electrical restraints JEEP GRAND CHEROKEE 2003 WJ / 2.G Workshop Manual
[x] Cancel search | Manufacturer: JEEP, Model Year: 2003, Model line: GRAND CHEROKEE, Model: JEEP GRAND CHEROKEE 2003 WJ / 2.GPages: 2199, PDF Size: 76.01 MB
Page 294 of 2199
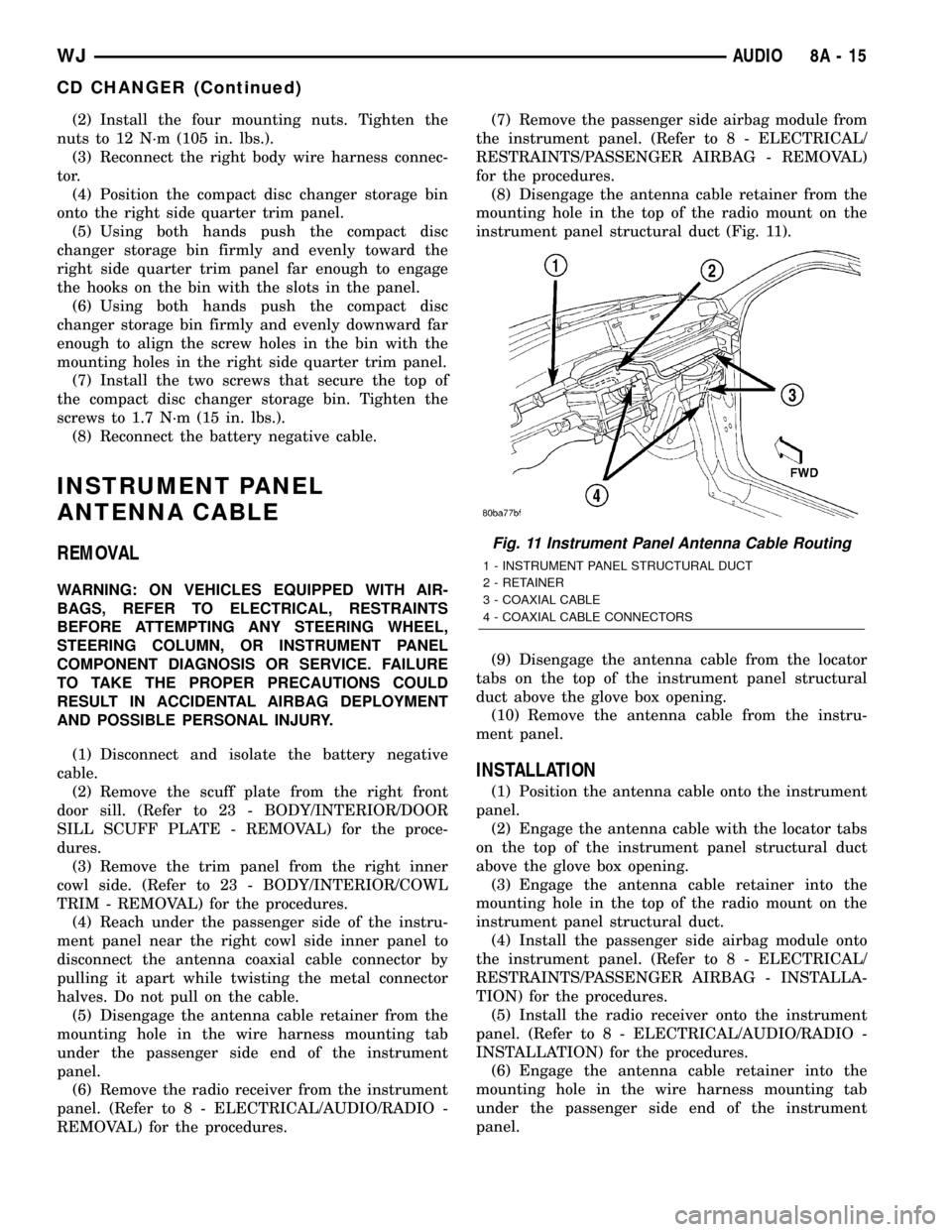
(2) Install the four mounting nuts. Tighten the
nuts to 12 N´m (105 in. lbs.).
(3) Reconnect the right body wire harness connec-
tor.
(4) Position the compact disc changer storage bin
onto the right side quarter trim panel.
(5) Using both hands push the compact disc
changer storage bin firmly and evenly toward the
right side quarter trim panel far enough to engage
the hooks on the bin with the slots in the panel.
(6) Using both hands push the compact disc
changer storage bin firmly and evenly downward far
enough to align the screw holes in the bin with the
mounting holes in the right side quarter trim panel.
(7) Install the two screws that secure the top of
the compact disc changer storage bin. Tighten the
screws to 1.7 N´m (15 in. lbs.).
(8) Reconnect the battery negative cable.
INSTRUMENT PANEL
ANTENNA CABLE
REMOVAL
WARNING: ON VEHICLES EQUIPPED WITH AIR-
BAGS, REFER TO ELECTRICAL, RESTRAINTS
BEFORE ATTEMPTING ANY STEERING WHEEL,
STEERING COLUMN, OR INSTRUMENT PANEL
COMPONENT DIAGNOSIS OR SERVICE. FAILURE
TO TAKE THE PROPER PRECAUTIONS COULD
RESULT IN ACCIDENTAL AIRBAG DEPLOYMENT
AND POSSIBLE PERSONAL INJURY.
(1) Disconnect and isolate the battery negative
cable.
(2) Remove the scuff plate from the right front
door sill. (Refer to 23 - BODY/INTERIOR/DOOR
SILL SCUFF PLATE - REMOVAL) for the proce-
dures.
(3) Remove the trim panel from the right inner
cowl side. (Refer to 23 - BODY/INTERIOR/COWL
TRIM - REMOVAL) for the procedures.
(4) Reach under the passenger side of the instru-
ment panel near the right cowl side inner panel to
disconnect the antenna coaxial cable connector by
pulling it apart while twisting the metal connector
halves. Do not pull on the cable.
(5) Disengage the antenna cable retainer from the
mounting hole in the wire harness mounting tab
under the passenger side end of the instrument
panel.
(6) Remove the radio receiver from the instrument
panel. (Refer to 8 - ELECTRICAL/AUDIO/RADIO -
REMOVAL) for the procedures.(7) Remove the passenger side airbag module from
the instrument panel. (Refer to 8 - ELECTRICAL/
RESTRAINTS/PASSENGER AIRBAG - REMOVAL)
for the procedures.
(8) Disengage the antenna cable retainer from the
mounting hole in the top of the radio mount on the
instrument panel structural duct (Fig. 11).
(9) Disengage the antenna cable from the locator
tabs on the top of the instrument panel structural
duct above the glove box opening.
(10) Remove the antenna cable from the instru-
ment panel.
INSTALLATION
(1) Position the antenna cable onto the instrument
panel.
(2) Engage the antenna cable with the locator tabs
on the top of the instrument panel structural duct
above the glove box opening.
(3) Engage the antenna cable retainer into the
mounting hole in the top of the radio mount on the
instrument panel structural duct.
(4) Install the passenger side airbag module onto
the instrument panel. (Refer to 8 - ELECTRICAL/
RESTRAINTS/PASSENGER AIRBAG - INSTALLA-
TION) for the procedures.
(5) Install the radio receiver onto the instrument
panel. (Refer to 8 - ELECTRICAL/AUDIO/RADIO -
INSTALLATION) for the procedures.
(6) Engage the antenna cable retainer into the
mounting hole in the wire harness mounting tab
under the passenger side end of the instrument
panel.
