toe in JEEP GRAND CHEROKEE 2003 WJ / 2.G Workshop Manual
[x] Cancel search | Manufacturer: JEEP, Model Year: 2003, Model line: GRAND CHEROKEE, Model: JEEP GRAND CHEROKEE 2003 WJ / 2.GPages: 2199, PDF Size: 76.01 MB
Page 24 of 2199
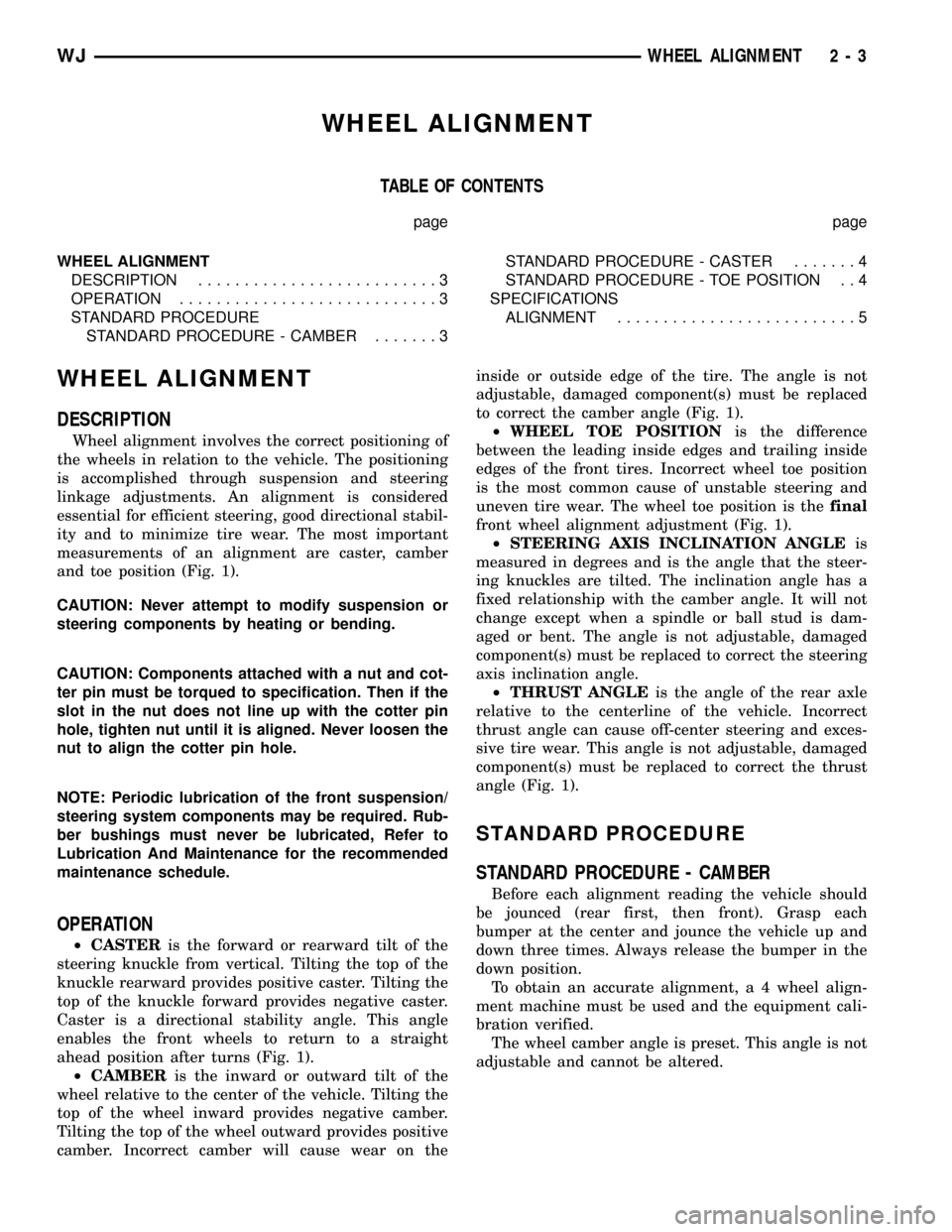
WHEEL ALIGNMENT
TABLE OF CONTENTS
page page
WHEEL ALIGNMENT
DESCRIPTION..........................3
OPERATION............................3
STANDARD PROCEDURE
STANDARD PROCEDURE - CAMBER.......3STANDARD PROCEDURE - CASTER.......4
STANDARD PROCEDURE - TOE POSITION . . 4
SPECIFICATIONS
ALIGNMENT..........................5
WHEEL ALIGNMENT
DESCRIPTION
Wheel alignment involves the correct positioning of
the wheels in relation to the vehicle. The positioning
is accomplished through suspension and steering
linkage adjustments. An alignment is considered
essential for efficient steering, good directional stabil-
ity and to minimize tire wear. The most important
measurements of an alignment are caster, camber
and toe position (Fig. 1).
CAUTION: Never attempt to modify suspension or
steering components by heating or bending.
CAUTION: Components attached with a nut and cot-
ter pin must be torqued to specification. Then if the
slot in the nut does not line up with the cotter pin
hole, tighten nut until it is aligned. Never loosen the
nut to align the cotter pin hole.
NOTE: Periodic lubrication of the front suspension/
steering system components may be required. Rub-
ber bushings must never be lubricated, Refer to
Lubrication And Maintenance for the recommended
maintenance schedule.
OPERATION
²CASTERis the forward or rearward tilt of the
steering knuckle from vertical. Tilting the top of the
knuckle rearward provides positive caster. Tilting the
top of the knuckle forward provides negative caster.
Caster is a directional stability angle. This angle
enables the front wheels to return to a straight
ahead position after turns (Fig. 1).
²CAMBERis the inward or outward tilt of the
wheel relative to the center of the vehicle. Tilting the
top of the wheel inward provides negative camber.
Tilting the top of the wheel outward provides positive
camber. Incorrect camber will cause wear on theinside or outside edge of the tire. The angle is not
adjustable, damaged component(s) must be replaced
to correct the camber angle (Fig. 1).
²WHEEL TOE POSITIONis the difference
between the leading inside edges and trailing inside
edges of the front tires. Incorrect wheel toe position
is the most common cause of unstable steering and
uneven tire wear. The wheel toe position is thefinal
front wheel alignment adjustment (Fig. 1).
²STEERING AXIS INCLINATION ANGLEis
measured in degrees and is the angle that the steer-
ing knuckles are tilted. The inclination angle has a
fixed relationship with the camber angle. It will not
change except when a spindle or ball stud is dam-
aged or bent. The angle is not adjustable, damaged
component(s) must be replaced to correct the steering
axis inclination angle.
²THRUST ANGLEis the angle of the rear axle
relative to the centerline of the vehicle. Incorrect
thrust angle can cause off-center steering and exces-
sive tire wear. This angle is not adjustable, damaged
component(s) must be replaced to correct the thrust
angle (Fig. 1).
STANDARD PROCEDURE
STANDARD PROCEDURE - CAMBER
Before each alignment reading the vehicle should
be jounced (rear first, then front). Grasp each
bumper at the center and jounce the vehicle up and
down three times. Always release the bumper in the
down position.
To obtain an accurate alignment, a 4 wheel align-
ment machine must be used and the equipment cali-
bration verified.
The wheel camber angle is preset. This angle is not
adjustable and cannot be altered.
