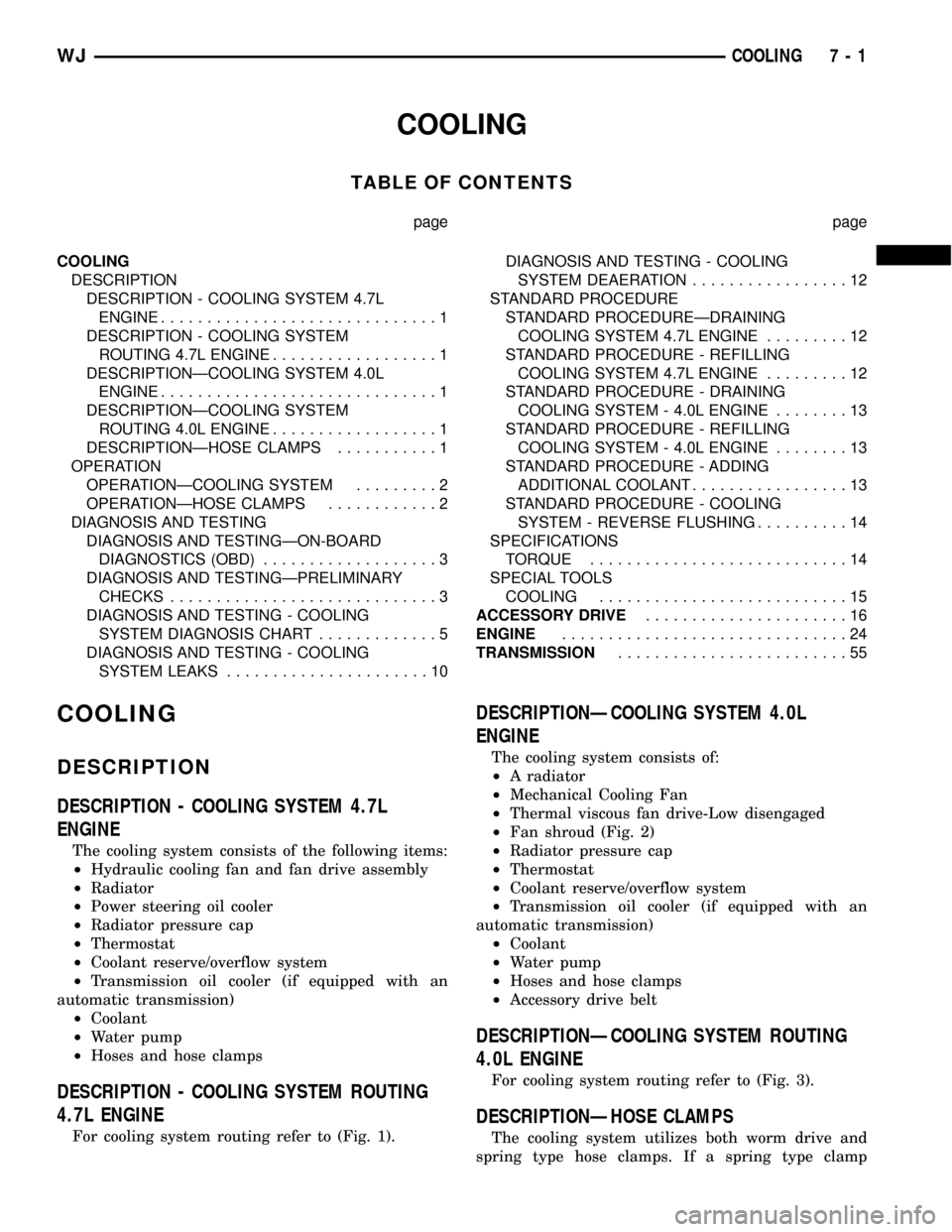
COOLING
TABLE OF CONTENTS
page page
COOLING
DESCRIPTION
DESCRIPTION - COOLING SYSTEM 4.7L
ENGINE..............................1
DESCRIPTION - COOLING SYSTEM
ROUTING 4.7L ENGINE..................1
DESCRIPTIONÐCOOLING SYSTEM 4.0L
ENGINE..............................1
DESCRIPTIONÐCOOLING SYSTEM
ROUTING 4.0L ENGINE..................1
DESCRIPTIONÐHOSE CLAMPS...........1
OPERATION
OPERATIONÐCOOLING SYSTEM.........2
OPERATIONÐHOSE CLAMPS............2
DIAGNOSIS AND TESTING
DIAGNOSIS AND TESTINGÐON-BOARD
DIAGNOSTICS (OBD)...................3
DIAGNOSIS AND TESTINGÐPRELIMINARY
CHECKS.............................3
DIAGNOSIS AND TESTING - COOLING
SYSTEM DIAGNOSIS CHART.............5
DIAGNOSIS AND TESTING - COOLING
SYSTEM LEAKS......................10DIAGNOSIS AND TESTING - COOLING
SYSTEM DEAERATION.................12
STANDARD PROCEDURE
STANDARD PROCEDUREÐDRAINING
COOLING SYSTEM 4.7L ENGINE.........12
STANDARD PROCEDURE - REFILLING
COOLING SYSTEM 4.7L ENGINE.........12
STANDARD PROCEDURE - DRAINING
COOLING SYSTEM - 4.0L ENGINE........13
STANDARD PROCEDURE - REFILLING
COOLING SYSTEM - 4.0L ENGINE........13
STANDARD PROCEDURE - ADDING
ADDITIONAL COOLANT.................13
STANDARD PROCEDURE - COOLING
SYSTEM - REVERSE FLUSHING..........14
SPECIFICATIONS
TORQUE............................14
SPECIAL TOOLS
COOLING...........................15
ACCESSORY DRIVE......................16
ENGINE...............................24
TRANSMISSION.........................55
COOLING
DESCRIPTION
DESCRIPTION - COOLING SYSTEM 4.7L
ENGINE
The cooling system consists of the following items:
²Hydraulic cooling fan and fan drive assembly
²Radiator
²Power steering oil cooler
²Radiator pressure cap
²Thermostat
²Coolant reserve/overflow system
²Transmission oil cooler (if equipped with an
automatic transmission)
²Coolant
²Water pump
²Hoses and hose clamps
DESCRIPTION - COOLING SYSTEM ROUTING
4.7L ENGINE
For cooling system routing refer to (Fig. 1).
DESCRIPTIONÐCOOLING SYSTEM 4.0L
ENGINE
The cooling system consists of:
²A radiator
²Mechanical Cooling Fan
²Thermal viscous fan drive-Low disengaged
²Fan shroud (Fig. 2)
²Radiator pressure cap
²Thermostat
²Coolant reserve/overflow system
²Transmission oil cooler (if equipped with an
automatic transmission)
²Coolant
²Water pump
²Hoses and hose clamps
²Accessory drive belt
DESCRIPTIONÐCOOLING SYSTEM ROUTING
4.0L ENGINE
For cooling system routing refer to (Fig. 3).