Fig. 11 Instrument Panel Antenna Cable Routing
1 - INSTRUMENT PANEL STRUCTURAL DUCT
2 - RETAINER
3 - COAXIAL CABLE
4 - COAXIAL CABLE CONNECTORS
WJAUDIO 8A - 15
CD CHANGER (Continued)
Page 299 of 2199
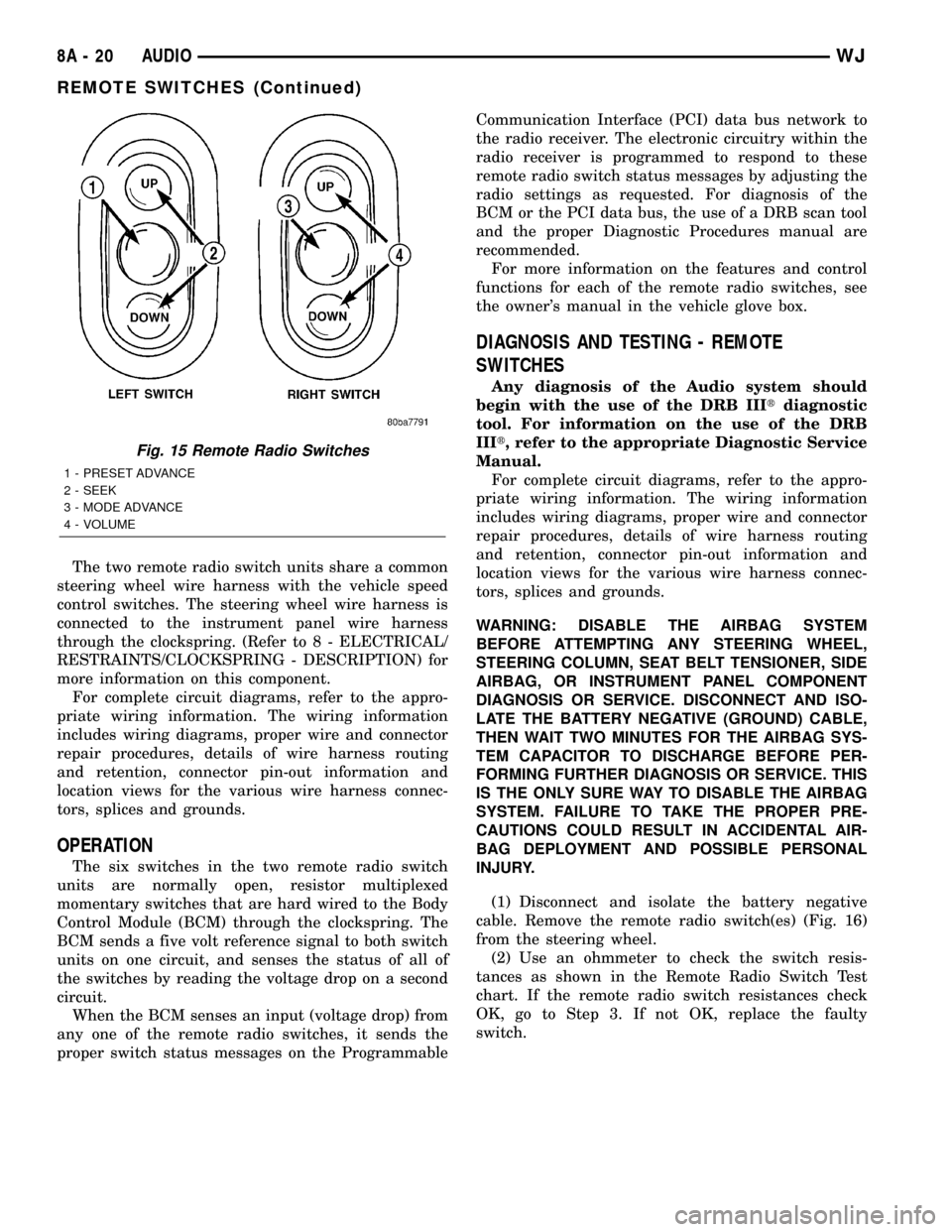
The two remote radio switch units share a common
steering wheel wire harness with the vehicle speed
control switches. The steering wheel wire harness is
connected to the instrument panel wire harness
through the clockspring. (Refer to 8 - ELECTRICAL/
RESTRAINTS/CLOCKSPRING - DESCRIPTION) for
more information on this component.
For complete circuit diagrams, refer to the appro-
priate wiring information. The wiring information
includes wiring diagrams, proper wire and connector
repair procedures, details of wire harness routing
and retention, connector pin-out information and
location views for the various wire harness connec-
tors, splices and grounds.
OPERATION
The six switches in the two remote radio switch
units are normally open, resistor multiplexed
momentary switches that are hard wired to the Body
Control Module (BCM) through the clockspring. The
BCM sends a five volt reference signal to both switch
units on one circuit, and senses the status of all of
the switches by reading the voltage drop on a second
circuit.
When the BCM senses an input (voltage drop) from
any one of the remote radio switches, it sends the
proper switch status messages on the ProgrammableCommunication Interface (PCI) data bus network to
the radio receiver. The electronic circuitry within the
radio receiver is programmed to respond to these
remote radio switch status messages by adjusting the
radio settings as requested. For diagnosis of the
BCM or the PCI data bus, the use of a DRB scan tool
and the proper Diagnostic Procedures manual are
recommended.
For more information on the features and control
functions for each of the remote radio switches, see
the owner's manual in the vehicle glove box.
DIAGNOSIS AND TESTING - REMOTE
SWITCHES
Any diagnosis of the Audio system should
begin with the use of the DRB IIItdiagnostic
tool. For information on the use of the DRB
IIIt, refer to the appropriate Diagnostic Service
Manual.
For complete circuit diagrams, refer to the appro-
priate wiring information. The wiring information
includes wiring diagrams, proper wire and connector
repair procedures, details of wire harness routing
and retention, connector pin-out information and
location views for the various wire harness connec-
tors, splices and grounds.
WARNING: DISABLE THE AIRBAG SYSTEM
BEFORE ATTEMPTING ANY STEERING WHEEL,
STEERING COLUMN, SEAT BELT TENSIONER, SIDE
AIRBAG, OR INSTRUMENT PANEL COMPONENT
DIAGNOSIS OR SERVICE. DISCONNECT AND ISO-
LATE THE BATTERY NEGATIVE (GROUND) CABLE,
THEN WAIT TWO MINUTES FOR THE AIRBAG SYS-
TEM CAPACITOR TO DISCHARGE BEFORE PER-
FORMING FURTHER DIAGNOSIS OR SERVICE. THIS
IS THE ONLY SURE WAY TO DISABLE THE AIRBAG
SYSTEM. FAILURE TO TAKE THE PROPER PRE-
CAUTIONS COULD RESULT IN ACCIDENTAL AIR-
BAG DEPLOYMENT AND POSSIBLE PERSONAL
INJURY.
(1) Disconnect and isolate the battery negative
cable. Remove the remote radio switch(es) (Fig. 16)
from the steering wheel.
(2) Use an ohmmeter to check the switch resis-
tances as shown in the Remote Radio Switch Test
chart. If the remote radio switch resistances check
OK, go to Step 3. If not OK, replace the faulty
switch.