WJWHEEL ALIGNMENT 2 - 3
Page 25 of 2199
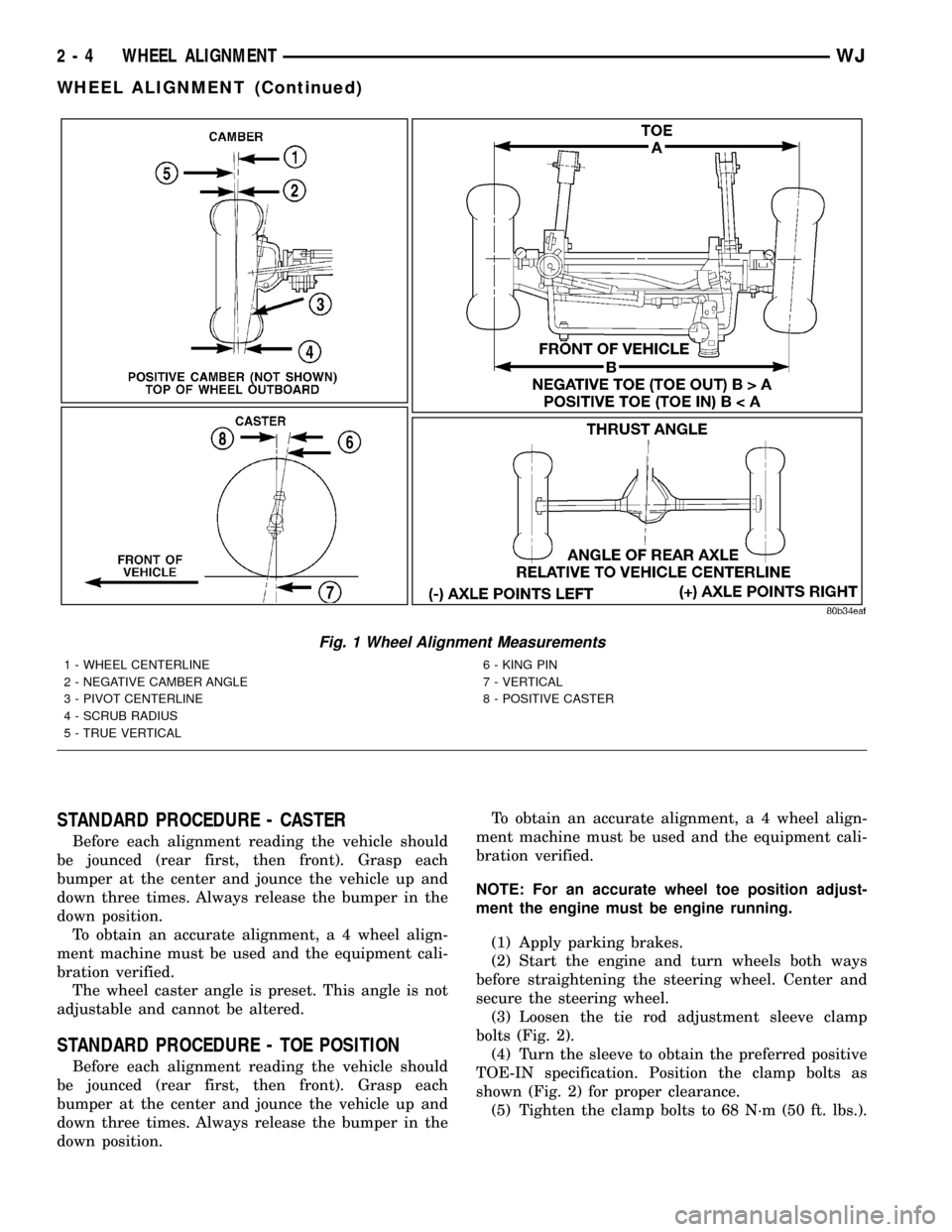
STANDARD PROCEDURE - CASTER
Before each alignment reading the vehicle should
be jounced (rear first, then front). Grasp each
bumper at the center and jounce the vehicle up and
down three times. Always release the bumper in the
down position.
To obtain an accurate alignment, a 4 wheel align-
ment machine must be used and the equipment cali-
bration verified.
The wheel caster angle is preset. This angle is not
adjustable and cannot be altered.
STANDARD PROCEDURE - TOE POSITION
Before each alignment reading the vehicle should
be jounced (rear first, then front). Grasp each
bumper at the center and jounce the vehicle up and
down three times. Always release the bumper in the
down position.To obtain an accurate alignment, a 4 wheel align-
ment machine must be used and the equipment cali-
bration verified.
NOTE: For an accurate wheel toe position adjust-
ment the engine must be engine running.
(1) Apply parking brakes.
(2) Start the engine and turn wheels both ways
before straightening the steering wheel. Center and
secure the steering wheel.
(3) Loosen the tie rod adjustment sleeve clamp
bolts (Fig. 2).
(4) Turn the sleeve to obtain the preferred positive
TOE-IN specification. Position the clamp bolts as
shown (Fig. 2) for proper clearance.
(5) Tighten the clamp bolts to 68 N´m (50 ft. lbs.).
Fig. 1 Wheel Alignment Measurements
1 - WHEEL CENTERLINE
2 - NEGATIVE CAMBER ANGLE
3 - PIVOT CENTERLINE
4 - SCRUB RADIUS
5 - TRUE VERTICAL6 - KING PIN
7 - VERTICAL
8 - POSITIVE CASTER
2 - 4 WHEEL ALIGNMENTWJ
WHEEL ALIGNMENT (Continued)
Page 26 of 2199
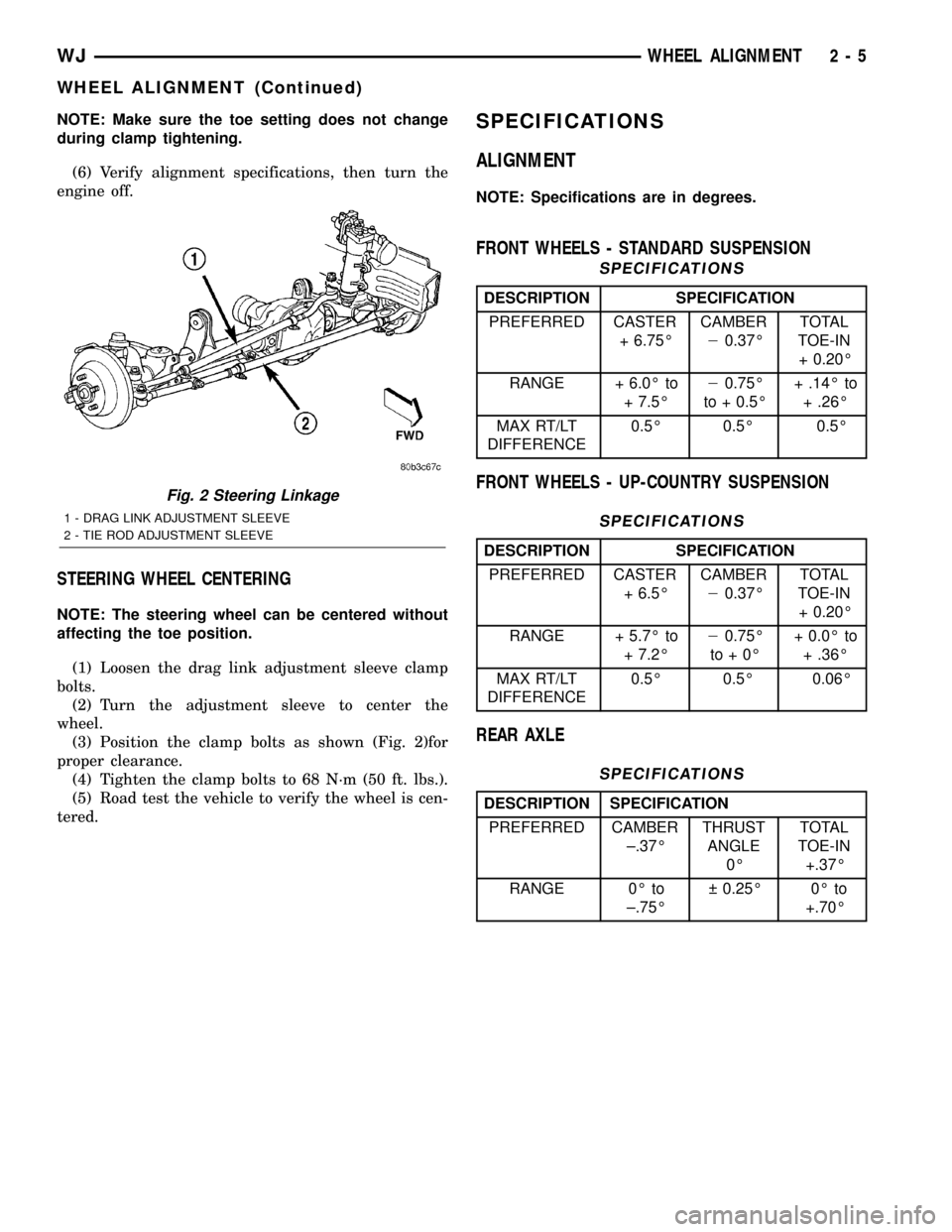
NOTE: Make sure the toe setting does not change
during clamp tightening.
(6) Verify alignment specifications, then turn the
engine off.