DESCRIPTIONÐHOSE CLAMPS
The cooling system utilizes both worm drive and
spring type hose clamps. If a spring type clamp
WJCOOLING 7 - 1
Page 226 of 2199
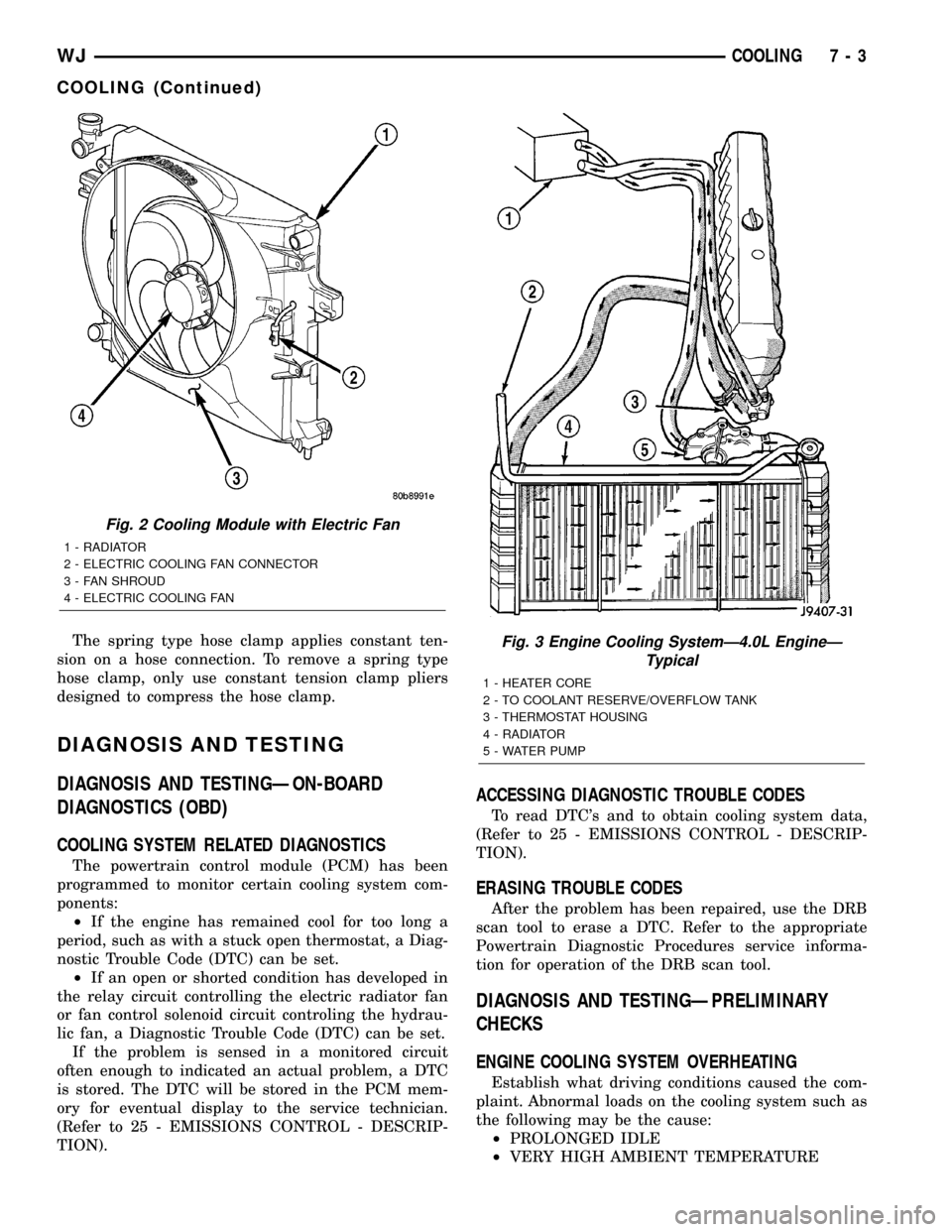
The spring type hose clamp applies constant ten-
sion on a hose connection. To remove a spring type
hose clamp, only use constant tension clamp pliers
designed to compress the hose clamp.
DIAGNOSIS AND TESTING
DIAGNOSIS AND TESTINGÐON-BOARD
DIAGNOSTICS (OBD)
COOLING SYSTEM RELATED DIAGNOSTICS
The powertrain control module (PCM) has been
programmed to monitor certain cooling system com-
ponents:
²If the engine has remained cool for too long a
period, such as with a stuck open thermostat, a Diag-
nostic Trouble Code (DTC) can be set.
²If an open or shorted condition has developed in
the relay circuit controlling the electric radiator fan
or fan control solenoid circuit controling the hydrau-
lic fan, a Diagnostic Trouble Code (DTC) can be set.
If the problem is sensed in a monitored circuit
often enough to indicated an actual problem, a DTC
is stored. The DTC will be stored in the PCM mem-
ory for eventual display to the service technician.
(Refer to 25 - EMISSIONS CONTROL - DESCRIP-
TION).
ACCESSING DIAGNOSTIC TROUBLE CODES
To read DTC's and to obtain cooling system data,
(Refer to 25 - EMISSIONS CONTROL - DESCRIP-
TION).
ERASING TROUBLE CODES
After the problem has been repaired, use the DRB
scan tool to erase a DTC. Refer to the appropriate
Powertrain Diagnostic Procedures service informa-
tion for operation of the DRB scan tool.
DIAGNOSIS AND TESTINGÐPRELIMINARY
CHECKS
ENGINE COOLING SYSTEM OVERHEATING
Establish what driving conditions caused the com-
plaint. Abnormal loads on the cooling system such as
the following may be the cause:
²PROLONGED IDLE
²VERY HIGH AMBIENT TEMPERATURE
Fig. 2 Cooling Module with Electric Fan
1 - RADIATOR
2 - ELECTRIC COOLING FAN CONNECTOR
3 - FAN SHROUD
4 - ELECTRIC COOLING FAN
Fig. 3 Engine Cooling SystemÐ4.0L EngineÐ
Typical
1 - HEATER CORE
2 - TO COOLANT RESERVE/OVERFLOW TANK
3 - THERMOSTAT HOUSING
4 - RADIATOR
5 - WATER PUMP
WJCOOLING 7 - 3
COOLING (Continued)
Page 333 of 2199
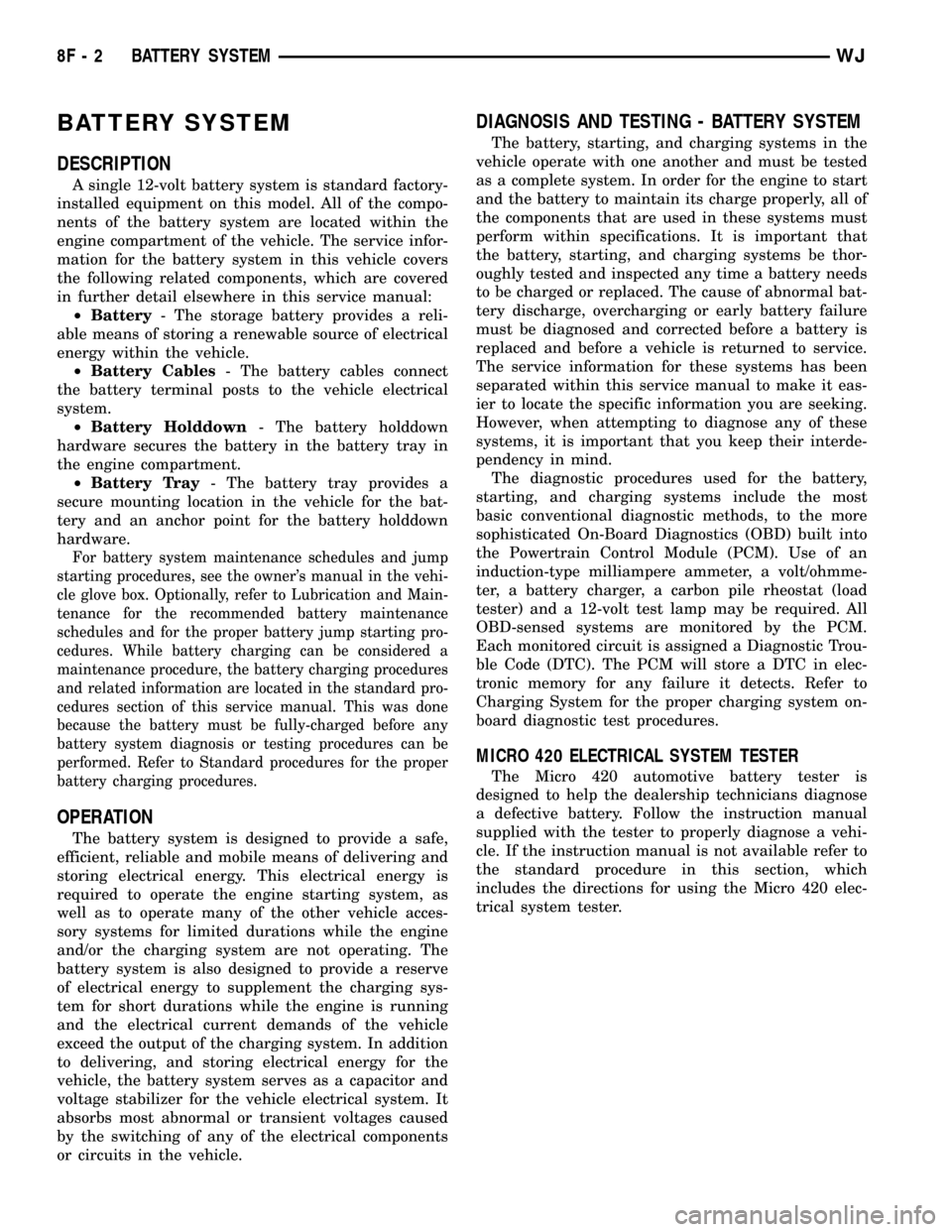
BATTERY SYSTEM
DESCRIPTION
A single 12-volt battery system is standard factory-
installed equipment on this model. All of the compo-
nents of the battery system are located within the
engine compartment of the vehicle. The service infor-
mation for the battery system in this vehicle covers
the following related components, which are covered
in further detail elsewhere in this service manual:
²Battery- The storage battery provides a reli-
able means of storing a renewable source of electrical
energy within the vehicle.
²Battery Cables- The battery cables connect
the battery terminal posts to the vehicle electrical
system.
²Battery Holddown- The battery holddown
hardware secures the battery in the battery tray in
the engine compartment.