Fig. 15 Remote Radio Switches
1 - PRESET ADVANCE
2 - SEEK
3 - MODE ADVANCE
4 - VOLUME
8A - 20 AUDIOWJ
REMOTE SWITCHES (Continued)
Page 300 of 2199
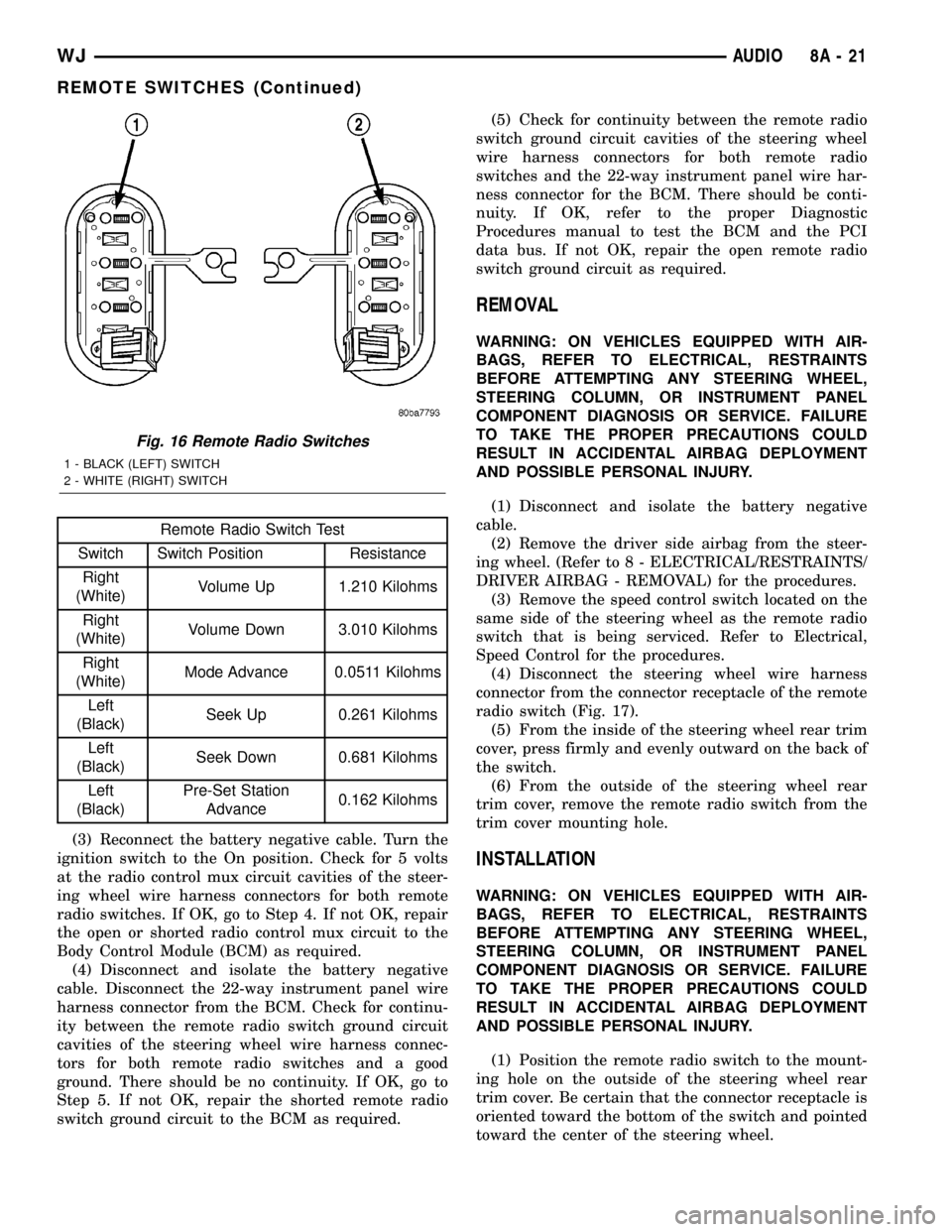
Remote Radio Switch Test
Switch Switch Position Resistance
Right
(White)Volume Up 1.210 Kilohms
Right
(White)Volume Down 3.010 Kilohms
Right
(White)Mode Advance 0.0511 Kilohms
Left
(Black)Seek Up 0.261 Kilohms
Left
(Black)Seek Down 0.681 Kilohms
Left
(Black)Pre-Set Station
Advance0.162 Kilohms
(3) Reconnect the battery negative cable. Turn the
ignition switch to the On position. Check for 5 volts
at the radio control mux circuit cavities of the steer-
ing wheel wire harness connectors for both remote
radio switches. If OK, go to Step 4. If not OK, repair
the open or shorted radio control mux circuit to the
Body Control Module (BCM) as required.
(4) Disconnect and isolate the battery negative
cable. Disconnect the 22-way instrument panel wire
harness connector from the BCM. Check for continu-
ity between the remote radio switch ground circuit
cavities of the steering wheel wire harness connec-
tors for both remote radio switches and a good
ground. There should be no continuity. If OK, go to
Step 5. If not OK, repair the shorted remote radio
switch ground circuit to the BCM as required.(5) Check for continuity between the remote radio
switch ground circuit cavities of the steering wheel
wire harness connectors for both remote radio
switches and the 22-way instrument panel wire har-
ness connector for the BCM. There should be conti-
nuity. If OK, refer to the proper Diagnostic
Procedures manual to test the BCM and the PCI
data bus. If not OK, repair the open remote radio
switch ground circuit as required.
REMOVAL
WARNING: ON VEHICLES EQUIPPED WITH AIR-
BAGS, REFER TO ELECTRICAL, RESTRAINTS
BEFORE ATTEMPTING ANY STEERING WHEEL,
STEERING COLUMN, OR INSTRUMENT PANEL
COMPONENT DIAGNOSIS OR SERVICE. FAILURE
TO TAKE THE PROPER PRECAUTIONS COULD
RESULT IN ACCIDENTAL AIRBAG DEPLOYMENT
AND POSSIBLE PERSONAL INJURY.
(1) Disconnect and isolate the battery negative
cable.
(2) Remove the driver side airbag from the steer-
ing wheel. (Refer to 8 - ELECTRICAL/RESTRAINTS/
DRIVER AIRBAG - REMOVAL) for the procedures.
(3) Remove the speed control switch located on the
same side of the steering wheel as the remote radio
switch that is being serviced. Refer to Electrical,
Speed Control for the procedures.
(4) Disconnect the steering wheel wire harness
connector from the connector receptacle of the remote
radio switch (Fig. 17).
(5) From the inside of the steering wheel rear trim
cover, press firmly and evenly outward on the back of
the switch.
(6) From the outside of the steering wheel rear
trim cover, remove the remote radio switch from the
trim cover mounting hole.
INSTALLATION
WARNING: ON VEHICLES EQUIPPED WITH AIR-
BAGS, REFER TO ELECTRICAL, RESTRAINTS
BEFORE ATTEMPTING ANY STEERING WHEEL,
STEERING COLUMN, OR INSTRUMENT PANEL
COMPONENT DIAGNOSIS OR SERVICE. FAILURE
TO TAKE THE PROPER PRECAUTIONS COULD
RESULT IN ACCIDENTAL AIRBAG DEPLOYMENT
AND POSSIBLE PERSONAL INJURY.
(1) Position the remote radio switch to the mount-
ing hole on the outside of the steering wheel rear
trim cover. Be certain that the connector receptacle is
oriented toward the bottom of the switch and pointed
toward the center of the steering wheel.