STEERING WHEEL CENTERING
NOTE: The steering wheel can be centered without
affecting the toe position.
(1) Loosen the drag link adjustment sleeve clamp
bolts.
(2) Turn the adjustment sleeve to center the
wheel.
(3) Position the clamp bolts as shown (Fig. 2)for
proper clearance.
(4) Tighten the clamp bolts to 68 N´m (50 ft. lbs.).
(5) Road test the vehicle to verify the wheel is cen-
tered.
SPECIFICATIONS
ALIGNMENT
NOTE: Specifications are in degrees.
FRONT WHEELS - STANDARD SUSPENSION
SPECIFICATIONS
DESCRIPTION SPECIFICATION
PREFERRED CASTER
+ 6.75ÉCAMBER
20.37ÉTOTAL
TOE-IN
+ 0.20É
RANGE + 6.0É to
+ 7.5É20.75É
to + 0.5É+ .14É to
+ .26É
MAX RT/LT
DIFFERENCE0.5É 0.5É 0.5É
FRONT WHEELS - UP-COUNTRY SUSPENSION
SPECIFICATIONS
DESCRIPTION SPECIFICATION
PREFERRED CASTER
+ 6.5ÉCAMBER
20.37ÉTOTAL
TOE-IN
+ 0.20É
RANGE + 5.7É to
+ 7.2É20.75É
to+0É+ 0.0É to
+ .36É
MAX RT/LT
DIFFERENCE0.5É 0.5É 0.06É
REAR AXLE
SPECIFICATIONS
DESCRIPTION SPECIFICATION
PREFERRED CAMBER
±.37ÉTHRUST
ANGLE
0ÉTOTAL
TOE-IN
+.37É
RANGE 0É to
±.75É 0.25É 0É to
+.70É
Fig. 2 Steering Linkage
1 - DRAG LINK ADJUSTMENT SLEEVE
2 - TIE ROD ADJUSTMENT SLEEVE
WJWHEEL ALIGNMENT 2 - 5
WHEEL ALIGNMENT (Continued)
Page 363 of 2199
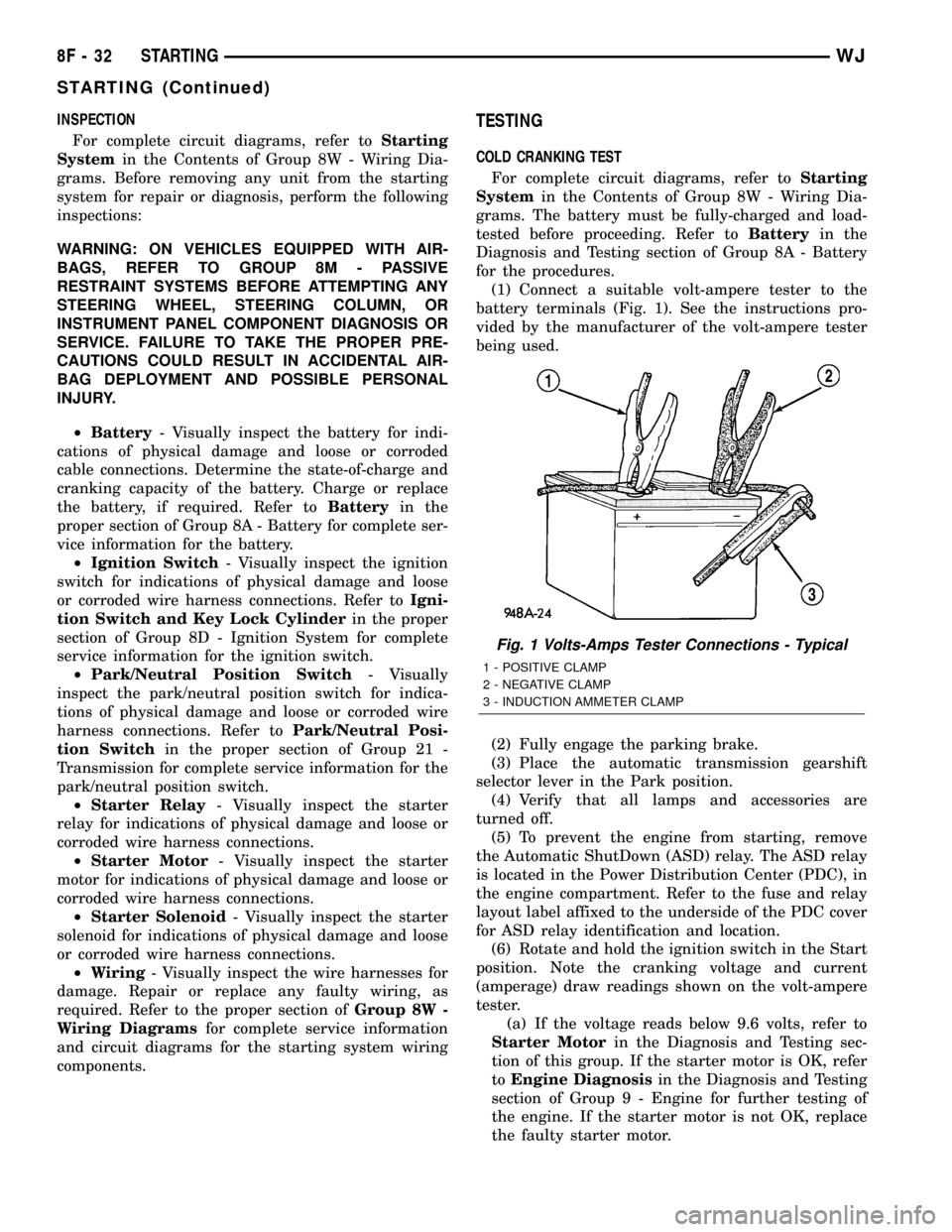
INSPECTION
For complete circuit diagrams, refer toStarting
Systemin the Contents of Group 8W - Wiring Dia-
grams. Before removing any unit from the starting
system for repair or diagnosis, perform the following
inspections:
WARNING: ON VEHICLES EQUIPPED WITH AIR-
BAGS, REFER TO GROUP 8M - PASSIVE
RESTRAINT SYSTEMS BEFORE ATTEMPTING ANY
STEERING WHEEL, STEERING COLUMN, OR
INSTRUMENT PANEL COMPONENT DIAGNOSIS OR
SERVICE. FAILURE TO TAKE THE PROPER PRE-
CAUTIONS COULD RESULT IN ACCIDENTAL AIR-
BAG DEPLOYMENT AND POSSIBLE PERSONAL
INJURY.
²Battery- Visually inspect the battery for indi-
cations of physical damage and loose or corroded
cable connections. Determine the state-of-charge and
cranking capacity of the battery. Charge or replace
the battery, if required. Refer toBatteryin the
proper section of Group 8A - Battery for complete ser-
vice information for the battery.
²Ignition Switch- Visually inspect the ignition
switch for indications of physical damage and loose
or corroded wire harness connections. Refer toIgni-
tion Switch and Key Lock Cylinderin the proper
section of Group 8D - Ignition System for complete
service information for the ignition switch.
²Park/Neutral Position Switch- Visually
inspect the park/neutral position switch for indica-
tions of physical damage and loose or corroded wire
harness connections. Refer toPark/Neutral Posi-
tion Switchin the proper section of Group 21 -
Transmission for complete service information for the
park/neutral position switch.
²Starter Relay- Visually inspect the starter
relay for indications of physical damage and loose or
corroded wire harness connections.
²Starter Motor- Visually inspect the starter
motor for indications of physical damage and loose or
corroded wire harness connections.
²Starter Solenoid- Visually inspect the starter
solenoid for indications of physical damage and loose
or corroded wire harness connections.
²Wiring- Visually inspect the wire harnesses for
damage. Repair or replace any faulty wiring, as
required. Refer to the proper section ofGroup 8W -
Wiring Diagramsfor complete service information
and circuit diagrams for the starting system wiring
components.TESTING
COLD CRANKING TEST
For complete circuit diagrams, refer toStarting
Systemin the Contents of Group 8W - Wiring Dia-
grams. The battery must be fully-charged and load-
tested before proceeding. Refer toBatteryin the
Diagnosis and Testing section of Group 8A - Battery
for the procedures.
(1) Connect a suitable volt-ampere tester to the
battery terminals (Fig. 1). See the instructions pro-
vided by the manufacturer of the volt-ampere tester
being used.