²Battery Tray- The battery tray provides a
secure mounting location in the vehicle for the bat-
tery and an anchor point for the battery holddown
hardware.
For battery system maintenance schedules and jump
starting procedures, see the owner's manual in the vehi-
cle glove box. Optionally, refer to Lubrication and Main-
tenance for the recommended battery maintenance
schedules and for the proper battery jump starting pro-
cedures. While battery charging can be considered a
maintenance procedure, the battery charging procedures
and related information are located in the standard pro-
cedures section of this service manual. This was done
because the battery must be fully-charged before any
battery system diagnosis or testing procedures can be
performed. Refer to Standard procedures for the proper
battery charging procedures.
OPERATION
The battery system is designed to provide a safe,
efficient, reliable and mobile means of delivering and
storing electrical energy. This electrical energy is
required to operate the engine starting system, as
well as to operate many of the other vehicle acces-
sory systems for limited durations while the engine
and/or the charging system are not operating. The
battery system is also designed to provide a reserve
of electrical energy to supplement the charging sys-
tem for short durations while the engine is running
and the electrical current demands of the vehicle
exceed the output of the charging system. In addition
to delivering, and storing electrical energy for the
vehicle, the battery system serves as a capacitor and
voltage stabilizer for the vehicle electrical system. It
absorbs most abnormal or transient voltages caused
by the switching of any of the electrical components
or circuits in the vehicle.
DIAGNOSIS AND TESTING - BATTERY SYSTEM
The battery, starting, and charging systems in the
vehicle operate with one another and must be tested
as a complete system. In order for the engine to start
and the battery to maintain its charge properly, all of
the components that are used in these systems must
perform within specifications. It is important that
the battery, starting, and charging systems be thor-
oughly tested and inspected any time a battery needs
to be charged or replaced. The cause of abnormal bat-
tery discharge, overcharging or early battery failure
must be diagnosed and corrected before a battery is
replaced and before a vehicle is returned to service.
The service information for these systems has been
separated within this service manual to make it eas-
ier to locate the specific information you are seeking.
However, when attempting to diagnose any of these
systems, it is important that you keep their interde-
pendency in mind.
The diagnostic procedures used for the battery,
starting, and charging systems include the most
basic conventional diagnostic methods, to the more
sophisticated On-Board Diagnostics (OBD) built into
the Powertrain Control Module (PCM). Use of an
induction-type milliampere ammeter, a volt/ohmme-
ter, a battery charger, a carbon pile rheostat (load
tester) and a 12-volt test lamp may be required. All
OBD-sensed systems are monitored by the PCM.
Each monitored circuit is assigned a Diagnostic Trou-
ble Code (DTC). The PCM will store a DTC in elec-
tronic memory for any failure it detects. Refer to
Charging System for the proper charging system on-
board diagnostic test procedures.
MICRO 420 ELECTRICAL SYSTEM TESTER
The Micro 420 automotive battery tester is
designed to help the dealership technicians diagnose
a defective battery. Follow the instruction manual
supplied with the tester to properly diagnose a vehi-
cle. If the instruction manual is not available refer to
the standard procedure in this section, which
includes the directions for using the Micro 420 elec-
trical system tester.
8F - 2 BATTERY SYSTEMWJ
Page 355 of 2199
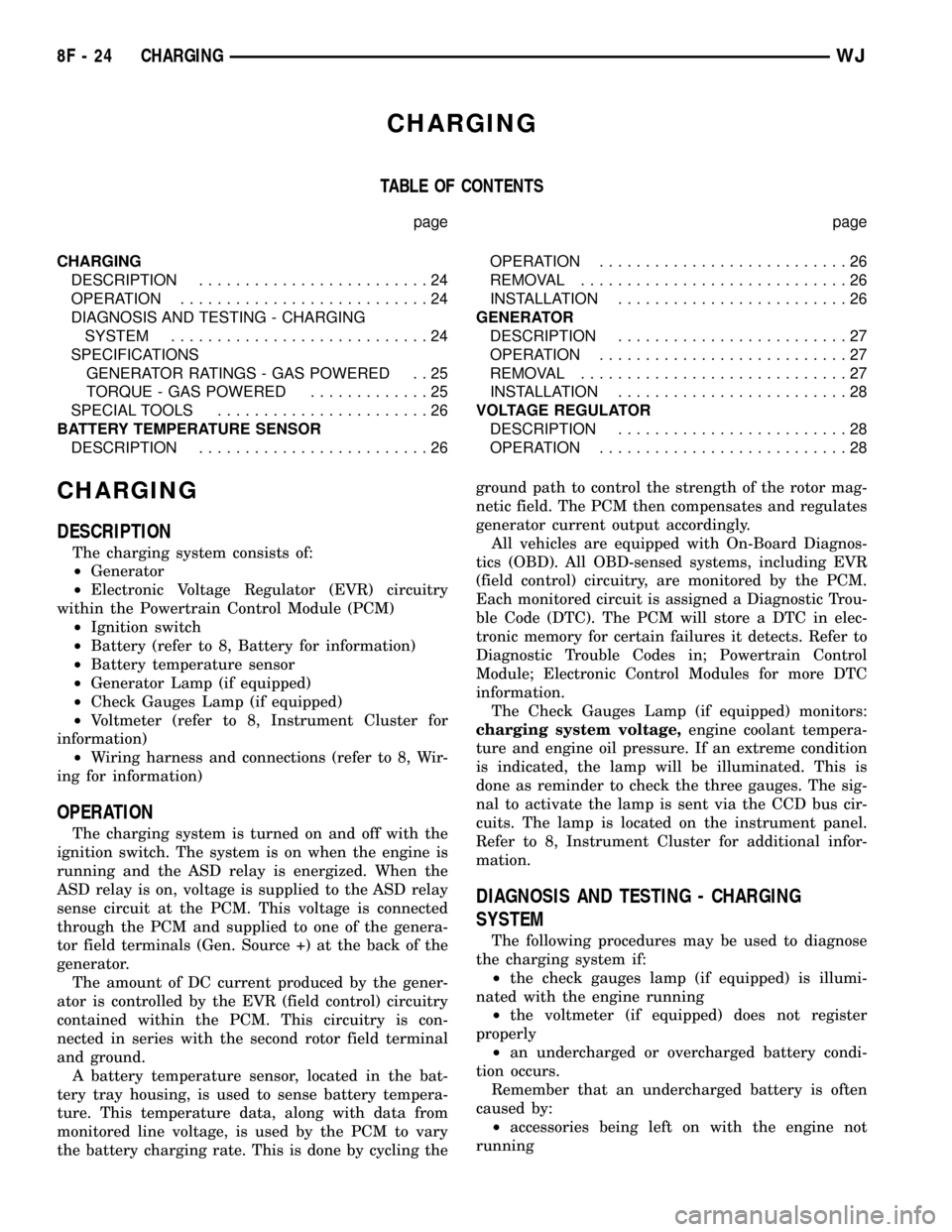
CHARGING
TABLE OF CONTENTS
page page
CHARGING
DESCRIPTION.........................24
OPERATION...........................24
DIAGNOSIS AND TESTING - CHARGING
SYSTEM............................24
SPECIFICATIONS
GENERATOR RATINGS - GAS POWERED . . 25
TORQUE - GAS POWERED.............25
SPECIAL TOOLS.......................26
BATTERY TEMPERATURE SENSOR
DESCRIPTION.........................26OPERATION...........................26
REMOVAL.............................26
INSTALLATION.........................26
GENERATOR
DESCRIPTION.........................27
OPERATION...........................27
REMOVAL.............................27
INSTALLATION.........................28
VOLTAGE REGULATOR
DESCRIPTION.........................28
OPERATION...........................28
CHARGING
DESCRIPTION
The charging system consists of:
²Generator
²Electronic Voltage Regulator (EVR) circuitry
within the Powertrain Control Module (PCM)
²Ignition switch
²Battery (refer to 8, Battery for information)
²Battery temperature sensor
²Generator Lamp (if equipped)
²Check Gauges Lamp (if equipped)
²Voltmeter (refer to 8, Instrument Cluster for
information)
²Wiring harness and connections (refer to 8, Wir-
ing for information)
OPERATION
The charging system is turned on and off with the
ignition switch. The system is on when the engine is
running and the ASD relay is energized. When the
ASD relay is on, voltage is supplied to the ASD relay
sense circuit at the PCM. This voltage is connected
through the PCM and supplied to one of the genera-
tor field terminals (Gen. Source +) at the back of the
generator.
The amount of DC current produced by the gener-
ator is controlled by the EVR (field control) circuitry
contained within the PCM. This circuitry is con-
nected in series with the second rotor field terminal
and ground.