Fig. 16 Remote Radio Switches
1 - BLACK (LEFT) SWITCH
2 - WHITE (RIGHT) SWITCH
WJAUDIO 8A - 21
REMOTE SWITCHES (Continued)
Page 301 of 2199
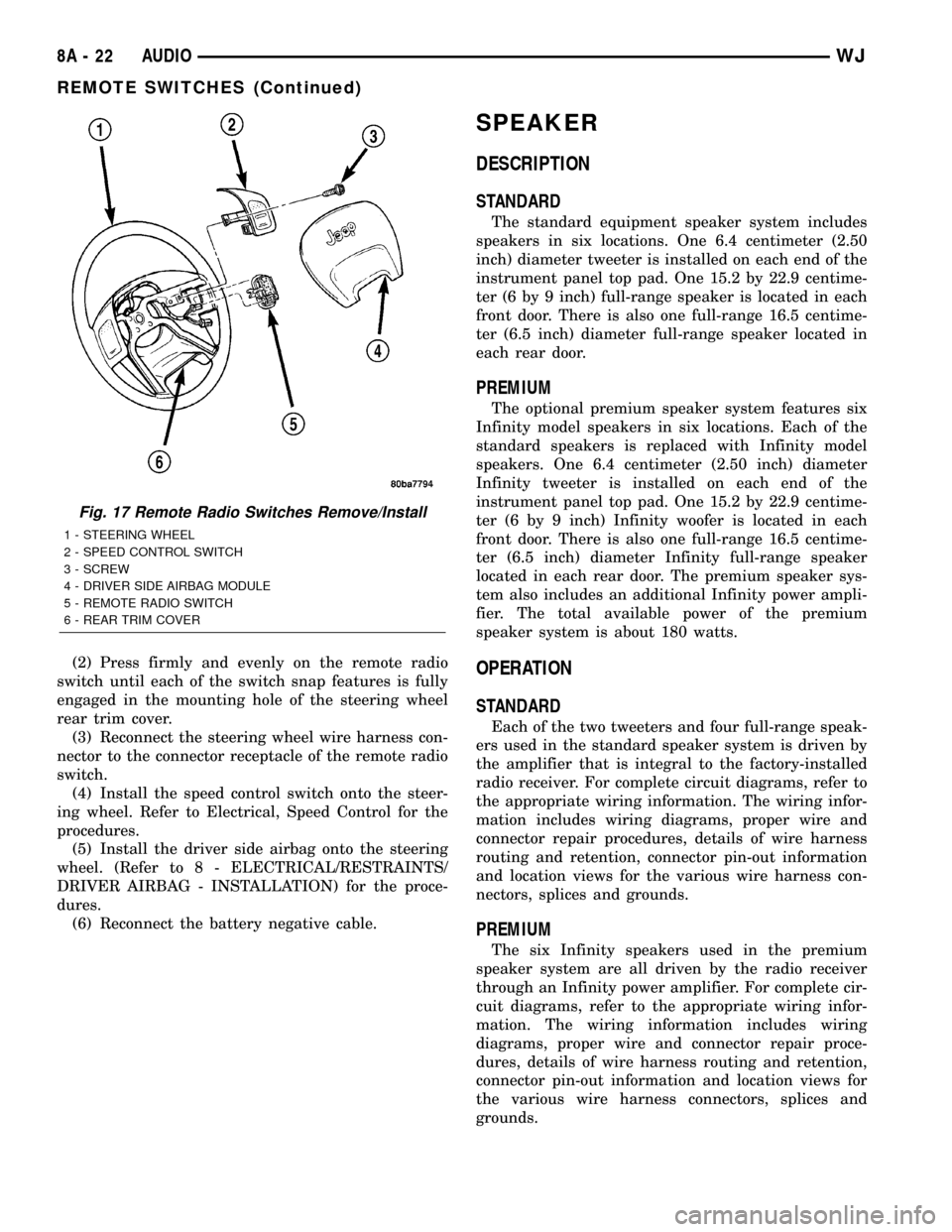
(2) Press firmly and evenly on the remote radio
switch until each of the switch snap features is fully
engaged in the mounting hole of the steering wheel
rear trim cover.
(3) Reconnect the steering wheel wire harness con-
nector to the connector receptacle of the remote radio
switch.
(4) Install the speed control switch onto the steer-
ing wheel. Refer to Electrical, Speed Control for the
procedures.
(5) Install the driver side airbag onto the steering
wheel. (Refer to 8 - ELECTRICAL/RESTRAINTS/
DRIVER AIRBAG - INSTALLATION) for the proce-
dures.
(6) Reconnect the battery negative cable.
SPEAKER
DESCRIPTION
STANDARD
The standard equipment speaker system includes
speakers in six locations. One 6.4 centimeter (2.50
inch) diameter tweeter is installed on each end of the
instrument panel top pad. One 15.2 by 22.9 centime-
ter (6 by 9 inch) full-range speaker is located in each
front door. There is also one full-range 16.5 centime-
ter (6.5 inch) diameter full-range speaker located in
each rear door.
PREMIUM
The optional premium speaker system features six
Infinity model speakers in six locations. Each of the
standard speakers is replaced with Infinity model
speakers. One 6.4 centimeter (2.50 inch) diameter
Infinity tweeter is installed on each end of the
instrument panel top pad. One 15.2 by 22.9 centime-
ter (6 by 9 inch) Infinity woofer is located in each
front door. There is also one full-range 16.5 centime-
ter (6.5 inch) diameter Infinity full-range speaker
located in each rear door. The premium speaker sys-
tem also includes an additional Infinity power ampli-
fier. The total available power of the premium
speaker system is about 180 watts.
OPERATION
STANDARD
Each of the two tweeters and four full-range speak-
ers used in the standard speaker system is driven by
the amplifier that is integral to the factory-installed
radio receiver. For complete circuit diagrams, refer to
the appropriate wiring information. The wiring infor-
mation includes wiring diagrams, proper wire and
connector repair procedures, details of wire harness
routing and retention, connector pin-out information
and location views for the various wire harness con-
nectors, splices and grounds.
PREMIUM
The six Infinity speakers used in the premium
speaker system are all driven by the radio receiver
through an Infinity power amplifier. For complete cir-
cuit diagrams, refer to the appropriate wiring infor-
mation. The wiring information includes wiring
diagrams, proper wire and connector repair proce-
dures, details of wire harness routing and retention,
connector pin-out information and location views for
the various wire harness connectors, splices and
grounds.
Fig. 17 Remote Radio Switches Remove/Install
1 - STEERING WHEEL
2 - SPEED CONTROL SWITCH
3 - SCREW
4 - DRIVER SIDE AIRBAG MODULE
5 - REMOTE RADIO SWITCH
6 - REAR TRIM COVER
8A - 22 AUDIOWJ
REMOTE SWITCHES (Continued)
Page 390 of 2199
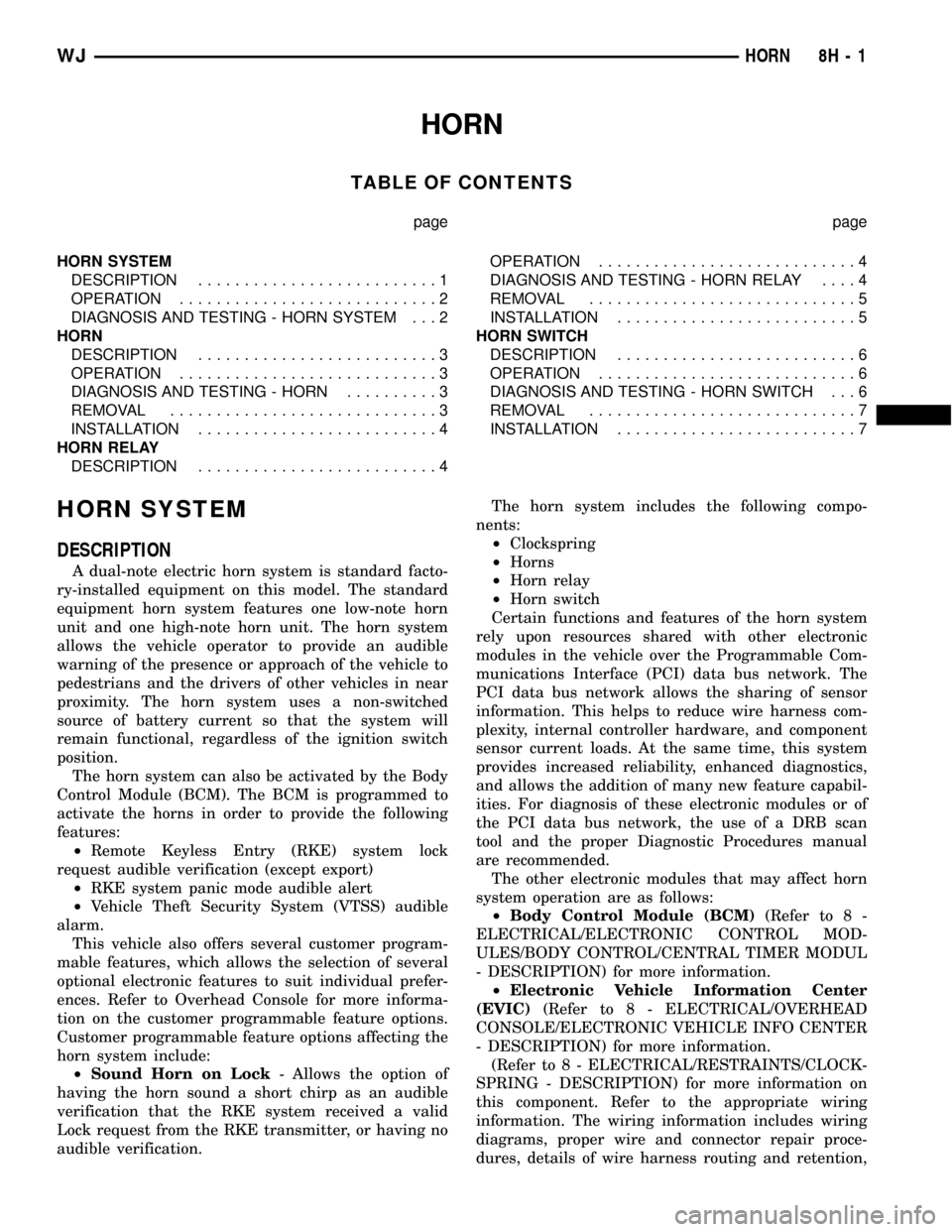
HORN
TABLE OF CONTENTS
page page
HORN SYSTEM
DESCRIPTION..........................1
OPERATION............................2
DIAGNOSIS AND TESTING - HORN SYSTEM . . . 2
HORN
DESCRIPTION..........................3
OPERATION............................3
DIAGNOSIS AND TESTING - HORN..........3
REMOVAL.............................3
INSTALLATION..........................4
HORN RELAY
DESCRIPTION..........................4OPERATION............................4
DIAGNOSIS AND TESTING - HORN RELAY....4
REMOVAL.............................5
INSTALLATION..........................5
HORN SWITCH
DESCRIPTION..........................6
OPERATION............................6
DIAGNOSIS AND TESTING - HORN SWITCH . . . 6
REMOVAL.............................7
INSTALLATION..........................7
HORN SYSTEM
DESCRIPTION
A dual-note electric horn system is standard facto-
ry-installed equipment on this model. The standard
equipment horn system features one low-note horn
unit and one high-note horn unit. The horn system
allows the vehicle operator to provide an audible
warning of the presence or approach of the vehicle to
pedestrians and the drivers of other vehicles in near
proximity. The horn system uses a non-switched
source of battery current so that the system will
remain functional, regardless of the ignition switch
position.
The horn system can also be activated by the Body
Control Module (BCM). The BCM is programmed to
activate the horns in order to provide the following
features:
²Remote Keyless Entry (RKE) system lock
request audible verification (except export)
²RKE system panic mode audible alert
²Vehicle Theft Security System (VTSS) audible