(2) Fully engage the parking brake.
(3) Place the automatic transmission gearshift
selector lever in the Park position.
(4) Verify that all lamps and accessories are
turned off.
(5) To prevent the engine from starting, remove
the Automatic ShutDown (ASD) relay. The ASD relay
is located in the Power Distribution Center (PDC), in
the engine compartment. Refer to the fuse and relay
layout label affixed to the underside of the PDC cover
for ASD relay identification and location.
(6) Rotate and hold the ignition switch in the Start
position. Note the cranking voltage and current
(amperage) draw readings shown on the volt-ampere
tester.
(a) If the voltage reads below 9.6 volts, refer to
Starter Motorin the Diagnosis and Testing sec-
tion of this group. If the starter motor is OK, refer
toEngine Diagnosisin the Diagnosis and Testing
section of Group 9 - Engine for further testing of
the engine. If the starter motor is not OK, replace
the faulty starter motor.
Fig. 1 Volts-Amps Tester Connections - Typical
1 - POSITIVE CLAMP
2 - NEGATIVE CLAMP
3 - INDUCTION AMMETER CLAMP
8F - 32 STARTINGWJ
STARTING (Continued)
Page 490 of 2199
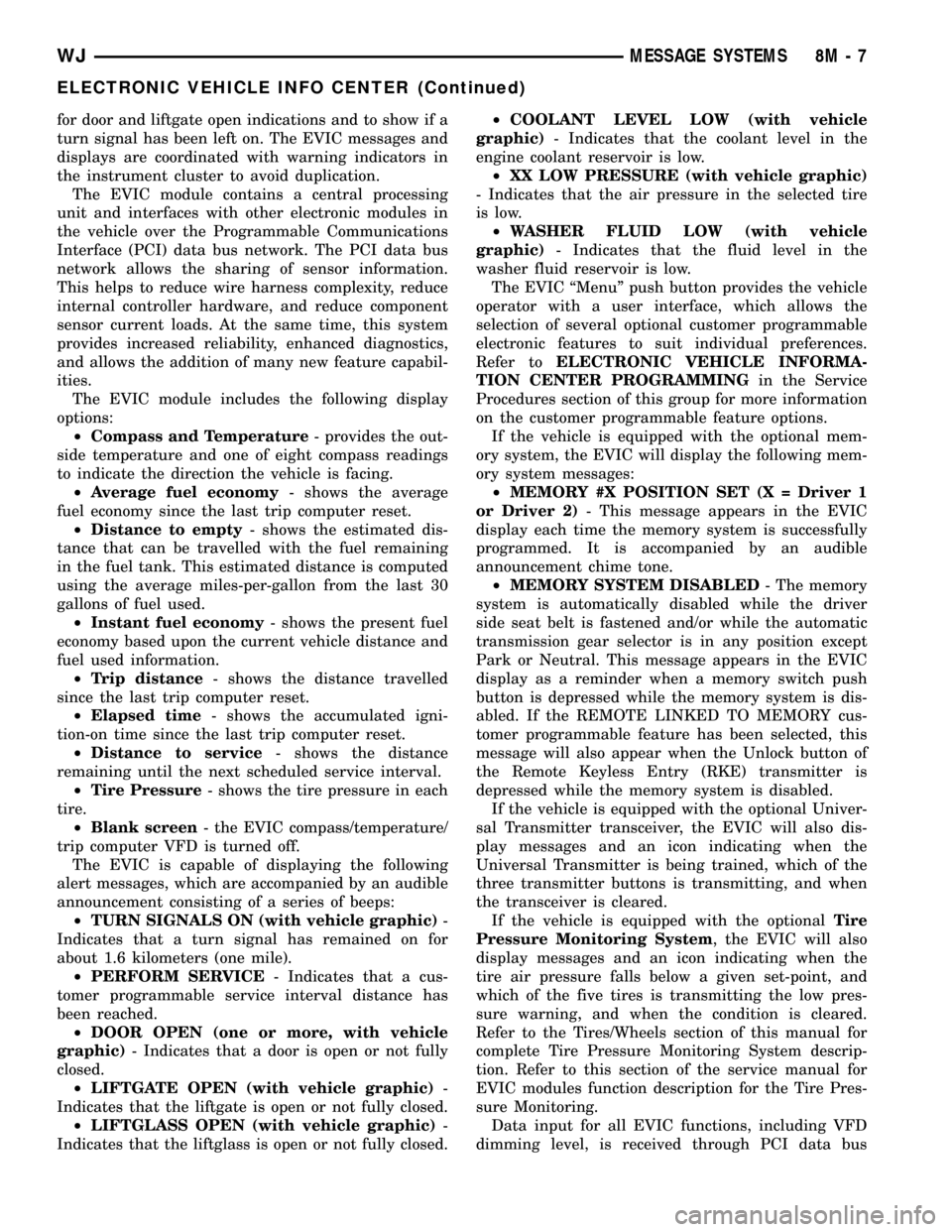
for door and liftgate open indications and to show if a
turn signal has been left on. The EVIC messages and
displays are coordinated with warning indicators in
the instrument cluster to avoid duplication.
The EVIC module contains a central processing
unit and interfaces with other electronic modules in
the vehicle over the Programmable Communications
Interface (PCI) data bus network. The PCI data bus
network allows the sharing of sensor information.
This helps to reduce wire harness complexity, reduce
internal controller hardware, and reduce component
sensor current loads. At the same time, this system
provides increased reliability, enhanced diagnostics,
and allows the addition of many new feature capabil-
ities.
The EVIC module includes the following display
options:
²Compass and Temperature- provides the out-
side temperature and one of eight compass readings
to indicate the direction the vehicle is facing.
²Average fuel economy- shows the average
fuel economy since the last trip computer reset.
²Distance to empty- shows the estimated dis-
tance that can be travelled with the fuel remaining
in the fuel tank. This estimated distance is computed
using the average miles-per-gallon from the last 30
gallons of fuel used.
²Instant fuel economy- shows the present fuel
economy based upon the current vehicle distance and
fuel used information.
²Trip distance- shows the distance travelled
since the last trip computer reset.
²Elapsed time- shows the accumulated igni-
tion-on time since the last trip computer reset.
²Distance to service- shows the distance
remaining until the next scheduled service interval.
²Tire Pressure- shows the tire pressure in each
tire.
²Blank screen- the EVIC compass/temperature/
trip computer VFD is turned off.
The EVIC is capable of displaying the following
alert messages, which are accompanied by an audible
announcement consisting of a series of beeps:
²TURN SIGNALS ON (with vehicle graphic)-
Indicates that a turn signal has remained on for
about 1.6 kilometers (one mile).
²PERFORM SERVICE- Indicates that a cus-
tomer programmable service interval distance has
been reached.
²DOOR OPEN (one or more, with vehicle
graphic)- Indicates that a door is open or not fully
closed.
²LIFTGATE OPEN (with vehicle graphic)-
Indicates that the liftgate is open or not fully closed.
²LIFTGLASS OPEN (with vehicle graphic)-
Indicates that the liftglass is open or not fully closed.²COOLANT LEVEL LOW (with vehicle
graphic)- Indicates that the coolant level in the
engine coolant reservoir is low.
²XX LOW PRESSURE (with vehicle graphic)
- Indicates that the air pressure in the selected tire
is low.
²WASHER FLUID LOW (with vehicle
graphic)- Indicates that the fluid level in the
washer fluid reservoir is low.
The EVIC ªMenuº push button provides the vehicle
operator with a user interface, which allows the
selection of several optional customer programmable
electronic features to suit individual preferences.
Refer toELECTRONIC VEHICLE INFORMA-
TION CENTER PROGRAMMINGin the Service
Procedures section of this group for more information
on the customer programmable feature options.
If the vehicle is equipped with the optional mem-
ory system, the EVIC will display the following mem-
ory system messages:
²MEMORY #X POSITION SET (X = Driver 1
or Driver 2)- This message appears in the EVIC
display each time the memory system is successfully
programmed. It is accompanied by an audible
announcement chime tone.
²MEMORY SYSTEM DISABLED- The memory
system is automatically disabled while the driver
side seat belt is fastened and/or while the automatic
transmission gear selector is in any position except
Park or Neutral. This message appears in the EVIC
display as a reminder when a memory switch push
button is depressed while the memory system is dis-
abled. If the REMOTE LINKED TO MEMORY cus-
tomer programmable feature has been selected, this
message will also appear when the Unlock button of
the Remote Keyless Entry (RKE) transmitter is
depressed while the memory system is disabled.