A battery temperature sensor, located in the bat-
tery tray housing, is used to sense battery tempera-
ture. This temperature data, along with data from
monitored line voltage, is used by the PCM to vary
the battery charging rate. This is done by cycling theground path to control the strength of the rotor mag-
netic field. The PCM then compensates and regulates
generator current output accordingly.
All vehicles are equipped with On-Board Diagnos-
tics (OBD). All OBD-sensed systems, including EVR
(field control) circuitry, are monitored by the PCM.
Each monitored circuit is assigned a Diagnostic Trou-
ble Code (DTC). The PCM will store a DTC in elec-
tronic memory for certain failures it detects. Refer to
Diagnostic Trouble Codes in; Powertrain Control
Module; Electronic Control Modules for more DTC
information.
The Check Gauges Lamp (if equipped) monitors:
charging system voltage,engine coolant tempera-
ture and engine oil pressure. If an extreme condition
is indicated, the lamp will be illuminated. This is
done as reminder to check the three gauges. The sig-
nal to activate the lamp is sent via the CCD bus cir-
cuits. The lamp is located on the instrument panel.
Refer to 8, Instrument Cluster for additional infor-
mation.
DIAGNOSIS AND TESTING - CHARGING
SYSTEM
The following procedures may be used to diagnose
the charging system if:
²the check gauges lamp (if equipped) is illumi-
nated with the engine running
²the voltmeter (if equipped) does not register
properly
²an undercharged or overcharged battery condi-
tion occurs.
Remember that an undercharged battery is often
caused by:
²accessories being left on with the engine not
running
8F - 24 CHARGINGWJ
Page 356 of 2199
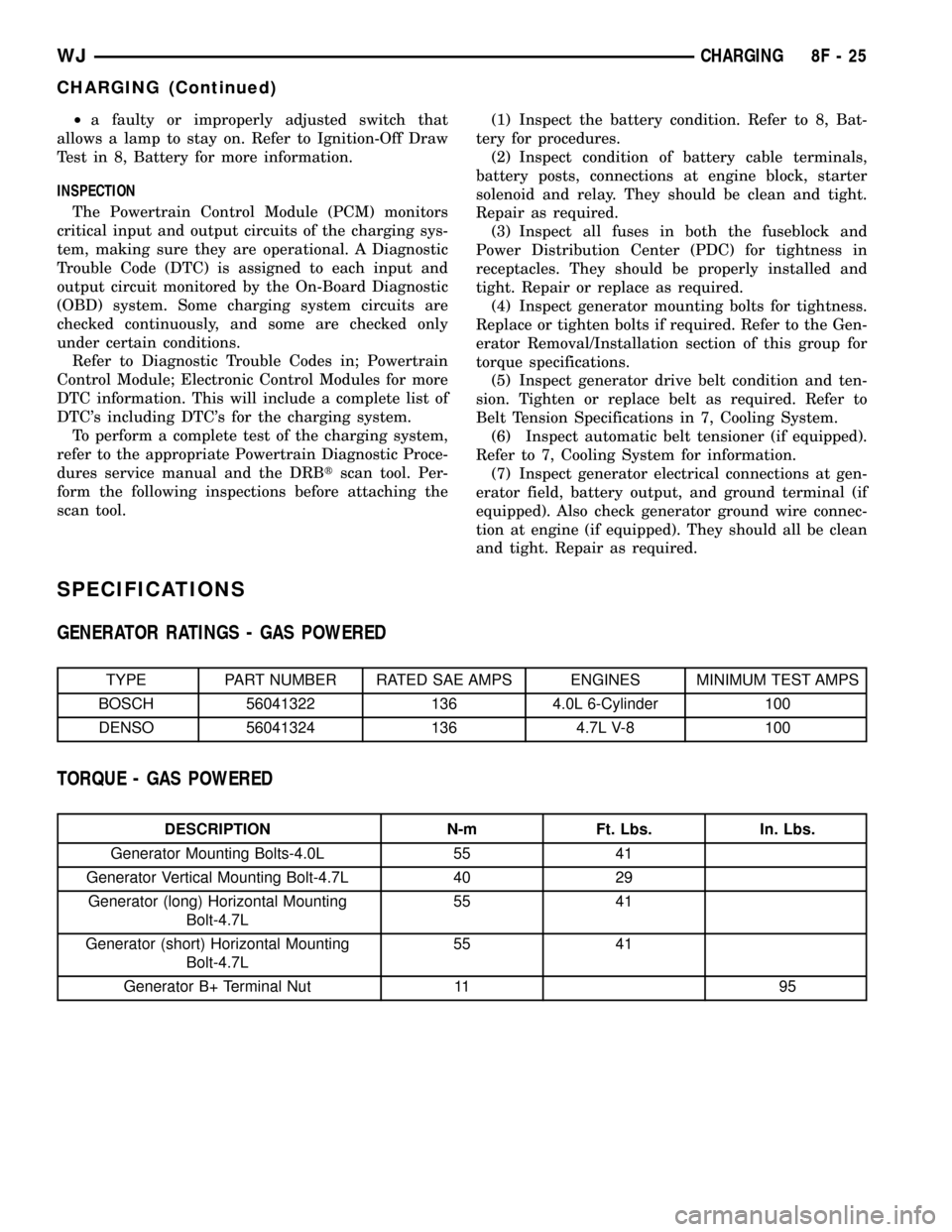
²a faulty or improperly adjusted switch that
allows a lamp to stay on. Refer to Ignition-Off Draw
Test in 8, Battery for more information.
INSPECTION
The Powertrain Control Module (PCM) monitors
critical input and output circuits of the charging sys-
tem, making sure they are operational. A Diagnostic
Trouble Code (DTC) is assigned to each input and
output circuit monitored by the On-Board Diagnostic
(OBD) system. Some charging system circuits are
checked continuously, and some are checked only
under certain conditions.
Refer to Diagnostic Trouble Codes in; Powertrain
Control Module; Electronic Control Modules for more
DTC information. This will include a complete list of
DTC's including DTC's for the charging system.
To perform a complete test of the charging system,
refer to the appropriate Powertrain Diagnostic Proce-
dures service manual and the DRBtscan tool. Per-
form the following inspections before attaching the
scan tool.(1) Inspect the battery condition. Refer to 8, Bat-
tery for procedures.
(2) Inspect condition of battery cable terminals,
battery posts, connections at engine block, starter
solenoid and relay. They should be clean and tight.
Repair as required.
(3) Inspect all fuses in both the fuseblock and
Power Distribution Center (PDC) for tightness in
receptacles. They should be properly installed and
tight. Repair or replace as required.
(4) Inspect generator mounting bolts for tightness.
Replace or tighten bolts if required. Refer to the Gen-
erator Removal/Installation section of this group for
torque specifications.
(5) Inspect generator drive belt condition and ten-
sion. Tighten or replace belt as required. Refer to
Belt Tension Specifications in 7, Cooling System.
(6) Inspect automatic belt tensioner (if equipped).
Refer to 7, Cooling System for information.
(7) Inspect generator electrical connections at gen-
erator field, battery output, and ground terminal (if
equipped). Also check generator ground wire connec-
tion at engine (if equipped). They should all be clean
and tight. Repair as required.
SPECIFICATIONS
GENERATOR RATINGS - GAS POWERED
TYPE PART NUMBER RATED SAE AMPS ENGINES MINIMUM TEST AMPS
BOSCH 56041322 136 4.0L 6-Cylinder 100
DENSO 56041324 136 4.7L V-8 100
TORQUE - GAS POWERED
DESCRIPTION N-m Ft. Lbs. In. Lbs.