alarm.
This vehicle also offers several customer program-
mable features, which allows the selection of several
optional electronic features to suit individual prefer-
ences. Refer to Overhead Console for more informa-
tion on the customer programmable feature options.
Customer programmable feature options affecting the
horn system include:
²Sound Horn on Lock- Allows the option of
having the horn sound a short chirp as an audible
verification that the RKE system received a valid
Lock request from the RKE transmitter, or having no
audible verification.The horn system includes the following compo-
nents:
²Clockspring
²Horns
²Horn relay
²Horn switch
Certain functions and features of the horn system
rely upon resources shared with other electronic
modules in the vehicle over the Programmable Com-
munications Interface (PCI) data bus network. The
PCI data bus network allows the sharing of sensor
information. This helps to reduce wire harness com-
plexity, internal controller hardware, and component
sensor current loads. At the same time, this system
provides increased reliability, enhanced diagnostics,
and allows the addition of many new feature capabil-
ities. For diagnosis of these electronic modules or of
the PCI data bus network, the use of a DRB scan
tool and the proper Diagnostic Procedures manual
are recommended.
The other electronic modules that may affect horn
system operation are as follows:
²Body Control Module (BCM)(Refer to 8 -
ELECTRICAL/ELECTRONIC CONTROL MOD-
ULES/BODY CONTROL/CENTRAL TIMER MODUL
- DESCRIPTION) for more information.
²Electronic Vehicle Information Center
(EVIC)(Refer to 8 - ELECTRICAL/OVERHEAD
CONSOLE/ELECTRONIC VEHICLE INFO CENTER
- DESCRIPTION) for more information.
(Refer to 8 - ELECTRICAL/RESTRAINTS/CLOCK-
SPRING - DESCRIPTION) for more information on
this component. Refer to the appropriate wiring
information. The wiring information includes wiring
diagrams, proper wire and connector repair proce-
dures, details of wire harness routing and retention,
WJHORN 8H - 1
Page 394 of 2199

WARNING: ON VEHICLES EQUIPPED WITH AIR-
BAGS, REFER TO ELECTRICAL, RESTRAINTS
BEFORE ATTEMPTING ANY STEERING WHEEL,
STEERING COLUMN, OR INSTRUMENT PANEL
COMPONENT DIAGNOSIS OR SERVICE. FAILURE
TO TAKE THE PROPER PRECAUTIONS COULD
RESULT IN ACCIDENTAL AIRBAG DEPLOYMENT
AND POSSIBLE PERSONAL INJURY.
(1) Remove the horn relay from the PDC. (Refer to
8 - ELECTRICAL/HORN/HORN RELAY -
REMOVAL) for the procedures.
(2) A relay in the de-energized position should
have continuity between terminals 87A and 30, and
no continuity between terminals 87 and 30. If OK, go
to Step 3. If not OK, replace the faulty relay.
(3) Resistance between terminals 85 and 86 (elec-
tromagnet) should be 75 5 ohms. If OK, go to Step
4. If not OK, replace the faulty relay.
(4) Connect a battery to terminals 85 and 86.
There should now be continuity between terminals
30 and 87, and no continuity between terminals 87A
and 30. If OK, perform the Relay Circuit Test that
follows. If not OK, replace the faulty relay.
RELAY CIRCUIT TEST
(1) The relay common feed terminal cavity (30) is
connected to battery voltage and should be hot at all
times. If OK, go to Step 2. If not OK, repair the open
circuit to the fuse in the PDC as required.
(2) The relay normally closed terminal (87A) is
connected to terminal 30 in the de-energized position,
but is not used for this application. Go to Step 3.(3) The relay normally open terminal (87) is con-
nected to the common feed terminal (30) in the ener-
gized position. This terminal supplies battery voltage
to the horn(s). There should be continuity between
the cavity for relay terminal 87 and the horn relay
output circuit cavity of each horn wire harness con-
nector at all times. If OK, go to Step 4. If not OK,
repair the open circuit to the horn(s) as required.
(4) The coil battery terminal (86) is connected to
the electromagnet in the relay. It is connected to bat-
tery voltage and should be hot at all times. Check for
battery voltage at the cavity for relay terminal 86. If
OK, go to Step 5. If not OK, repair the open circuit to
the fuse in the PDC as required.
(5) The coil ground terminal (85) is connected to
the electromagnet in the relay. It is grounded
through the horn switch when the horn switch is
depressed. The horn relay coil ground terminal can
also be grounded by the Body Control Module (BCM)
in response to certain inputs related to the RKE sys-
tem or the Vehicle Theft Security System. Check for
continuity to ground at the cavity for relay terminal
85. There should be continuity with the horn switch
depressed, and no continuity with the horn switch
released. If not OK, (Refer to 8 - ELECTRICAL/
HORN/HORN SWITCH - DIAGNOSIS AND TEST-
ING).