If the vehicle is equipped with the optional Univer-
sal Transmitter transceiver, the EVIC will also dis-
play messages and an icon indicating when the
Universal Transmitter is being trained, which of the
three transmitter buttons is transmitting, and when
the transceiver is cleared.
If the vehicle is equipped with the optionalTire
Pressure Monitoring System, the EVIC will also
display messages and an icon indicating when the
tire air pressure falls below a given set-point, and
which of the five tires is transmitting the low pres-
sure warning, and when the condition is cleared.
Refer to the Tires/Wheels section of this manual for
complete Tire Pressure Monitoring System descrip-
tion. Refer to this section of the service manual for
EVIC modules function description for the Tire Pres-
sure Monitoring.
Data input for all EVIC functions, including VFD
dimming level, is received through PCI data bus
WJMESSAGE SYSTEMS 8M - 7
ELECTRONIC VEHICLE INFO CENTER (Continued)
Page 494 of 2199
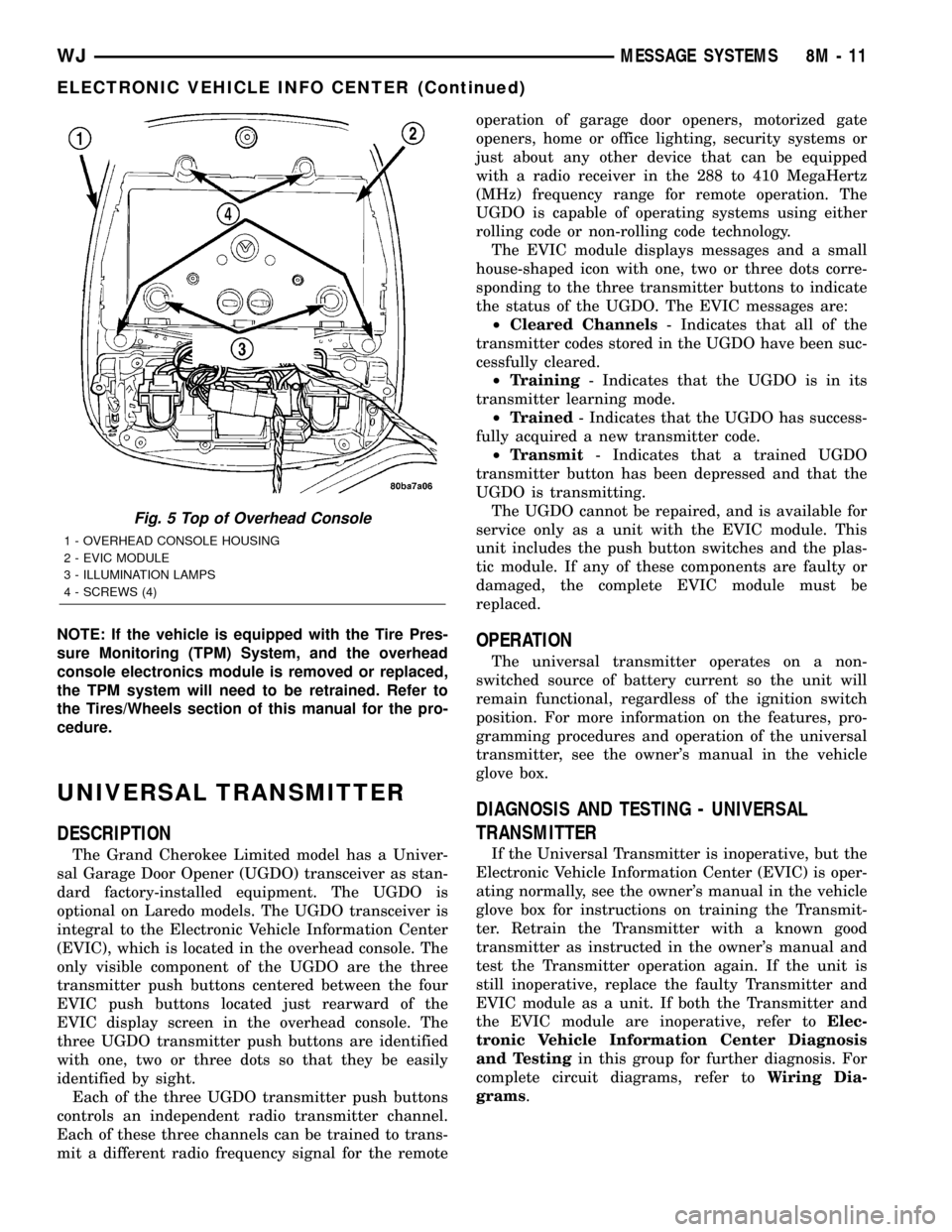
NOTE: If the vehicle is equipped with the Tire Pres-
sure Monitoring (TPM) System, and the overhead
console electronics module is removed or replaced,
the TPM system will need to be retrained. Refer to
the Tires/Wheels section of this manual for the pro-
cedure.
UNIVERSAL TRANSMITTER
DESCRIPTION
The Grand Cherokee Limited model has a Univer-
sal Garage Door Opener (UGDO) transceiver as stan-
dard factory-installed equipment. The UGDO is
optional on Laredo models. The UGDO transceiver is
integral to the Electronic Vehicle Information Center
(EVIC), which is located in the overhead console. The
only visible component of the UGDO are the three
transmitter push buttons centered between the four
EVIC push buttons located just rearward of the
EVIC display screen in the overhead console. The
three UGDO transmitter push buttons are identified
with one, two or three dots so that they be easily
identified by sight.
Each of the three UGDO transmitter push buttons
controls an independent radio transmitter channel.
Each of these three channels can be trained to trans-
mit a different radio frequency signal for the remoteoperation of garage door openers, motorized gate
openers, home or office lighting, security systems or
just about any other device that can be equipped
with a radio receiver in the 288 to 410 MegaHertz
(MHz) frequency range for remote operation. The
UGDO is capable of operating systems using either
rolling code or non-rolling code technology.
The EVIC module displays messages and a small
house-shaped icon with one, two or three dots corre-
sponding to the three transmitter buttons to indicate
the status of the UGDO. The EVIC messages are:
²Cleared Channels- Indicates that all of the
transmitter codes stored in the UGDO have been suc-
cessfully cleared.
²Training- Indicates that the UGDO is in its
transmitter learning mode.
²Trained- Indicates that the UGDO has success-
fully acquired a new transmitter code.
²Transmit- Indicates that a trained UGDO
transmitter button has been depressed and that the
UGDO is transmitting.
The UGDO cannot be repaired, and is available for
service only as a unit with the EVIC module. This
unit includes the push button switches and the plas-
tic module. If any of these components are faulty or
damaged, the complete EVIC module must be
replaced.
OPERATION
The universal transmitter operates on a non-
switched source of battery current so the unit will
remain functional, regardless of the ignition switch
position. For more information on the features, pro-
gramming procedures and operation of the universal
transmitter, see the owner's manual in the vehicle
glove box.
DIAGNOSIS AND TESTING - UNIVERSAL
TRANSMITTER
If the Universal Transmitter is inoperative, but the
Electronic Vehicle Information Center (EVIC) is oper-
ating normally, see the owner's manual in the vehicle
glove box for instructions on training the Transmit-
ter. Retrain the Transmitter with a known good
transmitter as instructed in the owner's manual and
test the Transmitter operation again. If the unit is
still inoperative, replace the faulty Transmitter and
EVIC module as a unit. If both the Transmitter and
the EVIC module are inoperative, refer toElec-
tronic Vehicle Information Center Diagnosis
and Testingin this group for further diagnosis. For
complete circuit diagrams, refer toWiring Dia-
grams.