Generator Mounting Bolts-4.0L 55 41
Generator Vertical Mounting Bolt-4.7L 40 29
Generator (long) Horizontal Mounting
Bolt-4.7L55 41
Generator (short) Horizontal Mounting
Bolt-4.7L55 41
Generator B+ Terminal Nut 11 95
WJCHARGING 8F - 25
CHARGING (Continued)
Page 357 of 2199
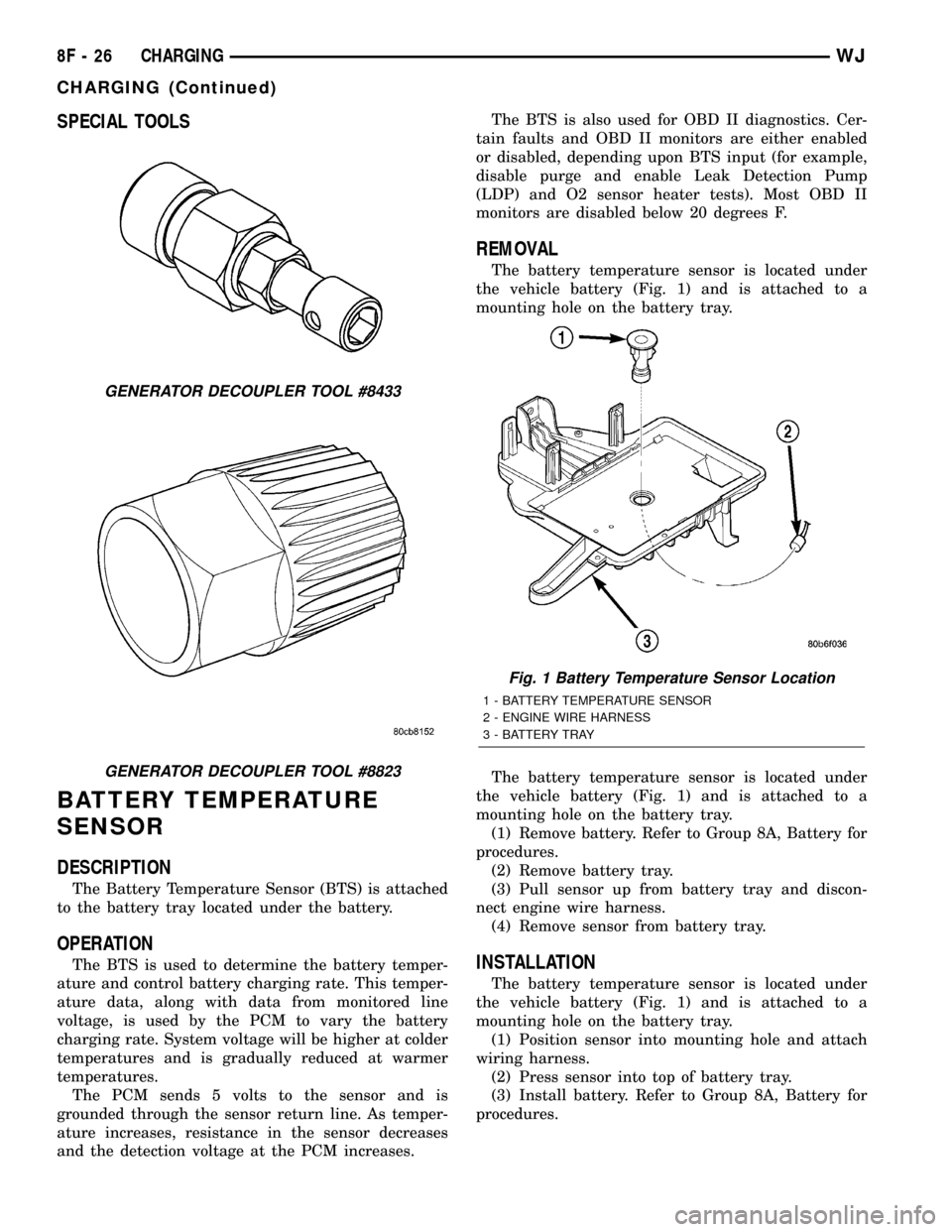
SPECIAL TOOLS
BATTERY TEMPERATURE
SENSOR
DESCRIPTION
The Battery Temperature Sensor (BTS) is attached
to the battery tray located under the battery.
OPERATION
The BTS is used to determine the battery temper-
ature and control battery charging rate. This temper-
ature data, along with data from monitored line
voltage, is used by the PCM to vary the battery
charging rate. System voltage will be higher at colder
temperatures and is gradually reduced at warmer
temperatures.
The PCM sends 5 volts to the sensor and is
grounded through the sensor return line. As temper-
ature increases, resistance in the sensor decreases
and the detection voltage at the PCM increases.The BTS is also used for OBD II diagnostics. Cer-
tain faults and OBD II monitors are either enabled
or disabled, depending upon BTS input (for example,
disable purge and enable Leak Detection Pump
(LDP) and O2 sensor heater tests). Most OBD II
monitors are disabled below 20 degrees F.
REMOVAL
The battery temperature sensor is located under
the vehicle battery (Fig. 1) and is attached to a
mounting hole on the battery tray.
The battery temperature sensor is located under
the vehicle battery (Fig. 1) and is attached to a
mounting hole on the battery tray.
(1) Remove battery. Refer to Group 8A, Battery for
procedures.
(2) Remove battery tray.
(3) Pull sensor up from battery tray and discon-
nect engine wire harness.
(4) Remove sensor from battery tray.
INSTALLATION
The battery temperature sensor is located under
the vehicle battery (Fig. 1) and is attached to a
mounting hole on the battery tray.
(1) Position sensor into mounting hole and attach
wiring harness.
(2) Press sensor into top of battery tray.
(3) Install battery. Refer to Group 8A, Battery for
procedures.
GENERATOR DECOUPLER TOOL #8433
GENERATOR DECOUPLER TOOL #8823
Fig. 1 Battery Temperature Sensor Location
1 - BATTERY TEMPERATURE SENSOR
2 - ENGINE WIRE HARNESS
3 - BATTERY TRAY
8F - 26 CHARGINGWJ
CHARGING (Continued)
Page 360 of 2199
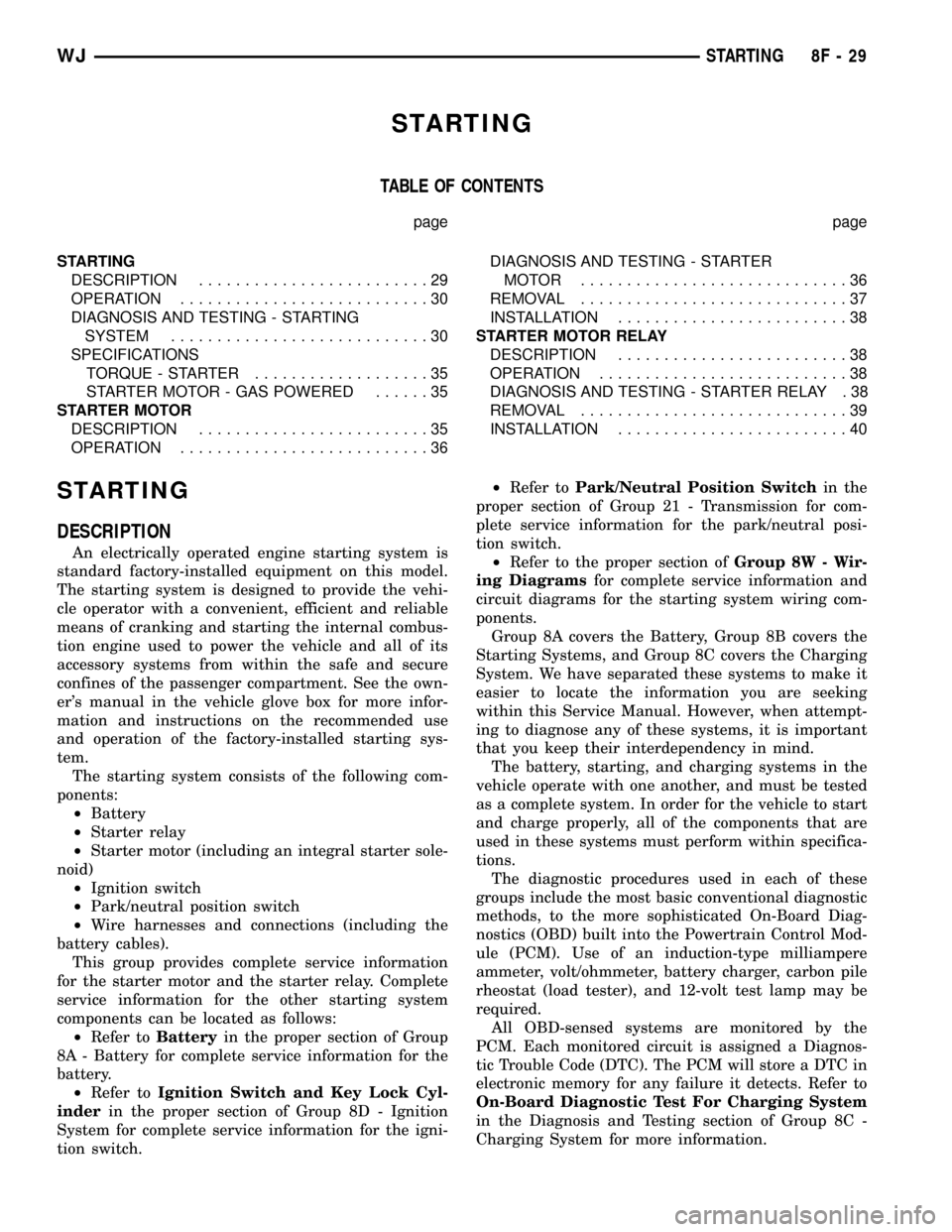
STARTING
TABLE OF CONTENTS
page page
STARTING
DESCRIPTION.........................29
OPERATION...........................30
DIAGNOSIS AND TESTING - STARTING
SYSTEM............................30
SPECIFICATIONS
TORQUE - STARTER...................35
STARTER MOTOR - GAS POWERED......35
STARTER MOTOR
DESCRIPTION.........................35
OPERATION...........................36DIAGNOSIS AND TESTING - STARTER
MOTOR .............................36
REMOVAL.............................37
INSTALLATION.........................38
STARTER MOTOR RELAY
DESCRIPTION.........................38
OPERATION...........................38
DIAGNOSIS AND TESTING - STARTER RELAY . 38
REMOVAL.............................39
INSTALLATION.........................40
STARTING
DESCRIPTION
An electrically operated engine starting system is
standard factory-installed equipment on this model.