REMOVAL
(1) Disconnect and isolate the battery negative
cable.
(2) Remove the cover from the Power Distribution
Center (PDC) (Fig. 3) .
(3) See the fuse and relay layout label affixed to
the underside of the PDC cover for horn relay iden-
tification and location.
(4) Remove the horn relay from the PDC.
INSTALLATION
(1) See the fuse and relay layout label affixed to
the underside of the PDC cover for the proper horn
relay location.
(2) Position the horn relay in the proper receptacle
in the PDC.
(3) Align the horn relay terminals with the termi-
nal cavities in the PDC receptacle.
(4) Push down firmly on the horn relay until the
terminals are fully seated in the terminal cavities in
the PDC receptacle.
(5) Install the cover onto the PDC.
(6) Reconnect the battery negative cable.
Fig. 2 Horn Relay
30 - COMMON FEED
85 - COIL GROUND
86 - COIL BATTERY
87 - NORMALLY OPEN
87A - NORMALLY CLOSED
WJHORN 8H - 5
HORN RELAY (Continued)
Page 395 of 2199
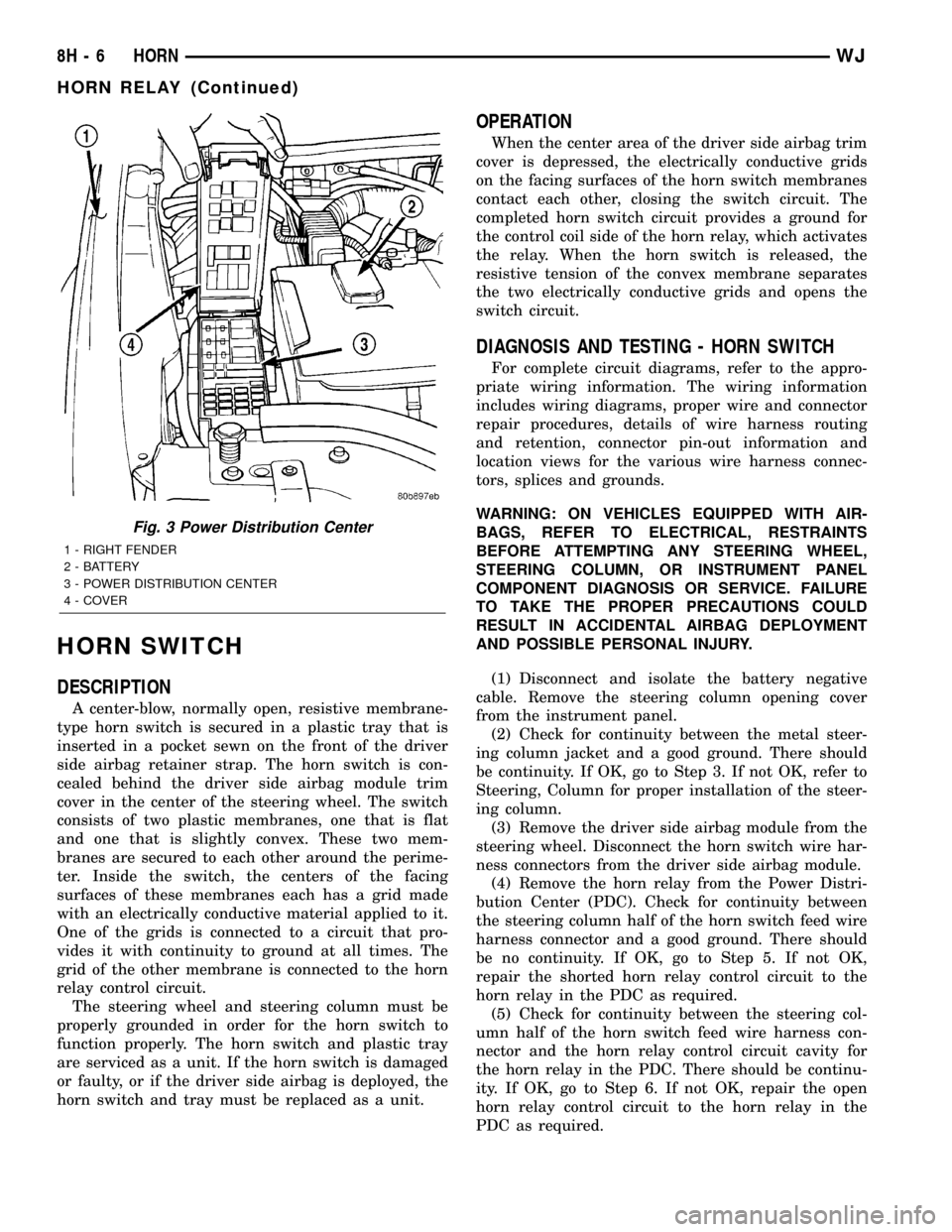
HORN SWITCH
DESCRIPTION
A center-blow, normally open, resistive membrane-
type horn switch is secured in a plastic tray that is
inserted in a pocket sewn on the front of the driver
side airbag retainer strap. The horn switch is con-
cealed behind the driver side airbag module trim
cover in the center of the steering wheel. The switch
consists of two plastic membranes, one that is flat
and one that is slightly convex. These two mem-
branes are secured to each other around the perime-
ter. Inside the switch, the centers of the facing
surfaces of these membranes each has a grid made
with an electrically conductive material applied to it.
One of the grids is connected to a circuit that pro-
vides it with continuity to ground at all times. The
grid of the other membrane is connected to the horn
relay control circuit.
The steering wheel and steering column must be
properly grounded in order for the horn switch to
function properly. The horn switch and plastic tray
are serviced as a unit. If the horn switch is damaged
or faulty, or if the driver side airbag is deployed, the
horn switch and tray must be replaced as a unit.
OPERATION
When the center area of the driver side airbag trim
cover is depressed, the electrically conductive grids
on the facing surfaces of the horn switch membranes
contact each other, closing the switch circuit. The
completed horn switch circuit provides a ground for
the control coil side of the horn relay, which activates
the relay. When the horn switch is released, the
resistive tension of the convex membrane separates
the two electrically conductive grids and opens the
switch circuit.
DIAGNOSIS AND TESTING - HORN SWITCH
For complete circuit diagrams, refer to the appro-
priate wiring information. The wiring information
includes wiring diagrams, proper wire and connector
repair procedures, details of wire harness routing
and retention, connector pin-out information and
location views for the various wire harness connec-
tors, splices and grounds.
WARNING: ON VEHICLES EQUIPPED WITH AIR-
BAGS, REFER TO ELECTRICAL, RESTRAINTS
BEFORE ATTEMPTING ANY STEERING WHEEL,
STEERING COLUMN, OR INSTRUMENT PANEL
COMPONENT DIAGNOSIS OR SERVICE. FAILURE
TO TAKE THE PROPER PRECAUTIONS COULD
RESULT IN ACCIDENTAL AIRBAG DEPLOYMENT
AND POSSIBLE PERSONAL INJURY.
(1) Disconnect and isolate the battery negative
cable. Remove the steering column opening cover
from the instrument panel.
(2) Check for continuity between the metal steer-
ing column jacket and a good ground. There should
be continuity. If OK, go to Step 3. If not OK, refer to
Steering, Column for proper installation of the steer-
ing column.
(3) Remove the driver side airbag module from the
steering wheel. Disconnect the horn switch wire har-
ness connectors from the driver side airbag module.
(4) Remove the horn relay from the Power Distri-
bution Center (PDC). Check for continuity between
the steering column half of the horn switch feed wire
harness connector and a good ground. There should
be no continuity. If OK, go to Step 5. If not OK,
repair the shorted horn relay control circuit to the
horn relay in the PDC as required.