Fig. 5 Top of Overhead Console
1 - OVERHEAD CONSOLE HOUSING
2 - EVIC MODULE
3 - ILLUMINATION LAMPS
4 - SCREWS (4)
WJMESSAGE SYSTEMS 8M - 11
ELECTRONIC VEHICLE INFO CENTER (Continued)
Page 516 of 2199
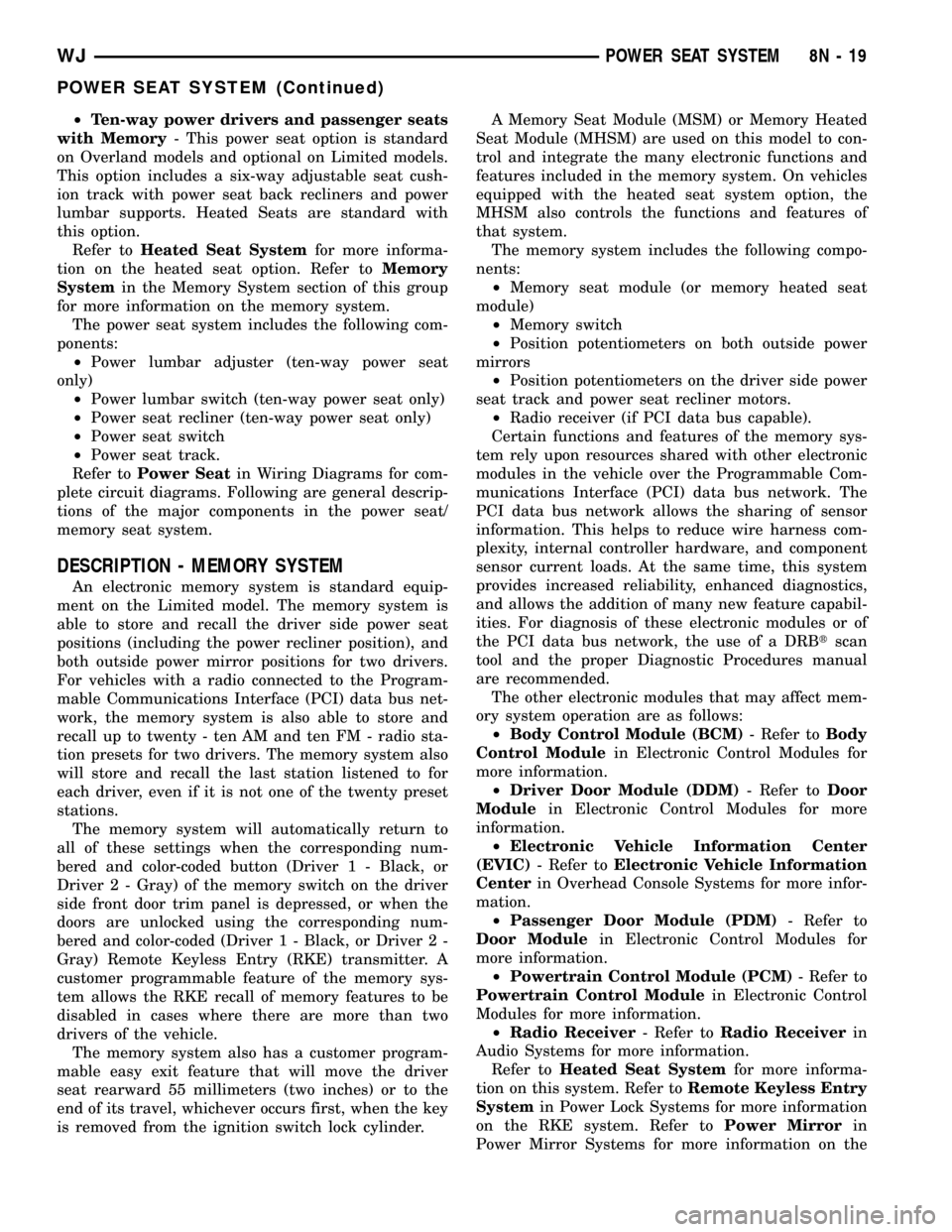
²Ten-way power drivers and passenger seats
with Memory- This power seat option is standard
on Overland models and optional on Limited models.
This option includes a six-way adjustable seat cush-
ion track with power seat back recliners and power
lumbar supports. Heated Seats are standard with
this option.
Refer toHeated Seat Systemfor more informa-
tion on the heated seat option. Refer toMemory
Systemin the Memory System section of this group
for more information on the memory system.
The power seat system includes the following com-
ponents:
²Power lumbar adjuster (ten-way power seat
only)
²Power lumbar switch (ten-way power seat only)
²Power seat recliner (ten-way power seat only)
²Power seat switch
²Power seat track.
Refer toPower Seatin Wiring Diagrams for com-
plete circuit diagrams. Following are general descrip-
tions of the major components in the power seat/
memory seat system.
DESCRIPTION - MEMORY SYSTEM
An electronic memory system is standard equip-
ment on the Limited model. The memory system is
able to store and recall the driver side power seat
positions (including the power recliner position), and
both outside power mirror positions for two drivers.
For vehicles with a radio connected to the Program-
mable Communications Interface (PCI) data bus net-
work, the memory system is also able to store and
recall up to twenty - ten AM and ten FM - radio sta-
tion presets for two drivers. The memory system also
will store and recall the last station listened to for
each driver, even if it is not one of the twenty preset
stations.
The memory system will automatically return to
all of these settings when the corresponding num-
bered and color-coded button (Driver 1 - Black, or
Driver 2 - Gray) of the memory switch on the driver
side front door trim panel is depressed, or when the
doors are unlocked using the corresponding num-
bered and color-coded (Driver 1 - Black, or Driver 2 -
Gray) Remote Keyless Entry (RKE) transmitter. A
customer programmable feature of the memory sys-
tem allows the RKE recall of memory features to be
disabled in cases where there are more than two
drivers of the vehicle.
The memory system also has a customer program-
mable easy exit feature that will move the driver
seat rearward 55 millimeters (two inches) or to the
end of its travel, whichever occurs first, when the key
is removed from the ignition switch lock cylinder.A Memory Seat Module (MSM) or Memory Heated
Seat Module (MHSM) are used on this model to con-
trol and integrate the many electronic functions and
features included in the memory system. On vehicles
equipped with the heated seat system option, the
MHSM also controls the functions and features of
that system.
The memory system includes the following compo-
nents:
²Memory seat module (or memory heated seat
module)
²Memory switch
²Position potentiometers on both outside power
mirrors
²Position potentiometers on the driver side power
seat track and power seat recliner motors.
²Radio receiver (if PCI data bus capable).
Certain functions and features of the memory sys-
tem rely upon resources shared with other electronic
modules in the vehicle over the Programmable Com-
munications Interface (PCI) data bus network. The
PCI data bus network allows the sharing of sensor
information. This helps to reduce wire harness com-
plexity, internal controller hardware, and component
sensor current loads. At the same time, this system
provides increased reliability, enhanced diagnostics,
and allows the addition of many new feature capabil-
ities. For diagnosis of these electronic modules or of
the PCI data bus network, the use of a DRBtscan
tool and the proper Diagnostic Procedures manual
are recommended.
The other electronic modules that may affect mem-
ory system operation are as follows:
²Body Control Module (BCM)- Refer toBody
Control Modulein Electronic Control Modules for
more information.
²Driver Door Module (DDM)- Refer toDoor
Modulein Electronic Control Modules for more
information.
²Electronic Vehicle Information Center
(EVIC)- Refer toElectronic Vehicle Information
Centerin Overhead Console Systems for more infor-
mation.
²Passenger Door Module (PDM)- Refer to
Door Modulein Electronic Control Modules for
more information.
²Powertrain Control Module (PCM)- Refer to
Powertrain Control Modulein Electronic Control
Modules for more information.
²Radio Receiver- Refer toRadio Receiverin
Audio Systems for more information.