The starting system is designed to provide the vehi-
cle operator with a convenient, efficient and reliable
means of cranking and starting the internal combus-
tion engine used to power the vehicle and all of its
accessory systems from within the safe and secure
confines of the passenger compartment. See the own-
er's manual in the vehicle glove box for more infor-
mation and instructions on the recommended use
and operation of the factory-installed starting sys-
tem.
The starting system consists of the following com-
ponents:
²Battery
²Starter relay
²Starter motor (including an integral starter sole-
noid)
²Ignition switch
²Park/neutral position switch
²Wire harnesses and connections (including the
battery cables).
This group provides complete service information
for the starter motor and the starter relay. Complete
service information for the other starting system
components can be located as follows:
²Refer toBatteryin the proper section of Group
8A - Battery for complete service information for the
battery.
²Refer toIgnition Switch and Key Lock Cyl-
inderin the proper section of Group 8D - Ignition
System for complete service information for the igni-
tion switch.²Refer toPark/Neutral Position Switchin the
proper section of Group 21 - Transmission for com-
plete service information for the park/neutral posi-
tion switch.
²Refer to the proper section ofGroup 8W - Wir-
ing Diagramsfor complete service information and
circuit diagrams for the starting system wiring com-
ponents.
Group 8A covers the Battery, Group 8B covers the
Starting Systems, and Group 8C covers the Charging
System. We have separated these systems to make it
easier to locate the information you are seeking
within this Service Manual. However, when attempt-
ing to diagnose any of these systems, it is important
that you keep their interdependency in mind.
The battery, starting, and charging systems in the
vehicle operate with one another, and must be tested
as a complete system. In order for the vehicle to start
and charge properly, all of the components that are
used in these systems must perform within specifica-
tions.
The diagnostic procedures used in each of these
groups include the most basic conventional diagnostic
methods, to the more sophisticated On-Board Diag-
nostics (OBD) built into the Powertrain Control Mod-
ule (PCM). Use of an induction-type milliampere
ammeter, volt/ohmmeter, battery charger, carbon pile
rheostat (load tester), and 12-volt test lamp may be
required.
All OBD-sensed systems are monitored by the
PCM. Each monitored circuit is assigned a Diagnos-
tic Trouble Code (DTC). The PCM will store a DTC in
electronic memory for any failure it detects. Refer to
On-Board Diagnostic Test For Charging System
in the Diagnosis and Testing section of Group 8C -
Charging System for more information.
WJSTARTING 8F - 29
Page 361 of 2199
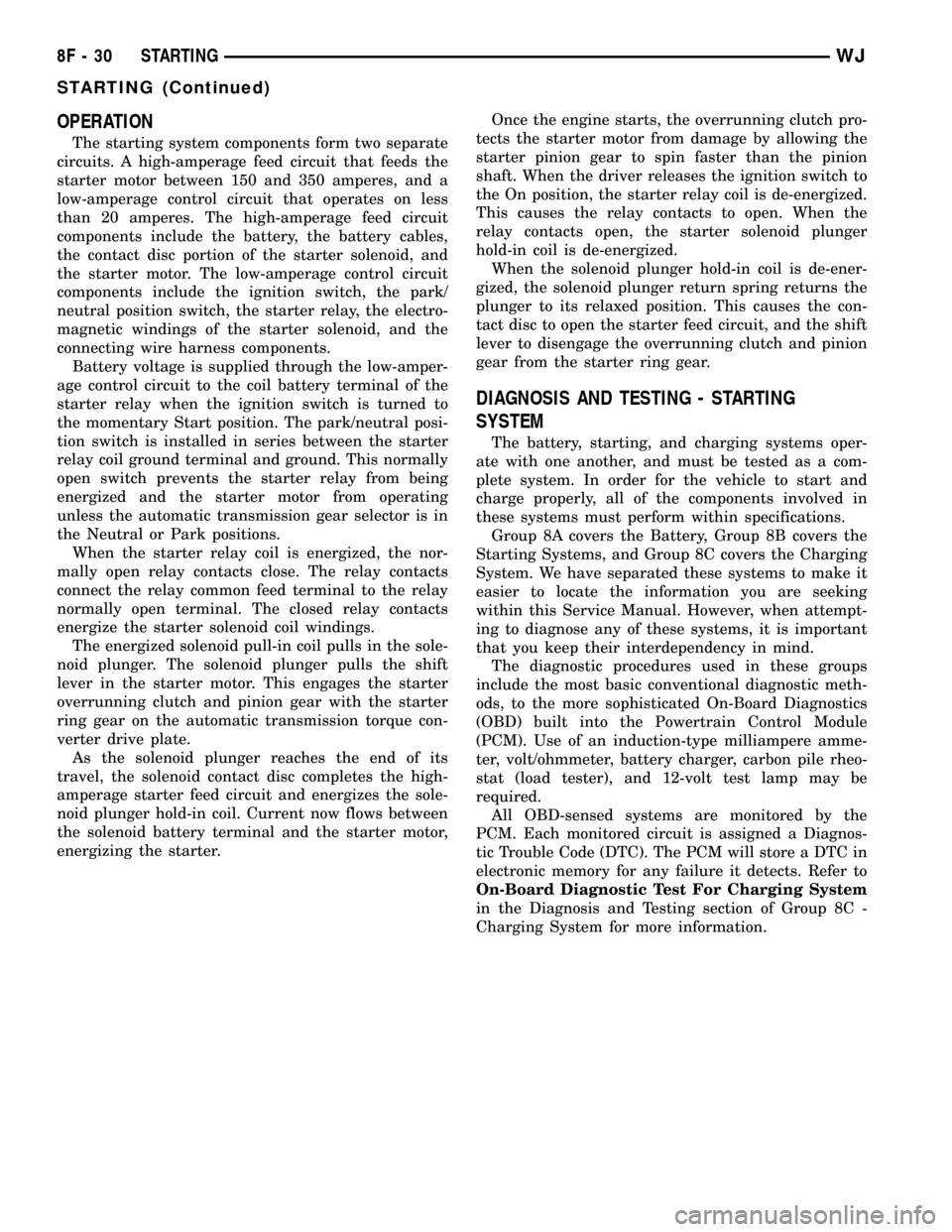
OPERATION
The starting system components form two separate
circuits. A high-amperage feed circuit that feeds the
starter motor between 150 and 350 amperes, and a
low-amperage control circuit that operates on less
than 20 amperes. The high-amperage feed circuit
components include the battery, the battery cables,
the contact disc portion of the starter solenoid, and
the starter motor. The low-amperage control circuit
components include the ignition switch, the park/
neutral position switch, the starter relay, the electro-
magnetic windings of the starter solenoid, and the
connecting wire harness components.
Battery voltage is supplied through the low-amper-
age control circuit to the coil battery terminal of the
starter relay when the ignition switch is turned to
the momentary Start position. The park/neutral posi-
tion switch is installed in series between the starter
relay coil ground terminal and ground. This normally
open switch prevents the starter relay from being
energized and the starter motor from operating
unless the automatic transmission gear selector is in
the Neutral or Park positions.
When the starter relay coil is energized, the nor-
mally open relay contacts close. The relay contacts
connect the relay common feed terminal to the relay
normally open terminal. The closed relay contacts
energize the starter solenoid coil windings.
The energized solenoid pull-in coil pulls in the sole-
noid plunger. The solenoid plunger pulls the shift
lever in the starter motor. This engages the starter
overrunning clutch and pinion gear with the starter
ring gear on the automatic transmission torque con-
verter drive plate.
As the solenoid plunger reaches the end of its
travel, the solenoid contact disc completes the high-
amperage starter feed circuit and energizes the sole-
noid plunger hold-in coil. Current now flows between
the solenoid battery terminal and the starter motor,
energizing the starter.Once the engine starts, the overrunning clutch pro-
tects the starter motor from damage by allowing the
starter pinion gear to spin faster than the pinion
shaft. When the driver releases the ignition switch to
the On position, the starter relay coil is de-energized.
This causes the relay contacts to open. When the
relay contacts open, the starter solenoid plunger
hold-in coil is de-energized.