(5) Check for continuity between the steering col-
umn half of the horn switch feed wire harness con-
nector and the horn relay control circuit cavity for
the horn relay in the PDC. There should be continu-
ity. If OK, go to Step 6. If not OK, repair the open
horn relay control circuit to the horn relay in the
PDC as required.
Fig. 3 Power Distribution Center
1 - RIGHT FENDER
2 - BATTERY
3 - POWER DISTRIBUTION CENTER
4 - COVER
8H - 6 HORNWJ
HORN RELAY (Continued)
Page 396 of 2199
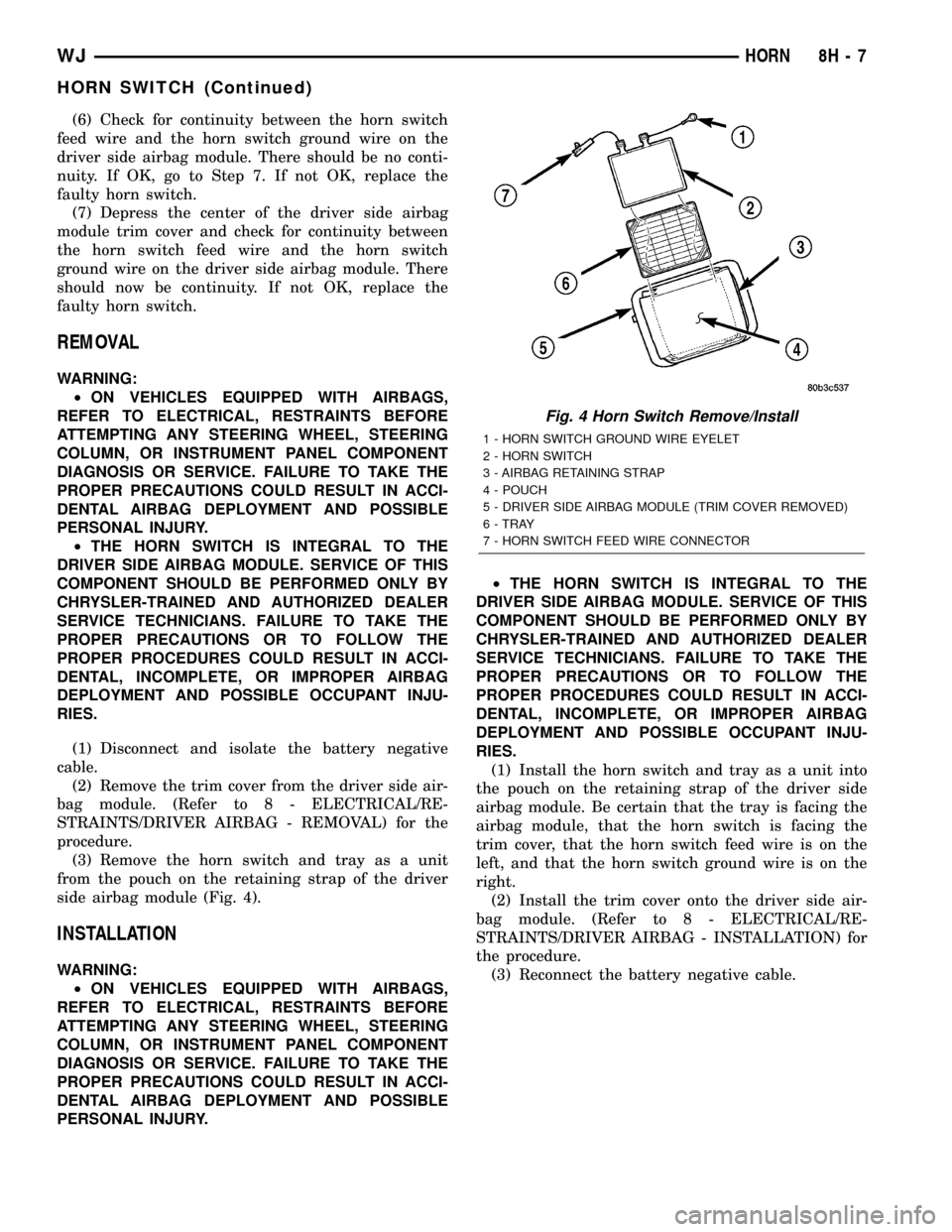
(6) Check for continuity between the horn switch
feed wire and the horn switch ground wire on the
driver side airbag module. There should be no conti-
nuity. If OK, go to Step 7. If not OK, replace the
faulty horn switch.
(7) Depress the center of the driver side airbag
module trim cover and check for continuity between
the horn switch feed wire and the horn switch
ground wire on the driver side airbag module. There
should now be continuity. If not OK, replace the
faulty horn switch.
REMOVAL
WARNING:
²ON VEHICLES EQUIPPED WITH AIRBAGS,
REFER TO ELECTRICAL, RESTRAINTS BEFORE
ATTEMPTING ANY STEERING WHEEL, STEERING
COLUMN, OR INSTRUMENT PANEL COMPONENT
DIAGNOSIS OR SERVICE. FAILURE TO TAKE THE
PROPER PRECAUTIONS COULD RESULT IN ACCI-
DENTAL AIRBAG DEPLOYMENT AND POSSIBLE
PERSONAL INJURY.
²THE HORN SWITCH IS INTEGRAL TO THE
DRIVER SIDE AIRBAG MODULE. SERVICE OF THIS
COMPONENT SHOULD BE PERFORMED ONLY BY
CHRYSLER-TRAINED AND AUTHORIZED DEALER
SERVICE TECHNICIANS. FAILURE TO TAKE THE
PROPER PRECAUTIONS OR TO FOLLOW THE
PROPER PROCEDURES COULD RESULT IN ACCI-
DENTAL, INCOMPLETE, OR IMPROPER AIRBAG
DEPLOYMENT AND POSSIBLE OCCUPANT INJU-
RIES.
(1) Disconnect and isolate the battery negative
cable.
(2) Remove the trim cover from the driver side air-
bag module. (Refer to 8 - ELECTRICAL/RE-
STRAINTS/DRIVER AIRBAG - REMOVAL) for the
procedure.
(3) Remove the horn switch and tray as a unit
from the pouch on the retaining strap of the driver
side airbag module (Fig. 4).
INSTALLATION
WARNING:
²ON VEHICLES EQUIPPED WITH AIRBAGS,
REFER TO ELECTRICAL, RESTRAINTS BEFORE
ATTEMPTING ANY STEERING WHEEL, STEERING
COLUMN, OR INSTRUMENT PANEL COMPONENT
DIAGNOSIS OR SERVICE. FAILURE TO TAKE THE
PROPER PRECAUTIONS COULD RESULT IN ACCI-
DENTAL AIRBAG DEPLOYMENT AND POSSIBLE
PERSONAL INJURY.²THE HORN SWITCH IS INTEGRAL TO THE
DRIVER SIDE AIRBAG MODULE. SERVICE OF THIS
COMPONENT SHOULD BE PERFORMED ONLY BY
CHRYSLER-TRAINED AND AUTHORIZED DEALER
SERVICE TECHNICIANS. FAILURE TO TAKE THE
PROPER PRECAUTIONS OR TO FOLLOW THE
PROPER PROCEDURES COULD RESULT IN ACCI-
DENTAL, INCOMPLETE, OR IMPROPER AIRBAG
DEPLOYMENT AND POSSIBLE OCCUPANT INJU-
RIES.
(1) Install the horn switch and tray as a unit into
the pouch on the retaining strap of the driver side
airbag module. Be certain that the tray is facing the
airbag module, that the horn switch is facing the
trim cover, that the horn switch feed wire is on the
left, and that the horn switch ground wire is on the
right.