Refer toHeated Seat Systemfor more informa-
tion on this system. Refer toRemote Keyless Entry
Systemin Power Lock Systems for more information
on the RKE system. Refer toPower Mirrorin
Power Mirror Systems for more information on the
WJPOWER SEAT SYSTEM 8N - 19
POWER SEAT SYSTEM (Continued)
Page 517 of 2199
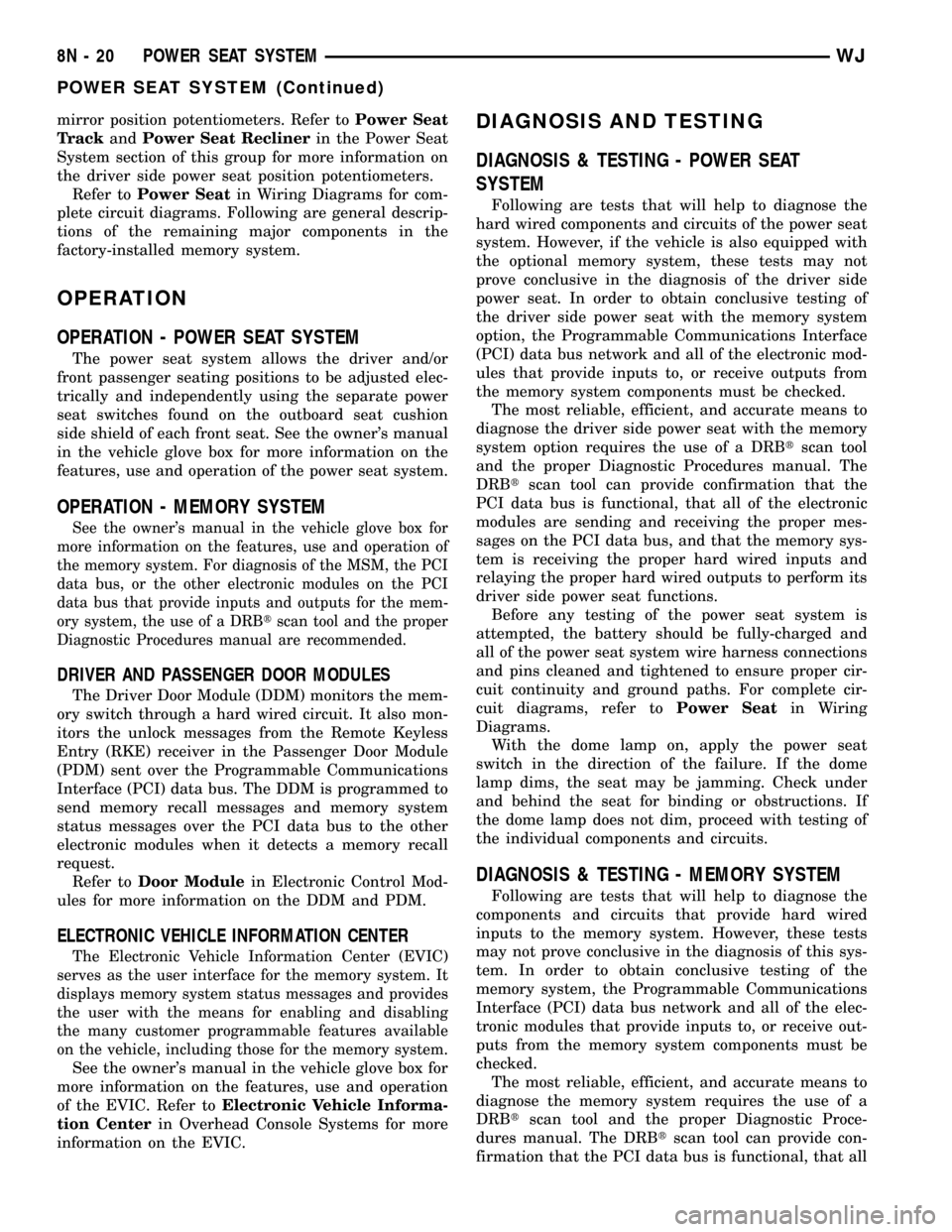
mirror position potentiometers. Refer toPower Seat
TrackandPower Seat Reclinerin the Power Seat
System section of this group for more information on
the driver side power seat position potentiometers.
Refer toPower Seatin Wiring Diagrams for com-
plete circuit diagrams. Following are general descrip-
tions of the remaining major components in the
factory-installed memory system.
OPERATION
OPERATION - POWER SEAT SYSTEM
The power seat system allows the driver and/or
front passenger seating positions to be adjusted elec-
trically and independently using the separate power
seat switches found on the outboard seat cushion
side shield of each front seat. See the owner's manual
in the vehicle glove box for more information on the
features, use and operation of the power seat system.
OPERATION - MEMORY SYSTEM
See the owner's manual in the vehicle glove box for
more information on the features, use and operation of
the memory system. For diagnosis of the MSM, the PCI
data bus, or the other electronic modules on the PCI
data bus that provide inputs and outputs for the mem-
ory system, the use of a DRBtscan tool and the proper
Diagnostic Procedures manual are recommended.
DRIVER AND PASSENGER DOOR MODULES
The Driver Door Module (DDM) monitors the mem-
ory switch through a hard wired circuit. It also mon-
itors the unlock messages from the Remote Keyless
Entry (RKE) receiver in the Passenger Door Module
(PDM) sent over the Programmable Communications
Interface (PCI) data bus. The DDM is programmed to
send memory recall messages and memory system
status messages over the PCI data bus to the other
electronic modules when it detects a memory recall
request.
Refer toDoor Modulein Electronic Control Mod-
ules for more information on the DDM and PDM.
ELECTRONIC VEHICLE INFORMATION CENTER
The Electronic Vehicle Information Center (EVIC)
serves as the user interface for the memory system. It
displays memory system status messages and provides
the user with the means for enabling and disabling
the many customer programmable features available
on the vehicle, including those for the memory system.
See the owner's manual in the vehicle glove box for
more information on the features, use and operation
of the EVIC. Refer toElectronic Vehicle Informa-
tion Centerin Overhead Console Systems for more
information on the EVIC.
DIAGNOSIS AND TESTING
DIAGNOSIS & TESTING - POWER SEAT
SYSTEM
Following are tests that will help to diagnose the
hard wired components and circuits of the power seat
system. However, if the vehicle is also equipped with
the optional memory system, these tests may not
prove conclusive in the diagnosis of the driver side
power seat. In order to obtain conclusive testing of
the driver side power seat with the memory system
option, the Programmable Communications Interface
(PCI) data bus network and all of the electronic mod-
ules that provide inputs to, or receive outputs from
the memory system components must be checked.
The most reliable, efficient, and accurate means to
diagnose the driver side power seat with the memory
system option requires the use of a DRBtscan tool
and the proper Diagnostic Procedures manual. The
DRBtscan tool can provide confirmation that the
PCI data bus is functional, that all of the electronic
modules are sending and receiving the proper mes-
sages on the PCI data bus, and that the memory sys-
tem is receiving the proper hard wired inputs and
relaying the proper hard wired outputs to perform its
driver side power seat functions.
Before any testing of the power seat system is
attempted, the battery should be fully-charged and
all of the power seat system wire harness connections
and pins cleaned and tightened to ensure proper cir-
cuit continuity and ground paths. For complete cir-
cuit diagrams, refer toPower Seatin Wiring
Diagrams.
With the dome lamp on, apply the power seat
switch in the direction of the failure. If the dome
lamp dims, the seat may be jamming. Check under
and behind the seat for binding or obstructions. If
the dome lamp does not dim, proceed with testing of
the individual components and circuits.
DIAGNOSIS & TESTING - MEMORY SYSTEM
Following are tests that will help to diagnose the
components and circuits that provide hard wired
inputs to the memory system. However, these tests
may not prove conclusive in the diagnosis of this sys-
tem. In order to obtain conclusive testing of the
memory system, the Programmable Communications
Interface (PCI) data bus network and all of the elec-
tronic modules that provide inputs to, or receive out-
puts from the memory system components must be
checked.
The most reliable, efficient, and accurate means to
diagnose the memory system requires the use of a
DRBtscan tool and the proper Diagnostic Proce-
dures manual. The DRBtscan tool can provide con-
firmation that the PCI data bus is functional, that all
8N - 20 POWER SEAT SYSTEMWJ
POWER SEAT SYSTEM (Continued)
Page 1229 of 2199

of the preparation procedures performed just prior to
new vehicle delivery.
The PDC has a molded plastic cover that can be
removed to provide service access to all of the fuses
and relays in the PDC. An integral latch and hinges
are molded into the PDC cover for easy removal. A
fuse layout map is integral to the underside of the
PDC cover to ensure proper fuse and relay identifica-
tion. The IOD fuse is a 50 ampere maxi-type car-
tridge fuse and, when removed, it is stored in a spare
fuse cavity within the PDC.
OPERATION
The term ignition-off draw identifies a normal con-
dition where power is being drained from the battery
with the ignition switch in the Off position. The IOD
fuse feeds the memory and sleep mode functions for
some of the electronic modules in the vehicle as well
as various other accessories that require battery cur-
rent when the ignition switch is in the Off position,
including the clock. The only reason the IOD fuse is
removed is to reduce the normal IOD of the vehicle
electrical system during new vehicle transportation
and pre-delivery storage to reduce battery depletion,
while still allowing vehicle operation so that the
vehicle can be loaded, unloaded and moved as needed
by both vehicle transportation company and dealer
personnel.