When the solenoid plunger hold-in coil is de-ener-
gized, the solenoid plunger return spring returns the
plunger to its relaxed position. This causes the con-
tact disc to open the starter feed circuit, and the shift
lever to disengage the overrunning clutch and pinion
gear from the starter ring gear.
DIAGNOSIS AND TESTING - STARTING
SYSTEM
The battery, starting, and charging systems oper-
ate with one another, and must be tested as a com-
plete system. In order for the vehicle to start and
charge properly, all of the components involved in
these systems must perform within specifications.
Group 8A covers the Battery, Group 8B covers the
Starting Systems, and Group 8C covers the Charging
System. We have separated these systems to make it
easier to locate the information you are seeking
within this Service Manual. However, when attempt-
ing to diagnose any of these systems, it is important
that you keep their interdependency in mind.
The diagnostic procedures used in these groups
include the most basic conventional diagnostic meth-
ods, to the more sophisticated On-Board Diagnostics
(OBD) built into the Powertrain Control Module
(PCM). Use of an induction-type milliampere amme-
ter, volt/ohmmeter, battery charger, carbon pile rheo-
stat (load tester), and 12-volt test lamp may be
required.
All OBD-sensed systems are monitored by the
PCM. Each monitored circuit is assigned a Diagnos-
tic Trouble Code (DTC). The PCM will store a DTC in
electronic memory for any failure it detects. Refer to
On-Board Diagnostic Test For Charging System
in the Diagnosis and Testing section of Group 8C -
Charging System for more information.
8F - 30 STARTINGWJ
STARTING (Continued)
Page 438 of 2199
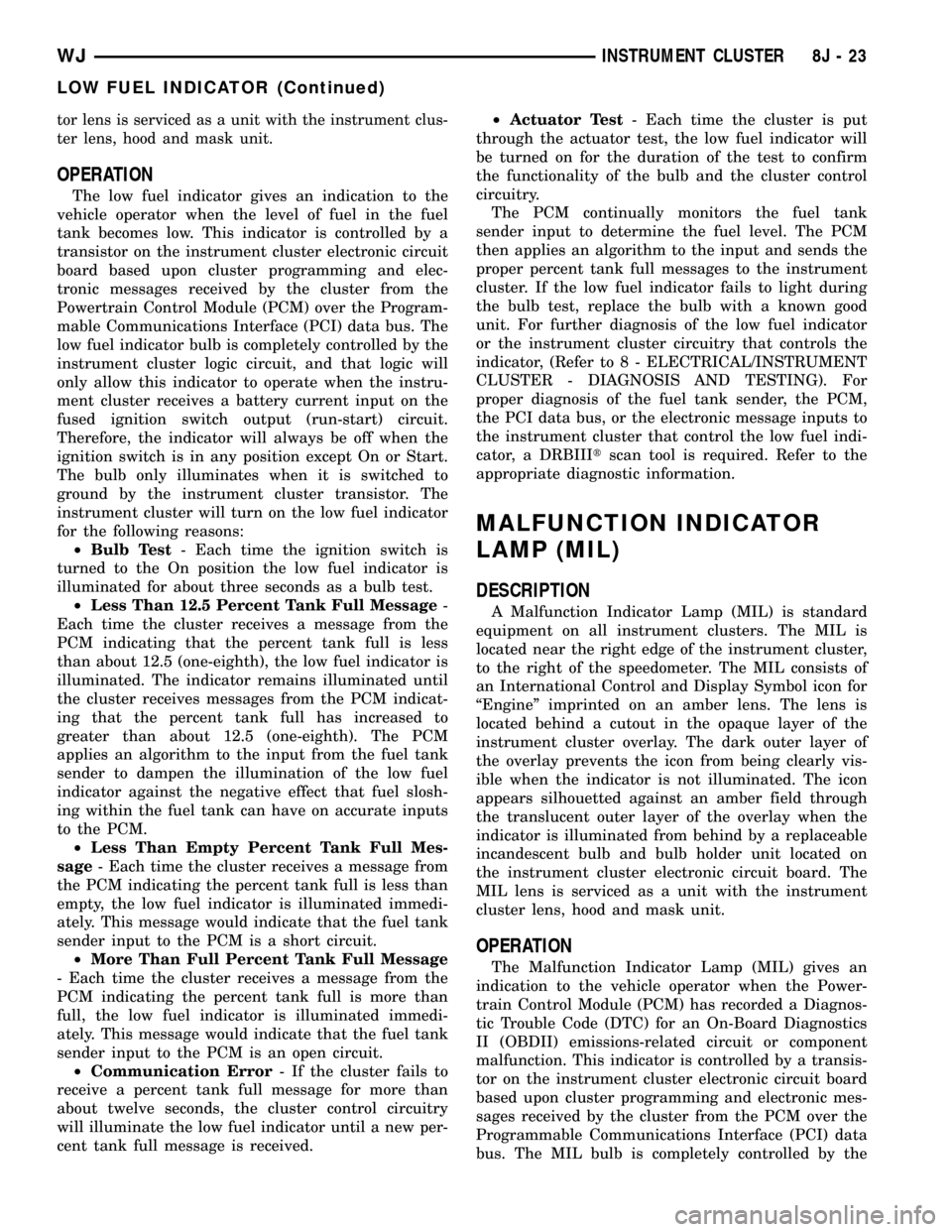
tor lens is serviced as a unit with the instrument clus-
ter lens, hood and mask unit.
OPERATION
The low fuel indicator gives an indication to the
vehicle operator when the level of fuel in the fuel
tank becomes low. This indicator is controlled by a
transistor on the instrument cluster electronic circuit
board based upon cluster programming and elec-
tronic messages received by the cluster from the
Powertrain Control Module (PCM) over the Program-
mable Communications Interface (PCI) data bus. The
low fuel indicator bulb is completely controlled by the
instrument cluster logic circuit, and that logic will
only allow this indicator to operate when the instru-
ment cluster receives a battery current input on the
fused ignition switch output (run-start) circuit.
Therefore, the indicator will always be off when the
ignition switch is in any position except On or Start.
The bulb only illuminates when it is switched to
ground by the instrument cluster transistor. The
instrument cluster will turn on the low fuel indicator
for the following reasons:
²Bulb Test- Each time the ignition switch is
turned to the On position the low fuel indicator is
illuminated for about three seconds as a bulb test.
²Less Than 12.5 Percent Tank Full Message-
Each time the cluster receives a message from the
PCM indicating that the percent tank full is less
than about 12.5 (one-eighth), the low fuel indicator is
illuminated. The indicator remains illuminated until
the cluster receives messages from the PCM indicat-
ing that the percent tank full has increased to
greater than about 12.5 (one-eighth). The PCM
applies an algorithm to the input from the fuel tank
sender to dampen the illumination of the low fuel
indicator against the negative effect that fuel slosh-
ing within the fuel tank can have on accurate inputs
to the PCM.
²Less Than Empty Percent Tank Full Mes-
sage- Each time the cluster receives a message from
the PCM indicating the percent tank full is less than
empty, the low fuel indicator is illuminated immedi-
ately. This message would indicate that the fuel tank
sender input to the PCM is a short circuit.
²More Than Full Percent Tank Full Message
- Each time the cluster receives a message from the
PCM indicating the percent tank full is more than
full, the low fuel indicator is illuminated immedi-
ately. This message would indicate that the fuel tank
sender input to the PCM is an open circuit.
²Communication Error- If the cluster fails to
receive a percent tank full message for more than
about twelve seconds, the cluster control circuitry
will illuminate the low fuel indicator until a new per-
cent tank full message is received.²Actuator Test- Each time the cluster is put
through the actuator test, the low fuel indicator will
be turned on for the duration of the test to confirm
the functionality of the bulb and the cluster control
circuitry.
The PCM continually monitors the fuel tank
sender input to determine the fuel level. The PCM
then applies an algorithm to the input and sends the
proper percent tank full messages to the instrument
cluster. If the low fuel indicator fails to light during
the bulb test, replace the bulb with a known good
unit. For further diagnosis of the low fuel indicator
or the instrument cluster circuitry that controls the
indicator, (Refer to 8 - ELECTRICAL/INSTRUMENT
CLUSTER - DIAGNOSIS AND TESTING). For
proper diagnosis of the fuel tank sender, the PCM,
the PCI data bus, or the electronic message inputs to
the instrument cluster that control the low fuel indi-
cator, a DRBIIItscan tool is required. Refer to the
appropriate diagnostic information.