(2) Install the trim cover onto the driver side air-
bag module. (Refer to 8 - ELECTRICAL/RE-
STRAINTS/DRIVER AIRBAG - INSTALLATION) for
the procedure.
(3) Reconnect the battery negative cable.
Fig. 4 Horn Switch Remove/Install
1 - HORN SWITCH GROUND WIRE EYELET
2 - HORN SWITCH
3 - AIRBAG RETAINING STRAP
4 - POUCH
5 - DRIVER SIDE AIRBAG MODULE (TRIM COVER REMOVED)
6 - TRAY
7 - HORN SWITCH FEED WIRE CONNECTOR
WJHORN 8H - 7
HORN SWITCH (Continued)
Page 466 of 2199

INSTALLATION - BULB
CAUTION: Do not touch the bulb glass with fingers
or other oily surfaces. Reduced bulb life will result.
(1) Position the bulb into socket and push into
place.
(2) Position the bulb socket in headlamp and turn
the bulb socket one quarter turn clockwise.
(3) Install the headlamp.
HEADLAMP SWITCH
DESCRIPTION
The headlamp switch is part of the left multi-func-
tion switch. A knob on the end of the multi-function
switch control stalk controls all of the exterior light-
ing switch functions. The exterior lighting switch is
hard wired to the Body Control Module (BCM).
The exterior lighting switch cannot be adjusted or
repaired and, if faulty or damaged, the entire left
multi-function switch unit must be replaced. (Refer
to 8 - ELECTRICAL/LAMPS/LIGHTING - EXTERI-
OR/TURN SIGNAL/HAZARD SWITCH - REMOVAL)
for the service procedures. (Refer to 8 - ELECTRI-
CAL/ELECTRONIC CONTROL MODULES/BODY
CONTROL/CENTRAL TIMER MODUL - DESCRIP-
TION) for more information on this component.
OPERATION
The exterior lighting switch uses a hard wired five
volt reference circuit from the BCM, resistor multi-
plexing and a hard wired switch output circuit to
provide the BCM with a zero to five volt signal thatindicates the status of all of the exterior lighting
switch settings. The BCM then uses control outputs
to energize the headlamp and park lamp relays that
activate the exterior lighting circuits.
The BCM monitors the exterior lighting switch sta-
tus, then sends the proper switch status messages to
other modules over the Programmable Communica-
tions Interface (PCI) data bus network. The exterior
lighting switch status is also used by the BCM as an
input for chime warning system operation.
DIAGNOSIS AND TESTING Ð HEADLAMP
SWITCH
Before testing the headlamp switch, turn on the
exterior lighting and open the driver side front door.
If the exterior lamps of the vehicle operate, but there
is no chime warning issued with the driver side front
door open, (Refer to 8 - ELECTRICAL/LAMPS/
LIGHTING - INTERIOR/DOOR AJAR SWITCH -
DIAGNOSIS AND TESTING). If the exterior lamps
of the vehicle are inoperative, but the chime warning
is issued, (Refer to 8 - ELECTRICAL/LAMPS/LIGHT-
ING - EXTERIOR - DIAGNOSIS AND TESTING).
If the exterior lamps and the chime warning are
both inoperative, test the left multi-function switch.
(Refer to 8 - ELECTRICAL/LAMPS/LIGHTING -
EXTERIOR - DIAGNOSIS AND TESTING). If the
multi-function switch tests OK, proceed as follows.
The following tests will help to locate a short or open
in the hard wired circuits between the multi-function
switch and the Body Control Module (BCM). For
complete circuit diagrams, refer to the appropriate
wiring information.
WARNING: ON VEHICLES EQUIPPED WITH AIR-
BAGS, REFER TO ELECTRICAL, RESTRAINTS
BEFORE ATTEMPTING ANY STEERING WHEEL,
STEERING COLUMN, OR INSTRUMENT PANEL
COMPONENT DIAGNOSIS OR SERVICE. FAILURE
TO TAKE THE PROPER PRECAUTIONS COULD
RESULT IN ACCIDENTAL AIRBAG DEPLOYMENT
AND POSSIBLE PERSONAL INJURY.
(1) Disconnect and isolate the battery negative
cable. Disconnect the instrument panel wire harness
connector from the left multi-function switch connec-
tor. Disconnect the instrument panel wire harness
connector from the Body Control Module (BCM).
Check for continuity between the headlamp switch
mux circuit of the instrument panel wire harness
connector for the multi-function switch and a good
ground. There should be no continuity. If OK, go to
Step 2. If not OK, repair the shorted headlamp
switch mux circuit.
(2) Check for continuity between the headlamp
switch mux circuit of the instrument panel wire har-
Fig. 13 Headlamp Bulb
1 - HIGH BEAM BULB
2 - LOW BEAM BULB
3 - MARKER BULB
4 - PARK/TURN SIGNAL BULB
WJLAMPS/LIGHTING - EXTERIOR 8L - 15
HEADLAMP (Continued)
Page 474 of 2199

(2) Remove the clockspring from the multi-function
switch mounting housing. (Refer to 8 - ELECTRI-
CAL/RESTRAINTS/CLOCKSPRING - REMOVAL).
(3) Remove the left multi-function switch from the
multi-function switch mounting housing. (Refer to 8 -
ELECTRICAL/LAMPS/LIGHTING - EXTERIOR/
LEFT MULTI-FUNCTION SWITCH - REMOVAL -
LEFT MULTI-FUNCTION SWITCH).
(4) Remove the right multi-function switch from
the multi-function switch mounting housing. (Refer
to 8 - ELECTRICAL/WIPERS/WASHERS/RIGHT
MULTI-FUNCTION SWITCH - REMOVAL).
(5) Remove the screw that secures the multi-func-
tion switch mounting housing to the steering column
housing (Fig. 26).
(6) Remove the multi-function switch mounting
housing (Fig. 27).
INSTALLATION
INSTALLATION - LEFT MULTI-FUNCTION
SWITCH
WARNING: ON VEHICLES EQUIPPED WITH AIR-
BAGS, DISABLE THE AIRBAG SYSTEM BEFORE
ATTEMPTING ANY STEERING WHEEL, STEERING
COLUMN, OR INSTRUMENT PANEL COMPONENT
DIAGNOSIS OR SERVICE. DISCONNECT AND ISO-
LATE THE BATTERY NEGATIVE (GROUND) CABLE,
THEN WAIT TWO MINUTES FOR THE AIRBAG SYS-
TEM CAPACITOR TO DISCHARGE BEFORE PER-
FORMING FURTHER DIAGNOSIS OR SERVICE. THIS
IS THE ONLY SURE WAY TO DISABLE THE AIRBAGSYSTEM. FAILURE TO TAKE THE PROPER PRE-
CAUTIONS COULD RESULT IN ACCIDENTAL AIR-
BAG DEPLOYMENT AND POSSIBLE PERSONAL
INJURY.
(1) Position the left multi-function switch onto the
housing (Fig. 28).
(2) Install and tighten the screws that secure the
left multi-function switch housing. Tighten the
screws to 2.5 N´m (22 in. lbs.).
(3) Reconnect the instrument panel wire harness
connector to the switch connector.
Fig. 26 Multi-Function Switch Mounting Housing
Screw Remove/Install
1 - CLOCK SPRING
2 - SCREW
3 - MULTI-FUNCTION SWITCH MOUNTING HOUSING
Fig. 27 Multi-Function Switch Mounting Housing
Remove/install
1 - MULTI-FUNCTION SWITCH ASSEMBLY
2 - CLOCKSPRING
Fig. 28 Left Multi-Function Switch Remove/Install
1 - SCREW (2)
2 - STEERING COLUMN
3 - MULTI-FUNCTION SWITCH MOUNTING HOUSING
4 - LEFT MULTI-FUNCTION SWITCH
WJLAMPS/LIGHTING - EXTERIOR 8L - 23
LEFT MULTI-FUNCTION SWITCH (Continued)