The IOD fuse is removed from PDC fuse cavity 15
when the vehicle is shipped from the assembly plant.
Dealer personnel must install the IOD fuse when the
vehicle is being prepared for delivery in order to
restore full electrical system operation. Once the
vehicle is prepared for delivery, the IOD function of
this fuse becomes transparent and the fuse that has
been assigned the IOD designation becomes only
another Fused B(+) circuit fuse. The IOD fuse serves
no useful purpose to the dealer technician in the ser-
vice or diagnosis of any vehicle system or condition,
other than the same purpose as that of any other
standard circuit protection device.
The IOD fuse can be used by the vehicle owner as
a convenient means of reducing battery depletion
when a vehicle is to be stored for periods not toexceed about thirty days. However, it must be
remembered that removing the IOD fuse will not
eliminate IOD, but only reduce this normal condition.
If a vehicle will be stored for more than about thirty
days, the battery negative cable should be discon-
nected to eliminate normal IOD; and, the battery
should be tested and recharged at regular intervals
during the vehicle storage period to prevent the bat-
tery from becoming discharged or damaged. Refer to
Battery Systemfor additional service information.
REMOVAL
The Ignition-Off Draw (IOD) fuses normal installa-
tion location is cavity 15 in the power distribution
center. When the vehicle is shipped from the assem-
bly plant the fuse is removed to maintain proper bat-
tery voltage during vehicle storage (in some cases).
Dealer personnel must install the IOD fuse when the
vehicle is being prepared for customer delivery in
order to restore full electrical system operation.
(1) Turn the ignition switch to the Off position.
(2) Unlatch and open the cover of the power distri-
bution center.
(3) Remove the IOD fuse from fusecavity 15of
the power distribution center (Fig. 2).
(4) Store the removed IOD fuse by installing it in
the unused fuse storagecavity 11of the PDC (Fig.
2).
(5) Close and latch the power distribution center
cover.
INSTALLATION
(1) Be certain the ignition switch is in the Off posi-
tion.
(2) Unlatch and open the cover of the power distri-
bution center.
(3) Remove the stored IOD fuse from fuse storage
cavity 11of the power distribution center.
(4) Use a thumb to press the IOD fuse firmly down
into power distribution center fusecavity 15.
(5) Close and latch the power distribution center
cover.
8W - 97 - 4 8W-97 POWER DISTRIBUTIONWJ
IOD FUSE (Continued)
Page 1503 of 2199
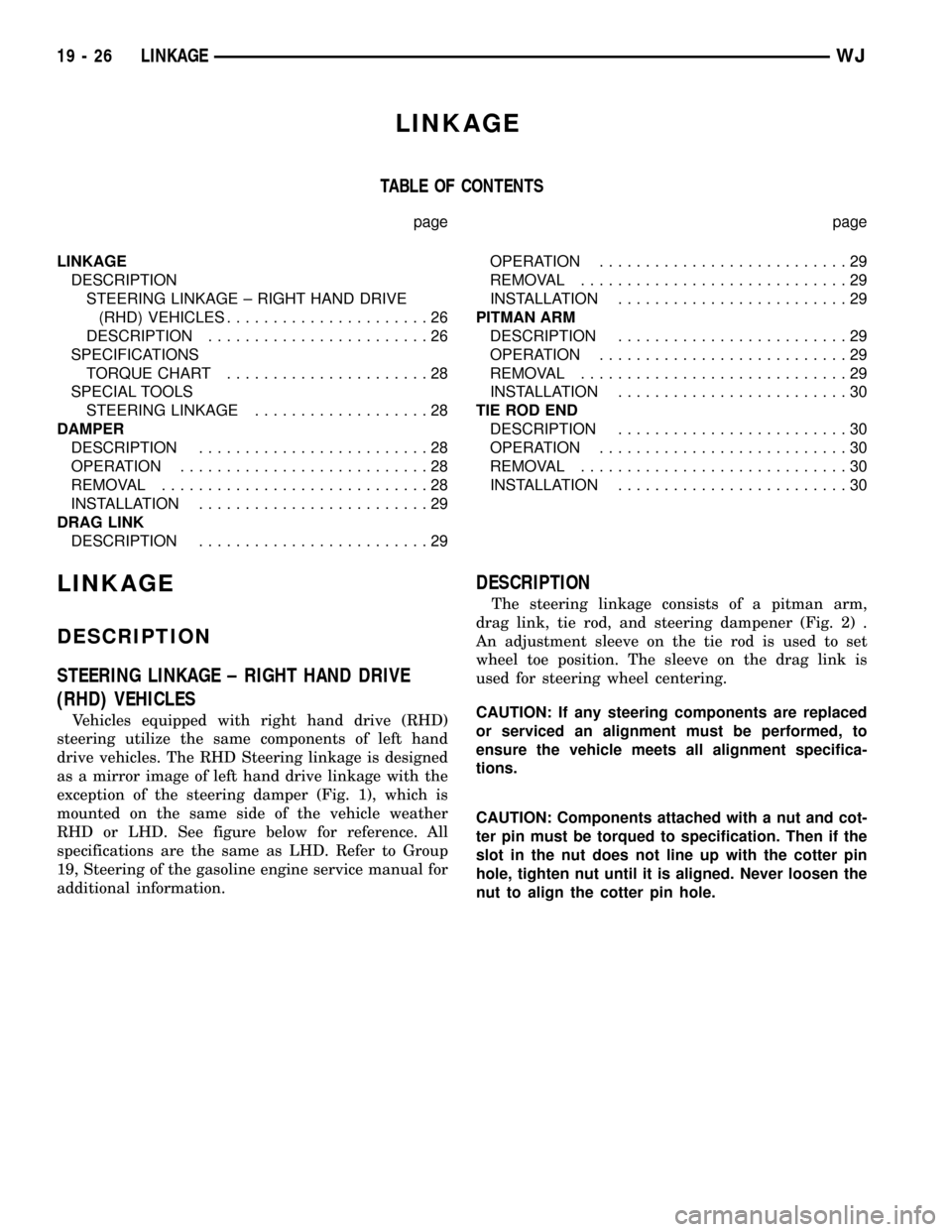
LINKAGE
TABLE OF CONTENTS
page page
LINKAGE
DESCRIPTION
STEERING LINKAGE ± RIGHT HAND DRIVE
(RHD) VEHICLES......................26
DESCRIPTION........................26
SPECIFICATIONS
TORQUE CHART......................28
SPECIAL TOOLS
STEERING LINKAGE...................28
DAMPER
DESCRIPTION.........................28
OPERATION...........................28
REMOVAL.............................28
INSTALLATION.........................29
DRAG LINK
DESCRIPTION.........................29OPERATION...........................29
REMOVAL.............................29
INSTALLATION.........................29
PITMAN ARM
DESCRIPTION.........................29
OPERATION...........................29
REMOVAL.............................29
INSTALLATION.........................30
TIE ROD END
DESCRIPTION.........................30
OPERATION...........................30
REMOVAL.............................30
INSTALLATION.........................30
LINKAGE
DESCRIPTION
STEERING LINKAGE ± RIGHT HAND DRIVE
(RHD) VEHICLES
Vehicles equipped with right hand drive (RHD)
steering utilize the same components of left hand
drive vehicles. The RHD Steering linkage is designed
as a mirror image of left hand drive linkage with the
exception of the steering damper (Fig. 1), which is
mounted on the same side of the vehicle weather
RHD or LHD. See figure below for reference. All
specifications are the same as LHD. Refer to Group
19, Steering of the gasoline engine service manual for
additional information.
DESCRIPTION
The steering linkage consists of a pitman arm,
drag link, tie rod, and steering dampener (Fig. 2) .
An adjustment sleeve on the tie rod is used to set
wheel toe position. The sleeve on the drag link is
used for steering wheel centering.
CAUTION: If any steering components are replaced
or serviced an alignment must be performed, to
ensure the vehicle meets all alignment specifica-
tions.
CAUTION: Components attached with a nut and cot-
ter pin must be torqued to specification. Then if the
slot in the nut does not line up with the cotter pin
hole, tighten nut until it is aligned. Never loosen the
nut to align the cotter pin hole.
19 - 26 LINKAGEWJ