MALFUNCTION INDICATOR
LAMP (MIL)
DESCRIPTION
A Malfunction Indicator Lamp (MIL) is standard
equipment on all instrument clusters. The MIL is
located near the right edge of the instrument cluster,
to the right of the speedometer. The MIL consists of
an International Control and Display Symbol icon for
ªEngineº imprinted on an amber lens. The lens is
located behind a cutout in the opaque layer of the
instrument cluster overlay. The dark outer layer of
the overlay prevents the icon from being clearly vis-
ible when the indicator is not illuminated. The icon
appears silhouetted against an amber field through
the translucent outer layer of the overlay when the
indicator is illuminated from behind by a replaceable
incandescent bulb and bulb holder unit located on
the instrument cluster electronic circuit board. The
MIL lens is serviced as a unit with the instrument
cluster lens, hood and mask unit.
OPERATION
The Malfunction Indicator Lamp (MIL) gives an
indication to the vehicle operator when the Power-
train Control Module (PCM) has recorded a Diagnos-
tic Trouble Code (DTC) for an On-Board Diagnostics
II (OBDII) emissions-related circuit or component
malfunction. This indicator is controlled by a transis-
tor on the instrument cluster electronic circuit board
based upon cluster programming and electronic mes-
sages received by the cluster from the PCM over the
Programmable Communications Interface (PCI) data
bus. The MIL bulb is completely controlled by the
WJINSTRUMENT CLUSTER 8J - 23
LOW FUEL INDICATOR (Continued)
Page 546 of 2199
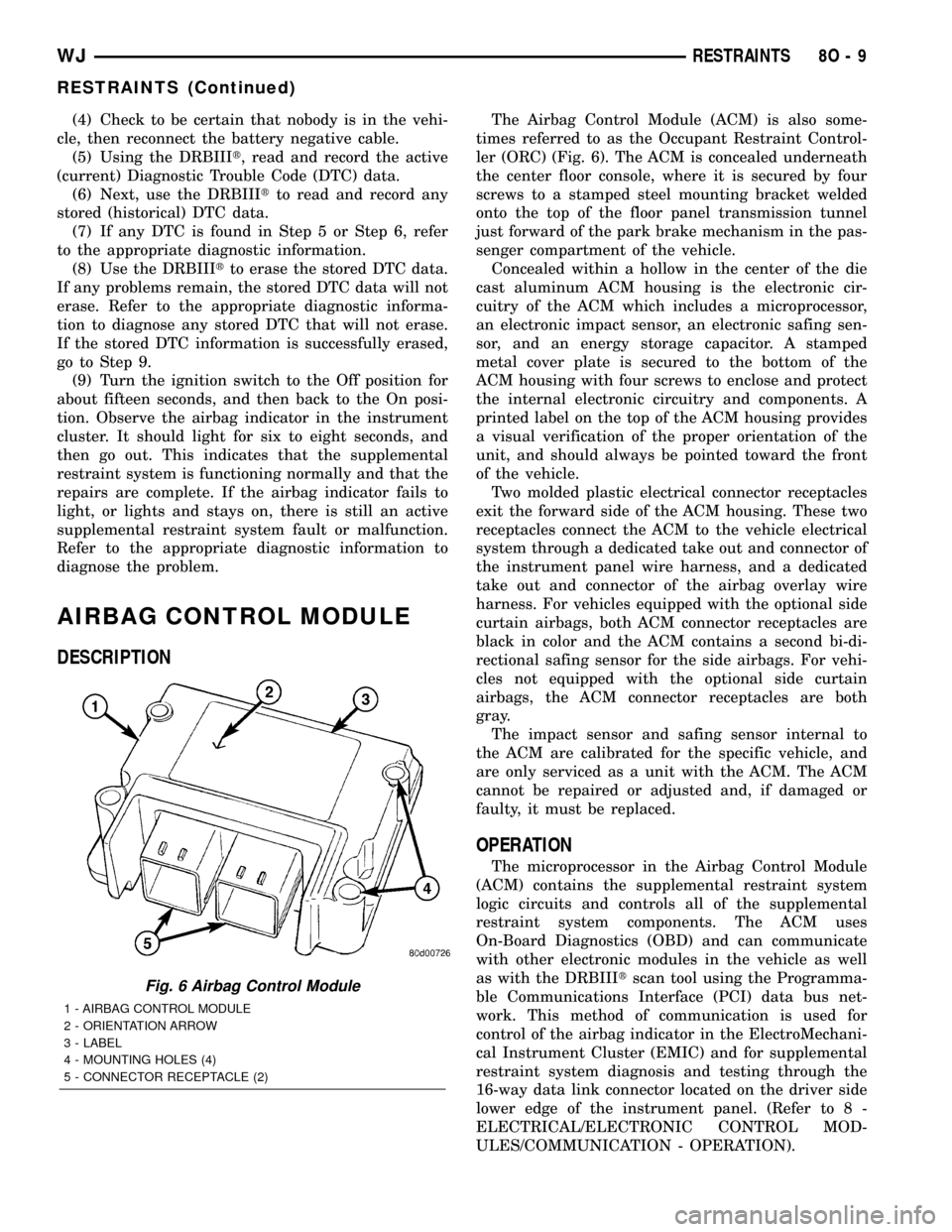
(4) Check to be certain that nobody is in the vehi-
cle, then reconnect the battery negative cable.
(5) Using the DRBIIIt, read and record the active
(current) Diagnostic Trouble Code (DTC) data.
(6) Next, use the DRBIIItto read and record any
stored (historical) DTC data.
(7) If any DTC is found in Step 5 or Step 6, refer
to the appropriate diagnostic information.
(8) Use the DRBIIItto erase the stored DTC data.
If any problems remain, the stored DTC data will not
erase. Refer to the appropriate diagnostic informa-
tion to diagnose any stored DTC that will not erase.
If the stored DTC information is successfully erased,
go to Step 9.
(9) Turn the ignition switch to the Off position for
about fifteen seconds, and then back to the On posi-
tion. Observe the airbag indicator in the instrument
cluster. It should light for six to eight seconds, and
then go out. This indicates that the supplemental
restraint system is functioning normally and that the
repairs are complete. If the airbag indicator fails to
light, or lights and stays on, there is still an active
supplemental restraint system fault or malfunction.
Refer to the appropriate diagnostic information to
diagnose the problem.
AIRBAG CONTROL MODULE
DESCRIPTION
The Airbag Control Module (ACM) is also some-
times referred to as the Occupant Restraint Control-
ler (ORC) (Fig. 6). The ACM is concealed underneath
the center floor console, where it is secured by four
screws to a stamped steel mounting bracket welded
onto the top of the floor panel transmission tunnel
just forward of the park brake mechanism in the pas-
senger compartment of the vehicle.
Concealed within a hollow in the center of the die
cast aluminum ACM housing is the electronic cir-
cuitry of the ACM which includes a microprocessor,
an electronic impact sensor, an electronic safing sen-
sor, and an energy storage capacitor. A stamped
metal cover plate is secured to the bottom of the
ACM housing with four screws to enclose and protect
the internal electronic circuitry and components. A
printed label on the top of the ACM housing provides
a visual verification of the proper orientation of the
unit, and should always be pointed toward the front
of the vehicle.
Two molded plastic electrical connector receptacles
exit the forward side of the ACM housing. These two
receptacles connect the ACM to the vehicle electrical
system through a dedicated take out and connector of
the instrument panel wire harness, and a dedicated
take out and connector of the airbag overlay wire
harness. For vehicles equipped with the optional side
curtain airbags, both ACM connector receptacles are
black in color and the ACM contains a second bi-di-
rectional safing sensor for the side airbags. For vehi-
cles not equipped with the optional side curtain
airbags, the ACM connector receptacles are both
gray.
The impact sensor and safing sensor internal to
the ACM are calibrated for the specific vehicle, and
are only serviced as a unit with the ACM. The ACM
cannot be repaired or adjusted and, if damaged or
faulty, it must be replaced.
OPERATION
The microprocessor in the Airbag Control Module
(ACM) contains the supplemental restraint system
logic circuits and controls all of the supplemental
restraint system components. The ACM uses
On-Board Diagnostics (OBD) and can communicate
with other electronic modules in the vehicle as well
as with the DRBIIItscan tool using the Programma-
ble Communications Interface (PCI) data bus net-
work. This method of communication is used for
control of the airbag indicator in the ElectroMechani-
cal Instrument Cluster (EMIC) and for supplemental
restraint system diagnosis and testing through the
16-way data link connector located on the driver side
lower edge of the instrument panel. (Refer to 8 -
ELECTRICAL/ELECTRONIC CONTROL MOD-
ULES/COMMUNICATION - OPERATION).
Fig. 6 Airbag Control Module
1 - AIRBAG CONTROL MODULE
2 - ORIENTATION ARROW
3 - LABEL
4 - MOUNTING HOLES (4)
5 - CONNECTOR RECEPTACLE (2)
WJRESTRAINTS 8O - 9
RESTRAINTS (Continued)